模具及注塑
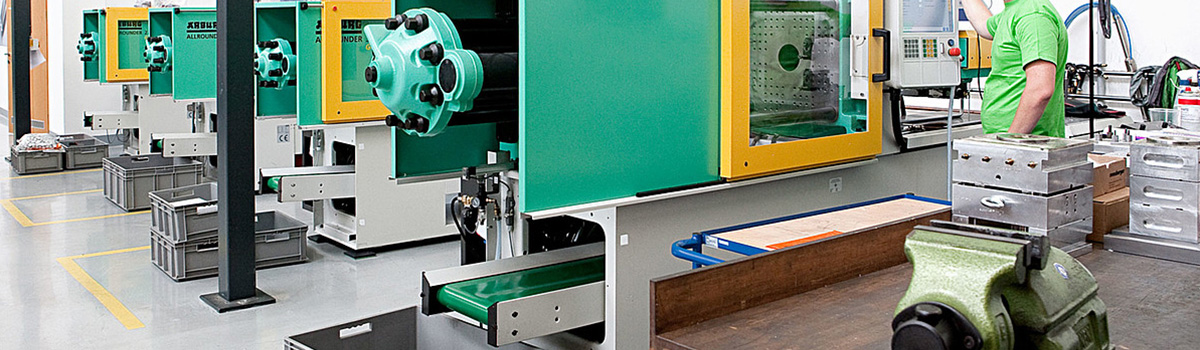
塑料注射成型是一种制造过程,涉及熔化塑料颗粒并将其注入模具型腔以创建三维物体。 这个过程从许多产品开始,从小型精密零件到重要的汽车零部件。 与其他制造工艺相比,塑料注射成型具有许多优势,包括高生产率、设计灵活性和成本效益。 本指南将深入探讨塑料注射成型并探讨其各种应用、优势和局限性。
注塑成型的历史
塑料注射成型是一种制造过程,涉及将熔融塑料注入模具型腔以形成特定形状。 塑料注射成型的历史可以追溯到 1800 年代后期,当时赛璐珞(一种塑料)首次被发明。 然而,直到 1940 年代,注塑成型才作为一种制造技术得到广泛应用。
第二次世界大战期间,对批量生产的塑料产品的需求增加,制造商开始寻找新的、更高效的生产方式。 1946年,美国发明家James Watson Hendry研制出第一台螺杆式注塑机,彻底改变了塑料注塑行业。 这台机器允许更精确和一致的注射过程控制,使大量塑料部件的生产更容易和高效。
在整个 1950 年代和 1960 年代,塑料技术的进步不断改进塑料注射成型工艺。 聚苯乙烯和聚乙烯等新材料的引入创造了更加复杂和耐用的塑料部件。 此外,成型机技术的改进(包括使用液压系统)使注塑成型工艺更加高效且更具成本效益。
今天,塑料注射成型是一种高度自动化的工艺,用于生产范围广泛的塑料产品,从玩具和消费品到汽车零件和医疗设备。 随着新材料和新技术的发展,塑料注射成型工艺不断发展和改进,确保它在许多年内仍然是一项重要的制造技术。
注塑成型基础知识
塑料注射成型是制造由塑料材料制成的零件和产品的制造过程。 该过程涉及将熔化的塑料注入模具中,模具冷却并凝固以形成所需的形状。
塑料注射成型过程中涉及的基本步骤如下:
- 模具设计:流程的第一步是设计用于制造所需零件的模具。 模具通常由金属制成,必须准备好考虑塑料冷却和固化时的收缩。
- 材料准备:注塑过程中使用的塑料材料以颗粒或颗粒的形式出现,必须将其熔化并准备好注入模具。 这通常在料斗中完成,塑料在料斗中被加热到特定温度并熔化成液态。
- 注射:塑料熔化后,使用专门的注射成型机将其注射到模具中。 机器对熔化的塑料施加压力,迫使它进入模具型腔,在那里它呈现出模具的形状。
- 冷却凝固:塑料注入模具后,可以冷却凝固。 这可能需要几秒到几分钟不等,具体取决于零件的大小和复杂程度。
- 顶出:塑料冷却固化后,打开模具,顶出零件。 该位置可能需要额外的修整工作,例如修剪或打磨,以去除多余的塑料或粗糙的边缘。
注塑成型是一种精确且可重复的工艺,非常适合批量生产质量稳定的零件和产品。 它还具有高度的通用性,因为它可以创建各种尺寸、形状和复杂性的零件和产品。 塑料注射成型的一些最常见应用包括玩具、消费品、汽车零件和医疗设备的生产。
塑料注射成型工艺:循序渐进
塑料注射成型是一个复杂的过程,涉及多个步骤。 以下是塑料注射成型工艺的分步指南:
- 设计模具:第一步是设计用于制造零件的模具。 模具通常由钢或铝制成,必须准备好适应塑料材料在冷却时的收缩。
- 创建模具:模具设计完成后,将使用计算机辅助设计 (CAD) 软件和计算机辅助制造 (CAM) 机械进行制造。 模具必须经过仔细加工和抛光,以确保最终产品的精度和光洁度。
- 材料选择:用于注塑工艺的塑料树脂材料必须根据零件的要求进行选择,例如其强度、柔韧性、颜色和质地。
