Пластикалык инъекциялык калыптоодогу жаңы өнүгүүлөр
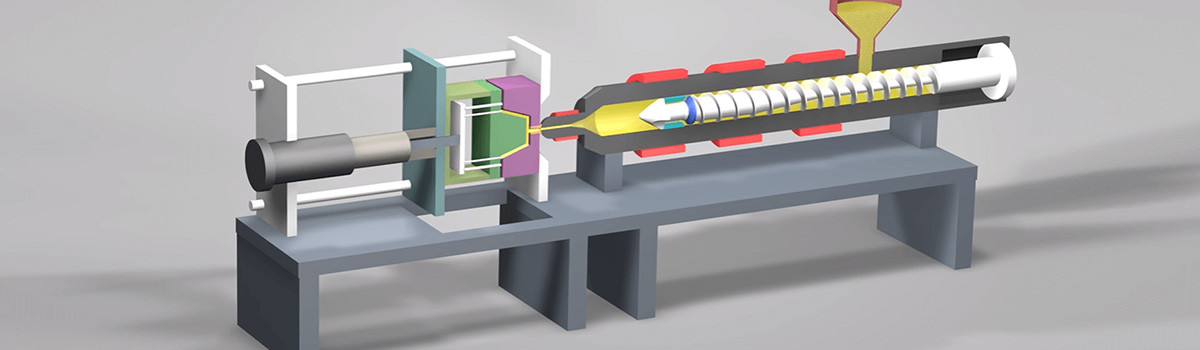
Пластикалык инъекциялык калыптоо өндүрүш ыкмасы катары ондогон жылдар бою болуп келген. Бирок, инжектордук форманын жаңы тенденциялары бул ыкманы алдыга жылдырып, аны тандаган компанияларга жаңы жана болуп көрбөгөндөй артыкчылыктарды алып келүүдө.
Инжектордук форманын жаңы тенденциялары жакынкы жылдардагы кандай экенин жана аларды колдонуудан компанияңыз кандай пайда алаарын билип алыңыз.
Пластикалык инъекциялык форма кандайча өнүккөн?
Пластмассалар 1850-жылдардан бери пайда болсо да, 1870-жылдары гана пластиктин ийкемдүү түрлөрү ойлоп табылган. Натыйжада инжектордук формалоо процесстери иштелип чыккан. Ошондон бери, бир катар жетишкендиктер пластикалык инъекциялык калыптоодогу мүмкүнчүлүктөрдү андан ары түрттү:
Бурама инъекциялык калыптоо машиналарын ойлоп табуу инъекциянын ылдамдыгын жеңилирээк башкара тургандыгын билдирген, ошондуктан акыркы продукт дагы жогорку сапатты көрсөттү. Бул процесс ошондой эле аралаш материалдарды колдонууга, түстүү жана кайра иштетилген пластмассалар үчүн эшикти ачууга мүмкүндүк берди.
Газ менен иштеген бурама машиналар дагы татаалыраак, ийкемдүү жана күчтүүрөөк продукцияны түзүүгө мүмкүндүк берди. Бул ыкма ошондой эле өндүрүш убактысы, калдыктары жана буюмдун салмагын азайтуу үчүн, экономикалык чыгымдардын төмөндөшүн билдирген.
Азыр компьютердин жардамы менен өндүрүштүн аркасында татаал формалар бар, дизайнерлер азыр татаал формаларды түзө алышат (алар бир нече бөлүмдөргө ээ болушу мүмкүн же деталдуу жана так болушу мүмкүн).
Газдын жардамы менен инжектордук формалоо
Инжектордук форманын бул формасында кадимки эриген пластикалык инъекцияга басымдагы газды калыпка куюу жардам берет – бул процесс үчүн көбүнчө азот колдонулат. Газ пластикти калыптын учуна түрткөн көбүктү пайда кылат; ошентип, көбүк кеңейген сайын ар кандай бөлүмдөр толтурулат. Пластмасса өнөр жайында колдонулган калыптандыруунун бир нече формалары бар, алар полимерди куюуда газ куюлган жери боюнча айырмаланат.
