Moldeo por inxección de termoplásticos
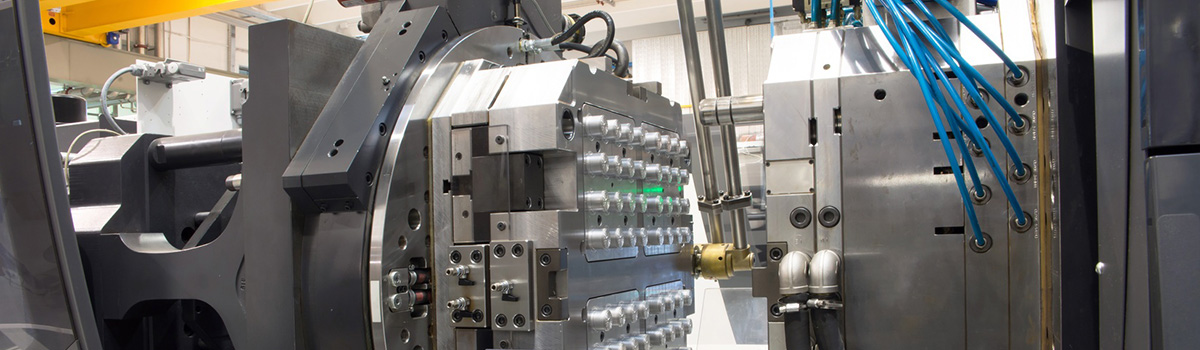
O moldeado por inxección de termoplástico é un proceso de fabricación popular usado para crear varias pezas de plástico para varias industrias. Este proceso consiste en fundir pellets de plástico e inxectalos nun molde para producir unha forma tridimensional. O moldeado por inxección de termoplástico é altamente eficiente e rendible para producir grandes volumes de pezas de plástico de alta calidade con tolerancias estreitas. Esta guía completa explorará os diversos aspectos do moldeado por inxección de termoplásticos, incluíndo as súas vantaxes e desvantaxes, os tipos de termoplásticos utilizados, o proceso de moldeo por inxección, consideracións de deseño e moito máis.
Historia do moldeado por inxección de termoplásticos
A historia do moldeado por inxección de termoplásticos abrangue máis dun século de avances tecnolóxicos, desenvolvementos de materiais e aplicacións industriais. Desde os seus humildes inicios como proceso de moldaxe de celuloide ata a sofisticada tecnoloxía actual, o moldeado por inxección segue a ser unha técnica de fabricación vital, impulsando a innovación e conformando varias industrias.
- Desenvolvementos iniciais:John Wesley Hyatt e o seu irmán Isaiah desenvolveron a primeira máquina de moldeo por inxección práctica, rastrexando as orixes do moldeo por inxección de termoplásticos ata finais do século XIX. En 19, patentaron un dispositivo que utilizaba un émbolo para inxectar celuloide nunha cavidade do molde, creando obxectos sólidos. Este avance sentou as bases para o moderno proceso de moldaxe por inxección.
- Avances nos materiais:A principios do século XX, a introdución de novos polímeros sintéticos abriu novas posibilidades para o moldeado por inxección. A baquelita, unha resina fenólica, converteuse nun material popular para moldear debido ás súas excelentes propiedades illantes eléctricas. Ao longo das décadas de 20 e 1930, os avances na química dos polímeros levaron ao desenvolvemento doutros termoplásticos, como o poliestireno e o polietileno, que ampliaron aínda máis a gama de materiais axeitados para o moldeado por inxección.
- Adopción industrial: A adopción xeneralizada do moldeado por inxección de termoplásticos comezou na década de 1950 cando os fabricantes recoñeceron a súa rendibilidade e versatilidade. A introdución de máquinas de alta presión permitiu tempos de ciclo máis rápidos e aumento dos volumes de produción. Como resultado, xurdiu unha diversa selección de produtos para uso persoal e industrial. Estes incluíron compoñentes do coche, electrodomésticos e xoguetes.
- Innovacións tecnolóxicas:Ao longo das décadas, a tecnoloxía de moldaxe por inxección continuou evolucionando. Na década de 1960 xurdiron máquinas controladas por ordenador, que permitían un control preciso do proceso de moldeo. A introdución de sistemas de canales quentes nos anos 1980 reduciu o desperdicio e mellorou a eficiencia ao eliminar a necesidade de canales e bebedoiros. Nos últimos anos, os avances na automatización, a robótica e a impresión 3D revolucionaron aínda máis a industria do moldeo por inxección, permitindo deseños complexos e reducindo o tempo de produción.
- Sostibilidade e reciclaxe:Coa crecente preocupación ambiental, a industria do moldeado por inxección adoptou medidas de sustentabilidade. Os fabricantes desenvolveron termoplásticos de base biolóxica e reciclados, reducindo a dependencia dos materiais baseados en combustibles fósiles. Ademais, as tecnoloxías de reciclaxe melloradas permitiron o reprocesamento de residuos post-consumo e post-industrial, minimizando o impacto ambiental do moldeado por inxección de termoplásticos.
- Perspectivas de futuro:O futuro do moldeado por inxección de termoplásticos parece prometedor. A industria está a explorar innovacións como o moldeado por microinxección para compoñentes en miniatura, as técnicas de multimateriais e de sobremoldeo para pezas complexas e a integración de tecnoloxías intelixentes para a monitorización e optimización de procesos. Ademais, os investigadores esperan que os avances nos materiais biodegradables e na fabricación aditiva revolucionen o campo, facendo que o moldeado por inxección sexa aínda máis sostible e versátil.
Vantaxes do moldeado por inxección de termoplásticos
O moldeado por inxección de termoplástico ofrece numerosas vantaxes para os fabricantes. Ofrece flexibilidade de deseño, permitindo deseños complexos e intrincados con varias características. O proceso é rendible, reducindo o desperdicio de material e reducindo os custos unitarios. A moldaxe por inxección de termoplástico admite múltiples materiais, proporcionando versatilidade para diferentes aplicacións.
- Flexibilidade de deseño:A moldaxe por inxección de termoplástico permite deseños complexos e complexos con características como socavacións, paredes delgadas e grosores variables, proporcionando aos deseñadores unha inmensa liberdade.
- Eficiencia de custos: O proceso é altamente eficiente, reducindo o desperdicio de material e reducindo os custos unitarios. O moldeado simultáneo de varias pezas e os ciclos de produción rápidos contribúen ao aforro de custos.
- Versatilidade do material: O moldeado por inxección de termoplástico admite unha ampla gama de materiais, o que permite aos fabricantes escoller a opción máis axeitada para cada aplicación, incluíndo materiais ríxidos ou flexibles, transparentes ou opacos e resistentes químicamente.
- Resistencia e durabilidade:Os termoplásticos moldeados por inxección poden presentar excelentes propiedades mecánicas, como alta resistencia, tenacidade e resistencia ao impacto. As opcións de reforzo, como as fibras de vidro ou de carbono, melloran aínda máis estas propiedades.
- Consistencia e calidade:O moldeado por inxección garante unha calidade consistente de peza a peza e unha precisión dimensional, ofrecendo tolerancias estritas e produtos fiables. O proceso tamén proporciona un acabado superficial liso e uniforme, eliminando a necesidade de operacións de acabado adicionais.
- Escalabilidade e produción en masa:O moldeado por inxección é escalable de volumes baixos a altos, polo que é axeitado para a produción en masa. Unha vez que os fabricantes crean o molde, poden producir grandes cantidades de pezas idénticas con variacións mínimas.
