塑膠射出成型
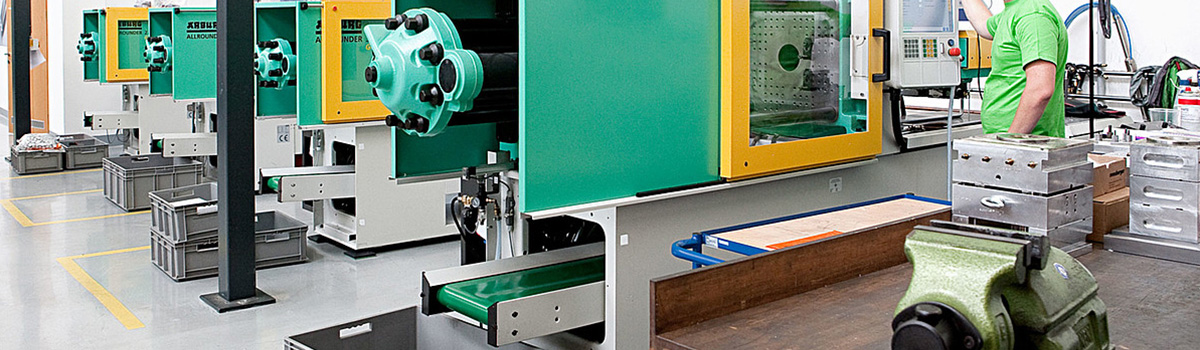
塑料注射成型是一種製造過程,涉及熔化塑料顆粒並將其註入模具型腔以創建三維物體。 這個過程從許多產品開始,從小型精密零件到重要的汽車零部件。 與其他製造工藝相比,塑料注射成型具有許多優勢,包括高生產率、設計靈活性和成本效益。 本指南將深入探討塑料注射成型並探討其各種應用、優勢和局限性。
注塑成型的歷史
塑料注射成型是一種製造過程,涉及將熔融塑料注入模具型腔以形成特定形狀。 塑料注射成型的歷史可以追溯到 1800 年代後期,當時賽璐珞(一種塑料)首次被發明。 然而,直到 1940 年代,注塑成型才作為一種製造技術得到廣泛應用。
第二次世界大戰期間,對批量生產的塑料產品的需求增加,製造商開始尋找新的、更高效的生產方式。 1946年,美國發明家James Watson Hendry研製出第一台螺桿式註塑機,徹底改變了塑料注塑行業。 這台機器允許更精確和一致的注射過程控制,使大量塑料部件的生產更容易和高效。
在整個 1950 年代和 1960 年代,塑料技術的進步不斷改進塑料注射成型工藝。 聚苯乙烯和聚乙烯等新材料的引入創造了更加複雜和耐用的塑料部件。 此外,成型機技術的改進(包括使用液壓系統)使注塑成型工藝更加高效且更具成本效益。
今天,塑料注射成型是一種高度自動化的工藝,用於生產範圍廣泛的塑料產品,從玩具和消費品到汽車零件和醫療設備。 隨著新材料和新技術的發展,塑料注射成型工藝不斷發展和改進,確保它在許多年內仍然是一項重要的製造技術。
注塑成型基礎知識
塑料注射成型是製造由塑料材料製成的零件和產品的製造過程。 該過程涉及將熔化的塑料注入模具中,模具冷卻並凝固以形成所需的形狀。
塑料注射成型過程中涉及的基本步驟如下:
- 模具設計:流程的第一步是設計用於製造所需零件的模具。 模具通常由金屬製成,必須準備好考慮塑料冷卻和固化時的收縮。
- 材料準備:注塑過程中使用的塑料材料以顆粒或顆粒的形式出現,必須將其熔化並準備好注入模具。 這通常在料斗中完成,塑料在料斗中被加熱到特定溫度並熔化成液態。
- 注射:塑料熔化後,使用專門的注射成型機將其註射到模具中。 機器對熔化的塑料施加壓力,迫使它進入模具型腔,在那裡它呈現出模具的形狀。
- 冷卻凝固:塑料注入模具後,可以冷卻凝固。 這可能需要幾秒到幾分鐘不等,具體取決於零件的大小和復雜程度。
- 頂出:塑料冷卻固化後,打開模具,頂出零件。 該位置可能需要額外的修整工作,例如修剪或打磨,以去除多餘的塑料或粗糙的邊緣。
注塑成型是一種精確且可重複的工藝,非常適合批量生產質量穩定的零件和產品。 它還具有高度的通用性,因為它可以創建各種尺寸、形狀和復雜性的零件和產品。 塑料注射成型的一些最常見應用包括玩具、消費品、汽車零件和醫療設備的生產。
塑料注射成型工藝:循序漸進
塑料注射成型是一個複雜的過程,涉及多個步驟。 以下是塑料注射成型工藝的分步指南:
- 設計模具:第一步是設計用於製造零件的模具。 模具通常由鋼或鋁製成,必須準備好適應塑料材料在冷卻時的收縮。
- 創建模具:模具設計完成後,將使用計算機輔助設計 (CAD) 軟件和計算機輔助製造 (CAM) 機械進行製造。 模具必須經過仔細加工和拋光,以確保最終產品的精度和光潔度。
- 材料選擇:用於注塑工藝的塑料樹脂材料必鬚根據零件的要求進行選擇,例如其強度、柔韌性、顏色和質地。
