Inject Injection Molding
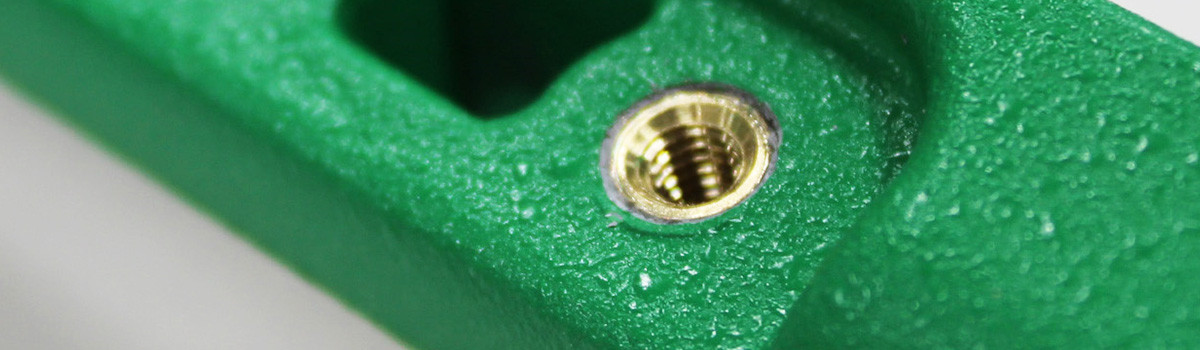
Insert инъекциялык калыптоо - бул камтылган компоненттери бар татаал пластик бөлүктөрдү өндүрүүдө кеңири колдонулган өндүрүш процесси. Бул ыкма инъекциялык калыптоо процессинин алдында калыптын көңдөйүнө металл же пластик бөлүктөрдү киргизүүнү камтыйт. Андан кийин эриген материал киргизилген элементтин айланасында агып, эки материалдын ортосунда бекем байланышты түзөт. Insert инъекциялык калыптоо бир нече артыкчылыктарды сунуш кылат, анын ичинде жакшыртылган дизайн ийкемдүүлүгү, кыскартылган чогултуу убактысы жана жакшыртылган бөлүктүн иштеши. Бул комплекстүү колдонмо инъекциялык форманын ар кандай ыкмаларын, артыкчылыктарын жана колдонмолорун изилдейт.
Insert Injection Molding деген эмне?
Injection калыптоо бөлүктөрү жана буюмдардын ар кандай түзүү үчүн колдонулган өндүрүш жараяны болуп саналат. Кыстаруу инъекциялык калыптоо - калыпка салуу процесси башталганга чейин калыпка алдын ала түзүлгөн элементтерди же вставкаларды киргизүүгө мүмкүндүк берген инжектордук форманын бир түрү. Бул ыкма салттуу сайынуу ыкмалары жетише албаган өзгөчө өзгөчөлүктөрүн талап кылган бөлүктөрүн түзүүгө мүмкүндүк берет.
Кыстаруу инъекциялык калыптоо формалоо процесси башталардан мурун калыптын көңдөйүнө алдын ала даярдалган кыстарманы коюу менен иштейт. Кыстарма ар кандай материалдарды, анын ичинде металл, пластик жана керамика камтышы мүмкүн. Калыптоо процесси адаттагыдай эле башталат, көктүн көңдөйүнө эриген пластик куюлат. Пластмасса муздап, катып калганда, ал кыстарма менен биригип, бирдиктүү, бирдиктүү бөлүккө айланат.
Инъекциялык форманы колдонуунун бир нече артыкчылыктары бар. Бул техниканын негизги артыкчылыктарынын бири, ал салттуу сайынуу ыкмалары жетише албаган өзгөчө өзгөчөлүктөрү бар бөлүктөрдү түзүүгө мүмкүндүк берет. Мисалы, кыстаруу инъекциялык калыптоо, эгерде функцияга арматура үчүн жиптүү кыстарма же металл компонент керек болсо, колдонулушу мүмкүн. Бул ыкма ошондой эле материалдардын айкалышы менен бөлүктөрдү түзүүгө мүмкүндүк берет, мисалы, металл салынуучу пластикалык бөлүк.
Инъекциялык форманын дагы бир артыкчылыгы - убакытты жана акчаны үнөмдөө. Бир нече компоненттерди чогултуунун ордуна, инъекциялык калыптоо бир, интеграцияланган бөлүктү жаратат. Муну менен компаниялар монтаждоо үчүн талап кылынган убакытты жана чыгымдарды кыскарта алышат.
Insert инъекциялык калыптоо татаал бөлүктөрүн түзүү үчүн да пайдалуу. Кыстарманы калыптоо процесси башталганга чейин калыптын көңдөйүнө жайгаштырууга болот, анткени, татаал геометриялык жана өзгөчөлүктөргө ээ бөлүктөрдү чыгарууга болот, аларга инжектордук форманын салттуу ыкмалары аркылуу жетишүү кыйын.
Insert Injection Molding кантип иштейт?
Бул формага түшүрүү процессинин бир түрү, ал калыпка даярдалган тетиктерди же кыстармаларды калыпка салуу процесси башталганга чейин киргизүүгө мүмкүндүк берет. Бул ыкма салттуу инжектордук формалоо ыкмалары жетише албаган спецификалык өзгөчөлүктөргө ээ бөлүктөрдү түзүүгө мүмкүндүк берет жана татаал бөлүктөрдү түзүү үчүн өзгөчө пайдалуу. Бул жерде биз инъекциялык формалоо иштерин кантип киргизүүнү талкуулайбыз.
Кыстаруу инъекциялык калыптоо процесси төмөнкү кадамдарды камтыйт:
- Жайгаштыруу:Кыстарма инъекциялык калыптоо процессинин биринчи кадамы калыптын көңдөйүнө алдын ала даярдалган кошумчаны жайгаштыруу болуп саналат. Өндүрүүчүлөр бул кошумчаны металл, пластик же керамика сыяктуу ар кандай материалдардан чыгара алышат.
- Көк кысуу:Кыстарма орнотулгандан кийин калып жабылат жана кысылып жабылат. Максаты — калыптоо процессинде кыстарманы ордунда кармап туруу.
- Эриген пластикти инъекциялоо:Инъекциялык калыптоо процессинде эриген пластмасса калыптын көңдөйүнө куюлат. Өндүрүүчүлөр адатта пластикти 200 жана 300 градус Цельсийдин ортосундагы температурага чейин ысытып, аны колдонулган конкреттүү пластиктин негизинде аныкташат.
- Муздатуу жана катуулантуу: Пластмасса муздап, катып калганда, ал кыстарма менен биригип, бирдиктүү, бирдиктүү бөлүккө айланат. Муздатуу жана катуулануу убактысы колдонулган конкреттүү пластмассадан жана кесимди жасоонун татаалдыгынан көз каранды.
- Көк ачуу жана чыгаруу: Тетик муздап, катып калгандан кийин, оператор калыпты ачып, буюмду чыгарат. Андан кийин кесим бүткөрүлүп, колдонууга даярдалышы мүмкүн.
Инъекциялык форманы колдонуунун бир нече артыкчылыктары бар. Бул артыкчылыктардын кээ бирлери төмөнкүлөрдү камтыйт:
- Салттуу инжектордук формалоо ыкмалары жетише албаган спецификалык өзгөчөлүктөргө ээ бөлүктөрдү түзүү жөндөмдүүлүгү
- Элементтер бирдиктүү, бирдиктүү бөлүкчө катары жасалышы мүмкүн, натыйжада монтаждоо убактысы жана чыгымдары кыскарат
- Татаал геометриялар жана өзгөчөлүктөр менен татаал бөлүктөрдү түзө билүү
- Металл, пластмасса жана керамика, анын ичинде ар кандай материалдарды колдонуу мүмкүнчүлүгү
- Injection калыптоо жогорку тактык жана тактык менен көп сандагы бөлүктөрүн өндүрө ала турган жогорку натыйжалуу жана кайталануучу процесс.
Инъекциялык формада колдонулуучу кошумчалардын түрлөрү
Өндүрүүчүлөр кошумчаларды жасоо үчүн ар кандай материалдарды, анын ичинде металлды, пластмассадан жана керамикадан колдоно алышат. Бул койгучтар салттуу инжектордук формага салуу ыкмалары жетише албаган өзгөчө өзгөчөлүктөрү бар бөлүктөрдү түзүүгө мүмкүндүк берет. Бул жерде биз инжектордук формада колдонулган кыстармалардын ар кандай түрлөрүн талкуулайбыз.
- Металл кыстармалар:Металл кыстармалар, адатта, пластикалык бөлүктөргө кошумча күч жана туруктуулукту камсыз кылуу үчүн инжектордук формада колдонулат. Алар, адатта, жезден, болоттон же алюминийден жасалат жана колдонууга жараша сай же жипсиз болушу мүмкүн. Өндүрүүчүлөр татаал геометриялык жана жогорку күч жана бекемдикти талап кылган факторлор менен бөлүктөрдү түзүү үчүн металл койгучтарды колдоно алышат.
- Пластикалык Кыстармалар: Пластикалык кыстармалар көбүнчө пластикалык бөлүктөргө колдоо жана бекемдөө үчүн инжектордук формада колдонулат. Алар, адатта, нейлондон, ABS же поликарбонат материалдарынан жасалат жана спецификалык өзгөчөлүктөргө ээ болгон бөлүктөрдү түзө алышат, мисалы, жабышчаак туташуу же сай тешикчелери. Өндүрүүчүлөр пластикалык салмаларды жеңил, үнөмдүү чечимдерди сунуштайт жана ар кандай формаларга жана өлчөмдөргө оңой калыптандырууга жөндөмдүүлүгү үчүн баалашат.
- Керамикалык Кыстармалар: Керамикалык койгучтар жогорку күчтү жана эскирүүгө каршылыкты талап кылган тетиктерди түзүү үчүн инжектордук формада колдонулат. Алар, адатта, цирконий же глинозем сыяктуу материалдардан жасалган жана автомобиль, аэрокосмостук жана медициналык өнөр жай үчүн бөлүктөрүн өндүрүү үчүн колдонулушу мүмкүн. Керамикалык кыстармалар жогорку температурага, коррозияга жана абразияга өтө туруктуу болгондуктан, аларды катаал чөйрөлөр үчүн идеалдуу кылат.
