ඔටෝමෝටිව් ප්ලාස්ටික් සංරචක එන්නත් අච්චු කිරීම
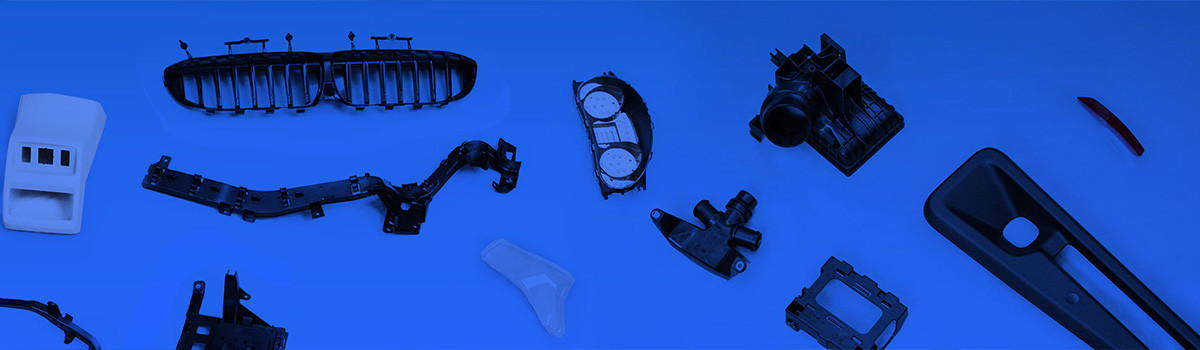
අද වාහන ප්ලාස්ටික් සංරචක
ඉහළ මෝටර් රථ කාර්ය සාධනය ඒ සියල්ල හසුරුවන කොටස් ඉල්ලා සිටී. ප්ලාස්ටික් එන්ජිමේ සිට චැසිය දක්වා සිදු කරයි; ඇතුළත සිට පිටත දක්වා. වර්තමාන වාහන ප්ලාස්ටික් නව සැහැල්ලු වාහනයක පරිමාවෙන් 50% ක් පමණ වන නමුත් එහි බරෙන් 10% ට වඩා අඩුය.
ආරක්ෂාව
වර්තමාන ද්රව්යවල ආරක්ෂිත දියුණුව ගණන් කළ නොහැකි ජීවිත බේරා ගනී. එයාර් බෑග්, වින්ඩ්ෂීල්ඩ්, සන්රූෆ් සහ බලශක්ති අවශෝෂණය කරන නවෝත්පාදන වාහන මාරක අඩු කරයි. ප්ලාස්ටික් ඉදිරිපස මොඩියුල, මොඩියුලර් ආසන සහ බලශක්ති අවශෝෂණ බම්පර් සෑම වසරකම ජීවිත බේරා ගැනීමට උපකාරී වේ.
ප්ලාස්ටික් සංයුක්ත ව්යුහයන් ආරක්ෂිත ලක්ෂණ ආරක්ෂා කරන අතරම සැහැල්ලු වාහනවලට උපකාර කළ හැකිය. වාහනයක් කඩා වැටෙන විට, ඉංජිනේරුවන්ට අවශ්ය වන්නේ ව්යුහය පුරෝකථනය කළ හැකි ආකාරයට තලා දැමීමයි. මෝටර් රථ ද්රව්ය මිනිසුන්ට "බලපෑමේ ශක්තිය" මාරු නොකළ යුතුය, අවශෝෂණය කළ යුතුය. කර්මාන්තය මෙය හඳුන්වන්නේ "පාලිත ක්රෂ්" ලෙසිනි.
තන්තු ශක්තිමත් කරන ලද පොලිමර් සංයෝග වානේ තලා දැමීමේ ශක්තිය මෙන් හතර ගුණයක් අවශෝෂණය කරයි. B-කණුව යනු වාහනයක වහලය එහි බඳට සම්බන්ධ කරන ආධාරක කණුවයි. එය ඉදිරිපස දොරේ පිටුපස ඇති අතර ගැටුමකදී ආක්රමණයට ප්රතිරෝධයේ ප්රධාන මූලාශ්රය සපයයි.
ජාතික මහාමාර්ග රථවාහන ආරක්ෂණ පරිපාලනය විසින් B-කුළුණු පිළිබඳ අධ්යයනයක් සඳහා මෑතකදී අරමුදල් සපයන ලදී. මෙම අධ්යයනයෙන් විශේෂයෙන්ම සංයුක්ත තීව්ර කාබන් ෆයිබර් තාප ප්ලාස්ටික් B-ස්ථම්භ සැලසුමක් දෙස බලන ලදී. ඉලක්කය වූයේ ලෝහමය පදනමට සාපේක්ෂව සැලසුමේ බර ඉතුරුම් සහ වාහන කඩා වැටීමේ ආරක්ෂාව තීරණය කිරීමයි. B-ස්ථම්භය සියයට 60 ක බර ඉතුරුම් පෙන්නුම් කර ඇති අතර, තෘප්තිමත් අතුරු-බලපෑම් බිඳ වැටීම් අවශ්යතා. ගණනය කිරීමේ මෙවලම් ගතික බලපෑම සහ තලන ප්රතිචාර B-කුළුණු ආදර්ශනය කළේය.
ප්ලාස්ටික් පදිකයින්ගේ ජීවිත බේරා ගැනීමට ද උපකාරී වේ. පොලිකාබනේට් මිශ්ර බම්පර් ගැටීම් වලදී මගීන් ආරක්ෂා කිරීමට උපකාරී වේ. ෆෝඩ් වාහනවල වැඩි පදික ආරක්ෂාවක් සඳහා ප්ලාස්ටික් ද වේගවත් යෙදවීම සක්රීය කරයි. නම්යශීලී පදික-ආරක්ෂාව කඩා වැටීමේ සෘජු සවිකර ඇති සංවේදක වරහන එන්නත් කිරීම ප්ලාස්ටික් වලින් සාදා ඇත. අපගේ "Crumple Zone Blog" සහ BMW i3 කාබන් ෆයිබර් චැසි ආරක්ෂණ සංරචක පිළිබඳ අපගේ සංචාරයේ තවත් බලන්න.
Windshields, Windows & Sunroofs
උතුරු ඇමරිකානු සුළං ආවරණ බහු ස්ථර ඒකකයක් ලෙස පැමිණේ. තුනී වීදුරු තහඩු දෙකක් අතර තුනී ප්ලාස්ටික් තට්ටුවක් පින්තාරු කරන්න. මෙම සංයෝජනය මෘදු වීදුරු වලට වඩා තුනී, සැහැල්ලු සහ ශක්තිමත් විය හැකිය. කඳුළු-ප්රතිරෝධී ප්ලාස්ටික් තට්ටුව නිවැසියන් පිටවීම වැළැක්වීමට උපකාරී වේ. ඇත්ත වශයෙන්ම, NHTSA ඇස්තමේන්තු කරන්නේ මෙම ස්ථර වසරකට මරණ 300 කට වඩා වැලැක්වීමට උපකාරී වේ.
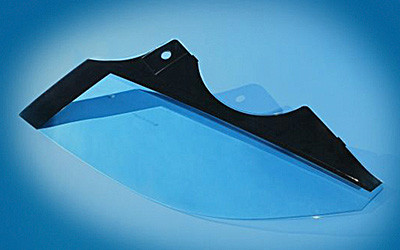
වහලවල් සඳහා සැහැල්ලු ප්ලාස්ටික් සංරචක ගුරුත්වාකර්ෂණ කේන්ද්රය අඩු කරන අතර ගැඹුරු වංගු කිරීමේ අනතුරු උපාමාරු වලදී ඔත්තුව ඉහළ යාමේ සම්භාවිතාව අඩු කරයි. පැහැදිලි විකෘති නොවන පොලිකාබනේට් දැන් පාරජම්බුල කිරණවලට ඔරොත්තු දෙන අතර බර සැලකිය යුතු ලෙස අඩු කළ හැකිය. සම්පූර්ණ වහළ එකලස්කිරීම් බහු අවයවික විය හැකිය.
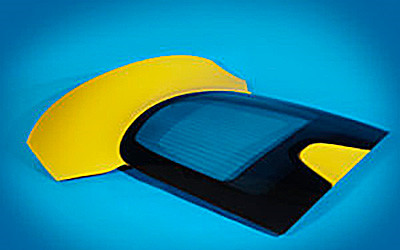
DJmolding's Automotive Plastic Components Injection මෝල්ඩින්
Djmolding යනු ISO/TS 16949:2009 සහිත වාහන ප්ලාස්ටික් ඉන්ජෙක්ෂන් මෝල්ඩින් සමාගම් වේ, අපි අභිරුචි ප්ලාස්ටික් එන්නත් අච්චුව, සැලසුම් කරන්නා සහ ඉංජිනේරු ශ්රේණියේ දුම්මල, වීදුරු, ටංස්ටන්, කාබන් සහ යකඩ පිරවූ ද්රව්ය භාවිතා කරමින් මෝටර් රථ, අභ්යවකාශ, ඉලෙක්ට්රොනික, නාවික, වෛද්ය සහ ටෙලිකොම් යෙදුම්.
මෝටර් රථ නිෂ්පාදනය සඳහා භාවිතා කරන ද්රව්යවලින් සියයට විස්සක් විවිධ ලක්ෂණ සහිත ප්ලාස්ටික් කොටස් වලින් සමන්විත වේ. DJmolding හි අපි මෝටර් රථ සමාගම්වලට, වාහනවල ඇතුළත සහ පිටත මෙන්ම වාහන උපකරණ සඳහා ප්ලාස්ටික් කොටස් සම්පූර්ණ පරාසයක් සපයන්නෙමු. ප්ලාස්ටික් කොටස් එන්නත් කිරීම සඳහා නවීන තාක්ෂණය සමඟ සහ වානේ වෙනුවට වෙළඳ නාම භාවිතා කරන කොටස් නිෂ්පාදනය සඳහා ඉංජිනේරු ද්රව්ය සමඟ අපි වැඩ කරන්නෙමු, ඒවා වඩාත් ප්රතිරෝධී, වඩා සැහැල්ලු සහ ප්රතිචක්රීකරණය කිරීමට පහසුය.
ප්ලාස්ටික් ඉන්ජෙක්ෂන් මෝල්ඩින් නිෂ්පාදකයෙකු සහ සැපයුම්කරුවෙකු ලෙස ඩීජේමෝල්ඩින්, තාප ප්ලාස්ටික් ඉන්ජෙක්ෂන් මෝල්ඩින් තාක්ෂණය පිළිබඳ විශේෂීකරණය කරයි. අපගේ දැනුමට ගෑස් එන්නත් අච්චු තාක්ෂණය, ඉහළ ග්ලෝස් සහ ඊ-මෝල්ඩින් ද ඇතුළත් වේ. මෝටර් රථ කර්මාන්තය සඳහා අපගේ ඉන්ජෙක්ෂන් අච්චු කරන ලද බාහිර සහ අභ්යන්තර මෝටර් රථ සංරචක ප්රධාන වශයෙන් පහත සඳහන් ද්රව්ය වලින් නිර්මාණය කර ඇත: - පොලි ස්ටයිරීන් (PS), - පොලිප්රොපිලීන් (PP), - ABS, - PC, - PC / ABS, - PC / PMMA.
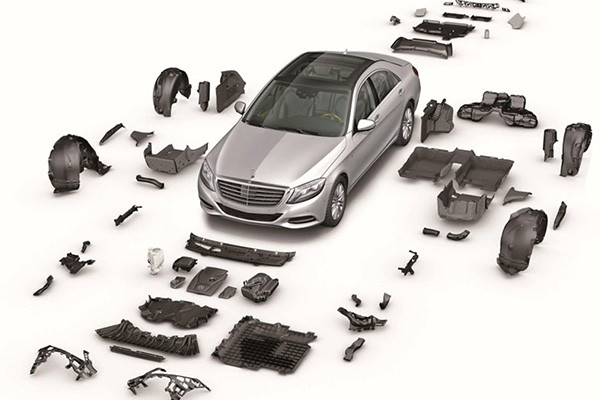
අභ්යන්තර එන්නත් අච්චු කරන ලද මෝටර් රථ සංරචක
ගතික මෝටර් රථ කර්මාන්තයට අපි විවිධ එන්නත් අච්චු කරන ලද අභ්යන්තර සංරචක නිෂ්පාදනයේ විශ්වාසදායක හවුල්කරුවෙකි. අපගේ ISO IATF පිළිගත් කර්මාන්තශාලා තුළ අපි ප්රමුඛ පෙළේ මෝටර් රථ නිෂ්පාදකයින් සඳහා අභ්යන්තර සංරචක ව්යාපෘති සිදු කරන්නෙමු. අපි පළපුරුදු OEM, Tier 1 මෝටර් රථ සැපයුම්කරු සහ මෝටර් රථ අභ්යන්තර සහ බාහිර සැරසිලි කොටස් නිෂ්පාදකයා වේ. අපගේ අභ්යන්තර ඉන්ජෙක්ෂන් මෝල්ඩින් සංරචකවල නිෂ්පාදන කළඹට ප්ලාස්ටික් වාහන අමතර කොටස් ඇතුළත් වේ: උපකරණ පුවරු මූලද්රව්ය (උදා: අත්වැසුම් මැදිරිය, දොර සහ ජනෙල් කුළුණු), සුක්කානම් තීරු සැරසිලි, දොර හැන්ඩ්ල්, වායු විවරය, මධ්ය කොන්සෝල, වහල මොඩියුල යනාදිය.
බාහිර ඉන්ජෙක්ෂන් මෝල්ඩ් කාර් සංරචක
ඉන්ජෙක්ෂන් මෝල්ඩින් යනු පුළුල් පරාසයක බාහිර මෝටර් රථ සංරචක නිෂ්පාදනය කිරීම සඳහා කදිම තාක්ෂණයකි. අපගේ පළපුරුදු ඉන්ජෙක්ෂන් මෝල්ඩින් වෘත්තිකයන් කණ්ඩායම සියලු තාක්ෂණික අවශ්යතා ඇගයීමට සහ නිර්වචනය කිරීමට මෝටර් රථ OEMs සහ Tier 1 සේවාදායකයින් සමඟ සමීපව ක්රියා කරන අතර එම නිසා නිර්දෝෂී බාහිර වාහන සංරචක නිෂ්පාදනය ප්රශස්ත කරයි. අපි මෝටර් රථ බාහිර කොටස්වල ප්ලාස්ටික් එන්නත් අච්චු නිෂ්පාදකයා වේ උදා: mudguards (fenders), රෝද ආරුක්කු, grilles, සංවේදක රඳවනයන්, බිම රේල් පීලි, කඳ ටිම් ඉදිරිපස සහ පසුපස ආවරණ, බම්පර් සහ බාහිර කාර් දොර ටිම්, දොර පුවරු. මෝටර් රථ සඳහා අපගේ එන්නත් ප්ලාස්ටික් කොටස් ලොව පුරා විවිධ මෝටර් රථ මාදිලිවල දක්නට ලැබේ.
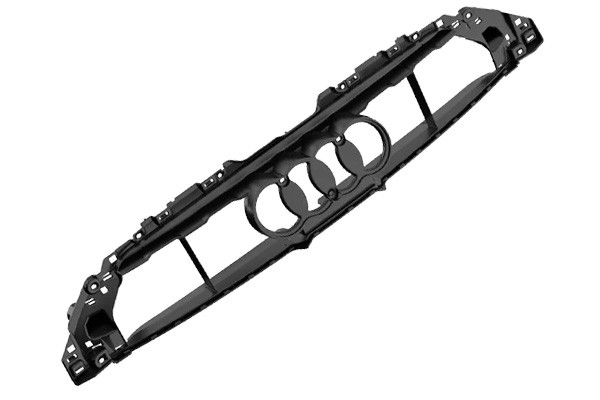
අපගේ ඉලක්කය වන්නේ අපගේ ගනුදෙනුකරුවන්ට උපරිම වටිනාකමක් ලබා දීමයි. ප්ලාස්ටික් කොටස් නිෂ්පාදනයට අමතරව, DJmolding ඉන්ජෙක්ෂන් මෝල්ඩින් සැලසුම් සහ නිෂ්පාදන සේවා සපයයි. අපි අපගේ ගනුදෙනුකරුවන්ට වෙළඳපොළට ලබා දීමට සූදානම් වන ආකාරයෙන් ප්ලාස්ටික් කොටස් ලබා ගැනීමට උපකාර කරමු. අපි සමස්ත ක්රියාවලියම අදහසින් ආවරණය කරන්නෙමු, එන්නත් අච්චු ගැසීම, මෝටර් රථ ප්ලාස්ටික් උපාංග කර්මාන්තය සඳහා නිමි භාණ්ඩ බෙදා හැරීම.