- Integración e montaxe:As pezas moldeadas por inxección poden incorporar varios compoñentes nunha soa peza, reducindo a necesidade de procesos de montaxe adicionais. Esta integración mellora o rendemento do produto, reduce o tempo de montaxe e reduce os custos.
- Sostibilidade:A industria do moldeado por inxección está a mostrar un foco crecente na sustentabilidade. A dispoñibilidade de materiais biolóxicos e reciclados permite producir produtos respectuosos co medio ambiente. O uso eficiente dos materiais e a reciclabilidade dos termoplásticos contribúen a un proceso de fabricación máis ecolóxico.
Estes beneficios convertérono nun método de fabricación amplamente adoptado en varias industrias, proporcionando solucións de alta calidade, rendibles e respectuosas co medio ambiente para requisitos complexos de produtos.
Desvantaxes do moldeado por inxección de termoplásticos
Aínda que o moldeado por inxección de termoplástico ofrece numerosas vantaxes, tamén hai varias desvantaxes. Os fabricantes deben avaliar coidadosamente estes factores e comparalos cos beneficios para determinar a idoneidade do moldeado por inxección de termoplásticos para as súas aplicacións específicas.
- Investimento inicial alto: A creación dunha operación de moldaxe por inxección de termoplásticos require un investimento inicial importante no deseño e fabricación de moldes e na compra de maquinaria especializada. Os custos asociados coa creación de moldes e ferramentas poden ser importantes, especialmente para deseños complexos e complexos.
- Limitacións de deseño: Aínda que a moldaxe por inxección de termoplásticos ofrece flexibilidade de deseño, existen certas limitacións. Por exemplo, conseguir un espesor de parede uniforme en toda a peza pode ser un reto, o que provoca variacións na distribución do material e potenciais debilidades estruturais. Ademais, a presenza de socavacións ou xeometrías complexas pode requirir o uso de características adicionais do molde ou operacións secundarias, aumentando os custos e o tempo de produción.
- Tempos longos:O proceso de deseño e fabricación de moldes para o moldeado por inxección pode levar moito tempo, o que leva a prazos máis longos para o desenvolvemento do produto. O proceso de iteración do deseño, a produción de moldes e as probas poden engadir un tempo significativo ao calendario de produción global, o que pode non ser axeitado para proxectos con prazos axustados.
- Restricións de selección de materiais:Aínda que o moldeado por inxección de termoplástico admite unha ampla gama de materiais, hai certas limitacións e restricións. Algúns materiais poden ter requisitos de procesamento específicos ou unha dispoñibilidade limitada, o que incide nas eleccións de deseño e na selección de materiais para unha aplicación concreta.
- Limitacións do tamaño das pezas:As máquinas de moldeo por inxección teñen limitacións de tamaño, tanto no que se refire ao tamaño físico do dispositivo como ao tamaño dos moldes que poden acomodar. A produción de pezas enormes pode requirir equipos especializados ou métodos de fabricación alternativos.
- Impacto Ambiental:Mentres a industria está a traballar pola sustentabilidade, o proceso de moldeo por inxección de termoplásticos aínda xera material de refugallo, incluíndo chatarra e bebedoiros. A eliminación e reciclaxe adecuadas destes materiais son necesarias para minimizar o impacto ambiental.
- A complexidade da optimización de procesos:Conseguir os parámetros de proceso óptimos para o moldeado por inxección de termoplásticos pode ser complexo e lento. Os fabricantes deben controlar e optimizar coidadosamente a temperatura, a presión, as taxas de refrixeración e os tempos de ciclo para garantir unha calidade consistente das pezas e minimizar os defectos.
Tipos de termoplásticos utilizados no moldeado por inxección
Estes son só algúns exemplos dos termoplásticos que se usan habitualmente no moldeo por inxección. Cada material ten propiedades únicas, polo que é axeitado para aplicacións específicas baseadas na resistencia, flexibilidade, resistencia química, transparencia e custo. Os fabricantes deben considerar estas propiedades e requisitos á hora de seleccionar o termoplástico axeitado para os seus proxectos de moldaxe por inxección.
- Polipropileno (PP):O polipropileno é un termoplástico versátil que se usa habitualmente no moldeo por inxección. Ofrece unha excelente resistencia química, baixa densidade e boa resistencia ao impacto. O PP (polipropileno) ten unha ampla aplicación en envases, compoñentes de automóbiles, electrodomésticos e dispositivos médicos.
- Polietileno (PE):O polietileno é outro termoplástico moi utilizado no moldeo por inxección. Está dispoñible en varias formas, como polietileno de alta densidade (HDPE) e polietileno de baixa densidade (LDPE). O PE ofrece unha boa resistencia química, dureza e flexibilidade, polo que é adecuado para botellas, recipientes e tubos.
- Poliestireno (PS):O poliestireno é un termoplástico versátil coñecido pola súa claridade, rixidez e accesibilidade. Atópase de uso común en envases, bens de consumo e produtos desbotables. O PS (poliestireno) permite un procesamento rápido e proporciona unha boa estabilidade dimensional, pero pode ser fráxil e susceptible ao agrietamento ambiental.
- Acrilonitrilo butadieno estireno (ABS): O ABS é un termoplástico popular coñecido pola súa excelente resistencia ao impacto e durabilidade. Combina as propiedades do acrilonitrilo, o butadieno e o estireno para crear un material versátil axeitado para pezas de automóbiles, carcasas electrónicas e xoguetes.
- Cloruro de polivinilo (PVC): O PVC é un termoplástico moi utilizado coñecido pola súa excelente resistencia química, durabilidade e baixo custo. Pode ser ríxido ou flexible dependendo da formulación e dos aditivos empregados. O PVC (cloruro de polivinilo) ten un uso común na construción, illamento eléctrico, produtos sanitarios e envases.
- Policarbonato (PC): O policarbonato é un termoplástico transparente con extraordinario impacto e alta resistencia á calor. Atópase de uso común en aplicacións que requiren claridade óptica, como compoñentes de automóbiles, cascos de seguridade e pantallas electrónicas.
- Nylon (poliamida):O nailon é un termoplástico forte e duradeiro coñecido polas súas excelentes propiedades mecánicas e resistencia química. Atópase de uso común en aplicacións que demandan alta resistencia, como pezas de automóbiles, compoñentes industriais e bens de consumo.
- Tereftalato de polietileno (PET):O PET é un termoplástico popular para producir botellas, envases e materiais de envasado. Ofrece unha boa claridade, resistencia química e propiedades de barreira, polo que é adecuado para aplicacións en alimentos e bebidas.
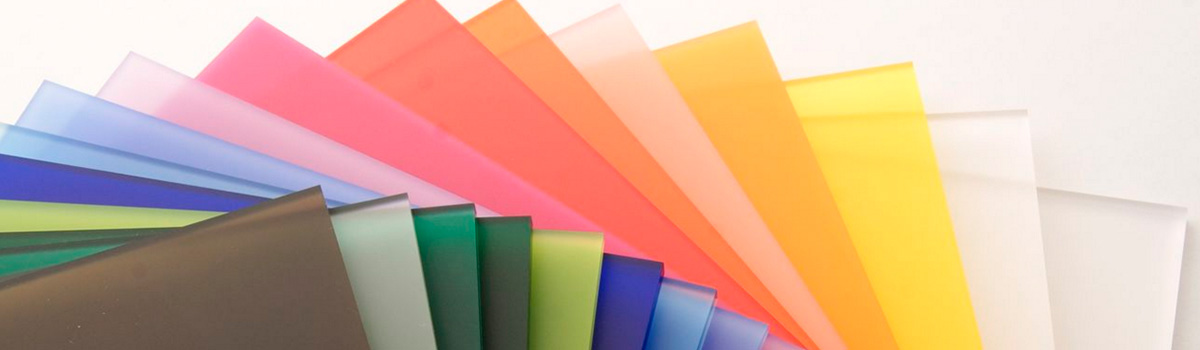
Propiedades dos termoplásticos utilizados no moldeado por inxección
Estas propiedades dos termoplásticos xogan un papel crucial na determinación da súa idoneidade para aplicacións específicas de moldaxe por inxección. Os fabricantes deben considerar coidadosamente estas propiedades e seleccionar o termoplástico adecuado en función do rendemento desexado, das condicións ambientais e dos requisitos de custo.
