इंजेक्शन मोल्डिंगच्या सामान्य मोल्डिंग दोषांवर उपाय
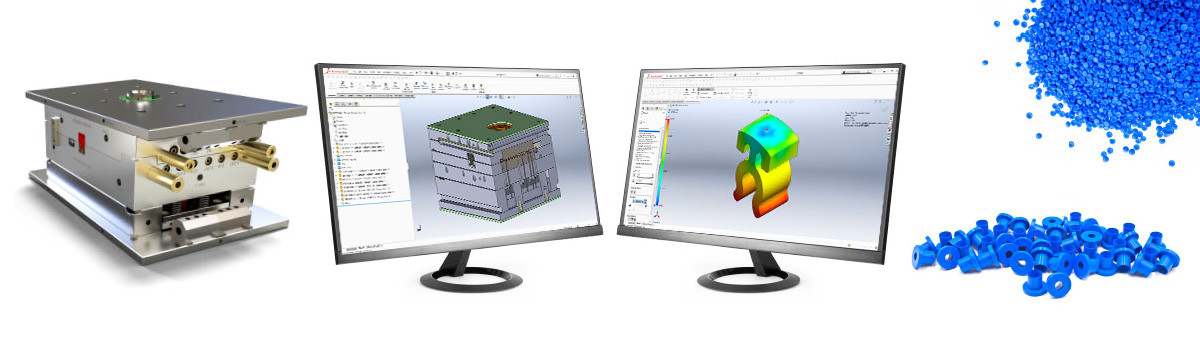
प्लॅस्टिक इंजेक्शन मोल्डिंग भागांवर प्रक्रिया करण्यासाठी मोल्ड वापरताना दोष सामान्य असतात आणि याचा मोठ्या प्रमाणावर प्रक्रियेच्या कार्यक्षमतेवर परिणाम होतो. खालील सामान्य मोल्डिंग दोष आणि प्लास्टिक इंजेक्शन मोल्ड भागांसाठी उपाय आहेत.
लहान शॉट्स
साचे पूर्णपणे भरलेले नसल्यामुळे तयार केलेल्या उत्पादनांचा शॉर्ट शॉट्स अपूर्ण आहेत.
हा दोष सामान्यत: गेटपासून दूर असलेल्या ठिकाणी किंवा साच्यातील अरुंद भागांतून पोहोचू शकणार्या भागांवर दिसून येतो कारण अरुंद भाग वितळण्याच्या प्रवाहावर परिणाम करू शकतात.
शॉर्ट शॉटमुळे मायक्रो फ्लो मार्क्स होऊ शकतात किंवा परिणामी उत्पादनाचा मोठा भाग गहाळ होऊ शकतो.
कारण:
लहान शॉट्सच्या कारणांमध्ये हे समाविष्ट आहे:
मोल्डमध्ये इंजेक्ट केलेला कच्चा माल पुरेसा नाही.
वितळण्याची प्रतिकारशक्ती मोठी असते, परिणामी साचा पूर्णपणे भरता येत नाही.
साच्याचे बाहेर पडणे खराब असते आणि पोकळ्या निर्माण होण्यास कारणीभूत ठरते जे वितळणे अवरोधित करते, ज्यामुळे वितळणे साच्याच्या काही भागात वाहू शकत नाही.
बर्न्स
साच्याच्या पोकळीतून उत्पादनात बाहेर काढलेल्या अतिरिक्त कच्च्या मालाच्या चिकटून बुर तयार होतात.
हा दोष उत्पादनाच्या काठावर किंवा मोल्डच्या प्रत्येक बनलेल्या भागावर असेल. कच्चा माल साच्यातून ओव्हरफ्लो होऊ शकतो, किंवा मूव्हिंग आणि फिक्सिंग मोल्डच्या बाँडिंग साइट्स.
