嵌件注塑成型
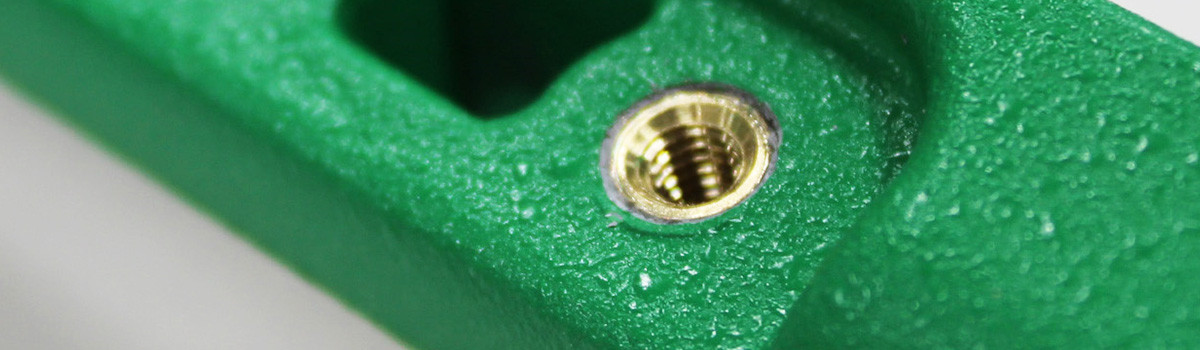
嵌件注塑成型是一种广泛使用的制造工艺,用于生产具有嵌入式组件的复杂塑料零件。 该技术涉及在注塑过程之前将金属或塑料部件插入模具型腔。 然后,熔融材料围绕插入的元件流动,在两种材料之间形成牢固的结合。 嵌件注塑成型具有多项优势,包括提高设计灵活性、缩短装配时间和增强零件功能。 这份综合指南将探讨嵌件注塑成型的不同技术、优势和应用。
什么是嵌件注塑成型?
注塑成型是一种用于制造各种零件和产品的制造工艺。 插入注射成型是一种注射成型,允许在成型过程开始之前将预制元件或插入物插入模具中。 这种技术允许创建需要传统注塑方法无法实现的特定功能的零件。
嵌件注塑成型的工作原理是在成型过程开始之前将预成型的嵌件放入模具型腔中。 插入件可以包含各种材料,包括金属、塑料和陶瓷。 成型过程照常开始,将熔融塑料注入模具型腔。 当塑料冷却并凝固时,它会与嵌件融合,形成一个完整的部件。
使用嵌件注塑成型有几个优点。 这种技术的主要优点之一是它允许创建具有传统注塑方法无法实现的特定功能的零件。 例如,如果功能需要螺纹嵌件或金属部件进行加固,则可以使用嵌件注塑成型。 该技术还允许使用材料组合创建零件,例如带有金属嵌件的塑料零件。
嵌件注塑成型的另一个优点是节省时间和金钱。 插入注塑成型不是组装多个组件,而是创建一个集成件。 通过这样做,公司可以减少组装所需的时间和成本。
插入注射成型也有助于制造复杂的零件。 由于嵌件可以在成型过程开始之前放置在模腔中,因此可以生产具有复杂几何形状和特征的零件,而这些零件很难通过传统的注塑成型方法实现。
嵌件注塑成型如何工作?
这是一种注射成型工艺,允许在成型工艺开始之前将预成型零件或嵌件插入模具中。 这种技术允许创建具有传统注塑方法无法实现的特定功能的零件,并且对于创建复杂零件特别有用。 在这里我们将讨论如何插入注塑件。
嵌件注塑工艺包括以下步骤:
- 插入位置:嵌件注塑成型工艺的第一步是将预制嵌件放入模腔中。 制造商可以用各种材料生产这种嵌件,例如金属、塑料或陶瓷。
- 合模:一旦插入件就位,模具就会关闭并夹紧。 目标是在成型过程中将嵌件保持在适当位置。
- 熔融塑料注射:注射成型工艺将熔融塑料注入模具型腔。 制造商通常将塑料加热到 200 到 300 摄氏度之间的温度,具体取决于所使用的特定塑料。
- 冷却凝固: 当塑料冷却并凝固时,它会与嵌件融合,形成一个完整的部件。 冷却和凝固时间取决于所使用的特定塑料和生产零件的复杂性。
- 开模和顶出: 一旦零件冷却并凝固,操作员打开模具并弹出物品。 然后可以完成该作品并准备使用。
使用嵌件注塑成型有几个优点。 其中一些优势包括:
- 能够创建具有传统注塑方法无法实现的特定功能的零件
- 可以将元件制成单个集成件,从而减少装配时间和成本
- 能够创建具有复杂几何形状和特征的复杂零件
- 能够使用各种材料,包括金属、塑料和陶瓷
- 注塑成型是一种高效且可重复的工艺,可以生产大量高精度和准确度的零件。
注塑成型中使用的嵌件类型
制造商可以使用各种材料(包括金属、塑料和陶瓷)来制作嵌件。 这些嵌件能够制造出具有传统注塑成型方法无法实现的特定特征的零件。 在这里,我们将讨论注塑成型中使用的不同类型的嵌件。
- 金属嵌件:金属嵌件通常用于注塑成型,为塑料部件提供额外的强度和稳定性。 它们通常由黄铜、钢或铝制成,可以是螺纹或非螺纹的,具体取决于应用。 制造商可以使用金属嵌件来制造具有复杂几何形状和需要高强度和耐用性的因素的零件。
- 塑料嵌件: 塑料嵌件通常用于注塑成型,以支撑和加固塑料部件。 它们通常由尼龙、ABS 或聚碳酸酯材料制成,可以制作具有特定功能的部件,例如卡扣连接或螺纹孔。 制造商重视塑料嵌件,因为它们能够提供重量轻、成本效益高的解决方案,并且可以轻松模塑成各种形状和尺寸。
- 陶瓷嵌件: 陶瓷嵌件用于注塑成型,以制造需要高强度和耐磨性的零件。 它们通常由氧化锆或氧化铝等材料制成,可用于生产汽车、航空航天和医疗行业的零件。 陶瓷嵌件高度耐高温、耐腐蚀和耐磨损,使其成为恶劣环境的理想选择。