- Propiedades mecánicas:Os termoplásticos utilizados no moldeo por inxección poden presentar varias propiedades mecánicas, incluíndo resistencia á tracción, resistencia ao impacto e resistencia á flexión. Estas propiedades determinan a capacidade do material para soportar forzas aplicadas e a súa durabilidade global en varias aplicacións.
- Resistencia química:Moitos termoplásticos utilizados no moldeado por inxección posúen unha notable resistencia a produtos químicos, disolventes e aceites. Esta propiedade é crucial para aplicacións que impliquen exposición a ambientes duros ou substancias corrosivas.
- Estabilidade térmica:A estabilidade térmica dos termoplásticos refírese á súa capacidade para soportar temperaturas elevadas sen unha degradación significativa. Algúns termoplásticos presentan unha excelente resistencia á calor, o que lles permite manter as súas propiedades mecánicas incluso a altas temperaturas.
- Propiedades eléctricas:Os termoplásticos utilizados no moldeado por inxección poden ter propiedades eléctricas específicas, incluíndo illamento eléctrico, condutividade ou forza dieléctrica. Estas propiedades son esenciais para aplicacións en industrias eléctricas e electrónicas, onde os materiais deben proporcionar un rendemento eléctrico fiable.
- Transparencia e claridade:Certos termoplásticos, como o policarbonato e o PET, ofrecen unha excelente transparencia e claridade, polo que son axeitados para aplicacións que requiren propiedades ópticas. Os fabricantes adoitan usar estes materiais en produtos como fiestras transparentes, lentes e pantallas.
- Flexibilidade e dureza: A flexibilidade e a dureza son propiedades esenciais dos termoplásticos utilizados en aplicacións que requiren resistencia ao impacto e durabilidade. Algúns termoplásticos, como o ABS e o nailon, ofrecen unha excelente dureza, o que lles permite soportar impactos repetidos sen romperse.
- Estabilidade dimensional:A estabilidade dimensional refírese á capacidade dun termoplástico para manter a súa forma e tamaño en condicións variables, incluíndo cambios de temperatura. Os materiais cunha boa estabilidade dimensional garanten dimensións consistentes das pezas, minimizando o risco de deformación ou deformación.
- Compatibilidade química:A compatibilidade química dos termoplásticos refírese á súa capacidade para resistir a degradación ou interacción con diversos produtos químicos, incluíndo ácidos, bases e disolventes. Para garantir un rendemento óptimo, é esencial seleccionar un termoplástico que poida soportar o ambiente químico específico que atopará na aplicación prevista.
- Densidade: Os termoplásticos teñen grosores variables, o que pode afectar o seu peso e as propiedades xerais das pezas. Os materiais de baixa densidade, como o polietileno, ofrecen solucións lixeiras, mentres que os materiais de alta densidade, como o polipropileno, proporcionan unha maior resistencia e rixidez.
Proceso de moldeo por inxección: paso a paso
O proceso de moldaxe por inxección segue estes pasos, o que permite a produción eficiente e precisa de pezas termoplásticas de alta calidade. Cada paso require un control e seguimento coidadosos para garantir as dimensións da peza, as propiedades do material e a calidade xeral.
- Deseño e fabricación de moldes: O primeiro paso no proceso de moldaxe por inxección é o deseño e fabricación do molde. Os fabricantes deben crear un deseño de molde preciso e detallado para acadar as especificacións das pezas desexadas. A continuación, os fabricantes fabrican o molde mediante diversas técnicas, como CNC ou mecanizado por descarga eléctrica (EDM).
- Preparación do material: O seguinte paso é a preparación unha vez que o molde estea listo. Os gránulos ou gránulos termoplásticos son seleccionados en función das propiedades do material desexado e fúndense nunha tolva. A continuación, os operarios alimentan o material no barril da máquina de moldeo por inxección, onde se somete a fusión e homoxeneización.
- Inxección:Durante a fase de inxección, os operadores inxectan o termoplástico fundido na cavidade do molde a alta presión. A unidade de inxección da máquina empuxa o material fundido a través dunha boquilla e no molde. O material enche a cavidade do molde, tomando a forma da peza desexada.
- Refrixeración e solidificación:Despois de encher o molde, os operadores permiten que o plástico fundido se arrefríe e se solidifique. O arrefriamento é fundamental para conseguir a estabilidade dimensional e a formación adecuada das pezas. Os operadores poden controlar o proceso de arrefriamento facendo circular o refrixerante a través de canles dentro do molde ou usando placas de arrefriamento.
- Apertura e expulsión do molde:Os operadores abren o molde e expulsan a peza da cavidade do molde unha vez que o plástico se solidifica. O sistema de expulsión dentro da máquina usa pasadores, placas expulsoras ou chorros de aire para eliminar a rexión do molde. O molde está listo para o seguinte ciclo de inxección.
- Post-procesamento: Despois da expulsión, a peza pode someterse a operacións de post-procesamento, como recorte, desbarbado ou acabado superficial. Estes pasos axudan a eliminar o exceso de material, a suavizar os bordos ásperos e a mellorar o aspecto final da peza.
- Inspección de Calidade: O paso final consiste en inspeccionar a calidade das pezas inxectadas e asegurarse de que cumpren os requisitos especificados. Pódense empregar varias técnicas de control de calidade, incluíndo medición dimensional, inspección visual e probas funcionais, para verificar a calidade e integridade da peza.
- Reciclaxe e reutilización de materiais:Calquera material en exceso ou refugallo xerado durante o moldeado por inxección pode ser reciclado e reutilizado. Reducir o uso de novo material termoplástico contribúe a minimizar os residuos e mellorar a sustentabilidade.
Equipos utilizados no moldeado por inxección
Estes compoñentes do equipamento facilitan o proceso de moldeo por inxección, desde a fusión e a inxección do material termoplástico ata a conformación, arrefriamento e expulsión da peza final. O correcto funcionamento e mantemento destes compoñentes do equipamento son fundamentais para conseguir unha produción eficiente e de alta calidade de moldaxe por inxección.
- Máquina de moldeo por inxección:O equipo principal no moldeado por inxección é o encargado de fundir o material termoplástico, inxectalo no molde e controlar o proceso.
- Molde: O molde, deseñado a medida para crear a forma e as características desexadas da parte de plástico, consta de dúas metades, a cavidade e o núcleo. Os operadores móveno na unidade de suxeición da máquina de moldeo por inxección.
- Tolva:Recipiente que contén o material termoplástico en forma de gránulos ou granulados e introdúceo no barril da máquina de moldeo por inxección para a súa fusión e inxección.
- Barril e parafuso: O barril, unha cámara cilíndrica, funde e homoxeneiza o material termoplástico mentres o parafuso xira no seu interior para fundir, mesturar e estandarizar o material.
- Sistemas de calefacción e refrixeración:As máquinas de moldeo por inxección teñen elementos de calefacción, como quentadores eléctricos ou quentadores que utilizan aceite quente, para elevar a temperatura do barril, e sistemas de refrixeración, como circulación de auga ou aceite, para arrefriar o molde e solidificar a parte de plástico.
