راه حل هایی برای نقص های معمول قالب گیری قالب گیری تزریقی
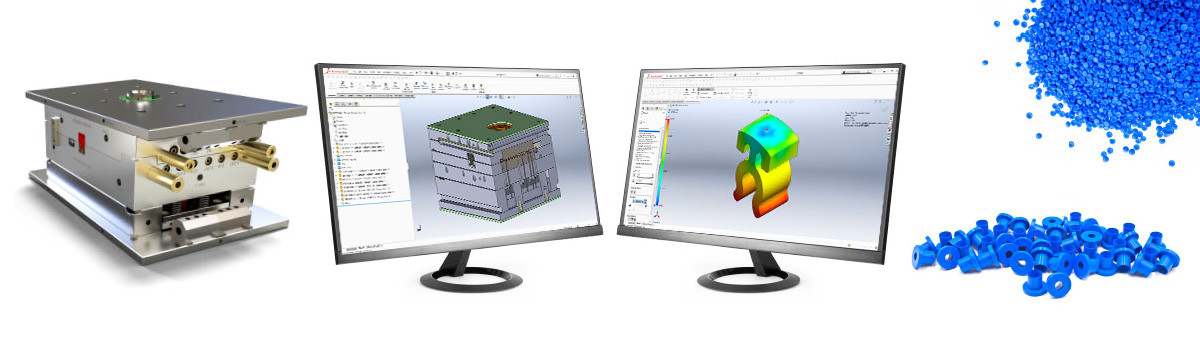
هنگام استفاده از قالبها برای پردازش قطعات قالبگیری تزریقی پلاستیک، نقصها رایج است و این تا حد زیادی بر راندمان پردازش تأثیر میگذارد. موارد زیر عیوب قالب گیری و راه حل های رایج برای قطعات قالب تزریق پلاستیک است.
عکس های کوتاه
شات های کوتاه اشاره دارد که محصولات ساخته شده به دلیل پر نشدن کامل قالب ها ناقص هستند.
این عیب معمولاً در دورترین نقطه دور از دروازه یا قسمت هایی ظاهر می شود که فقط از طریق نواحی باریک قالب می توان به آنها دسترسی داشت زیرا نواحی باریک ممکن است بر جریان مذاب تأثیر بگذارد.
شات کوتاه ممکن است باعث ایجاد علائم میکرو جریان شود یا منجر به گم شدن واضح بخش بزرگی از محصول شود.
علت:
دلایل شات های کوتاه عبارتند از:
مواد اولیه تزریق شده به قالب کافی نیست.
مقاومت مذاب ها زیاد است و در نتیجه نمی توان قالب را به طور کامل پر کرد.
تهویه قالب ضعیف است و باعث ایجاد حفره می شود که مذاب را مسدود می کند و باعث می شود مذاب نتواند به برخی از مناطق قالب جریان یابد.
بورس
فرزها از چسبندگی مواد خام اضافی اکسترود شده از حفره قالب به محصول ایجاد می شوند.
این عیب در لبه های محصول یا هر قسمت تشکیل شده از قالب ایجاد می شود. ممکن است مواد خام از قالب یا محل اتصال قالب های متحرک و ثابت سرریز شود.
بر روی هسته قالب نیز می توان فرزها را یافت که به دلیل فشار هیدرولیک یا پین زاویه ای است.
شدت جوش ها متفاوت است، گاهی نازک، گاهی ضخیم تر.
علت:
علل ایجاد فرز عبارتند از:
سطح قالب گیره آسیب دیده یا به شدت فرسوده شده است.
قالب متحرک و قالب ثابت هنگام قفل شدن از جای خود خارج می شوند.
فشار مواد خام در قالب بیشتر از نیروی گیره قالب است.
شرط سوم که در بالا ذکر شد به دلایل مختلفی ناشی می شود. در شرایط زیر فشار مواد اولیه بیشتر از نیروی گیره قالب است.
در مرحله اول قالب تزریق (مرحله پر کردن قالب) مواد اولیه بیش از حد پر می شود که باعث افزایش فشار داخل قالب می شود.
در طول فرآیند پر کردن قالب، مقاومت زیاد جریان مذاب باعث افزایش فشار داخل قالب نیز می شود.
