定制注塑成型
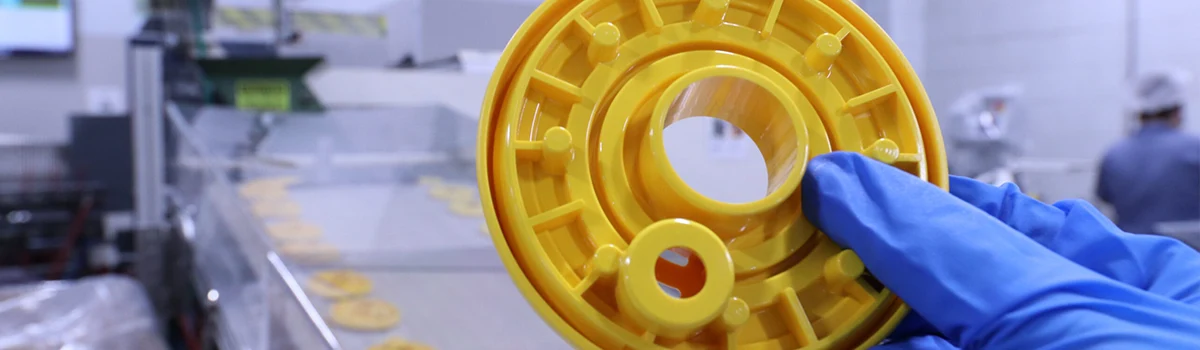
定制注塑成型是成功依賴於實現特定機械或美學特徵的塑料部件的理想選擇。 DJmolding 注塑成型的根本目標是幫助客戶生產最好的塑料零件。 對複雜性並不陌生,設計挑戰確實激發了我們為您創新的願望。 儘早讓我們參與進來使我們能夠在設計過程中增加價值。
注塑成型的好處
詳細功能
考慮美學或功能細節以提升您的品牌:壓印文字、裝飾性或紋理表面、模內裝飾、卡扣配合、靈活的鉸鏈、不同的硬度。
高效率
塑料注射成型的效率是無與倫比的。 我們從您的零件和工具中設計出不必要的成本。 我們長期任職的設計工程師和模塑大師在這方面非常擅長。
增強性能
我們努力了解您零件的預期功能,並通過應用材料科學、設計原理、分析工具和過程控制來滿足您的主要目標。
材質多樣
從 200 多種材料、商品和工程樹脂中進行選擇。 我們將幫助您平衡性能和價格,並確定替代材料等價物以降低成本。
注塑成型工藝
注塑成型是最古老的塑料製造方法之一,也是產品製造商零件開發的關鍵步驟。 對於希望將重金屬零件轉換為塑料的製造商來說,這也是一個很好的解決方案。 以最簡單的形式解釋,該過程使用聚合物或塑料樹脂,當加熱、熔化並在高壓下注入定制模具時,將生產用於產品製造的塑料部件。
雖然這個過程看起來很簡單,但實際上可能非常複雜,需要注塑合作夥伴具備高水平的經驗,以滿足您獨特的行業需求、規格、最終用途和時間/預算限制。 最好的起點是獲得塑料成型工藝和設計最佳實踐的基本知識。
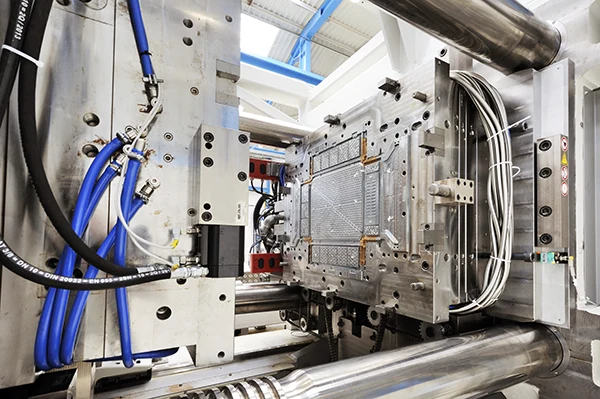
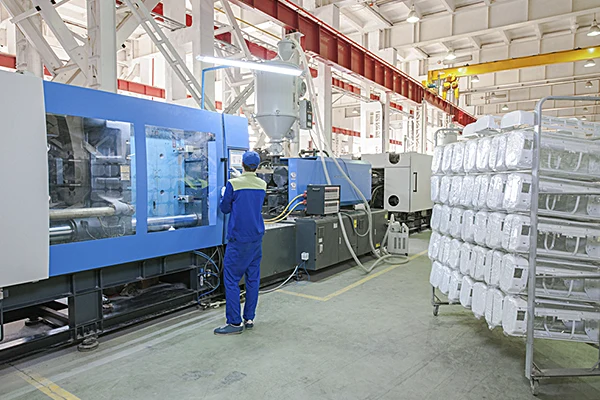
科學成型
科學的成型方法有利於生產需要特定性能和高精度的關鍵部件。 我們先進的成型技術確保了可重複性和一致性。 這意味著我們今天為您製造的產品,就是我們明天為您製造的產品。
科學的注塑成型始於模具開發。 優化壓力、溫度、型腔填充時間等因素,使模具設計最大限度地減少變化的機會。 模流分析顯示了要填充的零件的最后區域、材料如何隨模具定向以及暴露潛在的翹曲和應力點。 這是一個主動步驟,可提供工程預測分析和測量,並允許輕鬆確定零件或項目的成功或失敗。
穩健的生產流程進一步利用科學方法,通過監控和自動化流程控制減少廢料和加工時間。 如果發生變化或故障,會在製造不合格部件之前迅速識別和隔離。
包覆成型
兩種(或更多)材料可以通過包覆成型組合成一個零件。 此過程通常用於獨特的觸覺表面,例如較軟的抓握區域。 包覆成型可以是塑料基材上的塑料或塑料基材上的橡膠,通常通過二次注塑成型工藝完成。 樹脂配方和顏色可能會有所不同。 包覆成型的美學優勢很容易被注意到,但它們也消除了二次操作。 包覆成型非常適合帶把手的工具、手持物體、需要橡膠把手的機器人,或者只是用不同的顏色來增強零件的外觀。
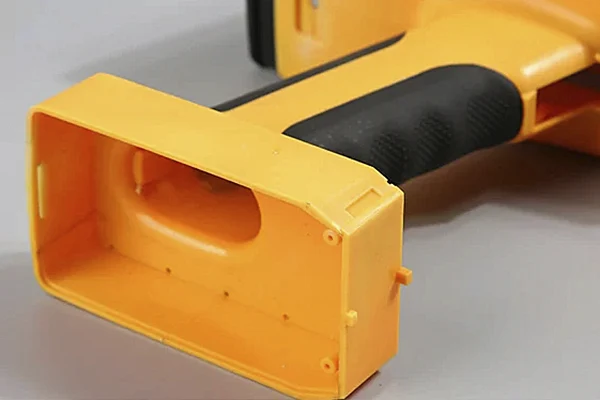
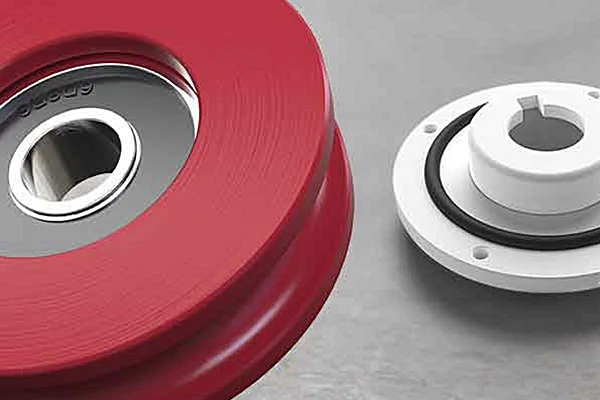
嵌件成型
嵌件成型類似於包覆成型,但包含放置在模腔內的物體。 嵌件成型將塑料粘合到嵌件上,通常是金屬或塑料。 螺紋嵌件很常見。 當用作緊固件、粘合劑或熱熔的替代品時,這消除了勞動力。 插入物也加強了部分。 插入物是手動裝載的或通過機器人自動化裝載的。
零件裝飾和標籤
模內裝飾 (IMD) 和模內貼標 (IML) 用於通過圖形或標籤創建視覺上引人注目的外觀。 在機器人技術和靜電或真空夾具的推動下,在註入熔融塑料樹脂之前,將印刷薄膜覆蓋層添加到模具型腔中。 這個過程在標籤和成品部件之間建立了永久的結合,通常不需要任何後處理操作。 廣泛的紋理、顏色和表面塗層選擇為創意的可能性敞開了大門。 我們鼓勵您與您的項目經理討論提升品牌的選項。
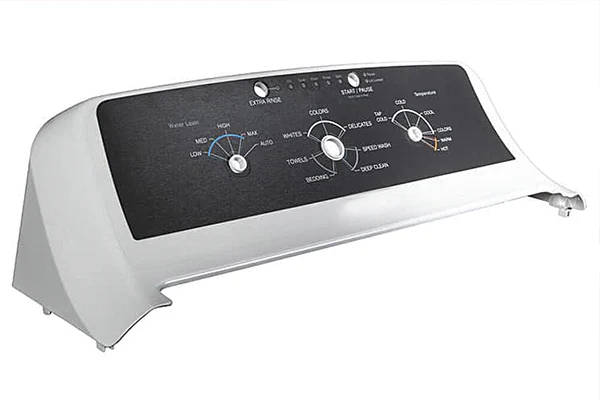
定制注塑成型服務中國
DJmolding 自 2010 年開始運營 | AFAQ ISO/TS 16949、UL 和 ISO 認證,目前主要供應給世界上許多 3D 打印公司。
在 Djmolding,我們專注於生產高品質塑料注塑件和模具。 我們主要為世界上許多 3D 打印公司提供塑料注射製造。 我們擁有 55 台用於機器人和自動塑料注射製造的機器。我們提供所有機加工和精加工服務,以使用各種材料製造工具,並且可以生產 100 到 200k+ 所有主要塑料的成品零件。 真正讓我們與眾不同的是我們先進的材料驗證、檢查和測試,以確保您的零件達到並超過您的最高期望。 立即聯繫我們的國際注塑成型專家獲取免費報價。