- 材料準備:然後將選定的塑料材料加熱到特定溫度並熔化成液體。 然後將材料注入成型機的料斗中。
- 注射成型:使用專門的注射成型機將熔融的塑料材料注射到模具型腔中。 機器對塑料材料施加壓力,迫使其進入模具型腔,在那裡它呈現出模具的形狀。
- 冷卻:一旦模具型腔充滿塑料,它就會冷卻凝固。 冷卻時間由塑料材料的特性、零件的尺寸和厚度以及模具溫度決定。
- 頂出:塑料固化後,打開模具,使用頂針將零件從模具中頂出。
- 精加工:彈出的零件可能需要額外的精加工,例如修剪、打磨或塗漆,以去除任何多餘的塑料或粗糙的邊緣。
- 質量控制:成品零件經過徹底檢查,以滿足所需的規格和質量標準。
塑料注射成型可以生產多種尺寸、形狀和復雜性的各種零件和產品。 該工藝廣泛應用於多個行業,包括汽車、醫療、消費品和電子產品。
注塑成型中使用的塑料類型
許多類型的塑料都可用於注塑成型。 塑料材料的選擇將取決於所生產的產品或零件的具體要求,例如強度、柔韌性、耐用性和外觀。 以下是注塑成型中使用的一些最常見的塑料類型:
- 聚乙烯 (PE):PE 是一種廣泛使用的塑料材料,以其強度和柔韌性著稱。 它用於生產各種產品,包括包裝材料、玩具和醫療器械。
- 聚丙烯 (PP):PP 是一種輕質耐用的塑料材料,常用於汽車行業的內飾部件,例如儀表板和門板。 它還生產包裝材料,例如容器和瓶子。
- 聚碳酸酯 (PC):PC 是一種堅固且透明的塑料材料,通常用於生產電子元件,例如電腦和手機殼。 它還用於汽車行業的前照燈透鏡和儀表板組件。
- 丙烯腈丁二烯苯乙烯 (ABS):ABS 是一種多功能塑料材料,以其強度、耐用性和耐熱性而著稱。 它通常用於生產汽車零件,例如儀表板、擋泥板、玩具和消費品。
- 聚酰胺 (PA):PA 也稱為尼龍,是一種堅固且輕質的塑料材料,通常用於生產汽車零件,例如發動機罩和進氣系統。 它還生產運動器材,例如滑雪靴和網球拍。
- 聚苯乙烯 (PS):PS 是一種輕質且堅硬的塑料材料,常用於生產包裝材料,例如杯子、托盤和食品容器。 它還生產消費品,例如玩具和電子元件。
- 聚對苯二甲酸乙二醇酯 (PET):PET 是一種堅固且透明的塑料材料,通常用於生產包裝材料,例如瓶子和容器。 它還用於紡織工業以生產纖維和織物。
這些只是注塑成型中使用的幾種最常見的塑料類型。 可以使用許多其他類型的塑料材料,每一種都具有獨特的性能和特性。 塑料材料的選擇將取決於所生產的零件或產品的具體要求。
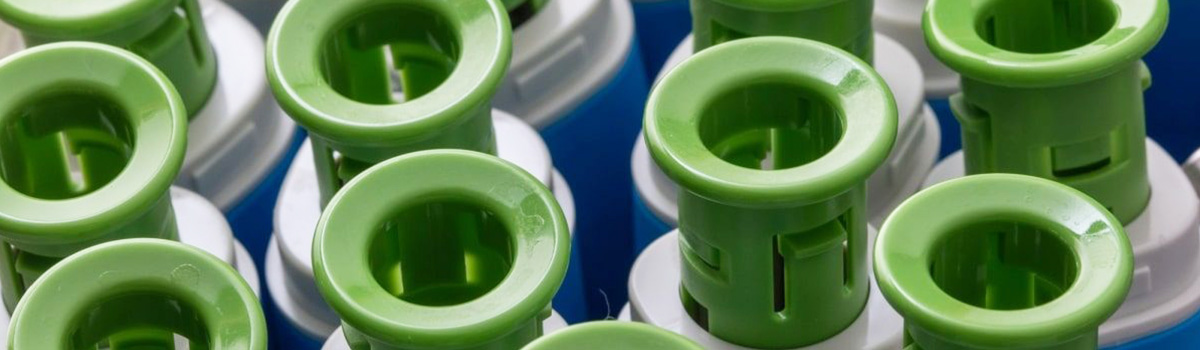
注塑機的類型
注塑機有多種類型和尺寸,每一種都旨在滿足特定的製造要求。 以下是一些最常見的注塑機類型:
- 油壓射出成型機:該機利用油壓動力產生壓力,將塑料射出模具。 液壓機通常用於需要高夾緊力的更重要的零件。
- 電動注塑機:電機使用電動機為註射裝置和合模機構提供動力。 它們以高精度和高能效著稱,因此以生產小型、複雜的零件而聞名。
- 混合式註塑機:混合式機器結合了液壓和電動裝置的優點,使用液壓和電力來產生必要的壓力和動力。 混合動力機器在速度、精度和能源效率之間實現了良好的平衡。
- 立式註塑機:立式註塑機生產需要嵌件成型或包覆成型的零件。 它們有一個垂直夾緊裝置,可以輕鬆接觸模具,使其成為製造小型或複雜零件的理想選擇。
