ඉන්දියාවේ නඩුව
DJmolidng's Insert Mould in Injection Molding Service for Indian Companies
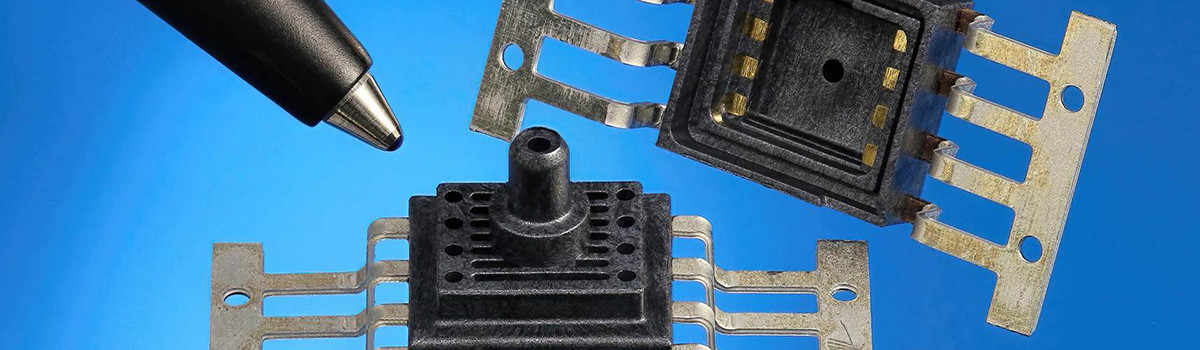
Insert mould යනු සාමාන්යයෙන් එන්නත් අච්චු ගැසීම සඳහා කුහර තුළ සවි කර ඇති ඇට වර්ග, ලෝහ කොටස් හෝ තද ප්ලාස්ටික් කොටස් සාදන අච්චුවකි.
DJmolding ඉන්දියානු වෙළඳපොළ සඳහා insert mlod injection molding සේවාව පිරිනමන අතර, අපි විවිධ කර්මාන්ත සඳහා, විශේෂයෙන්ම ගෘහ උපකරණ නිෂ්පාදකයින් සඳහා ඇතුළු කරන මෝල්ඩින්ගේ ප්ලාස්ටික් කොටස් විශාල ප්රමාණයක් නිෂ්පාදනය කරමු. සමහර ඉන්දියානු ගෘහ උපකරණ නිෂ්පාදකයින් DJmolding ආකාරයෙන් දිගු කාලයක් සඳහා ඇතුල් කිරීමේ අච්චු ප්ලාස්ටික් කොටස් මිලදී ගනී. මෙම ඉන්දියාවේ සමාගම් සමඟ අපට ඉතා හොඳ හවුල්කාරිත්වයක් ඇත.
ඇට වර්ග ඉන්ජෙක්ෂන් මෝල්ඩින් ඇතුල් කරන්න: ගෙඩි ද්රව්ය මල නොබැඳෙන වානේ, තඹ, ලෝකඩ සහ වානේ විය හැකිය, සාමාන්යයෙන් තඹ ගෙඩි බහුලව භාවිතා වේ. තඹ ගැටගැසීමට පහසුය, එය ගෙඩි සහ ප්ලාස්ටික් වඩා හොඳින් බෙදීමට උපකාරී වේ. ගෙඩි අභ්යන්තර සිදුරු වල ඉවසීම 0.02mm තුළ පාලනය කළ යුතු අතර, නොඑසේ නම්, ඉවසීම 0.02mm ට වඩා වැඩි නම් පහසුවෙන් ෆ්ලෑෂ් ඇති කරයි. අච්චුව සවි කිරීමේදී, පරීක්ෂා කිරීම සඳහා ඇට වර්ග ඇතුල් කිරීමේ කටු වලට එකතු කිරීම අවශ්ය වේ. එය ගෙඩි සහ අල්ෙපෙනති අතර තදින් ගැලපේ නම්, එම කොටස විසර්ජනය කිරීම අපහසු වන අතර පිටකිරීමේ සලකුණු හෝ ඇලවීමේ ගැටළු ඇති කරයි. එය ලිහිල්ව ගැලපේ නම්, එය ෆ්ලෑෂ් ඇති කරයි.
