Термопластикалык Injection Fording
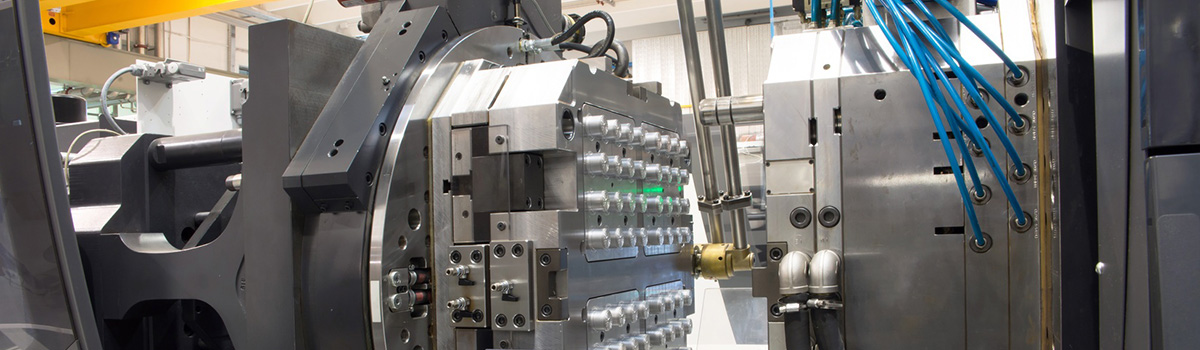
Термопластикалык инжектордук форма бир нече тармактар үчүн ар кандай пластик бөлүктөрдү түзүү үчүн колдонулган популярдуу өндүрүш процесси. Бул процесс пластикалык гранулдарды эритип, үч өлчөмдүү форманы алуу үчүн калыпка сайууну камтыйт. Термопластикалык инъекциялык калыптоо өтө эффективдүү жана үнөмдүү, чоң көлөмдөгү жогорку сапаттагы пластикалык бөлүктөрүн катуу толеранттуулук менен өндүрүү үчүн. Бул комплекстүү колдонмо термопластикалык инъекциялык калыптын ар кандай аспектилерин, анын ичинде анын артыкчылыктарын жана кемчиликтерин, колдонулган термопластиканын түрлөрүн, инъекциялык калыптоо процессин, дизайн ойлорун жана башка көптөгөн нерселерди изилдейт.
Термопластикалык Injection Fording тарыхы
Термопластикалык инъекциялык калыптын тарыхы бир кылымдан ашык технологиялык жетишкендиктерди, материалдык өнүгүүлөрдү жана өнөр жайлык колдонмолорду камтыйт. Целлулоидди калыптандыруу процесси катары жөнөкөй башталышынан баштап, азыркы татаал технологияга чейин, инъекциялык калыптоо инновацияларды жайылтуу жана ар кандай тармактарды калыптандыруу үчүн маанилүү өндүрүш ыкмасы болуп калууда.
- Алгачкы өнүгүүлөр:Жон Уэсли Хайатт жана анын бир тууганы Исайа 19-кылымдын аягында термопластикалык инъекциялык форманын келип чыгышын изилдеп, биринчи практикалык инъекциялык калыптоо машинасын иштеп чыгышкан. 1872-жылы алар калыптын көңдөйүнө целлулоидди киргизүү үчүн плунжерди колдонгон аппаратты патенттеп, катуу нерселерди жаратышкан. Бул ачылыш заманбап инжектордук калыптоо процессине негиз салган.
- Материалдардагы жетишкендиктер:20-кылымдын башында жаңы синтетикалык полимерлерди киргизүү инъекциялык формага жаңы мүмкүнчүлүктөрдү ачты. Бакелит, фенолдук чайыр, өзүнүн эң сонун электрдик изоляциялык касиеттеринен улам калыптоо үчүн популярдуу материал болуп калды. 1930-1940-жылдары полимердик химиядагы жетишкендиктер полистирол жана полиэтилен сыяктуу башка термопластикалардын өнүгүшүнө алып келди, бул инъекциялык формага ылайыктуу материалдардын спектрин андан ары кеңейтти.
- Өнөр жай кабыл алуу: Термопластикалык инъекциялык форманы кеңири жайылтуу 1950-жылдары өндүрүшчүлөр анын экономикалык натыйжалуулугун жана ар тараптуулугун моюнга алышкан. Жогорку басымдагы машиналарды ишке киргизуу циклди ылдамдатууга жана продукциянын келемун кебейтууге мумкундук берди. Натыйжада, жеке жана өнөр жайлык пайдалануу үчүн буюмдардын ар түрдүү тандоо пайда болду. Алардын ичинде унаа тетиктери, тиричилик техникасы жана оюнчуктар бар.
- Технологиялык инновациялар:Ондогон жылдар бою инжектордук калыптоо технологиясы өнүгүүнү улантты. 1960-жылдары калыптоо процессин так башкарууга мүмкүндүк берген компьютердик башкаруучу машиналар пайда болду. 1980-жылдары ысык чуркоо системаларынын ишке киргизилиши күлүктөргө жана шпагаларга болгон муктаждыкты жок кылуу менен калдыктарды азайтып, натыйжалуулукту жогорулатты. Акыркы жылдарда автоматташтыруу, робототехника жана 3D басып чыгаруудагы жетишкендиктер инжектордук калыптоо өнөр жайын андан ары өзгөртүп, татаал конструкцияларды иштеп чыгууга жана өндүрүш убактысын кыскартты.
- Туруктуулук жана кайра иштетүү:Айлана-чөйрөнү коргоо маселелери өсүп жаткандыктан, инжектордук калыптоо өнөр жайы туруктуулук чараларын кабыл алды. Өндүрүүчүлөр био-негизделген жана кайра иштетилген термопластикаларды иштеп чыгышты, бул казылып алынган отундун негизиндеги материалдарга болгон көз карандылыкты азайтты. Кошумчалай кетсек, кайра иштетүүнүн өркүндөтүлгөн технологиялары керектөөдөн кийинки жана өндүрүштөн кийинки калдыктарды кайра иштетүүгө мүмкүндүк берип, термопластикалык инъекциялык форманын айлана-чөйрөгө тийгизген таасирин азайтат.
- Келечектеги перспективалар:Термопластикалык инъекциялык форманын келечеги келечектүү көрүнөт. Өнөр жай миниатюралык компоненттер үчүн микро инъекциялык калыптоо, татаал тетиктер үчүн көп материалдуу жана ашыкча формалоо ыкмалары, процесстерге мониторинг жүргүзүү жана оптималдаштыруу үчүн интеллектуалдык технологияларды интеграциялоо сыяктуу инновацияларды изилдеп жатат. Андан тышкары, изилдөөчүлөр биологиялык ыдыратуучу материалдардын жана кошумча өндүрүшүнүн жетишкендиктери талаада төңкөрүш жасап, инжектордук форманы ого бетер туруктуу жана ар тараптуу кылат деп күтүшөт.
Термопластикалык инъекциялык калыптын артыкчылыктары
Термопластикалык инъекциялык калыптоо өндүрүүчүлөр үчүн көптөгөн артыкчылыктарды сунуш кылат. Бул ар кандай өзгөчөлүктөргө ээ татаал жана татаал дизайнга жол берип, дизайн ийкемдүүлүгүн камсыз кылат. Процесс үнөмдүү, материалдык калдыктарды азайтат жана бирдиктин чыгымдарын азайтат. Термопластикалык инъекциялык калыптоо ар кандай колдонмолор үчүн ар тараптуулукту камсыз кылуу менен бир нече материалдарды колдойт.
- Дизайн ийкемдүүлүгү:Термопластикалык инъекциялык калыптоо дизайнерлерге эбегейсиз эркиндикти камсыз кылуучу астын кесүү, жука дубалдар жана ар кандай калыңдыктар сыяктуу өзгөчөлүктөргө ээ татаал жана татаал конструкцияларды жасоого мүмкүндүк берет.
- Экономикалык натыйжалуулук: Процесс жогорку натыйжалуу, материалдык калдыктарды азайтат жана бирдиктин чыгымдарын азайтат. Бир эле учурда бир нече бөлүктөрдү калыптандыруу жана өндүрүштүн тез циклдери чыгымдарды үнөмдөөгө өбөлгө түзөт.
- Материалдык көп тараптуулугу: Термопластикалык инъекциялык форма материалдардын кеңири спектрин колдойт, бул өндүрүүчүлөргө ар бир колдонуу үчүн эң ылайыктуу вариантты, анын ичинде катуу же ийкемдүү, тунук же тунук эмес жана химиялык жактан туруктуу материалдарды тандоого мүмкүндүк берет.
- Күч жана туруктуулук:Инжекциялык формада жасалган термопластика жогорку күч, бышык жана соккуга туруштук берүү сыяктуу мыкты механикалык касиеттерди көрсөтө алат. Арматура параметрлери, айнек же көмүртек була сыяктуу, бул касиеттерин дагы жакшыртат.
- Ырааттуулук жана сапат:Инжектордук калыптоо ырааттуу жарым-жартылай сапатты жана өлчөмдөрдүн тактыгын камсыздайт, катуу толеранттуулуктарды жана ишенимдүү өнүмдөрдү жеткирет. Процесс ошондой эле беттин жылмакай жана бирдей жасалгасын камсыздайт, кошумча бүтүрүү операцияларын талап кылбайт.
- Масштабтоо жана массалык өндүрүш:Инжектордук форма аз көлөмдөн жогорку көлөмгө чейин масштабдалып, аны массалык өндүрүшкө ылайыктуу кылат. Өндүрүүчүлөр калыпты түзгөндөн кийин, алар минималдуу вариациялар менен бирдей бөлүктөрдү көп санда чыгара алышат.
- Интеграция жана Ассамблея:Инжекциялык формадагы тетиктер бир нече компоненттерди бир бөлүккө киргизип, кошумча монтаждоо процесстерине муктаждыкты азайтат. Бул интеграция продуктунун иштешин жакшыртат, чогултуу убактысын кыскартат жана чыгымдарды азайтат.