ඔබට පෙනෙන පරිදි, DJmolding සිය ගනුදෙනුකරුවන් තනිවම අත් නොහරියි. සෑම පියවරකදීම, පුළුල් ප්රවේශයක් ලබා දීමෙන් අපගේ ගනුදෙනුකරුවන්ට උපකාර කිරීමට අපි සිටිමු. මුලදී සංකීර්ණ ක්රියාවලියක් ලෙස පෙනෙන දෙය විශිෂ්ට ප්රතිඵල ගෙන දෙන සාර්ථක සහයෝගීතාවයක් බවට අපට පහසුවෙන් හැරවිය හැක.
සැහැල්ලු හා කාර්යක්ෂම ද්රව්ය දැඩි ලෙස අවධාරණය කරමින් මෝටර් රථ කර්මාන්තය වසර ගණනාවක් පුරා කැපී පෙනෙන දියුණුවක් අත්කර ගෙන ඇත. නවීන වාහන නිෂ්පාදනය, කල්පැවැත්ම, සැලසුම් නම්යශීලී බව සහ පිරිවැය-ඵලදායීතාවය ලබා දීම සඳහා ප්ලාස්ටික් සංරචක ඉතා වැදගත් වේ. මෝටර් රථ ප්ලාස්ටික් සංරචක සඳහා විවිධ නිෂ්පාදන ක්රියාවලීන් අතර, ඉන්ජෙක්ෂන් මෝල්ඩින් බහුලව භාවිතා වේ. මෙම බ්ලොග් සටහන මෝටර් රථ ප්ලාස්ටික් සංරචක එන්නත් අච්චු කිරීම, එහි ප්රතිලාභ, යෙදුම් සහ නැගී එන ප්රවණතා ගවේෂණය කරනු ඇත. මෝටර් රථ ප්ලාස්ටික් උපාංග අච්චු ගැසීමේ සිත් ඇදගන්නාසුළු ලෝකය ගවේෂණය කරමු!
මෝටර් රථ කර්මාන්තයේ එන්නත් අච්චුව අවබෝධ කර ගැනීම
මෝටර් රථ කර්මාන්තය උපකරණ පුවරු, බම්පර්, උපකරණ පැනල් යනාදිය ඇතුළු විවිධ සංරචක නිෂ්පාදනය කිරීම සඳහා ඉන්ජෙක්ෂන් මෝල්ඩින් භාවිතා කරයි.
මෝටර් රථ කර්මාන්තයේ ඉන්ජෙක්ෂන් මෝල්ඩින් අවබෝධ කර ගැනීමේදී සලකා බැලිය යුතු ප්රධාන අංග කිහිපයක් මෙන්න:
ඉන්ජෙක්ෂන් මෝල්ඩින් සඳහා භාවිතා කරන ද්රව්ය
එන්නත් අච්චුව පුළුල් පරාසයක තාප ප්ලාස්ටික් සහ තාප සැකසුම් ද්රව්ය භාවිතා කරයි, ඒවා අතර:
- පොලිප්රොපිලීන් (PP)
- පොලිඑතිලීන් (PE)
- පොලිවිවයිල් ක්ලෝරයිඩ් (පීවීසී)
- ඇක්රිලෝනිට්රයිල්-බියුටැඩීන්-ස්ටයිරීන් (ABS)
- පොලිකාබනේට් (PC)
- පොලිමයිඩ් (PA)
- පොලියුරේතන් (PU)
සෑම ද්රව්යයකටම නම්යශීලී බව, ශක්තිය, කල්පැවැත්ම සහ තාපයට හා රසායනික ද්රව්යවලට ප්රතිරෝධය වැනි අද්විතීය ගුණාංග සහ ලක්ෂණ ඇත. ද්රව්ය තෝරා ගැනීම නිෂ්පාදනය කරනු ලබන කොටස හෝ නිෂ්පාදනයේ නිශ්චිත අවශ්යතා මත රඳා පවතී.
මෝටර් රථ කර්මාන්තයේ ඉන්ජෙක්ෂන් මෝල්ඩින් වල වාසි
- ඉහළ නිෂ්පාදන කාර්යක්ෂමතාව: ඉන්ජෙක්ෂන් මෝල්ඩින් මඟින් නිෂ්පාදන කාලය සහ පිරිවැය අඩු කරමින් ඉක්මනින් හා කාර්යක්ෂමව කොටස් විශාල ප්රමාණයක් නිපදවිය හැක.
- නිරවද්යතාවය සහ අනුකූලතාව: එන්නත් අච්චුව කැබලි අතර අවම වෙනස්කම් ඇති නිරවද්ය සහ ස්ථාවර කොටස් නිෂ්පාදනය කරයි.
- සැලසුම් නම්යශීලිත්වය: ඉන්ජෙක්ෂන් මෝල්ඩින් සංකීර්ණ ජ්යාමිතීන් සහ සංකීර්ණ විස්තර කොටස් වලට ඇතුළත් කිරීමට ඉඩ සලසයි, නිශ්චිත ක්රියාකාරී සහ සෞන්දර්යාත්මක අවශ්යතා සපුරාලන කෑලි නිර්මාණය කිරීමට නිර්මාණකරුවන්ට හැකියාව ලබා දේ.
- පිරිවැය-ඵලදායීතාවය: යන්ත්ර කිරීම හෝ වාත්තු කිරීම වැනි අනෙකුත් නිෂ්පාදන ක්රමවලට වඩා අඩු වියදමකින් එන්නත් අච්චුවකින් කොටස් නිෂ්පාදනය කළ හැක.
මෝටර් රථ කර්මාන්තයේ එන්නත් අච්චු ගැසීමේ අභියෝග
- මෙවලම් පිරිවැය: එන්නත් අච්චු ගැසීම සඳහා අච්චු නිර්මාණය කිරීම අවශ්ය වේ, එය සැලසුම් කිරීම සහ නිෂ්පාදනය කිරීම සඳහා මිල අධික විය හැකිය.
- ද්රව්ය තෝරාගැනීම: විවිධ ද්රව්ය විවිධ ගුණ ඇති අතර අමතර සැකසුම් කොන්දේසි අවශ්ය විය හැකි බැවින්, කොටසක් හෝ නිෂ්පාදනයක් සඳහා සුදුසු ද්රව්ය තෝරා ගැනීම අභියෝගාත්මක විය හැක.
- නඩත්තු කිරීම සහ අළුත්වැඩියා කිරීම: ඉන්ජෙක්ෂන් මෝල්ඩින් උපකරණ ප්රශස්ත ක්රියාකාරිත්වය සහතික කිරීම සහ අක්රිය කාලය වැළැක්වීම සඳහා නිතිපතා නඩත්තු කිරීම සහ අලුත්වැඩියා කිරීම අවශ්ය වේ.
- පාරිසරික බලපෑම: එන්නත් අච්චුවකින් ජනනය වන ප්ලාස්ටික් අපද්රව්ය බැහැර කිරීම අහිතකර පාරිසරික ප්රතිවිපාක ඇති කළ හැකිය.
ඔටෝමෝටිව් ප්ලාස්ටික් සංරචක එන්නත් අච්චු ගැසීමේ ප්රතිලාභ
ඔටෝමෝටිව් ප්ලාස්ටික් සංරචක ඉන්ජෙක්ෂන් මෝල්ඩින් යනු අච්චු සහ ප්ලාස්ටික් පෙති භාවිතයෙන් සංකීර්ණ කොටස් නිර්මාණය කිරීම සම්බන්ධ ක්රියාවලියකි. මෙම ක්රමය බොහෝ ප්රතිලාභ නිසා මෝටර් රථ කර්මාන්තයේ බහුලව භාවිතා වේ. මෙම බ්ලොග් සටහන ඉන්ජෙක්ෂන් මෝල්ඩින් ඔටෝමෝටිව් ප්ලාස්ටික් සංරචකවල වාසි ගැන සාකච්ඡා කරනු ඇත.
පිරිවැය-ඵලදායී: වාහන ප්ලාස්ටික් සංරචක එන්නත් අච්චු ගැසීමේ වඩාත්ම වැදගත් ප්රතිලාභයක් වන්නේ එය කොටස් නිෂ්පාදනය කිරීමේ ලාභදායී ක්රමයකි. මෙම ක්රියාවලිය ඉක්මනින් හා කාර්යක්ෂමව විශාල ප්රමාණවලින් සංකීර්ණ කොටස් නිර්මාණය කළ හැකි බැවිනි. මෙය නිෂ්පාදන පිරිවැය අඩු කරන අතර, පිරිවැය සැමවිටම සැලකිලිමත් වන මෝටර් රථ කර්මාන්තය සඳහා කදිම විසඳුමක් බවට පත් කරයි.
සැහැල්ලු: මෝටර් රථ කර්මාන්තයේ ප්ලාස්ටික් ඉන්ජෙක්ෂන් මෝල්ඩින්ගේ තවත් සැලකිය යුතු වාසියක් වන්නේ ප්ලාස්ටික් සංරචක සැහැල්ලු වීමයි. පාරිසරික රෙගුලාසි සහ පාරිභෝගික අපේක්ෂාවන් සපුරාලීම සඳහා මෝටර් රථ නිෂ්පාදකයින්ට තීරණාත්මක සාධකයක් වන වාහනවල ඉන්ධන කාර්යක්ෂමතාව වැඩි දියුණු කරන බැවින් මෙය වැදගත් වේ.
ශක්තිය සහ කල්පැවැත්ම: ඉන්ජෙක්ෂන් මෝල්ඩින් මගින් නිපදවන ප්ලාස්ටික් සංරචක විශිෂ්ට ශක්තියක් සහ කල්පැවැත්මක් ඇත. මක්නිසාද යත්, මෙම ක්රියාවලිය ස්ථාවර බිත්ති ඝණත්වය සහ අවම විකෘති කිරීම් සහිත කොටස් නිර්මාණය කිරීමට ඉඩ සලසයි. එහි ප්රතිඵලයක් ලෙස, ඉන්ජෙක්ෂන් මෝල්ඩින් මගින් නිපදවන ප්ලාස්ටික් උපාංගවලට අධික උෂ්ණත්වය සහ කම්පනය වැනි මෝටර් රථ පරිසරයේ දෘඩතාවන්ට ඔරොත්තු දිය හැකිය.
පාරිභෝගිකයාගේ: එන්නත් අච්චුව විවිධ ප්රමාණවලින් සහ හැඩයෙන් කොටස් නිර්මාණය කිරීමට ඉඩ සලසයි. අභිරුචිකරණය අත්යවශ්ය වන මෝටර් රථ කර්මාන්තය සඳහා මෙය කදිම විසඳුමක් බවට පත් කරයි. ඉන්ජෙක්ෂන් මෝල්ඩින් හරහා, මෝටර් රථ නිෂ්පාදකයින්ට ප්රමාණය, හැඩය සහ වර්ණය වැනි නිශ්චිත අවශ්යතා සපුරාලන කොටස් පහසුවෙන් නිර්මාණය කළ හැකිය.
අඩු කළ අපද්රව්ය: ප්ලාස්ටික් ඉන්ජෙක්ෂන් මෝල්ඩින් සාම්ප්රදායික නිෂ්පාදන ක්රමවලට වඩා අඩු අපද්රව්ය නිපදවයි. ක්රියාවලිය ඉතා කාර්යක්ෂම වන අතර අවම සීරීම් සහිත කොටස් සෑදිය හැක. එහි ප්රතිඵලයක් වශයෙන්, මෝටර් රථ කර්මාන්තයට ඉන්ජෙක්ෂන් මෝල්ඩින් භාවිතයෙන් ප්ලාස්ටික් සංරචක නිෂ්පාදනය කිරීමෙන් එහි කාබන් පියසටහන අඩු කළ හැකිය.
වේගවත් නිෂ්පාදනය: ඉන්ජෙක්ෂන් මෝල්ඩින් යනු ප්ලාස්ටික් සංරචක නිෂ්පාදනය කිරීමේ ඉක්මන් හා කාර්යක්ෂම ක්රමයකි. මෙම ක්රියාවලියට තත්පර කිහිපයකින් කොටස් නිර්මාණය කළ හැකි අතර, වේගවත් නිෂ්පාදන කාලය තීරණාත්මක වන මෝටර් රථ කර්මාන්තය සඳහා එය කදිම විසඳුමක් බවට පත් කරයි.
වැඩිදියුණු කළ ගුණාත්මකභාවය: ඉන්ජෙක්ෂන් මෝල්ඩින් මගින් නිපදවන ප්ලාස්ටික් සංරචක ස්ථාවර ගුණාත්මක බවක් ඇත. මක්නිසාද යත්, උෂ්ණත්වය, පීඩනය සහ සිසිලන කාලය වැනි අච්චු පරාමිති මත නිශ්චිත පාලනයට ක්රියාවලිය ඉඩ සලසයි. එහි ප්රතිඵලයක් වශයෙන්, ඉන්ජෙක්ෂන් මෝල්ඩින් හරහා නිපදවන ප්ලාස්ටික් සංරචක විශිෂ්ට මාන නිරවද්යතාවක් සහ මතුපිට නිමාවක් ඇත.
එන්නත් අච්චු ගැසීමේදී බහුලව භාවිතා වන ප්ලාස්ටික් ගවේෂණය කිරීම
ඉන්ජෙක්ෂන් මෝල්ඩින් යනු ප්ලාස්ටික් පෙති උණු කිරීම සහ විශේෂිත හැඩයක් සෑදීම සඳහා අච්චු කුහරයකට එන්නත් කිරීමයි. මෙම ක්රියාවලියේ බහුකාර්යතාව නිසා නිෂ්පාදකයන්ට ඉහළ නිරවද්යතාවයකින් සහ අනුකූලතාවයකින් සංකීර්ණ කොටස් නිර්මාණය කිරීමට ඉඩ සලසයි. අපේක්ෂිත ගුණාංග ලබා ගැනීම සඳහා එන්නත් අච්චු ගැසීමේදී විවිධ ප්ලාස්ටික් ද්රව්ය භාවිතා වේ. මෙම බ්ලොග් සටහන එන්නත් අච්චු ගැසීමේදී බහුලව භාවිතා වන ප්ලාස්ටික් සහ ඒවායේ ගුණාංග ගවේෂණය කරනු ඇත.
- ඇක්රිලෝනිට්රයිල් බියුඩඩීන් ස්ටයිරීන් (ABS): ABS යනු එහි දැවැන්ත බලපෑම, තද බව සහ තාප ප්රතිරෝධය හේතුවෙන් එන්නත් අච්චු ගැසීමේදී බහුලව භාවිතා වන තාප ප්ලාස්ටික් බහුඅවයවයකි. එය මෝටර් රථ අමතර කොටස්, සෙල්ලම් බඩු සහ ඉලෙක්ට්රොනික නිවාසවල බහුලව භාවිතා වේ.
- පොලිකාබනේට් (PC): PC යනු ආරක්ෂිත වීදුරු, ඉලෙක්ට්රොනික උපාංග සහ මෝටර් රථ කොටස් වැනි බලපෑම් ප්රතිරෝධය සහ දෘශ්ය පැහැදිලි බව අවශ්ය නිෂ්පාදන සඳහා එන්නත් අච්චු වල භාවිතා කරන දෘඩ, විනිවිද පෙනෙන ප්ලාස්ටික් ද්රව්යයකි.
- Polypropylene (PP): PP යනු නම්යශීලී බව, ශක්තිය සහ රසායනික ප්රතිරෝධය අවශ්ය නිෂ්පාදන සඳහා එන්නත් අච්චු ගැසීමේදී භාවිතා කරන බහුකාර්ය ප්ලාස්ටික් ද්රව්යයකි. එය ඇසුරුම්කරණය, වාහන අමතර කොටස් සහ පාරිභෝගික භාණ්ඩ සඳහා බහුලව භාවිතා වේ.
- පොලිඑතිලීන් (PE): PE යනු නම්යශීලී බව සහ කල්පැවැත්ම අවශ්ය නිෂ්පාදන සඳහා එන්නත් අච්චු ගැසීමේදී භාවිතා කරන සැහැල්ලු ප්ලාස්ටික් ද්රව්යයකි. එය සාමාන්යයෙන් ඇසුරුම්, ගෘහ භාණ්ඩ සහ සෙල්ලම් බඩු වල භාවිතා වේ.
- Polyoxymethylene (POM): POM යනු මාන ස්ථායීතාවය සහ ඇඳුම් ප්රතිරෝධය අවශ්ය නිෂ්පාදන සඳහා එන්නත් අච්චු ගැසීමේදී භාවිතා කරන ඝන සහ දෘඩ ප්ලාස්ටික් ද්රව්යයකි. එය සාමාන්යයෙන් ගියර්, ෙබයාරිං සහ අනෙකුත් යාන්ත්රික කොටස්වල භාවිතා වේ.