- 复合嵌件: 制造商将两种或多种材料(例如金属和塑料)组合在一起,然后将它们模塑成复合嵌件,从而形成一个完整的零件。 制造商可以利用混合嵌件开发具有传统注塑方法无法实现的特定功能的零件。 此外,他们可以高度定制这些插件以满足特定应用的独特需求。
- 包覆成型嵌件: 在注塑成型过程中,制造商将嵌件模塑到塑料部件中,从而产生所谓的包覆成型嵌件。 这个过程涉及在插入件周围开发塑料的第一枪,然后在第一枪上设置第二枪以创建一个单一的集成部件。 制造商经常使用包覆成型嵌件来制造组合材料的零件,例如将金属嵌件结合到塑料部件中。
金属嵌件与塑料嵌件
该过程涉及在塑料注射成型过程开始之前将预成型零件或嵌件放入模具中。 制造商可以用各种材料制造嵌件,包括金属和塑料,每种材料都有其独特的优点和缺点。 本文将比较金属和塑料嵌件,并帮助您确定适合您应用的最佳选择。
金属嵌件
制造商通常在成型中使用金属嵌件,因为它们具有高强度和耐用性。 它们通常由黄铜、钢或铝制成,可以是螺纹或非螺纹的,具体取决于应用。 金属嵌件通常用于注塑成型,为塑料部件提供额外的强度和稳定性。
金属嵌件的优点
- 高强度和耐用性
- 耐磨损
- 它可以通过线程提供额外的功能
- 非常适合具有高应力或承重要求的零件
金属嵌件的缺点
- 成本高于塑料嵌件
- 比塑料嵌件更难成型
- 重,这在特定应用中可能是一个问题
塑料嵌件
塑料嵌件因其多功能性和成本效益而在成型中很受欢迎。 制造商通常使用尼龙、ABS 或聚碳酸酯等材料制造它们,并且可以轻松地将它们模塑成各种形状和尺寸。 塑料嵌件重量轻,可以制造具有特定特征的零件,例如卡扣连接或螺纹孔。
塑料嵌件的优点
- 物超所值
- 轻量化设计,方便挪动
- 轻松塑造成各种形状和尺寸
- 非常适合具有较低应力或承载要求的零件
塑料嵌件的缺点
- 不如金属嵌件耐用
- 不适用于具有高应力或承重要求的零件
- 随着时间的推移,它可能更容易磨损
何时选择金属嵌件
金属嵌件在需要高强度和耐用性的零件中表现出色,因为它们耐磨损并提供附加的螺纹功能。 金属嵌件也是具有高应力或承重要求的功能的理想选择。 但是,它们比塑料嵌件更昂贵,并且可能更难成型。
可能需要金属嵌件的应用包括
- 汽车和航空航天部件
- 医疗器械
- 工业设备
- 消费类电子产品
何时选择塑料嵌件
塑料嵌件具有成本效益,适用于应力或承载要求较低的零件。 它们表现出轻巧的特性; 制造商可以将它们塑造成各种形状和尺寸。 塑料嵌件也适用于需要特殊功能的位置,例如卡扣连接或螺纹孔。 但是,它们可能需要更适合具有高应力或承重要求的细节。
包括可能需要塑料嵌件的应用
- 消费品
- 家用设备
- 玩具和游戏
- 电子
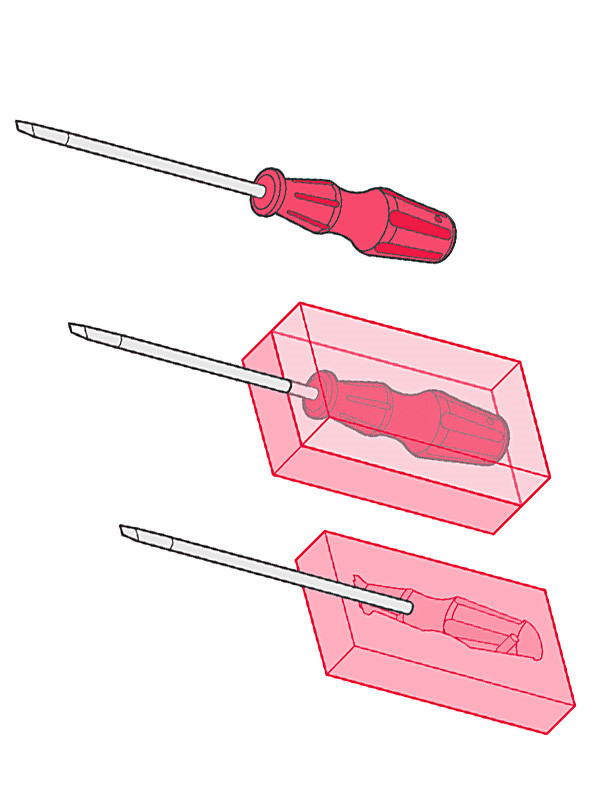
嵌件注塑成型的好处
嵌件注塑成型是一种流行的制造工艺,涉及在塑料注塑工艺开始之前将预成型零件或嵌件放入模具中。 与传统成型方法相比,该技术具有众多优势,使其成为各种应用的热门选择。 本文将讨论嵌件注塑成型的一些主要优点。
- 高性价比: 嵌件注塑成型是一种经济高效的制造解决方案,因为它消除了对单独零件进行模塑后组装的需要。 通过在成型过程中集成嵌件,制造商可以减少劳动力和组装成本,同时提高生产效率。
- 提高零件强度: 嵌件注塑成型可以通过在零件的不同区域使用不同的材料来增强零件的强度和耐用性。 此功能对于需要细节以承受高压力或承重要求的应用特别有益。
- 提高设计灵活性: 嵌件注塑成型提供了更大的设计灵活性,因为它可以制造具有多种特性和功能的复杂零件。 该工艺非常适合复杂的设计和几何形状,使其成为此类细节的理想选择。
- 一致性和准确性: 嵌件注塑成型在零件生产中提供了出色的一致性和准确性。 我们将预制嵌件精确定位到模具中,确保它们根据每个零件的要求准确放置。 因此,我们在生产的零件中实现了统一的尺寸和卓越的质量控制。
- 缩短周期时间: 嵌件注塑成型可以通过将多个步骤组合到一个过程中来缩短周期时间。 这种方法可以节省时间并提高生产率,尤其是在处理大批量生产运行时。
