ഇൻജക്ഷൻ മോൾഡിംഗിന്റെ സാധാരണ മോൾഡിംഗ് വൈകല്യങ്ങൾക്കുള്ള പരിഹാരങ്ങൾ
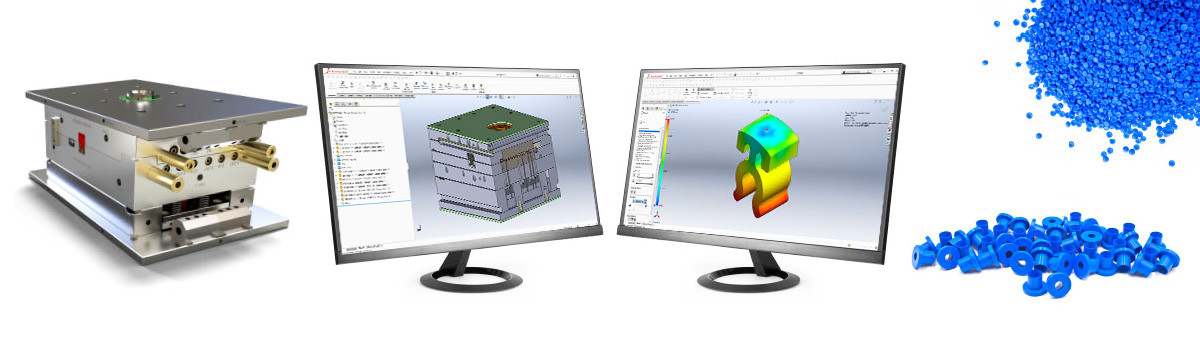
പ്ലാസ്റ്റിക് കുത്തിവയ്പ്പ് മോൾഡിംഗ് ഭാഗങ്ങൾ പ്രോസസ്സ് ചെയ്യുന്നതിന് അച്ചുകൾ ഉപയോഗിക്കുമ്പോൾ തകരാറുകൾ സാധാരണമാണ്, ഇത് പ്രോസസ്സിംഗ് കാര്യക്ഷമതയെ വളരെയധികം ബാധിക്കുന്നു. പ്ലാസ്റ്റിക് കുത്തിവയ്പ്പ് പൂപ്പൽ ഭാഗങ്ങൾക്കുള്ള സാധാരണ മോൾഡിംഗ് വൈകല്യങ്ങളും പരിഹാരങ്ങളും ഇനിപ്പറയുന്നവയാണ്.
ചെറിയ ഷോട്ടുകൾ
അച്ചുകൾ പൂർണ്ണമായി നിറയാത്തതിനാൽ നിർമ്മിച്ച ഉൽപ്പന്നങ്ങൾ അപൂർണ്ണമാണ് ഷോർട്ട് ഷോട്ടുകൾ സൂചിപ്പിക്കുന്നത്.
ഈ തകരാർ സാധാരണയായി ഗേറ്റിൽ നിന്ന് അകലെയുള്ള സ്ഥലങ്ങളിലോ അച്ചിലെ ഇടുങ്ങിയ പ്രദേശങ്ങളിലൂടെ മാത്രം എത്തിച്ചേരാവുന്ന ഭാഗങ്ങളിലോ പ്രത്യക്ഷപ്പെടുന്നു, കാരണം ഇടുങ്ങിയ പ്രദേശങ്ങൾ ഉരുകുന്നതിന്റെ ഒഴുക്കിനെ ബാധിച്ചേക്കാം.
ഷോർട്ട് ഷോട്ട് മൈക്രോ ഫ്ലോ മാർക്കുകൾക്ക് കാരണമായേക്കാം അല്ലെങ്കിൽ ഉൽപ്പന്നത്തിന്റെ വലിയൊരു ഭാഗം നഷ്ടമായേക്കാം.
കാരണം:
ഷോർട്ട് ഷോട്ടുകളുടെ കാരണങ്ങളിൽ ഇവ ഉൾപ്പെടുന്നു:
അച്ചിൽ കുത്തിവച്ച അസംസ്കൃത വസ്തുക്കൾ മതിയാകില്ല.
ഉരുകുന്നതിന്റെ പ്രതിരോധം വലുതാണ്, അതിന്റെ ഫലമായി പൂപ്പൽ പൂർണ്ണമായും പൂരിപ്പിക്കാൻ കഴിയില്ല.
പൂപ്പലിന്റെ വായുസഞ്ചാരം മോശമാണ്, ഇത് ഉരുകുന്നത് തടയുന്ന ഗുഹയുടെ തലമുറയ്ക്ക് കാരണമാകുന്നു, ഇത് പൂപ്പലിന്റെ ചില ഭാഗങ്ങളിലേക്ക് ഉരുകുന്നത് തടയുന്നു.
ബർസ്
പൂപ്പൽ അറയിൽ നിന്ന് ഉൽപന്നത്തിലേക്ക് വലിച്ചെടുക്കുന്ന അധിക അസംസ്കൃത വസ്തുക്കളുടെ ഒട്ടിപ്പിടത്തിൽ നിന്നാണ് ബർറുകൾ ഉണ്ടാകുന്നത്.
ഈ തകരാർ ഉൽപ്പന്നത്തിന്റെ അരികുകളിലോ പൂപ്പലിന്റെ ഓരോ ഭാഗങ്ങളിലോ ആയിരിക്കും. അസംസ്കൃത വസ്തുക്കൾ പൂപ്പലിൽ നിന്ന് ഒഴുകിയേക്കാം, അല്ലെങ്കിൽ ചലിക്കുന്നതും ഉറപ്പിക്കുന്നതുമായ അച്ചുകളുടെ ബോണ്ടിംഗ് സൈറ്റുകൾ.