- Polystyrene (PS): PS යනු හොඳ මාන ස්ථායීතාවයක් සහ පරිවාරක ගුණයක් අවශ්ය නිෂ්පාදන සඳහා එන්නත් අච්චු ගැසීමේදී භාවිතා කරන සැහැල්ලු සහ දෘඩ ප්ලාස්ටික් ද්රව්යයකි. එය බහුලව භාවිතා වන්නේ ආහාර ඇසුරුම්, ඉවත දැමිය හැකි උපකරණ සහ සී.ඩී.
- Polyethylene Terephthalate (PET): PET යනු ඉහළ පැහැදිලිකම, තද බව සහ රසායනික ප්රතිරෝධය අවශ්ය නිෂ්පාදන සඳහා එන්නත් අච්චු ගැසීමේදී භාවිතා කරන ශක්තිමත් සහ සැහැල්ලු ප්ලාස්ටික් ද්රව්යයකි. එය බීම බෝතල්, ආහාර ඇසුරුම් සහ වෛද්ය උපකරණවල බහුලව භාවිතා වේ.
- නයිලෝන් (PA): නයිලෝන් යනු ඉහළ ශක්තියක්, තාප ප්රතිරෝධයක් සහ රසායනික ප්රතිරෝධයක් අවශ්ය නිෂ්පාදන සඳහා එන්නත් අච්චු ගැසීමේදී භාවිතා කරන ශක්තිමත් සහ කල් පවතින ප්ලාස්ටික් ද්රව්යයකි. එය මෝටර් රථ අමතර කොටස්, ඉලෙක්ට්රොනික උපාංග සහ කාර්මික යන්ත්රෝපකරණවල බහුලව භාවිතා වේ.
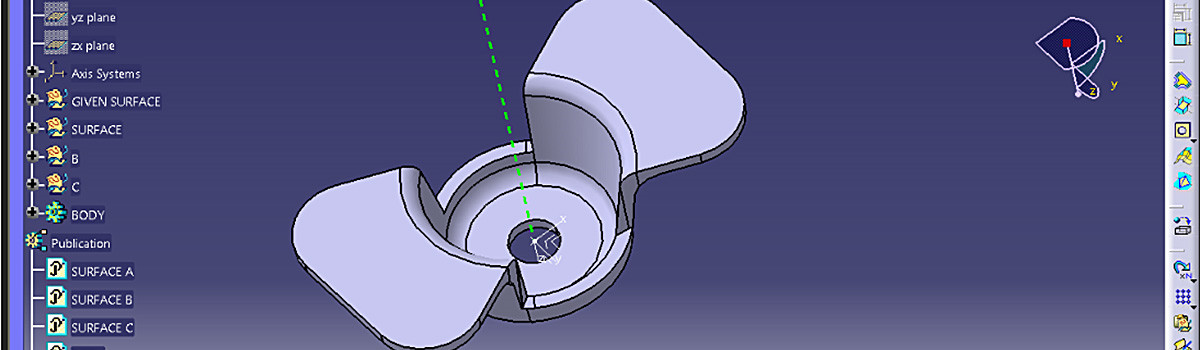
මෝටර් රථ ප්ලාස්ටික් සංරචක සඳහා සැලසුම් සලකා බැලීම්
මෙම බ්ලොග් සටහන මෝටර් රථ ප්ලාස්ටික් සංරචක සඳහා තීරණාත්මක සැලසුම් සලකා බැලීම් කිහිපයක් සාකච්ඡා කරනු ඇත.
ද්රව්ය තෝරාගැනීම:
- ප්ලාස්ටික් සංරචක පොලිප්රොපිලීන්, පොලිකාබනේට්, ABS සහ තවත් බොහෝ ද්රව්ය වලින් සෑදිය හැක.
- සෑම ද්රව්යයකටම ශක්තිය, තද බව, තාප ස්ථායීතාවය සහ රසායනික ද්රව්ය සහ UV විකිරණවලට ප්රතිරෝධය වැනි අද්විතීය ගුණාංග ඇත.
- කොටසෙහි අපේක්ෂිත භාවිතය සහ නියාමන ප්රමිතීන්හි නිශ්චිත අවශ්යතා සපුරාලන ද්රව්යයක් තෝරා ගැනීම ඉතා වැදගත් වේ.
නිෂ්පාදන ක්රමය:
- ඉන්ජෙක්ෂන් මෝල්ඩින්, බ්ලෝ මෝල්ඩින්, ටර්මෝෆෝමිං සහ භ්රමණ මෝල්ඩින් ඇතුළු ක්රම කිහිපයක් භාවිතයෙන් ප්ලාස්ටික් සංරචක නිෂ්පාදනය කළ හැකිය.
- සෑම ක්රමයක්ම පිරිවැය, නිෂ්පාදන වේගය, සංකීර්ණත්වය සහ කොටසෙහි ගුණාත්මකභාවය අනුව වාසි සහ අවාසි ඇත.
- නිෂ්පාදන ක්රමය තෝරා ගත යුත්තේ එහි ප්රමාණය, හැඩය සහ පරිමාව මෙන්ම අපේක්ෂිත මට්ටමේ නිරවද්යතාවය සහ අනුකූලතාවය වැනි කොටසෙහි නිශ්චිත අවශ්යතා මත ය.
කොටස් ක්රියාකාරිත්වය:
- එය සැලසුම් කිරීමේදී ප්ලාස්ටික් සංරචකයේ කාර්යය ප්රවේශමෙන් සලකා බැලිය යුතුය.
- යාන්ත්රික ආතතිය, උෂ්ණත්ව විචලනය, රසායනික නිරාවරණය සහ අනෙකුත් පාරිසරික සාධකවලට ඔරොත්තු දෙන ලෙස කොටස් නිර්මාණය කිරීමට අවශ්ය විය හැකිය.
- කොටසෙහි ගැළපීම, ආකෘතිය සහ ක්රියාකාරිත්වය සහ ඕනෑම සෞන්දර්යාත්මක අවශ්යතා ද සලකා බැලිය යුතුය.
එකලස් කිරීම සඳහා නිර්මාණය:
- ප්ලාස්ටික් සංරචක එකලස් කිරීමේ පහසුව සැලකිල්ලට ගනිමින් නිර්මාණය කළ යුතුය.
- එකලස් කිරීමට අපහසු හෝ කාලය ගතවන සංරචක නිෂ්පාදන පිරිවැය වැඩි කර ගුණාත්මක ගැටළු වලට තුඩු දිය හැකිය.
- අමතර දෘඩාංග හෝ ගාංචු සඳහා අවම අවශ්යතාවයක් සහිතව, පහසුවෙන් සහ ආරක්ෂිතව එකට ගැළපෙන පරිදි කොටස් නිර්මාණය කළ යුතුය.
නිෂ්පාදනය සඳහා නිර්මාණය:
- ප්ලාස්ටික් සංරචක සැලසුම් කිරීම නිෂ්පාදන ක්රියාවලිය සහ යම් සීමාවන් හෝ සීමාවන් ද සලකා බැලිය යුතුය.
- කෙටුම්පත් කෝණ, බිත්ති ඝණත්වය සහ කොටස් රේඛා වැනි සැලසුම් විශේෂාංග නිෂ්පාදනවල ගුණාත්මකභාවය සහ පිරිවැය සැලකිය යුතු ලෙස බලපෑ හැකිය.
- නිෂ්පාදකයා සමඟ සහයෝගයෙන් නිර්මාණය නිෂ්පාදනය සඳහා ප්රශස්ත බව සහතික කිරීමට උපකාරී වේ.
පරීක්ෂා කිරීම සහ තහවුරු කිරීම:
- ප්ලාස්ටික් සංරචකයේ සැලසුම අවසන් වූ පසු, එය අවශ්ය කාර්ය සාධනය සහ ආරක්ෂක අවශ්යතා සපුරාලීම සහතික කිරීම සඳහා එය පරීක්ෂා කර තහවුරු කළ යුතුය.
- පරීක්ෂණයට යාන්ත්රික, රසායනික සහ තාප පරීක්ෂණ සහ ගැළපුම සහ ක්රියාකාරිත්වය සඳහා පරීක්ෂණ ඇතුළත් විය හැකිය.
- ආරම්භක සැලසුමේ සිට අවසාන නිෂ්පාදනය දක්වා සංවර්ධන ක්රියාවලිය පුරාම වලංගුකරණය සිදු කළ යුතුය.
එන්නත් අච්චු ගැසීමේදී මූලාකෘතිකරණයේ කාර්යභාරය
ඉන්ජෙක්ෂන් මෝල්ඩින් ලෝකයේ මූලාකෘතිකරණය තීරණාත්මක කාර්යභාරයක් ඉටු කරයි. එය නිෂ්පාදනයේ වැදගත් පියවරක් වන අතර, නිර්මාණකරුවන්ට සහ ඉංජිනේරුවන්ට ඔවුන්ගේ සැලසුම් පිරිපහදු කිරීමට, ක්රියාකාරීත්වය පරීක්ෂා කිරීමට සහ පූර්ණ පරිමාණ නිෂ්පාදනය සමඟ ඉදිරියට යාමට පෙර විභව ගැටළු හඳුනා ගැනීමට ඉඩ සලසයි. මෙහිදී, අපි එන්නත් අච්චු ගැසීමේදී මූලාකෘතිකරණයේ වැදගත්කම සහ එහි බොහෝ ප්රතිලාභ ගවේෂණය කරන්නෙමු.
සැලසුම් වලංගුකරණය:
මූලාකෘතිකරණය නිර්මාණකරුවන්ට ඔවුන්ගේ නිෂ්පාදන සැලසුම් වලංගු කිරීමට සහ සැබෑ ලෝකයේ ඔවුන්ගේ ශක්යතා තක්සේරු කිරීමට හැකියාව ලබා දෙයි. භෞතික මූලාකෘතියක් නිර්මාණය කිරීමෙන්, නිර්මාණකරුවන්ට කොටස් ජ්යාමිතිය, යෝග්යතාවය සහ එකලස් කිරීම වැනි සාධක ඇගයීමට හැකිය. එය සැලසුම් දෝෂ හඳුනා ගැනීමට උපකාරී වේ, අවසාන නිෂ්පාදනය අපේක්ෂිත පිරිවිතරයන් සපුරාලීම සහ අපේක්ෂිත පරිදි ක්රියා කරයි.
පුනරාවර්තන වැඩිදියුණු කිරීම:
මූලාකෘතිකරණය නිෂ්පාදන සංවර්ධන චක්රය පුරාම පුනරාවර්තන වැඩිදියුණු කිරීම් සඳහා ඉඩ සලසයි. බහු මූලාකෘති නිර්මාණය කිරීමෙන් සහ ඒවා පරීක්ෂා කිරීමෙන්, නිර්මාණකරුවන්ට වටිනා ප්රතිපෝෂණ එක්රැස් කර අවශ්ය වෙනස් කිරීම් කළ හැකිය. මෙම පුනරාවර්තන ක්රියාවලිය සැලසුම පිරිපහදු කිරීමට, ක්රියාකාරීත්වය ප්රශස්ත කිරීමට සහ අවසාන නිෂ්පාදනයේ සමස්ත කාර්ය සාධනය වැඩි දියුණු කිරීමට උපකාරී වේ.
පිරිවැය සහ කාලය ඉතිරිකිරීම්:
මූලාකෘතිකරණයේදී සැලසුම් දෝෂ හෝ ක්රියාකාරීත්වයේ ගැටළු හඳුනා ගැනීම මහා පරිමාණ නිෂ්පාදනයේදී ඒවා සොයා ගැනීමට වඩා සැලකිය යුතු ලෙස පිරිවැය-ඵලදායී සහ කාලය ඉතිරි කරයි. සැලසුම් වෙනස්කම් කලින් සිදු කිරීම මිල අධික නැවත සකස් කිරීමේ අවශ්යතාවය අඩු කරන අතර නිෂ්පාදන ප්රමාද වීමේ අවදානම අඩු කරයි. මිල අධික මෙවලම් සහ නිෂ්පාදන ක්රියාවලීන් සඳහා කැපවීමට පෙර මූලාකෘතිකරණය කාර්යක්ෂම ගැටළු විසඳීමට සහ ප්රශස්තකරණයට ඉඩ සලසයි.
ද්රව්ය තෝරා ගැනීම:
මූලාකෘතිකරණය එන්නත් අච්චු කිරීම සඳහා සුදුසු ද්රව්ය තෝරාගැනීමට පහසුකම් සපයයි. විවිධ ද්රව්ය පරීක්ෂා කිරීමෙන්, ඉංජිනේරුවන්ට ශක්තිය, නම්යශීලී බව සහ තාප ප්රතිරෝධය ඇතුළුව ඒවායේ ගුණාංග තක්සේරු කළ හැකි අතර අපේක්ෂිත යෙදුම සඳහා වඩාත් සුදුසු ද්රව්ය තෝරා ගත හැකිය. මෙය සිදු කිරීමෙන්, ප්රතිඵලය කාර්ය සාධනය සහ කල්පැවැත්ම සඳහා අවශ්ය ප්රමිතීන් සපුරාලන බව අපි සහතික කරමු.
නිෂ්පාදන ක්රියාවලිය සත්යාපනය:
තෝරාගත් නිෂ්පාදන ක්රියාවලියේ ශක්යතාව සහ සඵලතාවය සත්යාපනය කිරීමේ මාධ්යයක් ලෙස මූලාකෘති සේවය කරයි. මහා පරිමාණ නිෂ්පාදනය සඳහා අදහස් කරන එකම ද්රව්ය සහ ක්රම භාවිතා කරමින් මූලාකෘති නිෂ්පාදනය කිරීමෙන්, ඉංජිනේරුවන්ට ඕනෑම අභියෝගයක් හෝ සීමාවක් කල් ඇතිව හඳුනාගත හැකිය. මෙම සත්යාපන ක්රියාවලිය නිෂ්පාදනය විධිමත් කිරීමට, දෝෂ අවම කිරීමට සහ අවසාන නිෂ්පාදනයේ ස්ථාවර ගුණාත්මක බව සහතික කිරීමට උපකාරී වේ.
සන්නිවේදනය සහ පාර්ශවකරුවන්ගේ සහභාගීත්වය:
මූලාකෘති යනු නිෂ්පාදන අදහසක ප්රත්යක්ෂ නිරූපණයන් වන අතර, ඵලදායී සන්නිවේදනයට සහ පාර්ශවකරුවන්ගේ සහභාගීත්වයට පහසුකම් සපයයි. නිර්මාණ සංකල්පය සේවාලාභීන්ට ඉදිරිපත් කිරීම හෝ අවසාන පරිශීලකයින්ගෙන් ප්රතිපෝෂණ එක්රැස් කිරීම වේවා, මූලාකෘති මඟින් නිෂ්පාදිතය දෘශ්යමාන කිරීම, ආදානය සැපයීම සහ දැනුවත් තීරණ ගැනීම සම්බන්ධ සියලු දෙනාටම පහසු කරයි. වැඩිදියුණු කරන ලද සහයෝගීතාවය අඩු වරදවා වටහාගැනීම් සහ වැඩි සමස්ත තෘප්තියට හේතු වේ.
එන්නත් අච්චු ගැසීමේ ක්රියාවලියේ තීරණාත්මක පියවර
මෙම බ්ලොග් සටහන එන්නත් අච්චු ගැසීමේ ක්රියාවලියේ තීරණාත්මක පියවර ගැන සාකච්ඡා කරනු ඇත.
පියවර 1: ද්රව්ය තෝරාගැනීම
ඉන්ජෙක්ෂන් මෝල්ඩින් ක්රියාවලියේ පළමු පියවර වන්නේ ද්රව්ය තෝරාගැනීමයි.
විවිධ ප්ලාස්ටික් ද්රව්යවල ශක්තිය, නම්යශීලීභාවය සහ රසායනික ප්රතිරෝධය වැනි අද්විතීය ගුණාංග ඇත.
ද්රව්ය තෝරා ගැනීම කොටසෙහි නිශ්චිත අවශ්යතා සහ එහි අපේක්ෂිත භාවිතය මත රඳා පවතී.
පියවර 2: පෙති සකස් කිරීම
ප්ලාස්ටික් පෙති වියළීම සහ අවශ්ය පිරිවිතරයන් මිශ්ර කිරීම මගින් සකස් කර ඇත.
අවසාන නිෂ්පාදනයේ ගුණාත්මක භාවයට බලපෑම් කළ හැකි තෙතමනය හා දූෂක වලින් ප්ලාස්ටික් නොමැති බව සහතික කිරීම සඳහා මෙම පියවර අත්යවශ්ය වේ.
පියවර 3: ප්ලාස්ටික් උණු කිරීම
ප්ලාස්ටික් පෙති ඉන්ජෙක්ෂන් මෝල්ඩින් යන්ත්රයේ උණු කර ඇත.
ද්රවාංක ක්රියාවලියේ උෂ්ණත්වය සහ පීඩනය භාවිතා කරන ප්ලාස්ටික් ද්රව්ය වර්ගය මත රඳා පවතී.
