Dasar-dasar Cetakan Injeksi Plastik
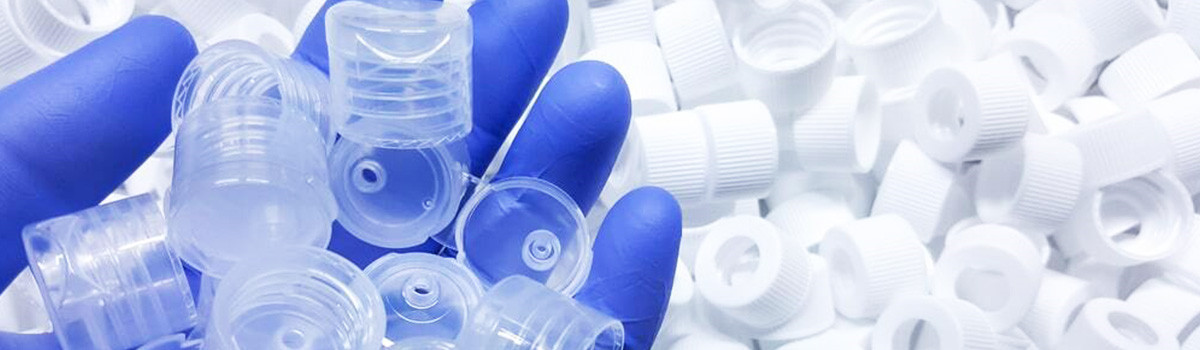
Jelajahi proses pencetakan injeksi dan cara kerjanya.
Cetakan injeksi plastik adalah teknik pembuatan yang populer di mana pelet termoplastik diubah menjadi bagian kompleks dengan volume tinggi. Proses pencetakan injeksi cocok untuk berbagai bahan plastik dan merupakan aspek vital kehidupan modern—casing telepon, rumah elektronik, mainan, dan bahkan suku cadang otomotif tidak akan mungkin tanpanya. Artikel ini akan menguraikan dasar-dasar pencetakan injeksi, menjelaskan cara kerja pencetakan injeksi, dan mengilustrasikan perbedaannya dengan pencetakan 3D.
Apa Dasar-dasar Cetakan Injeksi Plastik?
Dasar-dasar proses pencetakan injeksi plastik termasuk membuat desain produk, membuat cetakan perkakas agar sesuai dengan desain produk, melelehkan pelet resin plastik, dan menggunakan tekanan untuk menyuntikkan pelet yang meleleh ke dalam cetakan.
Lihat rincian setiap langkah di bawah ini:
1. Membuat Desain Produk
Desainer (insinyur, bisnis pembuat cetakan, dll.) membuat bagian (dalam bentuk file CAD atau format lain yang dapat ditransfer), mengikuti pedoman desain dasar khusus untuk proses pencetakan injeksi. Desainer harus mencoba menyertakan fitur berikut dalam desain mereka untuk membantu meningkatkan keberhasilan cetakan injeksi plastik:
* Bos untuk sisipan/pengencang berulir
* Ketebalan dinding konstan atau hampir konstan
* Transisi halus antara ketebalan dinding variabel
* Rongga berongga di bagian tebal
* Tepi membulat
* Konsep sudut pada dinding vertikal
* Tulang rusuk untuk penyangga
*Friction fit, sambungan snap-fit, dan fitur sambungan non-pengikat lainnya
* Engsel hidup
Selain itu, desainer harus meminimalkan fitur berikut untuk mengurangi cacat pada desainnya:
*Ketebalan dinding tidak seragam atau terutama dinding tipis/tebal
* Dinding vertikal tanpa sudut konsep
* Perubahan geometris mendadak (sudut, lubang, dll.)
* Rusuk yang dirancang dengan buruk
* Undercut / overhang
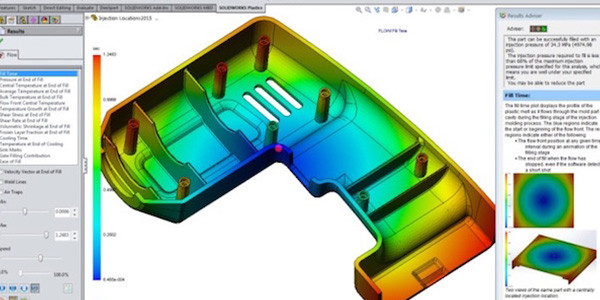
2. Membuat Cetakan Perkakas Sesuai Desain Produk
Teknisi dan pembuat alat yang sangat terampil, menggunakan desain produk, membuat cetakan perkakas untuk mesin cetak injeksi. Cetakan perkakas (juga dikenal sebagai alat sederhana) adalah jantung dan jiwa dari mesin cetak injeksi. Mereka dirancang dengan hati-hati untuk menampung rongga negatif untuk desain produk dan fitur tambahan seperti sprues, runner, gerbang, ventilasi, sistem ejektor, saluran pendingin, dan komponen bergerak. Cetakan perkakas terbuat dari baja dan aluminium kelas tertentu yang dapat menahan puluhan ribu (dan terkadang ratusan ribu) siklus pemanasan dan pendinginan, seperti aluminium 6063, baja P20, baja H13, dan baja tahan karat 420. Proses pembuatan cetakan membutuhkan waktu hingga 20 minggu untuk diselesaikan, termasuk pembuatan dan persetujuan, menjadikan langkah ini sebagai aspek cetakan injeksi yang paling luas. Ini juga merupakan bagian cetakan injeksi yang paling mahal, dan setelah cetakan perkakas dibuat, tidak dapat diubah secara drastis tanpa menimbulkan biaya tambahan.