ഹൈഡ്രോളിക് മർദ്ദം അല്ലെങ്കിൽ കോണീയ പിൻ മൂലമുണ്ടാകുന്ന പൂപ്പൽ കാമ്പിലും ബർറുകൾ കാണാം.
ബർസുകളുടെ തീവ്രത വ്യത്യാസപ്പെടുന്നു, ചിലപ്പോൾ നേർത്തതും ചിലപ്പോൾ കട്ടിയുള്ളതുമാണ്.
കാരണം:
ബർസിനുള്ള കാരണങ്ങളിൽ ഇവ ഉൾപ്പെടുന്നു:
ക്ലാമ്പിംഗ് പൂപ്പൽ ഉപരിതലത്തിന് കേടുപാടുകൾ സംഭവിച്ചു അല്ലെങ്കിൽ വളരെയധികം ധരിക്കുന്നു.
ചലിക്കുന്ന മോൾഡും ഫിക്സിംഗ് മോൾഡും ലോക്ക് ചെയ്യപ്പെടുമ്പോൾ ഡിസ്ലൊക്കേറ്റ് ചെയ്യപ്പെടും.
പൂപ്പലിൽ അസംസ്കൃത വസ്തുക്കളുടെ മർദ്ദം പൂപ്പൽ ക്ലാമ്പിംഗ് ശക്തിയേക്കാൾ കൂടുതലാണ്.
മുകളിൽ സൂചിപ്പിച്ച മൂന്നാമത്തെ അവസ്ഥ വിവിധ കാരണങ്ങളാൽ ഉണ്ടാകാം. ഇനിപ്പറയുന്ന സാഹചര്യങ്ങളിൽ, അസംസ്കൃത വസ്തുക്കളുടെ മർദ്ദം പൂപ്പൽ ക്ലാമ്പിംഗ് ശക്തിയേക്കാൾ കൂടുതലാണ്.
കുത്തിവയ്പ്പ് പൂപ്പലിന്റെ ആദ്യ ഘട്ടത്തിൽ (പൂപ്പൽ പൂരിപ്പിക്കൽ ഘട്ടം), വളരെയധികം അസംസ്കൃത വസ്തുക്കൾ നിറഞ്ഞിരിക്കുന്നു, ഇത് പൂപ്പിനുള്ളിലെ മർദ്ദം വർദ്ധിപ്പിക്കുന്നു.
പൂപ്പൽ പൂരിപ്പിക്കൽ പ്രക്രിയയിൽ, ഉരുകിയ പ്രവാഹത്തിന്റെ വലിയ പ്രതിരോധം പൂപ്പിനുള്ളിലെ മർദ്ദവും ഉയർത്തും.
പ്രഷർ ഹോൾഡിംഗ് ഘട്ടത്തിൽ പൂപ്പൽ അറയുടെ മർദ്ദം വളരെ കൂടുതലാണ്.
പൂപ്പൽ ക്ലാമ്പിംഗ് ശക്തി മതിയാകില്ല.
അപമാനിക്കൽ
വിഘടനം പല ഫലങ്ങളിലേക്കും നയിച്ചേക്കാം. പ്രശ്നത്തിന്റെ വ്യാപ്തിയും തീവ്രതയും വ്യത്യസ്തമാണ്. ഏറ്റവും ഗുരുതരമായ സാഹചര്യത്തിൽ, ഇത് ഉൽപ്പന്നത്തിന്റെ പൂർണ്ണമായ നിറവ്യത്യാസത്തിനും മോശം മെക്കാനിക്കൽ ഗുണങ്ങൾക്കും കാരണമാകും. പ്രാദേശിക അപചയം ഇരുണ്ട വരകളോ പാടുകളോ മാത്രമേ ഉണ്ടാക്കൂ.
കാരണം:
അസംസ്കൃത വസ്തുക്കൾക്ക് കേടുപാടുകൾ സംഭവിക്കുന്നതാണ് നശീകരണത്തിന് കാരണം. പ്ലാസ്റ്റിക്കുകൾ രൂപപ്പെടുന്ന നീണ്ട ചെയിൻ തന്മാത്രകൾ അമിതമായ ചൂട് അല്ലെങ്കിൽ അമിതമായ കത്രിക സമ്മർദ്ദത്തിന്റെ പ്രവർത്തനത്തിൽ വിഘടിക്കുന്നു. തന്മാത്രകളുടെ വിഘടന സമയത്ത്, അസ്ഥിരമായ വാതകം ഡീഗ്രേഡേഷൻ പ്രക്രിയയെ വേഗത്തിലാക്കും, ഇത് അസംസ്കൃത വസ്തുക്കളുടെ നിറം മാറ്റാൻ ഇടയാക്കും. വലിയ അളവിലുള്ള തന്മാത്രകളുടെ വിഘടനം ഒടുവിൽ അസംസ്കൃത വസ്തുക്കളുടെ ഉള്ളടക്കത്തെ തകർക്കുകയും മെക്കാനിക്കൽ ഗുണങ്ങളെ പ്രതികൂലമായി ബാധിക്കുകയും ചെയ്യും.
മെറ്റീരിയൽ ബാരലിന്റെ അസമമായ താപനിലയിൽ നിന്ന് പ്രാദേശിക ശോഷണം ഉണ്ടാകാം.
ഇനിപ്പറയുന്ന സാഹചര്യങ്ങളിൽ അപചയം സംഭവിക്കാം:
മെറ്റീരിയൽ ബാരലിലോ ഹോട്ട് റണ്ണർ സിസ്റ്റത്തിലോ അസംസ്കൃത വസ്തുക്കൾ അമിതമായി ചൂടാക്കപ്പെടുന്നു.