පියවර 4: එන්නත් කිරීම
පසුව උණු කළ ප්ලාස්ටික් අච්චුව තුළට එන්නත් කරනු ලැබේ.
අච්චුව සාමාන්යයෙන් වානේ වලින් සාදා ඇති අතර අවසාන නිෂ්පාදනයේ අපේක්ෂිත හැඩය නිර්මාණය කිරීම සඳහා නිර්මාණය කර ඇත.
පියවර 5: සිසිලනය සහ ඝන වීම
ප්ලාස්ටික් අච්චුව තුළට එන්නත් කිරීමෙන් පසුව, එය සිසිල් වන අතර අවශ්ය හැඩයට ඝන වේ.
සිසිලන කාලය කොටසෙහි ඝනකම හා සංකීර්ණත්වය මත රඳා පවතී.
පියවර 6: පිටකිරීම
ප්ලාස්ටික් සිසිල් වී ඝන වීමෙන් පසුව, අච්චුව විවෘත කර ඇති අතර, එම කොටස ඉවත් කරනු ලැබේ.
සමහර අවස්ථාවලදී, අච්චුවෙන් කොටස ඉවත් කිරීමට උපකාර කිරීම සඳහා ejector pins භාවිතා කරයි.
පියවර 7: කැපීම සහ අවසන් කිරීම
කොටස අච්චුවෙන් ඉවත් කිරීමෙන් පසු, අතිරික්ත ද්රව්ය ඉවත් කිරීම සහ දාර සුමට කිරීම සඳහා අතිරේක කැපීම සහ නිමාව අවශ්ය විය හැකිය.
පියවර 8: තත්ත්ව පාලනය
තත්ත්ව පාලනය ඉන්ජෙක්ෂන් මෝල්ඩින් ක්රියාවලියේ අත්යවශ්ය පියවරකි.
අවසන් නිශ්පාදනය විකෘති කිරීම, ඉරිතැලීම්, හෝ වර්ණ හෝ වයනයෙහි නොගැලපීම් වැනි දෝෂ සඳහා පරීක්ෂා කරනු ලැබේ.
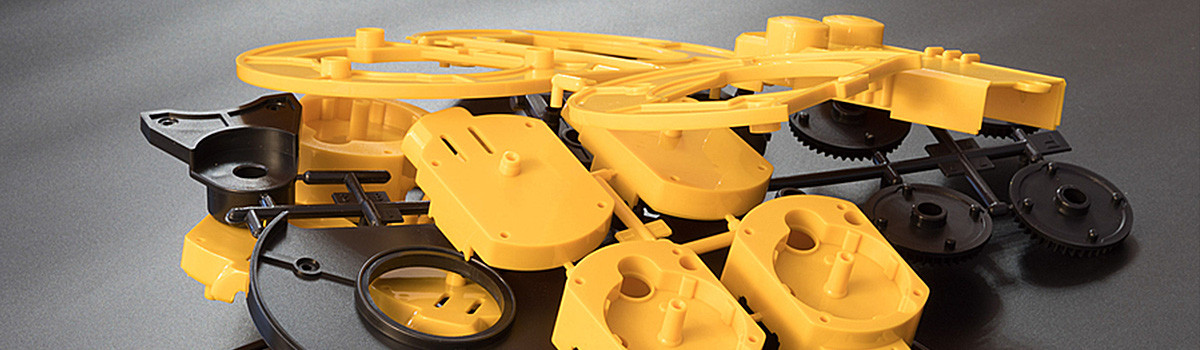
ප්ලාස්ටික් සංරචකවල ශක්තිය සහ කල්පැවැත්ම වැඩි දියුණු කිරීම සඳහා තාක්ෂණික ක්රම
කෙසේ වෙතත්, ඔවුන් බොහෝ විට ශක්තිය සහ කල්පැවැත්ම සමඟ අභියෝගවලට මුහුණ දෙයි, විශේෂයෙන් අධික ආතතියට හෝ දරුණු පාරිසරික තත්ත්වයන්ට නිරාවරණය වන විට. මෙම බ්ලොග් සටහනෙන් අපි ප්ලාස්ටික් සංරචකවල ශක්තිය සහ කල්පැවැත්ම වැඩි දියුණු කිරීම සඳහා තාක්ෂණික ක්රම කිහිපයක් සාකච්ඡා කරමු.
ආකලන සමඟ ශක්තිමත් කිරීම
- තන්තු, පිරවුම් හෝ නැනෝ අංශු සමඟ ශක්තිමත් කිරීම මගින් ප්ලාස්ටික් සංරචකවල ශක්තිය සහ කල්පැවැත්ම වැඩිදියුණු කළ හැක.
- පොදු ආකලනවලට වීදුරු කෙඳි, කාබන් තන්තු, සිලිකා, ටැල්ක් සහ මැටි ඇතුළත් වේ.
වෙනත් ද්රව්ය සමඟ මිශ්ර කිරීම
- රබර් හෝ ඉලාස්ටෝමර් වැනි වෙනත් ද්රව්ය සමඟ ප්ලාස්ටික් මිශ්ර කිරීමෙන් ඒවායේ ශක්තිය සහ කල්පැවැත්ම වැඩි දියුණු කළ හැකිය.
- උදාහරණයක් ලෙස, පොලිප්රොපිලීන් වලට කුඩා රබර් ප්රමාණයක් එකතු කිරීමෙන් එහි බලපෑම් ප්රතිරෝධය වැඩි දියුණු කළ හැක.
තාප ප්රතිකාර
- තාප පිරියම් කිරීම ඇතැම් වර්ගවල ප්ලාස්ටික් සංරචකවල ශක්තිය සහ කල්පැවැත්ම වැඩි කළ හැක.
- ප්ලාස්ටික් එහි රසායනික හා භෞතික ගුණාංග වෙනස් කිරීම සඳහා ඉහළ උෂ්ණත්වයකට නිරාවරණය කිරීම මෙයට ඇතුළත් වේ.
අඟුරු කිරීම
- Annealing යනු තාප පිරියම් කිරීමේ තාක්ෂණයක් වන අතර එය ප්ලාස්ටික් නිශ්චිත උෂ්ණත්වයකට රත් කර එය සෙමින් සිසිල් කරයි.
- මෙම තාක්ෂණය ප්ලාස්ටික් තුළ අභ්යන්තර ආතතීන් අඩු කර ගත හැකි අතර, එහි ශක්තිය සහ කල්පැවැත්ම වැඩි දියුණු කරයි.
ඉන්ජෙක්ෂන් මෝල්ඩින් ක්රියාවලිය ප්රශස්තකරණය
- ඉන්ජෙක්ෂන් මෝල්ඩින් ක්රියාවලිය ප්රශස්ත කිරීම ප්ලාස්ටික් සංරචකවල ශක්තිය සහ කල්පැවැත්ම වැඩි දියුණු කළ හැකිය.
- වාත්තු කිරීමේදී උෂ්ණත්වය, පීඩනය සහ සිසිලන වේගය පාලනය කිරීම මෙයට ඇතුළත් වේ.
මතුපිට ප්රතිකාර
- corona, plasma, හෝ flame treatment වැනි මතුපිට ප්රතිකාර ක්රම මගින් ප්ලාස්ටික් සහ අනෙකුත් ද්රව්ය අතර ඇලීම වැඩි දියුණු කළ හැක.
- බන්ධනය ඉතා වැදගත් වන යෙදුම්වල ප්ලාස්ටික් සංරචකයේ ශක්තිය සහ කල්පැවැත්ම වැඩි දියුණු කළ හැකිය.
ආලේපන
- ආලේපන අතිරේක ආරක්ෂිත තට්ටුවක් ලබා දීමෙන් ප්ලාස්ටික් සංරචකවල ශක්තිය සහ කල්පැවැත්ම වැඩි දියුණු කළ හැකිය.
- නිදසුනක් ලෙස, විඛාදනයට ඔරොත්තු දෙන ආලේපනයක් මගින් ප්ලාස්ටික් සංරචක දැඩි පරිසරවල හානිවලින් ආරක්ෂා කළ හැකිය.
ඔටෝමෝටිව් ඉන්ජෙක්ෂන් මෝල්ඩින් වල තත්ත්ව පාලන පියවර
ඔටෝමෝටිව් ඉන්ජෙක්ෂන් මෝල්ඩින් යනු උසස් තත්ත්වයේ මෝටර් රථ කොටස් නිෂ්පාදනය සඳහා ඉතා වැදගත් වන ක්රියාවලියකි. දැඩි තත්ත්ව සහ කාර්ය සාධන ප්රමිතීන් සපුරාලන කොටස් නිෂ්පාදනය කිරීම සඳහා විශේෂිත යන්ත්රෝපකරණ සහ අච්චු භාවිතා කිරීම ක්රියාවලියට ඇතුළත් වේ. මෙම ක්රියාවලිය හරහා සාදන ලද මෝටර් රථ අමතර කොටස් මෙම ප්රමිතීන්ට අනුකූල බව සහතික කිරීම සඳහා තත්ත්ව පාලන පියවරයන් අවශ්ය වේ. මෝටර් රථ එන්නත් අච්චු ගැසීමේදී ක්රියාත්මක වන තීරණාත්මක තත්ත්ව පාලන පියවර කිහිපයක් මෙන්න:
ද්රව්ය පරීක්ෂාව: තත්ත්ව පාලනයේ පළමු පියවර වන්නේ ද්රව්යමය පරීක්ෂාවයි. අවශ්ය පිරිවිතරයන් සපුරාලීම සඳහා අමුද්රව්ය පරීක්ෂා කරනු ලැබේ. ද්රව්ය සංයුතිය, සංශුද්ධතාවය සහ අනුකූලතාව පරීක්ෂා කිරීම මෙයට ඇතුළත් වේ.
වාත්තු ක්රියාවලි අධීක්ෂණය: අවශ්ය පිරිවිතරයන් තුළ කොටස් නිෂ්පාදනය කරන බව සහතික කිරීම සඳහා වාත්තු කිරීමේ ක්රියාවලිය අඛණ්ඩව අධීක්ෂණය කරනු ලැබේ. භාවිතා කරන ලද ද්රව්යවල උෂ්ණත්වය, පීඩනය සහ ප්රවාහ අනුපාතය නිරීක්ෂණය කිරීම මෙයට ඇතුළත් වේ.
කොටස් පරීක්ෂාව: අවශ්ය ප්රමිතීන් සපුරාලීම සඳහා නිෂ්පාදනයෙන් පසු කොටස් පරීක්ෂා කරනු ලැබේ. විකෘති කිරීම, ගිල්වීමේ සලකුණු සහ දැල්වීම වැනි දෝෂ සඳහා පරීක්ෂා කිරීම මෙයට ඇතුළත් වේ.
සංඛ්යාන ක්රියාවලි පාලනය (SPC): SPC යනු නිෂ්පාදන ක්රියාවලිය නිරීක්ෂණය කරන සහ පාලනය කරන සංඛ්යානමය මෙවලමකි. දත්ත විශ්ලේෂණය කිරීමට සහ ක්රියාවලියේ ඇති විය හැකි ගැටළු පෙන්නුම් කරන ප්රවණතා හෝ රටා හඳුනා ගැනීමට සංඛ්යානමය ශිල්පීය ක්රම භාවිතා කිරීම එයට ඇතුළත් වේ.
තත්ත්ව සහතිකය (QA): QA යනු අවසාන නිෂ්පාදනය අවශ්ය තත්ත්ව ප්රමිතීන්ට අනුකූල බව සහතික කිරීම සඳහා ක්රියා පටිපාටි සහ මාර්ගෝපදේශ මාලාවක් භාවිතා කිරීමයි. නිමි භාණ්ඩය අවශ්ය පිරිවිතරයන් සපුරාලන බව සහතික කිරීම සඳහා පරීක්ෂා කිරීම සහ පරීක්ෂා කිරීම මෙයට ඇතුළත් වේ.
හඳුනාගත හැකි බව: Traceability යනු නිෂ්පාදනයක් එහි ප්රභවය වෙත ආපසු ලුහුබැඳීමේ හැකියාවයි. ඔටෝමෝටිව් ඉන්ජෙක්ෂන් මෝල්ඩින් වලදී, කිසියම් දෝෂයක් හෝ ගුණාත්මක ගැටළු ඒවායේ මූලාශ්රය වෙත ආපසු ගොස් ඒවා නිවැරදි කළ හැකි බව සහතික කිරීම සඳහා සොයා ගැනීමේ හැකියාව ඉතා වැදගත් වේ.
අඛණ්ඩ වැඩිදියුණු කිරීම: අඛණ්ඩ වැඩිදියුණු කිරීම යනු වැඩිදියුණු කිරීම සඳහා ක්ෂේත්ර හඳුනා ගැනීම සහ නිෂ්පාදනවල ගුණාත්මකභාවය වැඩි දියුණු කිරීම සඳහා වෙනස්කම් ක්රියාත්මක කිරීම ඇතුළත් අඛණ්ඩ ක්රියාවලියකි. මෙයට දත්ත විශ්ලේෂණය කිරීම, ප්රවණතා හඳුනා ගැනීම සහ නිෂ්පාදනවල ගුණාත්මකභාවය සහ අනුකූලතාව ඉහළ නැංවීම සඳහා ක්රියාවලියේ වෙනස්කම් ක්රියාත්මක කිරීම ඇතුළත් වේ.
පිරිවැය විශ්ලේෂණය: ඉන්ජෙක්ෂන් මෝල්ඩින් එදිරිව සම්ප්රදායික නිෂ්පාදන ක්රම
නිෂ්පාදන කර්මාන්තය තුළ, තීරණ ගැනීමේ තීරණාත්මක අංගයක් වන්නේ පිරිවැය විශ්ලේෂණයයි. නිෂ්පාදකයින් විසින් වඩාත් ලාභදායී ආකාරය තීරණය කිරීම සඳහා විවිධ ක්රම භාවිතා කරමින් තම නිෂ්පාදන නිෂ්පාදනය කිරීමේ පිරිවැය ඇගයීමට ලක් කළ යුතුය. ඉන්ජෙක්ෂන් මෝල්ඩින් සහ සාම්ප්රදායික නිෂ්පාදන ක්රම බහුලව භාවිතා වන අතර නිෂ්පාදකයින් තම නිෂ්පාදන සඳහා වඩාත්ම ලාභදායී වන්නේ කුමන ආකාරයෙන්ද යන්න තීරණය කළ යුතුය. සාම්ප්රදායික නිෂ්පාදන ක්රමවලට එදිරිව ඉන්ජෙක්ෂන් මෝල්ඩින් පිරිවැය විශ්ලේෂණයක් මෙන්න.
එන්නත් අච්චු කිරීම:
ඉන්ජෙක්ෂන් මෝල්ඩින් යනු කොටස් නිෂ්පාදනය කිරීම සඳහා උණු කළ ප්ලාස්ටික් අච්චුවකට එන්නත් කිරීම ඇතුළත් නිෂ්පාදන ක්රමයකි. එන්නත් අච්චු ගැසීමේ වාසි සහ අවාසි කිහිපයක් මෙන්න:
වාසි:
- ඉහළ නිෂ්පාදන පරිමාව:එන්නත් අච්චුව සමාන කොටස්වල ඉහළ පොත් නිෂ්පාදනය කිරීම සඳහා සුදුසු වේ.
- අඩු ශ්රම පිරිවැය:සාම්ප්රදායික නිෂ්පාදන ක්රම හා සසඳන විට එන්නත් අච්චු කිරීම සඳහා අවම ශ්රමයක් අවශ්ය වේ.
- අනුකූලතාව: ඉන්ජෙක්ෂන් මෝල්ඩින් එකකට එක සමාන වන ගැළපෙන කොටස් සාදයි.
- අඩු ද්රව්ය අපද්රව්ය: සාම්ප්රදායික නිෂ්පාදන ක්රමවලට වඩා එන්නත් අච්චුවෙහි ද්රව්යමය අපද්රව්ය අඩුය.
අවාසි:
- ඉහළ පෙර පිරිවැය:සාම්ප්රදායික නිෂ්පාදන ක්රමවලට සාපේක්ෂව ඉන්ජෙක්ෂන් මෝල්ඩින් සැකසීමේ පිරිවැය වැඩි ය.
- සීමිත නම්යශීලීභාවය: සාම්ප්රදායික නිෂ්පාදන ක්රමවලට වඩා ඉන්ජෙක්ෂන් මෝල්ඩින් අඩු නම්යශීලී වන අතර, එය අභිරුචි කොටස් නිෂ්පාදනය සඳහා අඩු සුදුසුකමක් බවට පත් කරයි.
