थर्माप्लास्टिक इंजेक्शन मोल्डिंग
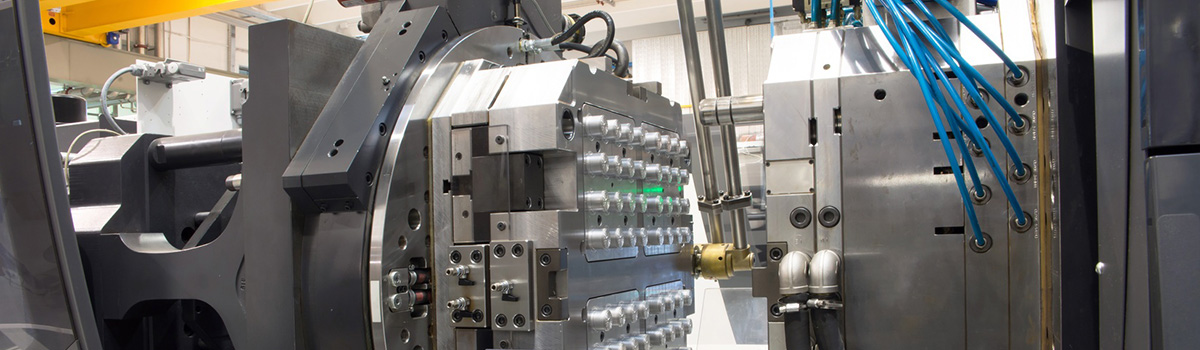
थर्माप्लास्टिक इंजेक्शन मोल्डिंग एक लोकप्रिय निर्माण प्रक्रिया है जिसका उपयोग कई उद्योगों के लिए विभिन्न प्लास्टिक भागों को बनाने के लिए किया जाता है। इस प्रक्रिया में प्लास्टिक के छर्रों को पिघलाना और उन्हें तीन आयामी आकार देने के लिए एक सांचे में इंजेक्ट करना शामिल है। थर्माप्लास्टिक इंजेक्शन मोल्डिंग सख्त सहनशीलता के साथ उच्च गुणवत्ता वाले प्लास्टिक भागों की बड़ी मात्रा के उत्पादन के लिए अत्यधिक कुशल और लागत प्रभावी है। यह व्यापक मार्गदर्शिका थर्माप्लास्टिक इंजेक्शन मोल्डिंग के विभिन्न पहलुओं का पता लगाएगी, जिसमें इसके फायदे और नुकसान, इस्तेमाल किए गए थर्माप्लास्टिक के प्रकार, इंजेक्शन मोल्डिंग प्रक्रिया, डिजाइन के विचार और बहुत कुछ शामिल हैं।
थर्मोप्लास्टिक इंजेक्शन मोल्डिंग का इतिहास
थर्मोप्लास्टिक इंजेक्शन मोल्डिंग का इतिहास तकनीकी प्रगति, सामग्री विकास और औद्योगिक अनुप्रयोगों की एक सदी से अधिक समय तक फैला है। सेल्युलाइड मोल्डिंग प्रक्रिया के रूप में अपनी साधारण शुरुआत से लेकर आज की परिष्कृत तकनीक तक, इंजेक्शन मोल्डिंग एक महत्वपूर्ण विनिर्माण तकनीक बनी हुई है, जो नवाचार लाती है और विभिन्न उद्योगों को आकार देती है।
- प्रारंभिक विकास:जॉन वेस्ले हयात और उनके भाई यशायाह ने पहली व्यावहारिक इंजेक्शन मोल्डिंग मशीन विकसित की, जिससे 19वीं शताब्दी के अंत में थर्मोप्लास्टिक इंजेक्शन मोल्डिंग की उत्पत्ति का पता चला। 1872 में, उन्होंने एक ऐसे उपकरण का पेटेंट कराया, जो प्लंजर का उपयोग करके सेल्युलाइड को मोल्ड कैविटी में इंजेक्ट करता था, जिससे ठोस वस्तुएं बनती थीं। इस सफलता ने आधुनिक इंजेक्शन मोल्डिंग प्रक्रिया की नींव रखी।
- सामग्री में प्रगति:20वीं सदी की शुरुआत में, नए सिंथेटिक पॉलिमर पेश करने से इंजेक्शन मोल्डिंग के लिए नई संभावनाएं खुल गईं। बेकेलाइट, एक फेनोलिक रेज़िन, अपने उत्कृष्ट विद्युत इन्सुलेशन गुणों के कारण मोल्डिंग के लिए एक लोकप्रिय सामग्री बन गया। 1930 और 1940 के दशक के दौरान, पॉलिमर रसायन विज्ञान में प्रगति के कारण पॉलीस्टाइनिन और पॉलीइथाइलीन जैसे अन्य थर्मोप्लास्टिक्स का विकास हुआ, जिसने इंजेक्शन मोल्डिंग के लिए उपयुक्त सामग्रियों की श्रृंखला का और विस्तार किया।
- औद्योगिक अंगीकरण: थर्मोप्लास्टिक इंजेक्शन मोल्डिंग को व्यापक रूप से अपनाना 1950 के दशक में शुरू हुआ क्योंकि निर्माताओं ने इसकी लागत-प्रभावशीलता और बहुमुखी प्रतिभा को पहचाना। उच्च दबाव वाली मशीनें पेश करने से चक्र समय में तेजी आई और उत्पादन मात्रा में वृद्धि हुई। परिणामस्वरूप, व्यक्तिगत और औद्योगिक उपयोग दोनों के लिए उत्पादों का विविध चयन अस्तित्व में आया। इनमें कार के घटक, घरेलू उपकरण और खेलने की चीजें शामिल थीं।
- तकनीकी नवाचार:दशकों से, इंजेक्शन मोल्डिंग तकनीक का विकास जारी रहा। 1960 के दशक में, कंप्यूटर-नियंत्रित मशीनें उभरीं, जिससे मोल्डिंग प्रक्रिया पर सटीक नियंत्रण संभव हो गया। 1980 के दशक में हॉट रनर सिस्टम की शुरूआत ने अपशिष्ट को कम किया और रनर और स्प्रूज़ की आवश्यकता को समाप्त करके दक्षता में सुधार किया। हाल के वर्षों में, स्वचालन, रोबोटिक्स और 3डी प्रिंटिंग प्रगति ने इंजेक्शन मोल्डिंग उद्योग में और क्रांति ला दी है, जिससे जटिल डिजाइन सक्षम हो गए हैं और उत्पादन समय कम हो गया है।
- स्थिरता और पुनर्चक्रण:बढ़ती पर्यावरणीय चिंताओं के साथ, इंजेक्शन मोल्डिंग उद्योग ने स्थिरता उपायों को अपनाया है। निर्माताओं ने जैव-आधारित और पुनर्नवीनीकरण थर्मोप्लास्टिक्स विकसित किया है, जिससे जीवाश्म ईंधन-आधारित सामग्रियों पर निर्भरता कम हो गई है। इसके अतिरिक्त, बेहतर रीसाइक्लिंग प्रौद्योगिकियों ने उपभोक्ता-उपभोक्ता और पोस्ट-औद्योगिक कचरे के पुन: प्रसंस्करण को सक्षम किया है, जिससे थर्मोप्लास्टिक इंजेक्शन मोल्डिंग के पर्यावरणीय प्रभाव को कम किया जा सका है।
- भविष्य की संभावनाओं:थर्मोप्लास्टिक इंजेक्शन मोल्डिंग का भविष्य आशाजनक दिखता है। उद्योग लघु घटकों के लिए माइक्रो-इंजेक्शन मोल्डिंग, जटिल भागों के लिए बहु-सामग्री और ओवरमोल्डिंग तकनीक और प्रक्रिया निगरानी और अनुकूलन के लिए बुद्धिमान प्रौद्योगिकियों को एकीकृत करने जैसे नवाचारों की खोज कर रहा है। इसके अलावा, शोधकर्ताओं को उम्मीद है कि बायोडिग्रेडेबल सामग्रियों और एडिटिव मैन्युफैक्चरिंग में प्रगति से क्षेत्र में क्रांति आ जाएगी, जिससे इंजेक्शन मोल्डिंग और भी अधिक टिकाऊ और बहुमुखी हो जाएगी।
थर्मोप्लास्टिक इंजेक्शन मोल्डिंग के लाभ
थर्माप्लास्टिक इंजेक्शन मोल्डिंग निर्माताओं के लिए कई फायदे प्रदान करता है। यह डिज़ाइन लचीलापन प्रदान करता है, जिससे विभिन्न विशेषताओं के साथ जटिल और जटिल डिज़ाइन की अनुमति मिलती है। यह प्रक्रिया लागत प्रभावी है, सामग्री की बर्बादी को कम करती है और इकाई लागत को कम करती है। थर्मोप्लास्टिक इंजेक्शन मोल्डिंग विभिन्न सामग्रियों का समर्थन करता है, जो विभिन्न अनुप्रयोगों के लिए बहुमुखी प्रतिभा प्रदान करता है।
- डिजाइन लचीलापन:थर्मोप्लास्टिक इंजेक्शन मोल्डिंग अंडरकट्स, पतली दीवारों और अलग-अलग मोटाई जैसी सुविधाओं के साथ जटिल और जटिल डिजाइन की अनुमति देता है, जिससे डिजाइनरों को अत्यधिक स्वतंत्रता मिलती है।
- कीमत का सामर्थ्य: यह प्रक्रिया अत्यधिक कुशल है, जिससे सामग्री की बर्बादी कम होती है और इकाई लागत कम होती है। कई भागों की एक साथ ढलाई और तेज़ उत्पादन चक्र लागत बचत में योगदान करते हैं।
- सामग्री की बहुमुखी प्रतिभा: थर्मोप्लास्टिक इंजेक्शन मोल्डिंग सामग्रियों की एक विस्तृत श्रृंखला का समर्थन करता है, जो निर्माताओं को प्रत्येक एप्लिकेशन के लिए सबसे उपयुक्त विकल्प चुनने में सक्षम बनाता है, जिसमें कठोर या लचीला, पारदर्शी या अपारदर्शी और रासायनिक रूप से प्रतिरोधी सामग्री शामिल है।
- शक्ति और स्थायित्व:इंजेक्शन-मोल्डेड थर्मोप्लास्टिक्स उच्च शक्ति, क्रूरता और प्रभाव प्रतिरोध जैसे उत्कृष्ट यांत्रिक गुणों का प्रदर्शन कर सकते हैं। सुदृढीकरण विकल्प, जैसे ग्लास या कार्बन फाइबर, इन गुणों को और बढ़ाते हैं।
- संगति और गुणवत्ता:इंजेक्शन मोल्डिंग लगातार पार्ट-टू-पार्ट गुणवत्ता और आयामी सटीकता सुनिश्चित करता है, सख्त सहनशीलता और विश्वसनीय उत्पाद प्रदान करता है। यह प्रक्रिया एक चिकनी और समान सतह फिनिश भी प्रदान करती है, जिससे अतिरिक्त फिनिशिंग कार्यों की आवश्यकता समाप्त हो जाती है।
- स्केलेबिलिटी और बड़े पैमाने पर उत्पादन:इंजेक्शन मोल्डिंग कम से उच्च मात्रा में स्केलेबल है, जो इसे बड़े पैमाने पर उत्पादन के लिए उपयुक्त बनाती है। एक बार जब निर्माता सांचा बना लेते हैं, तो वे न्यूनतम विविधताओं के साथ बड़ी मात्रा में समान भागों का उत्पादन कर सकते हैं।
- एकीकरण और संयोजन:इंजेक्शन-मोल्ड किए गए हिस्से कई घटकों को एक टुकड़े में शामिल कर सकते हैं, जिससे अतिरिक्त असेंबली प्रक्रियाओं की आवश्यकता कम हो जाती है। यह एकीकरण उत्पाद के प्रदर्शन को बढ़ाता है, संयोजन समय को कम करता है और लागत कम करता है।
- स्थिरता:इंजेक्शन मोल्डिंग उद्योग स्थिरता पर अधिक ध्यान केंद्रित कर रहा है। जैव-आधारित और पुनर्नवीनीकरण सामग्री की उपलब्धता पर्यावरण के अनुकूल उत्पादों के उत्पादन की अनुमति देती है। थर्मोप्लास्टिक्स की कुशल सामग्री का उपयोग और पुनर्चक्रण हरित विनिर्माण प्रक्रिया में योगदान देता है।