- Туруктуулук:Инжектордук калыптоо өнөр жайы туруктуулукка көбүрөөк көңүл буруп жатат. Биологиялык жана кайра иштетилген материалдардын болушу экологиялык жактан таза продукцияны өндүрүүгө мүмкүндүк берет. Термопластиканы эффективдүү пайдалануу жана кайра иштетүү өндүрүш процессинин жашыл болушуна өбөлгө түзөт.
Бул артыкчылыктар аны комплекстүү продукт талаптары үчүн жогорку сапаттагы, экономикалык жактан үнөмдүү жана экологиялык жактан таза чечимдерди камсыз кылуу менен ар кандай тармактарда кеңири кабыл алынган өндүрүш ыкмасына айлантты.
Термопластикалык инжектордук форманын кемчиликтери
Термопластикалык инъекциялык калыптоо көптөгөн артыкчылыктарды сунуш кылганы менен, бир катар кемчиликтери да бар. Өндүрүүчүлөр бул факторлорду кылдаттык менен баалап, термопластикалык инъекциялык форманын конкреттүү колдонууга ылайыктуулугун аныктоо үчүн аларды артыкчылыктарга каршы таразалап алышы керек.
- Жогорку баштапкы инвестиция: Термопластикалык инъекциялык формалоо операциясын орнотуу көктүн дизайнына жана даярдоого жана атайын техниканы сатып алууга олуттуу баштапкы инвестицияны талап кылат. Калыптарды жана инструменттерди түзүү менен байланышкан чыгымдар, өзгөчө татаал жана татаал конструкциялар үчүн олуттуу болушу мүмкүн.
- Дизайн чектөөлөрү: Термопластикалык инъекциялык форма дизайн ийкемдүүлүгүн сунуш кылганы менен, белгилүү бир чектөөлөр бар. Мисалы, бүт бөлүктө дубалдын бирдей калыңдыгына жетишүү татаал болушу мүмкүн, бул материалды бөлүштүрүүдөгү вариацияларга жана потенциалдуу структуралык алсыздыктарга алып келет. Кошумча, астын кесүү же татаал геометриянын болушу кошумча калыптын өзгөчөлүктөрүн же экинчи операцияларды колдонууну талап кылышы мүмкүн, чыгымдарды жана өндүрүш убактысын көбөйтөт.
- Узак убакыт:Инъекциялык формага арналган калыптарды долбоорлоо жана даярдоо процесси көп убакытты талап кылат, бул продуктуну иштеп чыгуу үчүн узак убакытка алып келет. Дизайн итерация процесси, калыптарды өндүрүү жана тестирлөө өндүрүштүн жалпы графигине олуттуу убакытты кошо алат, бул мөөнөттөрү чектелүү долбоорлор үчүн ылайыктуу эмес.
- Материалды тандоо боюнча чектөөлөр:Термопластикалык инъекциялык калыптоо материалдардын кеңири спектрин колдосо да, белгилүү бир чектөөлөр жана чектөөлөр бар. Кээ бир материалдар белгилүү бир колдонуу үчүн дизайн тандоосуна жана материалды тандоого таасир этүүчү конкреттүү иштетүү талаптары же чектелген болушу мүмкүн.
- Бөлүмдүн көлөмү чектөөлөр:Инжекциялык калыптоо машиналары аппараттын физикалык өлчөмү жана алар жайгаштыра турган калыптардын өлчөмү боюнча да чектөөлөргө ээ. Чоң тетиктерди өндүрүү атайын жабдууларды же башка өндүрүш ыкмаларын талап кылышы мүмкүн.
- Курчап турган чөйрөгө тийгизген таасири:Өнөр жай туруктуулукка карай иштеп жаткан учурда, термопластикалык инъекциялык калыптоо процесси дагы эле калдыктарды, анын ичинде сыныктарды жана балталарды пайда кылат. Бул материалдарды туура утилдештирүү жана кайра иштетүү айлана-чөйрөгө тийгизген таасирин азайтуу үчүн зарыл.
- Процессти оптималдаштыруунун татаалдыгы:Термопластикалык инъекциялык калыптоо процессинин оптималдуу параметрлерине жетишүү татаал жана көп убакытты талап кылат. Өндүрүүчүлөр тетиктердин ырааттуу сапатын камсыз кылуу жана кемчиликтерди азайтуу үчүн температураны, басымды, муздатуу ылдамдыгын жана цикл убакыттарын кылдат көзөмөлдөп, оптималдаштырышы керек.
Инжекциялык формада колдонулган термопластиканын түрлөрү
Бул көбүнчө инжектордук формада колдонулган термопластиканын бир нече мисалдары. Ар бир материал күчкө, ийкемдүүлүккө, химиялык туруктуулукка, ачык-айкындуулукка жана баага негизделген атайын колдонмолор үчүн ылайыктуу кылып, уникалдуу касиеттерге ээ. Өндүрүүчүлөр инжектордук калыптоо долбоорлору үчүн тиешелүү термопластиканы тандап жатканда ушул касиеттерди жана талаптарды эске алышы керек.
- Полипропилен (PP):Полипропилен - инъекциялык формада көбүнчө колдонулган көп тараптуу термопластика. Бул мыкты химиялык каршылык, төмөн тыгыздык жана жакшы таасир күчүн сунуш кылат. PP (полипропилен) таңгактоодо, автомобиль компоненттеринде, тиричилик техникасында жана медициналык аппараттарда кеңири колдонулат.
- Полиэтилен (ПЭ):Полиэтилен - инъекциялык формада кеңири колдонулган дагы бир термопластика. Бул жогорку тыгыздыктагы полиэтилен (HDPE) жана төмөн тыгыздыктагы полиэтилен (LDPE) сыяктуу ар кандай формаларда болот. PE жакшы химиялык туруктуулукту, катуулукту жана ийкемдүүлүктү сунуштайт, бул бөтөлкөлөргө, идиштерге жана түтүктөргө ылайыктуу.
- Полистирол (PS):Полистирол - анын ачыктыгы, катуулугу жана арзандыгы менен белгилүү болгон ар тараптуу термопластика. Бул таңгактарда, керектөө товарларында жана бир жолу колдонулуучу буюмдарда кеңири колдонулат. PS (полистирол) тез иштетүүгө мүмкүндүк берет жана жакшы өлчөмдүү туруктуулукту камсыз кылат, бирок ал морт жана экологиялык стресстен жаракалуу болушу мүмкүн.
- Акрилонитрил бутадиен стирол (ABS): ABS - анын мыкты таасирге туруктуулугу жана туруктуулугу менен белгилүү болгон популярдуу термопластика. Ал акрилонитрилдин, бутадиендин жана стиролдун касиеттерин бириктирип, автомобиль тетиктерине, электрондук корпустарга жана оюнчуктарга ылайыктуу көп тараптуу материалды түзөт.
- Поливинилхлорид (PVC): ПВХ - бул кеңири колдонулган термопластика, анын химиялык туруктуулугу, туруктуулугу жана арзандыгы менен белгилүү. Ал колдонулган формулага жана кошумчаларга жараша катуу же ийкемдүү болушу мүмкүн. ПВХ (поливинилхлорид) курулушта, электр изоляциясында, саламаттыкты сактоо буюмдарында жана таңгактоодо кеңири колдонулат.
- Поликарбонат (PC): Поликарбонат өзгөчө таасири жана жогорку жылуулук туруктуулугу менен тунук термопластика болуп саналат. Бул автомобиль компоненттери, коопсуздук каскалары жана электрондук дисплейлер сыяктуу оптикалык ачыктыкты талап кылган колдонмолордо кеңири колдонулат.
- Нейлон (полиамид):Нейлон өзүнүн мыкты механикалык касиеттери жана химиялык туруктуулугу менен белгилүү болгон күчтүү жана бышык термопластика. Ал унаа тетиктери, өнөр жай тетиктери жана керектөө товарлары сыяктуу жогорку күчтү талап кылган колдонмолордо кеңири колдонулат.
- Полиэтилентерефталат (ПЭТ):PET бөтөлкөлөрдү, контейнерлерди жана таңгактоочу материалдарды өндүрүү үчүн популярдуу термопластика болуп саналат. Бул тамак-аш жана суусундук колдонмолор үчүн ылайыктуу кылып, жакшы ачык-айкындуулук, химиялык каршылык, жана тоскоолдук касиеттерин сунуш кылат.
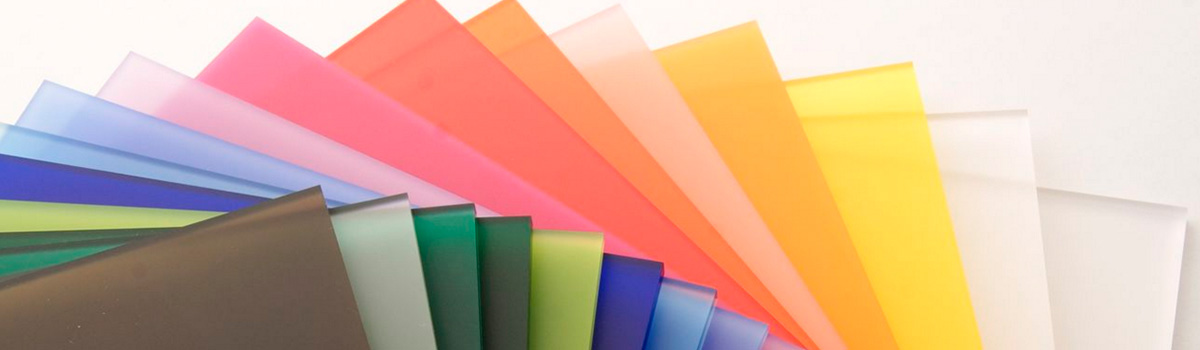
Инжекциялык формада колдонулган термопластикалардын касиеттери
Термопластиканын бул касиеттери алардын инжектордук формага ылайыктуулугун аныктоодо чечүүчү ролду ойнойт. Өндүрүүчүлөр бул касиеттерди кылдаттык менен карап чыгып, керектүү өндүрүмдүүлүктүн, экологиялык шарттардын жана нарктын талаптарынын негизинде тиешелүү термопластиканы тандап алышы керек.
