Справа в Індії
Служба вставки прес-форми DJmolidng у лиття під тиском для індійських компаній
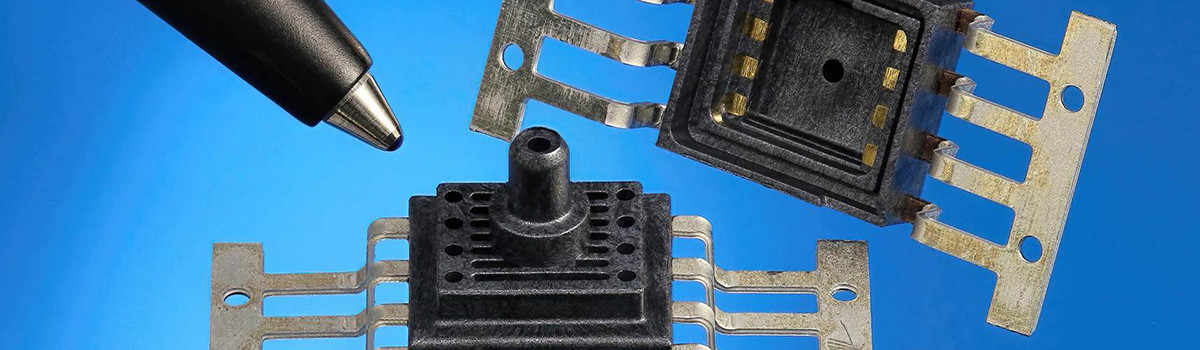
Вставна форма, як правило, є різновидом форми, яка виготовляє гайки, металеві деталі або жорсткі пластикові деталі, закріплені всередині порожнин для лиття під тиском.
DJmolding пропонує послуги лиття під тиском зі вставками для індійського ринку, і ми виробляємо багато пластикових деталей для вставок для різних галузей промисловості, особливо для виробників побутової техніки. Деякі індійські виробники побутової техніки закуповують пластикові деталі вставки на довгий час у DJmolding. Ми маємо дуже хороші партнерські стосунки з цими індійськими компаніями.
Інжекційне лиття вставних гайок: матеріалом для гайок може бути нержавіюча сталь, мідь, бронза та сталь, зазвичай використовуються мідні гайки. Мідь легко накатувати, що сприяє кращому зрощенню гайок і пластику. Допуск внутрішніх отворів гайки слід контролювати в межах 0.02 мм, інакше легко спричинити спалах, якщо допуск перевищує 0.02 мм. У прес-формі потрібно зібрати гайки в штифти для тестування. Якщо він щільно затиснутий між гайками та штифтами, деталь буде важко витягти, що спричинить сліди від викиду або проблеми з прилипанням. Якщо він не прилягає, це спричинить спалах.
Інжекційне лиття металевих частин:
Металеві частини можуть бути з нержавіючої сталі, алюмінію, міді, сталі тощо. Допуск металевих частин слід контролювати в межах 0.02 мм, інакше важко ущільнити матеріал і легко мати спалах. Площа металевих частин не може проектуватися занадто великою.
Якщо площа заповнення металевих частин занадто велика, буде дуже важко досягти повного впорскування через велику різницю температур між металевими частинами. Розташування металевих частин зазвичай проектується в порожнині, оскільки порожнина не рухається, що допомагає уникнути спалаху внаслідок втрати металевих частин під час руху (у важких випадках може пошкодити цвіль). В окремих випадках положення металевих частин можна проектувати лише всередині або бічній поверхні виробу.
Вставте твердий пластик під тиском:
Зазвичай обирають тверді пластики з високою температурою плавлення, такі як PEEK, PA66+30GF, PP+30GF, PA12+30GF, PPS… тощо. Допуск на ці тверді пластики має бути точним. Дефекти, такі як усадка, вм'ятини та деформація, не можуть існувати в зоні ущільнення. Під час кріплення прес-форми твердий пластик слід помістити всередину форми для тестування та залишити 0.05-0.1 мм попереднього пресування навколо зони ущільнення для досягнення кращого ущільнення.