बुरर्स मोल्ड कोरवर देखील आढळू शकतात, जे हायड्रॉलिक दाब किंवा कोनीय पिनमुळे होते.
burrs तीव्रता बदलते, कधी कधी पातळ, कधी कधी दाट.
कारण:
बुरशीच्या कारणांमध्ये हे समाविष्ट आहे:
क्लॅम्पिंग मोल्डची पृष्ठभाग खराब झाली आहे किंवा खूप जास्त थकलेली आहे.
मूव्हिंग मोल्ड आणि फिक्सिंग मोल्ड लॉक केलेले असताना ते विस्थापित असतात.
साच्यातील कच्च्या मालाचा दाब मोल्ड क्लॅम्पिंग फोर्सपेक्षा जास्त असतो.
वर नमूद केलेली तिसरी अट विविध कारणांमुळे निर्माण होईल. खालील परिस्थितींमध्ये, कच्च्या मालाचा दाब मोल्ड क्लॅम्पिंग फोर्सपेक्षा जास्त असतो.
इंजेक्शन मोल्डच्या पहिल्या टप्प्यावर (मोल्ड फिलिंग स्टेज) खूप कच्चा माल भरला जातो, ज्यामुळे साच्याच्या आत दाब वाढतो.
मोल्ड भरण्याच्या प्रक्रियेदरम्यान, वितळण्याच्या प्रवाहाचा मोठा प्रतिकार देखील साच्याच्या आत दबाव वाढवेल.
प्रेशर होल्डिंग स्टेज दरम्यान मोल्ड पोकळीचा दाब खूप जास्त असतो.
मोल्ड क्लॅम्पिंग फोर्स पुरेसे नाही.
अधोगती
विघटन अनेक परिणाम होऊ शकते. समस्येचे प्रमाण आणि तीव्रता देखील बदलते. सर्वात गंभीर प्रकरणात, यामुळे उत्पादनाची संपूर्ण विकृती आणि खराब यांत्रिक गुणधर्म होऊ शकतात. स्थानिक निकृष्टतेमुळे फक्त गडद पट्टे किंवा डाग पडतील.
कारण:
कच्चा माल खराब झाल्याने निकृष्ट दर्जा निर्माण होतो. प्लास्टिक बनवणारे लांब साखळीचे रेणू जास्त उष्णतेमुळे किंवा जास्त कातरण्याच्या ताणामुळे विघटित होतात. रेणूंच्या विघटनादरम्यान, वाष्पशील वायू विघटन प्रक्रियेस गती देईल, ज्यामुळे कच्च्या मालाचा रंग कमी होईल. मोठ्या प्रमाणातील रेणूंच्या विघटनाने शेवटी कच्च्या मालाची सामग्री खंडित होईल आणि यांत्रिक गुणधर्मांवर नकारात्मक प्रभाव पडेल.
मटेरियल बॅरलच्या असमान तापमानामुळे स्थानिक ऱ्हास होऊ शकतो.
खालील परिस्थितींमध्ये विघटन होऊ शकते:
मटेरियल बॅरल किंवा हॉट रनर सिस्टममध्ये कच्चा माल जास्त गरम केला जात आहे.
कच्चा माल बराच काळ बॅरलमध्ये राहतो.
इंजेक्शन मोल्डिंग प्रक्रियेदरम्यान, कच्च्या मालावर कातरण्याचा ताण खूप मोठा असतो. जर नोझल ब्लॉक केले असतील किंवा गेट्स आणि रनर खूप अरुंद असतील तर ते कातरणे तणाव वाढवेल.
विकृती
सामान्य परिस्थितींमध्ये, उत्पादनांचे आकार मोल्ड्सच्या अनुरूप असावेत. विकृती उत्पादनांच्या विकृतीचा संदर्भ देते.
जेव्हा स्थिती बिघडते, तेव्हा उत्पादने मोल्डमधून बाहेर काढल्यावर पूर्णपणे विकृत होतात. जेव्हा स्थिती गंभीर नसते, तेव्हा उत्पादनाच्या आकारात लहान अनियमितता दिसून येतील.