DJmolding 注塑成型工藝
一旦您的注塑模具準備就緒,成型過程包括以下基本步驟:
步驟 1. 塑料樹脂以原始顆粒形式出現。 這些被乾燥到合適的水分含量,然後如果需要,它們可以與顏料或母料著色劑混合。
步驟2.將乾燥的顆粒倒入成型機的料斗中。 機器機筒內的往復螺桿會將這些顆粒輸送到模具中。
步驟 3. 在桶內,將顆粒混合併加熱直至完全熔化,形成液態樹脂。
步驟 4. 加熱的模具自動關閉,樹脂在巨大壓力下通過澆口注入模腔。
步驟 5. 冷卻模具以固化內部零件。
第 6 步。模具打開,零件被頂出,開始新的循環。
注塑成型公差
所有塑料材料都會在熱量和水分的影響下膨脹和收縮。 我們的公差指南將提供有關典型零件特徵的最常見樹脂類型特性的更多一般信息。
我們將與您密切合作,優化您的製造設計。 我們將指出設計不當可能產生熱應力、收縮、翹曲等的任何區域。請參閱我們的設計指南以獲取有關常見缺陷以及如何避免這些缺陷的更多信息。
除非另有說明,否則我們符合 DIN 16742 注塑成型標準公差。 了解我們應用於注塑成型零件的視覺質量標準。
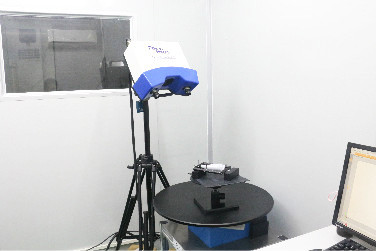
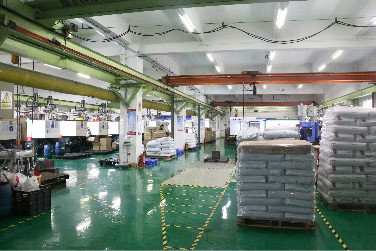
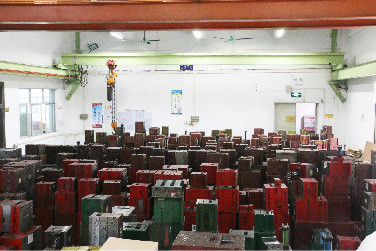
注塑成型材料
Djmolding 使用鋁 7075、P20 和 NAK80 半硬化鋼以及 H13 全硬化鋼製造注塑模具和模具。 此外,我們還提供標準 SPI 飾面、EDM 紋理和一系列蝕刻紋理。
對於某些應用,這些材料類型中的每一種都具有明顯的優勢。 *注意事項包括:
*原材料成本
*耐久性和耐腐蝕或耐磨性
*可加工性
*能夠進行高表面拋光
*熱處理所需時間
*預期刀具壽命
聯繫我們的技術專家,詳細了解哪一款適合您。
注塑件
有數以千計的熱成型和熱固性塑料可供您的項目選擇。 此外,還可以通過添加玻璃纖維、紫外線穩定劑和潤滑劑等添加劑來增強機械和化學特性。 我們的材料表將為您提供有關標準類型和每種標準類型的預期公差的更多詳細信息。
您對樹脂的選擇可能取決於以下一項或多項考慮因素:
*抗紫外線、化學、耐磨和抗衝擊
*原材料成本
*機械強度
*重量和密度
*靈活性
*透明度
*可回收性
聯繫我們的一位技術專家,了解有關材料特性的更多信息。
DJmolding注塑車間:
領先的注塑模具和快速成型服務製造商
Djmolding是中國較知名的注塑成型公司之一。 我們的注塑車間配備了50台高精度注塑機,從30噸到800噸,它們大多從台灣和日本進口,我們的注塑車間每週24天,每天7小時運行,並提供生產服務。
我們在許多工業領域的各種塑料產品方面經驗豐富,包括:汽車、醫療、照明、運動器材、家用電器和農業。 Djmolding 自 16949 年以來已通過 AFAQ ISO/TS 9001、UL 和 ISO 2010 認證,我們還有 15 名 IPQC 人員不斷觀察我們的生產並檢查零件質量,這確保我們的生產保持最高水平的質量。 在過去的 9 年中,Djmolding 在以合理的價格生產高質量工具和零件方面建立了良好的聲譽。我們與 appx 保持著牢固的業務關係。 50個客戶,主要來自美國和歐洲。
定制注塑成型
定制塑料注射成型是一種生產高質量塑料零件的創新且高效的方法。 這種製造工藝使用模具將塑料材料塑造成複雜的形狀和尺寸,使其成為各行各業的理想解決方案。 這篇博文將深入探討定制塑料注塑成型並探討其優勢、應用和最佳實踐。
了解定制注塑工藝
定制注塑成型是一種用於大批量生產塑料零件的製造工藝。 它涉及熔化塑料顆粒或顆粒,然後在高壓下將它們注入模具中,在那裡它們冷卻並固化以形成所需的形狀。 以下是注塑成型過程的工作原理:
- 夾緊:模具的兩半,稱為“工具”,用足夠的力夾緊在一起以承受注射壓力。
- 注射:塑料顆粒在加熱的桶中熔化,並在高壓下通過流道系統注射到模具中。 塑料填充模腔並形成模具的形狀。
- 冷卻:塑料可以在模具內冷卻凝固以保持所需的形狀。
- 頂出:塑料冷卻後模具打開,成品部件被頂出。
- 重複:然後重複該過程以創建多個相同的零件。