فشار حفره قالب در مرحله نگهداری فشار بسیار زیاد است.
نیروی بستن قالب کافی نیست.
تنزل
تجزیه می تواند به نتایج بسیاری منجر شود. وسعت و شدت مشکل نیز متفاوت است. در جدی ترین حالت، ممکن است باعث تغییر رنگ کامل محصول و خواص مکانیکی ضعیف شود. تخریب موضعی فقط باعث ایجاد خطوط یا لکه های تیره می شود.
علت:
تخریب ناشی از آسیب دیدن مواد خام است. مولکول های زنجیره بلند که پلاستیک را تشکیل می دهند تحت تأثیر گرمای بیش از حد یا تنش برشی بیش از حد تجزیه می شوند. در حین تجزیه مولکول ها، گاز فرار روند تجزیه را تسریع می کند که باعث رنگ زدایی ماده خام می شود. تجزیه مقدار زیادی از مولکول ها در نهایت باعث شکسته شدن محتوای ماده خام و تأثیر منفی بر خواص مکانیکی می شود.
تخریب موضعی ممکن است ناشی از دمای ناهموار بشکه مواد باشد.
تخریب ممکن است در شرایط زیر رخ دهد:
مواد خام در بشکه مواد یا سیستم دونده داغ بیش از حد گرم می شود.
مواد خام برای مدت طولانی در بشکه باقی می ماند.
در طی فرآیند قالب گیری تزریقی، تنش برشی اعمال شده بر ماده خام بسیار زیاد است. اگر نازل ها مسدود شده باشند یا دروازه ها و رانر خیلی باریک باشند، تنش برشی را افزایش می دهد.
تغییر شکل
در شرایط عادی، شکل محصولات باید مطابق با قالب باشد. تغییر شکل به تغییر شکل محصولات اشاره دارد.
هنگامی که وضعیت بدتر می شود، محصولات در هنگام بیرون ریختن از قالب کاملاً تغییر شکل می دهند. هنگامی که وضعیت جدی نیست، شکل محصول بی نظمی های کوچکی به نظر می رسد.
دراز اما بدون لبه های تکیه گاه یا صفحات بزرگ مناطقی هستند که مستعد تغییر شکل هستند.
علت:
دلایل تغییر شکل:
هنگامی که قالب آزاد می شود، دما بسیار بالا است.
از آنجایی که زمان خنک شدن در نواحی ضخیم و نازک متفاوت است یا تفاوت دمای قالب در قالب متحرک و قالب ثابت متفاوت است، انقباض داخل محصولات متفاوت است.
جریان قالب هنگام پر کردن صاف نیست (به اصطلاح "جهت انجماد") یا فشار داخل حفره قالب در مرحله نگهداری فشار خیلی زیاد است.
ناخالصی ها
ناخالصی ها اغلب به صورت لکه هایی در رنگ ها، لکه ها یا راه راه های مختلف ظاهر می شوند. شایع ترین آن لکه سیاه است.
ناخالصیها ممکن است فقط نقاط ریز باشند، اما در صورت جدی بودن، میتوانند راه راههای آشکار یا بخش بزرگی از رنگزدایی باشند.
علت:
ناخالصی ها در اثر مواد مختلف مخلوط شده با مواد خام ایجاد می شوند، مانند:
مواد خام هنگام انتقال به بشکه ها با مواد مختلف مخلوط می شود.
تجزیه مواد خام ممکن است از هر مکانیزم برشی سقوط کرده و با مواد خام مانند پیچ ماشین، دیواره داخلی درام خشک کن، اتصالات / نازل مخلوط شود.
لمینیت
لمینت باعث ایجاد "اثر پوستی" روی سطح محصولات می شود که به دلیل تفاوت در خواص و بافت سطح محصولات و سایر مواد اولیه ایجاد می شود و یک پوست لایه بردار ایجاد می کند که می توان آن را جدا کرد.
هنگامی که لمینیت جدی است، کل سطح مقطع از لایه های مختلف تشکیل شده است و با هم ذوب نشده اند. هنگامی که عیوب کمتر آشکار باشد، ظاهر محصولات ممکن است الزامات را برآورده کند، اما خواص مکانیکی محصولات را از بین می برد.
