Solusi untuk Cacat Moulding Umum dari Injection Moulding
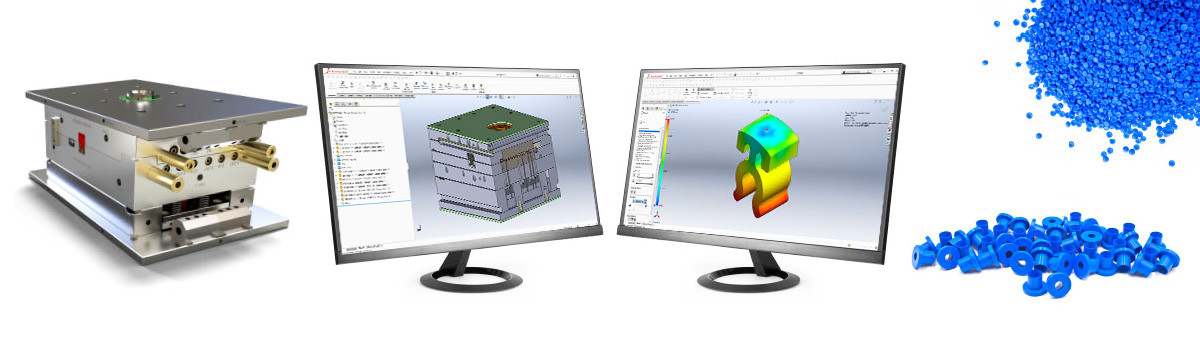
Cacat umum terjadi saat menggunakan cetakan untuk memproses bagian cetakan injeksi plastik, dan ini sangat memengaruhi efisiensi pemrosesan. Berikut ini adalah cacat cetakan umum dan solusi untuk bagian cetakan injeksi plastik.
Tembakan pendek
Short shot mengacu pada produk yang dibuat tidak lengkap karena cetakan tidak terisi penuh.
Cacat ini biasanya muncul pada titik terjauh dari pintu gerbang atau bagian yang hanya dapat dijangkau melalui area sempit pada cetakan karena area sempit dapat mempengaruhi aliran lelehan.
Tembakan pendek dapat menyebabkan tanda aliran mikro atau mengakibatkan sebagian besar produk hilang dengan jelas.
Sebab:
Penyebab tembakan pendek meliputi:
Bahan mentah yang disuntikkan ke dalam cetakan tidak cukup.
Resistansi lelehan besar, mengakibatkan cetakan tidak dapat terisi penuh.
Ventilasi cetakan buruk dan menyebabkan pembentukan kavitasi yang menghalangi lelehan, membuat lelehan tidak dapat mengalir ke beberapa area cetakan.
Gerinda
Gerinda dihasilkan dari adhesi bahan baku berlebih yang diekstrusi dari rongga cetakan ke produk.
Cacat ini akan terjadi pada bagian tepi produk atau setiap bagian cetakan yang tersusun. Bahan mentah mungkin meluap dari cetakan, atau tempat pengikatan cetakan bergerak dan pemasangan.
Gerinda juga dapat ditemukan pada inti cetakan, yang disebabkan oleh tekanan hidrolik atau pin sudut.
Tingkat keparahan gerinda bervariasi, terkadang tipis, terkadang lebih tebal.
Sebab:
Penyebab gerinda meliputi:
Permukaan cetakan penjepit rusak atau sangat aus.
Cetakan yang bergerak dan cetakan yang diperbaiki akan tergeser saat dikunci.
Tekanan bahan baku dalam cetakan lebih tinggi dari gaya penjepitan cetakan.
Kondisi ketiga yang disebutkan di atas akan dihasilkan dari berbagai alasan. Dalam situasi berikut, tekanan bahan baku lebih tinggi dari gaya penjepitan cetakan.
Pada tahap pertama cetakan injeksi (tahap pengisian cetakan), terlalu banyak bahan baku yang terisi, yang meningkatkan tekanan di dalam cetakan.