සාම්ප්රදායික නිෂ්පාදන ක්රම:
සාම්ප්රදායික නිෂ්පාදන ක්රම දශක ගණනාවක් තිස්සේ භාවිතා කරන සාම්ප්රදායික නිෂ්පාදන ක්රම වේ. මෙම ක්රමවලට ඇඹරීම, කැණීම සහ හැරීම ඇතුළත් වේ. සාම්ප්රදායික නිෂ්පාදන ක්රමවල වාසි සහ අවාසි කිහිපයක් මෙන්න:
වාසි:
- අඩු, පෙර වියදම්:සාම්ප්රදායික නිෂ්පාදන ක්රම සඳහා අවම පෙර වියදම් අවශ්ය වන අතර, ඒවා අඩු පරිමාවකින් කොටස් නිෂ්පාදනය කිරීම සඳහා වඩාත් සුදුසු වේ.
- නම්යශීලී බව:සම්ප්රදායික නිෂ්පාදන ක්රම එන්නත් අච්චු වලට වඩා නම්යශීලී වන අතර ඒවා අභිරුචි කොටස් නිෂ්පාදනය සඳහා වඩාත් සුදුසු වේ.
- අඩු මෙවලම් පිරිවැය:සම්ප්රදායික නිෂ්පාදන ක්රම සඳහා එන්නත් අච්චු වලට වඩා අඩු මෙවලම් පිරිවැයක් අවශ්ය වේ.
අවාසි:
- ඉහළ ශ්රම පිරිවැය:සාම්ප්රදායික නිෂ්පාදන ක්රම සඳහා එන්නත් අච්චු වලට වඩා වැඩි ශ්රමයක් අවශ්ය වන අතර එහි ප්රතිඵලයක් ලෙස ශ්රම පිරිවැය ඉහළ යයි.
- ඉහළ ද්රව්යමය අපද්රව්ය:සම්ප්රදායික නිෂ්පාදන ක්රම මගින් ඉන්ජෙක්ෂන් මෝල්ඩින්ට වඩා අපද්රව්ය නිපදවයි.
- නොගැලපෙන කොටස්:සාම්ප්රදායික නිෂ්පාදන ක්රම මගින් එකිනෙකින් සුළු වෙනස්කම් ඇති ප්රමාණ නිපදවයි.
ඉන්ජෙක්ෂන් මෝල්ඩින්ගේ තිරසාරභාවය සහ පාරිසරික බලපෑම
තිරසාරභාවය සහ පාරිසරික බලපෑම ව්යාපාර සහ නිෂ්පාදකයින් තම නිෂ්පාදන ක්රියාවලීන්හි සලකා බැලිය යුතු වැදගත් සාධක වේ. ජනප්රිය නිෂ්පාදන ක්රමයක් වන ඉන්ජෙක්ෂන් මෝල්ඩින් ධනාත්මක සහ අහිතකර පාරිසරික බලපෑම් ඇති කරයි. මෙම බ්ලොග් සටහනෙහි, අපි එන්නත් අච්චුවෙහි තිරසාරත්වය සහ පාරිසරික බලපෑම පිළිබඳව සාකච්ඡා කරනු ඇත.
තිරසාර බව:
තිරසාර බව යනු අනාගත පරපුරේ අවශ්යතා සපුරාලීමට ඇති හැකියාවට බාධාවක් නොවන පරිදි වර්තමාන අවශ්යතා සපුරාලීමයි. එන්නත් අච්චුවෙහි තිරසාර ප්රතිලාභ කිහිපයක් ඇත:
- ද්රව්ය කාර්යක්ෂමතාව:එන්නත් අච්චුව අවම ද්රව්යමය අපද්රව්ය සහිත කොටස් නිෂ්පාදනය කරයි, කොටස් සෑදීමට අවශ්ය ද්රව්ය අඩු කරයි.
- බලශක්ති කාර්යක්ෂමතාව:යන්ත්රකරණය සහ වාත්තු කිරීම වැනි අනෙකුත් නිෂ්පාදන ක්රමවලට වඩා ඉන්ජෙක්ෂන් මෝල්ඩින් කොටස් නිෂ්පාදනය කිරීමට අඩු ශක්තියක් අවශ්ය වේ.
- දිගු ආයු කාලය: ඉන්ජෙක්ෂන් මෝල්ඩින් මගින් නිපදවන කොටස් කල් පවතින හා කල් පවතින ඒවා වන අතර, නිතර නිතර ප්රතිස්ථාපනය කිරීමේ අවශ්යතාව අඩු කරයි.
පාරිසරික බලපෑම:
එන්නත් අච්චු ගැසීම සලකා බැලිය යුතු පාරිසරික බලපෑම් ද ඇත. එන්නත් අච්චු ගැසීමේ ධනාත්මක සහ negative ණාත්මක පාරිසරික බලපෑම් කිහිපයක් මෙන්න:
ධනාත්මක පාරිසරික බලපෑම:
- ප්රතිචක්රීකරණය: ප්ලාස්ටික් වැනි බොහෝ ඉන්ජෙක්ෂන් මෝල්ඩින් ද්රව්ය ප්රතිචක්රීකරණය කළ හැකි අතර, කුණු ගොඩවල් වෙත යවන අපද්රව්ය අඩු කරයි.
- පහළ කාබන් අඩිපාර:ඉන්ජෙක්ෂන් මෝල්ඩින් යන්ත්රකරණය සහ වාත්තු කිරීම වැනි අනෙකුත් නිෂ්පාදන ක්රමවලට වඩා අඩු හරිතාගාර වායු විමෝචනයක් නිපදවයි.
ඍණාත්මක පාරිසරික බලපෑම:
- පුනර්ජනනීය නොවන සම්පත් භාවිතය:එන්නත් අච්චු ගැසීම පුනර්ජනනීය නොවන සම්පත් වලින් ලබාගත් ප්ලාස්ටික් වැනි ඛනිජ තෙල් මත පදනම් වූ ද්රව්ය භාවිතා කරයි.
- අපද්රව්ය නිෂ්පාදනය:ඉන්ජෙක්ෂන් මෝල්ඩින් වෙනත් නිෂ්පාදන ක්රමවලට වඩා අඩු අපද්රව්ය නිපදවන නමුත්, එය තවමත් ඉවතලන ද්රව්ය සහ ඇසුරුම් අපද්රව්ය වැනි අපද්රව්ය නිපදවයි.
එන්නත් අච්චු ගැසීමේ තිරසාර පිළිවෙත්:
එන්නත් අච්චු ගැසීමේ ඍණාත්මක පාරිසරික බලපෑම අවම කිරීම සඳහා, නිෂ්පාදකයින්ට තිරසාර භාවිතයන් ක්රියාත්මක කළ හැකිය:
- ප්රතිචක්රීකරණය කරන ලද ද්රව්ය භාවිතය:නිෂ්පාදකයින්ට ප්රතිචක්රීකරණය කරන ලද ද්රව්ය ඔවුන්ගේ එන්නත් අච්චු සැකසීමේ ක්රියාවලියේදී භාවිතා කළ හැකි අතර, කුණු ගොඩවල් වෙත යවන අපද්රව්ය අඩු කරයි.
- පුනර්ජනනීය බලශක්ති භාවිතය:නිෂ්පාදකයින්ට ඔවුන්ගේ ඉන්ජෙක්ෂන් මෝල්ඩින් යන්ත්ර බල ගැන්වීමට, හරිතාගාර වායු විමෝචනය අඩු කිරීමට සූර්ය හෝ සුළං බලය වැනි පුනර්ජනනීය බලශක්ති ප්රභවයන් භාවිතා කළ හැකිය.
- අපද්රව්ය අඩු කිරීම:නිෂ්පාදකයින්ට නැවත භාවිතා කළ හැකි ඇසුරුම් භාවිතා කිරීම සහ නිෂ්පාදනය කරන ලද පරණ ද්රව්ය ප්රමාණය අඩු කිරීම වැනි අපද්රව්ය අඩු කිරීමේ ක්රම ක්රියාත්මක කළ හැකිය.
කාර්යක්ෂමතාව සඳහා ස්වයංක්රීය ඉන්ජෙක්ෂන් මෝල්ඩින් ක්රියාවලි
නිෂ්පාදන කර්මාන්තයේ දී, තරඟකාරීව හා ලාභදායීව සිටීම සඳහා කාර්යක්ෂමතාව ඉතා වැදගත් වේ. එන්නත් අච්චු කිරීම යනු උණු කළ ද්රව්ය අච්චුවකට එන්නත් කිරීමෙන් කොටස් නිෂ්පාදනය කිරීම ඇතුළත් ජනප්රිය නිෂ්පාදන ක්රමයකි. ස්වයංක්රීය ඉන්ජෙක්ෂන් මෝල්ඩින් ක්රියාවලීන් කාර්යක්ෂමතාව සහ ඵලදායිතාව සැලකිය යුතු ලෙස වැඩිදියුණු කළ හැකිය. මෙම බ්ලොග් සටහනෙන්, කාර්යක්ෂමතාව සඳහා එන්නත් අච්චු සැකසීමේ ක්රියාවලීන් ස්වයංක්රීය කිරීමේ ප්රතිලාභ අපි සාකච්ඡා කරමු.
ඉන්ජෙක්ෂන් මෝල්ඩින් ක්රියාවලීන් ස්වයංක්රීය කිරීමේ ප්රතිලාභ:
ඉන්ජෙක්ෂන් මෝල්ඩින් ක්රියාවලීන් ස්වයංක්රීය කිරීමේ ප්රතිලාභ කිහිපයක් මෙන්න:
- වැඩි වූ වේගය:ස්වයංක්රීයකරණය මඟින් එන්නත් අච්චු සැකසීමේ ක්රියාවලීන්ගේ වේගය සැලකිය යුතු ලෙස වැඩි කළ හැකිය. ස්වයංක්රීය යන්ත්රවලට අතින් යන්ත්රවලට වඩා වැඩි වේගයකින් කොටස් නිෂ්පාදනය කළ හැකිය.
- අනුකූලතාව:ස්වයංක්රීය ඉන්ජෙක්ෂන් මෝල්ඩින් යන්ත්රවල ගුණාත්මක භාවය සහ විශ්වසනීයත්වය සහතික කරමින් අවම විචල්යයන් සහිත ස්ථාවර කොටස් නිෂ්පාදනය කරයි.
- වැඩිදියුණු කළ නිරවද්යතාවය:ස්වයංක්රීය යන්ත්රවල ඉහළ නිරවද්යතාවයක් සහ නිරවද්යතාවයක් ඇත, තද ඉවසීම් සහ සංකීර්ණ ජ්යාමිතිය සහිත කොටස් නිෂ්පාදනය කරයි.
- අඩු කළ ශ්රම පිරිවැය:ස්වයංක්රීය ඉන්ජෙක්ෂන් මෝල්ඩින් ක්රියාවලීන් ශ්රම පිරිවැය අඩු කිරීම, අතින් ශ්රමය සඳහා අවශ්යතාවය අඩු කළ හැකිය.
- වැඩි දියුණු කළ ආරක්ෂාව:ස්වයංක්රීය යන්ත්ර මගින් මිනිසුන්ට අනතුරුදායක කාර්යයන් ඉටු කළ හැකි අතර නිෂ්පාදන පරිසරයේ ආරක්ෂාව වැඩි දියුණු කරයි.
- ද්රව්යමය අපද්රව්ය අඩු කිරීම:ස්වයංක්රීය යන්ත්ර මඟින් අවම ද්රව්යමය අපද්රව්ය සහිත කොටස් නිෂ්පාදනය කළ හැකි අතර, ද්රව්ය පිරිවැය සහ පාරිසරික බලපෑම අඩු කරයි.
ස්වයංක්රීය ඉන්ජෙක්ෂන් මෝල්ඩින් ක්රියාවලි:
එන්නත් අච්චු සැකසීමේ ක්රියාවලීන් ස්වයංක්රීය කිරීමට ක්රම කිහිපයක් මෙන්න:
- රොබෝ ස්වයංක්රීයකරණය:රොබෝවරුන්ට කොටස් පැටවීම සහ බෑම, කොටස් පරීක්ෂා කිරීම සහ නිමි භාණ්ඩ ඇසුරුම් කිරීම වැනි කාර්යයන් කළ හැකිය. රොබෝ ස්වයංක්රීයකරණය මඟින් ඉන්ජෙක්ෂන් මෝල්ඩින් ක්රියාවලීන්හි වේගය සහ නිරවද්යතාවය සැලකිය යුතු ලෙස වැඩි කළ හැකිය.
- ස්වයංක්රීය ද්රව්ය හැසිරවීම:ස්වයංක්රීය ද්රව්ය හැසිරවීමේ පද්ධති මඟින් ඉන්ජෙක්ෂන් මෝල්ඩින් යන්ත්රයට ද්රව්ය ප්රවාහනය කළ හැකි අතර, අතින් ශ්රමයේ අවශ්යතාවය අඩු කරයි.
- ස්වයංක්රීය තත්ත්ව පාලනය:ස්වයංක්රීය තත්ත්ව පාලන පද්ධති මඟින් දෝෂ සහ අපගමනය සඳහා කොටස් පරීක්ෂා කළ හැකි අතර, ස්ථාවර තත්ත්ව සහතික කිරීම සහ අතින් පරීක්ෂා කිරීමේ අවශ්යතාවය අඩු කරයි.
- තත්ය කාලීන අධීක්ෂණය: මෙම පද්ධතිවලට යන්ත්ර ක්රියාකාරිත්වය නිරීක්ෂණය කිරීමට සහ තත්ය කාලීන ගැටළු හඳුනා ගැනීමට, අක්රිය කාලය අඩු කිරීමට සහ කාර්යක්ෂමතාව වැඩි කිරීමට හැකිය.
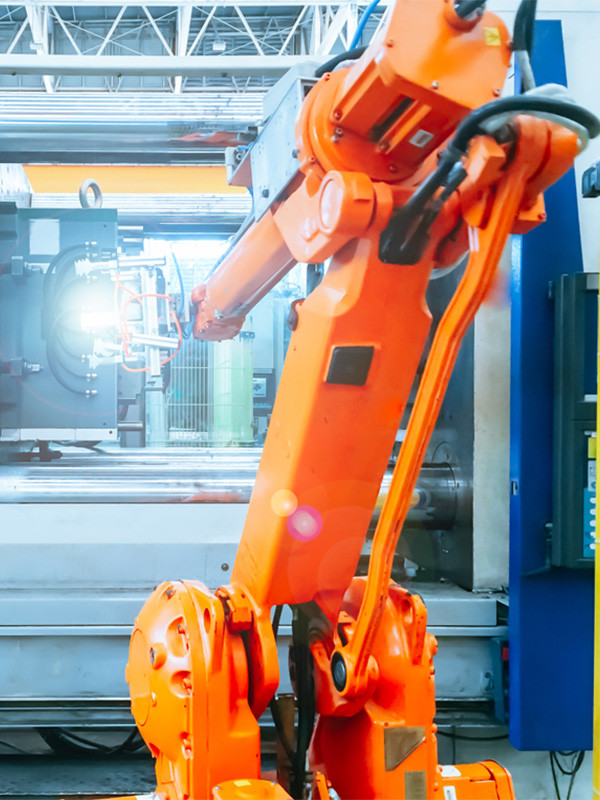
ඉන්ජෙක්ෂන් මෝල්ඩින් ක්රියාවලීන් ස්වයංක්රීය කිරීමේ අභියෝග:
ඉන්ජෙක්ෂන් මෝල්ඩින් ක්රියාවලීන් ස්වයංක්රීය කිරීම ප්රතිලාභ රාශියක් ඇතත්, එය සමහර අභියෝග ද ඉදිරිපත් කරයි:
- ඉහළ පෙර වියදම්:ඉන්ජෙක්ෂන් මෝල්ඩින් ක්රියාවලීන් ස්වයංක්රීය කිරීම උපකරණවල පිරිවැය සහ ක්රියාත්මක කිරීම හේතුවෙන් මිල අධික විය හැකිය.
- සංකීර්ණත්වය වැඩි වීම:ස්වයංක්රීය පද්ධති අතින් පද්ධති වලට වඩා සංකීර්ණ වන අතර විශේෂිත පුහුණුවක් සහ නඩත්තුවක් අවශ්ය වේ.
- අඩු කළ නම්යශීලිත්වය:ස්වයංක්රීය පද්ධති අතින් පද්ධති වලට වඩා නම්යශීලී නොවන අතර නිෂ්පාදන අවශ්යතා වල වෙනස්කම් වලට අනුවර්තනය වීම අභියෝගාත්මක වේ.
වාහන ප්ලාස්ටික් සංරචක එන්නත් අච්චු ගැසීමේ අභියෝග සහ සීමාවන්
කෙසේ වෙතත්, මෝටර් රථ ප්ලාස්ටික් සංරචක සඳහා එන්නත් අච්චු භාවිතා කිරීමේදී සමහර අභියෝග සහ සීමාවන් සලකා බැලිය යුතුය. මෙම බ්ලොග් සටහනෙන්, අපි මෝටර් රථ ප්ලාස්ටික් සංරචක එන්නත් අච්චු ගැසීමේ අභියෝග සහ සීමාවන් කිහිපයක් සාකච්ඡා කරමු.