3. Melelehkan Pelet Resin Plastik
Setelah operator mendapatkan cetakan yang sudah jadi, itu dimasukkan ke dalam mesin cetak injeksi, dan cetakan ditutup, memulai siklus cetak injeksi.
Butiran plastik dimasukkan ke dalam hopper dan ke dalam tong. Sekrup reciprocating ditarik ke belakang, memungkinkan bahan masuk ke ruang antara sekrup dan laras. Sekrup kemudian terjun ke depan, memaksa material ke dalam tong dan lebih dekat ke pita pemanas tempat ia meleleh menjadi plastik cair. Suhu leleh dijaga konstan sesuai spesifikasi material sehingga tidak terjadi degradasi pada laras atau cetakan itu sendiri.
4. Menggunakan Tekanan untuk Menyuntikkan Pelet Leleh Ke Dalam Cetakan
Sekrup bolak-balik memaksa plastik yang meleleh ini melalui nosel, yang terletak di dalam depresi pada cetakan yang dikenal sebagai busing sariawan cetakan. Tekanan pelat yang bergerak cocok dengan cetakan dan nosel dengan erat, memastikan tidak ada plastik yang bisa lepas. Plastik yang meleleh diberi tekanan oleh proses ini, menyebabkannya memasuki semua bagian rongga cetakan dan memindahkan udara rongga keluar melalui lubang cetakan.
Komponen Mesin Cetak Injeksi
Komponen mesin cetak injeksi meliputi hopper, laras, sekrup bolak-balik, pemanas, pelat bergerak, nosel, cetakan, dan rongga cetakan.
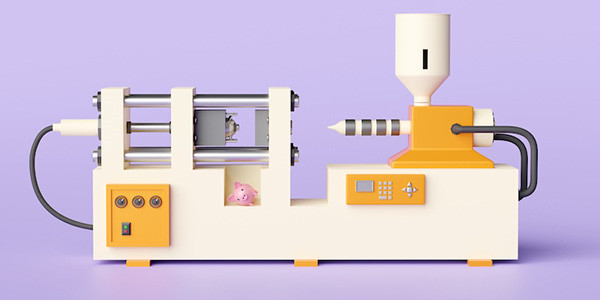
Informasi lebih lanjut tentang masing-masing komponen cetakan injeksi dalam daftar di bawah ini:
* Hopper: lubang tempat butiran plastik dimasukkan ke dalam mesin.
*Barel: rumah luar mesin cetak injeksi, yang berisi sekrup bolak-balik dan butiran plastik. Laras dibungkus dengan beberapa pita pemanas dan diberi ujung dengan nosel yang dipanaskan.
* Sekrup bolak-balik: komponen pembuka botol yang menyampaikan dan memberi tekanan pada bahan plastik saat meleleh melalui laras.
* Pemanas: juga dikenal sebagai pita pemanas, komponen ini memberikan energi panas ke butiran plastik, mengubahnya dari bentuk padat menjadi cair. membentuk.
* Pelat Bergerak: Komponen bergerak yang terhubung ke inti cetakan yang menerapkan tekanan untuk menjaga kedua bagian cetakan kedap udara dan juga melepaskan inti cetakan saat memperlihatkan bagian yang sudah jadi.
*Nozel: komponen yang dipanaskan yang menyediakan saluran keluar standar untuk plastik cair ke dalam rongga cetakan, menjaga suhu dan tekanan sestabil mungkin.
*Cetakan: komponen atau komponen yang berisi rongga cetakan dan fitur pendukung tambahan seperti pin ejector, saluran runner, saluran pendingin, ventilasi, dll. Minimal, cetakan dipisahkan menjadi dua bagian: sisi stasioner (lebih dekat ke laras) dan cetakan inti (pada pelat yang bergerak).
* Rongga cetakan: ruang negatif yang, ketika diisi dengan plastik cair, akan membentuknya menjadi bagian akhir yang diinginkan ditambah penyangga, gerbang, pelari, sprues, dll.
Bagaimana Cara Kerja Cetakan Injeksi?
Setelah plastik mengisi cetakan termasuk sprues, runners, gates, dll., cetakan disimpan pada suhu yang diatur untuk memungkinkan pemadatan material yang seragam ke dalam bentuk bagian. Tekanan penahan dipertahankan saat pendinginan untuk menghentikan aliran balik ke laras dan mengurangi efek penyusutan. Pada titik ini, lebih banyak butiran plastik ditambahkan ke hopper dengan harapan siklus (atau tembakan) berikutnya. Saat didinginkan, pelat terbuka dan memungkinkan bagian yang sudah selesai dikeluarkan, dan sekrup ditarik kembali sekali lagi, memungkinkan material masuk ke laras dan memulai proses dari awal lagi.
Siklus pencetakan injeksi bekerja dengan proses yang berkelanjutan ini — menutup cetakan, memberi makan / memanaskan butiran plastik, menekannya ke dalam cetakan, mendinginkannya menjadi bagian padat, mengeluarkan bagian tersebut, dan menutup cetakan lagi. Sistem ini memungkinkan produksi komponen plastik dengan cepat, dan lebih dari 10,000 komponen plastik dapat dibuat dalam satu hari kerja tergantung pada desain, ukuran, dan bahan.
Djmolding adalah perusahaan cetakan injeksi volume rendah di Cina. Proses pencetakan injeksi plastik kami menghasilkan prototipe khusus dan bagian produksi penggunaan akhir dengan waktu tunggu secepat 1 hari, pemasok bagian cetakan injeksi plastik volume rendah hingga 10000 bagian per tahun