അസംസ്കൃത വസ്തുക്കൾ വളരെക്കാലം ബാരലിൽ തങ്ങിനിൽക്കുന്നു.
ഇഞ്ചക്ഷൻ മോൾഡിംഗ് പ്രക്രിയയിൽ, അസംസ്കൃത വസ്തുക്കളിൽ ചെലുത്തുന്ന കത്രിക സമ്മർദ്ദം വളരെ വലുതാണ്. നോസിലുകൾ തടയുകയോ, ഗേറ്റുകളും റണ്ണറും വളരെ ഇടുങ്ങിയതും ആണെങ്കിൽ, അത് ഷിയർ സമ്മർദ്ദം വർദ്ധിപ്പിക്കും.
രൂപഭേദം
സാധാരണ സാഹചര്യങ്ങളിൽ, ഉൽപ്പന്നങ്ങളുടെ രൂപങ്ങൾ പൂപ്പലുകളുടേതിന് അനുസൃതമായിരിക്കണം. രൂപഭേദം ഉൽപ്പന്നങ്ങളുടെ വൈകല്യത്തെ സൂചിപ്പിക്കുന്നു.
അവസ്ഥ വഷളാകുമ്പോൾ, അച്ചിൽ നിന്ന് പുറന്തള്ളുമ്പോൾ ഉൽപ്പന്നങ്ങൾ പൂർണ്ണമായും രൂപഭേദം വരുത്തും. അവസ്ഥ ഗുരുതരമല്ലാത്തപ്പോൾ, ഉൽപ്പന്നത്തിന്റെ ആകൃതിയിൽ ചെറിയ ക്രമക്കേടുകൾ പ്രത്യക്ഷപ്പെടും.
നീളമുള്ളതും എന്നാൽ പിന്തുണയില്ലാത്തതുമായ അരികുകളോ വലിയ വിമാനങ്ങളോ രൂപഭേദം വരുത്താൻ ഏറ്റവും സാധ്യതയുള്ള പ്രദേശങ്ങളാണ്.
കാരണം:
രൂപഭേദം വരുത്തുന്നതിനുള്ള കാരണങ്ങൾ:
പൂപ്പൽ പുറത്തുവിടുമ്പോൾ താപനില വളരെ ഉയർന്നതാണ്.
കട്ടിയുള്ളതും നേർത്തതുമായ പ്രദേശങ്ങളിൽ തണുപ്പിക്കൽ സമയം വ്യത്യസ്തമായതിനാൽ, അല്ലെങ്കിൽ പൂപ്പൽ ചലിക്കുന്നതിലും പൂപ്പൽ ഉറപ്പിക്കുന്നതിലും പൂപ്പൽ താപനില വ്യത്യാസം, ഉൽപ്പന്നങ്ങൾക്കുള്ളിലെ ചുരുങ്ങൽ വ്യത്യസ്തമാണ്.
പൂരിപ്പിക്കുമ്പോൾ പൂപ്പൽ ഒഴുക്ക് സുഗമമല്ല ("ഫ്രീസിംഗ് ഓറിയന്റേഷൻ" എന്ന് വിളിക്കപ്പെടുന്നു) അല്ലെങ്കിൽ മർദ്ദം പിടിക്കുന്ന ഘട്ടത്തിൽ പൂപ്പൽ അറയ്ക്കുള്ളിലെ മർദ്ദം വളരെ കൂടുതലാണ്.
മാലിന്യങ്ങൾ
മാലിന്യങ്ങൾ പലപ്പോഴും വ്യത്യസ്ത നിറങ്ങളിലോ പാച്ചുകളിലോ വരകളിലോ പാടുകളുടെ രൂപത്തിൽ പ്രത്യക്ഷപ്പെടുന്നു. ഏറ്റവും സാധാരണമായത് കറുത്ത പാടാണ്.
മാലിന്യങ്ങൾ കേവലം ചെറിയ പാടുകൾ മാത്രമായിരിക്കാം, എന്നാൽ അവ ഗുരുതരമായ വരകളാകാം അല്ലെങ്കിൽ നിറം മാറ്റുന്നതിന്റെ വലിയ ഭാഗവും ആകാം.
കാരണം:
അസംസ്കൃത വസ്തുക്കളുമായി ഇടകലർന്ന പലതരം മാലിന്യങ്ങൾ മൂലമാണ് മാലിന്യങ്ങൾ ഉണ്ടാകുന്നത്:
ബാരലുകളിലേക്ക് കൊണ്ടുപോകുമ്പോൾ അസംസ്കൃത വസ്തുക്കൾ പലതരം മിശ്രിതങ്ങളുമായി കലർത്തുന്നു.
അസംസ്കൃത വസ്തുക്കളുടെ വിഘടനം ഏതെങ്കിലും കട്ടിംഗ് മെക്കാനിസത്തിൽ നിന്ന് വീഴുകയും മെഷീൻ ബോൾട്ടുകൾ, ഡ്രമ്മിന്റെ ആന്തരിക ഭിത്തി, സന്ധികൾ / നോസിലുകൾ എന്നിങ്ങനെയുള്ള അസംസ്കൃത വസ്തുക്കളിൽ കലർത്തുകയും ചെയ്യാം.
ലാമിനേഷൻ
ലാമിനേഷൻ ഉൽപ്പന്നങ്ങളുടെ ഉപരിതലത്തിൽ "സ്കിൻ ഇഫക്റ്റ്" സൃഷ്ടിക്കും, ഇത് ഉൽപ്പന്നങ്ങളുടെയും മറ്റ് അസംസ്കൃത വസ്തുക്കളുടെയും ഉപരിതലത്തിലെ ഗുണങ്ങളിലും ടെക്സ്ചറുകളിലും ഉള്ള വ്യത്യാസം മൂലമാണ്, അത് നീക്കം ചെയ്യാവുന്ന ഒരു തൊലി ഉണ്ടാക്കുന്നു.