Selama proses pengisian cetakan, hambatan aliran lelehan yang besar juga akan meningkatkan tekanan di dalam cetakan.
Tekanan rongga cetakan terlalu tinggi selama tahap penahan tekanan.
Kekuatan penjepit cetakan tidak cukup.
Degradasi
Dekomposisi dapat menyebabkan banyak hasil. Tingkat dan tingkat keparahan masalah juga bervariasi. Dalam kasus yang paling serius, ini dapat menyebabkan perubahan warna total pada produk dan sifat mekanik yang buruk. Degradasi lokal hanya akan menyebabkan garis-garis atau bintik-bintik gelap.
Sebab:
Degradasi disebabkan oleh bahan baku yang rusak. Molekul rantai panjang yang membentuk plastik akan terurai di bawah aksi panas yang berlebihan atau tegangan geser yang berlebihan. Selama penguraian molekul, gas yang mudah menguap akan mempercepat proses degradasi, yang akan menyebabkan hilangnya warna bahan baku. Dekomposisi molekul dalam jumlah besar pada akhirnya akan merusak kandungan bahan mentah dan menyebabkan pengaruh negatif pada sifat mekanik.
Degradasi lokal dapat dihasilkan dari suhu yang tidak merata dari laras material.
Degradasi dapat terjadi dalam situasi berikut:
Bahan baku terlalu panas dalam tong bahan atau sistem hot runner.
Bahan mentah tinggal di tong terlalu lama.
Selama proses pencetakan injeksi, tegangan geser yang diberikan pada bahan mentah terlalu besar. Jika nosel tersumbat, atau gerbang dan pelari terlalu sempit, ini akan meningkatkan tegangan geser.
Deformasi
Dalam situasi normal, bentuk produk harus sesuai dengan cetakan. Deformasi mengacu pada deformitas produk.
Saat kondisinya semakin parah, produk akan berubah bentuk seluruhnya saat dikeluarkan dari cetakan. Bila kondisinya tidak serius, bentuk produk akan tampak penyimpangan kecil.
Panjang tapi tanpa tepi penyangga atau bidang besar adalah area yang paling rentan terhadap deformasi.
Sebab:
Penyebab deformasi:
Suhu terlalu tinggi saat cetakan dilepaskan.
Karena waktu pendinginan berbeda di area tebal dan tipis, atau perbedaan suhu cetakan dalam memindahkan cetakan dan memperbaiki cetakan, penyusutan di dalam produk berbeda.
Aliran cetakan tidak lancar saat pengisian (yang disebut "orientasi Pembekuan") atau tekanan di dalam rongga cetakan terlalu tinggi pada tahap penahan tekanan.
Kotoran
Kotoran sering muncul dalam bentuk bintik-bintik dalam berbagai warna, bercak atau garis-garis. Yang paling umum adalah bintik hitam.
Kotoran mungkin hanya berupa bintik-bintik kecil, tetapi juga bisa berupa garis-garis yang jelas atau sebagian besar penghilangan warna jika serius.
Sebab:
Kotoran tersebut disebabkan oleh serba-serbi yang bercampur dengan bahan baku, seperti:
Bahan mentah dicampur dengan serba-serbi saat diangkut ke dalam tong.
Dekomposisi bahan mentah dapat jatuh dari mekanisme pemotongan apa pun dan tercampur menjadi bahan mentah, seperti baut mesin, dinding bagian dalam drum pengering, sambungan/nosel.
Laminasi
Laminasi akan menimbulkan “efek kulit” pada permukaan produk, yang disebabkan oleh perbedaan sifat dan tekstur permukaan produk dan bahan baku lainnya, serta membentuk kulit yang mengelupas yang dapat dihilangkan.
Saat laminasi serius, seluruh area penampang terdiri dari lapisan yang berbeda, dan belum dilebur menjadi satu. Ketika cacat kurang jelas, penampilan produk mungkin memenuhi persyaratan, tetapi akan merusak sifat mekanik produk.