- 各种材料: 嵌件注射成型可用于各种材料,包括塑料、金属和陶瓷。 制造商现在可以通过考虑强度、耐用性和成本来为任何应用选择最合适的材料。
- 环境效益: 嵌件注塑成型还可以通过减少浪费和尽量减少材料的使用来提供环境效益。 因为我们将嵌件精确地放入模具中,所以与传统成型方法相比,我们的材料浪费更少。 实施这一点可以减少对环境的影响并减少制造费用。
嵌件成型的设计注意事项
嵌件成型是一种流行的制造工艺,涉及将预制嵌件集成到塑料注射成型工艺中。 这种技术有很多好处,包括提高零件强度、降低装配成本和提高设计灵活性。 然而,设计用于嵌件成型的零件需要仔细考虑多个因素,以确保成功和高效的生产。 本文将讨论嵌件成型的一些关键设计考虑因素。
- 插入位置: 嵌件在模具内的放置对于嵌件成型工艺的成功至关重要。 嵌件必须精确定位在模具内,以确保塑料材料在成型过程中将其完全封装。 设计师还必须确保嵌件不会干扰塑料材料的流动或导致任何分型线问题。
- 材料兼容性: 嵌件和塑料材料的材料选择对于嵌件成型工艺的成功至关重要。 材料必须相容,以防止出现粘合问题或材料不相容。 设计人员必须仔细考虑材料特性,例如熔点、收缩率和热膨胀系数,以确保嵌件成型成功。
- 零件几何: 零件的几何形状是嵌件成型的另一个重要考虑因素。 该设计必须允许在插入件周围正确填充和包装塑料材料,以确保完全封装。 零件的几何形状还必须允许充分的通风和冷却,以防止出现任何翘曲、收缩或缩痕问题。
- 拔模角度和底切: 拔模角度和底切的存在会影响零件在嵌件成型中的成型性。 设计人员必须仔细考虑拔模角和底切的位置和几何形状,以确保他们可以轻松地从模具中取出镶件,而不会对零件或模具造成任何损坏。
- 工具注意事项: 嵌件成型所需的工具可能比传统成型方法更复杂。 设计师必须仔细考虑模具设计,包括嵌件的放置和几何形状、浇口和排气以及任何必要的辅助操作。 此外,工具必须能够保持严格的公差,以确保正确的插入位置并防止出现任何零件质量问题。
用于嵌件注塑成型的材料
嵌件注塑成型是一种高度专业化的工艺,可以精确、一致地生产复杂零件。 此过程涉及使用称为嵌件的预制特征,在注塑成型发生之前将其插入模具中。 这些嵌件可以由各种材料制成,每种材料都具有独特的特性和优势。 在这里,我们将讨论嵌件注塑成型中最常用的材料及其优势。
金属制品
注塑成型广泛使用由钢、铝和黄铜等金属制成的嵌件。 这些材料具有出色的强度和耐用性,非常适合用于需要高耐磨性和抗撕裂性的部件。 此外,金属嵌件可以承受高温,使其适用于要求苛刻的应用,例如航空航天和汽车工业。 在注塑成型中使用金属嵌件的一些具体优势包括:
- 高强度和耐用性
- 优异的耐热性
- 耐腐蚀性能
- 承受高压和压力的能力
塑料
塑料嵌件也常用于注塑成型,PEEK、PTFE 和 UHMW 等材料是流行的选择。 这些材料具有高度的耐温性、耐化学性和低摩擦特性。 由于这些组件的高精度和清洁度是这些应用中的关键因素,因此非常适合用于医疗设备和半导体制造。 在注塑成型中使用塑料嵌件的一些具体优势包括:
- 高耐化学性
- 优异的耐温性
- 低摩擦性能
- 易于加工和成型
陶瓷
在注塑成型中,陶瓷嵌件因其高强度、硬度和耐磨性而得到使用。 这些材料非常适合用于零件需要承受高温或恶劣环境的应用。 此外,陶瓷刀片具有出色的尺寸稳定性,使其适用于精密工程应用。 在注塑成型中使用陶瓷嵌件的一些具体优势包括:
- 高强度和硬度
- 极好的耐磨性
- 耐高温
- 尺寸稳定性
复合材料
碳纤维或玻璃纤维等复合材料因其高强度重量比而被用于注塑成型。 航空航天和汽车行业经常在对减轻重量至关重要的地方使用这些材料。 复合嵌件具有高刚度和强度,是风力涡轮机和高性能运动设备应用的理想选择。 在注塑成型中使用复合嵌件的一些具体优势包括:
- 高强度重量比
- 高刚度和强度
- 良好的抗冲击性
- 热膨胀系数低
橡胶
硅胶或氯丁橡胶等橡胶材料因其柔韧性和密封性能而被用于注塑成型。 这些材料通常用于密封和缓冲必不可少的医疗和汽车行业。 橡胶嵌件具有出色的耐化学性和耐高温性,使其成为在恶劣环境中使用的理想选择。 在注塑成型中使用橡胶嵌件的一些具体优势包括:
- 优良的密封性能
- 高度的灵活性
- 耐化学性和耐温性
- 良好的减震性
发泡
聚氨酯或聚苯乙烯等泡沫材料因其重量轻和减震特性而被用于注塑成型。 这些材料通常用于缓冲和抗冲击性至关重要的包装和汽车行业。 泡沫嵌件提供高绝缘性,使其成为对温度敏感的应用的理想选择。 在注塑成型中使用泡沫嵌件的一些具体优势包括:
- 轻巧灵活
- 出色的减震性能
- 良好的绝缘性能
- 它能够塑造成复杂的形状
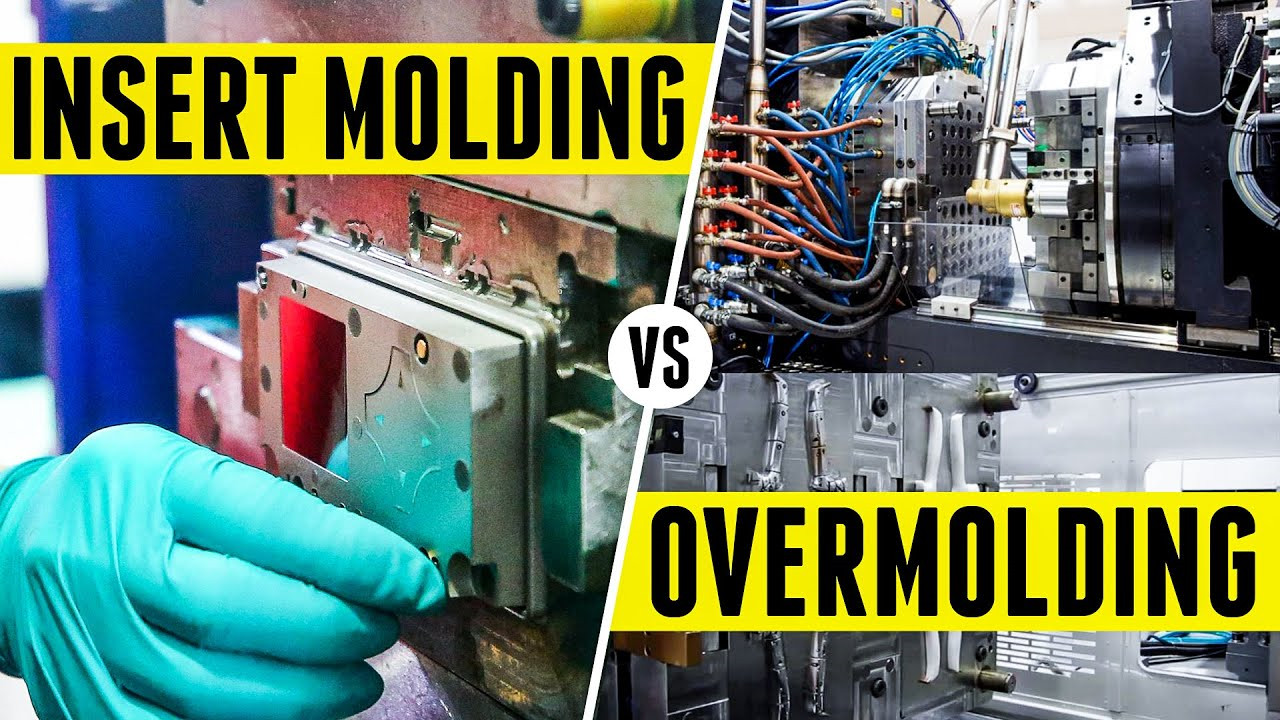
嵌件成型与二次成型:有什么区别?
嵌件成型和包覆成型是注塑成型中涉及多种材料的两种常用工艺。 尽管这些过程看起来相似,但它们有一些根本的区别。 在这里,我们将讨论嵌件成型和包覆成型之间的区别。
插入成型
插入成型是一种过程,涉及在注射成型过程发生之前将预制零件(称为插入件)插入模具中。 然后将塑料材料注入嵌件周围,形成结合了嵌件和塑料材料特性的成品。 该工艺通常用于汽车、医疗和航空航天工业,以制造高精度零件。
嵌件成型的优点
- 精度高
- 提高零件强度和耐用性
- 减少装配时间和成本
- 能够组合具有不同特性的材料
二次注塑成型
包覆成型是一种涉及在预先存在的零件上注射成型第二种材料的过程。 制造商使用此工艺制造触感柔软的手柄、把手和其他消费品。 包覆成型材料通常柔软且类似橡胶,可提供更好的抓地力和舒适度。 根据零件的复杂程度,我们可以在单射或双射工艺中进行包覆成型。
包覆成型的优点
- 改进的人体工程学和美学
- 改进的抓地力和舒适度
- 减少装配时间和成本
- 能够组合具有不同特性的材料
嵌件成型和二次成型的区别
- 嵌件成型涉及插入预制部件,而包覆成型包括在预先存在的部件上注射成型第二种材料。
- 我们利用嵌件成型来制造高精度的零件,同时我们利用包覆成型来增强产品的人体工程学和美感。
- 嵌件成型涉及组合具有不同特性的材料,而包覆成型涉及在包覆成型部分使用柔软的橡胶状材料。
- 嵌件成型通常用于汽车、医疗和航空航天工业,而包覆成型通常用于工具、电子产品和个人护理用品等消费品。
插入放置技术
嵌件成型是在注塑成型过程发生之前将预制零件或嵌件放入模具中的过程。 塑料材料被注射到嵌件周围以形成成品。 放置嵌件对于嵌件成型过程的成功至关重要。 在这里,我们将讨论插入放置的一些技术。
- 手动放置: 在这种技术中,操作员手动将镶件放入模具中。 制造商通常将这种技术用于只需要少量插入件的小型或简单零件。 然而,它可能耗时耗力,并且由于人工放置而存在更高的错误风险。
- 自动放置: 在这种技术中,使用计算机化系统(例如机器人或取放机)将嵌件放入模具中。 这种技术比手动贴装更快、更准确,非常适合大批量生产或复杂零件。 但是,它需要对设备进行初始投资,并且对于小规模生产可能需要更具成本效益。
- 嵌件成型二次成型: 我们将嵌件放入第二个包覆成型零件中,然后将其放入主模具中。 制造商通常将此技术用于具有复杂几何形状或难以到达区域的索赔。 它还可以将具有不同特性的材料组合在一起,例如将刚性塑料插入件与软模制材料相结合。
- 背胶插入物:在这种技术中,我们用粘合剂背衬预涂嵌件,使我们能够将它们放入模具中,而无需手动或自动放置。 粘合剂背衬在注塑成型过程中熔化,将嵌件粘合到塑料材料上。 这种技术通常用于小型、简单的零件,可以减少生产时间和成本。
- 螺纹嵌件: 在这种技术中,螺纹嵌件被放入模具中,用于在成品中创建螺纹。 制造商通常使用这种技术来制造需要插入螺钉或螺栓的产品,例如电子设备或汽车零件。
插入式注塑机的类型
注塑工艺的关键部件之一是注塑机。 这些机器有多种类型,每种都有独特的特点和优势。 在这里,我们将了解不同类型的嵌件注塑机。
首先,让我们定义一下什么是嵌件注塑机。 嵌件注塑机是一种注塑机,可以在注入塑料材料之前将预制部件(例如金属或塑料嵌件)插入模具中。 有了这种能力,就可以制造需要额外特征(例如螺纹开口或金属支撑)的复杂零件。
以下是不同类型的嵌件注塑机:
