Moldagem por injeção termoplástica
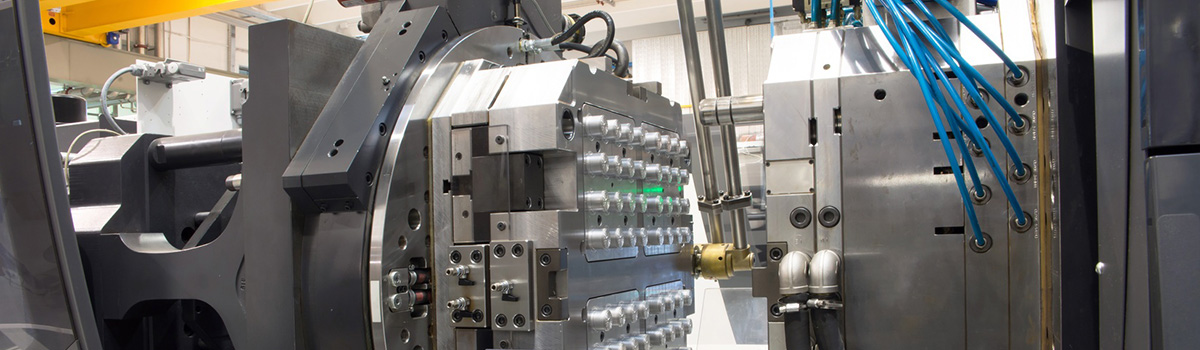
A moldagem por injeção de termoplásticos é um processo de fabricação popular usado para criar várias peças plásticas para vários setores. Este processo envolve derreter pellets de plástico e injetá-los em um molde para produzir uma forma tridimensional. A moldagem por injeção de termoplásticos é altamente eficiente e econômica para produzir grandes volumes de peças plásticas de alta qualidade com tolerâncias apertadas. Este guia abrangente irá explorar os vários aspectos da moldagem por injeção de termoplásticos, incluindo suas vantagens e desvantagens, os tipos de termoplásticos usados, o processo de moldagem por injeção, considerações de projeto e muito mais.
História da moldagem por injeção de termoplásticos
A história da moldagem por injeção de termoplásticos abrange mais de um século de avanços tecnológicos, desenvolvimentos de materiais e aplicações industriais. Desde o seu começo humilde como um processo de moldagem de celulóide até a sofisticada tecnologia atual, a moldagem por injeção continua a ser uma técnica de fabricação vital, impulsionando a inovação e moldando várias indústrias.
- Desenvolvimentos iniciais:John Wesley Hyatt e seu irmão Isaiah desenvolveram a primeira máquina de moldagem por injeção prática, traçando as origens da moldagem por injeção de termoplásticos até o final do século XIX. Em 19, eles patentearam um dispositivo que usava um êmbolo para injetar celulóide na cavidade de um molde, criando objetos sólidos. Este avanço lançou as bases para o moderno processo de moldagem por injeção.
- Avanços em Materiais:No início do século 20, a introdução de novos polímeros sintéticos abriu novas possibilidades para a moldagem por injeção. A baquelite, uma resina fenólica, tornou-se um material popular para moldagem devido às suas excelentes propriedades de isolamento elétrico. Ao longo das décadas de 1930 e 1940, os avanços na química dos polímeros levaram ao desenvolvimento de outros termoplásticos, como o poliestireno e o polietileno, que expandiram ainda mais a gama de materiais adequados para moldagem por injeção.
- Adoção industrial: A ampla adoção da moldagem por injeção de termoplásticos começou na década de 1950, quando os fabricantes reconheceram sua relação custo-benefício e versatilidade. A introdução de máquinas de alta pressão permitiu tempos de ciclo mais rápidos e maiores volumes de produção. Como resultado, surgiu uma seleção diversificada de produtos para uso pessoal e industrial. Isso incluía componentes de carros, eletrodomésticos e brinquedos.
- Inovações Tecnológicas:Ao longo das décadas, a tecnologia de moldagem por injeção continuou a evoluir. Na década de 1960, surgiram as máquinas controladas por computador, permitindo um controle preciso do processo de moldagem. A introdução de sistemas de câmara quente na década de 1980 reduziu o desperdício e melhorou a eficiência, eliminando a necessidade de canais e canais de alimentação. Nos últimos anos, os avanços em automação, robótica e impressão 3D revolucionaram ainda mais a indústria de moldagem por injeção, permitindo projetos complexos e reduzindo o tempo de produção.
- Sustentabilidade e Reciclagem:Com as crescentes preocupações ambientais, a indústria de moldagem por injeção adotou medidas de sustentabilidade. Os fabricantes desenvolveram termoplásticos de base biológica e reciclados, reduzindo a dependência de materiais à base de combustíveis fósseis. Além disso, tecnologias de reciclagem aprimoradas permitiram o reprocessamento de resíduos pós-consumo e pós-industriais, minimizando o impacto ambiental da moldagem por injeção de termoplásticos.
- Perspectivas futuras:O futuro da moldagem por injeção de termoplásticos parece promissor. A indústria está explorando inovações como moldagem por microinjeção para componentes em miniatura, técnicas multimateriais e de sobremoldagem para peças complexas e integração de tecnologias inteligentes para monitoramento e otimização de processos. Além disso, os pesquisadores esperam que os avanços em materiais biodegradáveis e manufatura aditiva revolucionem o campo, tornando a moldagem por injeção ainda mais sustentável e versátil.
Vantagens da moldagem por injeção de termoplásticos
A moldagem por injeção de termoplásticos oferece inúmeras vantagens para os fabricantes. Ele fornece flexibilidade de design, permitindo designs complexos e intrincados com vários recursos. O processo é econômico, reduzindo o desperdício de material e diminuindo os custos unitários. A moldagem por injeção de termoplástico suporta vários materiais, proporcionando versatilidade para diferentes aplicações.
- Flexibilidade de projeto:A moldagem por injeção de termoplástico permite designs intrincados e complexos com recursos como rebaixos, paredes finas e espessuras variadas, proporcionando imensa liberdade aos projetistas.
- Eficiência de custos: O processo é altamente eficiente, reduzindo o desperdício de material e diminuindo os custos unitários. A moldagem simultânea de várias peças e os ciclos de produção rápidos contribuem para economia de custos.
- Versatilidade de materiais: A moldagem por injeção de termoplásticos suporta uma ampla gama de materiais, permitindo que os fabricantes escolham a opção mais adequada para cada aplicação, incluindo materiais rígidos ou flexíveis, transparentes ou opacos e quimicamente resistentes.
- Força e Durabilidade:Os termoplásticos moldados por injeção podem exibir excelentes propriedades mecânicas, como alta resistência, tenacidade e resistência ao impacto. Opções de reforço, como vidro ou fibras de carbono, aprimoram ainda mais essas propriedades.
- Consistência e Qualidade:A moldagem por injeção garante qualidade consistente de peça a peça e precisão dimensional, oferecendo tolerâncias rígidas e produtos confiáveis. O processo também proporciona um acabamento superficial liso e uniforme, eliminando a necessidade de operações de acabamento adicionais.
- Escalabilidade e produção em massa:A moldagem por injeção é escalável de volumes baixos a altos, tornando-a adequada para produção em massa. Depois que os fabricantes criam o molde, eles podem produzir grandes quantidades de peças idênticas com variações mínimas.