- Композиттик кошумчалар: Өндүрүүчүлөр металл жана пластмасса сыяктуу эки же андан көп материалдарды бириктирип, аларды формага келтирип, композиттик кыстармаларды жаратышат, натыйжада бир, бирдиктүү бөлүк пайда болот. Өндүрүүчүлөр аралаштыргычтарды колдонсо болот, алар салттуу инъекциялык калыптоо ыкмалары жетише албаган өзгөчөлүктөргө ээ бөлүктөрүн иштеп чыгышат. Мындан тышкары, алар өзгөчө колдонмолордун уникалдуу муктаждыктарын канааттандыруу үчүн бул койгучтарды өзгөчө ыңгайлаштыра алышат.
- Overmolded Inserts: Инъекциялык калыптоо процессинде өндүрүүчүлөр пластмассадан жасалган бөлүкчөлөрдү калыпка салышат, натыйжада ашыкча калыпка салынган кыстармалар деп аталат. Бул процесс пластмассадан жасалган биринчи кадрды киргизүүнү, андан кийин бирдиктүү, интеграцияланган бөлүктү түзүү үчүн биринчи кадрдын үстүнө экинчисин орнотууну камтыйт. Өндүрүүчүлөр көбүнчө пластикалык компоненттин ичине металл кыстаруу сыяктуу материалдарды бириктирген бөлүктөрдү түзүү үчүн ашыкча калыптанган кошумчаларды колдонушат.
Металл Кыстармалар vs. Пластикалык Кыстармалар
Процесс пластикалык инъекциялык калыптоо процесси башталганга чейин калыпка коюлган алдын ала даярдалган тетиктерди же кыстармаларды колдонууну камтыйт. Өндүрүүчүлөр ар кандай материалдардан, анын ичинде металлдан жана пластмассадан кыстармаларды жасай алышат жана ар бир түрү өзүнүн уникалдуу артыкчылыктарын жана кемчиликтерин көрсөтөт. Бул макалада металл жана пластмасса кыстармаларды салыштырып, колдонмоңуз үчүн эң жакшы вариантты аныктоого жардам берет.
Металл койгучтар
Өндүрүүчүлөр, адатта, жогорку бекемдикке жана бышыктыгына байланыштуу калыптоодо металл кошумчаларын колдонушат. Алар, адатта, жезден, болоттон же алюминийден жасалат жана колдонууга жараша сай же жипсиз болушу мүмкүн. Металл кыстармалар көбүнчө пластикалык бөлүктөргө кошумча күч жана туруктуулукту камсыз кылуу үчүн инжектордук формада колдонулат.
Металл кыстармалардын артыкчылыктары
- Жогорку күч жана туруктуулук
- Эскирүүгө туруктуу
- Бул жип аркылуу кошумча функцияларды сунуш кыла алат
- Жогорку стресс же жүк көтөрүү талаптары бар бөлүктөр үчүн идеалдуу
Металлдардын кемчиликтери
- Пластикалык кошумчаларга караганда баасы жогору
- Пластикалык кошумчаларга караганда калыптоо кыйыныраак
- Оор, бул конкреттүү колдонмолордо тынчсызданууну жаратышы мүмкүн
Пластикалык Кыстармалар
Пластмассадан жасалган койгучтар ар тараптуулугу жана үнөмдүүлүгү менен калыптандыруу үчүн популярдуу. Өндүрүүчүлөр, адатта, аларды нейлон, ABS же поликарбонат сыяктуу материалдардан жасашат жана аларды ар кандай формада жана өлчөмдөрдө оңой калыпка салышат. Пластмассадан жасалган кыстармалар жеңил жана спецификалык өзгөчөлүктөргө ээ бөлүктөрдү түзө алат, мисалы, жабышчаак туташтыргычтар же сайлуу тешиктер.
Пластикалык Кыстармалардын артыкчылыктары
- Натыйжалуу
- даярдоо
- Ар кандай формада жана өлчөмдөрдө оңой калыпталат
- Төмөнкү стресс же жүк көтөрүү талаптары бар бөлүктөр үчүн идеалдуу
Пластикалык Кыстармалардын кемчиликтери
- Металл койгучтарга караганда азыраак бышык
- Жогорку стресс же жүк көтөрүү талаптары бар бөлүктөр үчүн идеалдуу эмес
- Убакыттын өтүшү менен эскирүү жана эскирүүгө көбүрөөк дуушар болушу мүмкүн
Металл кыстармаларды качан тандоо керек
Металл кыстармалар жогорку бекемдикти жана бышыктыкты талап кылган бөлүктөрдө өзгөчөлөнөт, анткени алар эскирүүгө жана эскирүүгө туруштук берет жана жиптин кошумча функцияларын камсыз кылат. Металл койгучтар ошондой эле жогорку стресс же жүк көтөрүү талаптары бар функциялар үчүн идеалдуу. Бирок, алар пластикалык салмаларга караганда кымбатыраак жана калыптандыруу кыйыныраак болушу мүмкүн.
Металл кыстармаларды талап кыла турган тиркемелер кирет
- Автоунаа жана аэрокосмостук компоненттер
- медициналык аппараттар
- Өнөр жай жабдуулары
- электроника
Пластикалык Кыстармаларды качан тандоо керек
Пластикалык кыстармалар азыраак стресс же жүк көтөрүү талаптары бар бөлүктөр үчүн үнөмдүү жана ар тараптуу. Алар жеңил мүнөздөмөлөрдү көрсөтөт; өндүрүүчүлөр ар кандай калыптарга жана өлчөмдөрдө аларды калыпка болот. Пластмассадан жасалган кыстармалар, ошондой эле жабышчаак туташуу же сай тешиктери сыяктуу өзгөчөлүктөрдү талап кылган кызматтар үчүн идеалдуу. Бирок, алар жогорку стресс же жүк көтөрүүчү талаптар менен деталдар үчүн ылайыктуу болушу керек болушу мүмкүн.
Пластикалык кыстармаларды талап кылган колдонмолор камтылган
- Керектөөчү товарлар
- Тиричилик техникасы
- Оюнчуктар жана оюндар
- электроника
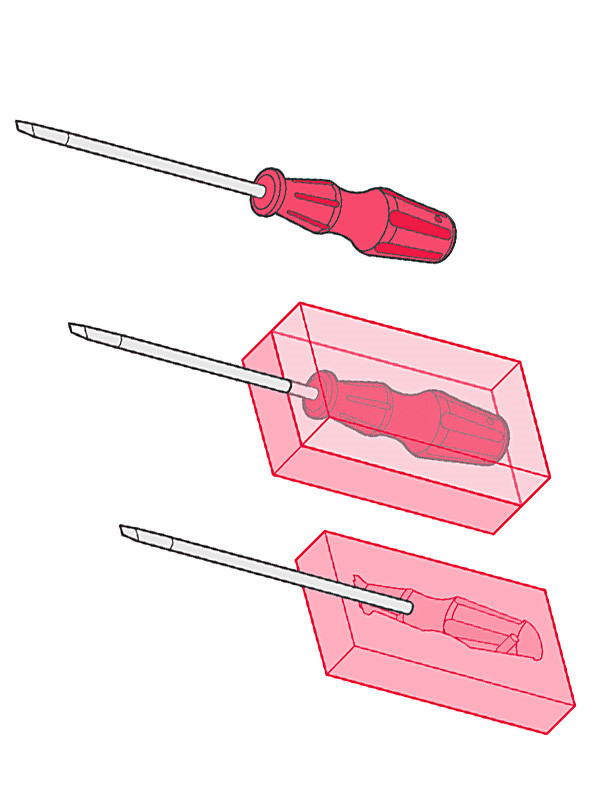
Insert Injection Formding артыкчылыктары
Кыстаруу инъекциялык калыптоо - пластикалык инъекциялоо процесси башталганга чейин калыпка жайгаштырылган алдын ала даярдалган тетиктерди же кыстармаларды камтыган популярдуу өндүрүш процесси. Бул ыкма салттуу калыптоо ыкмаларына караганда көптөгөн артыкчылыктарды сунуштайт, бул ар кандай колдонмолор үчүн популярдуу тандоо. Бул макалада инъекциялык форманын негизги артыкчылыктары талкууланат.
- Нарк-натыйжалуу: Кыстаруу инъекциялык калыптоо үнөмдүү өндүрүш чечими болушу мүмкүн, анткени ал өзүнчө бөлүктөрдү калыпка салуудан кийинки монтаждоо зарылдыгын жок кылат. Калыптоо учурунда кыстармаларды бириктирүү менен, өндүрүүчүлөр өндүрүштүн натыйжалуулугун жогорулатуу менен бирге эмгек жана монтаждоо чыгымдарын азайта алышат.
- Жакшыртылган бөлүктүн күчү: Кыстаруу инъекциялык калыптоо бөлүктүн ар кайсы аймактарында ар кандай материалдарды колдонуу менен бөлүктөрдүн бекемдигин жана туруктуулугун жогорулата алат. Бул өзгөчөлүк жогорку стресске же жүк көтөрүүчү талаптарга туруштук берүү үчүн деталдарды талап кылган колдонмолор үчүн өзгөчө пайдалуу болушу мүмкүн.
- Дизайндын ийкемдүүлүгүн жогорулатуу: Кыстаруу инъекциялык калыптоо дизайндын ийкемдүүлүгүн сунуштайт, анткени ал бир нече өзгөчөлүктөргө жана функцияларга ээ татаал бөлүктөрдү түзөт. Бул процесс татаал конструкцияларга жана геометрияга ылайыктуу болгондуктан, мындай деталдар үчүн идеалдуу тандоо болуп саналат.