- 立式注塑机:这些机器采用垂直方向设计,可以垂直安装模具。 它们非常适合嵌件成型,因为它们可以轻松地将嵌件从顶部插入模具中。 这种类型的机器占用的占地面积也较小,更适合较小的生产运行。
- 卧式注塑机:这些机器采用平面定位设计,水平安装模具。 它们最适合更大规模的生产运行,制造商通常使用它们来制造更重要的零件。 对于卧式机器,刀片可以从侧面装载,这使得确保正确对齐变得更具挑战性。
- 转台注塑机:这些机器有一个旋转台,允许安装多个模具并旋转到注射单元中进行生产。 这种类型的机器非常适合嵌件成型,因为它可以将各种嵌件插入模具中,从而制造出更复杂的零件。
- 穿梭式注塑机: 这些机器有一个梭子,可以在注射单元和成型区域之间来回移动模具。 它们最适合小批量生产,是嵌件成型的理想选择,因为它们可以轻松装卸嵌件。
嵌件成型工艺参数
与传统的注塑成型相比,所得产品具有更高的强度和耐用性。 嵌件成型的工艺参数对于实现高质量和一致的结果至关重要。 在这里,我们将了解嵌件成型的工艺参数。
- 材料选择: 材料选择是嵌件成型的重要工艺参数。 塑料材料必须与插入材料和应用兼容。 相容性可确保嵌件和塑料材料粘附良好,从而形成坚固耐用的产品。
- 温度: 温度在嵌件成型过程中起着至关重要的作用。 我们必须正确设置模具温度,以确保塑料材料流动均匀并充满型腔,没有空隙或变形。 我们还必须考虑插入件的温度,以确保塑料材料很好地粘附在插入件上而不会造成热损坏。
- 注射压力: 注射压力是嵌件成型的另一个重要参数。 我们必须正确设置张力,以确保我们将塑料材料均匀快速地注射到模具型腔中。 高注射压力会导致镶件或模具变形,而低注射压力会导致模腔填充不完全。
- 注射速度: 注射速度也是嵌件成型的一个重要参数。 我们必须正确设置速率,以确保塑料材料均匀地填充模具型腔,没有空隙或变形。 高注射速度会导致塑料材料中出现湍流,从而导致成品出现缺陷。
- 冷却时间: 塑料材料凝固并形成最终产品形状所需的冷却时间。 我们必须正确设置冷却时间,以确保我们达到成品所需的形状和尺寸。 较短的冷却时间会导致变形或收缩,而较长的冷却时间会导致较长的循环时间并降低生产率。
- 弹射时间: 我们要求顶出时间将成品从模具中顶出。 我们必须正确设置顶出时间,才能在不造成任何损坏或变形的情况下取出成品。 较短的顶出时间会导致不完全顶出或损坏产品,而较长的顶出时间会导致较长的循环时间并降低生产率。
常见的嵌件成型缺陷以及如何避免它们
嵌件成型是一种流行的制造工艺,它涉及在注入塑料材料之前将预制部件(例如金属或塑料嵌件)放入模具中。 与传统的注塑成型相比,此过程可生产出更结实耐用的产品。 然而,与任何制造工艺一样,嵌件成型可能存在影响最终产品质量和一致性的缺陷。 在这里,我们将仔细研究常见的嵌件成型缺陷以及如何避免它们。
闪光灯: 飞边是当多余的塑料材料从模具中漏出并在成品表面形成薄层时出现的缺陷。 这种缺陷会影响产品的外观和功能。 为避免闪光,您可以采取以下步骤:
- 降低注射压力
- 增加合模力
- 使用脱模剂
- 增加冷却时间
短镜头: 短射是当塑料材料未充满模具型腔时发生的缺陷,导致产品不完整或尺寸过小。 为避免短射,您可以采取以下步骤:
- 提高注射压力
- 提高注射速度
- 提高物料温度
- 提高模具温度
翘曲: 翘曲是成品因冷却不均或收缩不均匀而变形或扭曲的缺陷。 为避免翘曲,您可以采取以下步骤:
- 提高模具温度
- 增加冷却时间
- 增加保压压力
- 使用平衡的冷却系统
缩痕: 缩痕是成品表面因冷却不均或收缩不均匀而产生的凹陷或压痕。 为避免缩痕,您可以采取以下步骤:
- 提高模具温度
- 增加冷却时间
- 增加保压压力
- 使用更厚的壁或加强筋来加强产品
分层: 分层是当塑料材料和插入材料没有正确粘合时发生的缺陷,导致分离或剥落。 为避免分层,您可以采取以下步骤:
- 使用兼容的塑料材料和插入罐材料
- 提高注射压力和速度
- 提高刀片温度
- 提高模具温度
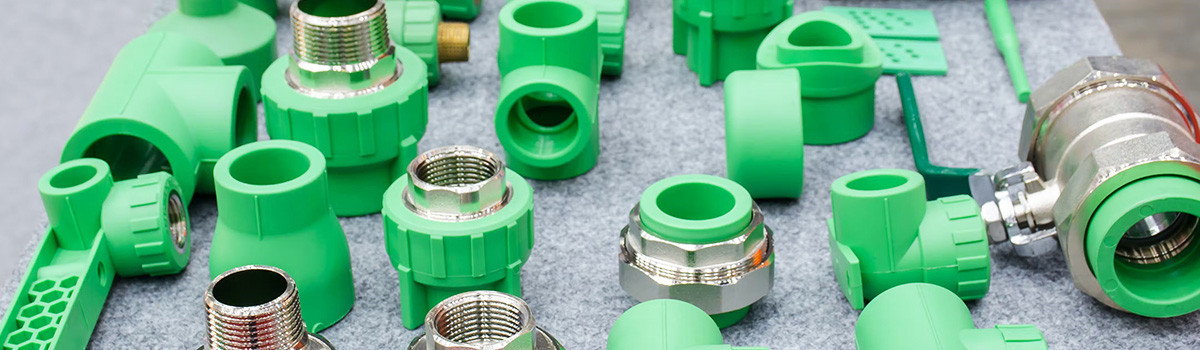
嵌件成型的后成型操作
然而,在完成嵌件成型工艺后,我们必须进行多次成型后操作,以确保最终产品符合所需规格。 在这里,我们将仔细研究嵌件成型的成型后操作。