- Integração e Montagem:As peças moldadas por injeção podem incorporar vários componentes em uma única peça, reduzindo a necessidade de processos de montagem adicionais. Essa integração melhora o desempenho do produto, reduz o tempo de montagem e diminui os custos.
- Sustentabilidade:A indústria de moldagem por injeção está mostrando um foco crescente na sustentabilidade. A disponibilidade de materiais de base biológica e reciclados permite a produção de produtos ecologicamente corretos. O uso eficiente de material e a reciclabilidade dos termoplásticos contribuem para um processo de fabricação mais ecológico.
Esses benefícios o tornaram um método de fabricação amplamente adotado em vários setores, fornecendo soluções de alta qualidade, econômicas e ecológicas para requisitos complexos de produtos.
Desvantagens da Moldagem por Injeção Termoplástica
Embora a moldagem por injeção termoplástica ofereça inúmeras vantagens, também existem várias desvantagens. Os fabricantes precisam avaliar cuidadosamente esses fatores e pesá-los em relação aos benefícios para determinar a adequação da moldagem por injeção de termoplástico para suas aplicações específicas.
- Alto Investimento Inicial: A configuração de uma operação de moldagem por injeção de termoplástico requer um investimento inicial significativo no projeto e fabricação de moldes e na compra de maquinário especializado. Os custos associados à criação de moldes e ferramentas podem ser substanciais, especialmente para projetos complexos e complexos.
- Limitações de projeto: Embora a moldagem por injeção termoplástica ofereça flexibilidade de projeto, existem certas limitações. Por exemplo, conseguir uma espessura de parede uniforme em toda a peça pode ser um desafio, levando a variações na distribuição do material e possíveis fragilidades estruturais. Além disso, a presença de rebaixos ou geometrias complexas pode exigir o uso de recursos de molde adicionais ou operações secundárias, aumentando os custos e o tempo de produção.
- Prazos de entrega longos:O processo de projetar e fabricar moldes para moldagem por injeção pode ser demorado, levando a prazos de entrega mais longos para o desenvolvimento do produto. O processo de iteração do projeto, a produção do molde e os testes podem adicionar um tempo significativo ao cronograma geral de produção, o que pode não ser adequado para projetos com prazos apertados.
- Restrições de seleção de materiais:Embora a moldagem por injeção de termoplástico suporte uma ampla gama de materiais, existem certas limitações e restrições. Alguns materiais podem ter requisitos de processamento específicos ou disponibilidade limitada, afetando as escolhas de design e a seleção de materiais para uma aplicação específica.
- Limitações de tamanho da peça:As máquinas de moldagem por injeção têm limitações de tamanho, tanto em termos de tamanho físico do dispositivo quanto do tamanho dos moldes que podem acomodar. A produção de peças enormes pode exigir equipamentos especializados ou métodos alternativos de fabricação.
- Impacto ambiental:Enquanto a indústria trabalha em direção à sustentabilidade, o processo de moldagem por injeção de termoplásticos ainda gera resíduos, incluindo sucatas e sprues. O descarte adequado e a reciclagem desses materiais são necessários para minimizar o impacto ambiental.
- A complexidade da Otimização de Processos:A obtenção de parâmetros de processo ideais para moldagem por injeção de termoplásticos pode ser complexa e demorada. Os fabricantes devem controlar e otimizar cuidadosamente a temperatura, a pressão, as taxas de resfriamento e os tempos de ciclo para garantir a qualidade consistente das peças e minimizar os defeitos.
Tipos de termoplásticos usados na moldagem por injeção
Estes são apenas alguns exemplos de termoplásticos comumente usados em moldagem por injeção. Cada material tem propriedades únicas, tornando-o adequado para aplicações específicas com base na força, flexibilidade, resistência química, transparência e custo. Os fabricantes devem considerar essas propriedades e requisitos ao selecionar o termoplástico apropriado para seus projetos de moldagem por injeção.
- Polipropileno (PP):O polipropileno é um termoplástico versátil comumente usado em moldagem por injeção. Oferece excelente resistência química, baixa densidade e boa resistência ao impacto. O PP (polipropileno) tem uma ampla gama de aplicações em embalagens, componentes automotivos, eletrodomésticos e dispositivos médicos.
- Polietileno (PE):O polietileno é outro termoplástico amplamente utilizado na moldagem por injeção. Está disponível em várias formas, como polietileno de alta densidade (HDPE) e polietileno de baixa densidade (LDPE). PE oferece boa resistência química, tenacidade e flexibilidade, tornando-o adequado para garrafas, recipientes e tubos.
- Poliestireno (PS):O poliestireno é um termoplástico versátil conhecido por sua clareza, rigidez e acessibilidade. Encontra uso comum em embalagens, bens de consumo e produtos descartáveis. O PS (poliestireno) permite processamento rápido e oferece boa estabilidade dimensional, mas pode ser frágil e suscetível a rachaduras por estresse ambiental.
- Acrilonitrila butadieno estireno (ABS): O ABS é um termoplástico popular conhecido por sua excelente resistência ao impacto e durabilidade. Ele combina as propriedades de acrilonitrila, butadieno e estireno para criar um material versátil adequado para peças automotivas, caixas eletrônicas e brinquedos.
- Cloreto de polivinila (PVC): O PVC é um termoplástico amplamente utilizado, conhecido por sua excelente resistência química, durabilidade e baixo custo. Pode ser rígido ou flexível dependendo da formulação e dos aditivos utilizados. PVC (policloreto de vinila) encontra uso comum na construção, isolamento elétrico, produtos de saúde e embalagens.
- Policarbonato (PC): O policarbonato é um termoplástico transparente com impacto extraordinário e alta resistência ao calor. Ele encontra uso comum em aplicações que requerem clareza óptica, como componentes automotivos, capacetes de segurança e displays eletrônicos.
- Nylon (Poliamida):O nylon é um termoplástico forte e durável, conhecido por suas excelentes propriedades mecânicas e resistência química. Ele encontra uso comum em aplicações que exigem alta resistência, como peças automotivas, componentes industriais e bens de consumo.
- Polietileno Tereftalato (PET):PET é um termoplástico popular para a produção de garrafas, recipientes e materiais de embalagem. Oferece boa transparência, resistência química e propriedades de barreira, tornando-o adequado para aplicações em alimentos e bebidas.
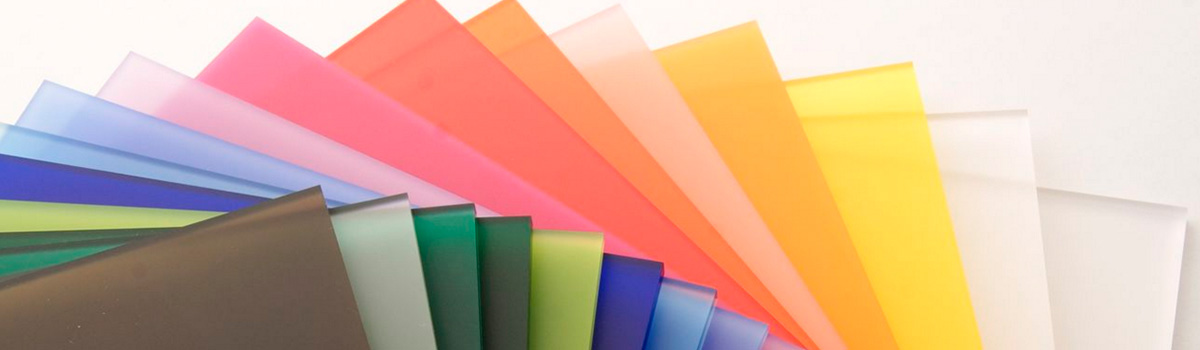
Propriedades dos termoplásticos usados na moldagem por injeção
Essas propriedades dos termoplásticos desempenham um papel crucial na determinação de sua adequação para aplicações específicas de moldagem por injeção. Os fabricantes devem considerar cuidadosamente essas propriedades e selecionar o termoplástico apropriado com base no desempenho desejado, nas condições ambientais e nos requisitos de custo.