- Ырааттуулук жана тактык: Кыстаруу инъекциялык калыптоо бөлүктөрдү өндүрүүдө эң сонун ырааттуулукту жана тактыкты сунуш кылат. Биз калыпка алдын ала даярдалган койгучтарды так жайгаштырабыз, алардын ар бир бөлүктүн талаптарына ылайык так жайгаштырылышын камсыздайбыз. Натыйжада, биз өндүрүлгөн бөлүктөрдө бирдиктүү өлчөмдөргө жана өзгөчө сапатты көзөмөлдөөгө жетишебиз.
- Кыскартылган цикл убактысы: Кыстаруу инъекциялык калыптоо бир процесске бир нече кадамдарды бириктирүү аркылуу цикл убактысын кыскарта алат. Бул ыкма убакытты үнөмдөөгө жана өндүрүмдүүлүктү жогорулатууга жардам берет, айрыкча, жогорку көлөмдөгү өндүрүш менен иштөөдө.
- Материалдардын ар түрдүүлүгү: Кыстаруу инъекциялык форманы ар кандай материалдар, анын ичинде пластик, металл жана керамика менен колдонсо болот. Өндүрүүчүлөр азыр күчүн, бышыктыгын жана баасын эске алуу менен ар кандай колдонуу үчүн эң ылайыктуу материалды тандай алышат.
- Экологиялык пайдалары: Кыстаруу инъекциялык калыптоо таштандыларды азайтуу жана материалдарды колдонууну азайтуу аркылуу экологиялык пайдаларды да сунуштай алат. Кыстармаларды калыпка так жайгаштыргандыктан, биз салттуу калыптоо ыкмаларына караганда материалдык калдыктарды азыраак сезебиз. Муну ишке ашыруу айлана-чөйрөгө тийгизген таасирдин азайышына жана өндүрүштүк чыгымдардын кыскарышына алып келиши мүмкүн.
Кыстарууну калыптандыруу үчүн долбоорлоо маселелери
Кыстарма калыптоо - бул алдын ала даярдалган койгучтарды пластикалык инъекциялык калыптоо процессине интеграциялоону камтыган популярдуу өндүрүш процесси. Бул техника көптөгөн артыкчылыктарды сунуштайт, анын ичинде бөлүктүн күчүнүн жакшырышы, монтаждоо чыгымдарынын азайышы жана дизайндын ийкемдүүлүгү жогорулайт. Бирок, кыстарма калыптоо үчүн бөлүктөрүн долбоорлоо ийгиликтүү жана натыйжалуу өндүрүштү камсыз кылуу үчүн бир нече факторлорду кылдаттык менен карап чыгууну талап кылат. Бул макалада кыстаруу калыптандыруу үчүн негизги дизайн ойлордун айрымдары талкууланат.
- Жайгаштыруу: Кыстарманы калыптын ичинде жайгаштыруу кыстаруу процессинин ийгилиги үчүн абдан маанилүү. Пластикалык материал калыптоо процессинде аны толугу менен капсулалаш үчүн кыстарма калыптын ичинде так жайгаштырылышы керек. Дизайнерлер ошондой эле пластмассалык материалдын агымына тоскоол болбошун же бөлүү сызыгында көйгөйлөрдү жаратпасын камсыз кылышы керек.
- Материалдык шайкештик: Кыстарма жана пластмасса материалы үчүн материалдарды тандоо кыстаруу калыптоо процессинин ийгилиги үчүн өтө маанилүү. Байланыш маселелерин же материалдык келишпестиктерди болтурбоо үчүн материалдар шайкеш болушу керек. Дизайнерлер эрүү чекити, кичирейүү жана термикалык кеңейүү коэффициенти сыяктуу материалдын касиеттерин кылдаттык менен карап чыгышы керек.
- Бөлүмдүн геометриясы: Бөлүктүн геометриясы кыстаруу формасында дагы бир маанилүү жагдай болуп саналат. Дизайн пластмасса материалды туура толтурууга жана аны толук капсулалашына кепилдик бериши керек. Бөлүктүн геометриясы ошондой эле ийрилүү, кичирейүү же чөгүп кетүү белгилерин болтурбоо үчүн адекваттуу желдетүү жана муздатуу мүмкүнчүлүгүн бериши керек.
- Долбоордук бурчтар жана асты кесүү: Долбоордун бурчтарынын жана астыңкы кесилиштеринин болушу кыстарма калыптоодо бөлүктүн калыпка келүүсүнө таасир этиши мүмкүн. Дизайнерлер бөлүккө же калыпка эч кандай зыян келтирбестен, форманы калыптан оңой алып салууну камсыз кылуу үчүн бурчтардын жана астыңкы кесүүлөрдүн жайгашуусун жана геометриясын кылдаттык менен карап чыгышы керек.
- Аспаптарды кароо: Кыстарма калыптоо үчүн талап кылынган аспаптар салттуу калыптоо ыкмаларына караганда татаалыраак болушу мүмкүн. Дизайнерлер калыптын дизайнын, анын ичинде коюунун жана геометриянын, дарбазаны жана желдеткичти жана зарыл болгон кошумча аракеттерди кылдаттык менен карап чыгышы керек. Кошумчалай кетсек, инструмент туура жайгаштырууну камсыз кылуу жана бөлүктүн сапаты менен байланышкан көйгөйлөрдүн алдын алуу үчүн катуу толеранттуулуктарды сактоого жөндөмдүү болушу керек.
Insert Injection Fording колдонулган материалдар
Insert инъекциялык калыптоо татаал бөлүктөрүн так жана ырааттуу чыгара турган жогорку адистештирилген процесс. Бул процесс, инъекциялык формага чейин калыпка киргизилген кыстармалар деп аталган алдын ала даярдалган функцияларды колдонууну камтыйт. Бул койгучтар ар кандай материалдардан жасалышы мүмкүн, алардын ар бири уникалдуу касиеттери жана артыкчылыктары бар. Бул жерде биз инъекциялык формада колдонулган эң кеңири таралган материалдарды жана алардын артыкчылыктарын талкуулайбыз.
металлдар
Инжектордук формада болот, алюминий жана жез сыяктуу металлдардан жасалган кыстармалар кеңири колдонулат. Бул материалдар мыкты бекемдикти жана бышыктыкты сунуштайт, бул аларды тозууга жана жыртылууга туруктуулукту талап кылган тетиктер үчүн идеалдуу кылат. Мындан тышкары, металл койгучтар жогорку температурага туруштук бере алат, бул аэрокосмостук жана автомобиль өнөр жайы сыяктуу талап кылынган колдонмолордо колдонууга ылайыктуу. Инжектордук формада металл кыстармаларды колдонуунун айрым артыкчылыктары төмөнкүлөрдү камтыйт:
- Жогорку күч жана туруктуулук
- Мыкты жылуулук каршылык
- коррозия каршылык
- Жогорку басымга жана стресске туруштук берүү мүмкүнчүлүгү
пластмассадан
Пластикалык кыстармалар көбүнчө инъекциялык формада колдонулат, PEEK, PTFE жана UHMW сыяктуу материалдар популярдуу тандоо болуп саналат. Бул материалдар жогорку температурага туруктуулукту, химиялык каршылыкты жана аз сүрүлүү касиеттерин сунуштайт. Бул компоненттер медициналык приборлордо жана жарым өткөргүчтөрдү өндүрүүдө колдонуу үчүн абдан ылайыктуу, анткени алардын жогорку тактыгы жана тазалыгы ошол колдонмолордо маанилүү фактор болуп саналат. Инжектордук формада пластикалык кыстармаларды колдонуунун айрым артыкчылыктары төмөнкүлөрдү камтыйт:
- Жогорку химиялык туруктуулук
- Мыкты температура каршылык
- Төмөн сүрүлүү касиеттери
- Машина жасоо жана калыптандыруу оңой
Керамика
Инъекциялык формада керамикалык кыстармалар жогорку бекемдигине, катуулугуна жана эскирүүгө туруктуулугуна байланыштуу колдонулат. Бул материалдар бөлүк жогорку температурага же катаал чөйрөгө туруштук бериши керек болгон колдонмолордо колдонуу үчүн идеалдуу. Мындан тышкары, керамикалык койгучтар мыкты өлчөмдүү туруктуулукту сунуштайт, бул аларды так инженердик колдонмолорго ылайыктуу кылат. Инжектордук формада керамикалык кыстармаларды колдонуунун айрым артыкчылыктары төмөнкүлөрдү камтыйт:
- Жогорку күч жана катуулугу
- Эскирүүгө мыкты каршылык
- Жогорку температура каршылык
- өлчөмдүү туруктуулук
композит
