එන්නත් අච්චු ඇතුල් කරන්න
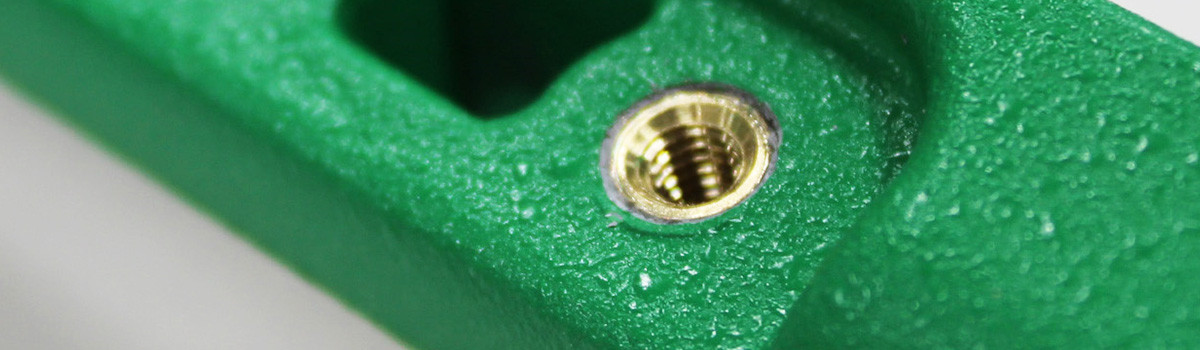
Insert injection molding යනු කාවැද්දූ සංරචක සහිත සංකීර්ණ ප්ලාස්ටික් කොටස් නිෂ්පාදනය කිරීමේදී බහුලව භාවිතා වන නිෂ්පාදන ක්රියාවලියකි. මෙම තාක්ෂණයට එන්නත් අච්චු ගැසීමේ ක්රියාවලියට පෙර ලෝහ හෝ ප්ලාස්ටික් කොටස් අච්චු කුහරයට ඇතුළු කිරීම ඇතුළත් වේ. පසුව උණු කළ ද්රව්යය ඇතුල් කරන ලද මූලද්රව්යය වටා ගලා යන අතර, ද්රව්ය දෙක අතර ඝන බන්ධනයක් නිර්මාණය කරයි. Insert injection molding වැඩිදියුණු කළ සැලසුම් නම්යතාවය, අඩු කරන ලද එකලස් කිරීමේ කාලය සහ වැඩිදියුණු කළ කොටස් ක්රියාකාරීත්වය ඇතුළු වාසි කිහිපයක් ලබා දෙයි. මෙම විස්තීර්ණ මාර්ගෝපදේශය විවිධ ශිල්පීය ක්රම, ප්රතිලාභ සහ ඇතුළු කිරීමේ එන්නත් අච්චුවේ යෙදීම් ගවේෂණය කරනු ඇත.
Insert Injection මෝල්ඩින් යනු කුමක්ද?
එන්නත් අච්චු කිරීම යනු විවිධ කොටස් සහ නිෂ්පාදන නිර්මාණය කිරීම සඳහා භාවිතා කරන නිෂ්පාදන ක්රියාවලියකි. Insert injection molding යනු වාත්තු කිරීමේ ක්රියාවලිය ආරම්භ වීමට පෙර අච්චුව තුළට පෙර සැකසූ මූලද්රව්ය හෝ ඇතුළු කිරීමට ඉඩ සලසන එන්නත් අච්චු වර්ගයකි. මෙම තාක්ෂණය මඟින් සම්ප්රදායික ඉන්ජෙක්ෂන් මෝල්ඩින් ක්රම ලබා ගත නොහැකි විශේෂිත ලක්ෂණ අවශ්ය වන කොටස් නිර්මාණය කිරීමට ඉඩ සලසයි.
ඉන්ජෙක්ෂන් මෝල්ඩින් ක්රියා කරන්නේ වාත්තු කිරීමේ ක්රියාවලිය ආරම්භ වීමට පෙර අච්චු කුහරය තුළට පෙර සැකසූ ඇතුල් කිරීමක් තැබීමෙනි. ඇතුල් කිරීම ලෝහ, ප්ලාස්ටික් සහ පිඟන් මැටි ඇතුළු විවිධ ද්රව්ය අඩංගු විය හැක. වාත්තු කිරීමේ ක්රියාවලිය සුපුරුදු පරිදි ආරම්භ වන අතර, අච්චු කුහරය තුළට එන්නත් කරන ලද උණු කළ ප්ලාස්ටික් සමඟ. ප්ලාස්ටික් සිසිල් වන අතර ඝනීභවනය වන විට, එය ඇතුල් කිරීම සමඟ ඒකාබද්ධ වන අතර, තනි, ඒකාබද්ධ කොටසක් නිර්මාණය කරයි.
Insert injection molding භාවිතා කිරීමේ වාසි කිහිපයක් ඇත. මෙම තාක්ෂණයේ එක් ප්රධාන වාසියක් වන්නේ සම්ප්රදායික ඉන්ජෙක්ෂන් මෝල්ඩින් ක්රම මගින් ලබා ගත නොහැකි විශේෂිත ලක්ෂණ සහිත කොටස් නිර්මාණය කිරීමට ඉඩ සැලසීමයි. උදාහරණයක් ලෙස, ශ්රිතයකට නූල් ඇතුළු කිරීමක් හෝ ශක්තිමත් කිරීම සඳහා ලෝහ සංරචකයක් අවශ්ය නම් ඇතුළු කරන්න එන්නත් අච්චුව භාවිතා කළ හැක. මෙම තාක්ෂණය ද ලෝහ ඇතුළු කිරීමක් සහිත ප්ලාස්ටික් කොටසක් වැනි ද්රව්යවල සංයෝජනයක් සහිත කොටස් නිර්මාණය කිරීමට ඉඩ සලසයි.
Insert injection molding වල තවත් වාසියක් වන්නේ කාලය සහ මුදල් ඉතිරි කිරීමයි. බහු සංරචක එකලස් කිරීම වෙනුවට, ඉන්ජෙක්ෂන් මෝල්ඩින් ඇතුල් කිරීම තනි, ඒකාබද්ධ කෑල්ලක් නිර්මාණය කරයි. එසේ කිරීමෙන්, සමාගම් එකලස් කිරීම සඳහා අවශ්ය කාලය සහ පිරිවැය අඩු කළ හැකිය.
සංකීර්ණ කොටස් නිර්මාණය කිරීම සඳහා Insert injection molding ද උපකාරී වේ. අච්චු ගැසීමේ ක්රියාවලිය ආරම්භ වීමට පෙර ඇතුල් කිරීම අච්චු කුහරය තුළ තැබිය හැකි බැවින්, සම්ප්රදායික එන්නත් අච්චු ගැසීමේ ක්රම මගින් සාක්ෂාත් කර ගැනීමට අපහසු සංකීර්ණ ජ්යාමිතීන් සහ ලක්ෂණ සහිත කොටස් නිෂ්පාදනය කළ හැකිය.
Insert Injection මෝල්ඩින් ක්රියා කරන්නේ කෙසේද?
එය එන්නත් අච්චු ගැසීමේ ක්රියාවලියක් වන අතර එය අච්චු ගැසීමේ ක්රියාවලිය ආරම්භ වීමට පෙර අච්චුවකට පෙර සැකසූ කොටස් හෝ ඇතුළු කිරීමට ඉඩ සලසයි. සාම්ප්රදායික ඉන්ජෙක්ෂන් මෝල්ඩින් ක්රම ලබා ගත නොහැකි විශේෂිත ලක්ෂණ සහිත කෑලි නිර්මාණය කිරීමට මෙම තාක්ෂණය ඉඩ ලබා දෙන අතර සංකීර්ණ කොටස් නිර්මාණය කිරීම සඳහා විශේෂයෙන් ප්රයෝජනවත් වේ. මෙහිදී අපි ඉන්ජෙක්ෂන් මෝල්ඩින් වැඩ ඇතුළත් කරන්නේ කෙසේද යන්න සාකච්ඡා කරමු.
ඇතුල් කිරීමේ එන්නත් අච්චු සැකසීමේ ක්රියාවලියට පහත පියවර ඇතුළත් වේ:
- ස්ථානගත කිරීම ඇතුළු කරන්න:ඇතුල් කිරීමේ එන්නත් අච්චු ගැසීමේ ක්රියාවලියේ පළමු පියවර වන්නේ පෙර සැකසූ ඇතුල් කිරීම අච්චු කුහරය තුළට තැබීමයි. නිෂ්පාදකයින්ට ලෝහ, ප්ලාස්ටික් හෝ පිඟන් මැටි වැනි විවිධ ද්රව්ය වලින් මෙම ඇතුළු කිරීම නිෂ්පාදනය කළ හැකිය.
- පුස් කලම්ප:අච්චුව වසා ඇති අතර ඇතුල් කිරීම ස්ථානගත වූ පසු වසා ඇත. ඉලක්කය වන්නේ වාත්තු කිරීමේ ක්රියාවලියේදී ඇතුල් කිරීම තබා ගැනීමයි.
- උණු කළ ප්ලාස්ටික් එන්නත් කිරීම:ඉන්ජෙක්ෂන් මෝල්ඩින් ක්රියාවලිය අච්චු කුහරයට උණු කළ ප්ලාස්ටික් එන්නත් කරයි. නිෂ්පාදකයන් සාමාන්යයෙන් ප්ලාස්ටික් සෙල්සියස් අංශක 200 ත් 300 ත් අතර උෂ්ණත්වයකට රත් කරන අතර, භාවිතා කරන විශේෂිත ප්ලාස්ටික් මත පදනම්ව එය තීරණය කරයි.
- සිසිලනය සහ ඝන වීම: ප්ලාස්ටික් සිසිල් වන අතර ඝනීභවනය වන විට, එය ඇතුල් කිරීම සමඟ ඒකාබද්ධ වන අතර, තනි, ඒකාබද්ධ කොටසක් නිර්මාණය කරයි. සිසිලනය සහ ඝණීකරණ කාලය රඳා පවතින්නේ භාවිතා කරන විශේෂිත ප්ලාස්ටික් සහ කෑල්ලක් නිෂ්පාදනය කිරීමේ සංකීර්ණත්වය මතය.
- අච්චුව විවෘත කිරීම සහ පිට කිරීම: කොටස සිසිල් වී ඝන වූ පසු, ක්රියාකරු අච්චුව විවෘත කර අයිතමය ඉවත් කරයි. ඉන්පසු කැබැල්ල අවසන් කර භාවිතයට සූදානම් කළ හැකිය.
Insert injection molding භාවිතා කිරීමේ වාසි කිහිපයක් ඇත. මෙම වාසි සමහරක් ඇතුළත් වේ:
- සාම්ප්රදායික ඉන්ජෙක්ෂන් මෝල්ඩින් ක්රම ලබා ගත නොහැකි විශේෂිත ලක්ෂණ සහිත කොටස් නිර්මාණය කිරීමේ හැකියාව
- මූලද්රව්ය තනි, ඒකාබද්ධ කෑල්ලක් ලෙස සාදා ගත හැකි අතර, එකලස් කිරීමේ කාලය හා පිරිවැය අඩු කරයි
- සංකීර්ණ ජ්යාමිතිය සහ ලක්ෂණ සහිත සංකීර්ණ කොටස් නිර්මාණය කිරීමේ හැකියාව
- ලෝහ, ප්ලාස්ටික් සහ පිඟන් මැටි ඇතුළු විවිධ ද්රව්ය භාවිතා කිරීමේ හැකියාව
- ඉන්ජෙක්ෂන් මෝල්ඩින් යනු ඉහළ නිරවද්යතාවයකින් සහ නිරවද්යතාවයකින් යුත් කොටස් විශාල ප්රමාණයක් නිපදවිය හැකි ඉතා කාර්යක්ෂම සහ පුනරාවර්තන ක්රියාවලියකි.
ඉන්ජෙක්ෂන් මෝල්ඩින් කිරීමේදී භාවිතා කරන ඇතුළු කිරීම් වර්ග
ඇතුළු කිරීම් සෑදීම සඳහා නිෂ්පාදකයන්ට ලෝහ, ප්ලාස්ටික් සහ පිඟන් මැටි ඇතුළු විවිධ ද්රව්ය භාවිතා කළ හැකිය. සාම්ප්රදායික ඉන්ජෙක්ෂන් මෝල්ඩින් ක්රම මගින් සාක්ෂාත් කරගත නොහැකි විශේෂිත ලක්ෂණ සහිත කොටස් නිර්මාණය කිරීමට මෙම ඇතුල් කිරීම් සක්රීය කරයි. මෙහිදී අපි ඉන්ජෙක්ෂන් මෝල්ඩින් භාවිතා කරන විවිධ ආකාරයේ ඇතුල් කිරීම් ගැන සාකච්ඡා කරමු.
- ලෝහ ඇතුළු කිරීම්:ප්ලාස්ටික් කොටස් වලට අමතර ශක්තියක් සහ ස්ථායීතාවයක් ලබා දීම සඳහා එන්නත් අච්චු ගැසීමේදී ලෝහ ඇතුළු කිරීම් බහුලව භාවිතා වේ. ඒවා සාමාන්යයෙන් පිත්තල, වානේ හෝ ඇලුමිනියම් වලින් සාදා ඇති අතර යෙදුම මත පදනම්ව නූල් හෝ නූල් නොකළ හැක. නිෂ්පාදකයින්ට සංකීර්ණ ජ්යාමිතිය සහ ඉහළ ශක්තියක් සහ කල්පැවැත්මක් අවශ්ය වන සාධක සහිත කොටස් නිර්මාණය කිරීම සඳහා ලෝහ ඇතුළු කිරීම් භාවිතා කළ හැකිය.
- ප්ලාස්ටික් ඇතුළත් කිරීම්: ප්ලාස්ටික් කොටස් සඳහා ආධාරක සහ ශක්තිමත් කිරීම සඳහා ප්ලාස්ටික් ඇතුළු කිරීම් බොහෝ විට එන්නත් අච්චු ගැසීමේදී භාවිතා වේ. ඒවා සාමාන්යයෙන් නයිලෝන්, ABS හෝ පොලිකාබනේට් ද්රව්ය වලින් සාදා ඇති අතර ස්නැප්-ෆිට් සම්බන්ධතා හෝ නූල් සිදුරු වැනි විශේෂිත ලක්ෂණ සහිත කෑලි සෑදිය හැක. නිෂ්පාදකයන් ප්ලාස්ටික් ඇතුළු කිරීම් අගය කරන්නේ සැහැල්ලු, ලාභදායී විසඳුම් ලබා දීමට සහ විවිධ හැඩයන් සහ ප්රමාණවලට පහසුවෙන් අච්චු කිරීමට ඇති හැකියාව සඳහා ය.
- සෙරමික් ඇතුළු කිරීම්: ඉහළ ශක්තියක් සහ ඇඳීමට සහ ඉරීම සඳහා ප්රතිරෝධයක් අවශ්ය වන කොටස් නිර්මාණය කිරීම සඳහා එන්නත් අච්චු ගැසීමේදී සෙරමික් ඇතුළු කිරීම් භාවිතා වේ. ඒවා සාමාන්යයෙන් සර්කෝනියා හෝ ඇලුමිනා වැනි ද්රව්ය වලින් සාදා ඇති අතර මෝටර් රථ, ගුවන් අභ්යවකාශ සහ වෛද්ය කර්මාන්ත සඳහා අමතර කොටස් නිෂ්පාදනය කිරීමට භාවිතා කළ හැකිය. සෙරමික් ඇතුළු කිරීම් අධික උෂ්ණත්වයන්ට, විඛාදනයට සහ සීරීම් වලට බෙහෙවින් ප්රතිරෝධී වන අතර, ඒවා කටුක පරිසරයන් සඳහා වඩාත් සුදුසු වේ.