इन लाभों ने इसे विभिन्न उद्योगों में व्यापक रूप से अपनाई जाने वाली विनिर्माण पद्धति बना दिया है, जो जटिल उत्पाद आवश्यकताओं के लिए उच्च गुणवत्ता, लागत प्रभावी और पर्यावरण के अनुकूल समाधान प्रदान करती है।
थर्मोप्लास्टिक इंजेक्शन मोल्डिंग के नुकसान
जबकि थर्मोप्लास्टिक इंजेक्शन मोल्डिंग कई फायदे प्रदान करता है, वहीं कई नुकसान भी हैं। निर्माताओं को अपने विशिष्ट अनुप्रयोगों के लिए थर्मोप्लास्टिक इंजेक्शन मोल्डिंग की उपयुक्तता निर्धारित करने के लिए इन कारकों का सावधानीपूर्वक मूल्यांकन करने और उन्हें लाभों के आधार पर तौलने की आवश्यकता है।
- उच्च प्रारंभिक निवेश: थर्मोप्लास्टिक इंजेक्शन मोल्डिंग ऑपरेशन की स्थापना के लिए मोल्ड डिजाइन और निर्माण और विशेष मशीनरी खरीदने में महत्वपूर्ण प्रारंभिक निवेश की आवश्यकता होती है। सांचे बनाने और टूलींग से जुड़ी लागत काफी हो सकती है, खासकर जटिल और जटिल डिजाइनों के लिए।
- डिज़ाइन सीमाएँ: जबकि थर्मोप्लास्टिक इंजेक्शन मोल्डिंग डिज़ाइन लचीलापन प्रदान करता है, कुछ सीमाएँ मौजूद हैं। उदाहरण के लिए, पूरे हिस्से में एक समान दीवार की मोटाई हासिल करना चुनौतीपूर्ण हो सकता है, जिससे सामग्री वितरण में भिन्नता और संभावित संरचनात्मक कमजोरियां हो सकती हैं। इसके अतिरिक्त, अंडरकट्स या जटिल ज्यामिति की उपस्थिति के लिए अतिरिक्त मोल्ड सुविधाओं या द्वितीयक संचालन के उपयोग की आवश्यकता हो सकती है, जिससे लागत और उत्पादन समय में वृद्धि हो सकती है।
- लंबे लीड टाइम्स:इंजेक्शन मोल्डिंग के लिए सांचों को डिजाइन करने और बनाने की प्रक्रिया में समय लग सकता है, जिससे उत्पाद विकास में लंबा समय लग सकता है। डिज़ाइन पुनरावृत्ति प्रक्रिया, मोल्ड उत्पादन और परीक्षण समग्र उत्पादन समयरेखा में महत्वपूर्ण समय जोड़ सकते हैं, जो तंग समय सीमा वाली परियोजनाओं के लिए उपयुक्त नहीं हो सकता है।
- सामग्री चयन बाधाएँ:यद्यपि थर्मोप्लास्टिक इंजेक्शन मोल्डिंग सामग्रियों की एक विस्तृत श्रृंखला का समर्थन करता है, लेकिन कुछ सीमाएँ और बाधाएँ हैं। कुछ सामग्रियों में विशिष्ट प्रसंस्करण आवश्यकताएं या सीमित उपलब्धता हो सकती है, जो किसी विशेष एप्लिकेशन के लिए डिज़ाइन विकल्पों और सामग्री चयन को प्रभावित कर सकती हैं।
- भाग आकार सीमाएँ:इंजेक्शन मोल्डिंग मशीनों की आकार सीमाएं होती हैं, डिवाइस के भौतिक आकार और उनके द्वारा समायोजित किए जा सकने वाले सांचों के आकार दोनों के संदर्भ में। विशाल भागों के उत्पादन के लिए विशेष उपकरण या वैकल्पिक विनिर्माण विधियों की आवश्यकता हो सकती है।
- पर्यावरणीय प्रभाव:जबकि उद्योग स्थिरता की दिशा में काम कर रहा है, थर्मोप्लास्टिक इंजेक्शन मोल्डिंग प्रक्रिया अभी भी स्क्रैप और स्प्रूस सहित अपशिष्ट पदार्थ उत्पन्न करती है। पर्यावरणीय प्रभाव को कम करने के लिए इन सामग्रियों का उचित निपटान और पुनर्चक्रण आवश्यक है।
- प्रक्रिया अनुकूलन की जटिलता:थर्मोप्लास्टिक इंजेक्शन मोल्डिंग के लिए इष्टतम प्रक्रिया पैरामीटर प्राप्त करना जटिल और समय लेने वाला हो सकता है। निर्माताओं को लगातार भाग की गुणवत्ता सुनिश्चित करने और दोषों को कम करने के लिए तापमान, दबाव, शीतलन दर और चक्र समय को सावधानीपूर्वक नियंत्रित और अनुकूलित करना चाहिए।
इंजेक्शन मोल्डिंग में प्रयुक्त थर्मोप्लास्टिक्स के प्रकार
ये आमतौर पर इंजेक्शन मोल्डिंग में उपयोग किए जाने वाले थर्मोप्लास्टिक्स के कुछ उदाहरण हैं। प्रत्येक सामग्री में अद्वितीय गुण होते हैं, जो इसे ताकत, लचीलेपन, रासायनिक प्रतिरोध, पारदर्शिता और लागत के आधार पर विशिष्ट अनुप्रयोगों के लिए उपयुक्त बनाते हैं। निर्माताओं को अपने इंजेक्शन मोल्डिंग प्रोजेक्ट के लिए उपयुक्त थर्मोप्लास्टिक का चयन करते समय इन गुणों और आवश्यकताओं पर विचार करना चाहिए।
- पॉलीप्रोपाइलीन (पीपी):पॉलीप्रोपाइलीन एक बहुमुखी थर्मोप्लास्टिक है जिसका उपयोग आमतौर पर इंजेक्शन मोल्डिंग में किया जाता है। यह उत्कृष्ट रासायनिक प्रतिरोध, कम घनत्व और अच्छी प्रभाव शक्ति प्रदान करता है। पीपी (पॉलीप्रोपाइलीन) का पैकेजिंग, ऑटोमोटिव घटकों, घरेलू उपकरणों और चिकित्सा उपकरणों में व्यापक अनुप्रयोग है।
- पॉलीथीन (पीई):पॉलीथीन इंजेक्शन मोल्डिंग में एक और व्यापक रूप से इस्तेमाल किया जाने वाला थर्मोप्लास्टिक है। यह विभिन्न रूपों में उपलब्ध है, जैसे उच्च-घनत्व पॉलीथीन (एचडीपीई) और कम-घनत्व पॉलीथीन (एलडीपीई)। पीई अच्छा रासायनिक प्रतिरोध, कठोरता और लचीलापन प्रदान करता है, जो इसे बोतलों, कंटेनरों और पाइपों के लिए उपयुक्त बनाता है।
- पॉलीस्टाइनिन (पीएस):पॉलीस्टाइनिन एक बहुमुखी थर्मोप्लास्टिक है जो अपनी स्पष्टता, कठोरता और सामर्थ्य के लिए जाना जाता है। इसका पैकेजिंग, उपभोक्ता वस्तुओं और डिस्पोजेबल उत्पादों में आम उपयोग होता है। पीएस (पॉलीस्टाइनिन) त्वरित प्रसंस्करण की अनुमति देता है और अच्छी आयामी स्थिरता प्रदान करता है, लेकिन यह पर्यावरणीय तनाव क्रैकिंग के लिए भंगुर और अतिसंवेदनशील हो सकता है।
- एक्रिलोनिट्राइल ब्यूटाडाइन स्टाइरीन (ABS): एबीएस एक लोकप्रिय थर्मोप्लास्टिक है जो अपने उत्कृष्ट प्रभाव प्रतिरोध और स्थायित्व के लिए जाना जाता है। यह ऑटोमोटिव पार्ट्स, इलेक्ट्रॉनिक हाउसिंग और खिलौनों के लिए उपयुक्त एक बहुमुखी सामग्री बनाने के लिए एक्रिलोनिट्राइल, ब्यूटाडीन और स्टाइरीन के गुणों को जोड़ती है।
- पॉलीविनाइल क्लोराइड (पीवीसी): पीवीसी एक व्यापक रूप से उपयोग किया जाने वाला थर्मोप्लास्टिक है जो अपने उत्कृष्ट रासायनिक प्रतिरोध, स्थायित्व और कम लागत के लिए जाना जाता है। यह उपयोग किए गए फॉर्मूलेशन और एडिटिव्स के आधार पर कठोर या लचीला हो सकता है। पीवीसी (पॉलीविनाइल क्लोराइड) का निर्माण, विद्युत इन्सुलेशन, स्वास्थ्य देखभाल उत्पादों और पैकेजिंग में आम उपयोग होता है।
- पॉली कार्बोनेट (पीसी): पॉलीकार्बोनेट असाधारण प्रभाव और उच्च ताप प्रतिरोध वाला एक पारदर्शी थर्मोप्लास्टिक है। यह उन अनुप्रयोगों में आम उपयोग पाता है जिनके लिए ऑप्टिकल स्पष्टता की आवश्यकता होती है, जैसे ऑटोमोटिव घटक, सुरक्षा हेलमेट और इलेक्ट्रॉनिक डिस्प्ले।
- नायलॉन (पॉलियामाइड):नायलॉन एक मजबूत और टिकाऊ थर्मोप्लास्टिक है जो अपने उत्कृष्ट यांत्रिक गुणों और रासायनिक प्रतिरोध के लिए जाना जाता है। यह उन अनुप्रयोगों में आम उपयोग पाता है जो उच्च शक्ति की मांग करते हैं, जैसे ऑटोमोटिव पार्ट्स, औद्योगिक घटक और उपभोक्ता सामान।
- पॉलीइथाइलीन टेरेफ्थेलेट (पीईटी):पीईटी बोतलों, कंटेनरों और पैकेजिंग सामग्री के उत्पादन के लिए एक लोकप्रिय थर्मोप्लास्टिक है। यह अच्छी स्पष्टता, रासायनिक प्रतिरोध और अवरोधक गुण प्रदान करता है, जो इसे भोजन और पेय अनुप्रयोगों के लिए उपयुक्त बनाता है।
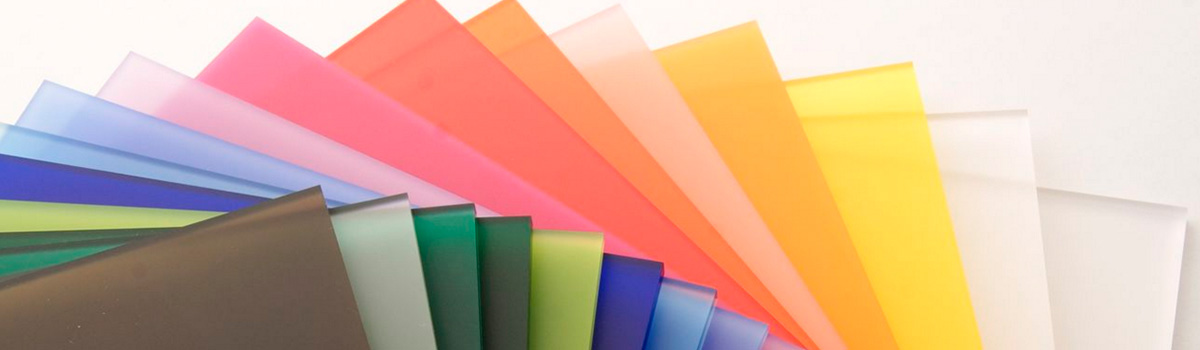
इंजेक्शन मोल्डिंग में प्रयुक्त थर्मोप्लास्टिक्स के गुण
थर्मोप्लास्टिक्स के ये गुण विशिष्ट इंजेक्शन मोल्डिंग अनुप्रयोगों के लिए उनकी उपयुक्तता निर्धारित करने में महत्वपूर्ण भूमिका निभाते हैं। निर्माताओं को इन गुणों पर सावधानीपूर्वक विचार करना चाहिए और वांछित प्रदर्शन, पर्यावरणीय परिस्थितियों और लागत आवश्यकताओं के आधार पर उपयुक्त थर्मोप्लास्टिक का चयन करना चाहिए।
- मैकेनिकल गुण:इंजेक्शन मोल्डिंग में उपयोग किए जाने वाले थर्मोप्लास्टिक्स विभिन्न यांत्रिक गुणों को प्रदर्शित कर सकते हैं, जिनमें तन्य शक्ति, प्रभाव प्रतिरोध और लचीली ताकत शामिल है। ये गुण लागू बलों को झेलने की सामग्री की क्षमता और विभिन्न अनुप्रयोगों में इसके समग्र स्थायित्व को निर्धारित करते हैं।
