ප්ලාස්ටික් ඉන්ජෙක්ෂන් මෝල්ඩින් ප්රධාන සලකා බැලීම්
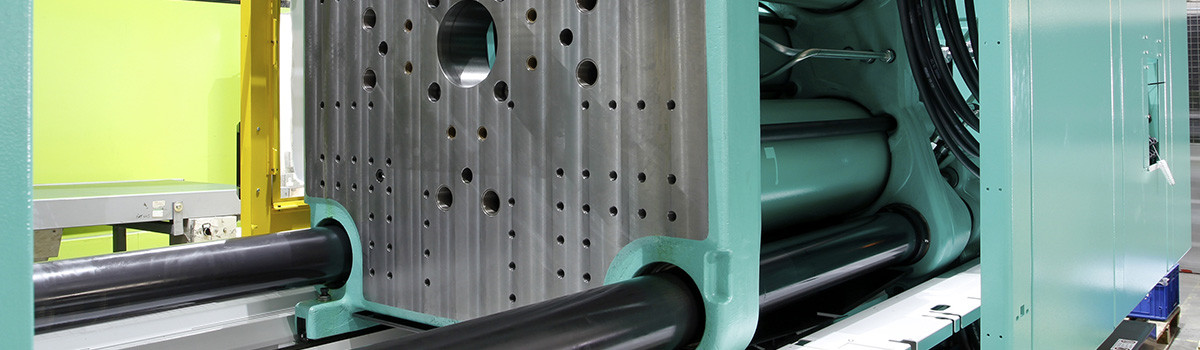
ඕනෑම සාර්ථක ඉන්ජෙක්ෂන් මෝල්ඩින් ව්යාපෘතියක් එකවර සාධක කිහිපයක් සැලකිල්ලට ගත යුතුය.
ද්රව්ය තෝරා ගැනීම
ඉන්ජෙක්ෂන් මෝල්ඩින් කිරීමේදී ද්රව්ය සැලකිය යුතු කාර්යභාරයක් ඉටු කරයි. දක්ෂ ඉන්ජෙක්ෂන් මෝල්ඩින් සපයන්නෙකුට ඔබේ අයවැය සහ කාර්ය සාධන අවශ්යතාවලට ගැලපෙන තාප ප්ලාස්ටික් තෝරා ගැනීමට ඔබට උපකාර කළ හැක. මෝල්ඩර් බොහෝ විට ඔවුන් මිලදී ගන්නා තාප ප්ලාස්ටික් ශ්රේණිවල විශාල ප්රමාණයන් සඳහා වට්ටම් ලබා ගන්නා බැවින්, ඔවුන්ට එම ඉතුරුම් ඔබට ලබා දිය හැකිය.
ඉවසීමේ වෙනස්කම්
ඉන්ජෙක්ෂන් මෝල්ඩින් හරහා සාදන ලද සෑම නිෂ්පාදනයක්ම ඔවුන්ගේ අපේක්ෂිත යෙදුමට ගැලපෙන පරිදි නිශ්චිත ඉවසීමක් තිබිය යුතුය. ඇතැම් ද්රව්ය අච්චු කිරීමට හෝ අවශ්ය ඉවසීම්වලට ඔරොත්තු දීමට අපහසු විය හැකි අතර, මෙවලම්වල සැලසුම අවසාන කොටසේ ඉවසීමට ද බලපෑ හැකිය. නිශ්චිත නිෂ්පාදන සඳහා පිළිගැනීමේ ඉවසීමේ පරාසය සැමවිටම ඔබේ එන්නත් අච්චුව සමඟ සාකච්ඡා කරන්න.
බැරල් සහ තුණ්ඩ උෂ්ණත්වය
අච්චුව පුරා දුම්මල ගලා යාමේ හැකියාව කෙරෙහි බලපාන බැවින් මෝල්ඩර් එන්නත් අච්චු ගැසීමේදී නිශ්චිත බැරල් සහ තුණ්ඩ උෂ්ණත්වය පවත්වා ගත යුතුය. බැරල් සහ තුණ්ඩ උෂ්ණත්වය තාප-වියෝජනය සහ ද්රවාංක උෂ්ණත්වය අතර නිශ්චිතව සැකසිය යුතුය. එසේ නොමැති නම්, එය පිටාර ගැලීම, ෆ්ලෑෂ්, මන්දගාමී ප්රවාහය හෝ පුරවා නැති කොටස් ඇති විය හැක.
තාප ප්ලාස්ටික් ප්රවාහ අනුපාත
රත් වූ ප්ලාස්ටික් 95% සිට 99% දක්වා පිරෙන තෙක් අච්චුවේ කුහරය තුළට හැකි ඉක්මනින් එන්නත් කිරීම සහතික කිරීම සඳහා අච්චුකරුවන් ප්රශස්ත ප්රවාහ අනුපාතයක් පවත්වා ගත යුතුය. නිසි ප්රවාහ අනුපාතයක් තිබීම ප්ලාස්ටික් කුහරය තුළට ගලා යාම සඳහා නිවැරදි දුස්ස්රාවීතා මට්ටම රඳවා තබා ගැනීම සහතික කරයි.
