قالب گیری تزریقی ترموپلاستیک
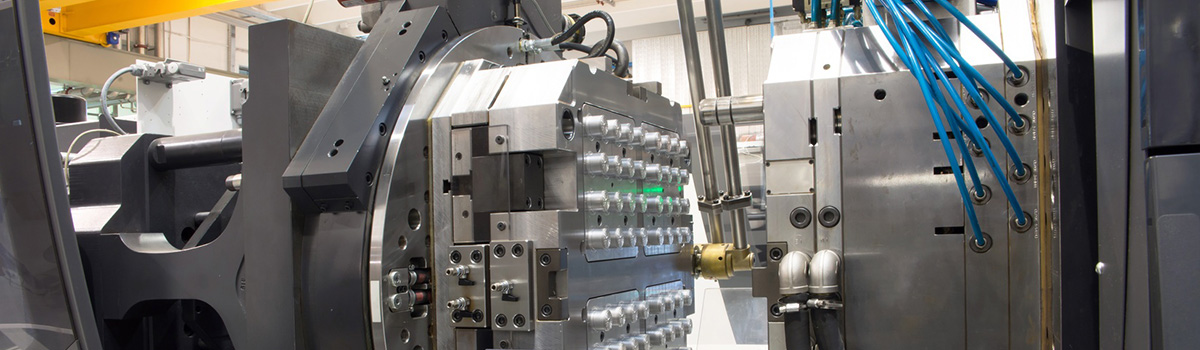
قالب گیری تزریقی ترموپلاستیک یک فرآیند تولید محبوب است که برای ایجاد قطعات پلاستیکی مختلف برای صنایع مختلف استفاده می شود. این فرآیند شامل ذوب گلوله های پلاستیکی و تزریق آنها به قالب برای ایجاد یک شکل سه بعدی است. قالب گیری تزریقی ترموپلاستیک برای تولید حجم زیادی از قطعات پلاستیکی با کیفیت بالا با تلرانس های تنگ بسیار کارآمد و مقرون به صرفه است. این راهنمای جامع جنبههای مختلف قالبگیری تزریقی ترموپلاستیک، از جمله مزایا و معایب آن، انواع ترموپلاستیکهای مورد استفاده، فرآیند قالبگیری تزریقی، ملاحظات طراحی و موارد دیگر را بررسی میکند.
تاریخچه قالب گیری تزریقی ترموپلاستیک
تاریخچه قالب گیری تزریقی ترموپلاستیک بیش از یک قرن از پیشرفت های تکنولوژیکی، پیشرفت مواد و کاربردهای صنعتی را در بر می گیرد. از آغاز ساده خود به عنوان یک فرآیند قالبگیری سلولوئیدی تا فناوری پیشرفته امروزی، قالبگیری تزریقی همچنان به عنوان یک تکنیک تولید حیاتی است که باعث نوآوری و شکلدهی به صنایع مختلف میشود.
- تحولات اولیه:جان وسلی حیات و برادرش آیزایا اولین ماشین قالبگیری تزریقی عملی را توسعه دادند که ریشههای قالبگیری تزریقی ترموپلاستیک را به اواخر قرن نوزدهم برمیگرداند. در سال 19، آنها دستگاهی را به ثبت رساندند که از یک پیستون برای تزریق سلولوئید به داخل حفره قالب استفاده می کرد و اجسام جامد ایجاد می کرد. این پیشرفت پایه و اساس فرآیند قالب گیری تزریقی مدرن را گذاشت.
- پیشرفت در مواد:در اوایل قرن بیستم، معرفی پلیمرهای مصنوعی جدید، فرصتهای جدیدی را برای قالبگیری تزریقی باز کرد. باکلیت، یک رزین فنلی، به دلیل خواص عالی عایق الکتریکی آن، به ماده ای محبوب برای قالب گیری تبدیل شد. در طول دهههای 20 و 1930، پیشرفتها در شیمی پلیمرها منجر به توسعه سایر ترموپلاستیکها، مانند پلی استایرن و پلی اتیلن شد که دامنه مواد مناسب برای قالبگیری تزریقی را بیشتر گسترش داد.
- پذیرش صنعتی: پذیرش گسترده قالبگیری تزریقی ترموپلاستیک در دهه 1950 آغاز شد زیرا تولیدکنندگان مقرونبهصرفه و تطبیقپذیری آن را تشخیص دادند. معرفی ماشینهای پرفشار امکان چرخه سریعتر و افزایش حجم تولید را فراهم کرد. در نتیجه، انتخاب متنوعی از محصولات برای استفاده شخصی و صنعتی به وجود آمد. اینها شامل اجزای ماشین، لوازم خانگی و اسباب بازی بود.
- نوآوری های تکنولوژیکی:در طول دههها، فناوری قالبگیری تزریقی به تکامل خود ادامه داد. در دهه 1960، ماشینهای کنترلشده توسط کامپیوتر ظهور کردند که امکان کنترل دقیق بر فرآیند قالبگیری را فراهم کردند. معرفی سیستم های دونده داغ در دهه 1980 با از بین بردن نیاز به رانر و اسپرو، ضایعات را کاهش داد و کارایی را بهبود بخشید. در سالهای اخیر، پیشرفتهای اتوماسیون، رباتیک و چاپ سهبعدی صنعت قالبگیری تزریقی را متحول کرده است و امکان طراحیهای پیچیده و کاهش زمان تولید را فراهم کرده است.
- پایداری و بازیافت:با افزایش نگرانی های زیست محیطی، صنعت قالب گیری تزریقی اقدامات پایداری را پذیرفته است. تولیدکنندگان ترموپلاستیکهای مبتنی بر زیستی و بازیافتی را توسعه دادهاند که وابستگی به مواد مبتنی بر سوخت فسیلی را کاهش میدهند. علاوه بر این، فناوریهای بازیافت بهبودیافته، پردازش مجدد زبالههای پس از مصرف و پسا صنعتی را امکانپذیر کرده و اثرات زیستمحیطی قالبگیری تزریقی ترموپلاستیک را به حداقل میرساند.
- چشم انداز آینده:آینده قالب گیری تزریقی ترموپلاستیک امیدوارکننده به نظر می رسد. این صنعت در حال بررسی نوآوریهایی مانند قالبگیری تزریقی میکرو برای قطعات مینیاتوری، تکنیکهای چند مادهای و قالبگیری بیش از حد برای قطعات پیچیده، و یکپارچهسازی فناوریهای هوشمند برای نظارت و بهینهسازی فرآیند است. علاوه بر این، محققان انتظار دارند پیشرفت در مواد زیست تخریبپذیر و تولید افزودنیها انقلابی در این زمینه ایجاد کند و قالبگیری تزریقی را پایدارتر و همهکارهتر کند.
مزایای قالب گیری تزریقی ترموپلاستیک
قالب گیری تزریقی ترموپلاستیک مزایای متعددی را برای تولید کنندگان ارائه می دهد. انعطافپذیری طراحی را فراهم میکند و امکان طراحیهای پیچیده و پیچیده با ویژگیهای مختلف را فراهم میکند. این فرآیند مقرون به صرفه است، ضایعات مواد را کاهش می دهد و هزینه های واحد را کاهش می دهد. قالبگیری تزریقی ترموپلاستیک از چندین ماده پشتیبانی میکند و تطبیق پذیری را برای کاربردهای مختلف فراهم میکند.
- انعطاف طراحی:قالبگیری تزریقی ترموپلاستیک امکان طراحیهای پیچیده و پیچیده با ویژگیهایی مانند بریدگی، دیوارههای نازک و ضخامتهای متفاوت را فراهم میکند که آزادی بسیار زیادی را برای طراحان فراهم میکند.
- کارایی هزینه: این فرآیند بسیار کارآمد است، ضایعات مواد را کاهش می دهد و هزینه های واحد را کاهش می دهد. قالب گیری همزمان چندین قطعه و چرخه های تولید سریع به صرفه جویی در هزینه کمک می کند.
- تطبیق پذیری مواد: قالبگیری تزریقی ترموپلاستیک طیف گستردهای از مواد را پشتیبانی میکند و تولیدکنندگان را قادر میسازد تا مناسبترین گزینه را برای هر کاربرد، از جمله مواد سفت یا انعطافپذیر، شفاف یا مات و مقاوم در برابر مواد شیمیایی انتخاب کنند.
- استحکام و دوام:ترموپلاستیک های قالب گیری تزریقی می توانند خواص مکانیکی عالی مانند استحکام بالا، چقرمگی و مقاومت در برابر ضربه را از خود نشان دهند. گزینه های تقویت کننده، مانند الیاف شیشه یا کربن، این ویژگی ها را بیشتر می کنند.
- سازگاری و کیفیت:قالبگیری تزریقی کیفیت ثابت و دقت ابعادی را تضمین میکند و تحملهای محکم و محصولات قابل اعتماد را ارائه میدهد. این فرآیند همچنین یک سطح صاف و یکنواخت را فراهم می کند و نیاز به عملیات تکمیلی اضافی را از بین می برد.
- مقیاس پذیری و تولید انبوه:قالب گیری تزریقی از حجم کم تا زیاد مقیاس پذیر است و برای تولید انبوه مناسب است. هنگامی که سازندگان قالب را ایجاد می کنند، می توانند مقادیر زیادی از قطعات یکسان را با حداقل تغییرات تولید کنند.
- ادغام و مونتاژ:قطعات تزریقی می توانند چندین جزء را در یک قطعه ترکیب کنند و نیاز به فرآیندهای مونتاژ اضافی را کاهش دهند. این ادغام باعث افزایش عملکرد محصول، کاهش زمان مونتاژ و کاهش هزینه ها می شود.
