Soluções para defeitos comuns de moldagem por injeção
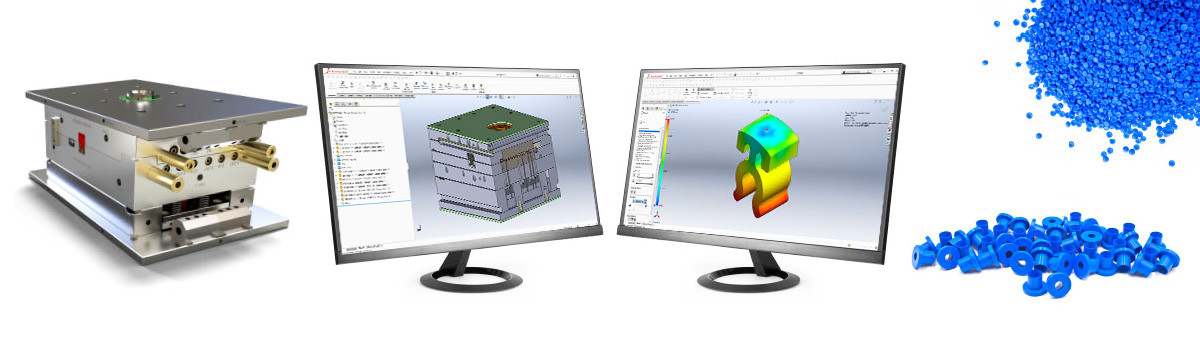
Defeitos são comuns ao usar moldes para processar peças de moldagem por injeção de plástico, e isso afeta muito a eficiência do processamento. A seguir estão defeitos de moldagem comuns e soluções para peças de moldes de injeção de plástico.
Tiros curtos
Os tiros curtos referem-se aos produtos feitos que estão incompletos devido aos moldes não estarem totalmente preenchidos.
Esse defeito geralmente aparece no ponto mais distante do portão ou das peças que só podem ser alcançadas através das áreas estreitas do molde porque as áreas estreitas podem afetar o fluxo de materiais fundidos.
Tiro curto pode causar micro marcas de fluxo ou resultar em uma grande parte do produto obviamente faltando.
causa:
Causas para tiros curtos incluem:
A matéria-prima injetada no molde não é suficiente.
A resistência dos fundidos é grande, fazendo com que o molde não possa ser preenchido completamente.
A ventilação do molde é pobre e causa a geração de cavitação que bloqueia o fundido, fazendo com que o fundido não possa fluir para algumas áreas do molde.
Rebarbas
As rebarbas são geradas a partir da adesão do excesso de matérias-primas extrudadas da cavidade do molde ao produto.
Este defeito será nas bordas do produto ou em cada parte composta do molde. A matéria-prima pode ser extravasada do molde, ou dos locais de colagem dos moldes de movimentação e fixação.
Rebarbas também podem ser encontradas no núcleo do molde, devido à pressão hidráulica ou ao pino angular.
A gravidade das rebarbas varia, às vezes finas, às vezes mais grossas.
causa:
Causas para rebarbas incluem:
A superfície do molde de fixação está danificada ou muito desgastada.
O molde móvel e o molde de fixação são deslocados quando são travados.
A pressão da matéria-prima no molde é maior do que a força de fixação do molde.
A terceira condição mencionada acima resultaria de várias razões. Nas situações a seguir, a pressão da matéria-prima é maior que a força de fixação do molde.
Na primeira etapa do molde de injeção (estágio de enchimento do molde), é preenchida muita matéria-prima, o que aumenta a pressão dentro do molde.
Durante o processo de enchimento do molde, a grande resistência do fluxo de fusão também aumentará a pressão dentro do molde.
A pressão da cavidade do molde é muito alta durante o estágio de manutenção da pressão.
A força de fixação do molde não é suficiente.
degradação
A decomposição pode levar a muitos resultados. A extensão e a gravidade do problema também variam. No caso mais grave, pode causar descoloração total do produto e propriedades mecânicas ruins. A degradação local causará apenas listras ou manchas escuras.
causa:
A degradação é causada pelo dano da matéria-prima. Moléculas de cadeia longa que formam plásticos se decompõem sob a ação de calor excessivo ou tensão de cisalhamento excessiva. Durante a decomposição das moléculas, o gás volátil acelerará o processo de degradação, o que causará a descoloração da matéria-prima. A decomposição de grande quantidade de moléculas finalmente quebrará o conteúdo da matéria-prima e causará influência negativa nas propriedades mecânicas.
