අධි පරිමා එන්නත් අච්චු ගැසීම
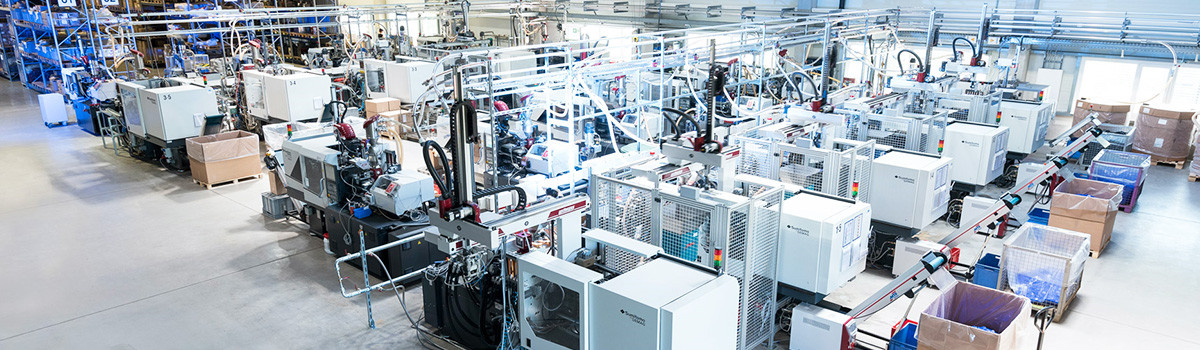
අධි පරිමා එන්නත් මෝල්ඩින් (ඉහළ පරිමාව නිෂ්පාදනය): ප්ලාස්ටික් එන්නත් අච්චුව
දහස් ගණනකට අධික ප්ලාස්ටික් ඉන්ජෙක්ෂන් මෝල්ඩින් සහ ප්ලාස්ටික් නිෂ්පාදන පහසුකම් සියල්ලෙන් තෝරා ගැනීමට ඇති අතර, අච්චු සමාගමක් කැපී පෙනෙන ඉහළම ගුණාංගවලින් එකක් මොනවාද? සැපයුම්කරුවෙකු තෝරාගැනීමේදී, බොහෝ සාධක සැලකිල්ලට ගත යුතුය; හැකියාවන්, තත්ත්ව සහතිකය, සමාගමේ කීර්තිය, පිරිවැය සහ බෙදා හැරීමේ කාලය ඇතුළුව. ඔබේ අවශ්යතාවලට සරිලන නිවැරදි ප්ලාස්ටික් එන්නත් අච්චුව සොයා ගැනීම කාලය ගතවන බවක් පෙනෙන්නට තිබුණත් ඔබේ අඩු සහ ඉහළ පරිමාවේ අවශ්යතා පළමුව තීරණය කිරීම සහ කාලයත් සමඟ ඒවා වෙනස් විය හැකි ආකාරය තීරණය කිරීම ඔබේ විකල්පයන් පටු කිරීමට උපකාරී වේ.
DJmolding's High-Volume Injection මෝල්ඩින් සේවාව
DJmolding හි, අපගේ නිෂ්පාදන පහසුකම යන්ත්ර කිහිපයක් සහ දක්ෂ ක්රියාකරුවන් සමඟ ඉහළ මට්ටමේ, කාර්යක්ෂම මෙහෙයුමකි. අපගේ විවිධ උපකරණ නිසා, ඒවායේ කර්මාන්ත, ප්ලාස්ටික් ගුණාත්මකභාවය සහ නිෂ්පාදනය කරන ලද කෑලි ගණන විශාල වශයෙන් පරාසයක විහිදෙන විවිධාකාර රැකියා අපට හැසිරවිය හැකිය. අඩු සහ ඉහළ පරිමාවන්, නිර්මාණයේ සිට නිෂ්පාදනය දක්වා, අපගේ පාරිභෝගිකයින්ට පිරිවැය, ගුණාත්මකභාවය සහ ඉදිරි කාලය තුළ තරඟකාරී වාසි ලබා දෙන ගෘහස්ථව සම්පූර්ණ කළ හැකිය.
DJmolding's injection molding යනු අධි පරිමා නිෂ්පාදන ක්රියාවලීන් ඔප්පු කරන ලද තාක්ෂණයකි. මෙය මසකට කෑලි මිලියන ගණනක් දක්වා පරිමාවකින් සම්පූර්ණ නිෂ්පාදන-ගුණාත්මක කොටස් ලබා දෙන විශේෂිත සේවාවකි. අධි-පරිමාණ ප්ලාස්ටික් ඉන්ජෙක්ෂන් මෝල්ඩින් ඉහළ ඉවසීමේ නිරවද්යතාවය, අඩු සීරීම් අලාභය සහ පිරිවැය ඉතිරිකිරීම් සඳහා ඉඩ සලසයි.
අපගේ ඉහළ පරිමා වාත්තු උපකරණ බොහොමයක් පරිගණකගත කර ඇති අතර කාර්යක්ෂමතාව වැඩි කිරීමට සහ ගුණාත්මකභාවය ආරක්ෂා කිරීමට යාන්ත්රික පද්ධති භාවිතා කරයි. සියලුම ඉහළ-පරිමා නිෂ්පාදන සඳහා තත්ත්ව පාලනය ඇතුළත් කර ඇති බව අපි සහතික කරන්නේ කෙසේදැයි බැලීමට අපගේ "තත්ත්ව පාලන පද්ධතිය" නැරඹීමට වග බලා ගන්න. මෙම වර්ගයේ නිෂ්පාදනය මධ්යම හා විශාල ප්රමාණයේ ව්යාපාර හෝ මහා පරිමාණ නිෂ්පාදනය සඳහා සුදුසු වේ.
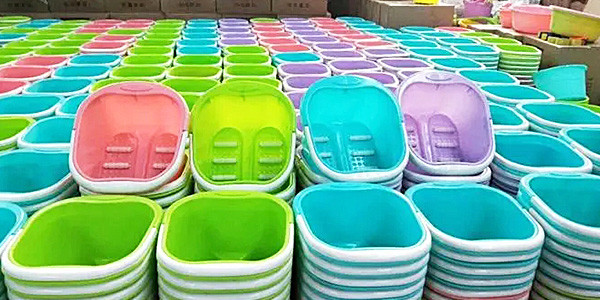
DJmolding's High-Volume Injection මෝල්ඩින් වාසි
* වේගවත් වේගයකින් වැඩි කොටස් නිෂ්පාදනය කරයි
*නිෂ්පාදකයා සඳහා ඒකක පිරිවැය සහ චක්ර කාලය අඩු කිරීම
*නිවැරදි සහ ස්ථාවර, උසස් තත්ත්වයේ මහා පරිමාණ කොටස් නිෂ්පාදනය
*නිෂ්පාදනය බොහෝ විට ඝණ, විශ්වාසදායක යන්ත්ර සූත්ර සමඟින්, වැඩ නොකරන වේලාවන්හිදී පවා ස්වයංක්රීය කළ හැක
*අවම පශ්චාත් නිෂ්පාදන කටයුතු
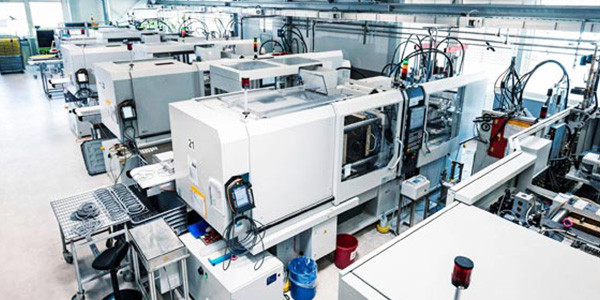
අභිරුචිකරණය කරන ලද ඉහළ වෙළුම් අච්චු (ප්ලාස්ටික් එන්නත් නිෂ්පාදන)
DJmolding හි අභිරුචි අච්චු සහ ඉහළ පරිමාවේ අච්චු වලට මූලාකෘතිවල සිට සම්පූර්ණ නිෂ්පාදන ප්රමාණයන් දක්වා සියල්ල ඇතුළත් වේ. අපගේ ඉහළ වෙළුම් අච්චු, කෙටි ධාවන, ඉහළ පරිමාවක් හෝ බහු කුහරයක් වේවා, ඒවා නිරීක්ෂණය කර පාලනය කරනු ලැබේ, එවිට අච්චු නිර්මාණයේ සහ ගොඩනැගීමේ සියලු අංශ පිළිබඳව ඔබට සහතික විය හැකිය. නිෂ්පාදන විස්තර සඳහා මෙම අවධානය ක්රියාවලියේ සෑම අදියරකදීම ඉලක්ක, අරමුණු සහ පෙර සැකසූ ව්යාපෘති ප්රතිඵල කාලසටහනට අනුව සහතික කරයි. සැලසුම් කිරීමේ සිට නිෂ්පාදනය දක්වා ඇති සියලුම ඉහළ පරිමාවේ අච්චු නිවස තුළ සම්පූර්ණ කර ඇති අතර අපගේ පාරිභෝගිකයින්ට පිරිවැය, ගුණාත්මකභාවය සහ ඉදිරි කාලය තුළ තරඟකාරී වාසි ලබා දේ.
DJmolding නිෂ්පාදන සැලසුම් කිරීම සහ ඉංජිනේරු කිරීම සඳහා සේවාලාභියා සමඟ ක්රියා කරයි, පිරිවැය කාර්යක්ෂමතාව සඳහා වඩාත් ඵලදායී ඉහළ පරිමාවේ අච්චු සංවර්ධනය කරයි. අපි පුළුල් පරාසයක සේවාවන් සපයන ප්ලාස්ටික් එන්නත් අච්චු කර්මාන්තයට පමණක් සීමා වූ විශිෂ්ට තත්ත්වයේ ඉහළ පරිමාවේ අච්චු සපයන්නෙමු. අඩු පරිමාවක් අච්චු ගැසීමේ සිට, අච්චු ඇතුළු කිරීම සහ පෑඩ් මුද්රණය කිරීම දක්වා, PTI, Inc. යනු ඔබේ ප්ලාස්ටික් එන්නත් මෝල්ඩින් සේවා සඳහා ඔබට විශ්වාස කළ හැකි සන්නාමයයි.
වෛද්ය, විදුලි, අත් ආයුධ, සන්නිවේදන සහ මෝටර් රථ කර්මාන්ත වැනි විවිධ ක්ෂේත්රවල පාරිභෝගිකයින් සඳහා DJmolding මූලාකෘති සංරචක. ටොන් 85-500 දක්වා විහිදෙන එන්නත් සහ සම්පීඩන මුද්රණ ඇතුළුව, DJmolding හි ඉහළ පරිමාවක් ඇති මෝල්ඩින් උපකරණ බොහොමයක් පරිගණක ගත කර ඇති අතර කාර්යක්ෂමතාව වැඩි කිරීමට සහ ගුණාත්මකභාවය ආරක්ෂා කිරීමට යාන්ත්රික පද්ධති භාවිතා කරයි. DJmolding හි දී අපි සෑම ව්යාපාරයක් සඳහාම හවුල්කාරිත්ව ආකල්පයක් ගනිමු, පුළුල් ප්ලාස්ටික් එන්නත් අච්චු අත්දැකීමක් ලබා දීම සඳහා නිර්මාණය කර ඇති පහසුකමකට වසර ගණනාවක ප්ලාස්ටික් එන්නත් අච්චු දැනුම සහ තාක්ෂණික ප්රවීණතාවය ගෙන එයි.
ප්ලාස්ටික් සංරචක සඳහා පාහේ අසීමිත ජ්යාමිතිය සමඟ ඉක්මනින් එන්නත් අච්චු නිර්මාණය කිරීමට තාක්ෂණය, උපකරණ සහ සුදුසුකම් ලත් අච්චු සාදන්නන්ගේ එකතුවක් අවශ්ය වේ.
සැලසුමේ සිට බෙදා හැරීම දක්වා, DJmolding හට ඔබේ සම්පූර්ණ මෙවලම් ගොඩනැගීමේ වැඩසටහන ආරම්භයේ සිට අවසානය දක්වා සම්බන්ධීකරණය කළ හැක. එහි තත්ත්ව සහතික කිරීමේ වැඩසටහනේ සහාය ඇතිව, PTI හි මෙහෙවර වන්නේ තම පාරිභෝගිකයින්ගේ අවශ්යතා සහ අපේක්ෂාවන් සම්පුර්ණයෙන්ම සපුරාලන හෝ ඉක්මවා යන අච්චු නිෂ්පාදන සැපයීමයි. සමාගම් කළමනාකාරිත්වය අඛණ්ඩ ගුණාත්මක දියුණුව සඳහා කැපවී සිටී. උසස් තත්ත්වයේ සහ කාර්යක්ෂම ඉහළ පරිමාවක් සහිත මෝල්ඩින් සේවා සඳහා, DJmolding අමතන්න. අද.
බොහෝ සමාගම්වලට පුස් සෑදීමේ අත්දැකීම අවසන් කිරීමට එතරම් පුළුල් ආරම්භයක් ලබා දීමට හැකියාවක් නැත. ඔබ වේගවත් මූලාකෘති කිහිපයක් සොයමින් සිටියත්, වෙළෙඳපොළට සූදානම් පාරිභෝගික ප්ලාස්ටික් දහස් ගණනක් හෝ නිෂ්පාදන කොටස් මිලියනයක් සොයන්නේ නම්, DJmolding හට ඔබට අවශ්ය දේ සැපයිය හැක. අඩු සහ ඉහළ පරිමාවක්, සෑම ඇණවුමක්ම එකම මට්ටමේ ගුණාත්මක බවකින් යුක්ත බව අපි ආඩම්බරයෙන් අවධාරනය කරමු. අදම අපගේ විශේෂඥයින් අමතන්න.
සැලසුමේ සිට බෙදා හැරීම දක්වා, DJmolding හට ඔබේ සම්පූර්ණ මෙවලම් ගොඩනැගීමේ වැඩසටහන ආරම්භයේ සිට අවසානය දක්වා සම්බන්ධීකරණය කළ හැක. උසස් තත්ත්වයේ සහ කාර්යක්ෂම සේවා සඳහා, ඔබේ තොරතුරු යැවීමෙන් මිල කැඳවීමක් ඉල්ලන්න info@jasonmolding.com
ඉහළ පරිමාවකින් යුත් ඉන්ජෙක්ෂන් මෝල්ඩින් නිෂ්පාදන ක්රියාවලිය බොහෝ සමාන ප්ලාස්ටික් කොටස් නිෂ්පාදනය කරයි. මෙම ක්රියාවලිය ජනප්රිය වන්නේ එය ලාභදායී, කාර්යක්ෂම සහ ස්ථාවර, උසස් තත්ත්වයේ කෑලි ලබා දෙන බැවිනි. මෙම බ්ලොග් සටහන එහි වාසි, අවාසි, යෙදුම් සහ තවත් බොහෝ දේ ඇතුළුව, ඉහළ පරිමාවකින් යුත් එන්නත් අච්චු ගැසීම ගැන ඔබට අවශ්ය සියල්ල ගවේෂණය කරනු ඇත.
High Volume Injection මෝල්ඩින් යනු කුමක්ද?