වාහන ප්ලාස්ටික් සංරචක එන්නත් අච්චු ගැසීමේ අභියෝග:
වාහන ප්ලාස්ටික් සංරචක එන්නත් අච්චු ගැසීමේ අභියෝග කිහිපයක් මෙන්න:
- ද්රව්ය තෝරාගැනීම:ඉන්ජෙක්ෂන් මෝල්ඩින් ඔටෝමෝටිව් ප්ලාස්ටික් සංරචක සඳහා නිවැරදි ද්රව්ය තෝරාගැනීම අභියෝගාත්මක විය හැකිය. ද්රව්යය ශක්තිමත්, කල්පවත්නා විය යුතු අතර ආන්තික උෂ්ණත්ව හා දරුණු පාරිසරික තත්ත්වයන්ට ඔරොත්තු දිය යුතුය.
- මෙවලම් පිරිවැය:ඉන්ජෙක්ෂන් මෝල්ඩින් සඳහා මෙවලම් පිරිවැය මිල අධික විය හැකිය, විශේෂයෙන් සංකීර්ණ මෝස්තර සහිත සංකීර්ණ කොටස් සඳහා.
- කොටස් නිර්මාණය:ඉන්ජෙක්ෂන් මෝල්ඩින් සඳහා කොටස් සැලසුම් කිරීම අභියෝගාත්මක විය හැකිය, සැලසුම අච්චු ගැසීම, හැකිලීම සහ විකෘති කිරීම වැනි සාධක සලකා බැලිය යුතුය.
- තත්ත්ව පාලනය:ද්රව්ය, ක්රියාවලි සහ මෙවලම් විචලනයන් හේතුවෙන් එන්නත් කරන ලද මෝටර් රථ ප්ලාස්ටික් සංරචකවල ස්ථාවර ගුණාත්මක භාවය සහ ක්රියාකාරීත්වය සහතික කිරීම අභියෝගාත්මක විය හැකිය.
ඔටෝමෝටිව් ප්ලාස්ටික් සංරචක එන්නත් අච්චු ගැසීමේ සීමාවන්:
වාහන ප්ලාස්ටික් සංරචක එන්නත් අච්චු ගැසීමේ සීමාවන් කිහිපයක් මෙන්න:
- ප්රමාණයේ සීමාවන්:එන්නත් අච්චු ගැසීමේ ප්රමාණයේ සීමාවන් ඇති අතර, ඉන්ජෙක්ෂන් මෝල්ඩින් භාවිතයෙන් විශාල වාහන ප්ලාස්ටික් සංරචක නිෂ්පාදනය කිරීමට නොහැකි විය හැක.
- නිෂ්පාදන පරිමාව:ඉන්ජෙක්ෂන් මෝල්ඩින් ඉහළ-පරිමා නිෂ්පාදනය සඳහා වඩාත් සුදුසු වන අතර අඩු-පරිමා නිෂ්පාදනය සඳහා පිරිවැය-ඵලදායී නොවිය හැක.
- සංකීර්ණත්වය:බහු ද්රව්ය හෝ එකලස් කිරීම අවශ්ය සංකීර්ණ ජ්යාමිතිය හෝ මෝස්තර සහිත කොටස් සඳහා එන්නත් අච්චුව නුසුදුසුය.
- පාරිසරික බලපෑම:එන්නත් අච්චුව අපද්රව්ය නිපදවන අතර පරිසරයට හානි කළ හැකි පුනර්ජනනීය නොවන සම්පත් භාවිතා කරයි.
අභියෝග සහ සීමාවන් ජය ගැනීම:
මෝටර් රථ ප්ලාස්ටික් සංරචක එන්නත් අච්චු ගැසීමේ අභියෝග සහ සීමාවන් ජය ගැනීමට ක්රම කිහිපයක් මෙන්න:
- ද්රව්ය තෝරාගැනීම:ඉන්ජෙක්ෂන් මෝල්ඩින් සඳහා නිවැරදි ද්රව්ය තෝරා ගැනීම සඳහා කොටසෙහි අවශ්යතා සහ කාර්ය සාධනය ප්රවේශමෙන් සලකා බැලීම අවශ්ය වේ. කොටසෙහි නිශ්චිත අවශ්යතා සපුරාලන ද්රව්ය තෝරාගැනීම සඳහා නිෂ්පාදකයින්ට සැපයුම්කරුවන් සමඟ වැඩ කළ හැකිය.
- මෙවලම් පිරිවැය:උසස් තත්ත්වයේ මෙවලම් සඳහා ආයෝජනය කිරීමෙන් අක්රීය කාලය අඩු කිරීමෙන් සහ ඵලදායිතාව වැඩි කිරීමෙන් දිගු කාලීනව පිරිවැය අඩු කළ හැකිය.
- කොටස් නිර්මාණය:ඉන්ජෙක්ෂන් මෝල්ඩින් සඳහා කොටස් නිර්මාණය ප්රශස්ත කිරීම සඳහා ඉන්ජෙක්ෂන් මෝල්ඩින් භාවිතයෙන් කොටස කාර්යක්ෂමව හා ඵලදායී ලෙස නිෂ්පාදනය කළ හැකි බව සහතික කිරීම සඳහා නිර්මාණකරුවන්, ඉංජිනේරුවන් සහ නිෂ්පාදන විශේෂඥයින් අතර සහයෝගීතාව අවශ්ය වේ.
- තත්ත්ව පාලනය:ස්වයංක්රීය තත්ත්ව පාලන පද්ධති ක්රියාත්මක කිරීම මගින් අනුකූලතාව වැඩි දියුණු කිරීමට සහ අර්ධ ගුණාත්මක භාවයේ විචල්යතාවය අඩු කිරීමට හැකි වේ.
ඉන්ජෙක්ෂන් මෝල්ඩින් තාක්ෂණයේ නවෝත්පාදන
එන්නත් අච්චුව යනු සංකීර්ණ ප්ලාස්ටික් කොටස් නිෂ්පාදනය කිරීම සඳහා බහුලව භාවිතා වන නිෂ්පාදන ක්රියාවලියකි. එයට උණු කළ ප්ලාස්ටික් ද්රව්ය ඉහළ පීඩනයක් යටතේ අච්චුවකට ඇතුළු කර අවශ්ය හැඩය සෑදීමට එය සිසිල් කිරීම ඇතුළත් වේ. නිෂ්පාදන කර්මාන්තයේ නිරවද්යතාවය සහ කාර්යක්ෂමතාව සඳහා වැඩිවන ඉල්ලුමත් සමඟ, එන්නත් අච්චු තාක්ෂණයේ නවෝත්පාදනයන් මෙම අවශ්යතා සපුරාලීම සඳහා තීරණාත්මක කාර්යභාරයක් ඉටු කර ඇත. මෙම බ්ලොග් සටහනෙහි, අපි එන්නත් අච්චු තාක්ෂණයේ නවතම වර්ධනයන් කිහිපයක් ගවේෂණය කරන්නෙමු.
- ක්ෂුද්ර එන්නත් අච්චුව: මෙම තාක්ෂණයෙන් මයික්රෝන කිහිපයක් තරම් අඩු ඉවසීමක් සහිත අතිශය කුඩා කොටස් නිෂ්පාදනය කිරීමට හැකියාව ලැබේ. කුඩා, සංකීර්ණ කොටස් සඳහා ඉල්ලුම වැඩි වන වෛද්ය සහ ඉලෙක්ට්රොනික කර්මාන්ත සඳහා ක්ෂුද්ර එන්නත් අච්චුව විශේෂයෙන් ප්රයෝජනවත් වේ.
- බහු සංරචක වාත්තු කිරීම: මෙම ක්රියාවලියට විවිධ ද්රව්ය එකම අච්චුවකට එන්නත් කිරීම, බහු වර්ණ හෝ ද්රව්ය සහිත කොටස් නිෂ්පාදනය කිරීමට ඉඩ සලසයි. මෙම තාක්ෂණය මෝටර් රථ සහ පාරිභෝගික භාණ්ඩ කර්මාන්තයේ බහුලව භාවිතා වේ.
- අච්චුව තුළ සැරසිලි:මෙම තාක්ෂණයට එන්නත් අච්චු ගැසීමේදී අච්චු කරන ලද කොටස් වලට ග්රැෆික්ස්, වයනය සහ රටා එකතු කිරීම ඇතුළත් වේ. අච්චුව තුළ ඇති සැරසිලි අතිරේක සැකසුම් නොමැතිව උසස් තත්ත්වයේ නිමාවක් ලබා ගැනීම සඳහා ලාභදායී ක්රමයකි.
- සම-එන්නත් අච්චුව: මෙම තාක්ෂණය එකවර ද්රව්ය දෙකක් එන්නත් කරයි, සමක් සහ හර ද්රව්යයක් සහිත කොටසක් නිර්මාණය කරයි. සම-ඉන්ජෙක්ෂන් මෝල්ඩින් මෘදු ස්පර්ශ හැඟීමක් හෝ වැඩි දියුණු කළ යාන්ත්රික ගුණ සහිත කොටස් නිර්මාණය කිරීම සඳහා ප්රයෝජනවත් වේ.
- ගෑස් ආධාරක එන්නත් අච්චුව:මෙම තාක්ෂණයට එන්නත් අච්චු ගැසීමේදී වායුවක්, සාමාන්යයෙන් නයිට්රජන්, අච්චුවට එන්නත් කිරීම ඇතුළත් වේ. වායුව කොටස තුළ නාලිකා සාදයි, ද්රව්යමය භාවිතය අඩු කිරීම සහ නිෂ්පාදන කාර්ය සාධනය වැඩි දියුණු කිරීම.
- අධිවේගී එන්නත් අච්චුව:මෙම තාක්ෂණය වේගවත් එන්නත් කිරීමේ වේගය සහ චක්ර කාලය, නිෂ්පාදන කාර්යක්ෂමතාව වැඩි කිරීම සහ පිරිවැය අඩු කරයි. සිහින් බිත්ති සහිත කොටස් නිෂ්පාදනය කිරීමේදී අධිවේගී එන්නත් අච්චුව විශේෂයෙන් ප්රයෝජනවත් වේ.
- බුද්ධිමත් අච්චුව: මෙම තාක්ෂණය ඉන්ජෙක්ෂන් මෝල්ඩින් ක්රියාවලිය ප්රශස්ත කිරීම සඳහා සංවේදක සහ දත්ත විශ්ලේෂණ භාවිතා කරයි. උෂ්ණත්වය, පීඩනය සහ ද්රව්ය ප්රවාහය වැනි සාධක අධීක්ෂණය කිරීමෙන් නිෂ්පාදනයේ ගුණාත්මක භාවය වැඩිදියුණු කිරීමට සහ නාස්තිය අඩු කිරීමට බුද්ධිමත් අච්චුවකට හැකිය.
යෙදුම් අවධානය: අභ්යන්තර ප්ලාස්ටික් සංරචක
මෝටර් රථ කර්මාන්තය තුළ, උසස් රියදුරු අත්දැකීමක් ලබා දීම සඳහා අභ්යන්තර නිර්මාණය සහ ක්රියාකාරිත්වය අත්යවශ්ය වේ. අභ්යන්තර ප්ලාස්ටික් සංරචක මෙම අරමුණ සාක්ෂාත් කර ගැනීම සඳහා තීරනාත්මක කාර්යභාරයක් ඉටු කරයි, සුවපහසුව, ශෛලිය සහ කල්පැවැත්ම ලබා දෙයි. මෙම බ්ලොග් සටහන මෝටර් රථ අභ්යන්තරයේ බහුලව භාවිතා වන ප්ලාස්ටික් සංරචක කිහිපයක් ගවේෂණය කරනු ඇත.
- උපකරණ පුවරුව: උපකරණ පුවරුව යනු මැනුම්, වායු විවරයන්, තොරතුරු රසාස්වාදය පද්ධති සහ අනෙකුත් වැදගත් පාලනයන් ඇතුළත් ප්රමුඛ අභ්යන්තර අංගයකි. ප්ලාස්ටික් සංරචක ඒවායේ කල්පැවැත්ම, සැලසුම් නම්යශීලීභාවය සහ සැකසීමේ පහසුව හේතුවෙන් උපකරණ පුවරු නිෂ්පාදනය සඳහා බහුලව භාවිතා වේ.
- දොර පුවරු:අභ්යන්තර සැලසුම සඳහා දොර පැනල් අත්යවශ්ය වන අතර ආරක්ෂාව සහ සුවපහසුව සපයයි. බලපෑමට ඔරොත්තු දීමේ හැකියාව, ශබ්දය අඩු කිරීම සහ සැහැල්ලු ගුණාංග නිසා ප්ලාස්ටික් සංරචක බොහෝ විට දොර පැනල් නිර්මාණය කිරීමට යොදා ගනී.
- ආසන:මෝටර් රථ ආසන සඳහා සුවපහසුව සහ සහාය ලබා දෙන ඉහළ කාර්යසාධන ද්රව්ය අවශ්ය වේ. ආසන පිටුපස, අත්වාරු සහ ආසන ව්යුහයේ අනෙකුත් කොටස් නිර්මාණය කිරීම සඳහා ප්ලාස්ටික් සංරචක භාවිතා වේ. මෙම සංරචක ශක්තිය සහ නම්යශීලී බවක් ලබා දෙන අතර විවිධ මෝස්තරවලට අනුකූල වන පරිදි පහසුවෙන් හැඩගස්වා ගත හැකිය.
- මධ්ය කොන්සෝලය:මධ්ය කොන්සෝලය දේශගුණ පාලනය, ශ්රව්ය පද්ධති සහ ගබඩා වැනි අත්යවශ්ය පාලන සඳහා කේන්ද්රස්ථානයකි. තාපය, ආර්ද්රතාවය සහ අනෙකුත් පාරිසරික සාධකවලට ඔරොත්තු දීමේ හැකියාව හේතුවෙන් මධ්ය කොන්සෝල නිර්මාණය කිරීම සඳහා ප්ලාස්ටික් සංරචක බහුලව භාවිතා වේ.
- පුවරු කපා දමන්න: කුළුණු, හෙඩ්ලයිනර් සහ ආසන පිටුපස වැනි වාහනයේ අභ්යන්තර ප්රදේශ ආවරණය කිරීමට ටිම් පැනල් භාවිතා කරයි. මෙම පුවරු නිර්මාණය කිරීම සඳහා ප්ලාස්ටික් සංරචක භාවිතා කරනුයේ ඒවායේ සැලසුම් නම්යශීලී බව, වර්ණ විවිධත්වය සහ සැකසීමේ පහසුව නිසාය.
යෙදුම් අවධානය: බාහිර ප්ලාස්ටික් සංරචක
මෝටර් රථ කර්මාන්තයේ බාහිර ප්ලාස්ටික් සංරචක වැඩි වැඩියෙන් පොදු වී ඇත. සැහැල්ලු ද්රව්ය සඳහා ඇති ඉල්ලුම, වැඩි දියුණු කළ ඉන්ධන කාර්යක්ෂමතාව සහ නව්ය සැලසුම් සමඟ, ප්ලාස්ටික් උපාංග වාහනවල විවිධ බාහිර කොටස් නිෂ්පාදනය සඳහා ජනප්රිය තේරීමක් බවට පත්ව ඇත. මෙම බ්ලොග් සටහනේ, අපි මෝටර් රථ කර්මාන්තයේ බහුලව භාවිතා වන බාහිර ප්ලාස්ටික් සංරචක කිහිපයක් ගවේෂණය කරන්නෙමු.
- බම්පර්: බම්පර් යනු ගැටීමකදී වාහනය ආරක්ෂා කරන තීරණාත්මක බාහිර සංරචකයකි. බම්පර් නිෂ්පාදනය සඳහා ප්ලාස්ටික් සංරචක බොහෝ විට භාවිතා කරනුයේ ඒවා සැහැල්ලු, බලපෑම්-ප්රතිරෝධී සහ පිරිවැය-ඵලදායී බැවිනි.
- ග්රිල්ස්: ග්රිල් යනු වාහනයේ කැපී පෙනෙන බාහිර අංගයක් වන අතර, එය එහි සමස්ත සැලසුම සහ වායුගතිකත්වය තුළ වැදගත් කාර්යභාරයක් ඉටු කරයි. ප්ලාස්ටික් සංරචක ඒවායේ සැලසුම් නම්යශීලී බව සහ සංකීර්ණ හැඩතලවලට හැඩගැස්වීමේ හැකියාව හේතුවෙන් ග්රිල් නිෂ්පාදනය සඳහා බහුලව භාවිතා වේ.