Тверда пластикова частина не повинна бути призначена для занадто великої площі, що спричинить різницю температур і ускладнить заповнення матеріалу під час ін’єкції. Зазвичай тверду пластикову частину закріплюють збоку порожнини, оскільки порожнина не рухається, щоб уникнути спалаху або навіть пошкодження цвілі під час руху форми. В окремих випадках розташування металевих частин можна проектувати лише в серцевині або бічній поверхні виробу.
Ключові моменти дизайну
1. Розрахункова усадка для виробів з гайковими вставками, тоді як для виробів з металевими частинами та твердими пластиковими вставками проектна усадка не потрібна. Для областей, які потребують суворого допуску, змініть допуск розміру продуктів до середнього значення.
2. Зазвичай використовуйте основу форми зі стандартними точковими воротами при проектуванні прес-форми, а при вторинній ін’єкції помістіть вставні частини в порожнину якомога більше. За умови виготовлення вставок, закріплених у порожнині, розгляньте, як зробити частину, що залишилася в сердечнику після лиття під тиском, таким чином, деталь може бути викинута. Зазвичай додають еластичні блоки в порожнину та еластичний клей, щоб частина залишалася в серцевині. Відстань між еластичними блоками і клеєм не може бути занадто великою, інакше сила пружності призведе до деформації жорстких пластикових або металевих деталей. Відстань зазвичай розрахована в межах 2 мм, і відповідно збільште кількість еластичних блоків і еластичного клею, коли металеві або тверді пластикові вставки мають відносно велику площу.
3. Товщина матеріалу найкраща в межах 1.3-1.8 мм (приблизно 1.5 мм є найкращою), якщо ні, потрібно перевірити креслення продукту та запропонувати клієнту змінити його. Якщо товщина матеріалу менше 1.3 мм, це важко заповнити матеріалом, тоді як товщина матеріалу товщі 1.8 мм, усадка легко відбутися під час виробництва.
4.Gating дуже важливий у формі. Необхідно повністю враховувати баланс заповнення матеріалом для точки воріт. Коли матеріал надходить до зони, де закріплені металеві або тверді пластикові деталі, швидкість заповнення матеріалом і тиск зменшаться через опір вставок і різницю температур.
5. Для системи ежектора прес-форми необхідно враховувати баланс викиду, інакше після викиду відбудеться деформація. Якщо частини не можуть бути викинуті в рівновазі, потрібно розглянути можливість згортання, щоб вирішити проблему балансу в конструкції конструкції.
6. Щоб забезпечити кваліфікацію зовнішнього вигляду деталей після викиду під час лиття під тиском, ежекторний пристрій має бути твердим пластиковим шматком, вставленим з ABS або PMMA. Якщо поверх прес-форми є герметичне ущільнення, дизайн ковзає в порожнині якомога більше, тому що ковзання в порожнині полегшують установку форми.
7. Щоб забезпечити міцність ущільнення SA (припуск на шов), для продукту, виготовленого методом подвійного лиття під тиском, ширина ущільнення SA має бути не менше 0.8 мм. Для вторинного ін’єкційного матеріалу є твердий пластик, ширина ущільнення SA має бути принаймні 1.0 мм, інакше потрібно запропонувати клієнту змінити продукт.
8. При проектуванні прес-форми ми повинні взяти до уваги машини для лиття під тиском для виробництва, щоб побачити, який тип машини він приймає, вертикальний чи горизонтальний. Рекомендується не проектувати занадто багато порожнин, особливо для прес-форм із холодними литниками, оскільки занадто багато порожнин робить бігун довшим, витрачаючи матеріал, а також шкідливо для досягнення високоефективного впорскування. Щоб відповідати машині для лиття під тиском, ми повинні розглянути, чи є вона компактною та розумною для механізмів продукту. Продукти повинні бути виправлені, щоб гарантувати, що продукти знаходяться в однаковій ситуації кожного разу, коли їх поміщають у форму. Іншим способом є система реагування конструкції, яка попереджає, якщо деталь знаходиться не на тому місці перед закриттям форми, що допомагає зупинити закриття форми. Таким чином, деталі знаходяться в однаковій ситуації у прес-формі, що підвищує кваліфіковані показники та ефективність виробництва при лиття під тиском.
