Cetakan Injeksi Termoplastik
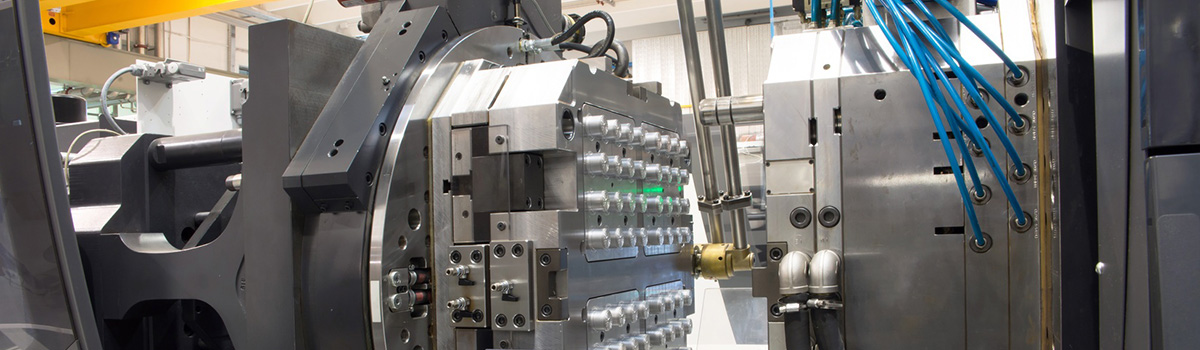
Cetakan injeksi termoplastik adalah proses manufaktur populer yang digunakan untuk membuat berbagai komponen plastik untuk berbagai industri. Proses ini melibatkan peleburan pelet plastik dan menyuntikkannya ke dalam cetakan untuk menghasilkan bentuk tiga dimensi. Cetakan injeksi termoplastik sangat efisien dan hemat biaya untuk memproduksi volume besar komponen plastik berkualitas tinggi dengan toleransi yang ketat. Panduan komprehensif ini akan mengeksplorasi berbagai aspek cetakan injeksi termoplastik, termasuk kelebihan dan kekurangannya, jenis termoplastik yang digunakan, proses pencetakan injeksi, pertimbangan desain, dan banyak lagi.
Sejarah Cetakan Injeksi Termoplastik
Sejarah cetakan injeksi termoplastik mencakup lebih dari satu abad kemajuan teknologi, perkembangan material, dan aplikasi industri. Dari awal yang sederhana sebagai proses pencetakan seluloid hingga teknologi canggih saat ini, pencetakan injeksi terus menjadi teknik manufaktur yang vital, mendorong inovasi dan membentuk berbagai industri.
- Perkembangan Awal:John Wesley Hyatt dan saudaranya Isaiah mengembangkan mesin cetak injeksi pertama yang praktis, menelusuri asal-usul cetakan injeksi termoplastik kembali ke akhir abad ke-19. Pada tahun 1872, mereka mematenkan perangkat yang menggunakan pendorong untuk menyuntikkan seluloid ke dalam rongga cetakan, menciptakan benda padat. Terobosan ini meletakkan dasar untuk proses pencetakan injeksi modern.
- Kemajuan dalam Bahan:Pada awal abad ke-20, memperkenalkan polimer sintetik baru membuka kemungkinan baru untuk pencetakan injeksi. Bakelite, resin fenolik, menjadi bahan cetakan yang populer karena sifat isolasi listriknya yang sangat baik. Sepanjang tahun 1930-an dan 1940-an, kemajuan dalam kimia polimer mengarah pada pengembangan termoplastik lainnya, seperti polistirena dan polietilen, yang selanjutnya memperluas jangkauan bahan yang cocok untuk cetakan injeksi.
- Adopsi Industri: Adopsi yang luas dari cetakan injeksi termoplastik dimulai pada 1950-an karena produsen mengakui keefektifan biaya dan keserbagunaannya. Memperkenalkan mesin bertekanan tinggi memungkinkan waktu siklus yang lebih cepat dan peningkatan volume produksi. Akibatnya, beragam pilihan produk untuk penggunaan pribadi dan industri muncul. Ini termasuk komponen mobil, peralatan rumah tangga, dan mainan.
- Inovasi Teknologi:Selama beberapa dekade, teknologi cetakan injeksi terus berkembang. Pada 1960-an, mesin yang dikendalikan komputer muncul, memungkinkan kontrol yang tepat atas proses pencetakan. Pengenalan sistem hot runner pada 1980-an mengurangi limbah dan meningkatkan efisiensi dengan menghilangkan kebutuhan akan runner dan sprues. Dalam beberapa tahun terakhir, otomatisasi, robotika, dan kemajuan pencetakan 3D telah merevolusi industri cetakan injeksi, memungkinkan desain yang rumit dan mengurangi waktu produksi.
- Keberlanjutan dan Daur Ulang:Dengan meningkatnya kepedulian terhadap lingkungan, industri cetakan injeksi telah menganut langkah-langkah keberlanjutan. Produsen telah mengembangkan termoplastik berbasis bio dan daur ulang, mengurangi ketergantungan pada bahan berbasis bahan bakar fosil. Selain itu, teknologi daur ulang yang ditingkatkan telah memungkinkan pemrosesan ulang limbah pasca-konsumen dan pasca-industri, meminimalkan dampak lingkungan dari cetakan injeksi termoplastik.
- Prospek masa depan:Masa depan cetakan injeksi termoplastik terlihat menjanjikan. Industri ini sedang menjajaki inovasi seperti micro-injection moulding untuk komponen miniatur, teknik multi-material dan overmolding untuk komponen kompleks, dan mengintegrasikan teknologi cerdas untuk pemantauan dan pengoptimalan proses. Selain itu, para peneliti mengharapkan kemajuan dalam bahan biodegradable dan manufaktur aditif untuk merevolusi lapangan, membuat cetakan injeksi menjadi lebih berkelanjutan dan serbaguna.
Keuntungan dari Cetakan Injeksi Termoplastik
Cetakan injeksi termoplastik menawarkan banyak keuntungan bagi produsen. Ini memberikan fleksibilitas desain, memungkinkan desain yang rumit dan rumit dengan berbagai fitur. Prosesnya hemat biaya, mengurangi pemborosan material dan menurunkan biaya satuan. Cetakan injeksi termoplastik mendukung banyak bahan, memberikan keserbagunaan untuk aplikasi yang berbeda.
- Fleksibilitas Desain:Cetakan injeksi termoplastik memungkinkan desain yang rumit dan kompleks dengan fitur seperti potongan bawah, dinding tipis, dan ketebalan yang bervariasi, memberikan kebebasan yang sangat besar kepada desainer.
- Penghematan biaya: Prosesnya sangat efisien, mengurangi pemborosan material dan menurunkan biaya satuan. Pencetakan beberapa bagian secara bersamaan dan siklus produksi yang cepat berkontribusi pada penghematan biaya.
- Fleksibilitas Bahan: Cetakan injeksi termoplastik mendukung berbagai bahan, memungkinkan produsen memilih opsi yang paling sesuai untuk setiap aplikasi, termasuk bahan yang kaku atau fleksibel, transparan atau buram, dan tahan bahan kimia.
- Kekuatan dan Daya Tahan:Termoplastik cetakan injeksi dapat menunjukkan sifat mekanik yang sangat baik, seperti kekuatan tinggi, ketangguhan, dan ketahanan benturan. Opsi penguat, seperti kaca atau serat karbon, semakin meningkatkan sifat ini.
- Konsistensi dan Kualitas:Cetakan injeksi memastikan kualitas bagian-ke-bagian yang konsisten dan akurasi dimensi, memberikan toleransi yang ketat dan produk yang andal. Proses ini juga memberikan penyelesaian permukaan yang halus dan seragam, menghilangkan kebutuhan untuk operasi penyelesaian tambahan.
- Skalabilitas dan Produksi Massal:Cetakan injeksi dapat diskalakan dari volume rendah hingga tinggi, sehingga cocok untuk produksi massal. Setelah pabrikan membuat cetakan, mereka dapat memproduksi komponen identik dalam jumlah besar dengan variasi minimal.
- Integrasi dan Majelis:Bagian cetakan injeksi dapat menggabungkan beberapa komponen menjadi satu bagian, mengurangi kebutuhan akan proses perakitan tambahan. Integrasi ini meningkatkan kinerja produk, mengurangi waktu perakitan, dan menurunkan biaya.
- Keberlanjutan:Industri cetakan injeksi menunjukkan peningkatan fokus pada keberlanjutan. Ketersediaan bahan berbasis bio dan daur ulang memungkinkan untuk menghasilkan produk yang ramah lingkungan. Penggunaan material yang efisien dan daur ulang termoplastik berkontribusi pada proses produksi yang lebih ramah lingkungan.
