注塑成型常见成型缺陷的解决方法
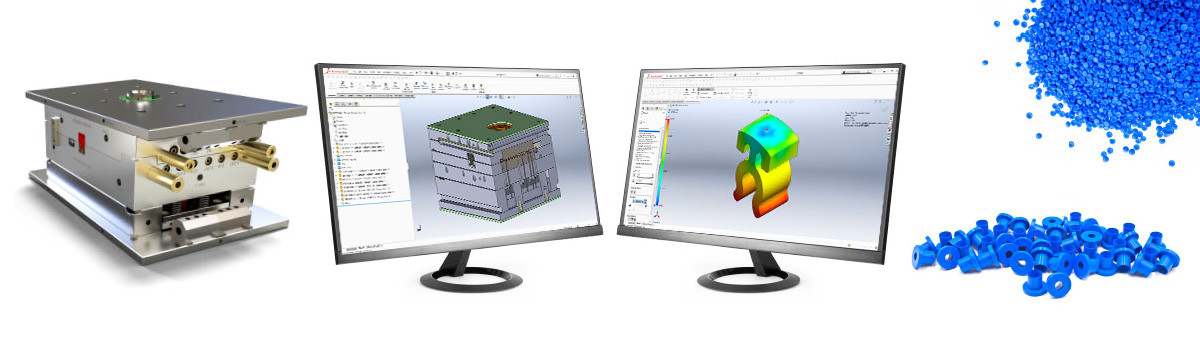
在使用模具加工注塑件时,缺陷是很常见的,这在很大程度上影响了加工效率。 以下是注塑模具零件常见的成型缺陷及解决方法。
短镜头
短射是指由于模具未完全填充而导致的产品不完整。
这种缺陷通常出现在离浇口最远的地方或只能通过模具上狭窄区域才能到达的部分,因为狭窄区域可能会影响熔体的流动。
短射可能会导致微流痕或导致产品的很大一部分明显缺失。
原因:
短射的原因包括:
注入模具的原料不够。
熔体阻力大,导致模具不能完全充满。
模具排气不良造成气蚀的产生,堵塞熔体,使熔体无法流到模具的某些区域。
毛刺
毛边是从模具型腔挤出的多余原料粘附在制品上而产生的。
这种缺陷会出现在产品的边缘或模具的每个组成部分。 原料可能会从模具中溢出,或从动模和定模的结合处溢出。
模芯上也会出现毛刺,这是由于液压压力或角销造成的。
毛刺的严重程度不一,有时细,有时厚。
原因:
毛刺的原因包括:
合模面损坏或严重磨损。
动模与定模锁紧时错位。
原料在模具中的压力高于合模力。
上面提到的第三种情况可能是由多种原因造成的。 在下列情况下,原料压力高于合模力。
在注塑模具的第一阶段(充模阶段),原料填充过多,增加了模具内的压力。
在充模过程中,熔体流动的较大阻力也会使模具内的压力升高。
保压阶段模腔压力过高。
合模力不够。
降解
分解可能导致许多结果。 问题的范围和严重程度也各不相同。 在最严重的情况下,它可能会导致产品完全变色和机械性能变差。 局部退化只会造成深色条纹或斑点。
原因:
降解是由于原材料被破坏引起的。 形成塑料的长链分子在过热或过大的剪切应力作用下会发生分解。 在分子分解过程中,挥发的气体会加速降解过程,从而引起原料脱色。 大量分子的分解最终会破坏原材料的含量,并对机械性能造成负面影响。
料筒温度不均可能导致局部降解。
在以下情况下可能会发生降级:
原料在料筒或热流道系统中过热。
原料在桶内停留时间过长。
在注塑成型过程中,对原材料施加的剪切应力过大。 如果喷嘴堵塞,或浇口和流道太窄,都会增加剪切应力。
形变
在正常情况下,产品的形状应与模具的形状一致。 变形是指产品变形。
当情况变得更糟时,产品在脱模时会完全变形。 情况不严重时,产品形状会出现细小的凹凸不平。
长但没有支撑边或大平面是最容易变形的区域。
原因:
变形原因:
脱模时温度过高。
由于厚薄区域冷却时间不同,或动模和定模的模具温度不同,制品内部收缩率不同。
充型时模流不畅(所谓“凝固取向”)或保压阶段模腔内压力过高。
杂质
杂质常以不同颜色的斑点、斑块或条纹的形式出现。 最常见的是黑点。
杂质可能只是微小的斑点,严重时也可能是明显的条纹或大部分脱色。
原因:
杂质是由原料中混入的杂物引起的,如:
原料在运入桶中时混有杂物。
原料的分解可能会从任何切割机构掉落并混入原料中,例如机器螺栓、干燥滚筒的内壁、接头/喷嘴。
层压
层压会在产品表面产生“结皮效应”,这是由于产品表面与其他原材料的性能和质地不同造成的,形成可去除的剥皮。
分层严重时,整个横截面由不同的层组成,还没有熔合在一起。 当缺陷不太明显时,产品的外观可能符合要求,但会破坏产品的机械性能。
原因:
层压有两个主要原因。 第一个是当两种不同的原材料不正确地混合在一起时。 两种原料在压力下同时输送到机筒中。 然而,当模具冷却时不能熔合在一起,就像不同的层被强行压在一起形成产品一样。
第二:如果冷熔体被迫通过窄浇口,会产生剪切应力。 过高的剪切应力会导致提前熔化的熔体层不能完全熔合。
混合风险:
需要注意的一点是有些原料混合在一起会产生强烈的化学反应,比如PVC和Avetal是绝对不能混合的。
银色线性
条状线状可能只是局部现象,但严重时可扩展到整个表面。
银线会影响产品的外观,也会损害产品的机械性能。
原因:
以下两点造成银色线性:
原料潮湿,有些会吸收空气中的水蒸气。 如果原料太湿,在机筒高温高压的作用下,可能会产生加压蒸汽。 这些蒸气会穿透产品表面并形成银色条纹。
熔体受到热损坏并产生局部降解。 产生的挥发性气体会阻塞在模具表面,在制品表面产生条纹。
这并不像退化那么糟糕。 只要熔体温度高或在塑化或注入模具时受到剪切应力,就可能发生这种情况。
光泽/阴影
产品表面光洁度应与模具相同。 当两者的表面光洁度不同时,就会出现光泽/阴影缺陷。
出现缺陷时表面灰暗,粗糙的表面光滑有光泽。
原因:
光泽/阴影的原因包括:
熔体流动不畅或模具表面温度低,导致材料成型时模具表面光洁度无法复制。
保压时型腔内压力不够高,使材料在冷却过程中紧贴模具表面,留下缩痕。
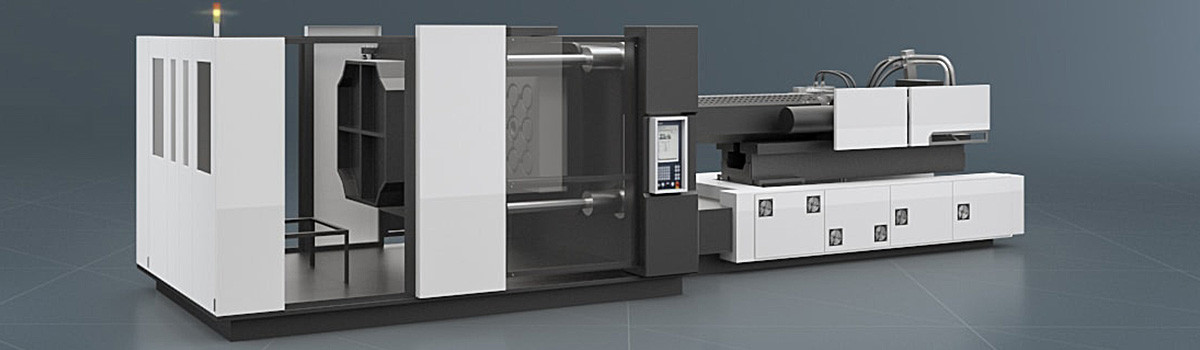
流痕
流痕可以多种形式存在于产品表面。 一般会形成阴影区。
流痕不会在产品表面产生任何用手指感觉不到的压花或凹陷。 这种缺陷也称为拖痕、重影和阴影。
流痕明显时,会产生沟槽,在产品表面留下痕迹等缺陷。
原因:
在以下情况下可以找到流痕:
熔体流动性差或模具表面温度低,造成塑料在充模过程中流动阻力大。
在充模过程中,熔体流动有阻力,这可能是由于模具表面凹凸不平,模具表面印刷的标记或图案,或在填充过程中熔体流动方向的改变造成的。
合缝线
合线是在充模过程中两个熔体前沿相遇时产生的,会像一条线一样出现在产品表面。
合缝线就像产品表面的开裂线,不易察觉。
在设计模具时,一些可见的合缝线是不可避免的。 在这种情况下,尽可能缩短接合线,以防止损坏产品的强度和外观。
原因:
熔锋的产生有多种原因。 最可能的原因可能是熔体沿着模芯的边缘流动。 当两种熔体相遇时,就会产生接合线。 两个熔体前沿的温度要高到足以使它们成功熔合在一起,并且不影响产品的强度和外观。