注塑成型生產塑料產品,從小部件到汽車零件和家用電器等大型物品。 該工藝非常高效,可以生產具有復雜幾何形狀和嚴格公差的零件,而且非常精確,浪費最少,廢品率低。
該過程需要專用設備,包括模具、注塑機和控制系統,以確保准確和一致的結果。 模具通常由鋼製成,可以設計為使用多腔成型生產多個零件。
注塑成型還可用於各種材料,包括熱塑性塑料、熱固性塑料和彈性體。 每種材料都具有獨特的特性,可以針對特定應用進行定制。
總體而言,注塑成型是一種用途廣泛且高效的製造工藝,廣泛應用於許多行業。
定制注塑成型的優勢
定制塑料注射成型是一種用於大批量生產定制塑料零件的製造工藝。 以下是此過程的一些優點:
高效率和生產力: 定制塑料注射成型是一種高效的工藝,可以快速、一致地生產大量相同的零件。 這使其成為批量生產塑料零件的理想選擇。
多功能性: 該工藝可用於多種塑料材料,包括熱塑性塑料、熱固性塑料和彈性體。 這允許各種各樣的零件設計和應用。
一致性和精確性: 注塑成型提供一致和精確的結果,具有嚴格的公差和零件之間的最小變化。 這確保了每一件都與下一件相同,這對於許多應用程序來說都是必不可少的。
具有成本效益:定制塑料注射成型對於大批量生產運行具有成本效益。 初始加工成本可能很高,但隨著體積的增加,每個零件的成本會降低。
複雜: 注塑成型可以生產具有復雜形狀和幾何形狀的零件,包括薄壁和復雜的特徵。 這允許更大的設計靈活性,並能夠生產使用其他方法難以或不可能生產的因素。
最少的浪費: 與其他製造工藝相比,注塑成型產生的廢物最少,因為任何多餘的塑料都可以回收再利用。
表面處理: 注塑成型可以生產具有高質量表面光潔度的零件,而無需額外的後處理或精加工操作。 這使它成為一種具有成本效益的解決方案,可用於創建具有光滑和拋光外觀的作品。
自動化: 注塑成型可以很容易地實現自動化,機器人可以從模具中裝載和卸載零件以及檢查和分類功能。 這減少了對體力勞動的需求並提高了效率。
定制塑料注射成型是一種高度通用且高效的製造工藝,與其他方法相比具有許多優勢。 它能夠快速準確地生產大量相同的零件,這使其成為許多行業的理想選擇,包括汽車、航空航天、醫療和消費品。
注塑成型的應用
注塑成型是一種廣泛用於製造各種工業塑料產品的製造工藝。 以下是注塑成型的一些最常見應用:
- 汽車工業:注塑生產各種汽車零部件,包括內外飾件、儀表板部件、門把手和發動機部件。 它是優選的,因為它可以具有高強度和尺寸精度的特徵。
- 消費品:注塑成型可製造各種消費品,包括玩具、家用電器和電子設備。 它允許生產複雜的形狀和幾何形狀以及高質量的表面光潔度。
- 醫療器械:注塑成型用於生產各種醫療器械,包括注射器、IV 組件和診斷設備。 它提供高精度、清潔製造以及生產具有復雜幾何形狀的零件的能力,這在醫療行業中是必不可少的。
- 包裝行業:注塑成型生產包裝材料,包括瓶子、罐子和蓋子。 它允許創建輕巧耐用的容器並自定義顏色、紋理和形狀。
- 航空航天工業:注塑成型用於生產航空航天零件的各種組件,包括結構元件和內部配件。 它允許創建能夠承受極端溫度和壓力的高性能材料。
- 建築行業:注塑成型生產各種建築材料,包括 PVC 管道、排水溝系統和屋頂材料。 它具有高耐用性、耐候性和耐化學性,並且能夠大批量生產零件。
- 電子工業:注塑成型生產各種電子元件,包括外殼、連接器和開關。 它提供高精度、均勻性以及生產具有復雜幾何形狀的零件的能力,這在電子行業中是必不可少的。
總的來說,注塑成型是一種多功能的製造工藝,可以為許多行業生產許多塑料零件。 它能夠生產具有復雜幾何形狀、高精度和一致質量的零件,使其成為許多製造商的熱門選擇。
注塑成型中使用的材料類型
注塑成型是一種製造工藝,涉及將熔融塑料注入模具型腔以形成特定形狀。 根據最終產品的所需特性,可在註塑成型中使用不同的材料。 以下是注塑成型中使用的一些最常見的材料類型:
- 熱塑性塑料:這些是注塑成型中最常用的材料。 它們是一種塑料,加熱時變得柔軟且可塑,冷卻時變硬。 熱塑性塑料可以多次模塑和重塑而不會失去其性能。 注塑成型中常用的熱塑性塑料包括聚丙烯、聚乙烯、聚苯乙烯和尼龍。
- 熱固性塑料:這些塑料只能成型一次。 它們被加熱並發展成特定的形狀,一旦硬化,就無法重塑。 熱固性塑料用於需要高強度和耐用性的應用。 注塑成型中常用的熱固性樹脂包括環氧樹脂、三聚氰胺樹脂和酚醛樹脂。
- 彈性體:這些材料具有彈性,可以拉伸並恢復到原來的形狀。 彈性體用於需要柔韌性和減震性的應用。 注塑成型中使用的標準彈性體包括橡膠、矽膠和聚氨酯。
