අභිරුචි ප්ලාස්ටික් එන්නත් අච්චු ගැසීම
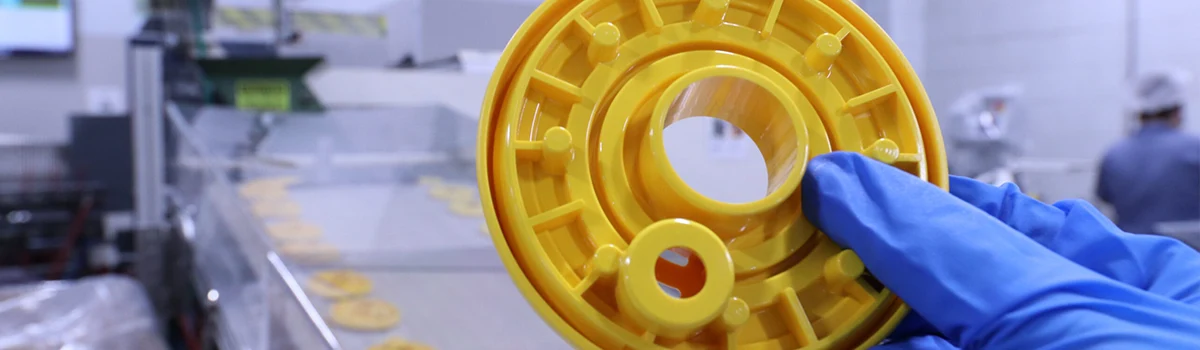
නිශ්චිත යාන්ත්රික හෝ සෞන්දර්යාත්මක ලක්ෂණ සාක්ෂාත් කර ගැනීම මත සාර්ථකත්වය රඳා පවතින ප්ලාස්ටික් කොටස් සඳහා අභිරුචි එන්නත් අච්චුව වඩාත් සුදුසු වේ. DJmolding ප්ලාස්ටික් එන්නත් අච්චුව මෙහෙයවනු ලබන්නේ පාරිභෝගිකයින්ට හොඳම ප්ලාස්ටික් කොටස් නිෂ්පාදනය කිරීමට උපකාර කිරීමේ මූලික ඉලක්කය මගිනි. සංකීර්ණත්වයට ආගන්තුක නැත, නිර්මාණ අභියෝග ඇත්තෙන්ම ඔබ වෙනුවෙන් නව්යකරණය කිරීමට අපගේ ආශාව අවුලුවා ඇත. අපව කලින්ම සම්බන්ධ කර ගැනීමෙන් නිර්මාණ ක්රියාවලියේ අගය එකතු කිරීමට අපට හැකියාව ලැබේ.
ප්ලාස්ටික් ඉන්ජෙක්ෂන් මෝල්ඩින් වල ප්රතිලාභ
සවිස්තරාත්මක විශේෂාංග
ඔබේ වෙළඳ නාමය වැඩිදියුණු කිරීම සඳහා සෞන්දර්යාත්මක හෝ ක්රියාකාරී තොරතුරු සලකා බලන්න: මුද්රිත පෙළ, රූපලාවන්ය හෝ වයනය සහිත මතුපිට, අච්චුව තුළ අලංකාර කිරීම, ක්ෂණික ගැලපීම්, නම්යශීලී සරනේරු, විවිධ දෘඪතාව.
ඉහළ කාර්යක්ෂමතාව
ප්ලාස්ටික් ඉන්ජෙක්ෂන් මෝල්ඩින්ගේ කාර්යක්ෂමතාව අසමසමයි. අපි ඔබේ කොටසෙන් සහ මෙවලමෙන් අනවශ්ය වියදම් ඉන්ජිනේරු කරන්නෙමු. අපගේ දිගුකාලීන නිර්මාණ ඉංජිනේරුවන් සහ ප්රධාන අච්චුකරුවන් මෙය සැබවින්ම විශිෂ්ටයි.
කාර්යක්ෂමතාව ඉහළ නැංවීම
ද්රව්ය විද්යාව, සැලසුම් මූලධර්ම, විශ්ලේෂණාත්මක මෙවලම් සහ ක්රියාවලි පාලනයන් යෙදීමෙන් ඔබේ කොටසෙහි අපේක්ෂිත කාර්යය තේරුම් ගැනීමට සහ ඔබේ ප්රධාන අරමුණු සපුරාලීමට අපි වෙහෙස මහන්සි වී වැඩ කරන්නෙමු.
ද්රව්ය විවිධත්වය
ද්රව්ය, භාණ්ඩ සහ ඉංජිනේරු දුම්මල 200කට වඩා වැඩි ගණනකින් තෝරන්න. කාර්ය සාධනය සහ මිල සමතුලිත කිරීමට සහ පිරිවැය අඩු කිරීම සඳහා විකල්ප ද්රව්ය සමානකම් හඳුනා ගැනීමට අපි ඔබට උදව් කරන්නෙමු.
එන්නත් අච්චු කිරීමේ ක්රියාවලිය
ප්ලාස්ටික් ඉන්ජෙක්ෂන් මෝල්ඩින් යනු ප්ලාස්ටික් නිෂ්පාදනයේ පැරණිතම ක්රමවලින් එකක් වන අතර නිෂ්පාදන නිෂ්පාදකයින් සඳහා කොටස් සංවර්ධනය කිරීමේ තීරණාත්මක පියවරකි. බැර ලෝහ කොටස් ප්ලාස්ටික් බවට පරිවර්තනය කිරීමට බලාපොරොත්තු වන නිෂ්පාදකයින්ට ද එය විශිෂ්ට විසඳුමකි. එහි සරලම ආකාරයෙන් පැහැදිලි කළහොත්, ක්රියාවලිය බහු අවයවික හෝ ප්ලාස්ටික් දුම්මල භාවිතා කරන අතර එය රත් කළ විට, උණු කළ විට සහ අභිරුචි අච්චුවකට අධි පීඩනයක් යටතේ එන්නත් කළ විට, නිෂ්පාදන නිෂ්පාදනයේදී භාවිතා කිරීමට ප්ලාස්ටික් කොටස් නිපදවනු ඇත.
එම ක්රියාවලිය සරල බව පෙනුනද, එය ඇත්ත වශයෙන්ම බෙහෙවින් සංකීර්ණ විය හැකි අතර ඔබේ අද්විතීය කර්මාන්ත අවශ්යතා, පිරිවිතරයන්, අවසාන භාවිතයන් සහ කාලය/අයවැය සීමාවන් සපුරාලිය හැකි ඉන්ජෙක්ෂන් මෝල්ඩර් හවුල්කරුවෙකුගෙන් ඉහළ මට්ටමේ අත්දැකීමක් අවශ්ය වේ. ආරම්භ කිරීමට හොඳම ස්ථානය වන්නේ ප්ලාස්ටික් අච්චු සැකසීමේ ක්රියාවලිය පිළිබඳ මූලික දැනුම ලබා ගැනීම සහ හොඳම භාවිතයන් සැලසුම් කිරීමයි.
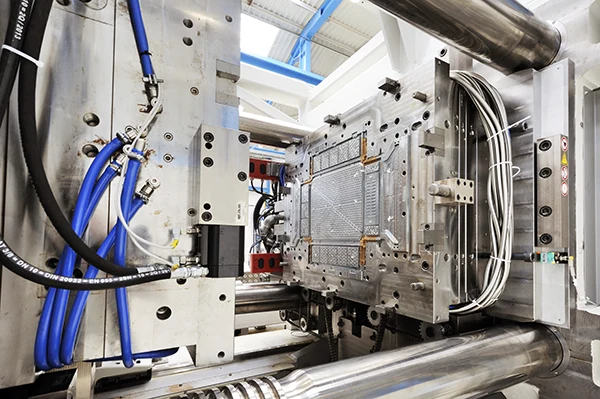
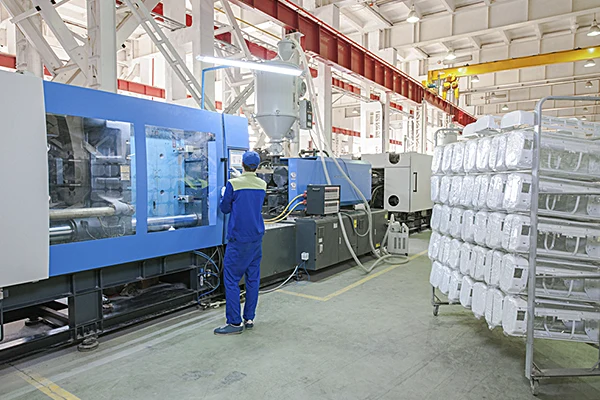
විද්යාත්මක අච්චු ගැසීම
නිශ්චිත කාර්ය සාධනයක් සහ ඉහළ නිරවද්යතාවයක් ඉල්ලා සිටින තීරණාත්මක කොටස් නිෂ්පාදනය සඳහා විද්යාත්මක අච්චු ප්රවේශයක් ප්රතිලාභ ලබයි. අපගේ උසස් අච්චු තාක්ෂණය පුනරාවර්තනය සහ අනුකූලතාව සහතික කරයි. ඒ කියන්නේ අද අපි ඔබ වෙනුවෙන් හදන භාණ්ඩය, හෙට අපි ඔබ වෙනුවෙන් හදන භාණ්ඩය.
මෙවලම් සංවර්ධනය කිරීමේදී විද්යාත්මක එන්නත් අච්චු ගැසීම ආරම්භ වේ. පීඩනය, උෂ්ණත්වය, කුහරය පිරවීමේ කාලය වැනි සාධක ප්රශස්ත කර ඇති අතර එමඟින් අච්චු සැලසුම විචලනය වීමේ අවස්ථා අවම කරයි. අච්චු ප්රවාහ විශ්ලේෂණය මඟින් පිරවිය යුතු කොටසෙහි අවසාන ප්රදේශ, ද්රව්යය අච්චුව සමඟ දිශානතිය වන ආකාරය සහ විභව විකෘති සහ ආතති ස්ථාන නිරාවරණය කරයි. එය ඉංජිනේරුමය පුරෝකථන විශ්ලේෂණය සහ මිනුම් සපයන ක්රියාකාරී පියවරක් වන අතර කොටසක හෝ ව්යාපෘතියක සාර්ථකත්වය හෝ අසාර්ථකත්වය පහසුවෙන් තීරණය කිරීමට ඉඩ සලසයි.
ශක්තිමත් නිෂ්පාදන ක්රියාවලීන් අධීක්ෂණ සහ ස්වයංක්රීය ක්රියාවලි පාලනය හරහා විද්යාත්මක ප්රවේශයක් තවදුරටත් භාවිතා කරන අතර එමඟින් සීරීම් සහ සැකසුම් කාලය අඩු කරයි. විචල්යයක් හෝ අක්රිය ක්රියාකාරිත්වයක් සිදු වුවහොත්, නොගැලපෙන කොටස් සෑදීමට පෙර එය වේගයෙන් හඳුනාගෙන හුදකලා වේ.
අධික ලෙස සකස් කිරීම
දෙකක් (හෝ ඊට වැඩි) ද්රව්ය overmolding සමග තනි කොටසකට ඒකාබද්ධ කළ හැක. මෙම ක්රියාවලිය බොහෝ විට මෘදු ග්රහණය ප්රදේශයක් වැනි වෙනස් ස්පර්ශක මතුපිටක් සඳහා භාවිතා වේ. ඕවර්මෝල්ඩින් ප්ලාස්ටික් උපස්ථරයක් මත ප්ලාස්ටික් හෝ ප්ලාස්ටික් උපස්ථරයක් මත රබර් විය හැක, සාමාන්යයෙන් දෙකක්-වෙඩි එන්නත් අච්චු ගැසීමේ ක්රියාවලියක් මගින් සිදු කෙරේ. ෙරසින් සැකසීම සහ වර්ණ වෙනස් විය හැක. overmolding වල සෞන්දර්යාත්මක වාසි පහසුවෙන් දැකගත හැකි නමුත් ඒවා ද්විතියික මෙහෙයුම් ඉවත් කරයි. අත් ග්රහණයන් සහිත මෙවලම්, අතින් ගෙන යා හැකි වස්තූන්, රබර් ග්රහණයන් අවශ්ය වන රොබෝ යන්ත්ර සඳහා හෝ සරලව වෙනස් වර්ණ සහිත කොටසක පෙනුම වැඩි දියුණු කිරීම සඳහා Overmolding පරිපූර්ණ වේ.
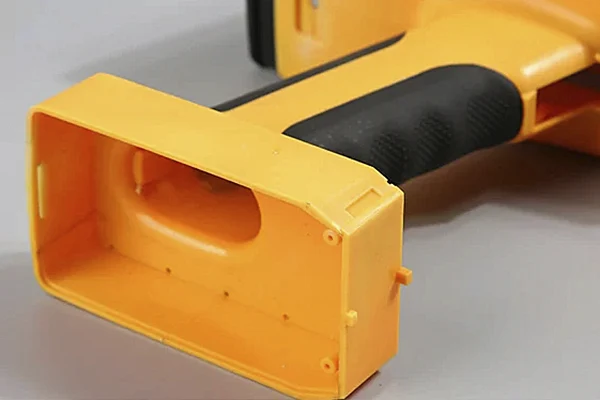
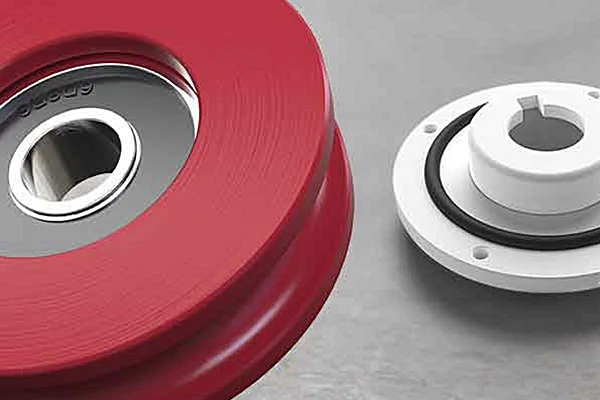
මෝල්ඩින් ඇතුල් කරන්න
ඇතුල් කිරීමේ අච්චුව අධි අච්චුවකට සමාන නමුත් අච්චු කුහරයක් තුළ තබා ඇති වස්තුවක් ඇතුළත් වේ. සාමාන්යයෙන් ලෝහ හෝ ප්ලාස්ටික් ඇතුළු කිරීම්වලට වාත්තු බන්ධන ප්ලාස්ටික් ඇතුළු කරන්න. නූල් ඇතුළත් කිරීම් බහුලව දක්නට ලැබේ. මෙය ගාංචු, ඇලවුම් හෝ තාප ස්ථායීතාවය සඳහා විකල්පයක් ලෙස භාවිතා කරන විට ශ්රමය ඉවත් කරයි. ඇතුල් කිරීම් ද කොටස ශක්තිමත් කරයි. ඇතුළු කිරීම් අතින් හෝ රොබෝ ස්වයංක්රීයකරණයෙන් පටවනු ලැබේ.
කොටස් අලංකරණය සහ ලේබල් කිරීම
චිත්රක හෝ ලේබල් සමඟ දෘශ්යමය වශයෙන් කැපී පෙනෙන පෙනුමක් නිර්මාණය කිරීමට අච්චු තුළ සැරසිලි (IMD) සහ අච්චු ලේබල් කිරීම (IML) භාවිතා වේ. රොබෝ විද්යාව සහ විද්යුත් ස්ථිතික හෝ රික්ත ග්රහණය මගින් පහසු කර ඇති අතර, උණු කළ ප්ලාස්ටික් දුම්මල එන්නත් කිරීමට පෙර අච්චු කුහරයට මුද්රිත පටල ආවරණයක් එකතු කරනු ලැබේ. මෙම ක්රියාවලිය ලේබලය සහ නිමි කොටස අතර ස්ථීර බැඳීමක් ඇති කරයි, සාමාන්යයෙන් පසු සැකසුම් මෙහෙයුම් සඳහා අවශ්යතාවය ඉවත් කරයි. පුළුල් පරාසයක වයනය, වර්ණය සහ මතුපිට ආලේපන තේරීම් නිර්මාණාත්මක හැකියාවන් සඳහා දොර විවෘත කරයි. ඔබේ වෙළඳ නාමය වැඩිදියුණු කිරීමට විකල්ප ගැන ඔබේ ව්යාපෘති කළමනාකරු සමඟ කතා කිරීමට අපි ඔබව දිරිමත් කරමු.