- پایداری:صنعت قالب گیری تزریقی تمرکز فزاینده ای بر پایداری نشان می دهد. در دسترس بودن مواد زیستی و بازیافتی امکان تولید محصولات سازگار با محیط زیست را فراهم می کند. استفاده کارآمد از مواد و قابلیت بازیافت ترموپلاستیک ها به فرآیند تولید سبزتر کمک می کند.
این مزایا آن را به روشی گسترده در صنایع مختلف تبدیل کرده است که راه حل هایی با کیفیت بالا، مقرون به صرفه و سازگار با محیط زیست برای الزامات محصول پیچیده ارائه می دهد.
معایب قالب گیری تزریقی ترموپلاستیک
در حالی که قالب گیری تزریقی ترموپلاستیک مزایای زیادی دارد، معایب متعددی نیز وجود دارد. تولیدکنندگان باید این عوامل را به دقت ارزیابی کنند و آنها را در برابر مزایا بسنجید تا مناسب بودن قالبگیری تزریقی ترموپلاستیک برای کاربردهای خاص آنها را تعیین کنند.
- سرمایه گذاری اولیه بالا: راه اندازی عملیات قالب گیری تزریقی ترموپلاستیک نیاز به سرمایه گذاری اولیه قابل توجهی در طراحی و ساخت قالب و خرید ماشین آلات تخصصی دارد. هزینه های مربوط به ایجاد قالب و ابزار می تواند قابل توجه باشد، به خصوص برای طرح های پیچیده و پیچیده.
- محدودیت های طراحی: در حالی که قالبگیری تزریقی ترموپلاستیک انعطافپذیری طراحی را ارائه میدهد، محدودیتهای خاصی وجود دارد. به عنوان مثال، دستیابی به ضخامت دیواره یکنواخت در سراسر قطعه می تواند چالش برانگیز باشد و منجر به تغییرات در توزیع مواد و ضعف های ساختاری بالقوه شود. علاوه بر این، وجود برشها یا هندسههای پیچیده ممکن است نیاز به استفاده از ویژگیهای قالب اضافی یا عملیات ثانویه، افزایش هزینهها و زمان تولید داشته باشد.
- لانگ سرب تایمز:فرآیند طراحی و ساخت قالبها برای قالبگیری تزریقی میتواند زمانبر باشد و منجر به زمان طولانیتری برای توسعه محصول شود. فرآیند تکرار طراحی، تولید قالب و آزمایش میتواند زمان قابل توجهی را به جدول زمانی کلی تولید اضافه کند، که ممکن است برای پروژههایی با ضربالاجلهای محدود مناسب نباشد.
- محدودیت های انتخاب مواد:اگرچه قالبگیری تزریقی ترموپلاستیک طیف وسیعی از مواد را پشتیبانی میکند، اما محدودیتها و محدودیتهای خاصی وجود دارد. برخی از مواد ممکن است نیازهای پردازش خاصی داشته باشند یا در دسترس بودن محدود داشته باشند که بر انتخاب طراحی و انتخاب مواد برای یک کاربرد خاص تأثیر بگذارد.
- محدودیت های اندازه قطعه:ماشینهای قالبگیری تزریقی محدودیتهایی در اندازه دارند، هم از نظر اندازه فیزیکی دستگاه و هم اندازه قالبهایی که میتوانند در خود جای دهند. تولید قطعات عظیم ممکن است به تجهیزات تخصصی یا روش های ساخت جایگزین نیاز داشته باشد.
- اثرات زیست محیطی:در حالی که صنعت به سمت پایداری کار می کند، فرآیند قالب گیری تزریقی ترموپلاستیک همچنان مواد زائد از جمله قراضه و اسپرو تولید می کند. دفع صحیح و بازیافت این مواد برای به حداقل رساندن اثرات زیست محیطی ضروری است.
- پیچیدگی بهینه سازی فرآیند:دستیابی به پارامترهای فرآیند بهینه برای قالب گیری تزریقی ترموپلاستیک می تواند پیچیده و زمان بر باشد. سازندگان باید دما، فشار، نرخ های خنک کننده و زمان چرخه را به دقت کنترل و بهینه کنند تا از کیفیت ثابت قطعه اطمینان حاصل کنند و عیوب را به حداقل برسانند.
انواع ترموپلاستیک های مورد استفاده در قالب گیری تزریقی
اینها تنها چند نمونه از ترموپلاستیکهایی هستند که معمولاً در قالبگیری تزریقی استفاده میشوند. هر ماده دارای خواص منحصر به فردی است که آن را برای کاربردهای خاص بر اساس استحکام، انعطاف پذیری، مقاومت شیمیایی، شفافیت و هزینه مناسب می کند. هنگام انتخاب ترموپلاستیک مناسب برای پروژه های قالب گیری تزریقی، سازندگان باید این ویژگی ها و الزامات را در نظر بگیرند.
- پلی پروپیلن (PP):پلی پروپیلن یک ترموپلاستیک همه کاره است که معمولا در قالب گیری تزریقی استفاده می شود. مقاومت شیمیایی عالی، چگالی کم و مقاومت ضربه ای خوب را ارائه می دهد. PP (پلی پروپیلن) کاربردهای گسترده ای در بسته بندی، قطعات خودرو، لوازم خانگی و تجهیزات پزشکی دارد.
- پلی اتیلن (PE):پلی اتیلن یکی دیگر از ترموپلاستیک های پرکاربرد در قالب گیری تزریقی است. این در اشکال مختلف مانند پلی اتیلن با چگالی بالا (HDPE) و پلی اتیلن با چگالی کم (LDPE) موجود است. پلی اتیلن مقاومت شیمیایی، چقرمگی و انعطاف پذیری خوبی را ارائه می دهد و آن را برای بطری ها، ظروف و لوله ها مناسب می کند.
- پلی استایرن (PS):پلی استایرن یک ترموپلاستیک همه کاره است که به دلیل شفافیت، استحکام و مقرون به صرفه بودن شناخته شده است. در بسته بندی، کالاهای مصرفی و محصولات یکبار مصرف کاربرد رایجی دارد. PS (پلی استایرن) امکان پردازش سریع را فراهم می کند و ثبات ابعادی خوبی را فراهم می کند، اما می تواند شکننده باشد و در برابر ترک خوردگی استرس محیطی حساس باشد.
- اکریلونیتریل بوتادین استایرن (ABS): ABS یک ترموپلاستیک محبوب است که به دلیل مقاومت عالی در برابر ضربه و دوام شناخته شده است. این ترکیب خواص اکریلونیتریل، بوتادین و استایرن را برای ایجاد یک ماده همه کاره مناسب برای قطعات خودرو، محفظه های الکترونیکی و اسباب بازی ها ایجاد می کند.
- پلی وینیل کلراید (PVC): PVC یک ترموپلاستیک پرمصرف است که به دلیل مقاومت شیمیایی عالی، دوام و هزینه کم شناخته شده است. بسته به فرمولاسیون و مواد افزودنی مورد استفاده می تواند سفت یا انعطاف پذیر باشد. پی وی سی (پلی وینیل کلراید) در ساخت و ساز، عایق الکتریکی، محصولات بهداشتی و بسته بندی کاربرد رایج دارد.
- پلی کربنات (PC): پلی کربنات یک ترموپلاستیک شفاف با ضربه فوق العاده و مقاومت در برابر حرارت بالا است. در برنامه هایی که به وضوح نوری نیاز دارند، مانند اجزای خودرو، کلاه ایمنی و نمایشگرهای الکترونیکی، استفاده رایجی پیدا می کند.
- نایلون (پلی آمید):نایلون یک ترموپلاستیک قوی و بادوام است که به دلیل خواص مکانیکی عالی و مقاومت شیمیایی شناخته شده است. در کاربردهایی که به استحکام بالایی نیاز دارند، مانند قطعات خودرو، قطعات صنعتی و کالاهای مصرفی، کاربرد رایجی دارد.
- پلی اتیلن ترفتالات (PET):PET یک ترموپلاستیک محبوب برای تولید بطری ها، ظروف و مواد بسته بندی است. این شفافیت، مقاومت شیمیایی و خواص مانع را ارائه می دهد و آن را برای برنامه های غذایی و نوشیدنی مناسب می کند.
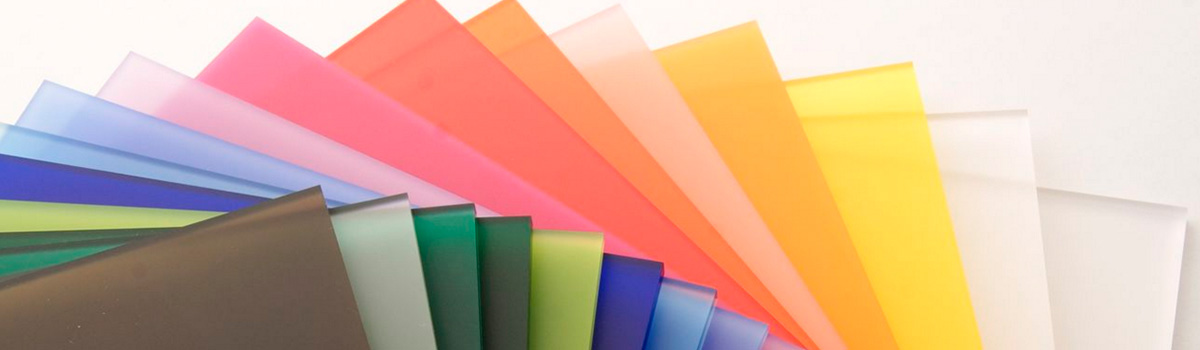
خواص ترموپلاستیک های مورد استفاده در قالب گیری تزریقی
این ویژگیهای ترموپلاستیکها نقش مهمی در تعیین مناسب بودن آنها برای کاربردهای قالبگیری تزریقی خاص دارند. سازندگان باید این ویژگی ها را به دقت در نظر بگیرند و بر اساس عملکرد مطلوب، شرایط محیطی و هزینه مورد نیاز، ترموپلاستیک مناسب را انتخاب کنند.
