注塑成型常見成型缺陷的解決方法
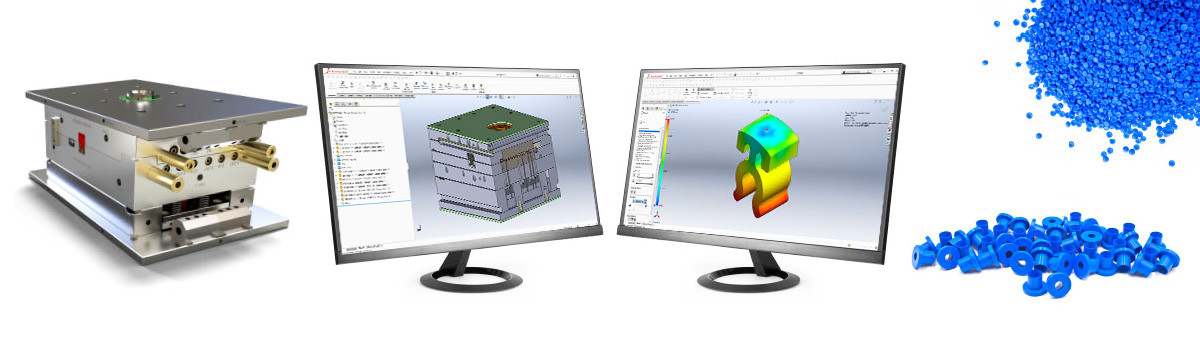
在使用模具加工注塑件時,缺陷是很常見的,這在很大程度上影響了加工效率。 以下是注塑模具零件常見的成型缺陷及解決方法。
短鏡頭
短射是指由於模具未完全填充而導致的產品不完整。
這種缺陷通常出現在離澆口最遠的地方或只能通過模具上狹窄區域才能到達的部分,因為狹窄區域可能會影響熔體的流動。
短射可能會導致微流痕或導致產品的很大一部分明顯缺失。
原因:
短射的原因包括:
注入模具的原料不夠。
熔體阻力大,導致模具不能完全充滿。
模具排氣不良造成氣蝕的產生,堵塞熔體,使熔體無法流到模具的某些區域。
毛刺
毛邊是從模具型腔擠出的多餘原料粘附在製品上而產生的。
這種缺陷會出現在產品的邊緣或模具的每個組成部分。 原料可能會從模具中溢出,或從動模和定模的結合處溢出。
模芯上也會出現毛刺,這是由於液壓壓力或角銷造成的。
毛刺的嚴重程度不一,有時細,有時厚。
原因:
毛刺的原因包括:
合模面損壞或嚴重磨損。
動模與定模鎖緊時錯位。
原料在模具中的壓力高於合模力。
上面提到的第三種情況可能是由多種原因造成的。 在下列情況下,原料壓力高於合模力。
在註塑模具的第一階段(充模階段),原料填充過多,增加了模具內的壓力。
在充模過程中,熔體流動的較大阻力也會使模具內的壓力升高。
保壓階段模腔壓力過高。
合模力不夠。
降解
分解可能導致許多結果。 問題的範圍和嚴重程度也各不相同。 在最嚴重的情況下,它可能會導致產品完全變色和機械性能變差。 局部退化只會造成深色條紋或斑點。
原因:
降解是由於原材料被破壞引起的。 形成塑料的長鏈分子在過熱或過大的剪切應力作用下會發生分解。 在分子分解過程中,揮發的氣體會加速降解過程,從而引起原料脫色。 大量分子的分解最終會破壞原材料的含量,並對機械性能造成負面影響。
料筒溫度不均可能導致局部降解。
在以下情況下可能會發生降級:
原料在料桶或熱流道系統中過熱。
原料在桶內停留時間過長。
在註塑成型過程中,對原材料施加的剪切應力過大。 如果噴嘴堵塞,或澆口和流道太窄,都會增加剪切應力。
形變
在正常情況下,產品的形狀應與模具的形狀一致。 變形是指產品變形。
當情況變得更糟時,產品在脫模時會完全變形。 情況不嚴重時,產品形狀會出現細小的凹凸不平。
長但沒有支撐邊或大平面是最容易變形的區域。
原因:
變形原因:
脫模時溫度過高。
由於厚薄區域冷卻時間不同,或動模和定模的模具溫度不同,製品內部收縮率不同。
充型時模流不暢(所謂“凝固取向”)或保壓階段模腔內壓力過高。
雜質
雜質常以不同顏色的斑點、斑塊或條紋的形式出現。 最常見的是黑點。
雜質可能只是微小的斑點,嚴重時也可能是明顯的條紋或大部分脫色。
原因:
雜質是由原料中混入的雜物引起的,如:
原料在運入桶中時混有雜物。