- Механикалык касиеттер:Инжектордук формада колдонулган термопластика ар кандай механикалык касиеттерди, анын ичинде чоюлууга, соккуга туруштук берүүгө жана ийилүүгө туруктуулукту көрсөтө алат. Бул касиеттер материалдын колдонулган күчтөргө туруштук берүү жөндөмдүүлүгүн жана ар кандай колдонууда анын жалпы бышыктыгын аныктайт.
- Химиялык туруктуулук:Инъекциялык формада колдонулган көптөгөн термопластика химиялык заттарга, эриткичтерге жана майларга укмуштуудай туруктуулукка ээ. Бул касиет катаал чөйрөгө же коррозияга дуушар кылуучу заттарга дуушар болгон колдонмолор үчүн өтө маанилүү.
- Жылуулук туруктуулугу:Термопластиканын жылуулук туруктуулугу алардын жогорулатылган температурага олуттуу бузулбастан туруштук берүү жөндөмүн билдирет. Кээ бир термопластика жогорку температурада да алардын механикалык касиеттерин сактап калууга мүмкүндүк берген эң сонун ысыкка туруктуулукту көрсөтөт.
- Электрдик касиеттери:Инжектордук формада колдонулган термопластика электрдик изоляция, өткөргүчтүк же диэлектрдик күчтү кошкондо, белгилүү электрдик касиеттерге ээ болушу мүмкүн. Бул касиеттер электрдик жана электроникалык өнөр жайларында колдонуу үчүн абдан маанилүү, мында материалдар ишенимдүү электрдик көрсөткүчтөрдү камсыз кылышы керек.
- Ачыктык жана айкындык:Кээ бир термопластика, мисалы, поликарбонат жана ПЭТ, оптикалык касиеттерди талап кылган колдонмолорго ылайыктуу кылып, эң сонун ачык-айкындуулукту жана айкындуулукту сунуштайт. Өндүрүүчүлөр бул материалдарды көбүнчө тунук терезелер, линзалар жана дисплейлер сыяктуу буюмдарда колдонушат.
- Ийкемдүүлүк жана катуулугу: Ийкемдүүлүк жана бышыктык - таасирге туруктуулукту жана туруктуулукту талап кылган колдонмолордо колдонулган термопластиканын маанилүү касиеттери. Кээ бир термопластика, мисалы, ABS жана нейлон, алар сынбай туруп, кайра-кайра таасирлерге туруштук берүүгө мүмкүнчүлүк берет, мыкты катуулугун сунуш кылат.
- Өлчөмдүк туруктуулук:Өлчөмдүү туруктуулук термопластиканын ар кандай шарттарда, анын ичинде температуранын өзгөрүшүнө жараша формасын жана өлчөмүн сактап калуу жөндөмүн билдирет. Жакшы өлчөмдүү туруктуулугу бар материалдар бөлүктүн ырааттуу өлчөмдөрүн камсыздайт, ийилип же бурмаланып кетүү коркунучун азайтат.
- Химиялык шайкештик:Термопластиканын химиялык шайкештиги алардын бузулууга же ар кандай химиялык заттар, анын ичинде кислоталар, негиздер жана эриткичтер менен өз ара аракеттенүүсүнө туруштук берүү жөндөмүн билдирет. Оптималдуу иштешин камсыз кылуу үчүн, атайын химиялык чөйрөгө туруштук бере ала турган термопластикти тандоо зарыл.
- жыштыгы: Термопластика ар кандай жоондуктарга ээ, бул алардын салмагына жана жалпы бөлүгүнүн касиеттерине таасир этиши мүмкүн. Полиэтилен сыяктуу төмөн тыгыздыктагы материалдар жеңил чечимдерди сунуштайт, ал эми полипропилен сыяктуу жогорку тыгыздыктагы материалдар кошумча күч жана катуулукту камсыз кылат.
Injection Fording Process: Кадам-кадам
Инжектордук формалоо процесси бул кадамдарды аткарат, бул жогорку сапаттагы термопластикалык бөлүктөрдү натыйжалуу жана так чыгарууга мүмкүндүк берет. Ар бир кадам ырааттуу бөлүктүн өлчөмдөрүн, материалдык касиеттерин жана жалпы сапатын камсыз кылуу үчүн кылдат көзөмөлдү жана мониторингди талап кылат.
- Көк дизайн жана даярдоо: Инъекциялык калыптоо процессиндеги биринчи кадам калыпты долбоорлоо жана даярдоо болуп саналат. Өндүрүүчүлөр керектүү бөлүктүн спецификацияларына жетүү үчүн так жана деталдуу калыптын дизайнын түзүшү керек. Өндүрүүчүлөр андан кийин калыпты CNC же электрдик разрядды иштетүү (EDM) сыяктуу ар кандай ыкмаларды колдонуп жасашат.
- Материалды даярдоо: Кийинки кадам калып даяр болгондон кийин даярдоо болуп саналат. Термопластикалык гранулдар же гранулдар керектүү материалдын касиеттерине жараша тандалып алынат жана бункерде эрийт. Андан кийин операторлор материалды инжектордук формалоочу машинанын бочкасына киргизип, ал жерде эрүү жана гомогенизациядан өтөт.
- Инъекция:Инъекция фазасында операторлор эритилген термопластиканы жогорку басым астында калыптын көңдөйүнө сайышат. Машинанын инжектордук агрегаты эриген материалды саптама аркылуу калыпка түртөт. Материал керектүү бөлүктүн формасын алып, көктүн көңдөйүн толтурат.
- Муздатуу жана катуулантуу:Калыпты толтургандан кийин операторлор эриген пластмасса муздатып, катуулашына мүмкүндүк берет. Муздатуу өлчөмдүү туруктуулукту жана бөлүктүн туура калыптанышына жетишүү үчүн өтө маанилүү. Операторлор муздатуу процессин калыптын ичиндеги каналдар аркылуу муздаткычтын айлануусу же муздаткыч плиталардын жардамы менен көзөмөлдөй алышат.
- Көк ачуу жана чыгаруу:Операторлор калыпты ачып, пластмасса катып калгандан кийин аны калыптын көңдөйүнөн чыгарышат. Машинанын ичиндеги чыгаруу системасы аймакты калыптан алып салуу үчүн төөнөгүчтөрдү, эжектордук плиталарды же аба жардыргычтарын колдонот. Көк анда кийинки инъекция циклине даяр болот.
- Кийинки иштетүү: Чыгаргандан кийин, тетик кыркып алуу, кыруу, же үстүн тазалоо сыяктуу кийинки иштетүү операцияларынан өтүшү мүмкүн. Бул кадамдар ашыкча материалды алып салууга, орой четтерин жылмалоого жана тетиктин акыркы көрүнүшүн жакшыртууга жардам берет.
- Сапатты текшерүү: Акыркы кадам сапаты үчүн сайылган бөлүктөрүн текшерүү жана алардын көрсөтүлгөн талаптарга жооп берүүсүн камтыйт. Сапатты башкаруунун ар кандай ыкмалары, анын ичинде өлчөмдүү өлчөө, визуалдык текшерүү жана функционалдык тестирлөө бөлүктүн сапатын жана бүтүндүгүн текшерүү үчүн колдонулушу мүмкүн.
- Кайра иштетүү жана материалдарды кайра пайдалануу:Инъекциялык формада пайда болгон ар кандай ашыкча же калдык материалды кайра иштетүүгө жана кайра колдонууга болот. Жаңы термопластикалык материалдарды колдонууну азайтуу калдыктарды азайтууга жана туруктуулукту жакшыртууга жардам берет.
Инжектордук формада колдонулган жабдуулар
Бул жабдуулардын компоненттери термопластикалык материалды эритүү жана инъекциялоодон тартып формага келтирүү, муздатуу жана акыркы бөлүгүн чыгарууга чейин инъекциялык калыптоо процессин жеңилдетет. Бул жабдуулардын компоненттерин туура иштетүү жана тейлөө эффективдүү, жогорку сапаттагы инжектордук форма өндүрүшүнө жетишүү үчүн өтө маанилүү.
- Injection Fording Machine:Инъекциялык формадагы негизги жабдуулар термопластикалык материалды эритүү, аны калыпка киргизүү жана процессти көзөмөлдөө үчүн жооптуу.
- көк: Пластикалык бөлүктүн каалаган формасын жана өзгөчөлүктөрүн түзүү үчүн атайын иштелип чыккан калып эки жарымдан, көңдөйдөн жана өзөктөн турат. Операторлор аны инжектордук формалоочу машинанын кысуучу блогуна орнотушат.
- Хоппер:Термопластикалык материалды гранулда же гранулда кармаган жана эрүү жана инъекция үчүн инъекциялык калыптоо машинасынын бочкасына берүүчү контейнер.
- Баррель жана бурамалар: Баррель, цилиндрдик камера, термопластикалык материалды эритет жана гомогенизациялайт, анткени бурама анын ичинде айланып, материалды эритип, аралаштырып жана стандартташтырат.
- Жылытуу жана муздатуу системалары:Инжектордук формалоо машиналарында баррлдин температурасын көтөрүү үчүн электр жылыткычтары же ысык майды колдонгон жылыткычтар сыяктуу жылытуу элементтери жана калыпты муздатуу жана пластикалык бөлүгүн бекемдөө үчүн суу же май айлануу сыяктуу муздатуу системалары бар.
- Эжектор системасы:Катуулангандан кийин калыптанган бөлүгүн калыптын көңдөйүнөн чыгарат, адатта, калыпты ачуу учурунда эжектор төөнөгүчтөрдү, плиталарды же аба жардыргычтарын колдонот.
- Control системасы:Инжектордук формалоо процессинин ар кандай параметрлерин көзөмөлдөйт жана көзөмөлдөйт, бул операторлорго инъекциянын ылдамдыгы, температура, басым жана муздатуу убактысы сыяктуу параметрлерди орнотууга жана жөнгө салууга мүмкүндүк берет.
Injection Fording Machines: түрлөрү жана мүнөздөмөлөрү
Инжектордук формалоочу машинанын ар бир түрү өзүнүн өзгөчөлүктөрүнө жана артыкчылыктарына ээ, бул өндүрүүчүлөргө өндүрүштүк талаптарга ылайыктуу аппаратты тандоого мүмкүндүк берет.