- ویژگی های مکانیکی:ترموپلاستیک های مورد استفاده در قالب گیری تزریقی می توانند خواص مکانیکی مختلفی از جمله مقاومت کششی، مقاومت در برابر ضربه و مقاومت خمشی را از خود نشان دهند. این ویژگی ها توانایی مواد را برای مقاومت در برابر نیروهای وارده و دوام کلی آن در کاربردهای مختلف تعیین می کند.
- مقاومت شیمیایی:بسیاری از ترموپلاستیک های مورد استفاده در قالب گیری تزریقی مقاومت قابل توجهی در برابر مواد شیمیایی، حلال ها و روغن ها دارند. این ویژگی برای کاربردهایی که شامل قرار گرفتن در معرض محیط های خشن یا مواد خورنده است، بسیار مهم است.
- پایداری حرارتی:پایداری حرارتی ترموپلاستیک ها به توانایی آنها در تحمل دماهای بالا بدون تخریب قابل توجه اشاره دارد. برخی از ترموپلاستیک ها مقاومت حرارتی بسیار خوبی از خود نشان می دهند و به آنها اجازه می دهد تا خواص مکانیکی خود را حتی در دماهای بالا حفظ کنند.
- خواص الکتریکی:ترموپلاستیک های مورد استفاده در قالب گیری تزریقی می توانند خواص الکتریکی خاصی از جمله عایق الکتریکی، رسانایی یا مقاومت دی الکتریک داشته باشند. این خواص برای کاربردها در صنایع الکتریکی و الکترونیکی ضروری است، جایی که مواد باید عملکرد الکتریکی قابل اعتمادی را ارائه دهند.
- شفافیت و شفافیت:برخی از ترموپلاستیکها، مانند پلی کربنات و PET، شفافیت و شفافیت فوقالعادهای را ارائه میدهند و برای کاربردهایی که نیاز به خواص نوری دارند، مناسب هستند. تولیدکنندگان معمولا از این مواد در محصولاتی مانند پنجره های شفاف، لنزها و نمایشگرها استفاده می کنند.
- انعطاف پذیری و استحکام: انعطافپذیری و چقرمگی از ویژگیهای ضروری ترموپلاستیکها هستند که در کاربردهایی که نیاز به مقاومت در برابر ضربه و دوام دارند استفاده میشوند. برخی از ترموپلاستیکها، مانند ABS و نایلون، چقرمگی بسیار خوبی دارند و به آنها اجازه میدهند در برابر ضربات مکرر بدون شکستگی مقاومت کنند.
- ثبات ابعادی:پایداری ابعادی به توانایی یک ترموپلاستیک برای حفظ شکل و اندازه خود در شرایط مختلف از جمله تغییرات دما اشاره دارد. مواد با ثبات ابعادی خوب، ابعاد قطعه را ثابت میکنند و خطر تاب برداشتن یا اعوجاج را به حداقل میرسانند.
- سازگاری شیمیایی:سازگاری شیمیایی ترموپلاستیک ها به توانایی آنها در مقاومت در برابر تخریب یا برهمکنش با مواد شیمیایی مختلف از جمله اسیدها، بازها و حلال ها اشاره دارد. برای اطمینان از عملکرد بهینه، انتخاب یک ترموپلاستیک که بتواند محیط شیمیایی خاصی را که در کاربرد مورد نظر با آن مواجه می شود، تحمل کند، ضروری است.
- دانسیته: ترموپلاستیک ها دارای ضخامت های متفاوتی هستند که می تواند بر وزن و ویژگی های کلی قطعه تاثیر بگذارد. مواد با چگالی کم، مانند پلی اتیلن، راه حل های سبک وزن ارائه می دهند، در حالی که مواد با چگالی بالا، مانند پلی پروپیلن، استحکام و استحکام بیشتری را ارائه می دهند.
فرآیند قالب گیری تزریقی: گام به گام
فرآیند قالب گیری تزریقی از این مراحل پیروی می کند و امکان تولید موثر و دقیق قطعات ترموپلاستیک با کیفیت بالا را فراهم می کند. هر مرحله نیاز به کنترل و نظارت دقیق دارد تا از ابعاد قطعه، خواص مواد و کیفیت کلی اطمینان حاصل شود.
- طراحی و ساخت قالب: اولین مرحله در فرآیند قالب گیری تزریقی، طراحی و ساخت قالب است. سازندگان برای دستیابی به مشخصات قطعه مورد نظر باید یک طراحی قالب دقیق و دقیق ایجاد کنند. سپس سازندگان قالب را با استفاده از تکنیک های مختلف مانند CNC یا ماشینکاری تخلیه الکتریکی (EDM) می سازند.
- آماده سازی مواد: مرحله بعدی آماده سازی پس از آماده شدن قالب است. گلوله ها یا گرانول های ترموپلاستیک بر اساس خواص مواد مورد نظر انتخاب شده و در قیف ذوب می شوند. سپس اپراتورها مواد را وارد بشکه دستگاه قالب گیری تزریقی می کنند، جایی که تحت ذوب و همگن شدن قرار می گیرد.
- تزریق:در طول مرحله تزریق، اپراتورها ترموپلاست مذاب را تحت فشار بالا به داخل حفره قالب تزریق می کنند. واحد تزریق دستگاه، مواد ذوب شده را از طریق یک نازل و به داخل قالب هل می دهد. این ماده حفره قالب را پر می کند و شکل قسمت مورد نظر را می گیرد.
- خنک سازی و انجماد:پس از پر کردن قالب، اپراتورها اجازه میدهند پلاستیک مذاب سرد و جامد شود. خنک سازی برای دستیابی به ثبات ابعادی و شکل گیری مناسب قطعه بسیار مهم است. اپراتورها می توانند فرآیند خنک سازی را با گردش مایع خنک کننده از طریق کانال های داخل قالب یا با استفاده از صفحات خنک کننده کنترل کنند.
- باز شدن و خروج قالب:اپراتورها قالب را باز می کنند و پس از جامد شدن پلاستیک، قطعه را از حفره قالب خارج می کنند. سیستم جهش داخل دستگاه از پین ها، صفحات اجکتور یا انفجارهای هوا برای حذف ناحیه از قالب استفاده می کند. سپس قالب برای چرخه تزریق بعدی آماده است.
- پس پردازش: پس از پرتاب، قطعه ممکن است تحت عملیات پس از پردازش، مانند برش، جداسازی، یا تکمیل سطح قرار گیرد. این مراحل به حذف مواد اضافی، صاف کردن لبه های ناهموار و بهبود ظاهر نهایی قطعه کمک می کند.
- بازرسی کیفیت: مرحله نهایی شامل بازرسی قطعات تزریق شده از نظر کیفیت و حصول اطمینان از مطابقت با الزامات مشخص شده است. تکنیکهای مختلف کنترل کیفیت، از جمله اندازهگیری ابعاد، بازرسی بصری، و آزمایش عملکردی، میتواند برای تأیید کیفیت و یکپارچگی قطعه مورد استفاده قرار گیرد.
- بازیافت و استفاده مجدد از مواد:هر گونه مواد اضافی یا ضایعاتی که در طی قالب گیری تزریقی تولید می شود، می تواند بازیافت و دوباره استفاده شود. کاهش استفاده از مواد ترموپلاستیک جدید به کاهش ضایعات و بهبود پایداری کمک می کند.
تجهیزات مورد استفاده در قالب گیری تزریقی
این اجزای تجهیزات فرآیند قالب گیری تزریقی را از ذوب و تزریق مواد ترموپلاستیک گرفته تا شکل دهی، خنک سازی و بیرون ریختن قسمت نهایی تسهیل می کنند. عملکرد و نگهداری صحیح این اجزای تجهیزات برای دستیابی به تولید قالب تزریقی کارآمد و با کیفیت بسیار مهم است.
- ماشین قالب گیری تزریقی:تجهیزات اولیه در قالب گیری تزریقی وظیفه ذوب مواد ترموپلاستیک، تزریق آن به قالب و کنترل فرآیند را بر عهده دارند.
- قالب: قالب که به صورت سفارشی برای ایجاد شکل و ویژگی های مورد نظر قسمت پلاستیکی طراحی شده است، از دو نیمه تشکیل شده است، حفره و هسته. اپراتورها آن را روی واحد گیره دستگاه قالب گیری تزریقی نصب می کنند.
- قیف:ظرفی که مواد ترموپلاستیک را به صورت پلت یا دانه ای نگه می دارد و برای ذوب و تزریق به داخل بشکه دستگاه قالب گیری تزریق می کند.
- بشکه و پیچ: بشکه، یک محفظه استوانه ای، مواد ترموپلاستیک را با چرخش پیچ درون آن ذوب و همگن می کند تا مواد را ذوب، مخلوط و استاندارد کند.
- سیستم های سرمایشی و گرمایشی:ماشینهای قالبگیری تزریقی دارای عناصر گرمایشی مانند بخاریهای برقی یا بخاریهایی هستند که از روغن داغ استفاده میکنند تا دمای بشکه را بالا ببرند و سیستمهای خنککننده مانند گردش آب یا روغن برای خنک کردن قالب و جامد کردن قسمت پلاستیکی.