- Propriedades Mecânicas:Os termoplásticos usados na moldagem por injeção podem exibir várias propriedades mecânicas, incluindo resistência à tração, resistência ao impacto e resistência à flexão. Essas propriedades determinam a capacidade do material de resistir às forças aplicadas e sua durabilidade geral em várias aplicações.
- Resistência química:Muitos termoplásticos utilizados na moldagem por injeção possuem notável resistência a produtos químicos, solventes e óleos. Esta propriedade é crucial para aplicações que envolvem exposição a ambientes hostis ou substâncias corrosivas.
- Estabilidade térmica:A estabilidade térmica dos termoplásticos refere-se à sua capacidade de suportar temperaturas elevadas sem degradação significativa. Alguns termoplásticos apresentam excelente resistência ao calor, permitindo-lhes manter suas propriedades mecânicas mesmo em altas temperaturas.
- Propriedades elétricas:Os termoplásticos usados na moldagem por injeção podem ter propriedades elétricas específicas, incluindo isolamento elétrico, condutividade ou rigidez dielétrica. Essas propriedades são essenciais para aplicações em indústrias elétricas e eletrônicas, onde os materiais devem fornecer desempenho elétrico confiável.
- Transparência e Clareza:Certos termoplásticos, como policarbonato e PET, oferecem excelente transparência e clareza, tornando-os adequados para aplicações que requerem propriedades ópticas. Os fabricantes geralmente usam esses materiais em produtos como janelas transparentes, lentes e displays.
- Flexibilidade e Resistência: Flexibilidade e tenacidade são propriedades essenciais dos termoplásticos usados em aplicações que exigem resistência ao impacto e durabilidade. Alguns termoplásticos, como o ABS e o nylon, oferecem excelente tenacidade, permitindo-lhes resistir a impactos repetidos sem quebrar.
- Estabilidade dimensional:A estabilidade dimensional refere-se à capacidade de um termoplástico de manter sua forma e tamanho sob condições variadas, incluindo mudanças de temperatura. Materiais com boa estabilidade dimensional garantem dimensões consistentes das peças, minimizando o risco de empenamento ou distorção.
- Compatibilidade química:A compatibilidade química dos termoplásticos refere-se à sua capacidade de resistir à degradação ou interação com vários produtos químicos, incluindo ácidos, bases e solventes. Para garantir o desempenho ideal, é essencial selecionar um termoplástico que possa suportar o ambiente químico específico que encontrará na aplicação pretendida.
- Densidade: Os termoplásticos têm espessuras variadas, o que pode afetar seu peso e as propriedades gerais da peça. Materiais de baixa densidade, como polietileno, oferecem soluções leves, enquanto materiais de alta densidade, como polipropileno, fornecem maior resistência e rigidez.
Processo de Moldagem por Injeção: Passo a Passo
O processo de moldagem por injeção segue essas etapas, permitindo a produção eficiente e precisa de peças termoplásticas de alta qualidade. Cada etapa requer controle e monitoramento cuidadosos para garantir dimensões consistentes da peça, propriedades do material e qualidade geral.
- Projeto e Fabricação de Moldes: A primeira etapa no processo de moldagem por injeção é o projeto e a fabricação do molde. Os fabricantes devem criar um projeto de molde preciso e detalhado para atingir as especificações de peças desejadas. Os fabricantes então fabricam o molde usando várias técnicas, como CNC ou usinagem por descarga elétrica (EDM).
- Preparação de Materiais: O próximo passo é a preparação quando o molde estiver pronto. Pelotas ou grânulos termoplásticos são selecionados com base nas propriedades desejadas do material e derretidos em um funil. Os operadores então alimentam o material no barril da máquina de moldagem por injeção, onde ele é fundido e homogeneizado.
- Injeção:Durante a fase de injeção, os operadores injetam o termoplástico fundido na cavidade do molde sob alta pressão. A unidade de injeção da máquina empurra o material derretido através de um bocal para dentro do molde. O material preenche a cavidade do molde, tomando a forma da peça desejada.
- Resfriamento e Solidificação:Depois de encher o molde, os operadores permitem que o plástico derretido esfrie e solidifique. O resfriamento é crucial para alcançar a estabilidade dimensional e a formação adequada da peça. Os operadores podem controlar o processo de resfriamento circulando o refrigerante pelos canais dentro do molde ou usando placas de resfriamento.
- Abertura e Ejeção do Molde:Os operadores abrem o molde e ejetam a peça da cavidade do molde assim que o plástico solidifica. O sistema de ejeção dentro da máquina utiliza pinos, placas ejetoras ou jatos de ar para retirar a região do molde. O molde está então pronto para o próximo ciclo de injeção.
- Pós-processamento: Após a ejeção, a peça pode passar por operações de pós-processamento, como corte, rebarbação ou acabamento superficial. Essas etapas ajudam a remover o excesso de material, suavizar arestas e melhorar a aparência final da peça.
- Inspeção de qualidade: A etapa final envolve a inspeção da qualidade das peças injetadas e a garantia de que atendem aos requisitos especificados. Várias técnicas de controle de qualidade, incluindo medição dimensional, inspeção visual e teste funcional, podem ser empregadas para verificar a qualidade e integridade da peça.
- Reciclagem e reaproveitamento de materiais:Qualquer excesso ou sucata gerado durante a moldagem por injeção pode ser reciclado e reutilizado. Reduzir o uso de novos materiais termoplásticos ajuda a minimizar o desperdício e melhorar a sustentabilidade.
Equipamentos Utilizados em Moldagem por Injeção
Esses componentes do equipamento facilitam o processo de moldagem por injeção, desde a fusão e injeção do material termoplástico até a modelagem, resfriamento e ejeção da peça final. A operação e manutenção adequadas desses componentes do equipamento são cruciais para alcançar uma produção de moldagem por injeção eficiente e de alta qualidade.
- Máquina de moldagem por injeção:O equipamento primário na moldagem por injeção é responsável por fundir o material termoplástico, injetá-lo no molde e controlar o processo.
- Mofo: O molde, projetado sob medida para criar a forma e as características desejadas da peça de plástico, compreende duas metades, a cavidade e o núcleo. Os operadores o montam na unidade de fixação da máquina de moldagem por injeção.
- Funil:Recipiente que contém o material termoplástico na forma de pellets ou granulados e o alimenta no barril da máquina de moldagem por injeção para fusão e injeção.
- Barril e Parafuso: O barril, uma câmara cilíndrica, funde e homogeneiza o material termoplástico enquanto o parafuso gira dentro dele para derreter, misturar e uniformizar o material.
- Sistemas de aquecimento e refrigeração:As máquinas injetoras possuem elementos de aquecimento, como aquecedores elétricos ou aquecedores a óleo quente, para elevar a temperatura do barril, e sistemas de resfriamento, como circulação de água ou óleo, para resfriar o molde e solidificar a peça plástica.