原材料的分解可能會從任何切割機構掉落並混入原材料中,例如機器螺栓、乾燥滾筒的內壁、接頭/噴嘴。
層壓
層壓會在產品表面產生“結皮效應”,這是由於產品表面與其他原材料的性能和質地不同造成的,形成可去除的剝皮。
分層嚴重時,整個橫截面由不同的層組成,還沒有熔合在一起。 當缺陷不太明顯時,產品的外觀可能符合要求,但會破壞產品的機械性能。
原因:
層壓有兩個主要原因。 第一個是當兩種不同的原材料不正確地混合在一起時。 兩種原料在壓力下同時輸送到機筒中。 然而,當模具冷卻時不能熔合在一起,就像不同的層被強行壓在一起形成產品一樣。
第二:如果冷熔體被迫通過窄澆口,會產生剪切應力。 過高的剪切應力會導致提前熔化的熔體層不能完全熔合。
混合風險:
需要注意的一點是有些原料混合在一起會產生強烈的化學反應,比如PVC和Avetal是絕對不能混合的。
銀色線性
條狀線狀可能只是局部現象,但嚴重時可擴展到整個表面。
銀線會影響產品的外觀,也會損害產品的機械性能。
原因:
以下兩點造成銀色線性:
原料潮濕,有些會吸收空氣中的水蒸氣。 如果原料太濕,在機筒高溫高壓的作用下,可能會產生加壓蒸汽。 這些蒸氣會穿透產品表面並形成銀色條紋。
熔體受到熱損壞並產生局部降解。 產生的揮發性氣體會阻塞在模具表面,在製品表面產生條紋。
這並不像退化那麼糟糕。 只要熔體溫度高或在塑化或註入模具時受到剪切應力,就可能發生這種情況。
光澤/陰影
產品表面光潔度應與模具相同。 當兩者的表面光潔度不同時,就會出現光澤/陰影缺陷。
出現缺陷時表面灰暗,粗糙的表面光滑有光澤。
原因:
光澤/陰影的原因包括:
熔體流動不暢或模具表面溫度低,導致材料成型時模具表面光潔度無法複製。
保壓時型腔內壓力不夠高,使材料在冷卻過程中緊貼模具表面,留下縮痕。
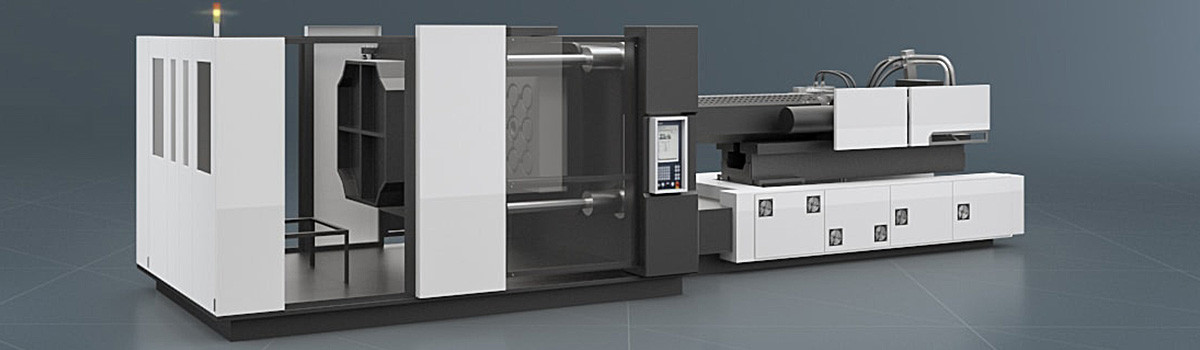
流痕
流痕可以多種形式存在於產品表面。 一般會形成陰影區。
流痕不會在產品表面產生任何用手指感覺不到的壓花或凹陷。 這種缺陷也稱為拖痕、重影和陰影。
流痕明顯時,會產生溝槽,在產品表面留下痕蹟等缺陷。
原因:
在以下情況下可以找到流痕:
熔體流動性差或模具表面溫度低,造成塑料在充模過程中流動阻力大。
在充模過程中,熔體流動有阻力,這可能是由於模具表面凹凸不平,模具表面印刷的標記或圖案,或在填充過程中熔體流動方向的改變造成的。
合縫線
合線是在充模過程中兩個熔體前沿相遇時產生的,會像一條線一樣出現在產品表面。
合縫線就像產品表面的開裂線,不易察覺。
在設計模具時,一些可見的合縫線是不可避免的。 在這種情況下,盡可能縮短接合線,以防止損壞產品的強度和外觀。
原因:
熔鋒的產生有多種原因。 最可能的原因可能是熔體沿著模芯的邊緣流動。 當兩種熔體相遇時,就會產生接合線。 兩個熔體前沿的溫度要高到足以使它們成功熔合在一起,並且不影響產品的強度和外觀。