අධි පරිමා ඉන්ජෙක්ෂන් මෝල්ඩින් යනු බොහෝ සමාන ප්ලාස්ටික් කොටස් නිපදවන නිෂ්පාදන ක්රියාවලියකි. මෙම ක්රියාවලියට උණු කළ ප්ලාස්ටික් ද්රව්ය ඉහළ පීඩනයකින් සහ උෂ්ණත්වයකදී අච්චු කුහරයකට එන්නත් කිරීමෙන් එය අවශ්ය හැඩයට සිසිල් කිරීමට සහ ඝන වීමට ඉඩ සලසයි. මෙම අධි ස්වයංක්රීය ක්රියාවලියට එක් නිෂ්පාදන ධාවනයකදී සමාන කොටස් දහස් ගණනක් හෝ මිලියන ගණනක් නිපදවිය හැක.
ඉහළ කාර්යක්ෂම නිෂ්පාදන ක්රියාවලියක් සාර්ථක අධි පරිමා එන්නත් අච්චුවකට යතුරයි. මෙම ක්රියාවලියට අධිවේගී ඉන්ජෙක්ෂන් මෝල්ඩින් යන්ත්ර සහ ස්වයංක්රීය පද්ධති භාවිතා කිරීම ඇතුළත් වන අතර එමඟින් කොටස් වේගයෙන් හා නිරවද්යව නිෂ්පාදනය කිරීමට හැකි වේ. මීට අමතරව, නිෂ්පාදකයින්ට උසස් තත්ත්වයේ අච්චු භාවිතා කිරීමෙන් සහ නිශ්චිත එන්නත් පරාමිතීන් යෙදීමෙන් එක් එක් මූලද්රව්ය පිරිවිතරයන්ට අනුව සිදු කිරීම සහතික කළ හැකිය.
ඉහළ පරිමාවකින් යුත් එන්නත් අච්චු ගැසීමේ වඩාත් වැදගත් වාසියක් වන්නේ සමාන කොටස් විශාල ප්රමාණයක් ඉක්මනින් හා ලාභදායී ලෙස නිෂ්පාදනය කිරීමට ඇති හැකියාවයි. නිෂ්පාදන ක්රියාවලිය මෝටර් රථ, පාරිභෝගික භාණ්ඩ, වෛද්ය උපකරණ සහ ඉලෙක්ට්රොනික කර්මාන්ත සඳහා පරිපූර්ණයි.
ඉහළ පරිමාවකින් යුත් ඉන්ජෙක්ෂන් මෝල්ඩින්ගේ තවත් වාසියක් වන්නේ දැඩි ඉවසීම් සහිත සංකීර්ණ කොටස් නිෂ්පාදනය කිරීමේ හැකියාවයි. ඉන්ජෙක්ෂන් මෝල්ඩින් ක්රියාවලිය නිරවද්ය සහ ස්ථාවර වන අතර, එහි ප්රතිඵලයක් ලෙස කෑලි අතර අවම වෙනස්කම් ඇති සංකීර්ණ විස්තර ඇත.
එහි බොහෝ වාසි තිබියදීත්, ඉහළ පරිමාවකින් යුත් එන්නත් අච්චුවකට යම් සීමාවන් තිබේ. උදාහරණයක් ලෙස, ඉතා විශාල හෝ අවම කොටස් නිෂ්පාදනය කිරීම සඳහා වඩා හොඳ තේරීම් තිබිය හැක, මන්ද අවශ්ය අච්චු වල මිල සහ සංකීර්ණත්වය තහනම් විය හැක. මීට අමතරව, ප්ලාස්ටික් විශාල ප්රමාණයක් පාරිසරික බලපෑම් ඇති කළ හැකි අතර, නිෂ්පාදකයින්ට තිරසාරභාවය සහ ප්රතිචක්රීකරණය කිරීමේ උත්සාහයන් සලකා බැලීම අත්යවශ්ය වේ.
අධි පරිමා ඉන්ජෙක්ෂන් මෝල්ඩින් යනු ඉතා කාර්යක්ෂම හා ඵලදායී නිෂ්පාදන ක්රියාවලියක් වන අතර එමඟින් සමාන ප්ලාස්ටික් කොටස් විශාල ප්රමාණයක් ඉක්මනින් හා ලාභදායී ලෙස නිපදවිය හැකිය. එය පුළුල් පරාසයක කර්මාන්ත සඳහා කදිම තේරීමක් වන අතර, එහි නිරවද්යතාවය සහ අනුකූලතාව දැඩි ඉවසීම් සහිත සංකීර්ණ කොටස් නිෂ්පාදනය කිරීම සඳහා ජනප්රිය තේරීමක් කරයි. එයට යම් සීමාවන් ඇතත්, ඉහළ ප්රමාණයේ ඉන්ජෙක්ෂන් මෝල්ඩින්ගේ ප්රතිලාභ එය උසස් තත්ත්වයේ ප්ලාස්ටික් කොටස් විශාල ප්රමාණයක් නිෂ්පාදනය කිරීමට උත්සාහ කරන නිෂ්පාදකයින් සඳහා වටිනා මෙවලමක් බවට පත් කරයි.
අධි පරිමා ඉන්ජෙක්ෂන් මෝල්ඩින් වැඩ කරන්නේ කෙසේද?
ක්රියාවලියට ප්රධාන පියවර කිහිපයක් ඇතුළත් වන අතර, ඒ සෑම එකක්ම උසස් තත්ත්වයේ කොටස් නිෂ්පාදනය කිරීමේදී වැදගත් වේ. මෙම බ්ලොග් සටහන එහි ප්රධාන පියවර සහ සලකා බැලීම් ඇතුළුව, ඉහළ පරිමාවක් සහිත එන්නත් අච්චුව ක්රියා කරන ආකාරය ගෙනහැර දක්වයි.
අච්චු නිර්මාණය සහ සකස් කිරීම
ඉහළ පරිමාවකින් යුත් එන්නත් අච්චු ගැසීමේ පළමු පියවර වන්නේ නිෂ්පාදකයින් විසින් කොටස් නිෂ්පාදනය කිරීමට භාවිතා කරන අච්චුව සැලසුම් කිරීම සහ සකස් කිරීමයි. අවශ්ය කොටස් සෑදීම සඳහා අවශ්ය සියලු පිරිවිතරයන් සපුරාලන නිවැරදි නිර්මාණයක් නිර්මාණය කිරීම සඳහා අච්චු නිෂ්පාදකයෙකු සමඟ සහයෝගයෙන් කටයුතු කිරීම අවශ්ය වේ. සාමාන්යයෙන්, නිෂ්පාදකයින් වානේ හෝ ඇලුමිනියම් වලින් අච්චුව සාදන අතර ඉන්ජෙක්ෂන් මෝල්ඩින් ක්රියාවලියේ අධික පීඩනය සහ උෂ්ණත්වයට ඔරොත්තු දෙන ලෙස එය නිර්මාණය කරයි.
ද්රව්ය සකස් කිරීම
ඊළඟ පියවර වන්නේ නිෂ්පාදකයින් විසින් කොටස් නිෂ්පාදනය කිරීමට භාවිතා කරන ප්ලාස්ටික් ද්රව්ය සකස් කිරීමයි. භාවිතා කරන දුම්මල වර්ගය නිශ්චිත අවශ්යතා මත රඳා පවතින බැවින් සුදුසු ප්ලාස්ටික් දුම්මල තෝරා ගැනීම අපේක්ෂිත අංගයන් නිර්මාණය කිරීම සඳහා ඉතා වැදගත් වේ. ඉන්පසු දුම්මල එන්නත් අච්චු යන්ත්රයට ලබා දී රත් කර දිය කර දියර බවට පත් කරයි.
එන්නත් අච්චු කිරීමේ ක්රියාවලිය
උණු කළ ප්ලාස්ටික් ද්රව්ය ඉහළ පීඩනයකින් සහ උෂ්ණත්වයකදී අච්චු කුහරයට එන්නත් කරන විට එන්නත් අච්චු සැකසීමේ ක්රියාවලිය ආරම්භ වේ. ප්ලාස්ටික් සිසිල් වී ඝනීභවනය වන තුරු අච්චුව පීඩනය යටතේ වසා ඇත; මෙම අවස්ථාවේදී, අච්චුව විවෘත වන අතර, එම කොටස ඉවත් කරනු ලැබේ.
තත්ත්ව පාලනය
කොටස් නිෂ්පාදනය කළ පසු, ඒවා අවශ්ය පිරිවිතරයන් සපුරාලීම සහතික කිරීම සඳහා දැඩි තත්ත්ව පාලන ක්රියාවලියකට භාජනය වේ. එක් එක් කොටස ප්රමාණයෙන්, හැඩයෙන් සහ ගුණාත්මක භාවයෙන් අනුකූල බව තහවුරු කර ගැනීම සඳහා දෘෂ්ය පරීක්ෂණය, මිනුම් සහ පරීක්ෂණය මෙයට ඇතුළත් විය හැකිය.
අධි පරිමා එන්නත් අච්චු කිරීම සඳහා සලකා බැලීම්
ඉහළ පරිමාවකින් යුත් එන්නත් අච්චු භාවිතා කරන විට නිෂ්පාදකයින් මතක තබා ගත යුතු කරුණු කිහිපයක් ඇත, ඒවා අතර:
- යන්ත්ර තේරීම: අධිවේගී ඉන්ජෙක්ෂන් මෝල්ඩින් යන්ත්ර සාමාන්යයෙන් අධි-පරිමා නිෂ්පාදන ධාවනය සඳහා භාවිතා වේ, ඒවාට ඉක්මනින් හා නිවැරදිව කොටස් නිෂ්පාදනය කළ හැකිය.
- අච්චු නිර්මාණය: ඉන්ජෙක්ෂන් මෝල්ඩින් ක්රියාවලියේ සාර්ථකත්වය සඳහා අච්චු සැලසුම ඉතා වැදගත් වේ, මන්ද එය නිරවද්ය විය යුතු අතර ක්රියාවලියේ අධික පීඩනය සහ උෂ්ණත්වයට ඔරොත්තු දිය යුතුය.
- ද්රව්ය තෝරා ගැනීම: ප්ලාස්ටික් ෙරසින් තෝරාගැනීම නිෂ්පාදනය කරන කොටස්වල ගුණාත්මකභාවය සහ කාර්යසාධනය කෙරෙහි බලපෑම් කළ හැකි අතර, කාර්යය සඳහා සුදුසු ද්රව්ය තෝරාගැනීම අත්යවශ්ය වේ.
- පිරිවැය: ඉහළ පරිමා එන්නත් අච්චු ගැසීම ලාභදායී නිෂ්පාදන ක්රියාවලියක් වන අතර, අච්චු නිර්මාණය, ද්රව්ය තෝරා ගැනීම සහ නිෂ්පාදනය සම්බන්ධයෙන් සලකා බැලිය යුතු පිරිවැය තවමත් පවතී.
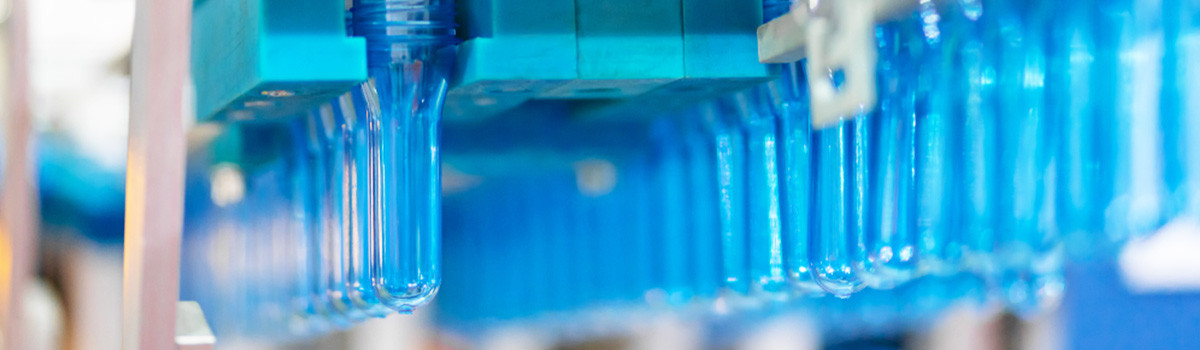
අධි පරිමා ඉන්ජෙක්ෂන් මෝල්ඩින් වල වාසි
ඉහළ පරිමාවකින් යුත් එන්නත් අච්චුව නිෂ්පාදන කර්මාන්තයේ විප්ලවීය වෙනසක් ඇති කර ඇති අතර, අසමසම වේගයකින් සහ කාර්යක්ෂමතාවයකින් විශාල ප්රමාණවලින් සමාන ප්ලාස්ටික් කොටස් නිෂ්පාදනය කිරීමට හැකි වේ. මෙම ක්රියාවලිය එහි බොහෝ වාසි නිසා විවිධ අංශ හරහා ජනප්රිය වී ඇති අතර, එය පිරිවැය අඩු කිරීමට, නාස්තිය අඩු කිරීමට සහ නිෂ්පාදන ප්රතිදානය වැඩි කිරීමට අපේක්ෂා කරන සමාගම් සඳහා නිෂ්පාදන ක්රමයක් බවට පත් කරයි.
- පිරිවැය ඵලදායී නිෂ්පාදනය: අධි පරිමා ඉන්ජෙක්ෂන් මෝල්ඩින් ඉතා කාර්යක්ෂම සහ ස්වයංක්රීය වන අතර එය අනෙකුත් නිෂ්පාදන ක්රියාවලීන් හා සසඳන විට ලාභදායී වේ. අච්චුව සැලසුම් කර සකස් කළ පසු, නිෂ්පාදන ක්රියාවලිය අඛණ්ඩව ක්රියාත්මක විය හැකි අතර, අවම ශ්රම හෝ ද්රව්යමය පිරිවැයක් සහිත සමාන කොටස් දහස් ගණනක් හෝ මිලියන ගණනක් නිෂ්පාදනය කරයි.
- ඉහළ නිෂ්පාදන ප්රතිදානය: අධිවේගී ඉන්ජෙක්ෂන් මෝල්ඩින් යන්ත්ර සමඟ, නිෂ්පාදකයින්ට කෙටි කාලයක් තුළ නිශ්චිත කොටස් විශාල ප්රමාණයක් නිෂ්පාදනය කළ හැකිය. මෙයින් අදහස් කරන්නේ වෙනස්වන ඉල්ලුම සපුරාලීම සඳහා නිෂ්පාදන නිෂ්පාදනය ඉක්මනින් වැඩි කිරීමට හෝ අඩු කිරීමට හැකි බවයි.
- ස්ථාවර ගුණාත්මකභාවය: අධි පරිමා එන්නත් අච්චුවෙහි නිරවද්යතාවය සහ අනුකූලතාවය දැඩි ඉවසීම් සහ සංකීර්ණ විස්තර සහිත කොටස් නිෂ්පාදනය කිරීම සඳහා වඩාත් සුදුසු වේ. ක්රියාවලිය ඉහළ නිරවද්යතාවයක් සඳහා ඉඩ සලසයි, නිෂ්පාදනය කරන සෑම කොටසක්ම අනෙක් ඒවාට සමාන බව සහතික කරයි.
- කොටස් නිර්මාණයේ බහුකාර්යතාව: අධි පරිමා ඉන්ජෙක්ෂන් මෝල්ඩින් සංකීර්ණ ජ්යාමිතිය සහිත ඒවා ඇතුළුව පුළුල් පරාසයක මෝස්තර සහ හැඩතල සහිත කොටස් නිෂ්පාදනය කළ හැකිය. මෙයින් අදහස් කරන්නේ නිෂ්පාදකයින්ට නිශ්චිත පාරිභෝගික අවශ්යතා සපුරාලන විශේෂාංග තිබිය හැකි අතර සැලසුම් හෝ නිෂ්පාදන පිරිවිතර වෙනස්කම් වලට පහසුවෙන් ගැලපීමට හැකි බවයි.
