ප්ලාස්ටික් එන්නත් අච්චු ගැසීමේ මූලික කරුණු
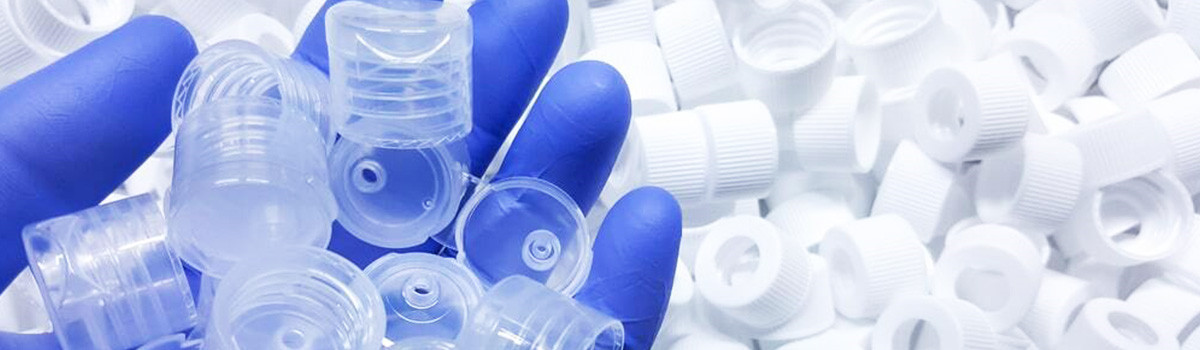
ඉන්ජෙක්ෂන් මෝල්ඩින් ක්රියාවලිය සහ එය ක්රියා කරන ආකාරය ගවේෂණය කරන්න.
ප්ලාස්ටික් ඉන්ජෙක්ෂන් මෝල්ඩින් යනු ජනප්රිය නිෂ්පාදන තාක්ෂණයකි, එහි තාප ප්ලාස්ටික් පෙති සංකීර්ණ කොටස්වල ඉහළ පරිමාවක් බවට පරිවර්තනය වේ. ඉන්ජෙක්ෂන් මෝල්ඩින් ක්රියාවලිය විවිධ ප්ලාස්ටික් ද්රව්ය සඳහා සුදුසු වන අතර නවීන ජීවිතයේ වැදගත් අංගයකි - දුරකථන ආවරණ, ඉලෙක්ට්රොනික නිවාස, සෙල්ලම් බඩු සහ වාහන අමතර කොටස් පවා එය නොමැතිව කළ නොහැක. මෙම ලිපියෙන් එන්නත් අච්චු ගැසීමේ මූලික කරුණු බිඳ දමයි, ඉන්ජෙක්ෂන් මෝල්ඩින් ක්රියා කරන ආකාරය විස්තර කරයි, සහ එය ත්රිමාණ මුද්රණයට වඩා වෙනස් වන්නේ කෙසේද යන්න නිදර්ශනය කරයි.
ප්ලාස්ටික් එන්නත් අච්චු ගැසීමේ මූලික කරුණු මොනවාද?
ප්ලාස්ටික් ඉන්ජෙක්ෂන් මෝල්ඩින් ක්රියාවලියේ මූලික කරුණු වන්නේ නිෂ්පාදන සැලසුම නිර්මාණය කිරීම, නිෂ්පාදන සැලසුමට සරිලන පරිදි මෙවලමක් අච්චුවක් සෑදීම, ප්ලාස්ටික් දුම්මල පෙති උණු කිරීම සහ උණු කළ පෙති අච්චුවට එන්නත් කිරීම සඳහා පීඩනය යෙදීමයි.