Manfaat ini membuatnya menjadi metode manufaktur yang diadopsi secara luas di berbagai industri, memberikan solusi berkualitas tinggi, hemat biaya, dan ramah lingkungan untuk kebutuhan produk yang kompleks.
Kerugian dari Cetakan Injeksi Termoplastik
Sementara cetakan injeksi termoplastik menawarkan banyak keuntungan, ada juga beberapa kelemahannya. Pabrikan perlu menilai faktor-faktor ini dengan hati-hati dan menimbangnya terhadap manfaatnya untuk menentukan kesesuaian cetakan injeksi termoplastik untuk aplikasi spesifiknya.
- Investasi Awal Tinggi: Menyiapkan operasi pencetakan injeksi termoplastik memerlukan investasi awal yang signifikan dalam desain dan fabrikasi cetakan serta pembelian mesin khusus. Biaya yang terkait dengan pembuatan cetakan dan perkakas bisa sangat besar, terutama untuk desain yang kompleks dan rumit.
- Keterbatasan Desain: Sementara cetakan injeksi termoplastik menawarkan fleksibilitas desain, ada batasan tertentu. Misalnya, mencapai ketebalan dinding yang seragam di seluruh bagian dapat menjadi tantangan, yang menyebabkan variasi dalam distribusi material dan potensi kelemahan struktural. Selain itu, adanya potongan bawah atau geometri kompleks mungkin memerlukan penggunaan fitur cetakan tambahan atau operasi sekunder, sehingga meningkatkan biaya dan waktu produksi.
- Waktu Pimpin Panjang:Proses perancangan dan fabrikasi cetakan untuk cetakan injeksi dapat memakan waktu, menyebabkan waktu tunggu yang lebih lama untuk pengembangan produk. Proses iterasi desain, produksi cetakan, dan pengujian dapat menambah waktu yang signifikan pada keseluruhan jadwal produksi, yang mungkin tidak sesuai untuk proyek dengan tenggat waktu yang ketat.
- Batasan Pemilihan Bahan:Meskipun cetakan injeksi termoplastik mendukung berbagai bahan, ada batasan dan kendala tertentu. Beberapa bahan mungkin memiliki persyaratan pemrosesan khusus atau ketersediaan terbatas, yang memengaruhi pilihan desain dan pemilihan bahan untuk aplikasi tertentu.
- Batasan Ukuran Bagian:Mesin cetak injeksi memiliki batasan ukuran, baik dari segi ukuran fisik alat maupun ukuran cetakan yang dapat ditampungnya. Memproduksi suku cadang besar mungkin memerlukan peralatan khusus atau metode manufaktur alternatif.
- Dampak lingkungan:Sementara industri bekerja menuju keberlanjutan, proses pencetakan injeksi termoplastik masih menghasilkan bahan limbah, termasuk skrap dan sprues. Pembuangan dan daur ulang yang tepat dari bahan-bahan ini diperlukan untuk meminimalkan dampak lingkungan.
- Kompleksitas Optimasi Proses:Mencapai parameter proses yang optimal untuk cetakan injeksi termoplastik dapat menjadi rumit dan memakan waktu. Pabrikan harus secara hati-hati mengontrol dan mengoptimalkan suhu, tekanan, laju pendinginan, dan waktu siklus untuk memastikan kualitas suku cadang yang konsisten dan meminimalkan kerusakan.
Jenis Termoplastik yang Digunakan dalam Cetakan Injeksi
Ini hanyalah beberapa contoh termoplastik yang biasa digunakan dalam cetakan injeksi. Setiap bahan memiliki sifat yang unik, sehingga cocok untuk aplikasi tertentu berdasarkan kekuatan, fleksibilitas, ketahanan terhadap bahan kimia, transparansi, dan biaya. Pabrikan harus mempertimbangkan sifat dan persyaratan ini saat memilih termoplastik yang sesuai untuk proyek pencetakan injeksi mereka.
- Polipropilena (PP):Polypropylene adalah termoplastik serbaguna yang biasa digunakan dalam cetakan injeksi. Ini menawarkan ketahanan kimia yang sangat baik, kepadatan rendah, dan kekuatan benturan yang baik. PP (polypropylene) memiliki aplikasi yang luas dalam pengemasan, komponen otomotif, peralatan rumah tangga, dan peralatan medis.
- Polietilen (PE):Polyethylene adalah termoplastik lain yang banyak digunakan dalam cetakan injeksi. Ini tersedia dalam berbagai bentuk, seperti polietilen densitas tinggi (HDPE) dan polietilen densitas rendah (LDPE). PE menawarkan ketahanan kimia, ketangguhan, dan fleksibilitas yang baik, sehingga cocok untuk botol, wadah, dan pipa.
- Polistirena (PS):Polystyrene adalah termoplastik serbaguna yang dikenal karena kejernihan, kekakuan, dan harganya yang terjangkau. Ini menemukan penggunaan umum dalam kemasan, barang konsumsi, dan produk sekali pakai. PS (polystyrene) memungkinkan pemrosesan cepat dan memberikan stabilitas dimensi yang baik, tetapi bisa rapuh dan rentan terhadap retak tekanan lingkungan.
- Akrilonitril Butadiena Styrene (ABS): ABS adalah termoplastik populer yang dikenal karena ketahanan benturan dan daya tahannya yang luar biasa. Ini menggabungkan sifat akrilonitril, butadiena, dan stirena untuk menciptakan bahan serbaguna yang cocok untuk suku cadang otomotif, rumah elektronik, dan mainan.
- Polivinil Klorida (PVC): PVC adalah termoplastik yang banyak digunakan yang dikenal karena ketahanan kimianya yang sangat baik, daya tahan, dan biaya rendah. Itu bisa kaku atau fleksibel tergantung pada formulasi dan aditif yang digunakan. PVC (polivinil klorida) menemukan penggunaan umum dalam konstruksi, isolasi listrik, produk perawatan kesehatan, dan pengemasan.
- Polikarbonat (PC): Polycarbonate adalah termoplastik transparan dengan dampak luar biasa dan ketahanan panas yang tinggi. Ini menemukan penggunaan umum dalam aplikasi yang membutuhkan kejernihan optik, seperti komponen otomotif, helm pengaman, dan tampilan elektronik.
- Nilon (Poliamida):Nylon adalah termoplastik yang kuat dan tahan lama yang dikenal karena sifat mekanik dan ketahanan kimianya yang sangat baik. Ini menemukan penggunaan umum dalam aplikasi yang menuntut kekuatan tinggi, seperti suku cadang otomotif, komponen industri, dan barang konsumsi.
- Polietilen Tereftalat (PET):PET adalah termoplastik yang populer untuk memproduksi botol, wadah, dan bahan pengemas. Ini menawarkan kejernihan yang baik, ketahanan kimia, dan sifat penghalang, sehingga cocok untuk aplikasi makanan dan minuman.
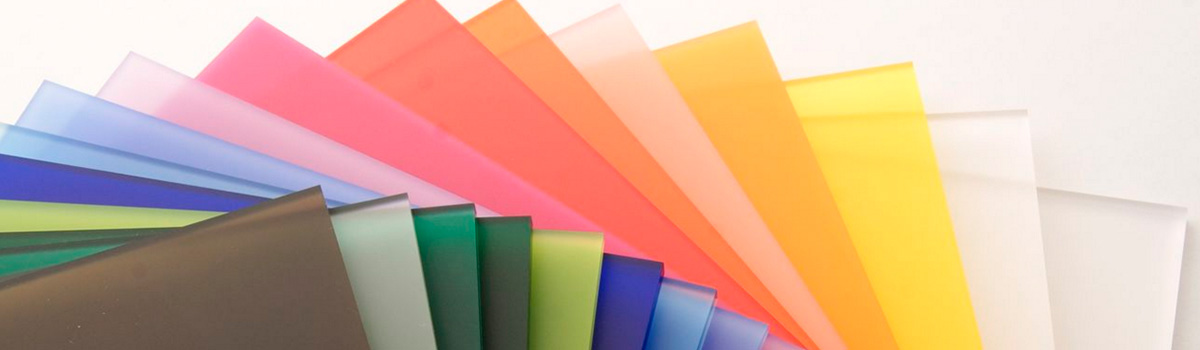
Sifat-sifat Termoplastik yang Digunakan dalam Cetakan Injeksi
Sifat-sifat termoplastik ini memainkan peran penting dalam menentukan kesesuaiannya untuk aplikasi cetakan injeksi tertentu. Produsen harus hati-hati mempertimbangkan sifat-sifat ini dan memilih termoplastik yang sesuai berdasarkan kinerja yang diinginkan, kondisi lingkungan, dan kebutuhan biaya.
