Основи лиття пластмас під тиском
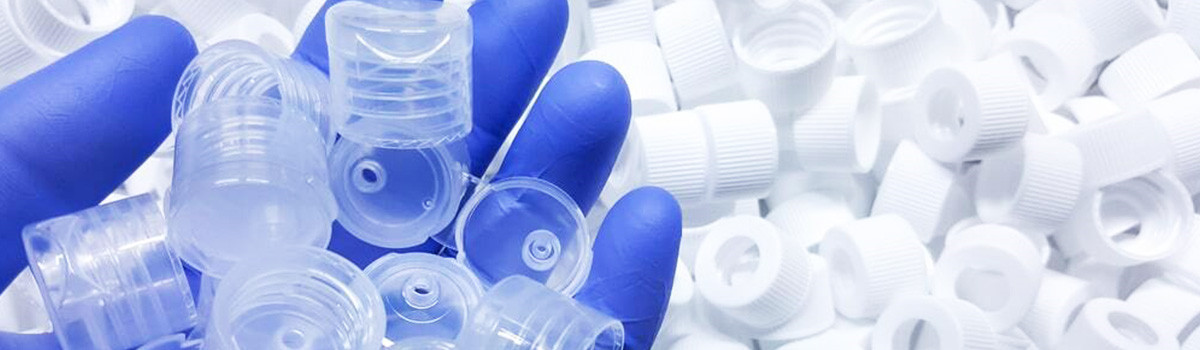
Дослідіть процес лиття під тиском і як він працює.
Лиття пластику під тиском — популярна техніка виробництва, за якої термопластичні гранули перетворюються на великі обсяги складних деталей. Процес лиття під тиском підходить для різноманітних пластикових матеріалів і є життєво важливим аспектом сучасного життя — без нього були б неможливі корпуси для телефонів, електронні корпуси, іграшки та навіть автомобільні деталі. У цій статті будуть розібрані основи лиття під тиском, описано, як працює лиття під тиском, і показано, чим воно відрізняється від 3D-друку.
Які основи лиття пластику під тиском?
Основи процесу лиття пластику під тиском включають створення дизайну виробу, виготовлення інструментів у формі, що відповідає дизайну виробу, плавлення гранул пластикової смоли та використання тиску для впорскування розплавлених гранул у форму.
Перегляньте розбивку кожного кроку нижче:
1. Створення дизайну продукту
Дизайнери (інженери, виробники прес-форм тощо) створюють деталь (у формі файлу CAD або іншого формату, який можна передавати), дотримуючись основних інструкцій щодо проектування, характерних для процесу лиття під тиском. Дизайнери повинні спробувати включити такі особливості у свої проекти, щоб допомогти підвищити успіх пластикових форм для лиття під тиском:
*Втулки для різьбових вставок/кріплень
*Постійна або майже постійна товщина стінок
* Плавні переходи між різними товщинами стінок
*Порожнини в товстих ділянках
* Заокруглені краї
*Осадкові кути на вертикальних стінах
*Ребра для опор
*Фрикційні посадки, з’єднання із замиканням та інші функції з’єднання без застібок
*Живі петлі
Крім того, дизайнери повинні звести до мінімуму такі функції, щоб зменшити кількість дефектів у своїх конструкціях:
*Нерівномірна товщина стінок або особливо тонкі/товсті стінки
*Вертикальні стіни без кутів ухилу
*Раптові геометричні зміни (кути, отвори тощо)
*Погано розроблене ребро
* Підрізи/звиси
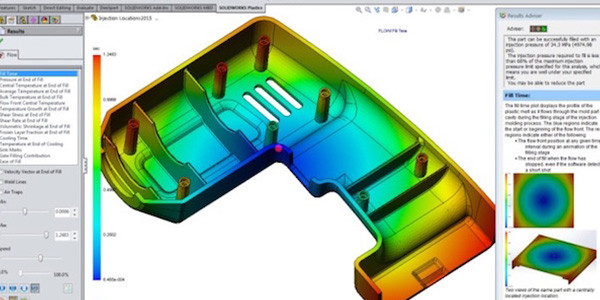
2. Виготовлення прес-форми для інструментів відповідно до дизайну продукту
Висококваліфіковані верстатники та інструментальники, використовуючи конструкцію виробу, виготовляють прес-форму для машини для лиття під тиском. Форма для інструментів (також відома як просто інструмент) є серцем і душею машини для лиття під тиском. Вони ретельно розроблені, щоб утримувати негативну порожнину для дизайну продукту та додаткових функцій, таких як литники, напрямні, ворота, вентиляційні отвори, системи ежектора, канали охолодження та рухомі компоненти. Прес-форми виготовляються зі сталі та алюмінію певних марок, які можуть витримувати десятки тисяч (і іноді сотні тисяч) циклів нагрівання та охолодження, наприклад, алюміній 6063, сталь P20, сталь H13 та нержавіюча сталь 420. Процес виготовлення прес-форми займає більше 20 тижнів, включаючи як виготовлення, так і затвердження, що робить цей етап найрозширенішим аспектом лиття під тиском. Це також найдорожча частина лиття під тиском, і коли форму для інструментів виготовлено, її неможливо кардинально змінити без додаткових витрат.
