Solucións aos defectos comúns de moldaxe do moldeo por inxección
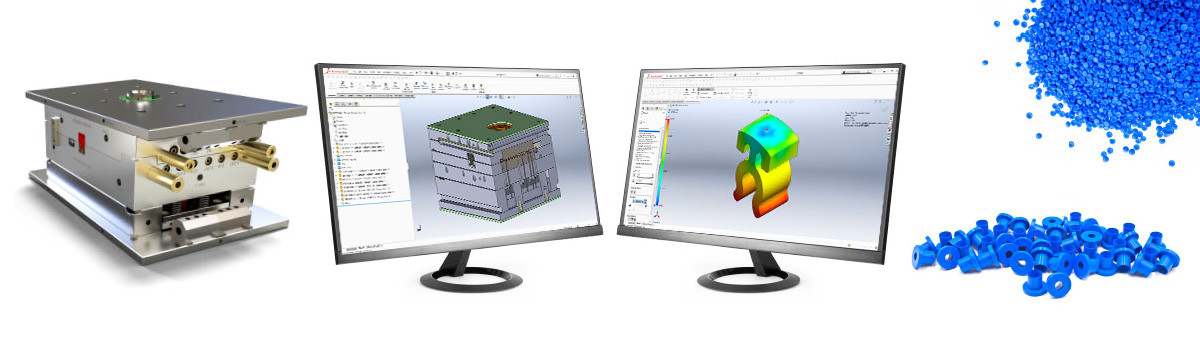
Os defectos son comúns cando se usan moldes para procesar pezas de moldaxe por inxección de plástico, e isto afecta en gran medida á eficiencia do procesamento. A continuación móstranse os defectos e solucións comúns de moldaxe para pezas de moldes de inxección de plástico.
Tiros curtos
As tomas curtas fan referencia a que os produtos elaborados están incompletos debido a que os moldes non están completamente cheos.
Este defecto adoita aparecer no punto máis afastado da porta ou nas partes ás que só se pode acceder a través das zonas estreitas do molde porque as zonas estreitas poden afectar o fluxo de fundidos.
O disparo curto pode causar marcas de microfluxo ou provocar que se falte unha gran parte do produto.
Porque:
As causas dos tiros curtos inclúen:
A materia prima inxectada no molde non é suficiente.
A resistencia dos fundidos é grande, polo que o molde non se pode encher completamente.
A ventilación do molde é deficiente e provoca a xeración de cavitación que bloquea o fundido, facendo que o fundido non poida fluír a algunhas áreas do molde.
Barros
As rebabas xéranse pola adhesión do exceso de materias primas extruídas desde a cavidade do molde ata o produto.
Este defecto vai sobre os bordos do produto ou cada parte composta de molde. A materia prima pode desbordarse do molde ou dos lugares de unión dos moldes móbiles e de fixación.
Tamén se poden atopar rebabas no núcleo do molde, que se debe á presión hidráulica ou a perno angular.
A gravidade das rebabas varía, ás veces finas, ás veces máis grosas.
Porque:
As causas das rebabas inclúen:
A superficie do molde de suxeición está danada ou está moi desgastada.
O molde móbil e o molde de fixación deslócanse cando están bloqueados.
A presión da materia prima no molde é maior que a forza de suxeición do molde.
A terceira condición mencionada anteriormente sería o resultado de varias razóns. Nas seguintes situacións, a presión da materia prima é maior que a forza de suxeición do molde.
Na primeira fase do molde de inxección (etapa de recheo do molde), énchese demasiada materia prima, o que aumenta a presión dentro do molde.
Durante o proceso de recheo do molde, a gran resistencia do fluxo de fusión tamén aumentará a presión dentro do molde.
A presión da cavidade do molde é demasiado alta durante a fase de mantemento da presión.
A forza de suxeición do molde non é suficiente.
Degradación
A descomposición pode levar a moitos resultados. O alcance e a gravidade do problema tamén varían. No caso máis grave, pode provocar unha decoloración completa do produto e unhas propiedades mecánicas deficientes. A degradación local só provocará franxas ou manchas escuras.
Porque:
A degradación prodúcese porque a materia prima está danada. As moléculas de cadea longa que forman plásticos descompoñeranse baixo a acción da calor excesiva ou un esforzo cortante excesivo. Durante a descomposición das moléculas, o gas volátil acelerará o proceso de degradación, o que provocará a descoloración da materia prima. A descomposición dunha gran cantidade de moléculas finalmente romperá o contido da materia prima e causará unha influencia negativa nas propiedades mecánicas.