當兩種熔體不能完全融合在一起時,就會產生缺陷。
缺陷原因:
模具有較厚和較薄的部分,熔體的流動速度不同,當熔體流過模具較薄的部分時,溫度較低。
每個跑步者的長度都不同。 獨來獨往的跑步者很容易降溫。
模腔壓力不足以讓熔體在保壓階段完全熔化。
殘留的氣泡使熔體前沿無法融合,也會導致燒焦。
燃燒
燃燒與短射相似,但有不規則的退色邊緣和輕微的燃燒氣味。 產品上會出現炭黑區域,情況嚴重時,還會伴有塑料燃燒的氣味。
如果不消除缺陷,模具上通常會出現黑色沉積物。 如果不立即檢查燃燒產生的氣體或油類物質,它們可能會堵塞氣孔。 燃燒通常出現在路徑的盡頭。
原因:
燃燒是由內燃效應引起的。 當空氣中的壓力在很短的時間內急劇增加時,溫度就會升高並引起燃燒。 根據收集到的數據,注塑過程中的內燃作用可產生高達600度的高溫。
在以下情況下可能會產生燃燒:
充模速度快,使模具型腔內的空氣無法排出,因進料受阻而產生氣泡,受壓後產生內燃效應。
氣孔堵塞或通風不暢。
模具中的空氣應從氣孔中排出。 如果通風受到位置、數量、大小或功能的影響,空氣將留在模具中並導致燃燒。 合模力大也會導致通氣不暢。
收縮
縮水是指產品表面的輕微凹陷。
當缺陷輕微時,產品表面不平整。 嚴重時,產品會大面積倒塌。 帶有拱形、把手和突起的產品通常會出現縮水缺陷。
原因:
縮孔是原材料在冷卻過程中大面積收縮造成的。
製品較厚的部位(如拱形),材料心部溫度低,收縮比表層晚,材料內部產生收縮力,將外側拉入向內的凹陷處產生收縮。
在以下情況下會發生收縮:
模腔內的壓力低於原料在冷卻過程中收縮產生的力。
冷卻過程中模具型腔加壓時間不夠,造成原料從澆口流出型腔。
原料在成型和保壓階段沒有足夠的緩衝能力,因為在註射過量原料之前螺桿已經完全退出。
澆口和流道的橫截面積遠小於產品的厚度,這意味著在產品擠出過程之前澆口已經凍結。
氣泡
真空氣泡以氣泡的形式呈現,在透明製品上很容易發現。 它也可以在不透明產品的橫截面上看到。
原因:
氣泡是產品的真空部分,是原材料在冷卻過程中收縮時產生的。
與收縮類似,原材料內部產生收縮力。 不同的是,氣泡形成時產品外觀已經凝固,沒有塌陷,所以產生空心氣泡。
產生氣泡的原因與減少的原因相同,包括:
模腔壓力低效
模腔加壓時間不足
流道和澆口尺寸太小
噴塗痕跡
噴塗標記是指澆口對面的螺紋區域。 噴塗痕跡不僅會影響產品的外觀,還會影響產品的強度。
原因:
噴痕是在充模過程中熔體流動失控造成的。
熔化的塑料在巨大的壓力下進入模具。 如果充模速度太快,塑料會從模腔的開口縫隙中噴出,並迅速回彈冷卻。 此時會形成螺紋,阻止熔化的塑料進入澆口。
造成噴塗痕蹟的主要原因是澆口位置不正確或澆口設計不當。 以下兩種情況會使缺陷情況惡化:
充模速度快
充模時熔體流動不暢