ලෝහ කොටස් එන්නත් අච්චු ඇතුල් කරන්න:
ලෝහ කොටස් මල නොබැඳෙන වානේ, ඇලුමිනියම්, තඹ, වානේ ... ආදිය විය හැක. ලෝහ කොටස්වල ඉවසීම මිලිමීටර් 0.02 ක් තුළ පාලනය කළ යුතුය, එසේ නොමැතිනම් ද්රව්ය මුද්රා තැබීම දුෂ්කර වන අතර ෆ්ලෑෂ් තිබීම පහසුය. ලෝහ කොටස් අක්කර විශාල ලෙස නිර්මාණය කළ නොහැක.
ලෝහ කොටස් සඳහා පිරවුම් අක්කරය ඉතා විශාල නම්, ලෝහ කොටස් අතර විශාල උෂ්ණත්ව වෙනසක් ලෙස සම්පූර්ණයෙන්ම එන්නත් කිරීම ඉතා අපහසු වනු ඇත. ලෝහ කොටස්වල පිහිටීම සාමාන්යයෙන් කුහරය තුළ නිර්මාණය කර ඇත්තේ කුහරය චලනය නොවන නිසා වන අතර එමඟින් චලනය වන විට ලෝහ කොටස් ගැලවී යාමෙන් ෆ්ලෑෂ් ප්රතිඵල වළක්වා ගැනීමට උපකාරී වේ (දැඩි අවස්ථාවකදී අච්චුවට හානි විය හැක). විශේෂිත අවස්ථාවන්හිදී, ලෝහ කොටස්වල පිහිටීම නිර්මාණය කළ හැක්කේ නිෂ්පාදනයේ හරය හෝ පැති මතුපිට පමණි.
තද ප්ලාස්ටික් එන්නත් අච්චු ඇතුල් කරන්න:
සාමාන්යයෙන් PEEK, PA66+30GF, PP+30GF, PA12+30GF, PPS....යනාදී ඉහළ ද්රවාංකයක් සහිත තද ප්ලාස්ටික් තෝරන්න. මෙම දෘඩ ප්ලාස්ටික් සඳහා ඉවසීම නිවැරදි විය යුතුය. හැකිලීම, දත් සහ විරූපණය වැනි දෝෂ මුද්රා තැබීමේ ප්රදේශයේ පැවතිය නොහැක. අච්චු සවි කිරීමේදී, දෘඩ ප්ලාස්ටික් පරීක්ෂා කිරීම සඳහා අච්චුව තුළට දැමිය යුතු අතර, වඩා හොඳ මුද්රා තැබීමක් ලබා ගැනීම සඳහා මුද්රා තැබීමේ ප්රදේශය වටා 0.05-0.1mm පෙර තද කළ යුතුය.
දෘඩ ප්ලාස්ටික් කොටස ඉතා විශාල අක්කරයක් නිර්මාණය නොකළ යුතුය, එය උෂ්ණත්ව වෙනස ඇති කරන අතර එන්නත් කිරීමේදී ද්රව්ය පිරවීම අපහසු වේ. සාමාන්යයෙන් දෘඩ ප්ලාස්ටික් කොටස කුහරයේ පැත්තේ සවි කරන්න, මන්ද කුහරය චලනය නොවන නිසා, ෆ්ලෑෂ් හෝ අච්චු චලනය වීමේදී හානි වන අච්චුව වළක්වා ගැනීමට. විශේෂිත අවස්ථාවන්හිදී, ලෝහ කොටස්වල පිහිටීම නිර්මාණය කළ හැක්කේ නිෂ්පාදනයේ හරය හෝ පැති මතුපිට පමණි.
ප්රධාන කරුණු සැලසුම් කරන්න
1. ගෙඩි ඇතුළු කිරීම් සහිත නිෂ්පාදන සඳහා සැලසුම් හැකිලීම, ලෝහ කොටස් සහ තද ප්ලාස්ටික් ඇතුළු කිරීම් සහිත නිෂ්පාදන සඳහා සැලසුම් හැකිලීමක් අවශ්ය නොවේ. දැඩි ඉවසීමක් අවශ්ය ප්රදේශ සඳහා, නිෂ්පාදන ප්රමාණයේ ඉවසීම මධ්යයට වෙනස් කරන්න.