- සංයුක්ත ඇතුළත් කිරීම්: නිෂ්පාදකයන් විසින් ලෝහ සහ ප්ලාස්ටික් වැනි ද්රව්ය දෙකක් හෝ වැඩි ගණනක් ඒකාබද්ධ කර, සංයුක්ත ඇතුළු කිරීම් නිර්මාණය කිරීම සඳහා ඒවා අච්චු ගැසීම, එහි ප්රතිඵලයක් ලෙස තනි, ඒකාබද්ධ කොටසක් සෑදේ. සාම්ප්රදායික ඉන්ජෙක්ෂන් මෝල්ඩින් ක්රම මගින් සාක්ෂාත් කරගත නොහැකි විශේෂිත ලක්ෂණ සහිත කොටස් සංවර්ධනය කිරීමට නිෂ්පාදකයින්ට මිශ්ර ඇතුළු කිරීම් භාවිතා කළ හැකිය. තවද, විශේෂිත යෙදුම්වල අනන්ය අවශ්යතා සපුරාලීම සඳහා ඔවුන්ට මෙම ඇතුළු කිරීම් ඉතා අභිරුචිකරණය කළ හැකිය.
- අධික ලෙස සකස් කරන ලද ඇතුළත් කිරීම්: ඉන්ජෙක්ෂන් මෝල්ඩින් ක්රියාවලියේදී, නිෂ්පාදකයන් විසින් ප්ලාස්ටික් කොටසකට අච්චු ඇතුල් කරන අතර, එහි ප්රතිඵලයක් ලෙස අධික ලෙස හැඩගැසුණු ඇතුල් කිරීම් ලෙස හැඳින්වේ. මෙම ක්රියාවලියට ඇතුළත් කිරීම වටා ප්ලාස්ටික් ප්රථම වෙඩිල්ලක් සංවර්ධනය කිරීම සහ පසුව තනි, ඒකාබද්ධ කොටසක් නිර්මාණය කිරීම සඳහා පළමු පහරට වඩා දෙවැන්නක් සැකසීම ඇතුළත් වේ. නිෂ්පාදකයින් බොහෝ විට ප්ලාස්ටික් සංරචකයකට ලෝහ ඇතුළු කිරීම වැනි ද්රව්ය ඒකාබද්ධ කරන කෑලි නිර්මාණය කිරීම සඳහා වැඩිපුර අච්චු ඇතුළු කිරීම් භාවිතා කරයි.
ලෝහ ඇතුළු කිරීම් එදිරිව ප්ලාස්ටික් ඇතුළු කිරීම්
ප්ලාස්ටික් ඉන්ජෙක්ෂන් මෝල්ඩින් ක්රියාවලිය ආරම්භ වීමට පෙර අච්චුවකට දැමූ පෙර සැකසූ කොටස් හෝ ඇතුළු කිරීම් භාවිතා කිරීම ක්රියාවලියට ඇතුළත් වේ. නිෂ්පාදකයන්ට ලෝහ සහ ප්ලාස්ටික් ඇතුළු විවිධ ද්රව්ය වලින් ඇතුළු කිරීම් සිදු කළ හැකි අතර, එක් එක් වර්ගය එහි අද්විතීය වාසි සහ අවාසි ඉදිරිපත් කරයි. මෙම ලිපිය ලෝහ සහ ප්ලාස්ටික් ඇතුළු කිරීම් සංසන්දනය කර ඔබගේ යෙදුම සඳහා හොඳම විකල්පය තීරණය කිරීමට උපකාරී වනු ඇත.
ලෝහ ඇතුළු කිරීම්
ඒවායේ ඉහළ ශක්තිය සහ කල්පැවැත්ම නිසා නිෂ්පාදකයින් සාමාන්යයෙන් වාත්තු කිරීමේදී ලෝහ ඇතුළු කිරීම් භාවිතා කරයි. ඒවා සාමාන්යයෙන් පිත්තල, වානේ හෝ ඇලුමිනියම් වලින් සාදා ඇති අතර යෙදුම මත පදනම්ව නූල් හෝ නූල් නොකළ හැක. ප්ලාස්ටික් කොටස් වලට අමතර ශක්තියක් සහ ස්ථායීතාවයක් ලබා දීම සඳහා එන්නත් අච්චු ගැසීමේදී ලෝහ ඇතුළු කිරීම් බොහෝ විට භාවිතා වේ.
ලෝහ ඇතුළු කිරීම් වල වාසි
- ඉහළ ශක්තිය සහ කල්පැවැත්ම
- ඇඳීමට හා ඉරීමට ප්රතිරෝධී වේ
- එයට නූල් දැමීම හරහා අමතර ක්රියාකාරීත්වයක් ලබා දිය හැක
- අධික ආතතිය හෝ බර උසුලන අවශ්යතා සහිත කොටස් සඳහා වඩාත් සුදුසුය
ලෝහ ඇතුළු කිරීම් වල අවාසි
- ප්ලාස්ටික් ඇතුළු කිරීම් වලට වඩා ඉහළ පිරිවැය
- ප්ලාස්ටික් ඇතුළු කිරීම් වලට වඩා අච්චු කිරීම වඩාත් අභියෝගාත්මක ය
- බර, විශේෂිත යෙදුම්වල සැලකිලිමත් විය හැක
ප්ලාස්ටික් ඇතුළු කිරීම්
ප්ලාස්ටික් ඇතුළු කිරීම් ඒවායේ බහුකාර්යතාව සහ පිරිවැය-ඵලදායීතාවය හේතුවෙන් වාත්තු කිරීම සඳහා ජනප්රිය වේ. නිෂ්පාදකයින් සාමාන්යයෙන් ඒවා නයිලෝන්, ඒබීඑස් හෝ පොලිකාබනේට් වැනි ද්රව්ය වලින් සාදන අතර ඒවා පහසුවෙන් විවිධ හැඩයන් සහ ප්රමාණවලට අච්චු කළ හැකිය. ප්ලාස්ටික් ඇතුළු කිරීම් සැහැල්ලු වන අතර ස්නැප්-ෆිට් සම්බන්ධතා හෝ නූල් සිදුරු වැනි විශේෂිත ලක්ෂණ සහිත කොටස් සෑදිය හැක.
ප්ලාස්ටික් ඇතුළත් කිරීම් වල වාසි
- පිරිවැය-ඵලදායී
- සැහැල්ලු
- විවිධ හැඩයන් සහ ප්රමාණවලින් පහසුවෙන් හැඩගස්වා ඇත
- අඩු ආතතිය හෝ බර උසුලන අවශ්යතා සහිත කොටස් සඳහා වඩාත් සුදුසුය
ප්ලාස්ටික් ඇතුළත් කිරීම් වල අවාසි
- ලෝහ ඇතුළු කිරීම් වලට වඩා අඩු කල් පවතින
- අධික ආතතිය හෝ බර උසුලන අවශ්යතා සහිත කොටස් සඳහා සුදුසු නොවේ
- කාලයත් සමඟ එය ඇඳීමට හා ඉරා දැමීමට වඩාත් ගොදුරු විය හැකිය
ලෝහ ඇතුළු කිරීම් තෝරාගත යුත්තේ කවදාද?
ලෝහ ඇතුළු කිරීම් ඉහළ ශක්තියක් සහ කල්පැවැත්මක් ඉල්ලා සිටින කොටස්වල විශිෂ්ටයි, මන්ද ඒවා ඇඳීමට සහ ඉරීමට ප්රතිරෝධී වන අතර නූල් දැමීමේ අමතර ක්රියාකාරීත්වය සපයයි. ලෝහ ඇතුළු කිරීම් ද අධි පීඩන හෝ බර උසුලන අවශ්යතා සහිත කාර්යයන් සඳහා සුදුසු වේ. කෙසේ වෙතත්, ඒවා ප්ලාස්ටික් ඇතුළු කිරීම් වලට වඩා මිල අධික වන අතර අච්චු කිරීමට වඩා අපහසු විය හැකිය.
ලෝහ ඇතුළු කිරීම් අවශ්ය විය හැකි යෙදුම් ඇතුළත් වේ
- මෝටර් රථ සහ අභ්යවකාශ සංරචක
- වෛද්ය උපකරණ
- කාර්මික උපකරණ
- පාරිභෝගික ඉලෙක්ට්රොනික උපකරණ
ප්ලාස්ටික් ඇතුළත් කිරීම් තෝරාගත යුත්තේ කවදාද?
අඩු ආතතියක් හෝ බරක් දරණ අවශ්යතා සහිත කොටස් සඳහා ප්ලාස්ටික් ඇතුළු කිරීම් ලාභදායී සහ බහුකාර්ය වේ. ඔවුන් සැහැල්ලු ලක්ෂණ පෙන්නුම් කරයි; නිෂ්පාදකයින්ට විවිධ හැඩයන් සහ ප්රමාණවලින් ඒවා සකස් කළ හැකිය. Snap-fit සම්බන්ධතා හෝ නූල් සිදුරු වැනි විශේෂිත විශේෂාංග අවශ්ය වන ස්ථාන සඳහාද ප්ලාස්ටික් ඇතුළු කිරීම් ඉතා සුදුසුය. කෙසේ වෙතත්, අධික ආතතිය හෝ බර උසුලන අවශ්යතා සහිත විස්තර සඳහා ඒවා වඩාත් සුදුසු විය යුතුය.
ප්ලාස්ටික් ඇතුළු කිරීම් අවශ්ය විය හැකි යෙදුම් ඇතුළත් වේ
- පාරිභෝගික භාණ්ඩ
- ගෘහ උපකරණ
- සෙල්ලම් බඩු සහ ක්රීඩා
- ඉලෙක්ට්රොනික උපකරණ
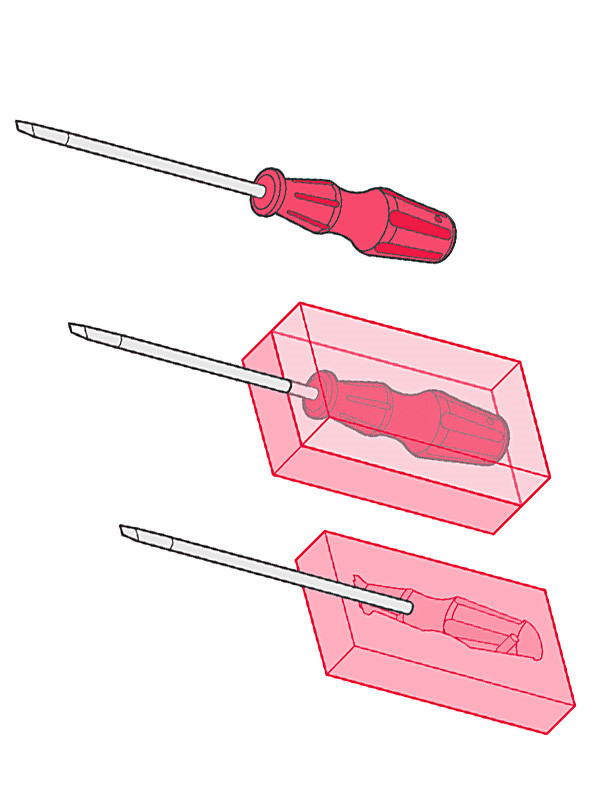
Insert Injection Molding වල ප්රතිලාභ
ඉන්සර්ට් ඉන්ජෙක්ෂන් මෝල්ඩින් යනු ප්ලාස්ටික් ඉන්ජෙක්ෂන් මෝල්ඩින් ක්රියාවලිය ආරම්භ වීමට පෙර අච්චුවක තැන්පත් කරන ලද පෙර සැකසූ කොටස් හෝ ඇතුළු කිරීම් ඇතුළත් ජනප්රිය නිෂ්පාදන ක්රියාවලියකි. මෙම තාක්ෂණය සාම්ප්රදායික වාත්තු ක්රමවලට වඩා බොහෝ ප්රතිලාභ ලබා දෙන අතර එය විවිධ යෙදුම් සඳහා ජනප්රිය තේරීමක් කරයි. මෙම ලිපියෙන් ඉන්ජෙක්ෂන් මෝල්ඩින් ඇතුළු කිරීමේ ප්රධාන වාසි කිහිපයක් සාකච්ඡා කරනු ඇත.
- ලාභදායී: ඉන්සර්ට් ඉන්ජෙක්ෂන් මෝල්ඩින් පිරිවැය-ඵලදායි නිෂ්පාදන විසඳුමක් විය හැක, මන්ද එය වෙනම කොටස්වල පශ්චාත්-මෝල්ඩින් එකලස් කිරීමේ අවශ්යතාවය ඉවත් කරයි. අච්චු ගැසීමේදී ඇතුළු කිරීම් ඒකාබද්ධ කිරීමෙන්, නිෂ්පාදකයින්ට නිෂ්පාදන කාර්යක්ෂමතාව වැඩි කරන අතරම ශ්රම සහ එකලස් කිරීමේ පිරිවැය අඩු කළ හැකිය.
- වැඩි දියුණු කළ කොටස් ශක්තිය: Insert injection molding මගින් කැබැල්ලේ විවිධ ප්රදේශවල විවිධ ද්රව්ය භාවිතා කිරීමෙන් කොටස්වල ශක්තිය සහ කල්පැවැත්ම වැඩි දියුණු කළ හැකිය. අධික ආතතිය හෝ බර උසුලන ඉල්ලීම් විඳදරාගැනීමට විස්තර අවශ්ය යෙදුම් සඳහා මෙම විශේෂාංගය විශේෂයෙන් ප්රයෝජනවත් විය හැක.
- නිර්මාණ නම්යශීලීභාවය වැඩි කිරීම: ඉන්සර්ට් ඉන්ජෙක්ෂන් මෝල්ඩින් බහුවිධ විශේෂාංග සහ කාර්යයන් සහිත සංකීර්ණ කොටස් නිර්මාණය කරන බැවින්, වැඩි නිර්මාණ නම්යතාවයක් ලබා දෙයි. මෙම ක්රියාවලිය සංකීර්ණ මෝස්තර සහ ජ්යාමිතිය සඳහා හොඳින් ගැලපේ, එය එවැනි විස්තර සඳහා කදිම තේරීමක් කරයි.
- අනුකූලතාව සහ නිරවද්යතාව: Insert injection molding කොටස් නිෂ්පාදනයේ විශිෂ්ට අනුකූලතාවයක් සහ නිරවද්යතාවයක් ලබා දෙයි. අපි එක් එක් කොටසෙහි අවශ්යතාවයන් අනුව ඒවායේ නිශ්චිත ස්ථානගත කිරීම සහතික කරමින්, අච්චුව තුළට පෙර සැකසූ ඇතුල් කිරීම් නිශ්චිතවම ස්ථානගත කරමු. එහි ප්රතිඵලයක් වශයෙන්, අපි නිෂ්පාදනය කරන ලද කොටස්වල ඒකාකාර මානයන් සහ සුවිශේෂී තත්ත්ව පාලනයක් ලබා ගනිමු.