- रासायनिक प्रतिरोध:इंजेक्शन मोल्डिंग में उपयोग किए जाने वाले कई थर्मोप्लास्टिक्स में रसायनों, सॉल्वैंट्स और तेलों के प्रति उल्लेखनीय प्रतिरोध होता है। यह गुण उन अनुप्रयोगों के लिए महत्वपूर्ण है जिनमें कठोर वातावरण या संक्षारक पदार्थों का संपर्क शामिल है।
- तापीय स्थिरता:थर्मोप्लास्टिक्स की थर्मल स्थिरता महत्वपूर्ण गिरावट के बिना ऊंचे तापमान का सामना करने की उनकी क्षमता को संदर्भित करती है। कुछ थर्मोप्लास्टिक्स उत्कृष्ट ताप प्रतिरोध प्रदर्शित करते हैं, जिससे वे उच्च तापमान पर भी अपने यांत्रिक गुणों को बनाए रख सकते हैं।
- विद्युत गुण:इंजेक्शन मोल्डिंग में उपयोग किए जाने वाले थर्मोप्लास्टिक्स में विद्युत इन्सुलेशन, चालकता, या ढांकता हुआ ताकत सहित विशिष्ट विद्युत गुण हो सकते हैं। ये गुण विद्युत और इलेक्ट्रॉनिक उद्योगों में अनुप्रयोगों के लिए आवश्यक हैं, जहां सामग्रियों को विश्वसनीय विद्युत प्रदर्शन प्रदान करना चाहिए।
- पारदर्शिता और स्पष्टता:कुछ थर्मोप्लास्टिक्स, जैसे पॉलीकार्बोनेट और पीईटी, उत्कृष्ट पारदर्शिता और स्पष्टता प्रदान करते हैं, जो उन्हें उन अनुप्रयोगों के लिए उपयुक्त बनाते हैं जिनके लिए ऑप्टिकल गुणों की आवश्यकता होती है। निर्माता आमतौर पर इन सामग्रियों का उपयोग पारदर्शी खिड़कियों, लेंस और डिस्प्ले जैसे उत्पादों में करते हैं।
- लचीलापन और कठोरता: लचीलापन और कठोरता उन अनुप्रयोगों में उपयोग किए जाने वाले थर्मोप्लास्टिक्स के आवश्यक गुण हैं जिनके लिए प्रभाव प्रतिरोध और स्थायित्व की आवश्यकता होती है। कुछ थर्मोप्लास्टिक्स, जैसे एबीएस और नायलॉन, उत्कृष्ट कठोरता प्रदान करते हैं, जिससे वे बिना टूटे बार-बार के प्रभावों का सामना कर सकते हैं।
- आयामी स्थिरता:आयामी स्थिरता तापमान परिवर्तन सहित विभिन्न परिस्थितियों में अपने आकार और आकार को बनाए रखने की थर्मोप्लास्टिक की क्षमता को संदर्भित करती है। अच्छी आयामी स्थिरता वाली सामग्रियां लगातार भाग आयाम सुनिश्चित करती हैं, जिससे विकृति या विरूपण का जोखिम कम हो जाता है।
- रासायनिक अनुकूलता:थर्मोप्लास्टिक्स की रासायनिक अनुकूलता एसिड, बेस और सॉल्वैंट्स सहित विभिन्न रसायनों के साथ गिरावट या बातचीत का विरोध करने की उनकी क्षमता को संदर्भित करती है। इष्टतम प्रदर्शन सुनिश्चित करने के लिए, ऐसे थर्मोप्लास्टिक का चयन करना आवश्यक है जो इच्छित अनुप्रयोग में विशिष्ट रासायनिक वातावरण का सामना कर सके।
- घनत्व: थर्मोप्लास्टिक्स की मोटाई अलग-अलग होती है, जो उनके वजन और समग्र भाग के गुणों को प्रभावित कर सकती है। कम घनत्व वाली सामग्री, जैसे कि पॉलीथीन, हल्के समाधान प्रदान करती है, जबकि उच्च घनत्व वाली सामग्री, जैसे पॉलीप्रोपाइलीन, अतिरिक्त ताकत और कठोरता प्रदान करती है।
इंजेक्शन मोल्डिंग प्रक्रिया: चरण-दर-चरण
इंजेक्शन मोल्डिंग प्रक्रिया इन चरणों का पालन करती है, जिससे उच्च गुणवत्ता वाले थर्मोप्लास्टिक भागों के कुशल और सटीक उत्पादन की अनुमति मिलती है। सुसंगत भाग आयाम, सामग्री गुण और समग्र गुणवत्ता सुनिश्चित करने के लिए प्रत्येक चरण में सावधानीपूर्वक नियंत्रण और निगरानी की आवश्यकता होती है।
- मोल्ड डिजाइन और निर्माण: इंजेक्शन मोल्डिंग प्रक्रिया में पहला कदम मोल्ड का डिजाइन और निर्माण है। वांछित भाग विनिर्देशों को प्राप्त करने के लिए निर्माताओं को एक सटीक और विस्तृत मोल्ड डिज़ाइन बनाना होगा। निर्माता फिर सीएनसी या इलेक्ट्रिकल डिस्चार्ज मशीनिंग (ईडीएम) जैसी विभिन्न तकनीकों का उपयोग करके मोल्ड बनाते हैं।
- सामग्री तैयारी: साँचा तैयार हो जाने पर अगला चरण तैयारी है। थर्मोप्लास्टिक छर्रों या कणिकाओं को वांछित सामग्री गुणों के आधार पर चुना जाता है और एक हॉपर में पिघलाया जाता है। ऑपरेटर फिर सामग्री को इंजेक्शन मोल्डिंग मशीन के बैरल में डालते हैं, जहां यह पिघलने और समरूपीकरण से गुजरता है।
- इंजेक्शन:इंजेक्शन चरण के दौरान, ऑपरेटर उच्च दबाव के तहत पिघले हुए थर्मोप्लास्टिक को मोल्ड गुहा में इंजेक्ट करते हैं। मशीन की इंजेक्शन इकाई पिघली हुई सामग्री को नोजल के माध्यम से और मोल्ड में धकेलती है। सामग्री वांछित भाग का आकार लेते हुए, मोल्ड गुहा को भर देती है।
- शीतलन और जमना:सांचे को भरने के बाद, ऑपरेटर पिघले हुए प्लास्टिक को ठंडा और जमने देते हैं। आयामी स्थिरता और उचित भाग निर्माण प्राप्त करने के लिए शीतलन महत्वपूर्ण है। ऑपरेटर मोल्ड के भीतर चैनलों के माध्यम से शीतलक प्रसारित करके या शीतलन प्लेटों का उपयोग करके शीतलन प्रक्रिया को नियंत्रित कर सकते हैं।
- साँचे का खुलना और बाहर निकलना:ऑपरेटर मोल्ड को खोलते हैं और प्लास्टिक के जमने पर उसके हिस्से को मोल्ड कैविटी से बाहर निकाल देते हैं। मशीन के भीतर इजेक्शन सिस्टम मोल्ड से क्षेत्र को हटाने के लिए पिन, इजेक्टर प्लेट या एयर ब्लास्ट का उपयोग करता है। फिर मोल्ड अगले इंजेक्शन चक्र के लिए तैयार है।
- प्रोसेसिंग के बाद: इजेक्शन के बाद, भाग को पोस्ट-प्रोसेसिंग ऑपरेशन से गुजरना पड़ सकता है, जैसे ट्रिमिंग, डिबरिंग या सतह फिनिशिंग। ये चरण अतिरिक्त सामग्री को हटाने, खुरदरे किनारों को चिकना करने और भाग के अंतिम स्वरूप को बेहतर बनाने में मदद करते हैं।
- गुणवत्ता जांच: अंतिम चरण में गुणवत्ता के लिए इंजेक्ट किए गए भागों का निरीक्षण करना और यह सुनिश्चित करना शामिल है कि वे निर्दिष्ट आवश्यकताओं को पूरा करते हैं। भाग की गुणवत्ता और अखंडता को सत्यापित करने के लिए आयामी माप, दृश्य निरीक्षण और कार्यात्मक परीक्षण सहित विभिन्न गुणवत्ता नियंत्रण तकनीकों को नियोजित किया जा सकता है।
- पुनर्चक्रण और सामग्री का पुन: उपयोग:इंजेक्शन मोल्डिंग के दौरान उत्पन्न किसी भी अतिरिक्त या स्क्रैप सामग्री को पुनर्नवीनीकरण और पुन: उपयोग किया जा सकता है। नई थर्मोप्लास्टिक सामग्री का उपयोग कम करने से अपशिष्ट को कम करने और स्थिरता में सुधार करने में मदद मिलती है।
इंजेक्शन मोल्डिंग में प्रयुक्त उपकरण
ये उपकरण घटक थर्मोप्लास्टिक सामग्री को पिघलाने और इंजेक्ट करने से लेकर आकार देने, ठंडा करने और अंतिम भाग को बाहर निकालने तक इंजेक्शन मोल्डिंग प्रक्रिया को सुविधाजनक बनाते हैं। कुशल, उच्च गुणवत्ता वाले इंजेक्शन मोल्डिंग उत्पादन प्राप्त करने के लिए इन उपकरण घटकों का उचित संचालन और रखरखाव महत्वपूर्ण है।
- इंजेक्शन मोल्डिंग मशीन:इंजेक्शन मोल्डिंग में प्राथमिक उपकरण थर्मोप्लास्टिक सामग्री को पिघलाने, इसे मोल्ड में इंजेक्ट करने और प्रक्रिया को नियंत्रित करने के लिए जिम्मेदार है।
- मोल्ड: प्लास्टिक भाग के वांछित आकार और विशेषताओं को बनाने के लिए कस्टम-डिज़ाइन किए गए सांचे में दो हिस्से, गुहा और कोर शामिल हैं। ऑपरेटर इसे इंजेक्शन मोल्डिंग मशीन की क्लैंपिंग यूनिट पर लगाते हैं।
- हूपर:कंटेनर जो थर्मोप्लास्टिक सामग्री को गोली या दानेदार रूप में रखता है और इसे पिघलने और इंजेक्शन के लिए इंजेक्शन मोल्डिंग मशीन के बैरल में डालता है।
- बैरल और पेंच: बैरल, एक बेलनाकार कक्ष, थर्मोप्लास्टिक सामग्री को पिघलाता और समरूप बनाता है क्योंकि सामग्री को पिघलाने, मिश्रण करने और मानकीकृत करने के लिए स्क्रू इसके भीतर घूमता है।
- ताप और शीतलन प्रणाली:इंजेक्शन मोल्डिंग मशीनों में हीटिंग तत्व होते हैं, जैसे कि इलेक्ट्रिक हीटर या गर्म तेल का उपयोग करने वाले हीटर, बैरल का तापमान बढ़ाने के लिए, और शीतलन प्रणाली, जैसे पानी या तेल परिसंचरण, मोल्ड को ठंडा करने और प्लास्टिक के हिस्से को ठोस बनाने के लिए।
- इजेक्टर प्रणाली:जमने के बाद मोल्ड कैविटी से मोल्ड किए गए हिस्से को हटा देता है, आमतौर पर मोल्ड खोलने के दौरान इजेक्टर पिन, प्लेट या एयर ब्लास्ट का उपयोग करता है।
