Термопластичне лиття під тиском
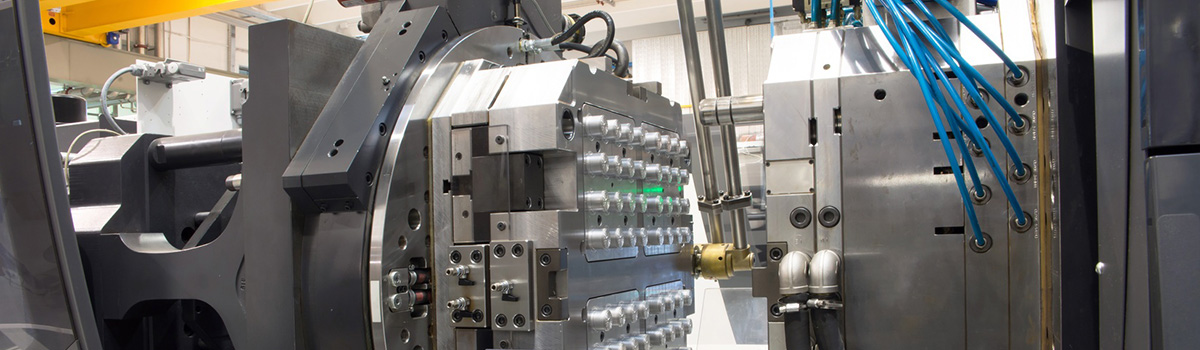
Термопластичне лиття під тиском — це популярний виробничий процес, який використовується для створення різних пластикових деталей для багатьох галузей промисловості. Цей процес передбачає розплавлення пластикових гранул і введення їх у форму для отримання тривимірної форми. Термопластичне лиття під тиском є високоефективним і економічно вигідним для виробництва великих обсягів високоякісних пластикових деталей із жорсткими допусками. У цьому вичерпному посібнику розглядатимуться різні аспекти термопластичного лиття під тиском, зокрема його переваги та недоліки, типи термопластів, що використовуються, процес лиття під тиском, конструктивні міркування та багато іншого.
Історія термопластичного лиття під тиском
Історія термопластичного лиття під тиском охоплює понад століття технологічного прогресу, розробок матеріалів і промислового застосування. Від свого скромного початку як процесу формування целулоїду до сучасної складної технології, лиття під тиском продовжує залишатися життєво важливою технікою виробництва, що стимулює інновації та формує різні галузі.
- Ранні розробки:Джон Уеслі Хаятт і його брат Ісайя розробили першу практичну машину для лиття під тиском, простежуючи походження термопластичного лиття під тиском до кінця 19 століття. У 1872 році вони запатентували пристрій, який використовував поршень для впорскування целулоїду в порожнину форми, створюючи тверді об’єкти. Цей прорив заклав основу для сучасного процесу лиття під тиском.
- Досягнення в матеріалах:На початку 20 століття впровадження нових синтетичних полімерів відкрило нові можливості для лиття під тиском. Бакеліт, фенольна смола, став популярним матеріалом для формування завдяки своїм чудовим електроізоляційним властивостям. Протягом 1930-х і 1940-х років прогрес у хімії полімерів призвів до розробки інших термопластів, таких як полістирол і поліетилен, що ще більше розширило діапазон матеріалів, придатних для лиття під тиском.
- Промислове прийняття: Широке впровадження термопластичного лиття під тиском почалося в 1950-х роках, коли виробники визнали його економічну ефективність і універсальність. Впровадження машин високого тиску дозволило скоротити тривалість циклу та збільшити обсяги виробництва. У результаті з’явився різноманітний вибір продуктів як для особистого, так і для промислового використання. Це були автомобільні комплектуючі, побутова техніка та іграшки.
- Технологічні інновації:Протягом десятиліть технологія лиття під тиском продовжувала розвиватися. У 1960-х роках з’явилися машини з комп’ютерним керуванням, які дозволяли точно контролювати процес формування. Запровадження систем гарячих каналів у 1980-х роках зменшило кількість відходів і підвищило ефективність, усунувши потребу в каналах і литниках. В останні роки автоматизація, робототехніка та прогрес у 3D-друкі зробили ще більшу революцію в індустрії лиття під тиском, уможлививши створення складних конструкцій і скоротивши час виробництва.
- Екологічність і переробка:З огляду на зростаючу стурбованість навколишнім середовищем промисловість лиття під тиском прийняла заходи сталого розвитку. Виробники розробили біологічні та перероблені термопластики, зменшивши залежність від матеріалів на основі викопного палива. Крім того, удосконалені технології переробки дозволили переробляти постспоживчі та постпромислові відходи, мінімізуючи вплив термопластичного лиття під тиском на навколишнє середовище.
- Майбутні перспективи:Майбутнє термопластичного лиття під тиском виглядає багатообіцяючим. Галузь досліджує такі інновації, як мікролиття під тиском для мініатюрних компонентів, методи використання кількох матеріалів і лиття складних деталей, а також інтеграція інтелектуальних технологій для моніторингу та оптимізації процесів. Крім того, дослідники очікують, що прогрес у біорозкладаних матеріалах і виробництві добавок зробить революцію в галузі, зробивши лиття під тиском ще більш стійким і універсальним.
Переваги термопластичного лиття під тиском
Термопластичне лиття під тиском пропонує численні переваги для виробників. Це забезпечує гнучкість дизайну, дозволяючи створювати складні та заплутані конструкції з різними функціями. Процес є економічно ефективним, зменшуючи матеріальні відходи та знижуючи витрати на одиницю продукції. Термопластичне лиття під тиском підтримує кілька матеріалів, забезпечуючи універсальність для різних застосувань.
- Гнучкість дизайну:Термопластичне лиття під тиском дозволяє створювати заплутані та складні конструкції з вирізами, тонкими стінками та різною товщиною, надаючи дизайнерам величезну свободу.
- Ефективність витрат: Процес є високоефективним, скорочує матеріальні відходи та знижує витрати на одиницю. Одночасне формування кількох деталей і швидкі виробничі цикли сприяють економії коштів.
- Універсальність матеріалу: Термопластичне лиття під тиском підтримує широкий спектр матеріалів, що дозволяє виробникам вибирати найбільш прийнятний варіант для кожного застосування, включаючи жорсткі або гнучкі, прозорі або непрозорі та хімічно стійкі матеріали.
- Міцність і довговічність:Формовані під тиском термопласти можуть демонструвати відмінні механічні властивості, такі як висока міцність, міцність і стійкість до ударів. Варіанти армування, як скло або вуглецеві волокна, ще більше покращують ці властивості.
- Постійність і якість:Лиття під тиском забезпечує постійну якість деталей і точність розмірів, забезпечуючи жорсткі допуски та надійні продукти. Процес також забезпечує гладку та рівномірну обробку поверхні, усуваючи потребу в додаткових фінішних операціях.
- Масштабність і масове виробництво:Лиття під тиском масштабується від малих до великих обсягів, що робить його придатним для масового виробництва. Коли виробники створюють прес-форму, вони можуть виготовляти велику кількість ідентичних деталей з мінімальними варіаціями.
- Інтеграція та збірка:Литі під тиском деталі можуть включати кілька компонентів в одну деталь, зменшуючи потребу в додаткових процесах складання. Ця інтеграція підвищує продуктивність продукту, скорочує час складання та знижує витрати.