लांब पण आधार नसलेली कडा किंवा मोठी विमाने ही अशी क्षेत्रे आहेत जी विकृत होण्याची सर्वाधिक शक्यता असते.
कारण:
विकृतीची कारणे:
जेव्हा मूस सोडला जातो तेव्हा तापमान खूप जास्त असते.
जाड आणि पातळ भागात थंड होण्याची वेळ वेगळी असते किंवा मूस हलवताना आणि फिक्सिंग मोल्डमध्ये तापमानाचा फरक असतो, उत्पादनांच्या आतील संकोचन वेगळे असते.
भरताना साचा प्रवाह गुळगुळीत नसतो (तथाकथित "फ्रीझिंग ओरिएंटेशन") किंवा दाब होल्डिंग स्टेजवर मोल्ड पोकळीतील दाब खूप जास्त असतो.
अशुद्धी
अशुद्धता अनेकदा वेगवेगळ्या रंग, पॅच किंवा पट्ट्यांमध्ये स्पॉट्सच्या स्वरूपात दिसून येते. सर्वात सामान्य म्हणजे ब्लॅक स्पॉट.
अशुद्धता फक्त लहान ठिपके असू शकतात, परंतु जेव्हा ते गंभीर असते तेव्हा स्पष्ट पट्टे किंवा डी-कलरिंगचा मोठा भाग देखील असू शकतो.
कारण:
अशुद्धता कच्च्या मालामध्ये मिसळलेल्या विविध पदार्थांमुळे उद्भवते, जसे की:
कच्चा माल बॅरल्समध्ये नेला जातो तेव्हा विविध वस्तूंमध्ये मिसळतो.
कच्च्या मालाचे विघटन हे कोणत्याही कटिंग यंत्रणेतून पडलेले असू शकते आणि कच्च्या मालामध्ये मिसळले जाऊ शकते, जसे की मशीन बोल्ट, ड्रायिंग ड्रमची आतील भिंत, सांधे/नोझल्स.
लॅमिनेशन
लॅमिनेशन उत्पादनांच्या पृष्ठभागावर "त्वचा प्रभाव" निर्माण करेल, जो उत्पादनांच्या पृष्ठभागाच्या गुणधर्म आणि पोतमधील फरकामुळे आणि इतर कच्च्या मालामुळे होतो आणि ते सोलून काढता येणारी त्वचा तयार करते.
जेव्हा लॅमिनेशन गंभीर असते, तेव्हा संपूर्ण क्रॉस सेक्शन क्षेत्र वेगवेगळ्या स्तरांनी बनलेले असते, आणि एकत्र वितळलेले नाही. जेव्हा दोष कमी स्पष्ट असतात, तेव्हा उत्पादनांचे स्वरूप आवश्यकता पूर्ण करू शकते, परंतु उत्पादनांचे यांत्रिक गुणधर्म खंडित करतात.
कारण:
लॅमिनेशनची दोन मुख्य कारणे आहेत. पहिली गोष्ट म्हणजे जेव्हा दोन वेगवेगळ्या प्रकारचे कच्चा माल चुकीच्या पद्धतीने मिसळला जातो. दबावाखाली दोन कच्चा माल एकाच वेळी बॅरलमध्ये नेला जाईल. तथापि, जेव्हा मोल्ड थंड झाल्यावर एकत्र वितळता येत नाही, त्याचप्रमाणे उत्पादने तयार करण्यासाठी वेगवेगळ्या स्तरांना जबरदस्तीने एकत्र दाबले जाते.
दुसरे: जर थंड वितळणे अरुंद गेटमधून जाण्यास भाग पाडले गेले तर कातरणे तणाव निर्माण होईल. खूप जास्त कातरणे तणावामुळे आधीच वितळलेला वितळलेला थर पूर्णपणे मिसळला जाऊ शकत नाही.