A degradação local pode ser resultado da temperatura irregular do barril de material.
A degradação pode ocorrer nas seguintes situações:
A matéria-prima está sendo superaquecida no barril de material ou no sistema de câmara quente.
A matéria-prima fica muito tempo no barril.
Durante o processo de moldagem por injeção, a tensão de cisalhamento exercida sobre a matéria-prima é muito grande. Se os bicos estiverem bloqueados ou os portões e o corredor forem muito estreitos, isso aumentará a tensão de cisalhamento.
Deformação
Nas situações normais, as formas dos produtos devem estar alinhadas com as dos moldes. A deformação refere-se à deformidade dos produtos.
Quando a condição piorar, os produtos ficarão completamente deformados ao serem ejetados do molde. Quando a condição não é grave, o formato do produto apresentará pequenas irregularidades.
Longas, mas sem bordas de apoio ou planos grandes, são as áreas mais propensas a deformações.
causa:
Causas da deformação:
A temperatura é muito alta quando o molde é liberado.
Como o tempo de resfriamento é diferente em áreas grossas e finas, ou a diferença de temperatura do molde no molde em movimento e no molde de fixação, o encolhimento dentro dos produtos é diferente.
O fluxo do molde não é suave durante o enchimento (a chamada “orientação de congelamento”) ou a pressão dentro da cavidade do molde é muito alta no estágio de retenção de pressão.
Impurezas
As impurezas geralmente aparecem na forma de manchas em cores diferentes, manchas ou listras. O mais comum é a mancha preta.
As impurezas podem ser apenas pequenas manchas, mas também podem ser listras óbvias ou grande parte da descoloração quando é grave.
causa:
As impurezas são causadas pelos diversos misturados com matérias-primas, tais como:
A matéria-prima misturada com diversos quando é transportada para os barris.
A decomposição da matéria-prima pode cair de qualquer mecanismo de corte e ser misturada às matérias-primas, como parafusos de máquina, parede interna do tambor de secagem, juntas/bicos.
laminação
A laminação vai gerar na superfície dos produtos o “efeito de pele”, que é causado pela diferença de propriedades e texturas da superfície dos produtos e outras matérias-primas, e forma uma película descamativa que pode ser removida.
Quando a laminação é séria, toda a área da seção transversal é composta de diferentes camadas e não foi fundida. Quando os defeitos são menos óbvios, a aparência dos produtos pode atender aos requisitos, mas quebra as propriedades mecânicas dos produtos.
causa:
Existem duas causas principais para a laminação. A primeira é quando dois tipos diferentes de matérias-primas são misturados incorretamente. As duas matérias-primas serão transportadas para o barril ao mesmo tempo sob pressão. No entanto, quando o molde não pode ser fundido quando é resfriado, assim como diferentes camadas são pressionadas à força para formar produtos.
Segundo: se o cold melt for forçado a passar pela porta estreita, a tensão de cisalhamento será gerada. Tensão de cisalhamento muito alta fará com que a camada fundida antecipadamente não possa ser completamente fundida.
Risco de mistura:
Uma coisa que deve estar ciente é que algumas matérias-primas misturadas resultarão em forte reação química, como PVC e Avetal não devem ser misturados.
Prata linear
Sliver linear pode ser apenas um fenômeno local, mas pode ser expandido para toda a superfície quando é sério.
O linear de prata afetará a aparência dos produtos e também danificará as propriedades mecânicas dos produtos.
causa:
Os dois pontos a seguir causam o linear prateado:
A matéria-prima está molhada e algumas delas vão absorver o vapor do ar. Se a matéria-prima estiver muito úmida, o vapor pressurizado pode ser gerado sob a alta temperatura e alta pressão do barril. Esses vapores rompem a superfície do produto e formam listras prateadas.
O fundido sofreu danos térmicos e gera degradação local. O gás volátil gerado será bloqueado na superfície do molde e gerará listras na superfície dos produtos.
Isso não é tão pior quanto a degradação. Enquanto a temperatura do fundido for alta ou estiver sujeito a tensão de cisalhamento durante a plastificação ou injeção no molde, isso pode acontecer.
Brilho/sombra
O acabamento superficial dos produtos deve ser igual ao dos moldes. Quando o acabamento da superfície de dois é diferente, ocorrem defeitos de brilho/sombra.
