Caso en Corea
Deseño estrutural de espesor de parede de pezas de inxección de plástico para empresas de automóbiles coreanas
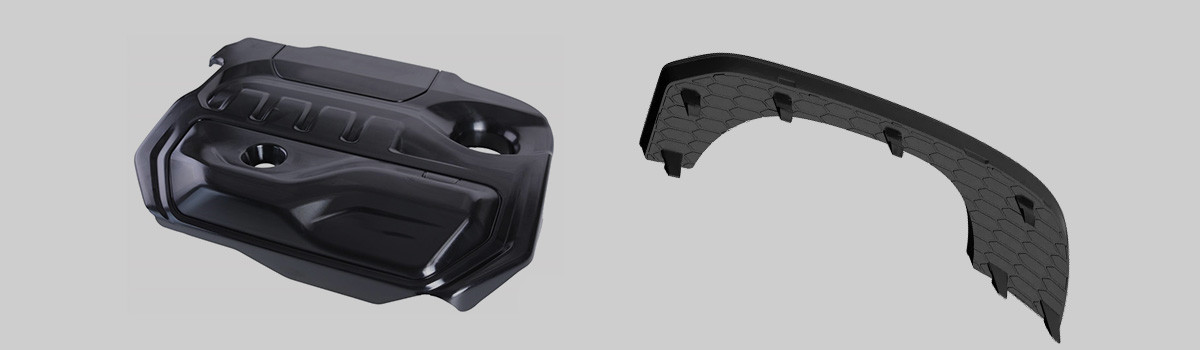
As pezas de plástico son moi importadas para un coche, e a súa estrutura forte afectará a vida útil e a condución segura, polo que os fabricantes de automóbiles coreanos compran pezas de plástico moi estritas. A industria automotriz usará moitas pezas de plástico nun coche, as compañías de inxección locais de Corea non poden ofrecer a gran oferta e estes fabricantes de automóbiles comprarán pezas de plástico no exterior, como DJmolding de China.
As pezas de plástico son tan importantes para un coche, entón como deseñar a estrutura da parede das pezas de inxección de plástico para as compañías de automóbiles coreanas? Agora, DJmolding amosarache o deseño das pezas de inxección de plástico do grosor estrutural.
Definición de espesor de parede
O espesor da parede é unha característica estrutural básica das pezas plásticas. Se a superficie exterior das pezas plásticas chámase parede exterior, a superficie interior chámase parede interior, entón hai un valor de espesor entre as paredes exterior e interior. O valor chámase espesor da parede. O valor introducido cando se extrae a capa no software durante o deseño estrutural tamén se pode dicir que é o grosor da parede.
Función do espesor da parede
Para a parede exterior dos produtos
A parede exterior das pezas é como a pel exterior das pezas. A parede interior son os esqueletos estruturais das pezas. Pódense conseguir diferentes efectos de aparencia mediante o tratamento superficial da parede exterior das pezas. A parede interior só conecta as estruturas (nervaduras, barras de parafuso, fibela, etc.) entre si e permite unha certa resistencia ás pezas. Mentres tanto, outras estruturas poden ser cubertas durante o proceso de moldeamento da infección. Non hai requisitos específicos para as paredes interiores e exteriores (refrixeración, montaxe). Normalmente, faise un todo para que as partes poidan ter a suficiente resistencia para protexer as partes internas de danos ou interferencias polo medio ambiente.
Para as partes internas do produto
Como soporte ou soporte de conexión, non hai requisitos estritos para as paredes interiores e exteriores, que poden establecer outras estruturas (nervaduras, barras de parafuso, fibelas, etc.) na parede exterior segundo as condicións reais. Non obstante, en aras dunha fabricación cómoda (refírese principalmente a cando os moldes dianteiro e traseiro están separados, para manter as pezas de plástico no molde traseiro, a cara frontal do molde, que a parede exterior debe deseñarse o máis sinxelo posible. Se non, axustando o ángulo de debuxo dos moldes dianteiro e traseiro, incluso ter un dedal no molde frontal ou un pequeno recorte no molde traseiro), e xeralmente deseñar outras estruturas na parede interior.