- سیستم اجکتور:قسمت قالبگیری شده را پس از انجماد از حفره قالب خارج میکند، معمولاً از پینهای اجکتور، صفحات یا انفجارهای هوا در طول باز شدن قالب استفاده میکند.
- سیستم کنترل:پارامترهای مختلف فرآیند قالبگیری تزریقی را تحت نظر و کنترل میکند و به اپراتورها اجازه میدهد تا پارامترهایی مانند سرعت تزریق، دما، فشار و زمان خنکسازی را تنظیم و تنظیم کنند.
ماشین های قالب گیری تزریقی: انواع و ویژگی ها
هر نوع ماشین قالب گیری تزریقی ویژگی ها و مزایای خود را دارد که به تولید کنندگان این امکان را می دهد تا مناسب ترین دستگاه را برای نیازهای تولید خاص خود انتخاب کنند.
- ماشین های قالب گیری تزریقی هیدرولیک: این ماشین ها از سیستم های هیدرولیک برای ایجاد فشار لازم برای تزریق پلاستیک مذاب به داخل قالب استفاده می کنند. آنها به دلیل نیروی گیره بالا، کنترل دقیق و تطبیق پذیری در کار با ترموپلاستیک های مختلف شناخته شده اند. ماشین های هیدرولیک برای تولید در مقیاس بزرگ مناسب هستند و می توانند قالب های پیچیده را در خود جای دهند.
- ماشین های قالب گیری تزریقی الکتریکی:ماشین های الکتریکی از موتورهای سروو الکتریکی برای عملکرد ماشین استفاده می کنند، از جمله سیستم های تزریق، گیره و اجکتور. آنها کنترل دقیق، بهره وری انرژی و زمان پاسخ سریعتر را نسبت به ماشین های هیدرولیک ارائه می دهند. ماشین های الکتریکی برای کاربردهای قالب گیری دقیق که نیاز به تکرارپذیری و دقت بالایی دارند ایده آل هستند.
- ماشین های قالب گیری تزریقی هیبریدی:ماشین های هیبریدی مزایای هر دو دستگاه هیدرولیک و الکتریکی را با هم ترکیب می کنند. آنها از ترکیبی از سیستم های سروو هیدرولیک و الکتریکی برای دستیابی به دقت بالا، بهره وری انرژی و مقرون به صرفه استفاده می کنند. ماشین های هیبریدی برای طیف وسیعی از کاربردها مناسب هستند و تعادلی بین عملکرد و هزینه های عملیاتی ایجاد می کنند.
- ماشین های قالب گیری تزریقی دو صفحه ای: دستگاه های دو صفحه ای دارای طراحی منحصر به فرد با دو صفحه مجزا برای بستن قالب می باشند. این طراحی پایداری افزایش یافته، هماهنگ سازی قالب را بهبود می بخشد و امکان اندازه های قالب بزرگتر و نیروهای گیره بالاتر را فراهم می کند. ماشین های دو صفحه ای برای قطعات بزرگ و پیچیده که نیاز به قالب گیری دقیق دارند مناسب هستند.
- ماشین های قالب گیری تزریقی چند جزئی:سازندگان این ماشین ها را برای تولید قطعات با مواد یا رنگ های متعدد در یک چرخه قالب گیری طراحی می کنند. آنها دارای واحدها و قالب های تزریق مختلف هستند که امکان تزریق همزمان مواد مختلف را فراهم می کند. ماشین های چند جزئی انعطاف پذیری و کارایی را در ساخت قطعات پیچیده با ویژگی های متفاوت ارائه می دهند.
- ماشین های قالب گیری میکرو تزریق:ماشینهای قالبگیری میکرو تزریقی که بهطور خاص برای تولید قطعات کوچک و دقیق طراحی شدهاند، دقت و دقت فوقالعادهای را ارائه میکنند. آنها می توانند جزئیات پیچیده ای را با تلورانس های سخت و حداقل ضایعات مواد تولید کنند. وسایل الکترونیکی، تجهیزات پزشکی و میکرواپتیک معمولاً از ماشینهای قالبگیری تزریقی میکرو استفاده میکنند.
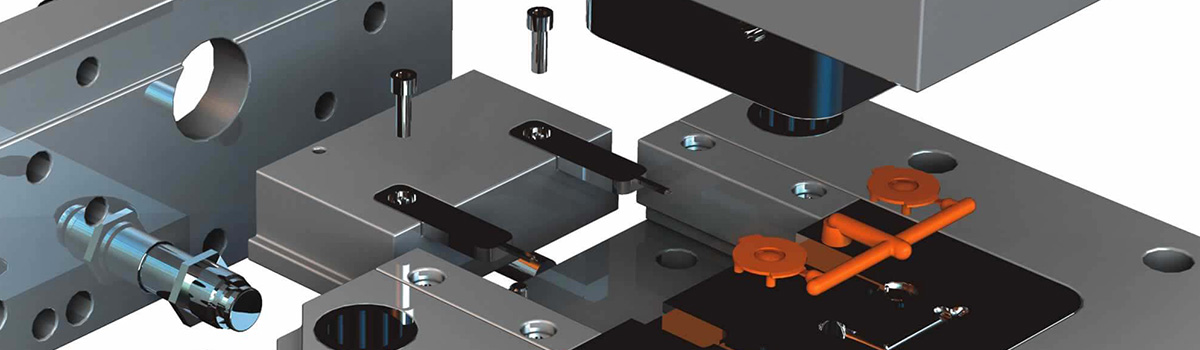
ملاحظات طراحی قالب برای قالب گیری تزریقی
ملاحظات دقیق طراحی قالب برای تولید موفقیت آمیز قالب گیری تزریقی ضروری است.
- طراحی قسمت:طراحی قالب باید الزامات خاص قطعه، از جمله شکل، ابعاد و ویژگی های عملکردی آن را در نظر بگیرد. سازندگان باید به درستی زوایای کشش، ضخامت دیوار، برش های زیرین و هر عنصر ضروری را برای اطمینان از سهولت تخلیه و کیفیت قطعه در نظر بگیرند.
- مواد قالب: انتخاب مواد قالب برای دستیابی به دوام، ثبات ابعادی و مقاومت در برابر حرارت بسیار مهم است. مواد قالب معمولی شامل آلیاژهای فولادی، آلیاژهای آلومینیومی و فولادهای ابزار هستند. انتخاب مواد به عواملی مانند حجم تولید، پیچیدگی قطعه و عمر ابزار مورد انتظار بستگی دارد.
- سیستم خنک کننده:خنک سازی کارآمد برای انجماد مناسب قطعه و به حداقل رساندن زمان چرخه ضروری است. طراحی قالب باید دارای کانال های خنک کننده یا درج های استراتژیک باشد تا از خنک شدن یکنواخت قالب اطمینان حاصل شود. خنک کننده مناسب خطر تاب خوردگی، انقباض و نقص قطعه را کاهش می دهد.
- دریچه:تهویه کافی برای خروج هوا و گازها در طول فرآیند تزریق ضروری است. تهویه ناکافی می تواند منجر به تله گاز، آثار سوختگی یا پر شدن ناقص قطعه شود. تولیدکنندگان میتوانند با استفاده از شیارهای هواکش، پینها یا مکانیسمهای دیگر در طراحی قالب به هواگیری دست یابند.
- سیستم تخلیه:طراحی قالب باید شامل یک سیستم تخلیه موثر باشد تا به طور ایمن و کارآمد قسمت قالب گیری شده را از حفره قالب جدا کند. سیستم پرتاب میتواند شامل پینهای اجکتور، آستینها یا مکانیسمهای دیگر باشد که به صورت استراتژیک برای جلوگیری از تداخل با عملکرد یا ویژگیهای حیاتی قرار دارند.
- طراحی دروازه:دروازه جایی است که پلاستیک مذاب وارد حفره قالب می شود. طراحی دروازه باید از پر شدن مناسب قطعات اطمینان حاصل کند، خطوط جریان را به حداقل برساند و از یخ زدگی زودرس مواد جلوگیری کند. طراحیهای استاندارد دروازه شامل دروازههای لبه، دروازههای تونل و سیستمهای دونده داغ، بسته به نیاز قطعه و خواص مواد است.
- خط فراق:طراحی قالب باید یک خط جداسازی مناسب را مشخص کند که همان خطی است که دو نیمه قالب به هم می رسند. قرارگیری مناسب خط جداکننده، حداقل عدم تطابق فلاش و خط جداکننده را تضمین میکند و مونتاژ کارآمد قالب را تسهیل میکند.
- تعمیر و نگهداری قالب و قابلیت سرویس دهی: تولیدکنندگان باید سهولت تعمیر و نگهداری، تعمیر و سرویس قالب را در نظر بگیرند. اجزای قالب باید برای تمیز کردن، بازرسی و تعویض به راحتی در دسترس باشند. ترکیب ویژگی هایی مانند درج های با تغییر سریع یا طرح های قالب مدولار می تواند قابلیت سرویس دهی قالب را بهبود بخشد.
مواد قالب مورد استفاده در قالب گیری تزریقی
همکاری با متخصصان مواد قالب و در نظر گرفتن نیازهای خاص کاربرد قالب می تواند به تعیین مناسب ترین ماده برای دستیابی به عملکرد مطلوب قالب و کیفیت قطعه کمک کند.