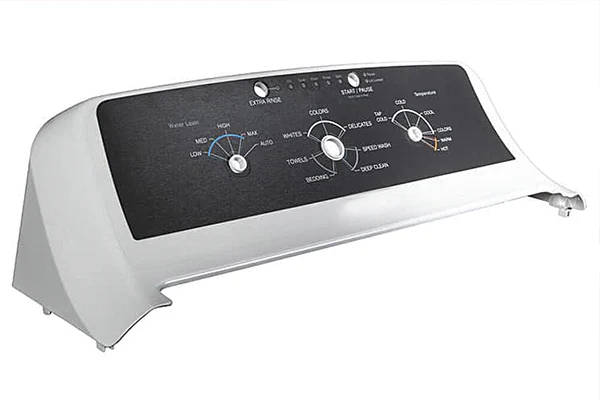
අභිරුචි ප්ලාස්ටික් එන්නත් මෝල්ඩින් සේවාව චීනය
2010 සිට DJmolding මෙහෙයුම් | AFAQ ISO/TS 16949, UL සහ ISO සහතික, ප්රධාන වශයෙන් දැන් ලෝකයේ බොහෝ 3D මුද්රණ සමාගම් වෙත සපයයි.
Djmolding හි අපි උසස් තත්ත්වයේ ප්ලාස්ටික් එන්නත් අච්චු කරන ලද කොටස් සහ අච්චු මෙවලම් නිෂ්පාදනය කිරීමට විශේෂීකරණය කරමු. ලෝකයේ බොහෝ 3D මුද්රණ සමාගම් සඳහා අපි ප්රධාන වශයෙන් අපගේ ප්ලාස්ටික් එන්නත් නිෂ්පාදනය සපයන්නෙමු. රොබෝ තාක්ෂණය සහ ස්වයංක්රීය ප්ලාස්ටික් එන්නත් නිෂ්පාදනය සඳහා යන්ත්ර 55ක් අප සතුව ඇත. විවිධ ද්රව්ය වලින් මෙවලම් සෑදීම සඳහා අපි සියලුම යන්ත්ර සහ නිම කිරීමේ සේවාවන් සපයන අතර සියලුම ප්රධාන ප්ලාස්ටික් වල නිමි කොටස් 100 සිට 200k+ දක්වා නිෂ්පාදනය කළ හැකිය. සැබවින්ම අපව වෙන් කරන්නේ අපගේ උසස් ද්රව්ය සත්යාපනය, පරීක්ෂා කිරීම සහ ඔබගේ කොටස් ඔබගේ ඉහළම අපේක්ෂාවන් සපුරාලීම සහ ඒවා ඉක්මවා යාම සහතික කිරීම සඳහා වන පරීක්ෂණයයි. අද නොමිලේ උපුටා ගැනීමක් සඳහා අපගේ ජාත්යන්තර එන්නත් අච්චු විශේෂඥයින් අමතන්න.
DJmolding ප්ලාස්ටික් ඉන්ජෙක්ෂන් මෝල්ඩින් ක්රියාවලිය
ඔබේ ප්ලාස්ටික් එන්නත් අච්චු මෙවලම් සූදානම් වූ පසු, අච්චු සැකසීමේ ක්රියාවලිය පහත මූලික පියවර වලින් සමන්විත වේ:
පියවර 1. ප්ලාස්ටික් ෙරසින් අමු පෙති වලින් පැමිණේ. මේවා නිවැරදි තෙතමන ප්රමාණයට වියලනු ලබන අතර, අවශ්ය නම් ඒවා වර්ණක හෝ ප්රධාන කණ්ඩායම් වර්ණක සමඟ මිශ්ර කළ හැකිය.
පියවර 2. වියලන ලද පෙති අච්චු යන්ත්රයේ ආප්පයට වත් කරනු ලැබේ. යන්ත්රයේ බැරලය තුළ ඇති ප්රතිවිකුණුම් ඉස්කුරුප්පුවක් මෙම පෙති අච්චුව දෙසට ප්රවාහනය කරනු ඇත.
පියවර 3. බැරලය තුළ, පෙති මිශ්ර කර සම්පූර්ණයෙන්ම උණු කරන තෙක් රත් කර, දියර දුම්මල සාදයි.
පියවර 4. රත් වූ අච්චුව ස්වයංක්රීයව වැසෙන අතර විශාල පීඩනයක් යටතේ දුම්මල ගේට්ටුවක් හරහා සහ අච්චු කුහරයට එන්නත් කරනු ලැබේ.
පියවර 5. ඇතුළත කොටස ඝන කිරීම සඳහා අච්චුව සිසිල් කරනු ලැබේ.
පියවර 6. අච්චුව විවෘත වන අතර නව චක්රයක් ආරම්භ කිරීම සඳහා කොටස ඉවත් කරනු ලැබේ.
ප්ලාස්ටික් එන්නත් මෝල්ඩින් ඉවසීම
සියලු ප්ලාස්ටික් ද්රව්ය තාපය හා තෙතමනය බලපෑම යටතේ පුළුල් හා හැකිලෙනු ඇත. අපගේ ඉවසීමේ මාර්ගෝපදේශය සාමාන්ය කොටස් ලක්ෂණ සඳහා වඩාත් පොදු දුම්මල වර්ගවල ලක්ෂණ පිළිබඳ වඩාත් සාමාන්ය තොරතුරු ලබා දෙනු ඇත.
නිෂ්පාදනය සඳහා ඔබේ නිර්මාණ ප්රශස්ත කිරීමට අපි ඔබ සමඟ සමීපව කටයුතු කරන්නෙමු. දුර්වල සැලසුම තාප ආතතිය, හැකිලීම, විකෘති කිරීම ආදිය ඇති කළ හැකි ඕනෑම ප්රදේශයක් අපි දක්වන්නෙමු. පොදු දෝෂ සහ ඒවා වළක්වා ගන්නේ කෙසේද යන්න පිළිබඳ වැඩි විස්තර සඳහා අපගේ නිර්මාණ මාර්ගෝපදේශය බලන්න.
වෙනත් ආකාරයකින් නිශ්චිතව දක්වා නොමැති නම්, අපි ප්ලාස්ටික් එන්නත් අච්චු සඳහා DIN 16742 සම්මත ඉවසීම් වලට අනුකූල වේ. අපි එන්නත් අච්චු කරන ලද කොටස් සඳහා අදාළ වන දෘශ්ය තත්ත්ව ප්රමිතීන් ගැන කියවන්න.
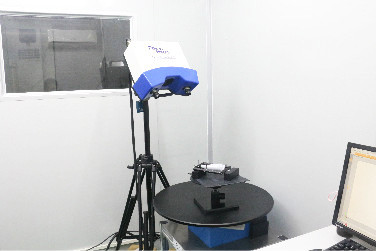
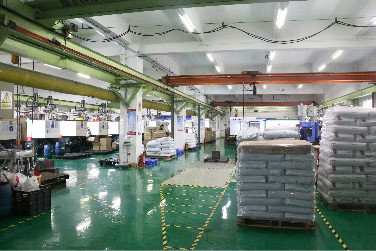
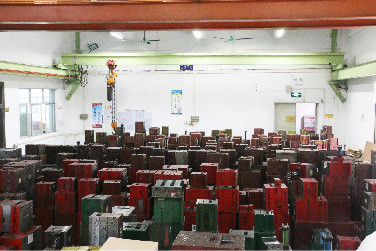
ප්ලාස්ටික් ඉන්ජෙක්ෂන් මෝල්ඩින් ද්රව්ය
Djmolding ඉන්ජෙක්ෂන් මෝල්ඩින් මෙවලම් නිපදවන අතර ඇලුමිනියම් 7075, P20 සහ NAK80 අර්ධ දෘඪ වානේ සහ H13 සම්පූර්ණයෙන්ම-දැඩි වානේ වලින් මිය යයි. මීට අමතරව, අපි සම්මත SPI නිමාව, EDM ටෙක්ස්චරින් සහ කැටයම් කළ වයනය පිරිනමන්නෙමු.
මෙම සෑම ද්රව්ය වර්ගයකටම ඇතැම් යෙදුම් සඳහා සුවිශේෂී වාසි ඇත. * සලකා බැලීම් ඇතුළත් වේ:
*අමුද්රව්යවල මිල
* කල්පැවැත්ම සහ විඛාදනයට හෝ සීරීම් වලට ඔරොත්තු දීම
* යන්ත්රෝපකරණ හැකියාව
*ඉහළ මතුපිට ඔප දැමීමේ හැකියාව
* තාප පිරියම් කිරීම සඳහා අවශ්ය කාලය
* අපේක්ෂිත මෙවලම් ආයු කාලය
ඔබට ගැලපෙන එක ගැන වැඩිදුර දැන ගැනීමට අපගේ තාක්ෂණික විශේෂඥයින් අමතන්න.
ප්ලාස්ටික් එන්නත් කරන ලද කොටස්
ඔබේ ව්යාපෘතිය සඳහා තෝරා ගැනීමට තාප හැඩගැන්වීම් සහ තාප සැකසුම් ප්ලාස්ටික් දහස් ගණනක් ඇත. මීට අමතරව, වීදුරු කෙඳි, UV ස්ථායීකාරක සහ ලිහිසි තෙල් වැනි ආකලන සමඟ යාන්ත්රික හා රසායනික ලක්ෂණ ද වැඩිදියුණු කළ හැකිය. අපගේ ද්රව්ය පත්රය ඔබට සම්මත වර්ග සහ එක් එක් සමඟ අපේක්ෂා කළ යුතු ඉවසීම් පිළිබඳ වඩාත් සවිස්තරාත්මක තොරතුරු ලබා දෙනු ඇත.
ඔබේ දුම්මල තේරීම පහත සලකා බැලීම් වලින් එකක් හෝ කිහිපයක් මත රඳා පවතී:
*UV, රසායනික, උල්ෙල්ඛ සහ බලපෑම් ප්රතිරෝධය
*අමුද්රව්ය මිල
* යාන්ත්රික ශක්තිය
*බර සහ ඝනත්වය
* නම්යශීලී බව
*විනිවිදභාවය
*ප්රතිචක්රීකරණය
ද්රව්යමය ගුණාංග ගැන වැඩිදුර දැන ගැනීමට අපගේ තාක්ෂණික විශේෂඥයෙකු අමතන්න.
DJmolding එන්නත් සාප්පුව:
ප්රමුඛ පෙළේ ප්ලාස්ටික් එන්නත් අච්චුව සහ වේගවත් මූලාකෘති සේවා නිෂ්පාදකයා
Djmolding යනු චීනයේ වඩාත් හොඳින් දන්නා ප්ලාස්ටික් ඉන්ජෙක්ෂන් මෝල්ඩින් සමාගමකි. අපගේ ඉන්ජෙක්ෂන් මෝල්ඩින් සාප්පුව ටොන් 50 සිට ටොන් 30 දක්වා ඉහළ නිරවද්යතාවයකින් යුත් ඉන්ජෙක්ෂන් මෝල්ඩින් යන්ත්ර කට්ටල 800 කින් සමන්විත වේ, ඒවා බොහෝ දුරට තායිවානයෙන් සහ ජපානයෙන් ආනයනය කර ඇත, අපගේ එන්නත් සාප්පුව දවසේ පැය 24 පුරාම සතියේ දින 7 පුරාම ක්රියාත්මක වන අතර නිෂ්පාදනය සපයයි. සේවා.
අපි: මෝටර් රථ, වෛද්ය, ආලෝකකරණය, ක්රීඩා උපකරණ, ගෘහ උපකරණ සහ කෘෂිකර්මාන්තය ඇතුළු බොහෝ කාර්මික සඳහා විවිධ ප්ලාස්ටික් නිෂ්පාදන සමඟ අත්දැකීම් ඇත්තෙමු. Djmolding හට 16949 වසරේ සිට AFAQ ISO/TS 9001, UL සහ ISO 2010 සහතික සමත් වී ඇත, IPQC පුද්ගලයින් 15 දෙනෙකු ද අපගේ නිෂ්පාදනය නිරන්තරයෙන් නරඹන අතර කොටසේ ගුණාත්මකභාවය පරීක්ෂා කරයි, මෙමගින් අපගේ නිෂ්පාදනය ඉහළම ගුණාත්මක භාවයක් පවත්වා ගැනීම සහතික කරයි. පසුගිය වසර 9 තුළ, Djmolding උසස් තත්ත්වයේ මෙවලමක් සහ කොටසක් සාධාරණ මිලකට නිෂ්පාදනය කිරීමේ ශක්තිමත් කීර්තියක් ස්ථාපිත කර ඇත. අපි appx සමඟ ශක්තිමත් ව්යාපාරික සබඳතා පවත්වමු. පාරිභෝගිකයින් 50ක්, ප්රධාන වශයෙන් ඇමරිකා එක්සත් ජනපදයෙන් සහ යුරෝපයෙන්.
අභිරුචි ප්ලාස්ටික් එන්නත් අච්චු ගැසීම
අභිරුචි ප්ලාස්ටික් ඉන්ජෙක්ෂන් මෝල්ඩින් යනු උසස් තත්ත්වයේ ප්ලාස්ටික් කොටස් නිෂ්පාදනය කිරීමේ නව්ය හා කාර්යක්ෂම ක්රමයකි. මෙම නිෂ්පාදන ක්රියාවලිය ප්ලාස්ටික් ද්රව්ය සංකීර්ණ හැඩයන් සහ ප්රමාණවලට හැඩගැස්වීම සඳහා අච්චුවක් භාවිතා කරයි, එය විවිධ කර්මාන්ත සඳහා කදිම විසඳුමක් බවට පත් කරයි. මෙම බ්ලොග් සටහන අභිරුචි ප්ලාස්ටික් ඉන්ජෙක්ෂන් මෝල්ඩින් වෙත ගැඹුරට කිමිදෙමින් එහි ප්රතිලාභ, යෙදුම් සහ හොඳම භාවිතයන් ගවේෂණය කරනු ඇත.
අභිරුචි එන්නත් අච්චු සැකසීමේ ක්රියාවලිය අවබෝධ කර ගැනීම
අභිරුචි ඉන්ජෙක්ෂන් මෝල්ඩින් යනු විශාල පරිමාවකින් ප්ලාස්ටික් කොටස් නිෂ්පාදනය කිරීම සඳහා භාවිතා කරන නිෂ්පාදන ක්රියාවලියකි. එයට ප්ලාස්ටික් පෙති හෝ කැටිති උණු කර අධික පීඩනයක් යටතේ අච්චුවකට එන්නත් කිරීම ඇතුළත් වන අතර එහිදී ඒවා සිසිල් වී අවශ්ය හැඩයක් සෑදීමට ඝන වේ. එන්නත් අච්චු ගැසීමේ ක්රියාවලිය ක්රියාත්මක වන ආකාරය මෙන්න:
- කලම්ප: "මෙවලම" ලෙස හඳුන්වන අච්චුවේ අර්ධ දෙක, එන්නත් පීඩනයට ඔරොත්තු දීම සඳහා ප්රමාණවත් බලයක් සමඟ එකට බැඳ ඇත.
- එන්නත් කිරීම: ප්ලාස්ටික් පෙති රත් වූ බැරලයක උණු කොට, අධික පීඩනය යටතේ ධාවන පද්ධතියක් හරහා අච්චුව තුළට එන්නත් කරනු ලැබේ. ප්ලාස්ටික් අච්චු කුහරය පුරවා අච්චුවේ හැඩය ගනී.
- සිසිලනය: ප්ලාස්ටික් අපේක්ෂිත හැඩය පවත්වා ගැනීම සඳහා අච්චුව ඇතුළත සිසිල් කර ඝන විය හැක.
- පිටකිරීම: ප්ලාස්ටික් සිසිල් වූ පසු අච්චුව විවෘත වන අතර නිමි කොටස ඉවත් කරනු ලැබේ.
- පුනරාවර්තනය: සමාන කොටස් කිහිපයක් සෑදීමට ක්රියාවලිය නැවත නැවතත් සිදු කෙරේ.