පහත එක් එක් පියවරේ බිඳ වැටීම බලන්න:
1. නිෂ්පාදන නිර්මාණය නිර්මාණය කිරීම
නිර්මාණකරුවන් (ඉංජිනේරුවන්, අච්චු සාදන්නා ව්යාපාර, ආදිය) එන්නත් අච්චු ගැසීමේ ක්රියාවලියට විශේෂිත වූ මූලික සැලසුම් මාර්ගෝපදේශ අනුගමනය කරමින් (CAD ගොනුවක් හෝ වෙනත් මාරු කළ හැකි ආකෘතියක් ආකාරයෙන්) කොටසක් නිර්මාණය කරයි. ප්ලාස්ටික් එන්නත් අච්චුවක සාර්ථකත්වය වැඩි කිරීම සඳහා නිර්මාණකරුවන් පහත සඳහන් අංග ඔවුන්ගේ මෝස්තරවලට ඇතුළත් කිරීමට උත්සාහ කළ යුතුය:
* නූල් ඇතුළු කිරීම් / ගාංචු සඳහා ලොක්කන්
*ස්ථාවර හෝ ආසන්න නියත බිත්ති ඝණත්වය
*විචල්ය බිත්ති ඝණත්වය අතර සුමට සංක්රාන්ති
*ඝන කොටස් වල කුහර
* වටකුරු දාර
*සිරස් බිත්ති මත කෙටුම්පත් කෝණ
* ආධාරක සඳහා ඉළ ඇට
*ඝර්ෂණ ගැලපීම්, ස්නැප්-ෆිට් සන්ධි, සහ වෙනත් නොවන ගාංචු සම්බන්ධ කිරීමේ විශේෂාංග
*සජීවී සරනේරු
මීට අමතරව, නිර්මාණකරුවන් ඔවුන්ගේ නිර්මාණවල අඩුපාඩු අවම කිරීම සඳහා පහත සඳහන් අංගයන් අවම කළ යුතුය:
*ඒකාකාරී නොවන බිත්ති ඝණත්වය හෝ විශේෂයෙන් සිහින්/ඝන බිත්ති
* කෙටුම්පත් කෝණ නොමැති සිරස් බිත්ති
* හදිසි ජ්යාමිතික වෙනස්කම් (කොනර්, සිදුරු, ආදිය)
* දුර්වල ලෙස නිර්මාණය කර ඇති රිබින්
*යටි කැපීම් / උඩින් එල්ලීම
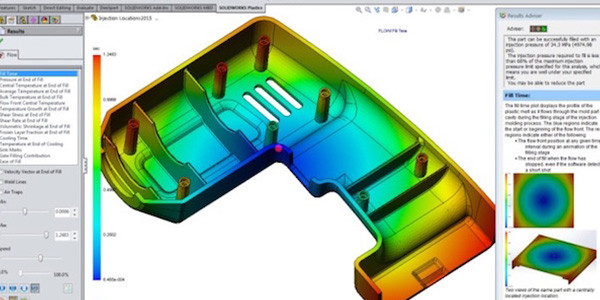
2. නිෂ්පාදන සැලසුමට ගැලපෙන පරිදි මෙවලම් අච්චුවක් සෑදීම
ඉහළ දක්ෂතා ඇති යන්ත්රෝපකරණ සහ මෙවලම් නිෂ්පාදකයින්, නිෂ්පාදන සැලසුම භාවිතා කරමින්, එන්නත් අච්චු යන්ත්රය සඳහා මෙවලම් අච්චුවක් නිපදවයි. මෙවලම් අච්චුව (සරලව මෙවලමක් ලෙසද හැඳින්වේ) යනු එන්නත් අච්චු යන්ත්රයේ හදවත සහ ආත්මයයි. ඒවා ප්රවේශමෙන් නිර්මාණය කර ඇත්තේ නිෂ්පාදන සැලසුම සඳහා සෘණ කුහරය සහ ස්පෘස්, ධාවකයන්, ගේට්ටු, වාතාශ්රය, ඉෙජක්ටර් පද්ධති, සිසිලන නාලිකා සහ චලනය වන සංරචක වැනි අමතර විශේෂාංග අඩංගු වන ලෙසයි. මෙවලම් අච්චු සෑදී ඇත්තේ 6063 ඇලුමිනියම්, P20 වානේ, H13 වානේ සහ 420 මල නොබැඳෙන වානේ වැනි තාපන සහ සිසිලන චක්ර දස දහස් ගණනකට (සහ සමහර විට සිය දහස් ගණනකට) ඔරොත්තු දිය හැකි වානේ සහ ඇලුමිනියම්වල නිශ්චිත ශ්රේණිවලින් ය. අච්චු සැකසීමේ ක්රියාවලිය සම්පූර්ණ කිරීමට සති 20කට වැඩි කාලයක් ගත වන අතර, සැකසීම සහ අනුමැතිය යන දෙකම ඇතුළුව, මෙම පියවර එන්නත් අච්චු ගැසීමේ වඩාත් පුළුල් අංගය බවට පත් කරයි. එය එන්නත් අච්චු ගැසීමේ මිල අධිකම කොටස වන අතර, මෙවලම් අච්චුවක් නිපදවූ පසු, අමතර වියදම් දැරීමෙන් තොරව එය දැඩි ලෙස වෙනස් කළ නොහැක.