- 二次注塑機:二次注塑機生產具有不同材料或顏色的零件。 該設備有兩個注射單元,每個單元都能夠將異物注射到模具中。 這種類型的機器通常用於生產汽車零件,例如把手和旋鈕。
- 多射注塑機:多射注塑機生產具有兩種以上材料或顏色的零件。 該設備有多個注射單元,每個單元都能夠將不同的材料注射到模具中。 這種類型的機器通常用於生產消費品,例如牙刷和剃須刀。
- 全電動注塑機:全電動注塑機使用電動機為註射裝置、合模機構和模具提供動力。 它們以高精度、速度和能源效率著稱,因此以生產小型高精度零件而聞名。
這些只是幾種最常見的注塑機類型。 每台機器都具有獨特的功能和優勢,因此必鬚根據特定的製造要求選擇合適的設備。
注塑機零件
注塑機有幾個部件可以用原材料製造塑料部件。 以下是注塑機的關鍵部件:
料斗:在將塑料原料送入註塑機之前,儲料槽會存放塑料原料。 該材料通常為顆粒或粉末形式。
料筒:料筒是注塑機的長圓柱形部分,裝有螺桿,螺桿可熔化和混合塑料材料。
螺桿:螺桿是機筒內的一種旋轉裝置,推動塑料材料前進,並通過摩擦和加熱使其熔化。
注射單元:注射單元包括料斗、料筒和螺桿,負責將塑料熔化並註射到模具中。
合模單元:合模單元負責在註塑過程中牢固地固定模具並施加必要的壓力。
模具:模具是創造塑料零件形狀和尺寸的工具。 模具通常由鋼製成,由裝配在一起的兩半組成。
射嘴:射嘴是注射裝置中連接注塑機和模具的部分。 熔化的塑料材料通過噴嘴注入模具中。
冷卻系統:冷卻系統負責冷卻注入模具後的塑料零件。 這確保了工件凝固並且可以在沒有損壞的情況下從模具中取出。
控制面板:控制面板是允許操作員監控和調整注塑機設置(例如溫度、壓力和循環時間)的界面。
這些零件中的每一個在註塑成型過程中都起著至關重要的作用,維護和優化每個零件以確保高效生產高質量零件至關重要。
注塑模具:設計和製造
注塑模具是指設計和製造用於注塑機生產塑料零件的模具。 模具的質量和效率直接影響注塑過程的質量和生產率。 以下是注塑模具設計和製造的關鍵步驟:
產品設計:注塑模具的第一步是設計要生產的產品。 產品設計包括確定零件的尺寸、形狀和材料,以及任何特定特徵或要求。
模具設計:一旦產品設計完成,模具設計過程就開始了。 模具設計師將確定最佳模具類型、所需型腔數量以及模具的尺寸和形狀。
模具構造:模具是根據模具設計構造的,使用鋼或鋁等優質材料。 模具通常分為兩半,每一半包含一個或多個空腔。
模具組裝:模具構建完成後,將進行組裝並測試其精度和功能。 模具必須承受注塑成型過程中的壓力和熱量。
模具測試和驗證:模具組裝後,進行測試和驗證,以確保生產出符合產品規格的高質量零件。 模具可能需要調整或修改以提高其性能。
模具維護:模具的定期維護和修理對於確保其使用壽命和性能至關重要。 這包括清潔、潤滑和更換任何磨損或損壞的零件。
注塑模具需要精度和專業知識,才能始終如一、高效地生產高質量的零件。 通過遵循完整的設計和製造流程,製造商可以製造滿足其產品獨特要求的模具並優化其註塑成型工藝。
注塑模具的類型
注塑成型是一種廣泛用於大批量生產零件的製造工藝。 它涉及將熔化的塑料注入模腔,然後使其冷卻並凝固成所需的形狀。 注塑模具是創建用於注塑成型的模具的過程。 有幾種類型的注塑模具,每種都有自己的優點和缺點。