Sebab:
Ada dua penyebab utama laminasi. Yang pertama adalah ketika dua jenis bahan baku yang berbeda dicampur secara tidak benar. Kedua bahan mentah tersebut akan diangkut ke dalam tong pada saat bersamaan di bawah tekanan. Namun, ketika cetakan tidak dapat dicairkan bersama ketika didinginkan, sama seperti lapisan yang berbeda ditekan bersama secara paksa untuk membentuk produk.
Kedua: jika lelehan dingin dipaksa melewati gerbang sempit, tegangan geser akan dihasilkan. Tegangan geser yang terlalu tinggi akan menyebabkan lapisan lelehan yang dilebur terlebih dahulu tidak dapat menyatu sempurna.
Risiko pencampuran:
Satu hal yang harus diperhatikan adalah beberapa bahan baku yang dicampur bersama akan mengakibatkan reaksi kimia yang kuat, seperti PVC dan Avetal tidak boleh dicampur.
Perak linier
Sliver linear mungkin hanya merupakan fenomena lokal, tetapi dapat diperluas ke seluruh permukaan saat serius.
Silver linear akan mempengaruhi penampilan produk dan juga merusak sifat mekanik produk.
Sebab:
Dua poin berikut menyebabkan garis perak:
Bahan bakunya basah dan sebagian akan menyerap uap di udara. Jika bahan bakunya terlalu basah, uap bertekanan mungkin dihasilkan di bawah suhu tinggi dan tekanan laras yang tinggi. Uap ini menembus permukaan produk dan membentuk garis-garis perak.
Pencairan mengalami kerusakan termal dan menghasilkan degradasi lokal. Gas volatil yang dihasilkan akan tertahan pada permukaan cetakan dan menimbulkan garis-garis pada permukaan produk.
Ini tidak seburuk degradasi. Selama suhu lelehan tinggi atau mengalami tegangan geser selama plastisisasi atau diinjeksikan ke dalam cetakan, hal ini dapat terjadi.
Gloss/bayangan
Permukaan akhir produk harus sama dengan cetakan. Ketika permukaan akhir dari dua berbeda, cacat kilap/bayangan terjadi.
Permukaan akan menjadi suram saat terjadi cacat, dan permukaan yang kasar menjadi halus dan mengkilap.
Sebab:
Penyebab kilap/bayangan meliputi:
Lelehan mengalir tidak lancar atau suhu permukaan cetakan rendah, sehingga hasil akhir permukaan cetakan tidak dapat diduplikasi saat pencetakan material.
Selama penahan tekanan, tekanan di dalam rongga tidak cukup tinggi sehingga material menempel pada permukaan cetakan dalam proses pendinginan, meninggalkan bekas penyusutan.
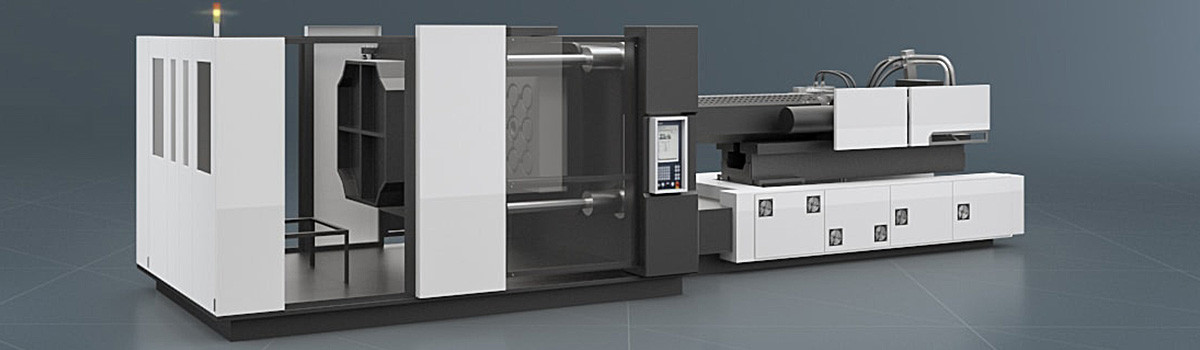
Tanda aliran
Tanda aliran dapat ditemukan di permukaan produk dalam berbagai bentuk. Umumnya akan membentuk area bayangan.