Композиттик материалдар, мисалы, көмүртек буласы же айнектен жасалган була, алардын жогорку күч-салмак катышы үчүн инжектордук формада колдонулат. Аэрокосмостук жана автомобиль өнөр жайы көбүнчө салмакты азайтуу маанилүү болгон бул материалдарды колдонушат. Композиттик кыстармалар жогорку катуулукту жана күчтү сунуштайт, бул аларды шамал турбиналары жана жогорку натыйжалуу спорттук жабдуулар үчүн идеалдуу кылат. Инжектордук формада композиттик кыстармаларды колдонуунун айрым артыкчылыктары төмөнкүлөрдү камтыйт:
- Салмагы менен күчүнүн жогорку катышы
- Жогорку катуулугу жана күчү
- Жакшы таасир каршылык
- Төмөнкү жылуулук кеңейүү коэффициенти
резина
Силикон же неопрен сыяктуу резина материалдары ийкемдүүлүгү жана мөөр басуу касиеттери үчүн инжектордук формада колдонулат. Бул материалдар, адатта, мөөр жана жаздык маанилүү болгон медициналык жана унаа өнөр жайында колдонулат. Резина кыстармалар химиялык заттарга жана жогорку температурага эң сонун каршылык көрсөтөт, бул аларды катаал шарттарда колдонуу үчүн идеалдуу кылат. Инжектордук формада резина кыстармаларды колдонуунун айрым артыкчылыктары төмөнкүлөрдү камтыйт:
- Мыкты жабуу касиеттери
- Жогорку ийкемдүүлүк
- Химиялык жана температурага туруктуулук
- Жакшы дирилдештирүү
көбүк
Полиуретан же полистирол сыяктуу пенопласт материалдар жеңил жана шок жутуу касиеттери үчүн инжектордук формада колдонулат. Бул материалдар көбүнчө таңгактоо жана унаа өнөр жайларында колдонулат, анда жумшартуу жана таасирге туруштук берүү зарыл. Пенопласт жогорку изоляцияны сунуштайт, бул аларды температурага сезгич колдонмолор үчүн идеалдуу кылат. Инжектордук формада пенопласттарды колдонуунун айрым артыкчылыктары төмөнкүлөрдү камтыйт:
- Жеңил жана ийкемдүү
- Мыкты шок жутуу
- Жакшы жылуулоо касиеттери
- Анын татаал формаларды калыптандыруу жөндөмдүүлүгү
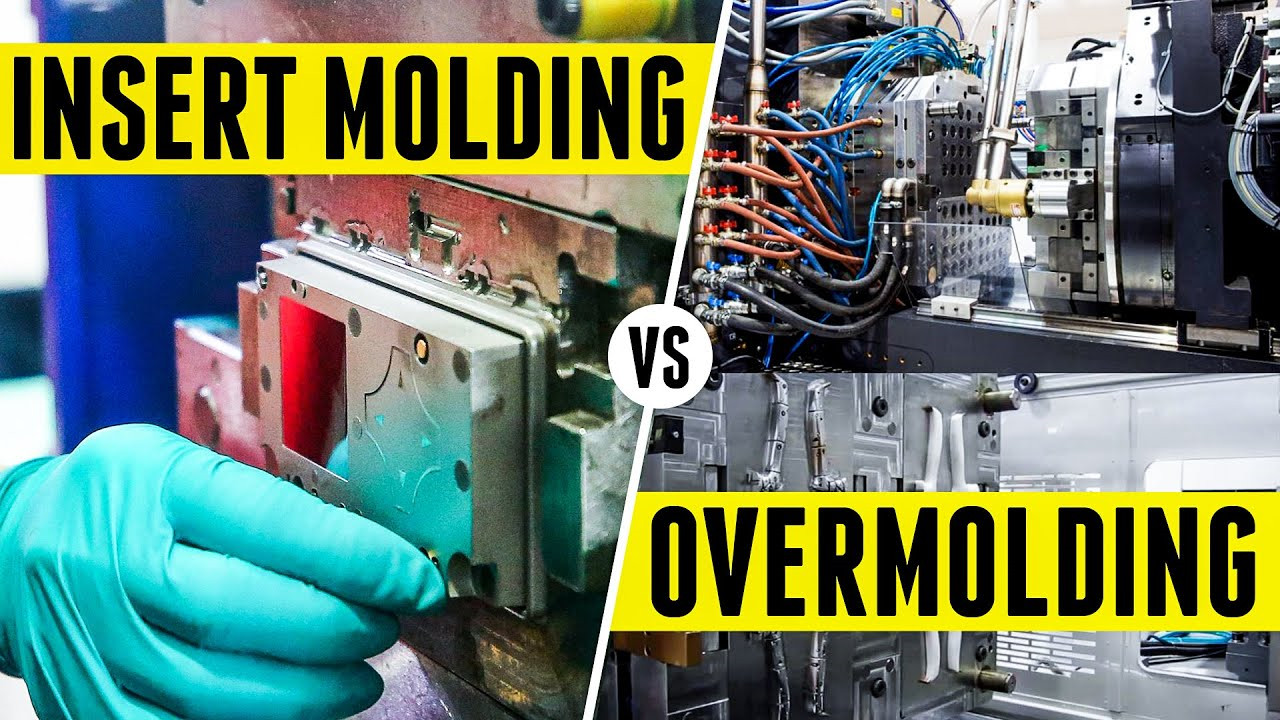
Insert Molding vs Overmolding: Кандай айырма бар?
Кыстарма калыптоо жана ашыкча формалоо бир нече материалдарды камтыган сайынуу формасында кеңири колдонулган эки процесс. Бул процесстер окшош көрүнгөнү менен, кээ бир негизги айырмачылыктары бар. Бул жерде биз кыстарма калыптандыруу менен ашыкча калыптандыруунун ортосундагы айырмачылыктарды талкуулайбыз.
Insert Molding
Кыстарма калыптоо – бул инъекциялык калыптоо процесси ишке ашар алдында калыпка киргизүү деп аталган алдын ала даярдалган тетиктерди киргизүүнү камтыган процесс. Андан кийин пластмассадан жасалган материал кошумчалардын тегерегине сайылып, пластмасса материалы менен пластмассанын касиеттерин айкалыштырган даяр продукт пайда болот. Бул процесс көбүнчө автомобиль, медициналык жана аэрокосмостук өнөр жайларында жогорку тактык менен тетиктерди түзүү үчүн колдонулат.
Киргизүүнүн артыкчылыктары
- Жогорку тактык жана тактык
- Жакшыртылган бөлүктүн бекемдиги жана туруктуулугу
- Кыскартылган монтаждоо убактысы жана наркы
- Ар кандай касиеттери бар материалдарды айкалыштыра билүү
Ашыкча калыптоо
Overmolding - бул мурда болгон бөлүккө экинчи материалды инъекциялоону камтыган процесс. Өндүрүүчүлөр бул процессти жумшак тийүү туткаларын, кармагычтарды жана башка керектөө буюмдарын түзүү үчүн колдонушат. Ашыкча калыптанган материал, адатта, жумшак жана резина сымал, жакшыраак кармашты жана ыңгайлуулукту камсыз кылат. Тетиктин татаалдыгына жараша, биз бир же эки атуучу процессте ашыкча формалоону аткара алабыз.
Ашыкча калыптандыруунун артыкчылыктары
- Жакшыртылган эргономика жана эстетика
- Жакшыртылган кармаш жана комфорт
- Кыскартылган монтаждоо убактысы жана наркы
- Ар кандай касиеттери бар материалдарды айкалыштыра билүү
Кыстарма калыптоо менен ашыкча калыптандыруунун ортосундагы айырмачылыктар
- Кыстаруу калыптоо алдын ала даярдалган тетиктерди киргизүүнү камтыйт, ал эми overmolding мурда болгон бөлүктүн үстүнө экинчи материалды инъекциялоодон турат.
- Биз жогорку тактыктагы бөлүктөрдү түзүү үчүн кыстарма форманы колдонобуз, ал эми буюмдун эргономикасын жана эстетикасын жогорулатуу үчүн ашыкча калыптандырууну колдонобуз.
- Кыстаруу формасында ар кандай касиеттери бар материалдарды айкалыштыруу кирет, ал эми ашыкча калыптоо ашыкча калыпка салынган бөлүгү үчүн жумшак, резина сымал материалды колдонууну камтыйт.
- Кыстарма калыптоо көбүнчө автоунаа, медициналык жана аэрокосмостук өнөр жайларында колдонулат, ал эми ашыкча калыптоо көбүнчө шаймандар, электроника жана жеке гигиеналык буюмдар сыяктуу керектөө буюмдарында колдонулат.
Кыстаруу техникасы
Кыстарма калыптоо - бул инъекциялык калыптоо процесси башталганга чейин калыпка алдын ала даярдалган тетиктер же вставкалар салынган процесс. Пластикалык материал даяр буюмду түзүү үчүн койгучтардын айланасына сайылат. Кыстармаларды жайгаштыруу кыстаруу калыптоо процессинин ийгилиги үчүн өтө маанилүү. Бул жерде биз кыстаруу жайгаштыруунун кээ бир ыкмаларын талкуулайбыз.
- Кол менен жайгаштыруу: Оператор кол менен бул техникада калыпка салып коёт. Өндүрүүчүлөр, адатта, бул ыкманы кичинекей же түз бөлүктөр үчүн колдонушат, алар бир нече кыстарууну талап кылат. Бирок, ал көп убакытты жана эмгекти көп талап кылат жана кол менен орноткондуктан ката кетирүү коркунучу жогору.
- Автоматташтырылган жайгаштыруу: Бул техникада кыстармалар калыпка робот же тандоо жана жайгаштыруучу машина сыяктуу компьютердик системанын жардамы менен жайгаштырылат. Бул ыкма кол менен жайгаштырууга караганда тезирээк жана так, аны ири өндүрүштүк же татаал бөлүктөр үчүн идеалдуу кылат. Бирок, ал жабдууларга алгачкы инвестицияны талап кылат жана чакан өндүрүш үчүн үнөмдүү болушу керек.
- Калыптын үстүнөн калыпка салуу: Кыстармаларды экинчи, ашыкча калыптанган бөлүккө салып, андан кийин аны негизги калыпка салабыз. Өндүрүүчүлөр бул ыкманы көбүнчө татаал геометриялык же жетүүгө кыйын жерлери бар дооматтар үчүн колдонушат. Ал ошондой эле ар кандай касиеттери бар материалдарды, мисалы, жумшак калыпка салынган материал менен катуу пластикалык кыстармаларды айкалыштыра алат.
- Жабышкак жабыштыргычтар:Бул техникада биз кошумчаларды жабышчаак таяныч менен алдын ала каптайбыз, бул кол менен же автоматташтырылган жайгаштырууну талап кылбастан калыпка салууга мүмкүндүк берет. Чабылган жабышчаак инъекциялык формада эрип, пластмасса материалга кыстарууну бириктирет. Бул ыкма көбүнчө кичинекей, жөнөкөй бөлүктөр үчүн колдонулат жана өндүрүш убактысын жана баасын азайтат.
- Жиптүү кошумчалар: Бул техникада жиптүү кошумчалар калыпка салынып, даяр буюмда жиптерди түзүү үчүн колдонулат. Өндүрүүчүлөр бул ыкманы көбүнчө электрондук шаймандар же унаа тетиктери сыяктуу бурама же болт киргизүүнү талап кылган өнүмдөрдү өндүрүүдө колдонушат.
Insert Injection Fording Machines түрлөрү
Инжекциялык калыптоо процессинин негизги компоненттеринин бири - инжектордук калыптоо машинасы. Бул машиналар уникалдуу өзгөчөлүктөрү жана артыкчылыктары менен ар кандай түрлөрү бар. Бул жерде биз инъекциялык калыптоо машиналарынын ар кандай түрлөрүн карап чыгабыз.