मिसळण्याचा धोका:
एक गोष्ट ज्याची जाणीव ठेवली पाहिजे ती म्हणजे काही कच्चा माल एकत्र मिसळल्यास मजबूत रासायनिक अभिक्रिया होईल, जसे की PVC आणि Avetal मिसळू नये.
चांदीचा रेषीय
स्लिव्हर रेखीय ही फक्त स्थानिक घटना असू शकते, परंतु जेव्हा ती गंभीर असते तेव्हा संपूर्ण पृष्ठभागावर विस्तृत केली जाऊ शकते.
सिल्व्हर लिनियर उत्पादनांच्या देखाव्यावर परिणाम करेल आणि उत्पादनांच्या यांत्रिक गुणधर्मांना देखील नुकसान करेल.
कारण:
खालील दोन बिंदूंमुळे सिल्व्हर रेषीय बनतात:
कच्चा माल ओला आहे आणि त्यातील काही हवेतील वाफ शोषून घेतील. जर कच्चा माल खूप ओला असेल तर, उच्च तापमान आणि बॅरलच्या उच्च दाबाखाली दाबयुक्त वाफ तयार होऊ शकते. ही वाफ उत्पादनाच्या पृष्ठभागावरुन फुटतात आणि चांदीचे पट्टे तयार करतात.
वितळल्याने थर्मल नुकसान होते आणि स्थानिक ऱ्हास निर्माण होतो. व्युत्पन्न होणारा वाष्पशील वायू साच्याच्या पृष्ठभागावर अवरोधित केला जाईल आणि उत्पादनांच्या पृष्ठभागावर पट्टे तयार होतील.
हे अधोगतीइतके वाईट नाही. जोपर्यंत वितळण्याचे तापमान जास्त असते किंवा प्लॅस्टिकायझेशन दरम्यान कातरणे किंवा मोल्डमध्ये इंजेक्ट केले जाते तोपर्यंत हे होऊ शकते.
चकचकीत/सावली
उत्पादनांची पृष्ठभागाची समाप्ती मोल्डच्या सारखीच असावी. जेव्हा दोनची पृष्ठभागाची समाप्ती भिन्न असते, तेव्हा चमक/सावली दोष आढळतात.
जेव्हा दोष आढळतात तेव्हा पृष्ठभाग उदास असेल आणि खडबडीत पृष्ठभाग गुळगुळीत आणि तकतकीत असेल.
कारण:
चकचकीत/सावलीच्या कारणांमध्ये हे समाविष्ट आहे:
वितळणे सहजतेने वाहते किंवा मोल्ड पृष्ठभागाचे तापमान कमी असते, परिणामी मटेरियल मोल्डिंग करताना मोल्ड पृष्ठभाग फिनिश डुप्लिकेट करता येत नाही.
प्रेशर होल्डिंग दरम्यान, पोकळीतील दाब इतका जास्त नसतो की सामग्री थंड होण्याच्या प्रक्रियेत साच्याच्या पृष्ठभागावर चिकटून राहते, ज्यामुळे संकोचन खुणा राहतात.