A degradación local pode ser o resultado da temperatura desigual do barril de material.
A degradación pode producirse nas seguintes situacións:
A materia prima está a ser sobrequentada no barril de material ou no sistema de canal quente.
A materia prima permanece no barril durante moito tempo.
Durante o proceso de moldaxe por inxección, a tensión de cizallamento exercida sobre a materia prima é demasiado grande. Se as boquillas están bloqueadas, ou as portas e o corredor son demasiado estreitos, aumentará o esforzo cortante.
Deformación
Nas situacións normais, as formas dos produtos deben estar en consonancia coa dos moldes. A deformación refírese á deformidade dos produtos.
Cando a condición empeora, os produtos deformaranse completamente cando se expulsa do molde. Cando a condición non é grave, a forma do produto aparecerá pequenas irregularidades.
Longas pero sen bordos de apoio ou grandes planos son as zonas máis propensas á deformación.
Porque:
Causas da deformación:
A temperatura é demasiado alta cando se libera o molde.
Como o tempo de arrefriamento é diferente en áreas grosas e finas, ou a diferenza de temperatura do molde no molde en movemento e no molde de fixación, a contracción no interior dos produtos é diferente.
O fluxo do molde non é suave ao encher (a chamada "orientación de conxelación") ou a presión dentro da cavidade do molde é demasiado alta na fase de mantemento da presión.
Impurezas
As impurezas adoitan aparecer en forma de manchas de diferentes cores, manchas ou raias. O máis común é a mancha negra.
As impurezas poden ser só pequenas manchas, pero tamén poden ser raias obvias ou gran parte da decoloración cando é grave.
Porque:
As impurezas son causadas por produtos diversos mesturados con materias primas, como:
A materia prima mestúrase con artigos diversos cando se transporta aos barrís.
A descomposición da materia prima pode caer de calquera mecanismo de corte e mesturarse con materias primas, como parafusos da máquina, parede interna do tambor de secado, xuntas / boquillas.
Laminación
A laminación xerará o "efecto pel" na superficie dos produtos, que é causado pola diferenza de propiedades e texturas da superficie dos produtos e outras materias primas, e forma unha pel descascarada que se pode eliminar.
Cando a laminación é seria, toda a área de sección transversal está formada por diferentes capas e non se fundiu. Cando os defectos son menos evidentes, a aparencia dos produtos pode cumprir os requisitos, pero romperá as propiedades mecánicas dos produtos.
Porque:
Hai dúas causas principais para a laminación. O primeiro é que cando dous tipos diferentes de materias primas se mesturan incorrectamente. As dúas materias primas transportaranse ao barril ao mesmo tempo baixo presión. Non obstante, cando o molde non se pode fundir cando se arrefría, así como as diferentes capas son presionadas á forza para formar produtos.
Segundo: se a fusión fría é forzada a pasar pola porta estreita, xerarase o esforzo cortante. O esforzo cortante demasiado alto fará que a capa de fusión fundida con antelación non se poida fundir completamente.
Risco de mestura:
Unha cousa que debes ter en conta é que algunhas materias primas mesturadas provocarán unha forte reacción química, como PVC e Avetal non se deben mesturar.
Prata lineal
A franxa lineal pode ser só un fenómeno local, pero podería expandirse a toda a superficie cando é grave.
A prata lineal afectará o aspecto dos produtos e tamén danará as propiedades mecánicas dos produtos.
Porque:
Os dous puntos seguintes provocan a liña de prata:
A materia prima está mollada e algunhas delas absorberán o vapor do aire. Se a materia prima está moi húmida, o vapor presurizado pode xerarse baixo a alta temperatura e a alta presión do barril. Estes vapores atravesan a superficie do produto e forman franxas prateadas.
O fundido danouse térmicamente e xera degradación local. O gas volátil xerado bloquearase na superficie do molde e xerará franxas na superficie dos produtos.
Isto non é tan peor como a degradación. Sempre que a temperatura de fusión sexa alta ou estea sometida a un esforzo cortante durante a plastificación ou a inxección no molde, isto pode ocorrer.
Brillo/sombra
O acabado superficial dos produtos debe ser o mesmo que o dos moldes. Cando o acabado superficial de dous é diferente, producíronse os defectos de brillo/sombra.
