ප්ලාස්ටික් ඉන්ජෙක්ෂන් මෝල්ඩින්
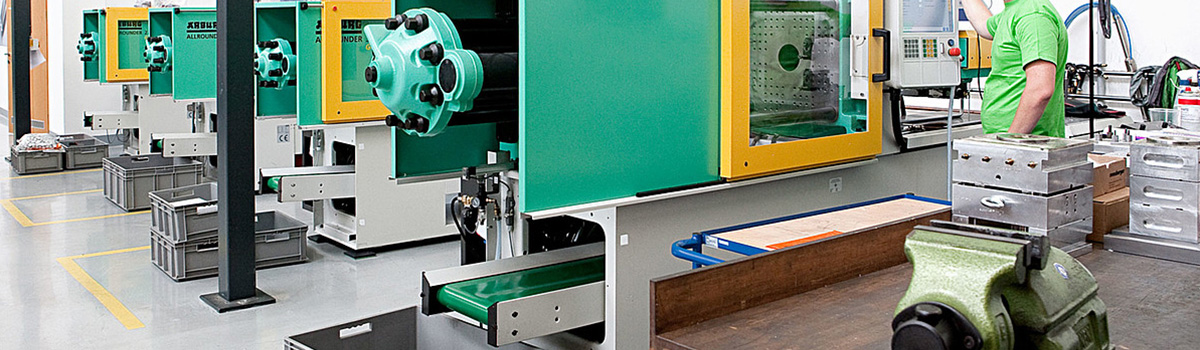
ප්ලාස්ටික් ඉන්ජෙක්ෂන් මෝල්ඩින් යනු නිෂ්පාදන ක්රියාවලියක් වන අතර එය ප්ලාස්ටික් පෙති උණු කිරීම සහ ත්රිමාණ වස්තුවක් නිර්මාණය කිරීම සඳහා අච්චු කුහරයකට එන්නත් කිරීම ඇතුළත් වේ. මෙම ක්රියාවලිය කුඩා නිරවද්ය කොටස්වල සිට සැලකිය යුතු මෝටර් රථ සංරචක දක්වා බොහෝ නිෂ්පාදන සමඟ ආරම්භ වේ. ප්ලාස්ටික් ඉන්ජෙක්ෂන් මෝල්ඩින් අනෙකුත් නිෂ්පාදන ක්රියාවලීන්ට වඩා බොහෝ වාසි ලබා දෙයි, ඉහළ නිෂ්පාදන අනුපාත, සැලසුම් නම්යශීලීභාවය සහ පිරිවැය-ඵලදායීතාවය ඇතුළුව. මෙම මාර්ගෝපදේශය ප්ලාස්ටික් එන්නත් අච්චුව ගැඹුරින් බලා එහි විවිධ යෙදුම්, ප්රතිලාභ සහ සීමාවන් ගවේෂණය කරනු ඇත.
ප්ලාස්ටික් එන්නත් අච්චු ගැසීමේ ඉතිහාසය
ප්ලාස්ටික් ඉන්ජෙක්ෂන් මෝල්ඩින් යනු නිශ්චිත හැඩයක් නිර්මාණය කිරීම සඳහා උණු කළ ප්ලාස්ටික් අච්චු කුහරයකට එන්නත් කිරීම ඇතුළත් නිෂ්පාදන ක්රියාවලියකි. ප්ලාස්ටික් එන්නත් අච්චු ගැසීමේ ඉතිහාසය 1800 ගණන්වල අගභාගයේ සිට සෙලියුලොයිඩ්, ප්ලාස්ටික් වර්ගයක් මුලින්ම සොයා ගත හැක. කෙසේ වෙතත්, 1940 ගණන්වලදී ප්ලාස්ටික් එන්නත් අච්චුව නිෂ්පාදන තාක්ෂණයක් ලෙස බහුලව භාවිතා විය.
දෙවන ලෝක සංග්රාමයේදී, මහා පරිමාණයෙන් නිපදවන ලද ප්ලාස්ටික් නිෂ්පාදන සඳහා ඇති ඉල්ලුම වැඩි වූ අතර, නිෂ්පාදකයින් ඒවා නිෂ්පාදනය කිරීමට නව සහ වඩා කාර්යක්ෂම ක්රම සෙවීමට පටන් ගත්හ. 1946 දී ඇමරිකානු නව නිපැයුම්කරුවෙකු වන ජේම්ස් වොට්සන් හෙන්ඩ්රි විසින් ප්ලාස්ටික් එන්නත් මෝල්ඩින් කර්මාන්තයේ විප්ලවීය වෙනසක් ඇති කළ පළමු ඉස්කුරුප්පු එන්නත් අච්චු යන්ත්රය නිපදවන ලදී. මෙම යන්ත්රය වඩාත් නිරවද්ය සහ ස්ථාවර එන්නත් ක්රියාවලි පාලනය සඳහා ඉඩ ලබා දුන් අතර, විශාල ප්රමාණයේ ප්ලාස්ටික් කොටස් නිෂ්පාදනය වඩාත් ප්රවේශ විය හැකි සහ කාර්යක්ෂම කරයි.