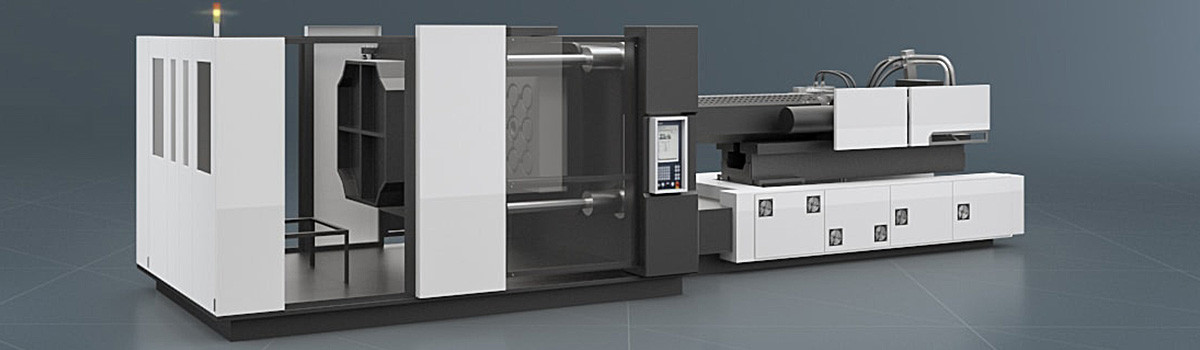
प्रवाहाचे गुण
फ्लो मार्क्स उत्पादनांच्या पृष्ठभागावर अनेक स्वरूपात आढळू शकतात. साधारणपणे, ते सावलीचे क्षेत्र तयार करेल.
प्रवाहाचे चिन्ह उत्पादनांच्या पृष्ठभागावर कोणतेही नक्षी किंवा उदासीनता निर्माण करत नाहीत, जे बोटांनी जाणवू शकत नाहीत. या दोषाला ड्रॅग मार्क्स, घोस्टिंग आणि शॅडो असेही म्हणतात.
जेव्हा प्रवाहाचे गुण स्पष्ट असतात, तेव्हा ते खोबणी तयार करतात आणि उत्पादनांच्या पृष्ठभागावर गुणांसारखे दोष सोडतात.
कारण:
प्रवाह चिन्हे आढळू शकतात जेव्हा:
वितळण्याची प्रवाहक्षमता खराब असते किंवा साच्याच्या पृष्ठभागाचे तापमान कमी असते, परिणामी साचा भरण्याच्या प्रक्रियेत प्लास्टिकचा प्रवाह मोठ्या प्रमाणात प्रतिरोधक असतो.
मोल्ड फिलिंगमध्ये, रेझिस्टन्ससह वितळणारा प्रवाह, जो डाईच्या असमान पृष्ठभागामुळे, डाईच्या पृष्ठभागावर छापलेले गुण किंवा नमुने किंवा फिलिंग प्रक्रियेदरम्यान वितळलेल्या प्रवाहाची दिशा बदलल्यामुळे होऊ शकतो.
जॉइंटिंग लाइन
जेव्हा मोल्ड भरण्याच्या वेळी दोन वितळलेल्या फ्रंट्स एकत्र येतात तेव्हा जोडण्याची ओळ तयार होते आणि उत्पादनाच्या पृष्ठभागावर एका रेषेप्रमाणे दिसून येते.
जॉइंटिंग लाइन ही उत्पादनांच्या पृष्ठभागावरील क्रॅकिंग लाइनसारखी असते, जी शोधणे स्पष्ट नसते.
मोल्ड डिझाइन करताना, काही दृश्यमान जोडणी रेषा अपरिहार्य असतात. या प्रकरणात, उत्पादनांची ताकद आणि देखावा खराब होऊ नये म्हणून जॉइंटिंग लाइन शक्य तितकी लहान करा.
कारण:
मेल्ट फ्रंटच्या पिढीची अनेक कारणे आहेत. सर्वात संभाव्य कारण मोल्ड कोरच्या काठावर वितळणारा प्रवाह असू शकतो. जेव्हा दोन वितळतात तेव्हा ते जोडणी रेषा तयार करतात. दोन मेल्ट्स फ्रंटचे तापमान पुरेसे उच्च असावे जेणेकरून ते यशस्वीरित्या एकत्र केले जातील आणि उत्पादनांची ताकद आणि देखावा प्रभावित करू नये.
जेव्हा दोन वितळणे पूर्णपणे एकत्र जमू शकत नाहीत, तेव्हा दोष निर्माण होतील.
