注塑成型的新发展
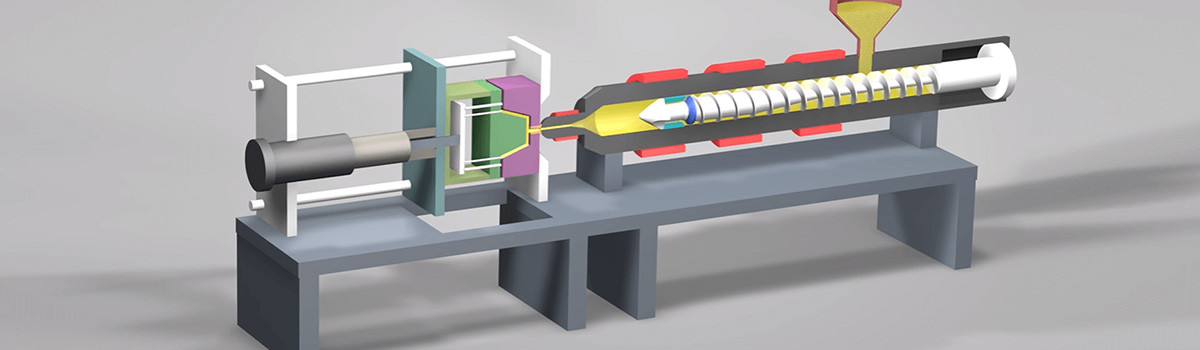
塑料注射成型作为一种制造技术已经存在了几十年。 然而,新的注塑成型趋势正在推动这种方法向前发展,为选择它的公司带来前所未有的新优势。
了解未来几年注塑成型的新趋势,以及贵公司如何从应用中获益。
注塑成型是如何演变的?
虽然塑料自 1850 年代就已存在,但直到 1870 年代才发明出更灵活的塑料类型。 因此,开发了注塑工艺。 从那时起,许多进步进一步推动了塑料注射成型的可能性:
螺杆注塑机的发明意味着注射速度更容易控制,因此最终产品也呈现出更高的质量。 这一过程还允许使用混合材料,为使用有色塑料和回收塑料打开了大门。
气体辅助螺杆机还能够创造出更复杂、更灵活和更坚固的产品。 这种方法还意味着经济成本下降,因为生产时间、浪费和产品重量都已最小化。
由于计算机辅助制造,现在存在更复杂的模具,设计师现在可以生成更复杂的形状(它们可以有多个部分,或者更详细和精确)。
气体辅助注射成型
在这种形式的注射成型中,典型的熔化塑料注射是通过将加压气体注入模具来辅助的——氮气通常用于此过程。 气体产生气泡,将塑料推向模具的末端; 因此,随着气泡的膨胀,不同的部分被填充。 塑料工业中使用了几种成型方式,它们的区别在于浇注聚合物时注入气体的位置。
更具体地说,气体可以通过机器中的喷嘴注入,或者在恒定的压力或体积下直接注入模具的型腔中。 其中一些方法受专利保护; 因此,应签订适当的许可协议才能使用它们。
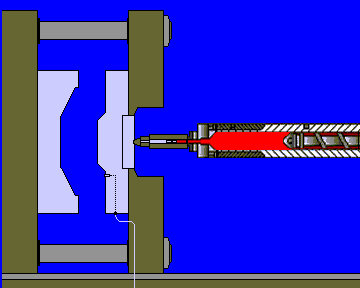
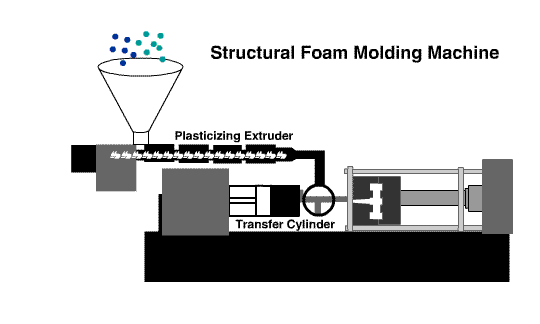
泡沫注塑成型
该技术提供了一种有效且经济的方式来实现结构部件的高阻力和刚度。 除了这一优势,结构泡沫部件还具有出色的隔热性能、更强的耐化学性以及改进的电气和声学特性。 这部分涉及两层之间的泡沫芯; 该芯是通过将惰性气体溶解在树脂中并在将气塑溶液注入模具型腔时使其膨胀而获得的。 我们在哪里可以找到通过泡沫注射成型制造的零件? 该工艺用于汽车面板,作为减轻零件重量的替代方法。
薄壁注塑成型
这种情况下的主要技术创新与最终结果有关:壁非常薄的部分。
这个过程的主要困难是决定什么宽度的墙应该被认为是“薄墙”。 作为一般规则,当制造宽度小于半毫米(1/50 英寸)的零部件时,它们被认为具有薄壁。
如今,与减少墙壁宽度相关的好处受到高度赞赏和追捧。
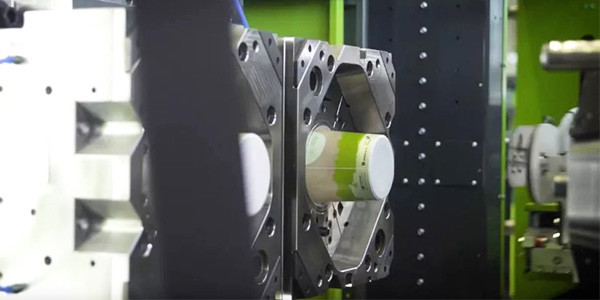
多组分注塑成型
也称为注塑包覆成型或包覆注塑,因为该项目涉及在通常为塑料或金属部件的基础材料(基材)上包覆成型硬质或软质聚合物。
总的来说,这项技术可以定义为在同一个模具中注入多个组件或材料,并作为单一工艺的一部分,允许组合两种、三种或更多种具有不同颜色、纹理和形状的材料。
多材料注塑成型有哪些好处?
多材料注塑成型可以制造由各种塑料制成的复杂零件。 这种塑料注射工艺的主要优点是可以获得具有高机械、耐热和耐化学性的部件。
明年注塑成型趋势
注塑成型的可持续性
塑料注塑成型行业正在迅速适应新的可持续性价值观和法规,尤其是在塑料行业受到越来越多的监控和监管的时候。 因此,新的注塑成型趋势指向:
使用 100% 可回收塑料材料,既安全又环保。
寻找替代品以减少制造过程中的碳足迹。 这可能包括应用可再生能源并努力最大限度地减少制造过程中的能源损失
同时,公司必须保证向可持续模式的转变不会影响产品质量,包括产品的机械和物理性能。
对轻质材料的需求增加
轻质材料通常转化为较低的经济成本(例如运输成本)以及较低的能源成本(例如,汽车零件)。 医疗器械中的轻质材料也可以改善患者的治疗效果。
注塑成型定制解决方案
在塑料注塑成型中寻找更具成本效益的选择也导致优先考虑定制解决方案,因为越来越多的公司意识到,当他们的技术部件定制以满足他们的特定需求时,他们的投资回报率会增加。
塑料注射成型自动化及新技术
不同的自动化软件选项,以及人工智能、机器学习和高级分析的引入,正在进一步推动塑料注射成型的可能性。
这些技术可以最大限度地减少设备停机时间和故障,开发预测性维护计划,并加快生产周期。 与此同时,新软件允许公司在设计过程中模拟注塑成型周期,测试不规则填充图案等问题。 这转化为在继续生产过程之前纠正问题,从而节省时间和金钱。