ඉන්ජෙක්ෂන් මෝල්ඩින් කුඩා කොටස්වල සිට වාහන අමතර කොටස් සහ ගෘහ උපකරණ වැනි විශාල අයිතම දක්වා ප්ලාස්ටික් නිෂ්පාදන නිෂ්පාදනය කරයි. මෙම ක්රියාවලිය ඉතා කාර්යක්ෂම වන අතර සංකීර්ණ ජ්යාමිතීන් සහ තද ඉවසීම් සහිත කොටස් නිපදවිය හැකි අතර, අවම අපද්රව්ය සහ අඩු සීරීම් අනුපාත සහිතව එයද නිවැරදිය.
මෙම ක්රියාවලිය නිවැරදි හා ස්ථාවර ප්රතිඵල සහතික කිරීම සඳහා අච්චුවක්, එන්නත් අච්චු යන්ත්රයක් සහ පාලන පද්ධතියක් ඇතුළුව විශේෂිත උපකරණ අවශ්ය වේ. අච්චුව සාමාන්යයෙන් වානේ වලින් සාදා ඇති අතර බහු කුහර අච්චු භාවිතයෙන් බහු කොටස් නිෂ්පාදනය කිරීමට සැලසුම් කළ හැකිය.
ඉන්ජෙක්ෂන් මෝල්ඩින් තාප ප්ලාස්ටික්, තර්මෝසෙට් සහ ඉලාස්ටෝමර් ඇතුළු විවිධ ද්රව්ය සමඟ ද භාවිතා කළ හැකිය. සෑම ද්රව්යයකටම අනන්ය ගුණ ඇති අතර විශේෂිත යෙදුම් වලට අනුව සකස් කළ හැක.
සමස්තයක් වශයෙන්, ඉන්ජෙක්ෂන් මෝල්ඩින් යනු බොහෝ කර්මාන්තවල බහුලව භාවිතා වන ඉතා බහුකාර්ය සහ කාර්යක්ෂම නිෂ්පාදන ක්රියාවලියකි.
අභිරුචි ප්ලාස්ටික් එන්නත් අච්චු වල වාසි
අභිරුචි ප්ලාස්ටික් ඉන්ජෙක්ෂන් මෝල්ඩින් යනු විශාල පරිමාවකින් අභිරුචි ප්ලාස්ටික් කොටස් නිර්මාණය කිරීමට භාවිතා කරන නිෂ්පාදන ක්රියාවලියකි. මෙම ක්රියාවලියේ වාසි කිහිපයක් මෙන්න:
ඉහළ කාර්යක්ෂමතාව සහ ඵලදායිතාව: අභිරුචි ප්ලාස්ටික් ඉන්ජෙක්ෂන් මෝල්ඩින් යනු ඉතා කාර්යක්ෂම ක්රියාවලියක් වන අතර එමඟින් සමාන කොටස් විශාල පරිමාවක් ඉක්මනින් හා ස්ථාවර ලෙස නිපදවිය හැකිය. මෙය ප්ලාස්ටික් කොටස් විශාල වශයෙන් නිෂ්පාදනය කිරීම සඳහා කදිම තේරීමක් කරයි.
බහුකාර්යතාව: මෙම ක්රියාවලිය තාප ප්ලාස්ටික්, උෂ්ණත්ව කට්ටල සහ ඉලාස්ටෝමර් ඇතුළු පුළුල් පරාසයක ප්ලාස්ටික් ද්රව්ය සමඟ භාවිතා කළ හැකිය. මෙය විවිධ කොටස් සැලසුම් සහ යෙදුම් සඳහා ඉඩ සලසයි.
අනුකූලතාව සහ නිරවද්යතාව: ඉන්ජෙක්ෂන් මෝල්ඩින් දැඩි ඉවසීම් සහ කොටස් අතර අවම විචලනය සමග, ස්ථාවර සහ නිවැරදි ප්රතිඵල සපයයි. මෙය බොහෝ යෙදුම් සඳහා අත්යවශ්ය වන එක් එක් කැබැල්ල ඊළඟට සමාන බව සහතික කරයි.
පිරිවැය-ඵලදායී: අභිරුචි ප්ලාස්ටික් ඉන්ජෙක්ෂන් මෝල්ඩින් ඉහළ පරිමාණ නිෂ්පාදන ධාවනය සඳහා ලාභදායී විය හැක. ආරම්භක මෙවලම් පිරිවැය ඉහළ විය හැකි නමුත් පරිමාව වැඩි වන විට කොටසක පිරිවැය අඩු වේ.
සංකීර්ණත්වය: ඉන්ජෙක්ෂන් මෝල්ඩින් මගින් තුනී බිත්ති සහ සංකීර්ණ ලක්ෂණ ඇතුළුව සංකීර්ණ හැඩයන් සහ ජ්යාමිතීන් සහිත කොටස් නිපදවිය හැක. මෙමගින් වැඩි නිර්මාණ නම්යශීලී බවක් ලබා දෙන අතර වෙනත් ක්රම භාවිතයෙන් නිෂ්පාදනය කිරීමට අපහසු හෝ කළ නොහැකි සාධක නිෂ්පාදනය කිරීමට හැකියාව ලැබේ.
අවම අපද්රව්ය: ඕනෑම අතිරික්ත ප්ලාස්ටික් ප්රතිචක්රීකරණය කර නැවත භාවිතා කළ හැකි බැවින් එන්නත් අච්චුව අනෙකුත් නිෂ්පාදන ක්රියාවලීන්ට සාපේක්ෂව අවම අපද්රව්ය ජනනය කරයි.
මතුපිට නිමාව: ඉන්ජෙක්ෂන් මෝල්ඩින් අතිරේක පශ්චාත් සැකසුම් හෝ නිම කිරීමේ මෙහෙයුම් නොමැතිව උසස් තත්ත්වයේ මතුපිට නිමාවක් සහිත කොටස් නිෂ්පාදනය කළ හැකිය. මෙය සුමට හා ඔප දැමූ පෙනුමක් සහිත කෑලි නිර්මාණය කිරීම සඳහා ලාභදායී විසඳුමක් බවට පත් කරයි.
ස්වයංක්රීයකරණය: එන්නත් අච්චුව පහසුවෙන් ස්වයංක්රීය කළ හැක, රොබෝවරුන් අච්චුවෙන් කොටස් පැටවීම සහ බෑම සහ විශේෂාංග පරීක්ෂා කිරීම සහ වර්ග කිරීම. මෙය ශ්රමික ශ්රමයේ අවශ්යතාවය අඩු කරන අතර කාර්යක්ෂමතාව වැඩි කරයි.
අභිරුචි ප්ලාස්ටික් ඉන්ජෙක්ෂන් මෝල්ඩින් යනු අනෙකුත් ක්රමවලට වඩා බොහෝ වාසි ලබා දෙන ඉතා බහුකාර්ය සහ කාර්යක්ෂම නිෂ්පාදන ක්රියාවලියකි. සමාන කොටස් විශාල පරිමාවක් ඉක්මනින් හා නිවැරදිව නිෂ්පාදනය කිරීමට එහි ඇති හැකියාව මෝටර් රථ, අභ්යවකාශ, වෛද්ය සහ පාරිභෝගික භාණ්ඩ ඇතුළු බොහෝ කර්මාන්ත සඳහා වඩාත් සුදුසු වේ.
එන්නත් අච්චු යෙදීම
ඉන්ජෙක්ෂන් මෝල්ඩින් යනු විවිධ කාර්මික ප්ලාස්ටික් නිෂ්පාදන නිර්මාණය කිරීම සඳහා බහුලව භාවිතා වන නිෂ්පාදන ක්රියාවලියකි. එන්නත් අච්චු ගැසීමේ වඩාත් පොදු යෙදුම් කිහිපයක් මෙන්න:
- මෝටර් රථ කර්මාන්තය: ඉන්ජෙක්ෂන් මෝල්ඩින් අභ්යන්තර සහ බාහිර සැරසිලි, උපකරණ පුවරු සංරචක, දොර හැන්ඩ්ල් සහ එන්ජින් කොටස් ඇතුළු විවිධ මෝටර් රථ කොටස් නිෂ්පාදනය කරයි. ඉහළ ශක්තියක් සහ මාන නිරවද්යතාවයක් සහිත විශේෂාංග තිබිය හැකි බැවින් එය වඩාත් කැමති වේ.
- පාරිභෝගික භාණ්ඩ: එන්නත් අච්චු කිරීම සෙල්ලම් බඩු, ගෘහ උපකරණ සහ ඉලෙක්ට්රොනික උපාංග ඇතුළු විවිධ පාරිභෝගික නිෂ්පාදන නිර්මාණය කරයි. එය සංකීර්ණ හැඩයන් සහ ජ්යාමිතිය සහ උසස් තත්ත්වයේ මතුපිට නිමාව නිෂ්පාදනය කිරීමට ඉඩ සලසයි.
- වෛද්ය උපකරණ: එන්නත් අච්චුව සිරින්ජ, IV සංරචක සහ රෝග විනිශ්චය උපකරණ ඇතුළු විවිධ වෛද්ය උපකරණ නිෂ්පාදනය කිරීමට භාවිතා කරයි. වෛද්ය කර්මාන්තයේ අත්යවශ්ය වන සංකීර්ණ ජ්යාමිතිය සහිත කොටස් නිෂ්පාදනය කිරීමේ හැකියාව ඉහළ නිරවද්යතාවයකින්, පිරිසිදුව නිෂ්පාදනය කරයි.
- ඇසුරුම් කර්මාන්තය: එන්නත් අච්චුව බෝතල්, භාජන සහ පියන ඇතුළු ඇසුරුම් ද්රව්ය නිෂ්පාදනය කරයි. එය සැහැල්ලු සහ කල් පවතින බහාලුම් නිර්මාණය කිරීමට සහ වර්ණ, වයනය සහ හැඩතල අභිරුචිකරණය කිරීමට ඉඩ සලසයි.
- අභ්යවකාශ කර්මාන්තය: ව්යුහාත්මක මූලද්රව්ය සහ අභ්යන්තර උපාංග ඇතුළු අභ්යවකාශ කොටස්වල විවිධ සංරචක නිෂ්පාදනය කිරීමට එන්නත් අච්චුව භාවිතා කරයි. අධික උෂ්ණත්ව හා පීඩනවලට ඔරොත්තු දිය හැකි ඉහළ කාර්යසාධනයක් සහිත ද්රව්ය නිර්මාණය කිරීමට එය ඉඩ සලසයි.
- ඉදිකිරීම් කර්මාන්තය: එන්නත් අච්චුව PVC පයිප්ප, ගටර් පද්ධති සහ සෙවිලි ද්රව්ය ඇතුළු විවිධ ඉදිකිරීම් ද්රව්ය නිෂ්පාදනය කරයි. එය ඉහළ කල්පැවැත්මක්, කාලගුණය සහ රසායනික ද්රව්යවලට ප්රතිරෝධයක් සහ විශාල පරිමාවකින් කොටස් නිෂ්පාදනය කිරීමේ හැකියාව ලබා දෙයි.
- ඉලෙක්ට්රොනික කර්මාන්තය: එන්නත් අච්චුව නිවාස, සම්බන්ධක සහ ස්විච ඇතුළු විවිධ ඉලෙක්ට්රොනික උපාංග නිෂ්පාදනය කරයි. එය ඉලෙක්ට්රොනික කර්මාන්තයේ අත්යවශ්ය වන සංකීර්ණ ජ්යාමිතිය සහිත කොටස් නිෂ්පාදනය කිරීමේ හැකියාව ඉහළ නිරවද්යතාවයක්, ඒකාකාරී බවක් ලබා දෙයි.
සමස්තයක් වශයෙන්, ඉන්ජෙක්ෂන් මෝල්ඩින් යනු බොහෝ කර්මාන්ත සඳහා බොහෝ ප්ලාස්ටික් කොටස් නිෂ්පාදනය කළ හැකි බහුකාර්ය නිෂ්පාදන ක්රියාවලියකි. සංකීර්ණ ජ්යාමිතිය, ඉහළ නිරවද්යතාව සහ ස්ථාවර ගුණාත්මක භාවය සහිත කොටස් නිෂ්පාදනය කිරීමට එහි ඇති හැකියාව බොහෝ නිෂ්පාදකයින් සඳහා ජනප්රිය තේරීමක් කරයි.
ඉන්ජෙක්ෂන් මෝල්ඩින් භාවිතා කරන ද්රව්ය වර්ග
ඉන්ජෙක්ෂන් මෝල්ඩින් යනු නිශ්චිත හැඩයක් නිර්මාණය කිරීම සඳහා උණු කළ ප්ලාස්ටික් අච්චු කුහරයකට එන්නත් කිරීම ඇතුළත් නිෂ්පාදන ක්රියාවලියකි. අවසාන නිෂ්පාදනයේ අපේක්ෂිත ගුණාංග මත පදනම්ව, එන්නත් අච්චු ගැසීමේදී විවිධ ද්රව්ය භාවිතා කළ හැකිය. එන්නත් අච්චු ගැසීමේදී බහුලව භාවිතා වන ද්රව්ය වර්ග කිහිපයක් මෙන්න:
- තාප ප්ලාස්ටික්: මේවා එන්නත් අච්චු ගැසීමේදී බහුලව භාවිතා වන ද්රව්ය වේ. ඒවා රත් වූ විට මෘදු හා අච්චු කළ හැකි ප්ලාස්ටික් වර්ගයක් වන අතර සිසිල් වූ විට දැඩි වේ. තාප ප්ලාස්ටික් ඒවායේ ගුණාංග අහිමි නොවී කිහිප වතාවක් අච්චු කර නැවත සකස් කළ හැකිය. ඉන්ජෙක්ෂන් මෝල්ඩින් සඳහා භාවිතා කරන පොදු තාප ප්ලාස්ටික් වලට පොලිප්රොපිලීන්, පොලිඑතිලීන්, පොලිස්ටිරින් සහ නයිලෝන් ඇතුළත් වේ.
- උෂ්ණත්ව කට්ටල: මේවා එක් වරක් පමණක් අච්චු කළ හැකි ප්ලාස්ටික් වේ. ඒවා රත් කර නිශ්චිත හැඩයක් දක්වා වර්ධනය කර ඇති අතර, ඒවා දැඩි වූ පසු, ඒවා නැවත සකස් කළ නොහැක. ඉහළ ශක්තියක් සහ කල්පැවැත්මක් අවශ්ය වන යෙදුම් සඳහා උෂ්ණත්ව කට්ටල භාවිතා වේ. ඉන්ජෙක්ෂන් මෝල්ඩින් සඳහා භාවිතා කරන පොදු තාප කට්ටලවලට ඉෙපොක්සි, මෙලමයින් සහ ෆීනොලික් ෙරසින් ඇතුළත් වේ.
- ඉලාස්ටෝමර්: මෙම ද්රව්ය ප්රත්යාස්ථ ගුණ ඇති අතර ඒවායේ මුල් හැඩයට දිගු කර ආපසු යා හැක. නම්යශීලී බව සහ කම්පන අවශෝෂණය අවශ්ය වන යෙදුම් සඳහා ඉලාස්ටෝමර් භාවිතා වේ. එන්නත් අච්චු ගැසීමේදී භාවිතා කරන සම්මත ඉලාස්ටෝමර්වලට රබර්, සිලිකොන් සහ පොලියුරේටීන් ඇතුළත් වේ.
- ජෛව හායනයට ලක්විය හැකි ද්රව්ය: මේවාට හානිකර අපද්රව්ය ඉතිරි නොකර පරිසරය තුළ ස්වභාවිකව බිඳ වැටිය හැක. පාරිසරික තිරසාරභාවය පිළිබඳ සැලකිලිමත් වන යෙදුම් සඳහා ඒවා භාවිතා වේ. එන්නත් අච්චු ගැසීමේදී භාවිතා වන සාමාන්ය ජෛව හායනයට ලක්විය හැකි ද්රව්ය පොලිලැක්ටික් අම්ලය (PLA) සහ polyhydroxyalkanoates (PHAs) ඇතුළත් වේ.
- සංයුති යනු විවිධ ද්රව්ය දෙකක් හෝ වැඩි ගණනක් එකතු කර නිශ්චිත ගුණ සහිත නව ද්රව්යයක් නිර්මාණය කිරීම මගින් සාදන ලද ද්රව්ය වේ. ඉහළ ශක්තියක් සහ තද බවක් අවශ්ය වන යෙදුම් සඳහා සංයුක්ත භාවිතා වේ. ඉන්ජෙක්ෂන් මෝල්ඩින් කිරීමේදී භාවිතා කරන සම්මත සංයෝග අතර වීදුරු තන්තු ශක්තිමත් කරන ලද ප්ලාස්ටික් (GRP) සහ කාබන් ෆයිබර් ශක්තිමත් කරන ලද ප්ලාස්ටික් (CFRP) ඇතුළත් වේ.