- 材料准备:然后将选定的塑料材料加热到特定温度并熔化成液体。 然后将材料注入成型机的料斗中。
- 注射成型:使用专门的注射成型机将熔融的塑料材料注射到模具型腔中。 机器对塑料材料施加压力,迫使其进入模具型腔,在那里它呈现出模具的形状。
- 冷却:一旦模具型腔充满塑料,它就会冷却凝固。 冷却时间由塑料材料的特性、零件的尺寸和厚度以及模具温度决定。
- 顶出:塑料固化后,打开模具,使用顶针将零件从模具中顶出。
- 精加工:弹出的零件可能需要额外的精加工,例如修剪、打磨或涂漆,以去除任何多余的塑料或粗糙的边缘。
- 质量控制:成品零件经过彻底检查,以满足所需的规格和质量标准。
塑料注射成型可以生产多种尺寸、形状和复杂性的各种零件和产品。 该工艺广泛应用于多个行业,包括汽车、医疗、消费品和电子产品。
注塑成型中使用的塑料类型
许多类型的塑料都可用于注塑成型。 塑料材料的选择将取决于所生产的产品或零件的具体要求,例如强度、柔韧性、耐用性和外观。 以下是注塑成型中使用的一些最常见的塑料类型:
- 聚乙烯 (PE):PE 是一种广泛使用的塑料材料,以其强度和柔韧性着称。 它用于生产各种产品,包括包装材料、玩具和医疗器械。
- 聚丙烯 (PP):PP 是一种轻质耐用的塑料材料,常用于汽车行业的内饰部件,例如仪表板和门板。 它还生产包装材料,例如容器和瓶子。
- 聚碳酸酯 (PC):PC 是一种坚固且透明的塑料材料,通常用于生产电子元件,例如电脑和手机外壳。 它还用于汽车行业的前照灯透镜和仪表板组件。
- 丙烯腈丁二烯苯乙烯 (ABS):ABS 是一种多功能塑料材料,以其强度、耐用性和耐热性而著称。 它通常用于生产汽车零件,例如仪表板、挡泥板、玩具和消费品。
- 聚酰胺 (PA):PA 也称为尼龙,是一种坚固且轻质的塑料材料,通常用于生产汽车零件,例如发动机罩和进气系统。 它还生产运动器材,例如滑雪靴和网球拍。
- 聚苯乙烯 (PS):PS 是一种轻质且坚硬的塑料材料,常用于生产包装材料,例如杯子、托盘和食品容器。 它还生产消费品,例如玩具和电子元件。
- 聚对苯二甲酸乙二醇酯 (PET):PET 是一种坚固且透明的塑料材料,通常用于生产包装材料,例如瓶子和容器。 它还用于纺织工业以生产纤维和织物。
这些只是注塑成型中使用的几种最常见的塑料类型。 可以使用许多其他类型的塑料材料,每一种都具有独特的性能和特性。 塑料材料的选择将取决于所生产的零件或产品的具体要求。
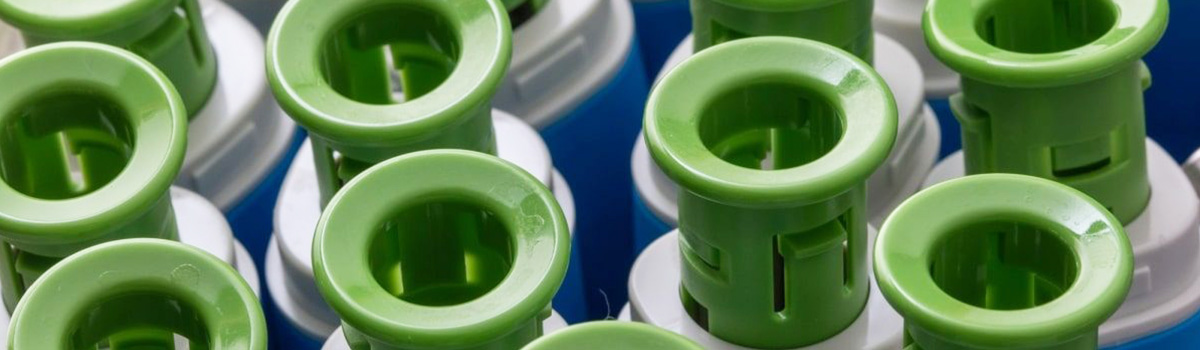
注塑机的种类
注塑机有多种类型和尺寸,每一种都旨在满足特定的制造要求。 以下是一些最常见的注塑机类型:
- 油压射出成型机:该机利用油压动力产生压力,将塑料射出模具。 液压机通常用于需要高夹紧力的更重要的零件。
- 电动注塑机:电机使用电动机为注射装置和合模机构提供动力。 它们以高精度和高能效着称,因此以生产小型、复杂的零件而闻名。
- 混合式注塑机:混合式机器结合了液压和电动装置的优点,使用液压和电力来产生必要的压力和动力。 混合动力机器在速度、精度和能源效率之间实现了良好的平衡。
- 立式注塑机:立式注塑机生产需要嵌件成型或包覆成型的零件。 它们有一个垂直夹紧装置,可以轻松接触模具,使其成为制造小型或复杂零件的理想选择。