- 可生物降解材料:這些材料可以在環境中自然分解而不會留下有害殘留物。 它們用於環境可持續性受到關注的應用。 注塑成型中常用的可生物降解材料包括聚乳酸 (PLA) 和聚羥基脂肪酸酯 (PHA)。
- 複合材料是通過組合兩種或多種不同材料製成的材料,以創建具有特定特性的新材料。 複合材料用於需要高強度和剛度的應用。 用於注塑成型的標準複合材料包括玻璃纖維增強塑料 (GRP) 和碳纖維增強塑料 (CFRP)。
- 金屬填充塑料是注入金屬顆粒的塑料,可製成具有高導電性和導熱性以及其他特定性能的材料。 金屬填充塑料用於具有必要的導電或導熱性的應用。 注塑成型中常用的金屬填充塑料包括銅填充塑料和鎳填充塑料。
總的來說,注塑材料的選擇取決於最終產品的具體要求,包括強度、柔韌性、導電性和耐用性。 製造商通常根據成本、可用性、加工難易程度以及最終產品所需的特性來選擇材料。
選擇注塑材料時要考慮的因素
選擇合適的材料對於注塑成型至關重要,因為它會影響最終產品的特性和性能。 以下是選擇注塑材料時需要考慮的一些因素:
- 機械性能:選擇材料時要考慮的最重要因素之一是其機械性能。 這包括它的強度、剛度、韌性和耐磨性。 最終產品所需的機械性能將取決於應用和產品將承受的應力。
- 熱性能:材料的熱性能也很重要,尤其是當最終產品將暴露於高溫或熱循環時。 這包括材料的熔點、熱導率和熱膨脹係數。
- 耐化學性:如果最終產品暴露於化學品,則選擇能夠抵抗化學降解的材料至關重要。 該材料應能承受酸、鹼、溶劑和其他化學品的暴露,而不會分解或失去其特性。
- 環境因素:濕度和紫外線照射等環境因素也會影響材料的特性和性能。 必須考慮最終產品的環境條件並選擇能夠承受這些條件的材料。
- 成本:材料的成本也是一個重要的考慮因素,特別是對於大批量生產。 應根據材料的性能和特性權衡材料的成本,以確保它是最終產品的具有成本效益的選擇。
- 加工要求:材料的加工要求也會影響選擇過程。 有些材料可能需要特定的加工設備或技術,有些可能更難加工。 應考慮加工要求,以確保材料能夠成功用於注塑成型過程。
- 法規遵從性:最後,必須考慮最終產品必須滿足的任何法規要求。 一些行業,例如醫療和食品行業,對其產品中使用的材料有特定的規定。 選擇滿足這些法規要求的材料對於確保最終產品安全且合規至關重要。
總的來說,選擇合適的注塑成型材料需要仔細考慮各種因素,包括機械和熱性能、耐化學性、環境因素、成本、加工要求和法規遵從性。 製造商必須相互權衡這些因素,以選擇最適合最終產品的材料。
模具設計在註塑成型中的重要性
模具設計是注塑成型工藝的一個關鍵方面。 模具的設計會影響最終產品的質量,以及製造過程的效率和成本效益。 以下是模具設計在註塑成型中必不可少的一些原因:
- 產品質量:模具的設計會影響最終產品的質量。 如果模具設計不當,可能會導致翹曲、縮痕和飛邊等缺陷。 這些缺陷會使最終產品無法使用、降低性能並增加報廢率和生產成本。
- 製造效率:模具的設計也會影響製造過程的效率。 如果模具未針對最佳流動和冷卻進行設計,則可能會導致循環時間延長、能耗增加和產量降低。 優化的模具設計可以提高效率並降低生產成本。
- 成本效益:模具設計也會影響注塑工藝的成本效益。 設計良好的模具可以減少材料浪費,提高零件質量,增加產量,降低生產成本。 此外,專為大批量生產而設計的模具可以降低每個零件的成本並提高投資回報率。
- 定制:模具設計在最終產品的定制中也起著至關重要的作用。 通過針對特定形狀和特徵設計模具,製造商可以製造出滿足客戶需求的產品。 這允許市場具有更大的靈活性和差異化,從而提高客戶滿意度和忠誠度。
- 材料選擇:模具設計也會影響注塑成型所用材料的選擇。 成型方法會影響材料的流動和冷卻,從而影響最終產品的機械和熱性能。 通過選擇正確的模具設計,製造商可以優化材料選擇並確保最終產品滿足所需的性能要求。
總的來說,模具設計是注塑成型過程中的一個關鍵因素。 設計良好的模具可以提高產品質量、製造效率、成本效益、定制化和材料選擇。 製造商必須投入時間和資源來設計優化的模具以滿足他們的特定需求,以在註塑成型過程中獲得最佳結果。
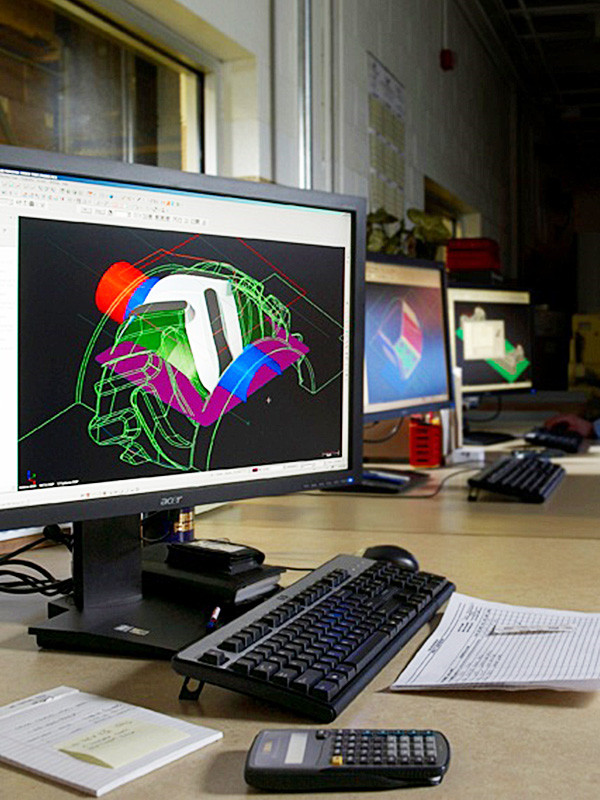
注塑成型中使用的不同類型的模具
注塑成型是一種用途廣泛的製造工藝,可以生產各種塑料製品。 決定注塑成型質量和效率的一個關鍵因素是所用模具的類型。 以下是注塑成型中使用的一些不同類型的模具:
- 雙板模具:雙板模具是注塑成型中最常用的模具。 它們由兩個由模腔隔開的板組成。 將塑料材料注入型腔,將兩塊板結合起來形成最終產品。
- 三板模具:三板模具類似於兩板模具,但有一個額外的板將流道系統與成型零件隔開。 這樣可以更輕鬆地彈出零件並縮短循環時間。
- 熱流道模具:熱流道模具用於大批量生產,因為它們可以減少週期時間和材料浪費。 該模具包含一個加熱流道系統,可將熔融塑料直接輸送到模具型腔,無需冷流道。
- 冷流道模具:冷流道模具是最基本的模具類型,由澆口、流道和模具型腔組成。 熔融塑料被注入澆口,澆口將塑料送入流道,然後進入模具型腔。
- 家庭模具:家庭模具在一個週期內生產多個零件。 模具包含多個型腔,每個型腔都有不同的部分。 家庭模具通常用於小型、大批量的部件。
- 堆疊模具:堆疊模具在一個循環中生產多層塑料。 模具包含許多層腔,這些腔層層疊疊。 將塑料注入孔中,然後將各層組合在一起形成一個單一的多層產品。
- 嵌件模具:嵌件模具用於在成型過程中將金屬或塑料部件插入成型零件中。 在註入塑料之前,將嵌件放入模腔中,然後塑料將嵌件包圍起來。
總的來說,注塑成型中使用的模具類型取決於所生產產品的具體要求。 通過選擇正確的模具類型,製造商可以優化注塑工藝的效率、質量和成本效益。
注塑成型的最佳實踐
注塑成型是一個複雜的製造過程,需要仔細規劃和執行才能達到預期的結果。 以下是一些有助於確保最佳質量、效率和成本效益的注塑成型最佳實踐:
- 可製造性設計:產品的設計應針對注塑成型進行優化。 這包括最大限度地減少零件數量、確保均勻的壁厚以及避免底切和其他使成型複雜化的特徵。
- 材料選擇:注塑成型所用的材料應根據產品的要求來選擇。 應考慮機械性能、熱性能和耐環境性等因素。
- 模具設計:模具設計應針對特定產品進行優化。 這包括確保適當的冷卻、排氣和澆口,以及選擇合適的模具類型。
- 注射參數:應仔細控制和監測注射參數,如注射壓力、溫度和速度,以確保最佳質量和一致性。
- 維護:定期對注塑機和模具進行維護對於確保最佳性能和防止停機至關重要。
- 質量控制:質量控制應貫穿整個注塑過程,從進料檢驗到最終產品檢驗。 這包括監控翹曲、縮痕和飛邊等缺陷。
- 工藝優化:持續的工藝改進應該是注塑成型操作的重點。 這包括監控流程性能指標,如周期時間、廢品率和機器利用率,並根據需要進行調整以優化效率和質量。
總的來說,注塑成型需要仔細關注細節並專注於持續改進。 通過遵循注塑成型的最佳實踐,製造商可以確保最佳質量、效率和成本效益,並生產出滿足客戶需求的高質量塑料產品。
注塑成型的質量控制措施
質量控制對注塑成型至關重要,因為它確保最終產品符合要求的規格和標準。 以下是注塑成型的一些質量控制措施:
- 來料檢驗:質量控製過程應從審查用於注塑成型的原材料開始。 這包括驗證材料的類型、等級和顏色是否正確,並滿足所需的機械和熱性能規格。
- 過程中檢查:在註塑過程中,質量控制人員應定期檢查產品以確保其正確成型。 這包括監控縮痕、翹曲和飛邊等缺陷,並驗證產品是否滿足所需的尺寸公差。
- 最終產品檢驗:注塑成型過程完成後,應對最終產品進行檢驗,以確保其符合規定的規格和標準。 這包括驗證產品沒有缺陷,例如裂紋、氣泡和空隙,並滿足所需的尺寸公差。
- 統計過程控制:統計過程控制 (SPC) 是一種監視和控製過程以確保其產生始終如一的高質量結果的方法。 SPC 涉及收集關鍵工藝參數的數據,例如注射壓力和溫度,並使用統計分析來識別表明工藝可變性的趨勢和模式。
- 持續改進:質量控制應該是一個不斷改進的持續過程。 這包括分析有關流程性能的數據,確定需要改進的領域,以及對流程進行更改以優化質量和效率。
- 文件記錄和可追溯性:質量控制人員應保存注塑成型工藝的詳細文件,包括工藝參數、檢查結果和糾正措施。 該文檔提供可追溯性,有助於確保可以快速識別和糾正任何質量問題。
總的來說,質量控制是注塑成型的一個關鍵方面,應該融入製造過程的各個方面。 通過實施這些質量控制措施,製造商可以生產出滿足客戶需求的優質塑料產品。
注塑成型常見缺陷及預防方法
注塑成型是一個複雜的過程,如果執行不當可能會導致缺陷。 以下是注塑成型中的一些常見缺陷及其預防方法:
- 縮痕是產品表面的凹陷或凹痕。 它們是由冷卻不均勻或保壓壓力不足引起的。 確保模具設計包括均勻的壁厚和足夠的拔模角以防止縮痕。 調整保壓壓力和冷卻時間也有助於防止縮痕。