- ලෝහ පිරවූ ප්ලාස්ටික් යනු ඉහළ විද්යුත් සහ තාප සන්නායකතාවය සහ අනෙකුත් විශේෂිත ගුණාංග සහිත ද්රව්ය නිර්මාණය කිරීම සඳහා ලෝහ අංශු වලින් පුරවා ඇති ප්ලාස්ටික් ය. අවශ්ය විද්යුත් හෝ තාප සන්නායකතාවය සහිත යෙදුම් සඳහා ලෝහ පිරවූ ප්ලාස්ටික් භාවිතා වේ. ඉන්ජෙක්ෂන් මෝල්ඩින් සඳහා භාවිතා කරන පොදු ලෝහ පිරවූ ප්ලාස්ටික් වර්ග තඹ පිරවූ ප්ලාස්ටික් සහ නිකල් පිරවූ ප්ලාස්ටික් ඇතුළත් වේ.
සමස්තයක් වශයෙන්, ඉන්ජෙක්ෂන් මෝල්ඩින් ද්රව්ය තෝරාගැනීම ශක්තිය, නම්යශීලී බව, සන්නායකතාවය සහ කල්පැවැත්ම ඇතුළුව අවසාන නිෂ්පාදනයේ නිශ්චිත අවශ්යතා මත රඳා පවතී. නිෂ්පාදකයින් බොහෝ විට පිරිවැය, ලබා ගැනීමේ හැකියාව, සැකසීමේ පහසුව සහ අවසාන නිෂ්පාදනය සඳහා අවශ්ය ගුණාංග මත පදනම්ව ද්රව්ය තෝරා ගනී.
එන්නත් අච්චු ද්රව්ය තෝරාගැනීමේදී සලකා බැලිය යුතු සාධක
ඉන්ජෙක්ෂන් මෝල්ඩින් කිරීමේදී සුදුසු ද්රව්යයක් තෝරා ගැනීම ඉතා වැදගත් වේ, එය අවසාන නිෂ්පාදනයේ ගුණාංග සහ ක්රියාකාරිත්වයට බලපෑම් කළ හැකිය. එන්නත් අච්චු ද්රව්ය තෝරාගැනීමේදී සලකා බැලිය යුතු සාධක කිහිපයක් මෙන්න:
- යාන්ත්රික ගුණ: ද්රව්යයක් තෝරාගැනීමේදී සලකා බැලිය යුතු වැදගත්ම සාධකයක් වන්නේ එහි යාන්ත්රික ගුණයි. එහි ශක්තිය, තද බව, තද බව සහ ඇඳීමට හා ඉරා දැමීමට ඇති ප්රතිරෝධය මෙයට ඇතුළත් වේ. අවසාන නිෂ්පාදනය සඳහා අවශ්ය යාන්ත්රික ගුණාංග යෙදුම සහ නිෂ්පාදනය නිරාවරණය වන ආතතිය මත රඳා පවතී.
- තාප ගුණ: ද්රව්යයක තාප ගුණ ද වැදගත් වේ, විශේෂයෙන් අවසාන නිෂ්පාදනය ඉහළ උෂ්ණත්වයකට හෝ තාප චක්රීයකරණයට නිරාවරණය වේ නම්. ද්රව්යයේ ද්රවාංකය, තාප සන්නායකතාවය සහ තාප ප්රසාරණ සංගුණකය මෙයට ඇතුළත් වේ.
- රසායනික ප්රතිරෝධය: අවසාන නිෂ්පාදනය රසායනික ද්රව්යවලට නිරාවරණය වන්නේ නම්, රසායනික හායනයට ඔරොත්තු දිය හැකි ද්රව්යයක් තෝරා ගැනීම අත්යවශ්ය වේ. ද්රව්යය අම්ල, භෂ්ම, ද්රාවක සහ අනෙකුත් රසායනික ද්රව්යවලට නිරාවරණය වීමට ඔරොත්තු දිය යුතුය, එහි ගුණාංග බිඳවැටීම හෝ නැතිවීමකින් තොරව.
- පාරිසරික සාධක: ආර්ද්රතාවය සහ පාරජම්බුල කිරණ නිරාවරණය වැනි පාරිසරික සාධක ද ද්රව්යයක ගුණ සහ ක්රියාකාරීත්වයට බලපෑ හැකිය. අවසාන නිෂ්පාදනයේ පාරිසරික තත්ත්වයන් සලකා බැලීම සහ ඒවාට ඔරොත්තු දිය හැකි ද්රව්ය තෝරා ගැනීම අත්යවශ්ය වේ.
- පිරිවැය: ද්රව්යයේ පිරිවැය ද වැදගත් කරුණකි, විශේෂයෙන් ඉහළ පරිමාවකින් යුත් නිෂ්පාදන ධාවනය සඳහා. අවසාන නිෂ්පාදනය සඳහා ලාභදායී තේරීමක් බව සහතික කිරීම සඳහා ද්රව්යයේ පිරිවැය එහි කාර්යසාධනය සහ ගුණාංගවලට සාපේක්ෂව කිරා මැන බැලිය යුතුය.
- සැකසුම් අවශ්යතා: ද්රව්යයක් සඳහා වන සැකසුම් අවශ්යතා තෝරාගැනීමේ ක්රියාවලියට ද බලපෑ හැකිය. සමහර ද්රව්ය සඳහා නිශ්චිත සැකසුම් උපකරණ හෝ ශිල්පීය ක්රම අවශ්ය විය හැකි අතර සමහරක් සැකසීමට අපහසු විය හැක. ඉන්ජෙක්ෂන් මෝල්ඩින් ක්රියාවලියේදී ද්රව්ය සාර්ථකව භාවිතා කළ හැකි බව සහතික කිරීම සඳහා සැකසුම් අවශ්යතා සලකා බැලිය යුතුය.
- නියාමන අනුකූලතාව: අවසාන වශයෙන්, අවසාන නිෂ්පාදනය සපුරාලිය යුතු ඕනෑම නියාමන අවශ්යතා සලකා බැලීම අත්යවශ්ය වේ. වෛද්ය සහ ආහාර කර්මාන්ත වැනි සමහර කර්මාන්තවලට ඔවුන්ගේ නිෂ්පාදනවල භාවිතා කරන ද්රව්ය සඳහා නිශ්චිත රෙගුලාසි ඇත. අවසාන නිෂ්පාදනය ආරක්ෂිත සහ අනුකූල බව සහතික කිරීම සඳහා මෙම නියාමන අවශ්යතා සපුරාලන ද්රව්යයක් තෝරා ගැනීම අත්යවශ්ය වේ.
සමස්තයක් වශයෙන්, ඉන්ජෙක්ෂන් මෝල්ඩින් සඳහා සුදුසු ද්රව්ය තෝරාගැනීමේදී යාන්ත්රික හා තාප ගුණ, රසායනික ප්රතිරෝධය, පාරිසරික සාධක, පිරිවැය, සැකසුම් අවශ්යතා සහ නියාමන අනුකූලතාවය ඇතුළු විවිධ සාධක හොඳින් සලකා බැලීම අවශ්ය වේ. අවසාන නිෂ්පාදනය සඳහා වඩාත් සුදුසු ද්රව්ය තෝරාගැනීම සඳහා නිෂ්පාදකයින් විසින් මෙම සාධක එකිනෙකට එරෙහිව කිරා මැන බැලිය යුතුය.
එන්නත් අච්චුවෙහි අච්චු නිර්මාණයේ වැදගත්කම
අච්චු නිර්මාණය යනු එන්නත් අච්චු ගැසීමේ ක්රියාවලියේ තීරණාත්මක අංගයකි. අච්චුවේ සැලසුම අවසාන නිෂ්පාදනයේ ගුණාත්මක භාවයට මෙන්ම නිෂ්පාදන ක්රියාවලියේ කාර්යක්ෂමතාව සහ පිරිවැය-ඵලදායීතාවයට බලපෑම් කළ හැකිය. එන්නත් අච්චු ගැසීමේදී අච්චු නිර්මාණය අත්යවශ්ය වීමට හේතු කිහිපයක් මෙන්න:
- නිෂ්පාදනයේ ගුණාත්මකභාවය: අච්චුවේ සැලසුම අවසාන නිෂ්පාදනයේ ගුණාත්මක භාවයට බලපෑ හැකිය. අච්චුව නිසි ලෙස නිර්මාණය කර නොමැති නම්, එය විකෘති කිරීම, ගිල්වීමේ සලකුණු සහ ෆ්ලෑෂ් වැනි දෝෂ ඇති විය හැක. මෙම දෝෂ හේතුවෙන් අවසාන නිෂ්පාදනය භාවිතයට ගත නොහැකි, කාර්ය සාධනය අඩු කිරීමට සහ සීරීම් අනුපාත සහ නිෂ්පාදන පිරිවැය වැඩි කළ හැක.
- නිෂ්පාදන කාර්යක්ෂමතාව: අච්චුවේ සැලසුම නිෂ්පාදන ක්රියාවලියේ කාර්යක්ෂමතාවයට ද බලපෑ හැකිය. අච්චුව ප්රශස්ත ප්රවාහ සහ සිසිලනය සඳහා නිර්මාණය කර නොමැති නම්, එය දිගු චක්ර කාලය, බලශක්ති පරිභෝජනය වැඩි කිරීම සහ ප්රතිදානය අඩු කිරීමට හේතු විය හැක. ප්රශස්ත අච්චු නිර්මාණයක් මඟින් කාර්යක්ෂමතාව වැඩි දියුණු කර නිෂ්පාදන පිරිවැය අඩු කළ හැකිය.
- පිරිවැය-ඵලදායීතාවය: අච්චු නිර්මාණය එන්නත් අච්චු සැකසීමේ ක්රියාවලියේ පිරිවැය-ඵලදායීතාවයට ද බලපෑ හැකිය. හොඳින් සැලසුම් කරන ලද අච්චුවකට ද්රව්යමය අපද්රව්ය අඩු කිරීමට, කොටස්වල ගුණාත්මකභාවය වැඩි දියුණු කිරීමට සහ ප්රතිදානය වැඩි කිරීමට, නිෂ්පාදන පිරිවැය අඩු කිරීමට හැකිය. අතිරේකව, ඉහළ පරිමාවකින් නිෂ්පාදනය සඳහා නිර්මාණය කර ඇති අච්චුවකට කොටසක පිරිවැය අඩු කර ආයෝජනයේ ප්රතිලාභය වැඩි කළ හැකිය.
- අභිරුචිකරණය: අවසාන නිෂ්පාදනයේ අභිරුචිකරණය සඳහා අච්චු නිර්මාණය ද වැදගත් කාර්යභාරයක් ඉටු කරයි. නිශ්චිත හැඩයන් සහ විශේෂාංග සඳහා අච්චුව සැලසුම් කිරීමෙන්, නිෂ්පාදකයින්ට තම පාරිභෝගිකයින්ගේ අවශ්යතාවන්ට ගැලපෙන නිෂ්පාදන නිර්මාණය කළ හැකිය. මෙමගින් පාරිභෝගික තෘප්තිය සහ පක්ෂපාතිත්වය වැඩි කිරීමට හේතු වන පරිදි වෙළඳපොලේ වැඩි නම්යශීලී බවක් සහ වෙනස්කම් ඇති කිරීමට ඉඩ සලසයි.
- ද්රව්ය තෝරාගැනීම: අච්චු සැලසුම එන්නත් අච්චු ගැසීමේදී භාවිතා කරන ද්රව්ය තේරීමට ද බලපෑම් කළ හැකිය. වාත්තු කිරීමේ ක්රමය ද්රව්ය ප්රවාහයට සහ සිසිලනයට බලපෑ හැකි අතර, එය අවසාන නිෂ්පාදනයේ යාන්ත්රික හා තාප ගුණාංගවලට බලපෑම් කළ හැකිය. නිවැරදි අච්චු මෝස්තරය තෝරා ගැනීමෙන්, නිෂ්පාදකයින්ට ද්රව්ය තෝරාගැනීම ප්රශස්ත කළ හැකි අතර අවසාන නිෂ්පාදනය අපේක්ෂිත කාර්ය සාධන අවශ්යතා සපුරාලන බවට සහතික විය හැක.
සමස්තයක් වශයෙන්, අච්චු නිර්මාණය එන්නත් අච්චු කිරීමේ ක්රියාවලියේ තීරණාත්මක සාධකයකි. හොඳින් සැලසුම් කරන ලද අච්චුවකට නිෂ්පාදනයේ ගුණාත්මකභාවය, නිෂ්පාදන කාර්යක්ෂමතාව, පිරිවැය-ඵලදායීතාවය, අභිරුචිකරණය සහ ද්රව්ය තෝරාගැනීම වැඩිදියුණු කළ හැකිය. නිෂ්පාදකයින් එන්නත් අච්චු ගැසීමේ ක්රියාවලියේ හොඳම ප්රතිඵල ලබා ගැනීම සඳහා ඔවුන්ගේ නිශ්චිත අවශ්යතා සඳහා ප්රශස්ත අච්චු නිර්මාණය කිරීමට කාලය සහ සම්පත් ආයෝජනය කළ යුතුය.
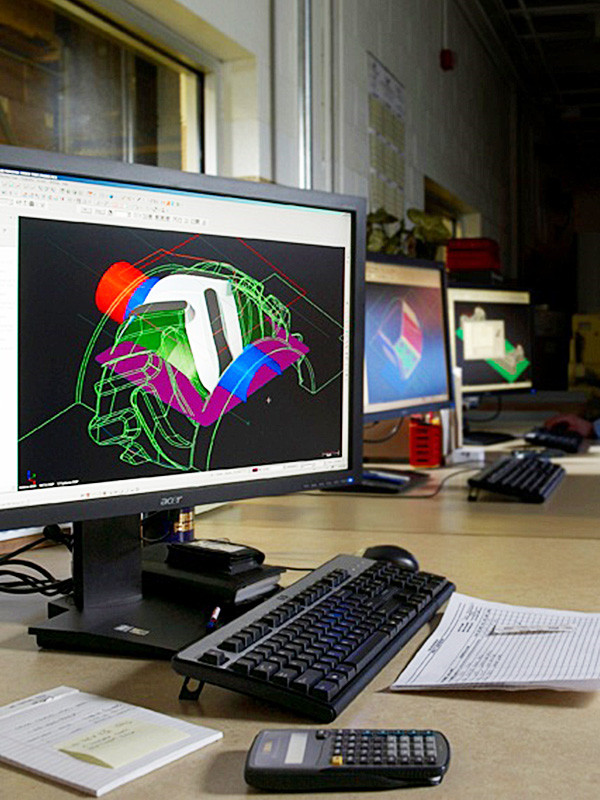
එන්නත් අච්චු ගැසීමේදී භාවිතා කරන විවිධ වර්ගයේ අච්චු
ඉන්ජෙක්ෂන් මෝල්ඩින් යනු විවිධ ප්ලාස්ටික් නිෂ්පාදන නිපදවිය හැකි බහුකාර්ය නිෂ්පාදන ක්රියාවලියකි. ඉන්ජෙක්ෂන් මෝල්ඩින්ගේ ගුණාත්මකභාවය සහ කාර්යක්ෂමතාව තීරණය කරන එක් තීරණාත්මක සාධකයක් වන්නේ භාවිතා කරන අච්චු වර්ගයයි. එන්නත් අච්චු ගැසීමේදී භාවිතා කරන විවිධ වර්ගයේ අච්චු කිහිපයක් මෙන්න:
- ද්වි-තහඩු අච්චුව: ඉන්ජෙක්ෂන් මෝල්ඩින් කිරීමේදී භාවිතා කරන වඩාත් පොදු අච්චුව ද්වි-තහඩු අච්චු වේ. ඒවා අච්චු කුහරයකින් වෙන් කරන ලද තහඩු දෙකකින් සමන්විත වේ. ප්ලාස්ටික් ද්රව්ය කුහරය තුළට එන්නත් කරනු ලැබේ, අවසන් නිශ්පාදනය සෑදීමට තහඩු දෙක ඒකාබද්ධ කරයි.