- Properti mekanik:Termoplastik yang digunakan dalam cetakan injeksi dapat menunjukkan berbagai sifat mekanik, termasuk kekuatan tarik, ketahanan benturan, dan kekuatan lentur. Properti ini menentukan kemampuan material untuk menahan gaya yang diterapkan dan daya tahan keseluruhannya dalam berbagai aplikasi.
- Ketahanan Kimia:Banyak termoplastik yang digunakan dalam cetakan injeksi memiliki ketahanan yang luar biasa terhadap bahan kimia, pelarut, dan minyak. Properti ini sangat penting untuk aplikasi yang melibatkan paparan lingkungan yang keras atau zat korosif.
- Stabilitas Termal:Stabilitas termal termoplastik mengacu pada kemampuannya untuk menahan suhu tinggi tanpa degradasi yang signifikan. Beberapa termoplastik menunjukkan ketahanan panas yang sangat baik, memungkinkan mereka mempertahankan sifat mekaniknya bahkan pada suhu tinggi.
- Properti Listrik:Termoplastik yang digunakan dalam cetakan injeksi dapat memiliki sifat listrik tertentu, termasuk insulasi listrik, konduktivitas, atau kekuatan dielektrik. Properti ini sangat penting untuk aplikasi dalam industri listrik dan elektronik, di mana material harus memberikan kinerja listrik yang andal.
- Transparansi dan Kejelasan:Termoplastik tertentu, seperti polikarbonat dan PET, menawarkan transparansi dan kejelasan yang sangat baik, menjadikannya cocok untuk aplikasi yang membutuhkan sifat optik. Pabrikan biasanya menggunakan bahan ini dalam produk seperti jendela transparan, lensa, dan layar.
- Fleksibilitas dan Ketangguhan: Fleksibilitas dan ketangguhan adalah sifat penting dari termoplastik yang digunakan dalam aplikasi yang membutuhkan ketahanan benturan dan daya tahan. Beberapa termoplastik, seperti ABS dan nilon, menawarkan ketangguhan yang sangat baik, memungkinkannya menahan benturan berulang kali tanpa putus.
- Stabilitas dimensi:Stabilitas dimensi mengacu pada kemampuan termoplastik untuk mempertahankan bentuk dan ukurannya dalam berbagai kondisi, termasuk perubahan suhu. Material dengan stabilitas dimensi yang baik memastikan dimensi bagian yang konsisten, meminimalkan risiko bengkok atau distorsi.
- Kompatibilitas Kimia:Kompatibilitas kimia termoplastik mengacu pada kemampuannya untuk menahan degradasi atau interaksi dengan berbagai bahan kimia, termasuk asam, basa, dan pelarut. Untuk memastikan kinerja yang optimal, memilih termoplastik yang dapat menahan lingkungan kimia tertentu yang akan dihadapinya dalam aplikasi yang dimaksud sangatlah penting.
- Kepadatan: Termoplastik memiliki ketebalan yang bervariasi, yang dapat memengaruhi berat dan sifat bagian keseluruhannya. Bahan dengan kerapatan rendah, seperti polietilen, menawarkan solusi yang ringan, sedangkan bahan dengan kerapatan tinggi, seperti polipropilena, memberikan kekuatan dan kekakuan tambahan.
Proses Pencetakan Injeksi: Langkah demi Langkah
Proses pencetakan injeksi mengikuti langkah-langkah ini, memungkinkan produksi komponen termoplastik berkualitas tinggi yang efisien dan presisi. Setiap langkah memerlukan kontrol dan pemantauan yang cermat untuk memastikan konsistensi dimensi bagian, sifat material, dan kualitas keseluruhan.
- Desain dan Fabrikasi Mould: Langkah pertama dalam proses pencetakan injeksi adalah desain dan pembuatan cetakan. Pabrikan harus membuat desain cetakan yang tepat dan detail untuk mencapai spesifikasi part yang diinginkan. Produsen kemudian membuat cetakan menggunakan berbagai teknik, seperti CNC atau pemesinan pelepasan listrik (EDM).
- Persiapan Bahan: Langkah selanjutnya adalah persiapan setelah cetakan siap. Pelet atau butiran termoplastik dipilih berdasarkan sifat material yang diinginkan dan dilebur dalam hopper. Operator kemudian memasukkan bahan tersebut ke dalam tong mesin cetak injeksi, di mana ia mengalami peleburan dan homogenisasi.
- Injeksi:Selama fase injeksi, operator menyuntikkan termoplastik cair ke dalam rongga cetakan di bawah tekanan tinggi. Unit injeksi mesin mendorong bahan yang meleleh melalui nosel dan masuk ke dalam cetakan. Bahan mengisi rongga cetakan, mengambil bentuk bagian yang diinginkan.
- Pendinginan dan Pemadatan:Setelah mengisi cetakan, operator membiarkan plastik cair menjadi dingin dan mengeras. Pendinginan sangat penting untuk mencapai stabilitas dimensi dan pembentukan bagian yang tepat. Operator dapat mengontrol proses pendinginan dengan mensirkulasikan cairan pendingin melalui saluran di dalam cetakan atau dengan menggunakan pelat pendingin.
- Pembukaan dan Pengeluaran Cetakan:Operator membuka cetakan dan mengeluarkan bagian dari rongga cetakan setelah plastik mengeras. Sistem ejeksi di dalam mesin menggunakan pin, pelat ejektor, atau semburan udara untuk menghilangkan bagian dari cetakan. Cetakan kemudian siap untuk siklus injeksi berikutnya.
- Pengolahan pasca: Setelah dikeluarkan, bagian tersebut dapat menjalani operasi pasca-pemrosesan, seperti pemangkasan, penghalusan, atau penyelesaian permukaan. Langkah-langkah ini membantu menghilangkan material berlebih, menghaluskan tepi kasar, dan menyempurnakan tampilan akhir komponen.
- Pengecekan kualitas: Langkah terakhir melibatkan pemeriksaan bagian yang disuntikkan untuk kualitas dan memastikan mereka memenuhi persyaratan yang ditentukan. Berbagai teknik kontrol kualitas, termasuk pengukuran dimensi, inspeksi visual, dan pengujian fungsional, dapat digunakan untuk memverifikasi kualitas dan integritas komponen.
- Daur Ulang dan Penggunaan Kembali Material:Bahan sisa atau sisa yang dihasilkan selama pencetakan injeksi dapat didaur ulang dan digunakan kembali. Mengurangi penggunaan bahan termoplastik baru membantu meminimalkan limbah dan meningkatkan keberlanjutan.
Peralatan yang Digunakan dalam Cetakan Injeksi
Komponen peralatan ini memfasilitasi proses pencetakan injeksi, mulai dari melelehkan dan menyuntikkan bahan termoplastik hingga membentuk, mendinginkan, dan mengeluarkan bagian akhir. Pengoperasian dan pemeliharaan yang tepat dari komponen peralatan ini sangat penting untuk mencapai produksi cetakan injeksi yang efisien dan berkualitas tinggi.
- Mesin Cetak Injeksi:Peralatan utama dalam cetakan injeksi bertanggung jawab untuk melelehkan bahan termoplastik, menyuntikkannya ke dalam cetakan, dan mengendalikan prosesnya.
- Cetakan: Cetakan, dirancang khusus untuk menciptakan bentuk dan fitur bagian plastik yang diinginkan, terdiri dari dua bagian, rongga dan inti. Operator memasangnya ke unit penjepit mesin cetak injeksi.
- hopper:Wadah yang menampung bahan termoplastik dalam bentuk pelet atau butiran dan memasukkannya ke dalam tong mesin cetak injeksi untuk peleburan dan injeksi.
- Laras dan Sekrup: Laras, ruang silinder, melelehkan dan menghomogenkan bahan termoplastik saat sekrup berputar di dalamnya untuk melelehkan, mencampur, dan membakukan bahan.
- Sistem Pemanasan dan Pendinginan:Mesin cetak injeksi memiliki elemen pemanas, seperti pemanas listrik atau pemanas yang menggunakan minyak panas, untuk menaikkan suhu laras, dan sistem pendingin, seperti sirkulasi air atau oli, untuk mendinginkan cetakan dan memadatkan bagian plastik.
- Sistem ejektor:Menghilangkan bagian cetakan dari rongga cetakan setelah pemadatan, biasanya menggunakan pin ejektor, pelat, atau semburan udara selama pembukaan cetakan.