- අඩු කළ චක්ර කාලය: එක් ක්රියාවලියකට පියවර කිහිපයක් ඒකාබද්ධ කිරීමෙන් ඉන්ජෙක්ෂන් මෝල්ඩින් ඇතුල් කිරීම චක්ර කාලය අඩු කළ හැක. මෙම ක්රමය මඟින් කාලය ඉතිරි කර ගත හැකි අතර ඵලදායිතාව ඉහළ නැංවිය හැකිය, විශේෂයෙන් ඉහළ පරිමාණ නිෂ්පාදන ධාවනය සමඟ කටයුතු කිරීමේදී.
- ද්රව්ය විවිධත්වය: ප්ලාස්ටික්, ලෝහ සහ සෙරමික් ඇතුළු විවිධ ද්රව්ය සමඟ ඇතුල් කරන්න එන්නත් අච්චුව භාවිතා කළ හැකිය. නිෂ්පාදකයින්ට දැන් ශක්තිය, කල්පැවැත්ම සහ පිරිවැය සැලකිල්ලට ගනිමින් ඕනෑම යෙදුමක් සඳහා වඩාත් සුදුසු ද්රව්ය තෝරා ගත හැකිය.
- පාරිසරික ප්රතිලාභ: Insert injection molding මගින් ද අපද්රව්ය අවම කිරීම සහ ද්රව්ය භාවිතය අවම කිරීම මගින් පාරිසරික ප්රතිලාභ ලබා දිය හැක. අපි නිශ්චිතවම අච්චුව තුළට ඇතුල් කිරීම් තබන නිසා, අපි සාම්ප්රදායික අච්චු ක්රමවලට වඩා අඩු ද්රව්යමය අපද්රව්ය අත්විඳින්නෙමු. මෙය ක්රියාත්මක කිරීමෙන් පාරිසරික බලපෑම අඩුවීමටත් නිෂ්පාදන වියදම් අඩුවීමටත් හැකිවේ.
Insert මෝල්ඩින් සඳහා සැලසුම් සලකා බැලීම්
Insert molding යනු ප්ලාස්ටික් ඉන්ජෙක්ෂන් මෝල්ඩින් ක්රියාවලියකට පෙර සැකසූ ඇතුළු කිරීම් ඒකාබද්ධ කිරීම ඇතුළත් ජනප්රිය නිෂ්පාදන ක්රියාවලියකි. මෙම තාක්ෂණය වැඩිදියුණු කළ කොටස් ශක්තිය, එකලස් කිරීමේ පිරිවැය අඩු කිරීම සහ සැලසුම් නම්යශීලී බව ඇතුළු බොහෝ ප්රතිලාභ ලබා දෙයි. කෙසේ වෙතත්, ඇතුල් කිරීමේ අච්චු සඳහා කොටස් සැලසුම් කිරීම සාර්ථක හා කාර්යක්ෂම නිෂ්පාදනයක් සහතික කිරීම සඳහා සාධක කිහිපයක් ප්රවේශමෙන් සලකා බැලීම අවශ්ය වේ. මෙම ලිපිය ඇතුල් කිරීමේ අච්චුව සඳහා ප්රධාන සැලසුම් සලකා බැලීම් කිහිපයක් සාකච්ඡා කරනු ඇත.
- ස්ථානගත කිරීම ඇතුළු කරන්න: ඇතුල් කිරීම අච්චුව තුළ ස්ථානගත කිරීම ඇතුල් කිරීමේ අච්චු ක්රියාවලියේ සාර්ථකත්වය සඳහා ඉතා වැදගත් වේ. වාත්තු කිරීමේ ක්රියාවලියේදී ප්ලාස්ටික් ද්රව්ය සම්පූර්ණයෙන්ම ආවරණය වන බව සහතික කිරීම සඳහා ඇතුළු කිරීම අච්චුව තුළ නිශ්චිතව ස්ථානගත කළ යුතුය. ඇතුළත් කිරීම ප්ලාස්ටික් ද්රව්ය ගලායාමට බාධා නොකරන බවට හෝ වෙන්වීමේ රේඛාවේ ගැටළු ඇති නොවන බවට නිර්මාණකරුවන් සහතික විය යුතුය.
- ද්රව්ය අනුකූලතාව: ඇතුළු කිරීම සහ ප්ලාස්ටික් ද්රව්ය යන දෙකටම අවශ්ය ද්රව්ය තෝරා ගැනීම ඇතුළු කිරීමේ වාත්තු කිරීමේ ක්රියාවලියේ සාර්ථකත්වය සඳහා ඉතා වැදගත් වේ. බන්ධන ගැටළු හෝ ද්රව්යමය නොගැලපීම් වැළැක්වීම සඳහා ද්රව්ය අනුකූල විය යුතුය. සාර්ථක ඇතුළු කිරීම් අච්චු ගැසීම සහතික කිරීම සඳහා නිර්මාණකරුවන් ද්රවාංකය, හැකිලීම සහ තාප ප්රසාරණයේ සංගුණකය වැනි ද්රව්යමය ගුණාංග හොඳින් සලකා බැලිය යුතුය.
- ජ්යාමිතිය කොටස: කොටසෙහි ජ්යාමිතිය ඇතුල් කිරීමේ අච්චුව සඳහා තවත් තීරනාත්මක සලකා බැලීමකි. සැලසුම එය සම්පුර්ණයෙන්ම ආවරණය කර ඇති බව සහතික කිරීම සඳහා ඇතුළු කිරීම වටා ඇති ප්ලාස්ටික් ද්රව්ය නිසි ලෙස පිරවීමට සහ ඇසුරුම් කිරීමට ඉඩ දිය යුතුය. කොටස් ජ්යාමිතිය විකෘති වීම, හැකිලීම හෝ ගිලී යාමේ සලකුණු සමඟ ගැටළු වළක්වා ගැනීම සඳහා ප්රමාණවත් වාතාශ්රයක් සහ සිසිලනය සඳහා ඉඩ ලබා දිය යුතුය.
- කෙටුම්පත් කෝණ සහ යටි කැපීම්: කෙටුම්පත් කෝණ සහ යටි කැපුම් තිබීම ඇතුල් කිරීමේ අච්චුවේ කොටසක අච්චු භාවයට බලපායි. කොටසට හෝ අච්චුවට කිසිදු හානියක් සිදු නොකර අච්චුවෙන් ඇතුළු කිරීම පහසුවෙන් ඉවත් කළ හැකි බව සහතික කිරීම සඳහා නිර්මාණකරුවන් කෙටුම්පත් කෝණ සහ යටි කැපීම් ස්ථානගත කිරීම සහ ජ්යාමිතිය ප්රවේශමෙන් සලකා බැලිය යුතුය.
- මෙවලම් සලකා බැලීම්: සම්ප්රදායික වාත්තු ක්රමවලට වඩා ඇතුල් කිරීමේ අච්චුව සඳහා අවශ්ය මෙවලම් සංකීර්ණ විය හැක. ඇතුළු කිරීමේ ස්ථානගත කිරීම සහ ජ්යාමිතිය, ද්වාරය සහ වාතාශ්රය සහ අවශ්ය ඕනෑම අතුරු ක්රියා ඇතුළුව, නිර්මාණකරුවන් අච්චු සැලසුම ප්රවේශමෙන් සලකා බැලිය යුතුය. අතිරේකව, නිසි ඇතුළු කිරීම් ස්ථානගත කිරීම සහතික කිරීම සහ කොටසේ ගුණාත්මක භාවය පිළිබඳ ගැටළු වළක්වා ගැනීම සඳහා මෙවලම දැඩි ඉවසීමක් පවත්වා ගැනීමට සමත් විය යුතුය.
Insert Injection Molding සඳහා භාවිතා කරන ද්රව්ය
Insert injection molding යනු සංකීර්ණ කොටස් නිශ්චිතව සහ ස්ථාවර ලෙස නිපදවන අතිශය විශේෂිත ක්රියාවලියකි. මෙම ක්රියාවලියට ඉන්ජෙක්ෂන් මෝල්ඩින් වීමට පෙර අච්චුවකට ඇතුළු කරන ලද ඇතුළු කිරීම් ලෙස හඳුන්වන පෙර-නිෂ්පාදිත විශේෂාංග භාවිතා කිරීම ඇතුළත් වේ. මෙම ඇතුළු කිරීම් විවිධ ද්රව්ය වලින් සාදා ගත හැකි අතර, ඒ සෑම එකක්ම අද්විතීය ගුණාංග සහ ප්රතිලාභ ඇත. ඇතුල් කරන්න එන්නත් අච්චු ගැසීමේදී භාවිතා කරන වඩාත් සුලභ ද්රව්ය සහ ඒවායේ වාසි පිළිබඳව අපි මෙහිදී සාකච්ඡා කරමු.
ලෝහ
ඉන්ජෙක්ෂන් මෝල්ඩින් පුළුල් ලෙස වානේ, ඇලුමිනියම් සහ පිත්තල වැනි ලෝහ වලින් සාදන ලද ඇතුල් කිරීම් භාවිතා කරයි. මෙම ද්රව්ය විශිෂ්ට ශක්තියක් සහ කල්පැවැත්මක් ලබා දෙයි, ඉහළ ඇඳුම් සහ කඳුළු ප්රතිරෝධයක් අවශ්ය කොටස් සඳහා ඒවා වඩාත් සුදුසු වේ. මීට අමතරව, ලෝහ ඇතුළු කිරීම්වලට ඉහළ උෂ්ණත්වයන්ට ඔරොත්තු දිය හැකි අතර, ඒවා අභ්යවකාශ සහ මෝටර් රථ කර්මාන්ත වැනි ඉල්ලුම සහිත යෙදුම්වල භාවිතයට සුදුසු වේ. ඉන්ජෙක්ෂන් මෝල්ඩින් කිරීමේදී ලෝහ ඇතුළු කිරීම් භාවිතා කිරීමේ විශේෂිත වාසි සමහරක් ඇතුළත් වේ:
- ඉහළ ශක්තිය සහ කල්පැවැත්ම
- විශිෂ්ට තාප ප්රතිරෝධය
- ක්ෂය වීමට ප්රතිරෝධකතාව
- අධික පීඩනය හා ආතතියට ඔරොත්තු දීමේ හැකියාව
ප්ලාස්ටික්
PEEK, PTFE, සහ UHMW වැනි ද්රව්ය ජනප්රිය තේරීම් සමඟින් ප්ලාස්ටික් ඇතුළු කිරීම් එන්නත් අච්චු ගැසීමේදී බහුලව භාවිතා වේ. මෙම ද්රව්ය ඉහළ උෂ්ණත්ව ප්රතිරෝධය, රසායනික ප්රතිරෝධය සහ අඩු ඝර්ෂණ ගුණාංග ලබා දෙයි. එම යෙදුම්වල තීරනාත්මක සාධක වන ඒවායේ ඉහළ නිරවද්යතාවය සහ පිරිසිදුකම හේතුවෙන් මෙම සංරචක වෛද්ය උපකරණ සහ අර්ධ සන්නායක නිෂ්පාදනය සඳහා භාවිතා කිරීම සඳහා හොඳින් ගැලපේ. එන්නත් අච්චු ගැසීමේදී ප්ලාස්ටික් ඇතුළු කිරීම් භාවිතා කිරීමේ විශේෂිත වාසි සමහරක් ඇතුළත් වේ:
- ඉහළ රසායනික ප්රතිරෝධයක්
- විශිෂ්ට උෂ්ණත්ව ප්රතිරෝධය
- අඩු ඝර්ෂණ ගුණ
- යන්ත්ර සහ හැඩයට පහසුය
පිඟන් භාණ්ඩ
එන්නත් අච්චු ගැසීමේදී, සෙරමික් ඇතුළු කිරීම් ඒවායේ ඉහළ ශක්තිය, දෘඪතාව සහ ඇඳුම් ප්රතිරෝධය හේතුවෙන් භාවිතයට ගනී. මෙම ද්රව්ය කොටස අධික උෂ්ණත්වයකට හෝ කටුක පරිසරයකට ඔරොත්තු දීමට අවශ්ය යෙදුම්වල භාවිතයට සුදුසු වේ. මීට අමතරව, සෙරමික් ඇතුළු කිරීම් විශිෂ්ට මාන ස්ථාවරත්වයක් ලබා දෙයි, ඒවා නිරවද්ය ඉංජිනේරු යෙදුම් සඳහා සුදුසු වේ. එන්නත් අච්චු ගැසීමේදී සෙරමික් ඇතුළු කිරීම් භාවිතා කිරීමේ විශේෂිත වාසි සමහරක් ඇතුළත් වේ:
- ඉහළ ශක්තිය සහ දෘඪතාව
- විශිෂ්ට ඇඳුම් ප්රතිරෝධය
- ඉහළ උෂ්ණත්ව ප්රතිරෝධය
- විචල්ය ස්ථායීතාව
සංයුක්ත
කාබන් ෆයිබර් හෝ ෆයිබර්ග්ලාස් වැනි සංයුක්ත ද්රව්ය, ඒවායේ ඉහළ ශක්තියට බර අනුපාතය සඳහා එන්නත් අච්චු ගැසීමේදී භාවිතා වේ. අභ්යවකාශ සහ මෝටර් රථ කර්මාන්ත බොහෝ විට බර අඩු කර ගැනීම තීරණාත්මක වන විට මෙම ද්රව්ය භාවිතා කරයි. සංයුක්ත ඇතුළු කිරීම් ඉහළ තද බවක් සහ ශක්තියක් ලබා දෙන අතර, ඒවා සුළං ටර්බයින සහ ඉහළ කාර්ය සාධනයක් සහිත ක්රීඩා උපකරණ යෙදුම් සඳහා වඩාත් සුදුසු වේ. එන්නත් අච්චු ගැසීමේදී සංයුක්ත ඇතුළත් කිරීම් භාවිතා කිරීමේ විශේෂිත වාසි සමහරක් ඇතුළත් වේ:
- අධික ශක්ති-බර අනුපාතයක්
- ඉහළ තද බව සහ ශක්තිය
- හොඳ බලපෑම් ප්රතිරෝධය
- අඩු තාප ප්රසාරණ සංගුණකය
රබර්
සිලිකන් හෝ නියෝප්රීන් වැනි රබර් ද්රව්ය, ඒවායේ නම්යශීලීභාවය සහ මුද්රා තැබීමේ ගුණාංග සඳහා එන්නත් අච්චු ගැසීමේදී භාවිතා වේ. මුද්රා තැබීම සහ කුෂන් කිරීම අත්යවශ්ය වන වෛද්ය සහ මෝටර් රථ කර්මාන්තවල මෙම ද්රව්ය බහුලව භාවිතා වේ. රබර් ඇතුළු කිරීම් රසායනික ද්රව්යවලට සහ අධික උෂ්ණත්වයන්ට විශිෂ්ට ප්රතිරෝධයක් ලබා දෙන අතර, ඒවා කටුක පරිසරවල භාවිතයට සුදුසු වේ. එන්නත් අච්චු ගැසීමේදී රබර් ඇතුළු කිරීම් භාවිතා කිරීමේ විශේෂිත වාසි සමහරක් ඇතුළත් වේ:
- විශිෂ්ට මුද්රා තැබීමේ ගුණාංග
- ඉහළ නම්යශීලී බවක්
- රසායනික හා උෂ්ණත්ව ප්රතිරෝධය
- හොඳ කම්පන තෙතමනය
පෙන
පොලියුරේටීන් හෝ ෙපොලිස්ටිරින් වැනි පෙණ ද්රව්ය, ඒවායේ සැහැල්ලු සහ කම්පන අවශෝෂණ ගුණ සඳහා එන්නත් අච්චු ගැසීමේදී භාවිතා වේ. කුෂන් කිරීම සහ බලපෑම් ප්රතිරෝධය අත්යවශ්ය වන ඇසුරුම්කරණයේ සහ මෝටර් රථ කර්මාන්තවල මෙම ද්රව්ය බොහෝ විට භාවිතා වේ. ෆෝම් ඇතුළු කිරීම් ඉහළ පරිවරණයක් ලබා දෙයි, ඒවා උෂ්ණත්ව සංවේදී යෙදුම් සඳහා වඩාත් සුදුසු වේ. ඉන්ජෙක්ෂන් මෝල්ඩින් කිරීමේදී ෆෝම් ඇතුළු කිරීම් භාවිතා කිරීමේ විශේෂිත වාසි සමහරක් ඇතුළත් වේ:
- සැහැල්ලු හා නම්යශීලී
- විශිෂ්ට කම්පන අවශෝෂණය
- හොඳ පරිවාරක ගුණ
- සංකීර්ණ හැඩතලවලට හැඩගැසීමේ හැකියාව
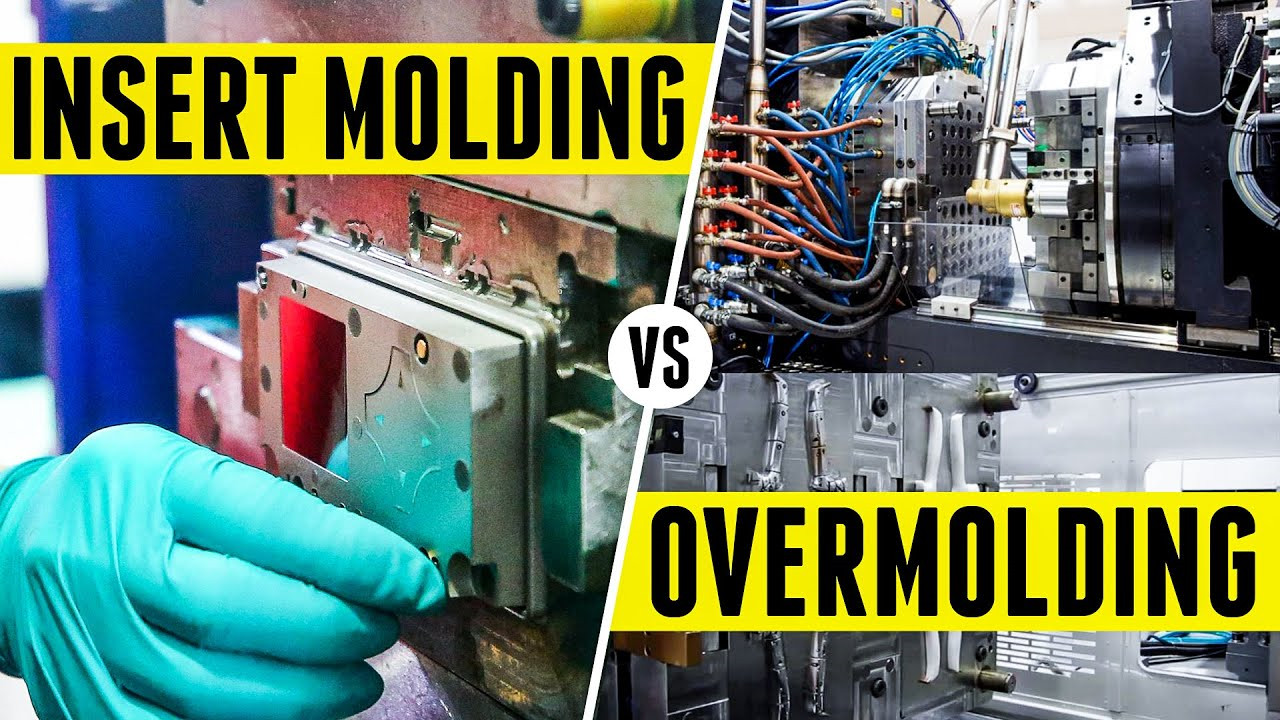
මෝල්ඩින් එදිරිව ඕවර්මෝල්ඩින් ඇතුළු කරන්න: වෙනස කුමක්ද?