- බාහිර සැරසිලි:වාහනයේ පෙනුම වැඩි දියුණු කරන මෝල්ඩින්, ෆෙන්ඩර් ෆ්ලෙයාර්ස් සහ අනෙකුත් අලංකරණ උපාංග බාහිර සැරසිලි ඇතුළත් වේ. මෙම සැරසිලි නිෂ්පාදනය කිරීම සඳහා ප්ලාස්ටික් සංරචක බොහෝ විට භාවිතා කරනුයේ ඒවා වර්ණ හා වයනය කළ හැකි නිසා, පුළුල් පරාසයක සැලසුම් විකල්පයන් සපයයි.
- දර්පණ: දර්පණ යනු ඕනෑම වාහනයක අත්යවශ්ය අංගයකි, දෘශ්යතාව සහ ආරක්ෂාව සපයයි. ප්ලාස්ටික් සංරචක ඒවායේ සැහැල්ලු ගුණාංග, බලපෑම් ප්රතිරෝධය සහ සැලසුම් නම්යශීලීභාවය හේතුවෙන් දර්පණ නිවාස නිෂ්පාදනය සඳහා බොහෝ විට භාවිතා වේ.
- ස්පොයිලර්: ස්පොයිලර් යනු බොහෝ වාහන සඳහා ජනප්රිය එකතු කිරීමකි, වායුගතිකත්වය වැඩිදියුණු කිරීම සහ සමස්ත පෙනුම වැඩි දියුණු කිරීම. ස්පොයිලර් නිෂ්පාදනය සඳහා ප්ලාස්ටික් සංරචක බොහෝ විට භාවිතා කරනුයේ ඒවායේ සැහැල්ලු සහ සැලසුම් නම්යශීලී බව හේතුවෙනි.
ඔටෝමෝටිව් ප්ලාස්ටික් සංරචක එන්නත් මෝල්ඩින්ගේ අනාගතය
ඔටෝමෝටිව් ප්ලාස්ටික් උපාංග එන්නත් අච්චු ගැසීම මෝටර් රථ කර්මාන්තයේ වඩ වඩාත් වැදගත් වී ඇත. තාක්ෂණය අඛණ්ඩව දියුණු වන විට, මෙම ක්රියාවලියේ අනාගතය යහපත් බව පෙනේ. මෝටර් රථ ප්ලාස්ටික් සංරචක එන්නත් අච්චු ගැසීමේ අනාගතය සඳහා ප්රවණතා සහ අනාවැකි කිහිපයක් මෙන්න:
- සැහැල්ලු ද්රව්ය භාවිතය වැඩි කිරීම: කාබන් ෆයිබර් සහ තාප ප්ලාස්ටික් වැනි සැහැල්ලු ද්රව්ය මෝටර් රථ කර්මාන්තයේ වැඩි වැඩියෙන් ජනප්රිය වෙමින් පවතී. මෙයට හේතුව ඉන්ධන කාර්යක්ෂමතාව, කාර්ය සාධනය සහ අඩු විමෝචනය අනුව ඒවායේ ප්රතිලාභය. එහි ප්රතිඵලයක් වශයෙන්, මෙම සැහැල්ලු ද්රව්ය නිෂ්පාදනය කිරීමේදී මෝටර් රථ ප්ලාස්ටික් සංරචක එන්නත් අච්චුව තීරණාත්මක කාර්යභාරයක් ඉටු කරනු ඇත.
- ආකලන නිෂ්පාදන ඒකාබද්ධ කිරීම:ත්රිමාණ මුද්රණය ලෙසද හැඳින්වෙන ආකලන නිෂ්පාදනය මෝටර් රථ කර්මාන්තයේ බහුලව දක්නට ලැබේ. සාම්ප්රදායික ඉන්ජෙක්ෂන් මෝල්ඩින් භාවිතයෙන් නිෂ්පාදනය කිරීමට අපහසු හෝ කළ නොහැකි සංකීර්ණ ජ්යාමිතීන් සහ හැඩතල නිර්මාණය කිරීමට මෙම තාක්ෂණය ඉඩ සලසයි. අනාගතයේදී, මෝටර් රථ ප්ලාස්ටික් සංරචක එන්නත් මෝල්ඩින් වඩාත් සංකීර්ණ මෝස්තර නිර්මාණය කිරීම සඳහා ආකලන නිෂ්පාදනය නිෂ්පාදනයට ඒකාබද්ධ කළ හැකිය.
- ස්වයංක්රීයකරණය වැඩි කිරීම: තාක්ෂණය දියුණු වන විට, ඉන්ජෙක්ෂන් මෝල්ඩින් ක්රියාවලියේ තවත් ස්වයංක්රීයකරණයක් දැකීමට අපට අපේක්ෂා කළ හැකිය. මෙය කාර්යක්ෂමතාව වැඩි කිරීමට සහ නිෂ්පාදන කාලය අඩු කිරීමට හේතු වේ. මීට අමතරව, ස්වයංක්රීයකරණයට මානව දෝෂ ඇතිවීමේ සම්භාවිතාව අඩු කළ හැකි අතර, එහි ප්රතිඵලයක් ලෙස උසස් තත්ත්වයේ නිෂ්පාදන ලැබේ.
- තවත් තිරසාර ද්රව්ය: මෝටර් රථ කර්මාන්තයේ තිරසාරභාවය වඩ වඩාත් වැදගත් කාරණයක් බවට පත්වෙමින් තිබේ. මෝටර් රථ ප්ලාස්ටික් සංරචක එන්නත් අච්චුව වඩාත් තිරසාර ද්රව්ය භාවිතා කිරීමෙන් මෙම ප්රවණතාවයට අනුවර්තනය වීමට අවශ්ය වනු ඇත. උදාහරණයක් ලෙස, අපද්රව්ය සහ කාබන් විමෝචනය අවම කිරීම සඳහා එන්නත් අච්චු සැකසීමේ ක්රියාවලියේදී ජෛව පාදක ප්ලාස්ටික් සහ ප්රතිචක්රීකරණය කරන ලද ද්රව්ය භාවිතා කළ හැකිය.
- වැඩි කළ අභිරුචිකරණය:අභිරුචිකරණය සහ පුද්ගලීකරණය සම්බන්ධයෙන් පාරිභෝගිකයින් වැඩි ඉල්ලුමක් ඇති කරයි. අනාගතයේ දී, මෝටර් රථ ප්ලාස්ටික් සංරචක එන්නත් මෝල්ඩින් නිෂ්පාදන වඩාත් අභිරුචිකරණය කිරීමට ඉඩ සලසන තාක්ෂණයන් ඇතුළත් විය හැක. ප්ලාස්ටික් සංරචකවල සැලසුම, වර්ණය සහ වයනය පුද්ගලීකරණය කිරීමේ හැකියාව මෙයට ඇතුළත් විය හැකිය.
- ස්මාර්ට් තාක්ෂණයන් ඒකාබද්ධ කිරීම: සංවේදක සහ ඉන්ටර්නෙට් ඔෆ් තින්ග්ස් (IoT) උපාංග වැනි ස්මාර්ට් තාක්ෂණයන් මෝටර් රථ කර්මාන්තයේ බහුලව දක්නට ලැබේ. අනාගතයේ දී, මෝටර් රථ ප්ලාස්ටික් සංරචක එන්නත් අච්චු මෙම තාක්ෂණයන් නිෂ්පාදනයට ඇතුළත් කළ හැකිය. මෙය වාහනයේ අනෙකුත් කොටස් සහ රියදුරු සමඟ සන්නිවේදනය කළ හැකි සංරචක නිර්මාණය කිරීමට ඉඩ සලසයි.
සිද්ධි අධ්යයනය: මෝටර් රථ කර්මාන්තයේ ඉන්ජෙක්ෂන් මෝල්ඩින් සාර්ථක ලෙස ක්රියාත්මක කිරීම
ඉන්ජෙක්ෂන් මෝල්ඩින් යනු මෝටර් රථ කර්මාන්තයේ වැඩි වැඩියෙන් ජනප්රිය වී ඇති බහුලව භාවිතා වන නිෂ්පාදන ක්රියාවලියකි. මෙම බ්ලොග් සටහනේදී, මෝටර් රථ කර්මාන්තයේ ඉන්ජෙක්ෂන් මෝල්ඩින් සාර්ථකව ක්රියාත්මක කිරීම පිළිබඳ සිද්ධි අධ්යයනයක් අපි සාකච්ඡා කරමු.
නඩුව: මෝටර් රථ ආලෝකකරණය
මෝටර් රථ කර්මාන්තයේ ඉන්ජෙක්ෂන් මෝල්ඩින් විශේෂයෙන් සාර්ථක වී ඇති එක් අංශයක් වන්නේ මෝටර් රථ ආලෝක උපාංග නිෂ්පාදනයයි. මෙම සිද්ධි අධ්යයනයේදී, ජනප්රිය සෙඩාන් මාදිලියක් සඳහා ටේලයිට් කාචයක් නිෂ්පාදනය කිරීම සඳහා ඉන්ජෙක්ෂන් මෝල්ඩින් ක්රියාත්මක කිරීම කෙරෙහි අපි අවධානය යොමු කරමු.
අභියෝග:
ටේලයිට් කාචයට පහත අවශ්යතා සපුරාලිය යුතුය:
- පාරජම්බුල කිරණ සහ කාලගුණයට ප්රතිරෝධය
- හොඳ දෘශ්ය පැහැදිලිතාව
- කල්පැවැත්ම
- සෞන්දර්යාත්මකව ප්රසන්න නිර්මාණය
- කාර්යක්ෂම නිෂ්පාදන කාලය
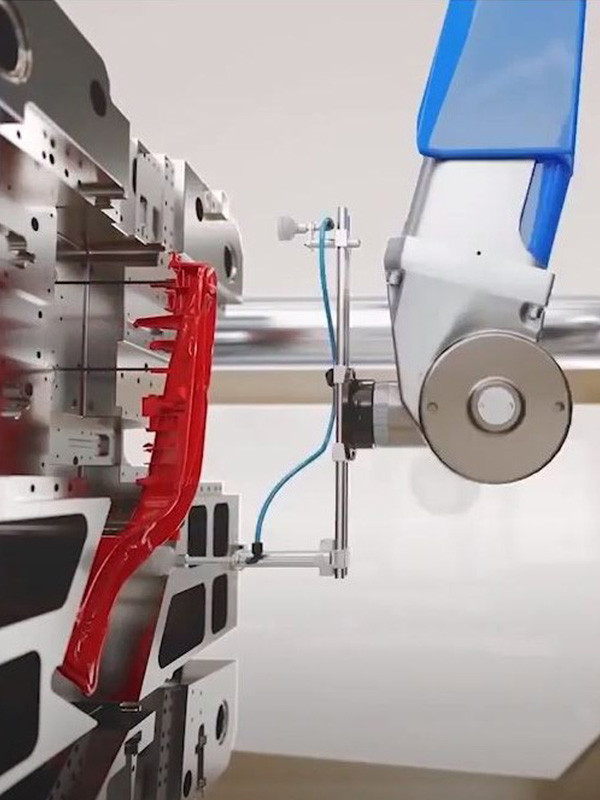
විසඳුමක්:
අවශ්යතා සහ අභියෝග විශ්ලේෂණය කිරීමෙන් පසුව, මෝටර් රථ ආලෝකකරණ නිෂ්පාදකයා ටේල් ලයිට් කාචය නිෂ්පාදනය සඳහා හොඳම විසඳුම ලෙස ඉන්ජෙක්ෂන් මෝල්ඩින් තෝරා ගත්තේය. නිෂ්පාදකයා උසස් තත්ත්වයේ මෝටර් රථ සංරචක නිෂ්පාදනය කිරීමේ වාර්තාවක් ඇති පළපුරුදු ඉන්ජෙක්ෂන් මෝල්ඩින් සමාගමක් සමඟ හවුල් විය.
එන්නත් අච්චු සැකසීමේ ක්රියාවලියට පහත පියවර ඇතුළත් වේ:
- ද්රව්ය තෝරාගැනීම:ටේලයිට් කාචය සඳහා UV-ප්රතිරෝධී පොලිකාබනේට් ද්රව්යයක් තෝරා ගන්නා ලදී.
- අච්චු නිර්මාණය:ඉන්ජෙක්ෂන් මෝල්ඩින් සමාගම අවශ්ය පිරිවිතරයන් සපුරාලීම සඳහා ටේලයිට් කාචය නිෂ්පාදනය කිරීම සඳහා අභිරුචි අච්චුවක් නිර්මාණය කළේය.
- එන්නත් අච්චුව:ඉන්ජෙක්ෂන් මෝල්ඩින් ක්රියාවලියේදී ටේලයිට් කාචය නිපදවීම සඳහා අච්චුව පසුව භාවිතා කරන ලදී.
- තත්ත්ව පාලනය:ටේලයිට් කාචය අවශ්ය ප්රමිතීන් සපුරාලීම සහතික කිරීම සඳහා දැඩි තත්ත්ව පාලන පියවරයන්ට යටත් විය.
ප්රතිපල:
ටේලයිට් කාච නිෂ්පාදනය සඳහා එන්නත් අච්චුව ක්රියාත්මක කිරීම සාර්ථක විය. මෝටර් රථ ආලෝකකරණ නිෂ්පාදකයා අවශ්ය සියලුම පිරිවිතරයන් සපුරාලන උසස් තත්ත්වයේ ටේල් ලයිට් කාචයක් නිෂ්පාදනය කළේය.
මෙම යෙදුම සඳහා එන්නත් අච්චු භාවිතා කිරීමේ ප්රතිලාභ ඇතුළත් වේ:
- ස්ථාවර ගුණාත්මකභාවය:ඉන්ජෙක්ෂන් මෝල්ඩින් අවශ්ය ප්රමිතීන්ට අනුකූල වන ටේලයිට් කාචයේ ස්ථාවර ගුණාත්මක භාවය සහතික කළේය.
- කාර්යක්ෂම නිෂ්පාදනය: ඉන්ජෙක්ෂන් මෝල්ඩින් ක්රියාවලිය ටේලයිට් කාචය කාර්යක්ෂමව නිෂ්පාදනය කිරීමට ඉඩ සලසන අතර එහි ප්රතිඵලයක් ලෙස නිෂ්පාදන කාලය සහ පිරිවැය අඩු විය.
- සෞන්දර්යාත්මකව ප්රසන්න නිර්මාණය:ඉන්ජෙක්ෂන් මෝල්ඩින් ටේලයිට් කාචය සඳහා සෞන්දර්යාත්මකව ප්රසන්න මෝස්තරයක් නිර්මාණය කිරීමට ඉඩ දී ඇත.
- කල් පවතින: ඉන්ජෙක්ෂන් මෝල්ඩින් මගින් නිපදවන ලද ටේලයිට් කාචය කල් පවතින අතර UV ආලෝකයට සහ කාලගුණයට ප්රතිරෝධී විය.
එන්නත් අච්චු කිරීම පිළිබඳ පොදු වැරදි වැටහීම්
ඉන්ජෙක්ෂන් මෝල්ඩින් යනු බහුලව භාවිතා වන නිෂ්පාදන ක්රියාවලියක් වන අතර එයට අවශ්ය හැඩයක් නිර්මාණය කිරීම සඳහා උණු කළ ද්රව්ය අච්චුවකට එන්නත් කිරීම ඇතුළත් වේ. කෙසේ වෙතත්, ඉන්ජෙක්ෂන් මෝල්ඩින් පිළිබඳ බොහෝ වැරදි වැටහීම් ක්රියාවලිය පිළිබඳ වැරදි වැටහීම් ඇති විය හැක. මෙම බ්ලොග් සටහන එන්නත් අච්චු ගැසීම පිළිබඳ පොදු වැරදි මත කිහිපයක් සාකච්ඡා කරනු ඇත.
වැරදි වැටහීම 1: එන්නත් අච්චු කිරීම සුදුසු වන්නේ විශාල නිෂ්පාදන ප්රමාණයක් නිෂ්පාදනය කිරීම සඳහා පමණි.
බොහෝ අය විශ්වාස කරන්නේ එන්නත් අච්චුව සුදුසු වන්නේ විශාල නිෂ්පාදන ප්රමාණයක් නිෂ්පාදනය කිරීම සඳහා පමණි. ඉන්ජෙක්ෂන් මෝල්ඩින් විශාල නිෂ්පාදන ප්රමාණයක් නිපදවිය හැකි අතර, එය කුඩා නිෂ්පාදන ධාවනය සඳහා ද භාවිතා කළ හැක. කුඩා හා මධ්යම ප්රමාණයේ නිෂ්පාදන ධාවනය සඳහා එන්නත් අච්චු කිරීම කාර්යක්ෂම හා ලාභදායී විය හැක.
වැරදි වැටහීම 2: එන්නත් අච්චු කිරීම මන්දගාමී ක්රියාවලියකි.