1950 ගනන් සහ 1960 ගනන් පුරාවටම ප්ලාස්ටික් තාක්ෂණයේ දියුණුව ප්ලාස්ටික් එන්නත් අච්චු ගැසීමේ ක්රියාවලිය වැඩිදියුණු කිරීමට අඛණ්ඩව සිදු විය. ෙපොලිස්ටිරින් සහ ෙපොලිඑතිලීන් වැනි නව ද්රව්ය හඳුන්වාදීම, වඩාත් සංකීර්ණ සහ කල් පවතින ප්ලාස්ටික් කොටස් නිර්මාණය විය. මීට අමතරව, හයිඩ්රොලික් පද්ධති භාවිතා කිරීම ඇතුළුව මෝල්ඩින් යන්ත්ර තාක්ෂණයේ වැඩිදියුණු කිරීම්, එන්නත් අච්චු ගැසීමේ ක්රියාවලිය වඩාත් කාර්යක්ෂම හා ලාභදායී විය.
අද, ප්ලාස්ටික් එන්නත් අච්චුව යනු සෙල්ලම් බඩු සහ පාරිභෝගික භාණ්ඩවල සිට වාහන අමතර කොටස් සහ වෛද්ය උපකරණ දක්වා පුළුල් පරාසයක ප්ලාස්ටික් නිෂ්පාදන නිෂ්පාදනය කිරීම සඳහා භාවිතා කරන ඉතා ස්වයංක්රීය ක්රියාවලියකි. නව ද්රව්ය හා තාක්ෂණයන් දියුණු කිරීමත් සමඟ ප්ලාස්ටික් එන්නත් අච්චු ගැසීමේ ක්රියාවලිය අඛණ්ඩව පරිණාමය වෙමින් වැඩිදියුණු වෙමින් පවතින අතර එය වසර ගණනාවක් පුරා අත්යවශ්ය නිෂ්පාදන තාක්ෂණයක් ලෙස පවතිනු ඇත.
ප්ලාස්ටික් එන්නත් අච්චු ගැසීමේ මූලික කරුණු
ප්ලාස්ටික් ඉන්ජෙක්ෂන් මෝල්ඩින් යනු ප්ලාස්ටික් ද්රව්ය වලින් සාදන ලද කොටස් සහ නිෂ්පාදන නිර්මාණය කිරීම සඳහා නිෂ්පාදන ක්රියාවලියකි. මෙම ක්රියාවලියට උණු කළ ප්ලාස්ටික් අච්චුවකට එන්නත් කිරීම ඇතුළත් වන අතර, එය සිසිල් වී අවශ්ය හැඩය සෑදීමට ඝන වේ.
ප්ලාස්ටික් එන්නත් අච්චු සැකසීමේ ක්රියාවලියට සම්බන්ධ මූලික පියවර පහත පරිදි වේ:
- අච්චු නිර්මාණය: ක්රියාවලියෙහි පළමු පියවර වන්නේ අපේක්ෂිත කොටස නිර්මාණය කිරීම සඳහා භාවිතා කරන අච්චුව නිර්මාණය කිරීමයි. අච්චුව සාමාන්යයෙන් ලෝහයෙන් සාදා ඇති අතර ප්ලාස්ටික් සිසිල් වී ඝණීකරනය වන විට හැකිලීම සඳහා එය සූදානම් විය යුතුය.
- ද්රව්ය සකස් කිරීම: එන්නත් අච්චු ගැසීමේ ක්රියාවලියේදී භාවිතා කරන ප්ලාස්ටික් ද්රව්ය පෙති හෝ කැටිති ආකාරයෙන් එන අතර ඒවා උණු කොට අච්චුවට එන්නත් කිරීම සඳහා සූදානම් කළ යුතුය. මෙය සාමාන්යයෙන් සිදු කරනුයේ ආප්පයක වන අතර එහිදී ප්ලාස්ටික් නිශ්චිත උෂ්ණත්වයකට රත් කර ද්රව තත්වයට දිය වේ.