ലാമിനേഷൻ ഗുരുതരമാകുമ്പോൾ, മുഴുവൻ ക്രോസ് സെക്ഷൻ ഏരിയയും വ്യത്യസ്ത പാളികളാൽ നിർമ്മിതമാണ്, മാത്രമല്ല ഒരുമിച്ച് ഉരുകിയിട്ടില്ല. വൈകല്യങ്ങൾ വ്യക്തമല്ലെങ്കിൽ, ഉൽപ്പന്നങ്ങളുടെ രൂപം ആവശ്യകതകൾ നിറവേറ്റിയേക്കാം, പക്ഷേ ഉൽപ്പന്നങ്ങളുടെ മെക്കാനിക്കൽ ഗുണങ്ങളെ തകർക്കും.
കാരണം:
ലാമിനേഷൻ ഉണ്ടാകുന്നതിന് രണ്ട് പ്രധാന കാരണങ്ങളുണ്ട്. ആദ്യത്തേത്, രണ്ട് വ്യത്യസ്ത തരം അസംസ്കൃത വസ്തുക്കൾ തെറ്റായി കൂടിച്ചേർന്നതാണ്. രണ്ട് അസംസ്കൃത വസ്തുക്കളും സമ്മർദ്ദത്തിൽ ഒരേ സമയം ബാരലിലേക്ക് കൊണ്ടുപോകും. എന്നിരുന്നാലും, പൂപ്പൽ തണുപ്പിക്കുമ്പോൾ ഒരുമിച്ച് ഉരുകാൻ കഴിയാത്തപ്പോൾ, ഉൽപ്പന്നങ്ങൾ രൂപപ്പെടുത്തുന്നതിന് വ്യത്യസ്ത പാളികൾ നിർബന്ധിതമായി ഒരുമിച്ച് അമർത്തുന്നത് പോലെ.
രണ്ടാമത്: തണുത്ത ഉരുകുന്നത് ഇടുങ്ങിയ ഗേറ്റിലൂടെ കടന്നുപോകാൻ നിർബന്ധിതരായാൽ, ഷിയർ സമ്മർദ്ദം സൃഷ്ടിക്കപ്പെടും. വളരെ ഉയർന്ന കത്രിക സമ്മർദ്ദം മുൻകൂട്ടി ഉരുകിയ മെൽറ്റ് ലെയർ പൂർണ്ണമായും സംയോജിപ്പിക്കാൻ കഴിയില്ല.
മിശ്രിതത്തിന്റെ അപകടസാധ്യത:
അറിഞ്ഞിരിക്കേണ്ട ഒരു കാര്യം, ചില അസംസ്കൃത വസ്തുക്കൾ ഒരുമിച്ച് കലർത്തുന്നത് ശക്തമായ രാസപ്രവർത്തനത്തിന് കാരണമാകും, പിവിസി, അവെറ്റൽ എന്നിവ കലർത്താൻ പാടില്ല.
സിൽവർ ലീനിയർ
സ്ലിവർ ലീനിയർ കേവലം പ്രാദേശിക പ്രതിഭാസമായിരിക്കാം, പക്ഷേ അത് ഗുരുതരമായിരിക്കുമ്പോൾ മുഴുവൻ ഉപരിതലത്തിലേക്കും വ്യാപിച്ചേക്കാം.
സിൽവർ ലീനിയർ ഉൽപ്പന്നങ്ങളുടെ രൂപഭാവത്തെ ബാധിക്കുകയും ഉൽപ്പന്നങ്ങളുടെ മെക്കാനിക്കൽ ഗുണങ്ങളെ നശിപ്പിക്കുകയും ചെയ്യും.
കാരണം:
ഇനിപ്പറയുന്ന രണ്ട് പോയിന്റുകൾ സിൽവർ ലീനിയറിന് കാരണമാകുന്നു:
അസംസ്കൃത വസ്തുക്കൾ ഈർപ്പമുള്ളതാണ്, അവയിൽ ചിലത് വായുവിലെ നീരാവി ആഗിരണം ചെയ്യും. അസംസ്കൃത വസ്തുക്കൾ വളരെ നനഞ്ഞതാണെങ്കിൽ, ബാരലിന്റെ ഉയർന്ന താപനിലയിലും ഉയർന്ന മർദ്ദത്തിലും സമ്മർദ്ദമുള്ള നീരാവി സൃഷ്ടിക്കപ്പെട്ടേക്കാം. ഈ നീരാവി ഉൽപ്പന്നത്തിന്റെ ഉപരിതലത്തിലൂടെ കടന്നുപോകുകയും വെള്ളി വരകൾ ഉണ്ടാക്കുകയും ചെയ്യുന്നു.
ഉരുകുന്നത് താപ തകരാറിലാകുകയും പ്രാദേശിക നാശം സൃഷ്ടിക്കുകയും ചെയ്യുന്നു. ഉൽപ്പാദിപ്പിക്കുന്ന അസ്ഥിര വാതകം പൂപ്പൽ ഉപരിതലത്തിൽ തടയുകയും ഉൽപ്പന്നങ്ങളുടെ ഉപരിതലത്തിൽ വരകൾ സൃഷ്ടിക്കുകയും ചെയ്യും.
ഇത് അധഃപതനം പോലെ മോശമല്ല. ഉരുകുന്നതിന്റെ താപനില ഉയർന്നതോ പ്ലാസ്റ്റിലൈസേഷൻ സമയത്ത് അല്ലെങ്കിൽ അച്ചിൽ കുത്തിവയ്ക്കുന്ന സമയത്തോ അത് ഷിയർ സമ്മർദ്ദത്തിന് വിധേയമാകുമ്പോഴോ, ഇത് സംഭവിക്കാം.