- Sistema de expulsión:Elimina a parte moldeada da cavidade do molde despois da solidificación, normalmente utilizando pasadores de expulsión, placas ou chorros de aire durante a apertura do molde.
- Sistema de control:Supervisa e controla varios parámetros do proceso de moldaxe por inxección, o que permite aos operadores establecer e axustar parámetros como a velocidade de inxección, a temperatura, a presión e o tempo de arrefriamento.
Máquinas de moldeo por inxección: tipos e características
Cada tipo de máquina de moldeo por inxección ten as súas características e vantaxes, o que permite aos fabricantes escoller o dispositivo máis axeitado para as súas necesidades específicas de produción.
- Máquinas de moldeo por inxección hidráulica: Estas máquinas utilizan sistemas hidráulicos para xerar a presión necesaria para inxectar plástico fundido no molde. Son coñecidos pola súa alta forza de suxeición, control preciso e versatilidade no manexo de varios termoplásticos. As máquinas hidráulicas son adecuadas para a produción a gran escala e poden acomodar moldes complexos.
- Máquinas eléctricas de moldeo por inxección:As máquinas eléctricas utilizan servomotores eléctricos para o funcionamento da máquina, incluíndo os sistemas de inxección, suxeición e expulsión. Ofrecen control preciso, eficiencia enerxética e tempos de resposta máis rápidos que as máquinas hidráulicas. As máquinas eléctricas son ideais para aplicacións de moldaxe de precisión que requiren alta repetibilidade e precisión.
- Máquinas de moldeo por inxección híbridas:As máquinas híbridas combinan as vantaxes dos dispositivos hidráulicos e eléctricos. Utilizan unha combinación de servosistemas hidráulicos e eléctricos para lograr unha alta precisión, eficiencia enerxética e rendibilidade. As máquinas híbridas son adecuadas para unha ampla gama de aplicacións, proporcionando un equilibrio entre o rendemento e os custos operativos.
- Máquinas de moldeo por inxección de dúas placas: As máquinas de dúas placas teñen un deseño único con dúas placas separadas para suxeitar o molde. Este deseño proporciona unha estabilidade mellorada, unha sincronización de moldes mellorada e permite tamaños de molde máis grandes e forzas de suxeición máis altas. As máquinas de dúas placas son adecuadas para pezas grandes e complexas que requiren un moldeado preciso.
- Máquinas de moldeo por inxección multicomponente:Os fabricantes deseñan estas máquinas para producir pezas con varios materiais ou cores nun único ciclo de moldeo. Teñen varias unidades de inxección e moldes, que permiten a inxección simultánea de diferentes materiais. As máquinas multicompoñente ofrecen flexibilidade e eficiencia na fabricación de pezas complexas con diferentes características.
- Máquinas de micromoldeo por inxección:Deseñadas especificamente para producir pezas pequenas e precisas, as máquinas de moldeo por microinxección ofrecen unha precisión e precisión incriblemente altas. Poden producir detalles complicados con tolerancias estritas e un mínimo desperdicio de material. A electrónica, os dispositivos médicos e a micro óptica usan habitualmente máquinas de moldeo por microinxección.
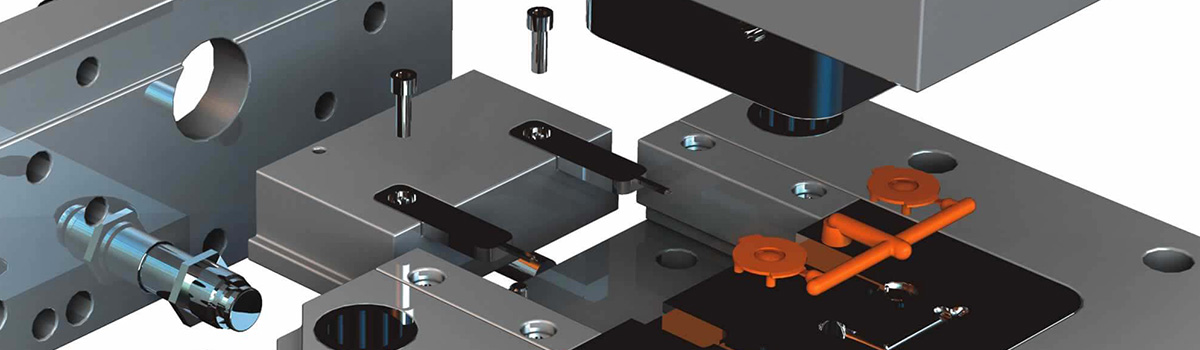
Consideracións de deseño de moldes para o moldeado por inxección
As consideracións coidadosas do deseño de moldes son esenciais para unha produción exitosa de moldaxe por inxección.
- Deseño de pezas:O deseño do molde debe acomodar os requisitos específicos da peza, incluíndo a súa forma, dimensións e características funcionais. Os fabricantes deben considerar adecuadamente os ángulos de calado, o grosor da parede, os socavamentos e calquera elemento necesario para garantir a facilidade de expulsión e a calidade das pezas.
- Material do molde: A selección do material do molde é crucial para lograr durabilidade, estabilidade dimensional e resistencia á calor. Os materiais de moldes comúns inclúen aliaxes de aceiro, aliaxes de aluminio e aceiros para ferramentas. A elección do material depende de factores como o volume de produción, a complexidade da peza e a vida útil esperada da ferramenta.
- Sistema de refrixeración:O arrefriamento eficiente é esencial para a solidificación correcta da peza e para minimizar o tempo de ciclo. O deseño do molde debe incorporar canles de refrixeración ou insercións estratexicamente posicionadas para garantir un arrefriamento uniforme do molde. O arrefriamento adecuado reduce o risco de deformación, encollemento e defectos nas pezas.
- Ventilación:É necesaria unha ventilación adecuada para permitir a fuga de aire e gases durante o proceso de inxección. A ventilación insuficiente pode provocar trampas de gas, marcas de queimaduras ou recheo incompleto das pezas. Os fabricantes poden lograr a ventilación incorporando ranuras de ventilación, pasadores ou outros mecanismos no deseño do molde.
- Sistema de expulsión:O deseño do molde debe incluír un sistema de expulsión eficaz para eliminar de forma segura e eficiente a parte moldeada da cavidade do molde. O sistema de expulsión pode consistir en pasadores de expulsión, mangas ou outros mecanismos, situados estratexicamente para evitar interferencias coa función ou as características críticas.
- Deseño de porta:A porta é onde o plástico fundido entra na cavidade do molde. O deseño da porta debe garantir o recheo axeitado das pezas, minimizar as liñas de fluxo e evitar a conxelación prematura do material. Os deseños de portas estándar inclúen portas de bordo, portas de túneles e sistemas de canles quentes, dependendo dos requisitos da peza e das propiedades do material.
- Liña de partida:O deseño do molde debe definir unha liña de separación adecuada, que é a liña onde se unen as dúas metades do molde. A colocación axeitada da liña de separación garante un desaxuste mínimo de flash e liña de separación e facilita a montaxe eficiente do molde.
- Mantemento e mantemento do molde: Os fabricantes deben considerar a facilidade de mantemento, reparación e mantemento de moldes. Os compoñentes do molde deben ser facilmente accesibles para a súa limpeza, inspección e substitución. A incorporación de funcións como insercións de cambio rápido ou deseños de moldes modulares pode mellorar a funcionalidade do molde.
Materiais de moldes utilizados no moldeado por inxección
Colaborar con especialistas en materiais de molde e ter en conta as necesidades específicas da aplicación de moldaxe pode axudar a determinar o material máis axeitado para conseguir un rendemento óptimo do molde e a calidade das pezas.
