Pritsevormimise tavaliste vormimisdefektide lahendused
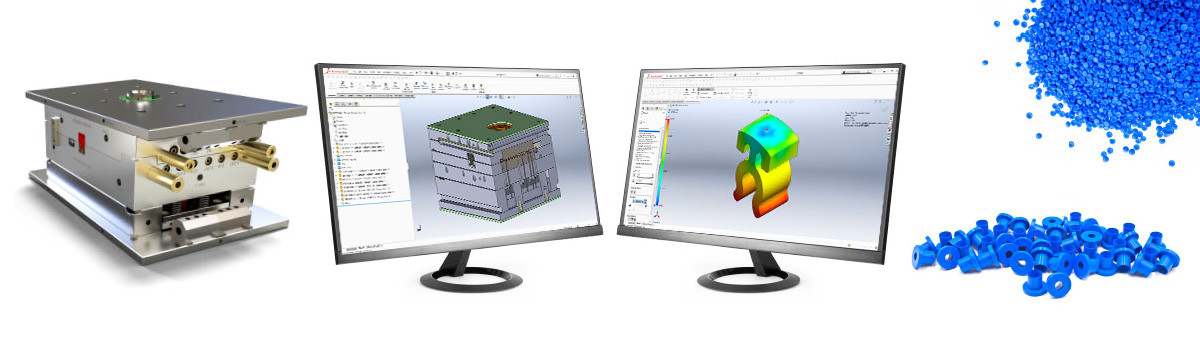
Defektid on tavalised, kui kasutatakse plastmassist survevaludetailide töötlemiseks vorme ja see mõjutab suuresti töötlemise efektiivsust. Järgnevalt on toodud plastist survevaluvormide osade levinumad valudefektid ja lahendused.
Lühikesed kaadrid
Lühikesed kaadrid viitavad sellele, et valmistatud tooted on puudulikud, kuna vormid pole täielikult täidetud.
See defekt ilmneb tavaliselt väravast kaugeimas kohas või osades, kuhu pääseb ligi ainult vormi kitsaste alade kaudu, kuna kitsad alad võivad mõjutada sulandite voolu.
Lühike võte võib põhjustada mikrovoolu jälgi või suure osa tootest ilmselgelt puudumist.
Põhjus:
Lühikeste võtete põhjused on järgmised:
Hallitusse süstitud toorainest ei piisa.
Sulamiskindlus on suur, mistõttu ei saa vormi täielikult täita.
Hallituse ventilatsioon on halb ja põhjustab kavitatsiooni teket, mis blokeerib sulatise, mistõttu sula ei saa voolata teatud hallituse piirkondadesse.
Burrid
Burrid tekivad vormiõõnsusest toote külge ekstrudeeritud liigse tooraine nakkumisel.
See defekt jääb toote servadele või igale hallituse osale. Tooraine võib vormist või liigutus- ja kinnitusvormide ühenduskohtadest üle voolata.
Burre võib leida ka vormisüdamikul, mis on tingitud hüdraulilisest rõhust või nurktihvtist.
Murde raskusaste on erinev, mõnikord õhuke, mõnikord paksem.
Põhjus:
Murde põhjused on järgmised:
Kinnitusvormi pind on kahjustatud või tugevalt kulunud.
Liikuv vorm ja kinnitusvorm nihkuvad, kui need on lukustatud.
Tooraine rõhk vormis on suurem kui vormi kinnitusjõud.
Eespool mainitud kolmas tingimus tuleneb mitmesugustest põhjustest. Järgmistes olukordades on toormaterjali rõhk suurem kui vormi kinnitusjõud.
Survevormi esimeses etapis (vormi täitmise etapp) täidetakse liiga palju toorainet, mis suurendab survet vormi sees.
Vormi täitmise käigus tõstab sulavoolu suur takistus ka vormi sees olevat rõhku.
Vormiõõnsuse rõhk on rõhu hoidmise etapis liiga kõrge.
Vormi kinnitusjõust ei piisa.
degradeerumine
Lagundamine võib viia paljude tulemusteni. Ka probleemi ulatus ja tõsidus on erinev. Kõige tõsisemal juhul võib see põhjustada toote täielikku värvimuutust ja halbu mehaanilisi omadusi. Kohalik lagunemine põhjustab ainult tumedaid triipe või laike.
Põhjus:
Lagunemise põhjuseks on tooraine kahjustumine. Plaste moodustavad pika ahelaga molekulid lagunevad liigse kuumuse või liigse nihkepinge toimel. Molekulide lagunemise ajal kiirendab lenduv gaas lagunemisprotsessi, mis põhjustab tooraine värvuse kadu. Suure hulga molekulide lagunemine lõhub lõpuks tooraine sisalduse ja avaldab negatiivset mõju mehaanilistele omadustele.