- Sistema Ejetor:Remove a peça moldada da cavidade do molde após a solidificação, normalmente utilizando pinos ejetores, placas ou jatos de ar durante a abertura do molde.
- Sistema de Controle:Monitora e controla vários parâmetros do processo de moldagem por injeção, permitindo que os operadores definam e ajustem parâmetros como velocidade de injeção, temperatura, pressão e tempo de resfriamento.
Máquinas de Moldagem por Injeção: Tipos e Características
Cada tipo de máquina de moldagem por injeção tem suas características e vantagens, permitindo que os fabricantes escolham o dispositivo mais adequado para suas necessidades específicas de produção.
- Máquinas de moldagem por injeção hidráulica: Essas máquinas utilizam sistemas hidráulicos para gerar a pressão necessária para injetar o plástico fundido no molde. Eles são conhecidos por sua alta força de fixação, controle preciso e versatilidade no manuseio de vários termoplásticos. As máquinas hidráulicas são adequadas para produção em larga escala e podem acomodar moldes complexos.
- Máquinas de moldagem por injeção elétrica:As máquinas elétricas utilizam servomotores elétricos para a operação da máquina, incluindo os sistemas de injeção, fixação e ejeção. Eles oferecem controle preciso, eficiência energética e tempos de resposta mais rápidos do que as máquinas hidráulicas. As máquinas elétricas são ideais para aplicações de moldagem de precisão que exigem alta repetibilidade e precisão.
- Máquinas de moldagem por injeção híbridas:As máquinas híbridas combinam os benefícios dos dispositivos hidráulicos e elétricos. Eles utilizam uma combinação de sistemas servo hidráulicos e elétricos para obter alta precisão, eficiência energética e economia. As máquinas híbridas são adequadas para uma ampla gama de aplicações, proporcionando um equilíbrio entre desempenho e custos operacionais.
- Máquinas de moldagem por injeção de duas placas: As máquinas de duas placas têm um design exclusivo com duas placas separadas para prender o molde. Esse projeto oferece maior estabilidade, melhor sincronização do molde e permite tamanhos de molde maiores e forças de fixação mais altas. As máquinas de duas placas são adequadas para peças grandes e complexas que requerem moldagem precisa.
- Máquinas de moldagem por injeção de vários componentes:Os fabricantes projetam essas máquinas para produzir peças com vários materiais ou cores em um único ciclo de moldagem. Possuem várias unidades de injeção e moldes, possibilitando a injeção simultânea de diversos materiais. As máquinas multicomponentes oferecem flexibilidade e eficiência na fabricação de peças complexas com características variadas.
- Máquinas de moldagem por microinjeção:Especificamente projetadas para produzir peças pequenas e precisas, as máquinas de moldagem por microinjeção oferecem precisão e precisão incrivelmente altas. Eles podem produzir detalhes intrincados com tolerâncias rígidas e desperdício mínimo de material. Eletrônicos, dispositivos médicos e micro-óptica geralmente usam máquinas de moldagem por micro-injeção.
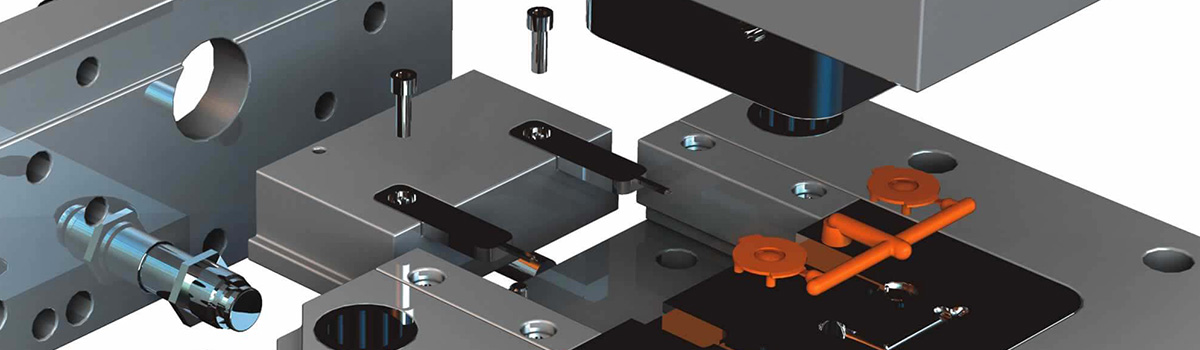
Considerações de projeto de molde para moldagem por injeção
Considerações cuidadosas sobre o projeto do molde são essenciais para uma produção bem-sucedida de moldagem por injeção.
- Design da Peça:O projeto do molde deve acomodar os requisitos específicos da peça, incluindo sua forma, dimensões e características funcionais. Os fabricantes devem considerar adequadamente os ângulos de inclinação, a espessura da parede, os rebaixos e todos os elementos necessários para garantir a facilidade de ejeção e a qualidade da peça.
- Material do molde: A seleção do material do molde é crucial para alcançar durabilidade, estabilidade dimensional e resistência ao calor. Materiais de molde comuns incluem ligas de aço, ligas de alumínio e aços para ferramentas. A escolha do material depende de fatores como volume de produção, complexidade da peça e vida útil esperada da ferramenta.
- Sistema de resfriamento:O resfriamento eficiente é essencial para a solidificação adequada da peça e para minimizar o tempo de ciclo. O projeto do molde deve incorporar canais de resfriamento ou inserções estrategicamente posicionadas para garantir o resfriamento uniforme do molde. O resfriamento adequado reduz o risco de empenamento, encolhimento e defeitos nas peças.
- Ventilação:Ventilação adequada é necessária para permitir a saída de ar e gases durante o processo de injeção. Ventilação insuficiente pode levar a armadilhas de gás, marcas de queimadura ou preenchimento incompleto de peças. Os fabricantes podem obter ventilação incorporando ranhuras, pinos ou outros mecanismos de ventilação no projeto do molde.
- Sistema de Ejeção:O projeto do molde deve incluir um sistema de ejeção eficaz para remover com segurança e eficiência a peça moldada da cavidade do molde. O sistema de ejeção pode consistir em pinos ejetores, mangas ou outros mecanismos, estrategicamente posicionados para evitar interferência com a função ou recursos críticos.
- Projeto do portão:O portão é onde o plástico fundido entra na cavidade do molde. O projeto do portão deve garantir o preenchimento adequado das peças, minimizar as linhas de fluxo e evitar o congelamento prematuro do material. Projetos de comportas padrão incluem comportas de borda, comportas de túnel e sistemas de canal quente, dependendo dos requisitos da peça e das propriedades do material.
- Linha de separação:O projeto do molde deve definir uma linha de partição adequada, que é a linha onde as duas metades do molde se unem. O posicionamento adequado da linha de partição garante o mínimo de rebarbas e incompatibilidade da linha de partição e facilita a montagem eficiente do molde.
- Manutenção e facilidade de manutenção do molde: Os fabricantes devem considerar a facilidade de manutenção, reparo e manutenção do molde. Os componentes do molde devem ser facilmente acessíveis para limpeza, inspeção e substituição. A incorporação de recursos como inserções de troca rápida ou projetos de moldes modulares pode melhorar a facilidade de manutenção do molde.
Materiais de molde usados na moldagem por injeção
Colaborar com especialistas em materiais de molde e considerar as necessidades específicas da aplicação de moldagem pode ajudar a determinar o material mais adequado para obter o desempenho ideal do molde e a qualidade da peça.