- 翹曲:翹曲是產品從模具中取出後的變形。 這是由於產品冷卻不均勻或內部應力造成的。 為防止翹曲,確保模具設計包括均勻的壁厚和足夠的冷卻時間。 避免尖角或產品幾何形狀的突然變化,這會產生應力點。
- 飛邊:飛邊是超出產品邊界的多餘塑料,通常出現在模具邊緣周圍。 這是由於注射壓力過大、合模力不足或模具磨損造成的。 為防止飛邊,調整注射壓力和鎖模力並定期檢查模具是否有磨損跡象。
- 短射:當模具部分填充塑料時,就會出現短射。 這可能是由於注射壓力或溫度不足或流動通道堵塞或受限造成的。 為防止短射,調整注射壓力和溫度,保證流道暢通無阻。
- 燒痕:燒痕是由於模具過熱或過度摩擦造成的產品表面的深色變色。 為防止燒痕,確保模具充分冷卻和潤滑,並根據需要調整注射速度和壓力。
- 空隙和氣泡:空隙和氣泡是缺少材料或含有氣泡的產品區域。 它們是由模具中滯留的空氣或氣體或材料流動不足引起的。 為防止空隙和氣泡,確保模具排氣正確,注射速度和壓力足以確保均勻的材料流動。
注塑設備保養小貼士
注塑設備對製造商來說是一項重大投資,適當的維護對於確保最佳性能和使用壽命至關重要。 以下是注塑設備的一些維護技巧:
- 進行定期檢查:定期檢查設備以發現任何磨損、損壞或其他問題。 檢查液壓軟管、密封件和其他關鍵部件,確保它們處於良好狀態。
- 清潔和潤滑設備:定期清潔和潤滑設備,以防止腐蝕和磨損。 使用推薦的清潔和潤滑產品,並遵循製造商的說明。
- 監控和維護液壓油:定期監控以確保其清潔且粘度正確。 根據需要更換機油,並使用推薦的機油類型。
- 維護加熱帶:定期檢查它們以確保它們處於良好狀態並正確加熱。 立即更換任何損壞或磨損的加熱帶。
- 監控和維護冷卻系統:它對注塑成型至關重要,因為它可以防止過熱和翹曲。 定期監控冷卻系統以確保其正常運行,並根據需要清潔冷卻通道。
- 培訓操作員:對操作員進行正確的設備操作和維護程序培訓,以防止損壞並確保最佳性能。
- 安排定期維護:制定維護計劃並堅持執行。 安排例行維護任務,例如潤滑和換油,並記錄所有維護活動。
- 準備好備件:提供備件,例如液壓軟管、密封件和加熱帶。 這將快速更換損壞或磨損的零件並最大限度地減少停機時間。
正確維護注塑設備對於確保其高效運行、生產高質量產品和延長使用壽命至關重要。 通過遵循這些維護技巧,製造商可以使他們的設備保持最佳狀態,並最大限度地減少停機時間和維修成本。
如何選擇合適的注塑廠家
選擇合適的注塑成型製造商是一個重要的決定,它會顯著影響產品的質量和成本。 以下是選擇注塑製造商時需要考慮的一些因素:
- 經驗和專業知識:尋找在註塑成型方面具有豐富經驗和專業知識的製造商。 詢問他們的製造過程、質量控制措施和認證。
- 技術和設備:尋找使用現代技術和設備的製造商。 這有助於確保一致的質量、更短的交貨時間和成本效益。
- 材料和能力:考慮製造商可以使用的材料類型及其能力。 尋找可以處理各種材料(包括專用材料)並且可以生產各種尺寸和形狀的產品的製造商。
- 質量控制措施:尋找非常注重質量控制的製造商。 詢問他們的質量控制措施,例如檢查和測試程序,以及他們可能擁有的任何證書。
- 客戶服務:尋找提供優質客戶服務的製造商。 考慮響應能力、溝通能力以及與您合作以滿足您的特定需求的意願。
- 成本和交貨時間:考慮製造商為您的項目提供的成本和交貨時間。 尋找能夠提供具有競爭力的價格和符合您要求的實際交貨時間的製造商。
- 參考資料和評論:索取參考資料並查看製造商的在線評論。 這可以幫助您更好地了解他們的聲譽和其他客戶的體驗。
通過考慮這些因素並進行深入研究,您可以為您的項目選擇合適的注塑成型製造商。 具有適當經驗、能力和對質量承諾的信譽良好的製造商可以幫助確保您的產品高效、經濟地生產並符合您的確切規格。
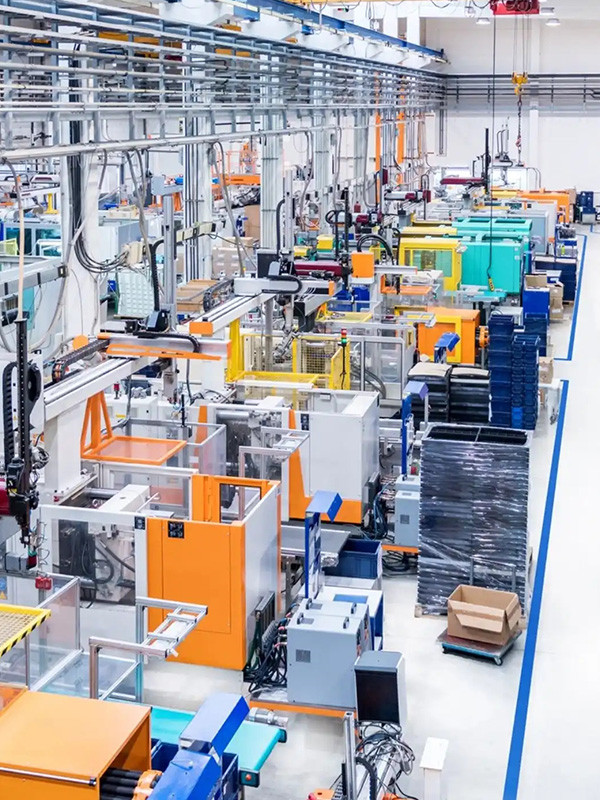
定制塑料注射成型的成本考慮
定制塑料注射成型是一種高度通用的製造工藝,可以大規模生產複雜、高質量的零件。 然而,成本考慮是使用該製造工藝的關鍵因素。 以下是定制塑料注塑成型的一些關鍵成本考慮因素:
- 材料成本:注塑過程中使用的材料類型和數量會影響價格。 一些材料,例如高性能工程塑料,比其他材料更貴。 材料成本也會受到供應鏈中斷、市場需求和價格波動的影響。
- 工具成本:工具或用於生產零件的模具的成本是定制塑料注塑成型中的一項重要費用。 零件的複雜性、模具中的型腔數量以及製造模具所用的材料都會影響模具成本。 工具的前期成本可能很高,但隨著時間的推移可以通過提高生產效率來幫助降低單位成本。