- ත්රි-තහඩු අච්චුව: ත්රි-තහඩු අච්චු තහඩු දෙකක අච්චු වලට සමාන නමුත් අච්චු කරන ලද කොටසෙන් ධාවන පද්ධතිය වෙන් කරන අතිරේක තහඩුවක් ඇත. මෙම කොටස පහසුවෙන් ඉවත් කිරීමට ඉඩ ලබා දෙන අතර චක්රය කාලය අඩු කළ හැකිය.
- උණුසුම් ධාවන අච්චුව: චක්ර කාලය සහ ද්රව්ය නාස්තිය අවම කර ගත හැකි බැවින්, උණුසුම් ධාවන අච්චු, අධි-පරිමා නිෂ්පාදන ධාවනය සඳහා භාවිතා වේ. අච්චුවේ රත් වූ ධාවන පද්ධතියක් අඩංගු වන අතර එමඟින් උණු කළ ප්ලාස්ටික් කෙලින්ම අච්චු කුහරයට ලබා දෙන අතර සීතල ධාවකයෙකුගේ අවශ්යතාවය ඉවත් කරයි.
- Cold Runer mould: Cold Runer අච්චු යනු වඩාත් මූලික පුස් වර්ගය වන අතර එය sprue, runners සහ අච්චු කුහරයකින් සමන්විත වේ. උණු කළ ප්ලාස්ටික් ස්පෘස් තුළට එන්නත් කරනු ලබන අතර, එම ප්ලාස්ටික් ධාවකයන් තුළට පෝෂණය වන අතර පසුව අච්චු කුහරය තුළට ඇතුල් වේ.
- පවුලේ අච්චුව: පවුලේ අච්චු තනි චක්රයක් තුළ කොටස් කිහිපයක් නිපදවයි. අච්චුවෙහි විවිධ කුහර කිහිපයක් අඩංගු වන අතර, ඒ සෑම එකක්ම වෙනස් කොටසක් ඇත. පවුලේ අච්චු බොහෝ විට කුඩා, ඉහළ පරිමාවකින් යුත් සංරචක සඳහා භාවිතා වේ.
- ස්ටැක් අච්චුව: ස්ටැක් අච්චු තනි චක්රයක් තුළ ප්ලාස්ටික් ස්ථර කිහිපයක් නිපදවයි. අච්චුවෙහි කුහර ස්ථර රාශියක් අඩංගු වන අතර ඒවා එකිනෙක මත ගොඩගැසී ඇත. ප්ලාස්ටික් සිදුරු තුලට එන්නත් කරනු ලබන අතර, පසුව ස්ථර එකට එකතු කර තනි, බහු ස්ථර නිෂ්පාදනයක් සාදනු ලැබේ.
- අච්චු ඇතුල් කරන්න: වාත්තු කිරීමේ ක්රියාවලියේදී වාත්තු කරන ලද කොටසට ලෝහ හෝ ප්ලාස්ටික් සංරචක ඇතුළු කිරීමට අච්චු ඇතුළු කරන්න. ප්ලාස්ටික් එන්නත් කිරීමට පෙර ඇතුල් කිරීම අච්චු කුහරය තුලට දමා ඇති අතර ප්ලාස්ටික් පසුව ඇතුල් කිරීම වට කරයි.
සමස්තයක් වශයෙන්, ඉන්ජෙක්ෂන් මෝල්ඩින් භාවිතා කරන අච්චු වර්ගය නිෂ්පාදනය කරනු ලබන නිෂ්පාදනයේ නිශ්චිත අවශ්යතා මත රඳා පවතී. නිවැරදි අච්චුව තෝරා ගැනීමෙන්, නිෂ්පාදකයින්ට එන්නත් අච්චු කිරීමේ ක්රියාවලියේ කාර්යක්ෂමතාව, ගුණාත්මකභාවය සහ පිරිවැය-ඵලදායීතාවය ප්රශස්ත කළ හැක.
ඉන්ජෙක්ෂන් මෝල්ඩින් සඳහා හොඳම භාවිතයන්
ඉන්ජෙක්ෂන් මෝල්ඩින් යනු සංකීර්ණ නිෂ්පාදන ක්රියාවලියක් වන අතර එය අපේක්ෂිත ප්රතිඵල ලබා ගැනීම සඳහා ප්රවේශමෙන් සැලසුම් කිරීම සහ ක්රියාත්මක කිරීම අවශ්ය වේ. ප්රශස්ත ගුණාත්මකභාවය, කාර්යක්ෂමතාව සහ පිරිවැය-ඵලදායී බව සහතික කිරීමට උපකාරී වන එන්නත් අච්චුව සඳහා හොඳම භාවිතයන් කිහිපයක් මෙන්න:
- නිෂ්පාදන හැකියාව සඳහා නිර්මාණය: නිෂ්පාදනයේ සැලසුම එන්නත් අච්චු කිරීම සඳහා ප්රශස්ත කළ යුතුය. මෙයට කොටස් ගණන අවම කිරීම, ඒකාකාර බිත්ති ඝණත්වය සහතික කිරීම සහ අච්චු ගැසීම සංකීර්ණ කරන යටි කැපීම් සහ අනෙකුත් ලක්ෂණ වළක්වා ගැනීම ඇතුළත් වේ.
- ද්රව්ය තෝරාගැනීම: නිෂ්පාදනයේ අවශ්යතා මත පදනම්ව ඉන්ජෙක්ෂන් මෝල්ඩින් භාවිතා කරන ද්රව්ය තෝරා ගත යුතුය. යාන්ත්රික ගුණ, තාප ගුණ සහ පාරිසරික ප්රතිරෝධය වැනි සාධක සලකා බැලිය යුතුය.
- අච්චු නිර්මාණය: නිශ්චිත නිෂ්පාදනය සඳහා අච්චු නිර්මාණය ප්රශස්ත කළ යුතුය. නිසි සිසිලනය, වාතාශ්රය සහ ගේට්ටුව සහතික කිරීම මෙන්ම සුදුසු අච්චුව තෝරා ගැනීම මෙයට ඇතුළත් වේ.
- එන්නත් පරාමිති: එන්නත් කිරීමේ පීඩනය, උෂ්ණත්වය සහ වේගය වැනි එන්නත් පරාමිතීන් ප්රශස්ත ගුණාත්මක භාවය සහ අනුකූලතාව සහතික කිරීම සඳහා ප්රවේශමෙන් පාලනය කර නිරීක්ෂණය කළ යුතුය.
- නඩත්තු කිරීම: ප්රශස්ත ක්රියාකාරිත්වය සහතික කිරීම සහ අක්රිය කාලය වැළැක්වීම සඳහා නිතිපතා එන්නත් අච්චු යන්ත්රය සහ අච්චු නඩත්තුව ඉතා වැදගත් වේ.
- තත්ත්ව පාලනය: පැමිණෙන ද්රව්ය පරීක්ෂාවේ සිට අවසාන නිෂ්පාදන පරීක්ෂාව දක්වා එන්නත් අච්චු ගැසීමේ ක්රියාවලිය පුරාම තත්ත්ව පාලනය ක්රියාත්මක කළ යුතුය. මෙයට Warpage, sink marks සහ flash වැනි අධීක්ෂණ දෝෂ ඇතුළත් වේ.
- ක්රියාවලි ප්රශස්තකරණය: අඛණ්ඩ ක්රියාවලි වැඩිදියුණු කිරීම එන්නත් අච්චු මෙහෙයුම්වල ප්රධාන අවධානයක් විය යුතුය. මෙයට චක්ර කාලය, සීරීම් අනුපාතය, සහ යන්ත්ර භාවිතය වැනි ක්රියාවලි කාර්ය සාධන ප්රමිතික අධීක්ෂණය කිරීම සහ කාර්යක්ෂමතාව සහ ගුණාත්මකභාවය ප්රශස්ත කිරීම සඳහා අවශ්ය පරිදි ගැලපීම් ඇතුළත් වේ.
සමස්තයක් වශයෙන්, ඉන්ජෙක්ෂන් මෝල්ඩින් සවිස්තරාත්මකව අවධානය යොමු කිරීම සහ අඛණ්ඩ වැඩිදියුණු කිරීම කෙරෙහි අවධානය යොමු කිරීම අවශ්ය වේ. ඉන්ජෙක්ෂන් මෝල්ඩින් සඳහා හොඳම පිළිවෙත් අනුගමනය කිරීමෙන්, නිෂ්පාදකයින්ට ප්රශස්ත ගුණාත්මක භාවය, කාර්යක්ෂමතාව සහ පිරිවැය-ඵලදායීතාවය සහතික කළ හැකි අතර ඔවුන්ගේ පාරිභෝගිකයින්ගේ අවශ්යතා සපුරාලන උසස් තත්ත්වයේ ප්ලාස්ටික් නිෂ්පාදන නිෂ්පාදනය කළ හැකිය.
ඉන්ජෙක්ෂන් මෝල්ඩින් සඳහා තත්ත්ව පාලන පියවර
ඉන්ජෙක්ෂන් මෝල්ඩින් කිරීම සඳහා තත්ත්ව පාලනය ඉතා වැදගත් වේ, එය අවසන් නිෂ්පාදනයට අවශ්ය පිරිවිතරයන් සහ ප්රමිතීන් සපුරාලන බව සහතික කරයි. එන්නත් අච්චුව සඳහා තත්ත්ව පාලන පියවර කිහිපයක් මෙන්න:
- එන ද්රව්ය පරීක්ෂාව: තත්ත්ව පාලන ක්රියාවලිය ආරම්භ කළ යුත්තේ ඉන්ජෙක්ෂන් මෝල්ඩින් සඳහා භාවිතා කරන අමුද්රව්ය සමාලෝචනය කිරීමෙනි. ද්රව්යය නිවැරදි වර්ගය, ශ්රේණිය සහ වර්ණය බව සහ අවශ්ය යාන්ත්රික සහ තාප ගුණ පිරිවිතරයන් සපුරාලන බව සත්යාපනය කිරීම මෙයට ඇතුළත් වේ.
- ක්රියාවලිය තුළ පරීක්ෂා කිරීම: එන්නත් අච්චු ගැසීමේදී, තත්ත්ව පාලන නිලධාරීන් විසින් නිෂ්පාදිතය නිවැරදිව අච්චු ගැසීම සහතික කිරීම සඳහා නිතිපතා පරීක්ෂා කළ යුතුය. සින්ක් ලකුණු, විකෘති කිරීම සහ ෆ්ලෑෂ් වැනි දෝෂ සඳහා අධීක්ෂණය කිරීම සහ නිෂ්පාදනය අවශ්ය මාන ඉවසීම් සපුරාලන බව තහවුරු කිරීම මෙයට ඇතුළත් වේ.
- අවසාන නිෂ්පාදන පරීක්ෂාව: ඉන්ජෙක්ෂන් මෝල්ඩින් ක්රියාවලිය අවසන් වූ පසු, අවශ්ය පිරිවිතරයන් සහ ප්රමිතීන් සපුරාලන බව සහතික කිරීම සඳහා අවසාන නිෂ්පාදනය පරීක්ෂා කළ යුතුය. නිෂ්පාදනයේ ඉරිතැලීම්, බුබුලු සහ හිස් තැන් වැනි දෝෂ වලින් තොර බව සහ අවශ්ය මාන ඉවසීම් සපුරාලන බවට සත්යාපනය කිරීම මෙයට ඇතුළත් වේ.
- සංඛ්යාන ක්රියාවලි පාලනය: සංඛ්යාන ක්රියාවලි පාලනය (SPC) යනු ක්රියාවලියක් නිරන්තරව උසස් තත්ත්වයේ ප්රතිඵල නිපදවන බව සහතික කිරීම සඳහා අධීක්ෂණය සහ පාලනය කිරීමේ ක්රමයකි. SPC යනු එන්නත් පීඩනය සහ උෂ්ණත්වය වැනි තීරණාත්මක ක්රියාවලි පරාමිතීන් පිළිබඳ දත්ත රැස් කිරීම සහ ක්රියාවලි විචල්යතාවය පෙන්නුම් කරන ප්රවණතා සහ රටා හඳුනා ගැනීමට සංඛ්යානමය විශ්ලේෂණය භාවිතා කිරීමයි.
- අඛණ්ඩ වැඩිදියුණු කිරීම: තත්ත්ව පාලනය නිරන්තර වැඩිදියුණු කිරීමේ අඛණ්ඩ ක්රියාවලියක් විය යුතුය. ක්රියාවලි කාර්ය සාධනය පිළිබඳ දත්ත විශ්ලේෂණය කිරීම, වැඩිදියුණු කිරීම සඳහා ක්ෂේත්ර හඳුනා ගැනීම සහ ගුණාත්මකභාවය සහ කාර්යක්ෂමතාව ප්රශස්ත කිරීම සඳහා ක්රියාවලියේ වෙනස්කම් සිදු කිරීම මෙයට ඇතුළත් වේ.
- ලේඛනගත කිරීම සහ සොයා ගැනීමේ හැකියාව: තත්ත්ව පාලන පුද්ගලයින් විසින් ක්රියාවලි පරාමිතීන්, පරීක්ෂණ ප්රතිඵල සහ නිවැරදි කිරීමේ ක්රියා ඇතුළුව එන්නත් අච්චු සැකසීමේ ක්රියාවලියේ සවිස්තරාත්මක ලියකියවිලි පවත්වා ගත යුතුය. මෙම ප්රලේඛනය සොයා ගැනීමේ හැකියාව ලබා දෙන අතර ඕනෑම ගුණාත්මක ගැටළු ඉක්මනින් හඳුනාගෙන නිවැරදි කළ හැකි බව සහතික කිරීමට උපකාරී වේ.
සමස්තයක් වශයෙන්, තත්ත්ව පාලනය එන්නත් අච්චු ගැසීමේ තීරණාත්මක අංගයක් වන අතර නිෂ්පාදන ක්රියාවලියේ සෑම අංශයකටම ඒකාබද්ධ කළ යුතුය. මෙම තත්ත්ව පාලන ක්රම ක්රියාත්මක කිරීමෙන් නිෂ්පාදකයින්ට තම පාරිභෝගිකයින්ගේ අවශ්යතා සපුරාලන උසස් තත්ත්වයේ ප්ලාස්ටික් නිෂ්පාදන නිෂ්පාදනය කළ හැකිය.
එන්නත් අච්චු ගැසීමේ පොදු දෝෂ සහ ඒවා වළක්වා ගන්නේ කෙසේද
එන්නත් අච්චු ගැසීම සංකීර්ණ ක්රියාවලියක් වන අතර එය නුසුදුසු ලෙස ක්රියාත්මක කළහොත් දෝෂ ඇති විය හැක. එන්නත් අච්චු ගැසීමේ පොදු දෝෂ කිහිපයක් සහ ඒවා වළක්වා ගන්නේ කෙසේද:
- සින්ක් ලකුණු යනු නිෂ්පාදනයේ මතුපිට ඇති අවපාත හෝ දත් වේ. ඒවා අසමාන සිසිලනය හෝ ප්රමාණවත් ඇසුරුම් පීඩනය නිසා ඇතිවේ. අච්චු නිර්මාණයට ඒකාකාර බිත්ති ඝණත්වය සහ සින්ක් ලකුණු වැලැක්වීම සඳහා ප්රමාණවත් කෙටුම්පත් කෝණ ඇතුළත් බව සහතික කර ගන්න. ඇසුරුම් පීඩනය සහ සිසිලන කාලය සකස් කිරීම සින්ක් ලකුණු වළක්වා ගැනීමට ද උපකාරී වේ.
- Warpage: Warpage යනු අච්චුවෙන් ඉවත් කිරීමෙන් පසු නිෂ්පාදනයේ විකෘති කිරීමයි. එය නිෂ්පාදනයේ අසමාන සිසිලනය හෝ අභ්යන්තර ආතතීන් නිසා සිදු වේ. Warpage වැළැක්වීම සඳහා, අච්චු නිර්මාණයට ඒකාකාර බිත්ති ඝණත්වය සහ ප්රමාණවත් සිසිලන කාලය ඇතුළත් බව සහතික කරන්න. ආතති ලක්ෂ්ය නිර්මාණය කළ හැකි නිෂ්පාදන ජ්යාමිතියෙහි තියුණු කොන හෝ හදිසි වෙනස්වීම් වළක්වා ගන්න.