- අඩු කළ අපද්රව්ය: ඉහළ ප්රමාණයේ ඉන්ජෙක්ෂන් මෝල්ඩින් කිරීමේදී උසස් තත්ත්වයේ අච්චු සහ නිශ්චිත එන්නත් පරාමිතීන් භාවිතා කිරීම නිෂ්පාදන ක්රියාවලියේදී නිපදවන සීරීම් හෝ අපද්රව්ය ප්රමාණය අවම කරයි. මෙයින් අදහස් කරන්නේ නිෂ්පාදකයන්ට අවම ද්රව්යමය අපද්රව්ය සහිත කොටස් සෑදිය හැකි බවයි, පිරිවැය අඩු කිරීම සහ පාරිසරික බලපෑම.
- නිෂ්පාදන කාර්යක්ෂමතාව වැඩි කිරීම: අධි පරිමා ඉන්ජෙක්ෂන් මෝල්ඩින් ඉතා ස්වයංක්රීය වේ, එයින් අදහස් කරන්නේ එයට අවම ශ්රමයක් අවශ්ය වන අතර කුඩා මැදිහත්වීමකින් අඛණ්ඩව ක්රියාත්මක විය හැකි බවයි. අතින් වැඩ කිරීම හෝ අධීක්ෂණය කිරීමකින් තොරව නිෂ්පාදකයින්ට ඉක්මනින් හා කාර්යක්ෂමව කොටස් නිෂ්පාදනය කළ හැකි බැවින් මෙය නිෂ්පාදන කාර්යක්ෂමතාව වැඩි කිරීමට හේතු වේ.
අධි පරිමා එන්නත් අච්චු ගැසීමේ අවාසි
අධි පරිමා ඉන්ජෙක්ෂන් මෝල්ඩින් යනු සමාන ප්ලාස්ටික් කොටස් විශාල ප්රමාණයක් ඉක්මනින් හා ලාභදායී ලෙස නිෂ්පාදනය කිරීම සඳහා බහුලව භාවිතා වන නිෂ්පාදන ක්රියාවලියකි. එහි පිරිවැය-ඵලදායීතාවය සහ ස්ථාවර ගුණාත්මකභාවය වැනි බොහෝ වාසි ඇතත්, අවාසි ද ඇත. මෙම බ්ලොග් සටහන ඉහළ පරිමාවකින් යුත් එන්නත් අච්චු ගැසීමේ අවාසි කිහිපයක් ගවේෂණය කරනු ඇත.
- ඉහළ ආරම්භක ආයෝජන: ඉහළ පරිමාවකින් යුත් එන්නත් අච්චු ගැසීමේ මූලික අවාසියක් නම් අච්චුව සැලසුම් කිරීම සහ නිෂ්පාදනය කිරීම සඳහා අවශ්ය මූලික ආයෝජන වැඩි වීමයි. මෙම පිරිවැය විශේෂයෙන් කුඩා ව්යාපාර සඳහා හෝ විශේෂිත කොටස් සඳහා අභිරුචි කළ අච්චු අවශ්ය අය සඳහා සැලකිය යුතු විය හැකිය.
- ලෝන්ග් ලීඩ් ටයිම්ස්:අධි පරිමා ඉන්ජෙක්ෂන් මෝල්ඩින් සඳහා අච්චු සැලසුම් කිරීමේ සහ නිෂ්පාදනය කිරීමේ ක්රියාවලියට සති කිහිපයක් හෝ මාස කිහිපයක් ගත විය හැකි අතර, එහි ප්රතිඵලයක් ලෙස දිගු කාලයක් ගත වේ. ඉක්මනින් කොටස් නිෂ්පාදනය කිරීමට හෝ ඉල්ලුමේ වෙනස්කම් වලට ප්රතිචාර දැක්වීමට අවශ්ය සමාගම් සඳහා මෙය අවාසියක් විය හැකිය.
- සීමිත ද්රව්ය තේරීම්: ඉහළ පරිමාවකින් යුත් එන්නත් අච්චු ගැසීම සඳහා ප්ලාස්ටික් දුම්මල වර්ග බොහොමයක් පවතින අතර, විශේෂිත යෙදුම අනුව තෝරාගැනීම සීමා විය හැක. සමහර ප්ලාස්ටික් දුම්මල ද්රව්යමය තේරීම් සීමා කළ හැකි ඒවායේ ගුණාංග නිසා ඉහළ පරිමාවක් නිෂ්පාදනය සඳහා සුදුසු නොවේ.
- සීමිත නිර්මාණ නම්යශීලිත්වය: අධි පරිමා ඉන්ජෙක්ෂන් මෝල්ඩින් යනු නිශ්චිත පිරිවිතරයන් සමඟ අච්චු නිර්මාණය කළ යුතු නිශ්චිත ක්රියාවලියකි. මෙයින් අදහස් කරන්නේ මෙම ක්රියාවලිය හරහා නිෂ්පාදනය කරන ලද කොටස් සැලසුම් කිරීමේදී සීමාවන් තිබිය හැකි බවයි, විශේෂයෙන් පිහිටීම සංකීර්ණ ජ්යාමිතිය හෝ වෙනත් සුවිශේෂී සැලසුම් අවශ්යතා තිබේ නම්.
- ඉහළ නඩත්තු සහ අලුත්වැඩියා වියදම්: ප්රශස්ත ක්රියාකාරිත්වය සහතික කිරීම සඳහා ඉහළ පරිමාවකින් යුත් එන්නත් අච්චු ගැසීමේදී භාවිතා කරන අච්චු නඩත්තු කිරීම සහ අලුත්වැඩියා කිරීම නිතිපතා කළ යුතුය. නඩත්තු හා අලුත්වැඩියා කිරීමේ පිරිවැය සැලකිය යුතු විය හැකිය, ප්රධාන වශයෙන් අච්චු නිතර නිතර හෝ දිගු කාලයක් සඳහා භාවිතා කරයි නම්.
මෙම අවාසි තිබියදීත්, ඉහළ පරිමාවකින් යුත් එන්නත් අච්චුව සමාන ප්ලාස්ටික් කොටස් විශාල ප්රමාණයක් නිෂ්පාදනය කිරීම සඳහා ජනප්රිය හා ඵලදායී නිෂ්පාදන ක්රියාවලියක් ලෙස පවතී. මෙම ක්රියාවලියේ වාසි සහ අවාසි පරෙස්සමින් සලකා බැලීමෙන්, නිෂ්පාදකයින්ට ඔවුන්ගේ නිශ්චිත නිෂ්පාදන අවශ්යතා සඳහා එය නිවැරදි තේරීමද යන්න පිළිබඳව දැනුවත් තීරණ ගත හැකිය.
අධි පරිමා එන්නත් අච්චු ගැසීමේදී භාවිතා කරන ද්රව්ය
අවසාන නිෂ්පාදනයේ ගුණාත්මකභාවය සහ කාර්ය සාධනය සහතික කිරීම සඳහා ඉහළ පරිමාවකින් යුත් එන්නත් අච්චුව සඳහා සුදුසු ද්රව්ය තෝරා ගැනීම අත්යවශ්ය වේ. මෙම ලිපිය ඉහළ පරිමාවකින් යුත් එන්නත් අච්චු ගැසීමේදී භාවිතා කරන ද්රව්ය, ඒවායේ ගුණාංග සහ ඒවායේ යෙදීම් පිළිබඳව සොයා බලයි.
පොලිප්රොපිලීන් (PP)
පොලිප්රොපිලීන් යනු එහි අඩු පිරිවැය, ශක්තිය-බර අනුපාතය සහ කල්පැවැත්ම හේතුවෙන් ඉහළ පරිමා එන්නත් අච්චු ගැසීමේදී බහුලව භාවිතා වන තාප ප්ලාස්ටික් බහුඅවයවයකි. PP මෝටර් රථ, ඇසුරුම්කරණය සහ පාරිභෝගික භාණ්ඩ නිෂ්පාදනය සඳහා බහුකාර්ය වේ. ඉන්ජෙක්ෂන් මෝල්ඩින් කිරීමේදී PP භාවිතා කිරීමේ වාසි එහි සැහැල්ලු ස්වභාවය, රසායනික ප්රතිරෝධය සහ මාන ස්ථායීතාවය ඇතුළත් වන අතර එමඟින් එය නිරවද්ය කොටස් සඳහා වඩාත් සුදුසු වේ.
ඇක්රිලෝනයිට්රයිල් බියුඩඩීන් ස්ටයිරීන් (ABS)
ABS යනු එහි තද බව, බලපෑම් ප්රතිරෝධය සහ ඉහළ ග්ලෝස් නිමාව සඳහා ප්රසිද්ධ තාප ප්ලාස්ටික් බහුඅවයවයකි. මෙම ද්රව්ය සාමාන්යයෙන් සෙල්ලම් බඩු, මෝටර් රථ කොටස් සහ ඉලෙක්ට්රොනික නිවාසවල භාවිතා වේ. ABS හි බලපෑම් ප්රතිරෝධය එය බලපෑමට හෝ කම්පනයට ලක්වන විස්තර සඳහා සුදුසු වේ. එය සැකසීමට පහසු වන අතර විශිෂ්ට මතුපිට නිමාවකින් යුක්ත වන අතර එය ඉහළ පරිමාවකින් යුත් නිෂ්පාදන ධාවනය සඳහා වඩාත් සුදුසු වේ.
පොලිකාබනේට් (PC)
පොලිකාබනේට් යනු තාප ප්ලාස්ටික් බහුඅවයවයක් වන අතර එය අධික බලපෑම්-ප්රතිරෝධී, දෘශ්ය පැහැදිලි සහ තාප ප්රතිරෝධී වේ. එය මෝටර් රථ, අභ්යවකාශ සහ ඉලෙක්ට්රොනික කර්මාන්ත සඳහා ජනප්රිය ද්රව්යයකි. PC හි ප්රතිලාභ අතර විශිෂ්ට බලපෑම් ප්රතිරෝධය, දෘශ්ය පැහැදිලි බව සහ තාප ප්රතිරෝධය ඇතුළත් වන අතර එය ඉහළ උෂ්ණත්ව යෙදුම්, කාච සහ තිර සඳහා වඩාත් සුදුසු වේ.
පොලිඑතිලීන් (PE)
පොලිඑතිලීන් යනු නම්යශීලී, දැඩි සහ රසායනික-ප්රතිරෝධී තාප ප්ලාස්ටික් බහු අවයවයකි. ඇසුරුම් ද්රව්ය, ප්ලාස්ටික් බෑග් සහ කෘෂිකාර්මික චිත්රපට නිෂ්පාදනය සඳහා බහුලව භාවිතා වේ. PE හි රසායනික ප්රතිරෝධය, නම්යශීලී බව සහ සැහැල්ලු ස්වභාවය එය රසායනික සැකසුම් උපකරණ, රසායනික ද්රව්ය සඳහා ඇසුරුම් කිරීම සහ කොටස් නැමීමට හෝ නැමීමට අවශ්ය යෙදුම් සඳහා වඩාත් සුදුසු වේ.
පොලිඑතිලීන් ටෙරෙෆ්තලේට් (පීඊටී)
PET යනු ඉහළ ශක්තියට බර අනුපාතය, පැහැදිලි බව සහ බාධක ගුණ සහිත තාප ප්ලාස්ටික් බහුඅවයවයකි. එය බීම බෝතල්, ආහාර බහාලුම් සහ ඇසුරුම් ද්රව්ය නිෂ්පාදනය කරයි. PET හි ප්රතිලාභ අතර එහි ශක්තියට බර සමතුලිතතාවය, විනිවිදභාවය සහ බාධක ගුණාංග ඇතුළත් වන අතර එමඟින් ශක්තිය අවශ්ය යෙදුම් සඳහා වඩාත් සුදුසු වේ, එනම් බීම බෝතල් සහ අන්තර්ගතය තෙතමනය හා ඔක්සිජන් වලින් ආරක්ෂා කළ යුතු ඇසුරුම් ය.
පොලිඑස්ටිරන් (PS)
Polystyrene යනු තාප ප්ලාස්ටික් බහුඅවයවයක් වන අතර එය සැහැල්ලු, ලාභදායී සහ හොඳ පරිවාරක ගුණ ඇත. ඉවත දැමිය හැකි කෝප්ප, ඇසුරුම් ද්රව්ය සහ පරිවාරක නිෂ්පාදනය සඳහා PS බහුලව භාවිතා වන අතර එහි වාසි අතර අඩු මිල, සැහැල්ලු ස්වභාවය සහ හොඳ පරිවාරක ගුණ ඇතුළත් වේ.
අධි වෙළුම් නිෂ්පාදනය සඳහා භාවිතා කරන ඉන්ජෙක්ෂන් මෝල්ඩින් යන්ත්ර වර්ග
ක්රියාවලියට උණු කළ ප්ලාස්ටික් ද්රව්ය අච්චු කුහරයකට එන්නත් කිරීම ඇතුළත් වන අතර එහිදී එය ඝන වී අච්චුවේ හැඩය ගනී. ඉන්ජෙක්ෂන් මෝල්ඩින් යන්ත්ර විවිධ වර්ග වලින් පැමිණෙන අතර, ඒ සෑම එකක්ම නිශ්චිත නිෂ්පාදනයක් සඳහා සුදුසු වේ. ඉහළ පරිමාවක් නිෂ්පාදනය සඳහා භාවිතා කරන ප්රධාන ඉන්ජෙක්ෂන් මෝල්ඩින් යන්ත්ර මෙන්න:
- හයිඩ්රොලික් ඉන්ජෙක්ෂන් මෝල්ඩින් යන්ත්ර: මෙම යන්ත්ර මගින් අච්චුව චලනය කිරීමට හයිඩ්රොලික් පීඩනය භාවිතා කරන අතර උණු කළ ප්ලාස්ටික් කුහරයට එන්නත් කරයි. ඒවා ඉහළ නිෂ්පාදන නිමැවුම් සඳහා ප්රසිද්ධ නමුත් මන්දගාමී චක්රීය කාලයක් ද ඇත, ඉහළ නිරවද්යතාවය සහ අධිවේගී යෙදුම් සඳහා ඒවායේ භාවිතය සීමා කරයි.
- විද්යුත් ඉන්ජෙක්ෂන් මෝල්ඩින් යන්ත්ර: මෙම යන්ත්ර එන්නත් කිරීමේ ඒකකය සහ අච්චුව ධාවනය කිරීම සඳහා විදුලි සර්වෝ මෝටර භාවිතා කරයි. ඔවුන් ඉහළ නිරවද්යතාවයක් සහ වේගයක් ලබා දෙන අතර, වෛද්ය උපකරණ සහ ඉලෙක්ට්රොනික උපකරණ වැනි අධි තාක්ෂණික කර්මාන්ත සඳහා ඒවා වඩාත් සුදුසු වේ.
- හයිබ්රිඩ් ඉන්ජෙක්ෂන් මෝල්ඩින් යන්ත්ර: මෙම යන්ත්ර ලෝක දෙකෙන්ම හොඳම දේ ඒකාබද්ධ කරයි. ඉන්ජෙක්ෂන් ඒකකය සහ අච්චුව ධාවනය කිරීම සඳහා ඔවුන් හයිඩ්රොලික් සහ විදුලි පද්ධති භාවිතා කරයි. හයිබ්රිඩ් එන්ජින් කාර්යක්ෂම හා වේගවත් වන අතර ඉහළ නිෂ්පාදන ප්රතිදානයක් ඇති අතර ඒවා ඉහළ පරිමාවක් නිෂ්පාදනය සඳහා වඩාත් සුදුසු වේ.
