Geval in Indië
DJmolidng se insetvorm in spuitgietdiens vir Indiese maatskappye
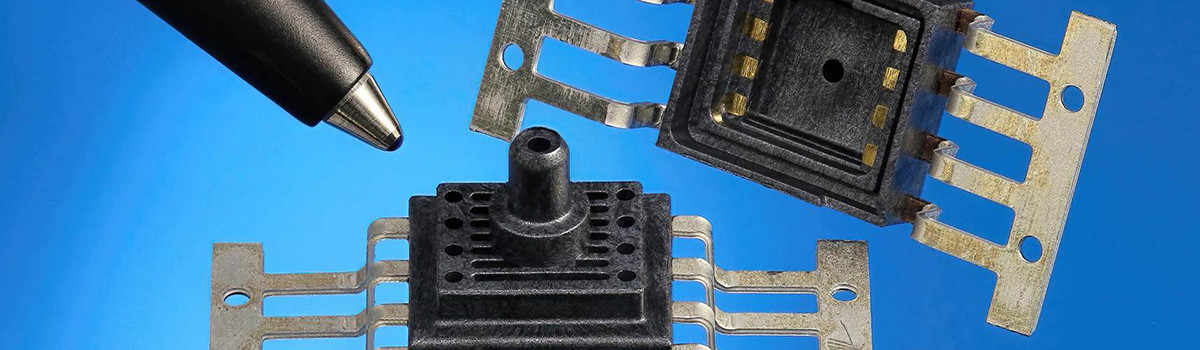
Invoegvorm is oor die algemeen 'n soort vorm wat neute, metaalonderdele of harde plastiekonderdele maak wat in holtes vasgemaak word vir spuitgiet.
DJmolding bied die inset-mlod-spuitgietdiens vir die Indiese mark aan, en ons vervaardig baie plastiekonderdele van insetselvormwerk vir verskillende industrieë, veral vir vervaardigers van huishoudelike toestelle. Sommige Indiese huishoudelike toestelle se vervaardigers koop die insetvorm se plastiekonderdele vir 'n lang tyd van DJmolding. Ons het 'n baie goeie vennootskap met hierdie Indië se maatskappye.
Voeg neute spuitgiet in: neutemateriaal kan vlekvrye staal, koper, brons en staal wees, gewoonlik word kopermoere algemeen gebruik. Koper is maklik om te kartel, wat help om neute en plastiek beter te verbind. Die toleransie van moer binneborings moet binne 0.02mm beheer word, anders veroorsaak maklik flits as die toleransie verder as 0.02mm. In vormpassing, moet moere in insetpenne bymekaargemaak word vir toetsing. As dit styf tussen moere en penne pas, sal dit moeilik wees om die onderdeel uit te stoot en uitwerpmerke of vasbytprobleme veroorsaak. As dit los pas, sal dit flits veroorsaak.
Voeg metaalonderdele spuitgietwerk in:
Metaalonderdele kan vlekvrye staal, aluminium, koper, staal … ens wees. Die toleransie van metaalonderdele moet binne 0.02 mm beheer word, anders is dit moeilik om materiaal te verseël en maklik om flits te hê. Die oppervlakte van metaalonderdele kan nie te groot ontwerp word nie.
As die vuloppervlakte vir metaalonderdele te groot is, sal dit baie moeilik wees om volle inspuiting te bewerkstellig aangesien groot temperatuurverskil tussen metaalonderdele. Posisies van metaalonderdele word gewoonlik in holte ontwerp aangesien holte nie beweeg nie, wat help om flitse te voorkom as gevolg van metaalonderdele wat in beweging verloor (in ernstige gevalle kan dit vorm beskadig). In spesifieke gevalle kan posisies van metaalonderdele slegs in die kern of syoppervlak van die produk ontwerp word.
Voeg harde plastiek spuitgietwerk in:
Kies gewoonlik harde plastiek met hoë smeltpunte, soos PEEK, PA66+30GF, PP+30GF, PA12+30GF, PPS….ens. Verdraagsaamheid vir hierdie harde plastiek moet akkuraat wees. Defekte soos krimping, duik en vervorming kan nie in die seëlarea bestaan nie. In vormpassing moet die harde plastiek in die vorm geplaas word vir toetsing, en 0.05-0.1 mm gelaat word om vooraf te druk om die seëlarea om beter verseëling te verkry.