- Сталий розвиток:Індустрія лиття під тиском все більше приділяє увагу екологічності. Доступність біологічних та перероблених матеріалів дозволяє виробляти екологічно чисті продукти. Ефективне використання матеріалів і можливість вторинної переробки термопластів сприяють екологічнішому виробничому процесу.
Ці переваги зробили його широко поширеним методом виробництва в різних галузях промисловості, забезпечуючи високоякісні, економічно ефективні та екологічно чисті рішення для складних вимог до продукції.
Недоліки термопластичного лиття під тиском
Хоча термопластичне лиття під тиском має численні переваги, є також кілька недоліків. Виробники повинні ретельно оцінити ці фактори та зважити їх проти переваг, щоб визначити придатність термопластичного лиття під тиском для їх конкретних застосувань.
- Високі початкові інвестиції: Налагодження процесу лиття під тиском термопластів потребує значних початкових інвестицій у проектування й виготовлення форм, а також придбання спеціалізованого обладнання. Витрати, пов’язані зі створенням форм і інструментів, можуть бути значними, особливо для складних і складних конструкцій.
- Обмеження дизайну: Хоча термопластичне лиття під тиском забезпечує гнучкість конструкції, існують певні обмеження. Наприклад, досягнення однакової товщини стінки по всій деталі може бути складним завданням, що призводить до різного розподілу матеріалу та потенційних конструктивних недоліків. Крім того, наявність виточок або складної геометрії може вимагати використання додаткових елементів прес-форми або додаткових операцій, збільшуючи витрати та час виробництва.
- Тривалі терміни:Процес проектування та виготовлення прес-форм для лиття під тиском може зайняти багато часу, що призведе до більш тривалого часу розробки продукту. Ітераційний процес проектування, виготовлення прес-форм і тестування можуть значно збільшити загальний графік виробництва, що може не підійти для проектів із стислими термінами.
- Обмеження вибору матеріалу:Хоча термопластичне лиття під тиском підтримує широкий діапазон матеріалів, існують певні обмеження. Деякі матеріали можуть мати особливі вимоги до обробки або обмежену доступність, що впливає на вибір дизайну та вибір матеріалу для конкретного застосування.
- Обмеження розміру частини:Машини для лиття під тиском мають обмеження щодо розміру як фізичного розміру пристрою, так і розміру форм, які вони можуть вмістити. Для виготовлення величезних деталей може знадобитися спеціальне обладнання або альтернативні методи виробництва.
- Вплив на навколишнє середовище:Незважаючи на те, що галузь працює над сталістю, процес лиття під тиском термопластів все ще створює відходи, зокрема брухт і литники. Належна утилізація та переробка цих матеріалів необхідні для мінімізації впливу на навколишнє середовище.
- Складність оптимізації процесу:Досягнення оптимальних параметрів процесу для термопластичного лиття під тиском може бути складним і трудомістким. Виробники повинні ретельно контролювати та оптимізувати температуру, тиск, швидкість охолодження та тривалість циклу, щоб забезпечити стабільну якість деталей і мінімізувати дефекти.
Типи термопластів, що використовуються при лиття під тиском
Це лише кілька прикладів термопластів, які зазвичай використовуються для лиття під тиском. Кожен матеріал має унікальні властивості, що робить його придатним для певних застосувань на основі міцності, гнучкості, хімічної стійкості, прозорості та вартості. Виробники повинні враховувати ці властивості та вимоги при виборі відповідного термопластику для своїх проектів лиття під тиском.
- Поліпропілен (PP):Поліпропілен — це універсальний термопласт, який зазвичай використовується для лиття під тиском. Він забезпечує відмінну хімічну стійкість, низьку щільність і хорошу ударну міцність. PP (поліпропілен) має широке застосування в упаковці, автомобільних компонентах, побутовій техніці та медичних пристроях.
- Поліетилен (PE):Поліетилен є ще одним широко використовуваним термопластом у литві під тиском. Він доступний у різних формах, таких як поліетилен високої щільності (HDPE) і поліетилен низької щільності (LDPE). PE забезпечує хорошу хімічну стійкість, міцність і гнучкість, що робить його придатним для пляшок, контейнерів і труб.
- Полістирол (PS):Полістирол — це універсальний термопласт, відомий своєю прозорістю, жорсткістю та доступністю. Він широко використовується в упаковці, споживчих товарах і одноразових виробах. PS (полістирол) забезпечує швидку обробку та забезпечує хорошу стабільність розмірів, але він може бути крихким і чутливим до розтріскування під дією зовнішнього середовища.
- Акрилонітрилбутадієнстирол (АБС): ABS — це популярний термопластик, відомий своєю чудовою ударостійкістю та довговічністю. Він поєднує в собі властивості акрилонітрилу, бутадієну та стиролу для створення універсального матеріалу, придатного для автомобільних деталей, корпусів електроніки та іграшок.
- Полівінілхлорид (ПВХ): ПВХ – широко використовуваний термопласт, відомий своєю відмінною хімічною стійкістю, довговічністю та низькою вартістю. Він може бути жорстким або гнучким залежно від складу та використовуваних добавок. ПВХ (полівінілхлорид) широко використовується в будівництві, електроізоляції, продуктах охорони здоров'я та упаковці.
- Полікарбонат (PC): Полікарбонат - це прозорий термопластик з надзвичайною удароміцністю та високою термостійкістю. Він знаходить поширене використання в програмах, які вимагають оптичної чіткості, таких як автомобільні компоненти, захисні шоломи та електронні дисплеї.
- Нейлон (поліамід):Нейлон — це міцний і довговічний термопласт, відомий своїми чудовими механічними властивостями та хімічною стійкістю. Його широко використовують у сферах застосування, які вимагають високої міцності, таких як автомобільні деталі, промислові компоненти та споживчі товари.
- Поліетилентерефталат (ПЕТ):ПЕТ — популярний термопластик для виробництва пляшок, контейнерів і пакувальних матеріалів. Він забезпечує хорошу прозорість, хімічну стійкість і бар'єрні властивості, що робить його придатним для харчових продуктів і напоїв.
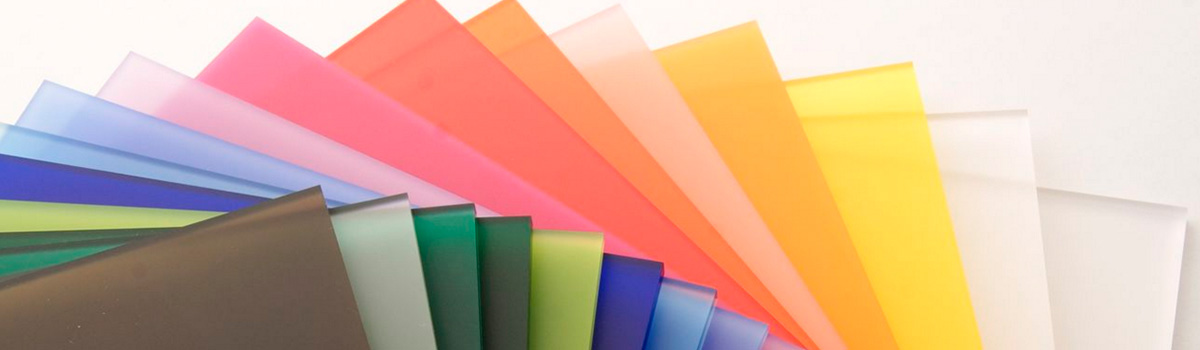
Властивості термопластів, що використовуються при лиття під тиском
Ці властивості термопластів відіграють вирішальну роль у визначенні їх придатності для конкретних застосувань лиття під тиском. Виробники повинні ретельно розглянути ці властивості та вибрати відповідний термопласт на основі бажаних характеристик, умов навколишнього середовища та вимог до вартості.