- 去飞边:去飞边是从成品中去除任何多余材料(例如飞边或毛刺)的过程。 此过程可以手动或自动执行,具体取决于产品的大小和复杂程度。
- 修整:修整是从成品中去除任何多余材料或突出物的过程。 根据产品的形状和尺寸,可以使用各种切割工具或方法执行此过程。
- 清洁: 清洁是从成品中去除任何污垢、碎屑或污染物的过程。 根据嵌件成型工艺中使用的材料类型,可以使用多种清洁剂或方法执行此工艺。
- 大会:组装是将多个组件连接在一起以形成成品的过程。 根据材料的类型和所需的最终产品,可以使用各种方法执行此过程,例如超声波焊接、热冲压或粘合。
- 测试: 测试是确保成品符合所需规格和质量标准的过程。 这个过程可以包括各种测试,例如机械、电气或视觉检查,具体取决于产品类型及其预期用途。
除了这些模制后操作之外,在设计嵌件模制工艺以最大限度地减少模制后工序的需要时,还需要考虑几个因素。 这些包括:
- 为嵌件和模制件选择合适的材料
- 确保插入件在成型过程中正确定位并固定到位
- 调整成型参数,例如温度和压力,以尽量减少缺陷和多余材料
- 使用优质模具和设备,确保成品的一致性和准确性
嵌件注射成型的应用
嵌件注塑成型是一种高度通用的制造工艺,用于许多行业,以生产具有更高强度和耐用性的高质量、复杂零件。 在这里,我们将仔细研究嵌件注塑成型的应用及其对不同行业的好处。
- 汽车行业:汽车行业是嵌件注塑成型最重要的用户之一。 它可用于生产各种部件,包括安全气囊外壳、安全带和发动机部件。 该工艺允许对能够承受汽车使用的恶劣条件的零件进行精确和准确的成型。
- 电子行业:电子行业也严重依赖嵌件注塑成型来生产用于智能手机、笔记本电脑和其他电子设备的组件。 该过程可用于创建电子元件的连接器、开关和外壳等元件。 该过程非常高效,可以快速且经济高效地生产大量零件。
- 医疗行业: 医疗行业也从嵌件注塑成型中受益匪浅。 该工艺可用于生产各种组件,包括手术器械、药物输送装置和医疗植入物。 该方法能够精确成型能够承受医疗使用严酷条件的元件,并允许大批量生产。
- 航天工业: 航空航天业是另一个广泛使用嵌件注塑成型的行业。 该工艺可用于生产飞机部件的风管、支架和外壳等部件。 该工艺允许创建能够承受航空航天使用的高应力和极端温度的高强度部件。
- 消费品行业: 消费品行业广泛使用嵌件注塑成型来生产范围广泛的产品,例如玩具、家用电器和运动器材。 该过程允许创建高质量、耐用、轻便且美观的组件。
除了这些行业之外,嵌件注塑成型还用于许多其他应用,包括:
- 包装行业: 用于生产瓶盖、瓶盖和其他包装部件
- 建造业: 用于生产管道、配件和其他建筑部件
- 军工: 用于生产军用车辆和设备的零件
汽车行业应用
汽车行业是塑料注射成型最重要的用户之一,因为它是制造复杂汽车部件的一种经济高效的方式。 在这里,我们将仔细研究塑料注射成型在汽车行业中的各种应用。
- 内部组件: 汽车的内部由几个对汽车的整体美观和功能至关重要的塑料部件组成。 这些组件包括仪表板、门板、空调通风口和方向盘组件。 注塑成型可以快速、经济地大批量生产这些零件,同时保持高精度。
- 外部组件: 车辆的外部由多个塑料部件组成,包括保险杠罩、前照灯组件和尾灯组件。 注塑成型以高精度生产这些部件,确保它们满足汽车行业要求的严格安全和质量标准。
- 引擎组件: 注塑成型还可用于生产多种发动机部件,包括进气歧管、发动机罩和机油滤清器。 我们必须按照严格的公差和标准制造这些组件,而注塑成型可以生产满足这些要求的高质量成分。
- 电气元件: 车辆中的电气元件,例如连接器、开关和传感器外壳,也是使用注塑成型制造的。 这些组件必须经久耐用并能承受恶劣的操作条件,而注塑成型可以生产出能够承受这些条件的高质量成分。
- 暖通空调组件:注塑成型生产用于车辆 HVAC 系统的多个部件,包括空调管道和通风口。 这些部件必须按照精确的公差制造,以确保车内适当的气流和通风。
除了这些应用之外,制造商还使用注塑成型来生产其他几种汽车部件,包括燃油、制动和悬架系统。
在汽车行业使用注塑成型的好处很多,包括:
- 高效率:注塑成型可以快速大批量生产高质量的部件,从而减少生产时间和成本。
- 精确:注塑成型允许创建具有高精度和一致性的组件,确保它们符合严格的质量标准。
- 定制: 注塑成型允许生产复杂的形状和设计,允许制造商定制组件以满足特定的设计要求。
医疗行业应用
医疗行业是一个精度和可靠性至关重要的领域,这使得塑料注射成型成为生产医疗部件的理想制造工艺。 在这里,我们将仔细研究塑料注射成型在医疗行业中的各种应用。
- 手术器械: 注塑成型生产许多手术器械,包括镊子、夹子和手术刀。 制造商必须按照严格的公差和标准制造这些组件,以确保最高的准确度和精度。
- 医疗设备:制造商还使用注塑成型来生产医疗设备,例如导管和呼吸组件。 为了保证患者的安全和可靠性,制造商必须根据严格的标准制造这些组件。
- 诊断组件: 制造商使用注塑成型生产用于诊断设备的多种组件,例如移液管、注射器和试管。 这些组件必须按照精确的公差制造,以确保准确的测试结果。
- 包装: 注塑成型生产医疗产品的包装,例如无菌托盘、容器和包装组件。 这些组件必须按照严格的标准制造,以确保医疗产品的无菌性和安全性。
- 牙科组件: 注塑成型可生产多种牙科组件,包括护齿器、牙托和正畸部件。 这些部件必须按照精确的公差制造,以确保患者的合适和舒适。
除了这些应用之外,制造商还使用注塑成型来生产其他几种医疗部件,包括假肢、助听器和实验室设备。
在医疗行业使用注塑成型的好处很多,包括:
- 高精准度:注塑成型允许生产具有高精度和一致性的组件,确保它们符合严格的质量标准。
- 定制:注塑成型允许生产复杂的形状和设计,允许制造商定制组件以满足特定的设计要求。
- 性价比高: 注塑成型是一种经济高效的制造工艺,可以大批量生产高质量的部件,从而减少生产时间和成本。
电子行业应用
电子行业是一个高度依赖精密高效制造工艺的领域。 由于其准确性、多功能性和速度,塑料注射成型是生产电子元件的理想工艺。 在这里,我们将详细了解塑料注射成型在电子行业中的各种应用。
- 连接器: 注塑成型生产用于电子行业的各种连接器,包括 USB 连接器、HDMI 连接器和音频插孔。 这些组件必须按照精确的公差制造,以确保正常的功能和兼容性。
- 外壳和外壳: 注塑成型为电子设备生产外壳和外壳,包括手机、笔记本电脑和其他消费电子产品。 制造商必须按照精确的规格制造这些组件,以确保适当的配合和功能。
- 开关: 注塑成型可生产多种用于电子设备的控件,包括翘板开关、按钮开关和滑动开关。 这些组件必须按照精确的公差制造,以确保可靠的功能。
- LED 组件:注塑成型生产用于 LED 照明的多种组件,包括透镜、反射器和漫射器。 制造商必须按照精确的规格制造这些组件,以确保适当的光分布和效率。
- 电源组件: 注塑成型可生产用于电源装置的多种组件,包括插座、插头和电缆连接器。 这些组件必须按照精确的公差制造,以确保安全可靠地运行。
除了这些应用之外,制造商还使用注塑成型来生产其他几种电子元件,包括键盘、计算机鼠标和遥控器。
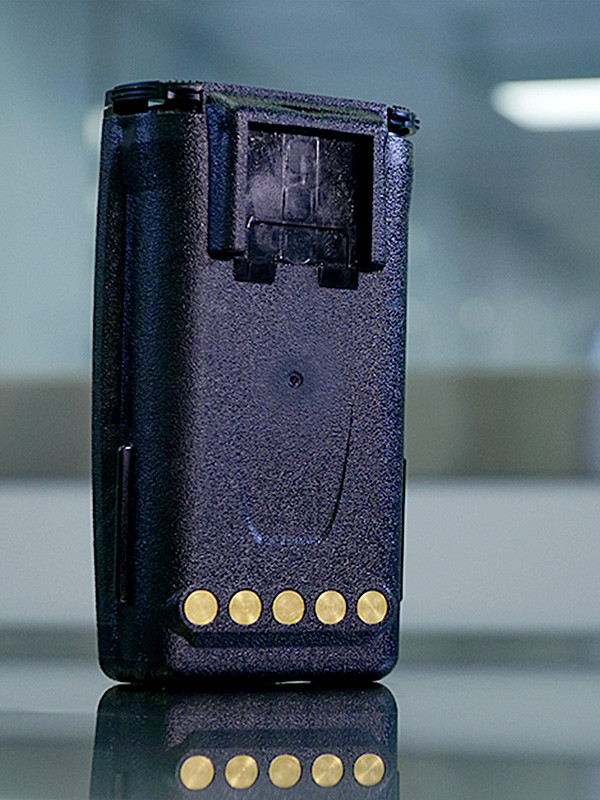
在电子行业使用注塑成型的好处很多,包括:
- 高精准度: 注塑成型允许生产具有高精度和一致性的组件,确保它们符合严格的质量标准。
- 定制: 注塑成型允许生产复杂的形状和设计,允许制造商定制组件以满足特定的设计要求。
- 速度:注塑成型是一种快速高效的制造工艺,可以大批量生产高质量的部件,从而减少生产时间和成本。
航天工业应用
航空航天业是一个对其所有组件都要求最高水平的精度、准确性和耐用性的行业。 塑料注射成型在航空航天工业中变得越来越普遍,因为它能够生产复杂的几何形状、减轻重量和增强结构完整性。 在这里,我们将仔细研究塑料注射成型在航空航天工业中的各种应用。
- 内部组件: 注塑成型为飞机生产一系列内部组件,包括座椅靠背、托盘桌和头顶隔间。 这些组件必须轻巧耐用,能够承受高压力和磨损。
- 结构组件: 注塑成型生产飞机的结构部件,包括翼尖、整流罩和机身部分。 这些部件必须重量轻、坚固耐用,以确保飞机的安全和效率。