Тагыраак айтканда, газды станоктун соплосу аркылуу же түздөн-түз калыптын көңдөйүнө туруктуу басымдын же көлөмдүн астында куюуга болот. Бул ыкмалардын айрымдары патенттер менен корголот; ошондуктан аларды пайдалануу үчүн тийиштүү лицензиялык келишимдер түзүлүшү керек.
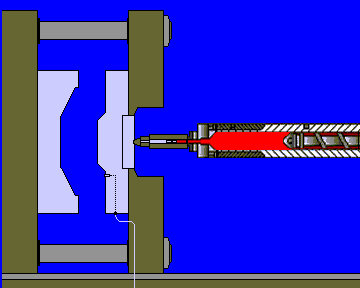
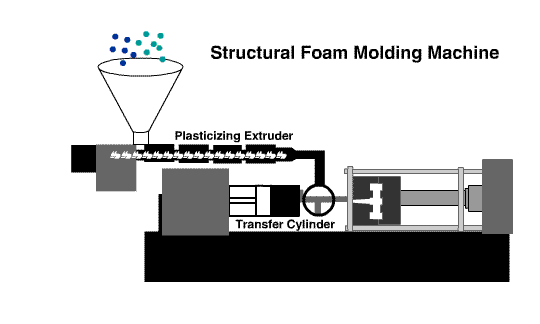
Foam Injection Fording
Бул ыкма структуралык бөлүктөрүндө жогорку каршылык жана катуулугун жетүү үчүн натыйжалуу, жеткиликтүү жол менен камсыз кылат. Бул артыкчылыкка кошумча, структуралык көбүк бөлүктөрү жогорку жылуулук изоляцияга, көбүрөөк химиялык каршылыкка жана жакшыртылган электр жана акустикалык мүнөздөмөлөргө ээ. Бул бөлүктөр эки катмардын ортосундагы көбүк өзөгүн камтыйт; бул өзөк чайырдагы инерттүү газды эритип, калыптын көңдөйүнө газ-пластикалык эритмени куюганда анын кеңейишине жол берүү менен алынат. Биз көбүк инъекциялык калыптоо аркылуу өндүрүлгөн тетиктерди кайдан тапсак болот? Бул процесс унаа панелдеринде бир бөлүгүнүн салмагын азайтуу үчүн альтернатива катары колдонулат.
Жука дубал инъекциялык калыптоо
Бул учурда негизги технологиялык инновация акыркы натыйжага байланыштуу: абдан жука дубалдары бар бөлүм.
Бул процесстин негизги кыйынчылыгы - бул дубалдын туурасы кандай болушу керек экенин "ичке дубал" деп эсептөө. Жалпы эреже катары, туурасы жарым миллиметрден (1/50 дюймдан) ашпаган тетиктер жасалганда, алар жука дубалга ээ деп эсептелет.
Дубалдын туурасын кыскартуу менен байланышкан артыкчылыктар бүгүнкү күндө абдан жогору бааланып, изделүүдө.
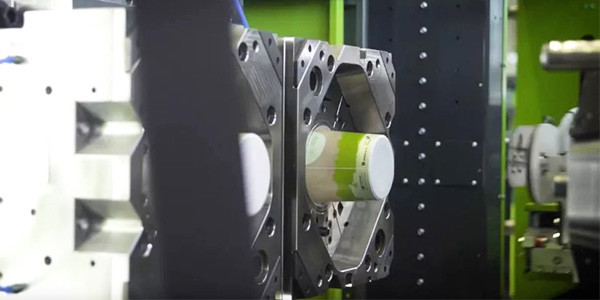
Көп компоненттүү Injection Molding
Ошондой эле инъекциялык формалоо же ашыкча инъекция деп аталат, анткени бул долбоор негизинен пластик же металлдык компонент болгон негизги материалдын (субстрат) үстүнө катуу же жумшак полимерди каптап коюуну камтыйт.