- Ligas de Aço: Ligas de aço, como aços para ferramentas (por exemplo, P20, H13) e aços inoxidáveis, são comumente usados para moldes de moldagem por injeção devido à sua excelente durabilidade, resistência ao calor e resistência ao desgaste. Esses materiais podem suportar altas temperaturas e pressões no processo de moldagem por injeção e oferecem boa estabilidade dimensional para a produção de peças de alta qualidade.
- Ligas de Alumínio:As ligas de alumínio, como 7075 e 6061, são leves e oferecem boa condutividade térmica, tornando-as adequadas para moldes que requerem refrigeração eficiente. Os fabricantes costumam usar moldes de alumínio para prototipagem, produção de baixo volume ou aplicações em que a redução de peso é crítica. No entanto, os moldes de alumínio podem ter uma durabilidade menor em comparação com as ligas de aço.
- Ligas de cobre:As ligas de cobre, como cobre-berílio, exibem alta condutividade térmica e boa usinabilidade. Eles encontram uso em moldes que exigem excelente transferência de calor para resfriamento eficaz. As ligas de cobre podem ajudar a reduzir os tempos de ciclo, dissipando rapidamente o calor da peça moldada, resultando em uma solidificação mais rápida.
- Aços Ferramenta:Os aços para ferramentas, incluindo H13, S7 e D2, são projetados para aplicações de ferramentas de alto desempenho. Esses aços oferecem uma combinação de alta resistência, dureza e resistência ao desgaste. Os aços para ferramentas são adequados para moldes com altos volumes de produção, materiais abrasivos ou condições de moldagem exigentes.
- Ligas de Níquel:Ligas de níquel, como Inconel e Hastelloy, são conhecidas por sua excepcional resistência à corrosão, resistência a altas temperaturas e estabilidade térmica. Os fabricantes usam essas ligas em moldes que lidam com materiais corrosivos ou requerem resistência a temperaturas extremas e ambientes de moldagem agressivos.
- Materiais compostos:Materiais compostos, como plásticos reforçados ou compostos com inserções de metal, são ocasionalmente usados para aplicações específicas de moldagem. Esses materiais oferecem um equilíbrio de propriedades, como alta resistência, estabilidade térmica e peso reduzido. Os moldes compostos podem ser alternativas econômicas para requisitos de produção específicos.
Tipos de Moldes de Injeção
A moldagem por injeção é um processo de fabricação versátil e amplamente utilizado para peças plásticas.
- Molde de duas placas:O molde de duas placas é o tipo mais comum de molde de injeção. Consiste em duas placas, a placa de cavidade e a placa de núcleo, que se separam para permitir a ejeção da peça moldada. A placa da cavidade contém o lado da cavidade do molde, enquanto a placa do núcleo abriga o lado do núcleo. Os fabricantes usam moldes de duas placas para produzir uma ampla gama de peças devido ao seu design relativamente simples.
- Molde de três placas:O molde de três placas é uma versão avançada do molde de duas placas. Inclui uma placa adicional, o corredor ou a placa de entrada. A placa do canal cria um canal separado para o sprue, canais e portas, permitindo uma remoção mais fácil da peça moldada. Os fabricantes geralmente usam moldes de três placas para detalhes com sistemas de gatões complexos ou quando é desejável evitar vestígios de gatões na peça.
- Molde de Canal Quente:O sistema de canal e comporta é aquecido em moldes de canal quente, eliminando a necessidade de solidificação e refundição do material a cada ciclo. O sistema de câmara quente consiste em coletores e bicos aquecidos que mantêm o estado fundido do plástico. Os moldes de câmara quente oferecem vantagens como tempo de ciclo reduzido, menor desperdício de material e melhor qualidade da peça, minimizando os vestígios do portão.
- Molde do canal frio: Os moldes de canais frios têm um sistema tradicional de canal e portão, onde o plástico fundido flui através de canais frios que se solidificam a cada ciclo. Posteriormente, os operadores removem os canais solidificados, resultando em desperdício de material. Os fabricantes normalmente usam moldes de canal complexos para produção de menor volume ou quando os custos de material são menos críticos devido ao seu design mais direto.
- Inserir Molde:Os moldes de inserção incorporam inserções de metal ou plástico na cavidade do molde durante a moldagem por injeção. As inserções podem ser pré-colocadas no molde ou inseridas por processos automatizados. Este molde permite integrar componentes adicionais ou elementos de reforço na peça moldada, aumentando sua funcionalidade ou resistência.
- Sobremoldagem: A sobremoldagem envolve a moldagem de um material sobre outro, normalmente ligando um substrato de plástico rígido com um elastômero ou termoplástico mais macio. Esse processo permite a criação de peças com vários materiais ou texturas em um único molde, proporcionando melhor aderência, amortecimento ou características estéticas.
Fatores que afetam os custos de moldagem por injeção
A consideração desses fatores pode ajudar os fabricantes a estimar e otimizar o custo da moldagem por injeção, garantindo um equilíbrio entre qualidade, eficiência e economia para seus requisitos específicos de produção.
- Complexidade da peça:A complexidade do projeto da peça desempenha um papel significativo na determinação do custo da moldagem por injeção. Geometrias intrincadas, rebaixos, paredes finas ou recursos complexos podem exigir ferramentas adicionais, moldes especializados ou ciclos mais longos, aumentando o custo geral de fabricação.
- Seleção de Material:A escolha do material termoplástico afeta o custo da moldagem por injeção. Diferentes materiais têm preços variados por quilo, e fatores como disponibilidade de material, propriedades e requisitos de processamento podem influenciar o custo geral do material.
- Projeto de ferramentas e moldes: Os custos iniciais de ferramental e projeto de molde são significativos nos custos de moldagem por injeção. Fatores como complexidade do molde, número de cavidades, tamanho do molde e material do molde contribuem para as despesas de fabricação de ferramentas e moldes. Moldes mais complexos ou moldes que requerem recursos avançados podem aumentar o investimento inicial.
- Volume de produção: O volume de produção impacta diretamente no custo por peça na moldagem por injeção. Livros mais altos geralmente resultam em economias de escala, reduzindo o custo por peça. Por outro lado, execuções de produção de baixo volume podem incorrer em cobranças mais altas devido à configuração, ferramental e desperdício de material.
- Tempo do ciclo: O tempo de ciclo, que inclui as fases de resfriamento e ejeção, afeta a capacidade de produção e o custo total. Tempos de ciclo mais longos resultam em produção reduzida e preços potencialmente mais altos. A otimização do projeto do molde, do sistema de resfriamento e dos parâmetros do processo pode minimizar os tempos de ciclo e melhorar a eficiência.
- Requerimentos de qualidade:Requisitos de qualidade rigorosos ou certificações específicas podem afetar o custo da moldagem por injeção. Atender tolerâncias exatas, requisitos de acabamento de superfície ou testes adicionais podem exigir outros recursos, processos ou inspeções, aumentando o custo geral.
- Operações Secundárias:Se as peças moldadas exigirem operações de pós-processamento, como montagem, pintura ou etapas adicionais de acabamento, essas operações podem aumentar o custo geral da moldagem por injeção.
- Fornecedor e Localização:A escolha do fornecedor de moldagem por injeção e sua localização podem afetar os custos. Os custos de mão-de-obra, despesas gerais, logística e despesas de transporte variam de acordo com a localização do fornecedor, impactando o custo geral de fabricação.