- ෆ්ලෑෂ්: ෆ්ලෑෂ් යනු නිෂ්පාදනයේ සීමාවෙන් ඔබ්බට විහිදෙන අතිරික්ත ප්ලාස්ටික්, සාමාන්යයෙන් අච්චුවේ දාර වටා සිදු වේ. එය අධික එන්නත් පීඩනය, ප්රමාණවත් තද කිරීමේ බලයක් හෝ අඳින ලද අච්චුවක් නිසා ඇතිවේ. ෆ්ලෑෂ් වැළැක්වීම සඳහා, එන්නත් කිරීමේ පීඩනය සහ කලම්ප බලය සකස් කර ඇඳීමේ සලකුණු සඳහා අච්චුව නිතිපතා පරීක්ෂා කරන්න.
- කෙටි වෙඩි තැබීම්: අච්චුව අර්ධ වශයෙන් ප්ලාස්ටික් වලින් පුරවා ඇති විට කෙටි වෙඩි තැබීම් සිදු වේ. මෙය ප්රමාණවත් එන්නත් පීඩනය හෝ උෂ්ණත්වය හෝ අවහිර වූ හෝ සීමා කරන ලද ප්රවාහ නාලිකාවක් නිසා විය හැක. කෙටි වෙඩි වැලැක්වීම සඳහා, එන්නත් පීඩනය සහ උෂ්ණත්වය සකස් කරන්න, ප්රවාහ නාලිකාව පැහැදිලි සහ බාධාවකින් තොරව සහතික කරන්න.
- පිළිස්සුම් ලකුණු: පිළිස්සුම් සලකුණු යනු අධික උනුසුම් වීම හෝ අච්චුවේ අධික ඝර්ෂණය හේතුවෙන් නිෂ්පාදනයේ මතුපිට ඇති අඳුරු අවපැහැ ගැන්වීම් වේ. පිළිස්සුම් සලකුණු වලක්වා ගැනීම සඳහා, අච්චුව ප්රමාණවත් ලෙස සිසිල් කර ලිහිසි කර ඇති බවට වග බලා ගන්න, අවශ්ය පරිදි එන්නත් කිරීමේ වේගය සහ පීඩනය සකස් කරන්න.
- හිස් සහ බුබුලු: හිස් සහ බුබුලු යනු ද්රව්ය නොමැති හෝ වායු සාක්කු අඩංගු නිෂ්පාදන ප්රදේශ වේ. අච්චුවෙහි සිරවී ඇති වාතය හෝ වායුව හෝ ප්රමාණවත් ද්රව්ය ප්රවාහයක් හේතුවෙන් ඒවාට හේතු වේ. හිස් හා බුබුලු වළක්වා ගැනීම සඳහා, අච්චුව නිවැරදිව වාතාශ්රය කර ඇති බවත්, ඒකාකාර ද්රව්ය ප්රවාහය සහතික කිරීම සඳහා එන්නත් කිරීමේ වේගය සහ පීඩනය ප්රමාණවත් බවත් සහතික කරන්න.
ඉන්ජෙක්ෂන් මෝල්ඩින් උපකරණ සඳහා නඩත්තු උපදෙස්
ඉන්ජෙක්ෂන් මෝල්ඩින් උපකරණ නිෂ්පාදකයින් සඳහා සැලකිය යුතු ආයෝජනයක් වන අතර, ප්රශස්ත කාර්ය සාධනය සහ කල්පැවැත්ම සහතික කිරීම සඳහා නිසි නඩත්තු කිරීම අත්යවශ්ය වේ. එන්නත් අච්චු උපකරණ සඳහා නඩත්තු උපදෙස් කිහිපයක් මෙන්න:
- නිතිපතා පරීක්ෂණ පවත්වන්න: ඕනෑම ඇඳීම් සහ ඉරීම, හානි හෝ වෙනත් ගැටළු හඳුනා ගැනීමට උපකරණ නිතිපතා පරීක්ෂා කරන්න. හයිඩ්රොලික් හෝස්, සීල් සහ අනෙකුත් තීරණාත්මක සංරචක හොඳ තත්ත්වයේ ඇති බව සහතික කර ගන්න.
- උපකරණ පිරිසිදු කිරීම සහ ලිහිසි කිරීම: විඛාදනයට හා ඇඳීම වැළැක්වීම සඳහා උපකරණ නිතිපතා පිරිසිදු කර ලිහිසි කිරීම. නිර්දේශිත පිරිසිදු කිරීමේ සහ ලිහිසි කිරීමේ නිෂ්පාදන භාවිතා කරන්න, නිෂ්පාදකයාගේ උපදෙස් අනුගමනය කරන්න.
- හයිඩ්රොලික් ඔයිල් අධීක්ෂණය සහ නඩත්තු කිරීම: එය පිරිසිදුව සහ නිවැරදි දුස්ස්රාවිතතාවයෙන් යුක්ත බව සහතික කිරීම සඳහා එය නිතිපතා නිරීක්ෂණය කරන්න. අවශ්ය පරිදි තෙල් වෙනස් කරන්න, නිර්දේශිත තෙල් වර්ගය භාවිතා කරන්න.
- හීටර් බෑන්ඩ් නඩත්තු කරන්න: ඒවා හොඳ තත්ත්වයේ සහ නිවැරදිව උනුසුම් වීම සහතික කිරීම සඳහා ඒවා නිතිපතා පරීක්ෂා කරන්න. හානියට පත් හෝ අබලන් වූ තාපක පටි වහාම ප්රතිස්ථාපනය කරන්න.
- සිසිලන පද්ධතිය නිරීක්ෂණය කිරීම සහ නඩත්තු කිරීම: එය එන්නත් අච්චුව සඳහා ඉතා වැදගත් වේ, එය අධික උනුසුම් වීම සහ යුධ පිටවීම වළක්වයි. සිසිලන පද්ධතිය නිවැරදිව ක්රියාත්මක වන බව සහතික කිරීම සඳහා නිතිපතා අධීක්ෂණය කරන්න, අවශ්ය පරිදි සිසිලන නාලිකා පිරිසිදු කරන්න.
- දුම්රිය ක්රියාකරුවන්: හානි වැළැක්වීම සහ ප්රශස්ත ක්රියාකාරිත්වය සහතික කිරීම සඳහා නිසි උපකරණ ක්රියාත්මක කිරීම සහ නඩත්තු ක්රියා පටිපාටි පිළිබඳව දුම්රිය ක්රියාකරුවන් පුහුණු කරන්න.
- නිතිපතා නඩත්තු කිරීම උපලේඛනගත කරන්න: නඩත්තු කාලසටහනක් ස්ථාපිත කර එයට ඇලී සිටින්න. ලිහිසි තෙල් සහ තෙල් වෙනස් කිරීම් වැනි සාමාන්ය නඩත්තු කාර්යයන් උපලේඛනගත කරන්න, සහ සියලුම නඩත්තු කටයුතු ලේඛනගත කරන්න.
- අමතර කොටස් අතේ තබා ගන්න: හයිඩ්රොලික් හෝස්, සීල් සහ හීටර් බෑන්ඩ් වැනි අමතර කොටස් සපයන්න. මෙය ඉක්මනින් හානියට පත් හෝ ගෙවී ගිය කොටස් ප්රතිස්ථාපනය කර අක්රීය කාලය අවම කරයි.
ඉන්ජෙක්ෂන් මෝල්ඩින් උපකරණ නිසි ලෙස නඩත්තු කිරීම, එය කාර්යක්ෂමව ක්රියාත්මක කිරීම, උසස් තත්ත්වයේ නිෂ්පාදන නිෂ්පාදනය කිරීම සහ දිගු ආයු කාලයක් ඇති බව සහතික කිරීම සඳහා අත්යවශ්ය වේ. මෙම නඩත්තු උපදෙස් අනුගමනය කිරීමෙන්, නිෂ්පාදකයින්ට ඔවුන්ගේ උපකරණ ඉහළම තත්ත්වයේ තබා ගත හැකි අතර අක්රීය කාලය සහ අලුත්වැඩියා වියදම් අවම කර ගත හැකිය.
නිසි එන්නත් අච්චු නිෂ්පාදකයා තෝරා ගන්නේ කෙසේද
නිසි ඉන්ජෙක්ෂන් මෝල්ඩින් නිෂ්පාදකයා තෝරා ගැනීම ඔබේ නිෂ්පාදනවල ගුණාත්මකභාවය සහ පිරිවැය සැලකිය යුතු ලෙස බලපාන වැදගත් තීරණයකි. එන්නත් අච්චු නිෂ්පාදකයෙකු තෝරාගැනීමේදී සලකා බැලිය යුතු කරුණු කිහිපයක් මෙන්න:
- පළපුරුද්ද සහ ප්රවීණත්වය: එන්නත් අච්චු ගැසීම පිළිබඳ පුළුල් පළපුරුද්දක් සහ ප්රවීණත්වයක් ඇති නිෂ්පාදකයෙකු සොයන්න. ඔවුන්ගේ නිෂ්පාදන ක්රියාවලීන්, තත්ත්ව පාලන පියවර සහ සහතික කිරීම් ගැන විමසන්න.
- තාක්ෂණය සහ උපකරණ: නවීන තාක්ෂණය සහ උපකරණ භාවිතා කරන නිෂ්පාදකයෙකු සොයන්න. මෙය ස්ථාවර ගුණාත්මක භාවය, කෙටි ඊයම් කාලය සහ පිරිවැය-ඵලදායී බව සහතික කිරීමට උපකාරී වේ.
- ද්රව්ය සහ හැකියාවන්: නිෂ්පාදකයාට වැඩ කළ හැකි ද්රව්ය වර්ග සහ ඒවායේ හැකියාවන් සලකා බලන්න. විශේෂිත ද්රව්ය ඇතුළුව පුළුල් පරාසයක ද්රව්ය හැසිරවිය හැකි සහ විවිධ නිෂ්පාදන ප්රමාණයන් සහ හැඩයන් නිෂ්පාදනය කළ හැකි නිෂ්පාදකයෙකු සොයන්න.
- තත්ත්ව පාලන පියවර: තත්ත්ව පාලනය කෙරෙහි දැඩි අවධානයක් යොමු කරන නිෂ්පාදකයෙකු සොයන්න. පරීක්ෂා කිරීම සහ පරීක්ෂණ ක්රියා පටිපාටි, සහ ඔවුන්ට තිබිය හැකි ඕනෑම සහතිකයක් වැනි ඔවුන්ගේ තත්ත්ව පාලන පියවර ගැන විමසන්න.
- පාරිභෝගික සේවය: විශිෂ්ට පාරිභෝගික සේවාවක් සපයන නිෂ්පාදකයෙකු සොයන්න. ඔබේ නිශ්චිත අවශ්යතා සපුරාලීම සඳහා ප්රතිචාර දැක්වීම, සන්නිවේදනය සහ ඔබ සමඟ වැඩ කිරීමට ඇති කැමැත්ත සලකා බලන්න.
- පිරිවැය සහ ඉදිරි කාලය: ඔබේ ව්යාපෘතිය සඳහා නිෂ්පාදකයාගේ පිරිවැය සහ ඉදිරි කාලය සලකා බලන්න. ඔබේ අවශ්යතා සපුරාලන තරඟකාරී මිල ගණන් සහ යථාර්ථවාදී ඉදිරි කාලයන් ලබා දෙන නිෂ්පාදකයෙකු සොයන්න.
- යොමු කිරීම් සහ සමාලෝචන: යොමු කිරීම් සඳහා විමසන්න සහ නිෂ්පාදකයාගේ මාර්ගගත සමාලෝචන පරීක්ෂා කරන්න. මෙය ඔබට ඔවුන්ගේ කීර්තිය සහ අනෙකුත් පාරිභෝගිකයින්ගේ අත්දැකීම් පිළිබඳ වඩා හොඳ හැඟීමක් ලබා ගැනීමට උපකාරී වේ.
මෙම සාධක සලකා බැලීමෙන් සහ ගැඹුරු පර්යේෂණ පැවැත්වීමෙන් ඔබේ ව්යාපෘතිය සඳහා නිසි එන්නත් අච්චු නිෂ්පාදකයා තෝරා ගත හැකිය. නිවැරදි අත්දැකීම්, හැකියාවන් සහ ගුණාත්මකභාවය සඳහා කැපවීම සහිත පිළිගත් නිෂ්පාදකයෙකුට ඔබේ නිෂ්පාදන කාර්යක්ෂමව, ලාභදායී ලෙස සහ ඔබේ නිශ්චිත පිරිවිතරයන්ට අනුව නිෂ්පාදනය කිරීම සහතික කිරීමට උපකාරී වේ.
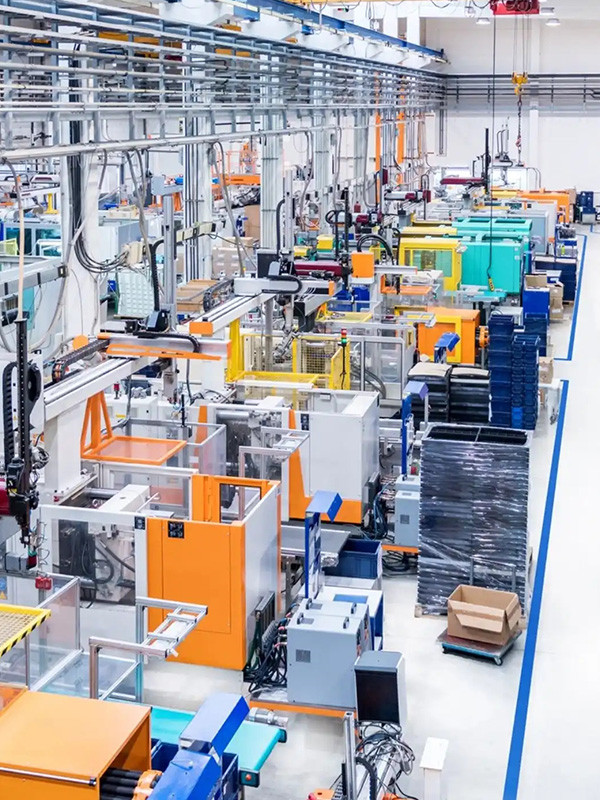
අභිරුචි ප්ලාස්ටික් එන්නත් අච්චු ගැසීමේ පිරිවැය සලකා බැලීම
අභිරුචි ප්ලාස්ටික් ඉන්ජෙක්ෂන් මෝල්ඩින් යනු සංකීර්ණ, උසස් තත්ත්වයේ කොටස් පරිමාණයෙන් නිපදවිය හැකි ඉතා බහුකාර්ය නිෂ්පාදන ක්රියාවලියකි. කෙසේ වෙතත්, මෙම නිෂ්පාදන ක්රියාවලිය භාවිතා කිරීමේදී පිරිවැය සලකා බැලීම තීරණාත්මක සාධකයකි. අභිරුචි ප්ලාස්ටික් එන්නත් අච්චු ගැසීමේ ප්රධාන පිරිවැය සලකා බැලීම් කිහිපයක් මෙන්න:
- ද්රව්ය පිරිවැය: ඉන්ජෙක්ෂන් මෝල්ඩින් ක්රියාවලියේදී භාවිතා කරන ද්රව්ය වර්ගය සහ ප්රමාණය මිලට බලපානු ඇත. ඉහළ කාර්යසාධනයක් සහිත ඉංජිනේරු ප්ලාස්ටික් වැනි සමහර ද්රව්ය අනෙකුත් ඒවාට වඩා මිල අධිකය. සැපයුම් දාම කඩාකප්පල් කිරීම්, වෙළඳපල ඉල්ලුම සහ මිල උච්චාවචනයන් ද ද්රව්යවල පිරිවැයට බලපෑ හැකිය.
- මෙවලම් පිරිවැය: මෙවලම්වල පිරිවැය, හෝ කොටස් නිෂ්පාදනය කිරීමට භාවිතා කරන අච්චු, අභිරුචි ප්ලාස්ටික් එන්නත් අච්චු ගැසීමේදී සැලකිය යුතු වියදමකි. කොටසෙහි සංකීර්ණත්වය, අච්චුවේ ඇති කුහර ගණන සහ අච්චුව සෑදීමට භාවිතා කරන ද්රව්ය සියල්ලම මෙවලම් පිරිවැයට බලපානු ඇත. මෙවලම් මිල අධික විය හැකි නමුත් නිෂ්පාදන කාර්යක්ෂමතාව වැඩි කිරීමෙන් කාලයත් සමඟ ඒකක පිරිවැය අඩු කිරීමට උපකාරී වේ.