- Гидротехникалык инжектордук калыптоо машиналары: Бул машиналар калыпка эриген пластмасса куюу үчүн керектүү басымды түзүү үчүн гидротехникалык системаларды колдонушат. Алар жогорку кысуу күчү, так башкаруусу жана ар кандай термопластика менен иштөөдө ар тараптуулугу менен белгилүү. Гидротехникалык машиналар ири өндүрүш үчүн ылайыктуу болуп саналат жана татаал калыптарды жайгаштыра алат.
- Электр инжектордук калыптоо машиналары:Электр машиналары машинанын иштеши үчүн электр серво кыймылдаткычтарын, анын ичинде инжектордук, кысуу жана эжектордук системаларды колдонушат. Алар гидравликалык машиналарга караганда так башкарууну, энергияны үнөмдөөчүлукту жана тезирээк жооп берүүнү сунуштайт. Электр машиналары жогорку кайталануучулукту жана тактыкты талап кылган так калыптоо колдонмолору үчүн идеалдуу.
- Гибриддик инъекциялык калыптоо машиналары:Гибриддик машиналар гидравликалык жана электрдик түзүлүштөрдүн артыкчылыктарын айкалыштырат. Алар жогорку тактыкка, энергиянын натыйжалуулугуна жана үнөмдүүлүгүнө жетүү үчүн гидротехникалык жана электрдик серво системалардын айкалышын колдонушат. Гибриддик машиналар өндүрүмдүүлүк менен эксплуатациялык чыгымдардын ортосундагы тең салмактуулукту камсыз кылуучу колдонмолордун кеңири спектри үчүн ылайыктуу.
- Эки пластинкалуу инъекциялык калыптоо машиналары: Эки пластинкалуу машиналар калыпты кысуу үчүн эки өзүнчө пластинадан турган уникалдуу конструкцияга ээ. Бул дизайн жакшыртылган туруктуулукту, калыптын синхрондоштурууну жакшыртып, көктүн чоңураак өлчөмдөрүн жана жогорку кысуучу күчтөрдү камсыз кылат. Эки пластинкалуу машиналар так калыптандырууну талап кылган чоң жана татаал бөлүктөргө ылайыктуу.
- Көп компоненттүү инжектордук калыптоо машиналары:Өндүрүүчүлөр бул машиналарды бир калыптоо циклинде бир нече материалдар же түстөр менен бөлүктөрүн өндүрүү үчүн иштеп чыгышат. Аларда ар кандай инъекциялык агрегаттар жана калыптар бар, алар бир эле учурда ар кандай материалдарды инъекциялоого мүмкүндүк берет. Көп компоненттүү машиналар ар кандай мүнөздөмөлөргө ээ татаал тетиктерди өндүрүүдө ийкемдүүлүктү жана натыйжалуулукту сунуштайт.
- Микро-инъекциялык калыптоо машиналары:Атайын кичинекей жана так бөлүктөрүн өндүрүү үчүн иштелип чыккан, микро-инъекциялык калыптоо машиналар укмуштуудай жогорку тактык жана тактык сунуш кылат. Алар катуу толеранттуулук жана минималдуу материалдык калдыктар менен татаал деталдарды чыгара алышат. Электроника, медициналык аппараттар жана микро-оптика көбүнчө микро инъекциялык калыптоо машиналарын колдонушат.
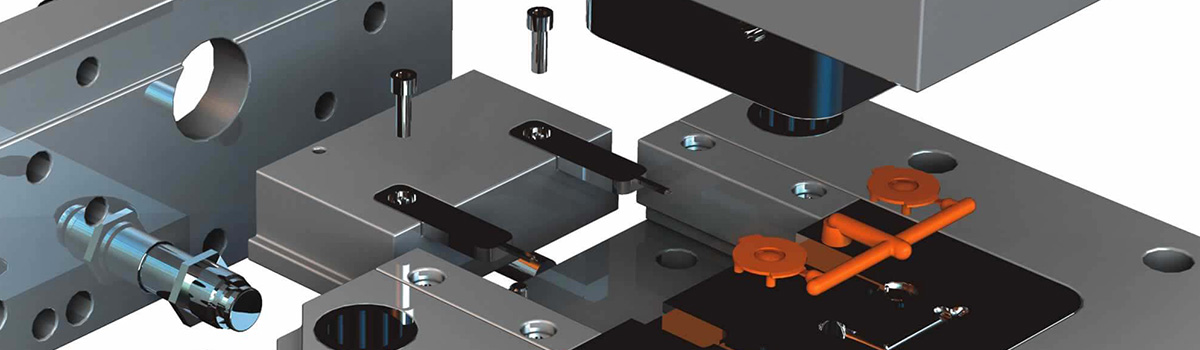
Инжекциялык калыптоо үчүн калыптын дизайнын кароо
Көктүн дизайнын кылдаттык менен кароо ийгиликтүү инжектордук форманы өндүрүү үчүн маанилүү.
- Бөлүмдүн дизайны:Калыптын дизайны бөлүктүн өзгөчө талаптарын, анын ичинде формасын, өлчөмдөрүн жана функционалдык өзгөчөлүктөрүн эске алышы керек. Өндүрүүчүлөр чийме бурчтарын, дубалдын калыңдыгын, астыңкы кесилиштерин жана чыгаруунун оңойлугун жана бөлүктүн сапатын камсыз кылуу үчүн керектүү элементтерди туура карап чыгышы керек.
- Көк материалы: Көк материалды тандоо бышыктыкка, өлчөмдүү туруктуулукка жана ысыкка туруктуулукка жетүү үчүн өтө маанилүү. Common көк материалдар болот эритмелери, алюминий эритмелери, жана аспап болот. Материалды тандоо өндүрүш көлөмү, бөлүктүн татаалдыгы жана куралдын күтүлгөн мөөнөтү сыяктуу факторлорго көз каранды.
- Системасын муздатуу:Натыйжалуу муздатуу бөлүктүн туура катууланышы жана цикл убактысын азайтуу үчүн маанилүү. Калыптын дизайны муздатуу каналдарын же калыптын бир калыпта муздатышын камсыз кылуу үчүн стратегиялык жайгаштырылган кошумчаларды камтууга тийиш. Туура муздатуу ийрилүү, кичирейүү жана бөлүктөрдүн бузулуу коркунучун азайтат.
- Желдетүү:Адекваттуу желдетүү инъекция процессинде абанын жана газдардын сыртка чыгышын камсыз кылуу үчүн зарыл. Жетишсиз желдетүү газ кармагычтарга, күйүк издерине же бөлүктүн толук толтурулбай калышына алып келиши мүмкүн. Өндүрүүчүлөр көктүн дизайнына желдетүүчү оюктарды, төөнөгүчтөрдү же башка механизмдерди киргизүү аркылуу желдетүүгө жетише алышат.
- чыгаруу системасы:Калыптын дизайны калыптанган бөлүгүн калыптын көңдөйүнөн коопсуз жана натыйжалуу алып салуу үчүн эффективдүү чыгаруу системасын камтышы керек. Эжектор системасы функцияга же критикалык өзгөчөлүктөргө тоскоол болбош үчүн стратегиялык жактан жайгаштырылган эжектор төөнөгүчтөрүнөн, жеңдеринен же башка механизмдерден турушу мүмкүн.
- Дарбаза дизайны:Дарбаза эриген пластмасса калыптын көңдөйүнө кирген жер. Дарбазанын дизайны бөлүктүн туура толтурулушун камсыз кылуусу, агымдын сызыктарын азайтуу жана материалдын эрте тоңуп калышына жол бербөө керек. Стандарттык дарбаза конструкциялары бөлүктүн талаптарына жана материалдык касиеттерине жараша четки дарбазаларды, туннель дарбазаларын жана ысык жөө жүрүүчү системаларды камтыйт.
- Ажырашуу сызыгы:Калыптын дизайны ылайыктуу бөлүү сызыгын аныкташы керек, бул көктүн эки жарымы бириккен сызык. Ажыратуу сызыгын туура жайгаштыруу минималдуу жаркырап жана бөлүү сызыгынын дал келбестигин камсыздайт жана форманы эффективдүү чогултууну жеңилдетет.
- Калыпты тейлөө жана тейлөө: Өндүрүүчүлөр тейлөөнүн, оңдоонун жана калыптарды тейлөөнүн жеңилдигин эске алышы керек. Көктүн компоненттери тазалоо, текшерүү жана алмаштыруу үчүн оңой жеткиликтүү болушу керек. Ыкчам алмаштыруучу кыстармалар же модулдук калыптардын конструкциялары сыяктуу функцияларды кошуу көктүн тейлөө мүмкүнчүлүгүн жакшыртат.
Инжектордук формада колдонулган көк материалдар
Көк материал адистери менен кызматташуу жана калыптандыруу өтүнмөнүн спецификалык муктаждыктарын эске алуу оптималдуу көктүн иштешине жана бөлүктүн сапатына жетишүү үчүн эң ылайыктуу материалды аныктоого жардам берет.
- Болот эритмелери: Инструменталдык болоттор (мисалы, P20, H13) жана дат баспас болоттор сыяктуу болот эритмелери, адатта, мыкты бышыктыгына, ысыкка туруктуулугуна жана эскирүүгө туруктуулугуна байланыштуу инъекциялык калыптарга колдонулат. Бул материалдар инъекциялык калыптоо процессиндеги жогорку температурага жана басымга туруштук бере алат жана жогорку сапаттагы тетиктерди өндүрүү үчүн жакшы өлчөмдүү туруктуулукту сунуштайт.
- Алюминий эритмелери:Алюминий эритмелери, мисалы, 7075 жана 6061, жеңил жана жакшы жылуулук өткөрүмдүүлүктү сунуштайт, бул аларды эффективдүү муздатууну талап кылган калыптарга ылайыктуу кылат. Өндүрүүчүлөр көбүнчө прототиптөө, аз көлөмдөгү өндүрүш же салмагын азайтуу маанилүү болгон колдонмолор үчүн алюминий калыптарын колдонушат. Бирок, алюминий калыптар болот эритмелери салыштырмалуу төмөн бышык болушу мүмкүн.