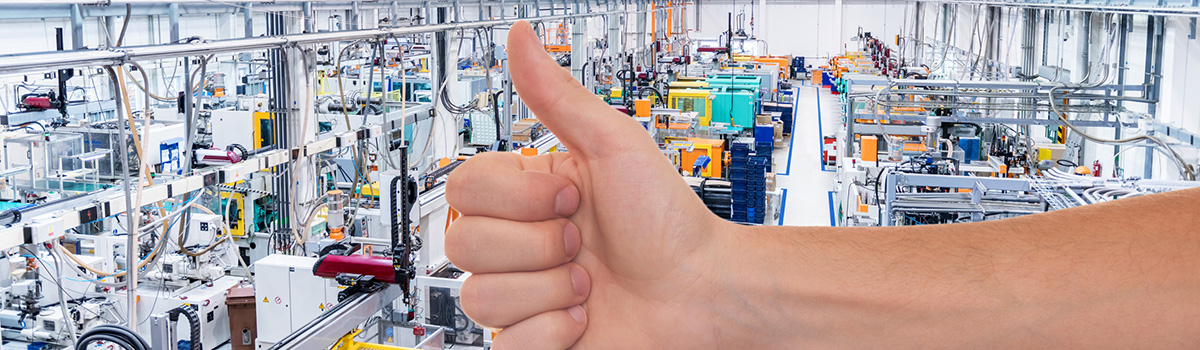
Controle de Qualidade em Moldagem por Injeção
A implementação de medidas robustas de controle de qualidade em todo o processo de moldagem por injeção ajuda a identificar e tratar possíveis defeitos, desvios ou inconsistências, garantindo a produção de peças de alta qualidade que atendem às especificações e requisitos do cliente.
- Monitoramento de processos: O monitoramento contínuo dos principais parâmetros do processo, como temperatura de fusão, pressão de injeção, tempo de resfriamento e tempo de ciclo, garante consistência e repetibilidade na produção de peças. O monitoramento em tempo real e os sistemas automatizados podem detectar variações ou desvios dos parâmetros definidos, permitindo ajustes oportunos e mantendo a estabilidade do processo.
- Inspeção e Medição:A revisão e a medição regulares das peças moldadas são essenciais para verificar a precisão dimensional, a qualidade da peça e a aderência às especificações. Nossos serviços abrangem uma variedade de métodos de controle de qualidade, como medição de dimensões, análise da qualidade da superfície, realização de inspeções visuais e realização de testes funcionais. Várias técnicas de inspeção, como máquinas de medição por coordenadas (CMM) e sistemas de inspeção óptica e visual, são empregadas para uma avaliação precisa.
- Controle Estatístico de Processo (SPC): O SPC envolve a coleta e análise de dados do processo para monitorar e controlar a qualidade da moldagem por injeção. Métodos estatísticos, como gráficos de controle e análise de capacidade de processo, ajudam a identificar tendências, detectar variações de processo e garantir que o processo permaneça dentro dos limites de controle definidos. O SPC permite a identificação proativa de problemas e facilita a otimização do processo.
- Teste de Material: Testar as matérias-primas, como termoplásticos, aditivos e corantes, garante sua qualidade e adequação para moldagem por injeção. O teste de material pode incluir análise do índice de fluxo de fusão (MFI), propriedades mecânicas, características térmicas e composição do material. A verificação da qualidade do material ajuda a prevenir defeitos e inconsistências nas peças moldadas.
- Manutenção e Inspeção de Ferramentas:A manutenção adequada e a inspeção regular dos moldes de injeção são cruciais para garantir a qualidade na moldagem por injeção. Limpeza, lubrificação e avaliação regulares dos componentes do molde ajudam a evitar desgaste, danos ou degradação que podem afetar a qualidade da peça. A reparação ou substituição atempada de componentes de molde desgastados ou danificados é essencial para manter um desempenho de moldagem consistente.
- Documentação e Rastreabilidade:Manter uma documentação abrangente e registros de rastreabilidade é essencial para o controle de qualidade na moldagem por injeção. É vital registrar parâmetros de processo, resultados de inspeção, informações de material e quaisquer alterações ou ajustes feitos durante a produção. A documentação adequada permite a rastreabilidade das peças, facilita a análise da causa raiz e garante consistência na qualidade.
- Treinamento e Desenvolvimento de Habilidades: Fornecer treinamento adequado e programas de desenvolvimento de habilidades para operadores, técnicos e pessoal de controle de qualidade aprimora sua compreensão dos processos de moldagem por injeção, requisitos de qualidade e técnicas de inspeção. Pessoal bem treinado pode detectar defeitos, solucionar problemas e implementar medidas corretivas de forma eficaz, garantindo uma produção de alta qualidade.
Defeitos comuns de moldagem por injeção e como evitá-los
Inspeção regular, monitoramento e análise de processos de moldagem por injeção e manutenção e ajuste adequados de equipamentos e moldes podem ajudar a identificar e corrigir esses defeitos comuns.
- Marcas de pia:Marcas de afundamento são depressões ou reentrâncias na superfície da peça moldada causadas por resfriamento ou encolhimento desigual. Deve-se considerar a localização e o projeto adequados do portão, o projeto ideal do sistema de resfriamento e a distribuição uniforme da espessura da parede para evitar marcas de afundamento. Aumentar a pressão de injeção ou ajustar o tempo de resfriamento também pode ajudar a minimizar marcas de afundamento.
- Empenamento:Empenamento refere-se à deformação ou flexão de uma peça moldada após a ejeção devido ao resfriamento desigual ou tensões residuais. Manter a espessura uniforme da parede, usar canais de resfriamento adequados e garantir o preenchimento e empacotamento equilibrados do molde são cruciais para evitar o empenamento. A otimização da temperatura do molde, o uso de ângulos de inclinação apropriados e o controle da temperatura do material e da velocidade de injeção podem ajudar a minimizar o empenamento.
- Flash:A rebarba ocorre quando o excesso de material flui para a linha de partição do molde, resultando em projeções finas e indesejadas ou material extra na peça final. Pode-se prevenir efetivamente o flash garantindo um projeto de molde adequado, incluindo a aplicação de força de fixação adequada, alinhamento preciso e uso de técnicas de ventilação apropriadas. A otimização dos parâmetros do processo, como pressão de injeção, temperatura e tempo de ciclo, reduz o flash.
- Tiro curto:Um tiro rápido acontece quando o material injetado não preenche a cavidade do molde, resultando em uma peça incompleta. A seleção adequada do material, garantindo a temperatura e a viscosidade adequadas do fundido e mantendo a pressão e o tempo de injeção apropriados são essenciais para evitar fotos curtas. Além disso, verificar o projeto do molde quanto ao tamanho suficiente do canal e da porta e ventilação adequada pode ajudar a evitar disparos rápidos.
- Linhas de solda:As linhas de solda ocorrem quando duas ou mais frentes de fluxo de material fundido se encontram e se solidificam, resultando em uma linha ou marca visível na superfície da peça. Um bom design de canal e canal, temperatura de fusão ideal, velocidade de injeção e ajuste do fluxo de material e geometria da peça podem minimizar as linhas de solda. A análise do fluxo do molde e a otimização do posicionamento do portão também podem ajudar a prevenir ou atenuar as linhas de solda.
- Marcas de queimadura:Marcas de queimadura são descolorações ou manchas pretas na superfície da peça moldada causadas por calor excessivo ou superaquecimento do material. Evitar temperaturas extremas de fusão, usar canais de resfriamento apropriados e otimizar o tempo de ciclo pode ajudar a evitar marcas de queimadura. A ventilação adequada, o projeto adequado do portão e o controle da temperatura do molde também contribuem para minimizar as marcas de queimadura.