- آلیاژهای فولادی: آلیاژهای فولادی مانند فولادهای ابزار (به عنوان مثال، P20، H13) و فولادهای ضد زنگ، به دلیل دوام عالی، مقاومت در برابر حرارت و مقاومت در برابر سایش، معمولاً برای قالبهای قالبگیری تزریقی استفاده میشوند. این مواد می توانند دماها و فشارهای بالا در فرآیند قالب گیری تزریقی را تحمل کنند و ثبات ابعادی خوبی را برای تولید قطعات با کیفیت بالا ارائه دهند.
- آلیاژهای آلومینیوم:آلیاژهای آلومینیوم، مانند 7075 و 6061، سبک وزن هستند و رسانایی حرارتی خوبی دارند و برای قالب هایی که نیاز به خنک کننده کارآمد دارند، مناسب هستند. سازندگان اغلب از قالب های آلومینیومی برای نمونه سازی، تولید کم حجم یا کاربردهایی که کاهش وزن حیاتی است استفاده می کنند. با این حال، قالب های آلومینیومی ممکن است دوام کمتری در مقایسه با آلیاژهای فولادی داشته باشند.
- آلیاژهای مس:آلیاژهای مس، مانند مس بریلیوم، هدایت حرارتی بالا و ماشین کاری خوبی را نشان می دهند. آنها در قالب هایی استفاده می شوند که به انتقال حرارت عالی برای خنک سازی موثر نیاز دارند. آلیاژهای مس میتوانند با دفع سریع گرما از قسمت قالبگیری شده، به کاهش زمان چرخه کمک کنند و در نتیجه انجماد سریعتر انجام شود.
- فولادهای ابزار:فولادهای ابزار، از جمله H13، S7 و D2، برای کاربردهای ابزارسازی با کارایی بالا طراحی شدهاند. این فولادها ترکیبی از استحکام، سختی و مقاومت در برابر سایش بالا را ارائه می دهند. فولادهای ابزار مناسب قالب هایی با حجم تولید بالا، مواد ساینده یا شرایط قالب گیری سخت هستند.
- آلیاژهای نیکل:آلیاژهای نیکل مانند Inconel و Hastelloy به دلیل مقاومت در برابر خوردگی استثنایی، استحکام در دمای بالا و پایداری حرارتی معروف هستند. سازندگان از این آلیاژها در قالب هایی استفاده می کنند که مواد خورنده را مدیریت می کنند یا به مقاومت در برابر دماهای شدید و محیط های قالب گیری تهاجمی نیاز دارند.
- مواد کامپوزیت:مواد کامپوزیت، مانند پلاستیک های تقویت شده یا کامپوزیت ها با درج های فلزی، گهگاه برای کاربردهای قالب گیری خاص استفاده می شوند. این مواد دارای تعادلی از خواص مانند استحکام بالا، پایداری حرارتی و کاهش وزن هستند. قالب های کامپوزیتی می توانند جایگزین های مقرون به صرفه ای برای نیازهای تولید خاص باشند.
انواع قالب های تزریق
قالب گیری تزریقی یک فرآیند تولید همه کاره و پرکاربرد برای قطعات پلاستیکی است.
- قالب دو صفحه ای:قالب دو صفحه ای رایج ترین نوع قالب تزریقی است. از دو صفحه، صفحه حفره و صفحه هسته تشکیل شده است که برای خروج قسمت قالب گیری شده از هم جدا می شوند. صفحه حفره شامل سمت حفره قالب است، در حالی که صفحه هسته سمت هسته را در خود جای می دهد. سازندگان به دلیل طراحی نسبتا ساده از قالب های دو صفحه ای برای تولید طیف وسیعی از قطعات استفاده می کنند.
- قالب سه صفحه ای:قالب سه صفحه ای نسخه پیشرفته قالب دو صفحه ای است. این شامل یک صفحه اضافی، رانر یا صفحه اسپرو است. صفحه رانر یک کانال مجزا برای اسپرو، رانرها و دروازهها ایجاد میکند که امکان جداسازی آسانتر قسمت قالبگیری شده را فراهم میکند. سازندگان معمولاً از قالبهای سه صفحهای برای جزئیات با سیستمهای دروازهای پیچیده یا زمانی که اجتناب از بقایای دروازه روی قطعه مطلوب است، استفاده میکنند.
- قالب دونده داغ:سیستم رانر و گیت در قالب های رانر داغ گرم می شود و نیاز به انجماد و ذوب مجدد مواد در طول هر چرخه را از بین می برد. سیستم دونده داغ شامل منیفولدهای گرم شده و نازل هایی است که حالت مذاب پلاستیک را حفظ می کند. قالب های دونده داغ مزایایی مانند کاهش زمان چرخه، ضایعات کمتر مواد و بهبود کیفیت قطعه با به حداقل رساندن بقایای دروازه ارائه می دهند.
- قالب دونده سرد: قالبهای دونده سرد دارای یک سیستم دونده و دروازه سنتی هستند که در آن پلاستیک مذاب از طریق دوندههای سرد جریان مییابد که با هر چرخه جامد میشوند. متعاقباً اپراتورها رانرهای جامد شده را حذف میکنند که منجر به ضایعات مواد میشود. تولیدکنندگان معمولاً از قالبهای دونده پیچیده برای تولید با حجم کمتر یا زمانی که هزینههای مواد به دلیل طراحی سادهتر آنها حیاتیتر است، استفاده میکنند.
- درج قالب:قالبهای درج شامل درجهای فلزی یا پلاستیکی در حفره قالب در طول قالبگیری تزریقی است. درج ها را می توان از قبل در قالب قرار داد یا با فرآیندهای خودکار وارد کرد. این قالب امکان ادغام اجزای اضافی یا عناصر تقویتکننده را در قسمت قالبگیری شده فراهم میکند و عملکرد یا استحکام آن را افزایش میدهد.
- قالب بیش از حد: قالب گیری بیش از حد شامل قالب گیری یک ماده بر روی ماده دیگر است که معمولاً یک بستر پلاستیکی سفت و سخت را با یک الاستومر نرم تر یا ترموپلاستیک پیوند می دهد. این فرآیند امکان ایجاد قطعاتی با مواد یا بافت های متعدد را در یک قالب واحد فراهم می کند که چسبندگی، بالشتک یا ویژگی های زیبایی شناختی را بهبود می بخشد.
عوامل موثر بر هزینه های قالب گیری تزریقی
در نظر گرفتن این عوامل میتواند به تولیدکنندگان کمک کند تا هزینه قالبگیری تزریقی را تخمین زده و بهینه کنند و از تعادل بین کیفیت، کارایی و مقرون به صرفه بودن برای الزامات تولید خاص خود اطمینان حاصل کنند.
- پیچیدگی قسمت:پیچیدگی طراحی قطعه نقش بسزایی در تعیین هزینه قالب گیری تزریقی دارد. هندسه های پیچیده، زیر برش ها، دیوارهای نازک یا ویژگی های پیچیده ممکن است به ابزار اضافی، قالب های تخصصی یا چرخه های طولانی تر نیاز داشته باشند که هزینه کلی تولید را افزایش می دهد.
- انتخاب مواد:انتخاب مواد ترموپلاستیک بر هزینه قالب گیری تزریقی تأثیر می گذارد. مواد مختلف قیمتهای متفاوتی در هر کیلوگرم دارند و عواملی مانند در دسترس بودن مواد، خواص و نیازهای پردازش میتوانند بر هزینه کلی مواد تأثیر بگذارند.
- طراحی ابزار و قالب: هزینه های اولیه ابزار و طراحی قالب در هزینه های قالب گیری تزریقی قابل توجه است. عواملی مانند پیچیدگی قالب، تعداد حفره ها، اندازه قالب و مواد قالب در هزینه های ابزار و ساخت قالب نقش دارند. قالب های پیچیده تر یا قالب هایی که به ویژگی های پیشرفته نیاز دارند می توانند سرمایه گذاری اولیه را افزایش دهند.
- حجم تولید: حجم تولید مستقیماً بر هزینه هر قطعه در قالب گیری تزریقی تأثیر می گذارد. کتابهای بالاتر اغلب منجر به صرفهجویی در مقیاس میشوند و هزینه هر قطعه را کاهش میدهند. برعکس، دورههای تولید با حجم کم ممکن است هزینههای بیشتری را به دلیل راهاندازی، ابزارآلات و ضایعات مواد متحمل شوند.
- زمان چرخه: زمان چرخه، که شامل فازهای خنک کننده و جهش است، بر ظرفیت تولید و هزینه کلی تأثیر می گذارد. زمان چرخه طولانی تر منجر به کاهش بازده تولید و قیمت های بالقوه بالاتر می شود. بهینه سازی طراحی قالب، سیستم خنک کننده و پارامترهای فرآیند می تواند زمان چرخه را به حداقل برساند و کارایی را بهبود بخشد.
- الزامات کیفیت:الزامات کیفیت دقیق یا گواهینامه های خاص می تواند بر هزینه قالب گیری تزریقی تأثیر بگذارد. برآورده کردن تلورانسهای دقیق، الزامات پرداخت سطح یا آزمایشهای اضافی ممکن است به منابع، فرآیندها یا بازرسیهای دیگری نیاز داشته باشد که به هزینه کلی میافزاید.
- عملیات ثانویه:اگر قطعات قالبگیری شده به عملیات پس از پردازش مانند مونتاژ، رنگآمیزی یا مراحل تکمیلی اضافی نیاز داشته باشند، این عملیات میتواند به هزینه کلی قالبگیری تزریقی اضافه کند.
- تامین کننده و مکان:انتخاب تامین کننده قالب تزریق و محل آنها می تواند بر هزینه ها تأثیر بگذارد. هزینه های نیروی کار، سربار، لجستیک و هزینه های حمل و نقل بر اساس محل تامین کننده متفاوت است و بر هزینه کلی تولید تاثیر می گذارد.