തിളക്കം/നിഴൽ
ഉൽപ്പന്നങ്ങളുടെ ഉപരിതല ഫിനിഷിംഗ് പൂപ്പലുകൾക്ക് തുല്യമായിരിക്കണം. രണ്ടിന്റെ ഉപരിതല ഫിനിഷ് വ്യത്യസ്തമായപ്പോൾ, ഗ്ലോസ്/ഷാഡോ വൈകല്യങ്ങൾ സംഭവിച്ചു.
വൈകല്യങ്ങൾ സംഭവിക്കുമ്പോൾ ഉപരിതലം ഇരുണ്ടതായിരിക്കും, പരുക്കൻ പ്രതലം മിനുസമാർന്നതും തിളങ്ങുന്നതുമാണ്.
കാരണം:
തിളക്കം/നിഴലിനുള്ള കാരണങ്ങൾ ഇവയാണ്:
ഉരുകുന്നത് സുഗമമായി ഒഴുകുന്നു അല്ലെങ്കിൽ പൂപ്പൽ പ്രതലത്തിന്റെ താപനില കുറവായതിനാൽ, മെറ്റീരിയൽ മോൾഡിംഗ് ചെയ്യുമ്പോൾ പൂപ്പൽ ഉപരിതല ഫിനിഷ് ഡ്യൂപ്ലിക്കേറ്റ് ചെയ്യാൻ കഴിയില്ല.
പ്രഷർ ഹോൾഡിംഗ് സമയത്ത്, ശീതീകരണ പ്രക്രിയയിൽ മെറ്റീരിയൽ പൂപ്പലിന്റെ ഉപരിതലത്തിൽ പറ്റിപ്പിടിച്ച് ചുരുങ്ങൽ അടയാളങ്ങൾ അവശേഷിപ്പിക്കുന്നതിന് അറയിലെ മർദ്ദം വേണ്ടത്ര ഉയർന്നതല്ല.
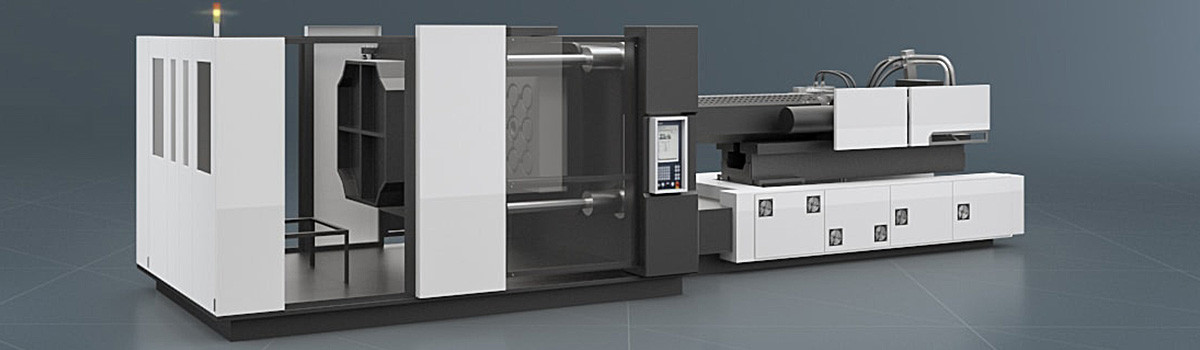
ഫ്ലോ മാർക്കുകൾ
ഉൽപ്പന്നങ്ങളുടെ ഉപരിതലത്തിൽ ഫ്ലോ അടയാളങ്ങൾ ഒന്നിലധികം രൂപങ്ങളിൽ കാണാം. സാധാരണയായി, ഇത് ഒരു നിഴൽ പ്രദേശം ഉണ്ടാക്കും.
ഫ്ലോ മാർക്കുകൾ ഉൽപ്പന്നങ്ങളുടെ ഉപരിതലത്തിൽ ഒരു എംബോസിംഗും വിഷാദവും ഉണ്ടാക്കുന്നില്ല, അത് വിരലുകൾ കൊണ്ട് അനുഭവിക്കാൻ കഴിയില്ല. ഈ വൈകല്യത്തെ ഡ്രാഗ് മാർക്കുകൾ, ഗോസ്റ്റിംഗ്, ഷാഡോകൾ എന്നും വിളിക്കുന്നു.
ഒഴുക്ക് അടയാളങ്ങൾ വ്യക്തമാകുമ്പോൾ, അത് ഗ്രോവുകൾ സൃഷ്ടിക്കുകയും ഉൽപ്പന്നങ്ങളുടെ ഉപരിതലത്തിൽ അടയാളങ്ങൾ പോലെയുള്ള വൈകല്യങ്ങൾ അവശേഷിപ്പിക്കുകയും ചെയ്യും.
കാരണം:
ഇനിപ്പറയുന്ന സന്ദർഭങ്ങളിൽ ഫ്ലോ മാർക്ക് കണ്ടെത്താനാകും:
ഉരുകുന്നതിന്റെ ഒഴുക്ക് മോശമാണ് അല്ലെങ്കിൽ പൂപ്പലിന്റെ ഉപരിതല താപനില കുറവാണ്, ഇത് പൂപ്പൽ പൂരിപ്പിക്കൽ പ്രക്രിയയിൽ പ്ലാസ്റ്റിക്കിന്റെ വലിയ ഒഴുക്ക് പ്രതിരോധത്തിന് കാരണമാകുന്നു.