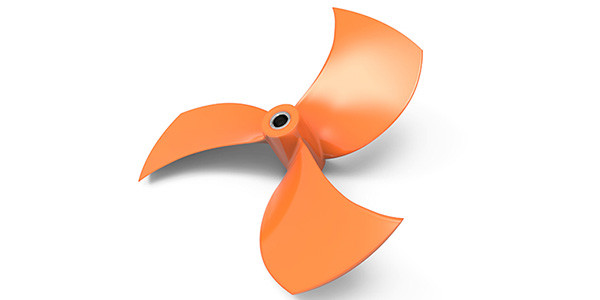
9. Необхідно спроектувати сталеву опору, оскільки зона ін’єкційної форми зазнає великого тиску під час ін’єкційної роботи (форма та розмір мають бути на 5-10 мм більшими, ніж частина). Не можна залишати зазор між деталями навколо зони лиття, інакше деталь втратить форму після вторинного вприскування. Для деталей без SA (припуск на шов) потрібно приділяти цьому аспекту набагато більше уваги.
10. Повітряна поїздка легко Повітряна поїздка відбувається легко під час лиття під тиском, тому необхідно повністю враховувати вентиляцію при проектуванні форми. У всіх сліпих кутах і положеннях для міжміських водопровідних ліній слід проектувати вентиляційні отвори на жорсткій пластиковій частині, оскільки набагато важче заповнювати матеріал у сліпих кутах.
11. Щоб гарантувати, що введений матеріал і кваліфікована тяга повністю заповнені, одним із способів є створення підрізів у кутах деталі, щоб покращити результат приклеювання, а потім зробити деталі більш щільними.
12. У зоні герметизації та лінії розділення ми не повинні виймати форму з порожнини та серцевини, тому що лінії затиску в прес-формі та тяга виймання призведуть до спалаху у формі. Спробуйте вийняти форму за допомогою LISS-OFF.
Типи воріт вставки прес-форми
Точка воріт для вставної форми може бути призначена для спрямування вентиля гарячого литникового клапана, гарячого литникового штифтового затвора, точкового затвора, допоміжного затвора, крайового затвора… тощо.
Ворот клапана з гарячим литником: хороша ліквідність, гнучкий вибір положення, маленька точка затвора. Підходить для масового виробництва і для виробів з товстою стінкою. Може допомогти заощадити матеріал, відсутність матеріальних відходів для воріт, короткий час виконання та висока якість. Єдиним недоліком є незначний слід стробування.
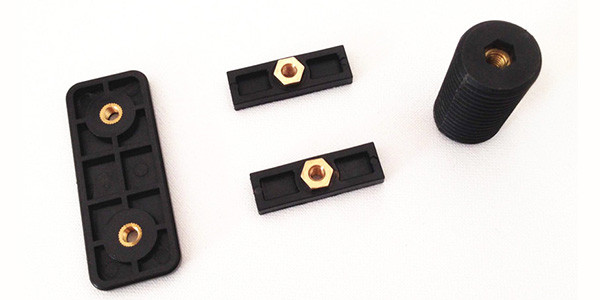
Гаряча литникова шпилька: хороша ліквідність, гнучкий вибір позиції, невелика точка доступу. Підходить для масового виробництва і для виробів з товстою стінкою. Може допомогти заощадити матеріал, відсутність матеріальних відходів для воріт, короткий час виконання та висока якість. Але є дефекти, такі як 0.1 мм матеріалу, що залишився навколо точки воріт, і його легко задирити. Потрібно зробити пази, щоб покрити лівий матеріал навколо точки воріт.