- එන්නත් කිරීම: ප්ලාස්ටික් උණු කළ පසු, විශේෂිත ඉන්ජෙක්ෂන් මෝල්ඩින් යන්ත්රයක් භාවිතයෙන් එය අච්චුව තුළට එන්නත් කරනු ලැබේ. යන්ත්රය උණු කළ ප්ලාස්ටික් සඳහා පීඩනය යොදන අතර, එය අච්චු කුහරය තුළට බලහත්කාරයෙන් බල කරයි, එය අච්චුවේ හැඩය ගනී.
- සිසිලනය සහ ඝනීභවනය: ප්ලාස්ටික් අච්චුව තුළට එන්නත් කිරීමෙන් පසුව, එය සිසිල් සහ ඝනීභවනය කළ හැකිය. කොටසෙහි විශාලත්වය සහ සංකීර්ණත්වය අනුව මෙය තත්පර කිහිපයක සිට මිනිත්තු කිහිපයක් දක්වා ගත විය හැක.
- පිටකිරීම: ප්ලාස්ටික් සිසිල් වී ඝන වූ පසු, අච්චුව විවෘත කර ඇති අතර, එම කොටස ඉවත් කරනු ලැබේ. අතිරික්ත ප්ලාස්ටික් හෝ රළු දාර ඉවත් කිරීම සඳහා, සිඳීම හෝ වැලි දැමීම වැනි අමතර නිම කිරීමේ කාර්යයක් අවශ්ය විය හැකිය.
ප්ලාස්ටික් ඉන්ජෙක්ෂන් මෝල්ඩින් යනු නිශ්චිත හා පුනරාවර්තන ක්රියාවලියක් වන අතර, එය ස්ථාවර ගුණාත්මක භාවයෙන් යුත් කොටස් සහ නිෂ්පාදන මහා පරිමාණයෙන් නිෂ්පාදනය කිරීම සඳහා වඩාත් සුදුසු වේ. විවිධ ප්රමාණවලින්, හැඩවලින් සහ සංකීර්ණත්වයෙන් කෑලි සහ නිෂ්පාදන නිර්මාණය කළ හැකි බැවින් එය ඉතා බහුකාර්ය වේ. ප්ලාස්ටික් ඉන්ජෙක්ෂන් මෝල්ඩින්ගේ වඩාත් පොදු යෙදුම් අතරට සෙල්ලම් බඩු, පාරිභෝගික භාණ්ඩ, වාහන අමතර කොටස් සහ වෛද්ය උපකරණ නිෂ්පාදනය ඇතුළත් වේ.
ප්ලාස්ටික් ඉන්ජෙක්ෂන් මෝල්ඩින් ක්රියාවලිය: පියවරෙන් පියවර
ප්ලාස්ටික් එන්නත් අච්චුව යනු පියවර කිහිපයකින් සමන්විත සංකීර්ණ ක්රියාවලියකි. ප්ලාස්ටික් එන්නත් අච්චු ගැසීමේ ක්රියාවලිය සඳහා පියවරෙන් පියවර මාර්ගෝපදේශයක් මෙන්න:
- අච්චුව සැලසුම් කිරීම: පළමු පියවර වන්නේ කොටස නිර්මාණය කිරීමට භාවිතා කරන අච්චුව නිර්මාණය කිරීමයි. අච්චුව සාමාන්යයෙන් වානේ හෝ ඇලුමිනියම් වලින් සාදා ඇති අතර එය සිසිල් වන විට ප්ලාස්ටික් ද්රව්ය හැකිලීමට ඉඩ සැලසීමට සූදානම් විය යුතුය.
- අච්චුව නිර්මාණය කිරීම: අච්චු නිර්මාණය සම්පූර්ණ වූ පසු, එය පරිගණක ආශ්රිත නිර්මාණ (CAD) මෘදුකාංග සහ පරිගණක ආශ්රිත නිෂ්පාදන (CAM) යන්ත්රෝපකරණ භාවිතයෙන් නිෂ්පාදනය කෙරේ. අවසාන නිෂ්පාදනයේ නිරවද්යතාවය සහ නිමාව සහතික කිරීම සඳහා අච්චුව ප්රවේශමෙන් යන්ත්රගත කර ඔප දැමිය යුතුය.
- ද්රව්ය තෝරාගැනීම: ඉන්ජෙක්ෂන් මෝල්ඩින් ක්රියාවලිය සඳහා භාවිතා කරන ප්ලාස්ටික් ෙරසින් ද්රව්ය එහි ශක්තිය, නම්යශීලී බව, වර්ණය සහ වයනය වැනි කොටසෙහි අවශ්යතා මත පදනම්ව තෝරා ගත යුතුය.