Insert molding සහ overmolding යනු බහු ද්රව්ය ඇතුළත් එන්නත් අච්චු ගැසීමේදී බහුලව භාවිතා වන ක්රියාවලි දෙකකි. මෙම ක්රියාවලීන් සමාන බවක් පෙනෙන්නට තිබුණද, ඒවාට මූලික වෙනස්කම් තිබේ. මෙහිදී අපි insert molding සහ over-molding අතර ඇති වෙනස්කම් සාකච්ඡා කරමු.
මෝල්ඩින් ඇතුල් කරන්න
Insert molding යනු, ඉන්ජෙක්ෂන් මෝල්ඩින් ක්රියාවලිය සිදු වීමට පෙර, ඇතුල් කිරීම් ලෙස හඳුන්වන, පෙර සැකසූ කොටස් අච්චුවකට ඇතුළු කිරීම ඇතුළත් ක්රියාවලියකි. ප්ලාස්ටික් ද්රව්ය පසුව ඇතුල් කිරීම් වටා එන්නත් කරනු ලබන අතර, ඇතුල් කිරීමේ ගුණාංග සහ ප්ලාස්ටික් ද්රව්ය ඒකාබද්ධ කරන නිමි භාණ්ඩයක් නිර්මාණය කරයි. මෙම ක්රියාවලිය සාමාන්යයෙන් මෝටර් රථ, වෛද්ය සහ අභ්යවකාශ කර්මාන්තවල ඉහළ නිරවද්යතාවයකින් යුත් කොටස් නිර්මාණය කිරීමට භාවිතා කරයි.
ඇතුල් කිරීමේ අච්චු වල වාසි
- ඉහළ නිරවද්යතාව සහ නිරවද්යතාව
- වැඩි දියුණු කරන ලද කොටසෙහි ශක්තිය සහ කල්පැවැත්ම
- එකලස් කිරීමේ කාලය සහ පිරිවැය අඩු කිරීම
- විවිධ ගුණාංග සහිත ද්රව්ය ඒකාබද්ධ කිරීමේ හැකියාව
අධික ලෙස සකස් කිරීම
ඕවර්මෝල්ඩින් යනු පෙර පැවති කොටසකට වඩා දෙවන ද්රව්යයක් එන්නත් කිරීම ඇතුළත් ක්රියාවලියකි. නිෂ්පාදකයින් මෙම ක්රියාවලිය මෘදු ස්පර්ශ හසුරුවීම්, ග්රහණයන් සහ අනෙකුත් පාරිභෝගික නිෂ්පාදන නිර්මාණය කිරීමට භාවිතා කරයි. වැඩිපුර අච්චු කරන ලද ද්රව්ය සාමාන්යයෙන් මෘදු සහ රබර් වැනි වන අතර එය වැඩිදියුණු කළ ග්රහණය සහ සුවපහසුව සපයයි. කොටසෙහි සංකීර්ණත්වය අනුව, අපට තනි-වෙඩි හෝ දෙකක්-වෙඩි ක්රියාවලියකින් අධික ලෙස අච්චු ගැසීම සිදු කළ හැකිය.
අධික ලෙස අච්චු ගැසීමේ වාසි
- වැඩිදියුණු කළ ergonomics සහ සෞන්දර්යය
- වැඩි දියුණු කළ ග්රහණය සහ සුවපහසුව
- එකලස් කිරීමේ කාලය සහ පිරිවැය අඩු කිරීම
- විවිධ ගුණාංග සහිත ද්රව්ය ඒකාබද්ධ කිරීමේ හැකියාව
ඇතුල් කිරීම සහ අධික ලෙස අච්චු කිරීම අතර වෙනස්කම්
- ඇතුල් කිරීමේ අච්චුව පෙර-නිර්මාණය කරන ලද කොටස් ඇතුළත් කිරීම ඇතුළත් වන අතර, අධි අච්චුවකින් සමන්විත වන්නේ පෙර පැවති කොටසකට වඩා දෙවන ද්රව්යයක් එන්නත් කිරීමෙනි.
- නිෂ්පාදනයක ergonomics සහ සෞන්දර්යය වැඩි දියුණු කිරීම සඳහා අපි අධි-මෝල්ඩින් භාවිතා කරන අතරම, ඉහළ නිරවද්යතාවයකින් කෑලි නිර්මාණය කිරීමට අපි ඇතුල් කිරීමේ අච්චු භාවිතා කරමු.
- විවිධ ගුණ සහිත ද්රව්ය ඒකාබද්ධ කිරීම ඇතුළු කිරීම ඇතුළත් වන අතර, අධික ලෙස අච්චු ගැසීමේදී අධික ලෙස අච්චු කරන ලද කොටස සඳහා මෘදු රබර් වැනි ද්රව්යයක් භාවිතා කිරීම ඇතුළත් වේ.
- Insert molding බොහෝ විට මෝටර් රථ, වෛද්ය සහ අභ්යවකාශ කර්මාන්තවල භාවිතා වන අතර, මෙවලම්, ඉලෙක්ට්රොනික උපකරණ සහ පුද්ගලික සත්කාර අයිතම වැනි පාරිභෝගික නිෂ්පාදනවල වැඩිපුර අච්චු ගැසීම බහුලව භාවිතා වේ.
ඇතුල් කිරීම ස්ථානගත කිරීම සඳහා තාක්ෂණික ක්රම
ඉන්සර්ට් මෝල්ඩින් යනු ඉන්ජෙක්ෂන් මෝල්ඩින් ක්රියාවලිය සිදුවීමට පෙර කලින් සාදන ලද කොටස් හෝ ඇතුළු කිරීම් අච්චුවකට දමන ක්රියාවලියකි. නිමි භාණ්ඩයක් නිර්මාණය කිරීම සඳහා ප්ලාස්ටික් ද්රව්ය ඇතුල් කිරීම් වටා එන්නත් කරනු ලැබේ. ඇතුල් කිරීම් අච්චු ගැසීමේ ක්රියාවලියේ සාර්ථකත්වය සඳහා ඇතුළු කිරීම් තැබීම ඉතා වැදගත් වේ. මෙහිදී අපි ඇතුල් කිරීම් ස්ථානගත කිරීම සඳහා තාක්ෂණික ක්රම කිහිපයක් සාකච්ඡා කරමු.
- අතින් ස්ථානගත කිරීම: ක්රියාකරු විසින් මෙම තාක්ෂණය තුළ අච්චුව තුළට ඇතුළු කිරීම් අතින් තබයි. නිෂ්පාදකයින් සාමාන්යයෙන් මෙම තාක්ෂණය කුඩා හෝ සරල කොටස් සඳහා භාවිතා කරයි, ඒවාට ඇතුළත් කිරීම් කිහිපයක් පමණක් අවශ්ය වේ. කෙසේ වෙතත්, එය කාලය ගතවන සහ ශ්රම-දැඩි විය හැකි අතර, අතින් ස්ථානගත කිරීම හේතුවෙන් දෝෂයක් ඇතිවීමේ වැඩි අවදානමක් ඇත.
- ස්වයංක්රීය ස්ථානගත කිරීම: මෙම තාක්ෂණයේදී, රොබෝ යන්ත්රයක් හෝ පික් ඇන්ඩ් ප්ලේස් යන්ත්රයක් වැනි පරිගණක ගත පද්ධතියක් භාවිතයෙන් ඇතුළු කිරීම් අච්චුව තුළට දමනු ලැබේ. මෙම තාක්ෂණය අතින් ස්ථානගත කිරීමට වඩා වේගවත් හා නිවැරදි වන අතර, එය විශාල නිෂ්පාදන ධාවනය හෝ සංකීර්ණ කොටස් සඳහා වඩාත් සුදුසු වේ. කෙසේ වෙතත්, එය උපකරණ සඳහා මූලික ආයෝජනයක් අවශ්ය වන අතර කුඩා පරිමාණ නිෂ්පාදනය සඳහා වඩා ලාභදායී විය යුතුය.
- මෝල්ඩින් අධි-මෝල්ඩින් ඇතුල් කරන්න: අපි ඇතුල් කිරීම් දෙවන, වැඩිපුර අච්චු කරන ලද කොටසකට දමා පසුව එය ප්රාථමික අච්චුව තුළට ස්ථානගත කරන්න. සංකීර්ණ ජ්යාමිතිය හෝ ළඟා වීමට අපහසු ප්රදේශ සහිත හිමිකම් සඳහා නිෂ්පාදකයින් සාමාන්යයෙන් මෙම තාක්ෂණය භාවිතා කරයි. මෘදු අච්චු සහිත ද්රව්යයක් සහිත දෘඩ ප්ලාස්ටික් ඇතුළු කිරීමක් වැනි විවිධ ගුණාංග සහිත ද්රව්ය ද එයට ඒකාබද්ධ කළ හැකිය.
- ඇලවුම් පිටුබලය සහිත ඇතුල් කිරීම්:මෙම තාක්ෂණයේදී, අපි ඇලවුම් ආධාරකයක් සහිත ඇතුළු කිරීම් පූර්ව-ආලේපනය කරන අතර, අතින් හෝ ස්වයංක්රීය ස්ථානගත කිරීමකින් තොරව ඒවා අච්චුවේ තැබීමට අපට ඉඩ සලසයි. ඉන්ජෙක්ෂන් මෝල්ඩින් අතරතුර ඇලවුම් පිටුබලය දියවී, ප්ලාස්ටික් ද්රව්යයට ඇතුළු කිරීම බන්ධනය කරයි. මෙම තාක්ෂණය කුඩා, සරල කොටස් සඳහා බහුලව භාවිතා වන අතර නිෂ්පාදන කාලය සහ පිරිවැය අඩු කළ හැකිය.
- නූල් ඇතුළත් කිරීම්: මෙම තාක්ෂණයේ දී, නූල් ඇතුල් කිරීම් අච්චුව තුළට දමා නිමි භාණ්ඩයේ නූල් නිර්මාණය කිරීමට යොදා ගනී. ඉලෙක්ට්රොනික උපාංග හෝ වාහන අමතර කොටස් වැනි ඉස්කුරුප්පුවක් හෝ බෝල්ට් එකක් ඇතුළු කිරීමට අවශ්ය නිෂ්පාදන නිෂ්පාදනය කිරීමේදී නිෂ්පාදකයින් මෙම තාක්ෂණය සාමාන්යයෙන් භාවිතා කරයි.
Insert Injection මෝල්ඩින් යන්ත්ර වර්ග
ඉන්ජෙක්ෂන් මෝල්ඩින් ක්රියාවලියේ ප්රධාන අංගයක් වන්නේ ඉන්ජෙක්ෂන් මෝල්ඩින් යන්ත්රයයි. මෙම යන්ත්ර විවිධ වර්ග වලින් පැමිණේ, එක් එක් සුවිශේෂී ලක්ෂණ සහ වාසි ඇත. මෙන්න අපි විවිධ ආකාරයේ ඇතුල් කිරීමේ ඉන්ජෙක්ෂන් මෝල්ඩින් යන්ත්ර දෙස බලමු.