علت:
دو دلیل اصلی برای لمینیت وجود دارد. اولین مورد این است که وقتی دو نوع مواد خام مختلف به اشتباه با هم مخلوط می شوند. دو ماده خام به طور همزمان تحت فشار وارد بشکه می شوند. با این حال، زمانی که قالب هنگام سرد شدن نمی تواند با هم ذوب شود، همانطور که لایه های مختلف به زور به هم فشار داده می شوند تا محصولی تشکیل شود.
دوم: اگر مذاب سرد مجبور شود از دروازه باریک عبور کند، تنش برشی ایجاد می شود. تنش برشی بسیار زیاد باعث می شود که لایه مذاب که از قبل ذوب شده است، نتواند به طور کامل ذوب شود.
خطر اختلاط:
نکته ای که باید به آن توجه داشت این است که برخی از مواد اولیه مخلوط با هم واکنش شیمیایی قوی ایجاد می کند، مانند PVC و اوتال نباید مخلوط شوند.
نقره ای خطی
Sliver linear ممکن است فقط یک پدیده محلی باشد، اما در صورت جدی بودن می تواند به کل سطح گسترش یابد.
نقره خطی بر ظاهر محصولات تاثیر می گذارد و همچنین به خواص مکانیکی محصولات آسیب می رساند.
علت:
دو نقطه زیر باعث خطی شدن نقره می شود:
مواد اولیه مرطوب است و برخی از آنها بخار موجود در هوا را جذب می کنند. اگر ماده خام خیلی مرطوب باشد، بخار تحت فشار ممکن است تحت دمای بالا و فشار بالای بشکه تولید شود. این بخارات از سطح محصول عبور کرده و نوارهای نقره ای را تشکیل می دهند.
مذاب دچار آسیب حرارتی شده و باعث تخریب موضعی می شود. گاز فرار تولید شده روی سطح قالب مسدود می شود و نوارهایی روی سطح محصولات ایجاد می کند.
این بدتر از تخریب نیست. تا زمانی که دمای مذاب بالا باشد یا در حین پلاستیک سازی تحت تنش برشی قرار گیرد یا به داخل قالب تزریق شود، ممکن است این اتفاق بیفتد.
براق/سایه
پوشش سطح محصولات باید مانند قالب ها باشد. هنگامی که پرداخت سطح دو متفاوت است، نقص براق/سایه رخ می دهد.
در صورت بروز نقص، سطح تاریک خواهد بود و سطح ناهموار صاف و براق است.
علت:
دلایل براقیت/سایه عبارتند از:
مذاب به آرامی جریان می یابد یا دمای سطح قالب پایین است، در نتیجه نمی توان در هنگام قالب گیری مواد، سطح قالب را تکرار کرد.
در حین نگهداری فشار، فشار در حفره به اندازه کافی زیاد نیست که باعث شود مواد در فرآیند خنکسازی به سطح قالب بچسبد و آثار انقباض باقی بماند.
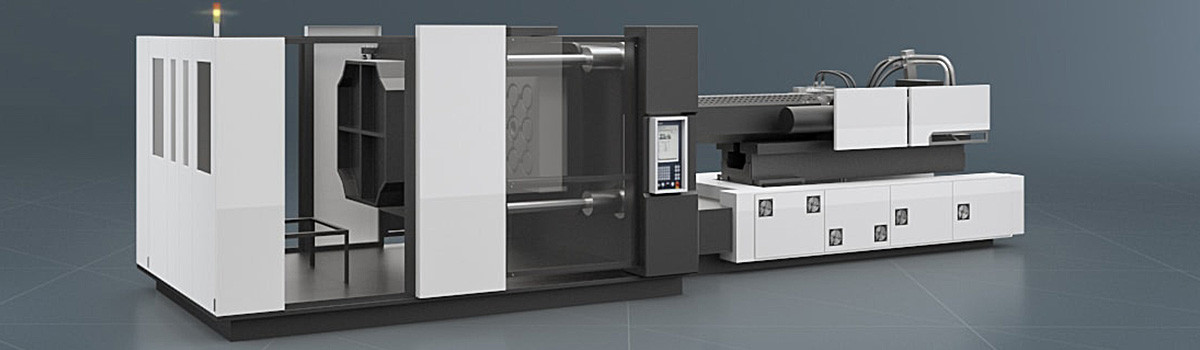
علائم جریان
علائم جریان را می توان بر روی سطح محصولات به اشکال مختلف یافت. به طور کلی، یک ناحیه سایه را تشکیل می دهد.