- Механічні властивості:Термопласти, які використовуються при лиття під тиском, можуть проявляти різні механічні властивості, включаючи міцність на розтяг, ударну стійкість і міцність на вигин. Ці властивості визначають здатність матеріалу витримувати прикладені зусилля та його загальну довговічність у різних застосуваннях.
- Хімічна стійкість:Багато термопластів, які використовуються для лиття під тиском, мають чудову стійкість до хімікатів, розчинників і масел. Ця властивість має вирішальне значення для застосувань, які включають вплив агресивних середовищ або корозійних речовин.
- Термічна стабільність:Термостабільність термопластів означає їхню здатність витримувати високі температури без значної деградації. Деякі термопласти демонструють чудову термостійкість, що дозволяє їм зберігати свої механічні властивості навіть за високих температур.
- Електричні властивості:Термопласти, які використовуються при лиття під тиском, можуть мати специфічні електричні властивості, включаючи електричну ізоляцію, провідність або діелектричну міцність. Ці властивості необхідні для застосування в електротехнічній та електронній промисловості, де матеріали повинні забезпечувати надійні електричні характеристики.
- Прозорість і ясність:Певні термопласти, такі як полікарбонат і ПЕТ, забезпечують чудову прозорість і прозорість, що робить їх придатними для застосування, де потрібні оптичні властивості. Виробники зазвичай використовують ці матеріали в таких продуктах, як прозорі вікна, лінзи та дисплеї.
- Гнучкість і міцність: Гнучкість і міцність є основними властивостями термопластів, які використовуються в сферах застосування, які вимагають стійкості до ударів і довговічності. Деякі термопласти, такі як АБС і нейлон, мають чудову міцність, що дозволяє їм витримувати повторні удари, не руйнуючись.
- Стабільність розмірів:Стабільність розмірів означає здатність термопласту зберігати свою форму та розмір за різних умов, включаючи зміни температури. Матеріали з хорошою стабільністю розмірів забезпечують постійні розміри деталей, мінімізуючи ризик викривлення або викривлення.
- Хімічна сумісність:Хімічна сумісність термопластів означає їх здатність протистояти розкладанню або взаємодії з різними хімічними речовинами, включаючи кислоти, основи та розчинники. Щоб забезпечити оптимальну продуктивність, дуже важливо вибрати термопластик, який може витримувати специфічне хімічне середовище, з яким він зіткнеться в передбачуваному застосуванні.
- Щільність: Термопластики мають різну товщину, що може вплинути на їх вагу та загальні властивості деталей. Матеріали низької щільності, такі як поліетилен, пропонують легкі рішення, тоді як матеріали високої щільності, такі як поліпропілен, забезпечують додаткову міцність і жорсткість.
Процес лиття під тиском: крок за кроком
Процес лиття під тиском відбувається за цими етапами, що дозволяє ефективно та точно виготовляти високоякісні термопластичні деталі. Кожен крок вимагає ретельного контролю та моніторингу, щоб забезпечити постійні розміри деталей, властивості матеріалів і загальну якість.
- Дизайн і виготовлення форми: Першим кроком у процесі лиття під тиском є проектування та виготовлення прес-форми. Виробники повинні створити точну та детальну конструкцію прес-форми для досягнення бажаних характеристик деталей. Потім виробники виготовляють прес-форму за допомогою різних технологій, таких як ЧПК або електроерозійна обробка (EDM).
- Підготовка матеріалу: Наступний крок — підготовка форми, коли вона готова. Термопластичні пелети або гранули вибираються на основі бажаних властивостей матеріалу та розплавляються в бункері. Потім оператори подають матеріал у ствол машини для лиття під тиском, де він проходить плавлення та гомогенізацію.
- Ін'єкція:Під час фази впорскування оператори впорскують розплавлений термопласт у порожнину форми під високим тиском. Інжекційний блок машини проштовхує розплавлений матеріал через сопло у форму. Матеріал заповнює порожнину форми, приймаючи форму потрібної деталі.
- Охолодження та затвердіння:Після заповнення форми оператори дають розплавленому пластику охолонути та затвердіти. Охолодження має вирішальне значення для досягнення стабільності розмірів і правильного формування деталей. Оператори можуть контролювати процес охолодження за допомогою циркуляції охолоджуючої рідини через канали всередині прес-форми або за допомогою охолоджуючих пластин.
- Відкриття та викид форми:Оператори відкривають форму та виймають деталь із порожнини форми, коли пластик затвердіє. Система виштовхування в машині використовує штифти, виштовхувальні пластини або повітряні потоки для видалення області з форми. Після цього форма готова до наступного циклу вприскування.
- Подальша обробка: Після викиду деталь може пройти наступну обробку, таку як обрізка, видалення задирок або обробка поверхні. Ці кроки допомагають видалити надлишки матеріалу, згладити шорсткі краї та покращити остаточний зовнішній вигляд деталі.
- Перевірка якості: Останнім кроком є перевірка якості шприцованих деталей і забезпечення їх відповідності встановленим вимогам. Для перевірки якості та цілісності деталі можна використовувати різні методи контролю якості, включаючи вимірювання розмірів, візуальний огляд і функціональне тестування.
- Переробка та повторне використання матеріалів:Будь-який надлишок або брухт матеріалу, що утворюється під час лиття під тиском, можна переробити та повторно використати. Зменшення використання нових термопластичних матеріалів допомагає мінімізувати відходи та підвищити екологічність.
Обладнання, що використовується для лиття під тиском
Ці компоненти обладнання полегшують процес лиття під тиском, починаючи від плавлення та впорскування термопластичного матеріалу до формування, охолодження та викидання кінцевої частини. Належна експлуатація та технічне обслуговування цих компонентів обладнання мають вирішальне значення для досягнення ефективного високоякісного виробництва лиття під тиском.
- Машина для лиття під тиском:Основне обладнання для лиття під тиском відповідає за плавлення термопластичного матеріалу, впорскування його у форму та контроль процесу.
- Форма: Форма, спеціально розроблена для створення бажаної форми та характеристик пластикової частини, складається з двох половин: порожнини та серцевини. Оператори встановлюють його на затискний вузол машини для лиття під тиском.
- Бункер:Контейнер, який містить термопластичний матеріал у гранульованій або гранульованій формі та подає його в ствол машини для лиття під тиском для плавлення та ін’єкції.
- Стовбур і гвинт: Стовбур, циліндрична камера, розплавляє та гомогенізує термопластичний матеріал, коли гвинт обертається всередині нього, щоб розплавити, змішати та стандартизувати матеріал.
- Системи опалення та охолодження:Машини для лиття під тиском мають нагрівальні елементи, такі як електричні нагрівачі або нагрівачі, що використовують гарячу олію, для підвищення температури стовбура, і системи охолодження, такі як циркуляція води або олії, для охолодження форми та затвердіння пластикової частини.
- Ежекторна система:Видаляє формовану частину з порожнини форми після затвердіння, як правило, використовуючи штифти виштовхувача, пластини або повітряні удари під час відкриття форми.