Operações Pós-Moldagem: Acabamento e Montagem
Após a moldagem por injeção, muitas peças moldadas podem exigir operações adicionais de acabamento e montagem para obter o produto final desejado. Estas operações de pós-moldagem podem incluir:
- Corte:Remova qualquer excesso de material ou rebarba ao redor da peça moldada usando ferramentas de corte ou corte.
- Tratamento de superfície:Aprimorar a aparência ou a funcionalidade da superfície da peça usando várias técnicas, como pintura, revestimento ou texturização.
- Montagem:Unir várias peças moldadas ou adicionar componentes como fixadores, inserções ou etiquetas para completar o produto final.
- Teste:Verificação da qualidade e funcionalidade da peça por meio de vários métodos de teste, como análise dimensional, teste de propriedades de materiais ou teste de desempenho.
- Embalagem e Transporte:Embalagem e rotulagem adequadas do produto acabado para envio aos clientes ou usuários finais.
A seleção de operações de pós-moldagem depende da aplicação específica e das características desejadas do produto final. A estreita colaboração entre especialistas em moldagem por injeção, especialistas em acabamento e montagem e o cliente é crucial para alcançar a qualidade e a funcionalidade absolutas desejadas do produto. O planejamento adequado e a integração das operações de pós-moldagem no processo de fabricação podem ajudar a garantir uma produção eficiente e a entrega pontual de produtos de alta qualidade.
Moldagem por injeção versus outros processos de fabricação de plástico
Cada processo de fabricação de plástico possui vantagens e limitações, tornando-os adequados para diferentes aplicações.
- Moldagem por injeção: A moldagem por injeção é um processo de fabricação altamente versátil e amplamente utilizado para a produção de peças plásticas. Ele oferece vantagens como alta eficiência de produção, replicação precisa de peças e capacidade de criar geometrias complexas. A moldagem por injeção é adequada para grandes volumes de produção e permite o uso de uma ampla gama de materiais termoplásticos. Oferece excelente precisão dimensional e acabamento superficial, tornando-o ideal para vários setores, como automotivo, bens de consumo e dispositivos médicos.
- Moldagem por sopro: A moldagem por sopro é um processo usado principalmente para produzir peças plásticas ocas, como garrafas, recipientes e componentes automotivos. Envolve derreter o plástico e inflá-lo em uma cavidade do molde, criando a forma desejada. A moldagem por sopro é adequada para produção de alto volume e pode produzir peças grandes e leves com espessura de parede uniforme. No entanto, é limitado em termos de complexidade da peça e seleção de material em comparação com a moldagem por injeção.
- Termoformação:A termoformagem é um processo usado para produzir peças plásticas aquecendo uma folha termoplástica e moldando-a usando moldes ou formação a vácuo. Encontra uso comum em embalagens, produtos descartáveis e produtos de grande escala, como bandejas e tampas. A termoformagem oferece produção econômica para peças grandes e permite prototipagem rápida. No entanto, tem limitações em relação à complexidade da peça, seleção de material e precisão dimensional em comparação com a moldagem por injeção.
- Extrusão:A extrusão é um processo contínuo para produzir perfis, folhas, tubos e filmes de plástico. Envolve derreter resina plástica e forçá-la através de uma matriz para criar a forma desejada. A extrusão é adequada para produzir comprimentos longos e contínuos de produtos plásticos com uma seção transversal consistente. Embora a extrusão ofereça altas taxas de produção e economia, ela é limitada em termos de geometrias de peças complexas e controle dimensional preciso em comparação com a moldagem por injeção.
- Moldagem por compressão:A moldagem por compressão envolve colocar uma quantidade pré-medida de material termoendurecível em uma cavidade de molde aquecida e comprimi-la sob alta pressão até que cure. Encontra uso comum na produção de peças com alta resistência e estabilidade dimensional, como componentes automotivos e isolamento elétrico. A moldagem por compressão oferece boa consistência de peças, alta eficiência de produção e a capacidade de usar uma ampla variedade de materiais. No entanto, é limitado em termos de complexidade da peça e tempo de ciclo em comparação com a moldagem por injeção.
Aplicações da Moldagem por Injeção de Termoplásticos
Várias indústrias usam amplamente a moldagem por injeção de termoplásticos devido à sua versatilidade, eficiência e economia. Algumas das aplicações de moldagem por injeção de termoplásticos incluem:
- Indústria automobilística: A indústria automotiva usa amplamente a moldagem por injeção de termoplástico para fabricar vários componentes, incluindo acabamento interno e externo, painéis, painéis de porta, pára-choques e conectores elétricos. O processo permite replicação precisa de peças, geometrias complexas e materiais leves, melhorando a eficiência de combustível e a flexibilidade do projeto.
- Bens de consumo:A moldagem por injeção encontra extensas aplicações na produção de bens de consumo, como eletrodomésticos, dispositivos eletrônicos, embalagens e brinquedos. O processo permite a produção em massa de produtos duráveis e de alta qualidade com dimensões consistentes e acabamento superficial. Ele também permite opções de personalização e iterações rápidas de produtos.
- Dispositivos médicos:A moldagem por injeção desempenha um papel crucial na indústria médica para a produção de uma ampla gama de dispositivos, incluindo seringas, instrumentos cirúrgicos, componentes implantáveis e sistemas de administração de medicamentos. O processo garante a produção de peças estéreis, precisas e biocompatíveis que atendem aos rigorosos requisitos regulatórios do setor de saúde.
- Indústria Eletrônica e Elétrica:A indústria eletrônica utiliza moldagem por injeção para fabricar conectores elétricos, gabinetes, interruptores e outros componentes. O processo oferece alta precisão dimensional, excelente acabamento superficial e a capacidade de incorporar recursos como moldagem por inserção e sobremoldagem, permitindo a produção eficiente de montagens eletrônicas complexas.
- Indústria de embalagens:Várias indústrias, incluindo alimentos e bebidas, produtos farmacêuticos e cuidados pessoais, comumente usam moldagem por injeção para produzir recipientes de embalagens plásticas, tampas, tampas e garrafas. O processo permite a criação de soluções de embalagens leves, duráveis e esteticamente atraentes com ciclos de fabricação eficientes.
- Indústria aeroespacial:O setor aeroespacial emprega a moldagem por injeção para a fabricação de componentes leves e de alto desempenho, como dutos de ar, suportes, painéis internos e peças estruturais. O processo permite o uso de materiais avançados e geometrias complexas das peças, contribuindo para a redução de peso e maior eficiência de combustível.
Impacto Ambiental da Moldagem por Injeção de Termoplásticos
A moldagem por injeção de termoplásticos é um processo de fabricação popular devido a seus muitos benefícios, mas também é essencial considerar seu impacto ambiental. Aqui estão alguns pontos a considerar:
- Eficiência Material:A moldagem por injeção de termoplástico promove a eficiência do material, minimizando o desperdício. O processo utiliza um controle preciso sobre a quantidade de material injetado no molde, reduzindo a necessidade de excesso de material. Os fabricantes também podem empregar técnicas de retificação e reciclagem para reutilizar sucata ou peças rejeitadas, reduzindo ainda mais o desperdício de material.