- ද්රව්ය සකස් කිරීම: තෝරාගත් ප්ලාස්ටික් ද්රව්ය නිශ්චිත උෂ්ණත්වයකට රත් කර ද්රවයක් බවට පත් කරනු ලැබේ. පසුව එම ද්රව්යය අච්චු යන්ත්රයේ ආප්පයට එන්නත් කරනු ලැබේ.
- ඉන්ජෙක්ෂන් මෝල්ඩින්: උණු කළ ප්ලාස්ටික් ද්රව්ය විශේෂිත එන්නත් අච්චු යන්ත්රයක් භාවිතයෙන් අච්චු කුහරයට එන්නත් කරනු ලැබේ. යන්ත්රය ප්ලාස්ටික් ද්රව්යයට පීඩනය යොදන අතර එය අච්චු කුහරය තුළට බල කරයි, එහිදී එය අච්චුවේ හැඩය ගනී.
- සිසිලනය: අච්චු කුහරය ප්ලාස්ටික් වලින් පුරවා ගත් පසු, එය සිසිල් කර ඝන විය හැක. ප්ලාස්ටික් ද්රව්යයේ ලක්ෂණ, කොටසෙහි විශාලත්වය සහ ඝණකම සහ අච්චු උෂ්ණත්වය අනුව සිසිලන කාලය තීරණය වේ.
- පිටකිරීම: ප්ලාස්ටික් ඝන වීමෙන් පසුව, අච්චුව විවෘත කර ඇති අතර, එම කොටස ejector pins භාවිතයෙන් අච්චුවෙන් ඉවත් කරනු ලැබේ.
- අවසන් කිරීම: පිට කරන ලද කොටසෙහි අතිරික්ත ප්ලාස්ටික් හෝ රළු දාර ඉවත් කිරීම සඳහා කැපීම, වැලි දැමීම හෝ පින්තාරු කිරීම වැනි අමතර නිම කිරීමේ කාර්යයක් අවශ්ය විය හැකිය.
- තත්ත්ව පාලනය: අවශ්ය පිරිවිතරයන් සහ තත්ත්ව ප්රමිතීන් සපුරාලීම සඳහා නිමි කොටස සම්පූර්ණ පරීක්ෂාවකට භාජනය වේ.
ප්ලාස්ටික් ඉන්ජෙක්ෂන් මෝල්ඩින් විවිධ කොටස් සහ නිෂ්පාදන බහු ප්රමාණවලින්, හැඩයන්ගෙන් සහ සංකීර්ණත්වයෙන් නිපදවිය හැක. මෙම ක්රියාවලිය මෝටර් රථ, වෛද්ය, පාරිභෝගික භාණ්ඩ සහ ඉලෙක්ට්රොනික උපකරණ ඇතුළු කර්මාන්ත කිහිපයක බහුලව භාවිතා වේ.
එන්නත් අච්චු ගැසීමේදී භාවිතා කරන ප්ලාස්ටික් වර්ග
ඉන්ජෙක්ෂන් මෝල්ඩින් කිරීමේදී බොහෝ ප්ලාස්ටික් වර්ග භාවිතා කළ හැකිය. ප්ලාස්ටික් ද්රව්ය තෝරා ගැනීම නිෂ්පාදනයේ හෝ නිෂ්පාදනය කරන කොටසෙහි ශක්තිය, නම්යශීලීභාවය, කල්පැවැත්ම සහ පෙනුම වැනි නිශ්චිත අවශ්යතා මත රඳා පවතී. එන්නත් අච්චු ගැසීමේදී බහුලව භාවිතා වන ප්ලාස්ටික් වර්ග කිහිපයක් මෙන්න:
- පොලිඑතිලීන් (PE): PE යනු එහි ශක්තිය සහ නම්යශීලී බව සඳහා ප්රසිද්ධ බහුලව භාවිතා වන ප්ලාස්ටික් ද්රව්යයකි. ඇසුරුම් ද්රව්ය, සෙල්ලම් බඩු සහ වෛද්ය උපකරණ ඇතුළු විවිධ නිෂ්පාදන නිෂ්පාදනය කිරීමට එය භාවිතා කරයි.
- පොලිප්රොපිලීන් (PP): PP යනු උපකරණ පුවරු සහ දොර පැනල් වැනි අභ්යන්තර කොටස් සඳහා මෝටර් රථ කර්මාන්තයේ බහුලව භාවිතා වන සැහැල්ලු සහ කල් පවතින ප්ලාස්ටික් ද්රව්යයකි. එය බහාලුම් සහ බෝතල් වැනි ඇසුරුම් ද්රව්ය ද නිෂ්පාදනය කරයි.