- Aliaxes de aceiro: As aliaxes de aceiro, como os aceiros para ferramentas (por exemplo, P20, H13) e os aceiros inoxidables, úsanse habitualmente para moldes de moldeo por inxección debido á súa excelente durabilidade, resistencia á calor e resistencia ao desgaste. Estes materiais poden soportar as altas temperaturas e presións no proceso de moldaxe por inxección e ofrecen unha boa estabilidade dimensional para producir pezas de alta calidade.
- Aliaxes de aluminio:As aliaxes de aluminio, como 7075 e 6061, son lixeiras e ofrecen unha boa condutividade térmica, polo que son aptas para moldes que requiren un arrefriamento eficiente. Os fabricantes adoitan usar moldes de aluminio para prototipado, produción de baixo volume ou aplicacións nas que a redución de peso é fundamental. Non obstante, os moldes de aluminio poden ter unha durabilidade inferior en comparación coas aliaxes de aceiro.
- Aliaxes de cobre:As aliaxes de cobre, como o cobre de berilio, presentan unha alta condutividade térmica e boa maquinabilidade. Atopan uso en moldes que requiren unha excelente transferencia de calor para un arrefriamento eficaz. As aliaxes de cobre poden axudar a reducir os tempos de ciclo ao disipar rapidamente a calor da parte moldeada, o que resulta nunha solidificación máis rápida.
- Aceiros para ferramentas:Os aceiros para ferramentas, incluídos H13, S7 e D2, están deseñados para aplicacións de ferramentas de alto rendemento. Estes aceiros ofrecen unha combinación de alta resistencia, dureza e resistencia ao desgaste. Os aceiros para ferramentas axústanse a moldes con grandes volumes de produción, materiais abrasivos ou condicións de moldeo esixentes.
- Aliaxes de níquel:As aliaxes de níquel, como o Inconel e o Hastelloy, son coñecidas pola súa excepcional resistencia á corrosión, resistencia ás altas temperaturas e estabilidade térmica. Os fabricantes usan estas aliaxes en moldes que manipulan materiais corrosivos ou requiren resistencia a temperaturas extremas e ambientes de moldaxe agresivos.
- Materiais compostos:Os materiais compostos, como os plásticos reforzados ou os compostos con insercións metálicas, úsanse ocasionalmente para aplicacións de moldaxe específicas. Estes materiais ofrecen un equilibrio de propiedades, como alta resistencia, estabilidade térmica e peso reducido. Os moldes compostos poden ser alternativas rendibles para requisitos específicos de produción.
Tipos de moldes de inxección
O moldeado por inxección é un proceso de fabricación versátil e amplamente utilizado para pezas de plástico.
- Molde de dúas placas:O molde de dúas placas é o tipo máis común de molde de inxección. Consta de dúas placas, a placa cavidade e a placa central, que se separan para permitir a expulsión da peza moldeada. A placa da cavidade contén o lado da cavidade do molde, mentres que a placa do núcleo alberga o lado do núcleo. Os fabricantes usan moldes de dúas placas para producir unha ampla gama de pezas debido ao seu deseño relativamente sinxelo.
- Molde de tres placas:O molde de tres placas é unha versión avanzada do molde de dúas placas. Inclúe unha placa adicional, o corredor ou a placa de bebedero. A placa de guía crea unha canle separada para o bebedoiro, os corredores e as portas, o que permite a eliminación máis sinxela da parte moldeada. Os fabricantes adoitan usar moldes de tres placas para detalles con sistemas complexos de cancelación ou cando se desexa evitar un vestixio de porta na peza.
- Molde de corredor quente:O sistema de corredor e porta quéntase en moldes de canal quente, eliminando a necesidade de solidificación e fusión do material durante cada ciclo. O sistema de canal quente consta de colectores e boquillas quentes que manteñen o estado fundido do plástico. Os moldes de canal quente ofrecen vantaxes como o tempo de ciclo reducido, o menor desperdicio de material e a mellora da calidade das pezas ao minimizar os vestixios da porta.
- Molde de corredor frío: Os moldes de corredor frío teñen un sistema tradicional de corredor e porta onde o plástico fundido flúe a través de corredores fríos que se solidifican con cada ciclo. Os operadores retiran posteriormente os corredores solidificados, o que orixina residuos de material. Os fabricantes adoitan usar moldes de corredor complexos para a produción de menor volume ou cando os custos dos materiais son menos críticos debido ao seu deseño máis sinxelo.
- Insertar molde:Os moldes de inserción incorporan insercións de metal ou plástico na cavidade do molde durante o moldeado por inxección. Os insertos pódense colocar previamente no molde ou inserirse mediante procesos automatizados. Este molde permite integrar compoñentes adicionais ou elementos de reforzo na peza moldeada, mellorando a súa funcionalidade ou resistencia.
- Sobremoldeo: O sobremoldeo implica moldear un material sobre outro, normalmente unindo un substrato plástico ríxido cun elastómero ou termoplástico máis suave. Este proceso permite a creación de pezas con múltiples materiais ou texturas nun só molde, proporcionando unha mellor adherencia, amortiguación ou características estéticas.
Factores que afectan os custos de moldeo por inxección
Considerar estes factores pode axudar aos fabricantes a estimar e optimizar o custo do moldeado por inxección, garantindo un equilibrio entre calidade, eficiencia e rendibilidade para os seus requisitos específicos de produción.
- Complexidade da parte:A complexidade do deseño da peza xoga un papel importante na determinación do custo do moldeo por inxección. Xeometrías complicadas, socavacións, paredes delgadas ou características complexas poden requirir ferramentas adicionais, moldes especializados ou ciclos máis longos, o que aumenta o custo total de fabricación.
- Selección de material:A elección do material termoplástico afecta o custo de moldaxe por inxección. Os diferentes materiais teñen prezos variables por quilogramo e factores como a dispoñibilidade do material, as propiedades e os requisitos de procesamento poden influír no custo global do material.
- Deseño de ferramentas e moldes: Os custos iniciais de ferramentas e deseño de moldes son significativos nos custos de moldaxe por inxección. Factores como a complexidade do molde, o número de cavidades, o tamaño do molde e o material do molde contribúen aos gastos de fabricación de ferramentas e moldes. Os moldes máis complexos ou os que requiren funcións avanzadas poden aumentar o investimento inicial.
- Volume de produción: O volume de produción incide directamente no custo por peza no moldeado por inxección. Os libros máis altos adoitan producir economías de escala, reducindo o custo por parte. Pola contra, as producións de baixo volume poden incorrer en custos máis elevados debido á instalación, ás ferramentas e ao desperdicio de material.
- Tempo de ciclo: O tempo de ciclo, que inclúe as fases de refrixeración e expulsión, afecta á capacidade de produción e ao custo global. Ciclos máis longos dan lugar a unha redución da produción e prezos potencialmente máis elevados. Optimizar o deseño do molde, o sistema de refrixeración e os parámetros do proceso pode minimizar os tempos de ciclo e mellorar a eficiencia.
- Requisitos de calidade:Os estritos requisitos de calidade ou certificacións específicas poden afectar o custo de moldaxe por inxección. Cumprir tolerancias exactas, requisitos de acabado de superficie ou probas adicionais poden requirir outros recursos, procesos ou inspeccións, que se suman ao custo global.
- Operacións secundarias:Se as pezas moldeadas requiren operacións de post-procesamento, como montaxe, pintura ou pasos adicionais de acabado, estas operacións poden aumentar o custo total de moldaxe por inxección.
- Provedor e localización:A elección do provedor de moldaxe por inxección e a súa localización poden afectar os custos. Os custos laborais, os gastos xerais, a loxística e os gastos de transporte varían en función da localización do provedor, afectando o custo total de fabricación.
