注塑模具制造
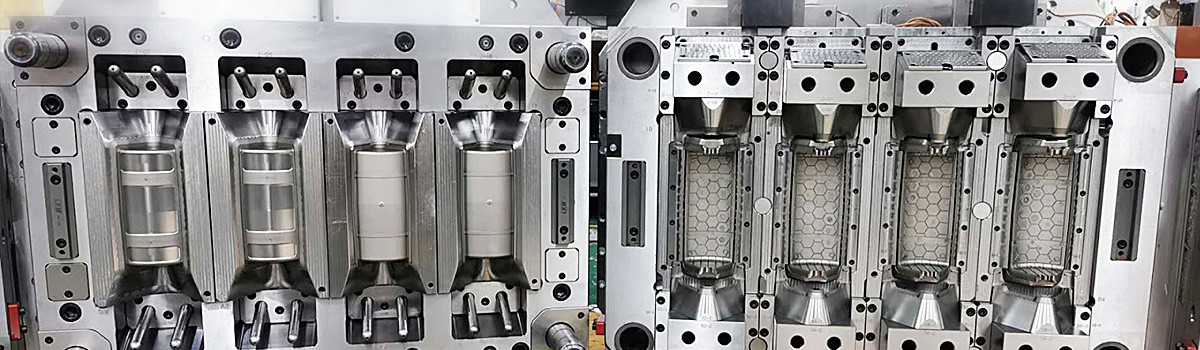
塑料是一种常用于各种行业产品的材料。 玩具、汽车零部件、医疗设备、工具等都是由塑料制成的。 我们在日常生活中遇到的许多塑料制品都是通过将熔化的树脂加工成特定设计,并采用称为注塑成型的制造工艺生产出来的。 这种高效的工艺可以制造多种尺寸和形状的零件,并且可以使用同一模具多次复制同一零件。 这个过程的核心是模具,也称为工具。 高质量的模具制造工艺对于生产优质零件同时保持成本效益至关重要。 投资于高质量模具制造时,零件质量会提高,总体项目成本会降低。
注塑工艺步骤
注塑成型是用于生产塑料制品的最常见制造工艺之一。 这是一个高要求的过程,可以将相同的零件复制数千次。 该过程从包含零件数字副本的计算机辅助设计 (CAD) 文件开始。 然后将 CAD 文件用作一组指令,以帮助模具制造过程。 模具或工具通常由两块金属制成。 零件形状的型腔被切入模具的每一侧。 这种模具通常由铝、钢或合金制成。
模具制作完成后,下一步就是选择合适的塑料材料。 材料选择将取决于最终零件的使用方式。 塑料材料有多种特性需要考虑。 这包括所有外观和感觉,以及耐化学性、耐热性和耐磨性。 与 DJmolding 的专家交谈,了解更多关于可用于注塑成型的塑料材料的信息。
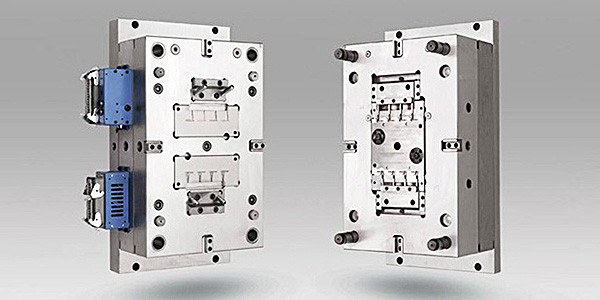
选定的材料最初是塑料颗粒,被送入注塑机的料斗中。 颗粒穿过加热室,在那里它们被熔化、压缩,然后注入模具腔体。 零件冷却后,模具的两半打开以弹出零件。 然后机器重置以再次开始该过程。
制作模具用什么材料?