- පොලිකාබනේට් (PC): PC යනු පරිගණක සහ දුරකථන ආවරණ වැනි ඉලෙක්ට්රොනික උපාංග නිෂ්පාදනය සඳහා බහුලව භාවිතා වන ඝන සහ විනිවිද පෙනෙන ප්ලාස්ටික් ද්රව්යයකි. එය මෝටර් රථ කර්මාන්තයේ හෙඩ්ලාම්ප් කාච සහ උපකරණ පුවරු සංරචක සඳහා ද භාවිතා වේ.
- Acrylonitrile Butadiene Styrene (ABS): ABS යනු එහි ශක්තිය, කල්පැවැත්ම සහ තාප ප්රතිරෝධය සඳහා ප්රසිද්ධ බහුකාර්ය ප්ලාස්ටික් ද්රව්යයකි. උපකරණ පුවරු, ෆෙන්ඩර් ගිනි දැල්, සෙල්ලම් බඩු සහ පාරිභෝගික භාණ්ඩ වැනි වාහන අමතර කොටස් නිෂ්පාදනය කිරීමට එය බහුලව භාවිතා වේ.
- Polyamide (PA): PA, නයිලෝන් ලෙසද හැඳින්වේ, එය එන්ජින් ආවරණ සහ වාතය ලබා ගැනීමේ පද්ධති වැනි මෝටර් රථ කොටස් නිෂ්පාදනය සඳහා බහුලව භාවිතා වන ශක්තිමත් සහ සැහැල්ලු ප්ලාස්ටික් ද්රව්යයකි. එය ස්කී බූට් සහ ටෙනිස් ජාවාරම් වැනි ක්රීඩා උපකරණ ද නිෂ්පාදනය කරයි.
- Polystyrene (PS): PS යනු කෝප්ප, තැටි සහ ආහාර බහාලුම් වැනි ඇසුරුම් ද්රව්ය නිෂ්පාදනයේදී බහුලව භාවිතා වන සැහැල්ලු හා දෘඩ ප්ලාස්ටික් ද්රව්යයකි. එය සෙල්ලම් බඩු සහ ඉලෙක්ට්රොනික උපාංග වැනි පාරිභෝගික භාණ්ඩ ද නිෂ්පාදනය කරයි.
- Polyethylene Terephthalate (PET): PET යනු බෝතල් සහ බහාලුම් වැනි ඇසුරුම් ද්රව්ය නිෂ්පාදනය සඳහා බහුලව භාවිතා වන ශක්තිමත් සහ විනිවිද පෙනෙන ප්ලාස්ටික් ද්රව්යයකි. එය තන්තු සහ රෙදි නිෂ්පාදනය සඳහා රෙදිපිළි කර්මාන්තයේ ද භාවිතා වේ.
මේවා එන්නත් අච්චු ගැසීමේදී බහුලව භාවිතා වන ප්ලාස්ටික් වර්ග කිහිපයක් පමණි. තවත් බොහෝ ප්ලාස්ටික් ද්රව්ය ලබා ගත හැකි අතර, එක් එක් අද්විතීය ගුණාංග සහ ලක්ෂණ ඇත. ප්ලාස්ටික් ද්රව්ය තෝරාගැනීම නිෂ්පාදනය කරනු ලබන කොටස හෝ නිෂ්පාදනයේ නිශ්චිත අවශ්යතා මත රඳා පවතී.