दोषांची कारणे:
साच्यामध्ये जाड आणि पातळ भाग असतात आणि वितळण्याचा वेग वेगळा असतो, जेव्हा वितळणे साच्याच्या पातळ भागातून वाहते तेव्हा तापमान कमी असते.
प्रत्येक धावपटूची लांबी वेगळी असते. एकाकी धावपटू थंड करणे सोपे होईल.
प्रेशर होल्डिंग स्टेज दरम्यान पूर्णपणे वितळण्यास परवानगी देण्यासाठी मोल्ड पोकळीचा दाब पुरेसा नाही.
उर्वरित बुडबुडे वितळलेल्या फ्रंटला फ्यूज करण्यास अक्षम करतात, ज्यामुळे बर्न देखील होईल.
बर्निंग
जळणे हे शॉर्ट शॉटसारखेच असते, परंतु अनियमित लुप्त होत जाणार्या कडा आणि किंचित जळत्या वासासह. प्लॅस्टिक जळण्याच्या वासासह, स्थिती गंभीर असताना, उत्पादनावर कार्बन ब्लॅक भाग दिसून येतील.
दोष दूर न केल्यास, साच्यावर अनेकदा काळे साचले जातात. जळल्यामुळे तयार होणारे वायू किंवा तेल पदार्थ ताबडतोब तपासले नाहीत तर ते हवेतील छिद्रे अडवू शकतात. बर्निंग सामान्यतः मार्गांच्या शेवटी आढळते.
कारण:
ज्वलन अंतर्गत ज्वलन परिणामामुळे होते. जेव्हा हवेचा दाब फारच कमी वेळात झपाट्याने वाढतो तेव्हा तापमान वाढते आणि जळजळ होते. गोळा केलेल्या डेटानुसार, इंजेक्शन मोल्डिंग प्रक्रियेतील अंतर्गत ज्वलन प्रभाव 600 अंशांपर्यंत उच्च तापमान निर्माण करू शकतो.
जळजळ निर्माण होऊ शकते जेव्हा:
मोल्ड भरण्याचा वेग वेगवान आहे ज्यामुळे मोल्ड पोकळीतून हवा रिकामी होऊ शकत नाही आणि येणार्या प्लास्टिकच्या ब्लॉकमुळे हवेचे फुगे तयार होतात आणि संकुचित झाल्यानंतर अंतर्गत ज्वलनाचा परिणाम होतो.
हवेतील छिद्रे अवरोधित आहेत किंवा वायुवीजन गुळगुळीत नाही.
साच्यातील हवा हवेच्या छिद्रांमधून रिकामी केली पाहिजे. जर वायुवीजन स्थिती, संख्या, आकार किंवा फंक्शन्समुळे प्रभावित होत असेल तर हवा साच्यात राहून जळते. मोठ्या मोल्ड क्लॅम्पिंग फोर्समुळे खराब वायुवीजन देखील होईल.
संकोच
संकोचन म्हणजे उत्पादनांच्या पृष्ठभागावरील किंचित पोकळी.
जेव्हा दोष थोडे असतात तेव्हा उत्पादनांची पृष्ठभाग असमान असते. जेव्हा ते गंभीर असेल तेव्हा उत्पादनांचे मोठे क्षेत्र कोसळेल. कमानी, हँडल आणि प्रोट्रेशन्स असलेली उत्पादने सहसा संकोचन दोषांमुळे ग्रस्त असतात.
कारण:
कूलिंग दरम्यान कच्च्या मालाच्या मोठ्या क्षेत्राच्या संकोचनामुळे संकोचन होते.
उत्पादनांच्या जाड भागामध्ये (कमान सारख्या), सामग्रीचा कोर समशीतोष्ण कमी असतो, त्यामुळे पृष्ठभागाच्या तुलनेत संकोचन नंतर होईल, ज्यामुळे कच्च्या मालाच्या आत एक आकुंचन शक्ती निर्माण होईल आणि बाहेरील बाजू आवक उदासीनतेमध्ये खेचली जाईल. संकोचन निर्माण करण्यासाठी.
