इंजेक्शन मोल्डिंग के सामान्य मोल्डिंग दोषों का समाधान
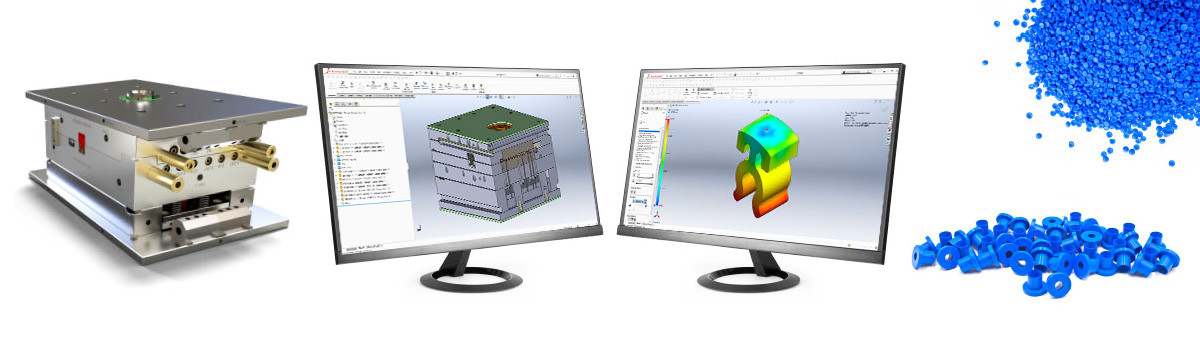
प्लास्टिक इंजेक्शन मोल्डिंग भागों को संसाधित करने के लिए सांचों का उपयोग करते समय दोष आम हैं, और यह प्रसंस्करण दक्षता को काफी हद तक प्रभावित करता है। प्लास्टिक इंजेक्शन मोल्ड भागों के लिए सामान्य मोल्डिंग दोष और समाधान निम्नलिखित हैं।
छोटे शॉट
शॉर्ट शॉट्स से तात्पर्य है कि बने उत्पाद अधूरे हैं क्योंकि सांचे पूरी तरह से भरे नहीं हैं।
यह दोष आमतौर पर गेट या उन हिस्सों से सबसे दूर के स्थान पर दिखाई देता है, जहां मोल्ड पर संकीर्ण क्षेत्रों के माध्यम से ही पहुंचा जा सकता है क्योंकि संकीर्ण क्षेत्र पिघलने के प्रवाह को प्रभावित कर सकते हैं।
शॉर्ट शॉट से सूक्ष्म प्रवाह के निशान हो सकते हैं या उत्पाद का एक बड़ा हिस्सा स्पष्ट रूप से गायब हो सकता है।
कारण:
शॉर्ट शॉट के कारणों में शामिल हैं:
साँचे में डाला गया कच्चा माल पर्याप्त नहीं है।
पिघलने का प्रतिरोध बड़ा है, जिसके परिणामस्वरूप मोल्ड को पूरी तरह से नहीं भरा जा सकता है।
मोल्ड का निकास खराब है और गुहिकायन की उत्पत्ति का कारण बनता है जो पिघल को अवरुद्ध करता है, जिससे पिघल मोल्ड के कुछ क्षेत्रों में प्रवाहित नहीं हो सकता है।
burrs
मोल्ड कैविटी से उत्पाद तक एक्सट्रूडेड अतिरिक्त कच्चे माल के आसंजन से गड़गड़ाहट उत्पन्न होती है।
यह दोष उत्पाद या मोल्ड के प्रत्येक भाग के किनारों पर होगा। कच्चे माल को मोल्ड, या मूविंग और फिक्सिंग मोल्ड्स के बॉन्डिंग साइट्स से ओवरफ्लो किया जा सकता है।
मोल्ड कोर पर गड़गड़ाहट भी पाई जा सकती है, जो हाइड्रोलिक दबाव या कोणीय पिन के कारण होती है।
गड़गड़ाहट की गंभीरता अलग-अलग होती है, कभी पतली, कभी मोटी।
कारण:
गड़गड़ाहट के कारणों में शामिल हैं:
क्लैम्पिंग मोल्ड की सतह क्षतिग्रस्त है या बहुत घिस चुकी है।
मूविंग मोल्ड और फिक्सिंग मोल्ड लॉक होने पर डिस-लोकेटेड होते हैं।
मोल्ड में कच्चे माल का दबाव मोल्ड क्लैम्पिंग बल से अधिक होता है।
ऊपर उल्लिखित तीसरी शर्त विभिन्न कारणों से उत्पन्न होगी। निम्नलिखित स्थितियों में, कच्चे माल का दबाव मोल्ड क्लैम्पिंग बल से अधिक होता है।
इंजेक्शन मोल्ड (मोल्ड फिलिंग स्टेज) के पहले चरण में, बहुत अधिक कच्चा माल भरा जाता है, जिससे मोल्ड के अंदर दबाव बढ़ जाता है।
मोल्ड भरने की प्रक्रिया के दौरान, पिघल प्रवाह का बड़ा प्रतिरोध मोल्ड के अंदर भी दबाव बढ़ाएगा।
दबाव धारण अवस्था के दौरान मोल्ड कैविटी का दबाव बहुत अधिक होता है।
मोल्ड क्लैम्पिंग बल पर्याप्त नहीं है।