Tanda aliran tidak menghasilkan emboss atau depresi pada permukaan produk, yang tidak dapat dirasakan dengan jari. Cacat ini disebut juga dengan drag mark, ghosting, dan shadow.
Ketika tanda aliran terlihat jelas, itu akan menghasilkan alur, dan meninggalkan cacat seperti tanda di permukaan produk.
Sebab:
Tanda aliran dapat ditemukan ketika:
Daya alir lelehan buruk atau suhu permukaan cetakan rendah, menghasilkan hambatan aliran plastik yang besar dalam proses pengisian cetakan.
Dalam pengisian cetakan, lelehan mengalir dengan hambatan, yang mungkin disebabkan oleh permukaan cetakan yang tidak rata, tanda atau pola yang tercetak pada permukaan cetakan, atau perubahan arah aliran lelehan selama proses pengisian.
Jalur penyambungan
Garis sambungan dihasilkan ketika dua bagian depan lelehan bertemu selama pengisian cetakan, dan akan muncul di permukaan produk seperti garis.
Garis penyambungan seperti garis retakan pada permukaan produk, yang tidak jelas untuk dideteksi.
Saat mendesain cetakan, beberapa garis sambungan yang terlihat tidak dapat dihindari. Dalam hal ini, perpendek garis penyambungan sebanyak mungkin untuk mencegah kerusakan kekuatan dan penampilan produk.
Sebab:
Ada banyak alasan untuk generasi front leleh. Alasan yang paling mungkin adalah aliran lelehan di sepanjang tepi inti cetakan. Ketika dua lelehan bertemu, itu menghasilkan garis sambungan. Temperatur dua bagian depan lelehan harus cukup tinggi untuk memungkinkan mereka melebur bersama dengan sukses, dan tidak mempengaruhi kekuatan dan penampilan produk.
Ketika kedua lelehan tidak dapat menyatu sepenuhnya, cacat akan dihasilkan.
Penyebab cacat:
Cetakan memiliki bagian yang lebih tebal dan lebih tipis, dan kecepatan aliran lelehan berbeda, ketika lelehan mengalir melalui bagian cetakan yang tipis, suhunya rendah.
Panjang setiap pelari berbeda-beda. Pelari penyendiri akan mudah menjadi dingin.
Tekanan rongga cetakan tidak cukup untuk memungkinkan lelehan melebur sepenuhnya selama tahap penahan tekanan.
Gelembung yang tersisa membuat bagian depan yang meleleh tidak dapat menyatu, yang juga akan menyebabkan pembakaran.
terbakar
Pembakarannya mirip dengan tembakan pendek, tetapi dengan tepi memudar tidak teratur dan sedikit bau terbakar. Area karbon hitam akan muncul pada produk, bila kondisinya parah, disertai dengan bau plastik terbakar.
Jika cacat tidak dihilangkan, seringkali terdapat pengendapan hitam pada cetakan. Jika zat gas atau minyak yang dihasilkan dari pembakaran tidak segera diperiksa, dapat menyumbat lubang udara. Pembakaran umumnya ditemukan di ujung jalur.
Sebab:
Pembakaran disebabkan oleh efek pembakaran internal. Ketika tekanan di udara meningkat tajam dalam waktu yang sangat singkat, suhu akan naik dan menyebabkan pembakaran. Menurut data yang terkumpul, efek internal combustion pada proses injection molding dapat menghasilkan temperatur tinggi hingga 600 derajat.