A superfície ficará sombria quando ocorrerem defeitos e a superfície áspera é lisa e brilhante.
causa:
Causas de brilho/sombra incluem:
A fusão flui de forma irregular ou a temperatura da superfície do molde é baixa, resultando no acabamento da superfície do molde que não pode ser duplicado durante a moldagem do material.
Durante a retenção de pressão, a pressão na cavidade não é alta o suficiente para fazer o material aderir à superfície do molde no processo de resfriamento, deixando marcas de encolhimento.
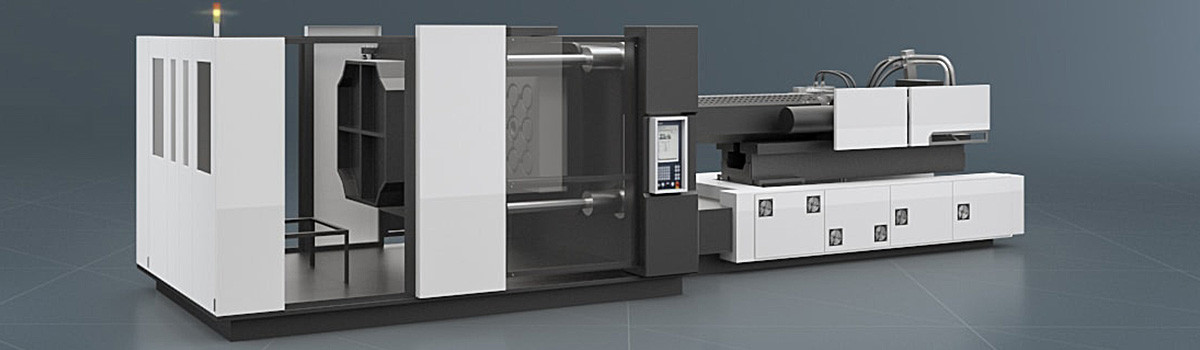
Marcas de fluxo
As marcas de fluxo podem ser encontradas na superfície dos produtos em várias formas. Geralmente, formará uma área de sombra.
As marcas de fluxo não produzem nenhum relevo ou depressão na superfície dos produtos, que não podem ser sentidos com os dedos. Esse defeito também é chamado de marcas de arrasto, fantasmas e sombras.
Quando as marcas de fluxo são óbvias, elas geram sulcos e deixam defeitos como marcas na superfície dos produtos.
causa:
As marcas de fluxo podem ser encontradas quando:
A fluidez do fundido é baixa ou a temperatura da superfície do molde é baixa, resultando em uma grande resistência ao fluxo do plástico no processo de preenchimento do molde.
No enchimento do molde, o fluxo do fundido apresenta resistência, o que pode ser causado pela superfície irregular da matriz, pelas marcas ou padrões impressos na superfície da matriz ou pela mudança de direção do fluxo do fundido durante o processo de enchimento.
linha de união
A linha de junção é gerada quando duas frentes fundidas se encontram durante o preenchimento do molde e aparecerá na superfície do produto como uma linha.
A linha de junção é como a linha de rachaduras na superfície dos produtos, que não é óbvia de detectar.
Ao projetar moldes, algumas linhas de junção visíveis são inevitáveis. Neste caso, reduza ao máximo a linha de união para evitar que a resistência e a aparência dos produtos sejam danificadas.
causa:
Existem muitas razões para a geração de frente de fusão. A razão mais possível pode ser o fluxo de fusão ao longo das bordas do núcleo do molde. Quando os dois fundidos se encontram, produz as linhas de união. A temperatura de duas frentes de fusão deve ser alta o suficiente para permitir que sejam fundidas com sucesso e não afete a resistência e a aparência dos produtos.
Quando os dois fundidos não podem se fundir completamente, os defeitos serão produzidos.
Causas de defeitos:
O molde tem partes mais grossas e mais finas, e a velocidade do fluxo de derretimento é diferente, quando o derretimento flui através da parte fina do molde, a temperatura é baixa.
O comprimento de cada corredor é diferente. Os corredores solitários serão fáceis de esfriar.
A pressão da cavidade do molde não é suficiente para permitir que o fundido se funda completamente durante o estágio de manutenção da pressão.
As bolhas restantes impedem a fusão da frente de derretimento, o que também levará à queima.