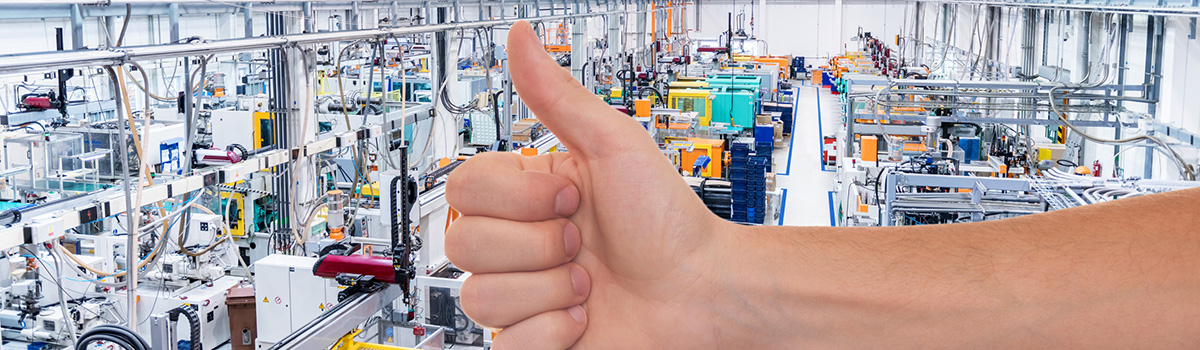
Control de Calidade en Moldeo por Inxección
A implementación de medidas sólidas de control de calidade ao longo do proceso de moldaxe por inxección axuda a identificar e abordar os posibles defectos, desviacións ou inconsistencias, garantindo a produción de pezas de alta calidade que cumpran as especificacións e requisitos do cliente.
- Seguimento do proceso: O seguimento continuo dos parámetros clave do proceso, como a temperatura de fusión, a presión de inxección, o tempo de arrefriamento e o tempo de ciclo, garante a consistencia e a repetibilidade na produción de pezas. A monitorización en tempo real e os sistemas automatizados poden detectar variacións ou desviacións dos parámetros establecidos, o que permite axustes oportunos e manter a estabilidade do proceso.
- Inspección e medición:A revisión e medición regular das pezas moldeadas son esenciais para verificar a precisión dimensional, a calidade das pezas e o cumprimento das especificacións. Os nosos servizos abranguen unha variedade de métodos de control de calidade, como a medición de dimensións, a análise da calidade da superficie, a realización de inspeccións visuais e a realización de probas funcionais. Empréganse diversas técnicas de inspección, como máquinas de medición de coordenadas (CMM) e sistemas de inspección óptica e visual, para unha avaliación precisa.
- Control estatístico de procesos (SPC): SPC implica a recollida e análise de datos do proceso para supervisar e controlar a calidade do moldeo por inxección. Os métodos estatísticos, como os gráficos de control e a análise da capacidade do proceso, axudan a identificar tendencias, detectar variacións do proceso e garantir que o proceso permanece dentro dos límites de control definidos. SPC permite a identificación proactiva de problemas e facilita a optimización do proceso.
- Proba de materiais: A proba das materias primas, como termoplásticos, aditivos e colorantes, garante a súa calidade e idoneidade para o moldeado por inxección. As probas de materiais poden incluír análise do índice de fluxo de fusión (MFI), propiedades mecánicas, características térmicas e composición do material. A verificación da calidade do material axuda a evitar defectos e inconsistencias nas pezas moldeadas.
- Mantemento e inspección de ferramentas:O mantemento axeitado e a inspección regular dos moldes de inxección son fundamentais para garantir a calidade no moldeo por inxección. A limpeza, a lubricación e a avaliación regulares dos compoñentes do molde axudan a evitar o desgaste, danos ou degradacións que poidan afectar á calidade das pezas. A reparación ou substitución oportuna dos compoñentes desgastados ou danados do molde é esencial para manter un rendemento de moldaxe consistente.
- Documentación e Trazabilidade:Manter unha documentación completa e rexistros de trazabilidade é esencial para o control de calidade no moldeo por inxección. É vital rexistrar os parámetros do proceso, os resultados da inspección, a información do material e calquera cambio ou axuste realizado durante a produción. A documentación adecuada permite a trazabilidade das pezas, facilita a análise da causa raíz e garante a coherencia na calidade.
- Formación e desenvolvemento de habilidades: Proporcionar programas adecuados de formación e desenvolvemento de habilidades para operadores, técnicos e persoal de control de calidade mellora a súa comprensión dos procesos de moldaxe por inxección, os requisitos de calidade e as técnicas de inspección. O persoal ben adestrado pode detectar defectos, solucionar problemas e implementar medidas correctoras de forma eficaz, garantindo unha produción de alta calidade.
Defectos comúns de moldaxe por inxección e como evitalos
A inspección, seguimento e análise regular dos procesos de moldaxe por inxección e o mantemento e axuste axeitado dos equipos e moldes poden axudar a identificar e solucionar estes defectos comúns.
- Marcas de pía:As marcas de pía son depresións ou muescas na superficie da peza moldeada causadas por un arrefriamento ou encollemento desigual. Débese considerar a localización e deseño adecuados da porta, o deseño óptimo do sistema de refrixeración e a distribución uniforme do grosor da parede para evitar marcas de afundimento. Aumentar a presión de inxección ou axustar o tempo de arrefriamento tamén pode axudar a minimizar as marcas do pía.
- Warpage:A deformación refírese á deformación ou flexión dunha peza moldeada despois da expulsión debido ao arrefriamento irregular ou a tensións residuais. Manter un espesor de parede uniforme, usar canles de refrixeración adecuadas e garantir un recheo e embalaxe equilibrados do molde son fundamentais para evitar a deformación. A optimización da temperatura do molde, o uso de ángulos de calado axeitados e o control da temperatura do material e da velocidade de inxección poden axudar a minimizar a deformación.
- Flash:O destello prodúcese cando o exceso de material flúe na liña de separación do molde, o que orixina proxeccións delgadas e non desexadas ou material extra na parte final. Pódese evitar eficazmente o flash garantindo un deseño axeitado do molde, incluíndo a aplicación da forza de suxeición adecuada, o aliñamento preciso e o uso de técnicas de ventilación adecuadas. A optimización dos parámetros do proceso como a presión de inxección, a temperatura e o tempo de ciclo reduce o flash.
- Tiro curto:Un disparo rápido ocorre cando o material inxectado non enche a cavidade do molde, o que resulta nunha peza incompleta. A selección adecuada do material, garantir a temperatura de fusión e a viscosidade adecuadas e manter a presión e o tempo de inxección adecuados son esenciais para evitar fotos curtas. Ademais, verificar o deseño do molde para obter o tamaño suficiente de corredor e porta e unha ventilación adecuada pode axudar a evitar disparos rápidos.
- Liñas de soldadura:As liñas de soldadura ocorren cando dúas ou máis frontes de fluxo de material fundido se atopan e se solidifican, resultando unha liña ou marca visible na superficie da peza. Un bo deseño de porta e corredor, a temperatura de fusión óptima, a velocidade de inxección e o axuste do fluxo de material e da xeometría da peza poden minimizar as liñas de soldadura. A análise do fluxo de moldes e a optimización da colocación da porta tamén poden axudar a previr ou mitigar as liñas de soldadura.