Pembakaran dapat dihasilkan ketika:
Kecepatan pengisian cetakan cepat sehingga udara tidak dapat dikeluarkan dari rongga cetakan, dan menimbulkan gelembung udara karena blok plastik yang masuk, dan menyebabkan efek pembakaran internal setelah dikompresi.
Lubang udara tersumbat atau ventilasi tidak lancar.
Udara dalam cetakan harus dikeluarkan dari lubang udara. Jika ventilasi dipengaruhi oleh posisi, jumlah, ukuran atau fungsinya, maka udara akan tertahan di dalam cetakan dan menyebabkan pembakaran. Kekuatan penjepit cetakan yang besar juga akan menyebabkan ventilasi yang buruk.
Penyusutan
Penyusutan mengacu pada sedikit cekungan pada permukaan produk.
Jika cacatnya kecil, permukaan produk tidak rata. Ketika serius, area produk yang luas akan runtuh. Produk dengan lengkungan, pegangan, dan tonjolan sering mengalami cacat penyusutan.
Sebab:
Penyusutan disebabkan oleh penyusutan bahan baku yang luas selama pendinginan.
Di area produk yang tebal (seperti lengkungan), suhu inti material rendah, sehingga penyusutan akan terjadi lebih lambat dari permukaan, yang akan menghasilkan gaya kontraksi di dalam bahan mentah, dan menarik sisi luar ke dalam depresi ke dalam. untuk menghasilkan penyusutan.
Penyusutan terjadi dalam situasi berikut:
Tekanan di rongga cetakan lebih rendah dari gaya yang dihasilkan dari penyusutan bahan baku dalam proses pendinginan.
Waktu tekanan rongga cetakan yang tidak mencukupi selama proses pendinginan, mengakibatkan aliran bahan baku keluar dari rongga dari pintu gerbang.
Bahan baku tidak memiliki kapasitas penyangga yang cukup selama tahap pencetakan dan penahan tekanan karena sekrup ditarik sepenuhnya sebelum bahan baku yang berlebihan disuntikkan.
Area penampang gerbang dan pelari jauh lebih kecil dari ketebalan produk, yang berarti gerbang sudah dibekukan sebelum proses ekstrusi produk.
gelembung
Gelembung vakum disajikan dalam bentuk gelembung udara yang dapat ditemukan dengan mudah pada produk transparan. Itu juga bisa dilihat pada penampang produk buram.
Sebab:
Gelembung udara adalah bagian vakum dari produk, yang dihasilkan saat bahan baku menyusut selama proses pendinginan.
Mirip dengan penyusutan, bagian dalam bahan mentah menghasilkan gaya kontraktil. Apa perbedaannya adalah bahwa penampilan luar produk telah dipadatkan ketika gelembung terbentuk, dan tidak ada keruntuhan, sehingga dihasilkan gelembung berongga.
Penyebab gelembung sama dengan penyebab reduksi, antara lain:
Tekanan rongga cetakan tidak efisien
Waktu tekanan rongga tidak mencukupi
Ukuran runner dan gate terlalu kecil
Tanda penyemprotan
Tanda penyemprotan mengacu pada area berulir di seberang gerbang. Tanda penyemprotan tidak hanya mempengaruhi penampilan produk, tetapi juga mempengaruhi kekuatan produk.
Sebab:
Bekas penyemprotan disebabkan oleh aliran lelehan yang tidak terkendali selama proses pengisian cetakan.
Plastik cair masuk ke cetakan di bawah tekanan besar. Jika kecepatan pengisian cetakan terlalu tinggi, plastik akan keluar dari celah terbuka rongga cetakan, dan dengan cepat kembali dan dingin. Pada saat itu, terbentuk benang-benang yang menghalangi plastik cair masuk ke dalam gerbang.
Penyebab utama tanda penyemprotan adalah posisi gerbang yang salah atau desain gerbang. Dua situasi berikut akan memperburuk situasi cacat:
Kecepatan pengisian cetakan tinggi
Aliran lelehan yang buruk selama pengisian cetakan