- ද්වි-වෙඩි එන්නත් අච්චු යන්ත්ර: මෙම යන්ත්ර විවිධ ද්රව්ය හෝ වර්ණ දෙකක් අවශ්ය වන සංකීර්ණ කොටස් නිෂ්පාදනය කරයි. උපාංගයේ අවසාන කොටස නිර්මාණය කිරීම සඳහා එකට වැඩ කරන එන්නත් ඒකක දෙකක් ඇත. ද්වි-වෙඩි එන්නත් මෝල්ඩින් යන්ත්ර බහු සංරචක සහිත උසස් තත්ත්වයේ නිෂ්පාදන නිෂ්පාදනය කිරීම සඳහා වඩාත් සුදුසු වේ.
- බහු-ද්රව්ය එන්නත් අච්චු යන්ත්ර:මෙම යන්ත්ර විවිධ ද්රව්ය වලින් සාදන ලද කොටස් නිෂ්පාදනය කරයි. ඔවුන්ට වෙනත් ද්රව්ය එකවර භාවිතා කිරීමට ඉඩ සලසන බහු එන්නත් ඒකක ඇත. බහු-ද්රව්ය ඉන්ජෙක්ෂන් මෝල්ඩින් යන්ත්ර ශක්තිය, කල්පැවැත්ම සහ නම්යශීලී බව වැනි විවිධ ගුණාංග අවශ්ය කෑලි නිර්මාණය කිරීම සඳහා වඩාත් සුදුසු වේ.
- දියර එන්නත් අච්චු යන්ත්ර: මෙම යන්ත්ර ද්රව සිලිකොන් රබර් (LSR) වලින් සාදන ලද කොටස් නිෂ්පාදනය කිරීමට යොදා ගනී. යන්ත්රය පුස් කුහරයට LSR එන්නත් කරයි, එහිදී එය ඝන වී අච්චුවේ හැඩය ගනී. වෛද්ය උපකරණ සහ වාහන අමතර කොටස් වැනි ඉහළ නිරවද්යතාවයක් සහ කල්පැවැත්මක් අවශ්ය වන කොටස් නිෂ්පාදනය කිරීම සඳහා ද්රව එන්නත් අච්චු යන්ත්ර වඩාත් සුදුසු වේ.
අධි-පරිමා නිෂ්පාදනය සඳහා එන්නත් මෝල්ඩින් ක්රියාවලි පියවර
ක්රියාවලියට උණු කළ ප්ලාස්ටික් ද්රව්ය අච්චු කුහරයකට එන්නත් කිරීම ඇතුළත් වන අතර එහිදී එය ඝන වී අච්චුවේ හැඩය ගනී. ඉහළ පරිමාවක් නිෂ්පාදනය සඳහා එන්නත් අච්චු සැකසීමේ ක්රියාවලියට සම්බන්ධ පියවර මෙන්න:
- ද්රව්ය තෝරා ගැනීම: ඉන්ජෙක්ෂන් මෝල්ඩින් ක්රියාවලියේ පළමු පියවර වන්නේ කොටස නිෂ්පාදනය කිරීම සඳහා සුදුසු ද්රව්ය තෝරා ගැනීමයි. තෝරාගත් ද්රව්යයේ ශක්තිය, කල්පැවැත්ම සහ නම්යශීලීභාවය වැනි අවශ්ය ගුණාංග තිබිය යුතු අතර, ඉන්ජෙක්ෂන් මෝල්ඩින් යන්ත්රය සමඟ අනුකූල විය යුතුය.
- අච්චු නිර්මාණය: ඊළඟ පියවර වන්නේ ද්රව්යය තෝරාගත් පසු අච්චුව සැලසුම් කිරීමයි. එහි හැඩය, ප්රමාණය සහ ලක්ෂණ ඇතුළුව නිෂ්පාදනය කරන කොටසෙහි නිශ්චිත පිරිවිතරයන්ට අනුව අච්චුව සකස් කළ යුතුය. අච්චුව භාවිතා කරන එන්නත් අච්චු යන්ත්ර වර්ගය සහ නිෂ්පාදන ක්රියාවලියේ නිශ්චිත අවශ්යතා ද සැලකිල්ලට ගත යුතුය.
- යන්ත්ර සැකසුම: අච්චුව නිර්මාණය කිරීමෙන් පසුව, ඉන්ජෙක්ෂන් මෝල්ඩින් යන්ත්රය සකස් කර ඇත. මෙය උපාංගයට අච්චුව ඇමිණීම, නිසි උෂ්ණත්ව හා පීඩන සැකසුම් සැකසීම සහ සියල්ල නිවැරදිව ක්රියාත්මක වන බව තහවුරු කිරීම ඇතුළත් වේ.
- එන්නත් කිරීම: උණු කළ ප්ලාස්ටික් ද්රව්ය අච්චු කුහරය තුළට එන්නත් කරන විට එන්නත් කිරීමේ ක්රියාවලිය ආරම්භ වේ. මෙය සිදු කරනු ලබන්නේ අධි පීඩන එන්නත් ඒකකයක් භාවිතා කර ඇති අතර එමඟින් ද්රව්යය නිශ්චිත අනුපාතයකින් සහ පීඩනයකින් අච්චුව තුලට බල කරයි.
- සිසිලස:උණු කළ ප්ලාස්ටික් ද්රව්ය අච්චු කුහරය තුළට එන්නත් කිරීමෙන් පසුව, එය සිසිල් කිරීමට සහ ඝන වීමට ඉඩ දිය යුතුය. මෙය සිදු කරනු ලබන්නේ ද්රව්යයේ උෂ්ණත්වය අඩු කිරීම සඳහා අච්චු කුහරය හරහා සිසිල් වාතය හෝ ජලය සංසරණය කිරීමෙනි.
- පිටකිරීම: ප්ලාස්ටික් ද්රව්ය සිසිල් වී ඝන වීමෙන් පසුව, අච්චුව විවෘත කර ඇති අතර, එම කොටස ඉවත් කරනු ලැබේ. පිටකිරීමේ ක්රියාවලියට යාන්ත්රික හෝ හයිඩ්රොලික් පද්ධතියක් භාවිතයෙන් අච්චු කුහරයෙන් කොටස තල්ලු කිරීම ඇතුළත් වේ.
- තත්ත්ව පාලනය: කොටස ඉවත් කළ පසු, එය අවශ්ය පිරිවිතරයන් සපුරාලන බව සහතික කිරීම සඳහා තත්ත්ව පාලන පරීක්ෂාවලට භාජනය වේ. මෙයට දෘශ්ය පරීක්ෂණය, මිනුම් සහ පරීක්ෂණය ඇතුළත් විය හැකි අතර එම කොටස උසස් තත්ත්වයේ සහ දෝෂ රහිත බව තහවුරු කරයි.
අධි පරිමා එන්නත් අච්චු කිරීම සඳහා සැලසුම් සලකා බැලීම්
ඉහළ පරිමාවකින් යුත් එන්නත් මෝල්ඩින් සඳහා ප්ලාස්ටික් කොටසක් සැලසුම් කිරීම, කෑල්ලක් කාර්යක්ෂමව හා ලාභදායී ලෙස නිෂ්පාදනය කළ හැකි බව සහතික කිරීම සඳහා සාධක කිහිපයක් ප්රවේශමෙන් සලකා බැලීම අවශ්ය වේ. ඉහළ පරිමාවකින් යුත් එන්නත් අච්චු කිරීම සඳහා සැලසුම් සලකා බැලීම් කිහිපයක් මෙන්න:
- බිත්ති ick ණකම: ප්ලාස්ටික් කොටසක බිත්ති ඝණත්වය ඉන්ජෙක්ෂන් මෝල්ඩින් සඳහා අත්යවශ්ය කරුණකි. කැබැල්ලේ අසමාන සිසිලනය සහ විකෘති වීම වැළැක්වීම සඳහා බිත්තිවල ඝණකම ඒකාකාර විය යුතුය. තුනී බිත්ති ද්රව්යමය භාවිතය සහ චක්ර කාලය අඩු කරන බැවින්, ඝන බිත්ති අමතර ශක්තියක් අවශ්ය වන කොටස් සඳහා සුදුසු වන බැවින්, ඉහළ පරිමාවක් නිෂ්පාදනය සඳහා සුදුසු වේ.
- කොටස් ප්රමාණය සහ හැඩය: කොටසෙහි ප්රමාණය සහ හැඩය එන්නත් කිරීමේ ක්රියාවලියට බලපානු ඇත. ඉතා විශාල හෝ සංකීර්ණ සාධක සඳහා දිගු චක්ර කාලයන් හෝ විශේෂිත උපකරණ අවශ්ය විය හැක, නිෂ්පාදන පිරිවැය වැඩි කරයි. ඉහළ පරිමාවක් නිෂ්පාදනය සඳහා සරල, ජ්යාමිතික හැඩතල වඩාත් සුදුසු වේ.
- කෙටුම්පත් කෝණ: කෙටුම්පත් කෝණයක් යනු අච්චු කුහරයේ බිත්තියේ කෝණය වන අතර එමඟින් කොටස පහසුවෙන් ඉවත් කිරීමට ඉඩ සලසයි. කැබැල්ල ඉක්මනින් අච්චුවෙන් ඉවත් කළ හැකි බව සහතික කිරීම සඳහා කොටස් සැලසුමේ කෙටුම්පත් කෝණ ඇතුළුව අත්යවශ්ය වේ. කෙටුම්පත් කෝණ නොමැති ප්රමාණයන් ඉරිතැලීම් හෝ විරූපණය වැනි මිල අධික නිෂ්පාදන ගැටළු වලට හේතු විය හැක.
- ගේට්ටුවේ පිහිටීම සහ ප්රමාණය:ද්වාරයෙහි පිහිටීම සහ ප්රමාණය, උණු කළ ප්ලාස්ටික් ද්රව්ය අච්චු කුහරයට ඇතුළු වන විට, එන්නත් අච්චු ගැසීම සඳහා තීරනාත්මක සැලසුම් සලකා බැලීමකි. දොරටුවේ පිහිටීම කොටසෙහි ව්යුහාත්මක අඛණ්ඩතාවට බලපානු නොලැබෙන ප්රදේශයක තැබිය යුතුය. ද්වාර ප්රමාණය ද්රව්ය නිවැරදිව ගලා යාමට ඉඩ සලසන තරම් විශාල විය යුතු නමුත් පිහිටීමෙහි දෝෂ ඇති කරන තරම් විශාල නොවිය යුතුය.
- ද්රව්ය තෝරා ගැනීම: කොටස කාර්යක්ෂමව හා ලාභදායී ලෙස නිෂ්පාදනය කළ හැකි බව සහතික කිරීම සඳහා ද්රව්ය තෝරා ගැනීම අත්යවශ්ය වේ. ද්රව්ය තෝරා ගැනීම ශක්තිය, කල්පැවැත්ම සහ නම්යශීලීභාවය ඇතුළුව කැබැල්ලේ නිශ්චිත අවශ්යතා මත පදනම් විය යුතුය.
- මතුපිට නිමාව: ඉන්ජෙක්ෂන් මෝල්ඩින් කිරීම සඳහා කොටසෙහි මතුපිට නිමාව අත්යවශ්ය කරුණකි. ප්රමාණයේ මතුපිට නිමාව සුමට විය යුතු අතර විකෘති වීම හෝ ගිල්වීමේ සලකුණු වැනි දෝෂ වලින් තොර විය යුතුය. නිසි ගේට්ටු තැබීම, අච්චු නිර්මාණය සහ ද්රව්ය තෝරාගැනීම සුමට මතුපිට නිමාවක් ලබා ගත හැකිය.
- ඉවසීම: ඉවසීම යනු කොටසක මානයන්හි ඉඩ දී ඇති විචල්ය ප්රමාණයයි. කොටස නිවැරදිව හා නිවැරදිව නිෂ්පාදනය කළ හැකි බව සහතික කිරීම සඳහා කොටස් සැලසුම් අවධියේදී ඉවසීම සැලකිල්ලට ගත යුතුය.
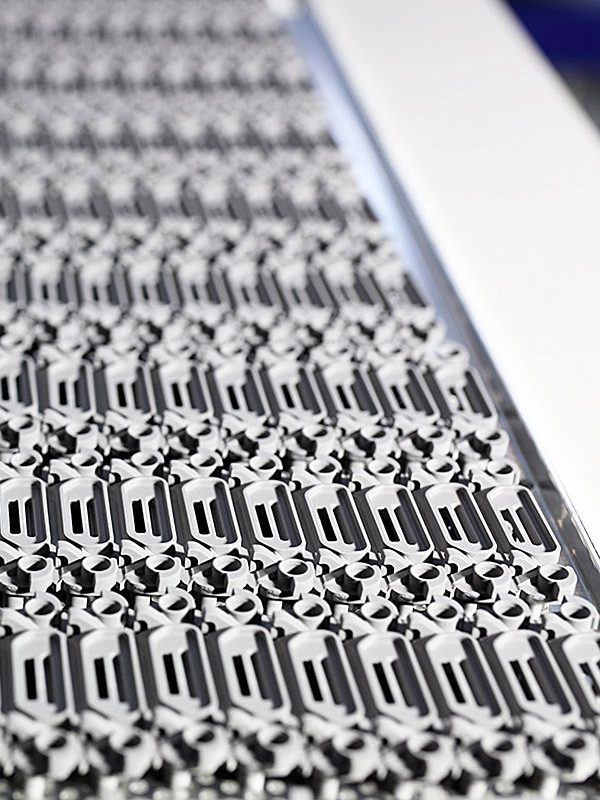
අධි පරිමා එන්නත් අච්චු ගැසීමේ තත්ත්ව පාලන පියවර
නිෂ්පාදනය කරන ලද කොටස් අවශ්ය පිරිවිතරයන් සපුරාලීම සහ දෝෂ වලින් තොර බව සහතික කරන බැවින්, ඉහළ පරිමා එන්නත් අච්චු ගැසීම සඳහා තත්ත්ව පාලනය අත්යවශ්ය වේ. ඉහළ පරිමාවකින් යුත් එන්නත් අච්චු ගැසීමේදී භාවිතා කරන තත්ත්ව පාලන පියවර කිහිපයක් මෙන්න:
- නිෂ්පාදන ක්රියාවලියේදී පරීක්ෂා කිරීම: නිෂ්පාදන ක්රියාවලියේදී නිතිපතා සමාලෝචනය මඟින් දෝෂ කල්තියා හඳුනා ගැනීමට සහ ඒවා වඩාත් වැදගත් ගැටළු බවට පත්වීම වළක්වා ගැනීමට උපකාරී වේ. මෙම කොටස නිවැරදිව නිෂ්පාදනය කරන බව තහවුරු කර ගැනීම සඳහා දෘශ්ය පරීක්ෂාව, මිනුම් සහ පරීක්ෂණ ඇතුළත් විය හැකිය.
- සංඛ්යාන ක්රියාවලි පාලනය (SPC): SPC යනු නිෂ්පාදන ක්රියාවලියක් නිරීක්ෂණය කිරීම සහ පාලනය කිරීම සඳහා භාවිතා කරන සංඛ්යානමය ක්රමයකි. නිෂ්පාදන ක්රියාවලිය පිළිබඳ දත්ත රැස් කිරීම සහ ක්රියාවලියේ ගැටළු පෙන්නුම් කරන ප්රවණතා සහ රටා හඳුනා ගැනීම සඳහා එය විශ්ලේෂණය කිරීම එයට ඇතුළත් වේ. දෝෂ සහිත කොටස් ඇති වීමට පෙර ගැටළු හඳුනා ගැනීමට සහ නිවැරදි කිරීමට SPC හට උපකාර කළ හැක.