පළමුව, ඇතුල් කිරීමේ ඉන්ජෙක්ෂන් මෝල්ඩින් යන්ත්රයක් යනු කුමක්දැයි නිර්වචනය කරමු. ඇතුල් කිරීමේ ඉන්ජෙක්ෂන් මෝල්ඩින් යන්ත්රයක් යනු ප්ලාස්ටික් ද්රව්ය එන්නත් කිරීමට පෙර අච්චුවට ලෝහ හෝ ප්ලාස්ටික් ඇතුළු කිරීම් වැනි පෙර සැකසූ සංරචක ඇතුළු කිරීමට හැකි වන ඉන්ජෙක්ෂන් මෝල්ඩින් යන්ත්රයකි. මෙම හැකියාව සමඟ, නූල් විවරයන් හෝ ලෝහ ආධාරක වැනි අමතර විශේෂාංග අවශ්ය වන සංකීර්ණ කොටස් නිෂ්පාදනය කිරීම ශක්ය වේ.
විවිධ ආකාරයේ ඇතුළු කිරීමේ එන්නත් අච්චු යන්ත්ර මෙන්න:
- සිරස් එන්නත් අච්චු යන්ත්ර:මෙම යන්ත්රවල සිරස් දිශානති සැලසුමක් ඇති අතර එහිදී අච්චුව සිරස් අතට සවි කරයි. ඉහළ සිට අච්චුව තුළට ඇතුළු කිරීම පහසුවෙන් ඇතුල් කිරීමට ඉඩ සලසන බැවින් ඒවා ඇතුල් කිරීමේ අච්චුව සඳහා වඩාත් සුදුසු වේ. මෙම වර්ගයේ යන්ත්රය අඩු බිම් ඉඩ ප්රමාණයක් ගන්නා අතර කුඩා නිෂ්පාදන ධාවනය සඳහා වඩාත් සුදුසු වේ.
- තිරස් එන්නත් අච්චු යන්ත්ර:මෙම යන්ත්රවල පැතලි දිශානති සැලසුමක් ඇත, එහිදී අච්චුව තිරස් අතට සවි කරයි. ඔවුන් විශාල නිෂ්පාදන ධාවනය සඳහා හොඳම යෝග්යතාවය ලබා දෙන අතර නිෂ්පාදකයින් සාමාන්යයෙන් ඒවා වඩාත් වැදගත් කොටස් නිෂ්පාදනය සඳහා භාවිතා කරයි. තිරස් යන්ත්ර සමඟින්, ඇතුළු කිරීම් පැත්තකින් පැටවිය හැකි අතර, නිසි පෙළගැස්ම සහතික කිරීම වඩාත් අභියෝගාත්මක වේ.
- රොටරි මේස එන්නත් මෝල්ඩින් යන්ත්ර:මෙම යන්ත්රවල භ්රමණය වන මේසයක් ඇති අතර එමඟින් බහු අච්චු සවි කිරීමට සහ නිෂ්පාදනය සඳහා එන්නත් ඒකකයට කරකැවීමට ඉඩ සලසයි. මෙම වර්ගයේ යන්ත්රය අච්චුව ඇතුළු කිරීම සඳහා වඩාත් සුදුසු වන්නේ එය අච්චුවට විවිධ ඇතුළු කිරීම් සක්රීය කර වඩාත් සංකීර්ණ කොටස් නිර්මාණය කරන බැවිනි.
- ෂටල එන්නත් අච්චු යන්ත්ර: මෙම යන්ත්රවල එන්නත් ඒකකය සහ අච්චු පෙදෙස අතර අච්චුව එහා මෙහා ගෙන යන ෂටලයක් ඇත. ඒවා කුඩා නිෂ්පාදන ධාවනය සඳහා වඩාත් සුදුසු වන අතර ඇතුළු කිරීම් පහසුවෙන් පැටවීමට සහ බෑමට ඉඩ සලසන බැවින් ඒවා ඇතුල් කිරීමේ අච්චුව සඳහා වඩාත් සුදුසු වේ.
අච්චු ඇතුල් කිරීම සඳහා ක්රියාවලි පරාමිතීන්
සාම්ප්රදායික ඉන්ජෙක්ෂන් මෝල්ඩින් හා සසඳන විට ලැබෙන නිෂ්පාදනයට වැඩි ශක්තියක් සහ කල්පැවැත්මක් ඇත. උසස් තත්ත්වයේ සහ ස්ථාවර ප්රතිඵල ලබා ගැනීම සඳහා ඇතුල් කිරීමේ අච්චුව සඳහා ක්රියාවලි පරාමිතීන් ඉතා වැදගත් වේ. මෙන්න අපි ඇතුල් කිරීමේ අච්චුව සඳහා ක්රියාවලි පරාමිතීන් දෙස බලමු.
- ද්රව්ය තෝරා ගැනීම: ද්රව්ය තෝරා ගැනීම අච්චු ඇතුළු කිරීම සඳහා අත්යවශ්ය ක්රියාවලි පරාමිතියකි. ප්ලාස්ටික් ද්රව්ය ඇතුල් කිරීමේ ද්රව්ය සහ යෙදුම සමඟ අනුකූල විය යුතුය. ගැළපුම, ඇතුළු කිරීම සහ ප්ලාස්ටික් ද්රව්ය හොඳින් පිළිපැදීම සහතික කරයි, ප්රතිඵලයක් ලෙස ශක්තිමත් සහ කල් පවතින නිෂ්පාදනයක් ලැබේ.
- උෂ්ණත්වය: ඇතුල් කිරීමේ ක්රියාවලියේදී උෂ්ණත්වය තීරණාත්මක කාර්යභාරයක් ඉටු කරයි. ප්ලාස්ටික් ද්රව්ය ඒකාකාරව ගලා යාම සහ හිස් හෝ විරූපණයන් නොමැතිව කුහරය පිරවීම සහතික කිරීම සඳහා අපි අච්චු උෂ්ණත්වය නිවැරදිව සකස් කළ යුතුය. ප්ලාස්ටික් ද්රව්ය තාප හානියකින් තොරව ඇතුළු කිරීමට හොඳින් අනුගත වන බව සහතික කිරීම සඳහා අපි ඇතුළු කිරීමේ උෂ්ණත්වය ද සලකා බැලිය යුතුය.
- එන්නත් පීඩනය: එන්නත් පීඩනය ඇතුල් කිරීමේ අච්චුව සඳහා තවත් අත්යවශ්ය පරාමිතියකි. ප්ලාස්ටික් ද්රව්ය අච්චු කුහරයට ඒකාකාරව හා ඉක්මනින් එන්නත් කිරීම සහතික කිරීම සඳහා අපි ආතතිය නිවැරදිව සැකසිය යුතුය. ඉහළ එන්නත් පීඩනයක් ඇතුල් කිරීමේ හෝ අච්චුවේ විරූපණයට හේතු විය හැකි අතර, අඩු එන්නත් පීඩනය පුස් කුහරය අසම්පූර්ණ ලෙස පිරවීමට හේතු විය හැක.
- එන්නත් වේගය: එන්නත් කිරීමේ වේගය ද ඇතුල් කිරීමේ අච්චුව සඳහා අත්යවශ්ය පරාමිතියකි. ප්ලාස්ටික් ද්රව්ය හිස් හෝ විරූපණයකින් තොරව අච්චු කුහරය ඒකාකාරව පුරවා ඇති බව සහතික කිරීම සඳහා අපි අනුපාතය නිවැරදිව සැකසිය යුතුය. ඉහළ එන්නත් වේගයක් ප්ලාස්ටික් ද්රව්යයේ කැළඹීමට හේතු විය හැක, නිමි භාණ්ඩයේ දෝෂ ඇති විය හැක.
- සිසිලන කාලය: ප්ලාස්ටික් ද්රව්ය ඝනීභවනය කිරීම සහ අවසන් නිශ්පාදන හැඩය සෑදීම සඳහා සිසිලන කාලය අවශ්ය වේ. නිමි භාණ්ඩය සඳහා අපේක්ෂිත හැඩය සහ ප්රමාණය ලබා ගැනීම සහතික කිරීම සඳහා අපි සිසිලන කාලය නිවැරදිව සැකසිය යුතුය. කෙටි සිසිලන කාලයක් විරූපණයට හෝ හැකිලීමට හේතු විය හැකි අතර, දිගු සිසිලන කාලය දිගු චක්ර කාලය හා ඵලදායිතාව අඩු වීමට හේතු විය හැක.
- පිටකිරීමේ වේලාව: නිමි භාණ්ඩය අච්චුවෙන් ඉවත් කිරීමට අපට පිටකිරීමේ කාලය අවශ්ය වේ. කිසිදු හානියක් හෝ විකෘතියක් ඇති නොකර නිමි භාණ්ඩය ඉවත් කිරීම සඳහා අපි නිෂ්කාශනය කිරීමේ කාලය නිවැරදිව සැකසිය යුතුය. කෙටි විසර්ජන කාලයකින් අසම්පූර්ණ පිටකිරීමක් හෝ නිෂ්පාදනයට හානි සිදු විය හැකි අතර, දිගු විසර්ජන කාලය දිගු චක්ර කාලයකට සහ ඵලදායිතාව අඩුවීමට හේතු විය හැක.
පොදු ඇතුල් කිරීමේ අච්චු දෝෂ සහ ඒවා වළක්වා ගන්නේ කෙසේද
Insert molding යනු ප්ලාස්ටික් ද්රව්ය එන්නත් කිරීමට පෙර ලෝහ හෝ ප්ලාස්ටික් ඇතුළු කිරීම් වැනි පෙර සැකසූ සංරචක අච්චුවට තැබීම ඇතුළත් වන ජනප්රිය නිෂ්පාදන ක්රියාවලියකි. මෙම ක්රියාවලිය සාම්ප්රදායික ඉන්ජෙක්ෂන් මෝල්ඩින් වලට වඩා සැලකිය යුතු සහ කල් පවතින නිෂ්පාදන ඇති කරයි. කෙසේ වෙතත්, ඕනෑම නිෂ්පාදන ක්රියාවලියක් මෙන්, ඇතුළු කිරීමේ අච්චුවෙහි අවසාන නිෂ්පාදනයේ ගුණාත්මකභාවය සහ අනුකූලතාවයට බලපාන දෝෂ තිබිය හැකිය. මෙහිදී අපි සාමාන්ය ඇතුළු කිරීමේ අච්චු දෝෂ සහ ඒවා වළක්වා ගන්නේ කෙසේද යන්න දෙස සමීපව බලමු.
සැණෙළිය: ෆ්ලෑෂ් යනු අච්චුවෙන් අතිරික්ත ප්ලාස්ටික් ද්රව්ය කාන්දු වී නිමි භාණ්ඩයේ මතුපිට තුනී ස්ථරයක් සාදන විට සිදුවන දෝෂයකි. මෙම දෝෂය නිෂ්පාදනයේ පෙනුම හා කාර්යයට බලපෑ හැකිය. ෆ්ලෑෂ් වළක්වා ගැනීම සඳහා, ඔබට පහත පියවර ගත හැකිය:
- එන්නත් පීඩනය අඩු කරන්න
- අච්චු කලම්ප බලය වැඩි කරන්න
- අච්චු මුදා හැරීමේ කාරකයක් භාවිතා කරන්න
- සිසිලන කාලය වැඩි කරන්න
කෙටි වෙඩි තැබීම: කෙටි වෙඩිල්ල යනු ප්ලාස්ටික් ද්රව්ය අච්චු කුහරය පුරවා නොගත් විට සිදුවන දෝෂයක් වන අතර එමඟින් අසම්පූර්ණ හෝ අඩු ප්රමාණයේ නිෂ්පාදනයක් ඇති වේ. කෙටි පහරක් වළක්වා ගැනීම සඳහා, ඔබට පහත පියවර ගත හැකිය:
- එන්නත් පීඩනය වැඩි කරන්න
- එන්නත් කිරීමේ වේගය වැඩි කරන්න
- ද්රව්යයේ උෂ්ණත්වය වැඩි කරන්න
- අච්චු උෂ්ණත්වය වැඩි කරන්න
යුධ පිටුව: Warpage යනු අසමාන සිසිලනය හෝ හැකිලීම හේතුවෙන් නිමි භාණ්ඩය විකෘති වී හෝ ඇඹරුණු විට දෝෂයකි. Warpage වළක්වා ගැනීමට, ඔබට පහත පියවර ගත හැක:
- අච්චු උෂ්ණත්වය වැඩි කරන්න
- සිසිලන කාලය වැඩි කරන්න
- ඇසුරුම් පීඩනය වැඩි කරන්න
- සමබර සිසිලන පද්ධතියක් භාවිතා කරන්න
සින්ක් ලකුණු: සින්ක් ලකුණු යනු අසමාන සිසිලනය හෝ හැකිලීම හේතුවෙන් නිමි භාණ්ඩයේ මතුපිට ඇති වන අවපාත හෝ ඉන්ඩෙන්ටේෂන් වේ. සින්ක් ලකුණු වළක්වා ගැනීම සඳහා, ඔබට පහත පියවර ගත හැකිය:
- අච්චු උෂ්ණත්වය වැඩි කරන්න
- සිසිලන කාලය වැඩි කරන්න
- ඇසුරුම් පීඩනය වැඩි කරන්න
- නිෂ්පාදිතය ශක්තිමත් කිරීම සඳහා ඝන බිත්ති හෝ රිබින් භාවිතා කරන්න
ඉවත් කිරීම: Delamination යනු ප්ලාස්ටික් ද්රව්ය සහ ඇතුළු කරන ද්රව්ය නිසියාකාරව බන්ධනය නොවන විට සිදුවන දෝෂයක් වන අතර එහි ප්රතිඵලයක් ලෙස වෙන්වීම හෝ පීල් වීම සිදුවේ. දිරාපත් වීම වළක්වා ගැනීම සඳහා, ඔබට පහත පියවර ගත හැකිය:
- අනුකූල ප්ලාස්ටික් ද්රව්යයක් භාවිතා කර කෑන් ද්රව්ය ඇතුළු කරන්න
- එන්නත් කිරීමේ පීඩනය සහ වේගය වැඩි කරන්න
- ඇතුල් කිරීමේ උෂ්ණත්වය වැඩි කරන්න
- අච්චු උෂ්ණත්වය වැඩි කරන්න
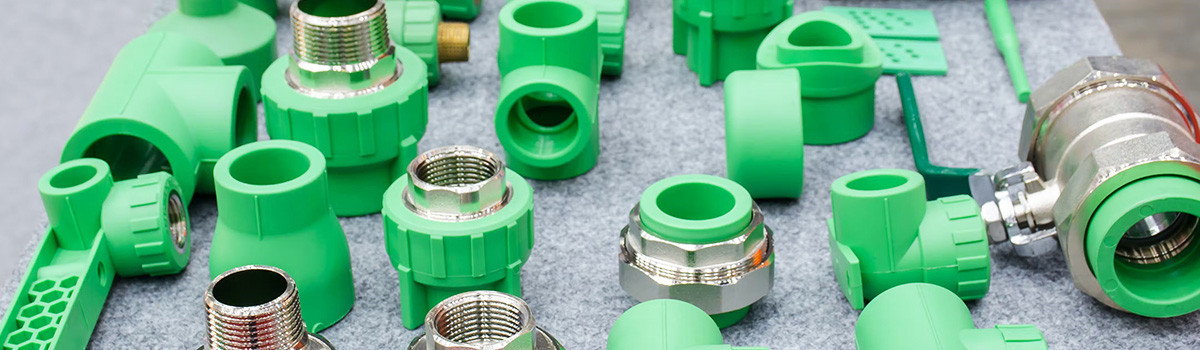
අච්චු ඇතුල් කිරීම සඳහා පශ්චාත්-මෝල්ඩින් මෙහෙයුම්
කෙසේ වෙතත්, ඇතුළු කිරීමේ වාත්තු කිරීමේ ක්රියාවලිය සම්පූර්ණ කිරීමෙන් පසු, අවසාන නිෂ්පාදනය අපේක්ෂිත පිරිවිතරයන් සපුරාලන බව සහතික කිරීම සඳහා අප විසින් පශ්චාත් අච්චු මෙහෙයුම් කිහිපයක් සිදු කළ යුතුය. මෙන්න අපි ඇතුල් කිරීමේ අච්චුව සඳහා පශ්චාත්-මෝල්ඩින් මෙහෙයුම් දෙස සමීපව බලමු.