- नियंत्रण प्रणाली:इंजेक्शन मोल्डिंग प्रक्रिया के विभिन्न मापदंडों की निगरानी और नियंत्रण करता है, जिससे ऑपरेटरों को इंजेक्शन की गति, तापमान, दबाव और शीतलन समय जैसे मापदंडों को सेट और समायोजित करने की अनुमति मिलती है।
इंजेक्शन मोल्डिंग मशीनें: प्रकार और विशेषताएं
प्रत्येक प्रकार की इंजेक्शन मोल्डिंग मशीन की अपनी विशेषताएं और फायदे हैं, जिससे निर्माताओं को अपनी विशिष्ट उत्पादन आवश्यकताओं के लिए सबसे उपयुक्त उपकरण चुनने की अनुमति मिलती है।
- हाइड्रोलिक इंजेक्शन मोल्डिंग मशीनें: ये मशीनें पिघले हुए प्लास्टिक को मोल्ड में डालने के लिए आवश्यक दबाव उत्पन्न करने के लिए हाइड्रोलिक सिस्टम का उपयोग करती हैं। वे अपने उच्च क्लैम्पिंग बल, सटीक नियंत्रण और विभिन्न थर्मोप्लास्टिक्स को संभालने में बहुमुखी प्रतिभा के लिए जाने जाते हैं। हाइड्रोलिक मशीनें बड़े पैमाने पर उत्पादन के लिए उपयुक्त हैं और जटिल सांचों को समायोजित कर सकती हैं।
- इलेक्ट्रिक इंजेक्शन मोल्डिंग मशीनें:इलेक्ट्रिक मशीनें इंजेक्शन, क्लैम्पिंग और इजेक्टर सिस्टम सहित मशीन के संचालन के लिए इलेक्ट्रिक सर्वो मोटर्स का उपयोग करती हैं। वे हाइड्रोलिक मशीनों की तुलना में सटीक नियंत्रण, ऊर्जा दक्षता और तेज़ प्रतिक्रिया समय प्रदान करते हैं। इलेक्ट्रिक मशीनें सटीक मोल्डिंग अनुप्रयोगों के लिए आदर्श हैं जिनके लिए उच्च दोहराव और सटीकता की आवश्यकता होती है।
- हाइब्रिड इंजेक्शन मोल्डिंग मशीनें:हाइब्रिड मशीनें हाइड्रोलिक और इलेक्ट्रिक दोनों उपकरणों के लाभों को जोड़ती हैं। वे उच्च परिशुद्धता, ऊर्जा दक्षता और लागत-प्रभावशीलता प्राप्त करने के लिए हाइड्रोलिक और इलेक्ट्रिक सर्वो सिस्टम के संयोजन का उपयोग करते हैं। हाइब्रिड मशीनें विभिन्न प्रकार के अनुप्रयोगों के लिए उपयुक्त हैं, जो प्रदर्शन और परिचालन लागत के बीच संतुलन प्रदान करती हैं।
- दो-प्लेटन इंजेक्शन मोल्डिंग मशीनें: दो-प्लेटन मशीनों में मोल्ड को क्लैंप करने के लिए दो अलग-अलग प्लेटों के साथ एक अद्वितीय डिज़ाइन होता है। यह डिज़ाइन बेहतर स्थिरता, बेहतर मोल्ड सिंक्रनाइज़ेशन प्रदान करता है और बड़े मोल्ड आकार और उच्च क्लैंपिंग बलों की अनुमति देता है। दो-प्लेटन मशीनें बड़े और जटिल भागों के लिए उपयुक्त हैं जिन्हें सटीक मोल्डिंग की आवश्यकता होती है।
- बहु-घटक इंजेक्शन मोल्डिंग मशीनें:निर्माता इन मशीनों को एक ही मोल्डिंग चक्र में कई सामग्रियों या रंगों के साथ भागों का उत्पादन करने के लिए डिज़ाइन करते हैं। उनके पास विभिन्न इंजेक्शन इकाइयां और मोल्ड हैं, जो विभिन्न सामग्रियों के एक साथ इंजेक्शन को सक्षम करते हैं। बहु-घटक मशीनें अलग-अलग विशेषताओं वाले जटिल भागों के निर्माण में लचीलापन और दक्षता प्रदान करती हैं।
- माइक्रो-इंजेक्शन मोल्डिंग मशीनें:विशेष रूप से छोटे और सटीक भागों के उत्पादन के लिए डिज़ाइन की गई, माइक्रो-इंजेक्शन मोल्डिंग मशीनें अविश्वसनीय रूप से उच्च परिशुद्धता और सटीकता प्रदान करती हैं। वे कड़ी सहनशीलता और न्यूनतम सामग्री अपशिष्ट के साथ जटिल विवरण तैयार कर सकते हैं। इलेक्ट्रॉनिक्स, चिकित्सा उपकरण और माइक्रो-ऑप्टिक्स आमतौर पर माइक्रो-इंजेक्शन मोल्डिंग मशीनों का उपयोग करते हैं।
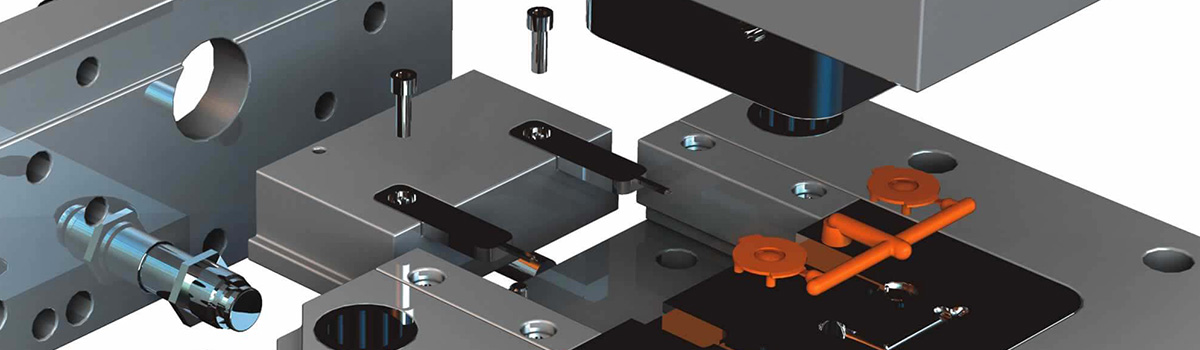
इंजेक्शन मोल्डिंग के लिए मोल्ड डिजाइन संबंधी विचार
सफल इंजेक्शन मोल्डिंग उत्पादन के लिए सावधानीपूर्वक मोल्ड डिजाइन विचार आवश्यक हैं।
- भाग डिजाइन:मोल्ड डिज़ाइन को उसके आकार, आयाम और कार्यात्मक विशेषताओं सहित भाग की विशिष्ट आवश्यकताओं को समायोजित करना चाहिए। निर्माताओं को इजेक्शन में आसानी और भाग की गुणवत्ता सुनिश्चित करने के लिए ड्राफ्ट कोण, दीवार की मोटाई, अंडरकट्स और किसी भी आवश्यक तत्व पर उचित रूप से विचार करना चाहिए।
- मोल्ड सामग्री: स्थायित्व, आयामी स्थिरता और गर्मी प्रतिरोध प्राप्त करने के लिए मोल्ड सामग्री का चयन महत्वपूर्ण है। सामान्य मोल्ड सामग्री में स्टील मिश्र धातु, एल्यूमीनियम मिश्र धातु और उपकरण स्टील शामिल हैं। सामग्री का चुनाव उत्पादन की मात्रा, भाग की जटिलता और अपेक्षित उपकरण जीवन जैसे कारकों पर निर्भर करता है।
- शीतलन प्रणाली:उचित रूप से ठोसकरण और चक्र समय को कम करने के लिए कुशल शीतलन आवश्यक है। मोल्ड डिज़ाइन में समान मोल्ड कूलिंग सुनिश्चित करने के लिए कूलिंग चैनल या रणनीतिक रूप से स्थित आवेषण शामिल होना चाहिए। उचित शीतलन से वारपेज, सिकुड़न और भाग दोष का खतरा कम हो जाता है।
- निकाल:इंजेक्शन प्रक्रिया के दौरान हवा और गैसों को बाहर निकलने की अनुमति देने के लिए पर्याप्त वेंटिंग आवश्यक है। अपर्याप्त वेंटिलेशन के कारण गैस फंस सकती है, जलने के निशान हो सकते हैं, या भाग अधूरा भरा हो सकता है। निर्माता मोल्ड डिज़ाइन में वेंटिंग ग्रूव्स, पिन या अन्य तंत्र को शामिल करके वेंटिंग प्राप्त कर सकते हैं।
- इजेक्शन सिस्टम:मोल्ड डिज़ाइन में मोल्ड कैविटी से मोल्ड किए गए हिस्से को सुरक्षित और कुशलता से हटाने के लिए एक प्रभावी इजेक्शन सिस्टम शामिल होना चाहिए। इजेक्शन सिस्टम में इजेक्टर पिन, स्लीव्स या अन्य तंत्र शामिल हो सकते हैं, जो फ़ंक्शन या महत्वपूर्ण सुविधाओं में हस्तक्षेप से बचने के लिए रणनीतिक रूप से स्थित होते हैं।
- गेट डिज़ाइन:गेट वह जगह है जहां पिघला हुआ प्लास्टिक मोल्ड गुहा में प्रवेश करता है। गेट डिज़ाइन को उचित भाग भरना सुनिश्चित करना चाहिए, प्रवाह रेखाओं को कम करना चाहिए और सामग्री को समय से पहले जमने से रोकना चाहिए। मानक गेट डिज़ाइन में भाग की आवश्यकताओं और सामग्री गुणों के आधार पर किनारे वाले गेट, सुरंग गेट और हॉट रनर सिस्टम शामिल हैं।
- विदाई के बोल:मोल्ड डिज़ाइन को एक उपयुक्त विभाजन रेखा को परिभाषित करना चाहिए, जो वह रेखा है जहां मोल्ड के दो हिस्से एक साथ आते हैं। उचित पार्टिंग लाइन प्लेसमेंट न्यूनतम फ्लैश और पार्टिंग लाइन बेमेल सुनिश्चित करता है और कुशल मोल्ड असेंबली की सुविधा प्रदान करता है।
- मोल्ड रखरखाव और सेवाक्षमता: निर्माताओं को रखरखाव, मरम्मत और मोल्ड सर्विसिंग में आसानी पर विचार करना चाहिए। सफाई, निरीक्षण और प्रतिस्थापन के लिए मोल्ड घटक आसानी से उपलब्ध होने चाहिए। त्वरित-परिवर्तन आवेषण या मॉड्यूलर मोल्ड डिज़ाइन जैसी सुविधाओं को शामिल करने से मोल्ड सेवाक्षमता में सुधार हो सकता है।
इंजेक्शन मोल्डिंग में प्रयुक्त मोल्ड सामग्री
मोल्ड सामग्री विशेषज्ञों के साथ सहयोग करने और मोल्डिंग एप्लिकेशन की विशिष्ट आवश्यकताओं पर विचार करने से इष्टतम मोल्ड प्रदर्शन और भाग की गुणवत्ता प्राप्त करने के लिए सबसे उपयुक्त सामग्री निर्धारित करने में मदद मिल सकती है।
- इस्पात मिश्र: स्टील मिश्र धातु, जैसे टूल स्टील (जैसे, पी20, एच13) और स्टेनलेस स्टील, आमतौर पर उनके उत्कृष्ट स्थायित्व, गर्मी प्रतिरोध और पहनने के प्रतिरोध के कारण इंजेक्शन मोल्डिंग मोल्ड के लिए उपयोग किए जाते हैं। ये सामग्रियां इंजेक्शन मोल्डिंग प्रक्रिया में उच्च तापमान और दबाव का सामना कर सकती हैं और उच्च गुणवत्ता वाले भागों के उत्पादन के लिए अच्छी आयामी स्थिरता प्रदान करती हैं।
- एल्यूमिनियम मिश्र धातु:7075 और 6061 जैसे एल्यूमीनियम मिश्र धातु हल्के होते हैं और अच्छी तापीय चालकता प्रदान करते हैं, जो उन्हें उन साँचे के लिए उपयुक्त बनाते हैं जिन्हें कुशल शीतलन की आवश्यकता होती है। निर्माता अक्सर प्रोटोटाइपिंग, कम मात्रा में उत्पादन, या ऐसे अनुप्रयोगों के लिए एल्यूमीनियम मोल्ड का उपयोग करते हैं जहां वजन में कमी महत्वपूर्ण है। हालाँकि, एल्यूमीनियम सांचों में स्टील मिश्र धातुओं की तुलना में कम स्थायित्व हो सकता है।