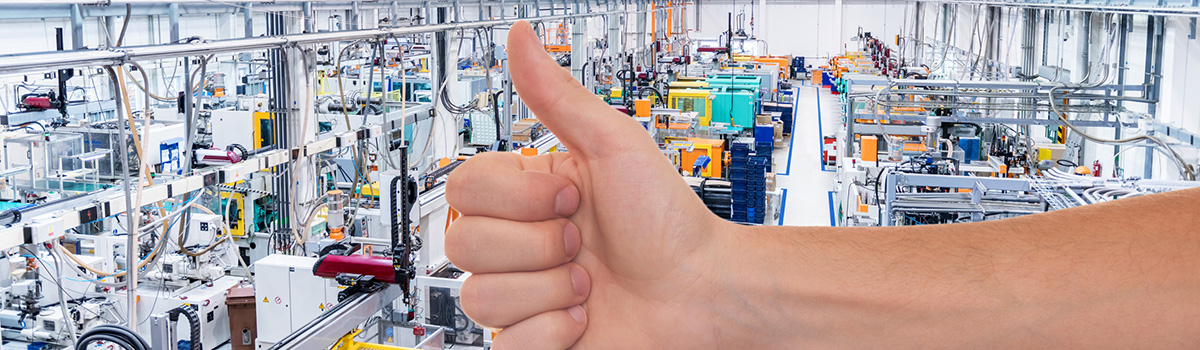
کنترل کیفیت در قالب گیری تزریقی
اجرای اقدامات کنترل کیفیت قوی در طول فرآیند قالب گیری تزریقی به شناسایی و رفع عیوب، انحرافات یا ناسازگاری های احتمالی کمک می کند و از تولید قطعات با کیفیت بالا که مشخصات و نیازهای مشتری را برآورده می کند، اطمینان حاصل می کند.
- نظارت بر فرآیند: نظارت مداوم بر پارامترهای کلیدی فرآیند، مانند دمای مذاب، فشار تزریق، زمان خنکسازی و زمان چرخه، ثبات و تکرارپذیری را در تولید قطعه تضمین میکند. مانیتورینگ بلادرنگ و سیستمهای خودکار میتوانند تغییرات یا انحرافات از پارامترهای تنظیمشده را تشخیص دهند و امکان تنظیمات به موقع و حفظ ثبات فرآیند را فراهم کنند.
- بازرسی و اندازه گیری:بررسی و اندازهگیری منظم قطعات قالبگیری شده برای تأیید صحت ابعاد، کیفیت قطعه و رعایت مشخصات ضروری است. خدمات ما طیف وسیعی از روش های کنترل کیفیت مانند اندازه گیری ابعاد، تجزیه و تحلیل کیفیت سطح، انجام بازرسی های بصری و انجام تست های عملکردی را پوشش می دهد. تکنیک های مختلف بازرسی، مانند ماشین های اندازه گیری مختصات (CMM) و سیستم های بازرسی نوری و بصری، برای ارزیابی دقیق استفاده می شود.
- کنترل فرآیند آماری (SPC): SPC شامل جمع آوری و تجزیه و تحلیل داده های فرآیند برای نظارت و کنترل کیفیت قالب گیری تزریقی است. روش های آماری، مانند نمودارهای کنترل و تجزیه و تحلیل قابلیت فرآیند، به شناسایی روندها، شناسایی تغییرات فرآیند و اطمینان از باقی ماندن فرآیند در محدوده های کنترلی تعریف شده کمک می کند. SPC شناسایی فعال مسائل را امکان پذیر می کند و بهینه سازی فرآیند را تسهیل می کند.
- تست مواد: آزمایش مواد اولیه مانند ترموپلاستیک ها، افزودنی ها و رنگ ها، کیفیت و مناسب بودن آنها را برای قالب گیری تزریقی تضمین می کند. آزمایش مواد ممکن است شامل تجزیه و تحلیل شاخص جریان مذاب (MFI)، خواص مکانیکی، مشخصات حرارتی و ترکیب مواد باشد. بررسی کیفیت مواد به جلوگیری از نقص و ناهماهنگی در قطعات قالبگیری شده کمک میکند.
- تعمیر و نگهداری و بازرسی ابزار:نگهداری مناسب و بازرسی منظم قالب های تزریق برای اطمینان از کیفیت در قالب گیری تزریقی بسیار مهم است. تمیز کردن منظم، روغن کاری و ارزیابی اجزای قالب به جلوگیری از سایش، آسیب یا تخریب که می تواند بر کیفیت قطعه تأثیر بگذارد کمک می کند. تعمیر یا تعویض به موقع اجزای قالب فرسوده یا آسیب دیده برای حفظ عملکرد قالب گیری سازگار ضروری است.
- اسناد و قابلیت ردیابی:نگهداری اسناد جامع و سوابق ردیابی برای کنترل کیفیت در قالب گیری تزریقی ضروری است. ثبت پارامترهای فرآیند، نتایج بازرسی، اطلاعات مواد و هرگونه تغییر یا تنظیمی که در طول تولید انجام شده است، حیاتی است. اسناد مناسب ردیابی قطعات را امکان پذیر می کند، تجزیه و تحلیل علت اصلی را تسهیل می کند و ثبات کیفیت را تضمین می کند.
- آموزش و پرورش مهارت: ارائه آموزش و برنامه های توسعه مهارت کافی برای اپراتورها، تکنسین ها و پرسنل کنترل کیفیت، درک آنها از فرآیندهای قالب گیری تزریقی، الزامات کیفیت و تکنیک های بازرسی را افزایش می دهد. پرسنل آموزش دیده می توانند عیوب را تشخیص دهند، مشکلات را عیب یابی کنند و اقدامات اصلاحی را به طور موثر اجرا کنند و از تولید با کیفیت بالا اطمینان حاصل کنند.
نقص های رایج قالب گیری تزریقی و نحوه جلوگیری از آنها
بازرسی، نظارت و تجزیه و تحلیل منظم فرآیندهای قالب گیری تزریقی و نگهداری و تنظیم مناسب تجهیزات و قالب ها می تواند به شناسایی و رفع این عیوب رایج کمک کند.
- علائم سینک:علائم سینک فرورفتگی یا فرورفتگی روی سطح قطعه قالبگیری شده است که در اثر سرد شدن یا انقباض ناهموار ایجاد میشود. باید محل و طراحی مناسب دروازه، طراحی بهینه سیستم خنک کننده و توزیع یکنواخت ضخامت دیواره را برای جلوگیری از آثار سینک در نظر گرفت. افزایش فشار تزریق یا تنظیم زمان خنکسازی نیز میتواند به به حداقل رساندن علائم سینک کمک کند.
- Warpage:Warpage به تغییر شکل یا خم شدن یک قطعه قالبگیری شده پس از بیرون ریختن در اثر سرمایش ناهموار یا تنشهای پسماند اشاره دارد. حفظ ضخامت دیواره یکنواخت، استفاده از کانال های خنک کننده مناسب و اطمینان از پر شدن و بسته بندی متعادل قالب برای جلوگیری از تاب برداشتن بسیار مهم است. بهینه سازی دمای قالب، استفاده از زوایای کشش مناسب و کنترل دمای مواد و سرعت تزریق می تواند به به حداقل رساندن تاب خوردگی کمک کند.
- برق زدن:فلاش زمانی اتفاق میافتد که مواد اضافی به داخل خط جداکننده قالب جریان مییابد و منجر به برآمدگیهای نازک و ناخواسته یا مواد اضافی روی قسمت نهایی میشود. با حصول اطمینان از طراحی مناسب قالب، از جمله اعمال نیروی گیره کافی، هم ترازی دقیق و استفاده از تکنیک های تهویه مناسب، می توان به طور موثری از فلاش جلوگیری کرد. بهینه سازی پارامترهای فرآیند مانند فشار تزریق، دما و زمان چرخه فلاش را کاهش می دهد.
- شلیک کوتاه:یک شات سریع زمانی اتفاق می افتد که مواد تزریق شده حفره قالب را پر نمی کند و در نتیجه یک قسمت ناقص ایجاد می شود. انتخاب مناسب مواد، اطمینان از دمای مذاب و ویسکوزیته مناسب، و حفظ فشار و زمان تزریق مناسب برای جلوگیری از عکسهای کوتاه ضروری است. علاوه بر این، تأیید طراحی قالب برای اندازه کافی دونده و دروازه و تهویه مناسب می تواند به جلوگیری از شلیک سریع کمک کند.
- خطوط جوش:خطوط جوش زمانی رخ می دهند که دو یا چند جبهه جریان مواد مذاب به هم می رسند و جامد می شوند و در نتیجه یک خط یا علامت قابل مشاهده روی سطح قطعه ایجاد می شود. طراحی خوب دروازه و دونده، دمای مذاب بهینه، سرعت تزریق، و تنظیم جریان مواد و هندسه قطعات می تواند خطوط جوش را به حداقل برساند. تجزیه و تحلیل جریان قالب و بهینه سازی قرارگیری دروازه نیز می تواند به جلوگیری یا کاهش خطوط جوش کمک کند.
- علائم سوختگی:علائم سوختگی تغییر رنگ یا لکه های سیاه روی سطح قطعه قالب گیری شده است که در اثر گرمای بیش از حد یا گرم شدن بیش از حد مواد ایجاد می شود. اجتناب از دمای مذاب شدید، استفاده از کانال های خنک کننده مناسب و بهینه سازی زمان چرخه می تواند به جلوگیری از علائم سوختگی کمک کند. تهویه مناسب، طراحی مناسب دروازه و کنترل دمای قالب نیز به به حداقل رساندن علائم سوختگی کمک می کند.