- Deflashing:Deflashing යනු නිමි භාණ්ඩයෙන් ෆ්ලෑෂ් හෝ බර්ස් වැනි අතිරික්ත ද්රව්ය ඉවත් කරන ක්රියාවලියකි. නිෂ්පාදනයේ විශාලත්වය සහ සංකීර්ණත්වය අනුව මෙම ක්රියාවලිය අතින් හෝ ස්වයංක්රීයව සිදු කළ හැක.
- කැපීම:කප්පාදු කිරීම යනු නිමි භාණ්ඩයේ අතිරික්ත ද්රව්ය හෝ නෙරා යාම ඉවත් කරන ක්රියාවලියකි. නිෂ්පාදනයේ හැඩය සහ ප්රමාණය අනුව විවිධ කැපුම් මෙවලම් හෝ ක්රම භාවිතයෙන් මෙම ක්රියාවලිය සිදු කළ හැක.
- පිරිසිදු කිරීම: පිරිසිදු කිරීම යනු නිමි භාණ්ඩයෙන් අපිරිසිදු, සුන්බුන් හෝ දූෂිත ද්රව්ය ඉවත් කරන ක්රියාවලියකි. මෙම ක්රියාවලිය විවිධ පිරිසිදු කිරීමේ ද්රව්ය හෝ ක්රම භාවිතයෙන් සිදු කළ හැකි අතර, එය ඇතුල් කිරීමේ වාත්තු කිරීමේ ක්රියාවලියේදී භාවිතා කරන ද්රව්ය වර්ගය මත රඳා පවතී.
- එකලස් කිරීම:එකලස් කිරීම යනු නිමි භාණ්ඩයක් සෑදීම සඳහා බහු සංරචක එකට සම්බන්ධ කිරීම ඇතුළත් ක්රියාවලියකි. මෙම ක්රියාවලිය ද්රව්ය වර්ගය සහ අපේක්ෂිත අවසන් නිශ්පාදනය මත පදනම්ව අතිධ්වනි වෑල්ඩින්, උණුසුම් මුද්දර දැමීම හෝ ඇලවුම් බන්ධනය වැනි විවිධ ක්රම භාවිතයෙන් සිදු කළ හැක.
- පරීක්ෂා කිරීම: පරීක්ෂා කිරීම යනු නිමි භාණ්ඩය අපේක්ෂිත පිරිවිතරයන් සහ තත්ත්ව ප්රමිතීන් සපුරාලීම සහතික කරන ක්රියාවලියකි. මෙම ක්රියාවලියට නිෂ්පාදන වර්ගය සහ එහි අපේක්ෂිත භාවිතය අනුව යාන්ත්රික, විද්යුත් හෝ දෘශ්ය පරීක්ෂණ වැනි විවිධ පරීක්ෂණ ඇතුළත් විය හැක.
මෙම පසු අච්චු ගැසීමේ මෙහෙයුම් වලට අමතරව, පශ්චාත් අච්චු පටිපාටිවල අවශ්යතාවය අවම කරන ඇතුළු කිරීමේ අච්චු ක්රියාවලියක් සැලසුම් කිරීමේදී සලකා බැලිය යුතු සාධක කිහිපයක් ද තිබේ. මේවාට ඇතුළත් වන්නේ:
- ඇතුල් කිරීම සහ අච්චු කරන ලද කොටස සඳහා සුදුසු ද්රව්ය තෝරා ගැනීම
- අච්චු ගැසීමේ ක්රියාවලියේදී ඇතුළු කිරීම සුදුසු පරිදි ස්ථානගත කර ඇති බව සහතික කිරීම
- දෝෂ සහ අතිරික්ත ද්රව්ය අවම කිරීම සඳහා උෂ්ණත්වය සහ පීඩනය වැනි වාත්තු පරාමිතීන් සකස් කිරීම
- නිමි භාණ්ඩයේ අනුකූලතාව සහ නිරවද්යතාව සහතික කිරීම සඳහා උසස් තත්ත්වයේ අච්චු සහ උපකරණ භාවිතා කිරීම
Insert Injection මෝල්ඩින් වල යෙදුම්
Insert injection molding යනු වැඩි ශක්තියක් සහ කල්පැවැත්මක් සහිත උසස් තත්ත්වයේ, සංකීර්ණ කොටස් නිෂ්පාදනය කිරීම සඳහා බොහෝ කර්මාන්තවල භාවිතා වන ඉතා බහුකාර්ය නිෂ්පාදන ක්රියාවලියකි. මෙහිදී අපි insert injection molding යෙදුම් සහ විවිධ කර්මාන්ත සඳහා එහි ප්රතිලාභ දෙස සමීපව බලමු.
- වාහන නිෂ්පාදන කර්මාන්තය:මෝටර් රථ කර්මාන්තය ඉන්ජෙක්ෂන් මෝල්ඩින් භාවිතා කරන වඩාත් වැදගත් පරිශීලකයන්ගෙන් එකකි. එය එයාර් බෑග් හවුසිං, සීට් බෙල්ට් සහ එන්ජින් සංරචක ඇතුළු විවිධ සංරචක නිෂ්පාදනය කිරීමේදී භාවිතය සොයා ගනී. මෙම ක්රියාවලිය මඟින් මෝටර් රථ භාවිතයේ කටුක තත්වයන්ට ඔරොත්තු දිය හැකි කොටස් නිවැරදිව හා නිවැරදිව සකස් කිරීමට ඉඩ සලසයි.
- ඉලෙක්ට්රොනික කර්මාන්තය:ඉලෙක්ට්රොනික කර්මාන්තය ස්මාර්ට් ෆෝන්, ලැප්ටොප් සහ වෙනත් ඉලෙක්ට්රොනික උපාංග වැනි උපාංග සඳහා සංරචක නිෂ්පාදනය කිරීම සඳහා ඇතුළු කිරීමේ එන්නත් අච්චුව මත දැඩි ලෙස රඳා පවතී. ඉලෙක්ට්රොනික උපාංග සඳහා සම්බන්ධක, ස්විච සහ නිවාස වැනි මූලද්රව්ය නිර්මාණය කිරීමේදී ක්රියාවලිය භාවිතා කරයි. ක්රියාවලිය ඉතා කාර්යක්ෂම වන අතර ඉක්මනින් හා ලාභදායී ලෙස කොටස් විශාල ප්රමාණයක් නිපදවිය හැක.
- වෛද්ය කර්මාන්තය: ඉන්සර්ට් ඉන්ජෙක්ෂන් මෝල්ඩින් වලින් වෛද්ය කර්මාන්තය ද සැලකිය යුතු ප්රතිලාභ ලබයි. ශල්ය උපකරණ, ඖෂධ බෙදා හැරීමේ උපකරණ සහ වෛද්ය තැන්පත් කිරීම් ඇතුළු විවිධ සංරචක නිෂ්පාදනය කිරීමේදී ක්රියාවලිය භාවිතා කරයි. මෙම ක්රමය මගින් වෛද්යමය භාවිතයේ දැඩිකමට ඔරොත්තු දිය හැකි මූලද්රව්යවල නිරවද්ය හැඩගැස්ම සක්රීය කරන අතර විශාල පරිමාවක් නිෂ්පාදනය කිරීමට ඉඩ සලසයි.
- අභ්යවකාශ කර්මාන්තය: අභ්යවකාශ කර්මාන්තය යනු ඉන්ජෙක්ෂන් මෝල්ඩින් බහුලව භාවිතා කරන තවත් කර්මාන්තයකි. ක්රියාවලිය ගුවන් යානා සංරචක සඳහා වායු නාලිකා, වරහන් සහ නිවාස වැනි සංරචක නිෂ්පාදනය කිරීමේදී යෙදුම සොයා ගනී. මෙම ක්රියාවලිය මගින් අභ්යවකාශ භාවිතයේ අධික ආතතීන්ට සහ අධික උෂ්ණත්වයන්ට ඔරොත්තු දිය හැකි අධි ශක්ති සංරචක නිර්මාණය කිරීමට ඉඩ සලසයි.
- පාරිභෝගික භාණ්ඩ කර්මාන්තය: පාරිභෝගික භාණ්ඩ කර්මාන්තය සෙල්ලම් බඩු, ගෘහ උපකරණ සහ ක්රීඩා උපකරණ වැනි පුළුල් පරාසයක නිෂ්පාදන නිෂ්පාදනය කිරීම සඳහා ඇතුළු කිරීමේ එන්නත් අච්චුව පුළුල් ලෙස භාවිතා කරයි. මෙම ක්රියාවලිය උසස් තත්ත්වයේ, කල් පවතින, සැහැල්ලු, සහ සෞන්දර්යාත්මකව ප්රියජනක සංරචක නිර්මාණය කිරීමට ඉඩ සලසයි.
මෙම කර්මාන්තවලට අමතරව, ඇතුළු කිරීම් එන්නත් අච්චුව වෙනත් බොහෝ යෙදුම්වල ද භාවිතා වේ, ඇතුළුව:
- ඇසුරුම් කර්මාන්තය: කැප්, වසා දැමීම් සහ අනෙකුත් ඇසුරුම් සංරචක නිෂ්පාදනය කිරීම සඳහා
- ඉදිකිරීම් කර්මාන්තයේ: පයිප්ප, සවිකෘත සහ අනෙකුත් ඉදිකිරීම් සංරචක නිෂ්පාදනය කිරීම සඳහා
- හමුදා කර්මාන්තය: හමුදා වාහන සහ උපකරණ සඳහා කොටස් නිෂ්පාදනය සඳහා
මෝටර් රථ කර්මාන්ත යෙදුම්
මෝටර් රථ කර්මාන්තය යනු ප්ලාස්ටික් ඉන්ජෙක්ෂන් මෝල්ඩින් භාවිතා කරන වඩාත් වැදගත් පරිශීලකයන්ගෙන් එකකි, මන්ද එය සංකීර්ණ වාහන සංරචක නිෂ්පාදනය කිරීම සඳහා ලාභදායී සහ කාර්යක්ෂම ක්රමයකි. මෙන්න අපි මෝටර් රථ කර්මාන්තයේ ප්ලාස්ටික් ඉන්ජෙක්ෂන් මෝල්ඩින්ගේ විවිධ යෙදුම් දෙස සමීපව බලමු.
- අභ්යන්තර සංරචක: වාහනයක අභ්යන්තරය මෝටර් රථයේ සමස්ත සෞන්දර්යය සහ ක්රියාකාරීත්වය සඳහා අත්යවශ්ය ප්ලාස්ටික් සංරචක කිහිපයකින් සමන්විත වේ. මෙම සංරචකවලට උපකරණ පුවරුව, දොර පැනල්, වායු සමීකරණ වාතාශ්රය සහ සුක්කානම් රෝද සංරචක ඇතුළත් වේ. ඉන්ජෙක්ෂන් මෝල්ඩින් මඟින් මෙම කොටස් ඉහළ පරිමාවකින් ඉක්මනින් හා ලාභදායී ලෙස නිෂ්පාදනය කිරීමට හැකි වන අතර ඉහළ නිරවද්යතාවයක් පවත්වා ගනී.
- බාහිර සංරචක: වාහනයක බාහිර කොටස බම්පර් කවර, හෙඩ් ලෑම්ප් එකලස් කිරීම් සහ ටේල් ලයිට් එකලස් කිරීම් ඇතුළු ප්ලාස්ටික් උපාංග කිහිපයකින් සමන්විත වේ. ඉන්ජෙක්ෂන් මෝල්ඩින් මෙම සංරචක ඉහළ මට්ටමේ නිරවද්යතාවයකින් නිපදවයි, ඒවා මෝටර් රථ කර්මාන්තයේ අවශ්ය දැඩි ආරක්ෂාව සහ තත්ත්ව ප්රමිතීන් සපුරාලන බව සහතික කරයි.
- එන්ජින් සංරචක: ඉන්ජෙක්ෂන් මෝල්ඩින් වාතය ඇතුළු කිරීමේ බහුවිධ, එන්ජින් ආවරණ සහ තෙල් පෙරහන් ඇතුළු එන්ජින් සංරචක කිහිපයක් නිෂ්පාදනය කිරීමේදී ද භාවිතා කරයි. අපි මෙම සංරචක දැඩි ඉවසීම් සහ ප්රමිතීන්ට අනුකූලව නිෂ්පාදනය කළ යුතු අතර, ඉන්ජෙක්ෂන් මෝල්ඩින් මෙම අවශ්යතා සපුරාලන උසස් තත්ත්වයේ අමුද්රව්ය නිෂ්පාදනය කිරීමට හැකි වේ.
- විදුලි සංරචක: වාහනයක ඇති සම්බන්ධක, ස්විච සහ සංවේදක නිවාස වැනි විද්යුත් සංරචක ද නිපදවනු ලබන්නේ ඉන්ජෙක්ෂන් මෝල්ඩින් භාවිතා කරමිනි. මෙම සංරචක කල් පවතින හා දැඩි මෙහෙයුම් තත්වයන්ට ඔරොත්තු දිය යුතු අතර, ඉන්ජෙක්ෂන් මෝල්ඩින් මෙම තත්වයන්ට ඔරොත්තු දිය හැකි උසස් තත්ත්වයේ අමුද්රව්ය නිෂ්පාදනය කිරීමට ඉඩ සලසයි.
- HVAC සංරචක:ඉන්ජෙක්ෂන් මෝල්ඩින් වායු සමීකරණ නාලිකා සහ වාතාශ්රය ඇතුළුව වාහනයක HVAC පද්ධතියේ භාවිතා කරන සංරචක කිහිපයක් නිෂ්පාදනය කරයි. මෝටර් රථයේ නිසි වාතාශ්රය සහ වාතාශ්රය සහතික කිරීම සඳහා මෙම සංරචක නිශ්චිත ඉවසීමකින් නිපදවිය යුතුය.
මෙම යෙදුම් වලට අමතරව, නිෂ්පාදකයින් ඉන්ධන, තිරිංග සහ අත්හිටුවීමේ පද්ධති ඇතුළු තවත් මෝටර් රථ සංරචක කිහිපයක් නිෂ්පාදනය කිරීමට ඉන්ජෙක්ෂන් මෝල්ඩින් භාවිතා කරයි.