2.සාමාන්යයෙන් අච්චු නිර්මාණයේදී සම්මත පින්-පොයින්ට් ගේට්ටුවක් සහිත අච්චු පදනමක් භාවිතා කරන්න, සහ ද්විතියික එන්නත් කිරීමේදී, ඇතුළු කරන කොටස් හැකිතාක් කුහරයට දමන්න. ඇතුල් කිරීම් කුහරය තුළ සවි කිරීමේ කොන්දේසිය මත, ඉන්ජෙක්ෂන් මෝල්ඩින් කිරීමෙන් පසු හරයේ ඉතිරි කොටස සාදා ගන්නේ කෙසේදැයි සලකා බලන්න, මේ ආකාරයෙන්, කොටසක් පිට කළ හැකිය. සාමාන්යයෙන් කුහරය තුළ ප්රත්යාස්ථ කුට්ටි සහ හරයේ කොටසක් රැඳී සිටීමට නම්යශීලී මැලියම් එකතු කරන්න. ඉලාස්ටික් කුට්ටි සහ මැලියම් අතර දුර ප්රමාණය ඉතා විශාල විය නොහැක, එසේ නොමැති නම් ප්රත්යාස්ථ බලය දෘඪ ප්ලාස්ටික් හෝ ලෝහ කොටස් විරූපණයට හේතු වේ. දුර ප්රමාණය සාමාන්යයෙන් 2mm තුළ නිර්මාණය කර ඇති අතර, ලෝහ හෝ දෘඩ ප්ලාස්ටික් ඇතුළු කිරීම් සාපේක්ෂව විශාල අක්කරයක් ඇති විට ප්රත්යාස්ථ කුට්ටි සහ ප්රත්යාස්ථ මැලියම් ප්රමාණය සුදුසු ලෙස වැඩි කරන්න.
3. ද්රව්යයේ ඝනකම 1.3-1.8mm (මි.මී. 1.5 පමණ හොඳම) ඇතුළත හොඳම වේ, එසේ නොවේ නම්, නිෂ්පාදන ඇඳීම් හරහා පරීක්ෂා කර පාරිභෝගිකයාට එය වෙනස් කිරීමට යෝජනා කළ යුතුය. ද්රව්ය ඝණකම 1.3mm ට වඩා තුනී නම්, ද්රව්ය පිරවීම සඳහා අපහසු වේ, ද්රව්ය ඝණකම 1.8mm ට වඩා ඝන වන අතර, නිෂ්පාදනයේදී හැකිලීම පහසු වේ.
4.Gating අච්චුවේදී ඉතා වැදගත් වේ. ද්වාර ලක්ෂ්යය සඳහා ද්රව්ය පිරවීමේ ශේෂය සම්පූර්ණයෙන් සලකා බැලිය යුතුය. ලෝහ හෝ දෘඩ ප්ලාස්ටික් කොටස් සවි කර ඇති ප්රදේශයට ද්රව්ය දිවෙන විට, ඇතුළු කිරීම් ප්රතිරෝධය සහ උෂ්ණත්ව වෙනස නිසා ද්රව්ය පිරවීමේ වේගය සහ පීඩනය අඩු වේ.
5. අච්චු ejector පද්ධතිය සඳහා, ejecting හි ශේෂය සලකා බැලිය යුතුය, නැතහොත් විරූපණය පිටකිරීමෙන් පසුව සිදුවනු ඇත. කොටස් සමතුලිතව බැහැර කළ නොහැකි නිසා, ව්යුහය සැලසුම් කිරීමේදී සමතුලිත ගැටලුව වැඩිදියුණු කිරීම සඳහා කඩා වැටීම සලකා බැලිය යුතුය.
6.ඉන්ජෙක්ෂන් මෝල්ඩින් වලදී විසර්ජනය කිරීමෙන් පසු කොටස්වල පෙනුමේ සුදුසුකම් සහතික කිරීම සඳහා, ejector උපාංගය ABS හෝ PMMA සහිත තද ප්ලාස්ටික් ගැටිත්තක් විය යුතුය. අච්චුවකට උඩින් ස්ලයිඩ මුද්රා තබා ඇත්නම්, හැකිතාක් කුහරය තුළ ස්ලයිඩ සැලසුම් කරන්න, මන්ද කුහරය තුළ ඇති ස්ලයිඩ අච්චුව සවි කිරීමට පහසුකම් සපයයි.