Materjali tünni ebaühtlane temperatuur võib tuleneda lokaalsest lagunemisest.
Degradatsioon võib ilmneda järgmistes olukordades:
Toorainet kuumutatakse materjalitünnis või kuumakanalisüsteemis üle.
Tooraine seisab tünnis liiga kaua.
Survevalu protsessi ajal on toormaterjalile avaldatav nihkepinge liiga suur. Kui düüsid on ummistunud või väravad ja jooksur on liiga kitsad, suurendab see nihkepinget.
Deformatsioon
Tavaolukorras peaks toodete kuju olema vormide kujuga kooskõlas. Deformatsioon viitab toodete deformatsioonile.
Kui seisund halveneb, deformeeruvad tooted vormist väljumisel täielikult. Kui seisund ei ole tõsine, ilmnevad toote kuju väikesed ebakorrapärasused.
Pikad, kuid ilma tugiservadeta või suurte tasapindadeta on alad, mis on kõige altid deformatsioonile.
Põhjus:
Deformatsiooni põhjused:
Vormi vabastamisel on temperatuur liiga kõrge.
Kuna jahutusaeg on paksude ja õhukeste alade puhul erinev või hallituse temperatuuride erinevus vormi liigutamisel ja vormi kinnitamisel, on kahanemine toodete sees erinev.
Vormivool ei ole täitmisel sujuv (nn külmutussuund) või rõhk vormiõõnes on rõhu hoidmise etapis liiga kõrge.
Lisandid
Lisandid ilmuvad sageli erinevat värvi täppide, laikude või triipudena. Kõige tavalisem on must täpp.
Lisandid võivad olla vaid pisikesed laigud, kuid võivad olla ka ilmsed triibud või suur osa värvi kadumisest, kui see on tõsine.
Põhjus:
Lisandid on põhjustatud mitmesugustest toorainetest, näiteks:
Tooraine segatakse tünnidesse transportimisel mitmesuguste toodetega.
Tooraine lagunemine võib kukkuda mis tahes lõikemehhanismidest ja seguneda toorainesse, nagu masina poldid, kuivatustrumli sisesein, liitmikud/düüsid.
Lamineerimine
Lamineerimine tekitab toodete pinnale “nahaefekti”, mis tuleneb toodete ja muude toorainete pinna omaduste ja tekstuuride erinevusest ning moodustab kooruva naha, mida saab eemaldada.
Kui lamineerimine on tõsine, koosneb kogu ristlõike pindala erinevatest kihtidest ja seda ei ole kokku sulatatud. Kui defektid on vähem ilmsed, võib toodete välimus küll nõuetele vastata, kuid rikub toodete mehaanilisi omadusi.
Põhjus:
Lamineerimisel on kaks peamist põhjust. Esimene on see, kui kaks erinevat tüüpi toorainet on omavahel valesti segatud. Kaks toorainet transporditakse surve all samal ajal tünni. Kui aga vormi ei saa jahtudes kokku sulatada, pressitakse erinevad kihid sunniviisiliselt kokku, et moodustada tooteid.
Teiseks: kui külmsulatus on sunnitud läbi kitsa värava läbima, tekib nihkepinge. Liiga suure nihkepinge tõttu ei saa eelnevalt sulatatud sulamiskihti täielikult sulatada.
Segamise oht:
Üks asi, mida peaksite teadma, on see, et mõned omavahel segatud toorained põhjustavad tugeva keemilise reaktsiooni, näiteks PVC-d ja Avetali ei tohi segada.
Hõbedane lineaarne
Sliver lineaarne võib olla lihtsalt lokaalne nähtus, kuid tõsine võib see laieneda kogu pinnale.
Lineaarne hõbedane mõjutab toodete välimust ja kahjustab ka toodete mehaanilisi omadusi.
Põhjus:
Järgmised kaks punkti põhjustavad hõbedase lineaarse:
Tooraine on märg ja osa neist neelab õhus oleva auru. Kui tooraine on liiga märg, võib tünni kõrgel temperatuuril ja kõrgel rõhul tekkida rõhu all olev aur. Need aurud tungivad läbi toote pinna ja moodustavad hõbedased triibud.
Sulatus sai termiliselt kahjustatud ja tekitab lokaalset lagunemist. Tekkiv lenduv gaas blokeerub hallituse pinnal ja tekitab toodete pinnale triipe.
See pole nii hullem kui lagunemine. Niikaua võib see juhtuda seni, kuni sulatise temperatuur on kõrge või see on plastifitseerimisel või vormi süstimisel nihkepinge all.