- Sistem pengaturan:Memantau dan mengontrol berbagai parameter proses pencetakan injeksi, memungkinkan operator mengatur dan menyesuaikan parameter seperti kecepatan injeksi, suhu, tekanan, dan waktu pendinginan.
Mesin Cetak Injeksi: Jenis dan Karakteristiknya
Setiap jenis mesin cetak injeksi memiliki karakteristik dan keunggulannya masing-masing, memungkinkan produsen memilih perangkat yang paling sesuai untuk kebutuhan produksi spesifik mereka.
- Mesin Cetak Injeksi Hidrolik: Mesin ini menggunakan sistem hidrolik untuk menghasilkan tekanan yang diperlukan untuk menyuntikkan plastik cair ke dalam cetakan. Mereka dikenal karena kekuatan penjepitnya yang tinggi, kontrol yang presisi, dan keserbagunaan dalam menangani berbagai termoplastik. Mesin hidrolik cocok untuk produksi skala besar dan dapat mengakomodasi cetakan yang rumit.
- Mesin Cetak Injeksi Listrik:Mesin listrik menggunakan motor servo listrik untuk pengoperasian mesin, termasuk sistem injeksi, penjepitan, dan ejektor. Mereka menawarkan kontrol yang presisi, efisiensi energi, dan waktu respons yang lebih cepat daripada mesin hidrolik. Mesin listrik ideal untuk aplikasi pencetakan presisi yang membutuhkan pengulangan dan akurasi tinggi.
- Mesin Cetak Injeksi Hibrida:Mesin hybrid menggabungkan keunggulan perangkat hidrolik dan listrik. Mereka menggunakan kombinasi sistem servo hidrolik dan listrik untuk mencapai presisi tinggi, efisiensi energi, dan efektivitas biaya. Mesin hybrid cocok untuk berbagai aplikasi, memberikan keseimbangan antara performa dan biaya operasional.
- Mesin Cetak Injeksi Dua Pelat: Mesin dua pelat memiliki desain unik dengan dua pelat terpisah untuk menjepit cetakan. Desain ini memberikan stabilitas yang ditingkatkan, sinkronisasi cetakan yang lebih baik, dan memungkinkan ukuran cetakan yang lebih besar dan gaya penjepitan yang lebih tinggi. Mesin dua pelat cocok untuk bagian besar dan kompleks yang membutuhkan cetakan yang presisi.
- Mesin Cetak Injeksi Multi-Komponen:Pabrikan merancang mesin ini untuk memproduksi suku cadang dengan berbagai bahan atau warna dalam satu siklus pencetakan. Mereka memiliki berbagai unit dan cetakan injeksi, memungkinkan injeksi bahan yang berbeda secara bersamaan. Mesin multi-komponen menawarkan fleksibilitas dan efisiensi dalam pembuatan komponen kompleks dengan berbagai karakteristik.
- Mesin Cetak Injeksi Mikro:Dirancang khusus untuk memproduksi komponen kecil dan presisi, mesin cetak mikro-injeksi menawarkan presisi dan akurasi yang sangat tinggi. Mereka dapat menghasilkan detail yang rumit dengan toleransi yang ketat dan pemborosan material yang minimal. Elektronik, perangkat medis, dan mikro-optik umumnya menggunakan mesin cetak mikro-injeksi.
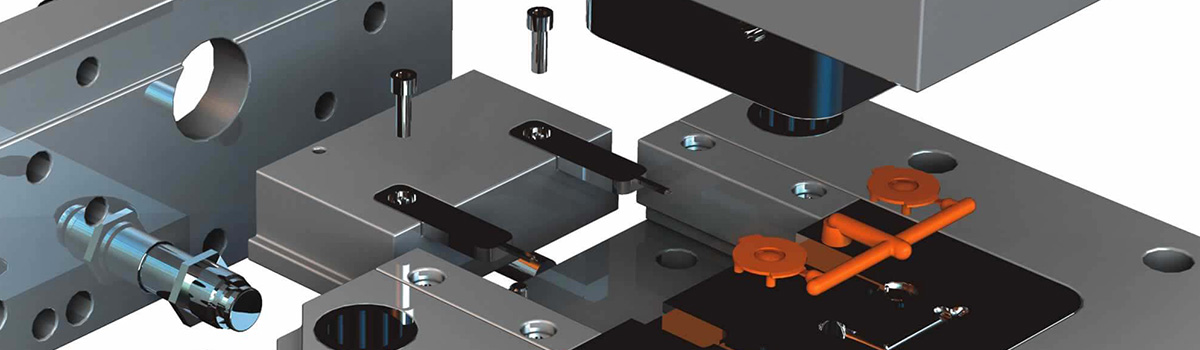
Pertimbangan Desain Cetakan untuk Cetakan Injeksi
Pertimbangan desain cetakan yang cermat sangat penting untuk keberhasilan produksi cetakan injeksi.
- Desain Bagian:Desain cetakan harus mengakomodasi persyaratan khusus dari bagian tersebut, termasuk bentuk, dimensi, dan fitur fungsionalnya. Produsen harus benar-benar mempertimbangkan sudut draf, ketebalan dinding, potongan bawah, dan elemen apa pun yang diperlukan untuk memastikan kemudahan pengeluaran dan kualitas suku cadang.
- Bahan cetakan: Pemilihan bahan cetakan sangat penting untuk mencapai daya tahan, stabilitas dimensi, dan tahan panas. Bahan cetakan umum termasuk paduan baja, paduan aluminium, dan baja perkakas. Pilihan material bergantung pada faktor-faktor seperti volume produksi, kerumitan komponen, dan masa pakai alat yang diharapkan.
- Sistem pendingin:Pendinginan yang efisien sangat penting untuk pemadatan bagian yang tepat dan meminimalkan waktu siklus. Desain cetakan harus menggabungkan saluran pendingin atau sisipan yang ditempatkan secara strategis untuk memastikan pendinginan cetakan yang seragam. Pendinginan yang tepat mengurangi risiko kelengkungan, penyusutan, dan kerusakan komponen.
- Ventilasi:Ventilasi yang memadai diperlukan untuk memungkinkan keluarnya udara dan gas selama proses injeksi. Ventilasi yang tidak memadai dapat menyebabkan perangkap gas, bekas luka bakar, atau pengisian komponen yang tidak lengkap. Produsen dapat mencapai ventilasi dengan memasukkan alur ventilasi, pin, atau mekanisme lain ke dalam desain cetakan.
- Sistem pengeluaran:Desain cetakan harus mencakup sistem ejeksi yang efektif untuk mengeluarkan bagian cetakan dari rongga cetakan dengan aman dan efisien. Sistem ejeksi dapat terdiri dari pin ejektor, selongsong, atau mekanisme lain, yang ditempatkan secara strategis untuk menghindari gangguan pada fungsi atau fitur penting.
- Desain Gerbang:Gerbang adalah tempat plastik cair memasuki rongga cetakan. Desain gerbang harus memastikan pengisian bagian yang tepat, meminimalkan garis aliran, dan mencegah pembekuan material sebelum waktunya. Desain gerbang standar meliputi gerbang tepi, gerbang terowongan, dan sistem hot runner, bergantung pada persyaratan suku cadang dan sifat material.
- Garis Perpisahan:Desain cetakan harus menentukan garis perpisahan yang sesuai, yaitu garis di mana kedua bagian cetakan bertemu. Penempatan parting line yang tepat memastikan flash minimal dan ketidakcocokan parting line dan memfasilitasi perakitan cetakan yang efisien.
- Perawatan Mould dan Kemudahan Servis: Pabrikan harus mempertimbangkan kemudahan perawatan, perbaikan, dan servis cetakan. Komponen cetakan harus mudah dijangkau untuk dibersihkan, diperiksa, dan diganti. Menggabungkan fitur seperti sisipan perubahan cepat atau desain cetakan modular dapat meningkatkan kemudahan servis cetakan.
Bahan Cetakan yang Digunakan dalam Cetakan Injeksi
Berkolaborasi dengan spesialis bahan cetakan dan mempertimbangkan kebutuhan khusus aplikasi cetakan dapat membantu menentukan bahan yang paling cocok untuk mencapai kinerja cetakan dan kualitas komponen yang optimal.
- Paduan Baja: Paduan baja, seperti baja perkakas (misalnya, P20, H13) dan baja tahan karat, biasanya digunakan untuk cetakan injeksi karena daya tahannya yang sangat baik, tahan panas, dan tahan aus. Bahan-bahan ini dapat menahan suhu dan tekanan tinggi dalam proses pencetakan injeksi dan menawarkan stabilitas dimensi yang baik untuk menghasilkan komponen berkualitas tinggi.