- 二次注塑机:二次注塑机生产具有不同材料或颜色的零件。 该设备有两个注射单元,每个单元都能够将异物注射到模具中。 这种类型的机器通常用于生产汽车零件,例如把手和旋钮。
- 多射注塑机:多射注塑机生产具有两种以上材料或颜色的零件。 该设备有多个注射单元,每个单元都能够将不同的材料注射到模具中。 这种类型的机器通常用于生产消费品,例如牙刷和剃须刀。
- 全电动注塑机:全电动注塑机使用电动机为注射装置、合模机构和模具提供动力。 它们以高精度、速度和能源效率着称,因此以生产小型高精度零件而闻名。
这些只是几种最常见的注塑机类型。 每台机器都具有独特的功能和优势,因此必须根据特定的制造要求选择合适的设备。
注塑机零件
注塑机有几个部件可以用原材料制造塑料部件。 以下是注塑机的关键部件:
料斗:在将塑料原料送入注塑机之前,储料槽会存放塑料原料。 该材料通常为颗粒或粉末形式。
料筒:料筒是注塑机的长圆柱形部分,装有螺杆,螺杆可熔化和混合塑料材料。
螺杆:螺杆是机筒内的一种旋转装置,推动塑料材料前进,并通过摩擦和加热使其熔化。
注射单元:注射单元包括料斗、料筒和螺杆,负责将塑料熔化并注射到模具中。
合模单元:合模单元负责在注塑过程中牢固地固定模具并施加必要的压力。
模具:模具是创造塑料零件形状和尺寸的工具。 模具通常由钢制成,由装配在一起的两半组成。
射嘴:射嘴是注射装置中连接注塑机和模具的部分。 熔化的塑料材料通过喷嘴注入模具中。
冷却系统:冷却系统负责冷却注入模具后的塑料零件。 这确保了工件凝固并且可以在没有损坏的情况下从模具中取出。
控制面板:控制面板是允许操作员监控和调整注塑机设置(例如温度、压力和循环时间)的界面。
这些零件中的每一个在注塑成型过程中都起着至关重要的作用,维护和优化每个零件以确保高效生产高质量零件至关重要。
注塑模具:设计和制造
注塑模具是指设计和制造用于注塑机生产塑料零件的模具。 模具的质量和效率直接影响注塑过程的质量和生产率。 以下是注塑模具设计和制造的关键步骤:
产品设计:注塑模具的第一步是设计要生产的产品。 产品设计包括确定零件的尺寸、形状和材料,以及任何特定特征或要求。
模具设计:一旦产品设计完成,模具设计过程就开始了。 模具设计师将确定最佳模具类型、所需型腔数量以及模具的尺寸和形状。
模具构造:模具是根据模具设计构造的,使用钢或铝等优质材料。 模具通常分为两半,每一半包含一个或多个空腔。
模具组装:模具构建完成后,将进行组装并测试其精度和功能。 模具必须承受注塑成型过程中的压力和热量。
模具测试和验证:模具组装后,进行测试和验证,以确保生产出符合产品规格的高质量零件。 模具可能需要调整或修改以提高其性能。
模具维护:模具的定期维护和修理对于确保其使用寿命和性能至关重要。 这包括清洁、润滑和更换任何磨损或损坏的零件。
注塑模具需要精度和专业知识,才能始终如一、高效地生产高质量的零件。 通过遵循完整的设计和制造流程,制造商可以制造满足其产品独特要求的模具并优化其注塑成型工艺。
注塑模具的类型
注塑成型是一种广泛用于大批量生产零件的制造工艺。 它涉及将熔化的塑料注入模腔,然后使其冷却并凝固成所需的形状。 注塑模具是创建用于注塑成型的模具的过程。 有几种类型的注塑模具,每种都有自己的优点和缺点。