Биринчиден, инъекциялык формалоочу машина деген эмне экенин аныктап алалы. Кыстарма инъекциялык калыптоо машинасы - бул пластик материалды сайганга чейин калыпка металл же пластмасса кыстармалар сыяктуу алдын ала түзүлгөн компоненттерди киргизүүгө мүмкүндүк берген инжектордук калыптоо машинасы. Бул мүмкүнчүлүктүн жардамы менен, сай тешиктери же металл таянычтар сыяктуу кошумча функцияларды талап кылган татаал бөлүктөрдү жасоо мүмкүн болот.
Бул жерде инъекциялык калыптоо машиналарынын ар кандай түрлөрү бар:
- Вертикалдык инъекциялык калыптоо машиналары:Бул машиналар вертикалдык багыттуу дизайнга ээ, алар калыпты вертикалдуу орнотушат. Алар кыстарманы калыпка салуу үчүн идеалдуу, анткени алар кыстарманы калыпка жогору жактан оңой киргизүүгө мүмкүндүк берет. Машинанын бул түрү дагы азыраак мейкиндикти ээлейт жана азыраак өндүрүш иштерине ылайыктуу.
- Горизонталдык инъекциялык калыптоо машиналары:Бул машиналар горизонталдуу түрдө калыпты орнотулган жалпак багыттуу дизайнга ээ. Алар ири өндүрүштүк иштетүү үчүн мыкты ылайыктуулугун сунуш, жана өндүрүүчүлөр, адатта, кыйла маанилүү бөлүктөрүн өндүрүү үчүн аларды колдонушат. Горизонталдык машиналар менен кыстармаларды капталдан жүктөсө болот, бул туура тегиздөөнү камсыз кылууну кыйындатат.
- Айлануучу үстөл инжектордук калыптоо машиналары:Бул машиналарда бир нече калыптарды орнотууга жана өндүрүш үчүн инжектордук агрегатка айлантууга мүмкүндүк берүүчү айлануучу үстөл бар. Бул типтеги машина кыстаруу калыптоо үчүн идеалдуу келет, анткени ал калыпка ар кандай койгучтарды иштетип, татаалыраак бөлүктөрдү жаратат.
- Шаттл инъекциялык калыптоо машиналары: Бул машиналарда калыпты алдыга жана артка жылдыруучу машина бар, ал инжектордук аппарат менен калыптоо аянтынын ортосунда. Алар кичинекей өндүрүштүк жүрүштөр үчүн эң ылайыктуу жана кыстармаларды калыпка салуу үчүн идеалдуу, анткени алар кыстармаларды жеңил жүктөө жана түшүрүүгө мүмкүндүк берет.
Кыстаруу калыптоо процессинин параметрлери
Натыйжадагы продукт салттуу инжектордук формага салыштырмалуу көбүрөөк күчкө жана туруктуулукка ээ. Кыстарма калыптоо процессинин параметрлери жогорку сапаттагы жана ырааттуу натыйжаларга жетишүү үчүн маанилүү. Бул жерде биз кыстарма калыптоо процессинин параметрлерин карайбыз.
- Материалдарды тандоо: Материалды тандоо кыстаруу формасында процесстин маанилүү параметри болуп саналат. Пластик материал кыстаруу материалына жана колдонмого шайкеш келиши керек. Шайкештик кыстарма менен пластик материалдын жакшы жабышып калышын камсыздайт, натыйжада күчтүү жана бышык продукт пайда болот.
- Абанын температурасы: Температура кыстаруу калыптоо процессинде чечүүчү ролду ойнойт. Пластикалык материал бир калыпта агып, көңдөйдү боштуктар жана деформацияларсыз толтуруу үчүн калыптын температурасын туура орнотуу керек. Пластик материалдын термикалык зыян келтирбестен кыстармага жакшы жабышып калышы үчүн биз кошумча температурасын да эске алышыбыз керек.
- Инъекция басымы: Инъекция басымы кыстаруу формасында дагы бир маанилүү параметр болуп саналат. Пластикалык материалды калыптын көңдөйүнө бир калыпта жана тез киргизүү үчүн чыңалууну туура орнотуу керек. Инъекциянын жогорку басымы кыстарма же калыптын деформациясына алып келиши мүмкүн, ал эми төмөн инъекциялык басым көктүн көңдөйүнүн толук толтурулбай калышына алып келиши мүмкүн.
- Инъекциянын ылдамдыгы: Инъекциянын ылдамдыгы да кыстаруу формасында маанилүү параметр болуп саналат. Пластмассадан жасалган материал көктүн көңдөйүн боштуктар жана деформацияларсыз бир калыпта толтуруусу үчүн норманы туура коюшубуз керек. Инжекциянын жогорку ылдамдыгы пластмассалык материалда турбуленттүүлүккө алып келиши мүмкүн, натыйжада даяр продукцияда кемчиликтер пайда болот.
- Муздатуу убактысы: Муздатуу убактысы пластмассалык материалдын катууланышы жана акыркы продукт формасын түзүү үчүн талап кылынат. Даяр продукт үчүн керектүү формага жана өлчөмдөргө жетишүү үчүн муздатуу убактысын туура орнотуу керек. Кыскараак муздатуу убактысы деформацияга же кичирейүүгө алып келиши мүмкүн, ал эми муздатуу узактыгы циклдин узактыгына жана өндүрүмдүүлүктүн төмөндөшүнө алып келиши мүмкүн.
- Чыгаруу убактысы: Даяр продуктуну калыптан чыгаруу үчүн биз чыгаруу убактысын талап кылабыз. Даяр продуктуну эч кандай зыянга же деформацияга алып келбестен алып салуу үчүн чыгаруу убактысын туура коюшубуз керек. Кыскараак чыгаруу убактысы буюмдун толук эмес чыгарылышына же бузулушуна алып келиши мүмкүн, ал эми чыгаруунун узактыгы циклдин узактыгына жана өндүрүмдүүлүктүн төмөндөшүнө алып келиши мүмкүн.
Common Insert калыптоо кемчиликтери жана алардан кантип сактануу керек
Кыстарма калыптоо - пластикалык материалды сайганга чейин калыпка металл же пластмасса кыстармалар сыяктуу алдын ала даярдалган компоненттерди коюуну камтыган популярдуу өндүрүш процесси. Бул процесс салттуу инжектордук формага караганда кыйла олуттуу жана бышык продуктуларга алып келет. Бирок, ар кандай өндүрүш процессиндей эле, кыстаруу формасында акыркы продукттун сапатына жана ырааттуулугуна таасир этүүчү кемчиликтер болушу мүмкүн. Бул жерде биз кыстарма калыптоодо кеңири таралган кемчиликтерди жана аларды кантип болтурбоо керектигин карап чыгабыз.
Flash: Жаркылдоо – калыптан ашыкча пластик материал агып чыгып, даяр продукциянын бетинде жука катмарды пайда кылган кемчилик. Бул кемчилик буюмдун көрүнүшүнө жана иштешине таасир этиши мүмкүн. Жарк этүүнү болтурбоо үчүн, сиз төмөнкү кадамдарды жасасаңыз болот:
- Инъекциянын басымын азайтыңыз
- калыптын кысуу күчүн жогорулатуу
- Көк чыгаруучу агентти колдонуңуз
- Муздатуу убактысын көбөйтүңүз
Кыска кадр: Кыска атуу - бул пластмассалык материал көктүн көңдөйүн толтурбаганда пайда болгон кемчилик, натыйжада буюм толук эмес же азыраак болот. Кыска атууну болтурбоо үчүн, төмөнкү кадамдарды жасасаңыз болот:
- Инъекциянын басымын жогорулатуу
- Инъекциянын ылдамдыгын жогорулатуу
- Материалдык температураны жогорулатуу
- Көктүн температурасын жогорулатуу
Warpage: Даяр продукт тегиз эмес муздаганда же кичирейгендиктен деформацияланып же буралып калган кемчилик. Warpageден качуу үчүн, сиз төмөнкү кадамдарды жасасаңыз болот:
- Көктүн температурасын жогорулатуу
- Муздатуу убактысын көбөйтүңүз
- Таңгактоо басымын жогорулатыңыз
- Салмактуу муздатуу системасын колдонуңуз
Раковина белгилери: Раковинанын белгилери – даяр продукциянын бетинде бир калыпта эмес муздатуудан же кичирейүүдөн пайда болгон чөкпөлөр же оюктар. Чөгүп кетүү белгилерин болтурбоо үчүн, сиз төмөнкү кадамдарды жасасаңыз болот:
- Көктүн температурасын жогорулатуу
- Муздатуу убактысын көбөйтүңүз
- Таңгактоо басымын жогорулатыңыз
- Буюмду бекемдөө үчүн калың дубалдарды же кабыргаларды колдонуңуз
Delamination: Деламинация – бул пластмасса материалы менен кыстарма материалы туура эмес бири-биринен ажырап же кабыгынан айрылып калганда пайда болгон кемчилик. Деламинацияны болтурбоо үчүн, сиз төмөнкү кадамдарды жасасаңыз болот:
- Шайкеш пластикалык материалды колдонуңуз жана банканын материалын салыңыз
- Инъекциянын басымын жана ылдамдыгын жогорулатуу
- Кыстаруу температурасын жогорулатыңыз
- Көктүн температурасын жогорулатуу
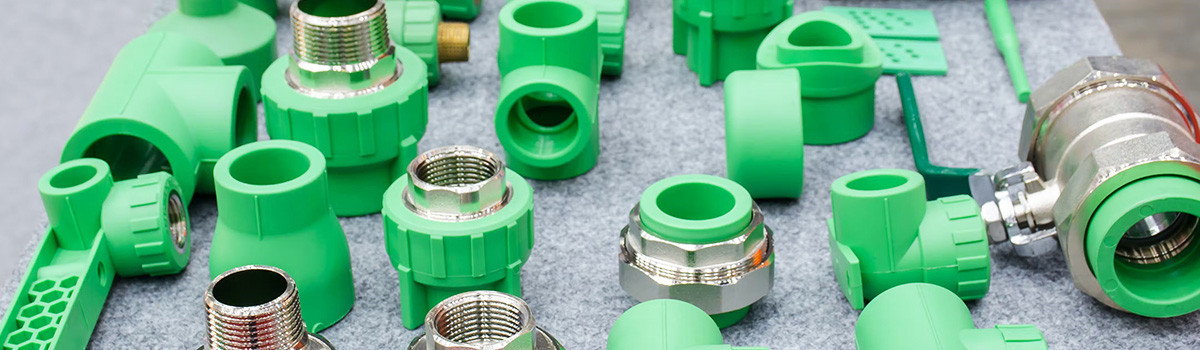
Кыстарма калыптоо үчүн формалоодон кийинки операциялар
Бирок, кыстарма калыптоо процессин аяктагандан кийин, биз акыркы продукт керектүү спецификацияларга жооп беришин камсыз кылуу үчүн формадан кийинки бир нече операцияларды аткарышыбыз керек. Бул жерде биз кыстарма калыптоо үчүн формалоодон кийинки операцияларды кененирээк карап чыгабыз.