- Жез эритмелери:Жез эритмелери, мисалы, бериллий жез, жогорку жылуулук өткөрүмдүүлүктү жана жакшы иштетилүүнү көрсөтөт. Алар эффективдүү муздатуу үчүн мыкты жылуулук өткөрүүнү талап кылган калыптарда колдонулат. Жез эритмелери калыптанган бөлүктөн жылуулукту тез таратып, цикл убакыттарын кыскартууга жардам берет, натыйжада тезирээк катуулашат.
- Tool Steels:H13, S7 жана D2, анын ичинде аспап болоттору, жогорку өндүрүмдүүлүгү инструменталдык колдонмолор үчүн иштелип чыккан. Бул болоттор жогорку күч, катуулук жана эскирүү туруктуулугун айкалыштырат. Аспап болоттору жогорку өндүрүш көлөмү, абразивдик материалдар же калыптоо шарттары талап кылынган калыптарга ылайыктуу.
- Никель эритмелери:Никель эритмелери, мисалы, Inconel жана Hastelloy, алардын өзгөчө коррозияга туруктуулугу, жогорку температуранын күчү жана жылуулук туруктуулугу менен белгилүү. Өндүрүүчүлөр бул эритмелерди жегич материалдар менен иштөөчү формаларда колдонушат же экстремалдык температурага жана агрессивдүү калыптоо чөйрөсүнө каршылык көрсөтүүнү талап кылат.
- Композиттик материалдар:Композиттик материалдар, мисалы, арматураланган пластмассалар же металл кошумчалары бар композиттер, кээде белгилүү бир калыптоо үчүн колдонулат. Бул материалдар жогорку күч, термикалык туруктуулук жана кыскартылган салмак сыяктуу касиеттердин балансын сунуштайт. Композиттик калыптар белгилүү бир өндүрүштүк талаптар үчүн экономикалык жактан натыйжалуу альтернатива боло алат.
Инъекциялык калыптардын түрлөрү
Инжектордук форма - пластикалык тетиктерди жасоонун ар тараптуу жана кеңири колдонулуучу процесси.
- Эки пластинкалуу калып:Эки пластинкалуу калып - инъекциялык калыптын эң кеңири таралган түрү. Ал эки пластинкадан, көңдөй пластинкадан жана калыптанган бөлүктүн чыгарылышына мүмкүндүк берүүчү өзөк пластинкасынан турат. Көңдөй пластина форманын көңдөй жагын камтыйт, ал эми өзөк пластина өзөк тарабын камтыйт. Өндүрүүчүлөр салыштырмалуу жөнөкөй дизайнына байланыштуу тетиктердин кеңири спектрин өндүрүү үчүн эки плиталуу калыптарды колдонушат.
- Үч пластинкалуу калып:Үч пластинкалуу калып эки табак форманын өркүндөтүлгөн түрү. Ал кошумча табакты, жөө күлүктү же балтырды камтыйт. Жөө күлүк пластина балка, жөө күлүктөр жана дарбазалар үчүн өзүнчө канал түзүп, калыптанган бөлүгүн оңой алып салууга мүмкүндүк берет. Өндүрүүчүлөр, адатта, татаал дарбаза системалары бар деталдар үчүн үч пластиналуу калыптарды колдонушат же бөлүктө дарбаза калдыктарын болтурбоо керек.
- Hot Runner Mold:Жөө күлүк жана дарбаза системасы ысык күлүк калыптарында жылытылат, бул ар бир циклде материалдын катуулануу жана кайра эрүү зарылдыгын жокко чыгарат. Ыстык чуркоо системасы пластиктин эриген абалын сактаган жылытылган коллекторлордон жана саптамалардан турат. Ыстык күлүк калыптары цикл убактысын кыскартуу, материалдык калдыктарды азайтуу жана дарбаза калдыктарын азайтуу менен тетиктердин сапатын жакшыртуу сыяктуу артыкчылыктарды сунуштайт.
- Cold Runner Mold: Муздак күлүк калыптары салттуу күлүк жана дарбаза системасы бар, мында эриген пластмасса муздак күлүктөр аркылуу агып, ар бир циклде катуулайт. Операторлор кийинчерээк катууланган жөө күлүктөрдү алып салышат, натыйжада материалдык калдыктар пайда болот. Өндүрүүчүлөр, адатта, азыраак көлөмдөгү өндүрүш үчүн же алардын жөнөкөй дизайнына байланыштуу материалдык чыгымдар анча маанилүү болбогондо, татаал күлүк калыптарын колдонушат.
- Калып киргизүү:Кыстаруу калыптары инъекциялык калыптоо учурунда калыптын көңдөйүнө металл же пластмассадан кыстармаларды камтыйт. Кыстармалар калыпка алдын ала салынышы же автоматташтырылган процесстер аркылуу салынышы мүмкүн. Бул калып кошумча компоненттерди же бекемдөөчү элементтерди калыпка келтирилген бөлүккө кошууга, анын иштөө мүмкүнчүлүгүн же күчүн жогорулатууга мүмкүндүк берет.
- Overmold: Ашыкча калыптандыруу бир материалды экинчисинин үстүнө калыптандырууну камтыйт, адатта, катуу пластикалык субстратты жумшак эластомер же термопластика менен бириктирет. Бул процесс бир калыпта бир нече материалдар же текстуралар менен бөлүктөрдү түзүүгө мүмкүндүк берет, жакшыртылган кармаш, жумшак же эстетикалык өзгөчөлүктөрдү камсыз кылат.
Injection Molding чыгымдарына таасир этүүчү факторлор
Бул факторлорду эске алуу өндүрүүчүлөргө инжектордук форманын баасын баалоого жана оптималдаштырууга жардам берип, алардын конкреттүү өндүрүштүк талаптары үчүн сапаттын, эффективдүүлүктүн жана экономикалык натыйжалуулуктун ортосундагы балансты камсыздай алат.
- Бөлүк татаалдыгы:Бөлүктүн конструкциясынын татаалдыгы инжектордук форманын баасын аныктоодо чоң роль ойнойт. Татаал геометриялар, астыңкы кесүүлөр, жука дубалдар же татаал өзгөчөлүктөр кошумча шаймандарды, адистештирилген калыптарды же узун циклдерди талап кылышы мүмкүн, бул жалпы өндүрүштүн наркын жогорулатат.
- Материалдарды тандоо:Термопластикалык материалды тандоо инжектордук формага баага таасир этет. Ар кандай материалдардын килограммына ар кандай баалар бар жана материалдык болушу, касиеттери жана иштетүү талаптары сыяктуу факторлор жалпы материалдык чыгымга таасир этиши мүмкүн.
- Куралдар жана калыптардын дизайны: Баштапкы инструменттер жана калыптарды долбоорлоо чыгымдары инжектордук формага чыгымдарда олуттуу. Көктүн татаалдыгы, көңдөйлөрдүн саны, калыптын өлчөмү жана калыптын материалы сыяктуу факторлор шаймандарды жана калыптарды даярдоого кеткен чыгымдарга салым кошот. Өркүндөтүлгөн функцияларды талап кылган татаал формалар же калыптар алдын ала инвестицияны көбөйтөт.
- Өндүрүштүн көлөмү: Өндүрүштүн көлөмү инжектордук формада бир бөлүктүн наркына түздөн-түз таасир этет. Жогорку китептер көбүнчө бөлүктүн баасын төмөндөтүп, масштабдуу үнөмдөөгө алып келет. Тескерисинче, аз көлөмдөгү өндүрүш процесстери орнотуу, шаймандар жана материалдык калдыктардан улам жогорураак чыгымдарды талап кылышы мүмкүн.
- Цикл убактысы: Муздатуу жана чыгаруу фазаларын камтыган цикл убактысы өндүрүштүк кубаттуулукка жана жалпы чыгымга таасирин тийгизет. Узак цикл мезгили өндүрүштүн көлөмүн азайтууга жана баанын жогорулашына алып келет. Калыптын дизайнын, муздатуу системасын жана процесстин параметрлерин оптималдаштыруу цикл убактысын азайтып, эффективдүүлүктү жакшыртат.
- Сапаттуу талаптар:Катуу сапат талаптары же атайын сертификаттар инжектордук форманын баасына таасир этиши мүмкүн. Так толеранттуулуктарды канааттандыруу, беттик бүтүрүү талаптары же кошумча тестирлөө жалпы чыгымды кошуп, башка ресурстарды, процесстерди же текшерүүлөрдү талап кылышы мүмкүн.
- Экинчи операциялар:Эгерде калыпка салынган тетиктер монтаждоо, сырдоо же кошумча бүтүрүү кадамдары сыяктуу кийинки кайра иштетүү операцияларын талап кылса, бул операциялар инжектордук форманын жалпы наркын кошо алат.
- Жабдуучу жана жайгашкан жери:Инжектордук форма берүүчүнү тандоо жана алардын жайгашкан жери чыгымдарга таасир этиши мүмкүн. Эмгек чыгымдары, кошумча чыгымдар, логистика жана транспорттук чыгымдар жеткирүүчүнүн жайгашкан жерине жараша өзгөрүп, жалпы өндүрүштүн наркына таасир этет.
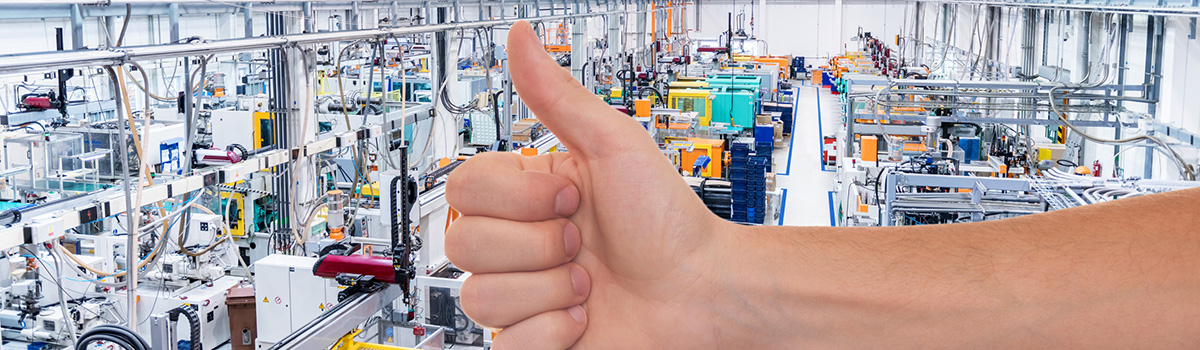
Инжектордук формада сапатты көзөмөлдөө
Инжектордук формалоо процессинде сапатты көзөмөлдөөнүн күчтүү чараларын ишке ашыруу мүмкүн болуучу кемчиликтерди, четтөөлөрдү же карама-каршылыктарды аныктоого жана чечүүгө жардам берет, кардарлардын спецификацияларына жана талаптарына жооп берген жогорку сапаттагы тетиктерди өндүрүүнү камсыз кылат.
