注塑成型基礎知識
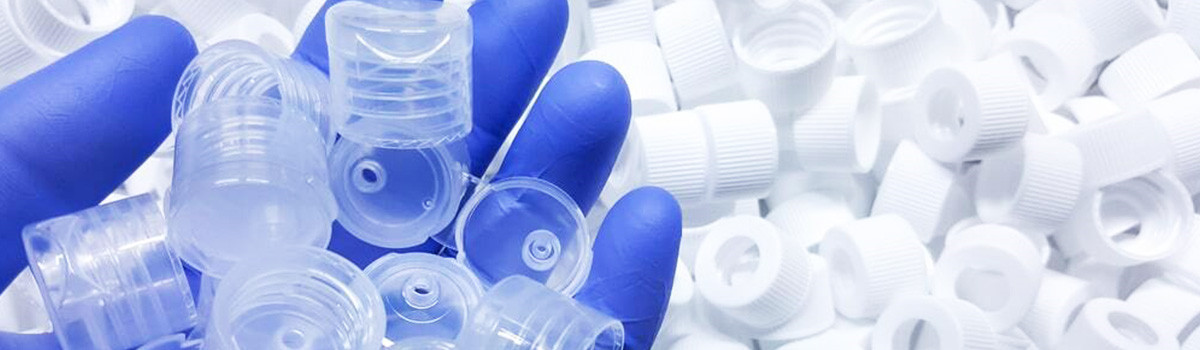
探索注塑成型工藝及其工作原理。
塑料注射成型是一種流行的製造技術,可將熱塑性顆粒轉化為大量複雜零件。 注塑成型工藝適用於多種塑料材料,是現代生活的重要組成部分——手機殼、電子產品外殼、玩具,甚至汽車零件都離不開它。 本文將分解注塑成型的基礎知識,描述注塑成型的工作原理,並說明它與 3D 打印有何不同。
注塑成型的基礎知識是什麼?
塑料注射成型工藝的基礎知識包括創建產品設計、製作適合產品設計的模具、熔化塑料樹脂顆粒,以及使用壓力將熔化的顆粒注入模具。
請參閱以下每個步驟的細分:
1. 創建產品設計
設計師(工程師、模具製造商等)按照特定於注塑成型工藝的基本設計指南創建零件(以 CAD 文件或其他可傳輸格式的形式)。 設計人員應嘗試在其設計中包含以下功能,以幫助提高注塑模具的成功率:
*用於螺紋嵌件/緊固件的凸台
*恆定或接近恆定的壁厚
*可變壁厚之間的平滑過渡
*厚截面中的空腔
*圓邊
*垂直牆上的拔模角度
*用於支撐的肋骨
*摩擦配合、卡扣接頭和其他非緊固件連接功能
*活動鉸鏈
此外,設計人員應盡量減少以下功能以減少設計中的缺陷:
*不均勻的壁厚或特別薄/厚的壁
*沒有拔模角度的垂直牆
*突然的幾何變化(角、孔等)
*羅紋設計不佳
*底切/懸垂
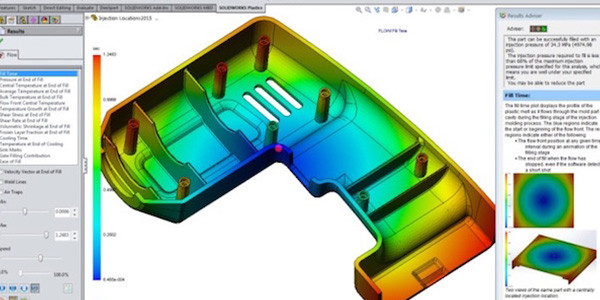
2.製作適合產品設計的工裝模具
技術精湛的機械師和模具製造商使用產品設計,為註塑機製造模具。 工裝模具(也簡稱為工具)是注塑機的心臟和靈魂。 它們經過精心設計,包含用於產品設計的陰腔和其他功能,例如澆口、流道、澆口、排氣孔、頂出系統、冷卻通道和移動部件。 工裝模具由特定等級的鋼和鋁製成,可以承受數万次(有時數十萬次)加熱和冷卻循環,例如 6063 鋁、P20 鋼、H13 鋼和 420 不銹鋼。 模具製造過程需要超過 20 週的時間才能完成,包括製造和批准,這使得該步驟成為註塑成型中最長的一個環節。 它也是注塑成型中最昂貴的部分,一旦製造出模具,就無法在不產生額外成本的情況下對其進行徹底更改。
3. 熔化塑料樹脂顆粒
操作員獲得成品模具後,將其插入註塑機,模具閉合,開始注塑循環。
塑料顆粒被送入料斗和桶中。 往復螺桿被拉回,使物料滑入螺桿和機筒之間的空間。 然後螺桿向前推進,迫使材料進入機筒並更靠近加熱帶,在那裡它熔化成熔融塑料。 根據材料規格,熔化溫度保持恆定,以便料筒或模具本身不會發生降解。