7. SA (මැහුම් දීමනාව) මුද්රා තැබීමේ ශක්තිය සහතික කිරීම සඳහා, දෙවරක් එන්නත් අච්චු වලින් සාදන ලද නිෂ්පාදනයක් සඳහා, මුද්රා තැබීමේ SA හි පළල අවම වශයෙන් 0.8mm විය යුතුය. ද්විතියික එන්නත් ද්රව්ය දෘඩ ප්ලාස්ටික් සඳහා, මුද්රා තැබීමේ පළල අවම වශයෙන් 1.0mm විය යුතුය, එසේ නොමැතිනම්, නිෂ්පාදනය වෙනස් කිරීමට පාරිභෝගිකයාට යෝජනා කළ යුතුය.
8. අච්චු නිර්මාණයේ දී, අපි නිෂ්පාදනය සඳහා ඉන්ජෙක්ෂන් මෝල්ඩින් යන්ත්ර සැලකිල්ලට ගත යුතු අතර, එය සිරස් හෝ තිරස් කුමන ආකාරයේ යන්ත්රයක් භාවිතා කරන්නේ දැයි බැලීමට. විශේෂයෙන් සීතල ධාවකයන් සහිත පුස් සඳහා ඕනෑවට වඩා කුහර නිර්මාණය නොකරන්නැයි යෝජනා කෙරේ. ඉන්ජෙක්ෂන් මෝල්ඩින් යන්ත්රය ගැලපීම සඳහා, නිෂ්පාදන සැකසීම් සඳහා එය සංයුක්ත සහ සාධාරණද යන්න අප සලකා බැලිය යුතුය. නිෂ්පාදන අච්චුවකට දැමූ සෑම අවස්ථාවකම එකම තත්ත්වයේ පවතින බව සහතික කිරීම සඳහා නිෂ්පාදන සවි කළ යුතුය. තවත් ක්රමයක් නම් අච්චුව වැසීමට පෙර කොටස නිවැරදි ස්ථානයේ නොමැති නම් අනතුරු ඇඟවීමට සැලසුම් ප්රතික්රියා පද්ධතියයි, එය අච්චුව වැසීම නැවැත්වීමට උපකාරී වේ. මේ ආකාරයෙන්, කොටස් අච්චුවෙහි එකම තත්වයක පවතින අතර, ඉන්ජෙක්ෂන් මෝල්ඩින් හි සුදුසුකම් ලත් අනුපාත සහ නිෂ්පාදන කාර්යක්ෂමතාව ඉහළ නංවයි.
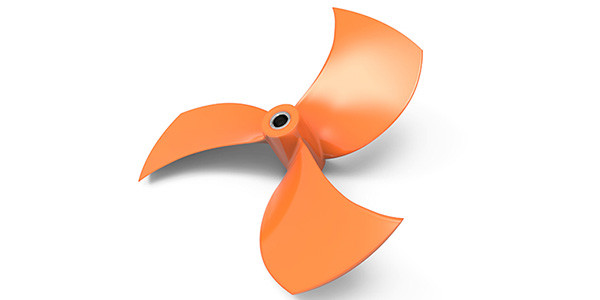
9.ඉන්ජෙක්ෂන් කිරීමේදී අච්චු එන්නත් ප්රදේශය විශාල පීඩනයක් ඇති බැවින් වානේ ආධාරකයක් නිර්මාණය කළ යුතුය (හැඩයේ සහ ප්රමාණයෙන් කොටසට වඩා 5-10 mm විශාල විය යුතුය). අධි වාත්තු ප්රදේශය අවට කොටස් අතර පරතරයක් නොතැබිය යුතුය, එසේ නොමැති නම් ද්විතියික එන්නත් කිරීමෙන් පසු කොටස හැඩයෙන් තොර වනු ඇත. SA (මැහුම් දීමනාව) නොමැති කොටස් සඳහා මෙම අංශය කෙරෙහි වැඩි අවධානයක් යොමු කළ යුතුය.