3. ප්ලාස්ටික් ෙරසින් පෙති උණු කිරීම
ක්රියාකරුවන් විසින් නිමි අච්චුව ලබා ගැනීමෙන් පසුව, එය ඉන්ජෙක්ෂන් මෝල්ඩින් යන්ත්රයට ඇතුල් කරනු ලබන අතර, අච්චුව වසා, එන්නත් අච්චු චක්රය ආරම්භ කරයි.
ප්ලාස්ටික් කැටිති ආප්ප සහ බැරලය තුළට පෝෂණය වේ. ප්රතිවිකුණුම් ඉස්කුරුප්පු ඇණ ආපසු ඇද ගන්නා අතර, ඉස්කුරුප්පු ඇණ සහ බැරලය අතර අවකාශයට ද්රව්ය ලිස්සා යාමට ඉඩ සලසයි. එවිට ඉස්කුරුප්පු ඇණ ඉදිරියට ඇද, ද්රව්යය බැරලයට බල කර එය උණු කළ ප්ලාස්ටික් බවට දියවන තාපක පටිවලට සමීප වේ. ද්රව්ය පිරිවිතරයන්ට අනුව ද්රවාංක උෂ්ණත්වය නියතව තබා ඇති අතර එමඟින් බැරලයේ හෝ අච්චුවේම කිසිදු පිරිහීමක් සිදු නොවේ.
4. උණු කළ පෙති අච්චුවට එන්නත් කිරීම සඳහා පීඩනය භාවිතා කිරීම
පුස් ස්පෘ බුෂිං ලෙස හඳුන්වන අච්චුවේ අවපාතයක් තුළ හිඳ ඇති තුණ්ඩය හරහා ප්රතිචක්රීකරණ ඉස්කුරුප්පු ඇණ මෙම උණු කළ ප්ලාස්ටික් බල කරයි. චලනය වන තහඩු පීඩනය අච්චුව සහ තුණ්ඩය එකට තදින් ගැලපේ, කිසිදු ප්ලාස්ටික් ගැලවිය නොහැකි බව සහතික කරයි. මෙම ක්රියාවලිය මගින් උණු කරන ලද ප්ලාස්ටික් පීඩනයට ලක් වන අතර, එය අච්චු කුහරයේ සියලුම කොටස් වලට ඇතුල් වන අතර පුස් වාතාශ්රය හරහා කුහරයේ වාතය පිටතට විස්ථාපනය කරයි.
ඉන්ජෙක්ෂන් මෝල්ඩින් මැෂින් සංරචක
ඉන්ජෙක්ෂන් මෝල්ඩින් යන්ත්රයක සංරචක වන්නේ ආප්ප, බැරලයක්, ප්රත්යාවර්තක ඉස්කුරුප්පුවක්, හීටරයක් (ය), චංචල තහඩුවක්, තුණ්ඩයක්, අච්චුවක් සහ අච්චු කුහරයක් ය.
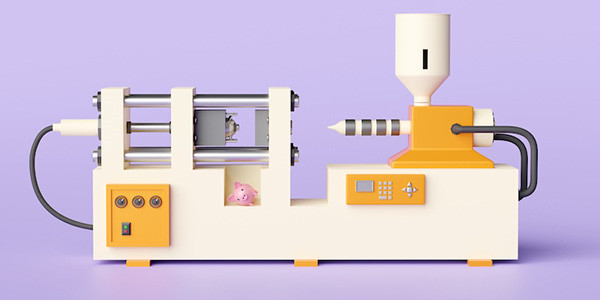
පහත ලැයිස්තුවේ එක් එක් එන්නත් අච්චු සංරචක පිළිබඳ වැඩි විස්තර:
*ආප්ප: ප්ලාස්ටික් කැටිති යන්ත්රයට ඇතුල් කරන විවරය.
*බැරල්: ප්රතිවිකුණුම් ඉස්කුරුප්පු ඇණ සහ ප්ලාස්ටික් කැටිති අඩංගු ඉන්ජෙක්ෂන් මෝල්ඩින් යන්ත්රයේ පිටත නිවාසය. බැරලය තාපක පටි කිහිපයකින් ඔතා ඇති අතර රත් වූ තුණ්ඩයක් සමඟ ඉඟි කර ඇත.
*ප්රතිවිකුණුම් ඉස්කුරුප්පු: ප්ලාස්ටික් ද්රව්ය බැරලය හරහා දියවන විට එය සම්ප්රේෂණය කරන සහ පීඩනය කරන කිරළ ඉස්කුරුප්පු සංරචකය.
*හීටර්: තාපන පටි ලෙසද හැඳින්වෙන, මෙම සංරචක ප්ලාස්ටික් කැටිති වලට තාප ශක්තිය ලබා දෙයි, ඒවා ඝන ස්වරූපයෙන් ද්රවයක් බවට පත් කරයි. ආකෘතිය.