A superficie será sombría cando se produzan defectos e a superficie rugosa é lisa e brillante.
Porque:
As causas do brillo/sombra inclúen:
O fundido flúe sen problemas ou a temperatura da superficie do molde é baixa, polo que o acabado da superficie do molde non se pode duplicar ao moldear o material.
Durante a retención de presión, a presión na cavidade non é o suficientemente alta como para que o material se adhiera á superficie do molde no proceso de arrefriamento, deixando marcas de encollemento.
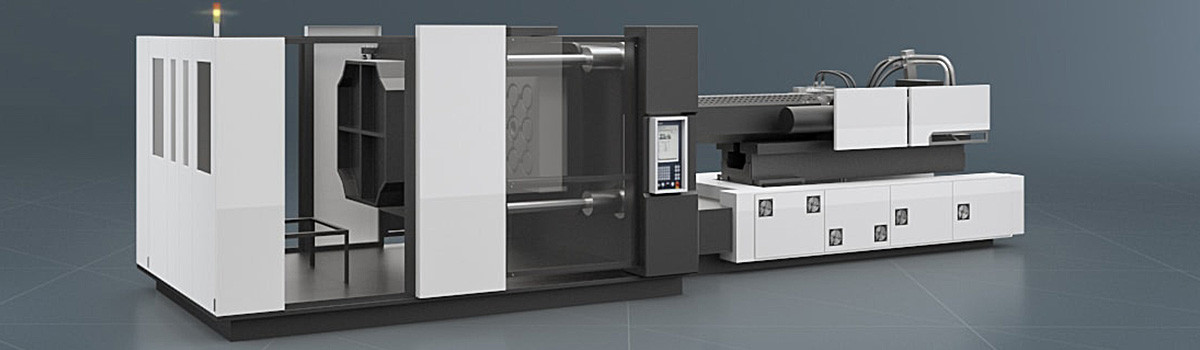
Fluxos
As marcas de fluxo pódense atopar na superficie dos produtos en múltiples formas. Xeralmente, formará unha zona de sombra.
As marcas de fluxo non producen ningún relevo ou depresión na superficie dos produtos, que non se poden sentir cos dedos. Este defecto tamén se denomina marcas de arrastre, fantasmas e sombras.
Cando as marcas de fluxo son obvias, xerará surcos e deixará defectos como marcas na superficie dos produtos.
Porque:
As marcas de fluxo pódense atopar cando:
A fluidez do fundido é pobre ou a temperatura superficial do molde é baixa, o que resulta nunha gran resistencia ao fluxo de plástico no proceso de recheo do molde.
No recheo do molde, o fluxo de fusión con resistencia, que pode ser causado pola superficie irregular da matriz, as marcas ou patróns impresos na superficie da matriz ou o cambio da dirección do fluxo de fusión durante o proceso de recheo.
Liña de unión
A liña de unión xérase cando dúas frontes de fusión se atopan durante o recheo do molde, e aparecerá na superficie do produto como unha liña.
A liña de unión é como a liña de rachaduras na superficie dos produtos, que non é obvio detectar.
Ao deseñar moldes, algunhas liñas de unión visibles son inevitables. Neste caso, acurta a liña de unión o máximo posible para evitar que a resistencia e o aspecto dos produtos sexan danados.
Porque:
Hai moitas razóns para a xeración de fronte de fusión. A razón máis posible podería ser o fluxo de fusión ao longo dos bordos do núcleo do molde. Cando as dúas fusións se atopan, produce as liñas de unión. A temperatura de dúas frontes de fusión debe ser o suficientemente alta como para permitir que se fusionen con éxito e non afecte á resistencia e ao aspecto dos produtos.
Cando os dous fundidos non poidan fusionarse por completo, produciranse os defectos.
Causas dos defectos:
O molde ten partes máis grosas e delgadas, e a velocidade de fluxo dos fundidos é diferente, cando o fundido flúe pola parte delgada do molde, a temperatura é baixa.
A lonxitude de cada corredor é diferente. Os corredores solitarios serán fáciles de arrefriar.
A presión da cavidade do molde non é suficiente para permitir que a masa fundida se fusione completamente durante a fase de mantemento da presión.
As burbullas restantes fan que a fronte de fusión non poida fundirse, o que tamén provocará a queima.