മോൾഡ് ഫില്ലിംഗിൽ, ഡൈയുടെ അസമമായ ഉപരിതലം, ഡൈ പ്രതലത്തിൽ അച്ചടിച്ച അടയാളങ്ങൾ അല്ലെങ്കിൽ പാറ്റേണുകൾ, അല്ലെങ്കിൽ പൂരിപ്പിക്കൽ പ്രക്രിയയിൽ ഉരുകുന്ന പ്രവാഹ ദിശയിലെ മാറ്റം എന്നിവ മൂലമുണ്ടാകുന്ന പ്രതിരോധത്തോടുകൂടിയ മെൽറ്റ് ഫ്ലോ.
ജോയിന്റിംഗ് ലൈൻ
പൂപ്പൽ പൂരിപ്പിക്കുമ്പോൾ രണ്ട് മെൽറ്റ് ഫ്രണ്ടുകൾ കണ്ടുമുട്ടുമ്പോൾ ചേരുന്ന ലൈൻ ജനറേറ്റുചെയ്യുന്നു, കൂടാതെ ഉൽപ്പന്നത്തിന്റെ ഉപരിതലത്തിൽ ഒരു ലൈൻ പോലെ ദൃശ്യമാകും.
ജോയിന്റിംഗ് ലൈൻ ഉൽപ്പന്നങ്ങളുടെ ഉപരിതലത്തിലെ വിള്ളൽ ലൈൻ പോലെയാണ്, അത് കണ്ടെത്താൻ വ്യക്തമല്ല.
അച്ചുകൾ രൂപകൽപ്പന ചെയ്യുമ്പോൾ, ചില ദൃശ്യമായ ജോയിന്റിംഗ് ലൈനുകൾ ഒഴിവാക്കാനാവില്ല. ഈ സാഹചര്യത്തിൽ, കേടുപാടുകൾ വരുത്തുന്ന ഉൽപ്പന്നങ്ങളുടെ ശക്തിയും രൂപവും തടയുന്നതിന് ജോയിന്റിംഗ് ലൈൻ കഴിയുന്നത്ര ചെറുതാക്കുന്നു.
കാരണം:
മെൽറ്റ് ഫ്രണ്ടിന്റെ തലമുറയ്ക്ക് നിരവധി കാരണങ്ങളുണ്ട്. ഏറ്റവും സാധ്യമായ കാരണം പൂപ്പൽ കാമ്പിന്റെ അരികുകളിൽ ഉരുകി ഒഴുകുന്നതാണ്. രണ്ടും കൂടിച്ചേരുമ്പോൾ, അത് ജോയിന്റിംഗ് ലൈനുകൾ ഉണ്ടാക്കുന്നു. രണ്ട് ഉരുകുന്നതിന്റെ മുൻഭാഗത്തെ താപനില, അവ വിജയകരമായി സംയോജിപ്പിക്കാൻ അനുവദിക്കുന്നതിന് ഉയർന്നതായിരിക്കണം, മാത്രമല്ല ഉൽപ്പന്നങ്ങളുടെ ശക്തിയെയും രൂപത്തെയും ബാധിക്കരുത്.
രണ്ടും ഉരുകുന്നത് പൂർണ്ണമായി സംയോജിപ്പിക്കാൻ കഴിയാതെ വരുമ്പോൾ, വൈകല്യങ്ങൾ ഉത്പാദിപ്പിക്കപ്പെടും.
വൈകല്യങ്ങളുടെ കാരണങ്ങൾ:
പൂപ്പലിന് കട്ടിയുള്ളതും നേർത്തതുമായ ഭാഗങ്ങളുണ്ട്, ഉരുകുന്നതിന്റെ വേഗത വ്യത്യസ്തമാണ്, ഉരുകുന്നത് പൂപ്പലിന്റെ നേർത്ത ഭാഗത്തിലൂടെ ഒഴുകുമ്പോൾ താപനില കുറവാണ്.
ഓരോ ഓട്ടക്കാരന്റെയും നീളം വ്യത്യസ്തമാണ്. ഒറ്റയ്ക്ക് ഓടുന്നവരെ തണുപ്പിക്കാൻ എളുപ്പമായിരിക്കും.
പ്രഷർ ഹോൾഡിംഗ് ഘട്ടത്തിൽ ഉരുകുന്നത് പൂർണ്ണമായും ഫ്യൂസ് ചെയ്യാൻ അനുവദിക്കുന്നതിന് പൂപ്പൽ അറയുടെ മർദ്ദം പര്യാപ്തമല്ല.
ശേഷിക്കുന്ന കുമിളകൾ ഉരുകുന്ന മുൻഭാഗത്തെ സംയോജിപ്പിക്കാൻ കഴിയില്ല, ഇത് കത്തുന്നതിലേക്കും നയിക്കും.
ബേൺ ചെയ്യുന്നു
കത്തുന്നത് ഷോർട്ട് ഷോട്ടിന് സമാനമാണ്, പക്ഷേ ക്രമരഹിതമായ മങ്ങൽ അരികുകളും നേരിയ കത്തുന്ന മണവും. കാർബൺ കറുത്ത ഭാഗങ്ങൾ ഉൽപ്പന്നത്തിൽ പ്രത്യക്ഷപ്പെടും, അവസ്ഥ ഗുരുതരമാകുമ്പോൾ, പ്ലാസ്റ്റിക് കത്തുന്ന ഗന്ധത്തോടൊപ്പം.
വൈകല്യങ്ങൾ ഇല്ലാതാക്കിയില്ലെങ്കിൽ, അച്ചിൽ പലപ്പോഴും കറുത്ത നിക്ഷേപം ഉണ്ടാകാറുണ്ട്. കത്തിച്ചാൽ ഉൽപ്പാദിപ്പിക്കുന്ന വാതകമോ എണ്ണയോ പദാർത്ഥങ്ങൾ ഉടനടി പരിശോധിച്ചില്ലെങ്കിൽ, അവ വായു ദ്വാരങ്ങളെ തടഞ്ഞേക്കാം. പാതകളുടെ അറ്റത്താണ് പൊതുവെ പൊള്ളൽ കാണപ്പെടുന്നത്.