- 双板模具 双板模具是最简单的注塑模具类型。 它们由夹在一起形成模腔的两块板组成。 熔化的塑料通过浇口注入孔中,然后冷却固化。 创建零件后,将两个板分开,然后弹出一定数量的零件。 双板模具通常用于具有简单几何形状的中小型部件。
- 三板模具 三板模具类似于两板模具,但它们有一个额外的板,称为脱料板,它将成型零件与流道系统分开。 流道系统是将熔融塑料输送到模具型腔的通道网络。 三板模具用于更重要的零件和更复杂的几何形状。
- 热流道模具 在热流道模具中,熔融塑料通过一系列加热通道而不是通过浇口直接注入模具型腔。 这减少了流道系统中浪费的材料,从而提高了工艺效率。 热流道模具用于复杂零件的大批量生产。
- 系列模具 系列模具在单个模具中生产多个零件。 它们具有各种腔体,其排列方式允许同时生产多个域。 家庭模具通常用于中小型体积的零件。
- 嵌件模具 嵌件模具生产需要金属或塑料嵌件的零件。 在注入熔融塑料之前,将嵌件放入模腔中。 一旦塑料冷却并固化,零件和嵌件就会永久粘合。 嵌件模具用于需要强度、耐用性或美学吸引力的位置。
- 包覆成型 包覆成型是将一个零件模制在另一个零件上的过程。 它通常用于需要柔软触感或改进抓地力的位置。 包覆成型涉及首先设置基材或基础部件,然后在其上成型第二种材料。 第二种材料可以是不同类型的塑料、类橡胶材料或热塑性弹性体。
总之,注塑模具的选择取决于所生产零件的类型、所需的生产量以及零件设计所涉及的复杂程度。 选择合适的工具对于确保流程高效且具有成本效益至关重要。
注塑成型设计指南
注塑成型是一种广泛用于生产塑料零件的制造工艺。 设计用于注塑成型的零件需要对工艺、材料和必须遵循的设计指南有很好的了解,以确保细节能够成功制造。 以下是一些需要牢记的注塑成型设计指南:
壁厚,零件的壁厚应均匀且尽可能薄,同时保持所需的强度和功能。 这有助于减少冷却和循环时间,并最大限度地降低翘曲和缩痕的风险。
肋和凸台 肋和凸台可用于增加零件的强度和刚度。 加强筋应不超过公称壁厚的60%,凸台应为公称壁厚的1.5倍。
脱模角,所有垂直表面应使用至少 1-2 度的脱模角,以促进零件顶出并防止损坏模具。
圆角和半径 应避免尖角和尖角,以防止应力集中,从而导致开裂和失效。 相反,圆角和圆角应分散应力并提高零件的强度。
浇口和流道 浇口和流道的位置和设计对于实现良好的零件质量至关重要。 零件最厚部分的入口应尽可能小。 流道的设计应使压降最小化并使流量最大化。
表面光洁度 零件的表面光洁度应根据应用要求指定。 可见部件可能需要较高的表面光洁度,而隐藏部件可能需要较低的表面光洁度。
材料选择 为零件选择的材料应适合注塑成型,并满足所需的机械、热和化学性能。
注塑成型中的二次操作
注塑成型是一种用途广泛的制造工艺,用于生产各种塑料零件。 除了主要成型工艺之外,许多位置还需要二次操作才能获得所需的形状、光洁度或功能。 以下是注塑成型中一些日常的二次操作:
- 修整是在模塑零件从模具中脱模后去除多余的材料。 这通常使用修整压力机或 CNC 机器来完成。 通常需要修整以达到零件的最终形状和尺寸。
- 焊接使用热量、压力或两者的组合来结合两个或多个塑料部件。 这通常用于创建无法在单个模具中生产的更大或更复杂的特征。
- 装饰是在模制零件表面添加视觉或功能特征的过程。 这可以包括绘画、印刷、标记或应用纹理或图案。
- 装配是连接多个零件以创建完整产品的过程。 这可以使用紧固件、粘合剂或其他连接技术来完成。