4. 使用壓力將熔化的顆粒注入模具
往復運動的螺桿迫使這種熔化的塑料通過噴嘴,該噴嘴位於模具的凹陷內,稱為模具澆口套。 移動壓板壓力將模具和噴嘴緊密貼合在一起,確保沒有塑料逸出。 熔化的塑料在這個過程中被加壓,使其進入模具型腔的所有部分,並通過模具通風口排出型腔中的空氣。
注塑機部件
注塑機的組成部分包括料斗、機筒、往復式螺桿、加熱器、活動壓板、噴嘴、模具和模腔。
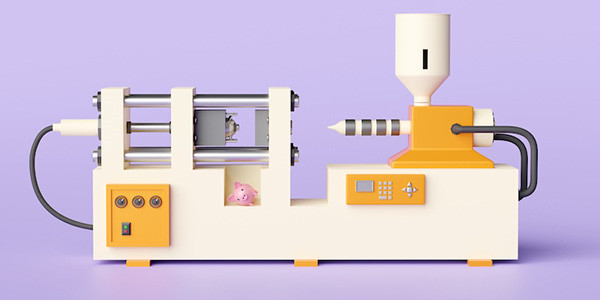
有關以下列表中每個注塑成型組件的更多信息:
*料斗: 將塑料顆粒送入機器的開口。
*桶: 注塑機的外殼,其中包含往復螺桿和塑料顆粒。 槍管被幾個加熱帶包裹著,頂端有一個加熱的噴嘴。
*往復螺桿: 開瓶器部件,在塑料材料熔化通過桶時輸送塑料材料並對其加壓。
*加熱器: 也稱為加熱帶,這些組件為塑料顆粒提供熱能,將它們從固體形式轉變為液體。 形式。
*活動壓板: 連接到模芯的移動部件施加壓力以保持兩個半模氣密,並在露出成品部件時釋放模芯。
*噴嘴: 加熱組件為熔融塑料提供進入模腔的標准出口,盡可能保持溫度和壓力穩定。
*模具: 包含模腔和附加支撐特徵(如頂針、流道通道、冷卻通道、通風孔等)的一個或多個組件。至少,模具分為兩半:固定側(靠近料筒)和模具芯(在移動壓板上)。
*模腔: 負空間,當充滿熔融塑料時,會將其塑造成所需的最終零件以及支撐、澆口、流道、澆口等。
注塑成型如何工作?
一旦塑料充滿了模具,包括澆口、流道、澆口等,模具就會保持在設定的溫度下,以使材料均勻凝固成零件形狀。 在冷卻的同時保持保壓,以阻止回流進入機筒並減少收縮效應。 在這一點上,更多的塑料顆粒被添加到料斗中以等待下一個循環(或發射)。 冷卻後,壓板打開並彈出成品零件,螺桿再次拉回,使材料進入機筒並重新開始該過程。
注塑成型循環通過這個連續的過程工作——關閉模具、餵入/加熱塑料顆粒、將它們加壓到模具中、將它們冷卻成固體部件、頂出部件,然後再次關閉模具。 該系統可實現塑料零件的快速生產,根據設計、尺寸和材料的不同,一個工作日內可製造超過 10,000 個塑料零件。
Djmolding 是中國的小批量注塑成型公司。我們的塑料注塑成型工藝可生產定制原型和最終用途生產零件,交貨時間快至 1 天,每年可生產多達 10000 個零件的小批量塑料注塑成型零件供應商