- Дефлаш:Дефлештирлөө - бул даяр продукциядан ашыкча материалдарды, мисалы, жаркыраган жерлерди жок кылуучу процесс. Бул процесс буюмдун көлөмүнө жана татаалдыгына жараша кол менен же автоматтык түрдө аткарылышы мүмкүн.
- Кыркуу:Кыркып алуу - даяр продукциядан ашыкча материалды же чыга турган жерлерди жок кылуучу процесс. Бул процесс буюмдун формасына жана өлчөмүнө жараша ар кандай кесүүчү шаймандарды же ыкмаларды колдонуу менен жүргүзүлүшү мүмкүн.
- тазалоо: Тазалоо – бул даяр продукциядан кирди, калдыктарды же булгоочу заттарды тазалоочу процесс. Бул процесс кыстаруу формасында колдонулган материалдын түрүнө жараша ар кандай тазалоочу каражаттарды же ыкмаларды колдонуу менен аткарылышы мүмкүн.
- Ассамблея:Монтаждоо - бул бир нече компоненттерди бириктирип, даяр продукцияны түзүү процесси. Бул процесс материалдын түрүнө жана каалаган акыркы продуктуна жараша, мисалы, ультра үн ширетүү, ысык штамптоо же чаптама байланыш сыяктуу ар кандай ыкмаларды колдонуу менен аткарылышы мүмкүн.
- Testing: Сыноо - бул даяр продукциянын керектүү спецификацияларга жана сапат стандарттарына жооп беришин камсыз кылуучу процесс. Бул процесс буюмдун түрүнө жана анын колдонуу максатына жараша механикалык, электрдик же визуалдык текшерүүлөр сыяктуу ар кандай сыноолорду камтышы мүмкүн.
Бул формалоодон кийинки операциялардан тышкары, кыстаруу калыптоо процессин долбоорлоодо эске алынуучу бир нече факторлор бар, алар формадан кийинки процедураларга болгон муктаждыкты азайтат. Аларга төмөнкүлөр кирет:
- Кыстарма жана калыпка салынган бөлүгү үчүн ылайыктуу материалдарды тандоо
- Кыстарма туура жайгаштырылышын жана калыптоо процессинде кармалышын камсыз кылуу
- Кемчиликтерди жана ашыкча материалды азайтуу үчүн температура жана басым сыяктуу калыптоо параметрлерин тууралоо
- Даяр продуктунун ырааттуулугун жана тактыгын камсыз кылуу үчүн жогорку сапаттагы калыптарды жана жабдууларды колдонуу
Insert Injection Molding Колдонмолору
Кыстаруу инъекциялык калыптоо - бул көптөгөн тармактарда жогорку сапаттагы татаал бөлүктөрдү өндүрүү үчүн колдонулган өтө ар тараптуу өндүрүш процесси. Бул жерде биз инъекциялык форманын колдонмолорун жана анын ар кандай тармактар үчүн пайдасын кененирээк карап чыгабыз.
- Автоунаа өнөр жайы:Автоунаа өнөр жайы инъекциялык форманын эң маанилүү колдонуучуларынын бири. Ал ар кандай компоненттерди, анын ичинде аба жаздыктарынын корпустарын, коопсуздук курун жана кыймылдаткыч тетиктерин өндүрүүдө колдонулат. Бул процесс автомобиль колдонуунун катаал шарттарына туруштук бере ала турган тетиктерди так жана так калыптоого мүмкүндүк берет.
- Электрондук өнөр жай:Электроника өнөр жайы ошондой эле смартфондор, ноутбуктар жана башка электрондук шаймандар сыяктуу түзмөктөр үчүн компоненттерди өндүрүү үчүн инъекциялык формага көп таянат. Процесс электрондук компоненттер үчүн туташтыргычтар, өчүргүчтөр жана корпустар сыяктуу элементтерди түзүүдө колдонууну табат. Процесс жогорку эффективдүү жана тез жана үнөмдүү тетиктердин чоң көлөмүн чыгара алат.
- Медициналык өнөр жай: Медициналык өнөр жай да инъекциялык формадан олуттуу пайда көрөт. Процесс ар кандай компоненттерди, анын ичинде хирургиялык аспаптарды, дары-дармектерди жеткирүү аппараттарын жана медициналык импланттарды өндүрүүдө колдонулат. Бул ыкма медициналык колдонуунун катаал шарттарына туруштук бере ала турган элементтерди так калыптоого мүмкүндүк берет жана чоң көлөмдө өндүрүүгө мүмкүндүк берет.
- Аэрокосмикалык өнөр жайы: Аэрокосмостук өнөр жай инъекциялык форманы кеңири колдонгон дагы бир тармак. Бул процесс аба каналдары, кашаалар жана учактын тетиктери үчүн корпустар сыяктуу компоненттерди өндүрүүдө колдонууну табат. Бул процесс аэрокосмостук пайдалануудагы жогорку стресстерге жана экстремалдык температурага туруштук бере ала турган жогорку бекем компоненттерди түзүүгө мүмкүндүк берет.
- Эл керектөөчү товарлар өнөр жайы: Эл керектөөчү товарлар өнөр жайы оюнчуктар, турмуш-тиричилик техникасы жана спорттук шаймандар сыяктуу буюмдардын кеңири ассортиментин өндүрүү үчүн инъекциялык форманы кеңири колдонот. Процесс жогорку сапаттагы, бышык, жеңил жана эстетикалык жактан жагымдуу компоненттерди түзүүгө мүмкүндүк берет.
Бул тармактардан тышкары, кыстаруу инъекциялык калыптоо башка көптөгөн колдонмолордо да колдонулат, анын ичинде:
- Таңгактоо өнөр жайы: капкактарды, жабууларды жана башка таңгактоочу компоненттерди өндүрүү үчүн
- Курулуш өнөр-жайы: түтүктөрдү, арматураларды жана башка курулуш компоненттерин өндүрүү үчүн
- Аскердик өнөр жай: аскердик машиналарды жана техниканы тетиктерди чыгаруу учун
Автоунаа өнөр жай колдонмолору
Автоунаа өнөр жайы пластикалык инъекциялык калыптын эң маанилүү колдонуучуларынын бири болуп саналат, анткени бул унаанын татаал тетиктерин өндүрүүнүн үнөмдүү жана эффективдүү жолу. Бул жерде биз автомобиль өнөр жайындагы пластикалык инжектордук форманын ар кандай колдонмолорун кылдат карап чыгабыз.
- Ички компоненттери: Унаанын ичи унаанын жалпы эстетикасы жана функционалдуулугу үчүн зарыл болгон бир нече пластикалык компоненттерден турат. Бул компоненттерге аспаптар тактасы, эшик панелдери, кондиционер вентиляторлору жана рулдун тетиктери кирет. Инжектордук форма бул тетиктерди жогорку көлөмдө тез жана үнөмдүү чыгарууга, ошол эле учурда жогорку тактыкка мүмкүндүк берет.
- Сырткы компоненттери: Унаанын сырты бир нече пластикалык тетиктерден, анын ичинде бампердин капкактарынан, фаралардын жана арткы жарыктын түзүлүштөрүнөн турат. Инжектордук калыптоо бул компоненттерди жогорку тактыкка чейин чыгарат, бул алардын автомобиль өнөр жайында талап кылынган коопсуздук жана сапат стандарттарына жооп беришин камсыз кылат.
- Мотор компоненттери: Инжектордук форма ошондой эле кыймылдаткычтын бир нече компоненттерин, анын ичинде аба соргучтарды, кыймылдаткычтын капкагын жана май чыпкаларын өндүрүүдө колдонулат. Биз бул компоненттерди катуу толеранттуулукка жана стандарттарга ылайык жасап чыгарышыбыз керек, ал эми инжектордук форма бул талаптарга жооп берген жогорку сапаттагы ингредиенттерди өндүрүүгө мүмкүндүк берет.
- Электрдик компоненттер: Унаадагы электрдик тетиктер, мисалы, туташтыргычтар, өчүргүчтөр жана сенсорлордун корпустары, ошондой эле инжектордук форма менен жасалат. Бул компоненттер бышык болушу керек жана катаал иштөө шарттарына туруштук бериши керек, ал эми инжектордук форма бул шарттарга туруштук бере ала турган жогорку сапаттагы ингредиенттерди өндүрүүгө мүмкүндүк берет.
- HVAC компоненттери:Инжектордук формада транспорттун HVAC тутумунда колдонулган бир нече компоненттер, анын ичинде кондиционер түтүктөр жана желдеткичтер өндүрүлөт. Бул тетиктер унаада туура аба агымын жана вентиляцияны камсыз кылуу үчүн так толеранттуулукта өндүрүлүшү керек.
Бул тиркемелерден тышкары, өндүрүүчүлөр күйүүчү май, тормоз жана суспензия системалары менен кошо бир нече башка автомобиль компоненттерин өндүрүү үчүн инжектордук форманы колдонушат.