थू थू
अपघटन से कई परिणाम हो सकते हैं। समस्या की सीमा और गंभीरता भी भिन्न होती है। सबसे गंभीर मामले में, यह उत्पाद के पूर्ण मलिनकिरण और खराब यांत्रिक गुणों का कारण बन सकता है। स्थानीय क्षरण से केवल काली धारियाँ या धब्बे बनेंगे।
कारण:
गिरावट कच्चे माल के क्षतिग्रस्त होने के कारण होती है। प्लास्टिक बनाने वाली लंबी श्रृंखला के अणु अत्यधिक गर्मी या अत्यधिक अपरूपण तनाव की क्रिया के तहत विघटित हो जाएंगे। अणुओं के अपघटन के दौरान वाष्पशील गैस अपघटन प्रक्रिया को गति देगी, जिससे कच्चे माल का रंग खराब हो जाएगा। बड़ी मात्रा में अणुओं का अपघटन अंततः कच्चे माल की सामग्री को तोड़ देगा और यांत्रिक गुणों पर नकारात्मक प्रभाव डालेगा।
सामग्री बैरल के असमान तापमान के कारण स्थानीय गिरावट हो सकती है।
गिरावट निम्न स्थितियों में हो सकती है:
सामग्री बैरल या गर्म धावक प्रणाली में कच्चे माल को गर्म किया जा रहा है।
बैरल में कच्चा माल बहुत देर तक रहता है।
इंजेक्शन मोल्डिंग प्रक्रिया के दौरान, कच्चे माल पर कतरनी का तनाव बहुत बड़ा होता है। यदि नोजल अवरुद्ध हैं, या गेट और रनर बहुत संकीर्ण हैं, तो यह अपरूपण तनाव को बढ़ा देगा।
विरूपण
सामान्य परिस्थितियों में, उत्पादों का आकार सांचों के अनुरूप होना चाहिए। विरूपण उत्पादों की विकृति को संदर्भित करता है।
जब हालत खराब हो जाती है, तो मोल्ड से बाहर निकलने पर उत्पाद पूरी तरह से ख़राब हो जाएगा। जब स्थिति गंभीर नहीं होती है, तो उत्पाद के आकार में छोटी अनियमितताएँ दिखाई देंगी।
लंबे लेकिन समर्थन किनारों या बड़े विमानों के बिना ऐसे क्षेत्र हैं जो विरूपण के लिए सबसे अधिक प्रवण हैं।
कारण:
विरूपण के कारण:
मोल्ड जारी होने पर तापमान बहुत अधिक होता है।
जैसा कि मोटे और पतले क्षेत्रों में ठंडा होने का समय अलग होता है, या मोल्ड के तापमान में मोल्ड और फिक्सिंग मोल्ड में अंतर होता है, उत्पादों के अंदर संकोचन अलग होता है।
भरते समय मोल्ड प्रवाह सुचारू नहीं होता है (तथाकथित "फ्रीजिंग ओरिएंटेशन") या मोल्ड कैविटी के अंदर का दबाव प्रेशर होल्डिंग स्टेज पर बहुत अधिक होता है।
अशुद्धियों
अशुद्धियाँ अक्सर विभिन्न रंगों, पैच या धारियों में धब्बों के रूप में दिखाई देती हैं। सबसे आम ब्लैक स्पॉट है।
अशुद्धियाँ केवल छोटे धब्बे हो सकती हैं, लेकिन गंभीर होने पर स्पष्ट धारियाँ या डी-कलरिंग का बड़ा हिस्सा भी हो सकता है।
कारण:
अशुद्धियाँ कच्चे माल के साथ मिश्रित हर तरह की चीज़ों के कारण होती हैं, जैसे:
हर तरह की चीज़ें जब बैरल में ले जाया जाता है के साथ मिश्रित कच्चे माल।