- 雙板模具 雙板模具是最簡單的注塑模具類型。 它們由夾在一起形成模腔的兩塊板組成。 熔化的塑料通過澆口注入孔中,然後冷卻固化。 創建零件後,將兩個板分開,然後彈出一定數量的零件。 雙板模具通常用於具有簡單幾何形狀的中小型部件。
- 三板模具 三板模具類似於兩板模具,但它們有一個額外的板,稱為脫料板,它將成型零件與流道系統分開。 流道系統是將熔融塑料輸送到模具型腔的通道網絡。 三板模具用於更重要的零件和更複雜的幾何形狀。
- 熱流道模具 在熱流道模具中,熔融塑料通過一系列加熱通道而不是通過澆口直接注入模具型腔。 這減少了流道系統中浪費的材料,從而提高了工藝效率。 熱流道模具用於復雜零件的大批量生產。
- 系列模具 系列模具在單個模具中生產多個零件。 它們具有各種腔體,其排列方式允許同時生產多個域。 家庭模具通常用於中小型體積的零件。
- 嵌件模具 嵌件模俱生產需要金屬或塑料嵌件的零件。 在註入熔融塑料之前,將嵌件放入模腔中。 一旦塑料冷卻並固化,零件和嵌件就會永久粘合。 嵌件模具用於需要強度、耐用性或美學吸引力的位置。
- 包覆成型 包覆成型是將一個零件模製在另一個零件上的過程。 它通常用於需要柔軟觸感或改進抓地力的位置。 包覆成型涉及首先設置基材或基礎部件,然後在其上成型第二種材料。 第二種材料可以是不同類型的塑料、類橡膠材料或熱塑性彈性體。
總之,注塑模具的選擇取決於所生產零件的類型、所需的生產量以及零件設計所涉及的複雜程度。 選擇合適的工具對於確保流程高效且具有成本效益至關重要。
注塑成型設計指南
注塑成型是一種廣泛用於生產塑料零件的製造工藝。 設計用於注塑成型的零件需要對工藝、材料和必須遵循的設計指南有很好的了解,以確保細節能夠成功製造。 以下是一些需要牢記的注塑成型設計指南:
壁厚,零件的壁厚應均勻且盡可能薄,同時保持所需的強度和功能。 這有助於減少冷卻和循環時間,並最大限度地降低翹曲和縮痕的風險。
肋和凸台 肋和凸台可用於增加零件的強度和剛度。 加強筋應不超過公稱壁厚的60%,凸台應為公稱壁厚的1.5倍。
脫模角,所有垂直表面應使用至少 1-2 度的脫模角,以促進零件頂出並防止損壞模具。
圓角和半徑 應避免尖角和尖角,以防止應力集中,從而導致開裂和失效。 相反,圓角和圓角應分散應力並提高零件的強度。
澆口和流道 澆口和流道的位置和設計對於實現良好的零件質量至關重要。 零件最厚部分的入口應盡可能小。 流道的設計應使壓降最小化並使流量最大化。
表面光潔度 零件的表面光潔度應根據應用要求指定。 可見部件可能需要較高的表面光潔度,而隱藏部件可能需要較低的表面光潔度。
材料選擇 為零件選擇的材料應適合注塑成型,並滿足所需的機械、熱和化學性能。
注塑成型中的二次操作
注塑成型是一種用途廣泛的製造工藝,用於生產各種塑料零件。 除了主要成型工藝之外,許多位置還需要二次操作才能獲得所需的形狀、光潔度或功能。 以下是注塑成型中一些日常的二次操作:
- 修整是在模塑零件從模具中脫模後去除多餘的材料。 這通常使用修整壓力機或 CNC 機器來完成。 通常需要修整以達到零件的最終形狀和尺寸。
- 焊接使用熱量、壓力或兩者的組合來結合兩個或多個塑料部件。 這通常用於創建無法在單個模具中生產的更大或更複雜的特徵。
- 裝飾是在模製零件表面添加視覺或功能特徵的過程。 這可以包括繪畫、印刷、標記或應用紋理或圖案。
- 裝配是連接多個零件以創建完整產品的過程。 這可以使用緊固件、粘合劑或其他連接技術來完成。