- Процесс мониторинги: Эрүү температурасы, инъекциянын басымы, муздатуу убактысы жана цикл убактысы сыяктуу процесстин негизги параметрлерине үзгүлтүксүз мониторинг бөлүктөрдү өндүрүүдө ырааттуулукту жана кайталанууну камсыз кылат. Реалдуу убакыт режиминде мониторинг жана автоматташтырылган системалар белгиленген параметрлерден вариацияларды же четтөөлөрдү аныктай алат, бул өз убагында тууралоолорду жүргүзүүгө жана процесстин туруктуулугун сактоого мүмкүндүк берет.
- Текшерүү жана өлчөө:Калыпталган бөлүктөрүн үзгүлтүксүз карап чыгуу жана өлчөө өлчөмдүн тактыгын, бөлүктүн сапатын жана спецификациялардын сакталышын текшерүү үчүн маанилүү. Биздин кызматтар сапатты көзөмөлдөөнүн бир катар ыкмаларын камтыйт, мисалы, өлчөмдөрдү өлчөө, беттин сапатын талдоо, визуалдык текшерүүлөрдү жүргүзүү жана функционалдык тесттерди жүргүзүү. Так баа берүү үчүн ар кандай текшерүү ыкмалары, мисалы, координатты өлчөөчү машиналар (CMM) жана оптикалык жана визуалдык текшерүү системалары колдонулат.
- Статистикалык процессти башкаруу (СПК): SPC инжектордук форманын сапатын көзөмөлдөө жана көзөмөлдөө үчүн процесстик маалыматтарды чогултууну жана талдоону камтыйт. Башкаруу диаграммалары жана процесстин мүмкүнчүлүктөрүн талдоо сыяктуу статистикалык ыкмалар тенденцияларды аныктоого, процесстин вариацияларын аныктоого жана процесстин аныкталган контролдук чектерде сакталышын камсыз кылууга жардам берет. SPC маселелерди проактивдүү аныктоого мүмкүндүк берет жана процессти оптималдаштырууга көмөктөшөт.
- Материалдык тестирлөө: Термопластика, кошумчалар жана боектор сыяктуу чийки материалдарды сыноо алардын сапатын жана инъекциялык формага ылайыктуулугун камсыздайт. Материалдык тестирлөө эрүү агымынын индексин (MFI) анализин, механикалык касиеттерин, жылуулук мүнөздөмөлөрүн жана материалдын курамын камтышы мүмкүн. Материалдын сапатын текшерүү калыптанган бөлүктөрдөгү кемчиликтерди жана дал келбестиктерди алдын алууга жардам берет.
- Инструментти тейлөө жана текшерүү:Инжекциялык калыптарды туура тейлөө жана үзгүлтүксүз текшерүү инжектордук формада сапатты камсыз кылуу үчүн өтө маанилүү. Калыптын компоненттерин үзгүлтүксүз тазалоо, майлоо жана баалоо бөлүктүн сапатына таасир эте турган эскирүүнүн, бузулуунун же бузулуунун алдын алууга жардам берет. Эскирген же бузулган калыптын компоненттерин өз убагында оңдоо же алмаштыруу ырааттуу калыптоо ишин камсыз кылуу үчүн маанилүү.
- Документтер жана байкоо жүргүзүү:Комплекстүү документтерди жана байкоо жүргүзүү жазууларын жүргүзүү инъекциялык формада сапатты көзөмөлдөө үчүн абдан маанилүү. Процесстин параметрлерин, текшерүүнүн натыйжаларын, материалдык маалыматты жана өндүрүш учурунда жасалган ар кандай өзгөртүүлөрдү же оңдоолорду жазуу өтө маанилүү. Туура документация бөлүктөргө байкоо жүргүзүүгө мүмкүндүк берет, түпкү себептерди талдоону жеңилдетет жана сапаттын ырааттуулугун камсыз кылат.
- Окутуу жана көндүмдөрдү өнүктүрүү: Операторлор, техниктер жана сапатты көзөмөлдөөчү персонал үчүн адекваттуу окутуу жана көндүмдөрдү өнүктүрүү программаларын камсыз кылуу алардын инжектордук формалоо процесстерин, сапат талаптарын жана текшерүү ыкмаларын түшүнүүсүн күчөтөт. Жакшы даярдалган персонал кемчиликтерди таап, көйгөйлөрдү чечип, оңдоп-түзөө чараларын натыйжалуу ишке ашырып, сапаттуу өндүрүштү камсыздай алат.
Инжектордук формада кеңири таралган кемчиликтер жана алардан кантип сактануу керек
Инжектордук форма процесстерин үзгүлтүксүз текшерүү, мониторинг жүргүзүү жана талдоо жана жабдууларды жана калыптарды туура тейлөө жана жөнгө салуу бул жалпы кемчиликтерди аныктоого жана жоюуга жардам берет.
- Раковина белгилери:Раковинанын белгилери — калыптанган бөлүктүн бетиндеги тегиз эмес муздатуудан же кичирейүүдөн пайда болгон оюктар же оюктар. Дарбазанын туура жайгашуусун жана дизайнын, муздатуу тутумунун оптималдуу дизайнын жана раковинанын белгилерин болтурбоо үчүн дубалдын калыңдыгын бирдей бөлүштүрүүнү эске алуу керек. Инъекциянын басымын жогорулатуу же муздатуу убактысын тууралоо да чөгүп кеткен белгилерди азайтууга жардам берет.
- Warpage:Согулуу деп калыптанган тетиктин тегиз эмес муздатуудан же калдык чыңалуудан улам сыртка чыгарылгандан кийин деформациясы же ийилиши айтылат. Дубалдын калыңдыгын бир калыпта кармоо, муздатуу каналдарын туура колдонуу жана калыптын тең салмактуу толтурулушун жана таңгактоосун камсыз кылуу бузулууну алдын алуу үчүн өтө маанилүү. Көктүн температурасын оптималдаштыруу, ылайыктуу бурчтарды колдонуу жана материалдын температурасын жана инъекциянын ылдамдыгын көзөмөлдөө бузулууну азайтууга жардам берет.
- Flash:Жарык ашыкча материал калыптын бөлүү сызыгына агып кеткенде пайда болот, натыйжада жука, керексиз проекциялар же акыркы бөлүктө кошумча материал пайда болот. Калыптын туура дизайнын камсыз кылуу, анын ичинде адекваттуу кысуу күчүн колдонуу, так тегиздөө жана тиешелүү желдетүү ыкмаларын колдонуу менен жарк этүүнү эффективдүү алдын алса болот. Инъекциянын басымы, температура жана цикл убактысы сыяктуу процесстин параметрлерин оптималдаштыруу жарк этүүнү азайтат.
- Кыска кадр:Инъекцияланган материал көктүн көңдөйүн толтурбай калганда тез атуу болот, натыйжада толук эмес бөлүгү пайда болот. Кыска сүрөттөрдү болтурбоо үчүн материалды туура тандоо, эритмелердин адекваттуу температурасын жана илешкектүүлүгүн камсыз кылуу жана инъекциянын тиешелүү басымын жана убактысын сактоо зарыл. Кошумчалай кетсек, калыптын дизайнын жетиштүү жөө күлүк жана дарбаза өлчөмү жана туура желдетүү үчүн текшерүү тез атуулардын алдын алууга жардам берет.
- Ширетүү линиялары:Шире сызыктары эки же андан көп эриген материалдын агымынын фронттору жолугушуп, катып калганда пайда болот, натыйжада бөлүктүн бетинде көрүнгөн сызык же белги пайда болот. Жакшы дарбаза жана жөө күлүк дизайн, оптималдуу эрүү температурасы, сайынуу ылдамдыгы, ошондой эле материалдын агымын жана геометрияны жөнгө салуу ширетүүчү сызыктарды азайтуу мүмкүн. Көктүн агымын талдоо жана дарбазаны жайгаштырууну оптималдаштыруу да ширетүүчү сызыктарды алдын алууга же жумшартууга жардам берет.
- Күйүү белгилери:Күйүк издери – бул материалдын ашыкча ысышы же ашыкча ысып кетүүсүнөн улам калыптанган бөлүктүн бетиндеги түстүн өзгөрүшү же кара тактар. Ашыкча эрүү температурасына жол бербөө, тиешелүү муздатуу каналдарын колдонуу жана цикл убактысын оптималдаштыруу күйүк белгилерин алдын алууга жардам берет. Адекваттуу желдетүү, дарбазанын туура дизайны жана көктүн температурасын көзөмөлдөө күйүк белгилерин азайтууга өбөлгө түзөт.
Калыптан кийинки операциялар: бүтүрүү жана монтаждоо
Инжектордук формадан кийин, көптөгөн калыпка салынган тетиктер каалаган акыркы продуктуга жетүү үчүн кошумча бүтүрүү жана монтаждоо операцияларын талап кылышы мүмкүн. Бул формалоодон кийинки операциялар төмөнкүлөрдү камтышы мүмкүн:
- Кыркуу:Ашыкча материалды алып салыңыз же кыркуучу же кесүүчү шаймандарды колдонуп калыптанган бөлүктүн тегерегинде жарк этиңиз.
- Surface Дарылоо:Сырдоо, каптоо же текстуралоо сыяктуу ар кандай ыкмаларды колдонуу менен бөлүктүн бетинин көрүнүшүн же функционалдуулугун жогорулатуу.