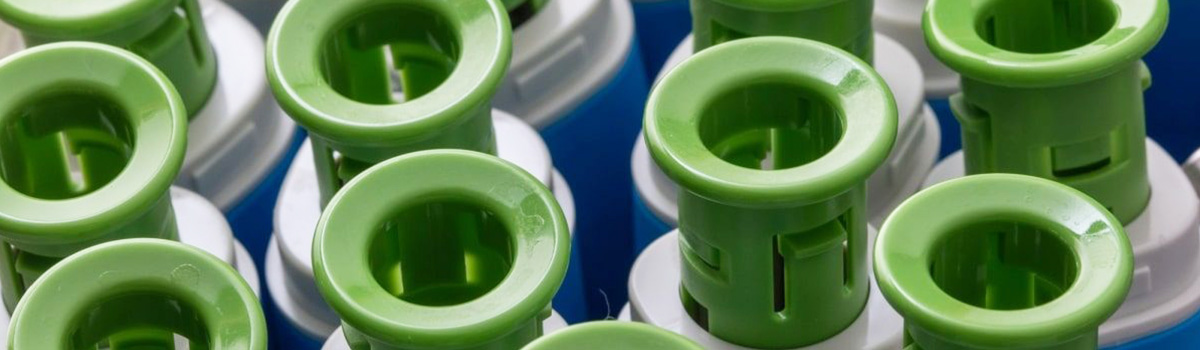
ඉන්ජෙක්ෂන් මෝල්ඩින් යන්ත්ර වර්ග
ඉන්ජෙක්ෂන් මෝල්ඩින් යන්ත්ර විවිධ වර්ග සහ ප්රමාණවලින් පැමිණේ, එක් එක් විශේෂිත නිෂ්පාදන අවශ්යතා සපුරාලීම සඳහා නිර්මාණය කර ඇත. එන්නත් මෝල්ඩින් යන්ත්රවල වඩාත් සුලභ වර්ග කිහිපයක් මෙන්න:
- හයිඩ්රොලික් ඉන්ජෙක්ෂන් මෝල්ඩින් යන්ත්රය: මෙම යන්ත්රය අච්චුවට ප්ලාස්ටික් එන්නත් කිරීම සඳහා පීඩනය ජනනය කිරීමට හයිඩ්රොලික් බලය භාවිතා කරයි. හයිඩ්රොලික් යන්ත්ර සාමාන්යයෙන් භාවිතා කරනුයේ ඉහළ කලම්ප බලයක් අවශ්ය වන වඩාත් වැදගත් කොටස් සඳහාය.
- විද්යුත් ඉන්ජෙක්ෂන් මෝල්ඩින් යන්ත්රය: විදුලි යන්ත්ර එන්නත් ඒකකය සහ කලම්ප යාන්ත්රණය බල ගැන්වීම සඳහා විදුලි මෝටර භාවිතා කරයි. ඔවුන් කුඩා, සංකීර්ණ කොටස් නිෂ්පාදනය සඳහා ප්රසිද්ධ කර, ඔවුන්ගේ ඉහළ නිරවද්යතාව සහ බලශක්ති කාර්යක්ෂමතාව සඳහා ප්රසිද්ධ වේ.
- හයිබ්රිඩ් ඉන්ජෙක්ෂන් මෝල්ඩින් යන්ත්රය: හයිබ්රිඩ් යන්ත්ර හයිඩ්රොලික් සහ විද්යුත් උපාංගවල ප්රතිලාභ ඒකාබද්ධ කරයි, අවශ්ය පීඩනය සහ බලය ජනනය කිරීම සඳහා හයිඩ්රොලික් සහ විදුලි බලය යන දෙකම භාවිතා කරයි. හයිබ්රිඩ් යන්ත්ර වේගයෙන්, නිරවද්යතාවයෙන් සහ බලශක්ති කාර්යක්ෂමතාවයේ හොඳ සමතුලිතතාවයක් ලබා දෙයි.
- සිරස් ඉන්ජෙක්ෂන් මෝල්ඩින් යන්ත්රය: සිරස් යන්ත්ර මඟින් අච්චු ඇතුළු කිරීම හෝ අධික ලෙස අච්චු ගැසීම අවශ්ය කොටස් නිෂ්පාදනය කරයි. ඔවුන් කුඩා හෝ සංකීර්ණ කොටස් නිර්මාණය කිරීම සඳහා සුදුසු වන පරිදි, අච්චුව වෙත පහසුවෙන් ප්රවේශ වීමට ඉඩ සලසන සිරස් කලම්ප ඒකකයක් ඇත.
- Two-shot Injection මෝල්ඩින් යන්ත්රය: ද්වි-වෙඩි යන්ත්ර විවිධ ද්රව්ය හෝ වර්ණ සහිත කොටස් නිෂ්පාදනය කරයි. උපාංගයට එන්නත් ඒකක දෙකක් ඇත, ඒ සෑම එකක්ම අච්චුවට විදේශීය ද්රව්ය එන්නත් කළ හැකිය. මෙම වර්ගයේ යන්ත්ර සාමාන්යයෙන් භාවිතා කරනුයේ හැන්ඩ්ල් සහ බොත්තම් වැනි වාහන අමතර කොටස් නිෂ්පාදනය කිරීමට ය.