Точкові ворота: вибір позиції гнучкий, слабка ліквідність, довга дистанція бігуна, мала точка воріт. Підходить для дрібносерійного виробництва. Більше відходів навколо точки воріт. Потрібні механічні руки для затискання точки воріт на виробництві. Тривалий термін виконання. Дефект — 0.1-0.2 мм матеріалу, що залишився навколо точки воріт, потрібно зробити канавки, щоб покрити лівий матеріал навколо точки воріт.
Додаткові ворота: можуть бути розроблені на ребрах у порожнині, серцевині, бічних стінках та виштовхувальних штифтах. Можна гнучко вибирати точку воріт, заливні ворота автоматично відокремлюються від частини, невеликий слід стробування. Дефекти: легко витягнути матеріал навколо точки воріт, легко спричинити сліди висихання в положенні стробування, потрібно витирати матеріал вручну, великі втрати тиску з точки воріт через порожнини.
Крайові ворота: розплавлений пластик тече через затвор, розподіляється рівномірно, зменшує напругу; зменшити ймовірність потрапляння повітря в порожнину, уникати утворення смуг і бульбашок. Дефекти: заливний затвор не може автоматично відокремитися від деталі, залишилися сліди литників на краях деталі, потрібні інструменти для обробки заливного затвора. Крайовий затвор може допомогти пропорціонувати впорскування та утримання тиску, а також добре підходить для утримання тиску та подачі, таким чином, це краще для покращення повітропроводів, позначок потоку… тощо.
Обробка та підгонка для вставної форми
1. Перед обробкою відпрацюйте технологію обробки цвілі. Виберіть високоточні машини для обробки, високошвидкісну машину, машину для різання дроту з ЧПУ з повільною подачею, машину для електроерозійної обробки дзеркал тощо.
2. Дизайн 0.05-0.1 мм залишився в місці попереднього пресування.
3. Зверніть увагу на вимоги до точності при обробці основи форми, перевірте допуск після отримання основи форми та не використовуйте її, якщо допуск є некваліфікованим.
4. Помістіть гайки, металеві деталі та тверді пластикові деталі всередину форми для встановлення форми. Якщо ви виявите проблеми з підгонкою форми, перевірте гайки, металеві деталі, жорсткі пластикові деталі та форми, щоб визначити, яка з них невірна. Обробляйте деталь відповідно до креслення, наскільки це можливо, що допомагає відстежувати дані в майбутньому.
5. Не можна використовувати шліфувальну машину для встановлення форми. Зверніться до верстатів для виправлення у випадках, коли прес-форма не підходить.
6. Виконайте перевірку дій перед випробуванням, уникайте пропущеного складання та помилкового складання. Помилкове складання призведе до пошкодження основи форми.
Випробування прес-форми для вставки
1. Під час тестування прес-форми потрібно чітко знати послідовність відкриття, закриття та викидання форми. Розуміти структурні особливості та властивості металевих частин і твердих пластикових деталей.
2. Чітко знайте про кількість зразків, які потрібні клієнтам, підготуйте достатню кількість горіхів, металевих деталей і твердого пластику, оскільки для тестування прес-форми потрібно багато зразків.
3. Зверніть увагу, чи можна тестувати форму без вставок з гайок, металевих частин або твердого пластику. Якщо вставні гайки, металеві деталі та твердий пластик не зібрані у формі, деталі можуть мати дефекти, такі як прилипання до форми або короткий удар.
4. У багатьох випадках потрібно відрегулювати пластину водяної лінії на прес-формі, але іноді вона не може відрегулювати пластину водяної лінії в деякій вставній формі на основі їх структури, або навіть гірше, форма сильно застрягла і потребує модифікації, або форма пошкоджена в відкриття.
5. Проблеми можуть виникнути під час тестування форми, наприклад короткі постріли, повітряні поїздки, спалахи або прилипання до форми. Якщо проблеми можна перевірити на машині для лиття під тиском, краще їх вирішити.
DJmolding має більш ніж 10-річний досвід формування вставок, якщо у вас виникли запитання, зв’яжіться з нами.