3. Розплавлення гранул пластикової смоли
Після того, як оператори отримують готову форму, її вставляють у машину для лиття під тиском, і форма закривається, починаючи цикл лиття під тиском.
Пластикові гранули подаються в бункер і в бочку. Поворотний гвинт відтягується назад, дозволяючи матеріалам прослизати в простір між гвинтом і стовбуром. Потім гвинт занурюється вперед, проштовхуючи матеріал у стовбур і ближче до смуг нагрівача, де він плавиться у розплавлений пластик. Температура плавлення підтримується постійною відповідно до специфікацій матеріалу, щоб не відбувалося погіршення якості в бочці чи самій формі.
4. Використання тиску для впорскування розплавлених гранул у форму
Зворотно-поступальний гвинт проштовхує розплавлений пластик через сопло, яке розташоване в поглибленні у формі, відомому як втулка литника форми. Тиск рухомого валика щільно прилягає до форми та насадки, не допускаючи виходу пластику. Під час цього процесу розплавлений пластик піддається тиску, змушуючи його проникати в усі частини порожнини форми та витісняти повітря з порожнини через вентиляційні отвори форми.
Компоненти машини для лиття під тиском
Компоненти машини для лиття під тиском включають бункер, бочку, зворотно-поступальний шнек, нагрівач(и), рухомий валик, сопло, форму та порожнину форми.
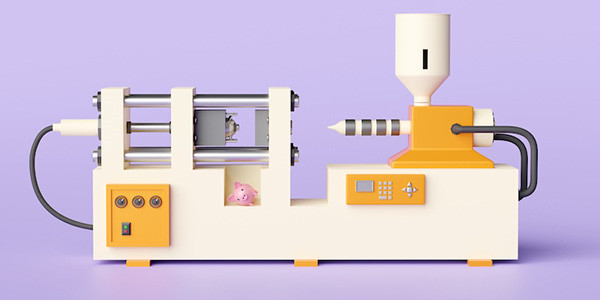
Більше інформації про кожен із компонентів лиття під тиском у списку нижче:
* Бункер: отвір, через який пластикові гранули подаються в машину.
*Бочка: зовнішній корпус машини для лиття під тиском, який містить зворотно-поступальний гвинт і пластикові гранули. Стовбур обтягнутий декількома нагрівальними стрічками і наконечником з підігрітою насадкою.
* Поворотний гвинт: компонент штопора, який транспортує та тисне пластиковий матеріал під час його плавлення через стовбур.
*Обігрівачі: Ці компоненти, також відомі як нагрівальні стрічки, забезпечують теплову енергію пластиковим гранулам, перетворюючи їх із твердої форми на рідку. форму.
*Рухома пластина: Рухомий компонент, з’єднаний із стрижнем форми, який чинить тиск, щоб утримувати обидві половини форми герметичними, а також відпускає стрижень форми, коли відкривається готова деталь.
*Насадка: нагрітий компонент, який забезпечує стандартний вихід для розплавленого пластику в порожнину форми, зберігаючи як температуру, так і тиск максимально стабільними.
* Цвіль: компонент або компоненти, які містять порожнину прес-форми та додаткові опорні елементи, як-от виштовхувальні штифти, робочі канали, канали охолодження, вентиляційні отвори тощо. Як мінімум форми розділені на дві половини: нерухому сторону (ближче до стовбура) і форму сердечник (на рухомому валику).
* Порожнина форми: негативний простір, який, заповнений розплавленим пластиком, формує його в бажану кінцеву частину, а також опори, ворота, напрямні, литники тощо.
Як працює лиття під тиском?
Після того, як пластик заповнив форму, включаючи її литники, напрямні, ворота тощо, форма підтримується при встановленій температурі, щоб забезпечити рівномірне затвердіння матеріалу в формі деталі. Під час охолодження підтримується тиск утримання, щоб зупинити зворотний потік у стовбур і зменшити ефект усадки. У цей момент до бункера додається більше пластикових гранул в очікуванні наступного циклу (або пострілу). Коли охолоджується, валик відкривається і дозволяє викинути готову деталь, а гвинт знову відтягується, дозволяючи матеріалу потрапити в стовбур і почати процес заново.
Цикл лиття під тиском працює за допомогою цього безперервного процесу — закриття форми, подача/нагрівання пластикових гранул, нагнітання їх у форму, охолодження їх у тверду деталь, виштовхування деталі та повторне закриття форми. Ця система дозволяє швидко виготовляти пластикові деталі, і протягом робочого дня можна виготовити понад 10,000 XNUMX пластикових деталей залежно від конструкції, розміру та матеріалу.
Djmolding — китайські компанії, що займаються литтям під тиском. Наш процес лиття під тиском пластику створює нестандартні прототипи та кінцеві виробничі деталі за 1 день, постачальник деталей для лиття під тиском невеликих обсягів до 10000 XNUMX деталей на рік.