- බහු-වෙඩි එන්නත් අච්චු යන්ත්රය: බහු-වෙඩි යන්ත්ර ද්රව්ය හෝ වර්ණ දෙකකට වඩා වැඩි කොටස් නිෂ්පාදනය කරයි. උපාංගයට බහු එන්නත් ඒකක ඇත, ඒ සෑම එකක්ම අච්චුව තුළට විවිධ ද්රව්ය එන්නත් කළ හැකිය. දත් බුරුසු සහ රේසර් වැනි පාරිභෝගික භාණ්ඩ නිෂ්පාදනය සඳහා මෙම වර්ගයේ යන්ත්ර බහුලව භාවිතා වේ.
- සියලුම-විද්යුත් ඉන්ජෙක්ෂන් මෝල්ඩින් යන්ත්රය: සියලුම විද්යුත් යන්ත්ර එන්නත් ඒකකය, කලම්ප යාන්ත්රණය සහ අච්චුව බල ගැන්වීම සඳහා විදුලි මෝටර භාවිතා කරයි. ඒවායේ ඉහළ නිරවද්යතාවය, වේගය සහ බලශක්ති කාර්යක්ෂමතාව සඳහා ප්රසිද්ධ වී ඇති අතර, ඒවා කුඩා, ඉහළ නිරවද්ය කොටස් නිෂ්පාදනය සඳහා ප්රසිද්ධියට පත් කරයි.
මේවා වඩාත් සුලභ ඉන්ජෙක්ෂන් මෝල්ඩින් යන්ත්ර කිහිපයක් පමණි. සෑම යන්ත්රයකම සුවිශේෂී ලක්ෂණ සහ වාසි ඇත, නිශ්චිත නිෂ්පාදන අවශ්යතා සඳහා සුදුසු උපාංගයක් තෝරා ගැනීම අත්යවශ්ය වේ.
ඉන්ජෙක්ෂන් මෝල්ඩින් යන්ත්රයක කොටස්
ඉන්ජෙක්ෂන් මෝල්ඩින් යන්ත්රවල අමුද්රව්ය වලින් ප්ලාස්ටික් කොටස් නිර්මාණය කරන කොටස් කිහිපයක් ඇත. එන්නත් මෝල්ඩින් යන්ත්රයක තීරණාත්මක සංරචක මෙන්න:
ආප්ප: අමු ප්ලාස්ටික් ද්රව්ය ඉන්ජෙක්ෂන් මෝල්ඩින් යන්ත්රයට ලබා දීමට පෙර ජලාශය රඳවා තබා ගනී. ද්රව්යය සාමාන්යයෙන් පෙති හෝ කුඩු ආකාරයෙන් වේ.
බැරලය: බැරලය යනු ප්ලාස්ටික් ද්රව්ය උණු කර මිශ්ර කරන ඉස්කුරුප්පු ඇණ සවි කර ඇති ඉන්ජෙක්ෂන් මෝල්ඩින් යන්ත්රයේ දිගු සිලින්ඩරාකාර කොටසයි.
ඉස්කුරුප්පු ඇණ: ඉස්කුරුප්පු ඇණ යනු ප්ලාස්ටික් ද්රව්ය ඉදිරියට තල්ලු කර ඝර්ෂණය සහ තාපය මගින් එය උණු කරන බැරලය තුළ භ්රමණය වන උපකරණයකි.
එන්නත් ඒකකය: එන්නත් කිරීමේ ඒකකයට ආප්ප, බැරල් සහ ඉස්කුරුප්පු ඇණ ඇතුළත් වන අතර ප්ලාස්ටික් උණු කිරීම සහ අච්චුවට එන්නත් කිරීම සඳහා වගකිව යුතුය.
කලම්ප ඒකකය: ක්ලැම්පින් ඒකකය ආරක්ෂිතව අච්චුව රඳවා තබා ගැනීම සහ එන්නත් අච්චු ගැසීමේ ක්රියාවලියේදී අවශ්ය පීඩනය යෙදීම සඳහා වගකිව යුතුය.
අච්චුව: අච්චුව යනු ප්ලාස්ටික් කොටසෙහි හැඩය සහ ප්රමාණය නිර්මාණය කරන මෙවලමයි. අච්චුව සාමාන්යයෙන් වානේ වලින් සාදා ඇති අතර එකට ගැලපෙන කොටස් දෙකකින් සමන්විත වේ.
තුණ්ඩය: තුණ්ඩය යනු ඉන්ජෙක්ෂන් මෝල්ඩින් යන්ත්රය අච්චුවට සම්බන්ධ කරන එන්නත් ඒකකයේ කොටසයි. උණු කරන ලද ප්ලාස්ටික් ද්රව්ය තුණ්ඩය හරහා සහ අච්චුව තුලට එන්නත් කරනු ලැබේ.