कच्चे माल का अपघटन किसी भी काटने के तंत्र से गिर सकता है और कच्चे माल में मिश्रित हो सकता है, जैसे मशीन बोल्ट, सुखाने वाले ड्रम की भीतरी दीवार, जोड़ों / नलिका।
लेमिनेशन
फाड़ना उत्पादों की सतह पर "त्वचा प्रभाव" उत्पन्न करेगा, जो उत्पादों और अन्य कच्चे माल की सतह के गुणों और बनावट में अंतर के कारण होता है, और यह एक छीलने वाली त्वचा बनाता है जिसे हटाया जा सकता है।
जब लेमिनेशन गंभीर होता है, तो पूरा क्रॉस सेक्शन अलग-अलग परतों से बना होता है, और एक साथ पिघलाया नहीं जाता है। जब दोष कम स्पष्ट होते हैं, तो उत्पादों की उपस्थिति आवश्यकताओं को पूरा कर सकती है, लेकिन उत्पादों के यांत्रिक गुणों को तोड़ देगी।
कारण:
फाड़ना के दो मुख्य कारण हैं। पहला वह है जब दो अलग-अलग प्रकार के कच्चे माल को एक साथ गलत तरीके से मिलाया जाता है। दबाव में एक ही समय में दो कच्चे माल को बैरल में ले जाया जाएगा। हालाँकि, जब ठंडा होने पर मोल्ड को एक साथ नहीं पिघलाया जा सकता है, जैसे कि उत्पादों को बनाने के लिए अलग-अलग परतों को जबरन एक साथ दबाया जाता है।
दूसरा: यदि ठंड के पिघलने को संकीर्ण द्वार से गुजरने के लिए मजबूर किया जाता है, तो कतरनी का तनाव उत्पन्न होगा। बहुत अधिक कतरनी तनाव के कारण पिघली हुई परत पहले से पिघल जाएगी और पूरी तरह से फ्यूज नहीं हो पाएगी।
मिश्रण का खतरा:
एक बात का ध्यान रखना चाहिए कि कुछ कच्चे माल को एक साथ मिलाने से मजबूत रासायनिक प्रतिक्रिया होती है, जैसे कि पीवीसी और एवेटल को नहीं मिलाया जाना चाहिए।
रजत रैखिक
स्लिवर रैखिक केवल स्थानीय घटना हो सकती है, लेकिन गंभीर होने पर पूरी सतह पर इसका विस्तार किया जा सकता है।
सिल्वर लीनियर उत्पादों की उपस्थिति को प्रभावित करेगा और उत्पादों के यांत्रिक गुणों को भी नुकसान पहुँचाएगा।
कारण:
निम्नलिखित दो बिंदु चांदी के रैखिक का कारण बनते हैं:
कच्चा माल गीला है और उनमें से कुछ हवा में भाप को सोख लेंगे। यदि कच्चा माल बहुत अधिक गीला है, तो उच्च तापमान और बैरल के उच्च दबाव के तहत दबावयुक्त वाष्प उत्पन्न हो सकता है। ये वाष्प उत्पाद की सतह से होकर निकल जाते हैं और चांदी की धारियां बनाते हैं।
पिघला हुआ थर्मल क्षतिग्रस्त हो गया और स्थानीय गिरावट उत्पन्न करता है। उत्पन्न वाष्पशील गैस मोल्ड की सतह पर अवरुद्ध हो जाएगी और उत्पादों की सतह पर पट्टियां उत्पन्न करेगी।
यह पतन जितना बुरा नहीं है। जब तक पिघल का तापमान अधिक होता है या यह प्लास्टिसाइजेशन के दौरान कतरनी के तनाव के अधीन होता है या मोल्ड में इंजेक्ट होता है, ऐसा हो सकता है।