- Система управління:Відстежує та контролює різні параметри процесу лиття під тиском, дозволяючи операторам встановлювати та регулювати такі параметри, як швидкість ін’єкції, температура, тиск і час охолодження.
Термопластавтомати: типи та характеристика
Кожен тип машини для лиття під тиском має свої характеристики та переваги, що дозволяє виробникам вибрати найбільш відповідний пристрій для своїх конкретних виробничих вимог.
- Гідравлічні машини для лиття під тиском: Ці машини використовують гідравлічні системи для створення необхідного тиску для впорскування розплавленого пластику у форму. Вони відомі своєю високою силою затиску, точним керуванням і універсальністю в роботі з різними термопластами. Гідравлічні машини підходять для великомасштабного виробництва і можуть вміщувати складні форми.
- Електричні машини для лиття під тиском:Електричні машини використовують електричні серводвигуни для роботи машини, включаючи системи впорскування, затиску та ежектора. Вони пропонують точне керування, енергоефективність і швидший час відгуку, ніж гідравлічні машини. Електричні машини ідеально підходять для прецизійного формування, що вимагає високої повторюваності та точності.
- Гібридні машини для лиття під тиском:Гібридні машини поєднують у собі переваги як гідравлічних, так і електричних пристроїв. Вони використовують комбінацію гідравлічних та електричних сервосистем для досягнення високої точності, енергоефективності та економічності. Гібридні машини підходять для широкого спектру застосувань, забезпечуючи баланс між продуктивністю та експлуатаційними витратами.
- Машини для лиття під тиском з двома плитами: Машини з двома плитами мають унікальну конструкцію з двома окремими пластинами для затиску прес-форми. Ця конструкція забезпечує підвищену стабільність, покращену синхронізацію прес-форми та дозволяє формувати більші розміри та вищі сили затиску. Машини з двома плитами підходять для великих і складних деталей, які потребують точного формування.
- Багатокомпонентні машини для лиття під тиском:Виробники розробляють ці машини для виготовлення деталей із різних матеріалів або кольорів за один цикл формування. Вони мають різноманітні інжекційні вузли та прес-форми, що дозволяють одночасно ін’єкувати різні матеріали. Багатокомпонентні машини пропонують гнучкість і ефективність у виготовленні складних деталей із різними характеристиками.
- Машини для мікроліття під тиском:Спеціально розроблені для виробництва невеликих і точних деталей машини для мікроліття під тиском пропонують неймовірно високу точність. Вони можуть виготовляти складні деталі з жорсткими допусками та мінімальними відходами матеріалу. Електроніка, медичне обладнання та мікрооптика зазвичай використовують машини для мікроліття під тиском.
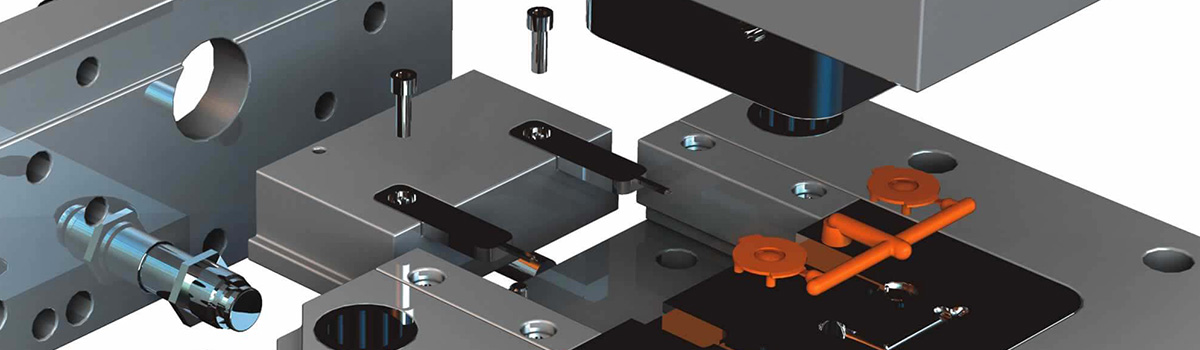
Розгляд конструкції прес-форм для лиття під тиском
Для успішного виробництва лиття під тиском важливо ретельно продумати дизайн форми.
- Дизайн частини:Конструкція прес-форми повинна відповідати конкретним вимогам деталі, включаючи її форму, розміри та функціональні особливості. Виробники повинні належним чином враховувати кути осадки, товщину стінок, підрізи та будь-які необхідні елементи, щоб забезпечити легкість виштовхування та якість деталей.
- Матеріал форми: Вибір матеріалу форми має вирішальне значення для досягнення довговічності, стабільності розмірів і термостійкості. Звичайні матеріали для форм включають сталеві сплави, алюмінієві сплави та інструментальну сталь. Вибір матеріалу залежить від таких факторів, як обсяг виробництва, складність деталей і очікуваний термін служби інструменту.
- Охолоджувальна система:Ефективне охолодження має важливе значення для належного затвердіння деталей і мінімізації часу циклу. Конструкція прес-форми повинна включати канали охолодження або стратегічно розташовані вставки для забезпечення рівномірного охолодження форми. Правильне охолодження зменшує ризик викривлення, усадки та дефектів деталей.
- Вентиляція:Відповідна вентиляція необхідна для виходу повітря та газів під час процесу впорскування. Недостатня вентиляція може призвести до газових пасток, слідів опіків або неповного заповнення деталей. Виробники можуть досягти вентиляції шляхом включення вентиляційних канавок, штифтів або інших механізмів у конструкцію форми.
- Система викиду:Конструкція прес-форми повинна включати ефективну систему викиду для безпечного та ефективного видалення формованої частини з порожнини форми. Система виштовхування може складатися з виштовхувальних штифтів, гільз або інших механізмів, стратегічно розташованих, щоб уникнути перешкод для роботи чи критичних функцій.
- Дизайн воріт:Ворота - це місце, де розплавлений пластик потрапляє в порожнину форми. Конструкція воріт повинна забезпечувати належне заповнення частин, мінімізувати потокові лінії та запобігати передчасному замерзанню матеріалу. Стандартні конструкції воріт включають крайові ворота, тунельні ворота та системи гарячих каналів, залежно від вимог до деталей і властивостей матеріалу.
- Лінія поділу:Конструкція прес-форми повинна визначати відповідну лінію розділення, яка є лінією, де з’єднуються дві половини форми. Правильне розміщення лінії роз’єднання забезпечує мінімальну невідповідність лінії роз’єднання та лінії роз’єднання та полегшує ефективне складання форми.
- Обслуговування прес-форми та зручність обслуговування: Виробники повинні враховувати легкість обслуговування, ремонту та обслуговування прес-форм. Компоненти форми повинні бути легкодоступними для очищення, перевірки та заміни. Включення таких функцій, як швидкозмінні вставки або модульні конструкції прес-форм, може покращити обслуговування прес-форм.
Матеріали прес-форм, які використовуються для лиття під тиском
Співпраця з фахівцями з прес-форм і врахування конкретних потреб формування може допомогти визначити найбільш підходящий матеріал для досягнення оптимальної продуктивності прес-форми та якості деталей.
- Сталеві сплави: Сталеві сплави, такі як інструментальна сталь (наприклад, P20, H13) і нержавіюча сталь, зазвичай використовуються для форм для лиття під тиском через їх чудову довговічність, термостійкість і зносостійкість. Ці матеріали можуть витримувати високі температури та тиск у процесі лиття під тиском і забезпечують хорошу стабільність розмірів для виробництва високоякісних деталей.