10.ගුවන් ගමන පහසුයි ගුවන් චාරිකාව එන්නත් අච්චු ගැසීමේදී පහසුවෙන් සිදු වේ, එබැවින් අච්චු සැලසුම් කිරීමේදී වාතාශ්රය කිරීම ගැන සම්පුර්ණයෙන්ම සලකා බැලිය යුතුය. දිගු දුර ජල මාර්ගය සඳහා සියලු අන්ධ කෝණ සහ ස්ථානවලදී, අන්ධ කෝණවල ද්රව්ය පිරවීම වඩා දුෂ්කර බැවින් දෘඩ ප්ලාස්ටික් කොටසෙහි වාතාශ්රය සිදුරු නිර්මාණය කළ යුතුය.
11. එන්නත් කරන ලද ද්රව්ය සහ සුදුසුකම් ලත් තෙරපුම සම්පුර්ණයෙන්ම පුරවා ඇති බව සහතික කිරීම සඳහා, එක් ක්රමයක් නම්, ඇලවුම් ප්රතිඵලය වැඩි දියුණු කිරීම සඳහා කොටසේ කොන් වල යටි කැපීමක් සැලසුම් කිරීම සහ පසුව කොටස් වඩාත් තදින් ඇලවීමයි.
12. මුද්රා තැබීමේ ප්රදේශයේ සහ වෙන් කිරීමේ රේඛා ප්රදේශයේ, අපි කුහරයෙන් සහ හරයෙන් ඉවත් නොකළ යුතුය, මන්ද අච්චුවේ රේඛා කලම්ප සහ කෙටුම්පත් කිරීම අච්චුව සවි කිරීමේදී ෆ්ලෑෂ් ඇති කරයි. LISS-OFF මගින් demould කිරීමට උත්සාහ කරන්න.
ඇතුල් කිරීමේ අච්චුවේ ගේට් පොයින්ට් වර්ග
ඇතුල් කිරීමේ අච්චුව සඳහා ගේට්ටු ලක්ෂ්යය උණුසුම් ස්ප්රූ කපාට ගේට්ටුව, උණුසුම් ස්ප්රූ පින් ගේට්ටුව, පින්-පොයින්ට් ගේට්ටුව, උප ගේට්ටුව, එජ් ගේට් යනාදිය සෘජු කිරීමට සැලසුම් කළ හැකිය.
Hot sprue valve gate: හොඳ ද්රවශීලතාවය, නම්යශීලී, කුඩා ගේට්ටු ලක්ෂ්ය තේරීමේ පිහිටීම. දැවැන්ත නිෂ්පාදනය සඳහා සහ ඝන බිත්ති ඝණකම සහිත නිෂ්පාදන සඳහා ඇඳුම්. ද්රව්ය සුරැකීමට උදව් විය හැක, ගේට්ටුව සඳහා ද්රව්යමය අපද්රව්ය නැත, කෙටි ඊයම් කාලය සහ උසස් තත්ත්වයේ. එකම අඩුපාඩුව වන්නේ කුඩා ගේටින් හෝඩුවාවක් පමණි.
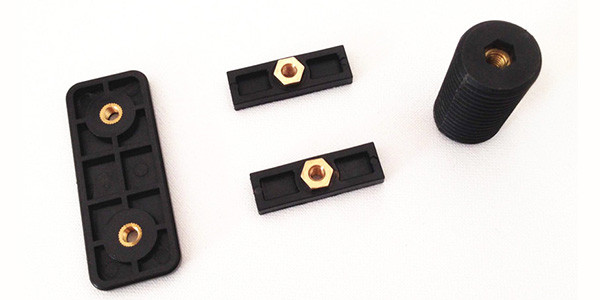
Hot sprue පින් ගේට්ටුව: හොඳ ද්රවශීලතාවය, නම්යශීලී, කුඩා ද්වාර ලක්ෂ්යය තේරීමේ පිහිටීම. දැවැන්ත නිෂ්පාදනය සඳහා සහ ඝන බිත්ති ඝණකම සහිත නිෂ්පාදන සඳහා ඇඳුම්. ද්රව්ය සුරැකීමට උදව් විය හැක, ගේට්ටුව සඳහා ද්රව්යමය අපද්රව්ය නැත, කෙටි ඊයම් කාලය සහ උසස් තත්ත්වයේ. නමුත් ද්වාර ලක්ෂ්යය වටා මිලිමීටර් 0.1 ද්රව්ය ඉතිරිව ඇති අතර, බුරන්නට පහසු වැනි දෝෂ තිබේ. ගේට්ටු ස්ථානය වටා වම් ද්රව්ය ආවරණය කිරීම සඳහා කට්ට සෑදිය යුතුය.