- 嵌件成型 嵌件成型是圍繞預成型的金屬或塑料嵌件成型塑料。 這通常用於製造具有高強度或耐用性的零件。
- 包覆成型 包覆成型是在預成型部件上模製第二種材料的過程。 這可以增加柔軟觸感的表面,提高抓地力,或創建雙色調或多材料的作品。
- 塗層在零件表面塗上一層薄薄的材料,以改善其外觀、耐用性或其他特性。 這可以包括塗層,例如鉻、鎳或粉末塗層。
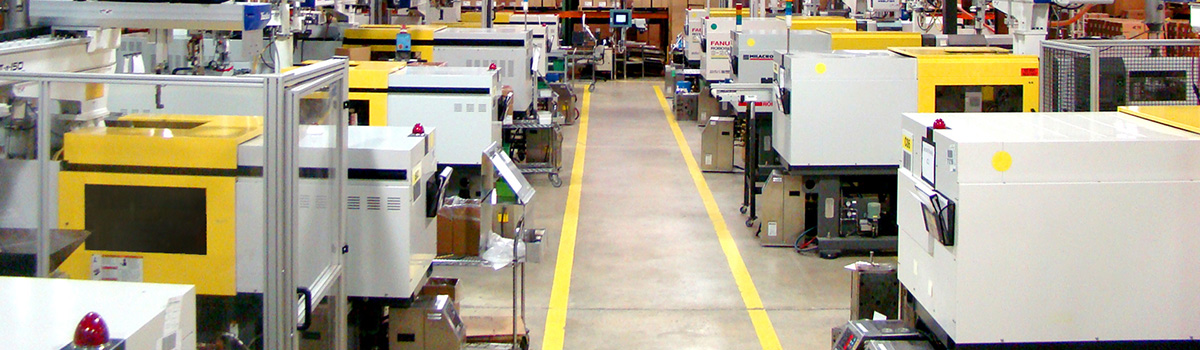
注塑成型的優勢
注塑成型是一種廣泛使用的製造工藝,用於生產高精度、一致性和高質量的塑料零件。 它涉及將熔化的塑料注入模腔並使其冷卻和固化。 以下是塑料注射成型的一些優點:
- 高效率和高生產力塑料注射成型是一種高效和自動化的過程,可以生產大量具有高一致性和質量的零件。 憑藉先進的自動化技術,生產週期時間可縮短至數秒,從而實現複雜零件的大批量生產。
- 高精度和精密注塑成型提高了生產複雜零件的準確性和精度。 計算機控制的機械和先進的軟件可實現具有高重複性和準確性的嚴格公差。
- 多功能性 注塑成型是一種多功能工藝,可以生產各種不同尺寸、形狀和復雜性的塑料零件。 該過程可用於製造從具有復雜細節的小件到具有復雜幾何形狀的大件的任何東西。
- 材料靈活性 注塑成型可以使用範圍廣泛的塑料材料,包括熱塑性塑料、熱固性塑料和彈性體。 這允許生產具有各種機械、熱和化學特性的零件。
- 低廢料生產 注塑成型是一種低廢料生產工藝,因為它在生產過程中產生的廢料最少。 任何多餘的材料都可以輕鬆回收並在生產中重複使用,使其成為一種環保的製造工藝。
- 降低勞動力成本注塑成型的高度自動化最大限度地減少了對勞動密集型流程的需求,從而顯著降低了勞動力成本。 這也降低了人為錯誤的風險,提高了最終產品的質量和一致性。
- 減少後期生產操作 注塑成型生產的零件具有高精度和一致性,減少了對後期生產操作(如修整、鑽孔或銑削)的需求。 這減少了最終產品的生產時間和成本。
- 一致性和質量 注塑成型生產的零件具有高度的一致性和質量。 先進的技術和計算機控制的機械確保每個細節在形狀、尺寸和質量上都完全相同。
- 設計靈活性 注塑成型提供了高度的設計靈活性,因為它允許生產具有復雜幾何形狀、底切和復雜細節的零件。 這將使設計師能夠創造出具有獨特形狀和功能的作品,而這些作品無法使用其他製造工藝製作。
- 大批量生產的成本效益 注塑成型是生產塑料零件的一種成本效益高的工藝。 初始模具成本可能很高,但隨著生產量的增加,每個零件的成本會降低。 這使其成為生產大量零件的理想工藝。
塑料注射成型具有許多優點,使其成為生產塑料零件的熱門選擇。 其高效率、準確性、多功能性、材料靈活性、低廢品產生、降低的勞動力成本以及一致性和質量使其成為各種應用的理想工藝。 能夠生產具有高度設計靈活性和成本效益的複雜零件以進行大批量生產,使其成為備受追捧的製造工藝。
注塑成型的缺點
塑料注射成型是一種廣泛使用的製造工藝,涉及將熔融塑料注入模具型腔以生產各種塑料零件和產品。 雖然塑料注射成型有很多好處,但也有一些缺點。 以下是塑料注射成型的一些主要缺點:
- 模具成本高:設計和生產塑料注射成型模具的成本可能非常高。 這是因為模具需要由優質材料製成,並經過精密加工才能製造出所需的零件。 此外,設計和製造模具的成本對於小規模生產運行來說可能過高,使得塑料注射成型對於小批量製造來說不太經濟。