- Алюмінієві сплави:Алюмінієві сплави, такі як 7075 і 6061, легкі та мають хорошу теплопровідність, що робить їх придатними для форм, які потребують ефективного охолодження. Виробники часто використовують алюмінієві форми для створення прототипів, малосерійного виробництва або застосувань, де зниження ваги є критичним. Однак алюмінієві форми можуть мати нижчу довговічність порівняно зі сталевими сплавами.
- Мідні сплави:Мідні сплави, такі як берилієва мідь, демонструють високу теплопровідність і хорошу оброблюваність. Вони знаходять застосування у формах, які вимагають чудової теплопередачі для ефективного охолодження. Мідні сплави можуть допомогти скоротити тривалість циклу за рахунок швидкого розсіювання тепла від формованої частини, що призводить до швидшого затвердіння.
- Інструментальні сталі:Інструментальні сталі, включаючи H13, S7 і D2, призначені для високопродуктивних інструментів. Ці сталі пропонують поєднання високої міцності, твердості та зносостійкості. Інструментальні сталі підходять для форм із великими обсягами виробництва, абразивних матеріалів або вимогливих умов формування.
- Нікелеві сплави:Нікелеві сплави, такі як інконель і хастеллой, відомі своєю винятковою стійкістю до корозії, високотемпературною міцністю та термічною стабільністю. Виробники використовують ці сплави у формах, які обробляють корозійні матеріали або вимагають стійкості до екстремальних температур і агресивних середовищ формування.
- Композитні матеріали:Композитні матеріали, такі як армований пластик або композити з металевими вставками, іноді використовуються для спеціального формування. Ці матеріали пропонують баланс таких властивостей, як висока міцність, термостабільність і зменшена вага. Композитні форми можуть бути економічно вигідною альтернативою для конкретних виробничих вимог.
Типи прес-форм
Лиття під тиском — це універсальний і широко використовуваний процес виробництва пластикових деталей.
- Форма з двома пластинами:Форма з двома пластинами є найпоширенішим типом прес-форми. Він складається з двох пластин, пластини з порожниною та основної пластини, які розділені, щоб дозволити викинути формовану частину. Порожниста пластина містить порожнину прес-форми, а серцевина містить серцевину. Виробники використовують двопластинчасті прес-форми для виготовлення широкого асортименту деталей завдяки їх відносно простій конструкції.
- Форма з трьох пластин:Прес-форма з трьома пластинами є вдосконаленою версією форми з двома пластинами. Він включає додаткову пластину, бігунок або литникову пластину. Направляюча пластина створює окремий канал для литника, напрямних і воріт, що полегшує видалення формованої частини. Виробники зазвичай використовують форми з трьома пластинами для деталей зі складними системами литників або коли бажано уникати залишків воріт на деталі.
- Прес-форма для гарячого потоку:Система канавок і затворів нагрівається в формах для гарячих канавок, усуваючи потребу в твердінні та повторному плавленні матеріалу під час кожного циклу. Система гарячого каналу складається з нагрітих колекторів і форсунок, які підтримують розплавлений стан пластику. Гарячеканальні прес-форми пропонують такі переваги, як скорочений час циклу, менші відходи матеріалу та покращена якість деталей завдяки мінімізації залишків воріт.
- Холодна прес-форма: Прес-форми для холодних канавок мають традиційну систему канавок і затворів, де розплавлений пластик протікає через холодні канавки, які твердіють з кожним циклом. Згодом оператори видаляють затверділі бігуни, що призводить до утворення відходів. Виробники зазвичай використовують складні ливарні форми для невеликих обсягів виробництва або коли витрати на матеріали менш критичні через їхню просту конструкцію.
- Вставити форму:Форми для вставок включають металеві або пластикові вставки в порожнину форми під час лиття під тиском. Вставки можна попередньо помістити у форму або вставити за допомогою автоматизованих процесів. Ця форма дозволяє інтегрувати додаткові компоненти або посилюючі елементи в формовану частину, підвищуючи її функціональність або міцність.
- Переформування: Верхнє формування передбачає формування одного матеріалу поверх іншого, як правило, з’єднання жорсткої пластикової підкладки з більш м’яким еластомером або термопластом. Цей процес дозволяє створювати деталі з кількох матеріалів або текстур в одній формі, забезпечуючи покращене зчеплення, амортизацію та естетичні характеристики.
Фактори, що впливають на витрати на лиття під тиском
Врахування цих факторів може допомогти виробникам оцінити та оптимізувати вартість лиття під тиском, забезпечуючи баланс між якістю, ефективністю та економічною ефективністю для своїх конкретних виробничих вимог.
- Складність частини:Складність конструкції деталі відіграє значну роль у визначенні вартості лиття під тиском. Складна геометрія, вирізи, тонкі стінки або складні елементи можуть вимагати додаткового інструменту, спеціальних форм або довших циклів, що збільшує загальну вартість виробництва.
- Вибір матеріалу:Вибір термопластичного матеріалу впливає на вартість лиття під тиском. Різні матеріали мають різні ціни за кілограм, і такі фактори, як доступність матеріалу, властивості та вимоги до обробки, можуть впливати на загальну вартість матеріалу.
- Інструменти та дизайн форми: Початкові витрати на інструменти та дизайн прес-форми є значними у витратах на лиття під тиском. Такі фактори, як складність прес-форми, кількість порожнин, розмір форми та матеріал форми, сприяють витратам на інструменти та виготовлення прес-форм. Більш складні прес-форми або прес-форми, які потребують розширених функцій, можуть збільшити початкові інвестиції.
- Обсяг виробництва: Обсяг виробництва безпосередньо впливає на вартість деталі при лиття під тиском. Вищі книги часто призводять до економії на масштабі, знижуючи вартість частини. І навпаки, малосерійне виробництво може призвести до більших витрат через налаштування, інструменти та відходи матеріалів.
- Час циклу: Тривалість циклу, яка включає фази охолодження та викиду, впливає на виробничу потужність і загальну вартість. Довший час циклу призводить до зменшення обсягу виробництва та потенційно вищих цін. Оптимізація конструкції форми, системи охолодження та параметрів процесу може мінімізувати час циклу та підвищити ефективність.
- Вимоги до якості:Суворі вимоги до якості або спеціальні сертифікати можуть вплинути на вартість лиття під тиском. Дотримання точних допусків, вимог до обробки поверхні або додаткові випробування можуть вимагати інших ресурсів, процесів або перевірок, що збільшує загальну вартість.
- Другорядні операції:Якщо формовані деталі вимагають таких операцій після обробки, як складання, фарбування або додаткові етапи обробки, ці операції можуть збільшити загальну вартість лиття під тиском.
- Постачальник і місцезнаходження:Вибір постачальника для лиття під тиском і його розташування можуть вплинути на витрати. Витрати на оплату праці, накладні витрати, витрати на логістику та транспортування залежать від місця розташування постачальника, що впливає на загальну вартість виробництва.