- तांबे की मिश्र धातु:कॉपर मिश्र धातु, जैसे बेरिलियम कॉपर, उच्च तापीय चालकता और अच्छी मशीनेबिलिटी प्रदर्शित करते हैं। इनका उपयोग उन सांचों में किया जाता है जिन्हें प्रभावी शीतलन के लिए उत्कृष्ट ताप हस्तांतरण की आवश्यकता होती है। तांबे की मिश्रधातु ढले हुए हिस्से से गर्मी को तेजी से खत्म करके चक्र के समय को कम करने में मदद कर सकती है, जिसके परिणामस्वरूप तेजी से जमना होता है।
- टूल स्टील्स:H13, S7 और D2 सहित टूल स्टील्स को उच्च-प्रदर्शन टूलींग अनुप्रयोगों के लिए डिज़ाइन किया गया है। ये स्टील्स उच्च शक्ति, कठोरता और पहनने के प्रतिरोध का संयोजन प्रदान करते हैं। टूल स्टील्स उच्च उत्पादन मात्रा, अपघर्षक सामग्री, या मांग वाली मोल्डिंग स्थितियों वाले सांचों के लिए उपयुक्त होते हैं।
- निकल मिश्र:निकेल मिश्र धातु, जैसे इनकोनेल और हास्टेलॉय, अपने असाधारण संक्षारण प्रतिरोध, उच्च तापमान शक्ति और थर्मल स्थिरता के लिए जाने जाते हैं। निर्माता इन मिश्र धातुओं का उपयोग उन सांचों में करते हैं जो संक्षारक सामग्रियों को संभालते हैं या अत्यधिक तापमान और आक्रामक मोल्डिंग वातावरण के प्रतिरोध की आवश्यकता होती है।
- कंपोजिट मटेरियल:मिश्रित सामग्री, जैसे प्रबलित प्लास्टिक या धातु आवेषण के साथ मिश्रित, कभी-कभी विशिष्ट मोल्डिंग अनुप्रयोगों के लिए उपयोग की जाती हैं। ये सामग्रियां उच्च शक्ति, थर्मल स्थिरता और कम वजन जैसे गुणों का संतुलन प्रदान करती हैं। विशिष्ट उत्पादन आवश्यकताओं के लिए मिश्रित सांचे लागत प्रभावी विकल्प हो सकते हैं।
इंजेक्शन मोल्ड्स के प्रकार
इंजेक्शन मोल्डिंग प्लास्टिक भागों के लिए एक बहुमुखी और व्यापक रूप से उपयोग की जाने वाली विनिर्माण प्रक्रिया है।
- दो-प्लेट मोल्ड:दो-प्लेट मोल्ड इंजेक्शन मोल्ड का सबसे आम प्रकार है। इसमें दो प्लेटें होती हैं, कैविटी प्लेट और कोर प्लेट, जो ढले हुए हिस्से को बाहर निकलने की अनुमति देने के लिए अलग हो जाती हैं। कैविटी प्लेट में मोल्ड का कैविटी वाला भाग होता है, जबकि कोर प्लेट में मूल भाग होता है। निर्माता अपने अपेक्षाकृत सरल डिज़ाइन के कारण भागों की एक विस्तृत श्रृंखला के उत्पादन के लिए दो-प्लेट मोल्ड का उपयोग करते हैं।
- थ्री-प्लेट मोल्ड:थ्री-प्लेट मोल्ड दो-प्लेट मोल्ड का उन्नत संस्करण है। इसमें एक अतिरिक्त प्लेट, रनर या स्प्रू प्लेट शामिल है। रनर प्लेट स्प्रू, रनर और गेट के लिए एक अलग चैनल बनाती है, जिससे मोल्ड किए गए हिस्से को आसानी से हटाया जा सकता है। निर्माता आमतौर पर जटिल गेटिंग सिस्टम के विवरण के लिए तीन-प्लेट मोल्ड का उपयोग करते हैं या जब टुकड़े पर गेट अवशेष से बचना वांछनीय होता है।
- हॉट रनर मोल्ड:रनर और गेट सिस्टम को गर्म रनर मोल्ड्स में गर्म किया जाता है, जिससे प्रत्येक चक्र के दौरान सामग्री के जमने और फिर से पिघलने की आवश्यकता समाप्त हो जाती है। हॉट रनर सिस्टम में गर्म मैनिफोल्ड और नोजल होते हैं जो प्लास्टिक की पिघली हुई अवस्था को बनाए रखते हैं। हॉट रनर मोल्ड कम चक्र समय, कम सामग्री अपशिष्ट, और गेट वेस्टेज को कम करके बेहतर गुणवत्ता वाले हिस्से जैसे लाभ प्रदान करते हैं।
- कोल्ड रनर मोल्ड: कोल्ड रनर मोल्ड्स में एक पारंपरिक रनर और गेट सिस्टम होता है जहां पिघला हुआ प्लास्टिक कोल्ड रनर के माध्यम से बहता है जो प्रत्येक चक्र के साथ जम जाता है। ऑपरेटर बाद में ठोस धावकों को हटा देते हैं, जिसके परिणामस्वरूप सामग्री बर्बाद हो जाती है। निर्माता आम तौर पर कम मात्रा में उत्पादन के लिए जटिल रनर मोल्ड्स का उपयोग करते हैं या जब उनके अधिक सरल डिजाइन के कारण सामग्री की लागत कम महत्वपूर्ण होती है।
- मोल्ड डालें:इंजेक्शन मोल्डिंग के दौरान इन्सर्ट मोल्ड्स में मोल्ड कैविटी में धातु या प्लास्टिक इन्सर्ट शामिल होते हैं। इन्सर्ट को पहले से ही सांचे में रखा जा सकता है या स्वचालित प्रक्रियाओं द्वारा डाला जा सकता है। यह साँचा अतिरिक्त घटकों को एकीकृत करने या ढाले हुए हिस्से में तत्वों को मजबूत करने, इसकी कार्यक्षमता या ताकत को बढ़ाने की अनुमति देता है।
- ओवरमोल्ड: ओवरमोल्डिंग में एक सामग्री को दूसरे के ऊपर ढालना शामिल है, आमतौर पर एक कठोर प्लास्टिक सब्सट्रेट को नरम इलास्टोमेर या थर्मोप्लास्टिक के साथ जोड़ना। यह प्रक्रिया एक ही साँचे में कई सामग्रियों या बनावट वाले भागों के निर्माण की अनुमति देती है, जिससे बेहतर पकड़, कुशनिंग या सौंदर्य सुविधाएँ मिलती हैं।
इंजेक्शन मोल्डिंग लागत को प्रभावित करने वाले कारक
इन कारकों पर विचार करने से निर्माताओं को इंजेक्शन मोल्डिंग की लागत का अनुमान लगाने और अनुकूलित करने में मदद मिल सकती है, जिससे उनकी विशिष्ट उत्पादन आवश्यकताओं के लिए गुणवत्ता, दक्षता और लागत-प्रभावशीलता के बीच संतुलन सुनिश्चित हो सके।
- भाग जटिलता:पार्ट डिज़ाइन की जटिलता इंजेक्शन मोल्डिंग की लागत निर्धारित करने में महत्वपूर्ण भूमिका निभाती है। जटिल ज्यामिति, अंडरकट्स, पतली दीवारें, या जटिल विशेषताओं के लिए अतिरिक्त टूलींग, विशेष मोल्ड या लंबे चक्र की आवश्यकता हो सकती है, जिससे समग्र विनिर्माण लागत बढ़ जाती है।
- सामग्री चयन:थर्मोप्लास्टिक सामग्री का चुनाव इंजेक्शन मोल्डिंग लागत को प्रभावित करता है। विभिन्न सामग्रियों की प्रति किलोग्राम कीमतें अलग-अलग होती हैं, और सामग्री की उपलब्धता, गुण और प्रसंस्करण आवश्यकताओं जैसे कारक समग्र सामग्री लागत को प्रभावित कर सकते हैं।
- टूलींग और मोल्ड डिजाइन: इंजेक्शन मोल्डिंग लागत में प्रारंभिक टूलींग और मोल्ड डिजाइन लागत महत्वपूर्ण हैं। मोल्ड की जटिलता, गुहाओं की संख्या, मोल्ड का आकार और मोल्ड सामग्री जैसे कारक टूलींग और मोल्ड निर्माण व्यय में योगदान करते हैं। अधिक जटिल साँचे या उन्नत सुविधाओं की आवश्यकता वाले साँचे अग्रिम निवेश को बढ़ा सकते हैं।
- उत्पादन मात्रा: उत्पादन की मात्रा सीधे इंजेक्शन मोल्डिंग में प्रति भाग लागत को प्रभावित करती है। उच्च पुस्तकों के परिणामस्वरूप अक्सर पैमाने की बचत होती है, जिससे प्रति भाग लागत कम हो जाती है। इसके विपरीत, कम मात्रा में उत्पादन चलाने पर सेटअप, टूलींग और सामग्री अपशिष्ट के कारण अधिक शुल्क लग सकता है।
- समय चक्र: चक्र समय, जिसमें शीतलन और इजेक्शन चरण शामिल हैं, उत्पादन क्षमता और समग्र लागत को प्रभावित करता है। लंबे चक्र समय के परिणामस्वरूप उत्पादन में कमी आती है और कीमतें संभावित रूप से अधिक हो जाती हैं। मोल्ड डिज़ाइन, शीतलन प्रणाली और प्रक्रिया मापदंडों को अनुकूलित करने से चक्र के समय को कम किया जा सकता है और दक्षता में सुधार हो सकता है।
- गुणवत्ता की आवश्यकताएं:कठोर गुणवत्ता आवश्यकताएँ या विशिष्ट प्रमाणपत्र इंजेक्शन मोल्डिंग लागत को प्रभावित कर सकते हैं। सटीक सहनशीलता, सतही फिनिश आवश्यकताओं या अतिरिक्त परीक्षण को पूरा करने के लिए अन्य संसाधनों, प्रक्रियाओं या निरीक्षणों की आवश्यकता हो सकती है, जिससे कुल लागत बढ़ जाएगी।
- द्वितीयक संचालन:यदि ढाले गए हिस्सों को असेंबली, पेंटिंग, या अतिरिक्त परिष्करण चरणों जैसे पोस्ट-प्रोसेसिंग ऑपरेशन की आवश्यकता होती है, तो ये ऑपरेशन समग्र इंजेक्शन मोल्डिंग लागत में जोड़ सकते हैं।
- आपूर्तिकर्ता और स्थान:इंजेक्शन मोल्डिंग आपूर्तिकर्ता की पसंद और उनका स्थान लागत को प्रभावित कर सकता है। आपूर्तिकर्ता के स्थान के आधार पर श्रम लागत, ओवरहेड्स, लॉजिस्टिक्स और परिवहन व्यय अलग-अलग होते हैं, जो समग्र विनिर्माण लागत को प्रभावित करते हैं।