- ස්වයංක්රීය උපකරණ භාවිතය: රොබෝවරු සහ සංවේදක වැනි ස්වයංක්රීය උපකරණ නිෂ්පාදන ක්රියාවලියේ අනුකූලතාව සහ නිරවද්යතාවය වැඩි දියුණු කිරීමට උපකාරී වේ. යාන්ත්රික උපකරණ මගින් මානව දෝෂ ඇතිවීමේ අවදානම ද අඩු කළ හැකි අතර, එහි ප්රතිඵලයක් ලෙස අඩු දෝෂ ඇතිවේ.
- අච්චු නඩත්තු කිරීම:නිෂ්පාදනය කරන ලද කොටස් උසස් තත්ත්වයේ බව සහතික කිරීම සඳහා නිසි අච්චු නඩත්තු කිරීම ඉතා වැදගත් වේ. අච්චුව නිතිපතා පිරිසිදු කිරීම සහ අච්චුව නිවැරදිව ක්රියාත්මක වන බව සහතික කිරීම සඳහා අවශ්ය ඕනෑම අලුත්වැඩියාවක් හෝ ප්රතිස්ථාපනයක් සිදු කිරීම මෙයට ඇතුළත් වේ.
- පශ්චාත් නිෂ්පාදන පරීක්ෂාව: කොටස් නිෂ්පාදනය කිරීමෙන් පසු, ඒවා අවශ්ය පිරිවිතරයන් සපුරාලීම සහතික කිරීම සඳහා අවසාන පරීක්ෂණයකට භාජනය වේ. මෙයට දෘශ්ය පරීක්ෂාව, මැනීම සහ කොටස් දෝෂ වලින් තොර බව තහවුරු කර ගැනීම ඇතුළත් විය හැක.
- පුහුණුව සහ අධ්යාපනය: සේවකයින්ගේ නිසි පුහුණුව සහ අධ්යාපනය නිෂ්පාදන ක්රියාවලියේ ගුණාත්මක භාවය වැඩිදියුණු කළ හැකිය. ගැටළු පැනනගින විට ඒවා හඳුනාගෙන ඒවා නිවැරදි කළ හැකි බව සහතික කිරීම සඳහා නිසි නිෂ්පාදන ශිල්පීය ක්රම සහ තත්ත්ව පාලන ක්රම පිළිබඳව සේවකයින් පුහුණු කළ යුතුය.
- අඛණ්ඩ වැඩිදියුණු කිරීම: අධි පරිමා එන්නත් අච්චු ගැසීමේදී තත්ත්ව පාලනය සඳහා අඛණ්ඩ වැඩිදියුණු කිරීම් අත්යවශ්ය වේ. නිෂ්පාදන ක්රියාවලිය නිතිපතා සමාලෝචනය කිරීමෙන් සහ වැඩිදියුණු කිරීම සඳහා ක්ෂේත්ර හඳුනා ගැනීමෙන්, නිෂ්පාදකයින්ට දෝෂ අවම කර නිෂ්පාදනය කරන ලද කොටස්වල ගුණාත්මකභාවය වැඩි දියුණු කළ හැකිය.
අධි පරිමා එන්නත් අච්චුවෙහි පිරිවැය විශ්ලේෂණය
අධි පරිමා ඉන්ජෙක්ෂන් මෝල්ඩින් යනු ප්ලාස්ටික් කොටස් විශාල ප්රමාණයක් නිෂ්පාදනය කිරීම සඳහා ලාභදායී නිෂ්පාදන ක්රියාවලියකි. කෙසේ වෙතත්, ඉන්ජෙක්ෂන් මෝල්ඩින් හරහා කොටස් නිෂ්පාදනය කිරීමේ පිරිවැය සාධක කිහිපයක් මත පදනම්ව වෙනස් විය හැක. ඉහළ පරිමාවකින් යුත් එන්නත් අච්චුව සඳහා පිරිවැය විශ්ලේෂණ සලකා බැලීම් කිහිපයක් මෙන්න:
- ද්රව්ය පිරිවැය: අමුද්රව්යවල පිරිවැය එන්නත් අච්චුවක මිලට බලපාන වඩාත්ම වැදගත් සාධකයකි. භාවිතා කරන ද්රව්යවල වර්ගය සහ ගුණාත්මකභාවය මිලට බලපානු ඇත, සමහර ද්රව්ය අනෙක් ඒවාට වඩා මිල අධික වේ. නිෂ්පාදකයින් විසින් කොටසෙහි නිශ්චිත අවශ්යතා මත පදනම්ව සුදුසු ද්රව්ය තෝරා ගත යුතුය.
- මෙවලම් පිරිවැය: ඉන්ජෙක්ෂන් මෝල්ඩින් සඳහා අවශ්ය අච්චු සහ අනෙකුත් උපකරණ ඇතුළුව මෙවලම් පිරිවැය නිෂ්පාදන පිරිවැයට බලපාන තවත් වැදගත් සාධකයකි. කොටසෙහි සංකීර්ණත්වය, අච්චුවේ විශාලත්වය සහ අච්චුවේ ඇති කුහර ගණන අනුව මෙවලම් පිරිවැය වෙනස් විය හැක.
- ශ්රම පිරිවැය: යන්ත්ර ක්රියාත්මක කිරීමට සහ නිෂ්පාදන ක්රියාවලිය අධීක්ෂණය කිරීමට දක්ෂ සේවකයින් අවශ්ය වන බැවින්, ශ්රම පිරිවැය එන්නත් අච්චු ගැසීමේ දී සැලකිය යුතු සාධකයකි. කම්කරුවන්ගේ ස්ථානය සහ පළපුරුද්ද අනුව ශ්රම පිරිවැය වෙනස් විය හැක.
- පොදු කාර්ය පිරිවැය: උපයෝගිතා, කුලී සහ අනෙකුත් වියදම් ඇතුළු පොදු කාර්ය පිරිවැය, එන්නත් අච්චු පිරිවැයට බලපෑම් කළ හැකිය. නිෂ්පාදන පහසුකම්වල පිහිටීම සහ මෙහෙයුමේ විශාලත්වය අනුව මෙම පිරිවැය වෙනස් විය හැක.
- නිෂ්පාදන පරිමාව: නිෂ්පාදන පරිමාව එන්නත් අච්චු පිරිවැයට බලපාන අත්යවශ්ය සාධකයකි. පරිමාණයේ ආර්ථිකයන් හේතුවෙන් ඉහළ නිෂ්පාදන පරිමාවන් කොටසකට අඩු පිරිවැයක් ඇති කළ හැකිය.
- කොටස් නිර්මාණය: සැලසුම ඉන්ජෙක්ෂන් මෝල්ඩින් පිරිවැයට ද බලපෑම් කළ හැකිය. සංකීර්ණ හෝ විශේෂිත උපකරණ අවශ්ය වන සාධක නිෂ්පාදන පිරිවැය වැඩි කළ හැකිය.
- තත්ත්ව පාලනය: පරීක්ෂා කිරීම සහ පරීක්ෂා කිරීම ඇතුළු තත්ත්ව පාලන පියවරවල පිරිවැය නිෂ්පාදන පිරිවැයට ද බලපෑම් කළ හැකිය. නිෂ්පාදනය කරන ලද කොටස් අවශ්ය පිරිවිතරයන් සපුරාලීම සහ දෝෂ රහිත බව සහතික කිරීම සඳහා මෙම පියවර අවශ්ය වේ.
අධි පරිමා ඉන්ජෙක්ෂන් මෝල්ඩින් භාවිතා කරන කර්මාන්ත
අධි පරිමා ඉන්ජෙක්ෂන් මෝල්ඩින් යනු පුළුල් ලෙස භාවිතා වන නිෂ්පාදන ක්රියාවලියක් වන අතර එය විශාල ප්රමාණයේ ප්ලාස්ටික් කොටස් ඉක්මනින් හා කාර්යක්ෂමව නිෂ්පාදනය කළ හැකිය. ඉහළ පරිමාවකින් යුත් එන්නත් අච්චුව මත දැඩි ලෙස රඳා පවතින සමහර කර්මාන්ත මෙන්න:
- වාහන නිෂ්පාදන කර්මාන්තය: මෝටර් රථ කර්මාන්තය ඉහළ පරිමාවකින් යුත් ඉන්ජෙක්ෂන් මෝල්ඩින් වඩාත් වැදගත් පරිශීලකයන්ගෙන් එකකි. ක්රියාවලිය මඟින් උපකරණ පුවරු කොටස්, දොර හැන්ඩ්ල් සහ අභ්යන්තර ටිම් කෑලි වැනි විවිධ ප්ලාස්ටික් සංරචක නිෂ්පාදනය කරයි.
- පාරිභෝගික භාණ්ඩ කර්මාන්තය: ඉහළ පරිමාවකින් යුත් එන්නත් අච්චුව ගෘහ උපකරණ, සෙල්ලම් බඩු සහ ඉලෙක්ට්රොනික උපකරණ ඇතුළු විවිධ පාරිභෝගික භාණ්ඩ නිෂ්පාදනය කරයි. ක්රියාවලිය වඩාත් කැමති වන්නේ එය නිෂ්පාදකයින්ට විශාල කොටස් ලාභදායී ලෙස නිර්මාණය කිරීමට ඉඩ සලසන බැවිනි.
- වෛද්ය කර්මාන්තය: වෛද්ය කර්මාන්තයට රෝග විනිශ්චය උපකරණ, ශල්ය උපකරණ සහ ඉවත දැමිය හැකි වෛද්ය සැපයුම් වැනි විවිධ වෛද්ය උපකරණ සඳහා උසස් තත්ත්වයේ සහ නිරවද්ය ප්ලාස්ටික් සංරචක අවශ්ය වේ. මෙම කොටස් නිවැරදිව හා ස්ථාවර ලෙස නිපදවිය හැකි බැවින් අධි පරිමා එන්නත් අච්චුව වඩාත් කැමති වේ.
- කර්මාන්ත:ඇසුරුම් කර්මාන්තය විවිධ ප්ලාස්ටික් බහාලුම්, පියන සහ වසා දැමීම් නිෂ්පාදනය කිරීම සඳහා ඉහළ පරිමාවකින් යුත් එන්නත් අච්චුව මත දැඩි ලෙස රඳා පවතී. මෙම ක්රියාවලිය ලාභදායී වන අතර නිෂ්පාදකයින්ට විවිධ හැඩයන් සහ ප්රමාණ ඉක්මනින් නිර්මාණය කිරීමට ඉඩ සලසයි.
- අභ්යවකාශ කර්මාන්තය: අභ්යවකාශ කර්මාන්තයට ඉහළ උෂ්ණත්වයන් සහ පීඩනය වැනි ආන්තික තත්වයන්ට ඔරොත්තු දිය හැකි ඉහළ ක්රියාකාරී ප්ලාස්ටික් සංරචක අවශ්ය වේ. ඉහළ පරිමාවකින් යුත් එන්නත් අච්චුව අභ්යන්තර සහ බාහිර ගුවන් යානා කොටස්, ගුවන් යානා සහ ඉලෙක්ට්රොනික උපකරණ ඇතුළුව මෙම සංරචක නිෂ්පාදනය කරයි.
- ඉදිකිරීම් කර්මාන්තයේ: ඉදිකිරීම් කර්මාන්තය ජනෙල් රාමු, පයිප්ප සහ පරිවරණය ඇතුළු විවිධ ප්ලාස්ටික් සංරචක නිෂ්පාදනය කිරීම සඳහා ඉහළ පරිමාවකින් යුත් එන්නත් අච්චු භාවිතා කරයි. පාරිසරික සාධකවලට ඔරොත්තු දෙන කල් පවතින හා ප්රතිරෝධී කොටස් විශාල ප්රමාණයක් නිෂ්පාදනය කිරීමට ඉඩ සලසන බැවින් ක්රියාවලිය වඩාත් කැමති වේ.
- ක්රීඩා සහ විනෝදාස්වාද කර්මාන්තය: ඉහළ පරිමාවකින් යුත් එන්නත් අච්චුව ක්රීඩා සහ විනෝදාස්වාද කර්මාන්තය සඳහා හිස්වැසුම්, ආරක්ෂිත ආම්පන්න සහ සෙල්ලම් බඩු ඇතුළු විවිධ ප්ලාස්ටික් සංරචක නිෂ්පාදනය කරයි. සැහැල්ලු, කල් පවතින සහ සෞන්දර්යාත්මක කොටස් සෑදීමට ඉඩ සලසන බැවින් ක්රියාවලිය වඩාත් කැමති වේ.
වෛද්ය කර්මාන්තය සඳහා අධි පරිමා එන්නත් අච්චු ගැසීමේ ප්රතිලාභ
වෛද්ය කර්මාන්තය ලොව විශාලතම හා වේගයෙන්ම වර්ධනය වන කර්මාන්තවලින් එකකි. තාක්ෂණයේ දියුණුවත් සමඟ වෛද්ය උපකරණ සහ උපකරණ සඳහා වැඩිවන ඉල්ලුමත් සමඟ උසස් තත්ත්වයේ සංරචක නිෂ්පාදනය කළ හැකි කාර්යක්ෂම නිෂ්පාදන ක්රියාවලීන් අවශ්ය වේ. අධි පරිමා එන්නත් අච්චු ගැසීම වෛද්ය කර්මාන්තයට ප්රතිලාභ කිහිපයක් ලබා දෙන එවැනි ක්රියාවලියකි. වෛද්ය ක්ෂේත්රයේ ඉහළ ප්රමාණයේ එන්නත් අච්චු ගැසීමේ වාසි කිහිපයක් අපි සොයා බලමු.
- ලාභදායී: අධි පරිමා ඉන්ජෙක්ෂන් මෝල්ඩින් යනු පිරිවැය-ඵලදායී නිෂ්පාදන ක්රියාවලියක් වන අතර එය ඒකකයකට අඩු වියදමකින් විශාල ප්රමාණයේ ප්ලාස්ටික් සංරචක නිෂ්පාදනය කරයි.
- අනුකූලතාව: ඉහළ පරිමාවකින් යුත් එන්නත් අච්චුව මඟින් ඉහළ දුස්ස්රාවිතතාවයකින් සහ නිරවද්යතාවයකින් යුත් කොටස් නිෂ්පාදනය කිරීමට ඉඩ සලසයි, එක් එක් කැබැල්ල අවශ්ය පිරිවිතරයන් සපුරාලන බව සහතික කරයි.
- පාරිභෝගිකයාගේ: වර්ණය, වයනය සහ ද්රව්ය ඇතුළුව විශේෂිත අවශ්යතාවලට ගැලපෙන පරිදි විශේෂාංග අභිරුචිකරණය කිරීමට ක්රියාවලිය ඉඩ දෙයි.
- වේගය: ඉහළ පරිමාවකින් යුත් එන්නත් අච්චුව ඉක්මනින් තනතුරු නිෂ්පාදනය කිරීමට ඉඩ සලසයි, ඊයම් කාලය අඩු කිරීම සහ කාර්යක්ෂමතාව වැඩි කිරීම.
- තත්ත්ව: අධි පරිමා ඉන්ජෙක්ෂන් මෝල්ඩින් ක්රියාවලිය වෛද්ය උපකරණ සඳහා අවශ්ය දැඩි ප්රමිතීන් සපුරාලන උසස් තත්ත්වයේ කොටස් නිෂ්පාදනය කරයි.