- 生產量:生產的零件量將影響注塑成型成本。 大批量生產有助於降低單位成本,而小批量生產可能由於需要更多的工具和設置時間而具有更高的單位成本。
- 勞動力成本:勞動力成本是注塑成型的一個重要因素,特別是對於需要更多體力勞動的更複雜的零件。 操作員的技能水平和零件的複雜性會影響交付成本。
- 質量控製成本:保持質量控制對於確保零件的完整性至關重要。 質量控制的價格可以包括檢驗設備、測試和人工。
- 運輸成本:將零件運送到客戶或其他地點可能是一筆不菲的費用,尤其是對於大型或重型零件。
製造商可以通過考慮這些成本因素並優化注塑成型工藝,以更低的成本生產高質量的零件。 這可以通過減少材料浪費、提高生產效率以及最大限度地減少設置和轉換時間來實現。 與經驗豐富、知識淵博的注塑製造商合作也有助於優化流程並降低成本。
注塑技術的趨勢和創新
注塑成型技術已經存在多年,但仍有許多創新和趨勢塑造著這一製造工藝的未來。 以下是注塑成型技術的一些主要趨勢和創新:
- 3D 打印和增材製造:3D 打印和增材製造在註塑行業越來越受歡迎。 該技術允許創建傳統注塑成型難以或不可能實現的複雜形狀和幾何形狀。
- 多材料注塑成型:多材料注塑成型允許在一次注射中創建具有多種材料或顏色的零件。 這個過程可以減少製造時間和成本,並創造出具有獨特性能和外觀的功能。
- 自動化和工業 4.0:自動化和工業 4.0 技術,例如物聯網傳感器和機器人技術,正在被集成到注塑機和工藝中。 這可以提高生產效率,降低人工成本,並改善質量控制。
- 可持續材料和工藝:隨著公司尋求減少對環境的影響,可持續材料和方法在註塑行業變得越來越重要。 這包括使用可生物降解或回收的材料和工藝,最大限度地減少浪費和能源消耗。
- 智能製造和預測性維護:機器學習和預測性維護等智能製造技術正被用於優化注塑成型工藝並減少停機時間。 這可以提高整體效率並降低維護成本。
- 高性能材料:正在開髮用於注塑成型的新型高性能材料,包括具有更高強度、耐用性和耐熱性的材料。 這些材料可用於從汽車零件到醫療設備的各種應用。
通過緊跟這些趨勢和創新,注塑製造商可以保持競爭力並繼續為客戶提供高質量的零件。 隨著新技術和材料的開發,注塑成型行業將繼續發展和適應消費者和企業不斷變化的需求。
注塑成型的可持續性:減少浪費和能源消耗
隨著公司尋求減少對環境的影響並滿足對環保產品不斷增長的需求,可持續性在註塑行業變得越來越重要。 以下是注塑成型製造商可以減少浪費和能源消耗的一些方法:
- 使用可持續材料:材料的選擇是可持續性的關鍵因素。 注塑成型製造商可以使用可生物降解或回收材料來減少對環境的影響。 例如,可生物降解的塑料可以隨著時間的推移自然分解並減少垃圾填埋場的廢物量。 回收材料,如消費後回收塑料,也有助於減少浪費和能源消耗。
- 減少材料浪費:注塑製造商還可以通過優化零件和模具的設計來減少材料浪費。 這包括減少多餘材料的使用量,最大限度地減少模具中的型腔數量,以及減輕零件的總重量。 通過減少材料浪費,製造商可以節省材料成本並減少對環境的影響。
- 優化生產效率:注塑製造商可以優化其生產流程以降低能耗。 這包括使用高效注塑機、優化成型工藝參數以及最大限度地減少停機時間。 通過減少能源消耗,製造商可以節省能源成本並減少碳足跡。
- 實施可持續實踐:注塑成型製造商還可以在其運營中實施可持續實踐,例如回收和減少廢物計劃、使用可再生能源以及促進員工和供應商的可持續發展。 通過在整個供應鏈中推廣可持續實踐,製造商可以幫助創建一個整體上更具可持續性的行業。
- 使用可持續包裝:最後,注塑製造商可以使用可持續包裝材料和設計來減少浪費和環境影響。 這包括使用可生物降解或可回收的包裝材料,最大限度地減少包裝浪費,以及設計可重複使用或可重新填充的包裝。
通過實施這些可持續實踐,注塑成型製造商可以減少對環境的影響,並打造一個更具可持續性的整體行業。 隨著可持續性對消費者和企業越來越重要,將可持續性放在首位的注塑製造商將能夠很好地滿足對環保產品日益增長的需求。
定制塑料注射成型與其他製造工藝相比如何
定制塑料注射成型是一種流行的製造工藝,用於大批量生產高質量的塑料零件。 然而,其他幾種製造工藝也可用於製造塑料部件,各有優缺點。 以下是定制塑料注射成型與其他製造工藝的比較:
- 3D 打印:3D 打印是一項快速發展的技術,可以創建複雜的形狀和幾何形狀。 雖然 3D 打印可用於小規模生產,但在生產大型零件時,注塑成型的成本效益和效率通常低於注塑成型。