Non importa que sexan pezas de casca ou partes internas, o grosor da parede é esencial como a superficie receptora do pasador expulsor do molde, o que permite que as pezas sexan expulsadas sen problemas.
Principios de deseño do espesor da parede:
No deseño das pezas plásticas, o grosor da parede é a prioridade, fundamental como cimentación dun edificio. Hai que construír sobre el as outras estruturas. Mentres tanto, tamén afecta as propiedades mecánicas, a formabilidade, o aspecto e o custo das pezas plásticas. Así, o grosor da parede debe basearse nos factores anteriores para deseñar.
Mencionou que o grosor da parede debe ser un valor específico. Se hai un valor, refírese ao grosor da parede uniforme. Se hai moitos valores, refírese ao grosor desigual da parede. A diferenza entre par ou desigual introducirase despois. Agora, falaremos sobre o O principio do deseño do grosor da parede debe ser seguido.
1. Baseado no principio de propiedades mecánicas:
Mencionou que non importa que se trate de pezas de casca ou partes internas, ambas precisan un certo nivel de forza. Ademais doutros factores, a forza de liberación da resistencia é necesaria cando se considera a formación de pezas. Pódese deformar facilmente se a peza é demasiado delgada. En xeral, canto máis groso sexa o grosor da parede, maior será a resistencia das pezas (o grosor da parede aumenta un 10%, a resistencia aumentará nun 33%). Se o grosor da parede supera un determinado intervalo, sumando o grosor da parede, diminuirá a resistencia das pezas debido á contracción e á porosidade. O aumento do grosor da parede reducirá a resistencia das pezas e aumentará o peso, estende o círculo de moldaxe por inxección, o custo, etc. Obviamente, aumentar a resistencia das pezas simplemente aumentando o grosor da parede non é o programa ideal. É mellor utilizar as características xeométricas para aumentar a rixidez, como nervios, curvas, superficies onduladas, rixidez, etc.
Non se descarta que debido ás limitacións de espazo e outros factores, a resistencia dalgunhas pezas se realice principalmente polo espesor da parede. Polo tanto, recoméndase determinar un grosor de parede adecuado imitando a simulación mecánica se a resistencia é un factor importante. De feito, o valor do espesor da parede tamén debe cumprirse cos seguintes principios de formalidade.
2. Baseándose no principio de formabilidade:
O grosor real da parede é o grosor da cavidade do molde entre os moldes dianteiro e traseiro. Cando a resina fundida enche a cavidade do molde e arrefría, obtense o grosor da parede.
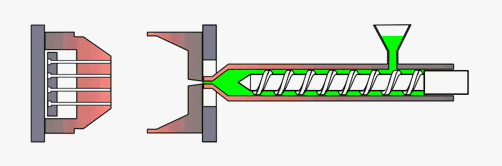
1) Como flúe a resina fundida durante o proceso de inxección e recheo?
O fluxo de plástico dentro da cavidade pódese considerar como fluxo laminar. Segundo a teoría da mecánica de fluídos, o fluído laminar pode considerarse como as capas de líquido que se atopan xunto a outras que escorren baixo a acción da forza de cizallamento.
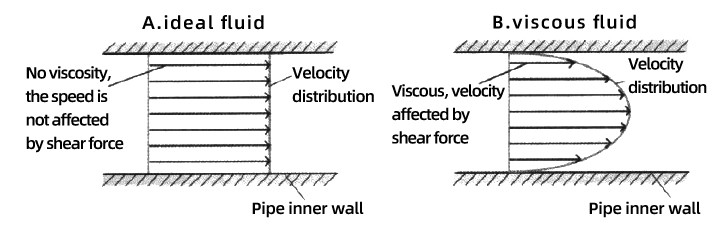
Durante o proceso de moldaxe por inxección, a resina fundida entra en contacto coa parede dos corredores (parede da cavidade do molde), facendo que as capas do fluxo se adhiran á parede dos corredores (ou parede da cavidade do molde) arrefriadas en primeiro lugar. A velocidade é cero, e hai unha resistencia á fricción producida coa súa capa líquida adxacente. Pasa así, a velocidade da capa intermedia é a máis alta. Forma de fluxo na que a velocidade laminar diminúe preto da parede do corredor (ou da parede da cavidade do molde) a ambos os dous lados.