കാരണം:
ആന്തരിക ജ്വലന പ്രഭാവം മൂലമാണ് കത്തുന്നത്. വളരെ ചുരുങ്ങിയ സമയത്തിനുള്ളിൽ വായുവിലെ മർദ്ദം കുത്തനെ വർദ്ധിക്കുമ്പോൾ, താപനില ഉയരുകയും കത്തുന്നതിന് കാരണമാവുകയും ചെയ്യും. ശേഖരിച്ച ഡാറ്റ അനുസരിച്ച്, ഇൻജക്ഷൻ മോൾഡിംഗ് പ്രക്രിയയിലെ ആന്തരിക ജ്വലന പ്രഭാവം 600 ഡിഗ്രി വരെ ഉയർന്ന താപനില ഉണ്ടാക്കും.
ഇനിപ്പറയുന്ന സന്ദർഭങ്ങളിൽ ജ്വലനം ഉണ്ടാകാം:
പൂപ്പൽ പൂരിപ്പിക്കൽ വേഗത വേഗത്തിലായതിനാൽ പൂപ്പൽ അറയിൽ നിന്ന് വായു ശൂന്യമാക്കാൻ കഴിയില്ല, കൂടാതെ ഇൻകമിംഗ് പ്ലാസ്റ്റിക്കിന്റെ ബ്ലോക്ക് കാരണം വായു കുമിളകൾ സൃഷ്ടിക്കുകയും കംപ്രസ് ചെയ്തതിന് ശേഷം ആന്തരിക ജ്വലന ഫലത്തിലേക്ക് നയിക്കുകയും ചെയ്യുന്നു.
എയർ ഹോളുകൾ തടഞ്ഞിരിക്കുന്നു അല്ലെങ്കിൽ വെന്റിലേഷൻ സുഗമമല്ല.
അച്ചിലെ വായു എയർ ഹോളുകളിൽ നിന്ന് ശൂന്യമാക്കണം. സ്ഥാനം, നമ്പർ, വലിപ്പം അല്ലെങ്കിൽ പ്രവർത്തനങ്ങൾ എന്നിവയാൽ വെന്റിലേഷനെ ബാധിച്ചാൽ, വായു അച്ചിൽ തുടരുകയും കത്തുന്നതിലേക്ക് നയിക്കുകയും ചെയ്യും. വലിയ പൂപ്പൽ ക്ലാമ്പിംഗ് ശക്തിയും മോശം വെന്റിലേഷനിലേക്ക് നയിക്കും.
ചുരുങ്ങൽ
സങ്കോചം എന്നത് ഉൽപ്പന്നങ്ങളുടെ ഉപരിതലത്തിലെ ചെറിയ പൊള്ളകളെ സൂചിപ്പിക്കുന്നു.
വൈകല്യങ്ങൾ ചെറുതായിരിക്കുമ്പോൾ, ഉൽപ്പന്നങ്ങളുടെ ഉപരിതലം അസമമാണ്. ഇത് ഗുരുതരമാകുമ്പോൾ, ഉൽപ്പന്നങ്ങളുടെ വലിയ പ്രദേശം തകരും. കമാനങ്ങളും ഹാൻഡിലുകളും പ്രോട്രഷനുകളുമുള്ള ഉൽപ്പന്നങ്ങൾ പലപ്പോഴും ചുരുങ്ങൽ വൈകല്യങ്ങൾ അനുഭവിക്കുന്നു.
കാരണം:
തണുപ്പിക്കൽ സമയത്ത് അസംസ്കൃത വസ്തുക്കളുടെ വലിയ വിസ്തൃതി ചുരുങ്ങുന്നതാണ് ചുരുങ്ങലിന് കാരണം.
ഉൽപന്നങ്ങളുടെ കട്ടിയുള്ള ഭാഗത്ത് (കമാനം പോലെ), പദാർത്ഥത്തിന്റെ കാമ്പിന്റെ മിതശീതോഷ്ണത കുറവായതിനാൽ, ഉപരിതലത്തേക്കാൾ പിന്നീട് സങ്കോചം സംഭവിക്കും, ഇത് അസംസ്കൃത പദാർത്ഥത്തിനുള്ളിൽ ഒരു സങ്കോച ശക്തി ഉണ്ടാക്കുകയും പുറം വശം ഉള്ളിലെ വിഷാദത്തിലേക്ക് വലിച്ചെടുക്കുകയും ചെയ്യും. ചുരുങ്ങൽ ഉത്പാദിപ്പിക്കാൻ.
ഇനിപ്പറയുന്ന സാഹചര്യങ്ങളിൽ ചുരുങ്ങൽ സംഭവിക്കുന്നു:
പൂപ്പൽ അറയിലെ മർദ്ദം തണുപ്പിക്കൽ പ്രക്രിയയിൽ അസംസ്കൃത വസ്തുക്കളുടെ സങ്കോചത്തിൽ നിന്ന് ഉണ്ടാകുന്ന ശക്തിയേക്കാൾ കുറവാണ്.
തണുപ്പിക്കൽ പ്രക്രിയയിൽ പൂപ്പൽ അറയുടെ അപര്യാപ്തമായ മർദ്ദം, ഗേറ്റിൽ നിന്ന് അസംസ്കൃത വസ്തുക്കൾ അറയിൽ നിന്ന് പുറത്തേക്ക് ഒഴുകുന്നു.