Автоунаа өнөр жайында инжектордук форманы колдонуунун артыкчылыктары көп, анын ичинде:
- Жогорку Натыйжалуулук:Инжектордук калыптоо жогорку сапаттагы компоненттерди чоң көлөмдө тез чыгарууга, өндүрүш убактысын жана чыгымдарды кыскартууга мүмкүндүк берет.
- тактык:Инъекциялык калыптоо жогорку тактык жана ырааттуулук менен компоненттерди түзүүгө мүмкүндүк берет, алардын сапаттын катуу стандарттарына жооп берет.
- Customization: Инжектордук калыптоо татаал формаларды жана конструкцияларды чыгарууга мүмкүндүк берет, бул өндүрүүчүлөргө конкреттүү дизайн талаптарын канааттандыруу үчүн компоненттерди ыңгайлаштырууга мүмкүндүк берет.
Медициналык өнөр жай колдонмолору
Медициналык өнөр жайы тактык жана ишенимдүүлүк биринчи орунда турган тармак болуп саналат, бул пластикалык инъекциялык форманы медициналык компоненттерди өндүрүү үчүн идеалдуу өндүрүш процессине айлантат. Бул жерде биз медициналык өнөр жайда пластикалык инъекциялык форманын ар кандай колдонмолорун кененирээк карап чыгабыз.
- Хирургиялык аспаптар: Инъекциялык калыптоо көптөгөн хирургиялык аспаптарды, анын ичинде кычкачтарды, кыскычтарды жана скальпельдерди чыгарат. Өндүрүүчүлөр эң жогорку тактыкты жана тактыкты камсыз кылуу үчүн бул компоненттерди катуу толеранттуулукка жана стандарттарга ылайыкташтырып чыгарышы керек.
- Медициналык аппараттар:Өндүрүүчүлөр ошондой эле катетер жана дем алуу компоненттери сыяктуу медициналык шаймандарды өндүрүү үчүн инъекциялык форманы колдонушат. Пациенттердин коопсуздугун жана ишенимдүүлүгүн кепилдөө үчүн өндүрүүчүлөр бул компоненттерди катуу стандарттарга ылайык чыгарышы керек.
- Диагностикалык компоненттер: Өндүрүүчүлөр пипеткалар, шприцтер жана пробиркалар сыяктуу диагностикалык жабдууларда колдонулган бир нече компоненттерди өндүрүү үчүн инжектордук форманы колдонушат. Бул компоненттер так сыноо натыйжаларын камсыз кылуу үчүн так толеранттуулук менен өндүрүлгөн болушу керек.
- Packaging: Инъекциялык калыптоо стерилдүү лотоктор, контейнерлер жана таңгактоочу компоненттер сыяктуу медициналык буюмдар үчүн таңгактарды чыгарат. Бул компоненттер медициналык буюмдардын стерилдүүлүгүн жана коопсуздугун камсыз кылуу үчүн катуу стандарттарга ылайык даярдалышы керек.
- Стоматологиялык компоненттер: Инъекциялык калыптоо бир нече стоматологиялык компоненттерди, анын ичинде ооз коргоочуларды, лотокторду жана ортодонтиялык бөлүктөрдү чыгарат. Бул компоненттер бейтапка туура туура келүүнү жана ыңгайлуулукту камсыз кылуу үчүн так толеранттуулукта өндүрүлүшү керек.
Бул колдонмолордон тышкары, өндүрүүчүлөр протездерди, угуу аппараттарын жана лабораториялык жабдууларды камтыган бир нече башка медициналык компоненттерди өндүрүү үчүн инъекциялык форманы колдонушат.
Медицина тармагында инжектордук форманы колдонуунун артыкчылыктары көп, анын ичинде:
- Жогорку тактык:Инжектордук формалоо жогорку деңгээлдеги тактык жана ырааттуулук менен компоненттерди өндүрүүгө мүмкүндүк берет, алардын сапаттын катуу стандарттарына жооп берет.
- Customization:Инжектордук калыптоо татаал формаларды жана конструкцияларды чыгарууга мүмкүндүк берет, бул өндүрүүчүлөргө конкреттүү дизайн талаптарын канааттандыруу үчүн компоненттерди ыңгайлаштырууга мүмкүндүк берет.
- Үнөмдүү: Инжектордук формалоо - бул өндүрүш убактысын жана чыгымдарын кыскартуу менен чоң көлөмдө жогорку сапаттагы компоненттерди чыгарган үнөмдүү өндүрүш процесси.
Электрондук өнөр жай колдонмолору
Электрондук өнөр жайы так жана натыйжалуу өндүрүш процесстерине таянган тармак. Пластикалык инъекциялык калыптоо анын тактыгы, ар тараптуулугу жана ылдамдыгы менен электрондук компоненттерди өндүрүү үчүн идеалдуу процесс болуп саналат. Бул жерде биз электрондук өнөр жай пластикалык инжектордук калыптын ар кандай колдонмолорду кылдат карап чыгабыз.
- Connectors: Инжектордук формада электроника тармагында колдонулган туташтыргычтардын кеңири спектрин, анын ичинде USB туташтыргычтарын, HDMI туташтыргычтарын жана аудио уячаларын чыгарат. Бул компоненттер туура иштешин жана шайкеш келүүсүн камсыз кылуу үчүн так толеранттуулук менен өндүрүлүшү керек.
- Турак жайлар жана короолор: Инжектордук форма электрондук шаймандар, анын ичинде уюлдук телефондор, ноутбуктар жана башка керектөөчү электроника үчүн корпустарды жана корпустарды чыгарат. Өндүрүүчүлөр туура шайкештигин жана иштешин камсыз кылуу үчүн бул компоненттерди так спецификацияларга ылайыкташтырууга тийиш.
- Switches: Инжектордук формада электрондук шаймандарда колдонулган башкаруу элементтеринин бир нече түрлөрү, анын ичинде рокер которгучтары, баскыч баскычтары жана слайд өчүргүчтөр өндүрүлөт. Бул компоненттер ишенимдүү иштешин камсыз кылуу үчүн так толеранттуулук менен өндүрүлүшү керек.
- LED компоненттери:Инжектордук формада LED жарыктандырууда колдонулган бир нече компоненттер, анын ичинде линзалар, чагылдыргычтар жана диффузорлор өндүрүлөт. Өндүрүүчүлөр жарыктын туура бөлүштүрүлүшүн жана натыйжалуулугун камсыз кылуу үчүн бул компоненттерди так спецификацияларга ылайыкташтырууга тийиш.
- Электр энергиясы менен камсыздоо компоненттери: Инжектордук формада розеткаларды, сайгычтарды жана кабелдик туташтыргычтарды кошкондо, электр менен жабдуу бөлүмдөрүндө колдонулган бир нече компоненттерди өндүрөт. Бул компоненттер коопсуз жана ишенимдүү иштешин камсыз кылуу үчүн так толеранттуулук менен өндүрүлүшү керек.
Бул тиркемелерден тышкары, өндүрүүчүлөр клавиатура, компьютер чычкандары жана алыстан башкаруу каражаттары сыяктуу бир нече башка электрондук компоненттерди өндүрүү үчүн инжектордук форманы колдонушат.
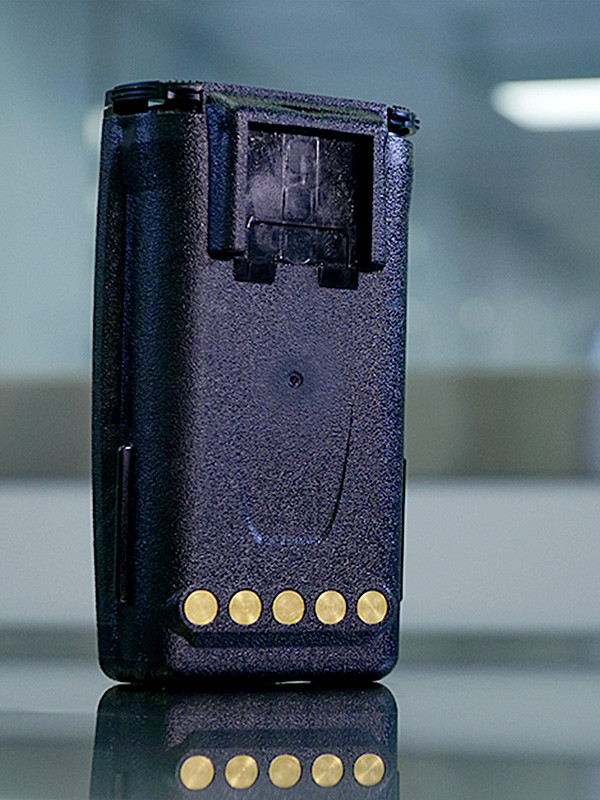
Электрондук өнөр жайда инжектордук форманы колдонуунун артыкчылыктары көп, анын ичинде:
- Жогорку тактык: Инжектордук формалоо жогорку деңгээлдеги тактык жана ырааттуулук менен компоненттерди өндүрүүгө мүмкүндүк берет, алардын сапаттын катуу стандарттарына жооп берет.
- Customization: Инжектордук калыптоо татаал формаларды жана конструкцияларды чыгарууга мүмкүндүк берет, бул өндүрүүчүлөргө конкреттүү дизайн талаптарын канааттандыруу үчүн компоненттерди ыңгайлаштырууга мүмкүндүк берет.
- ылдамдык:Инжектордук калыптоо - бул тез жана эффективдүү өндүрүш процесси, ал чоң көлөмдө жогорку сапаттагы компоненттерди чыгарууга, өндүрүш убактысын жана чыгымдарды кыскартууга мүмкүндүк берет.
Аэрокосмостук өнөр жай колдонмолору
Аэрокосмостук өнөр жайы – анын бардык компоненттеринде эң жогорку тактыкты, тактыкты жана туруктуулукту талап кылган тармак. Аэрокосмостук өнөр жайда пластикалык инъекциялык калыптоо татаал геометрияларды чыгаруу, салмакты азайтуу жана структуралык бүтүндүктү жогорулатуу жөндөмдүүлүгүнөн улам барган сайын кеңири таралган. Бул жерде биз аэрокосмостук өнөр жайда пластикалык инжектордук форманын ар кандай колдонмолорун кененирээк карап чыгабыз.