عملیات پس از قالب گیری: تکمیل و مونتاژ
پس از قالبگیری تزریقی، بسیاری از قطعات قالبگیری شده ممکن است به عملیات تکمیلی و مونتاژ اضافی برای دستیابی به محصول نهایی مورد نظر نیاز داشته باشند. این عملیات پس از قالب گیری ممکن است شامل موارد زیر باشد:
- پیرایش:هر گونه مواد اضافی یا فلاش را در اطراف قسمت قالب گیری شده با استفاده از ابزارهای برش یا برش بردارید.
- سطح درمان:بهبود ظاهر یا عملکرد سطح قطعه با استفاده از تکنیک های مختلف مانند رنگ آمیزی، پوشش یا بافت.
- مجمع:اتصال چندین قطعه قالبگیری شده یا افزودن اجزایی مانند اتصال دهندهها، درجها یا برچسبها برای تکمیل محصول نهایی.
- آزمایش کردن:تأیید کیفیت و عملکرد قطعه از طریق روشهای مختلف آزمایش مانند آنالیز ابعادی، آزمایش خواص مواد یا آزمایش عملکرد.
- بسته بندی و حمل و نقل:بسته بندی و برچسب گذاری مناسب محصول نهایی برای ارسال به مشتریان یا کاربران نهایی.
انتخاب عملیات پس از قالب گیری به کاربرد خاص و ویژگی های محصول نهایی مورد نظر بستگی دارد. همکاری نزدیک بین کارشناسان قالبگیری تزریقی، متخصصان تکمیل و مونتاژ، و مشتری برای دستیابی به کیفیت و عملکرد مطلق محصول ضروری است. برنامه ریزی مناسب و ادغام عملیات پس از قالب گیری در فرآیند تولید می تواند به اطمینان از تولید کارآمد و تحویل به موقع محصولات با کیفیت بالا کمک کند.
قالب گیری تزریقی در مقابل سایر فرآیندهای تولید پلاستیک
هر فرآیند تولید پلاستیک دارای مزایا و محدودیت هایی است که آنها را برای کاربردهای مختلف مناسب می کند.
- قالب گیری تزریقی: قالب گیری تزریقی یک فرآیند تولید بسیار متنوع و پرکاربرد برای تولید قطعات پلاستیکی است. مزایایی مانند راندمان تولید بالا، تکثیر دقیق قطعات و توانایی ایجاد هندسه های پیچیده را ارائه می دهد. قالب گیری تزریقی برای دوره های تولید با حجم بالا مناسب است و امکان استفاده از طیف گسترده ای از مواد ترموپلاستیک را فراهم می کند. دقت ابعادی و پرداخت سطح عالی را ارائه می دهد و برای صنایع مختلف مانند خودروسازی، کالاهای مصرفی و تجهیزات پزشکی ایده آل است.
- قالب گیری دمشی: قالب گیری دمشی فرآیندی است که عمدتاً برای تولید قطعات پلاستیکی توخالی مانند بطری ها، ظروف و اجزای خودرو استفاده می شود. این شامل ذوب پلاستیک و باد کردن آن در یک حفره قالب است و شکل مورد نظر را ایجاد می کند. قالب گیری دمشی برای تولید در حجم بالا مناسب است و می تواند قطعات بزرگ و سبک وزن با ضخامت دیواره یکنواخت تولید کند. با این حال، از نظر پیچیدگی قطعات و انتخاب مواد در مقایسه با قالب گیری تزریقی محدود است.
- ترموفرمینگ:ترموفرمینگ فرآیندی است که برای تولید قطعات پلاستیکی با گرم کردن ورق ترموپلاستیک و شکل دادن به آن با استفاده از قالبها یا شکلدهی خلاء استفاده میشود. در بسته بندی، محصولات یکبار مصرف و محصولات در مقیاس بزرگ مانند سینی ها و روکش ها کاربرد رایجی دارد. Thermoforming تولید مقرون به صرفه ای را برای قطعات بزرگ ارائه می دهد و امکان نمونه سازی سریع را فراهم می کند. با این حال، در مقایسه با قالب گیری تزریقی، محدودیت هایی در مورد پیچیدگی قطعه، انتخاب مواد و دقت ابعادی دارد.
- اکستروژن:اکستروژن یک فرآیند مداوم برای تولید پروفیل های پلاستیکی، ورق ها، لوله ها و فیلم ها است. این شامل ذوب رزین پلاستیکی و عبور دادن آن از طریق قالب برای ایجاد شکل مورد نظر است. اکستروژن برای تولید محصولات پلاستیکی با طول های طولانی و پیوسته با سطح مقطع ثابت مناسب است. در حالی که اکستروژن نرخ تولید بالا و مقرون به صرفه بودن را ارائه می دهد، از نظر هندسه قطعات پیچیده و کنترل ابعادی دقیق در مقایسه با قالب گیری تزریقی محدود است.
- قالب گیری فشاری:قالبگیری فشاری شامل قرار دادن مقداری از مواد ترموست از پیش اندازهگیری شده در یک حفره قالب گرم شده و فشرده کردن آن تحت فشار بالا تا زمانی است که خشک شود. در تولید قطعات با استحکام و پایداری ابعادی بالا، مانند قطعات خودرو و عایق الکتریکی، کاربرد رایجی دارد. قالبگیری فشاری قوام بخش خوب، راندمان تولید بالا و توانایی استفاده از طیف وسیعی از مواد را ارائه میدهد. با این حال، از نظر پیچیدگی قطعه و زمان چرخه در مقایسه با قالب گیری تزریقی محدود است.
کاربردهای قالب گیری تزریقی ترموپلاستیک
صنایع مختلف به دلیل تطبیق پذیری، کارایی و مقرون به صرفه بودن، از قالب گیری تزریقی ترموپلاستیک استفاده می کنند. برخی از کاربردهای قالب گیری تزریقی ترموپلاستیک عبارتند از:
- صنعت خودرو: صنعت خودرو به طور گسترده ای از قالب گیری تزریقی ترموپلاستیک برای تولید اجزای مختلف از جمله تزئینات داخلی و خارجی، داشبورد، پانل درها، ضربه گیرها و اتصالات الکتریکی استفاده می کند. این فرآیند امکان تکثیر دقیق قطعات، هندسه های پیچیده و مواد سبک وزن، بهبود بهره وری سوخت و انعطاف پذیری طراحی را فراهم می کند.
- کالاهای مصرفی:قالب گیری تزریقی کاربردهای گسترده ای در تولید کالاهای مصرفی مانند لوازم خانگی، دستگاه های الکترونیکی، ظروف بسته بندی و اسباب بازی ها پیدا می کند. این فرآیند تولید انبوه محصولات بادوام و باکیفیت با ابعاد ثابت و پرداخت سطح را امکان پذیر می کند. همچنین امکان سفارشی سازی و تکرار سریع محصول را فراهم می کند.
- تجهیزات پزشکی:قالبگیری تزریقی نقش مهمی در صنعت پزشکی برای تولید طیف وسیعی از دستگاهها از جمله سرنگها، ابزار جراحی، قطعات قابل کاشت و سیستمهای تحویل دارو ایفا میکند. این فرآیند تولید قطعات استریل، دقیق و زیست سازگار را تضمین می کند که الزامات نظارتی سختگیرانه بخش مراقبت های بهداشتی را برآورده می کند.
- صنایع الکترونیک و برق:صنعت الکترونیک از قالبگیری تزریقی برای تولید اتصالات الکتریکی، محفظهها، سوئیچها و سایر قطعات استفاده میکند. این فرآیند دقت ابعادی بالا، پرداخت سطح عالی، و توانایی ترکیب ویژگیهایی مانند قالبگیری و قالبگیری بیش از حد را ارائه میدهد که امکان تولید کارآمد مجموعههای الکترونیکی پیچیده را فراهم میکند.
- صنعت بسته بندی:صنایع مختلف، از جمله مواد غذایی و نوشیدنی، داروسازی و مراقبت های شخصی، معمولاً از قالب گیری تزریقی برای تولید ظروف بسته بندی پلاستیکی، درپوش ها، درب ها و بطری ها استفاده می کنند. این فرآیند امکان ایجاد راهحلهای بستهبندی سبک، بادوام و جذاب با چرخههای تولید کارآمد را فراهم میآورد.
- صنعت هوافضا:بخش هوافضا از قالبگیری تزریقی برای تولید قطعات سبک وزن و با کارایی بالا مانند کانالهای هوا، براکتها، پانلهای داخلی و قطعات ساختاری استفاده میکند. این فرآیند امکان استفاده از مواد پیشرفته و هندسه های پیچیده قطعات را فراهم می کند که به کاهش وزن و بهبود بهره وری سوخت کمک می کند.
تاثیر زیست محیطی قالب گیری تزریقی ترموپلاستیک
قالبگیری تزریقی ترموپلاستیک به دلیل مزایای فراوانی که دارد، یک فرآیند تولید محبوب است، اما در نظر گرفتن اثرات زیستمحیطی آن نیز ضروری است. در اینجا چند نکته وجود دارد که باید مورد توجه قرار گیرد:
- بهره وری مواد:قالب گیری تزریقی ترموپلاستیک با به حداقل رساندن ضایعات، کارایی مواد را افزایش می دهد. این فرآیند از کنترل دقیقی بر میزان مواد تزریق شده به قالب استفاده می کند و نیاز به مواد اضافی را کاهش می دهد. تولیدکنندگان همچنین میتوانند از تکنیکهای آسیاب مجدد و بازیافت برای استفاده مجدد از ضایعات یا قطعات رد شده استفاده کنند و ضایعات مواد را کاهش دهند.