Die harde plastiekdeel moet nie te groot oppervlakte ontwerp word nie, wat temperatuurverskil sal veroorsaak en dit moeilik maak om materiaal in inspuiting te vul. Maak gewoonlik die harde plastiekdeel in die kant van die holte vas, want holte beweeg nie, om flitse of selfs skadelike vorm in die vorm te vermy. In spesifieke gevalle kan posisies van metaalonderdele slegs in die kern of syoppervlak van die produk ontwerp word.
Ontwerp sleutelpunte
1. Ontwerp krimping vir produkte met neute-insetsels, terwyl geen ontwerp-krimping nodig is vir produkte met metaalonderdele en harde plastiek-insetsels nie. Vir areas wat streng toleransie benodig, verander die produkte se grootte toleransie na mediaan.
2. Gebruik gewoonlik vormbasis met standaard penpunthek in vormontwerp, en in sekondêre inspuiting, plaas die invoegonderdele so veel as moontlik in die holte. Op die voorwaarde dat die insetsels in die holte vasgemaak word, oorweeg hoe om 'n deel in die kern te maak na spuitgiet, op hierdie manier kan 'n deel uitgegooi word. Voeg gewoonlik elastiese blokke in holte en elastiese gom by om deel in die kern te laat bly. Die afstand tussen elastiese blokke en gom kan nie te groot wees nie, anders sal die elastiese krag harde plastiek- of metaaldele vervorming veroorsaak. Die afstand word gewoonlik binne 2 mm ontwerp, en verhoog die hoeveelheid elastiese blokke en elastiese gom gepas wanneer die metaal- of harde plastiek-insetsels relatief groot oppervlakte het.
3. Die dikte van die materiaal is die beste binne 1.3-1.8 mm (ongeveer 1.5 mm is die beste), indien nie, moet u die produktekeninge nagaan en voorstel dat klante dit verander. As materiaaldikte dunner as 1.3 mm is, is dit moeilik om materiaal te vul, terwyl materiaaldikte dikker as 1.8 mm is, is dit maklik om in produksie te krimp.
4.Gating is baie belangrik in vorm. Die balans van materiaalvul vir hekpunt moet ten volle oorweeg word. Wanneer materiaal na die area loop waar metaal- of harde plastiekonderdele vasgemaak is, sal die spoed van materiaalvul en druk laer wees omdat die insetselweerstand en temperatuurverskil.
5.Vir vormuitwerpstelsel moet die balans van uitwerping in ag geneem word of die vervorming sal plaasvind na uitwerping. Vir dele wat nie in balans uitgewerp kan word nie, moet dit oorweeg om ineen te stort om die balansprobleem in struktuurontwerp te verbeter.
6.Om die kwalifikasie van onderdele se voorkoms te verseker nadat dit in spuitgietwerk uitgewerp is, moet die uitwerptoestel harde plastiekklont wees wat met ABS of PMMA ingesit is. As die oorvorm gly verseëling het, ontwerp skyfies in holte soveel as moontlik, want skyfies in holte vergemaklik vormpassing.
7. Om die sterkte van verseëling SA (naattoelating) te verseker, vir produk gemaak van twee keer spuitgietwerk, moet die breedte van verseëling SA minstens 0.8 mm wees. Vir die sekondêre inspuitmateriaal is harde plastiek, moet die breedte van verseëling SA ten minste 1.0mm wees, anders moet die kliënt voorstel om die produk te verander.