ඕනෑම එන්නත් අච්චු මෙහෙයුමකදී සලකා බැලිය යුතු වෙනත් සාධක නම්:
*ගේට්ටුව පිහිටීම
*සින්ක් ලකුණු
* වසා දැමීමේ කෝණ
* වයනය
*කෙටුම්පත් සහ කෙටුම්පත් කෝණ දිශානතිය
*වානේ ආරක්ෂිත ප්රදේශ
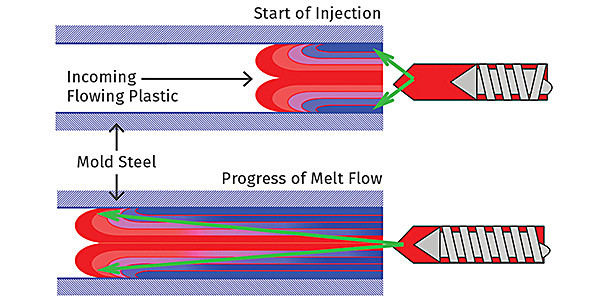
ඉන්ජෙක්ෂන් මෝල්ඩින් ක්රියාවලියේ ප්රධාන පියවර හයක්
ඉන්ජෙක්ෂන් මෝල්ඩින් ක්රියාවලියට ප්රධාන පියවර හයක් ඇතුළත් වන අතර, නිසියාකාරව සිදු නොකළහොත් මෙම ඕනෑම අදියරකදී ගැටලු මතුවිය හැකිය.
1. කලම්ප කිරීම
මෙම ක්රියාවලියේදී, අච්චුවේ කොටස් දෙක කලම්ප ඒකකයක් භාවිතයෙන් තදින් ආරක්ෂා කර ඇති අතර, අච්චුව වැසීමට ප්රමාණවත් බලයක් යෙදවීමට හයිඩ්රොලික් බලය භාවිතා කරයි. ප්රමාණවත් තද කිරීමේ බලයක් නොමැතිව, ක්රියාවලිය අසමාන බිත්ති කොටස්, නොගැලපෙන බර සහ විවිධ ප්රමාණවලට හේතු විය හැක. අධික කලම්ප බලය නිසා කෙටි වෙඩි තැබීම්, පිළිස්සුම් සහ ග්ලෝස් මට්ටමේ වෙනස්කම් ඇති විය හැක.
2.එන්නත් කිරීම
අච්චුකරුවන් විසින් උණුකරන ලද තාප ප්ලාස්ටික් ද්රව්ය ඉහළ පීඩනයක් යටතේ රැම්මිං උපාංගයක් හෝ ඉස්කුරුප්පුවක් සමඟ අච්චුවට එන්නත් කරයි. ඉන්පසුව, කොටස ඒකාකාර අනුපාතයකින් සිසිල් කිරීමට ඉඩ දිය යුතුය. එසේ නොමැති නම්, අවසාන කොටස එහි සෞන්දර්යය බලපාන ප්රවාහ රේඛා හෝ අනවශ්ය රටා තිබිය හැක.
3.නිවාස පීඩනය
තාප ප්ලාස්ටික් ද්රව්ය අච්චුවට එන්නත් කළ පසු, කුහර සම්පූර්ණයෙන්ම පිරවීම සඳහා අච්චුකරුවන් වැඩි පීඩනයක් යොදවයි. ඔවුන් සාමාන්යයෙන් අච්චුවේ ගේට්ටුව කැටි වන තුරු උණු කළ තාප ප්ලාස්ටික් ද්රව්ය රඳවා තබා ගනී. වාසස්ථාන කාලය නිවැරදි පීඩනය යෙදිය යුතුය - ඉතා අඩු වන අතර එය නිමි භාණ්ඩය මත සින්ක් සලකුණු තැබිය හැක. අධික පීඩනය නිසා බර්ර්ස්, විශාල මානයන් හෝ අච්චුවෙන් කොටස මුදා හැරීමේ ගැටළු ඇති විය හැක.
4. සිසිලනය
වාසස්ථානයෙන් පසු, අච්චුව පිරී ඇත, නමුත් එය අච්චුවෙන් ඉවත් කිරීමට තවමත් උණුසුම් විය හැකිය. එමනිසා, අච්චු ප්ලාස්ටික් වලින් තාපය අවශෝෂණය කිරීම සඳහා අච්චුව සඳහා නිශ්චිත කාලයක් වෙන් කරයි. අච්චුකරුවන් තාප ප්ලාස්ටික් ද්රව්යයේ ප්රමාණවත්, ඒකාකාර සිසිලනය පවත්වා ගත යුතුය, නැතහොත් අවසාන නිෂ්පාදනයේ විකෘති වීමේ අවදානමක් ඇත.