ඉන්ජෙක්ෂන් මෝල්ඩින් පිළිබඳ තවත් පොදු වැරදි වැටහීමක් වන්නේ එය මන්දගාමී ක්රියාවලියකි. ඉන්ජෙක්ෂන් මෝල්ඩින් කිරීම සඳහා නිශ්චිත සැකසුම් කාලයක් අවශ්ය බව සත්යයක් වුවද, ක්රියාවලිය ක්රියාත්මක වූ පසු, එය ඉක්මනින් හා කාර්යක්ෂමව නිෂ්පාදන විශාල ප්රමාණයක් නිෂ්පාදනය කළ හැකිය. මීට අමතරව, තාක්ෂණයේ දියුණුව වේගවත් එන්නත් අච්චු යන්ත්ර සහ ක්රියාවලීන් සඳහා ඉඩ ලබා දී ඇත.
වැරදි වැටහීම 3: ඉන්ජෙක්ෂන් මෝල්ඩින් සරල හැඩයන් නිෂ්පාදනය කිරීම සඳහා පමණක් සුදුසු වේ.
ඉන්ජෙක්ෂන් මෝල්ඩින් බොහෝ විට සරල හැඩතල නිපදවීම සමඟ සම්බන්ධ වේ, නමුත් මෙය අනිවාර්යයෙන්ම සත්ය නොවේ. අච්චු නිර්මාණය සහ ද්රව්ය තෝරාගැනීමේ දියුණුව එන්නත් අච්චුව හරහා වඩාත් සංකීර්ණ හැඩතල සහ මෝස්තර නිෂ්පාදනය කිරීමට ඉඩ ලබා දී ඇත. මීට අමතරව, ත්රිමාණ මුද්රණ සහ වෙනත් තාක්ෂණයන් ඒකාබද්ධ කිරීම එන්නත් අච්චු ගැසීමේ හැකියාව තවත් පුළුල් කර ඇත.
වැරදි වැටහීම 4: එන්නත් අච්චුව පරිසර හිතකාමී නොවේ.
එන්නත් අච්චු ගැසීම පරිසර හිතකාමී නොවන නිසා බොහෝ විට විවේචනයට ලක් වේ. ඉන්ජෙක්ෂන් මෝල්ඩින් මගින් යම් අපද්රව්ය නිර්මාණය කරන බව සත්යයක් වුවද, ද්රව්ය තෝරාගැනීමේ සහ ප්රතිචක්රීකරණ තාක්ෂණයේ දියුණුව එන්නත් අච්චු ගැසීම හරහා වඩාත් පරිසර හිතකාමී නිෂ්පාදන නිෂ්පාදනය කිරීමට ඉඩ ලබා දී ඇත. මීට අමතරව, ඉන්ජෙක්ෂන් මෝල්ඩින් නිෂ්පාදනවල කාබන් පියසටහන අඩු කිරීමට උපකාරී වන සැහැල්ලු සහ තිරසාර ද්රව්ය නිෂ්පාදනය කිරීමට ඉඩ සලසයි.
වැරදි වැටහීම 5: එන්නත් අච්චුව මිල අධිකයි.
බොහෝ අය විශ්වාස කරන්නේ ඉන්ජෙක්ෂන් මෝල්ඩින් මිල අධික නිෂ්පාදන ක්රියාවලියක් බවයි. අච්චු සැලසුම් කිරීම සහ නිෂ්පාදනය කිරීමේ පිරිවැය වැනි, එන්නත් අච්චු ගැසීම හා සම්බන්ධ ඇතැම් පූර්ව වියදම් ඇති බව සත්යයක් වුවද, නිෂ්පාදන පරිමාව වැඩි වන විට ඒකකයකට පිරිවැය අඩු වේ. මීට අමතරව, තාක්ෂණයේ දියුණුව නිසා ඉන්ජෙක්ෂන් මෝල්ඩින් වෙන කවරදාටත් වඩා ලාභදායී සහ කාර්යක්ෂම කර ඇත.
ඉන්ජෙක්ෂන් මෝල්ඩින් හි පොදු ගැටළු දෝශ නිරාකරණය කිරීම
ඉන්ජෙක්ෂන් මෝල්ඩින් යනු විවිධ කර්මාන්ත සඳහා උසස් තත්ත්වයේ ප්ලාස්ටික් සංරචක නිෂ්පාදනය කරන බහුලව භාවිතා වන නිෂ්පාදන ක්රියාවලියකි. කෙසේ වෙතත්, ඕනෑම නිෂ්පාදන ක්රියාවලියක් මෙන්, ඉන්ජෙක්ෂන් මෝල්ඩින් අවසන් නිෂ්පාදනයට අහිතකර ලෙස බලපාන පොදු ගැටළු අත්විඳිය හැකිය. මෙම බ්ලොග් සටහනේදී, එන්නත් අච්චු ගැසීමේ පොදු ගැටළු කිහිපයක් සහ ඒවා දෝශ නිරාකරණය කරන්නේ කෙසේද යන්න අපි සාකච්ඡා කරමු.
නිකුතුව 1: පිළිස්සුම් ලකුණු
ද්රව්යය අධික ලෙස රත් වීම නිසා දුම්මල දිරාපත්වීම සහ දුර්වර්ණ වීම හේතුවෙන් එන්නත් කරන ලද අච්චු කොටස්වල මතුපිට පිළිස්සුම් සලකුණු දිස්විය හැකිය. මෙම ගැටළුව විවිධ සාධක නිසා ඇති විය හැක, ඇතුළුව:
- ඉහළ දියවන උෂ්ණත්වය
- දිගු පදිංචි කාලය
- ප්රමාණවත් සිසිලන කාලය
- ඉහළ එන්නත් වේගය
පිළිස්සුම් ලකුණු දෝශ නිරාකරණය කිරීම සඳහා, නිෂ්පාදකයින් පහත පියවර සලකා බැලිය යුතුය:
- දියවන උෂ්ණත්වය අඩු කරන්න
- පදිංචි කාලය අඩු කරන්න
- සිසිලන කාලය වැඩි කරන්න
- එන්නත් කිරීමේ වේගය අඩු කරන්න
නිකුතුව 2: විකෘති කිරීම
ද්රව්යයේ අසමාන සිසිලනය හේතුවෙන් සිදුවිය හැකි එන්නත් අච්චු ගැසීමේදී විකෘති වීම පොදු ගැටළුවකි. මෙය එහි ක්රියාකාරීත්වයට සෘණාත්මකව බලපෑ හැකි අවසාන නිෂ්පාදනය විකෘති වීමට හෝ විකෘති කිරීමට හේතු විය හැක. මෙම ගැටළුව සාධක කිහිපයක් නිසා ඇති විය හැක, ඇතුළුව:
- අසමාන සිසිලනය
- ප්රමාණවත් ඇසුරුම් පීඩනය
- නුසුදුසු අච්චු නිර්මාණය
දෝශ නිරාකරණය කිරීම සඳහා, නිෂ්පාදකයින් පහත පියවර සලකා බැලිය යුතුය:
- අච්චුව පුරා ඒකාකාර සිසිලනය සහතික කරන්න
- ඇසුරුම් පීඩනය වැඩි කරන්න
- කොටස් ජ්යාමිතිය වැඩි දියුණු කිරීම සඳහා අච්චු නිර්මාණය වෙනස් කරන්න
නිකුතුව 3: සින්ක් ලකුණු
සින්ක් ලකුණු යනු අසමාන සිසිලනය හෝ ඇසුරුම් කිරීම හේතුවෙන් එන්නත් කරන ලද අච්චු කොටස් මතුපිට ඇති විය හැකි අවපාත වේ. මෙම ගැටළුව සාධක කිහිපයක් නිසා ඇති විය හැක, ඇතුළුව:
- ඉහළ එන්නත් වේගය
- ප්රමාණවත් ඇසුරුම් පීඩනය
- ඉහළ දියවන උෂ්ණත්වය
- දිගු පදිංචි කාලය
සින්ක් ලකුණු දෝශ නිරාකරණය කිරීම සඳහා, නිෂ්පාදකයින් පහත පියවර සලකා බැලිය යුතුය:
- එන්නත් කිරීමේ වේගය අඩු කරන්න
- ඇසුරුම් පීඩනය වැඩි කරන්න
- දියවන උෂ්ණත්වය අඩු කරන්න
- පදිංචි කාලය අඩු කරන්න
නිකුතුව 4: දැල්වීම
අතිරික්ත ද්රව්ය අච්චුවෙන් මිරිකන විට සිදු වන එන්නත් අච්චු ගැසීමේදී දැල්වීම පොදු ගැටළුවකි. මෙය අවසන් නිශ්පාදනයේ දාර වටා අතිරික්ත ද්රව්ය දිස්වීමට හේතු විය හැක, එහි සෞන්දර්යය හා ක්රියාකාරිත්වය සෘණාත්මකව බලපෑ හැකිය. මෙම ගැටළුව සාධක කිහිපයක් නිසා ඇති විය හැක, ඇතුළුව:
- නරක් වූ අච්චු සංරචක
- ප්රමාණවත් තද කිරීමේ බලය
- ප්රමාණවත් සිසිලන කාලය
දැල්වීම දෝශ නිරාකරණය කිරීම සඳහා, නිෂ්පාදකයින් පහත පියවර සලකා බැලිය යුතුය:
- නරක් වූ අච්චු සංරචක ප්රතිස්ථාපනය කරන්න
- කලම්ප බලය වැඩි කරන්න
- සිසිලන කාලය වැඩි කරන්න
විශේෂඥ තීක්ෂ්ණ බුද්ධිය: ඔටෝමෝටිව් ඉන්ජෙක්ෂන් මෝල්ඩින් පිළිබඳ කර්මාන්ත වෘත්තිකයන් සමඟ සම්මුඛ සාකච්ඡා
එන්නත් අච්චු ගැසීම මෝටර් රථ කර්මාන්තයේ තීරණාත්මක ක්රියාවලියක් වන අතර විවිධ වාහන කොටස්වල උසස් තත්ත්වයේ ප්ලාස්ටික් සංරචක නිෂ්පාදනය කරයි. කර්මාන්තය සහ එහි වත්මන් තත්ත්වය පිළිබඳ අවබෝධයක් ලබා ගැනීම සඳහා මෝටර් රථ එන්නත් අච්චු ගැසීම පිළිබඳ ඔවුන්ගේ විශේෂඥ අදහස් සහ තීක්ෂ්ණ බුද්ධිය බෙදාගත් කර්මාන්ත වෘත්තිකයන් සමඟ අපි කතා කළෙමු.
විශේෂඥ 1: ජෝන් ඩෝ, ඉන්ජෙක්ෂන් මෝල්ඩින් සමාගමක ප්රධාන විධායක නිලධාරී
- මෝටර් රථ කර්මාන්තයේ ජෛව ප්ලාස්ටික් භාවිතය වැඩි වැඩියෙන් ජනප්රිය වෙමින් පවතින බව ඩෝ බෙදා ගත්තේය. මෙම ප්ලාස්ටික් පරිසර හිතකාමී වන අතර වාහනයක කාබන් පියසටහන අඩු කළ හැකි අතර, ඒවා මෝටර් රථ නිෂ්පාදකයින් සඳහා ආකර්ෂණීය විකල්පයක් බවට පත් කරයි.
- ත්රිමාණ මුද්රණයේ දියුණුව වඩාත් සංකීර්ණ අච්චු නිර්මාණ සඳහා ඉඩ සලසා ඇති බවත්, එහි ප්රතිඵලයක් ලෙස උසස් තත්ත්වයේ අවසාන නිෂ්පාදන ඇති බවත් ඔහු සඳහන් කළේය.
- අභියෝග සම්බන්ධයෙන් ගත් කල, පුහුණු ශ්රම හිඟය කර්මාන්තයේ සැලකිය යුතු ප්රශ්නයක් ලෙස ඔහු සඳහන් කළේ ශ්රම පිරිවැය ඉහළ යාමට හේතු වන බවයි.
විශේෂඥ 2: ජේන් ස්මිත්, මෝටර් රථ සමාගමක නිර්මාණ ඉංජිනේරු
- ඉන්ධන කාර්යක්ෂමතාව වැඩි දියුණු කිරීම සහ විමෝචනය අවම කිරීම සඳහා සංයුති සහ ප්ලාස්ටික් වැනි සැහැල්ලු ද්රව්ය කෙරෙහි කර්මාන්තයේ වර්ධනය වන ප්රවණතාවක් පවතින බව ස්මිත් බෙදාහදා ගත්තේය.
- නිර්මාණ ක්රියාවලියේදී සමාකරණ මෘදුකාංග භාවිතය වැඩි වැඩියෙන් ජනප්රිය වී ඇති අතර එය වඩාත් කාර්යක්ෂම හා ලාභදායී නිෂ්පාදන සංවර්ධනයට ඉඩ සලසන බව ඇය සඳහන් කළාය.
- අභියෝග සම්බන්ධයෙන්, මෝටර් රථ උපාංගවල වැඩිවන සංකීර්ණත්වය සහ වඩාත් නිවැරදි නිෂ්පාදන ක්රියාවලීන්හි අවශ්යතාවය ඇය සඳහන් කළාය.
විශේෂඥ 3: බොබ් ජොන්සන්, ඉන්ජෙක්ෂන් මෝල්ඩින් සමාගමක තත්ත්ව පාලන කළමනාකරු
- මෝටර් රථ කර්මාන්තයේ තත්ත්ව පාලනය ඉතා වැදගත් බව ජොන්සන් බෙදා ගත්තේය. සුළු අඩුපාඩු පවා ආරක්ෂාව සහ ක්රියාකාරීත්වය අඩාල විය හැක.
- ස්වයංක්රීය පරීක්ෂණ පද්ධති වැනි තාක්ෂණික දියුණුව වඩාත් කාර්යක්ෂම සහ නිවැරදි තත්ත්ව පාලන ක්රියාවලීන් සඳහා ඉඩ ලබා දී ඇති බව ඔහු සඳහන් කළේය.
- අභියෝග සම්බන්ධයෙන් ගත් කල, උසස් තත්ත්වයේ ප්රමිතීන් පවත්වා ගනිමින් වේගවත් නිෂ්පාදන කාලය සඳහා වැඩිවන ඉල්ලුම ගැන ඔහු සඳහන් කළේය.
විශේෂඥ 4: සාරා ලී, ඉන්ජෙක්ෂන් මෝල්ඩින් සමාගමක විකුණුම් නියෝජිතයා
- තිරසාරභාවය සහ පිරිවැය-ඵලදායීතාවය කෙරෙහි වැඩි අවධානයක් යොමු කරමින් පාරිභෝගික ඉල්ලීම් නිරන්තරයෙන් වර්ධනය වන බව ලී බෙදාහදා ගත්තේය.
- අවසාන නිෂ්පාදනය අවශ්ය ප්රමිතීන් සහ අපේක්ෂාවන් සපුරාලන බව සහතික කිරීම සඳහා නිෂ්පාදකයින් සහ පාරිභෝගිකයින් අතර සන්නිවේදනය සහ සහයෝගීතාවය ඉතා වැදගත් බව ඇය සඳහන් කළාය. අභියෝග සම්බන්ධයෙන් ගත් කල, ඇය කර්මාන්තයේ වැඩිවන තරඟකාරිත්වය සහ නවෝත්පාදන සහ ගුණාත්මක භාවය තුළින් තමන්ව වෙනස් කර ගැනීමේ ඉන්ජෙක්ෂන් මෝල්ඩින් සමාගම්වල අවශ්යතාවය ගැන සඳහන් කළාය.
නිගමනය
මෝටර් රථ කර්මාන්තය අඛණ්ඩව විකාශනය වන බැවින්, උසස් තත්ත්වයේ ප්ලාස්ටික් සංරචක නිෂ්පාදනය කිරීම සඳහා ඉන්ජෙක්ෂන් මෝල්ඩින් තීරනාත්මක නිෂ්පාදන ක්රියාවලියක් ලෙස පවතී. අභ්යන්තර හෝ බාහිර කොටස් වේවා, ඉන්ජෙක්ෂන් මෝල්ඩින් කැපී පෙනෙන නිර්මාණ නිදහස, පිරිවැය-කාර්යක්ෂමතාව සහ තිරසාර ප්රතිලාභ ලබා දෙයි. මෝටර් රථ ප්ලාස්ටික් සංරචක එන්නත් අච්චු ගැසීමේ සංකීර්ණතා අවබෝධ කර ගැනීමෙන් නිෂ්පාදකයින්ට නව්ය සහ විශ්වාසදායක වාහන නිර්මාණය කිරීම සඳහා නව හැකියාවන් විවෘත කළ හැකිය. ඉන්ජෙක්ෂන් මෝල්ඩින් ලෝකය සහ මෝටර් රථ කර්මාන්තයට එහි බලපෑම පිළිබඳ වැඩිදුර අවබෝධය සඳහා මෙම බ්ලොගය වෙත රැඳී සිටින්න.