- නිෂ්පාදන පරිමාව: නිෂ්පාදනය කරන ලද කොටස් පරිමාව එන්නත් අච්චු පිරිවැයට බලපානු ඇත. ඉහළ පරිමා නිෂ්පාදනය ඒකක පිරිවැය අඩු කිරීමට උපකාර කළ හැකි අතර, අඩු-පරිමා නිෂ්පාදනය සඳහා වැඩි මෙවලම් සහ සැකසුම් කාලයක අවශ්යතාවය හේතුවෙන් වැඩි ඒකක පිරිවැයක් තිබිය හැක.
- ශ්රම පිරිවැය: ශ්රම පිරිවැය එන්නත් අච්චු ගැසීමේදී සැලකිය යුතු සාධකයකි, විශේෂයෙන් වැඩිපුර ශ්රම ශ්රමය අවශ්ය වන වඩාත් සංකීර්ණ කොටස් සඳහා. මෙහෙයුම්කරුවන්ගේ කුසලතා මට්ටම සහ කොටසෙහි සංකීර්ණත්වය බෙදා හැරීමේ පිරිවැයට බලපානු ඇත.
- තත්ත්ව පාලන පිරිවැය: කොටස්වල අඛණ්ඩතාව සහතික කිරීම සඳහා තත්ත්ව පාලනය පවත්වා ගැනීම අත්යවශ්ය වේ. තත්ත්ව පාලන මිලට පරීක්ෂණ උපකරණ, පරීක්ෂණ සහ ශ්රමය ඇතුළත් විය හැකිය.
- නැව්ගත කිරීමේ පිරිවැය: පාරිභෝගිකයාට හෝ වෙනත් ස්ථානවලට කොටස් නැව්ගත කිරීම සැලකිය යුතු වියදමක් විය හැකිය, විශේෂයෙන් විශාල හෝ බර විස්තර සඳහා.
මෙම පිරිවැය සාධක සලකා බැලීමෙන් සහ ඉන්ජෙක්ෂන් මෝල්ඩින් ක්රියාවලිය ප්රශස්ත කිරීම මගින් නිෂ්පාදකයින්ට අඩු මිලට උසස් තත්ත්වයේ කොටස් නිෂ්පාදනය කළ හැකිය. ද්රව්යමය අපද්රව්ය අවම කිරීම, නිෂ්පාදන කාර්යක්ෂමතාව වැඩි කිරීම සහ සැකසීම් සහ වෙනස්වීම් කාලය අවම කිරීම මගින් මෙය සාක්ෂාත් කරගත හැකිය. පළපුරුදු සහ දැනුවත් ඉන්ජෙක්ෂන් මෝල්ඩින් නිෂ්පාදකයෙකු සමඟ වැඩ කිරීමෙන් ක්රියාවලිය ප්රශස්ත කිරීමට සහ පිරිවැය අඩු කිරීමට ද උපකාරී වේ.
ඉන්ජෙක්ෂන් මෝල්ඩින් තාක්ෂණයේ ප්රවණතා සහ නවෝත්පාදනයන්
ඉන්ජෙක්ෂන් මෝල්ඩින් තාක්ෂණය වසර ගණනාවක් තිස්සේ පවතින නමුත්, මෙම නිෂ්පාදන ක්රියාවලියේ අනාගතය හැඩගස්වන බොහෝ නවෝත්පාදනයන් සහ ප්රවණතා තවමත් පවතී. එන්නත් අච්චු තාක්ෂණයේ ඉහළම ප්රවණතා සහ නවෝත්පාදන කිහිපයක් මෙන්න:
- ත්රිමාණ මුද්රණය සහ ආකලන නිෂ්පාදනය: ත්රිමාණ මුද්රණය සහ ආකලන නිෂ්පාදනය එන්නත් අච්චු කර්මාන්තයේ වැඩි වැඩියෙන් ජනප්රිය වෙමින් පවතී. සාම්ප්රදායික එන්නත් අච්චුවකින් සාක්ෂාත් කර ගැනීමට අපහසු හෝ කළ නොහැකි සංකීර්ණ හැඩතල සහ ජ්යාමිතීන් නිර්මාණය කිරීමට මෙම තාක්ෂණය ඉඩ සලසයි.
- බහු-ද්රව්ය එන්නත් අච්චුව: බහු-ද්රව්ය එන්නත් අච්චුව තනි පහරකින් බහු ද්රව්ය හෝ වර්ණ සහිත කොටස් නිර්මාණය කිරීමට ඉඩ සලසයි. මෙම ක්රියාවලිය නිෂ්පාදන කාලය හා පිරිවැය අඩු කර ගත හැකි අතර අද්විතීය ගුණාංග සහ පෙනුම සහිත කාර්යයන් නිර්මාණය කළ හැකිය.
- ස්වයංක්රීයකරණය සහ කර්මාන්ත 4.0: IoT සංවේදක සහ රොබෝ යන්ත්ර වැනි ස්වයංක්රීයකරණය සහ කර්මාන්ත 4.0 තාක්ෂණයන් එන්නත් අච්චු යන්ත්ර සහ ක්රියාවලි වලට ඒකාබද්ධ කෙරේ. මෙය නිෂ්පාදන කාර්යක්ෂමතාව වැඩි දියුණු කිරීම, ශ්රම පිරිවැය අඩු කිරීම සහ තත්ත්ව පාලනය වැඩිදියුණු කළ හැකිය.
- තිරසාර ද්රව්ය සහ ක්රියාවලි: සමාගම් තම පාරිසරික බලපෑම අවම කිරීමට උත්සාහ කරන විට, එන්නත් අච්චු කර්මාන්තයේ තිරසාර ද්රව්ය සහ ක්රම වඩාත් වැදගත් වෙමින් පවතී. අපද්රව්ය හා බලශක්ති පරිභෝජනය අවම කරන ජෛව හායනයට ලක්විය හැකි හෝ ප්රතිචක්රීකරණය කරන ලද ද්රව්ය සහ ක්රියාවලීන් භාවිතා කිරීම මෙයට ඇතුළත් වේ.
- ස්මාර්ට් නිෂ්පාදනය සහ අනාවැකි නඩත්තු කිරීම: යන්ත්ර ඉගෙනීම සහ අනාවැකි නඩත්තු කිරීම වැනි ස්මාර්ට් නිෂ්පාදන තාක්ෂණයන් එන්නත් අච්චු සැකසීමේ ක්රියාවලීන් ප්රශස්ත කිරීමට සහ අක්රිය කාලය අඩු කිරීමට භාවිතා කරයි. මෙය සමස්ත කාර්යක්ෂමතාව වැඩි දියුණු කර නඩත්තු වියදම් අඩු කළ හැකිය.
- ඉහළ ක්රියාකාරී ද්රව්ය: වැඩි දියුණු කළ ශක්තිය, කල්පැවැත්ම සහ තාප ප්රතිරෝධය සහිත ද්රව්ය ඇතුළුව එන්නත් අච්චු කිරීම සඳහා නව ඉහළ ක්රියාකාරී ද්රව්ය සංවර්ධනය වෙමින් පවතී. මෙම ද්රව්ය වාහන අමතර කොටස්වල සිට වෛද්ය උපකරණ දක්වා විවිධ යෙදුම්වල භාවිතා කළ හැක.
මෙම ප්රවණතා සහ නවෝත්පාදනයන් පිළිබඳව යාවත්කාලීනව සිටීමෙන්, ඉන්ජෙක්ෂන් මෝල්ඩින් නිෂ්පාදකයින්ට තරඟකාරීව සිටිය හැකි අතර ඔවුන්ගේ පාරිභෝගිකයින්ට උසස් තත්ත්වයේ කොටස් සැපයීම දිගටම කරගෙන යා හැකිය. නව තාක්ෂණයන් සහ ද්රව්ය සංවර්ධනය වන විට, එන්නත් අච්චු කර්මාන්තය අඛණ්ඩව පරිණාමය වෙමින් පාරිභෝගිකයින්ගේ සහ ව්යාපාරවල වෙනස්වන අවශ්යතා සපුරාලීමට අනුවර්තනය වනු ඇත.
ඉන්ජෙක්ෂන් මෝල්ඩින් හි තිරසාරත්වය: නාස්තිය සහ බලශක්ති පරිභෝජනය අඩු කිරීම
සමාගම් තම පාරිසරික බලපෑම අවම කිරීමට සහ පරිසර හිතකාමී නිෂ්පාදන සඳහා වැඩිවන ඉල්ලුම සපුරාලීමට උත්සාහ කරන බැවින් තිරසාරභාවය එන්නත් අච්චු කර්මාන්තයේ වඩ වඩාත් වැදගත් වෙමින් පවතී. එන්නත් අච්චු නිෂ්පාදකයින්ට අපද්රව්ය සහ බලශක්ති පරිභෝජනය අඩු කළ හැකි ක්රම කිහිපයක් මෙන්න:
- තිරසාර ද්රව්ය භාවිතා කරන්න: ද්රව්ය තෝරා ගැනීම තිරසාරභාවයේ තීරණාත්මක සාධකයකි. ඉන්ජෙක්ෂන් මෝල්ඩින් නිෂ්පාදකයින්ට පාරිසරික බලපෑම අවම කිරීම සඳහා ජෛව හායනයට ලක්විය හැකි හෝ ප්රතිචක්රීකරණය කළ ද්රව්ය භාවිතා කළ හැකිය. නිදසුනක් වශයෙන්, ජෛව හායනයට ලක්විය හැකි ප්ලාස්ටික්, කාලයත් සමඟ ස්වභාවිකව බිඳී යා හැකි අතර කුණු ගොඩකිරීම් වල අපද්රව්ය ප්රමාණය අඩු කරයි. පශ්චාත් පාරිභෝගික ප්රතිචක්රීකරණය කරන ලද ප්ලාස්ටික් වැනි ප්රතිචක්රීකරණය කරන ලද ද්රව්ය ද අපද්රව්ය හා බලශක්ති පරිභෝජනය අඩු කිරීමට උපකාරී වේ.
- ද්රව්ය අපද්රව්ය අඩු කරන්න: ඉන්ජෙක්ෂන් මෝල්ඩින් නිෂ්පාදකයින්ට කොටසේ සහ අච්චුවේ සැලසුම ප්රශස්ත කිරීම මගින් ද්රව්ය අපද්රව්ය අඩු කළ හැකිය. භාවිතා කරන අතිරික්ත ද්රව්ය ප්රමාණය අඩු කිරීම, අච්චුවේ ඇති කුහර සංඛ්යාව අවම කිරීම සහ කොටසෙහි සමස්ත බර අඩු කිරීම ඇතුළත් වේ. ද්රව්යමය අපද්රව්ය අඩු කිරීමෙන් නිෂ්පාදකයින්ට ද්රව්යමය පිරිවැය ඉතිරි කර ගත හැකි අතර ඔවුන්ගේ පාරිසරික බලපෑම අවම කර ගත හැකිය.
- නිෂ්පාදන කාර්යක්ෂමතාව ප්රශස්ත කිරීම: එන්නත් අච්චු නිෂ්පාදකයින්ට බලශක්ති පරිභෝජනය අඩු කිරීම සඳහා ඔවුන්ගේ නිෂ්පාදන ක්රියාවලීන් ප්රශස්ත කළ හැකිය. ඉහළ කාර්යක්ෂමතාවයකින් යුත් ඉන්ජෙක්ෂන් මෝල්ඩින් යන්ත්ර භාවිතා කිරීම, අච්චු ක්රියාවලි පරාමිතීන් ප්රශස්ත කිරීම සහ අක්රීය කාලය අවම කිරීම මෙයට ඇතුළත් වේ. බලශක්ති පරිභෝජනය අඩු කිරීමෙන් නිෂ්පාදකයින්ට බලශක්ති පිරිවැය ඉතිරි කර ගත හැකි අතර ඔවුන්ගේ කාබන් පියසටහන අඩු කළ හැකිය.
- තිරසාර භාවිතයන් ක්රියාත්මක කිරීම: එන්නත් අච්චු නිෂ්පාදකයින්ට ප්රතිචක්රීකරණය සහ අපද්රව්ය අවම කිරීමේ වැඩසටහන්, පුනර්ජනනීය බලශක්ති ප්රභවයන් භාවිතා කිරීම සහ ඔවුන්ගේ සේවකයින් සහ සැපයුම්කරුවන් අතර තිරසාරභාවය ප්රවර්ධනය කිරීම වැනි තිරසාර භාවිතයන් ද ක්රියාත්මක කළ හැකිය. සැපයුම් දාමය පුරා තිරසාර භාවිතයන් ප්රවර්ධනය කිරීමෙන්, සමස්තයක් වශයෙන් වඩාත් තිරසාර කර්මාන්තයක් නිර්මාණය කිරීමට නිෂ්පාදකයින්ට උපකාර කළ හැකිය.
- තිරසාර ඇසුරුම් භාවිතා කරන්න: අවසාන වශයෙන්, ඉන්ජෙක්ෂන් මෝල්ඩින් නිෂ්පාදකයින්ට අපද්රව්ය සහ පාරිසරික බලපෑම අවම කිරීම සඳහා තිරසාර ඇසුරුම් ද්රව්ය සහ මෝස්තර භාවිතා කළ හැකිය. මෙයට ජෛව හායනය කළ හැකි හෝ ප්රතිචක්රීකරණය කළ හැකි ඇසුරුම් ද්රව්ය භාවිතා කිරීම, ඇසුරුම් අපද්රව්ය අවම කිරීම සහ නැවත භාවිත කළ හැකි හෝ නැවත පිරවිය හැකි ඇසුරුම් සැලසුම් කිරීම ඇතුළත් වේ.
මෙම තිරසාර භාවිතයන් ක්රියාවට නැංවීමෙන්, ඉන්ජෙක්ෂන් මෝල්ඩින් නිෂ්පාදකයින්ට ඔවුන්ගේ පාරිසරික බලපෑම අවම කර සමස්තයක් ලෙස වඩාත් තිරසාර කර්මාන්තයක් නිර්මාණය කළ හැකිය. පාරිභෝගිකයින්ට සහ ව්යාපාර සඳහා තිරසාරභාවය වඩ වඩාත් වැදගත් වන බැවින්, තිරසාරභාවයට ප්රමුඛත්වය දෙන එන්නත් අච්චු නිෂ්පාදකයින් පරිසර හිතකාමී නිෂ්පාදන සඳහා වැඩිවන ඉල්ලුම සපුරාලීම සඳහා හොඳින් ස්ථානගත වනු ඇත.
අභිරුචි ප්ලාස්ටික් එන්නත් අච්චුව වෙනත් නිෂ්පාදන ක්රියාවලීන් සමඟ සංසන්දනය කරන ආකාරය
අභිරුචි ප්ලාස්ටික් ඉන්ජෙක්ෂන් මෝල්ඩින් යනු උසස් තත්ත්වයේ ප්ලාස්ටික් කොටස් විශාල ප්රමාණවලින් නිෂ්පාදනය කිරීම සඳහා ජනප්රිය නිෂ්පාදන ක්රියාවලියකි. කෙසේ වෙතත්, ප්ලාස්ටික් කොටස් සෑදීම සඳහා වෙනත් නිෂ්පාදන ක්රියාවලීන් කිහිපයක් භාවිතා කළ හැකි අතර, ඒ සෑම එකක්ම වාසි සහ අවාසි ඇත. අභිරුචි ප්ලාස්ටික් එන්නත් අච්චුව වෙනත් නිෂ්පාදන ක්රියාවලීන් සමඟ සංසන්දනය කිරීම මෙන්න:
- ත්රිමාණ මුද්රණය: ත්රිමාණ මුද්රණය යනු සංකීර්ණ හැඩතල සහ ජ්යාමිතිය නිර්මාණය කිරීමට ඉඩ සලසන වේගයෙන් වර්ධනය වන තාක්ෂණයකි. කුඩා පරිමාණ නිෂ්පාදනය සඳහා ත්රිමාණ මුද්රණය භාවිතා කළ හැකි අතර, ඉන්ජෙක්ෂන් මෝල්ඩින් සාමාන්යයෙන් විශාල කොටස් නිෂ්පාදනය සඳහා ඉන්ජෙක්ෂන් මෝල්ඩින් වලට වඩා අඩු පිරිවැයක් සහිත සහ කාර්යක්ෂම වේ.