5. අච්චු විවෘත කිරීම
අච්චු එන්නත් යන්ත්රයේ චංචල තහඩු විවෘත වේ. සමහර අච්චු වල වායු පිපිරුම් පාලනය හෝ හරය ඇද ඇති අතර, අච්චු යන්ත්රය කොටස ආරක්ෂා කරමින් අච්චුව විවෘත කිරීමට භාවිතා කරන බලයේ මට්ටම පාලනය කරයි.
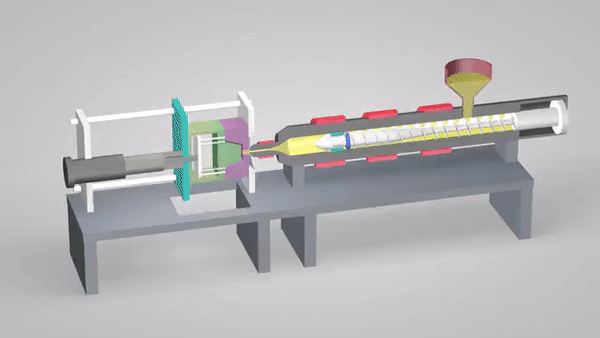
6.කොටස ඉවත් කිරීම
අවසන් නිශ්පාදනය පිටකිරීමේ පද්ධතියෙන්, දඬුවලින් හෝ රොබෝ තාක්ෂණයෙන් ස්පන්දනය සමඟ එන්නත් අච්චුවෙන් පිට කරනු ලැබේ. පුස් මතුපිට නැනෝ මුදා හැරීමේ ආලේපන පිටකිරීමේදී ඉරීම හෝ ඉරීම වැළැක්වීමට උපකාරී වේ.
ක්රියාවලි ගැටළු නිසා ඇති වන සාමාන්ය අච්චු දෝෂ
එන්නත් අච්චු ගැසීම හා සම්බන්ධ වාත්තු දෝෂ කිහිපයක් තිබේ, එනම්:
විකෘති කිරීම: විකෘති කිරීම යනු කොටස අසමාන හැකිලීමක් අත්විඳින විට සිදුවන විරූපණයකි. එය අනපේක්ෂිත නැමුණු හෝ ඇඹරුණු හැඩයන් ලෙස ඉදිරිපත් කරයි.
පැනීම: තාප ප්ලාස්ටික් ඉතා සෙමින් එන්නත් කර කුහරය පිරී යාමට පෙර සැකසීමට පටන් ගනී නම්, එය අවසන් නිෂ්පාදනයේ ජෙට් වීමට හේතු විය හැක. Jetting කොටසෙහි මතුපිට රැලි සහිත ජෙට් ධාරාවක් මෙන් පෙනේ.
සින්ක් ලකුණු: මේවා අසමාන සිසිලනය සමඟ ඇති වන පෘෂ්ඨීය අවපාතයන් වන අතර හෝ අච්චු මගින් කොටස සිසිල් වීමට ප්රමාණවත් කාලයක් ලබා නොදෙන විට ද්රව්ය ඇතුළට හැකිලීමට හේතු වේ.
වෑල්ඩින් රේඛා: මේවා සාමාන්යයෙන් සිදුරු සහිත කොටස් වටා ඇති තුනී රේඛා වේ. උණු කළ ප්ලාස්ටික් සිදුර වටා ගලා යන විට, එම ප්රවාහ දෙක හමු වේ, නමුත් උෂ්ණත්වය නිවැරදි නොවේ නම්, ප්රවාහයන් නිසි ලෙස බන්ධනය නොවේ. ප්රතිඵලය වන්නේ වෑල්ඩින් රේඛාවක් වන අතර, අවසාන කොටසෙහි කල්පැවැත්ම සහ ශක්තිය අඩු කරයි.
ඉවත් කිරීමේ ලකුණු: කොටස ඉතා ඉක්මනින් හෝ අතිරික්ත බලයක් සහිතව විසර්ජනය කරන්නේ නම්, ඉෙජක්ටර් දඬු අවසාන නිෂ්පාදනයේ සලකුණු තැබිය හැකිය.
රික්ත හිස්: කොටසෙහි මතුපිටට පහළින් වායු සාක්කු සිරවී ඇති විට රික්ත හිස් ඇතිවේ. කොටසෙහි අභ්යන්තර සහ පිටත කොටස් අතර අසමාන ඝණීකරනය හේතුවෙන් ඒවා සිදු වේ.
DJmolding වෙතින් එන්නත් මෝල්ඩින් සේවා
DJmolding, ඉහළ පරිමාවක්, අභිරුචි ඉන්ජෙක්ෂන් මෝල්ඩින් විශේෂඥයා, වසර 13 ක ඉන්ජෙක්ෂන් මෝල්ඩින් පළපුරුද්ද ඇත. DJmolding ස්ථාපිත කළ දා සිට, අපි අපගේ පාරිභෝගිකයින්ට ලබා ගත හැකි ඉහළම තත්ත්වයේ ඉන්ජෙක්ෂන් මෝල්ඩ් කොටස් ලබා දීමට කැපවී සිටිමු. අද, අපගේ දෝෂ අනුපාතය මිලියනයකට 1 කොටසකට වඩා අඩුය.