- 引擎组件:注塑成型为飞机发动机生产多种部件,包括涡轮叶片、燃料喷嘴和外壳。 这些组件必须按照精确的规格制造,以承受高温、压力和应力。
- 电气元件: 注塑成型为飞机生产电子元件,包括连接器、开关和线束。 这些组件必须按照精确的公差制造,以确保正常的功能和可靠性。
- 仪表组件:注塑成型生产飞机仪表部件,包括控制面板和仪表外壳。 这些组件必须经久耐用,能够承受高温、压力和振动。
除了这些应用之外,制造商还使用注塑成型为航空航天工业生产其他几种部件,包括支架、紧固件和垫圈。
在航空航天工业中使用注塑成型的好处很多,包括:
- 减轻重量: 注塑成型可以生产轻型部件,从而减轻飞机的重量,从而降低油耗并提高效率。
- 精确:注塑成型可以生产高精度和一致性的零件,确保它们符合严格的质量标准。
- 定制:注塑成型允许生产复杂的形状和设计,允许制造商定制组件以满足特定的设计要求。
- 耐用性:我注塑成型生产的部件经久耐用,能够承受高强度的应力、温度和压力,从而确保飞机的安全性和可靠性。
消费品行业应用
消费品行业是全球经济中最关键的行业之一。 消费品是个人日常使用的产品,包括家居用品、电子产品、玩具和个人护理产品。 塑料注射成型在消费品行业中越来越受欢迎,因为它能够精确地生产高质量的部件。 在这里,我们将仔细研究塑料注射成型在消费品行业中的各种应用。
- 包装: 注塑成型广泛用于生产消费品包装材料,包括食品包装、饮料瓶和化妆品容器。 注塑成型允许生产复杂的形状和设计,确保包装材料具有功能性和视觉吸引力。
- 家居用品: 注塑成型生产一系列家居用品,包括厨房用具、储物容器和清洁用品。 这些物品必须耐用、轻便并能承受日常使用。
- 玩具: 注塑成型生产各种玩具,包括可动人偶、玩偶和棋盘游戏。 这些玩具必须按照精确的规格制造,以确保它们安全耐用。
- 个人护理产品: 注塑成型生产独特的护理产品,包括牙刷、剃须刀和洗发水瓶。 这些产品必须美观、实用且经得起频繁使用。
- 电子产品: 注塑成型为电子设备生产多种组件,包括外壳、按钮和连接器。 这些组件必须耐用、重量轻,并能承受高温和高压。
除了这些应用之外,制造商还使用注塑成型为消费品行业生产其他几种组件,包括汽车零件、医疗设备和工业设备。
在消费品行业使用注塑成型的好处很多,包括:
- 性价比高:与其他制造工艺相比,注塑成型可以以更低的成本生产高质量的部件。
- 定制:我注塑成型允许创建具有复杂形状和设计的元素,允许制造商定制功能以满足特定的设计要求。
- 精确: 注塑成型具有高度准确和一致的细节,符合严格的质量标准。
- 耐用性: 注塑成型使零件经久耐用,能够承受高水平的应力、温度和压力,从而确保产品的安全性和可靠性。
嵌件注塑成型的未来趋势
随着技术的进步和消费者需求的变化,嵌件注塑成型行业也在不断发展。 制造商总是在寻找提高效率、降低成本和生产更高质量产品的方法。 在这里,我们将了解嵌件注塑成型的一些未来趋势。
- 自动化: 自动化在制造业中越来越受欢迎,嵌件注塑成型也不例外。 自动化系统可以降低劳动力成本、提高生产速度并改进质量控制。
- 可持续发展: 随着对环境问题的日益关注,制造商正在寻找减少浪费和提高可持续性的方法。 使用回收材料和设计易于回收或重复使用的产品只是制造商解决此问题的几种方法。
- 3D印刷: 嵌件注塑成型的某些方面已经使用了 3D 打印,但它有可能在未来变得更加普遍。 快速创建原型和生产定制组件的能力只是 3D 打印的优势之一。
- 先进材料: 研究人员和制造商正在开发能够承受各种温度、压力和压力的新材料。
- 智能制造:智能制造涉及使用技术实时收集和分析数据,从而实现更快的决策制定和更高效的生产。 该技术可以改善质量控制、减少停机时间并提高生产率。
结论
嵌件注塑成型是一种多功能且具有成本效益的制造工艺,可以制造具有嵌入式组件的复杂零件。 它优于传统组装方法的优势使其在汽车、医疗、电子、航空航天和消费品等各个行业中广受欢迎。 通过了解嵌件注塑成型中涉及的不同技术、材料和设计考虑因素,制造商可以优化其生产流程并向客户提供高质量的产品。 随着技术的进步,我们可以期待看到嵌件注塑成型的更多创新应用。