印度案例
DJmolidng 为印度公司提供注塑服务的嵌件模具
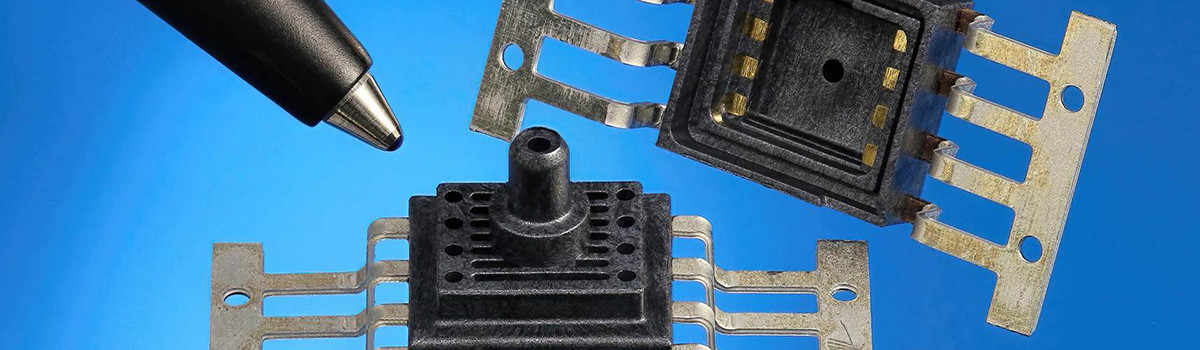
嵌件模具一般是将螺母、金属件或硬质塑料件固定在型腔内进行注塑成型的模具。
DJmolding 为印度市场提供嵌件注塑成型服务,我们为不同行业生产大量嵌件注塑塑料零件,尤其是家电制造商。 一些印度家电厂商长期从DJmolding采购嵌件成型的塑料件。 我们与这些印度公司有着很好的合作关系。
嵌入螺母注塑成型:螺母材料可以是不锈钢、铜、青铜和钢,一般常用铜螺母。 铜易于滚花,有助于螺母和塑料更好地拼接。 螺母内孔的公差应控制在0.02mm以内,否则超过0.02mm容易造成飞边。 在模具装配中,需要将螺母装配到插销中进行测试。 如果螺母和销之间的配合太紧,则很难顶出零件并导致顶出痕迹或粘附问题。 如果它松了,它会导致飞边。
嵌件金属件注塑成型:
金属零件可以是不锈钢、铝、铜、钢……等。 五金件的公差应控制在0.02mm以内,否则封料困难,易产生飞边。 金属件的面积不能设计的太大。
如果金属件的填充面积太大,则由于金属件之间的温差大,很难实现完全注射。 金属零件的位置通常设计在型腔内,因为型腔不会移动,这有助于避免金属零件在移动中松动而产生飞边(严重时可能会损坏模具)。 在特殊情况下,金属部件的位置只能设计在产品的核心或侧面。
嵌件硬塑注塑成型:
通常选用熔点高的硬质塑料,如PEEK、PA66+30GF、PP+30GF、PA12+30GF、PPS……等。 这些硬塑料的公差应该是准确的。 密封区不能有缩孔、凹陷、变形等缺陷。 合模时,应将硬塑料放入模具内进行试验,并在密封处预压0.05-0.1mm,以达到更好的密封效果。
硬塑件的面积不宜设计过大,会造成温差,使射出时难以充料。 通常将硬塑件固定在型腔的一侧,因为型腔是不动的,避免模具移动时出现飞边甚至损坏模具。 在特殊情况下,金属部件的位置只能设计在产品的核心或侧面。
设计要点
1.对于带螺母嵌件的产品设计收缩,而对于金属件和硬塑料嵌件的产品不需要设计收缩。 对于需要严格公差的区域,将产品的尺寸公差修改为中位数。
2.模具设计一般采用带标准针点浇口的模架,二次注射时尽量将镶件放入型腔内。 在使嵌件固定在型腔内的条件下,考虑如何使注塑成型后的零件留在型芯内,这样才能将零件顶出。 通常在型腔中加入弹性块和弹性胶,使零件留在型芯中。 弹性块与胶水的距离不能太大,否则弹力会使硬塑料或金属件变形。 距离一般设计在2mm以内,当金属或硬塑料嵌件面积较大时,适当增加弹性块和弹性胶的用量。
3.材料厚度最好在1.3-1.8mm之间(1.5mm左右最好),如果不是,需要通过产品图纸检查,建议客户修改。 料厚小于1.3mm,补料困难,料厚大于1.8mm,生产中容易缩孔。
4.浇注在模具中非常重要。 浇口点充料平衡要充分考虑。当物料运行到金属或硬塑料件固定区域时,由于嵌件阻力和温差,充料速度和压力会降低。
5.对于模具顶出系统,必须考虑顶出的平衡,否则顶出后会发生变形。 对于不能平衡顶出的零件,在结构设计上需要考虑倒塌来改善平衡问题。
6.为了保证注塑成型后零件的外观合格,顶出装置必须是嵌有ABS或PMMA的硬塑料块。 如果包模有滑道密封,尽量在型腔内设计滑道,因为滑道在型腔中便于合模。
7.为了保证封口SA(seam allowance)的强度,对于二次注塑成型的产品,封口SA的宽度至少要有0.8mm。 二次注塑材料为硬质塑料,封口SA宽度至少1.0mm,否则需建议客户修改产品。
8.在模具设计中,要考虑到注塑机的生产,看是用什么型号的机器,是立式的还是卧式的。 建议不要设计太多的型腔,尤其是冷流道模具,因为型腔太多会使流道变长,浪费材料,也不利于实现高效注射。 配合注塑机,必须考虑产品的排列是否紧凑合理。产品必须能够固定,以保证产品每次入模时都处于相同的状态。 另一种方法是设计反应系统,如果零件在合模前未在正确位置时发出警报,这有助于停止合模。 这样,零件在模具中处于相同的状态,从而提高了注塑的合格率和生产效率。