8.In vormontwerp moet ons die spuitgietmasjiene in ag neem vir produksie om te sien watter tipe masjien dit aanneem, vertikaal of horisontaal. Daar word voorgestel dat jy nie te veel holtes ontwerp nie, veral vir vorm met koue lopers, aangesien te veel holtes die hardloper langer maak, materiaal mors en ook skadelik is om hoë-doeltreffende inspuiting te bereik. Om by spuitgietmasjien te pas, moet ons oorweeg of dit kompak en redelik is vir die produkreëlings. Die produkte moet reggemaak word om te verseker dat die produkte in dieselfde situasie is elke keer wanneer dit in die vorm geplaas word. Nog 'n manier is die ontwerpreaksiestelsel om te waarsku as die onderdeel nie op die regte plek is voordat die vorm toemaak nie, wat help om die vorm te stop. Op hierdie manier is onderdele in dieselfde situasie in vorm, wat die gekwalifiseerde tariewe en produksiedoeltreffendheid in spuitgiet verhoog.
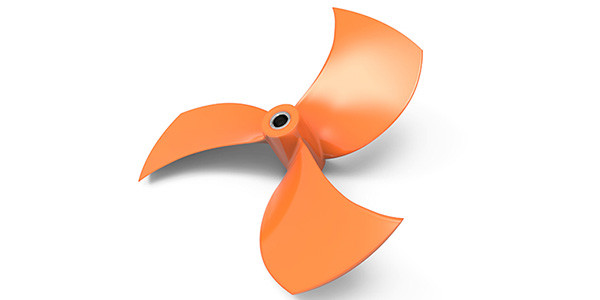
9. 'n Staalsteun moet ontwerp word aangesien die vorminspuitarea groot druk dra tydens inspuiting (moet 5-10 mm groter wees as dié van deel in vorm en grootte). Moet nie gapings tussen dele rondom oorvorm area laat nie, anders sal die deel uit vorm wees na die sekondêre inspuiting. Vir onderdele sonder SA (naattoelating) sal baie meer aandag aan hierdie aspek moet gee.
10.Airrit is maklik Air trip gebeur maklik in spuitgiet, so moet ten volle oorweeg ventilasie in vorm ontwerp. In alle blinde hoeke en posisies vir langafstand waterlyn, moet ventilasiegate op harde plastiek deel ontwerp aangesien dit baie moeiliker is om materiaal in blinde hoeke te vul.
11.Om te verseker dat die ingespuite materiaal en gekwalifiseerde stukrag ten volle gevul is, is een manier om 'n ondersnywerk by die hoeke van deel te ontwerp om die gomresultaat te verbeter en dan om dele stywer te laat heg.
12. In die seëlarea en skeilynarea moet ons nie uit holte en kern verwyder word nie, want klemlyne in vorm en ontvorming van die vorm sal flitse in vormpassing veroorsaak. Probeer ontvorm deur LISS-OFF.
Hekpunt tipes insetvorm
Hekpunt vir insetvorm kan ontwerp word om warmspuitklephek, warmspuitpenhek, penpunthek, subhek, randhek … ens.
Warmtoevoerklephek: goeie likiditeit, posisieseleksie buigsaam, klein hekpunt. Pas vir massiewe produksie en vir produkte met dik wanddikte. Kan help om materiaal te bespaar, geen materiaalvermorsing vir hek nie, kort deurlooptyd en hoë gehalte. Die enigste gebrek is die effense spoorspoor.
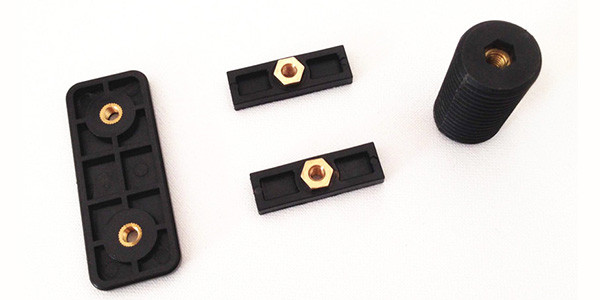
Warmspuitpen hek: goeie likiditeit, posisie kies buigsaam, klein hek punt. Pas vir massiewe produksie en vir produkte met dik wanddikte. Kan help om materiaal te bespaar, geen materiaalvermorsing vir hek nie, kort deurlooptyd en hoë gehalte. Maar daar is defekte, soos 0.1 mm-materiaal wat rondom die hekpunt gelaat word, en dit is maklik om te bars. Moet groewe maak om die linker materiaal rondom hekpunt te bedek.