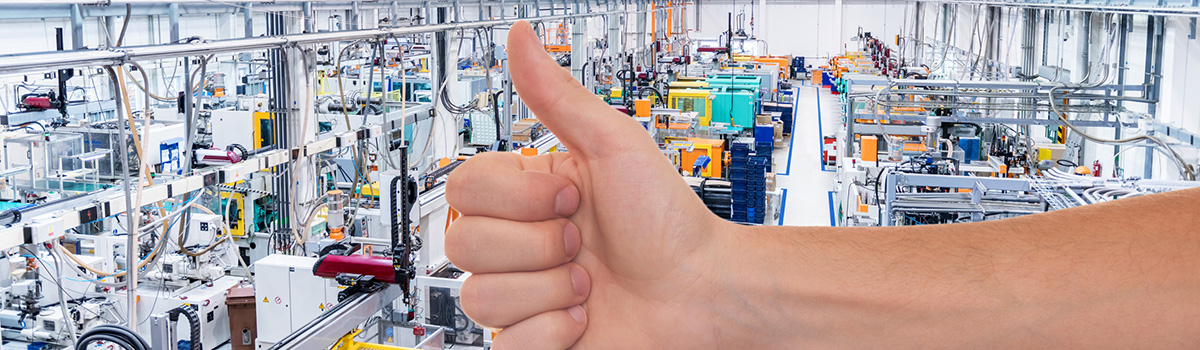
Контроль якості лиття під тиском
Впровадження надійних заходів контролю якості протягом усього процесу лиття під тиском допомагає виявляти та усувати потенційні дефекти, відхилення або невідповідності, забезпечуючи виробництво високоякісних деталей, які відповідають специфікаціям і вимогам замовника.
- Моніторинг процесу: Постійний моніторинг ключових параметрів процесу, таких як температура розплаву, тиск впорскування, час охолодження та тривалість циклу, забезпечує послідовність і повторюваність у виробництві деталей. Моніторинг у режимі реального часу та автоматизовані системи можуть виявляти варіації або відхилення від заданих параметрів, дозволяючи своєчасно коригувати та підтримувати стабільність процесу.
- Перевірка та вимірювання:Регулярний огляд і вимірювання формованих деталей є важливими для перевірки точності розмірів, якості деталей і дотримання специфікацій. Наші послуги охоплюють ряд методів контролю якості, таких як вимірювання розмірів, аналіз якості поверхні, проведення візуальних перевірок і виконання функціональних тестів. Для точної оцінки використовуються різні методи контролю, такі як координатно-вимірювальні машини (CMM) і оптичні та візуальні системи контролю.
- Статистичний контроль процесу (SPC): SPC передбачає збір і аналіз даних процесу для моніторингу та контролю якості лиття під тиском. Статистичні методи, такі як контрольні діаграми та аналіз можливостей процесу, допомагають визначити тенденції, виявити варіації процесу та гарантувати, що процес залишається в межах визначених контрольних меж. SPC дозволяє проактивно виявляти проблеми та сприяє оптимізації процесів.
- Випробування матеріалу: Перевірка сировини, такої як термопласти, добавки та барвники, гарантує її якість і придатність для лиття під тиском. Випробування матеріалу може включати аналіз індексу плинності розплаву (MFI), механічні властивості, термічні характеристики та склад матеріалу. Перевірка якості матеріалу допомагає запобігти дефектам і невідповідностям у формованих частинах.
- Технічне обслуговування та перевірка інструментів:Належне технічне обслуговування та регулярний огляд форм для лиття під тиском мають вирішальне значення для забезпечення якості лиття під тиском. Регулярне очищення, змащення та оцінка компонентів прес-форми допомагають запобігти зношенню, пошкодженню або деградації, які можуть вплинути на якість деталей. Своєчасний ремонт або заміна зношених або пошкоджених компонентів форми має важливе значення для підтримки сталої продуктивності формування.
- Документація та відстеження:Ведення повної документації та записів про відстеження є важливим для контролю якості лиття під тиском. Важливо записувати параметри процесу, результати перевірки, інформацію про матеріал і будь-які зміни або коригування, внесені під час виробництва. Належна документація забезпечує відстеження деталей, полегшує аналіз першопричини та забезпечує стабільність якості.
- Навчання та розвиток навичок: Забезпечення відповідних програм навчання та розвитку навичок для операторів, техніків і персоналу контролю якості покращує їхнє розуміння процесів лиття під тиском, вимог до якості та методів перевірки. Добре навчений персонал може виявляти дефекти, усувати проблеми та ефективно впроваджувати коригувальні заходи, забезпечуючи високу якість виробництва.
Поширені дефекти лиття під тиском і як їх уникнути
Регулярний огляд, моніторинг і аналіз процесів лиття під тиском, а також належне технічне обслуговування та налаштування обладнання та форм можуть допомогти виявити та усунути ці поширені дефекти.
- Знаки раковини:Сліди раковини - це западини або поглиблення на поверхні формованої деталі, викликані нерівномірним охолодженням або усадкою. Слід враховувати правильне розташування та конструкцію воріт, оптимальну конструкцію системи охолодження та рівномірний розподіл товщини стінок, щоб уникнути слідів раковини. Збільшення тиску впорскування або регулювання часу охолодження також може допомогти мінімізувати сліди раковини.
- Деформація:Викривлення відноситься до деформації або вигину формованої деталі після виштовхування через нерівномірне охолодження або залишкові напруги. Підтримання однакової товщини стінок, використання належних каналів охолодження та забезпечення збалансованого заповнення й упакування форми мають вирішальне значення для запобігання викривлення. Оптимізація температури прес-форми, використання відповідних кутів тяги та контроль температури матеріалу та швидкості впорскування можуть допомогти мінімізувати короблення.
- Спалах:Спалах виникає, коли надлишок матеріалу стікає в лінію розділення форми, що призводить до тонких, небажаних виступів або додаткового матеріалу на кінцевій частині. Можна ефективно запобігти спалаху, забезпечивши належну конструкцію прес-форми, включаючи застосування належної сили затиску, точне вирівнювання та використання відповідних методів вентиляції. Оптимізація параметрів процесу, таких як тиск упорскування, температура та тривалість циклу, зменшує спалах.
- Короткий знімок:Швидкий удар відбувається, коли введений матеріал не заповнює порожнину форми, що призводить до неповної деталі. Правильний вибір матеріалу, забезпечення відповідної температури та в’язкості розплаву, а також підтримка належного тиску та часу впорскування є важливими, щоб уникнути коротких фотографій. Крім того, перевірка конструкції прес-форми на достатній розмір бігуна та воріт і належну вентиляцію може допомогти запобігти швидким пострілам.
- Лінії зварювання:Лінії зварювання виникають, коли два або більше фронтів потоку розплавленого матеріалу зустрічаються та застигають, що призводить до появи видимої лінії або сліду на поверхні деталі. Хороша конструкція затвора та робочої лінії, оптимальна температура розплаву, швидкість впорскування, а також регулювання потоку матеріалу та геометрії деталей можуть мінімізувати лінії зварювання. Аналіз потоку прес-форми та оптимізація розміщення воріт також можуть допомогти запобігти або пом’якшити лінії зварювання.
- Сліди опіків:Випалені плями — це зміни кольору або чорні плями на поверхні формованої деталі, спричинені надмірним нагріванням або перегріванням матеріалу. Уникнення екстремальних температур плавлення, використання відповідних каналів охолодження та оптимізація тривалості циклу можуть допомогти запобігти вигорянню. Адекватна вентиляція, належна конструкція воріт і контроль температури форми також сприяють мінімізації слідів опіків.