Ardente
A queima é semelhante à do tiro curto, mas com bordas irregulares esmaecidas e leve cheiro de queimado. As áreas de negro de fumo aparecerão no produto, quando o quadro for grave, acompanhadas de cheiro de plástico queimado.
Se os defeitos não forem eliminados, muitas vezes há deposição preta no molde. Se as substâncias de gás ou óleo produzidas pela queima não forem verificadas imediatamente, elas podem bloquear os orifícios de ventilação. A queima é geralmente encontrada no final das vias.
causa:
A queima é causada pelo efeito de combustão interna. Quando a pressão no ar aumentar bruscamente em um tempo muito curto, a temperatura aumentará e causará queimaduras. De acordo com os dados coletados, o efeito de combustão interna no processo de moldagem por injeção pode produzir altas temperaturas de até 600 graus.
A queima pode ser produzida quando:
A velocidade de enchimento do molde é rápida para que o ar não possa ser esvaziado da cavidade do molde e gera bolhas de ar devido ao bloqueio do plástico que entra, levando ao efeito de combustão interna após ser comprimido.
Os orifícios de ar estão bloqueados ou a ventilação não é suave.
O ar no molde deve ser retirado dos orifícios de ar. Se a ventilação for afetada pela posição, número, tamanho ou funções, o ar permanecerá no molde e causará queimaduras. Uma grande força de fixação do molde também levará a uma ventilação deficiente.
encolhimento
O encolhimento refere-se às pequenas cavidades na superfície dos produtos.
Quando os defeitos são leves, a superfície dos produtos é irregular. Quando é sério, a grande área de produtos entrará em colapso. Produtos com arcos, alças e saliências geralmente sofrem de defeitos de encolhimento.
causa:
O encolhimento é causado pelo encolhimento de grande área de matérias-primas durante o resfriamento.
Na área espessa de produtos (como arco), o núcleo temperado do material é baixo, então o encolhimento ocorrerá mais tarde do que o da superfície, o que produzirá uma força de contração dentro da matéria-prima e puxará o lado externo para a depressão interna para produzir o encolhimento.
Os encolhimentos ocorrem nas seguintes situações:
A pressão na cavidade do molde é menor que a força gerada pela contração da matéria-prima no processo de resfriamento.
Tempo de pressurização insuficiente da cavidade do molde durante o processo de resfriamento, resultando no fluxo de matéria-prima para fora da cavidade do portão.
A matéria-prima não tem capacidade tampão suficiente durante o estágio de moldagem e retenção de pressão, pois o parafuso é completamente retirado antes que o excesso de matéria-prima seja injetado.
As áreas de seção transversal de portas e corredores são muito menores do que a espessura dos produtos, o que significa que as portas já estão congeladas antes do processo de extrusão dos produtos.
Bubbles
As bolhas de vácuo são apresentadas na forma de bolhas de ar, que podem ser facilmente encontradas nos produtos transparentes. Também pode ser visto na seção transversal de produtos opacos.
causa:
As bolhas de ar são a parte de vácuo dos produtos, que são produzidas quando a matéria-prima encolhe durante o processo de resfriamento.
Semelhante ao encolhimento, o interior da matéria-prima produz a força contrátil. A diferença é que a aparência externa dos produtos foi solidificada quando as bolhas são formadas, e não há colapso, então as bolhas ocas são geradas.
As causas das bolhas são as mesmas da redução, incluindo:
Pressão ineficiente da cavidade do molde
Tempo de pressurização da cavidade insuficiente
O tamanho do corredor e do portão são muito pequenos
marcas de pulverização
As marcas de pulverização referem-se à área roscada oposta ao portão. As marcas de pulverização não afetam apenas a aparência dos produtos, mas também afetam a resistência dos produtos.
causa:
As marcas de pulverização são causadas pelo fluxo de fusão fora de controle durante o processo de enchimento do molde.
O plástico derretido entra no molde sob enorme pressão. Se a velocidade de enchimento do molde for muito alta, o plástico será ejetado do espaço aberto da cavidade do molde e rapidamente retornará e esfriará. Na hora, são formadas as roscas, que bloqueiam a entrada do plástico fundido nas comportas.
A principal causa das marcas de pulverização é a posição incorreta das comportas ou o desenho das comportas. As duas situações a seguir piorarão a situação dos defeitos:
Alta velocidade de enchimento do molde
Baixo fluxo de fusão durante o enchimento do molde