*චංචල තහඩුව: අච්චු හරයට සම්බන්ධ චලනය වන සංරචකය අච්චු දෙකේම වාතය රහිතව තබා ගැනීමට පීඩනය යොදන අතර නිමි කොටස හෙළි කරන විට අච්චු හරය මුදා හරියි.
*තුණ්ඩය: උෂ්ණත්වය සහ පීඩනය හැකිතාක් ස්ථායීව තබා ගනිමින්, අච්චු කුහරය තුළට උණු කළ ප්ලාස්ටික් සඳහා සම්මත පිටවීමක් සපයන රත් වූ සංරචකය.
* අච්චුව: අච්චු කුහරය අඩංගු සංරචක හෝ සංරචක සහ ඉෙජක්ටර් අල්ෙපෙනති, ධාවන නාලිකා, සිසිලන නාලිකා, වාතාශ්රය වැනි අමතර ආධාරක ලක්ෂණ. අවම වශයෙන්, අච්චු කොටස් දෙකකට වෙන් කරනු ලැබේ: ස්ථාවර පැත්ත (බැරලයට ආසන්නව) සහ අච්චුව හරය (චලනය වන තහඩුව මත).
පුස් කුහරය: ඍණාත්මක අවකාශය, උණු කළ ප්ලාස්ටික් වලින් පුරවා ඇති විට, එය අපේක්ෂිත අවසාන කොටස සහ ආධාරක, ගේට්ටු, ධාවකයන්, ස්පෘස් යනාදිය ලෙස හැඩගස්වනු ඇත.
එන්නත් අච්චුව වැඩ කරන්නේ කෙසේද?
ප්ලාස්ටික් එහි ස්පෘස්, ධාවකයන්, ගේට්ටු ආදිය ඇතුළුව අච්චුව පුරවා ගත් පසු, අච්චුව කොටස් හැඩයට ද්රව්යයේ ඒකාකාර ඝණීකරනය කිරීමට ඉඩ සලසන උෂ්ණත්වයක තබා ඇත. බැරලයට ආපසු ගලායාම නැවැත්වීමට සහ හැකිලීමේ බලපෑම් අඩු කිරීමට සිසිලන අතරතුර රඳවා ගැනීමේ පීඩනයක් පවත්වා ගනී. මෙම අවස්ථාවේදී, ඊළඟ චක්රය (හෝ වෙඩි තැබීම) අපේක්ෂාවෙන් ආප්පයට තවත් ප්ලාස්ටික් කැටිති එකතු කරනු ලැබේ. සිසිලන විට, තහඩුව විවෘත වන අතර නිමි කොටස ඉවත් කිරීමට ඉඩ සලසයි, සහ ඉස්කුරුප්පු ඇණ නැවත වරක් ආපසු ඇද ගන්නා අතර, ද්රව්යය බැරලයට ඇතුළු වී නැවත ක්රියාවලිය ආරම්භ කිරීමට ඉඩ සලසයි.
ඉන්ජෙක්ෂන් මෝල්ඩින් චක්රය ක්රියා කරන්නේ මෙම අඛණ්ඩ ක්රියාවලියෙනි - අච්චුව වැසීම, ප්ලාස්ටික් කැටිති පෝෂණය කිරීම/උණුසුම් කිරීම, අච්චුවට පීඩනය යෙදීම, ඝන කොටසකට සිසිල් කිරීම, කොටස පිට කිරීම සහ අච්චුව නැවත වැසීම. මෙම ක්රමය මඟින් ප්ලාස්ටික් කොටස් වේගයෙන් නිෂ්පාදනය කිරීමට ඉඩ සලසයි, සැලසුම, ප්රමාණය සහ ද්රව්ය අනුව වැඩ කරන දිනකදී ප්ලාස්ටික් කොටස් 10,000කට වැඩි ප්රමාණයක් සෑදිය හැක.
Djmolding යනු චීනයේ අඩු ප්රමාණයේ එන්නත් මෝල්ඩින් සමාගම් වේ.අපගේ ප්ලාස්ටික් ඉන්ජෙක්ෂන් මෝල්ඩින් ක්රියාවලිය මඟින් අභිරුචි මූලාකෘති සහ අවසාන භාවිත නිෂ්පාදන කොටස් දින 1ක් තරම් වේගයෙන් නිෂ්පාදනය කරයි, අඩු පරිමාවකින් යුත් ප්ලාස්ටික් එන්නත් අච්චු කොටස් සැපයුම්කරු වසරකට කොටස් 10000 දක්වා