चमक / छाया
उत्पादों की सतह की फिनिश मोल्ड्स की तरह ही होनी चाहिए। जब दो की सतह खत्म अलग होती है, तो चमक/छाया दोष उत्पन्न होता है।
दोष होने पर सतह उदास होगी, और खुरदरी सतह चिकनी और चमकदार होगी।
कारण:
चमक/छाया के कारणों में शामिल हैं:
पिघल बिना सुचारू रूप से बहता है या मोल्ड की सतह का तापमान कम होता है, जिसके परिणामस्वरूप मोल्ड की सतह खत्म होने पर सामग्री मोल्डिंग के दौरान डुप्लिकेट नहीं किया जा सकता है।
दबाव बनाए रखने के दौरान, गुहा में दबाव इतना अधिक नहीं होता है कि सामग्री को ठंडा करने की प्रक्रिया में मोल्ड की सतह से चिपक जाता है, जिससे संकोचन के निशान निकल जाते हैं।
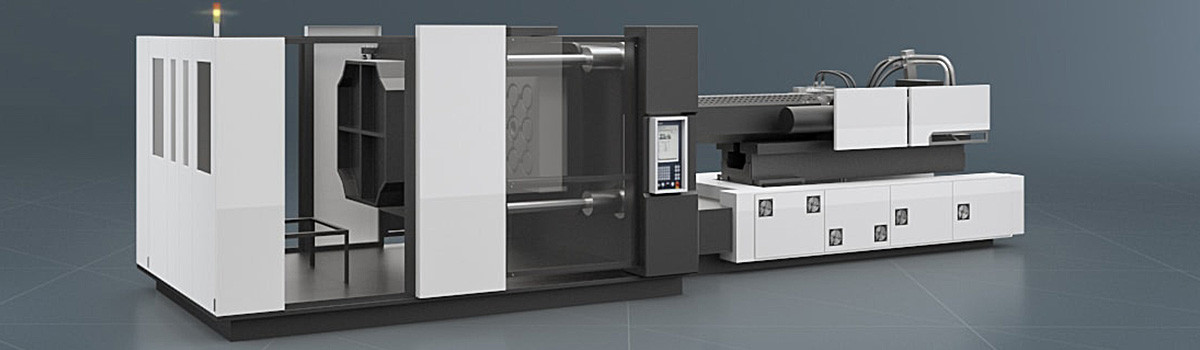
प्रवाह चिह्न
प्रवाह के निशान उत्पादों की सतह पर कई रूपों में पाए जा सकते हैं। आम तौर पर, यह एक छाया क्षेत्र का निर्माण करेगा।
प्रवाह के निशान उत्पादों की सतह पर कोई उभरा हुआ या गड्ढा नहीं बनाते हैं, जिसे उंगलियों से महसूस नहीं किया जा सकता है। इस दोष को ड्रैग मार्क, घोस्टिंग और शैडो भी कहते हैं।
जब प्रवाह के निशान स्पष्ट होते हैं, तो यह खांचे उत्पन्न करेगा, और उत्पादों की सतह पर दोष जैसे निशान छोड़ देगा।
कारण:
प्रवाह के निशान तब पाए जा सकते हैं जब:
पिघलने की प्रवाह क्षमता खराब है या मोल्ड की सतह का तापमान कम है, जिसके परिणामस्वरूप मोल्ड भरने की प्रक्रिया में प्लास्टिक का एक बड़ा प्रवाह प्रतिरोध होता है।
मोल्ड भरने में, प्रतिरोध के साथ पिघला हुआ प्रवाह, जो मरने की असमान सतह, मरने की सतह पर मुद्रित अंक या पैटर्न, या भरने की प्रक्रिया के दौरान पिघल प्रवाह दिशा में परिवर्तन के कारण हो सकता है।
जुड़ने वाली रेखा
ज्वाइनिंग लाइन तब उत्पन्न होती है जब दो पिघले हुए मोर्चे मोल्ड भरने के दौरान मिलते हैं, और एक लाइन की तरह उत्पाद की सतह पर दिखाई देंगे।
ज्वाइनिंग लाइन उत्पादों की सतह पर क्रैकिंग लाइन की तरह है, जिसका पता लगाना स्पष्ट नहीं है।
सांचों को डिजाइन करते समय, कुछ दिखाई देने वाली जुड़ने वाली रेखाएं अपरिहार्य होती हैं। इस मामले में, उत्पादों की ताकत और उपस्थिति को क्षतिग्रस्त होने से रोकने के लिए ज्वाइनिंग लाइन को जितना संभव हो उतना छोटा कर देता है।
कारण:
मेल्ट फ्रंट के बनने के कई कारण हैं। सबसे संभावित कारण मोल्ड कोर के किनारों के साथ पिघला हुआ प्रवाह हो सकता है। जब दोनों पिघलते हैं, तो यह जुड़ने वाली रेखाएँ बनाता है। दो पिघले हुए मोर्चे का तापमान इतना अधिक होना चाहिए कि वे सफलतापूर्वक एक साथ फ्यूज हो सकें, और उत्पादों की ताकत और उपस्थिति को प्रभावित न करें।