- 交貨時間長:設計和生產塑料注射成型模具的過程可能需要很長時間,這會延遲塑料零件的生產。 對於需要快速響應市場需求變化或快速開發新產品的企業來說,這尤其成問題。
- 靈活性有限:一旦設計和生產了模具,更改設計或修改生產過程就更容易且成本更低。 這會限制塑料注射成型的靈活性,使其不太適合生產定製或獨一無二的產品。
- 環境問題:塑料注射成型依賴於大量塑料,這會對生態產生負面影響。 塑料廢物是一個主要的環境問題,而塑料注射成型可能會導致這個問題。 此外,製造塑料產品的過程需要使用能源和自然資源,這會進一步影響環境。
- 廢品率高:注塑成型會產生大量廢料,處理或回收這些廢料的成本很高。 此外,廢料的產生會增加整體生產成本並降低製造過程的效率。
- 有限的材料選擇:注塑成型主要用於用熱塑性材料生產零件和產品,與金屬或陶瓷等其他材料相比,熱塑性材料的性能有限。 這會使塑料注射成型不太適合需要高強度、耐溫性或其他高級性能的應用。
注塑成型的局限性
雖然塑料注射成型具有許多優點,但該工藝也存在某些局限性。 以下是塑料注射成型的一些局限性:
高初始模具成本:可以增加設計和製造模具的初始成本。 模具需要精密耐用以承受重複的注塑成型過程,這可能需要大量的前期投資,特別是對於復雜或大型模具。
交貨時間:製造模具的交貨時間可能很長,從幾周到幾個月不等,具體取決於模具的複雜性和尺寸。 這可能會導致生產時間表的延遲,特別是對於時間敏感的項目。
設計限制:注塑成型有一定的設計限制,必須加以考慮。 例如,在整個零件中實現均勻的壁厚對於確保適當的填充和冷卻至關重要。 此外,垂直表面需要有拔模斜度,以便於從模具中脫模。
零件尺寸限制:注塑成型最適合生產中小型零件。 大型零件可能需要專門的設備和更大的模具,從而增加了成本和復雜性。
材料選擇:雖然注塑成型允許使用範圍廣泛的塑料材料,但與其他製造工藝相比,材料的選擇仍然有限。 熔點高或流動性差的材料可能不適合注塑成型。
表面光潔度:注塑成型過程可能會導致零件表面出現可見的編織線或分型線。 實現高質量的表面光潔度可能具有挑戰性,並且可能需要其他方法,例如拋光或塗層。
有限底切:底切是零件上的特徵或細節,可防止其輕易從模具中移除。 底切會使頂出過程複雜化,並且需要額外的模具特徵或二次操作才能獲得所需的零件幾何形狀。
修復選項有限:如果模具損壞或需要修改,修復或改造現有模具可能既費錢又費時。 有時,可能需要製造全新的模具,從而導致額外費用和延誤。
儘管有這些限制,塑料注射成型仍然是一種高度通用且廣泛使用的生產塑料零件的製造工藝。 通過在設計和生產計劃階段仔細考慮這些限制,可以減輕它們的影響並有效利用注塑成型的優勢。
注塑成型的應用
塑料注射成型是一種多功能製造工藝,可以生產範圍廣泛的塑料零件。 以下是塑料注射成型的一些應用:
- 消費品:注塑成型廣泛用於生產各種產品,例如玩具、廚具和電子產品。 該工藝可以生產具有復雜幾何形狀和精確尺寸的高質量零件,非常適合需要嚴格公差和復雜形狀的產品。
- 汽車部件:許多汽車塑料部件,如儀表板部件、門把手和照明,都是使用注塑成型生產的。 該工藝可實現高產量和穩定的質量,使其成為汽車製造商具有成本效益的選擇。
- 醫療器械:注塑成型通常用於生產醫療器械,例如注射器、吸入器和診斷設備。 該工藝可以生產出高精度和一致性的零件,確保器件的質量和可靠性。