- 嵌件成型 嵌件成型是围绕预成型的金属或塑料嵌件成型塑料。 这通常用于制造具有高强度或耐用性的零件。
- 包覆成型 包覆成型是在预成型部件上模制第二种材料的过程。 这可以增加柔软触感的表面,提高抓地力,或创建双色调或多材料的作品。
- 涂层在零件表面涂上一层薄薄的材料,以改善其外观、耐用性或其他特性。 这可以包括涂层,例如铬、镍或粉末涂层。
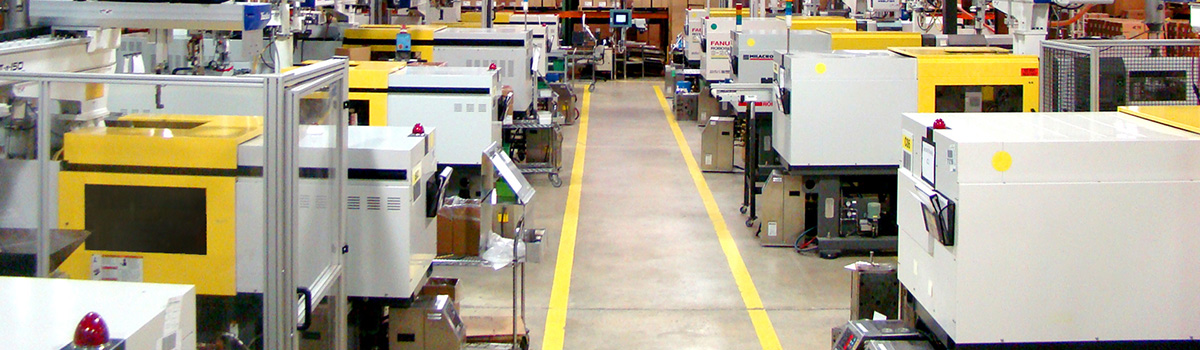
注塑成型的优势
注塑成型是一种广泛使用的制造工艺,用于生产高精度、一致性和高质量的塑料零件。 它涉及将熔化的塑料注入模腔并使其冷却和固化。 以下是塑料注射成型的一些优点:
- 高效率和高生产力塑料注射成型是一种高效和自动化的过程,可以生产大量具有高一致性和质量的零件。 凭借先进的自动化技术,生产周期时间可缩短至数秒,从而实现复杂零件的大批量生产。
- 高精度和精密注塑成型提高了生产复杂零件的准确性和精度。 计算机控制的机械和先进的软件可实现具有高重复性和准确性的严格公差。
- 多功能性 注塑成型是一种多功能工艺,可以生产各种不同尺寸、形状和复杂性的塑料零件。 该过程可用于制造从具有复杂细节的小件到具有复杂几何形状的大件的任何东西。
- 材料灵活性 注塑成型可以使用范围广泛的塑料材料,包括热塑性塑料、热固性塑料和弹性体。 这允许生产具有各种机械、热和化学特性的零件。
- 低废料生产 注塑成型是一种低废料生产工艺,因为它在生产过程中产生的废料最少。 任何多余的材料都可以轻松回收并在生产中重复使用,使其成为一种环保的制造工艺。
- 降低劳动力成本注塑成型的高度自动化最大限度地减少了对劳动密集型流程的需求,从而显着降低了劳动力成本。 这也降低了人为错误的风险,提高了最终产品的质量和一致性。
- 减少后期生产操作 注塑成型生产的零件具有高精度和一致性,减少了对后期生产操作(如修整、钻孔或铣削)的需求。 这减少了最终产品的生产时间和成本。
- 一致性和质量 注塑成型生产的零件具有高度的一致性和质量。 先进的技术和计算机控制的机械确保每个细节在形状、尺寸和质量上都完全相同。
- 设计灵活性 注塑成型提供了高度的设计灵活性,因为它允许生产具有复杂几何形状、底切和复杂细节的零件。 这将使设计师能够创造出具有独特形状和功能的作品,而这些作品无法使用其他制造工艺制作。
- 大批量生产的成本效益 注塑成型是生产塑料零件的一种成本效益高的工艺。 初始模具成本可能很高,但随着生产量的增加,每个零件的成本会降低。 这使其成为生产大量零件的理想工艺。
塑料注射成型具有许多优点,使其成为生产塑料零件的热门选择。 它的高效率、准确性、多功能性、材料灵活性、低废品产生、降低的劳动力成本以及一致性和质量使其成为各种应用的理想工艺。 能够生产具有高度设计灵活性和成本效益的复杂零件以进行大批量生产,使其成为备受追捧的制造工艺。
注塑成型的缺点
塑料注射成型是一种广泛使用的制造工艺,涉及将熔融塑料注入模具型腔以生产各种塑料零件和产品。 虽然塑料注射成型有很多好处,但也有一些缺点。 以下是塑料注射成型的一些主要缺点:
- 模具成本高:设计和生产塑料注射成型模具的成本可能非常高。 这是因为模具需要由优质材料制成,并经过精密加工才能制造出所需的零件。 此外,设计和制造模具的成本对于小规模生产运行来说可能过高,使得塑料注射成型对于小批量制造来说不太经济。
