Apa itu cetakan injeksi plastik
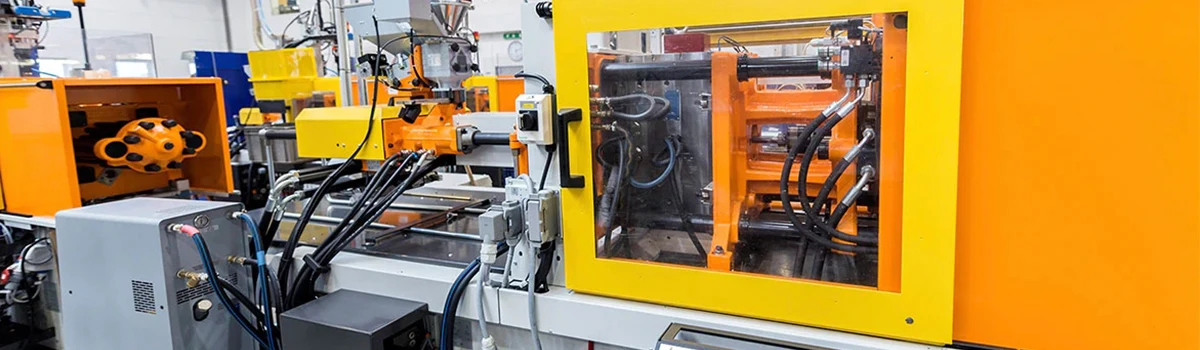
Cetakan injeksi termoplastik adalah metode pembuatan komponen volume tinggi dengan bahan plastik. Karena keandalan dan fleksibilitasnya dalam pilihan desain, cetakan injeksi digunakan di banyak industri, termasuk: pengemasan, konsumen & elektronik, otomotif, medis, dan banyak lagi.
Injection molding adalah salah satu proses manufaktur yang paling banyak digunakan di dunia. Termoplastik adalah polimer yang melunak dan mengalir saat dipanaskan, dan mengeras saat dingin.
Aplikasi
Cetakan injeksi adalah metode modern paling umum untuk pembuatan komponen plastik; itu sangat ideal untuk menghasilkan volume tinggi dari objek yang sama. Cetakan injeksi digunakan untuk membuat banyak hal, termasuk gulungan kawat, kemasan, tutup botol, komponen dan komponen otomotif, konsol game, sisir saku, alat musik, kursi dan meja kecil, wadah penyimpanan, komponen mekanis, dan banyak produk plastik lainnya.
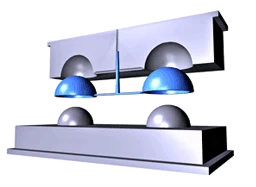
Desain cetakan
Setelah produk dirancang dalam Perangkat Lunak seperti paket CAD, cetakan dibuat dari logam, biasanya baja atau aluminium, dan dikerjakan dengan mesin presisi untuk membentuk fitur bagian yang diinginkan. Cetakan terdiri dari dua komponen utama, cetakan injeksi (pelat A) dan cetakan ejektor (pelat B). Resin plastik memasuki cetakan melalui sprue, atau gerbang, dan mengalir ke rongga cetakan melalui saluran, atau pelari, yang dikerjakan ke permukaan pelat A dan B.
Proses pencetakan injeksi
Ketika termoplastik dicetak, biasanya bahan baku pelet dimasukkan melalui hopper ke dalam tong yang dipanaskan dengan sekrup bolak-balik. Sekrup mengirimkan bahan mentah ke depan, melalui katup periksa, di mana ia terkumpul di bagian depan sekrup ke dalam volume yang dikenal sebagai tembakan.
Tembakan adalah jumlah resin yang dibutuhkan untuk mengisi sprue, runner, dan rongga cetakan. Ketika cukup banyak bahan yang terkumpul, bahan tersebut dipaksa dengan tekanan dan kecepatan tinggi ke dalam rongga pembentuk bagian.