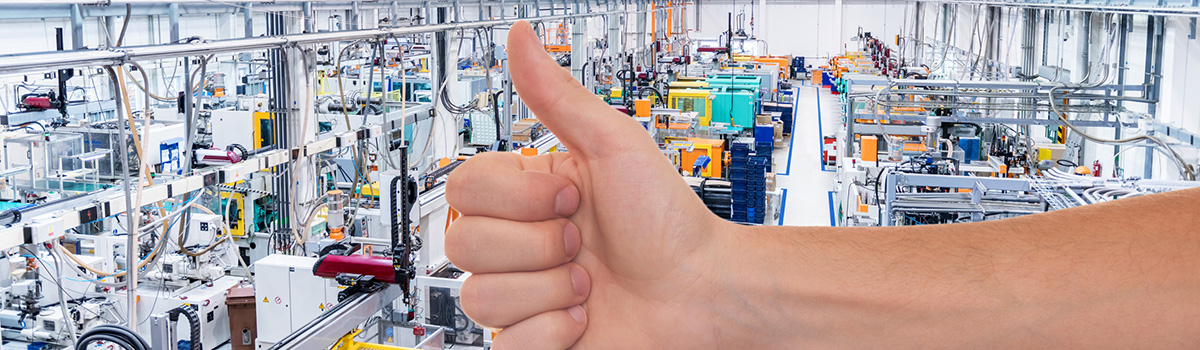
इंजेक्शन मोल्डिंग में गुणवत्ता नियंत्रण
इंजेक्शन मोल्डिंग प्रक्रिया के दौरान मजबूत गुणवत्ता नियंत्रण उपायों को लागू करने से संभावित दोषों, विचलनों या विसंगतियों की पहचान करने और उन्हें संबोधित करने में मदद मिलती है, जिससे ग्राहकों के विनिर्देशों और आवश्यकताओं को पूरा करने वाले उच्च गुणवत्ता वाले भागों का उत्पादन सुनिश्चित होता है।
- प्रक्रिया की निगरानी: पिघले तापमान, इंजेक्शन दबाव, शीतलन समय और चक्र समय जैसे प्रमुख प्रक्रिया मापदंडों की निरंतर निगरानी, आंशिक उत्पादन में स्थिरता और दोहराव सुनिश्चित करती है। वास्तविक समय की निगरानी और स्वचालित प्रणालियाँ निर्धारित मापदंडों से भिन्नता या विचलन का पता लगा सकती हैं, जिससे समय पर समायोजन और प्रक्रिया स्थिरता बनाए रखने की अनुमति मिलती है।
- निरीक्षण और माप:आयामी सटीकता, भाग की गुणवत्ता और विशिष्टताओं के पालन को सत्यापित करने के लिए ढाले गए भागों की नियमित समीक्षा और माप आवश्यक है। हमारी सेवाएँ गुणवत्ता नियंत्रण विधियों की एक श्रृंखला को कवर करती हैं, जैसे आयाम मापना, सतह की गुणवत्ता का विश्लेषण करना, दृश्य निरीक्षण करना और कार्यात्मक परीक्षण करना। सटीक मूल्यांकन के लिए विभिन्न निरीक्षण तकनीकों, जैसे समन्वय मापने वाली मशीनें (सीएमएम) और ऑप्टिकल और दृश्य निरीक्षण प्रणाली को नियोजित किया जाता है।
- सांख्यिकीय प्रक्रिया नियंत्रण (एसपीसी): एसपीसी में इंजेक्शन मोल्डिंग गुणवत्ता की निगरानी और नियंत्रण के लिए प्रक्रिया डेटा एकत्र करना और उसका विश्लेषण करना शामिल है। सांख्यिकीय तरीके, जैसे नियंत्रण चार्ट और प्रक्रिया क्षमता विश्लेषण, रुझानों की पहचान करने, प्रक्रिया विविधताओं का पता लगाने और यह सुनिश्चित करने में मदद करते हैं कि प्रक्रिया परिभाषित नियंत्रण सीमाओं के भीतर बनी रहे। एसपीसी मुद्दों की सक्रिय पहचान को सक्षम बनाता है और प्रक्रिया अनुकूलन की सुविधा प्रदान करता है।
- सामग्री परीक्षण: थर्मोप्लास्टिक्स, एडिटिव्स और कलरेंट जैसे कच्चे माल का परीक्षण, इंजेक्शन मोल्डिंग के लिए उनकी गुणवत्ता और उपयुक्तता सुनिश्चित करता है। सामग्री परीक्षण में पिघल प्रवाह सूचकांक (एमएफआई) विश्लेषण, यांत्रिक गुण, थर्मल विशेषताएं और सामग्री संरचना शामिल हो सकती है। सामग्री की गुणवत्ता को सत्यापित करने से ढाले गए हिस्सों में दोषों और विसंगतियों को रोकने में मदद मिलती है।
- टूलींग रखरखाव और निरीक्षण:इंजेक्शन मोल्डिंग में गुणवत्ता सुनिश्चित करने के लिए इंजेक्शन मोल्ड का उचित रखरखाव और नियमित निरीक्षण महत्वपूर्ण है। नियमित सफाई, चिकनाई और मोल्ड घटकों का मूल्यांकन पहनने, क्षति, या गिरावट को रोकने में मदद करता है जो भाग की गुणवत्ता को प्रभावित कर सकता है। लगातार मोल्डिंग प्रदर्शन को बनाए रखने के लिए घिसे-पिटे या क्षतिग्रस्त मोल्ड घटकों की समय पर मरम्मत या प्रतिस्थापन आवश्यक है।
- दस्तावेज़ीकरण और पता लगाने की क्षमता:इंजेक्शन मोल्डिंग में गुणवत्ता नियंत्रण के लिए व्यापक दस्तावेज़ीकरण और ट्रैसेबिलिटी रिकॉर्ड बनाए रखना आवश्यक है। प्रक्रिया मापदंडों, निरीक्षण परिणामों, सामग्री जानकारी और उत्पादन के दौरान किए गए किसी भी बदलाव या समायोजन को रिकॉर्ड करना महत्वपूर्ण है। उचित दस्तावेज़ीकरण भागों का पता लगाने में सक्षम बनाता है, मूल कारण विश्लेषण की सुविधा देता है और गुणवत्ता में स्थिरता सुनिश्चित करता है।
- प्रशिक्षण एवं कौशल विकास: ऑपरेटरों, तकनीशियनों और गुणवत्ता नियंत्रण कर्मियों के लिए पर्याप्त प्रशिक्षण और कौशल विकास कार्यक्रम प्रदान करने से इंजेक्शन मोल्डिंग प्रक्रियाओं, गुणवत्ता आवश्यकताओं और निरीक्षण तकनीकों के बारे में उनकी समझ बढ़ती है। अच्छी तरह से प्रशिक्षित कर्मचारी दोषों का पता लगा सकते हैं, समस्याओं का निवारण कर सकते हैं और उच्च गुणवत्ता वाले उत्पादन को सुनिश्चित करते हुए सुधारात्मक उपायों को प्रभावी ढंग से लागू कर सकते हैं।
सामान्य इंजेक्शन मोल्डिंग दोष और उनसे कैसे बचें
इंजेक्शन मोल्डिंग प्रक्रियाओं का नियमित निरीक्षण, निगरानी और विश्लेषण और उपकरणों और मोल्डों का उचित रखरखाव और समायोजन इन सामान्य दोषों को पहचानने और उनका समाधान करने में मदद कर सकता है।
- सिंक के निशान:सिंक के निशान ढले हुए हिस्से की सतह पर असमान शीतलन या सिकुड़न के कारण बने गड्ढे या इंडेंटेशन हैं। सिंक के निशान से बचने के लिए उचित गेट स्थान और डिज़ाइन, इष्टतम शीतलन प्रणाली डिज़ाइन और समान दीवार मोटाई वितरण पर विचार करना चाहिए। इंजेक्शन का दबाव बढ़ाने या शीतलन समय को समायोजित करने से भी सिंक के निशान को कम करने में मदद मिल सकती है।
- वारपेज:वारपेज का तात्पर्य असमान शीतलन या अवशिष्ट तनाव के कारण बाहर निकलने के बाद ढले हुए हिस्से की विकृति या झुकने से है। समान दीवार की मोटाई बनाए रखना, उचित शीतलन चैनलों का उपयोग करना, और मोल्ड की संतुलित भराई और पैकिंग सुनिश्चित करना युद्ध को रोकने के लिए महत्वपूर्ण है। मोल्ड तापमान को अनुकूलित करना, उचित ड्राफ्ट कोणों का उपयोग करना, और सामग्री तापमान और इंजेक्शन गति को नियंत्रित करने से वॉरपेज को कम करने में मदद मिल सकती है।
- फ्लैश:फ्लैश तब होता है जब अतिरिक्त सामग्री मोल्ड पार्टिंग लाइन में प्रवाहित होती है, जिसके परिणामस्वरूप अंतिम भाग पर पतले, अवांछित प्रक्षेपण या अतिरिक्त सामग्री होती है। पर्याप्त क्लैंपिंग बल लगाने, सटीक संरेखण और उचित वेंटिंग तकनीकों का उपयोग करने सहित उचित मोल्ड डिज़ाइन सुनिश्चित करके फ्लैश को प्रभावी ढंग से रोका जा सकता है। इंजेक्शन दबाव, तापमान और चक्र समय जैसे प्रक्रिया मापदंडों को अनुकूलित करने से फ्लैश कम हो जाता है।
- छोटा शॉट:एक त्वरित शॉट तब होता है जब इंजेक्ट की गई सामग्री मोल्ड गुहा को नहीं भरती है, जिसके परिणामस्वरूप अधूरा हिस्सा बन जाता है। छोटी तस्वीरों से बचने के लिए उचित सामग्री का चयन, पर्याप्त पिघल तापमान और चिपचिपाहट सुनिश्चित करना और उचित इंजेक्शन दबाव और समय बनाए रखना आवश्यक है। इसके अतिरिक्त, पर्याप्त रनर और गेट आकार और उचित वेंटिंग के लिए मोल्ड डिज़ाइन की पुष्टि करने से त्वरित शॉट्स को रोकने में मदद मिल सकती है।
- वेल्ड लाइनें:वेल्ड लाइनें तब होती हैं जब दो या दो से अधिक पिघली हुई सामग्री के प्रवाह अग्रभाग मिलते हैं और जम जाते हैं, जिसके परिणामस्वरूप भाग की सतह पर एक दृश्यमान रेखा या निशान बन जाता है। अच्छा गेट और रनर डिज़ाइन, इष्टतम पिघल तापमान, इंजेक्शन गति, और सामग्री प्रवाह और भाग ज्यामिति को समायोजित करने से वेल्ड लाइनों को कम किया जा सकता है। मोल्ड प्रवाह विश्लेषण और गेट प्लेसमेंट अनुकूलन भी वेल्ड लाइनों को रोकने या कम करने में मदद कर सकते हैं।
- जले का निशान:जलने के निशान अत्यधिक गर्मी या सामग्री के अधिक गर्म होने के कारण ढले हुए भाग की सतह पर मलिनकिरण या काले धब्बे होते हैं। अत्यधिक पिघले तापमान से बचना, उचित शीतलन चैनलों का उपयोग करना और चक्र समय को अनुकूलित करने से जलने के निशान को रोकने में मदद मिल सकती है। पर्याप्त वेंटिंग, उचित गेट डिज़ाइन और मोल्ड तापमान को नियंत्रित करना भी जलने के निशान को कम करने में योगदान देता है।
मोल्डिंग के बाद के ऑपरेशन: फिनिशिंग और असेंबली
इंजेक्शन मोल्डिंग के बाद, कई मोल्ड किए गए हिस्सों को वांछित अंतिम उत्पाद प्राप्त करने के लिए अतिरिक्त परिष्करण और असेंबली संचालन की आवश्यकता हो सकती है। इन पोस्ट-मोल्डिंग परिचालनों में शामिल हो सकते हैं:
- ट्रिमिंग:ट्रिमिंग या कटिंग टूल्स का उपयोग करके मोल्ड किए गए हिस्से के चारों ओर किसी भी अतिरिक्त सामग्री या फ्लैश को हटा दें।
- सतह के उपचार:पेंटिंग, कोटिंग या टेक्सचरिंग जैसी विभिन्न तकनीकों का उपयोग करके भाग की सतह की उपस्थिति या कार्यक्षमता को बढ़ाना।
- सभा:अंतिम उत्पाद को पूरा करने के लिए कई ढले हुए हिस्सों को जोड़ना या फास्टनरों, इंसर्ट या लेबल जैसे घटकों को जोड़ना।
- परीक्षण:विभिन्न परीक्षण विधियों जैसे आयामी विश्लेषण, सामग्री गुण परीक्षण, या प्रदर्शन परीक्षण के माध्यम से भाग की गुणवत्ता और कार्यक्षमता का सत्यापन।
- पैकेजिंग और शिपिंग:ग्राहकों या अंतिम-उपयोगकर्ताओं को शिपमेंट के लिए तैयार उत्पाद की उचित पैकेजिंग और लेबलिंग।
पोस्ट-मोल्डिंग परिचालनों का चयन विशिष्ट अनुप्रयोग और वांछित अंतिम उत्पाद विशेषताओं पर निर्भर करता है। वांछित पूर्ण उत्पाद गुणवत्ता और कार्यक्षमता प्राप्त करने के लिए इंजेक्शन मोल्डिंग विशेषज्ञों, फिनिशिंग और असेंबली विशेषज्ञों और ग्राहक के बीच घनिष्ठ सहयोग महत्वपूर्ण है। उचित योजना और निर्माण प्रक्रिया में पोस्ट-मोल्डिंग संचालन को एकीकृत करने से उच्च गुणवत्ता वाले उत्पादों के कुशल उत्पादन और समय पर डिलीवरी सुनिश्चित करने में मदद मिल सकती है।
इंजेक्शन मोल्डिंग बनाम अन्य प्लास्टिक विनिर्माण प्रक्रियाएं
प्रत्येक प्लास्टिक निर्माण प्रक्रिया के फायदे और सीमाएँ हैं, जो उन्हें विभिन्न अनुप्रयोगों के लिए उपयुक्त बनाती हैं।
- अंतः क्षेपण ढलाई: इंजेक्शन मोल्डिंग प्लास्टिक भागों के उत्पादन के लिए एक अत्यधिक बहुमुखी और व्यापक रूप से उपयोग की जाने वाली विनिर्माण प्रक्रिया है। यह उच्च उत्पादन दक्षता, सटीक भाग प्रतिकृति और जटिल ज्यामिति बनाने की क्षमता जैसे लाभ प्रदान करता है। इंजेक्शन मोल्डिंग उच्च मात्रा में उत्पादन चलाने के लिए उपयुक्त है और थर्मोप्लास्टिक सामग्रियों की एक विस्तृत श्रृंखला का उपयोग करने की अनुमति देता है। यह उत्कृष्ट आयामी सटीकता और सतह फिनिश प्रदान करता है, जो इसे ऑटोमोटिव, उपभोक्ता वस्तुओं और चिकित्सा उपकरणों जैसे विभिन्न उद्योगों के लिए आदर्श बनाता है।
- फूंक मार कर की जाने वाली मोल्डिंग: ब्लो मोल्डिंग एक ऐसी प्रक्रिया है जिसका उपयोग मुख्य रूप से खोखले प्लास्टिक भागों, जैसे बोतलें, कंटेनर और ऑटोमोटिव घटकों के उत्पादन के लिए किया जाता है। इसमें प्लास्टिक को पिघलाना और उसे मोल्ड कैविटी में फुलाकर वांछित आकार बनाना शामिल है। ब्लो मोल्डिंग उच्च मात्रा में उत्पादन के लिए उपयुक्त है और समान दीवार मोटाई के साथ बड़े, हल्के भागों का उत्पादन कर सकता है। हालाँकि, यह इंजेक्शन मोल्डिंग की तुलना में भाग जटिलता और सामग्री चयन के मामले में सीमित है।
- थर्मोफॉर्मिंग:थर्मोफॉर्मिंग एक प्रक्रिया है जिसका उपयोग थर्मोप्लास्टिक शीट को गर्म करके और मोल्ड या वैक्यूम फॉर्मिंग का उपयोग करके प्लास्टिक के हिस्सों का उत्पादन करने के लिए किया जाता है। इसका उपयोग पैकेजिंग, डिस्पोजेबल उत्पादों और ट्रे और कवर जैसे बड़े पैमाने के उत्पादों में आम तौर पर किया जाता है। थर्मोफॉर्मिंग बड़े हिस्सों के लिए लागत प्रभावी उत्पादन प्रदान करता है और त्वरित प्रोटोटाइप की अनुमति देता है। हालाँकि, इसमें इंजेक्शन मोल्डिंग की तुलना में भाग जटिलता, सामग्री चयन और आयामी सटीकता के संबंध में सीमाएं हैं।
- एक्सट्रूज़न:प्लास्टिक प्रोफाइल, शीट, ट्यूब और फिल्म बनाने के लिए एक्सट्रूज़न एक सतत प्रक्रिया है। इसमें प्लास्टिक रेज़िन को पिघलाना और वांछित आकार बनाने के लिए इसे डाई के माध्यम से डालना शामिल है। एक्सट्रूज़न एक सुसंगत क्रॉस-सेक्शन के साथ प्लास्टिक उत्पादों की लंबी, निरंतर लंबाई के उत्पादन के लिए उपयुक्त है। जबकि एक्सट्रूज़न उच्च उत्पादन दर और लागत-प्रभावशीलता प्रदान करता है, यह इंजेक्शन मोल्डिंग की तुलना में जटिल भाग ज्यामिति और सटीक आयामी नियंत्रण के संदर्भ में सीमित है।
- दबाव से सांचे में डालना:संपीड़न मोल्डिंग में थर्मोसेटिंग सामग्री की पूर्व-मापी मात्रा को गर्म मोल्ड गुहा में रखना और इसे ठीक होने तक उच्च दबाव में संपीड़ित करना शामिल है। इसका उपयोग उच्च शक्ति और आयामी स्थिरता वाले भागों, जैसे ऑटोमोटिव घटकों और विद्युत इन्सुलेशन के उत्पादन में आम तौर पर किया जाता है। संपीड़न मोल्डिंग अच्छी भाग स्थिरता, उच्च उत्पादन दक्षता और सामग्रियों की एक विस्तृत श्रृंखला का उपयोग करने की क्षमता प्रदान करती है। हालाँकि, यह इंजेक्शन मोल्डिंग की तुलना में भाग जटिलता और चक्र समय के संदर्भ में सीमित है।
थर्माप्लास्टिक इंजेक्शन मोल्डिंग के अनुप्रयोग
विभिन्न उद्योग इसकी बहुमुखी प्रतिभा, दक्षता और लागत-प्रभावशीलता के कारण व्यापक रूप से थर्मोप्लास्टिक इंजेक्शन मोल्डिंग का उपयोग करते हैं। थर्मोप्लास्टिक इंजेक्शन मोल्डिंग के कुछ अनुप्रयोगों में शामिल हैं:
- मोटर वाहन उद्योग: ऑटोमोटिव उद्योग व्यापक रूप से आंतरिक और बाहरी ट्रिम, डैशबोर्ड, दरवाजा पैनल, बंपर और इलेक्ट्रिकल कनेक्टर सहित विभिन्न घटकों के निर्माण के लिए थर्मोप्लास्टिक इंजेक्शन मोल्डिंग का उपयोग करता है। यह प्रक्रिया सटीक भाग प्रतिकृति, जटिल ज्यामिति और हल्की सामग्री की अनुमति देती है, जिससे ईंधन दक्षता और डिजाइन लचीलेपन में सुधार होता है।
- उपभोक्ता वस्तुओं:इंजेक्शन मोल्डिंग का उपयोग घरेलू उपकरणों, इलेक्ट्रॉनिक उपकरणों, पैकेजिंग कंटेनरों और खिलौनों जैसे उपभोक्ता वस्तुओं के उत्पादन में व्यापक रूप से किया जाता है। यह प्रक्रिया सुसंगत आयामों और सतह फिनिश के साथ टिकाऊ, उच्च गुणवत्ता वाले उत्पादों के बड़े पैमाने पर उत्पादन को सक्षम बनाती है। यह अनुकूलन विकल्पों और त्वरित उत्पाद पुनरावृत्तियों की भी अनुमति देता है।
- चिकित्सा उपकरण:सिरिंज, सर्जिकल उपकरण, इम्प्लांटेबल घटकों और दवा वितरण प्रणालियों सहित उपकरणों की एक विस्तृत श्रृंखला के उत्पादन के लिए इंजेक्शन मोल्डिंग चिकित्सा उद्योग में एक महत्वपूर्ण भूमिका निभाती है। यह प्रक्रिया बाँझ, सटीक और जैव-संगत भागों का उत्पादन सुनिश्चित करती है जो स्वास्थ्य सेवा क्षेत्र की कठोर नियामक आवश्यकताओं को पूरा करते हैं।
- इलेक्ट्रॉनिक्स और इलेक्ट्रिकल उद्योग:इलेक्ट्रॉनिक्स उद्योग विद्युत कनेक्टर, बाड़े, स्विच और अन्य घटकों के निर्माण के लिए इंजेक्शन मोल्डिंग का उपयोग करता है। यह प्रक्रिया उच्च आयामी सटीकता, उत्कृष्ट सतह फिनिश और इन्सर्ट मोल्डिंग और ओवरमोल्डिंग जैसी सुविधाओं को शामिल करने की क्षमता प्रदान करती है, जिससे जटिल इलेक्ट्रॉनिक असेंबली के कुशल उत्पादन की अनुमति मिलती है।
- पैकेजिंग उद्योग:खाद्य और पेय पदार्थ, फार्मास्यूटिकल्स और व्यक्तिगत देखभाल सहित विभिन्न उद्योग, आमतौर पर प्लास्टिक पैकेजिंग कंटेनर, कैप, क्लोजर और बोतलों के उत्पादन के लिए इंजेक्शन मोल्डिंग का उपयोग करते हैं। यह प्रक्रिया कुशल विनिर्माण चक्रों के साथ हल्के, टिकाऊ और सौंदर्य की दृष्टि से आकर्षक पैकेजिंग समाधान बनाने में सक्षम बनाती है।
- एयरोस्पेस उद्योग:एयरोस्पेस क्षेत्र वायु नलिकाओं, ब्रैकेट, आंतरिक पैनल और संरचनात्मक भागों जैसे हल्के और उच्च प्रदर्शन वाले घटकों के निर्माण के लिए इंजेक्शन मोल्डिंग का उपयोग करता है। यह प्रक्रिया उन्नत सामग्रियों और जटिल भाग ज्यामिति का उपयोग करने की अनुमति देती है, जिससे वजन कम करने और ईंधन दक्षता में सुधार होता है।
थर्मोप्लास्टिक इंजेक्शन मोल्डिंग का पर्यावरणीय प्रभाव