Läige/vari
Toodete pinnaviimistlus peaks olema sama, mis vormidel. Kui kahe pinna viimistlus on erinev, tekkisid läike/varju vead.
Pind on defektide ilmnemisel sünge ning kare pind on sile ja läikiv.
Põhjus:
Läike/varju põhjused on järgmised:
Sulatus voolab ebasujuvalt või vormi pinna temperatuur on madal, mistõttu ei saa materjali vormimisel vormi pinnaviimistlust dubleerida.
Surve hoidmise ajal ei ole rõhk õõnsuses piisavalt kõrge, et materjal jääks jahutusprotsessis vormi pinnale kinni, jättes kokkutõmbumisjälgi.
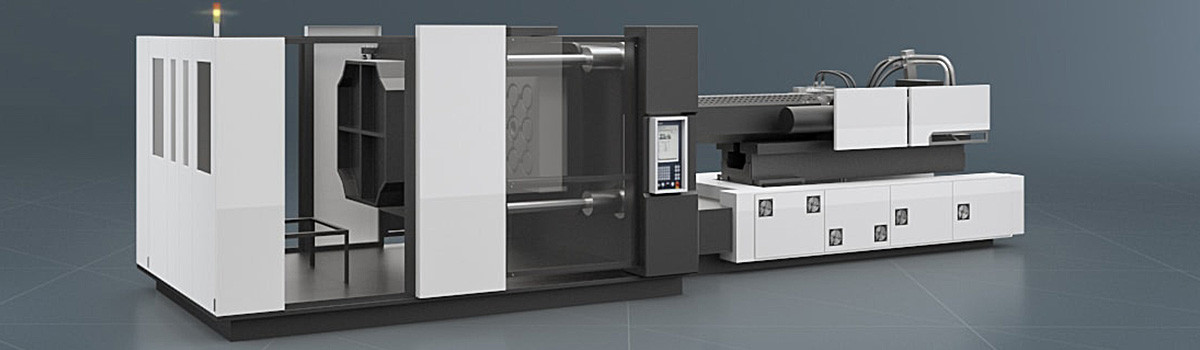
Voolumärgid
Voolujälgi võib toodete pinnalt leida mitmel kujul. Üldiselt moodustab see varjuala.
Voolujäljed ei tekita toodete pinnale reljeefseid ja süvendeid, mida pole sõrmedega tunda. Seda defekti nimetatakse ka lohistamisjälgedeks, kummitusteks ja varjudeks.
Kui voolamisjäljed on silmnähtavad, tekitab see sooned ja jätab toote pinnale defekte, nagu jäljed.
Põhjus:
Voolujälgi võib leida, kui:
Sula voolavus on halb või vormi pinnatemperatuur madal, mille tulemuseks on plasti voolutakistus vormi täitmise protsessis.
Vormitäidises voolab sula takistusega, mis võib olla põhjustatud matriitsi ebatasasest pinnast, matriitsi pinnale trükitud jäljedest või mustritest või sulamisvoolu suuna muutumisest täitmisprotsessi käigus.
Ühendusjoon
Ühendusjoon tekib siis, kui vormi täitmise ajal kohtuvad kaks sulami esiosa ja see ilmub toote pinnale joonena.
Ühendusjoon on nagu pragunemisjoon toodete pinnal, mida pole ilmselge tuvastada.
Vormide kujundamisel on mõned nähtavad ühendusjooned vältimatud. Sel juhul lühendage ühendusjoont nii palju kui võimalik, et vältida toodete tugevuse ja välimuse kahjustamist.
Põhjus:
Sulafrondi tekkeks on palju põhjuseid. Kõige võimalikum põhjus võib olla sulamisvool piki vormisüdamiku servi. Kui need kaks sulamist kokku saavad, tekitab see ühendusliinid. Kahe sulami esiosa temperatuur peaks olema piisavalt kõrge, et need saaksid edukalt kokku sulatada, ega mõjuta toodete tugevust ega välimust.
Kui kaks sulamit ei saa täielikult kokku sulada, tekivad defektid.
Defektide põhjused:
Vormis on paksemad ja õhemad osad ning sulandite voolukiirus on erinev, kui sulati voolab läbi vormi õhukese osa, on temperatuur madal.
Iga jooksja pikkus on erinev. Üksikjooksjaid on lihtne jahutada.
Vormiõõnsuse rõhk ei ole piisav, et võimaldada sulal rõhu hoidmise etapis täielikult sulada.
Ülejäänud mullid muudavad sulamise esiosa sulamisvõimetuks, mis põhjustab ka põlemist.
Põletamine
Põlemine sarnaneb lühikese haavli omaga, kuid ebakorrapäraste pleekivate servade ja kerge põlemislõhnaga. Kui seisund on tõsine, tekivad tootele tahma alad, millega kaasneb plasti põlemise lõhn.