模具生产是用钢、铝或合金完成的。 DJmolding采用优质钢材进行模具制造。 钢制模具的生产比使用铝或合金的成本稍高。 较高的成本通常被钢模具更长的使用寿命所抵消。 铝制模具虽然生产成本较低,但使用寿命不如钢制模具长,必须经常更换。 钢模具通常可以使用十万次以上。 铝模具需要更频繁地更换。 钢模具生产可以产生铝无法实现的高度复杂的设计。 钢模也可以通过焊接进行修复或改造。 如果模具损坏或为了适应变化,则需要从头开始加工铝模具。 高质量的钢模具可以使用几千、几十万,有时高达一百万个循环。
注塑模具组件
大多数注塑模具由两部分组成——A 面和 B 面,或型腔和型芯。 型腔一侧通常是最好的一侧,而另一半,即型芯,将有一些视觉上的缺陷,因为顶针会将成品零件推出模具。 注塑模具还包括支撑板、顶出箱、顶出杆、顶出销、顶出板、浇口衬套和定位环。
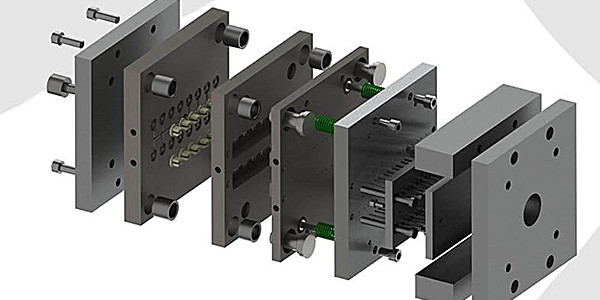
注塑成型是一种制造过程,有很多移动部件。 以下是描述模具生产和注塑成型所需的许多零件的术语列表。 该工具由框架内的几块钢板组成。 模具框架被放入注塑机中并用夹具固定到位。 从侧面看,注塑模具的切面类似于具有许多不同层的三明治。 查看我们的注塑成型术语表以获取完整的术语列表。
模架或模架: 将模具部件固定在一起的一系列钢板,包括型腔、型芯、流道系统、冷却系统和顶出系统。
一个碟子: 金属模具的二分之一。 该板不含移动部件。 可以包含型腔或型芯。
B板: 金属模具的另一半。 该板包含移动部件或空间,以允许移动部件与成品部件(通常是顶针)相互作用。
支撑板: 模具框架内的钢板在成型过程中提供稳定性。
弹射盒: 包含用于将成品零件推出模具的顶出系统。
喷射板: 包含顶杆的钢板。 顶出板移动,将成型后的成品顶出。
顶杆: 顶板的一部分。 顶杆连接到顶杆。
顶针: 接触成品零件并将其推出模具的钢销。 一些注塑制品上可以看到顶针标记,通常是零件背面的圆形印记。
浇道衬套: 模具和注塑机之间的连接件,熔融树脂将进入型腔。
浇道: 模具框架上熔融树脂进入模腔的位置。
定位环: 确保注塑机喷嘴与浇道衬套正确连接的金属环。
型腔或模腔: 模具中的凹痕,通常形成成型零件的外表面。 根据凹陷的数量,模具被指定为单腔或多腔。
核心: 模具中的凸压痕,通常形成成型零件的内表面。 这是模具的凸起部分。 它是空腔的反面。 熔融树脂总是被推入型腔,充满空间。 熔融树脂将在凸起的芯周围形成。
流道或流道系统: 金属模具内的通道允许熔融树脂从浇道流向型腔或型腔到型腔。