Pin-punt hek: posisie kies buigsaam, swak likiditeit, lang hardloper afstand, klein hek punt. Pas vir klein groepproduksie. Meer afvalmateriaal rondom hekpunt. Benodig meganiese arms om hekpunt in produksie vas te klem. Lang deurlooptyd. Defek is 0.1-0.2mm materiaal wat om hekpunt gelaat word, moet groewe maak om die linker materiaal rondom hekpunt te bedek.
Sub hek: kan op ribbes in holte, kern, sywande en uitwerppenne ontwerp word. Kan hekpunt buigsaam kies, giethek skei outomaties van deel, effense hekspoor. Defekte: maklik om materiaal rondom hekpunt uit te trek, maklik om droogmerke in hekposisie te veroorsaak, moet materiaal met die hand uitvee, baie drukverlies vanaf hekpunt uit holtes.
Randhek: gesmelte plastiek vloei deur hek, word laterale eweredig toegeken, verminder spanning; verminder die moontlikheid dat lug die holte binnedring, vermy strepe en borrels. Defekte: giethek kan nie outomaties van deel skei nie, het spuitmerke op deel se rande gelaat, benodig gereedskap om giethek plat te verwerk. Randhek kan help met proporsie inspuiting en drukhou, en is ook goed vir drukhou en voer, op hierdie manier is dit beter om luglyne, vloeimerke te verbeter ... ens.
Verwerking en pasvorm vir insetvorm
1. Voor verwerking, werk die verwerkingstegnologie van vorm uit. Kies hoë-presisie-verwerkingsmasjiene, hoëspoedmasjien, stadigvoerende NC-draadsnymasjien, spieël-EDM (elektriese ontladingsbewerking) masjien, ens.
2. Ontwerp 0.05-0.1 mm links in plek van voordruk.
3.Let op akkuraatheidsvereistes in vormbasisverwerking, inspekteer toleransie nadat u die vormbasis gekry het en gebruik dit nie as die toleransie ongekwalifiseerd is nie.
4.Sit neute, metaalonderdele en harde plastiekonderdele binne-in vorm vir vormpassing. As u probleme ondervind met die pasvorm van die vorm, kyk deur moere, metaalonderdele, harde plastiekonderdele en vorms om te sien watter een verkeerd is. Verwerk deel volgens tekening so ver moontlik, wat help om data in die toekoms op te spoor.
5.Kan nie grinder gebruik vir vormpassing nie. Draai na masjiene vir regstelling waar vormpassing nie goed is nie.
6. Doen aksietoetsing voor verhoor, vermy missamestelling en verkeerde montering. Verkeerde samestelling sal skade aan die vormbasis veroorsaak.
Vormtoetsing vir insetvorm
1.In 'n vormtoetsing moet 'n mens duidelik weet oor die volgorde van oopmaak, toemaak en uitstoot van 'n vorm. Verstaan die strukturele kenmerke en eienskappe van metaalonderdele en harde plastiekonderdele.
2. Weet duidelik van die monsterhoeveelheid wat die klant benodig, berei genoeg neute, metaalonderdele en harde plastiek voor, want dit benodig baie monsters in vormtoetsing.
3.Let op of vorm kan toets sonder insetsels van neute, metaalonderdele of harde plastiek. As insetmoere, metaalonderdele en harde plastiek nie in 'n vorm aanmekaargesit word nie, kan 'n deel defekte hê, soos om aan die vorm vas te sit of 'n kort skoot.
4. In baie gevalle moet die waterlynplaat op die vorm verstel word, maar soms kan dit nie die waterlynplaat in een of ander insetvorm aanpas op grond van hul struktuur nie, of nog erger, die vorm is baie vas en moet verander word, of die vorm word beskadig in die opening.
5.Probleme kan in vormtoetsing voorkom, soos kort skote, luguitstappies, flitse of vassit aan die vorm. As probleme op 'n spuitgietmasjien geverifieer kan word, is dit beter om dit op te los.
DJmolding het meer as 10+ jaar insetvorm-ondervinding, as u enige vrae het, kontak ons asseblief.