जब दो पिघल पूरी तरह से एक साथ नहीं मिल सकते हैं, तो दोष उत्पन्न होंगे।
दोषों के कारण:
मोल्ड में मोटे और पतले हिस्से होते हैं, और पिघलने की प्रवाह गति अलग होती है, जब पिघला हुआ मोल्ड के पतले हिस्से से बहता है, तो तापमान कम होता है।
हर धावक की लंबाई अलग-अलग होती है। एकाकी धावकों को शांत करना आसान होगा।
मोल्ड कैविटी प्रेशर इतना पर्याप्त नहीं है कि प्रेशर होल्डिंग स्टेज के दौरान मेल्ट पूरी तरह से फ्यूज हो जाए।
शेष बुलबुले पिघले हुए मोर्चे को फ्यूज करने में असमर्थ बना देते हैं, जिससे जलन भी होगी।
दहन
जलन शॉर्ट शॉट के समान है, लेकिन अनियमित लुप्त होती किनारों और हल्की जलती हुई गंध के साथ। स्थिति गंभीर होने पर उत्पाद पर कार्बन ब्लैक क्षेत्र दिखाई देंगे, साथ ही प्लास्टिक के जलने की गंध भी आएगी।
यदि दोषों को समाप्त नहीं किया जाता है, तो मोल्ड पर अक्सर काला जमाव होता है। यदि जलने से उत्पन्न गैस या तेल पदार्थों की तुरंत जाँच नहीं की जाती है, तो वे वायु छिद्रों को अवरुद्ध कर सकते हैं। जलन आमतौर पर रास्तों के अंत में पाई जाती है।
कारण:
जलन आंतरिक दहन प्रभाव के कारण होती है। जब हवा में दबाव बहुत कम समय में तेजी से बढ़ता है, तो तापमान बढ़ेगा और जलने का कारण बनेगा। एकत्रित आंकड़ों के मुताबिक, इंजेक्शन मोल्डिंग प्रक्रिया में आंतरिक दहन प्रभाव 600 डिग्री तक उच्च तापमान का उत्पादन कर सकता है।
जलने का उत्पादन तब हो सकता है जब:
मोल्ड भरने की गति तेज है ताकि हवा को मोल्ड गुहा से खाली नहीं किया जा सके, और आने वाले प्लास्टिक के ब्लॉक के कारण हवा के बुलबुले उत्पन्न होते हैं, और संपीड़ित होने के बाद आंतरिक दहन प्रभाव पैदा होता है।
वायु छिद्र अवरुद्ध हैं या वेंटिलेशन सुचारू नहीं है।
सांचे में हवा को हवा के छिद्रों से खाली किया जाना चाहिए। यदि वेंटिलेशन स्थिति, संख्या, आकार या कार्यों से प्रभावित होता है, तो हवा मोल्ड में रहेगी और जलने की ओर ले जाएगी। बड़े मोल्ड क्लैम्पिंग बल से खराब वेंटिलेशन भी होगा।
संकोचन
संकोचन उत्पादों की सतह पर मामूली गड्ढों को संदर्भित करता है।
जब दोष मामूली होते हैं, तो उत्पादों की सतह असमान होती है। जब यह गंभीर होता है, तो उत्पादों का बड़ा क्षेत्र ढह जाएगा। मेहराब, हैंडल और प्रोट्रेशन्स वाले उत्पाद अक्सर संकोचन दोष से पीड़ित होते हैं।
कारण:
संकोचन शीतलन के दौरान कच्चे माल के बड़े क्षेत्र के संकोचन के कारण होता है।