- 吹塑成型:吹塑成型是一種製造空心塑料部件(例如瓶子和容器)的製造工藝。 雖然吹塑成型適用於生產大量特徵,但注塑成型通常不如注塑成型精確,並且可能不適合創建更複雜的形狀和幾何形狀。
- CNC 加工:CNC 加工是一種減材製造工藝,涉及從實心材料塊切割和成型零件。 雖然 CNC 加工適用於小批量生產高精度零件,但它通常不如注塑成型那樣具有成本效益或效率。
- 旋轉成型:旋轉成型是一種製造過程,涉及在加熱模具的同時圍繞兩個垂直軸旋轉模具。 雖然旋轉成型可以生產具有復雜幾何形狀的大型零件,但注塑成型通常不如注塑成型精確,可能不適合製造較小的零件。
- 熱成型:熱成型是一種製造過程,涉及加熱塑料片,然後在模具上對其進行成型。 雖然熱成型可以生產具有簡單幾何形狀的大型零件,但注塑成型通常不如注塑成型精確,並且可能不適合創建更複雜的形狀和幾何形狀。
定制塑料注射成型是一種用途廣泛且具有成本效益的製造工藝,可用於大批量生產高質量的塑料零件。 雖然其他製造工藝可能更適合特定應用或生產量,但由於其速度、精度和成本效益,注塑成型通常是許多製造商的首選。 最終,製造工藝的選擇將取決於各種因素,包括零件設計、生產量和預算。
外購注塑的優缺點
對於希望在不投資自己的注塑設備或專業知識的情況下生產塑料零件的公司來說,外包注塑是一種常見的做法。 雖然外包可以提供一些好處,但它也有一些潛在的缺點。 以下是外包注塑成型的一些優缺點:
優點:
- 節省成本:外包注塑通常比建立內部生產設施更具成本效益。 對於需要更多資金或數量來證明投資昂貴的設備和人員的中小型公司來說尤其如此。
- 專業知識:注塑成型公司專注於製造,並擁有確保按照高質量標準生產零件的專業知識。 通過外包注塑成型,公司可以從經驗豐富的專業人員的專業知識中獲益。
- 能力:注塑公司可以快速高效地生產大量零件。 這對於必須定期製作大量功能的公司尤其有利。
- 靈活性:外包注塑成型可讓公司在生產計劃中更加靈活。 公司可以調整他們的產量或切換到不同的部分,而不用擔心更換設備和模具的資本成本。
缺點:
- 溝通:外包注塑成型會給客戶和公司之間的溝通帶來挑戰。 誤解或溝通延遲可能會導致錯誤或生產延誤。
- 質量控制:外包注塑意味著依靠外部公司生產符合要求質量標準的零件。 與外部公司合作時,質量控制可能具有挑戰性,並且總是存在收到必須滿足要求的規格的功能的風險。
- 依賴性:外包注塑意味著依賴於外部生產公司。 這會給供應商的可靠性、穩定性和交貨時間帶來風險。
- 知識產權:外包注塑成型會給保護知識產權帶來風險。 公司需要確保其設計和技術受到適當法律措施的保護。
定制塑料注射成型的未來前景
幾十年來,定制塑料注射成型一直是一種可靠且用途廣泛的製造工藝。 近年來,技術和材料的進步不斷提升注塑成型的能力和潛力。 以下是定制塑料注塑成型的一些未來前景:
- 採用工業 4.0 技術:人工智能、機器學習和物聯網 (IoT) 等工業 4.0 技術的集成有望提高自動化程度、改善質量控制並優化注塑成型的生產流程。
- 越來越多地使用可生物降解材料:環境問題促使在註塑成型中採用可生物降解材料。 可生物降解材料是傳統塑料的可持續替代品,有助於減少浪費和環境影響。
- 對醫療器械製造的需求不斷增長:由於人口老齡化和醫療技術的進步,對醫療器械的需求正在增加。 由於其精度、速度和成本效益,注塑成型是一種流行的醫療設備製造工藝。
- 3D 打印能力的擴展:3D 打印技術的發展使得以前無法使用注塑成型製造的複雜零件成為可能。 然而,與註塑成型相比,3D 打印仍然相對緩慢且昂貴,這兩種技術可能會繼續相互補充而不是相互替代。
- 增加多材料注射成型:多材料注射成型涉及在單個注射成型過程中使用兩種或更多種不同的材料。 該技術具有多項優勢,包括提高零件性能、減輕重量和節約成本。
- 模具技術的進步:新模具材料和設計的開發有望提高注塑成型的速度、效率和精度。 例如,工具中的隨形冷卻通道可以縮短循環時間並降低能耗。
結論:
定制塑料注塑成型是一種穩健的製造工藝,能夠以極高的精度和效率生產高質量的塑料零件。 通過了解注塑成型工藝、選擇合適的材料和模具設計以及實施質量控制和設備維護的最佳實踐,企業可以優化其註塑成型操作並取得巨大成功。 隨著行業中出現新趨勢和創新,保持最新狀態並探索新機會以提高定制塑料注塑成型的可持續性、效率和盈利能力至關重要。