- Ички компоненттери: Инжектордук форма учактын ички тетиктерин, анын ичинде отургучтун аркасын, лоток үстөлдөрүн жана үстүнкү бөлүмдөрдү чыгарат. Бул компоненттер жеңил жана бышык болушу керек, жогорку стресске жана эскирүүлөргө туруштук бере алат.
- Структуралык компоненттер: Инжектордук форма учактар үчүн конструкциялык компоненттерди, анын ичинде канаттардын учтарын, фюзеляждын бөлүктөрүн чыгарат. Бул компоненттер учактын коопсуздугун жана натыйжалуулугун камсыз кылуу үчүн жеңил, күчтүү жана бышык болушу керек.
- Мотор компоненттери:Инжектордук формада учак кыймылдаткычтары үчүн бир нече тетиктер, анын ичинде турбиналык бычак, күйүүчү май түтүктөрү жана корпустар өндүрүлөт. Бул компоненттер жогорку температурага, басымга жана стресске туруштук берүү үчүн так мүнөздөмөлөргө ылайык даярдалышы керек.
- Электрдик компоненттер: Инжектордук формада учактар үчүн электр компоненттери, анын ичинде туташтыргычтар, өчүргүчтөр жана зым жабдыктар өндүрүлөт. Бул компоненттер туура иштешин жана ишенимдүүлүгүн камсыз кылуу үчүн так толеранттуулук менен өндүрүлүшү керек.
- Аспаптын компоненттери:Инжектордук формада башкаруу панелдерин жана прибор корпустарын камтыган учактар үчүн приборлордун компоненттерин чыгарат. Бул компоненттер бышык жана жогорку температурага, басымга жана титирөөгө туруштук бериши керек.
Бул колдонмолордон тышкары, өндүрүүчүлөр аэрокосмостук өнөр жайы үчүн бир нече башка компоненттерди, анын ичинде кашааларды, бекиткичтерди жана прокладкаларды өндүрүү үчүн инжектордук форманы колдонушат.
Аэрокосмостук өнөр жайда инжектордук форманы колдонуунун артыкчылыктары көп, анын ичинде:
- Салмагын азайтуу: Инжектордук калыптоо учактын салмагын азайтуучу жеңил тетиктерди өндүрүүгө мүмкүндүк берет, натыйжада күйүүчү май азыраак чыгымдалат жана эффективдүүлүктү жогорулатат.
- тактык:Injection калыптоо жогорку тактык жана ырааттуулугу менен бөлүктөрүн өндүрүүгө мүмкүндүк берет, алар катуу сапат стандарттарына жооп берет.
- Customization:Инжектордук калыптоо татаал формаларды жана конструкцияларды чыгарууга мүмкүндүк берет, бул өндүрүүчүлөргө конкреттүү дизайн талаптарын канааттандыруу үчүн компоненттерди ыңгайлаштырууга мүмкүндүк берет.
- Узактыгы: Injection калыптоо учактын коопсуздугун жана ишенимдүүлүгүн камсыз кылуу, бышык жана жогорку стресске, температурага жана басымга туруштук бере алган бөлүктөрүн чыгарат.
Эл керектөөчү товарлар өнөр жайы
Эл керектөөчү товарлар өнөр жайы дүйнөлүк экономиканын эң маанилүү тармактарынын бири болуп саналат. Керектөөчү товарлар - бул жеке адамдар күнүмдүк колдонуучу буюмдар, анын ичинде тиричилик буюмдары, электроника, оюнчуктар жана жеке гигиеналык буюмдар. Эл керектеечу товарларды чыгаруучу енер жайында пластмассадан жасалган инжектордук калыптоо жогорку сапаттагы тетиктерди тактык жана тактык менен чыгаруу мумкунчулугунун аркасында барган сайын популярдуу болуп калды. Бул жерде биз керектөөчү товарлар тармагында пластикалык инжектордук форманын ар кандай колдонмолорун кененирээк карап чыгабыз.
- Packaging: Инъекциялык формалар керектөө товарлары үчүн таңгактоочу материалдарды, анын ичинде тамак-аш таңгактарын, суусундук бөтөлкөлөрүн жана косметикалык идиштерди өндүрүүдө кеңири колдонулат. Инъекциялык калыптоо таңгактоочу материалдардын функционалдык жана көзгө жагымдуу болушун камсыз кылуу менен татаал формаларды жана конструкцияларды чыгарууга мүмкүндүк берет.
- Үй-тиричилик буюмдары: Инжектордук формада бир катар үй-тиричилик буюмдары, анын ичинде ашкана идиштери, сактоочу контейнерлер жана тазалоочу буюмдар чыгарылат. Бул буюмдар бышык, жеңил жана күнүмдүк колдонууга туруштук бериши керек.
- Toys: Инжектордук формада ар кандай оюнчуктар, анын ичинде экшн фигуралары, куурчактар жана үстөл оюндары өндүрүлөт. Бул оюнчуктар коопсуз жана бышык болушу үчүн так мүнөздөмөлөргө ылайык өндүрүлүшү керек.
- Жеке кам көрүү каражаттары: Инъекциялык калыптоо уникалдуу кам көрүү каражаттарын, анын ичинде тиш щеткаларын, устараларды жана шампунь бөтөлкөлөрүн чыгарат. Бул буюмдар эстетикалык жактан жагымдуу, функционалдык жана көп колдонууга туруштук бериши керек.
- Электроника: Инжектордук формада электрондук түзүлүштөр үчүн бир нече компоненттер, анын ичинде каптар, баскычтар жана туташтыргычтар өндүрүлөт. Бул компоненттер бышык, жеңил жана жогорку температурага жана басымга туруштук бериши керек.
Бул колдонмолордон тышкары, өндүрүүчүлөр керектөө товарлары өнөр жайы үчүн бир нече башка компоненттерди, анын ичинде автомобиль тетиктерин, медициналык аппараттарды жана өнөр жай жабдууларын өндүрүү үчүн инжектордук форманы колдонушат.
Эл керектөөчү товарлар тармагында инжектордук форманы колдонуунун артыкчылыктары көп, анын ичинде:
- Үнөмдүү:Инжекциялык калыптоо башка өндүрүш процесстерине караганда төмөн баада жогорку сапаттагы компоненттерди өндүрүүгө мүмкүндүк берет.
- Ыңгайлаштыруу: Инжекциялык калыптоо татаал формалар жана конструкциялар менен элементтерди түзүүгө мүмкүндүк берет, бул өндүрүүчүлөргө өзгөчө дизайн талаптарын канааттандыруу үчүн функцияларды ыңгайлаштырууга мүмкүндүк берет.
- тактык: Инжектордук формада катуу сапат стандарттарына жооп берген так жана ырааттуу деталдар бар.
- узактык: Injection калыптоо буюмдардын коопсуздугун жана ишенимдүүлүгүн камсыз кылуу, бекем жана жогорку стресс, температура жана басымга туруштук бере алат кылат.
Insert Injection Molding келечектеги тенденциялары
Технология өнүккөн сайын жана керектөөчүлөрдүн талаптары өзгөргөн сайын, инъекциялык калыптоо өнөр жайы дайыма өнүгүп турат. Өндүрүүчүлөр дайыма эффективдүүлүктү жогорулатуунун, чыгымдарды азайтуунун жана сапаттуу продукция чыгаруунун жолдорун издешет. Бул жерде биз инъекциялык формада келечектеги кээ бир тенденцияларды карап чыгабыз.
- кабыл алуу: Өндүрүш тармагында автоматташтыруу барган сайын популярдуу болуп баратат, ал эми инъекциялык формалар да четте калбайт. Автоматташтырылган системалар эмгек чыгымдарын азайтат, өндүрүштүн ылдамдыгын жогорулатат жана сапатты көзөмөлдөөнү жакшыртат.
- Туруктуулук: Өсүп жаткан экологиялык тынчсыздануу менен, өндүрүүчүлөр калдыктарды азайтуу жана туруктуулукту жакшыртуу жолдорун издеп жатышат. Кайра иштетилген материалдарды колдонуу жана оңой кайра иштетүүгө же кайра иштетүүгө боло турган өнүмдөрдү долбоорлоо - бул өндүрүүчүлөр бул маселени чечүүнүн бир нече жолу.
- 3D басып чыгаруу: Инъекциялык форманын кээ бир аспектилери 3D басып чыгарууну мурунтан эле колдонушат, бирок келечекте анын дагы кеңири таралышы мүмкүн. Тез прототиптерди түзүү жана жекелештирилген компоненттерди чыгаруу мүмкүнчүлүгү 3D басып чыгаруунун бир гана артыкчылыгы.
- Өркүндөтүлгөн материалдар: Изилдөөчүлөр жана өндүрүүчүлөр ар кандай температурага, басымга жана стресске туруштук бере турган жаңы материалдарды иштеп чыгууда.
- Акылдуу өндүрүш:Акылдуу өндүрүш реалдуу убакыт режиминде маалыматтарды чогултуу жана талдоо үчүн технологияны колдонууну камтыйт, бул тезирээк чечим кабыл алууга жана натыйжалуу өндүрүшкө мүмкүндүк берет. Бул технология сапатты көзөмөлдөөнү жакшыртат, токтоп калуу убактысын азайтат жана өндүрүмдүүлүктү жогорулатат.
жыйынтыктоо
Insert инъекциялык калыптоо камтылган компоненттери менен татаал бөлүктөрүн түзүүгө мүмкүндүк берген ар тараптуу жана үнөмдүү өндүрүш процесси болуп саналат. Салттуу чогултуу ыкмаларына караганда анын артыкчылыктары аны ар кандай тармактарда, анын ичинде автомобиль, медициналык, электроника, аэрокосмостук жана керектөө товарларында популярдуу кылат. Инъекциялык формада ар кандай ыкмаларды, материалдарды жана дизайн ойлорун түшүнүү менен, өндүрүүчүлөр өндүрүш процесстерин оптималдаштырып, кардарларына жогорку сапаттагы өнүмдөрдү жеткире алышат. Технология өнүккөн сайын, биз инъекциялык форманын ого бетер инновациялык колдонмолорун көрө алабыз.