थर्मोप्लास्टिक इंजेक्शन मोल्डिंग अपने कई लाभों के कारण एक लोकप्रिय विनिर्माण प्रक्रिया है, लेकिन इसके पर्यावरणीय प्रभाव पर विचार करना भी आवश्यक है। यहां विचार करने योग्य कुछ बिंदु दिए गए हैं:
- सामग्री दक्षता:थर्मोप्लास्टिक इंजेक्शन मोल्डिंग अपशिष्ट को कम करके सामग्री दक्षता को बढ़ावा देता है। यह प्रक्रिया सांचे में डाली गई सामग्री की मात्रा पर सटीक नियंत्रण का उपयोग करती है, जिससे अतिरिक्त सामग्री की आवश्यकता कम हो जाती है। निर्माता स्क्रैप या अस्वीकृत भागों का पुन: उपयोग करने के लिए रीग्राइंडिंग और रीसाइक्लिंग तकनीकों को भी नियोजित कर सकते हैं, जिससे सामग्री की बर्बादी कम हो सकती है।
- ऊर्जा की खपत:निर्माता इंजेक्शन मोल्डिंग मशीनों को ऊर्जा-कुशल बनाने के लिए डिज़ाइन करते हैं, जिसमें आधुनिक मॉडल में सर्वो मोटर्स और वैरिएबल स्पीड ड्राइव जैसी उन्नत तकनीकों को शामिल किया जाता है। ये विशेषताएं मोल्डिंग के दौरान बिजली की खपत को कम करके ऊर्जा के उपयोग को अनुकूलित करती हैं, जिसके परिणामस्वरूप ऊर्जा की आवश्यकताएं कम होती हैं और पर्यावरणीय प्रभाव कम होता है।
- कचरे का प्रबंधन:सामग्री की बर्बादी को कम करते हुए, निर्माताओं को बची हुई सामग्री, स्प्रूज़ या रनर को संभालने के लिए उचित अपशिष्ट प्रबंधन प्रथाओं को लागू करना चाहिए। निर्माता इंजेक्शन मोल्डिंग के दौरान उत्पन्न प्लास्टिक कचरे को इकट्ठा करने और पुन: उपयोग करने के लिए रीसाइक्लिंग कार्यक्रम स्थापित कर सकते हैं, जिससे लैंडफिल में भेजे जाने वाले कचरे को कम किया जा सकता है।
- उत्सर्जन में कमी: थर्मोप्लास्टिक इंजेक्शन मोल्डिंग आम तौर पर अन्य विनिर्माण प्रक्रियाओं की तुलना में कम उत्सर्जन उत्पन्न करती है। निर्माता पर्यावरण-अनुकूल सामग्रियों का उपयोग करके, ऊर्जा-कुशल उपकरण लागू करके और जारी किए गए किसी भी उत्सर्जन को पकड़ने के लिए उन्नत निकास और निस्पंदन सिस्टम को नियोजित करके उत्सर्जन को कम कर सकते हैं।
- टिकाऊ सामग्री विकल्प:थर्मोप्लास्टिक सामग्रियों का चयन इंजेक्शन मोल्डिंग की पर्यावरणीय स्थिरता पर महत्वपूर्ण प्रभाव डाल सकता है। बायोडिग्रेडेबल या जैव-आधारित प्लास्टिक, साथ ही पुनर्नवीनीकरण या पुनर्चक्रण योग्य सामग्रियों का विकल्प चुनने से प्रक्रिया के समग्र पारिस्थितिक पदचिह्न को कम करने में मदद मिल सकती है।
जीवन चक्र संबंधी विचार: पर्यावरणीय प्रभाव का आकलन करने के लिए ढले हुए उत्पाद के संपूर्ण जीवन चक्र पर विचार करना आवश्यक है। डिज़ाइन और सामग्री चयन चरणों के दौरान, निर्माताओं को भाग के स्थायित्व, इसकी पुनर्चक्रण क्षमता और जीवन के अंत तक निपटान या पुन: उपयोग की संभावना जैसे कारकों पर विचार करना चाहिए।
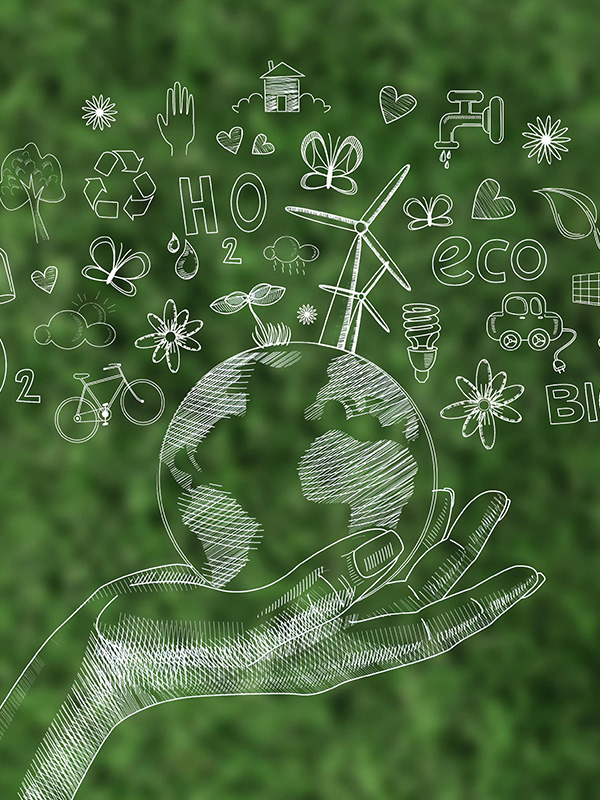
थर्मोप्लास्टिक इंजेक्शन मोल्डिंग का भविष्य
प्रौद्योगिकी में निरंतर प्रगति और विभिन्न उद्योगों में उच्च गुणवत्ता, सटीक भागों की बढ़ती मांग के साथ, थर्मोप्लास्टिक इंजेक्शन मोल्डिंग का भविष्य आशाजनक लग रहा है। आने वाले वर्षों में अपेक्षित कुछ प्रमुख विकासों में शामिल हैं:
- दक्षता में सुधार और लागत कम करने के लिए स्वचालन और रोबोटिक्स का उपयोग बढ़ाना।
- आंशिक प्रदर्शन को बेहतर बनाने और नए अनुप्रयोगों को सक्षम करने के लिए नई सामग्रियों और प्रक्रियाओं को विकसित करने पर प्रयास केंद्रित हैं।
- यह इंजेक्शन मोल्डिंग के पर्यावरणीय प्रभाव को कम करने के लिए टिकाऊ प्रथाओं को अपनाना है, जैसे पुनर्नवीनीकरण सामग्री का उपयोग करना और ऊर्जा खपत को अनुकूलित करना।
- डिजाइन और उत्पादन प्रक्रियाओं को बेहतर बनाने के लिए 3डी प्रिंटिंग और सिमुलेशन सॉफ्टवेयर जैसी डिजिटल प्रौद्योगिकियों का व्यापक एकीकरण।
वैश्विक इंजेक्शन मोल्डिंग बाजार का विस्तार हो रहा है, विशेष रूप से उभरती अर्थव्यवस्थाओं में, जो विभिन्न उद्योगों में प्लास्टिक उत्पादों की बढ़ती मांग से प्रेरित है।
सही इंजेक्शन मोल्डिंग पार्टनर चुनना
आपके प्रोजेक्ट की सफलता के लिए सही इंजेक्शन मोल्डिंग पार्टनर चुनना महत्वपूर्ण है। एक संगत और दीर्घकालिक साझेदारी सुनिश्चित करने के लिए कई विकल्पों का मूल्यांकन करने, साइट का दौरा करने और गहन चर्चा में शामिल होने के लिए समय निकालें।
- विशेषज्ञता और अनुभव:उद्योग में व्यापक ज्ञान और अनुभव वाले इंजेक्शन मोल्डिंग भागीदार की तलाश करें। उनके पास विभिन्न क्षेत्रों में ग्राहकों को उच्च गुणवत्ता वाले उत्पाद और समाधान प्रदान करने का एक सिद्ध ट्रैक रिकॉर्ड होना चाहिए। विभिन्न सामग्रियों, मोल्ड डिज़ाइन और विनिर्माण प्रक्रियाओं के बारे में उनकी समझ पर विचार करें।
- विनिर्माण क्षमता: इंजेक्शन मोल्डिंग पार्टनर की विनिर्माण क्षमताओं का आकलन करें। सुनिश्चित करें कि आपके प्रोजेक्ट की आवश्यकताओं को पूरा करने के लिए उनके पास आधुनिक मशीनरी और प्रौद्योगिकियों से सुसज्जित सुविधा हो। उनकी उत्पादन क्षमता, विभिन्न भाग आकारों और जटिलताओं को संभालने की क्षमता, और आपके वांछित उत्पादन मात्रा और समयसीमा को पूरा करने की क्षमता पर विचार करें।
- गुणवत्ता आश्वासन:इंजेक्शन मोल्डिंग में गुणवत्ता सर्वोपरि है। संभावित भागीदार की गुणवत्ता नियंत्रण प्रणालियों और प्रमाणपत्रों का मूल्यांकन करें। ऐसे साझेदारों की तलाश करें जो सख्त गुणवत्ता मानकों का पालन करते हों, जिनके पास मजबूत निरीक्षण प्रक्रियाएं हों और भाग की गुणवत्ता और स्थिरता सुनिश्चित करने के लिए व्यापक परीक्षण करते हों।
- डिज़ाइन और इंजीनियरिंग सहायता:एक विश्वसनीय इंजेक्शन मोल्डिंग पार्टनर को विनिर्माण क्षमता के लिए आपके हिस्से के डिजाइन को अनुकूलित करने के लिए डिजाइन और इंजीनियरिंग सहायता की पेशकश करनी चाहिए। उनके पास कुशल इंजीनियर होने चाहिए जो भाग की गुणवत्ता और दक्षता बढ़ाने के लिए सामग्री चयन, मोल्ड डिजाइन और प्रक्रिया अनुकूलन पर मूल्यवान इनपुट प्रदान कर सकें।
- लागत प्रतिस्पर्धात्मकता:जबकि लागत एकमात्र निर्धारण कारक नहीं होनी चाहिए, इंजेक्शन मोल्डिंग पार्टनर की कीमत और लागत प्रतिस्पर्धात्मकता का मूल्यांकन करना आवश्यक है। विस्तृत उद्धरण का अनुरोध करें और टूलींग लागत, सामग्री लागत, श्रम लागत और उनके द्वारा प्रदान की जाने वाली किसी भी अतिरिक्त सेवाओं पर विचार करें।
- संचार और सहयोग:एक सफल साझेदारी के लिए प्रभावी संचार और सहयोग आवश्यक है। सुनिश्चित करें कि इंजेक्शन मोल्डिंग पार्टनर के पास अच्छे संचार चैनल हैं, वह आपकी पूछताछ के प्रति उत्तरदायी है, और नियमित प्रोजेक्ट अपडेट प्रदान कर सकता है। एक सहयोगात्मक दृष्टिकोण यह सुनिश्चित करने में मदद करेगा कि हम आपकी आवश्यकताओं को पूरा करें और किसी भी चुनौती का तुरंत समाधान करें।
- ग्राहक संदर्भ और समीक्षाएँ:इंजेक्शन मोल्डिंग पार्टनर के साथ अन्य ग्राहकों के अनुभवों के बारे में जानकारी प्राप्त करने के लिए ग्राहक संदर्भ खोजें या समीक्षा/प्रशंसापत्र पढ़ें। इस जानकारी को प्राप्त करने से उनकी निर्भरता, तत्परता और ग्राहक संतुष्टि के समग्र स्तर को निर्धारित करने में मदद मिल सकती है।
निष्कर्ष
बड़ी मात्रा में प्लास्टिक भागों के निर्माण के लिए थर्मोप्लास्टिक इंजेक्शन मोल्डिंग एक बहुमुखी और लागत प्रभावी तरीका है। उच्च परिशुद्धता और स्थिरता के साथ जटिल आकार बनाने की इसकी क्षमता ऑटोमोटिव, चिकित्सा, इलेक्ट्रॉनिक्स और उपभोक्ता वस्तुओं सहित विभिन्न उद्योगों के लिए एक लोकप्रिय विकल्प बन गई है। थर्मोप्लास्टिक इंजेक्शन मोल्डिंग के विभिन्न पहलुओं को समझकर, इसके फायदे, नुकसान और डिज़ाइन संबंधी विचारों सहित, आप अपनी व्यावसायिक आवश्यकताओं के लिए सही इंजेक्शन मोल्डिंग पार्टनर चुनने के बारे में सूचित निर्णय ले सकते हैं।