Жалпысынан алганда, бул технология бир калыптын ичинде жана бир процесстин бир бөлүгү катары бирден ашык компоненттерди же материалдарды инъекциялоо катары аныкталышы мүмкүн, бул эки, үч же андан көп материалдарды түрдүү түстөгү, текстурадагы жана формадагы айкалыштырууга мүмкүндүк берет.
Көп материалдан жасалган инжектордук форманын кандай артыкчылыктары бар?
Көп материалдан жасалган инжектордук форма пластмассалардын ар кандай түрлөрүнөн түзүлө турган татаал бөлүктөрдү жасоого мүмкүндүк берет. Бул пластикалык инъекция процессинин негизги артыкчылыгы - механикалык, жылуулук жана химиялык туруктуулугу жогору болгон тетиктерди алууга болот.
Келерки жылдын пластмассадан куюу тенденциялары
Пластикалык инжектордук форманын туруктуулугу
Пластмассадан куюу өнөр жайы туруктуулуктун жаңы баалуулуктарына жана эрежелерине тез ыңгайлашууда, айрыкча пластик өнөр жайы барган сайын көзөмөлдөнүп, жөнгө салынып жаткан учурда. Ошентип, инжектордук форманын жаңы тенденциялары төмөнкүлөрдү көрсөтөт:
100% кайра иштетилүүчү пластикалык материалдарды колдонуу, ошондой эле коопсуз жана экологиялык жактан нейтралдуу.
Өндүрүш учурунда көмүртек изин азайтуу үчүн альтернативаларды издөө. Бул энергиянын кайра жаралуучу булактарын колдонууну жана өндүрүш процессинде энергиянын жоготууларын азайтуу багытында иштөөнү камтышы мүмкүн
Ошол эле учурда компаниялар туруктуу моделдерге өтүү продукциянын сапатына, анын ичинде продукциянын механикалык жана физикалык касиеттерине доо кетирбөөсүнө кепилдик бериши керек.
Жеңил материалдарга суроо-талаптын өсүшү
Жеңил материалдар көбүнчө азыраак экономикалык чыгымдарга (мисалы, транспортко тартылган), ошондой эле азыраак энергия чыгымдарына (мисалы, унаа бөлүктөрүндө) айланат. Медициналык аппараттардагы жеңил материалдар да бейтаптардын натыйжаларын жакшыртат.
Пластикалык инъекциялык калыптарга ылайыкташтырылган чечимдер
Пластикалык инъекциялык формада үнөмдүү варианттарды издөө, ошондой эле ыңгайлаштырылган чечимдерге артыкчылык берүүгө алып келди, анткени барган сайын көп компаниялар техникалык бөлүктөрү алардын өзгөчө муктаждыктарына ылайыкташтырылганда, алардын ROI жогорулашын түшүнүшөт.
Пластмассадан куюу автоматташтыруу жана жаңы технологиялар
Автоматташтырылган программалык камсыздоонун ар кандай варианттары, ошондой эле AI, Machine Learning жана өнүккөн аналитиканы киргизүү пластикалык инъекциялык форманын мүмкүнчүлүктөрүн андан ары түртүп жатат.
Бул технологиялар жабдуулардын иштебей калуу убактысын жана бузулууларын азайтууга, тейлөөнүн болжолдуу программаларын иштеп чыгууга жана өндүрүш циклдерин тездетүүгө мүмкүндүк берет. Ошол эле учурда, жаңы программалык камсыздоо компанияларга долбоорлоо процессинде инъекциялык калыптоо циклдерин окшоштурууга, туура эмес толтуруу үлгүлөрү сыяктуу маселелерди текшерүүгө мүмкүндүк берет. Бул өндүрүш процессине өтүүдөн мурун маселелерди оңдоп, убакытты жана акчаны үнөмдөйт.