- Marcas de queima:As marcas de queimadura son decoloracións ou manchas negras na superficie da peza moldeada causadas pola calor excesiva ou o sobrequecemento do material. Evitar temperaturas de fusión extremas, usar canles de refrixeración adecuadas e optimizar o tempo do ciclo poden axudar a evitar marcas de queimadura. A ventilación adecuada, o deseño adecuado da porta e o control da temperatura do molde tamén contribúen a minimizar as marcas de queimadura.
Operacións postmoldeo: acabado e montaxe
Despois do moldeado por inxección, moitas pezas moldeadas poden requirir operacións adicionais de acabado e montaxe para conseguir o produto final desexado. Estas operacións posteriores ao moldeado poden incluír:
- Recorte:Elimine o exceso de material ou flash ao redor da parte moldeada usando ferramentas de recorte ou de corte.
- Tratamento de superficie:Mellorar o aspecto ou a funcionalidade da superficie da peza mediante diversas técnicas como pintura, revestimento ou texturado.
- montaxe:Unir varias pezas moldeadas ou engadir compoñentes como fixadores, insercións ou etiquetas para completar o produto final.
- Proba:Verificación da calidade e da funcionalidade das pezas mediante diversos métodos de proba, como análise dimensional, probas de propiedades dos materiais ou probas de rendemento.
- Embalaje e envío:Embalaxe e etiquetaxe adecuados do produto acabado para o seu envío aos clientes ou usuarios finais.
A selección das operacións de postmoldeo depende da aplicación específica e das características do produto final desexado. A estreita colaboración entre expertos en moldaxe por inxección, especialistas en acabados e montaxe e o cliente é fundamental para acadar a calidade e a funcionalidade absolutas desexadas do produto. A planificación adecuada e a integración das operacións posteriores ao moldeado no proceso de fabricación poden axudar a garantir a produción eficiente e a entrega oportuna de produtos de alta calidade.
Moldeo por inxección fronte a outros procesos de fabricación de plástico
Cada proceso de fabricación de plásticos ten vantaxes e limitacións, polo que son axeitados para diferentes aplicacións.
- Moldeo por inxección: O moldeado por inxección é un proceso de fabricación moi versátil e moi utilizado para producir pezas de plástico. Ofrece vantaxes como a alta eficiencia de produción, a replicación precisa das pezas e a capacidade de crear xeometrías complexas. O moldeado por inxección é axeitado para series de produción de gran volume e permite o uso dunha ampla gama de materiais termoplásticos. Ofrece unha excelente precisión dimensional e acabado superficial, polo que é ideal para diversas industrias como a automoción, os bens de consumo e os dispositivos médicos.
- Moldeo por soplado: O moldeado por soplado é un proceso utilizado principalmente para producir pezas plásticas ocas, como botellas, envases e compoñentes de automóbiles. Implica fundir o plástico e inflalo nunha cavidade do molde, creando a forma desexada. O moldeado por soplado é axeitado para a produción de gran volume e pode producir pezas grandes e lixeiras cun grosor de parede uniforme. Non obstante, é limitado en termos de complexidade da peza e selección de materiais en comparación co moldeado por inxección.
- Termoformado:O termoformado é un proceso empregado para producir pezas de plástico quentando unha lámina termoplástica e dándolle forma mediante moldes ou conformación ao baleiro. Atópase de uso común en envases, produtos desbotables e produtos a gran escala, como bandexas e fundas. O termoformado ofrece unha produción rendible para pezas grandes e permite un prototipado rápido. Non obstante, ten limitacións en canto á complexidade das pezas, á selección do material e á precisión dimensional en comparación co moldeado por inxección.
- Extrusión:A extrusión é un proceso continuo para producir perfís, follas, tubos e películas de plástico. Implica fundir resina plástica e forzala a través dunha matriz para crear a forma desexada. A extrusión é adecuada para producir longos e continuos produtos plásticos cunha sección transversal consistente. Aínda que a extrusión ofrece altas taxas de produción e rendibilidade, é limitada en termos de xeometrías de pezas complexas e control dimensional preciso en comparación co moldeado por inxección.
- Moldeo por compresión:O moldeado por compresión consiste en colocar unha cantidade premedida de material termoendurecible nunha cavidade do molde quente e comprimilo a alta presión ata que cura. Atópase de uso común na produción de pezas con alta resistencia e estabilidade dimensional, como compoñentes de automóbiles e illamento eléctrico. O moldeado por compresión ofrece unha boa consistencia das pezas, unha alta eficiencia de produción e a capacidade de utilizar unha ampla gama de materiais. Non obstante, é limitado en termos de complexidade da peza e tempo de ciclo en comparación co moldeado por inxección.
Aplicacións do moldeado por inxección de termoplásticos
Varias industrias utilizan amplamente o moldeado por inxección de termoplásticos debido á súa versatilidade, eficiencia e rendibilidade. Algunhas das aplicacións do moldeado por inxección de termoplásticos inclúen:
- Industria da automoción: A industria do automóbil utiliza amplamente o moldeado por inxección de termoplásticos para fabricar varios compoñentes, incluíndo molduras interiores e exteriores, cadros de mandos, paneis de portas, parachoques e conectores eléctricos. O proceso permite a replicación precisa de pezas, xeometrías complexas e materiais lixeiros, mellorando a eficiencia do combustible e a flexibilidade do deseño.
- Bens de consumo:O moldeado por inxección atopa amplas aplicacións na produción de bens de consumo, como electrodomésticos, dispositivos electrónicos, envases de embalaxe e xoguetes. O proceso permite a produción en masa de produtos duradeiros e de alta calidade con dimensións e acabado superficial consistentes. Tamén permite opcións de personalización e iteracións rápidas do produto.
- Dispositivos médicos:O moldeado por inxección xoga un papel crucial na industria médica para producir unha ampla gama de dispositivos, incluíndo xeringas, instrumentos cirúrxicos, compoñentes implantables e sistemas de administración de medicamentos. O proceso garante a produción de pezas estériles, precisas e biocompatibles que cumpran os estritos requisitos regulamentarios do sector sanitario.
- Industria electrónica e eléctrica:A industria electrónica utiliza moldaxe por inxección para fabricar conectores eléctricos, carcasas, interruptores e outros compoñentes. O proceso ofrece unha alta precisión dimensional, un excelente acabado superficial e a capacidade de incorporar características como o moldeado por inserción e o sobremoldeo, o que permite unha produción eficiente de conxuntos electrónicos complexos.
- Industria de envases:Varias industrias, incluíndo alimentos e bebidas, produtos farmacéuticos e coidados persoais, adoitan utilizar o moldeado por inxección para producir envases de plástico, tapas, peches e botellas. O proceso permite a creación de solucións de envasado lixeiras, duradeiras e estéticamente atractivas con ciclos de fabricación eficientes.
- Industria aeroespacial:O sector aeroespacial emprega o moldeado por inxección para a fabricación de compoñentes lixeiros e de alto rendemento, como condutos de aire, soportes, paneis interiores e pezas estruturais. O proceso permite utilizar materiais avanzados e xeometrías de pezas complexas, contribuíndo á redución de peso e á mellora da eficiencia do combustible.
Impacto ambiental do moldeado por inxección de termoplásticos
O moldeado por inxección de termoplásticos é un proceso de fabricación popular debido aos seus moitos beneficios, pero tamén é esencial ter en conta o seu impacto ambiental. Aquí tes algúns puntos a ter en conta:
- Eficiencia do material:O moldeado por inxección de termoplástico promove a eficiencia do material minimizando os residuos. O proceso utiliza un control preciso sobre a cantidade de material inxectado no molde, reducindo a necesidade de exceso de material. Os fabricantes tamén poden empregar técnicas de moenda e reciclaxe para reutilizar chatarra ou pezas rexeitadas, reducindo aínda máis o desperdicio de material.