මෝටර් රථ කර්මාන්තයේ ඉන්ජෙක්ෂන් මෝල්ඩින් භාවිතා කිරීමේ ප්රතිලාභ බොහෝය, ඒවා අතර:
- ඉහළ කාර්යක්ෂමතා:එන්නත් අච්චුව විශාල පරිමාවකින් උසස් තත්ත්වයේ සංරචක වේගයෙන් නිෂ්පාදනය කිරීමට ඉඩ සලසයි, නිෂ්පාදන කාලය සහ පිරිවැය අඩු කරයි.
- නිරවද්යතාව:ඉන්ජෙක්ෂන් මෝල්ඩින් මඟින් දැඩි තත්ත්ව ප්රමිතීන් සපුරාලන බව සහතික කරමින් ඉහළ නිරවද්යතාවයකින් සහ අනුකූලතාවයකින් යුත් සංරචක නිර්මාණය කිරීමට ඉඩ සලසයි.
- පාරිභෝගිකයාගේ: ඉන්ජෙක්ෂන් මෝල්ඩින් සංකීර්ණ හැඩතල සහ මෝස්තර නිෂ්පාදනය කිරීමට ඉඩ සලසයි, නිෂ්පාදකයින්ට නිශ්චිත සැලසුම් අවශ්යතා සපුරාලීම සඳහා සංරචක අභිරුචිකරණය කිරීමට ඉඩ සලසයි.
වෛද්ය කර්මාන්ත යෙදුම්
වෛද්ය කර්මාන්තය යනු නිරවද්යතාවය සහ විශ්වසනීයත්වය ප්රමුඛ වන ක්ෂේත්රයක් වන අතර, ප්ලාස්ටික් එන්නත් අච්චුව වෛද්ය සංරචක නිෂ්පාදනය සඳහා කදිම නිෂ්පාදන ක්රියාවලියක් බවට පත් කරයි. මෙහිදී අපි වෛද්ය කර්මාන්තයේ ප්ලාස්ටික් එන්නත් අච්චු ගැසීමේ විවිධ යෙදුම් දෙස සමීපව බලමු.
- ශල්ය උපකරණ: ඉන්ජෙක්ෂන් මෝල්ඩින් මගින් බල, කලම්ප සහ හිස්කබල් ඇතුළු බොහෝ ශල්ය උපකරණ නිෂ්පාදනය කරයි. ඉහළම නිරවද්යතාවය සහ නිරවද්යතාවය සහතික කිරීම සඳහා නිෂ්පාදකයින් මෙම සංරචක දැඩි ඉවසීම් සහ ප්රමිතීන්ට අනුව නිෂ්පාදනය කළ යුතුය.
- වෛද්ය උපකරණ:නිෂ්පාදකයින් කැතීටර් සහ ශ්වසන සංරචක වැනි වෛද්ය උපකරණ නිෂ්පාදනය කිරීම සඳහා එන්නත් අච්චු භාවිතා කරයි. රෝගීන්ගේ ආරක්ෂාව සහ විශ්වසනීයත්වය සහතික කිරීම සඳහා, නිෂ්පාදකයින් මෙම සංරචක දැඩි ප්රමිතීන්ට අනුව නිෂ්පාදනය කළ යුතුය.
- රෝග විනිශ්චය සංරචක: නිෂ්පාදකයන් පයිප්ප, සිරින්ජ සහ පරීක්ෂණ නල වැනි රෝග විනිශ්චය උපකරණවල භාවිතා කරන සංරචක කිහිපයක් නිෂ්පාදනය කිරීම සඳහා එන්නත් අච්චු භාවිතා කරයි. නිරවද්ය පරීක්ෂණ ප්රතිඵල සහතික කිරීම සඳහා මෙම සංරචක නිරවද්ය ඉවසීම සඳහා නිපදවිය යුතුය.
- ඇසුරුම්: එන්නත් අච්චුව මගින් වඳ තැටි, බහාලුම් සහ ඇසුරුම් සංරචක වැනි වෛද්ය නිෂ්පාදන සඳහා ඇසුරුම් නිෂ්පාදනය කරයි. වෛද්ය නිෂ්පාදනවල වඳභාවය සහ ආරක්ෂාව සහතික කිරීම සඳහා මෙම සංරචක දැඩි ප්රමිතීන්ට අනුව නිෂ්පාදනය කළ යුතුය.
- දන්ත සංරචක: එන්නත් අච්චුව මුඛ ආවරණ, තැටි සහ විකලාංග කොටස් ඇතුළු දන්ත සංරචක කිහිපයක් නිෂ්පාදනය කරයි. රෝගියාට නිසි යෝග්යතාවය සහ සුවපහසුව සහතික කිරීම සඳහා මෙම සංරචක නිශ්චිත ඉවසීමකින් නිපදවිය යුතුය.
මෙම යෙදුම් වලට අමතරව, නිෂ්පාදකයින් කෘතිම, ශ්රවණාධාර සහ රසායනාගාර උපකරණ ඇතුළු තවත් වෛද්ය සංරචක කිහිපයක් නිෂ්පාදනය කිරීමට එන්නත් අච්චු භාවිතා කරයි.
වෛද්ය කර්මාන්තයේ එන්නත් අච්චු භාවිතා කිරීමේ ප්රතිලාභ බොහෝ ය, ඒවා අතර:
- ඉහළ නිරවද්යතාවය:ඉන්ජෙක්ෂන් මෝල්ඩින් දැඩි තත්ත්ව ප්රමිතීන් සපුරාලන බව සහතික කරමින් ඉහළ මට්ටමේ නිරවද්යතාවයක් සහ අනුකූලතාවයක් සහිත සංරචක නිෂ්පාදනය කිරීමට ඉඩ සලසයි.
- පාරිභෝගිකයාගේ:ඉන්ජෙක්ෂන් මෝල්ඩින් සංකීර්ණ හැඩතල සහ මෝස්තර නිෂ්පාදනය කිරීමට ඉඩ සලසයි, නිෂ්පාදකයින්ට නිශ්චිත සැලසුම් අවශ්යතා සපුරාලීම සඳහා සංරචක අභිරුචිකරණය කිරීමට ඉඩ සලසයි.
- පිරිවැය- ective ලදායී: ඉන්ජෙක්ෂන් මෝල්ඩින් යනු පිරිවැය-ඵලදායී නිෂ්පාදන ක්රියාවලියක් වන අතර එය නිෂ්පාදන කාලය සහ පිරිවැය අඩු කරමින් විශාල පරිමාවකින් උසස් තත්ත්වයේ සංරචක නිපදවයි.
ඉලෙක්ට්රොනික කර්මාන්ත යෙදුම්
ඉලෙක්ට්රොනික කර්මාන්තය යනු නිරවද්ය සහ කාර්යක්ෂම නිෂ්පාදන ක්රියාවලීන් මත දැඩි ලෙස රඳා පවතින ක්ෂේත්රයකි. ප්ලාස්ටික් ඉන්ජෙක්ෂන් මෝල්ඩින් යනු එහි නිරවද්යතාවය, බහුකාර්යතාව සහ වේගය හේතුවෙන් ඉලෙක්ට්රොනික උපාංග නිෂ්පාදනය සඳහා කදිම ක්රියාවලියකි. මෙහිදී අපි ඉලෙක්ට්රොනික කර්මාන්තයේ ප්ලාස්ටික් එන්නත් අච්චු ගැසීමේ විවිධ යෙදුම් දෙස සමීපව බලමු.
- සම්බන්ධක: ඉන්ජෙක්ෂන් මෝල්ඩින් USB සම්බන්ධක, HDMI සම්බන්ධක සහ ශ්රව්ය ජැක් ඇතුළු ඉලෙක්ට්රොනික කර්මාන්තයේ භාවිතා කරන පුළුල් පරාසයක සම්බන්ධක නිෂ්පාදනය කරයි. නිසි ක්රියාකාරීත්වය සහ ගැළපුම සහතික කිරීම සඳහා මෙම සංරචක නිශ්චිත ඉවසීමකට නිෂ්පාදනය කළ යුතුය.
- නිවාස සහ ආවරණ: එන්නත් අච්චුව මගින් ජංගම දුරකථන, ලැප්ටොප් සහ අනෙකුත් පාරිභෝගික ඉලෙක්ට්රොනික උපකරණ ඇතුළු ඉලෙක්ට්රොනික උපාංග සඳහා නිවාස සහ ආවරණ නිෂ්පාදනය කරයි. නිෂ්පාදකයින් විසින් මෙම සංරචක නිසි ලෙස ගැලපීම සහ ක්රියාකාරීත්වය සහතික කිරීම සඳහා නිශ්චිත පිරිවිතරයන්ට අනුව නිෂ්පාදනය කළ යුතුය.
- ස්විචයන්: ඉන්ජෙක්ෂන් මෝල්ඩින් ඉලෙක්ට්රොනික උපාංගවල භාවිතා කරන පාලන වර්ග කිහිපයක් නිෂ්පාදනය කරයි, රොකර් ස්විච, තල්ලු බොත්තම් ස්විච සහ ස්ලයිඩ් ස්විච ඇතුළුව. විශ්වසනීය ක්රියාකාරිත්වය සහතික කිරීම සඳහා මෙම සංරචක නිශ්චිත ඉවසීමකින් නිපදවිය යුතුය.
- LED සංරචක:ඉන්ජෙක්ෂන් මෝල්ඩින් LED ආලෝකකරණයේ භාවිතා කරන කාච, පරාවර්තක සහ විසරණ ඇතුළු සංරචක කිහිපයක් නිෂ්පාදනය කරයි. නිසි ආලෝකය බෙදා හැරීම සහ කාර්යක්ෂමතාව සහතික කිරීම සඳහා නිෂ්පාදකයින් විසින් නිශ්චිත පිරිවිතරයන් සඳහා මෙම සංරචක නිෂ්පාදනය කළ යුතුය.
- බල සැපයුම් සංරචක: ඉන්ජෙක්ෂන් මෝල්ඩින් සොකට්, පේනු සහ කේබල් සම්බන්ධක ඇතුළුව බල සැපයුම් ඒකකවල භාවිතා කරන සංරචක කිහිපයක් නිෂ්පාදනය කරයි. ආරක්ෂිත සහ විශ්වාසදායක ක්රියාකාරිත්වය සහතික කිරීම සඳහා මෙම සංරචක නිශ්චිත ඉවසීමකින් නිපදවිය යුතුය.
මෙම යෙදුම් වලට අමතරව, නිෂ්පාදකයින් යතුරුපුවරු, පරිගණක මීයන් සහ දුරස්ථ පාලක ඇතුළු තවත් ඉලෙක්ට්රොනික උපාංග කිහිපයක් නිෂ්පාදනය කිරීමට ඉන්ජෙක්ෂන් මෝල්ඩින් භාවිතා කරයි.
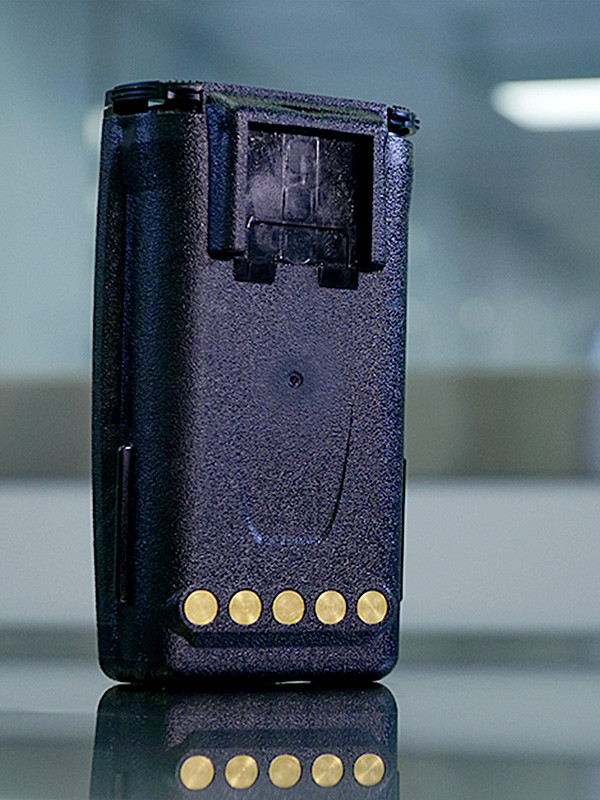
ඉලෙක්ට්රොනික කර්මාන්තයේ ඉන්ජෙක්ෂන් මෝල්ඩින් භාවිතා කිරීමේ ප්රතිලාභ රාශියක් ඇත, ඒවා අතර:
- ඉහළ නිරවද්යතාවය: ඉන්ජෙක්ෂන් මෝල්ඩින් දැඩි තත්ත්ව ප්රමිතීන් සපුරාලන බව සහතික කරමින් ඉහළ මට්ටමේ නිරවද්යතාවයක් සහ අනුකූලතාවයක් සහිත සංරචක නිෂ්පාදනය කිරීමට ඉඩ සලසයි.
- පාරිභෝගිකයාගේ: ඉන්ජෙක්ෂන් මෝල්ඩින් සංකීර්ණ හැඩතල සහ මෝස්තර නිෂ්පාදනය කිරීමට ඉඩ සලසයි, නිෂ්පාදකයින්ට නිශ්චිත සැලසුම් අවශ්යතා සපුරාලීම සඳහා සංරචක අභිරුචිකරණය කිරීමට ඉඩ සලසයි.
- වේගය:ඉන්ජෙක්ෂන් මෝල්ඩින් යනු වේගවත් හා කාර්යක්ෂම නිෂ්පාදන ක්රියාවලියක් වන අතර එමඟින් උසස් තත්ත්වයේ සංරචක විශාල පරිමාවකින් නිෂ්පාදනය කිරීමට, නිෂ්පාදන කාලය සහ පිරිවැය අඩු කිරීමට ඉඩ සලසයි.
අභ්යවකාශ කර්මාන්ත යෙදුම්
අභ්යවකාශ කර්මාන්තය යනු එහි සියලුම සංරචකවල ඉහළම මට්ටමේ නිරවද්යතාවය, නිරවද්යතාවය සහ කල්පැවැත්ම අවශ්ය වන අංශයකි. අභ්යවකාශ කර්මාන්තයේ ප්ලාස්ටික් ඉන්ජෙක්ෂන් මෝල්ඩින් සංකීර්ණ ජ්යාමිතිය නිපදවීමට, බර අඩු කිරීමට සහ ව්යුහාත්මක අඛණ්ඩතාව වැඩි කිරීමට ඇති හැකියාව හේතුවෙන් වඩ වඩාත් සුලභ වී ඇත. මෙහිදී අපි අභ්යවකාශ කර්මාන්තයේ ප්ලාස්ටික් එන්නත් අච්චු ගැසීමේ විවිධ යෙදුම් දෙස සමීපව බලමු.
- අභ්යන්තර සංරචක: ඉන්ජෙක්ෂන් මෝල්ඩින් මඟින් ගුවන් යානා සඳහා ආසන පිටුපස, තැටි මේස සහ උඩිස් මැදිරි ඇතුළු අභ්යන්තර උපාංග මාලාවක් නිෂ්පාදනය කරයි. මෙම සංරචක සැහැල්ලු හා කල් පවතින ඒවා විය යුතුය, අධික ආතතියට ඔරොත්තු දීමේ හැකියාව සහ ඇඳීමට සහ ඉරීම.