- مصرف انرژی:تولیدکنندگان ماشینهای قالبگیری تزریقی را به گونهای طراحی میکنند که از نظر انرژی کارآمد باشند، با مدلهای مدرن که از فناوریهای پیشرفتهای مانند موتورهای سروو و درایوهای سرعت متغیر استفاده میکنند. این ویژگی ها با کاهش مصرف انرژی در طول قالب گیری، مصرف انرژی را بهینه می کند و در نتیجه نیاز به انرژی کمتر و اثرات زیست محیطی را کاهش می دهد.
- مدیریت پسماند:در حالی که ضایعات مواد را به حداقل میرسانند، تولیدکنندگان باید شیوههای مدیریت ضایعات مناسب را برای رسیدگی به مواد باقیمانده، اسپروها یا رانرها اجرا کنند. تولیدکنندگان میتوانند برنامههای بازیافتی را برای جمعآوری و استفاده مجدد از زبالههای پلاستیکی تولید شده در طی قالبگیری تزریقی ایجاد کنند و در نتیجه زبالههای ارسالی به محلهای دفن زباله را کاهش دهند.
- کاهش انتشار: قالبگیری تزریقی ترموپلاستیک معمولاً انتشار کمتری نسبت به سایر فرآیندهای تولید ایجاد میکند. تولیدکنندگان می توانند با استفاده از مواد سازگار با محیط زیست، پیاده سازی تجهیزات کم مصرف، و استفاده از سیستم های اگزوز و فیلتراسیون پیشرفته، انتشار گازهای گلخانه ای را کاهش دهند.
- انتخاب مواد پایدار:انتخاب مواد ترموپلاستیک می تواند به طور قابل توجهی بر پایداری محیطی قالب گیری تزریقی تأثیر بگذارد. انتخاب پلاستیک های زیست تخریب پذیر یا زیستی، و همچنین مواد بازیافتی یا قابل بازیافت، می تواند به کاهش ردپای کلی اکولوژیکی این فرآیند کمک کند.
ملاحظات چرخه عمر: در نظر گرفتن کل چرخه عمر محصول قالب گیری شده برای ارزیابی اثرات زیست محیطی آن ضروری است. در طول مراحل طراحی و انتخاب مواد، سازندگان باید عواملی مانند دوام قطعه، قابلیت بازیافت آن، و احتمال دفع یا استفاده مجدد در پایان عمر را در نظر بگیرند.
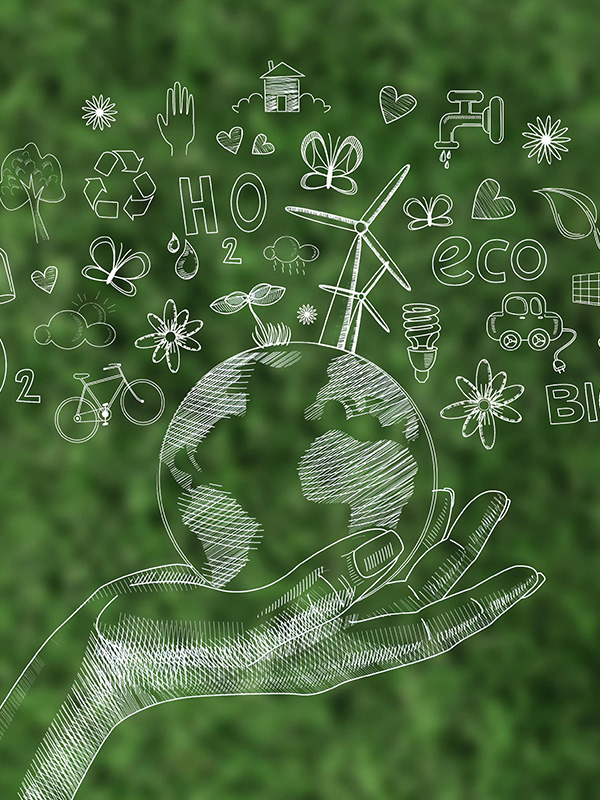
آینده قالب گیری تزریقی ترموپلاستیک
آینده قالبگیری تزریقی ترموپلاستیک، با پیشرفتهای مداوم در فناوری و افزایش تقاضا برای قطعات باکیفیت و دقیق در صنایع مختلف، امیدوارکننده به نظر میرسد. برخی از تحولات کلیدی مورد انتظار در سال های آینده عبارتند از:
- افزایش استفاده از اتوماسیون و رباتیک برای بهبود کارایی و کاهش هزینه ها.
- تلاش ها بر روی توسعه مواد و فرآیندهای جدید برای بهبود عملکرد قطعه و فعال کردن برنامه های کاربردی جدید متمرکز است.
- این یک پذیرش رو به رشد از شیوه های پایدار است، مانند استفاده از مواد بازیافتی و بهینه سازی مصرف انرژی، برای کاهش اثرات زیست محیطی قالب گیری تزریقی.
- ادغام بیشتر فناوری های دیجیتال، مانند پرینت سه بعدی و نرم افزارهای شبیه سازی، برای بهبود فرآیندهای طراحی و تولید.
بازار جهانی قالبگیری تزریقی، بهویژه در اقتصادهای نوظهور، به دلیل افزایش تقاضا برای محصولات پلاستیکی در صنایع مختلف، در حال گسترش است.
انتخاب شریک قالب گیری تزریقی مناسب
انتخاب شریک قالب تزریق مناسب برای موفقیت پروژه شما بسیار مهم است. برای ارزیابی گزینه های متعدد، انجام بازدید از سایت و شرکت در بحث های کامل برای اطمینان از یک مشارکت سازگار و طولانی مدت وقت بگذارید.
- تخصص و تجربه:به دنبال شریک قالب گیری تزریقی با دانش و تجربه گسترده در صنعت باشید. آنها باید سابقه اثبات شده ای در ارائه محصولات و راه حل های با کیفیت بالا به مشتریان در بخش های مختلف داشته باشند. درک آنها از مواد مختلف، طرح های قالب و فرآیندهای ساخت را در نظر بگیرید.
- قابلیت های تولید: قابلیتهای تولید شریک قالبگیری تزریقی را ارزیابی کنید. اطمینان حاصل کنید که آنها یک مرکز مجهز با ماشین آلات و فن آوری های مدرن برای رسیدگی به نیازهای پروژه شما دارند. ظرفیت تولید، توانایی آنها برای رسیدگی به اندازهها و پیچیدگیهای مختلف قطعات، و توانایی برآورده کردن حجم تولید و زمانبندی دلخواه شما را در نظر بگیرید.
- تضمین کیفیت:کیفیت در قالب گیری تزریقی مهم است. سیستم های کنترل کیفیت و گواهینامه های شریک بالقوه را ارزیابی کنید. به دنبال شرکای باشید که از استانداردهای کیفیت سختگیرانه پیروی می کنند، فرآیندهای بازرسی قوی دارند و برای اطمینان از کیفیت و سازگاری قطعه، آزمایشات جامعی را انجام می دهند.
- طراحی و پشتیبانی مهندسی:یک شریک قالب تزریق قابل اعتماد باید پشتیبانی طراحی و مهندسی را برای بهینه سازی طراحی قطعه شما برای قابلیت ساخت ارائه دهد. آنها باید مهندسان ماهری داشته باشند که می توانند ورودی ارزشمندی را در مورد انتخاب مواد، طراحی قالب و بهینه سازی فرآیند برای افزایش کیفیت و کارایی قطعه ارائه دهند.
- رقابت پذیری هزینه:در حالی که هزینه نباید تنها عامل تعیین کننده باشد، ارزیابی قیمت و رقابت در هزینه شریک قالب گیری تزریقی ضروری است. قیمتهای دقیق را درخواست کنید و هزینههای ابزار، هزینههای مواد، هزینههای نیروی کار و هر گونه خدمات اضافی را که ارائه میکنند در نظر بگیرید.
- ارتباط و همکاری:ارتباط و همکاری موثر برای یک مشارکت موفق ضروری است. اطمینان حاصل کنید که شریک قالبگیری تزریقی کانالهای ارتباطی خوبی دارد، به سؤالات شما پاسخ میدهد و میتواند بهروزرسانیهای منظم پروژه را ارائه دهد. یک رویکرد مشترک کمک خواهد کرد تا اطمینان حاصل شود که ما نیازهای شما را برآورده می کنیم و به سرعت هر چالشی را برطرف می کنیم.
- مراجع و نظرات مشتریان:به دنبال مراجع مشتری باشید یا نظرات/توصیه ها را بخوانید تا از تجربیات سایر مشتریان با شریک قالب گیری تزریقی مطلع شوید. به دست آوردن این اطلاعات می تواند به تعیین قابلیت اطمینان، سرعت و سطح کلی رضایت مشتری کمک کند.
نتیجه
قالب گیری تزریقی ترموپلاستیک روشی همه کاره و مقرون به صرفه برای تولید قطعات پلاستیکی در مقادیر زیاد است. توانایی آن در تولید اشکال پیچیده با دقت و سازگاری بالا به یک انتخاب محبوب برای صنایع مختلف از جمله خودروسازی، پزشکی، الکترونیک و کالاهای مصرفی تبدیل شده است. با درک جنبه های مختلف قالب گیری تزریقی ترموپلاستیک، از جمله مزایا، معایب و ملاحظات طراحی، می توانید تصمیمات آگاهانه ای در مورد انتخاب شریک قالب گیری تزریقی مناسب برای نیازهای تجاری خود بگیرید.