- Consumo de enerxía:Os fabricantes deseñan máquinas de moldeo por inxección para ser eficientes enerxéticamente, con modelos modernos que incorporan tecnoloxías avanzadas como servomotores e variadores de velocidade. Estas características optimizan o uso de enerxía reducindo o consumo de enerxía durante o moldeado, o que resulta en menores requisitos de enerxía e reducindo o impacto ambiental.
- Xestión de residuos:Mentres minimizan o desperdicio de material, os fabricantes deberían implementar prácticas adecuadas de xestión de residuos para manexar os materiais sobrantes, sprues ou corredores. Os fabricantes poden establecer programas de reciclaxe para recoller e reutilizar os residuos plásticos xerados durante o moldeado por inxección, reducindo así os residuos enviados aos vertedoiros.
- Redución de emisións: O moldeado por inxección de termoplástico xera xeralmente menos emisións que outros procesos de fabricación. Os fabricantes poden reducir as emisións empregando materiais ecolóxicos, implementando equipos de eficiencia enerxética e empregando sistemas avanzados de escape e filtración para capturar as emisións liberadas.
- Opcións de materiais sostibles:A selección de materiais termoplásticos pode afectar significativamente a sustentabilidade ambiental do moldeado por inxección. Optar por plásticos biodegradables ou de base biolóxica, así como por materiais reciclados ou reciclables, pode axudar a reducir a pegada ecolóxica global do proceso.
Consideracións do ciclo de vida: é fundamental ter en conta todo o ciclo de vida do produto moldeado para avaliar o seu impacto ambiental. Durante as etapas de deseño e selección de materiais, os fabricantes deben considerar factores como a durabilidade da peza, a súa reciclabilidade e o potencial de eliminación ou reutilización ao final da súa vida útil.
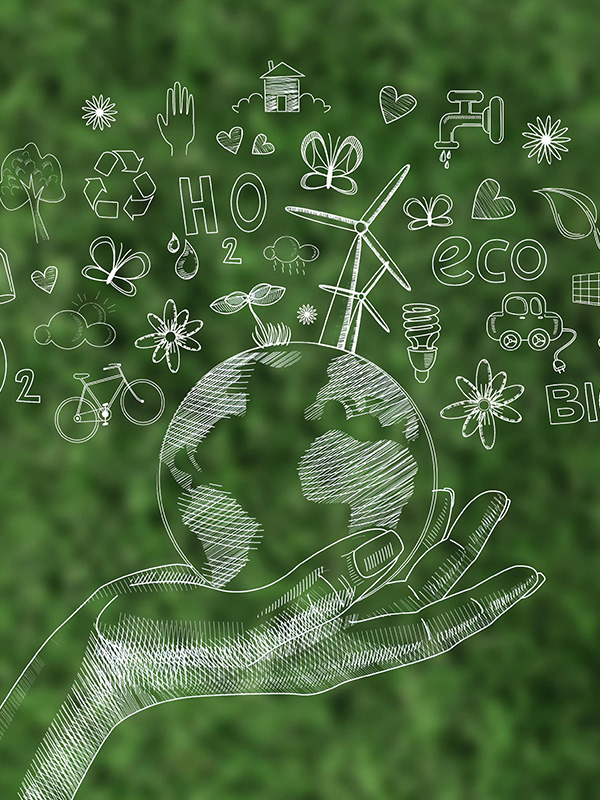
Futuro do moldeado por inxección de termoplásticos
O futuro do moldeado por inxección de termoplásticos parece prometedor, con continuos avances na tecnoloxía e unha maior demanda de pezas de alta calidade e precisión en varias industrias. Algunhas das principais novidades previstas nos próximos anos inclúen:
- Aumento do uso da automatización e da robótica para mellorar a eficiencia e reducir os custos.
- Os esforzos céntranse no desenvolvemento de novos materiais e procesos para mellorar o rendemento das pezas e habilitar novas aplicacións.
- Trátase dunha crecente adopción de prácticas sostibles, como o uso de materiais reciclados e a optimización do consumo de enerxía, para reducir o impacto ambiental do moldeado por inxección.
- Maior integración de tecnoloxías dixitais, como software de impresión e simulación 3D, para mellorar os procesos de deseño e produción.
O mercado global de moldaxe por inxección está en expansión, especialmente nas economías emerxentes, impulsado pola crecente demanda de produtos plásticos en varias industrias.
Elixir o socio adecuado de moldeo por inxección
Elixir o socio adecuado de moldaxe por inxección é fundamental para o éxito do seu proxecto. Tómese o tempo para avaliar varias opcións, realizar visitas ao sitio e participar en discusións exhaustivas para garantir unha colaboración compatible e duradeira.
- Pericia e experiencia:Busque un socio de moldaxe por inxección con amplos coñecementos e experiencia na industria. Deben ter un historial comprobado de ofrecer produtos e solucións de alta calidade a clientes de varios sectores. Considere a súa comprensión dos diferentes materiais, deseños de moldes e procesos de fabricación.
- Capacidades de fabricación: Avaliar as capacidades de fabricación do socio de moldaxe por inxección. Asegúrate de ter unha instalación ben equipada con maquinaria e tecnoloxías modernas para xestionar os requisitos do teu proxecto. Considere a súa capacidade de produción, a capacidade de manexar diferentes tamaños de pezas e complexidades e a capacidade de cumprir os seus volumes de produción e prazos desexados.
- Garantía de calidade:A calidade é primordial no moldeado por inxección. Avaliar os sistemas de control de calidade e as certificacións do socio potencial. Busque socios que sigan estritos estándares de calidade, teñan sólidos procesos de inspección e realicen probas exhaustivas para garantir a calidade e a coherencia das pezas.
- Apoio ao deseño e enxeñería:Un socio fiable de moldaxe por inxección debería ofrecer soporte de deseño e enxeñería para optimizar o deseño da súa peza para a súa fabricación. Deben contar con enxeñeiros cualificados que poidan proporcionar información valiosa sobre a selección de materiais, o deseño de moldes e a optimización do proceso para mellorar a calidade e a eficiencia das pezas.
- Competitividade de custos:Aínda que o custo non debe ser o único factor determinante, é esencial avaliar os prezos e a competitividade dos custos do socio de moldaxe por inxección. Solicite presupostos detallados e considere os custos de ferramentas, os custos de materiais, os custos de man de obra e calquera servizo adicional que proporcionen.
- Comunicación e colaboración:A comunicación e a colaboración efectivas son esenciais para unha asociación exitosa. Asegúrate de que o socio de moldaxe por inxección ten boas canles de comunicación, responde ás túas consultas e pode proporcionar actualizacións regulares do proxecto. Un enfoque colaborativo axudaralle a garantir que cumprimos os teus requisitos e abordamos con prontitude calquera reto.
- Referencias e comentarios de clientes:Busca referencias de clientes ou le recensións/testemuños para obter información sobre as experiencias doutros clientes co socio de moldaxe por inxección. A obtención desta información pode axudar a determinar a súa fiabilidade, rapidez e nivel xeral de satisfacción do cliente.
Conclusión
O moldeado por inxección de termoplástico é un método versátil e rendible para fabricar pezas de plástico en grandes cantidades. A súa capacidade para producir formas complexas con alta precisión e consistencia converteuse nunha opción popular para varias industrias, incluíndo a automoción, a médica, a electrónica e os bens de consumo. Ao comprender os diferentes aspectos do moldeado por inxección de termoplásticos, incluíndo as súas vantaxes, desvantaxes e consideracións de deseño, pode tomar decisións informadas sobre a elección do socio de moldaxe por inxección axeitado para as súas necesidades empresariais.