- Paduan Aluminium:Paduan aluminium, seperti 7075 dan 6061, ringan dan menawarkan konduktivitas termal yang baik, membuatnya cocok untuk cetakan yang membutuhkan pendinginan yang efisien. Produsen sering menggunakan cetakan aluminium untuk pembuatan prototipe, produksi volume rendah, atau aplikasi di mana pengurangan berat sangat penting. Namun, cetakan aluminium mungkin memiliki daya tahan yang lebih rendah dibandingkan dengan paduan baja.
- Paduan Tembaga:Paduan tembaga, seperti tembaga berilium, menunjukkan konduktivitas termal yang tinggi dan kemampuan mesin yang baik. Mereka menemukan penggunaan dalam cetakan yang membutuhkan perpindahan panas yang sangat baik untuk pendinginan yang efektif. Paduan tembaga dapat membantu mengurangi waktu siklus dengan menghilangkan panas dengan cepat dari bagian yang dicetak, menghasilkan pemadatan yang lebih cepat.
- Baja Alat:Baja perkakas, termasuk H13, S7, dan D2, dirancang untuk aplikasi perkakas berperforma tinggi. Baja ini menawarkan kombinasi kekuatan tinggi, kekerasan, dan ketahanan aus. Baja perkakas sesuai dengan cetakan dengan volume produksi tinggi, bahan abrasif, atau kondisi cetakan yang menuntut.
- Paduan Nikel:Paduan nikel, seperti Inconel dan Hastelloy, dikenal karena ketahanan korosinya yang luar biasa, kekuatan suhu tinggi, dan stabilitas termal. Produsen menggunakan paduan ini dalam cetakan yang menangani bahan korosif atau membutuhkan ketahanan terhadap suhu ekstrem dan lingkungan cetakan yang agresif.
- Bahan Komposit:Bahan komposit, seperti plastik yang diperkuat atau komposit dengan sisipan logam, kadang-kadang digunakan untuk aplikasi pencetakan tertentu. Bahan-bahan ini menawarkan keseimbangan sifat, seperti kekuatan tinggi, stabilitas termal, dan pengurangan bobot. Cetakan komposit dapat menjadi alternatif hemat biaya untuk kebutuhan produksi tertentu.
Jenis Cetakan Injeksi
Cetakan injeksi adalah proses pembuatan komponen plastik yang serbaguna dan banyak digunakan.
- Cetakan Dua Piring:Cetakan dua pelat adalah jenis cetakan injeksi yang paling umum. Ini terdiri dari dua pelat, pelat rongga, dan pelat inti, yang terpisah untuk memungkinkan pengeluaran bagian cetakan. Pelat rongga berisi sisi rongga cetakan, sedangkan pelat inti menampung sisi inti. Pabrikan menggunakan cetakan dua pelat untuk memproduksi berbagai suku cadang karena desainnya yang relatif sederhana.
- Cetakan Tiga Piring:Cetakan tiga pelat adalah versi lanjutan dari cetakan dua pelat. Ini termasuk pelat tambahan, pelari, atau pelat sariawan. Pelat runner membuat saluran terpisah untuk sprue, runner, dan gerbang, memungkinkan pelepasan bagian cetakan dengan lebih mudah. Pabrikan biasanya menggunakan cetakan tiga pelat untuk detail dengan sistem gating yang rumit atau saat menghindari sisa gerbang pada potongan yang diinginkan.
- Cetakan Pelari Panas:Sistem runner dan gate dipanaskan dalam cetakan hot runner, menghilangkan kebutuhan untuk pemadatan dan peleburan ulang material selama setiap siklus. Sistem pelari panas terdiri dari manifold yang dipanaskan dan nosel yang mempertahankan keadaan cair plastik. Cetakan hot runner menawarkan keuntungan seperti pengurangan waktu siklus, limbah material yang lebih rendah, dan kualitas komponen yang lebih baik dengan meminimalkan sisa-sisa gerbang.
- Cetakan Pelari Dingin: Cetakan cold runner memiliki sistem runner dan gate tradisional di mana plastik cair mengalir melalui cold runner yang mengeras di setiap siklus. Operator kemudian memindahkan pelari yang mengeras, menghasilkan limbah material. Pabrikan biasanya menggunakan cetakan pelari yang rumit untuk volume produksi yang lebih rendah atau ketika biaya bahan kurang kritis karena desainnya yang lebih lugas.
- Masukkan Cetakan:Masukkan cetakan memasukkan sisipan logam atau plastik ke dalam rongga cetakan selama cetakan injeksi. Sisipan dapat ditempatkan sebelumnya ke dalam cetakan atau dimasukkan dengan proses otomatis. Cetakan ini memungkinkan untuk mengintegrasikan komponen tambahan atau elemen penguat ke dalam bagian cetakan, meningkatkan fungsionalitas atau kekuatannya.
- Cetakan berlebih: Overmolding melibatkan pencetakan satu bahan di atas yang lain, biasanya mengikat substrat plastik yang kaku dengan elastomer atau termoplastik yang lebih lembut. Proses ini memungkinkan pembuatan komponen dengan berbagai bahan atau tekstur dalam satu cetakan, memberikan cengkeraman, bantalan, atau fitur estetika yang lebih baik.
Faktor-faktor yang Mempengaruhi Biaya Cetakan Injeksi
Mempertimbangkan faktor-faktor ini dapat membantu produsen memperkirakan dan mengoptimalkan biaya cetakan injeksi, memastikan keseimbangan antara kualitas, efisiensi, dan efektivitas biaya untuk kebutuhan produksi khusus mereka.
- Kompleksitas Bagian:Kompleksitas desain bagian memainkan peran penting dalam menentukan biaya cetakan injeksi. Geometri yang rumit, potongan bawah, dinding tipis, atau fitur kompleks mungkin memerlukan perkakas tambahan, cetakan khusus, atau siklus yang lebih panjang, sehingga meningkatkan biaya pembuatan secara keseluruhan.
- Pemilihan Material:Pemilihan bahan termoplastik mempengaruhi biaya pencetakan injeksi. Bahan yang berbeda memiliki harga per kilogram yang bervariasi, dan faktor-faktor seperti ketersediaan bahan, sifat, dan persyaratan pemrosesan dapat memengaruhi keseluruhan biaya bahan.
- Perkakas dan Desain Cetakan: Perkakas awal dan biaya desain cetakan signifikan dalam biaya pencetakan injeksi. Faktor-faktor seperti kompleksitas cetakan, jumlah rongga, ukuran cetakan, dan bahan cetakan berkontribusi pada biaya perkakas dan pembuatan cetakan. Cetakan atau cetakan yang lebih kompleks yang membutuhkan fitur canggih dapat meningkatkan investasi di muka.
- Volume produksi: Volume produksi berdampak langsung pada biaya per bagian dalam cetakan injeksi. Buku yang lebih tinggi sering menghasilkan skala ekonomi, mengurangi biaya per bagian. Sebaliknya, proses produksi dengan volume rendah dapat menimbulkan biaya yang lebih tinggi karena penyetelan, perkakas, dan pemborosan material.
- Waktu siklus: Waktu siklus, yang meliputi fase pendinginan dan ejeksi, memengaruhi kapasitas produksi dan biaya keseluruhan. Waktu siklus yang lebih lama menghasilkan output produksi yang berkurang dan harga yang berpotensi lebih tinggi. Mengoptimalkan desain cetakan, sistem pendingin, dan parameter proses dapat meminimalkan waktu siklus dan meningkatkan efisiensi.
- Persyaratan kualitas:Persyaratan kualitas yang ketat atau sertifikasi khusus dapat memengaruhi biaya cetak injeksi. Memenuhi toleransi yang tepat, persyaratan penyelesaian permukaan, atau pengujian tambahan mungkin memerlukan sumber daya, proses, atau inspeksi lain, yang menambah biaya keseluruhan.
- Operasi Sekunder:Jika bagian yang dicetak memerlukan operasi pasca-pemrosesan seperti perakitan, pengecatan, atau langkah penyelesaian tambahan, operasi ini dapat menambah biaya pencetakan injeksi secara keseluruhan.
- Pemasok dan Lokasi:Pilihan pemasok cetakan injeksi dan lokasinya dapat memengaruhi biaya. Biaya tenaga kerja, overhead, logistik, dan biaya transportasi bervariasi berdasarkan lokasi pemasok, yang berdampak pada keseluruhan biaya produksi.