- 交货时间长:设计和生产塑料注射成型模具的过程可能需要很长时间,这会延迟塑料零件的生产。 对于需要快速响应市场需求变化或快速开发新产品的企业来说,这尤其成问题。
- 灵活性有限:一旦设计和生产了模具,更改设计或修改生产过程就更容易且成本更低。 这会限制塑料注射成型的灵活性,使其不太适合生产定制或独一无二的产品。
- 环境问题:塑料注射成型依赖于大量塑料,这会对生态产生负面影响。 塑料废物是一个主要的环境问题,而塑料注射成型可能会导致这个问题。 此外,制造塑料产品的过程需要使用能源和自然资源,这会进一步影响环境。
- 废品率高:注塑成型会产生大量废料,处理或回收这些废料的成本很高。 此外,废料的产生会增加整体生产成本并降低制造过程的效率。
- 有限的材料选择:注塑成型主要用于用热塑性材料生产零件和产品,与金属或陶瓷等其他材料相比,热塑性材料的性能有限。 这会使塑料注射成型不太适合需要高强度、耐温性或其他高级性能的应用。
注塑成型的局限性
虽然塑料注射成型具有许多优点,但该工艺也存在某些局限性。 以下是塑料注射成型的一些局限性:
高初始模具成本:可以增加设计和制造模具的初始成本。 模具需要精密耐用以承受重复的注塑成型过程,这可能需要大量的前期投资,特别是对于复杂或大型模具。
交货时间:制造模具的交货时间可能很长,从几周到几个月不等,具体取决于模具的复杂性和尺寸。 这可能会导致生产时间表的延迟,特别是对于时间敏感的项目。
设计限制:注塑成型有一定的设计限制,必须加以考虑。 例如,在整个零件中实现均匀的壁厚对于确保适当的填充和冷却至关重要。 此外,垂直表面需要有拔模斜度,以便于从模具中脱模。
零件尺寸限制:注塑成型最适合生产中小型零件。 大型零件可能需要专门的设备和更大的模具,从而增加了成本和复杂性。
材料选择:虽然注塑成型允许使用范围广泛的塑料材料,但与其他制造工艺相比,材料的选择仍然有限。 熔点高或流动性差的材料可能不适合注塑成型。
表面光洁度:注塑成型过程可能会导致零件表面出现可见的编织线或分型线。 实现高质量的表面光洁度可能具有挑战性,并且可能需要其他方法,例如抛光或涂层。
有限底切:底切是零件上的特征或细节,可防止其轻易从模具中移除。 底切会使顶出过程复杂化,并且需要额外的模具特征或二次操作才能获得所需的零件几何形状。
修复选项有限:如果模具损坏或需要修改,修复或改造现有模具可能既费钱又费时。 有时,可能需要制造全新的模具,从而导致额外费用和延误。
尽管有这些限制,塑料注射成型仍然是一种高度通用且广泛使用的生产塑料零件的制造工艺。 通过在设计和生产计划阶段仔细考虑这些限制,可以减轻它们的影响并有效利用注塑成型的优势。
注塑成型的应用
塑料注射成型是一种多功能制造工艺,可以生产范围广泛的塑料零件。 以下是塑料注射成型的一些应用:
- 消费品:注塑成型广泛用于生产各种产品,例如玩具、厨具和电子产品。 该工艺可以生产具有复杂几何形状和精确尺寸的高质量零件,非常适合需要严格公差和复杂形状的产品。
- 汽车部件:许多汽车塑料部件,如仪表板部件、门把手和照明,都是使用注塑成型生产的。 该工艺可实现高产量和稳定的质量,使其成为汽车制造商具有成本效益的选择。
- 医疗器械:注塑成型通常用于生产医疗器械,例如注射器、吸入器和诊断设备。 该工艺可以生产出高精度和一致性的零件,确保器件的质量和可靠性。