Операції після формування: оздоблення та складання
Після лиття під тиском багато формованих деталей можуть вимагати додаткової обробки та складання для отримання бажаного кінцевого продукту. Ці операції після формування можуть включати:
- Обрізка:Видаліть будь-який зайвий матеріал або відшарування навколо формованої частини за допомогою інструментів для обрізання або різання.
- Обробка поверхонь:Покращення зовнішнього вигляду або функціональності поверхні деталей за допомогою різних технік, таких як фарбування, покриття або текстурування.
- монтаж:З’єднання кількох формованих деталей або додавання таких компонентів, як застібки, вставки чи етикетки, щоб завершити кінцевий продукт.
- Тестування:Перевірка якості та функціональності деталей за допомогою різних методів тестування, таких як аналіз розмірів, тестування властивостей матеріалів або тестування продуктивності.
- Упаковка та доставка:Належне пакування та маркування готового продукту для відправлення клієнтам або кінцевим споживачам.
Вибір операцій після формування залежить від конкретного застосування та бажаних характеристик кінцевого продукту. Тісна співпраця між фахівцями з лиття під тиском, фахівцями з оздоблення та складання та замовником має вирішальне значення для досягнення бажаної абсолютної якості та функціональності продукту. Правильне планування та інтеграція операцій після формування у виробничий процес може допомогти забезпечити ефективне виробництво та своєчасну доставку високоякісної продукції.
Лиття під тиском проти інших процесів виробництва пластику
Кожен процес виробництва пластику має переваги та обмеження, що робить його придатним для різних застосувань.
- Лиття під тиском: Лиття під тиском — це дуже універсальний і широко використовуваний виробничий процес для виготовлення пластикових деталей. Він пропонує такі переваги, як висока ефективність виробництва, точне повторення деталей і можливість створювати складні геометрії. Лиття під тиском підходить для виробництва великих обсягів і дозволяє використовувати широкий спектр термопластичних матеріалів. Він забезпечує чудову точність розмірів і обробку поверхні, що робить його ідеальним для різних галузей промисловості, таких як автомобільна промисловість, споживчі товари та медичне обладнання.
- Видувне формування: Видувне формування — це процес, який використовується переважно для виробництва порожнистих пластикових деталей, таких як пляшки, контейнери та автомобільні компоненти. Він передбачає розплавлення пластику та надування його в порожнину форми, створюючи бажану форму. Видувне формування підходить для виробництва великих обсягів і може виготовляти великі, легкі деталі з однаковою товщиною стінок. Однак він обмежений з точки зору складності деталей і вибору матеріалів порівняно з литтям під тиском.
- Термоформування:Термоформування - це процес, який використовується для виготовлення пластикових деталей шляхом нагрівання термопластичного листа та формування його за допомогою форм або вакуумного формування. Він широко використовується в упаковці, одноразових продуктах і великих продуктах, таких як лотки та кришки. Термоформування забезпечує економічно ефективне виробництво великих деталей і дозволяє швидко створювати прототипи. Однак він має обмеження щодо складності деталей, вибору матеріалу та точності розмірів порівняно з литтям під тиском.
- Екструзія:Екструзія - це безперервний процес виробництва пластикових профілів, листів, труб і плівок. Це включає в себе розплавлення пластикової смоли та продавлювання її через матрицю для створення потрібної форми. Екструзія підходить для виготовлення довгих безперервних відрізків пластикових виробів із постійним поперечним перерізом. Хоча екструзія пропонує високі показники виробництва та економічну ефективність, вона обмежена з точки зору складної геометрії деталей і точного контролю розмірів порівняно з литтям під тиском.
- Компресійне формування:Компресійне формування передбачає розміщення попередньо відміряної кількості термореактивного матеріалу в нагрітій порожнині форми та стиснення його під високим тиском до затвердіння. Він широко використовується у виробництві деталей з високою міцністю та стабільністю розмірів, таких як автомобільні компоненти та електрична ізоляція. Компресійне формування забезпечує хорошу консистенцію деталей, високу ефективність виробництва та можливість використання широкого діапазону матеріалів. Однак він обмежений з точки зору складності деталей і тривалості циклу порівняно з литтям під тиском.
Застосування термопластичного лиття під тиском
Різні галузі промисловості широко використовують термопластичне лиття під тиском завдяки його універсальності, ефективності та економічній ефективності. Деякі з застосувань термопластичного лиття під тиском включають:
- Автомобільна промисловість: Автомобільна промисловість широко використовує термопластичне лиття під тиском для виготовлення різних компонентів, включаючи внутрішнє та зовнішнє оздоблення, панелі приладів, дверні панелі, бампери та електричні роз’єми. Цей процес забезпечує точне копіювання деталей, складну геометрію та легкі матеріали, покращуючи паливну ефективність і гнучкість конструкції.
- Споживчі товари:Лиття під тиском знаходить широке застосування у виробництві споживчих товарів, таких як побутова техніка, електронні пристрої, пакувальні контейнери та іграшки. Цей процес дозволяє масово виробляти довговічні високоякісні вироби з незмінними розмірами та обробкою поверхні. Це також дозволяє налаштувати параметри та швидкі ітерації продукту.
- Медичні вироби:Лиття під тиском відіграє вирішальну роль у медичній промисловості для виробництва широкого спектру пристроїв, включаючи шприци, хірургічні інструменти, імплантовані компоненти та системи доставки ліків. Процес забезпечує виробництво стерильних, точних і біосумісних деталей, які відповідають суворим нормативним вимогам сектора охорони здоров’я.
- Електроніка та електротехнічна промисловість:Електронна промисловість використовує лиття під тиском для виготовлення електричних роз’ємів, корпусів, перемикачів та інших компонентів. Процес забезпечує високу точність розмірів, відмінну обробку поверхні та можливість включати такі функції, як формування вставок і накладання, що дозволяє ефективно виготовляти складні електронні вузли.
- Пакувальна промисловість:Різноманітні галузі промисловості, включаючи виробництво харчових продуктів і напоїв, фармацевтику та засоби особистої гігієни, зазвичай використовують лиття під тиском для виробництва пластикової упаковки, ковпачків, закупорювальних засобів і пляшок. Цей процес дозволяє створювати легкі, міцні та естетично привабливі пакувальні рішення з ефективними виробничими циклами.
- Аерокосмічна промисловість:В аерокосмічній галузі використовується лиття під тиском для виготовлення легких і високоефективних компонентів, таких як повітропроводи, кронштейни, внутрішні панелі та конструктивні деталі. Процес дозволяє використовувати передові матеріали та складну геометрію деталей, сприяючи зменшенню ваги та покращенню паливної ефективності.
Вплив термопластичного лиття під тиском на навколишнє середовище
Лиття термопластів під тиском є популярним процесом виробництва завдяки численним перевагам, але також важливо враховувати його вплив на навколишнє середовище. Ось кілька моментів, які слід враховувати:
- Матеріальна ефективність:Термопластичне лиття під тиском сприяє ефективності матеріалу за рахунок мінімізації відходів. У процесі використовується точний контроль над кількістю матеріалу, що вводиться у форму, зменшуючи потребу в надлишку матеріалу. Виробники також можуть застосовувати методи повторного шліфування та переробки для повторного використання брухту або бракованих деталей, що ще більше зменшує відходи.