Kui defekte ei kõrvaldata, tekib hallitusele sageli must ladestus. Kui põlemisel tekkivaid gaasi- või õliaineid kohe ei kontrollita, võivad need õhuaugud ummistada. Põletust leitakse tavaliselt radade lõpus.
Põhjus:
Põlemist põhjustab sisepõlemisefekt. Kui õhurõhk tõuseb väga lühikese aja jooksul järsult, tõuseb temperatuur ja põhjustab põletust. Kogutud andmete kohaselt võib sisepõlemisefekt survevaluprotsessis tekitada kõrge temperatuuri kuni 600 kraadi.
Põlemine võib tekkida, kui:
Vormi täitmise kiirus on kiire, nii et õhk ei pääse vormiõõnsusest välja ja tekitab sissetuleva plastiku blokeerimise tõttu õhumulle, mis pärast kokkusurumist põhjustab sisepõlemisefekti.
Õhuaugud on ummistunud või ventilatsioon ei ole sujuv.
Vormis olev õhk peaks õhuavadest väljuma. Kui ventilatsiooni mõjutab asend, arv, suurus või funktsioonid, jääb õhk vormi sisse ja põhjustab põletust. Suur hallituse kinnitusjõud põhjustab ka halva ventilatsiooni.
Kahanemine
Kokkutõmbumine viitab väikestele õõnsustele toodete pinnal.
Kui defektid on väikesed, on toodete pind ebaühtlane. Kui see on tõsine, kukub suur toodete ala kokku. Kaare, käepideme ja eendiga tooted kannatavad sageli kokkutõmbumisdefektide all.
Põhjus:
Kokkutõmbumise põhjuseks on tooraine suure pindala kokkutõmbumine jahutamisel.
Toodete paksus piirkonnas (nagu kaar) on materjali südamiku parasvöötme madal, nii et kokkutõmbumine toimub hiljem kui pinna kokkutõmbumine, mis tekitab tooraine sees kokkutõmbumisjõu ja tõmbab väliskülje sissepoole süvendisse. kokkutõmbumise tekitamiseks.
Kokkutõmbed ilmnevad järgmistel juhtudel:
Rõhk vormiõõnes on madalam kui jõud, mis tekib tooraine kokkutõmbumisel jahutusprotsessis.
Vormiõõnsuse ebapiisav survestamise aeg jahutusprotsessi ajal, mille tulemusena voolab tooraine väravast õõnsusest välja.
Toormaterjalil ei ole vormimise ja rõhu hoidmise etapis piisavat puhverdusvõimet, kuna kruvi tõmmatakse enne liigse tooraine sissepritsimist täielikult välja.
Väravate ja jooksutorude ristlõike pindala on palju väiksem kui toodete paksus, mis tähendab, et väravad on juba enne toodete väljapressimist külmunud.
Bubbles
Vaakummullid on õhumullidena, mida on lihtne leida läbipaistvatel toodetel. Seda on näha ka läbipaistmatute toodete ristlõikel.
Põhjus:
Õhumullid on toodete vaakumosa, mis tekib siis, kui tooraine jahutusprotsessis kokku tõmbub.
Sarnaselt kokkutõmbumisega tekitab tooraine sisemus kokkutõmbumisjõudu. Erinevus seisneb selles, et mullide tekkimisel on toodete välisilme tahkunud ja kokkuvarisemist ei toimu, mistõttu tekivad õõnsad mullid.
Mullide põhjused on samad, mis vähenemise põhjused, sealhulgas:
Ebaefektiivne hallitusõõnsuse rõhk
Ebapiisav õõnsuse survestamise aeg
Jooksu ja värava suurus on liiga väike
Pritsimisjäljed
Pritsimisjäljed viitavad värava vastas olevale keermestatud alale. Pihustusjäljed ei mõjuta mitte ainult toodete välimust, vaid mõjutavad ka toodete tugevust.
Põhjus:
Pritsimisjäljed on põhjustatud kontrolli alt väljuvast sulamisvoolust vormi täitmise käigus.
Sulaplast satub tohutu surve all vormi. Kui vormi täitmise kiirus on liiga suur, paiskub plast vormiõõne avatud pilust välja ning vetrub kiiresti tagasi ja jahtub. Sel ajal moodustuvad niidid, mis blokeerivad sulaplasti sisenemist väravatesse.
Pritsimisjälgede peamine põhjus on väravate vale asend või värava konstruktsioon. Järgmised kaks olukorda halvendavad defektide olukorda:
Suur vormi täitmise kiirus
Halb sulamisvool vormi täitmisel