संकोचन खालील परिस्थितींमध्ये होते:
शीतकरण प्रक्रियेत कच्च्या मालाच्या संकोचनातून निर्माण होणाऱ्या शक्तीपेक्षा मोल्ड पोकळीतील दाब कमी असतो.
कूलिंग प्रक्रियेदरम्यान मोल्ड पोकळीचा अपुरा दबाव वेळ, परिणामी कच्चा माल गेटमधून पोकळीतून बाहेर पडतो.
मोल्डिंग आणि प्रेशर होल्डिंग स्टेज दरम्यान कच्च्या मालाची पुरेशी बफरिंग क्षमता नसते कारण जास्त कच्चा माल टोचण्यापूर्वी स्क्रू पूर्णपणे मागे घेतला जातो.
गेट्स आणि रनर्सचे क्रॉस सेक्शन क्षेत्र उत्पादनांच्या जाडीपेक्षा खूपच लहान आहेत, याचा अर्थ उत्पादने एक्सट्रूझन प्रक्रियेपूर्वी गेट्स आधीच गोठलेले आहेत.
फुगे
व्हॅक्यूम फुगे हवेच्या बुडबुड्याच्या स्वरूपात सादर केले जातात, जे पारदर्शक उत्पादनांवर सहजपणे आढळू शकतात. हे अपारदर्शक उत्पादनांच्या क्रॉस सेक्शनवर देखील पाहिले जाऊ शकते.
कारण:
हवेचे फुगे हे उत्पादनांचे निर्वात भाग असतात, जे शीतकरण प्रक्रियेदरम्यान कच्चा माल संकुचित झाल्यावर तयार होतात.
संकोचन प्रमाणेच, कच्च्या मालाच्या आतील भाग आकुंचनशील शक्ती निर्माण करतो. फरक काय आहे की जेव्हा बुडबुडे तयार होतात तेव्हा उत्पादनांचे बाह्य स्वरूप घट्ट केले जाते आणि ते कोसळत नाहीत, त्यामुळे पोकळ फुगे तयार होतात.
बुडबुडे होण्याची कारणे कमी होण्यासारखीच आहेत, यासह:
अकार्यक्षम मोल्ड पोकळी दाब
अपुरा पोकळी दबाव वेळ
रनर आणि गेटचा आकार खूपच लहान आहे
फवारणीच्या खुणा
फवारणीचे चिन्ह गेटच्या समोरील थ्रेडेड क्षेत्रास सूचित करतात. फवारणीच्या खुणा केवळ उत्पादनांच्या देखाव्यावरच परिणाम करत नाहीत तर उत्पादनांच्या ताकदीवर देखील परिणाम करतात.
कारण:
साचा भरण्याच्या प्रक्रियेदरम्यान वितळण्याचा प्रवाह नियंत्रणाबाहेर गेल्याने फवारणीचे गुण येतात.
वितळलेले प्लास्टिक मोठ्या दाबाने साच्यात येते. जर मोल्ड भरण्याचा वेग खूप जास्त असेल तर, प्लास्टिक मोल्ड पोकळीच्या मोकळ्या अंतरातून बाहेर पडेल आणि त्वरीत परत येईल आणि थंड होईल. त्या वेळी, धागे तयार होतात, जे वितळलेल्या प्लास्टिकला गेट्समध्ये प्रवेश करण्यास अवरोधित करतात.
फवारणीच्या खुणांचे मुख्य कारण म्हणजे गेट्सची चुकीची स्थिती किंवा गेटची रचना. खालील दोन परिस्थिती दोषांची स्थिती बिघडवतील:
उच्च मोल्ड भरण्याची गती
साचा भरताना खराब वितळण्याचा प्रवाह