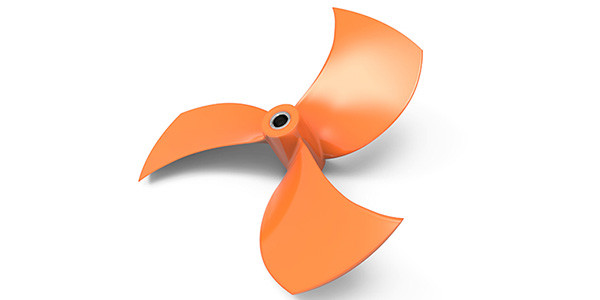
9. 模具注射区在注射时承受较大压力,必须设计钢支撑(形状和尺寸应比零件大5-10mm)。 Over-molding 区域周围的零件之间不得留有间隙,否则零件在二次注塑后会变形。 对于没有 SA(seam allowance)的零件,这方面需要更加注意。
10.容易漏气 注塑成型时容易漏气,所以在模具设计中必须充分考虑排气。 在长距离水线的所有死角和位置,必须在硬塑料部分设计排气孔,因为死角处的材料更难填充。
11.为了保证注入的材料和合格的推力完全充满,一种方法是在零件的拐角处设计一个底切,以增强粘合效果,然后使零件粘合更紧密。
12.在封口区和分型线区,不要从型腔和型芯上脱模,因为模具中的合模线和脱模斜度会造成合模飞边。 尝试通过 LISS-OFF 脱模。
嵌件模具的浇口点类型
嵌件模具的浇口点可设计成直接热浇口阀式浇口、热浇口针式浇口、针点浇口、分浇口、边缘浇口等。
热浇道阀式浇口:流动性好,选位灵活,浇口点小。 适用于大批量生产和厚壁产品。 可以帮助节省材料,浇口不浪费材料,交货期短,质量高。 唯一的缺陷是轻微的浇口痕迹。
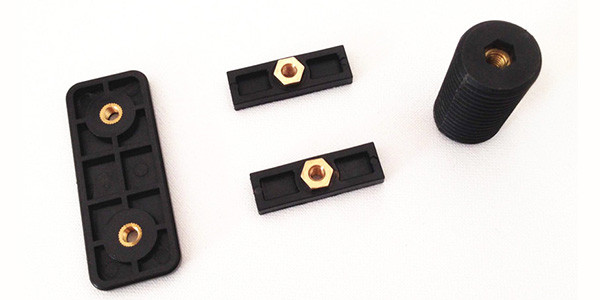
热浇道销浇口: 流动性好,选仓灵活,关口小。 适用于大批量生产和厚壁产品。 可以帮助节省材料,浇口不浪费材料,交货期短,质量高。 但存在缺陷,如浇口点周围有0.1mm的材料残留,容易产生毛刺。 需要制作凹槽以覆盖浇口点周围留下的材料。
针点门: 选仓灵活,流动性弱,跑垒距离长,关口小。 适合小批量生产。 浇口点周围有更多废料。 生产中需要机械手夹住浇口点。 交货时间长。 缺陷是浇口点周围有0.1-0.2mm的材料残留,需要开槽覆盖浇口点周围残留的材料。
副门: 可以设计在型腔、型芯、侧壁和顶针的肋条上。 可灵活选择浇口点,浇口自动与制件分离,浇口痕迹轻微。 缺陷:浇口点附近容易拉料,浇口位置容易产生干痕,需要用手擦料,浇口点压模模腔压力损失大。
边门: 熔融塑料流过浇口,横向均匀分配,减少应力; 减少空气进入型腔的可能性,避免产生条纹和气泡。 缺陷:浇口不能自动与零件分离,在零件边缘留下浇道痕迹,需要工具将浇口加工平整。 边浇口有利于比例注射和保压,也有利于保压和补料,这样有利于改善气纹、流痕等。
嵌件模具加工及装配
1.加工前,制定模具的加工工艺。 选用高精度加工机、高速机、慢进给数控线切割机、镜面EDM(电火花加工)机等。
2.设计预压位置留0.05-0.1mm。
3、模架加工注意精度要求,拿到模架后检查公差,公差不合格不得使用。
4.将螺母、五金件、硬塑件放入模具内进行合模。 如果发现合模有问题,要通过螺母、金属件、硬塑料件和模具检查,看看是哪一个不对。 尽量按图加工零件,有利于日后追溯数据。
5.不能使用磨床进行合模。 求助于机器来纠正模具装配不好的地方。
6.试用前做好动作测试,避免漏装、错装。 错误的装配会导致模架损坏。
嵌件模具模具测试
1、试模时,要清楚开模、合模、出模的顺序。 了解金属件和硬塑料件的结构特点和性能。
2.清楚客户需要的样品数量,准备足够的螺母,金属件和硬塑料,因为在模具测试中需要很多样品。
3.注意是否可以在没有插入螺母,金属零件或硬塑料的情况下测试模具。 如果嵌入螺母、金属零件和硬塑料没有在模具中组装,零件可能会出现粘模或短射等缺陷。
4. 很多时候需要调整模具上的水线板,但有些嵌件模具根据结构有时无法调整水线板,甚至严重卡死需要修改,或者模具在加工过程中损坏开幕。
5.试模可能会出现问题,如短射、空行程、飞边、粘模等。 如果问题可以在注塑机上验证,最好解决它。
DJmolding拥有超过10年以上的嵌件成型经验,如有任何疑问,请联系我们。