- වඳභාවය: ක්රියාවලිය වඳ පරිසරයක් තුළ සිදු කරනු ලබන අතර, නිෂ්පාදනය කරන ලද කොටස් දූෂණයෙන් තොර සහ වෛද්ය යෙදුම් සඳහා ආරක්ෂිත බව සහතික කරයි.
- කල්පැවැත්ම: අධි පරිමා ඉන්ජෙක්ෂන් මෝල්ඩින් භාවිතයෙන් නිෂ්පාදනය කරන ලද කොටස් කල් පවතින ඒවා වන අතර කටුක පරිසරයන්ට ඔරොත්තු දෙන අතර ඒවා දිගු කල් පවතින බව සහතික කිරීම සහ ප්රතිස්ථාපනය කිරීමේ අවශ්යතාවය අඩු කරයි. වෛද්ය ක්ෂේත්රයේ කල්පැවැත්ම තීරණාත්මක වන අතර, උපාංග සහ උපකරණ නිරන්තර භාවිතයට ඔරොත්තු දිය යුතු අතර රසායනික ද්රව්ය සහ අනෙකුත් කටුක මූලද්රව්යවලට නිරාවරණය වීමට ඉඩ ඇත.
- සංකීර්ණත්වය: නවීන වෛද්ය විද්යාවේ නියම අවශ්යතා සපුරාලීම සඳහා වෛද්ය උපකරණ සෑදිය හැකි බව සහතික කරමින්, අධි පරිමා එන්නත් අච්චු සැකසීමේ ක්රියාවලිය සංකීර්ණ මෝස්තර සහිත සංකීර්ණ කොටස් නිෂ්පාදනය කිරීමට ඉඩ සලසයි. මෙම ක්රියාවලිය වෛද්ය උපකරණ සහ උපකරණ සඳහා අත්යවශ්ය අද්විතීය ලක්ෂණ සහ මෝස්තර සහිත සංකීර්ණ සංරචක නිෂ්පාදනය කිරීම සඳහා සුදුසු වේ.
- බහුකාර්යතාව: ඉහළ පරිමාවකින් යුත් එන්නත් අච්චුවකට විවිධ හැඩයන් සහ ප්රමාණවලින් විවිධ කොටස් නිපදවිය හැකි අතර, එය විවිධ වෛද්ය යෙදුම්වල සංරචක නිර්මාණය කිරීම සඳහා වඩාත් සුදුසු වේ.
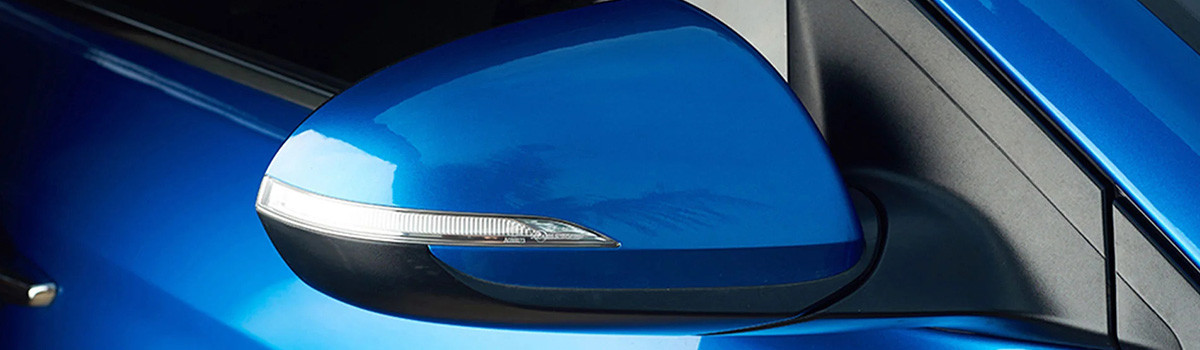
මෝටර් රථ කර්මාන්තය සඳහා ඉහළ වෙළුම් එන්නත් අච්චුව
ඉන්ජෙක්ෂන් මෝල්ඩින් යනු නිෂ්පාදන ක්රියාවලියක් වන අතර එය විවිධ ප්ලාස්ටික් සංරචක නිර්මාණය කිරීම සඳහා උණු කළ ප්ලාස්ටික් අච්චු කුහරයකට එන්නත් කිරීම ඇතුළත් වේ. දොර පැනල්, උපකරණ පුවරු, උපකරණ පුවරු, අභ්යන්තර සැරසිලි සහ බාහිර ශරීර කොටස් වැනි බහු කොටස් නිෂ්පාදනය කිරීම සඳහා මෙම ක්රියාවලිය මෝටර් රථ කර්මාන්තයේ බහුලව භාවිතා වේ. අධි පරිමා ඉන්ජෙක්ෂන් මෝල්ඩින් යනු නිෂ්පාදකයින්ට ඉක්මනින් සමාන කොටස් විශාල ප්රමාණයක් නිපදවීමට හැකි විශේෂිත තාක්ෂණයකි.
අධි පරිමා ඉන්ජෙක්ෂන් මෝල්ඩින් යනු මෝටර් රථ කර්මාන්තය සඳහා ප්රතිලාභ කිහිපයක් ලබා දෙන ඉතා කාර්යක්ෂම නිෂ්පාදන තාක්ෂණයකි. මෙම ප්රතිලාභ සමහරක් ඇතුළත් වේ:
- නිෂ්පාදන පිරිවැය අඩු කිරීම - මෙම ක්රියාවලිය බෙහෙවින් ස්වයංක්රීය වන අතර, ශ්රම පිරිවැය අඩු කරයි, සහ අච්චු නිෂ්පාදකයින්ට අඩු මිලකට සමාන කොටස් නිෂ්පාදනය කිරීමට ඉඩ සලසයි.
- වැඩි දියුණු කරන ලද කොටස් අනුකූලතාව - ඉහළ පරිමාවකින් යුත් එන්නත් මෝල්ඩින් එක සමාන කොටස් නිෂ්පාදනය කිරීමට ඉඩ සලසයි, නිෂ්පාදන ක්රියාවලියේ විචල්යතාව අඩු කිරීම සහ වයනය වැඩිදියුණු කිරීම.
- වේගවත් නිෂ්පාදන කාලය - මෙම ක්රියාවලිය අතිශයින් ස්වයංක්රීය වන අතර එමඟින් නිෂ්පාදකයින්ට විශාල කොටස් ප්රමාණයක් ඉක්මනින් නිෂ්පාදනය කිරීමට හැකි වන අතර එමඟින් ඊයම් කාලය අඩු වේ.
- උසස් තත්ත්වයේ කොටස් - අච්චු භාවිතය අවම දෝෂ සහ නොගැලපීම් සහිතව නිෂ්පාදනය කරන ලද කොටස් උසස් තත්ත්වයේ බව සහතික කරයි.
- නිර්මාණ නම්යශීලී බව -ඉන්ජෙක්ෂන් මෝල්ඩින් සංකීර්ණ හැඩතල සහ මෝස්තර වේගයෙන් නිෂ්පාදනය කිරීමට ඉඩ සලසයි, නිර්මාණකරුවන්ට ඔවුන්ගේ සැලසුම්වල වැඩි නම්යශීලී බවක් ලබා දෙයි.
ඉන්ජෙක්ෂන් මෝල්ඩින් යනු මෝටර් රථ කර්මාන්තය සඳහා කදිම නිෂ්පාදන තාක්ෂණයකි, එය කාර්යක්ෂමතාව වැඩි දියුණු කරන, පිරිවැය අඩු කරන සහ කොටස්වල ගුණාත්මකභාවය වැඩි දියුණු කරන ප්රතිලාභ රාශියක් ලබා දෙයි. අධි පරිමා ඉන්ජෙක්ෂන් මෝල්ඩින්, විශේෂයෙන්ම, නිෂ්පාදකයින්ට සමාන කොටස් විශාල ප්රමාණයක් ඉක්මනින් හා කාර්යක්ෂමව නිෂ්පාදනය කිරීමට හැකි විශේෂිත තාක්ෂණයකි.
මෝටර් රථ කර්මාන්තය විවිධ මෝටර් රථ සහ වාහන සංරචක නිෂ්පාදනය කිරීම සඳහා ඉන්ජෙක්ෂන් මෝල්ඩින් මත දැඩි ලෙස රඳා පවතී. බාහිර ශරීර කොටස්වල සිට අභ්යන්තර සැරසිලි සහ උපකරණ පුවරු දක්වා, ඉන්ජෙක්ෂන් මෝල්ඩින් මෝටර් රථ කර්මාන්තයේ අත්යවශ්ය නිෂ්පාදන ක්රියාවලියක් බවට පත්ව ඇත. ඉහළ ප්රමාණයේ එන්නත් අච්චුවකින්, නිෂ්පාදකයින්ට අඩු මිලකට, වැඩිදියුණු කළ අනුකූලතාව සහ ගුණාත්මකභාවය සමඟ සමාන කොටස් විශාල ප්රමාණයක් නිෂ්පාදනය කළ හැකිය.
පාරිභෝගික භාණ්ඩ කර්මාන්තය සඳහා ඉහළ වෙළුම් එන්නත් අච්චුව
අධි පරිමා ඉන්ජෙක්ෂන් මෝල්ඩින් යනු විශිෂ්ට නිරවද්යතාවයකින් සහ අනුකූලතාවයකින් යුත් උසස් තත්ත්වයේ කොටස් විශාල ප්රමාණයක් නිෂ්පාදනය කිරීමට ඇති හැකියාව හේතුවෙන් පාරිභෝගික භාණ්ඩ කර්මාන්තය විසින් බහුලව භාවිතා කරන නිෂ්පාදන ක්රියාවලියකි. මෙම ක්රියාවලිය සාමාන්යයෙන් සෙල්ලම් බඩු, මුළුතැන්ගෙයි උපකරණ සහ ඇසුරුම් ද්රව්ය වැනි පාරිභෝගික භාණ්ඩ නිෂ්පාදනය කිරීමේදී භාවිතා වේ. මෙම බ්ලොග් සටහන පාරිභෝගික භාණ්ඩ කර්මාන්තය සඳහා ඉහළ පරිමා එන්නත් අච්චු ගැසීමේ ප්රතිලාභ ගවේෂණය කරනු ඇත.
අධි පරිමා එන්නත් මෝල්ඩින්ගේ ප්රතිලාභ:
- ලාභදායී: ඉහළ පරිමාවකින් යුත් එන්නත් අච්චු ගැසීමේ මූලික ප්රතිලාභවලින් එකක් වන්නේ එය විශාල කොටස් ප්රමාණයක් නිෂ්පාදනය කිරීමට ලාභදායී ක්රමයක් වීමයි. මෙම ක්රියාවලිය බෙහෙවින් ස්වයංක්රීය වන අතර, ශ්රම පිරිවැය අඩු කරන අතර, අච්චු නැවත භාවිතා කළ හැකි අතර, ද්රව්යමය පිරිවැය අඩු කරයි.
- අනුකූලතාව සහ නිරවද්යතාව:ඉන්ජෙක්ෂන් මෝල්ඩින් කොටස් නිෂ්පාදනය කිරීමේදී විශිෂ්ට නිරවද්යතාවයක් සහ අනුකූලතාවයක් සපයයි. මක්නිසාද යත්, අච්චු නිර්මාණය කර ඇත්තේ මූලද්රව්යවල නිශ්චිත පිරිවිතරයන්ට අනුව, සෑම කැබැල්ලක්ම එකම ගුණාත්මක භාවයෙන් හා ප්රමාණයෙන් බව සහතික කරමිනි.
- වේගවත් නිෂ්පාදනය:අධි පරිමා එන්නත් අච්චු ගැසීම ක්ෂණික ක්රියාවලියක් වන අතර විශාල කොටස් ප්රමාණයක් සාපේක්ෂව ඉක්මනින් නිපදවිය හැක. මෙය ඉක්මන් හැරවුම් කාලයන් අවශ්ය වන පාරිභෝගික භාණ්ඩ නිෂ්පාදනය සඳහා වඩාත් සුදුසු වේ.
- පාරිභෝගිකයාගේ: එන්නත් අච්චුව විවිධ ද්රව්ය, වර්ණ සහ මතුපිට නිමාව භාවිතා කරමින් කොටස් අභිරුචිකරණය කිරීමට ඉඩ සලසයි. මෙම නම්යශීලී බව නිසා පාරිභෝගිකයන්ගේ නිශ්චිත අවශ්යතා සහ අවශ්යතා සපුරාලන කොටස් නිෂ්පාදනය කිරීමට හැකි වේ.
පාරිභෝගික භාණ්ඩ කර්මාන්තයේ ඉහළ වෙළුම් එන්නත් අච්චු ගැසීමේ යෙදුම්:
- ඇසුරුම් ද්රව්ය:ප්ලාස්ටික් බෝතල්, භාජන සහ බහාලුම් වැනි ඇසුරුම් ද්රව්ය නිෂ්පාදනය කිරීම සඳහා එන්නත් අච්චුව බහුලව භාවිතා වේ.
- සෙල්ලම් බඩු: එන්නත් අච්චු කිරීම ජනප්රිය සෙල්ලම් බඩු නිෂ්පාදන ක්රමයකි, එය ඉක්මනින් විශාල කොටස් ප්රමාණයක් නිෂ්පාදනය කිරීමට ඉඩ සලසයි.
- කුස්සියට උපකරණ: ඉන්ජෙක්ෂන් මෝල්ඩින් කෝප්ප, පිඟන් සහ උපකරණ වැනි විවිධ කුස්සියට උපකරණ භාණ්ඩ නිෂ්පාදනය කරයි.
- ඉලෙක්ට්රොනික උපකරණ: නිවාස, බොත්තම් සහ ස්විච වැනි විවිධ ඉලෙක්ට්රොනික උපාංග නිෂ්පාදනය කිරීම සඳහා එන්නත් අච්චුව භාවිතා කරයි.
අභ්යවකාශ කර්මාන්තය සඳහා ඉහළ වෙළුම් එන්නත් අච්චුව
ගුවන් යානා වල ආරක්ෂාව සහ කාර්යක්ෂමතාව සහතික කිරීම සඳහා අභ්යවකාශ කර්මාන්තය උසස් තත්ත්වයේ සහ නිරවද්ය කොටස් ඉල්ලා සිටී. ඉහළ ප්රමාණයේ ඉන්ජෙක්ෂන් මෝල්ඩින් අභ්යවකාශ කර්මාන්තය සඳහා අත්යවශ්ය ක්රියාවලියක් බවට පත්ව ඇත්තේ එය ස්ථාවර ගුණාත්මක භාවයෙන් යුත් උසස් තත්ත්වයේ සංරචක විශාල ප්රමාණයක් නිෂ්පාදනය කිරීම සඳහා ලාභදායී විසඳුමක් සපයන බැවිනි. මෙම බ්ලොග් සටහන අභ්යවකාශ කර්මාන්තය සඳහා ඉහළ වෙළුම් එන්නත් අච්චු ගැසීම ගැන සාකච්ඡා කරනු ඇත.
අභ්යවකාශ කර්මාන්තය සඳහා ඉහළ වෙළුම් එන්නත් මෝල්ඩින්ගේ ප්රතිලාභ:
අභ්යවකාශ කර්මාන්තයට ආන්තික උෂ්ණත්ව හා පීඩනවලට ඔරොත්තු දෙන සැහැල්ලු, කල් පවත්නා සංරචක අවශ්ය වේ. අධි පරිමා ඉන්ජෙක්ෂන් මෝල්ඩින් එවැනි මූලද්රව්ය නිෂ්පාදනය සඳහා බොහෝ ප්රතිලාභ ලබා දෙයි, ඒවා අතර:
- පිරිවැය ඵලදායී නිෂ්පාදනය: අධි පරිමා ඉන්ජෙක්ෂන් මෝල්ඩින් මඟින් විශාල කොටස් ප්රමාණයක් ඉක්මනින් නිපදවිය හැකි අතර එමඟින් නිෂ්පාදන පිරිවැය අඩු වේ.