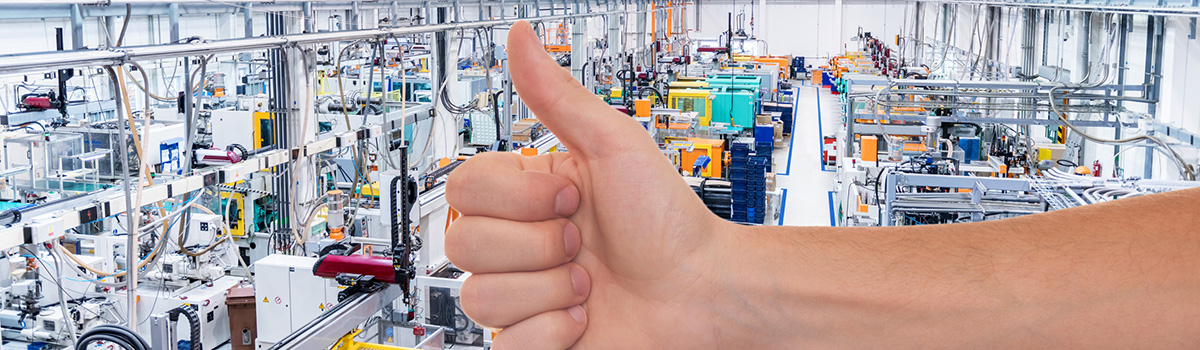
Kontrol Kualitas dalam Cetakan Injeksi
Menerapkan langkah-langkah kontrol kualitas yang kuat di seluruh proses pencetakan injeksi membantu mengidentifikasi dan mengatasi potensi cacat, penyimpangan, atau inkonsistensi, memastikan produksi suku cadang berkualitas tinggi yang memenuhi spesifikasi dan persyaratan pelanggan.
- Pemantauan Proses: Pemantauan berkelanjutan terhadap parameter proses utama, seperti suhu lelehan, tekanan injeksi, waktu pendinginan, dan waktu siklus, memastikan konsistensi dan pengulangan dalam produksi komponen. Pemantauan waktu nyata dan sistem otomatis dapat mendeteksi variasi atau penyimpangan dari parameter yang ditetapkan, memungkinkan penyesuaian tepat waktu dan menjaga stabilitas proses.
- Inspeksi dan Pengukuran:Peninjauan dan pengukuran rutin bagian cetakan sangat penting untuk memverifikasi akurasi dimensi, kualitas bagian, dan kepatuhan terhadap spesifikasi. Layanan kami mencakup berbagai metode kontrol kualitas, seperti mengukur dimensi, menganalisis kualitas permukaan, melakukan inspeksi visual, dan melakukan pengujian fungsional. Berbagai teknik inspeksi, seperti mesin pengukur koordinat (CMM) dan sistem inspeksi optik dan visual, digunakan untuk evaluasi yang akurat.
- Kontrol Proses Statistik (SPC): SPC melibatkan pengumpulan dan analisis data proses untuk memantau dan mengontrol kualitas cetakan injeksi. Metode statistik, seperti bagan kendali dan analisis kapabilitas proses, membantu mengidentifikasi tren, mendeteksi variasi proses, dan memastikan proses tetap berada dalam batas kendali yang ditentukan. SPC memungkinkan identifikasi masalah secara proaktif dan memfasilitasi pengoptimalan proses.
- Pengujian Material: Menguji bahan baku, seperti termoplastik, aditif, dan pewarna, memastikan kualitas dan kesesuaiannya untuk pencetakan injeksi. Pengujian material dapat mencakup analisis indeks aliran lelehan (MFI), sifat mekanik, karakteristik termal, dan komposisi material. Memverifikasi kualitas bahan membantu mencegah cacat dan ketidakkonsistenan pada bagian cetakan.
- Perawatan dan Pemeriksaan Perkakas:Perawatan yang tepat dan pemeriksaan cetakan injeksi secara teratur sangat penting untuk memastikan kualitas cetakan injeksi. Pembersihan, pelumasan, dan penilaian komponen cetakan secara teratur membantu mencegah keausan, kerusakan, atau degradasi yang dapat memengaruhi kualitas komponen. Perbaikan atau penggantian komponen cetakan yang aus atau rusak secara tepat waktu sangat penting untuk mempertahankan kinerja pencetakan yang konsisten.
- Dokumentasi dan Ketertelusuran:Mempertahankan dokumentasi yang komprehensif dan catatan ketertelusuran sangat penting untuk kontrol kualitas dalam pencetakan injeksi. Penting untuk mencatat parameter proses, hasil inspeksi, informasi material, dan setiap perubahan atau penyesuaian yang dibuat selama produksi. Dokumentasi yang tepat memungkinkan ketertelusuran suku cadang, memfasilitasi analisis akar masalah, dan memastikan konsistensi dalam kualitas.
- Pelatihan dan Pengembangan Keterampilan: Memberikan program pelatihan dan pengembangan keterampilan yang memadai untuk operator, teknisi, dan personel kontrol kualitas meningkatkan pemahaman mereka tentang proses pencetakan injeksi, persyaratan kualitas, dan teknik inspeksi. Personil yang terlatih dapat mendeteksi cacat, memecahkan masalah, dan menerapkan tindakan korektif secara efektif, memastikan produksi berkualitas tinggi.
Cacat Cetakan Injeksi Umum dan Cara Menghindarinya
Inspeksi, pemantauan, dan analisis rutin terhadap proses pencetakan injeksi serta pemeliharaan dan penyesuaian peralatan dan cetakan yang tepat dapat membantu mengidentifikasi dan mengatasi cacat umum ini.
- Tanda Tenggelam:Sink mark adalah depresi atau lekukan pada permukaan bagian cetakan yang disebabkan oleh pendinginan atau penyusutan yang tidak merata. Seseorang harus mempertimbangkan lokasi dan desain gerbang yang tepat, desain sistem pendingin yang optimal, dan distribusi ketebalan dinding yang seragam untuk menghindari bekas bak cuci. Meningkatkan tekanan injeksi atau menyesuaikan waktu pendinginan juga dapat membantu meminimalkan bekas bak cuci.
- Warp:Warpage mengacu pada deformasi atau pembengkokan bagian cetakan setelah dikeluarkan karena pendinginan yang tidak merata atau tegangan sisa. Mempertahankan ketebalan dinding yang seragam, menggunakan saluran pendinginan yang tepat, dan memastikan pengisian dan pengepakan cetakan yang seimbang sangat penting untuk mencegah kelengkungan. Mengoptimalkan suhu cetakan, menggunakan sudut draf yang sesuai, dan mengontrol suhu bahan dan kecepatan injeksi dapat membantu meminimalkan kelengkungan.
- Flash:Kilatan terjadi ketika bahan berlebih mengalir ke garis perpisahan cetakan, menghasilkan tonjolan tipis yang tidak diinginkan atau bahan tambahan pada bagian akhir. Satu dapat secara efektif mencegah flash dengan memastikan desain cetakan yang tepat, termasuk menerapkan gaya penjepitan yang memadai, keselarasan yang tepat, dan menggunakan teknik ventilasi yang tepat. Mengoptimalkan parameter proses seperti tekanan injeksi, suhu, dan waktu siklus mengurangi flash.
- Tembakan pendek:Tembakan cepat terjadi ketika bahan yang disuntikkan tidak mengisi rongga cetakan, menghasilkan bagian yang tidak lengkap. Pemilihan bahan yang tepat, memastikan suhu lelehan dan viskositas yang memadai, serta mempertahankan tekanan dan waktu injeksi yang tepat sangat penting untuk menghindari foto pendek. Selain itu, memverifikasi desain cetakan untuk ukuran pelari dan gerbang yang memadai serta ventilasi yang tepat dapat membantu mencegah bidikan cepat.
- Garis las:Garis las terjadi ketika dua atau lebih muka aliran material cair bertemu dan memadat, menghasilkan garis atau tanda yang terlihat pada permukaan bagian. Desain gate dan runner yang baik, temperatur leleh yang optimal, kecepatan injeksi, dan penyesuaian aliran material dan geometri part dapat meminimalkan garis las. Analisis aliran cetakan dan pengoptimalan penempatan gerbang juga dapat membantu mencegah atau mengurangi garis las.
- Tanda Bakar:Bekas luka bakar adalah perubahan warna atau bercak hitam pada permukaan bagian cetakan yang disebabkan oleh panas yang berlebihan atau bahan yang terlalu panas. Menghindari suhu lelehan yang ekstrem, menggunakan saluran pendingin yang sesuai, dan mengoptimalkan waktu siklus dapat membantu mencegah bekas luka bakar. Ventilasi yang memadai, desain gerbang yang tepat, dan pengontrolan suhu cetakan juga berkontribusi untuk meminimalkan bekas luka bakar.