- Споживання енергії:Виробники проектують машини для лиття під тиском, щоб бути енергоефективними, а сучасні моделі включають передові технології, такі як серводвигуни та приводи зі змінною швидкістю. Ці функції оптимізують споживання енергії шляхом зменшення споживання електроенергії під час формування, що призводить до зниження потреб у енергії та зменшення впливу на навколишнє середовище.
- Поводження з відходами:Зводячи до мінімуму матеріальні відходи, виробники повинні впроваджувати належні практики поводження з відходами, щоб поводитися із залишками матеріалів, литниками або напрямними. Виробники можуть запроваджувати програми переробки для збору та повторного використання пластикових відходів, утворених під час лиття під тиском, таким чином зменшуючи кількість відходів, які відправляються на звалища.
- Скорочення викидів: Лиття під тиском термопластів, як правило, генерує менші викиди, ніж інші виробничі процеси. Виробники можуть зменшити викиди, використовуючи екологічно чисті матеріали, впроваджуючи енергоефективне обладнання та передові системи вихлопу та фільтрації для уловлювання будь-яких викидів.
- Екологічний вибір матеріалів:Вибір термопластичних матеріалів може значно вплинути на екологічність лиття під тиском. Вибір біорозкладаного або біологічного пластику, а також перероблених або перероблених матеріалів може допомогти зменшити загальний екологічний слід процесу.
Розгляд життєвого циклу: Розгляд усього життєвого циклу формованого продукту має важливе значення для оцінки його впливу на навколишнє середовище. На етапах проектування та вибору матеріалу виробники повинні враховувати такі фактори, як довговічність деталі, можливість її повторної переробки та можливість утилізації або повторного використання в кінці терміну служби.
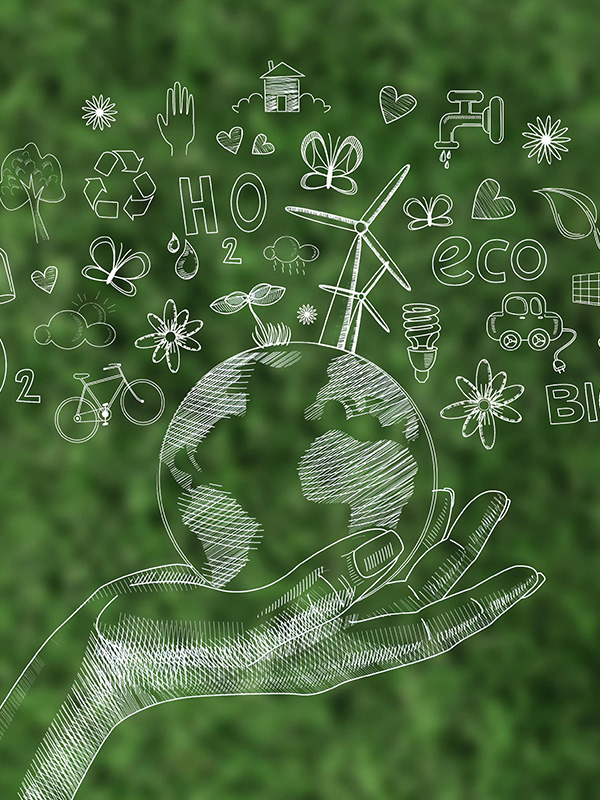
Майбутнє термопластичного лиття під тиском
Майбутнє термопластичного лиття під тиском виглядає багатообіцяючим із постійним прогресом технологій і зростанням попиту на високоякісні, точні деталі в різних галузях промисловості. Деякі з ключових подій, які очікуються в найближчі роки, включають:
- Збільшення використання автоматизації та роботизації для підвищення ефективності та зниження витрат.
- Зусилля зосереджені на розробці нових матеріалів і процесів для покращення продуктивності деталей і забезпечення нових застосувань.
- Це зростаюче впровадження стійких практик, таких як використання перероблених матеріалів та оптимізація споживання енергії, щоб зменшити вплив лиття під тиском на навколишнє середовище.
- Краща інтеграція цифрових технологій, таких як 3D-друк і програмне забезпечення для моделювання, для вдосконалення процесів проектування та виробництва.
Глобальний ринок лиття під тиском розширюється, особливо в країнах з економікою, що розвивається, завдяки зростаючому попиту на пластикові вироби в різних галузях.
Вибір правильного партнера з лиття під тиском
Вибір правильного партнера з лиття під тиском має вирішальне значення для успіху вашого проекту. Знайдіть час, щоб оцінити кілька варіантів, здійснити візити на сайт і взяти участь у ґрунтовних обговореннях, щоб забезпечити сумісне та довгострокове партнерство.
- Досвід та досвід:Шукайте партнера з лиття під тиском із великими знаннями та досвідом у галузі. Вони повинні мати підтверджений досвід надання високоякісних продуктів і рішень клієнтам у різних секторах. Розглянемо їхнє розуміння різних матеріалів, конструкцій форм і виробничих процесів.
- Виробничі можливості: Оцініть виробничі можливості партнера з лиття під тиском. Переконайтеся, що вони мають добре обладнане приміщення з сучасним обладнанням і технологіями для виконання вимог вашого проекту. Враховуйте їхню виробничу потужність, здатність обробляти деталі різних розмірів і складності, а також здатність задовольнити бажані обсяги виробництва та терміни.
- Гарантія якості:Якість має першорядне значення для лиття під тиском. Оцініть системи контролю якості та сертифікати потенційного партнера. Шукайте партнерів, які дотримуються суворих стандартів якості, мають надійні процеси перевірки та проводять комплексне тестування, щоб гарантувати якість і послідовність деталей.
- Проектно-технічна підтримка:Надійний партнер з лиття під тиском повинен запропонувати конструкторську та інженерну підтримку для оптимізації конструкції вашої деталі для технологічності. У них повинні бути кваліфіковані інженери, які можуть надати цінний внесок у вибір матеріалу, дизайн форми та оптимізацію процесу для підвищення якості та ефективності деталей.
- Конкурентоспроможність за вартістю:Хоча вартість не повинна бути єдиним визначальним фактором, важливо оцінити ціну та конкурентоспроможність партнера з лиття під тиском. Запитуйте детальні пропозиції та враховуйте витрати на інструменти, матеріали, робочу силу та будь-які додаткові послуги, які вони надають.
- Спілкування та співпраця:Ефективне спілкування та співпраця необхідні для успішного партнерства. Переконайтеся, що партнер із лиття під тиском має хороші канали зв’язку, відповідає на ваші запити та може надавати регулярні оновлення проекту. Спільний підхід допоможе забезпечити виконання ваших вимог і оперативне вирішення будь-яких проблем.
- Рекомендації та відгуки клієнтів:Шукайте рекомендації клієнтів або читайте огляди/відгуки, щоб отримати уявлення про досвід інших клієнтів із партнером із лиття під тиском. Отримання цієї інформації може допомогти визначити їхню надійність, оперативність і загальний рівень задоволеності клієнтів.
Висновок
Лиття під тиском із термопластів — це універсальний і економічно ефективний метод виготовлення пластикових деталей у великих кількостях. Його здатність виробляти складні форми з високою точністю та послідовністю стала популярним вибором для різних галузей промисловості, включаючи автомобільну, медичну, електроніку та споживчі товари. Розуміючи різні аспекти термопластичного лиття під тиском, включаючи його переваги, недоліки та конструктивні міркування, ви можете приймати обґрунтовані рішення щодо вибору правильного партнера з лиття під тиском для потреб вашого бізнесу.