门: 熔化树脂进入模腔的流道末端。 不同的应用有不同的门设计。 常用的浇口类型包括销式、辐条式、扇形、边缘式、圆盘式、扇形、隧道式、香蕉式或腰果式以及凿式。 在开始模具制造过程之前,浇口设计和放置是重要的考虑因素。
冷却系统: 模具外壳中的一系列通道。 这些通道循环流体以帮助冷却过程。 冷却不当的零件可能会出现各种表面或结构缺陷。 冷却过程通常占注塑成型周期的大部分。 减少冷却时间可以显着提高模具效率并降低成本。 Fathom 为许多注塑成型应用提供随形冷却,可将模具效率提高高达 60%
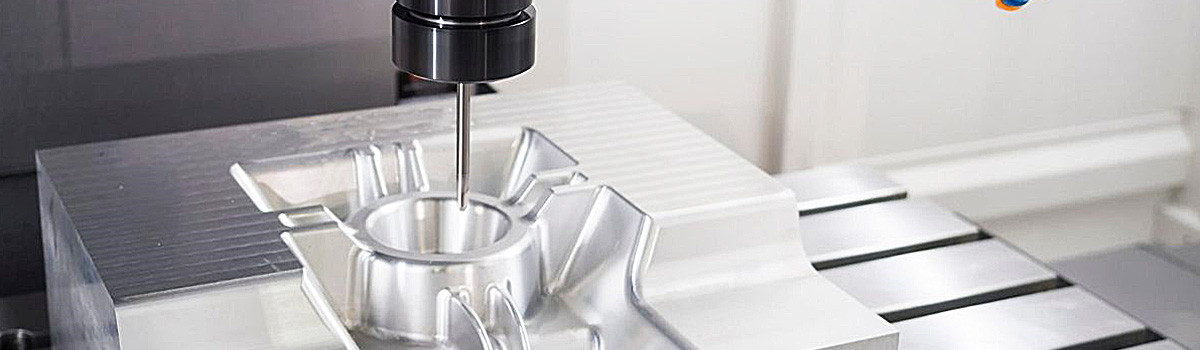
不同成型工艺的DJmolding模具制造
可以调整塑料注射成型工艺以适应不同和复杂的需求。 虽然它是制造大量简单塑料零件的理想选择,但它也可用于制造具有复杂几何形状或组件的极其复杂的零件。
多型腔或系列模具 – 该模具在单个模具框架中有多个型腔,在每个注射周期中生产多个相同或相关的零件。 这是增加运行量和降低单件价格的理想方式。
二次注塑成型 – 这种注塑成型方法用于制造由两种不同类型的塑料制成的零件。 一个很好的例子就是带有坚硬外壳和柔软橡胶手柄的便携式钻体或游戏控制器。 将先前成型的零件重新插入特制模具中。 关闭模具,在原始零件上添加第二层不同的塑料。 当需要两种不同的纹理时,这是一个理想的过程。
插入成型 – 允许将金属、陶瓷或塑料件结合到最终部件中的注塑成型工艺。 将金属或陶瓷部件放入模具中,然后将熔化的塑料注入模具中,以创建由两种不同材料制成的无缝部件。 嵌件成型是汽车应用的理想选择,因为它是一种减轻重量和减少金属等昂贵材料的创新方法。 不是用金属制造整个部件,只有连接件需要是金属,而物品的其余部分将由塑料制成。
共注塑成型 – 两种不同的聚合物依次或同时注入型腔。 此过程可用于制造具有一种塑料表皮和另一种塑料芯的零件。
薄壁成型 – 一种注塑成型形式,专注于更短的周期时间和更高的生产率,以生产薄、轻、廉价的塑料零件。
橡胶射出 – 使用类似于塑料注射成型的工艺将橡胶注射到模具中。 橡胶零件需要更大的压力才能成功注塑成型。
陶瓷射出 – 使用陶瓷材料的注塑成型工艺。 陶瓷是一种天然坚硬的化学惰性材料,可用于多种行业。 陶瓷注射需要几个额外的步骤; 包括烧结或固化新成型的零件,以确保特性的耐用性。
低压注塑成型 – 在较低压力下生产的塑料部件。 这对于需要封装精密部件(例如电子产品)的工作特别有用。
有关塑料注射成型的更多信息,请联系 DJmolding。 我们的专家团队可以协助您完成塑料注塑成型项目。