- Ассамблея:Бир нече калыпка салынган бөлүктөрдү бириктирүү же акыркы продуктуну аяктоо үчүн бекиткичтер, салгычтар же энбелгилер сыяктуу компоненттерди кошуу.
- Testing:Өлчөмдүү талдоо, материалдык касиеттерин тестирлөө же аткарууну сыноо сыяктуу ар кандай тестирлөө ыкмалары аркылуу бөлүктүн сапатын жана иштешин текшерүү.
- Таңгактоо жана жеткирүү:Кардарларга же акыркы колдонуучуларга жөнөтүү үчүн даяр продукцияны туура таңгактоо жана маркировкалоо.
Калыптан кийинки операцияларды тандоо конкреттүү колдонууга жана акыркы продукттун каалаган мүнөздөмөсүнө жараша болот. Каалаган абсолюттук продукт сапатына жана функционалдуулугуна жетүү үчүн инжектордук форма боюнча эксперттер, бүтүрүү жана монтаждоо боюнча адистер жана кардардын ортосундагы тыгыз кызматташуу абдан маанилүү. Туура пландаштыруу жана формалоодон кийинки операцияларды өндүрүш процессине киргизүү эффективдүү өндүрүштү жана жогорку сапаттагы продукцияны өз убагында жеткирүүгө жардам берет.
Injection Molding vs. Башка пластмасса өндүрүш процесстери
Ар бир пластмасса өндүрүш процессинин артыкчылыктары жана чектөөлөрү бар, аларды ар кандай колдонуу үчүн ылайыктуу кылат.
- Injection Molding: Инжекциялык калыптоо - пластикалык тетиктерди өндүрүү үчүн өтө универсалдуу жана кеңири колдонулган өндүрүш процесси. Ал өндүрүштүн жогорку эффективдүүлүгү, бөлүктү так кайталоо жана татаал геометрияларды түзүү мүмкүнчүлүгү сыяктуу артыкчылыктарды сунуш кылат. Инжекциялык калыптоо жогорку көлөмдөгү өндүрүш үчүн ылайыктуу жана термопластикалык материалдардын кеңири спектрин колдонууга мүмкүндүк берет. Бул эң сонун өлчөмдүү тактыкты жана беттин жасалгасын сунуштайт, бул аны автомобиль, керектөөчү товарлар жана медициналык аппараттар сыяктуу ар кандай тармактар үчүн идеалдуу кылат.
- Үлпөтүү: Үлмөлөө - бул негизинен бөтөлкөлөр, контейнерлер жана унаа тетиктери сыяктуу көңдөй пластик бөлүктөрүн өндүрүү үчүн колдонулган процесс. Ал пластикти эритип, аны калыптын көңдөйүнө үйлөп, керектүү форманы түзүүнү камтыйт. Үлмөлөө чоң көлөмдөгү өндүрүш үчүн ылайыктуу жана дубалдын калыңдыгы бирдей чоң, жеңил бөлүктөрдү чыгара алат. Бирок, инжектордук формага салыштырмалуу бөлүктүн татаалдыгы жана материалды тандоо жагынан чектелген.
- Термоформалоо:Термоформалоо - бул термопластикалык баракты ысытуу жана калыптарды же вакуумдук формада калыптандыруу жолу менен пластик бөлүктөрдү өндүрүү үчүн колдонулган процесс. Ал таңгактарда, бир жолу колдонулуучу буюмдарда жана лотоктор жана капкактар сыяктуу чоң масштабдагы буюмдарда кеңири колдонулат. Thermoforming чоң тетиктер үчүн үнөмдүү өндүрүштү сунуштайт жана тез прототиптештирүүгө мүмкүндүк берет. Бирок, инжектордук формага салыштырмалуу бөлүктүн татаалдыгы, материалды тандоо жана өлчөмдүү тактык боюнча чектөөлөр бар.
- атылуусунан:Экструзия пластикалык профилдерди, барактарды, түтүктөрдү жана пленкаларды өндүрүү үчүн үзгүлтүксүз процесс. Бул пластикалык чайырды эритип, керектүү форманы түзүү үчүн аны формадан өткөрүүнү камтыйт. Экструзия ырааттуу кесилиши менен узун, үзгүлтүксүз узундуктагы пластикалык буюмдарды өндүрүү үчүн ылайыктуу. Экструзия жогорку өндүрүш темпин жана экономикалык эффективдүүлүктү сунуш кылганы менен, инжектордук формага салыштырмалуу татаал бөлүктүн геометриясы жана так өлчөмдүү башкаруу жагынан чектелген.
- Компрессиялык калыптоо:Компрессиялык формада ысытылган калыптын көңдөйүнө алдын ала өлчөнгөн көлөмдөгү термореактивдүү материалды коюу жана ал айыкканга чейин жогорку басым астында кысуу кирет. Бул унаа компоненттери жана электр изоляциясы сыяктуу жогорку күч жана өлчөмдүү туруктуу бөлүктөрдү өндүрүүдө кеңири колдонулат. Компрессиялык калыптоо бөлүктөрдүн жакшы ырааттуулугун, өндүрүштүн жогорку натыйжалуулугун жана материалдардын кеңири спектрин колдонуу мүмкүнчүлүгүн сунуш кылат. Бирок, ал инжектордук формага салыштырмалуу бөлүктүн татаалдыгы жана цикл убактысы жагынан чектелген.
Термопластикалык Injection Molding Колдонмолору
Ар түрдүү тармактарда термопластикалык инъекциялык калыптоо анын ар тараптуулугу, эффективдүүлүгү жана экономикалык жактан натыйжалуулугунан улам кеңири колдонулат. Термопластикалык инжектордук форманын айрым колдонмолоруна төмөнкүлөр кирет:
- Автоунаа өнөр жайы: Автоунаа өнөр жайы ар кандай тетиктерди, анын ичинде ички жана тышкы жасалгаларды, аспаптар такталарын, эшик панелдерин, бамперлерди жана электр туташтыргычтарын өндүрүү үчүн термопластикалык инъекциялык форманы кеңири колдонот. Процесс бөлүктөрдү так кайталоого, татаал геометрияга жана жеңил материалдарды алууга мүмкүндүк берип, күйүүчү майдын натыйжалуулугун жана дизайн ийкемдүүлүгүн жогорулатат.
- Керектөөчү товарлар:Инжектордук формалар тиричилик техникасы, электрондук аппараттар, таңгактоочу контейнерлер жана оюнчуктар сыяктуу керектөө товарларын өндүрүүдө кеңири колдонууну табат. Процесс ырааттуу өлчөмдөрү жана үстүнкү бети менен бышык, жогорку сапаттагы буюмдарды массалык түрдө чыгарууга мүмкүндүк берет. Ал ошондой эле ыңгайлаштыруу параметрлерине жана продуктуну тез итерациялоого мүмкүндүк берет.
- Медициналык аппараттар:Инъекциялык калыптоо медицина тармагында шприцтерди, хирургиялык аспаптарды, имплантациялоочу компоненттерди жана дары-дармектерди жеткирүү системаларын камтыган кеңири спектрди өндүрүү үчүн маанилүү ролду ойнойт. Процесс стерилдүү, так жана биологиялык шайкеш бөлүктөрдү өндүрүүнү камсыз кылат, алар саламаттыкты сактоо секторунун катуу ченемдик талаптарына жооп берет.
- Электроника жана электротехника өнөр жайы:Электроника өнөр жайы электр туташтыргычтарды, корпустарды, өчүргүчтөрдү жана башка компоненттерди өндүрүү үчүн инжектордук форманы колдонот. Процесс жогорку өлчөмдүү тактыкты, беттин эң сонун жасалгасын жана татаал электрондук жыйындарды эффективдүү өндүрүүгө мүмкүндүк берүүчү кыстаруу жана ашыкча формалоо сыяктуу өзгөчөлүктөрдү камтуу мүмкүнчүлүгүн сунуштайт.
- Таңгактоо өнөр жайы:Ар кандай тармактар, анын ичинде тамак-аш жана суусундуктар, фармацевтика жана жеке кам көрүү, көбүнчө пластикалык таңгактоочу контейнерлерди, капкактарды, жабууларды жана бөтөлкөлөрдү өндүрүү үчүн инъекциялык форманы колдонушат. Процесс эффективдүү өндүрүш циклдери менен жеңил, бышык жана эстетикалык жактан жагымдуу таңгактоо чечимдерин түзүүгө мүмкүндүк берет.
- Аэрокосмикалык өнөр жайы:Аэрокосмостук сектордо аба өткөргүчтөрү, кашаалар, ички панелдер жана структуралык бөлүктөр сыяктуу жеңил жана жогорку өндүрүмдүүлүктөгү компоненттерди өндүрүү үчүн инжектордук форманы колдонот. Бул процесс алдыңкы материалдарды жана татаал тетиктердин геометриясын колдонууга мүмкүндүк берип, салмакты азайтууга жана күйүүчү майдын натыйжалуулугун жогорулатууга салым кошот.
Термопластикалык инжектордук форманын айлана-чөйрөгө тийгизген таасири
Термопластикалык инъекциялык калыптоо көптөгөн артыкчылыктары менен популярдуу өндүрүш процесси болуп саналат, бирок анын айлана-чөйрөгө тийгизген таасирин да эске алуу зарыл. Бул жерде эске алуу керек болгон кээ бир жагдайлар бар:
- Материалдык натыйжалуулугу:Термопластикалык инъекциялык калыптоо калдыктарды азайтуу менен материалдын натыйжалуулугун жогорулатат. Процесс формага сайылган материалдын көлөмүн так көзөмөлдөөнү колдонуп, ашыкча материалга болгон муктаждыкты азайтат. Өндүрүүчүлөр сыныктарды же четке кагылган тетиктерди кайра колдонуу үчүн кайра майдалоо жана кайра иштетүү ыкмаларын колдонушу мүмкүн, бул материалдык калдыктарды андан ары азайтат.
- Energy Керектөө:Өндүрүүчүлөр инъекциялык калыптоо машиналарын энергияны үнөмдөөчү кылып иштеп чыгышат, заманбап моделдер сервомоторлор жана өзгөрүлмө ылдамдыктагы дисктер сыяктуу алдыңкы технологияларды камтыган. Бул өзгөчөлүктөр калыптандыруу учурунда электр энергиясын керектөөнү азайтуу аркылуу энергияны колдонууну оптималдаштырат, натыйжада энергияга болгон талаптар азаят жана айлана-чөйрөгө тийгизген таасири азаят.