- Consumo de energia:Os fabricantes projetam máquinas de moldagem por injeção para serem energeticamente eficientes, com modelos modernos que incorporam tecnologias avançadas, como servomotores e acionamentos de velocidade variável. Esses recursos otimizam o uso de energia reduzindo o consumo de energia durante a moldagem, resultando em menores requisitos de energia e impacto ambiental reduzido.
- Gestão de resíduos:Ao minimizar o desperdício de material, os fabricantes devem implementar práticas adequadas de gerenciamento de resíduos para lidar com sobras de materiais, sprues ou canais. Os fabricantes podem estabelecer programas de reciclagem para coletar e reutilizar resíduos plásticos gerados durante a moldagem por injeção, reduzindo assim os resíduos enviados para aterros sanitários.
- Redução de Emissões: A moldagem por injeção de termoplásticos geralmente gera emissões mais baixas do que outros processos de fabricação. Os fabricantes podem reduzir as emissões usando materiais ecológicos, implementando equipamentos com eficiência energética e empregando sistemas avançados de exaustão e filtragem para capturar quaisquer emissões liberadas.
- Escolhas de materiais sustentáveis:A seleção de materiais termoplásticos pode impactar significativamente a sustentabilidade ambiental da moldagem por injeção. Optar por plásticos biodegradáveis ou de base biológica, bem como materiais reciclados ou recicláveis, pode ajudar a reduzir a pegada ecológica geral do processo.
Considerações sobre o ciclo de vida: Considerar todo o ciclo de vida do produto moldado é essencial para avaliar seu impacto ambiental. Durante os estágios de projeto e seleção de materiais, os fabricantes devem considerar fatores como a durabilidade da peça, sua reciclabilidade e o potencial de descarte ou reutilização no final da vida útil.
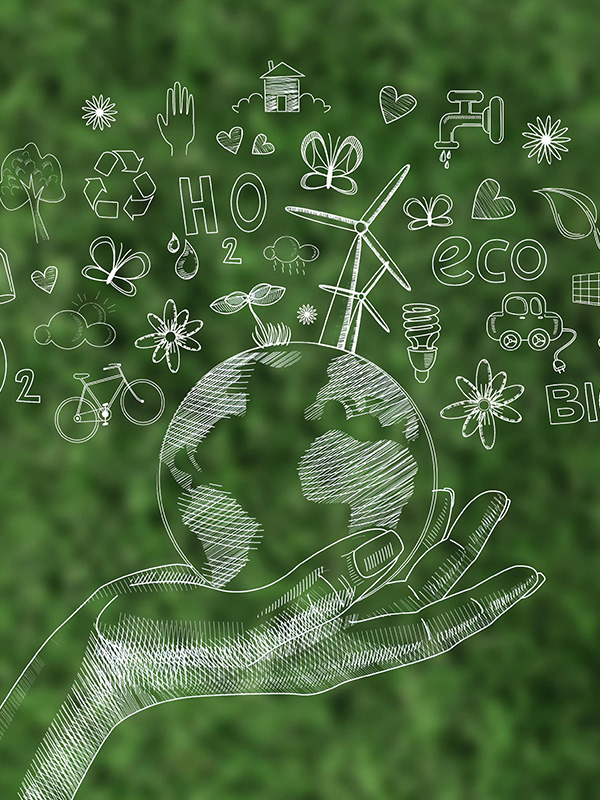
Futuro da moldagem por injeção de termoplásticos
O futuro da moldagem por injeção de termoplásticos parece promissor, com avanços contínuos em tecnologia e aumento da demanda por peças de precisão de alta qualidade em vários setores. Alguns dos principais desenvolvimentos esperados nos próximos anos incluem:
- Aumento do uso de automação e robótica para melhorar a eficiência e reduzir custos.
- Os esforços estão concentrados no desenvolvimento de novos materiais e processos para melhorar o desempenho das peças e possibilitar novas aplicações.
- É uma adoção crescente de práticas sustentáveis, como o uso de materiais reciclados e a otimização do consumo de energia, para reduzir o impacto ambiental da moldagem por injeção.
- Maior integração de tecnologias digitais, como impressão 3D e software de simulação, para melhorar os processos de design e produção.
O mercado global de moldagem por injeção está em expansão, principalmente nas economias emergentes, impulsionado pela crescente demanda por produtos plásticos em diversos setores.
Escolhendo o parceiro de moldagem por injeção certo
Escolher o parceiro de moldagem por injeção certo é crucial para o sucesso do seu projeto. Reserve um tempo para avaliar várias opções, realizar visitas ao local e participar de discussões completas para garantir uma parceria compatível e duradoura.
- Conhecimento e experiência:Procure um parceiro de moldagem por injeção com amplo conhecimento e experiência no setor. Eles devem ter um histórico comprovado de entrega de produtos e soluções de alta qualidade para clientes em vários setores. Considere sua compreensão de diferentes materiais, projetos de moldes e processos de fabricação.
- Capacidades de fabricação: Avalie as capacidades de fabricação do parceiro de moldagem por injeção. Certifique-se de que eles tenham uma instalação bem equipada com máquinas e tecnologias modernas para lidar com os requisitos do seu projeto. Considere a capacidade de produção, a capacidade de lidar com diferentes tamanhos e complexidades de peças e a capacidade de atender aos volumes e prazos de produção desejados.
- Garantia De Qualidade:A qualidade é fundamental na moldagem por injeção. Avalie os sistemas de controle de qualidade e as certificações do potencial parceiro. Procure parceiros que sigam rígidos padrões de qualidade, tenham processos de inspeção robustos e realizem testes abrangentes para garantir a qualidade e a consistência das peças.
- Suporte de design e engenharia:Um parceiro confiável de moldagem por injeção deve oferecer suporte de projeto e engenharia para otimizar o projeto de sua peça para fabricação. Eles devem ter engenheiros qualificados que possam fornecer informações valiosas sobre seleção de materiais, projeto de molde e otimização de processos para melhorar a qualidade e a eficiência das peças.
- Competitividade de custos:Embora o custo não deva ser o único fator determinante, é essencial avaliar o preço e a competitividade de custo do parceiro de moldagem por injeção. Solicite cotações detalhadas e considere custos de ferramentas, custos de materiais, custos de mão-de-obra e quaisquer serviços adicionais que eles forneçam.
- Comunicação e Colaboração:Comunicação e colaboração eficazes são essenciais para uma parceria de sucesso. Certifique-se de que o parceiro de moldagem por injeção tenha bons canais de comunicação, responda às suas perguntas e possa fornecer atualizações regulares do projeto. Uma abordagem colaborativa ajudará a garantir que atendamos às suas necessidades e enfrentemos prontamente quaisquer desafios.
- Referências e avaliações de clientes:Procure referências de clientes ou leia avaliações/depoimentos para obter informações sobre as experiências de outros clientes com o parceiro de moldagem por injeção. A obtenção dessas informações pode ajudar a determinar sua confiabilidade, prontidão e nível geral de satisfação do cliente.
Conclusão
A moldagem por injeção de termoplásticos é um método versátil e econômico para a fabricação de peças plásticas em grandes quantidades. Sua capacidade de produzir formas complexas com alta precisão e consistência tornou-se uma escolha popular para vários setores, incluindo automotivo, médico, eletrônico e bens de consumo. Compreendendo os diferentes aspectos da moldagem por injeção de termoplásticos, incluindo suas vantagens, desvantagens e considerações de projeto, você pode tomar decisões informadas sobre como escolher o parceiro de moldagem por injeção certo para suas necessidades de negócios.