- ස්ථාවර ගුණාත්මකභාවය: ස්වයංක්රීය ක්රියාවලිය මඟින් නිපදවන සෑම කොටසක්ම එකම උසස් තත්ත්වයේ බව සහතික කරයි, එය ගුවන් යානා සංරචකවල ආරක්ෂාව සහ විශ්වසනීයත්වය සඳහා තීරණාත්මක වේ.
- සංකීර්ණ ජ්යාමිතිය: ඉන්ජෙක්ෂන් මෝල්ඩින් ක්රියාවලිය සංකීර්ණ හැඩතල සහ ජ්යාමිතිය නිපදවන අතර ඒවා සාම්ප්රදායික නිෂ්පාදන ක්රම සමඟ සාක්ෂාත් කර ගැනීමට අපහසු විය හැක.
- ද්රව්ය තෝරා ගැනීම: ඉහළ පරිමාවකින් යුත් එන්නත් අච්චුවකට අභ්යවකාශ යෙදීම් සඳහා වඩාත් සුදුසු සංයුක්ත ද ඇතුළුව පුළුල් පරාසයක ද්රව්ය සැකසීමට හැකිය.
- අඩු කළ අපද්රව්ය: ඉන්ජෙක්ෂන් මෝල්ඩින් ක්රියාවලියේ ඉහළ මට්ටමේ ස්වයංක්රීයකරණය සහ නිරවද්යතාවය අඩු ද්රව්යමය අපද්රව්ය හා සීරීම් ඇති කරයි, එමඟින් සැලකිය යුතු පිරිවැය ඉතිරියක් සහ පාරිසරික ප්රතිලාභ ලබා ගත හැකිය.
අභ්යවකාශ කර්මාන්තයේ ඉහළ පරිමා එන්නත් මෝල්ඩින්ගේ යෙදුම්:
ඉහළ පරිමාවකින් යුත් එන්නත් අච්චුව අභ්යවකාශ කර්මාන්තයේ විවිධ සංරචක නිෂ්පාදනය සඳහා බහුලව භාවිතා වේ, ඒවා අතර:
- වායු නල සහ වාතාශ්රය පද්ධති
- අභ්යන්තර සහ බාහිර ගුවන් යානා සංරචක
- වරහන්, ක්ලිප් සහ නිවාස වැනි ව්යුහාත්මක මූලද්රව්ය
- විදුලි සහ රැහැන් කොටස්
- මුද්රා සහ ගෑස්කට්
අධි පරිමා එන්නත් අච්චු ගැසීමේ පොදු දෝෂ
කෙසේ වෙතත්, ඕනෑම නිෂ්පාදන ක්රියාවලියක් මෙන්, ඉන්ජෙක්ෂන් මෝල්ඩින් සමහර විට අවසාන නිෂ්පාදනයේ ගුණාත්මක භාවයට බලපාන දෝෂ ඇති විය හැක. මෙම බ්ලොග් සටහන මගින් අධි වෙළුම් එන්නත් අච්චු ගැසීමේ පොදු දෝෂ කිහිපයක් සහ ඒවා වළක්වා ගත හැකි ආකාරය සාකච්ඡා කරනු ඇත.
- සින්ක් ලකුණු: සින්ක් ලකුණු යනු අච්චු කරන ලද කොටසෙහි මතුපිට ඇති විය හැකි අවපාත හෝ ඉන්ඩෙන්ටේෂන් ය. ඒවා සිසිලනය වන විට ප්ලාස්ටික් ද්රව්ය හැකිලීම නිසා ද්රව්ය අසමාන ලෙස බෙදා හැරීමට හේතු වේ. සින්ක් ලකුණු වැළැක්වීම සඳහා, කොටසෙහි සැලසුම වෙනස් කිරීම සහ සම්පූර්ණ සංරචකය පුරා බිත්ති ඝණත්වය ඒකාකාරව සහතික කිරීම අවශ්ය වේ.
- විකෘති කිරීම:ප්ලාස්ටික් ද්රව්යයේ අසමාන සිසිලනය හේතුවෙන් අච්චු කරන ලද කොටස විරූපණය වීම Warping වේ. එහි ප්රතිඵලයක් වශයෙන් අවශ්ය පිරිවිතරයන් සපුරා නොමැති ඇඹරුණු හෝ නැමුණු කොටසකි. අච්චු උෂ්ණත්වය ස්ථාවර බව සහතික කිරීම සහ සිසිලනය අතරතුර කොටසෙහි ආතතිය අවම කරන නිර්මාණ ලක්ෂණ ඇතුළත් කිරීම මගින් විකෘති වීම වළක්වා ගත හැකිය.
- සැණෙළිය: ෆ්ලෑෂ් යනු අච්චු සන්ධියෙන් නෙරා එන අතිරික්ත ද්රව්ය වන අතර අච්චුව නිවැරදිව පෙළගස්වා නොමැති විට හෝ තද කළ විට සිදුවිය හැක. අච්චුව නිසි ලෙස පෙළගස්වා ඇති බවත්, එන්නත් කිරීමේදී අච්චුව වසා තබා ගැනීමට කලම්ප බලය ප්රමාණවත් බවත් සහතික කර ගැනීමෙන් ෆ්ලෑෂ් වළක්වා ගත හැකිය.
- කෙටි ඡායාරූප: ප්ලාස්ටික් ද්රව්ය සම්පූර්ණ පුස් කුහරය පුරවා නොගන්නා විට, අසම්පූර්ණ කොටසක ප්රතිඵලයක් ලෙස කෙටි වෙඩි තැබීම් සිදු වේ. ප්රමාණවත් එන්නත් පීඩනය, අඩු දියවන උෂ්ණත්වය හෝ අවහිර වූ ගේට්ටුවක් නිසා මෙය සිදුවිය හැක. එන්නත් කිරීමේ පරාමිතීන් ප්රශස්ත කිරීම සහ ගේට්ටුව නිසි ලෙස සැලසුම් කර ස්ථානගත කර ඇති බව සහතික කිරීම මගින් කෙටි වෙඩි තැබීම් වළක්වා ගත හැකිය.
- වෑල්ඩින් රේඛා: වෑල්ඩින් රේඛා දෙකක් හෝ වැඩි ප්රවාහ පෙරමුනු හමු වී ඝණ වීම සිදු වන අතර, එහි ප්රතිඵලයක් ලෙස වාත්තු කරන ලද කොටසෙහි දෘශ්ය රේඛාවක් හෝ මැහුම් ඇතිවේ. ප්ලාස්ටික් ද්රව්ය කුහරය හරහා ඒකාකාරව හා සුමටව ගලා යාම සහතික කිරීම සඳහා අච්චු සැලසුම් සහ එන්නත් පරාමිතීන් ප්රශස්ත කිරීම මගින් වෑල්ඩින් රේඛා වළක්වා ගත හැකිය.
අධි පරිමා ඉන්ජෙක්ෂන් මෝල්ඩින් සඳහා දෝශ නිරාකරණ ඉඟි
අධි පරිමා ඉන්ජෙක්ෂන් මෝල්ඩින් යනු සංකීර්ණ ක්රියාවලියක් වන අතර අවසාන නිෂ්පාදනය ඉහළම ගුණාත්මක බව සහතික කිරීම සඳහා සවිස්තරාත්මකව අවධානය යොමු කිරීම සහ ප්රවේශමෙන් නිරීක්ෂණය කිරීම අවශ්ය වේ. ඉන්ජෙක්ෂන් මෝල්ඩින් ක්රියාවලියේදී පොදු ගැටළු ගණනාවක් මතු විය හැකි අතර, අවසාන නිෂ්පාදනයේ දෝෂ ඇති විය හැක. මෙම පළ කිරීම ඉහළ පරිමාවකින් යුත් එන්නත් අච්චුව සඳහා වඩාත් පොදු දෝශ නිරාකරණ ඉඟි කිහිපයක් ගවේෂණය කරනු ඇත.
- ඉන්ජෙක්ෂන් මෝල්ඩින් යන්ත්ර සැකසුම් පරීක්ෂා කරන්න: ඉහළ පරිමාවකින් යුත් ඉන්ජෙක්ෂන් මෝල්ඩින් දෝශ නිරාකරණය කිරීමේදී පරීක්ෂා කළ යුතු පළමු දෙය නම් ඉන්ජෙක්ෂන් මෝල්ඩින් යන්ත්රයේ සැකසුම් ය. භාවිතා කරන නිශ්චිත ද්රව්ය සඳහා උෂ්ණත්වය, පීඩනය සහ චක්ර කාලය සියල්ල නිවැරදිව සකසා ඇති බවට සහතික වන්න.
- ද්රව්ය ප්රවාහ ගැටළු සඳහා පරීක්ෂා කරන්න: ද්රව්ය ප්රවාහ ගැටළු ඉහළ පරිමාවකින් යුත් එන්නත් අච්චු ගැසීමේ තවත් පොදු ගැටළුවකි. යන්ත්රයේ වැරදි සැකසුම් හෝ ඉන්ජෙක්ෂන් මෝල්ඩින් යන්ත්රයේ අවහිරතා ඇතුළු සාධක කිහිපයක් මෙයට හේතු විය හැක. උපාංගය හරහා ද්රව්යය සුමටව ගලා යන බවත්, ඉන්ජෙක්ෂන් මෝල්ඩින් යන්ත්රයේ කිසිදු අවහිරයක් නොමැති බවත් සහතික කර ගන්න.
- විකෘති වීම සහ හැකිලීම සඳහා පරීක්ෂා කරන්න: ඉහළ පරිමාවකින් යුත් එන්නත් අච්චු ගැසීමේදී විකෘති වීම සහ හැකිලීම පොදු ගැටළු වේ. මෙම ගැටළු බොහෝ විට සිදුවන්නේ ද්රව්යයේ අසමාන සිසිලනය නිසා වන අතර එමඟින් අවසාන නිෂ්පාදනයේ විකෘති වීමට හෝ හැකිලීමට හේතු විය හැක. භාවිතා කරන නිශ්චිත ද්රව්ය සඳහා සිසිලන කාලය නිවැරදිව සකසා ඇති අතර පද්ධතිය නිසි ලෙස ක්රියාත්මක වන බවට සහතික වන්න.
- ගුවන් උගුල් සඳහා පරීක්ෂා කරන්න: ඉහළ පරිමාවකින් යුත් එන්නත් අච්චු ගැසීමේදී වායු උගුල් තවත් පොදු ගැටළුවකි. අවසාන නිෂ්පාදනයේ හිස් හෝ බුබුලු ඇති කළ හැකි පුස් කුහරය තුළ වාතය සිර වූ විට මෙය සිදු වේ. වායු උගුල් ඇතිවීම වැළැක්වීම සඳහා අච්චුව ප්රමාණවත් ලෙස වාතාශ්රය ඇති බවට වග බලා ගන්න.
- ක්රියාවලිය නිරීක්ෂණය කරන්න: අවසාන වශයෙන්, ඕනෑම ගැටළුවක් ඉක්මනින් හසු කර ගැනීම සහ ඉක්මනින් විසඳා ගැනීම සහතික කිරීම සඳහා එන්නත් අච්චු සැකසීමේ ක්රියාවලිය සමීපව නිරීක්ෂණය කිරීම ඉතා වැදගත් වේ. යන්ත්ර සැකසුම්, ද්රව්ය ප්රවාහය සහ සිසිලන ක්රියාවලිය නිරීක්ෂණය කිරීමෙන් මෙය කළ හැකිය. ක්රියාවලිය සමීපව නිරීක්ෂණය කිරීමෙන්, අවසාන නිෂ්පාදනයේ දෝෂ ඇතිවීමට පෙර ඕනෑම ගැටළුවක් හඳුනාගෙන ඒවා විසඳා ගත හැකිය.
ඉන්ජෙක්ෂන් මෝල්ඩින් යන්ත්ර සඳහා නඩත්තු අවශ්යතා
ඉන්ජෙක්ෂන් මෝල්ඩින් යන්ත්ර යනු නිෂ්පාදන කර්මාන්තයේ අත්යවශ්ය උපකරණ වේ. ඒවා ප්ලාස්ටික් කොටස්වල සිට ලෝහ සංරචක දක්වා විවිධ නිෂ්පාදන නිෂ්පාදනය කිරීමට යොදා ගනී. කෙසේ වෙතත්, වෙනත් ඕනෑම යන්ත්රයක් මෙන්, ඉන්ජෙක්ෂන් මෝල්ඩින් යන්ත්ර සඳහා ප්රශස්ත ක්රියාකාරිත්වය සහතික කිරීම සහ මිල අධික බිඳවැටීම් වැළැක්වීම සඳහා නිතිපතා නඩත්තු කිරීම අවශ්ය වේ. මෙම සටහන එන්නත් අච්චු යන්ත්ර සඳහා නඩත්තු අවශ්යතා කිහිපයක් ගවේෂණය කරනු ඇත.
- ලිහිසි තෙල්: ඉන්ජෙක්ෂන් මෝල්ඩින් මැෂින් නඩත්තු කිරීමේදී නිසි ලිහිසි කිරීම අත්යවශ්ය අංගයකි. යන්ත්රයේ චලනය වන ඉන්ජෙක්ෂන් සහ ක්ලැම්පින් ඒකක වැනි කොටස් ඝර්ෂණය සහ ඇඳීම වැළැක්වීම සඳහා නිතිපතා ලිහිසි කළ යුතුය. නිවැරදි ලිහිසි තෙල් වර්ගය භාවිතා කිරීම සහ ලිහිසි කිරීමේ කාල පරතරයන් සඳහා නිෂ්පාදකයාගේ නිර්දේශ අනුගමනය කිරීම අත්යවශ්ය වේ.
- පිරිසිදු කිරීම: ඉන්ජෙක්ෂන් මෝල්ඩින් යන්ත්රය නඩත්තු කිරීමේ තවත් අත්යවශ්ය අංගයක් වන්නේ නිතිපතා පිරිසිදු කිරීමයි. යන්ත්රය එහි සංරචක මත එකතු විය හැකි දූවිලි, සුන්බුන් හෝ ප්ලාස්ටික් අපද්රව්ය ඉවත් කිරීම සඳහා නිතිපතා පිරිසිදු කළ යුතුය. මෙය යන්ත්රයේ තුණ්ඩ සහ ෆිල්ටර අවහිර වීම වැලැක්වීමට උපකාරී වන අතර එමඟින් ක්රියාකාරීත්වයේ ගැටළු හෝ එන්ජිමට හානි සිදු විය හැක.
- පරීක්ෂා: යන්ත්රය හොඳ තත්ත්වයේ පවතින බව සහතික කිරීම සඳහා නිතිපතා පරීක්ෂා කිරීම් ද අවශ්ය වේ. ඉරිතැලීම් හෝ කැඩුණු කොටස් වැනි ඇඳුම් ඇඳීමේ සලකුණු තිබේදැයි පරීක්ෂා කිරීම ඇගයීමට ඇතුළත් විය යුතුය. සංවේදක සහ ස්විච වැනි විද්යුත් සංරචක නිවැරදිව ක්රියා කිරීම සහතික කිරීම සඳහා නිතිපතා පරීක්ෂා කළ යුතුය.