පින්-පොයින්ට් ගේට්ටුව: ස්ථානය තෝරාගැනීම නම්යශීලී, දුර්වල ද්රවශීලතාවය, දිගු ධාවන දුර, කුඩා ගේට්ටු ස්ථානය. කුඩා කණ්ඩායම් නිෂ්පාදනය සඳහා ඇඳුම් කට්ටල. ගේට් පොයින්ට් අවට වැඩිපුර අපද්රව්ය. නිෂ්පාදනයේ ගේට්ටු ලක්ෂ්යය තද කිරීමට යාන්ත්රික ආයුධ අවශ්ය වේ. දිගු ඉදිරි කාලය. දෝෂය 0.1-0.2mm ද්රව්ය ද්වාර ලක්ෂ්යය වටා ඉතිරිව ඇත, ගේට්ටු ලක්ෂ්යය වටා වම් ද්රව්ය ආවරණය කිරීම සඳහා කට්ට සෑදිය යුතුය.
උප දොරටුව: කුහරය, හරය, පැති බිත්ති සහ ejector pins වල ඉළ ඇට මත නිර්මාණය කළ හැකිය. ගේට්ටු ලක්ෂ්යය නම්යශීලීව තෝරා ගත හැක, ගේට්ටුව ස්වයංක්රීයව කොටසකින් වෙන් වේ, සුළු ගේටින් හෝඩුවාවක්. දෝෂ: ගේට්ටු ස්ථානය වටා ද්රව්ය ඇද ගැනීමට පහසුය, ගේට්ටු ස්ථානයේ වියළන ලකුණු ඇති කිරීමට පහසුය, ද්රව්ය අතින් පිස දැමීම අවශ්ය වේ, කුහර වලින් ගේට්ටු ස්ථානයෙන් විශාල පීඩනයක් අලාභය.
දාර ගේට්ටුව: උණු කළ ප්ලාස්ටික් ගේට්ටුව හරහා ගලා යයි, පාර්ශ්වීය ඒකාකාරව පවරනු ලැබේ, ආතතිය අඩු කරයි; වාතය කුහරයට ඇතුළු වීමේ හැකියාව අඩු කරන්න, ඉරි සහ බුබුලු ඇතිවීමෙන් වළකින්න. දෝෂ: ගේට්ටුව වත් කිරීම ස්වයංක්රීයව කොටසෙන් වෙන් විය නොහැක, කොටසේ දාරවල වම් ස්පෘස් සලකුණු, ගේට්ටුව පැතලි ලෙස සැකසීමට මෙවලම් අවශ්ය වේ. එජ් ගේට්ටුව සමානුපාතික එන්නත් කිරීමට සහ පීඩනය රඳවා ගැනීමට උපකාරී වන අතර පීඩනය රඳවා තබා ගැනීමට සහ පෝෂණය කිරීමටද හොඳය, මේ ආකාරයෙන්, එය වායු රේඛා, ප්රවාහ ලකුණු... යනාදිය වැඩිදියුණු කිරීමට වඩා හොඳය.
ඇතුල් කිරීමේ අච්චුව සඳහා සැකසීම සහ සවි කිරීම
1. සැකසීමට පෙර, අච්චු සැකසීමේ තාක්ෂණය සකස් කරන්න. අධි-නිරවද්ය සැකසුම් යන්ත්ර, අධිවේගී යන්ත්රය, සෙමින් පෝෂණය වන NC වයර් කපන යන්ත්රය, දර්පණ EDM (විදුලි විසර්ජන යන්ත්ර යන්ත්ර) යනාදිය තෝරන්න.
2.නිර්මාණය 0.05-0.1mm පෙර පීඩන ස්ථානයේ ඉතිරිව ඇත.
3. අච්චු පදනම සැකසීමේදී නිරවද්ය අවශ්යතා සටහන් කරන්න, අච්චු පදනම ලබා ගැනීමෙන් පසු ඉවසීම පරීක්ෂා කරන්න සහ ඉවසීම නුසුදුසු නම් එය භාවිතා නොකරන්න.