Ardente
A queima é semellante á do tiro curto, pero con bordos esvaídos irregulares e un leve cheiro a queimado. As áreas negras de carbón aparecerán no produto, cando a condición sexa grave, acompañadas do cheiro a queimado de plástico.
Se non se eliminan os defectos, moitas veces hai deposición negra no molde. Se non se verifican inmediatamente as substancias gaseosas ou petrolíferas producidas pola queima, poden bloquear os orificios de aire. A queima atópase xeralmente ao final dos camiños.
Porque:
A queima é producida polo efecto de combustión interna. Cando a presión no aire aumenta bruscamente en moi pouco tempo, a temperatura aumentará e causará queima. Segundo os datos recollidos, o efecto de combustión interna no proceso de moldaxe por inxección pode producir altas temperaturas de ata 600 graos.
Pódese producir queimaduras cando:
A velocidade de recheo do molde é rápida para que o aire non se poida expulsar da cavidade do molde e xera burbullas de aire debido ao bloqueo do plástico entrante e provoca un efecto de combustión interna despois de ser comprimido.
Os orificios de aire están bloqueados ou a ventilación non é suave.
O aire no molde debe ser eliminado dos orificios de aire. Se a ventilación se ve afectada pola posición, número, tamaño ou funcións, o aire quedará no molde e provocará queima. A gran forza de suxeición do molde tamén levará a unha mala ventilación.
Encollemento
O encollemento refírese aos lixeiros ocos na superficie dos produtos.
Cando os defectos son leves, a superficie dos produtos é irregular. Cando sexa grave, a gran área de produtos colapsará. Os produtos con arcos, asas e protuberancias adoitan sufrir defectos de contracción.
Porque:
A contracción é causada pola contracción de gran superficie das materias primas durante o arrefriamento.
Na zona grosa dos produtos (como o arco), o núcleo temperado do material é baixo, polo que a contracción producirase máis tarde que a da superficie, o que producirá unha forza de contracción dentro da materia prima e tirará o lado exterior cara á depresión interior. para producir a contracción.
As contraccións ocorren nas seguintes situacións:
A presión na cavidade do molde é menor que a forza xerada pola contracción da materia prima no proceso de arrefriamento.
Tempo de presurización insuficiente da cavidade do molde durante o proceso de arrefriamento, o que fai que a materia prima saia da cavidade desde a porta.
A materia prima non ten suficiente capacidade de amortiguación durante a fase de moldeo e mantemento da presión xa que o parafuso está completamente retirado antes de que se inxecte o exceso de materia prima.
As áreas de sección transversal das portas e corredores son moito máis pequenas que o grosor dos produtos, o que significa que as portas xa están conxeladas antes do proceso de extrusión dos produtos.
Bubbles
As burbullas de baleiro preséntase en forma de burbullas de aire, que se poden atopar facilmente nos produtos transparentes. Tamén se pode ver na sección transversal dos produtos opacos.
Porque:
As burbullas de aire son a parte do baleiro dos produtos, que se producen cando a materia prima se encolle durante o proceso de arrefriamento.
Do mesmo xeito que a contracción, o interior da materia prima produce a forza contráctil. A diferenza é que o aspecto exterior dos produtos solidificouse cando se forman as burbullas e non hai colapso, polo que xéranse burbullas ocas.
As causas das burbullas son as mesmas que as da redución, incluíndo:
Presión ineficiente da cavidade do molde
Tempo de presurización da cavidade insuficiente
O tamaño do corredor e da porta son demasiado pequenos
Marcas de pulverización
As marcas de pulverización refírense á zona roscada oposta á porta. As marcas de pulverización non só afectan o aspecto dos produtos, senón que tamén afectan a forza dos produtos.
Porque:
As marcas de pulverización son causadas polo fluxo de fusión fóra de control durante o proceso de recheo do molde.
O plástico fundido entra no molde baixo a enorme presión. Se a velocidade de recheo do molde é demasiado alta, o plástico expulsarase do oco aberto da cavidade do molde, e volverá rapidamente e arrefriarase. Nese momento fórmanse os fíos, que bloquean o plástico fundido que entra nas portas.
A principal causa das marcas de pulverización é a posición incorrecta das portas ou o deseño da porta. As dúas situacións seguintes empeorarán a situación de defectos:
Alta velocidade de recheo de moldes
Fluxo de fusión deficiente durante o recheo do molde