Operasi Pasca Pencetakan: Penyelesaian dan Perakitan
Setelah cetakan injeksi, banyak bagian yang dicetak mungkin memerlukan operasi finishing dan perakitan tambahan untuk mencapai produk akhir yang diinginkan. Operasi pasca-pencetakan ini dapat mencakup:
- Pemangkasan:Buang bahan berlebih atau flash di sekitar bagian cetakan menggunakan alat pemangkas atau pemotong.
- Permukaan Pengobatan:Meningkatkan penampilan atau fungsionalitas permukaan bagian menggunakan berbagai teknik seperti pengecatan, pelapisan, atau tekstur.
- Majelis:Menggabungkan beberapa bagian cetakan atau menambahkan komponen seperti pengencang, sisipan, atau label untuk melengkapi produk akhir.
- Pengujian:Verifikasi kualitas dan fungsionalitas part melalui berbagai metode pengujian seperti analisis dimensi, pengujian sifat material, atau pengujian kinerja.
- Kemasan dan pengiriman:Pengemasan dan pelabelan produk jadi yang tepat untuk pengiriman ke pelanggan atau pengguna akhir.
Pemilihan operasi pasca-pencetakan bergantung pada aplikasi spesifik dan karakteristik produk akhir yang diinginkan. Kolaborasi erat antara ahli cetakan injeksi, spesialis finishing dan perakitan, dan pelanggan sangat penting untuk mencapai kualitas dan fungsionalitas produk absolut yang diinginkan. Perencanaan yang tepat dan integrasi operasi pasca-pencetakan ke dalam proses produksi dapat membantu memastikan produksi yang efisien dan pengiriman produk berkualitas tinggi secara tepat waktu.
Cetakan Injeksi vs. Proses Manufaktur Plastik Lainnya
Setiap proses pembuatan plastik memiliki kelebihan dan keterbatasan, sehingga cocok untuk aplikasi yang berbeda.
- Cetakan Injeksi: Cetakan injeksi adalah proses manufaktur yang sangat serbaguna dan banyak digunakan untuk memproduksi komponen plastik. Ini menawarkan keuntungan seperti efisiensi produksi yang tinggi, replikasi bagian yang presisi, dan kemampuan untuk membuat geometri yang kompleks. Cetakan injeksi cocok untuk proses produksi volume tinggi dan memungkinkan untuk menggunakan berbagai bahan termoplastik. Ini menawarkan akurasi dimensi dan penyelesaian permukaan yang sangat baik, menjadikannya ideal untuk berbagai industri seperti otomotif, barang konsumen, dan perangkat medis.
- cetakan tiup: Blow moulding adalah proses yang digunakan terutama untuk memproduksi komponen plastik berongga, seperti botol, wadah, dan komponen otomotif. Ini melibatkan peleburan plastik dan menggembungkannya ke dalam rongga cetakan, menciptakan bentuk yang diinginkan. Blow moulding cocok untuk produksi volume tinggi dan dapat menghasilkan bagian yang besar dan ringan dengan ketebalan dinding yang seragam. Namun, itu terbatas dalam hal kompleksitas bagian dan pemilihan material dibandingkan dengan cetakan injeksi.
- Pembentukan panas:Thermoforming adalah proses yang digunakan untuk memproduksi bagian plastik dengan memanaskan lembaran termoplastik dan membentuknya menggunakan cetakan atau pembentuk vakum. Ini menemukan penggunaan umum dalam kemasan, produk sekali pakai, dan produk berskala besar seperti baki dan penutup. Thermoforming menawarkan produksi hemat biaya untuk komponen besar dan memungkinkan pembuatan prototipe cepat. Namun, memiliki keterbatasan mengenai kompleksitas bagian, pemilihan material, dan akurasi dimensi dibandingkan dengan cetakan injeksi.
- Ekstrusi:Ekstrusi adalah proses berkelanjutan untuk menghasilkan profil plastik, lembaran, tabung, dan film. Ini melibatkan peleburan resin plastik dan memaksanya melalui cetakan untuk menciptakan bentuk yang diinginkan. Ekstrusi cocok untuk memproduksi produk plastik yang panjang dan terus menerus dengan penampang yang konsisten. Sementara ekstrusi menawarkan tingkat produksi yang tinggi dan efektivitas biaya, itu terbatas dalam hal geometri bagian yang kompleks dan kontrol dimensi yang tepat dibandingkan dengan cetakan injeksi.
- Cetakan Kompresi:Pencetakan kompresi melibatkan penempatan bahan termoset dalam jumlah yang telah diukur sebelumnya dalam rongga cetakan yang dipanaskan dan mengompresnya di bawah tekanan tinggi sampai sembuh. Ini menemukan penggunaan umum dalam memproduksi suku cadang dengan kekuatan tinggi dan stabilitas dimensi, seperti komponen otomotif dan isolasi listrik. Cetakan kompresi menawarkan konsistensi bagian yang baik, efisiensi produksi yang tinggi, dan kemampuan untuk menggunakan berbagai bahan. Namun, itu terbatas dalam hal kompleksitas bagian dan waktu siklus dibandingkan dengan cetakan injeksi.
Aplikasi Cetakan Injeksi Termoplastik
Berbagai industri banyak menggunakan cetakan injeksi termoplastik karena keserbagunaan, efisiensi, dan efektivitas biayanya. Beberapa aplikasi cetakan injeksi termoplastik meliputi:
- Industri otomotif: Industri otomotif banyak menggunakan cetakan injeksi termoplastik untuk memproduksi berbagai komponen, termasuk trim interior dan eksterior, dasbor, panel pintu, bumper, dan konektor listrik. Proses ini memungkinkan replikasi komponen secara presisi, geometri kompleks, dan material ringan, sehingga meningkatkan efisiensi bahan bakar dan fleksibilitas desain.
- Barang konsumsi:Cetakan injeksi menemukan aplikasi luas dalam memproduksi barang-barang konsumen seperti peralatan rumah tangga, perangkat elektronik, wadah pengemasan, dan mainan. Proses ini memungkinkan produksi massal produk yang tahan lama dan berkualitas tinggi dengan dimensi dan permukaan akhir yang konsisten. Ini juga memungkinkan opsi penyesuaian dan iterasi produk cepat.
- Alat kesehatan:Cetakan injeksi memainkan peran penting dalam industri medis untuk memproduksi berbagai perangkat, termasuk jarum suntik, instrumen bedah, komponen implan, dan sistem penghantaran obat. Proses tersebut memastikan produksi suku cadang yang steril, presisi, dan biokompatibel yang memenuhi persyaratan peraturan yang ketat dari sektor perawatan kesehatan.
- Industri Elektronik dan Listrik:Industri elektronik menggunakan cetakan injeksi untuk memproduksi konektor listrik, selungkup, sakelar, dan komponen lainnya. Proses ini menawarkan akurasi dimensi yang tinggi, penyelesaian permukaan yang sangat baik, dan kemampuan untuk menggabungkan fitur-fitur seperti insert moulding dan overmolding, memungkinkan produksi rakitan elektronik kompleks yang efisien.
- Industri Pengemasan:Berbagai industri, termasuk makanan dan minuman, obat-obatan, dan perawatan pribadi, biasanya menggunakan cetakan injeksi untuk memproduksi wadah, tutup, penutup, dan botol kemasan plastik. Proses ini memungkinkan terciptanya solusi pengemasan yang ringan, tahan lama, dan menarik secara estetika dengan siklus produksi yang efisien.
- Industri Dirgantara:Sektor kedirgantaraan menggunakan cetakan injeksi untuk pembuatan komponen ringan dan berkinerja tinggi seperti saluran udara, braket, panel interior, dan bagian struktural. Proses ini memungkinkan penggunaan material canggih dan geometri bagian yang rumit, berkontribusi pada pengurangan bobot dan peningkatan efisiensi bahan bakar.
Dampak Lingkungan dari Cetakan Injeksi Termoplastik
Cetakan injeksi termoplastik adalah proses pembuatan yang populer karena banyak manfaatnya, tetapi juga penting untuk mempertimbangkan dampak lingkungannya. Berikut adalah beberapa hal yang perlu dipertimbangkan:
- Efisiensi Bahan:Cetakan injeksi termoplastik meningkatkan efisiensi material dengan meminimalkan limbah. Proses ini menggunakan kontrol yang tepat atas jumlah bahan yang disuntikkan ke dalam cetakan, sehingga mengurangi kebutuhan akan bahan berlebih. Pabrikan juga dapat menggunakan teknik penggilingan ulang dan daur ulang untuk menggunakan kembali potongan atau suku cadang yang ditolak, yang selanjutnya mengurangi limbah material.