4. අච්චුව සවි කිරීම සඳහා ගෙඩි, ලෝහ කොටස් සහ දෘඩ ප්ලාස්ටික් කොටස් අච්චුව තුළට දමන්න. අච්චුව සවි කිරීමේදී ගැටළු සොයා ගන්නේ නම්, ගෙඩි, ලෝහ කොටස්, දෘඩ ප්ලාස්ටික් කොටස් සහ අච්චු හරහා පරීක්ෂා කර බලන්න. අනාගතයේදී දත්ත සොයා ගැනීමට උපකාර වන, හැකිතාක් දුරට ඇඳීමට අනුව කොටස සකසන්න.
5. අච්චු සවි කිරීම සඳහා ඇඹරුම් යන්තයක් භාවිතා කළ නොහැක. අච්චු සවි කිරීම හොඳ නැති තැන නිවැරදි කිරීම සඳහා යන්ත්ර වෙත හැරෙන්න.
6.අත්හදාවට පෙර ක්රියා පරීක්ෂණය කරන්න, එකලස් කිරීම අතපසු වීම සහ වැරදි එකලස් කිරීම වළක්වා ගන්න. වැරදි එකලස් කිරීම පුස් පදනමට හානි වීමට හේතු වේ.
අච්චු ඇතුල් කිරීම සඳහා අච්චු පරීක්ෂණය
1.පුස් පරීක්ෂාවකදී, අච්චුවක් විවෘත කිරීම, වැසීම සහ පිටකිරීමේ අනුපිළිවෙල පිළිබඳව පැහැදිලිව දැනගත යුතුය. ලෝහ කොටස් සහ දෘඩ ප්ලාස්ටික් කොටස්වල ව්යුහාත්මක ලක්ෂණ සහ ගුණාංග තේරුම් ගන්න.
2.පාරිභෝගිකයාට අවශ්ය සාම්පල ප්රමාණය ගැන පැහැදිලිව දැන ගන්න, අවශ්ය තරම් ඇට වර්ග, ලෝහ කොටස් සහ තද ප්ලාස්ටික් සකස් කරන්න, මන්ද එයට අච්චු පරීක්ෂණයේ දී සාම්පල බොහොමයක් අවශ්ය වේ.
3. ඇට වර්ග, ලෝහ කොටස් හෝ තද ප්ලාස්ටික් ඇතුළු කිරීම් නොමැතිව අච්චුව පරීක්ෂා කළ හැකිද යන්න සැලකිල්ලට ගන්න. ඇට වර්ග, ලෝහ කොටස් සහ තද ප්ලාස්ටික් අච්චුවක එකලස් කර නොමැති නම්, කොටසෙහි අච්චුවකට ඇලවීම හෝ කෙටි වෙඩි තැබීම වැනි දෝෂ තිබිය හැකිය.
4.බොහෝ අවස්ථාවලදී, අච්චුව මත වෝටර්ලයින් තහඩුව සකස් කිරීමට අවශ්ය වේ, නමුත් සමහර විට එයට ඒවායේ ව්යුහය මත පදනම්ව සමහර ඇතුල් කිරීමේ අච්චුවක ජල රේඛා තහඩුව සකස් කළ නොහැක, නැතහොත් ඊටත් වඩා නරක නම්, අච්චුව තදින් ඇලී ඇති අතර වෙනස් කිරීම හෝ අච්චුව හානි වීම අවශ්ය වේ. විවෘත.
5. කෙටි වෙඩි තැබීම්, ගුවන් ගමන්, දැල්වීම්, හෝ අච්චුවට ඇලවීම වැනි අච්චු පරීක්ෂා කිරීමේදී ගැටළු ඇති විය හැක. ඉන්ජෙක්ෂන් මෝල්ඩින් යන්ත්රයක් මත ගැටළු සත්යාපනය කළ හැකි නම්, එය විසඳීමට වඩා හොඳය.
DJmolding හට වසර 10+ කට වැඩි Insert molding පළපුරුද්ද ඇත, ඔබට කිසියම් ප්රශ්නයක් ඇත්නම්, කරුණාකර අප හා සම්බන්ධ වන්න.