علائم جریان هیچ گونه برجستگی یا فرورفتگی روی سطح محصولات ایجاد نمی کند که با انگشتان قابل لمس نیست. به این نقص علائم کشیدن، شبح و سایه نیز می گویند.
هنگامی که علائم جریان آشکار باشد، شیارهایی ایجاد می کند و نقص هایی مانند علائم روی سطح محصولات باقی می گذارد.
علت:
علائم جریان را می توان زمانی پیدا کرد که:
جریان پذیری مذاب ضعیف است یا دمای سطح قالب پایین است و در نتیجه مقاومت جریان زیادی پلاستیک در فرآیند پر کردن قالب ایجاد می شود.
در پر کردن قالب، جریان مذاب با مقاومت جریان دارد، که ممکن است ناشی از سطح ناهموار قالب، علائم یا الگوهای چاپ شده روی سطح قالب، یا تغییر جهت جریان مذاب در طول فرآیند پر کردن باشد.
خط اتصال
خط اتصال زمانی ایجاد می شود که دو جبهه مذاب در حین پر کردن قالب به هم برسند و مانند یک خط روی سطح محصول ظاهر می شود.
خط اتصال مانند خط ترک روی سطح محصولات است که تشخیص آن مشخص نیست.
هنگام طراحی قالب، برخی از خطوط اتصال قابل مشاهده اجتناب ناپذیر است. در این حالت خط اتصال را تا حد امکان کوتاه می کند تا از آسیب دیدن استحکام و ظاهر محصولات جلوگیری شود.
علت:
دلایل زیادی برای تولید جبهه مذاب وجود دارد. محتمل ترین دلیل می تواند جریان مذاب در امتداد لبه های هسته قالب باشد. هنگامی که این دو ذوب به هم می رسند، خطوط اتصال ایجاد می شود. دمای دو جلوی مذاب باید به حدی باشد که به آنها اجازه دهد تا با موفقیت با هم ترکیب شوند و بر استحکام و ظاهر محصولات تأثیری نگذارند.
زمانی که این دو ذوب نتوانند به طور کامل با هم ذوب شوند، نقص ایجاد می شود.
علل نقص:
قالب دارای قطعات ضخیم تر و نازک تری است و سرعت جریان مذاب ها متفاوت است، زمانی که مذاب از قسمت نازک قالب جریان می یابد، دما پایین است.
طول هر دونده متفاوت است. دونده های تنها به راحتی خنک می شوند.
فشار حفره قالب به اندازه کافی برای ذوب شدن کامل مذاب در مرحله نگهداری فشار کافی نیست.
حبابهای باقیمانده باعث میشود که جلوی مذاب نتواند جوش بخورد، که همچنین منجر به سوختن میشود.
سوزش
سوزش شبیه شات کوتاه است، اما با لبه های محو نامنظم و بوی سوختگی خفیف. در صورت جدی بودن شرایط، نواحی سیاه کربن روی محصول ظاهر میشوند که با بوی سوختگی پلاستیک همراه است.
اگر عیوب برطرف نشوند، اغلب رسوب سیاه روی قالب وجود دارد. اگر مواد گاز یا نفت تولید شده در اثر سوختن فورا بررسی نشوند، ممکن است سوراخ های هوا را مسدود کنند. سوزش معمولاً در انتهای مسیرها مشاهده می شود.
علت:
سوختن ناشی از اثر احتراق داخلی است. هنگامی که فشار هوا در مدت زمان بسیار کوتاهی به شدت افزایش می یابد، دما افزایش می یابد و باعث سوختگی می شود. با توجه به داده های جمع آوری شده، اثر احتراق داخلی در فرآیند قالب گیری تزریقی می تواند دمای بالا تا 600 درجه ایجاد کند.