- බ්ලෝ මෝල්ඩින්: බ්ලෝ මෝල්ඩින් යනු බෝතල් සහ බහාලුම් වැනි හිස් ප්ලාස්ටික් කොටස් නිර්මාණය කරන නිෂ්පාදන ක්රියාවලියකි. බ්ලෝ මෝල්ඩින් විශේෂාංග විශාල ප්රමාණයක් නිපදවීමට යෝග්ය වන අතර, ඉන්ජෙක්ෂන් මෝල්ඩින් සාමාන්යයෙන් ඉන්ජෙක්ෂන් මෝල්ඩින් වලට වඩා අඩු නිරවද්ය වන අතර වඩාත් සංකීර්ණ හැඩතල සහ ජ්යාමිතිය නිර්මාණය කිරීම සඳහා සුදුසු නොවේ.
- CNC යන්ත්රකරණය: CNC යන්ත්රකරණය යනු ඝන ද්රව්ය කොටසකින් කොටස් කැපීම සහ හැඩගැන්වීම ඇතුළත් වන අඩු කරන නිෂ්පාදන ක්රියාවලියකි. CNC යන්ත්රකරණය කුඩා ප්රමාණවලින් ඉහළ නිරවද්යතාවයකින් යුත් කොටස් නිෂ්පාදනය කිරීම සඳහා සුදුසු වන අතර, එය සාමාන්යයෙන් ඉන්ජෙක්ෂන් මෝල්ඩින් තරම් ලාභදායී හෝ කාර්යක්ෂම නොවේ.
- භ්රමණ මෝල්ඩින්: භ්රමණ අච්චුව යනු නිෂ්පාදන ක්රියාවලියක් වන අතර එය රත් කරන අතරතුර අච්චුවක් ලම්බක අක්ෂ දෙකක් වටා කරකැවීම ඇතුළත් වේ. භ්රමණ අච්චුව මගින් සංකීර්ණ ජ්යාමිතිය සහිත විශාල කොටස් නිපදවිය හැකි අතර, ඉන්ජෙක්ෂන් මෝල්ඩින් සාමාන්යයෙන් ඉන්ජෙක්ෂන් මෝල්ඩින් වලට වඩා අඩු නිරවද්ය වන අතර කුඩා කොටස් සෑදීමට සුදුසු නොවේ.
- Thermoforming: Thermoforming යනු නිෂ්පාදන ක්රියාවලියක් වන අතර එය ප්ලාස්ටික් පත්රයක් රත් කර අච්චුවක් මත හැඩ ගැන්වීම ඇතුළත් වේ. තාප හැඩගැන්වීම සරල ජ්යාමිතිය සහිත විශාල කොටස් නිපදවිය හැකි අතර, ඉන්ජෙක්ෂන් මෝල්ඩින් සාමාන්යයෙන් ඉන්ජෙක්ෂන් මෝල්ඩින් වලට වඩා අඩු නිරවද්යතාවයක් වන අතර වඩාත් සංකීර්ණ හැඩතල සහ ජ්යාමිතීන් නිර්මාණය කිරීම සඳහා සුදුසු නොවේ.
අභිරුචි ප්ලාස්ටික් ඉන්ජෙක්ෂන් මෝල්ඩින් යනු උසස් තත්ත්වයේ ප්ලාස්ටික් කොටස් විශාල ප්රමාණවලින් නිෂ්පාදනය කිරීම සඳහා ඉතා බහුකාර්ය සහ ලාභදායී නිෂ්පාදන ක්රියාවලියකි. වෙනත් නිෂ්පාදන ක්රියාවලීන් නිශ්චිත යෙදුම් හෝ නිෂ්පාදන පරිමාවන් සඳහා වඩාත් සුදුසු විය හැකි අතර, ඉන්ජෙක්ෂන් මෝල්ඩින් එහි වේගය, නිරවද්යතාවය සහ පිරිවැය-ඵලදායීතාවය හේතුවෙන් බොහෝ නිෂ්පාදකයින් සඳහා සාමාන්යයෙන් වඩාත් කැමති තේරීම වේ. අවසාන වශයෙන්, නිෂ්පාදන ක්රියාවලිය තෝරා ගැනීම කොටස් සැලසුම, නිෂ්පාදන පරිමාව සහ අයවැය ඇතුළු විවිධ සාධක මත රඳා පවතී.
ඉන්ජෙක්ෂන් මෝල්ඩින් බාහිරින් ලබා ගැනීමේ වාසි සහ අවාසි
බාහිරින් ලබා ගැනීම ඉන්ජෙක්ෂන් මෝල්ඩින් යනු තමන්ගේම එන්නත් අච්චු ගැසීමේ උපකරණ හෝ විශේෂඥතාව සඳහා ආයෝජනය නොකර ප්ලාස්ටික් කොටස් නිෂ්පාදනය කිරීමට බලාපොරොත්තු වන සමාගම් සඳහා පොදු භාවිතයකි. බාහිරින් ලබා දීමෙන් ප්රතිලාභ කිහිපයක් ලබා දිය හැකි අතර, එයට සමහර විභව අවාසි ද ඇත. මෙන්න සමහර වාසි සහ අවාසි බාහිරින් ලබා ගැනීමේ ඉන්ජෙක්ෂන් මෝල්ඩින්:
කිහිප දෙනකුගේ හොඳ:
- පිරිවැය ඉතිරිකිරීම්: ගෘහස්ථ නිෂ්පාදන පහසුකමක් පිහිටුවීමට වඩා බාහිරින් ලබාගන්නා එන්නත් අච්චුව බොහෝ විට ලාභදායී වේ. මිල අධික උපකරණ සහ පිරිස් සඳහා ආයෝජනය කිරීම සාධාරණීකරණය කිරීම සඳහා වැඩි මුදලක් හෝ පරිමාවක් අවශ්ය වන කුඩා හා මධ්යම ප්රමාණයේ සමාගම් සඳහා මෙය විශේෂයෙන්ම සත්ය වේ.
- ප්රවීණත්වය: ඉන්ජෙක්ෂන් මෝල්ඩින් සමාගම් නිෂ්පාදනය සම්බන්ධයෙන් විශේෂත්වයක් දක්වන අතර උසස් තත්ත්වයේ ප්රමිතියකට අමතර කොටස් නිෂ්පාදනය කිරීම සහතික කිරීමට විශේෂඥ දැනුමක් ඇත. ඉන්ජෙක්ෂන් මෝල්ඩින් බාහිරින් ලබා දීමෙන්, පළපුරුදු වෘත්තිකයන්ගේ විශේෂඥතාවයෙන් සමාගම්වලට ප්රයෝජන ගත හැකිය.
- ධාරිතාව: ඉන්ජෙක්ෂන් මෝල්ඩින් සමාගම්වලට ඉක්මනින් හා කාර්යක්ෂමව කොටස් විශාල ප්රමාණයක් නිෂ්පාදනය කළ හැක. නිතිපතා විශාල විශේෂාංග ප්රමාණයක් සෑදිය යුතු සමාගම් සඳහා මෙය විශේෂයෙන් ප්රයෝජනවත් වේ.
- නම්යශීලී බව: බාහිරින් ලබා දෙන එන්නත් අච්චු ගැසීම සමාගම්වලට ඔවුන්ගේ නිෂ්පාදන කාලසටහන් වලදී වඩාත් නම්යශීලී වීමට ඉඩ සලසයි. උපාංග සහ අච්චු වෙනස් කිරීමේ ප්රාග්ධන පිරිවැය ගැන කනස්සල්ලෙන් තොරව සමාගම්වලට ඔවුන්ගේ නිෂ්පාදන පරිමාව වෙනස් කිරීමට හෝ විවිධ කොටස්වලට මාරු වීමට හැකිය.
අවාසි:
- සන්නිවේදනය: බාහිරින් ලබා දීම ඉන්ජෙක්ෂන් මෝල්ඩින් පාරිභෝගිකයා සහ සමාගම අතර සන්නිවේදන අභියෝග ඇති කළ හැකිය. සන්නිවේදනයේ වරදවා වටහාගැනීම් හෝ ප්රමාදයන් නිසා නිෂ්පාදනයේ වැරදි හෝ ප්රමාදයන් ඇති විය හැක.
- තත්ත්ව පාලනය: බාහිරින් ලබා ගැනීම ඉන්ජෙක්ෂන් මෝල්ඩින් යනු අවශ්ය තත්ත්ව ප්රමිතීන්ට අනුව කොටස් නිෂ්පාදනය කිරීමට බාහිර සමාගමක් මත යැපීමයි. බාහිර සමාගමක් සමඟ වැඩ කිරීමේදී තත්ත්ව පාලනය අභියෝගාත්මක විය හැකි අතර, අවශ්ය පිරිවිතරයන් සපුරාලිය යුතු විශේෂාංග ලබා ගැනීමේ අවදානම සැමවිටම පවතී.
- යැපීම: බාහිර නිෂ්පාදන සමාගමක් මත යැපීම යනු බාහිරින් ලබා ගැනීමයි. මෙය සැපයුම්කරුගේ විශ්වසනීයත්වය, ස්ථාවරත්වය සහ බෙදා හැරීමේ වේලාවන් සම්බන්ධයෙන් අවදානම් ඇති කළ හැකිය.
- බුද්ධිමය දේපල: බාහිරින් ලබා දීම ඉන්ජෙක්ෂන් මෝල්ඩින් බුද්ධිමය දේපල ආරක්ෂා කිරීම සඳහා අවදානම් නිර්මාණය කළ හැකිය. සමාගම් ඔවුන්ගේ සැලසුම් සහ තාක්ෂණය සුදුසු නීතිමය පියවරයන් මගින් ආරක්ෂා කර ඇති බවට සහතික විය යුතුය.
අභිරුචි ප්ලාස්ටික් එන්නත් අච්චුව සඳහා අනාගත අපේක්ෂාවන්
අභිරුචි ප්ලාස්ටික් ඉන්ජෙක්ෂන් මෝල්ඩින් දශක ගණනාවක් තිස්සේ විශ්වසනීය හා බහුකාර්ය නිෂ්පාදන ක්රියාවලියකි. මෑත වසරවලදී, තාක්ෂණයේ සහ ද්රව්යවල දියුණුව එන්නත් අච්චු ගැසීමේ හැකියාවන් සහ විභවයන් අඛණ්ඩව වැඩි දියුණු කර ඇත. අභිරුචි ප්ලාස්ටික් එන්නත් අච්චුව සඳහා අනාගත අපේක්ෂාවන් කිහිපයක් මෙන්න:
- කර්මාන්ත 4.0 තාක්ෂණයන් අනුගමනය කිරීම: කෘත්රිම බුද්ධිය, යන්ත්ර ඉගෙනීම සහ ඉන්ටර්නෙට් ඔෆ් තින්ග්ස් (IoT) වැනි කර්මාන්ත 4.0 තාක්ෂණයන් ඒකාබද්ධ කිරීම ස්වයංක්රීයකරණය වැඩි කිරීමට, තත්ත්ව පාලනය වැඩි දියුණු කිරීමට සහ එන්නත් අච්චු ගැසීමේ නිෂ්පාදන ක්රියාවලීන් ප්රශස්ත කිරීමට අපේක්ෂා කෙරේ.
- ජෛව හායනයට ලක්විය හැකි ද්රව්ය භාවිතය වැඩි කිරීම: පාරිසරික ගැටළු එන්නත් අච්චු ගැසීමේදී දිරාපත් විය හැකි ද්රව්ය භාවිතා කිරීමට හේතු වේ. ජෛව හායනයට ලක්විය හැකි ද්රව්ය සාම්ප්රදායික ප්ලාස්ටික් සඳහා තිරසාර විකල්පයක් සපයන අතර අපද්රව්ය සහ පාරිසරික බලපෑම අවම කිරීමට උපකාරී වේ.
- වෛද්ය උපකරණ නිෂ්පාදනය සඳහා වැඩිවන ඉල්ලුම: වයස්ගත ජනගහනය සහ වෛද්ය තාක්ෂණයේ දියුණුව හේතුවෙන් වෛද්ය උපකරණවල අවශ්යතාවය වැඩි වෙමින් පවතී. ඉන්ජෙක්ෂන් මෝල්ඩින් යනු එහි නිරවද්යතාවය, වේගය සහ පිරිවැය-ඵලදායීතාවය හේතුවෙන් වෛද්ය උපකරණ සඳහා ජනප්රිය නිෂ්පාදන ක්රියාවලියකි.
- ත්රිමාණ මුද්රණ හැකියාවන් පුළුල් කිරීම: ත්රිමාණ මුද්රණ තාක්ෂණයේ දියුණුව නිසා කලින් ඉන්ජෙක්ෂන් මෝල්ඩින් භාවිතයෙන් නිෂ්පාදනය කිරීමට නොහැකි වූ සංකීර්ණ හා සංකීර්ණ කොටස් නිෂ්පාදනය කිරීමට හැකි වී තිබේ. කෙසේ වෙතත්, ත්රිමාණ මුද්රණය තවමත් සාපේක්ෂ වශයෙන් මන්දගාමී සහ මිල අධික ඉන්ජෙක්ෂන් මෝල්ඩින් හා සසඳන විට, තාක්ෂණයන් දෙක එකිනෙක ප්රතිස්ථාපනය කරනවාට වඩා එකිනෙක අනුපූරකව දිගටම පවතිනු ඇත.
- බහු-ද්රව්ය එන්නත් අච්චුව වැඩි කිරීම: බහු-ද්රව්ය එන්නත් අච්චුව තනි එන්නත් අච්චු කිරීමේ ක්රියාවලියක විවිධ ද්රව්ය දෙකක් හෝ වැඩි ගණනක් භාවිතා කිරීම ඇතුළත් වේ. මෙම තාක්ෂණය වැඩිදියුණු කළ කොටස් ක්රියාකාරිත්වය, අඩු බර සහ පිරිවැය ඉතිරිකිරීම ඇතුළු ප්රතිලාභ කිහිපයක් ලබා දෙයි.
- මෙවලම් තාක්ෂණයේ දියුණුව: නව මෙවලම් ද්රව්ය සහ මෝස්තර සංවර්ධනය කිරීම එන්නත් අච්චු ගැසීමේ වේගය, කාර්යක්ෂමතාව සහ නිරවද්යතාවය වැඩි කිරීමට අපේක්ෂා කෙරේ. නිදසුනක් ලෙස, මෙවලම්වල ඇති අනුකූල සිසිලන නාලිකා චක්ර කාලය වැඩි දියුණු කර බලශක්ති පරිභෝජනය අඩු කළ හැකිය.
නිගමනය:
අභිරුචි ප්ලාස්ටික් ඉන්ජෙක්ෂන් මෝල්ඩින් යනු ශක්තිමත් නිෂ්පාදන ක්රියාවලියක් වන අතර එය ඉතා නිරවද්යතාවයෙන් හා කාර්යක්ෂමතාවයෙන් උසස් තත්ත්වයේ ප්ලාස්ටික් කොටස් නිෂ්පාදනය කිරීමට හැකි වේ. ඉන්ජෙක්ෂන් මෝල්ඩින් ක්රියාවලිය අවබෝධ කර ගැනීමෙන්, සුදුසු ද්රව්ය සහ අච්චු මෝස්තර තෝරා ගැනීමෙන් සහ තත්ත්ව පාලනය සහ උපකරණ නඩත්තුව සඳහා හොඳම භාවිතයන් ක්රියාත්මක කිරීමෙන්, ව්යාපාරවලට ඔවුන්ගේ එන්නත් අච්චු ගැසීමේ මෙහෙයුම් ප්රශස්ත කර අතිවිශාල සාර්ථකත්වයක් අත්කර ගත හැකිය. කර්මාන්තයේ නව ප්රවණතා සහ නවෝත්පාදනයන් මතුවන විට, යාවත්කාලීනව සිටීම සහ අභිරුචි ප්ලාස්ටික් එන්නත් අච්චුවෙහි තිරසාරභාවය, කාර්යක්ෂමතාව සහ ලාභදායීතාවය ඉහළ නැංවීම සඳහා නව අවස්ථා ගවේෂණය කිරීම අත්යවශ්ය වේ.