当两种熔体不能完全融合在一起时,就会产生缺陷。
缺陷原因:
模具有较厚和较薄的部分,熔体的流动速度不同,当熔体流过模具较薄的部分时,温度较低。
每个跑步者的长度都不同。 独来独往的跑步者很容易降温。
模腔压力不足以让熔体在保压阶段完全熔化。
残留的气泡使熔体前沿无法融合,也会导致烧焦。
燃烧
燃烧与短射相似,但有不规则的退色边缘和轻微的燃烧气味。 产品上会出现炭黑区域,情况严重时,还会伴有塑料燃烧的气味。
如果不消除缺陷,模具上通常会出现黑色沉积物。 如果不立即检查燃烧产生的气体或油类物质,它们可能会堵塞气孔。 燃烧通常出现在路径的尽头。
原因:
燃烧是由内燃效应引起的。 当空气中的压力在很短的时间内急剧增加时,温度就会升高并引起燃烧。 根据收集到的数据,注塑过程中的内燃作用可产生高达600度的高温。
在以下情况下可能会产生燃烧:
充模速度快,使模具型腔内的空气无法排出,因进料受阻而产生气泡,受压后产生内燃效应。
气孔堵塞或通风不畅。
模具中的空气应从气孔中排出。 如果通风受到位置、数量、大小或功能的影响,空气将留在模具中并导致燃烧。 合模力大也会导致通气不畅。
收缩
缩水是指产品表面的轻微凹陷。
当缺陷轻微时,产品表面不平整。 严重时,产品会大面积倒塌。 带有拱形、把手和突起的产品通常会出现缩水缺陷。
原因:
缩孔是原材料在冷却过程中大面积收缩造成的。
制品较厚的部位(如拱形),材料心部温度低,收缩比表层晚,材料内部产生收缩力,将外侧拉入向内的凹陷处产生收缩。
在以下情况下会发生收缩:
模腔内的压力低于原料在冷却过程中收缩产生的力。
冷却过程中模具型腔加压时间不够,造成原料从浇口流出型腔。
原料在成型和保压阶段没有足够的缓冲能力,因为在注射过量原料之前螺杆已经完全退出。
浇口和流道的横截面积远小于产品的厚度,这意味着在产品挤出过程之前浇口已经冻结。
气泡
真空气泡以气泡的形式呈现,在透明制品上很容易发现。 它也可以在不透明产品的横截面上看到。
原因:
气泡是产品的真空部分,是原材料在冷却过程中收缩时产生的。
与收缩类似,原材料内部产生收缩力。 不同的是,气泡形成时产品外观已经凝固,没有塌陷,所以产生空心气泡。
产生气泡的原因与减少的原因相同,包括:
模腔压力低效
模腔加压时间不足
流道和浇口尺寸太小
喷涂痕迹
喷涂标记是指浇口对面的螺纹区域。 喷涂痕迹不仅会影响产品的外观,还会影响产品的强度。
原因:
喷痕是在充模过程中熔体流动失控造成的。
熔化的塑料在巨大的压力下进入模具。 如果充模速度太快,塑料会从模腔的开口缝隙中喷出,并迅速回弹冷却。 此时会形成螺纹,阻止熔化的塑料进入浇口。
造成喷涂痕迹的主要原因是浇口位置不正确或浇口设计不当。 以下两种情况会使缺陷情况恶化:
充模速度快
充模时熔体流动不畅