- 包裝:注塑成型廣泛用於生產塑料包裝,例如容器、蓋子和瓶蓋。 該工藝可以使部件具有一致的尺寸和高質量的飾面,使其成為具有吸引人的外觀和牢固貼合的包裝的理想選擇。
- 航空航天和國防:注塑成型生產各種航空航天和國防部件,例如飛機內飾、照明和通信系統。 該工藝的部件可以採用輕質、耐用的材料,使其適用於需要高強度重量比的應用。
- 建築:注塑成型可以生產各種建築材料,例如塑料瓦、屋頂和壁板。 該工藝可以使零件具有一致的尺寸和高質量的飾面,使其成為建築公司的一個有吸引力的選擇。
- 運動和娛樂:注塑成型廣泛用於生產運動器材,例如高爾夫球桿、網球拍和自行車部件。 該工藝可以生產具有輕質材料和精確幾何形狀的零件,確保設備的性能和耐用性。
總的來說,塑料注射成型是一種用途廣泛且應用廣泛的製造工藝,可以為各種應用生產高質量的塑料零件。 該工藝可以定制以滿足特定的設計和生產要求,使其成為多個行業製造商的一個有吸引力的選擇。
汽車工業和注塑成型
汽車行業是塑料注射成型技術的重要用戶。 塑料注射成型工藝徹底改變了汽車零部件的生產,使得以高精度和準確度生產複雜形狀成為可能。 以下是塑料注射成型在汽車行業中的一些應用方式:
- 內飾件:注塑成型產生許多內部因素,包括儀表板組件、門板、裝飾件等。 這些部件可以設計成複雜的形狀和紋理,並可以進行定制以符合每種車型的風格和功能要求。
- 外部部件:塑料注射成型也用於生產各種外部特徵,包括保險槓、格柵、後視鏡等。 這些部件可以設計成能夠承受極端天氣條件,並有多種顏色和飾面。
- 引擎蓋下部件:塑料注射成型可生產許多引擎蓋下部件,包括發動機罩、進氣系統和冷卻系統部件。 這些部件需要耐高溫和耐化學腐蝕,而這可以通過熱塑性材料來實現。
- 電氣和電子元件:塑料注射成型生產各種電氣和電子元件,包括連接器、外殼和傳感器。 這些部件需要很高的精度和可靠性,這可以通過塑料注射成型的精度和一致性來實現。
- 輕量化:塑料注射成型通常用於生產輕質部件,有助於減輕車輛的總重量,提高燃油效率並減少排放。 輕量化還可以改善車輛的操控性和性能。
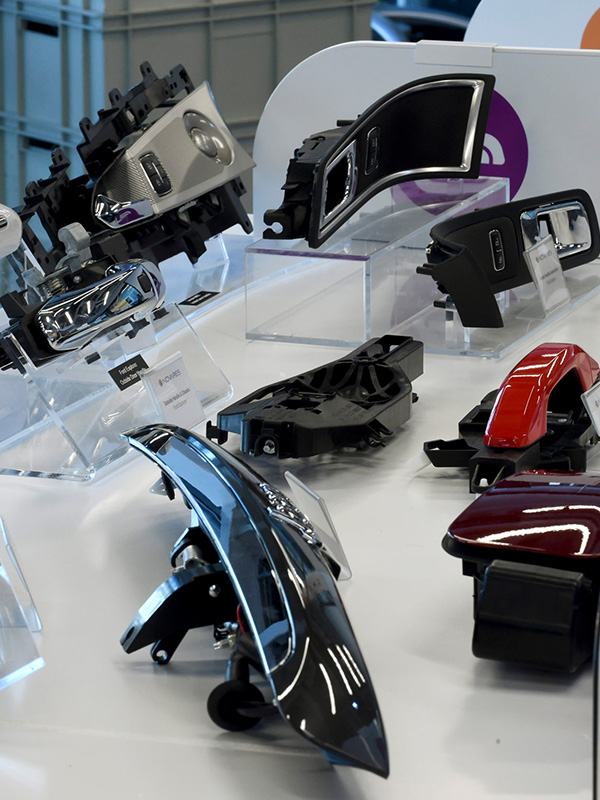
醫療行業和注塑成型
塑料注射成型廣泛應用於醫療行業,以生產各種醫療器械和部件。 塑料注射成型工藝允許以高精度和準確度生產複雜形狀,使其成為許多醫療應用的理想製造方法。 以下是塑料注射成型在醫療行業中的一些應用方式:
- 醫療器械:注塑成型生產各種醫療器械,包括手術器械、診斷工具、藥物輸送系統等。這些設備往往需要很高的精度和準確度,而注塑成型可以滿足這些要求。
- 植入物:塑料注射成型還用於生產各種植入物,包括關節置換物、牙科植入物等。 這些植入物可以設計成與患者的解剖結構相匹配,並使用生物相容性材料生產。
- 實驗室設備:塑料注射成型生產吸管、微孔板和試管。 這些組件需要高精度和準確度以確保可靠的結果。
- 包裝:塑料注射成型用於生產醫療器械包裝,包括無菌屏障系統和個別產品的定制包裝。 這些包裝解決方案有助於保持醫療器械的無菌性和完整性。
- 一次性設備:塑料注射成型通常生產一次性設備,例如注射器、針頭和導管。 這些設備可以低成本大批量生產,有助於防止感染在醫療機構中傳播。
消費品和注塑成型
塑料注射成型因其多功能性、效率和成本效益而廣泛用於消費品的生產。 塑料注射成型工藝允許以高精度和準確度生產複雜形狀,使其成為許多消費應用的理想製造方法。 以下是塑料注射成型用於生產消費品的一些方法:
- 玩具:塑料注射成型生產範圍廣泛的玩具,從小雕像到大型玩具組合。 該過程允許創建複雜的設計和細節,並製作各種顏色和材料的玩具。
- 家居用品:注塑成型生產各種家居用品,包括廚房用具、儲物容器和清潔用品。 這些產品可以設計為耐用、輕便且易於使用。
- 電子產品:注塑成型生產許多電子元件,包括電腦外殼、手機外殼和充電器。 工藝的精密度和準確度確保這些組件的製造具有高度的一致性和可靠性。
- 個人護理用品:注塑成型生產獨特的護理用品,包括牙刷、剃須刀和髮刷。 這些產品需要高精度和準確度,以確保易用性和安全性。
- 汽車配件:注塑成型生產一系列汽車配件,包括儀表板部件、杯架等。 這些組件可以設計得輕巧、耐用,並且能夠抵抗日常使用中的磨損。
注塑成型中的環境考慮
注塑成型是一種廣泛使用的製造工藝,但對環境有重大影響。 以下是塑料注射成型中的一些生態考慮因素:
- 材料選擇:注塑成型中使用的塑料材料的選擇會對環境產生重大影響。 有些材料是可生物降解或可回收的,而另一些則不是。 使用可生物降解或可回收材料有助於減少注塑成型對環境的影響。
- 能源消耗:塑料注射成型需要大量能量來熔化塑料並將其註入模具中。 節能設備和工藝,例如電機和閉環系統,可以減少能源消耗和環境影響。
- 廢物管理:塑料注射成型會產生多餘材料、有缺陷的零件和包裝的廢物。 適當的廢物管理實踐,例如回收和再利用廢料,有助於減少注塑成型對環境的影響。
- 化學品的使用:塑料注塑件中的一些化學品,如脫模劑和清潔溶劑,會對環境造成危害。 使用環保替代品或盡量減少這些化學品的使用有助於減少對環境的影響。
- 報廢注意事項:通過注塑成型生產的塑料產品通常最終會進入垃圾填埋場,這可能需要數百年才能降解。 設計可回收或可生物降解的產品可以減少塑料注射成型對環境的影響。
注塑成型的未來
塑料注射成型的未來看起來很有希望,因為技術和材料的進步有望使該過程更加高效、更具成本效益和可持續性。 以下是可能影響塑料注射成型未來的一些趨勢和發展:
- 增材製造:增材製造,也稱為 3D 打印,是一種新興技術,有可能改變塑料注塑成型。 通過使用 3D 打印創建模具,製造商可以顯著減少與傳統模具製造技術相關的時間和成本。
- 智能製造:涉及自動化、數據分析和機器學習的智能製造有望徹底改變塑料注塑成型。 製造商可以通過使用傳感器和數據分析來優化流程,從而提高效率、減少浪費並提高生產率。
- 可持續材料:可持續材料,如生物塑料和再生塑料,在塑料注塑成型行業中越來越受歡迎。 這些材料具有環境效益,可以幫助製造商實現可持續發展目標。
- 微成型:微成型涉及生產高精度的小零件,在醫療保健和電子等行業中變得越來越重要。 技術和材料的進步有望使微成型更容易獲得且更具成本效益。
- 定制化:隨著消費者對產品個性化需求的增加,注塑成型有望變得更加靈活和可定制化。 實時反饋和機器學習等技術的進步將使製造商能夠快速高效地生產定制產品。
結論:
塑料注射成型是一種高度通用且高效的製造工藝,它徹底改變了各種產品的生產。 從醫療設備到汽車零部件,注塑成型與其他製造工藝相比具有眾多優勢,包括高生產率、設計靈活性和成本效益。 隨著技術和材料的不斷進步,注塑成型的前景一片光明,未來幾年這一工藝很可能在製造業中發揮更重要的作用。