- Таштандыларды башкаруу:Материалдык калдыктарды азайтуу менен бирге, өндүрүүчүлөр калдыктарды, калканчтарды же жөө күлүктөрдү иштетүү үчүн таштандыларды башкаруунун туура ыкмаларын ишке ашырышы керек. Өндүрүүчүлөр инъекциялык формада пайда болгон пластик калдыктарын чогултуу жана кайра пайдалануу үчүн кайра иштетүү программаларын түзө алышат, ошону менен полигонго жөнөтүлгөн калдыктарды азайтат.
- Эмиссияны азайтуу: Термопластикалык инъекциялык калыптоо жалпысынан башка өндүрүш процесстерине караганда азыраак эмиссияларды жаратат. Өндүрүүчүлөр экологиялык таза материалдарды колдонуу, энергияны үнөмдөөчү жабдууларды ишке ашыруу, ошондой эле ар кандай чыгындыларды кармоо үчүн өнүккөн соргуч жана чыпкалоо системаларын колдонуу менен эмиссияларды азайта алышат.
- Туруктуу материалдарды тандоо:Термопластикалык материалдарды тандоо инжектордук форманын экологиялык туруктуулугуна олуттуу таасир этиши мүмкүн. Биологиялык жактан ажырай турган же био-негизделген пластмассаларды, ошондой эле кайра иштетилүүчү же кайра иштетилүүчү материалдарды тандоо процесстин жалпы экологиялык изин азайтууга жардам берет.
Жашоо циклинин кароолору: Калыпталган буюмдун бүт жашоо циклин эске алуу анын айлана-чөйрөгө тийгизген таасирин баалоо үчүн абдан маанилүү. Долбоорлоо жана материал тандоо этаптарында өндүрүүчүлөр тетиктин туруктуулугу, анын кайра иштетүүгө жөндөмдүүлүгү жана колдонуу мөөнөтү аяктагандан кийин утилдештирүү же кайра колдонуу потенциалы сыяктуу факторлорду эске алышы керек.
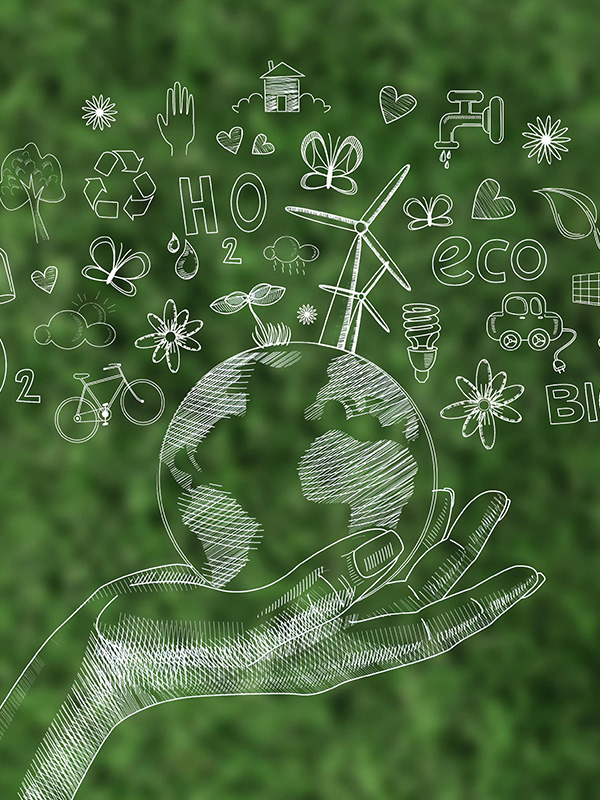
Термопластикалык инъекциялык калыптын келечеги
Термопластикалык инъекциялык форманын келечеги келечектүү көрүнөт, технологиянын өнүгүшү жана ар кандай тармактарда жогорку сапаттагы, так тетиктерге суроо-талаптын өсүшү. Жакынкы жылдарда күтүлгөн негизги окуялардын айрымдары төмөнкүлөрдү камтыйт:
- натыйжалуулугун жогорулатуу жана чыгымдарды азайтуу үчүн автоматташтыруу жана робототехниканы колдонуунун өсүшү.
- Күчтөр бөлүктүн иштешин жакшыртуу жана жаңы колдонмолорду иштетүү үчүн жаңы материалдарды жана процесстерди иштеп чыгууга багытталган.
- Бул инжектордук форманын айлана-чөйрөгө тийгизген таасирин азайтуу үчүн кайра иштетилген материалдарды колдонуу жана энергияны керектөөнү оптималдаштыруу сыяктуу туруктуу практикалардын өсүп келе жаткан кабыл алынышы.
- Дизайн жана өндүрүш процесстерин жакшыртуу үчүн 3D басып чыгаруу жана симуляциялык программалык камсыздоо сыяктуу санариптик технологияларды көбүрөөк интеграциялоо.
Инжектордук форманын глобалдык рыногу, айрыкча өнүгүп келе жаткан экономикаларда, ар кандай тармактарда пластикалык буюмдарга суроо-талаптын өсүшү менен шартталган.
Туура Injection Molding өнөктөш тандоо
Долбооруңуздун ийгилиги үчүн инжектордук форма боюнча өнөктөштү туура тандоо абдан маанилүү. Бир нече варианттарды баалоого, сайтка барууга жана шайкеш жана узакка созулган өнөктөштүктү камсыз кылуу үчүн кылдат талкуулоого убакыт бөлүңүз.
- Экспертиза жана тажрыйба:Өнөр жайда кеңири билими жана тажрыйбасы бар инжектордук форма боюнча өнөктөш издеңиз. Алар ар кандай секторлордогу кардарларга жогорку сапаттагы өнүмдөрдү жана чечимдерди жеткирүү боюнча далилденген тажрыйбага ээ болушу керек. Алардын ар кандай материалдар, калыптардын конструкциялары жана өндүрүш процесстери жөнүндө түшүнүгүн карап көрөлү.
- Өндүрүштүк мүмкүнчүлүктөр: Инжектордук форма боюнча өнөктөштүн өндүрүштүк мүмкүнчүлүктөрүн баалоо. Долбооруңуздун талаптарын аткаруу үчүн алар заманбап техника жана технологиялар менен жакшы жабдылган объектиге ээ болуңуз. Алардын өндүрүштүк кубаттуулугун, бөлүктөрүнүн ар кандай өлчөмдөрүн жана татаалдыктарын чечүүгө жөндөмдүүлүгүн жана сиз каалаган өндүрүш көлөмүн жана мөөнөттөрүн канааттандыруу мүмкүнчүлүгүн карап көрүңүз.
- Сапатты кармоо:Инжектордук формада сапат биринчи орунда турат. Потенциалдуу өнөктөштүн сапатты көзөмөлдөө тутумдарына жана сертификаттарына баа берүү. Катуу сапат стандарттарын карманган, текшерүү процесстери күчтүү жана бөлүктөрдүн сапатын жана ырааттуулугун камсыз кылуу үчүн комплекстүү тестирлөөдөн өткөн өнөктөштөрдү издеңиз.
- Дизайн жана инженердик колдоо:Ишенимдүү инъекциялык калыптоо өнөктөшү сиздин бөлүктөрүңүздүн дизайнын өндүрүшкө ылайыкташтыруу үчүн дизайн жана инженердик колдоону сунушташы керек. Алар материалды тандоодо, калыптарды долбоорлоодо жана процессти оптималдаштырууда бөлүктүн сапатын жана натыйжалуулугун жогорулатуу боюнча баалуу салымдарды бере турган квалификациялуу инженерлерге ээ болушу керек.
- Чыгымдардын атаандаштыкка жөндөмдүүлүгү:Наркы жалгыз аныктоочу фактор болбошу керек, бирок инжектордук форма боюнча өнөктөштүн баасын жана атаандаштыкка жөндөмдүүлүгүн баалоо маанилүү. Көбүрөөк цитаталарды сураңыз жана инструментке кеткен чыгымдарды, материалдык чыгымдарды, эмгек чыгымдарын жана алар көрсөткөн кошумча кызматтарды карап көрүңүз.
- Байланыш жана кызматташуу:Натыйжалуу байланыш жана кызматташуу ийгиликтүү өнөктөштүк үчүн маанилүү. Инжектордук форма боюнча өнөктөштүн жакшы байланыш каналдары бар экенине, сиздин сурооңузга жооп бере ала турганына жана долбоордун үзгүлтүксүз жаңыртууларын камсыздай ала тургандыгына кепилдик бериңиз. Биргелешип иштөө биздин талаптарды канааттандырууга жана бардык кыйынчылыктарды тез арада чечүүгө жардам берет.
- Кардар шилтемелери жана сын-пикирлер:Башка кардарлардын инжектордук форма боюнча өнөктөшү менен болгон тажрыйбалары тууралуу түшүнүк алуу үчүн кардарлардын шилтемелерин издеңиз же сын-пикирлерди/күбөлүктөрдү окуңуз. Бул маалыматты алуу алардын ишенимдүүлүгүн, ыкчамдыгын жана кардарлардын жалпы канааттануу деңгээлин аныктоого жардам берет.
жыйынтыктоо
Термопластикалык инъекциялык калыптоо - бул көп сандагы пластикалык тетиктерди өндүрүү үчүн ар тараптуу жана үнөмдүү ыкма. Анын жогорку тактык жана ырааттуулук менен татаал формаларды чыгарууга жөндөмдүүлүгү ар кандай тармактарда, анын ичинде автомобиль, медициналык, электроника жана керектөөчү товарлар үчүн популярдуу тандоо болуп калды. Термопластикалык инъекциялык форманын ар кандай аспектилерин, анын ичинде анын артыкчылыктарын, кемчиликтерин жана дизайндык ойлорду түшүнүү менен, сиз бизнес муктаждыктарыңыз үчүн туура инжектордук өнөктү тандоо жөнүндө негизделген чечим кабыл ала аласыз.