അമിതമായ അസംസ്കൃത വസ്തുക്കൾ കുത്തിവയ്ക്കുന്നതിന് മുമ്പ് സ്ക്രൂ പൂർണ്ണമായും പിൻവലിച്ചതിനാൽ അസംസ്കൃത വസ്തുവിന് മോൾഡിംഗ്, പ്രഷർ ഹോൾഡിംഗ് ഘട്ടത്തിൽ മതിയായ ബഫറിംഗ് ശേഷിയില്ല.
ഗേറ്റുകളുടെയും റണ്ണറുകളുടെയും ക്രോസ് സെക്ഷൻ ഏരിയകൾ ഉൽപ്പന്നങ്ങളുടെ കട്ടിയേക്കാൾ വളരെ ചെറുതാണ്, അതായത് ഉൽപ്പന്നങ്ങൾ എക്സ്ട്രൂഷൻ പ്രക്രിയയ്ക്ക് മുമ്പ് ഗേറ്റുകൾ ഇതിനകം മരവിപ്പിച്ചിരിക്കുന്നു.
കളങ്ങൾ
വാക്വം കുമിളകൾ വായു കുമിളകളുടെ രൂപത്തിലാണ് അവതരിപ്പിക്കുന്നത്, ഇത് സുതാര്യമായ ഉൽപ്പന്നങ്ങളിൽ എളുപ്പത്തിൽ കണ്ടെത്താനാകും. അതാര്യ ഉൽപ്പന്നങ്ങളുടെ ക്രോസ് സെക്ഷനിലും ഇത് കാണാം.
കാരണം:
തണുപ്പിക്കൽ പ്രക്രിയയിൽ അസംസ്കൃത വസ്തുക്കൾ ചുരുങ്ങുമ്പോൾ ഉൽപ്പാദിപ്പിക്കപ്പെടുന്ന ഉൽപ്പന്നങ്ങളുടെ വാക്വം ഭാഗമാണ് എയർ ബബിൾസ്.
ചുരുങ്ങലിന് സമാനമായി, അസംസ്കൃത വസ്തുക്കളുടെ ഉൾഭാഗം സങ്കോച ശക്തി ഉണ്ടാക്കുന്നു. വ്യത്യാസം എന്തെന്നാൽ, കുമിളകൾ രൂപപ്പെടുമ്പോൾ ഉൽപന്നങ്ങളുടെ ബാഹ്യ രൂപം ദൃഢീകരിക്കപ്പെട്ടു, തകർച്ചയില്ല, അതിനാൽ പൊള്ളയായ കുമിളകൾ സൃഷ്ടിക്കപ്പെടുന്നു.
കുമിളകളുടെ കാരണങ്ങൾ കുറയ്ക്കുന്നതിന് സമാനമാണ്, ഇനിപ്പറയുന്നവ ഉൾപ്പെടെ:
കാര്യക്ഷമമല്ലാത്ത പൂപ്പൽ അറയുടെ മർദ്ദം
അപര്യാപ്തമായ അറയുടെ മർദ്ദം സമയം
റണ്ണറുടെയും ഗേറ്റിന്റെയും വലിപ്പം വളരെ ചെറുതാണ്
സ്പ്രേ ചെയ്യുന്ന അടയാളങ്ങൾ
സ്പ്രേയിംഗ് മാർക്കുകൾ ഗേറ്റിന് എതിർവശത്തുള്ള ത്രെഡ്ഡ് ഏരിയയെ സൂചിപ്പിക്കുന്നു. സ്പ്രേ ചെയ്യുന്ന അടയാളങ്ങൾ ഉൽപ്പന്നങ്ങളുടെ രൂപത്തെ മാത്രമല്ല, ഉൽപ്പന്നങ്ങളുടെ ശക്തിയെയും ബാധിക്കുന്നു.
കാരണം:
പൂപ്പൽ പൂരിപ്പിക്കൽ പ്രക്രിയയിൽ നിയന്ത്രണാതീതമായ ഉരുകിയ പ്രവാഹമാണ് സ്പ്രേ ചെയ്യുന്ന അടയാളങ്ങൾക്ക് കാരണം.
ഉരുകിയ പ്ലാസ്റ്റിക് വലിയ സമ്മർദത്തിൽ അച്ചിൽ കയറുന്നു. പൂപ്പൽ പൂരിപ്പിക്കൽ വേഗത വളരെ ഉയർന്നതാണെങ്കിൽ, പൂപ്പൽ അറയുടെ തുറന്ന വിടവിൽ നിന്ന് പ്ലാസ്റ്റിക് പുറന്തള്ളുകയും വേഗത്തിൽ തിരികെ വന്ന് തണുക്കുകയും ചെയ്യും. ആ സമയത്ത്, ത്രെഡുകൾ രൂപം കൊള്ളുന്നു, ഇത് ഗേറ്റുകളിലേക്ക് പ്രവേശിക്കുന്ന ഉരുകിയ പ്ലാസ്റ്റിക്കിനെ തടയുന്നു.
ഗേറ്റുകളുടെ തെറ്റായ സ്ഥാനമോ ഗേറ്റിന്റെ രൂപകൽപ്പനയോ ആണ് അടയാളങ്ങൾ തളിക്കുന്നതിനുള്ള പ്രധാന കാരണം. ഇനിപ്പറയുന്ന രണ്ട് സാഹചര്യങ്ങൾ വൈകല്യങ്ങളുടെ അവസ്ഥയെ കൂടുതൽ വഷളാക്കും:
ഉയർന്ന പൂപ്പൽ പൂരിപ്പിക്കൽ വേഗത
പൂപ്പൽ പൂരിപ്പിക്കൽ സമയത്ത് മോശം ഉരുകൽ ഒഴുക്ക്