A capa media é a capa fluída e a capa de pel é a capa solidificada. A medida que pasa o tempo de arrefriamento, a capa de maldición aumentará. A área de sección transversal da capa fluída será menor gradualmente. Canto máis duro sexa o recheo, maior será a forza de inxección. De feito, é máis difícil empurrar a masa fundida na cavidade do molde para realizar a inxección.
Polo tanto, o tamaño do espesor da parede ten unha gran influencia no fluxo e recheo das pezas moldeadas por inxección durante o proceso de moldaxe por inxección e o seu valor non pode ser demasiado pequeno.
2) A viscosidade do plástico fundido tamén ten unha gran influencia na fluidez
Cando a fusión está baixo a acción externa, e hai movemento relativo entre as capas, xerarase unha forza de fricción interna para interferir no movemento relativo entre as capas fluídas. A forza de rozamento interna producida polo fluído chámase viscosidade. Avaliación da resistencia á viscosidade coa viscosidade dinámica (ou coeficiente de viscosidade). Numericamente a relación entre o esforzo cortante e a velocidade de corte da masa fundida.
A viscosidade dos fundidos reflicte as características da facilidade coa que flúe o fundido plástico. É unha medida da resistencia ao fluxo de fusión. Canto maior sexa a viscosidade, maior sexa a resistencia do fluído, máis difícil será o fluxo. Os factores influentes da viscosidade de fusión afecta non só está asociado coa estrutura molecular, pero tamén está relacionado coa temperatura, presión, velocidade de cizallamento, aditivos, etc (despois de decidir os tipos de materiais plásticos, a temperatura, presión, taxa de cizallamento, aditivos). e outros factores durante o proceso de moldaxe por inxección poden ser alterados para cambiar a fluidez do plástico no proceso de moldaxe por inxección. No futuro, escribiremos un artigo sobre o tema da liquidez dependendo da situación.)
Mentres, na aplicación real, o índice de fusión indica a fluidez dos materiais plásticos no procesamento. Canto maior sexa o valor, mellor será a fluidez do material. Pola contra, a fluidez do material será peor.
Polo tanto, o plástico con boa fluidez é máis fácil de encher a cavidade do molde, especialmente para pezas de moldaxe por inxección con estruturas complexas.
A fluidez dos plásticos de uso común pódese dividir aproximadamente en tres categorías segundo os requisitos de deseño do molde:
①Boa fluidez: PA, PE, PS, PP, CA, poli(4) metilpentileno;
② Fluididade media: resinas da serie de poliestireno (como ABS, AS), PMMA, POM, PPO;
③Fuidez pobre: PC, PVC duro, PPO, PSF, PASF, fluoroplásticos.
Como podemos ver na figura anterior, o material con menor fluidez, os requisitos para o espesor mínimo da parede serán maiores. Isto foi introducido na teoría do fluxo laminar.
O valor recomendado do espesor da parede anterior é só un número conservador. Na aplicación real, os tamaños das pezas inclúen pequenos, medianos e grandes, a imaxe anterior non especifica o rango de referencia.
3) Podemos calcular pola relación de lonxitude do fluxo
A relación de lonxitude do fluxo de plástico refírese á relación entre a lonxitude (L) e o espesor da parede (T) do fluxo de fusión de plástico. Isto significa que para un espesor de parede dado, canto maior sexa a relación de lonxitude do fluxo, máis lonxe correrá o plástico fundido. Ou cando a lonxitude do fluxo de fusión de plástico é certa, canto maior sexa a relación de lonxitude do fluxo, menor será o grosor da parede. Así, a relación de lonxitude do fluxo de plástico afecta directamente o número de alimentación e distribución de produtos plásticos. Ademais, afecta o grosor da parede do plástico.
Para ser máis precisos, o intervalo de valores específicos do espesor da parede pódese obter mediante o cálculo da relación de lonxitude do fluxo. De feito, este valor está relacionado coa temperatura do material, a temperatura do molde, o grao de pulido, etc. é só un valor aproximado do intervalo, as diferentes condicións son diferentes, é difícil ser preciso, pero pódese usar como valor de referencia.