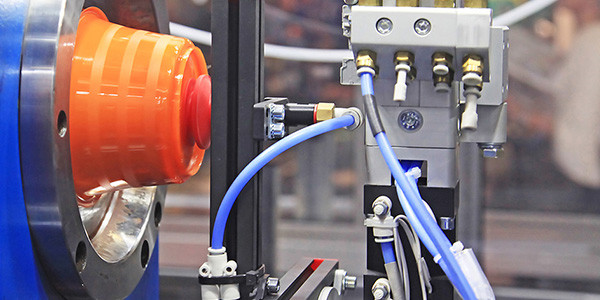
Bagaimana Cara Kerja Cetakan Injeksi?
Setelah plastik mengisi cetakan termasuk sprues, runners, gates, dll., cetakan disimpan pada suhu yang diatur untuk memungkinkan pemadatan material yang seragam ke dalam bentuk bagian. Tekanan penahan dipertahankan saat pendinginan untuk menghentikan aliran balik ke laras dan mengurangi efek penyusutan. Pada titik ini, lebih banyak butiran plastik ditambahkan ke hopper dengan harapan siklus (atau tembakan) berikutnya. Saat didinginkan, pelat terbuka dan memungkinkan bagian yang sudah selesai dikeluarkan, dan sekrup ditarik kembali sekali lagi, memungkinkan material masuk ke laras dan memulai proses dari awal lagi.
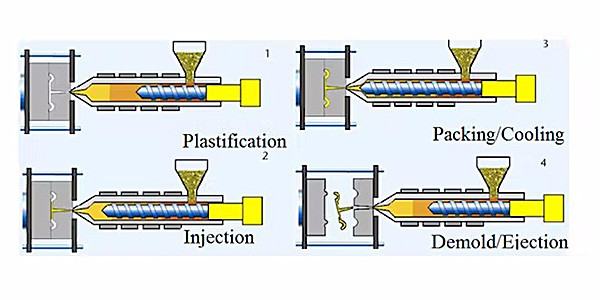
Siklus pencetakan injeksi bekerja dengan proses yang berkelanjutan ini — menutup cetakan, memberi makan / memanaskan butiran plastik, menekannya ke dalam cetakan, mendinginkannya menjadi bagian padat, mengeluarkan bagian tersebut, dan menutup cetakan lagi. Sistem ini memungkinkan produksi komponen plastik dengan cepat, dan lebih dari 10,000 komponen plastik dapat dibuat dalam satu hari kerja tergantung pada desain, ukuran, dan bahan.
Siklus pencetakan injeksi
Siklus pencetakan injeksi sangat singkat, biasanya antara 2 detik dan 2 menit. Ada beberapa tahapan:
1.Menjepit
Sebelum menyuntikkan bahan ke dalam cetakan, kedua bagian cetakan ditutup dengan aman oleh unit penjepit. Unit penjepit bertenaga hidrolik mendorong bagian cetakan bersama-sama dan memberikan kekuatan yang cukup untuk menjaga cetakan tetap tertutup saat bahan disuntikkan.
2. Injeksi
Dengan cetakan tertutup, tembakan polimer disuntikkan ke dalam rongga cetakan.
3. Pendinginan
Saat rongga diisi, tekanan penahan diterapkan yang memungkinkan lebih banyak polimer memasuki rongga untuk mengkompensasi penyusutan plastik saat mendingin. Sementara itu, sekrup berputar dan memasukkan tembakan berikutnya ke sekrup depan. Ini menyebabkan sekrup ditarik kembali saat bidikan berikutnya disiapkan.
4.Ejeksi
Saat bagian sudah cukup dingin, cetakan terbuka, bagian dikeluarkan, dan siklus dimulai lagi.
Kelebihan
1. Produksi cepat; 2. Fleksibilitas desain; 3. Akurasi; 4. Biaya tenaga kerja rendah; 5. Limbah rendah