سوزش ممکن است زمانی ایجاد شود که:
سرعت پر شدن قالب سریع است به طوری که هوا نمی تواند از حفره قالب خارج شود و به دلیل بلوک شدن پلاستیک ورودی حباب های هوا ایجاد می کند و پس از فشرده شدن منجر به اثر احتراق داخلی می شود.
سوراخ های هوا مسدود شده یا تهویه صاف نیست.
هوای داخل قالب باید از سوراخ های هوا خارج شود. اگر تهویه تحت تأثیر موقعیت، تعداد، اندازه یا عملکرد باشد، هوا در قالب باقی می ماند و منجر به سوختن می شود. نیروی بزرگ بستن قالب نیز منجر به تهویه ضعیف می شود.
انقباض
انقباض به حفره های جزئی روی سطح محصولات اشاره دارد.
هنگامی که عیوب جزئی باشد، سطح محصولات ناهموار است. وقتی جدی باشد، منطقه وسیعی از محصولات فرو می ریزد. محصولات دارای قوس، دستگیره و برآمدگی اغلب از ایرادات انقباض رنج می برند.
علت:
انقباض ناشی از انقباض سطح وسیع مواد خام در طول خنک شدن است.
در قسمت ضخیم محصولات (مانند قوس)، هسته معتدل مواد کم است، بنابراین انقباض دیرتر از سطح رخ می دهد که باعث ایجاد نیروی انقباض در داخل ماده خام می شود و سمت بیرونی را به داخل فرورفتگی به سمت داخل می کشد. برای تولید انقباض
انقباض در شرایط زیر رخ می دهد:
فشار در حفره قالب کمتر از نیروی ایجاد شده از انقباض مواد خام در فرآیند خنک سازی است.
زمان فشار ناکافی در حفره قالب در طول فرآیند خنکسازی، در نتیجه مواد خام از حفره از دروازه خارج میشود.
ماده خام ظرفیت بافر کافی در مرحله قالب گیری و نگهداری فشار ندارد زیرا پیچ قبل از تزریق بیش از حد مواد خام به طور کامل خارج می شود.
سطح مقطع دروازه ها و رانرها بسیار کوچکتر از ضخامت محصولات است، به این معنی که گیت ها قبل از فرآیند اکستروژن محصولات منجمد شده اند.
حباب
حباب های خلاء به صورت حباب های هوا ارائه می شوند که به راحتی بر روی محصولات شفاف یافت می شوند. روی سطح مقطع محصولات مات نیز دیده می شود.
علت:
حبابهای هوا بخش خلاء محصولات است که با انقباض مواد اولیه در طول فرآیند خنکسازی تولید میشوند.
مانند انقباض، داخل ماده خام نیروی انقباضی تولید می کند. تفاوت این است که ظاهر بیرونی محصولات با تشکیل حباب ها جامد شده است و هیچ فروریختگی وجود ندارد، بنابراین حباب های توخالی ایجاد می شوند.
علل ایجاد حباب مانند کاهش است، از جمله:
فشار ناکارآمد حفره قالب
زمان فشار ناکافی حفره
اندازه رانر و گیت خیلی کوچک است
علائم پاشش
علائم پاشش به ناحیه رزوه شده روبروی دروازه اشاره دارد. علائم پاشش نه تنها بر ظاهر محصولات تأثیر می گذارد، بلکه بر استحکام محصولات نیز تأثیر می گذارد.
علت:
علائم پاشش به دلیل خارج شدن جریان مذاب در طول فرآیند پر کردن قالب ایجاد می شود.
پلاستیک مذاب تحت فشار زیادی وارد قالب می شود. اگر سرعت پر شدن قالب خیلی زیاد باشد، پلاستیک از شکاف باز حفره قالب خارج می شود و به سرعت به عقب برمی گردد و خنک می شود. در آن زمان، نخ ها تشکیل می شوند، که مانع از ورود پلاستیک مذاب به دروازه ها می شود.
علت اصلی پاشیدن علائم، موقعیت نادرست دروازه ها یا طراحی دروازه است. دو وضعیت زیر وضعیت نقص را بدتر می کند:
سرعت پر شدن قالب بالا
جریان مذاب ضعیف در طول پر شدن قالب