- ව්යුහාත්මක සංරචක: ඉන්ජෙක්ෂන් මෝල්ඩින් මගින් පියාපත්, ෆෙයාරිං සහ ෆියුස්ලේජ් කොටස් ඇතුළුව ගුවන් යානා සඳහා ව්යුහාත්මක සංරචක නිෂ්පාදනය කරයි. යානයේ ආරක්ෂාව සහ කාර්යක්ෂමතාව සහතික කිරීම සඳහා මෙම සංරචක සැහැල්ලු, ශක්තිමත් සහ කල් පවතින ඒවා විය යුතුය.
- එන්ජින් සංරචක:ඉන්ජෙක්ෂන් මෝල්ඩින් ගුවන් යානා එන්ජින් සඳහා ටර්බයින තල, ඉන්ධන තුණ්ඩ සහ නිවාස ඇතුළු සංරචක කිහිපයක් නිෂ්පාදනය කරයි. මෙම සංරචක ඉහළ උෂ්ණත්වයන්, පීඩන සහ ආතතීන්ට ඔරොත්තු දීම සඳහා නිශ්චිත පිරිවිතරයන්ට නිෂ්පාදනය කළ යුතුය.
- විදුලි සංරචක: ඉන්ජෙක්ෂන් මෝල්ඩින් ගුවන් යානා සඳහා සම්බන්ධක, ස්විච සහ වයර් පටි ඇතුළු විදුලි උපාංග නිෂ්පාදනය කරයි. නිසි ක්රියාකාරීත්වය සහ විශ්වසනීයත්වය සහතික කිරීම සඳහා මෙම සංරචක නිශ්චිත ඉවසීම සඳහා නිපදවිය යුතුය.
- උපකරණ සංරචක:ඉන්ජෙක්ෂන් මෝල්ඩින් මගින් පාලක පැනල සහ උපකරණ නිවාස ඇතුළු ගුවන් යානා සඳහා උපකරණ සංරචක නිෂ්පාදනය කරයි. මෙම සංරචක කල් පවතින ඒවා විය යුතු අතර ඉහළ උෂ්ණත්ව, පීඩන සහ කම්පනවලට ඔරොත්තු දිය යුතුය.
මෙම යෙදුම් වලට අමතරව, නිෂ්පාදකයින් ගුවන් අභ්යවකාශ කර්මාන්තය සඳහා වරහන්, ගාංචු සහ ගෑස්කට් ඇතුළු තවත් සංරචක කිහිපයක් නිෂ්පාදනය කිරීමට එන්නත් අච්චු භාවිතා කරයි.
අභ්යවකාශ කර්මාන්තයේ ඉන්ජෙක්ෂන් මෝල්ඩින් භාවිතා කිරීමේ ප්රතිලාභ රාශියක් ඇත, ඒවා අතර:
- බර අඩු කිරීම: ඉන්ජෙක්ෂන් මෝල්ඩින් ගුවන් යානයේ බර අඩු කරන සැහැල්ලු සංරචක නිෂ්පාදනය කිරීමට ඉඩ සලසයි, එහි ප්රතිඵලයක් ලෙස අඩු ඉන්ධන පරිභෝජනය සහ කාර්යක්ෂමතාව වැඩි වේ.
- නිරවද්යතාව:ඉන්ජෙක්ෂන් මෝල්ඩින් දැඩි තත්ත්ව ප්රමිතීන් සපුරාලන බවට සහතික කරමින් ඉහළ නිරවද්යතාවයකින් සහ අනුකූලතාවයකින් කොටස් නිෂ්පාදනය කිරීමට ඉඩ සලසයි.
- පාරිභෝගිකයාගේ:ඉන්ජෙක්ෂන් මෝල්ඩින් සංකීර්ණ හැඩතල සහ මෝස්තර නිෂ්පාදනය කිරීමට ඉඩ සලසයි, නිෂ්පාදකයින්ට නිශ්චිත සැලසුම් අවශ්යතා සපුරාලීම සඳහා සංරචක අභිරුචිකරණය කිරීමට ඉඩ සලසයි.
- කල්පැවැත්ම: අයිnjection molding ගුවන් යානයේ ආරක්ෂාව සහ විශ්වසනීයත්වය සහතික කරමින්, කල් පවතින සහ ඉහළ මට්ටමේ ආතතිය, උෂ්ණත්වය සහ පීඩනයට ඔරොත්තු දිය හැකි කොටස් නිෂ්පාදනය කරයි.
පාරිභෝගික භාණ්ඩ කර්මාන්ත යෙදුම්
පාරිභෝගික භාණ්ඩ කර්මාන්තය ගෝලීය ආර්ථිකයේ වඩාත්ම තීරණාත්මක අංශයකි. පාරිභෝගික භාණ්ඩ යනු ගෘහාශ්රිත අයිතම, ඉලෙක්ට්රොනික උපකරණ, සෙල්ලම් බඩු සහ පුද්ගලික සත්කාර නිෂ්පාදන ඇතුළුව පුද්ගලයන් දිනපතා භාවිතා කරන නිෂ්පාදන වේ. නිරවද්යතාවයෙන් හා නිරවද්යතාවයෙන් උසස් තත්ත්වයේ සංරචක නිෂ්පාදනය කිරීමට ඇති හැකියාව හේතුවෙන් පාරිභෝගික භාණ්ඩ කර්මාන්තයේ ප්ලාස්ටික් එන්නත් අච්චුව වැඩි වැඩියෙන් ජනප්රිය වී තිබේ. මෙහිදී අපි පාරිභෝගික භාණ්ඩ කර්මාන්තයේ ප්ලාස්ටික් එන්නත් අච්චු ගැසීමේ විවිධ යෙදුම් දෙස සමීපව බලමු.
- ඇසුරුම්: ආහාර ඇසුරුම්, බීම බෝතල් සහ රූපලාවණ්ය බහාලුම් ඇතුළු පාරිභෝගික භාණ්ඩ සඳහා ඇසුරුම් ද්රව්ය නිෂ්පාදනය කිරීමේදී එන්නත් අච්චුව බහුලව භාවිතා වේ. ඉන්ජෙක්ෂන් මෝල්ඩින් සංකීර්ණ හැඩතල සහ මෝස්තර නිෂ්පාදනය කිරීමට ඉඩ සලසයි, ඇසුරුම් ද්රව්ය ක්රියාකාරී සහ දෘශ්යමාන බව සහතික කරයි.
- ගෘහ භාණ්ඩ: එන්නත් අච්චුව මගින් මුළුතැන්ගෙයි උපකරණ, ගබඩා බහාලුම් සහ පිරිසිදු කිරීමේ සැපයුම් ඇතුළු ගෘහාශ්රිත අයිතම රාශියක් නිෂ්පාදනය කරයි. මෙම අයිතම කල් පවතින, සැහැල්ලු හා දෛනික භාවිතයට ඔරොත්තු දිය යුතුය.
- සෙල්ලම් බඩු: ඉන්ජෙක්ෂන් මෝල්ඩින් ක්රියා රූප, බෝනික්කන් සහ පුවරු ක්රීඩා ඇතුළු විවිධ සෙල්ලම් බඩු නිෂ්පාදනය කරයි. මෙම සෙල්ලම් බඩු ආරක්ෂිත සහ කල් පවතින බව සහතික කිරීම සඳහා නිශ්චිත පිරිවිතරයන්ට අනුව නිෂ්පාදනය කළ යුතුය.
- පුද්ගලික සත්කාර නිෂ්පාදන: එන්නත් අච්චුව දත් බුරුසු, රේසර් සහ ෂැම්පූ බෝතල් ඇතුළු අද්විතීය සත්කාර නිෂ්පාදන නිෂ්පාදනය කරයි. මෙම නිෂ්පාදන සෞන්දර්යාත්මක, ක්රියාකාරී සහ නිතර භාවිතා කිරීමට ඔරොත්තු දිය යුතුය.
- ඉලෙක්ට්රොනික උපකරණ: ඉන්ජෙක්ෂන් මෝල්ඩින් ඉලෙක්ට්රොනික උපාංග සඳහා කේස්, බොත්තම් සහ සම්බන්ධක ඇතුළු සංරචක කිහිපයක් නිෂ්පාදනය කරයි. මෙම සංරචක කල් පවතින, සැහැල්ලු විය යුතු අතර ඉහළ උෂ්ණත්ව හා පීඩනවලට ඔරොත්තු දිය යුතුය.
මෙම යෙදුම් වලට අමතරව, මෝටර් රථ අමතර කොටස්, වෛද්ය උපාංග සහ කාර්මික උපකරණ ඇතුළුව පාරිභෝගික භාණ්ඩ කර්මාන්තය සඳහා තවත් සංරචක කිහිපයක් නිෂ්පාදනය කිරීමට නිෂ්පාදකයින් එන්නත් අච්චු භාවිතා කරයි.
පාරිභෝගික භාණ්ඩ කර්මාන්තයේ ඉන්ජෙක්ෂන් මෝල්ඩින් භාවිතා කිරීමේ ප්රතිලාභ බොහෝය, ඒවා අතර:
- පිරිවැය- ective ලදායී:වෙනත් නිෂ්පාදන ක්රියාවලීන්ට වඩා අඩු වියදමකින් උසස් තත්ත්වයේ සංරචක නිෂ්පාදනය කිරීමට එන්නත් අච්චුව ඉඩ දෙයි.
- අභිරුචිකරණය: අයිnjection molding මඟින් සංකීර්ණ හැඩතල සහ මෝස්තර සහිත මූලද්රව්ය නිර්මාණය කිරීමට ඉඩ සලසයි, නිෂ්පාදකයින්ට නිශ්චිත සැලසුම් අවශ්යතා සපුරාලීම සඳහා විශේෂාංග අභිරුචිකරණය කිරීමට ඉඩ සලසයි.
- නිරවද්යතාව: එන්නත් අච්චුවෙහි දැඩි තත්ත්ව ප්රමිතීන් සපුරාලන ඉතා නිවැරදි සහ ස්ථාවර විස්තර ඇත.
- කල්පැවැත්ම: ඉන්ජෙක්ෂන් මෝල්ඩින් කොටස් කල් පවතින අතර ඉහළ මට්ටමේ ආතතිය, උෂ්ණත්වය සහ පීඩනයට ඔරොත්තු දෙන අතර නිෂ්පාදනවල ආරක්ෂාව සහ විශ්වසනීයත්වය සහතික කරයි.
ඉන්සර්ට් ඉන්ජෙක්ෂන් මෝල්ඩින් හි අනාගත ප්රවණතා
තාක්ෂණය දියුණු වන විට සහ පාරිභෝගික ඉල්ලීම් වෙනස් වන විට, ඇතුළු කිරීමේ එන්නත් අච්චු කර්මාන්තය නිරන්තරයෙන් පරිණාමය වේ. නිෂ්පාදකයින් සෑම විටම කාර්යක්ෂමතාව වැඩි කිරීමට, පිරිවැය අඩු කිරීමට සහ උසස් තත්ත්වයේ නිෂ්පාදන නිෂ්පාදනය කිරීමට මාර්ග සොයයි. මෙන්න අපි insert injection molding වල අනාගත ප්රවණතා කිහිපයක් බලමු.
- ස්වයංක්රීයකරණය: නිෂ්පාදන කර්මාන්තයේ ස්වයංක්රීයකරණය වැඩි වැඩියෙන් ජනප්රිය වෙමින් පවතින අතර ඉන්ජෙක්ෂන් මෝල්ඩින් ඇතුළු කිරීම ව්යතිරේකයක් නොවේ. ස්වයංක්රීය පද්ධති ශ්රම පිරිවැය අඩු කිරීමට, නිෂ්පාදන වේගය වැඩි කිරීමට සහ තත්ත්ව පාලනය වැඩිදියුණු කිරීමට හැකිය.
- තිරසාර බව: වර්ධනය වන පාරිසරික සැලකිල්ලත් සමඟ, නිෂ්පාදකයින් නාස්තිය අඩු කිරීමට සහ තිරසාරත්වය වැඩිදියුණු කිරීමට මාර්ග සොයමින් සිටිති. ප්රතිචක්රීකරණය කරන ලද ද්රව්ය භාවිතා කිරීම සහ පහසුවෙන් ප්රතිචක්රීකරණය කළ හැකි හෝ නැවත භාවිත කළ හැකි නිෂ්පාදන සැලසුම් කිරීම නිෂ්පාදකයින් මෙම ගැටලුව විසඳන ක්රම කිහිපයකි.
- ත්රිමාණ මුද්රණය: Insert injection molding හි සමහර අංග දැනටමත් ත්රිමාණ මුද්රණය භාවිතා කරයි, නමුත් අනාගතයේදී එය වඩාත් ප්රචලිත වීමට හැකියාව ඇත. ඉක්මනින් මූලාකෘති නිර්මාණය කිරීමට සහ අභිරුචි කළ සංරචක නිෂ්පාදනය කිරීමට ඇති හැකියාව ත්රිමාණ මුද්රණයේ එක් වාසියක් පමණි.
- උසස් ද්රව්ය: පර්යේෂකයන් සහ නිෂ්පාදකයින් විවිධ උෂ්ණත්ව, පීඩන සහ ආතතීන්ට ඔරොත්තු දෙන නව ද්රව්ය සංවර්ධනය කරයි.
- ස්මාර්ට් නිෂ්පාදනය:Smart Manufacturing යනු තත්ය කාලීනව දත්ත රැස් කිරීම සහ විශ්ලේෂණය කිරීම සඳහා තාක්ෂණය භාවිතා කිරීම, වේගවත් තීරණ ගැනීමට සහ වඩාත් කාර්යක්ෂම නිෂ්පාදනයට ඉඩ සලසයි. මෙම තාක්ෂණය මගින් තත්ත්ව පාලනය වැඩිදියුණු කිරීමට, අක්රීය කාලය අඩු කිරීමට සහ ඵලදායිතාව වැඩි කිරීමට හැකිය.
නිගමනය
Insert injection molding යනු කාවැද්දූ සංරචක සහිත සංකීර්ණ කොටස් නිර්මාණය කිරීමට ඉඩ සලසන බහුකාර්ය සහ ලාභදායී නිෂ්පාදන ක්රියාවලියකි. සාම්ප්රදායික එකලස් කිරීමේ ක්රමවලට වඩා එහි ඇති වාසි මෝටර් රථ, වෛද්ය, ඉලෙක්ට්රොනික, ගුවන් අභ්යවකාශ සහ පාරිභෝගික භාණ්ඩ ඇතුළු විවිධ කර්මාන්තවල එය ජනප්රිය කරයි. ඉන්ජෙක්ෂන් මෝල්ඩින් සම්බන්ධ විවිධ ශිල්පීය ක්රම, ද්රව්ය සහ සැලසුම් සලකා බැලීම් අවබෝධ කර ගැනීමෙන්, නිෂ්පාදකයින්ට ඔවුන්ගේ නිෂ්පාදන ක්රියාවලීන් ප්රශස්ත කර උසස් තත්ත්වයේ නිෂ්පාදන ඔවුන්ගේ පාරිභෝගිකයින්ට ලබා දිය හැකිය. තාක්ෂණය දියුණු වන විට, ඇතුළු කිරීමේ එන්නත් අච්චු ගැසීමේ ඊටත් වඩා නව්ය යෙදුම් දැකීමට අපට අපේක්ෂා කළ හැකිය.