Cálculo da relación de lonxitude de caudal:
L/T (total) = L1/T1 (canle principal) + L2/T2 (canle dividido) + L3/T3 (produto) A relación de lonxitude de fluxo calculada debe ser inferior ao valor indicado na táboa de propiedades físicas, se non, pode haber ser O fenómeno do mal recheo.
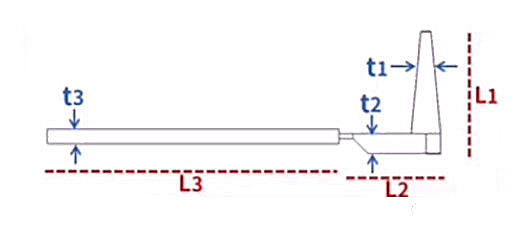
Por exemplo
Unha carcasa de goma, material de PC, o grosor da parede é de 2, a distancia de recheo é de 200, o corredor é de 100, o diámetro dos corredores é de 5.
Calculation: L/T(total)=100/5+200/2=120
O valor de referencia para a relación de lonxitude de fluxo de PC é 90, o que é obviamente maior que o valor de referencia. Hai que aumentar a velocidade e a presión de inxección xa que é difícil de inxectar, ou mesmo requiren máquinas específicas de moldeo por inxección de alto rendemento. Se adopta dous puntos de alimentación ou cambia a posición dos puntos de alimentación, a distancia de recheo dos produtos pódese reducir a 100, que é L/T(total)=100/5+100/2=70. A relación de lonxitude agora é inferior ao valor de referencia e é fácil de moldear por inxección. L/T(total)=100/5+200/3=87 cando o grosor da parede se cambia a 3, o que permite o moldeado por inxección normal.
3. Baseado no principio de aparencia:
O rendemento específico do espesor da parede que afecta o aspecto das pezas é o seguinte:
1) Espesor desigual da parede: encollemento da superficie (incluíndo defectos de aparencia como contracción, fosas, impresións grosas e finas), deformación por deformación, etc.
2) Espesor excesivo da parede: defectos como a contracción superficial e os buratos de contracción internos.
3) O grosor da parede é demasiado pequeno: defectos como falta de cola, impresión con dedal, deformación e deformación.
encollemento ou porosidade
a contracción ou a porosidade ocorre normalmente nas áreas de espesor de parede grosa. O mecanismo: segundo o principio de solidificación do material, a porosidade interna e a contracción superficial durante o proceso de moldaxe por inxección débense á constante contracción durante o proceso de arrefriamento. Cando a contracción se concentra na posición de conxelación detrás, pero non se pode compensar de inmediato, é máis probable que se produzan encollemento e porosidade no interior.
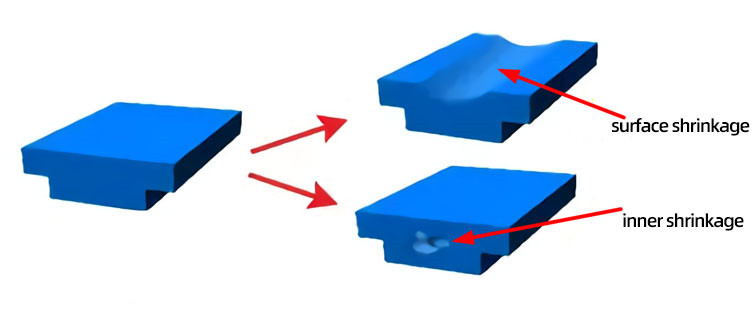
Os principios de deseño do espesor da parede anteriores preséntanse desde catro aspectos, que son as propiedades mecánicas, a formabilidade, o aspecto e o custo. Se usa unha frase para describir o deseño do grosor da parede, ese é o valor do grosor da parede das pezas moldeadas por inxección debe ser o máis pequeno posible e o máis uniforme posible a condición de satisfacer as propiedades mecánicas e o rendemento de procesamento. En caso contrario, debería realizarse unha transición uniforme.
DJmolding ofrece servizos de deseño e fabricación de pezas de plástico para o mercado global, se queres comezar o teu proxecto, póñase en contacto connosco agora mesmo.