उत्पादों के मोटे क्षेत्र (मेहराब की तरह) में, सामग्री का मुख्य समशीतोष्ण कम होता है, इसलिए बाद में सतह की तुलना में संकोचन होगा, जो कच्चे माल के अंदर एक संकुचन बल पैदा करेगा, और बाहरी पक्ष को आवक अवसाद में खींचेगा सिकुड़न पैदा करने के लिए।
निम्नलिखित स्थितियों में सिकुड़न होती है:
शीतलन प्रक्रिया में कच्चे माल के संकोचन से उत्पन्न बल की तुलना में मोल्ड गुहा में दबाव कम होता है।
शीतलन प्रक्रिया के दौरान मोल्ड गुहा का अपर्याप्त दबाव समय, जिसके परिणामस्वरूप गेट से गुहा से कच्चे माल का प्रवाह होता है।
मोल्डिंग और प्रेशर होल्डिंग चरण के दौरान कच्चे माल में पर्याप्त बफरिंग क्षमता नहीं होती है क्योंकि अत्यधिक कच्चे माल को इंजेक्ट करने से पहले पेंच पूरी तरह से वापस ले लिया जाता है।
फाटकों और धावकों के क्रॉस सेक्शन क्षेत्र उत्पादों की मोटाई की तुलना में बहुत छोटे हैं, जिसका अर्थ है कि उत्पाद बाहर निकालना प्रक्रिया से पहले ही फाटकों को जमे हुए हैं।
बुलबुले
वैक्यूम बुलबुले हवा के बुलबुले के रूप में प्रस्तुत किए जाते हैं, जो पारदर्शी उत्पादों पर आसानी से पाए जा सकते हैं। इसे अपारदर्शी उत्पादों के क्रॉस सेक्शन पर भी देखा जा सकता है।
कारण:
हवा के बुलबुले उत्पादों का निर्वात हिस्सा है, जो शीतलन प्रक्रिया के दौरान कच्चे माल के सिकुड़ने पर उत्पन्न होते हैं।
संकोचन के समान, कच्चे माल के अंदर सिकुड़न बल पैदा करता है। क्या अंतर है कि बुलबुले बनने पर उत्पादों की बाहरी उपस्थिति जम जाती है, और कोई पतन नहीं होता है, इसलिए खोखले बुलबुले उत्पन्न होते हैं।
बुलबुले के कारण कमी के समान ही हैं, जिनमें निम्न शामिल हैं:
अक्षम मोल्ड गुहा दबाव
अपर्याप्त गुहा दबाव समय
रनर और गेट का साइज बहुत छोटा होता है
छिड़काव के निशान
छिड़काव के निशान गेट के सामने थ्रेडेड क्षेत्र को संदर्भित करते हैं। छिड़काव के निशान न केवल उत्पादों की उपस्थिति को प्रभावित करते हैं, बल्कि उत्पादों की ताकत को भी प्रभावित करते हैं।
कारण:
छिड़काव के निशान मोल्ड भरने की प्रक्रिया के दौरान पिघल प्रवाह के नियंत्रण से बाहर होने के कारण होते हैं।
भारी दबाव में पिघला हुआ प्लास्टिक सांचे में मिल जाता है। यदि मोल्ड भरने की गति बहुत अधिक है, तो प्लास्टिक मोल्ड गुहा के खुले अंतराल से निकल जाएगा, और जल्दी से वापस वसंत और ठंडा हो जाएगा। उस समय, धागे बनते हैं, जो पिघले हुए प्लास्टिक को फाटकों में प्रवेश करने से रोकते हैं।
छिड़काव के निशान का मुख्य कारण फाटकों की गलत स्थिति या फाटकों के डिजाइन हैं। निम्नलिखित दो स्थितियों से दोषों की स्थिति और खराब हो जाएगी:
उच्च मोल्ड भरने की गति
मोल्ड भरने के दौरान खराब पिघल प्रवाह