- Konsumsi energi:Produsen merancang mesin cetak injeksi agar hemat energi, dengan model modern yang menggabungkan teknologi canggih seperti motor servo dan penggerak kecepatan variabel. Fitur-fitur ini mengoptimalkan penggunaan energi dengan mengurangi konsumsi daya selama pencetakan, menghasilkan kebutuhan energi yang lebih rendah dan mengurangi dampak lingkungan.
- Penanganan limbah:Sambil meminimalkan limbah material, pabrikan harus menerapkan praktik pengelolaan limbah yang tepat untuk menangani material sisa, sprues, atau runner. Produsen dapat membuat program daur ulang untuk mengumpulkan dan menggunakan kembali limbah plastik yang dihasilkan selama pencetakan injeksi, sehingga mengurangi limbah yang dikirim ke tempat pembuangan sampah.
- Pengurangan Emisi: Cetakan injeksi termoplastik umumnya menghasilkan emisi lebih rendah daripada proses pembuatan lainnya. Produsen dapat mengurangi emisi dengan menggunakan bahan ramah lingkungan, menerapkan peralatan hemat energi, dan menggunakan sistem pembuangan dan filtrasi canggih untuk menangkap setiap emisi yang dilepaskan.
- Pilihan Material Berkelanjutan:Pemilihan bahan termoplastik dapat berdampak signifikan terhadap kelestarian lingkungan cetakan injeksi. Memilih plastik biodegradable atau berbasis bio, serta bahan daur ulang atau daur ulang, dapat membantu mengurangi jejak ekologi keseluruhan dari proses tersebut.
Pertimbangan Siklus Hidup: Mempertimbangkan seluruh siklus hidup produk cetakan sangat penting untuk menilai dampak lingkungannya. Selama tahap desain dan pemilihan material, pabrikan harus mempertimbangkan faktor-faktor seperti daya tahan suku cadang, kemampuan daur ulangnya, dan potensi pembuangan atau penggunaan kembali di akhir masa pakainya.
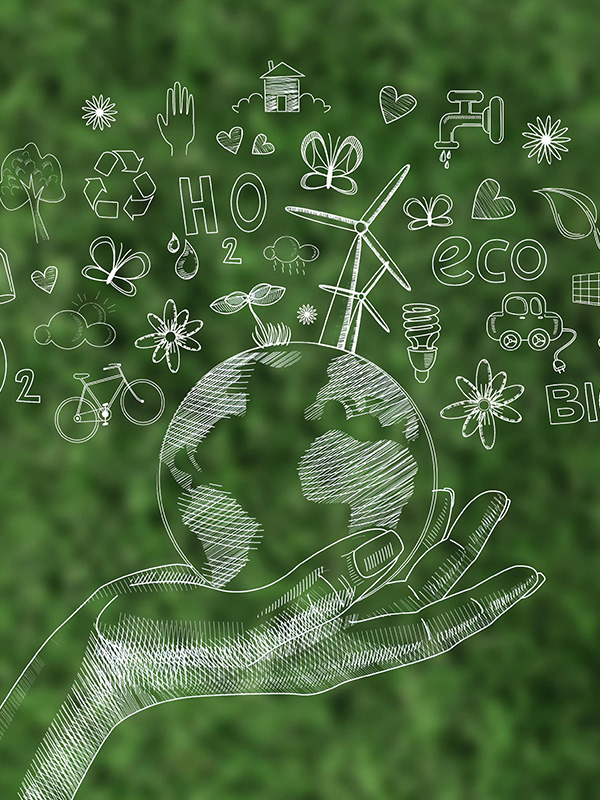
Masa Depan Cetakan Injeksi Termoplastik
Masa depan cetakan injeksi termoplastik terlihat menjanjikan, dengan kemajuan teknologi yang berkelanjutan dan meningkatnya permintaan akan suku cadang presisi berkualitas tinggi di berbagai industri. Beberapa perkembangan utama yang diharapkan di tahun-tahun mendatang meliputi:
- Peningkatan penggunaan otomatisasi dan robotika untuk meningkatkan efisiensi dan mengurangi biaya.
- Upaya difokuskan pada pengembangan material dan proses baru untuk meningkatkan kinerja komponen dan mengaktifkan aplikasi baru.
- Ini adalah adopsi praktik berkelanjutan yang berkembang, seperti menggunakan bahan daur ulang dan mengoptimalkan konsumsi energi, untuk mengurangi dampak lingkungan dari cetakan injeksi.
- Integrasi teknologi digital yang lebih besar, seperti pencetakan 3D dan perangkat lunak simulasi, untuk meningkatkan desain dan proses produksi.
Pasar cetakan injeksi global berkembang, terutama di negara berkembang, didorong oleh meningkatnya permintaan produk plastik di berbagai industri.
Memilih Mitra Pencetakan Injeksi yang Tepat
Memilih mitra pencetakan injeksi yang tepat sangat penting untuk keberhasilan proyek Anda. Luangkan waktu untuk mengevaluasi berbagai opsi, melakukan kunjungan ke lokasi, dan terlibat dalam diskusi menyeluruh untuk memastikan kemitraan yang kompatibel dan tahan lama.
- Keahlian dan Pengalaman:Cari mitra cetakan injeksi dengan pengetahuan dan pengalaman luas di industri ini. Mereka harus memiliki rekam jejak yang terbukti dalam memberikan produk dan solusi berkualitas tinggi kepada klien di berbagai sektor. Pertimbangkan pemahaman mereka tentang berbagai bahan, desain cetakan, dan proses manufaktur.
- Kemampuan Manufaktur: Menilai kemampuan manufaktur mitra cetak injeksi. Pastikan mereka memiliki fasilitas yang lengkap dengan mesin dan teknologi modern untuk menangani kebutuhan proyek Anda. Pertimbangkan kapasitas produksi mereka, kemampuan untuk menangani berbagai ukuran dan kerumitan suku cadang, dan kemampuan untuk memenuhi volume dan jadwal produksi yang Anda inginkan.
- Kualitas Asuransi:Kualitas adalah yang terpenting dalam cetakan injeksi. Mengevaluasi sistem kontrol kualitas dan sertifikasi mitra potensial. Cari mitra yang mengikuti standar kualitas yang ketat, memiliki proses pemeriksaan yang kuat, dan melakukan pengujian komprehensif untuk memastikan kualitas dan konsistensi suku cadang.
- Dukungan Desain dan Rekayasa:Mitra pencetakan injeksi yang andal harus menawarkan dukungan desain dan teknik untuk mengoptimalkan desain suku cadang Anda agar dapat diproduksi. Mereka harus memiliki insinyur terampil yang dapat memberikan masukan berharga tentang pemilihan material, desain cetakan, dan pengoptimalan proses untuk meningkatkan kualitas dan efisiensi suku cadang.
- Daya Saing Biaya:Sementara biaya seharusnya tidak menjadi satu-satunya faktor penentu, penting untuk mengevaluasi harga dan daya saing biaya dari mitra cetakan injeksi. Minta penawaran terperinci dan pertimbangkan biaya perkakas, biaya material, biaya tenaga kerja, dan layanan tambahan apa pun yang mereka sediakan.
- Komunikasi dan Kolaborasi:Komunikasi dan kolaborasi yang efektif sangat penting untuk kemitraan yang sukses. Pastikan mitra cetakan injeksi memiliki saluran komunikasi yang baik, responsif terhadap pertanyaan Anda, dan dapat memberikan pembaruan proyek secara berkala. Pendekatan kolaboratif akan membantu memastikan kami memenuhi kebutuhan Anda dan segera mengatasi setiap tantangan.
- Referensi dan Ulasan Pelanggan:Carilah referensi pelanggan atau baca ulasan/testimoni untuk mendapatkan wawasan tentang pengalaman klien lain dengan mitra cetakan injeksi. Memperoleh informasi ini dapat membantu menentukan ketergantungan, ketepatan waktu, dan tingkat kepuasan pelanggan secara keseluruhan.
Kesimpulan
Cetakan injeksi termoplastik adalah metode serbaguna dan hemat biaya untuk pembuatan komponen plastik dalam jumlah besar. Kemampuannya untuk menghasilkan bentuk kompleks dengan presisi dan konsistensi tinggi telah menjadi pilihan populer untuk berbagai industri, termasuk otomotif, medis, elektronik, dan barang konsumsi. Dengan memahami berbagai aspek cetakan injeksi termoplastik, termasuk kelebihan, kekurangan, dan pertimbangan desainnya, Anda dapat membuat keputusan yang tepat tentang memilih mitra cetakan injeksi yang tepat untuk kebutuhan bisnis Anda.