- 包装:注塑成型广泛用于生产塑料包装,例如容器、盖子和瓶盖。 该工艺可以使部件具有一致的尺寸和高质量的饰面,使其成为具有吸引人的外观和牢固贴合的包装的理想选择。
- 航空航天和国防:注塑成型生产各种航空航天和国防部件,例如飞机内饰、照明和通信系统。 该工艺的部件可以采用轻质、耐用的材料,使其适用于需要高强度重量比的应用。
- 建筑:注塑成型可以生产各种建筑材料,例如塑料瓦、屋顶和壁板。 该工艺可以使零件具有一致的尺寸和高质量的饰面,使其成为建筑公司的一个有吸引力的选择。
- 运动和娱乐:注塑成型广泛用于生产运动器材,例如高尔夫球杆、网球拍和自行车部件。 该工艺可以生产具有轻质材料和精确几何形状的零件,确保设备的性能和耐用性。
总的来说,塑料注射成型是一种用途广泛且应用广泛的制造工艺,可以为各种应用生产高质量的塑料零件。 该工艺可以定制以满足特定的设计和生产要求,使其成为多个行业制造商的一个有吸引力的选择。
汽车工业和注塑成型
汽车行业是塑料注射成型技术的重要用户。 塑料注射成型工艺彻底改变了汽车零部件的生产,使得以高精度和准确度生产复杂形状成为可能。 以下是塑料注射成型在汽车行业中的一些应用方式:
- 内饰件:注塑成型产生许多内部因素,包括仪表板组件、门板、装饰件等。 这些零件可以设计成复杂的形状和纹理,并可以进行定制以符合每种车型的风格和功能要求。
- 外部部件:塑料注射成型也用于生产各种外部特征,包括保险杠、格栅、后视镜等。 这些部件可以设计成能够承受极端天气条件,并有多种颜色和饰面。
- 引擎盖下部件:塑料注射成型可生产许多引擎盖下部件,包括发动机罩、进气系统和冷却系统部件。 这些部件需要耐高温和耐化学腐蚀,而这可以通过热塑性材料来实现。
- 电气和电子元件:塑料注射成型生产各种电气和电子元件,包括连接器、外壳和传感器。 这些部件需要很高的精度和可靠性,这可以通过塑料注射成型的精度和一致性来实现。
- 轻量化:塑料注射成型通常用于生产轻质部件,有助于减轻车辆的总重量,提高燃油效率并减少排放。 轻量化还可以改善车辆的操控性和性能。
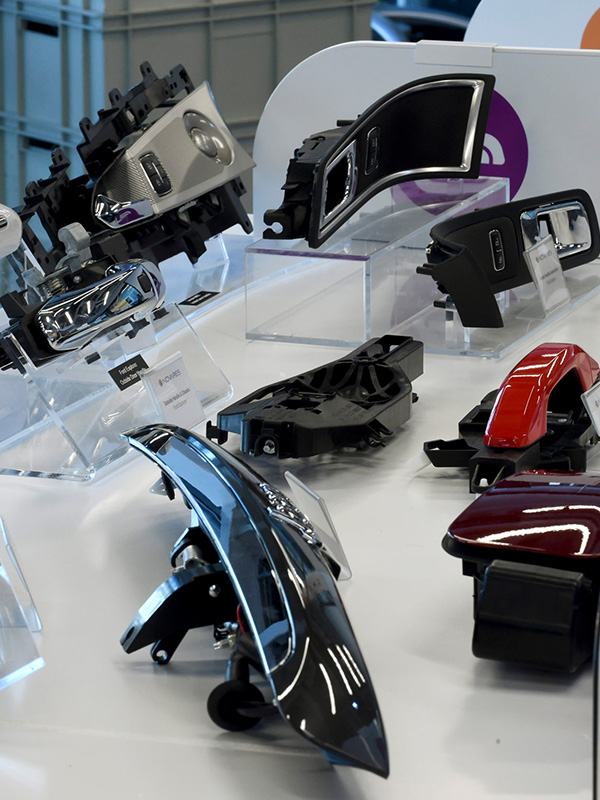
医疗行业和注塑成型
塑料注射成型广泛应用于医疗行业,以生产各种医疗器械和部件。 塑料注射成型工艺允许以高精度和准确度生产复杂形状,使其成为许多医疗应用的理想制造方法。 以下是塑料注射成型在医疗行业中的一些应用方式:
- 医疗器械:注塑成型生产各种医疗器械,包括手术器械、诊断工具、药物输送系统等。这些设备往往需要很高的精度和准确度,而注塑成型可以满足这些要求。
- 植入物:塑料注射成型还用于生产各种植入物,包括关节置换物、牙科植入物等。 这些植入物可以设计成与患者的解剖结构相匹配,并使用生物相容性材料生产。
- 实验室设备:塑料注射成型生产吸管、微孔板和试管。 这些组件需要高精度和准确度以确保可靠的结果。
- 包装:塑料注射成型用于生产医疗器械包装,包括无菌屏障系统和个别产品的定制包装。 这些包装解决方案有助于保持医疗器械的无菌性和完整性。
- 一次性设备:塑料注射成型通常生产一次性设备,例如注射器、针头和导管。 这些设备可以低成本大批量生产,有助于防止感染在医疗机构中传播。
消费品和注塑成型
塑料注射成型因其多功能性、效率和成本效益而广泛用于消费品的生产。 塑料注射成型工艺允许以高精度和准确度生产复杂形状,使其成为许多消费应用的理想制造方法。 以下是塑料注射成型用于生产消费品的一些方法:
- 玩具:塑料注射成型生产范围广泛的玩具,从小雕像到大型玩具组合。 该过程允许创建复杂的设计和细节,并制作各种颜色和材料的玩具。
- 家居用品:注塑成型生产各种家居用品,包括厨房用具、储物容器和清洁用品。 这些产品可以设计为耐用、轻便且易于使用。
- 电子产品:注塑成型生产许多电子元件,包括电脑外壳、手机外壳和充电器。 工艺的精密度和准确度确保这些组件的制造具有高度的一致性和可靠性。
- 个人护理用品:注塑成型生产独特的护理用品,包括牙刷、剃须刀和发刷。 这些产品需要高精度和准确度,以确保易用性和安全性。
- 汽车配件:注塑成型生产一系列汽车配件,包括仪表板部件、杯架等。 这些组件可以设计得轻巧、耐用,并且能够抵抗日常使用中的磨损。
注塑成型中的环境考虑
注塑成型是一种广泛使用的制造工艺,但对环境有重大影响。 以下是塑料注射成型中的一些生态考虑因素:
- 材料选择:注塑成型中使用的塑料材料的选择会对环境产生重大影响。 有些材料是可生物降解或可回收的,而另一些则不是。 使用可生物降解或可回收材料有助于减少注塑成型对环境的影响。
- 能源消耗:塑料注射成型需要大量能量来熔化塑料并将其注入模具中。 节能设备和工艺,例如电机和闭环系统,可以减少能源消耗和环境影响。
- 废物管理:塑料注射成型会产生多余材料、有缺陷的零件和包装的废物。 适当的废物管理实践,例如回收和再利用废料,有助于减少注塑成型对环境的影响。
- 化学品的使用:塑料注塑件中的一些化学品,如脱模剂和清洁溶剂,会对环境造成危害。 使用环保替代品或尽量减少这些化学品的使用有助于减少对环境的影响。
- 报废注意事项:通过注塑成型生产的塑料产品通常最终会进入垃圾填埋场,这可能需要数百年才能降解。 设计可回收或可生物降解的产品可以减少塑料注射成型对环境的影响。
注塑成型的未来
塑料注射成型的未来看起来很有希望,因为技术和材料的进步有望使该过程更加高效、更具成本效益和可持续性。 以下是可能影响塑料注射成型未来的一些趋势和发展:
- 增材制造:增材制造,也称为 3D 打印,是一种新兴技术,有可能改变塑料注塑成型。 通过使用 3D 打印创建模具,制造商可以显着减少与传统模具制造技术相关的时间和成本。
- 智能制造:涉及自动化、数据分析和机器学习的智能制造有望彻底改变塑料注塑成型。 制造商可以通过使用传感器和数据分析来优化流程,从而提高效率、减少浪费并提高生产率。
- 可持续材料:可持续材料,如生物塑料和再生塑料,在塑料注塑成型行业中越来越受欢迎。 这些材料具有环境效益,可以帮助制造商实现可持续发展目标。
- 微成型:微成型涉及生产高精度的小零件,在医疗保健和电子等行业中变得越来越重要。 技术和材料的进步有望使微成型更容易获得且更具成本效益。
- 定制化:随着消费者对产品个性化需求的增加,注塑成型有望变得更加灵活和可定制化。 实时反馈和机器学习等技术的进步将使制造商能够快速高效地生产定制产品。
总结
塑料注射成型是一种高度通用且高效的制造工艺,它彻底改变了各种产品的生产。 从医疗设备到汽车零部件,注塑成型与其他制造工艺相比具有众多优势,包括高生产率、设计灵活性和成本效益。 随着技术和材料的不断进步,注塑成型的前景一片光明,未来几年这一工艺很可能在制造业中发挥更重要的作用。