- ක්රමාංකනය: ඉන්ජෙක්ෂන් මෝල්ඩින් යන්ත්ර නිවැරදි පරාමිතීන් තුළ ක්රියාත්මක වන බව සහතික කිරීම සඳහා ක්රමාංකනය ද අවශ්ය වේ. යන්ත්රයේ උෂ්ණත්වය, පීඩනය සහ වේග සැකසුම් නිෂ්පාදකයාගේ පිරිවිතරයන් තුළ ඒවා තිබේ දැයි පරීක්ෂා කිරීම මෙයට ඇතුළත් වේ. උපාංගය එහි ප්රශස්ත මට්ටමේ ක්රියාත්මක වන බව සහතික කිරීම සඳහා ක්රමාංකනය නිතිපතා සිදු කළ යුතුය.
- දිරාපත් වූ කොටස් ආදේශ කිරීම: අවසාන වශයෙන්, හැකි ඉක්මනින් අඳින ලද හෝ හානි වූ කොටස් ප්රතිස්ථාපනය කිරීම අත්යවශ්ය වේ. මෙමගින් යන්ත්රයට තවදුරටත් හානි වීම වැලැක්වීමට සහ මිල අධික බිඳවැටීම් වල අවදානම අවම කර ගත හැක. ප්රතිස්ථාපන කොටස් මුල් කොටස් වලට සමාන ගුණාත්මක භාවයෙන් යුක්ත විය යුතු අතර සුදුසුකම් ලත් කාර්මිකයින් විසින් ස්ථාපනය කළ යුතුය.
තිරසාර බව සහ අධි පරිමා එන්නත් අච්චු ගැසීම
මෑත වසරවලදී නිෂ්පාදන කර්මාන්තයේ තිරසාරභාවය වඩ වඩාත් වැදගත් කරුණක් බවට පත්ව ඇත. කාර්මික ක්රියාවලීන්ගේ පාරිසරික බලපෑම පිළිබඳව ලෝකය වඩාත් දැනුවත් වන විට, සමාගම් ඵලදායිතාව සහ ලාභදායීතාවය පවත්වා ගනිමින් ඔවුන්ගේ පාරිසරික පියසටහන අඩු කිරීමට ක්රම සොයමින් සිටී. අධි පරිමා ඉන්ජෙක්ෂන් මෝල්ඩින් යනු තිරසාර බව සැලකිය යුතු බලපෑමක් ඇති කළ හැකි එක් අංශයකි.
ඉහළ පරිමාවකින් යුත් එන්නත් අච්චුවකට තිරසාරත්වය ඇතුළත් කළ හැකි ක්රම කිහිපයක් තිබේ:
- ද්රව්ය තෝරාගැනීම:ඉන්ජෙක්ෂන් මෝල්ඩින්වල තිරසාරත්වය ලබා ගැනීම සඳහා සුදුසු ද්රව්ය තෝරාගැනීම අත්යවශ්ය වේ. බොහෝ විකල්ප සඳහා ජෛව ප්ලාස්ටික්, ප්රතිචක්රීකරණය කරන ලද ප්ලාස්ටික් සහ ජෛව පාදක ද්රව්ය ඇතුළත් වේ. පරිසර හිතකාමී සහ අඩු කාබන් පියසටහනක් ඇති ද්රව්ය තෝරාගැනීමෙන්, නිෂ්පාදකයින්ට පරිසරයට ඔවුන්ගේ බලපෑම සැලකිය යුතු ලෙස අඩු කළ හැකිය.
- බලශක්ති කාර්යක්ෂමතාව: අධි පරිමා ඉන්ජෙක්ෂන් මෝල්ඩින් ක්රියාත්මක වීමට සැලකිය යුතු ශක්තියක් අවශ්ය වේ. බලශක්ති-කාර්යක්ෂම ක්රියාවලීන් සහ උපකරණ ක්රියාත්මක කිරීම මගින් නිෂ්පාදකයින්ට බලශක්ති පරිභෝජනය අඩු කර කාබන් විමෝචනය අඩු කළ හැකිය. බලශක්ති කාර්යක්ෂම යන්ත්ර භාවිතා කිරීම, නිෂ්පාදන ක්රියාවලීන් ප්රශස්ත කිරීම සහ පුනර්ජනනීය බලශක්ති ප්රභවයන් සඳහා ආයෝජනය කිරීමෙන් මෙය සාක්ෂාත් කරගත හැකිය.
- අපද්රව්ය අඩු කිරීම: එන්නත් අච්චු ගැසීම සැලකිය යුතු අපද්රව්ය, විශේෂයෙන් අතිරික්ත ප්ලාස්ටික් ජනනය කළ හැකිය. අපද්රව්ය අඩු කිරීමේ ක්රමෝපායන් ක්රියාවට නැංවීමෙන්, නිෂ්පාදකයින්ට ජනනය වන අපද්රව්ය ප්රමාණය අවම කර ඔවුන්ගේ තිරසාරභාවය වැඩි දියුණු කළ හැකිය. මෙය ප්රතිචක්රීකරණය කිරීම, ද්රව්ය නැවත භාවිතා කිරීම සහ අපද්රව්ය අවම කිරීම සඳහා නිෂ්පාදන ක්රියාවලිය ප්රශස්ත කිරීම තුළින් ලබා ගත හැක.
- ජීවන චක්ර විශ්ලේෂණය: ජීවන චක්ර විශ්ලේෂණයක් සිදු කිරීම නිෂ්පාදකයින්ට ඔවුන්ගේ මුළු ජීවන චක්රය පුරාම තම නිෂ්පාදනවල පාරිසරික බලපෑම අවබෝධ කර ගැනීමට උපකාරී වේ. මෙම විශ්ලේෂණය මගින් තිරසාරත්වය වැඩිදියුණු කළ හැකි ක්ෂේත්ර හඳුනා ගැනීමට සහ වඩාත් පරිසර හිතකාමී නිෂ්පාදන නිර්මාණය කිරීමට තීරණ ගැනීමට මඟ පෙන්විය හැක.
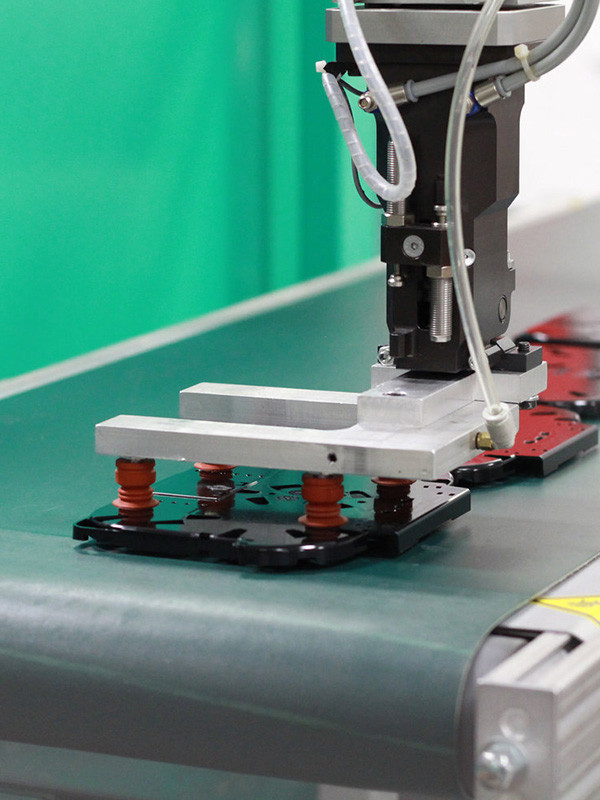
ප්රධාන කරුණු:
- ද්රව්ය තෝරාගැනීම ඉන්ජෙක්ෂන් මෝල්ඩින් හි තිරසාර බව සාක්ෂාත් කර ගැනීම සඳහා තීරණාත්මක කාර්යභාරයක් ඉටු කරයි.
- බලශක්ති කාර්යක්ෂම ක්රියාවලීන් සහ උපකරණ බලශක්ති පරිභෝජනය අඩු කර කාබන් විමෝචනය අඩු කළ හැකිය.
- ද්රව්ය ප්රතිචක්රීකරණය කිරීම සහ නැවත භාවිතා කිරීම වැනි අපද්රව්ය අඩු කිරීමේ උපාය මාර්ග මගින් ජනනය වන අපද්රව්ය ප්රමාණය අවම කර ගත හැක.
- ජීවන චක්ර විශ්ලේෂණය මඟින් තිරසාරත්වය වැඩිදියුණු කළ හැකි ක්ෂේත්ර හඳුනා ගැනීමට උපකාරී වේ.
- ඉහළ ප්රමාණයේ එන්නත් අච්චු ගැසීම සඳහා තිරසාරභාවය ඇතුළත් කිරීම පිරිවැය අඩු කිරීමෙන් සහ පාරිසරික දැනුවත් පාරිභෝගිකයින් වෙත ආයාචනා කිරීමෙන් නිෂ්පාදකයින්ට ප්රතිලාභ ලබා ගත හැකිය.
- අධි-පරිමාණ එන්නත් මෝල්ඩින් අනාගතය
අධි පරිමා එන්නත් අච්චුව දශක ගණනාවක් තිස්සේ බොහෝ කර්මාන්ත සඳහා අත්යවශ්ය නිෂ්පාදන ක්රියාවලියක් වී ඇති අතර එය පුළුල් පරාසයක ප්ලාස්ටික් නිෂ්පාදන නිෂ්පාදනය කිරීමේදී අත්යවශ්ය කාර්යභාරයක් ඉටු කරයි. තාක්ෂණය දියුණු වන විට සහ පාරිභෝගික ඉල්ලුම වඩාත් තිරසාර සහ අභිරුචිකරණය කළ හැකි නිෂ්පාදන වෙත මාරු වන විට, ඉහළ පරිමාවකින් යුත් එන්නත් අච්චුවෙහි අනාගතය දීප්තිමත් බව පෙනේ. මෙම කර්මාන්තයේ අවසානය හැඩගස්වන ප්රවණතා සහ නවෝත්පාදනයන් කිහිපයක් මෙන්න.
- තිරසාර බව: පරිසර හිතකාමී නිෂ්පාදන සඳහා පාරිභෝගික ඉල්ලුම වැඩි වීමත් සමඟ, ඉහළ පරිමා එන්නත් අච්චු ගැසීමේදී තිරසාරභාවය තීරණාත්මක වී ඇත. නිෂ්පාදකයින් ජෛව ප්ලාස්ටික් සහ ජෛව පාදක ද්රව්ය වැනි නව ද්රව්ය ගවේෂණය කරන අතර ඔවුන්ගේ නිෂ්පාදනවල පාරිසරික බලපෑම අවම කිරීම සඳහා අපද්රව්ය අඩු කිරීමේ උපාය මාර්ග ක්රියාත්මක කරයි.
- පාරිභෝගිකයාගේ: පාරිභෝගිකයින් ඔවුන්ගේ අද්විතීය අවශ්යතා සහ මනාපයන් සපුරාලන නිෂ්පාදන සොයමින් සිටින අතර, මෙම ඉල්ලුම සපුරාලීම සඳහා ඉහළ පරිමාවකින් යුත් එන්නත් අච්චුව හොඳින් ගැලපේ. ත්රිමාණ මුද්රණය වැනි තාක්ෂණයේ දියුණුව, විශාල පරිමාවකින් අභිරුචි කළ කොටස් සහ නිෂ්පාදන නිෂ්පාදනය කිරීම පහසු සහ ලාභදායී කරයි.
- ස්වයංක්රීයකරණය: නිෂ්පාදන කර්මාන්තයේ ස්වයංක්රීයකරණය වැඩි වැඩියෙන් ප්රචලිත වෙමින් පවතින අතර ඉහළ පරිමාවකින් යුත් එන්නත් අච්චුව ව්යතිරේකයක් නොවේ. රොබෝ ආයුධ සහ පරිගණක ආශ්රිත නිර්මාණය වැනි ස්වයංක්රීය ක්රියාවලීන් නිෂ්පාදන කාර්යක්ෂමතාව වැඩිදියුණු කිරීමට සහ පිරිවැය අඩු කිරීමට හැකිය.
- කර්මාන්තය 4.0: සිව්වන කාර්මික විප්ලවය, Industry 4.0, කෘතිම බුද්ධිය, අන්තර්ජාලයේ දේවල් (IoT) සහ විශාල දත්ත විශ්ලේෂණ වැනි උසස් තාක්ෂණයන් ඒකාබද්ධ කිරීම මගින් නිෂ්පාදන කර්මාන්තය පරිවර්තනය කරයි. මෙම තාක්ෂණයන් නිෂ්පාදකයින්ට නිෂ්පාදන ක්රියාවලීන් ප්රශස්ත කිරීමට සහ නිෂ්පාදනයේ ගුණාත්මකභාවය වැඩි දියුණු කිරීමට පහසු කරයි.
- වෛද්ය කර්මාන්තය:අධි පරිමා එන්නත් අච්චුව එහි නිරවද්යතාවය සහ අනුකූලතාවය හේතුවෙන් වෛද්ය උපකරණ සහ උපකරණ නිෂ්පාදනය කිරීම සඳහා හොඳින් ගැලපේ. වෛද්ය නිෂ්පාදන සඳහා ඇති ඉල්ලුම වර්ධනය වනු ඇතැයි අපේක්ෂා කරන අතර, මෙය එන්නත් අච්චු කර්මාන්තය සඳහා වැදගත් ක්ෂේත්රයක් බවට පත් කරයි.
- විදුලි වාහන:විද්යුත් මෝටර් රථ දෙසට මාරුවීම අධි පරිමා ඉන්ජෙක්ෂන් මෝල්ඩින් කර්මාන්තය සඳහා නව අවස්ථා නිර්මාණය කරයි. බැටරි නිවාස සහ විදුලි සම්බන්ධක වැනි ප්ලාස්ටික් උපාංග විදුලි මෝටර් රථ සඳහා අත්යවශ්ය වන අතර විද්යුත් වාහන වඩාත් ප්රචලිත වන විට මෙම උපාංග සඳහා ඇති ඉල්ලුම වර්ධනය වනු ඇතැයි අපේක්ෂා කෙරේ.
නිගමනය:
ප්ලාස්ටික් කොටස් විශාල ප්රමාණයක් නිෂ්පාදනය කිරීම සඳහා අධි පරිමා එන්නත් අච්චුව අත්යවශ්ය වේ. වාසි, අවාසි, ද්රව්ය, යන්ත්ර, ක්රම, සැලසුම් සලකා බැලීම්, තත්ත්ව පාලන ක්රම, සහ ඉහළ ප්රමාණයේ එන්නත් මෝල්ඩින්ගේ යෙදුම් අවබෝධ කර ගැනීමෙන්, ව්යාපාරවලට තම නිෂ්පාදන ක්රියාවලීන් ප්රශස්ත කිරීමට, පිරිවැය අඩු කිරීමට සහ ඔවුන්ගේ නිෂ්පාදනවල ගුණාත්මකභාවය වැඩි දියුණු කළ හැකිය. ඔබ වෛද්ය, මෝටර් රථ, පාරිභෝගික භාණ්ඩ, හෝ අභ්යවකාශ කර්මාන්තයේ යෙදී සිටියත්, ඉහළ පරිමාවකින් යුත් එන්නත් අච්චු ගැසීම අඩු මිලකට ස්ථාවර, උසස් තත්ත්වයේ කොටස් සැපයීමෙන් ඔබේ ව්යාපාරයට ප්රතිලාභ ලැබිය හැකිය.