සිසිලන පද්ධතිය: අච්චුව තුළට එන්නත් කළ ප්ලාස්ටික් කොටස සිසිල් කිරීම සඳහා සිසිලන පද්ධතිය වගකිව යුතුය. මෙම කෑල්ල ඝනීභවනය වන අතර හානියකින් තොරව අච්චුවෙන් ඉවත් කළ හැකිය.
පාලන පැනලය: පාලන පැනලය යනු උෂ්ණත්වය, පීඩනය සහ චක්ර කාලය වැනි එන්නත් අච්චු යන්ත්රයේ සැකසුම් නිරීක්ෂණය කිරීමට සහ සැකසීමට ක්රියාකරුට ඉඩ දෙන අතුරු මුහුණතයි.
මෙම සෑම කොටසක්ම එන්නත් අච්චු ගැසීමේ ක්රියාවලියේදී තීරණාත්මක කාර්යභාරයක් ඉටු කරන අතර උසස් තත්ත්වයේ කොටස් කාර්යක්ෂමව නිෂ්පාදනය කිරීම සහතික කිරීම සඳහා එක් එක් කැබැල්ල නඩත්තු කිරීම සහ ප්රශස්ත කිරීම අත්යවශ්ය වේ.
ඉන්ජෙක්ෂන් මෝල්ඩින් මෙවලම්: සැලසුම් කිරීම සහ නිෂ්පාදනය කිරීම
ඉන්ජෙක්ෂන් මෝල්ඩින් මෙවලම් යනු ප්ලාස්ටික් කොටස් නිෂ්පාදනය කිරීම සඳහා ඉන්ජෙක්ෂන් මෝල්ඩින් යන්ත්රවල භාවිතා කරන අච්චු සැලසුම් කිරීම සහ නිෂ්පාදනය කිරීමයි. අච්චු වල ගුණාත්මකභාවය සහ කාර්යක්ෂමතාවය එන්නත් කිරීමේ වාත්තු ක්රියාවලියේ ගුණාත්මකභාවය සහ ඵලදායිතාවයට සෘජුවම බලපායි. ඉන්ජෙක්ෂන් මෝල්ඩින් මෙවලම් නිර්මාණය සහ නිෂ්පාදනය කිරීමේ තීරණාත්මක පියවර මෙන්න:
නිෂ්පාදන සැලසුම: ඉන්ජෙක්ෂන් මෝල්ඩින් මෙවලම්වල පළමු පියවර වන්නේ නිෂ්පාදනය කළ යුතු නිෂ්පාදනය සැලසුම් කිරීමයි. නිෂ්පාදන සැලසුමට කොටසේ ප්රමාණය, හැඩය සහ ද්රව්ය මෙන්ම කිසියම් විශේෂිත ලක්ෂණ හෝ අවශ්යතා තීරණය කිරීම ඇතුළත් වේ.
අච්චු නිර්මාණය: නිෂ්පාදන සැලසුම අවසන් වූ පසු අච්චු නිර්මාණ ක්රියාවලිය ආරම්භ වේ. අච්චු නිර්මාණකරු විසින් හොඳම වර්ගයේ අච්චුව, අවශ්ය කුහර ගණන සහ අච්චුවේ ප්රමාණය සහ හැඩය තීරණය කරනු ඇත.
අච්චු ඉදි කිරීම්: අච්චුව නිර්මාණය කර ඇත්තේ වානේ හෝ ඇලුමිනියම් වැනි උසස් තත්ත්වයේ ද්රව්ය භාවිතා කරමිනි. අච්චුව සාමාන්යයෙන් අර්ධ දෙකකින් සාදා ඇති අතර, එක් එක් කුහර එකක් හෝ කිහිපයක් අඩංගු වේ.
අච්චු එකලස් කිරීම: අච්චුව ඉදිකරන ලද පසු, එය එකලස් කර නිරවද්යතාවය සහ ක්රියාකාරීත්වය සඳහා පරීක්ෂා කරනු ලැබේ. අච්චුව එන්නත් අච්චු කිරීමේ ක්රියාවලියේ පීඩනය හා තාපයට ඔරොත්තු දිය යුතුය.
අච්චුව පරීක්ෂා කිරීම සහ වලංගු කිරීම: අච්චුව එකලස් කිරීමෙන් පසුව, එය නිෂ්පාදන පිරිවිතරයන්ට අනුකූලව උසස් තත්ත්වයේ කොටස් නිපදවන බව සහතික කිරීම සඳහා එය පරීක්ෂා කර වලංගු වේ. එහි කාර්ය සාධනය වැඩි දියුණු කිරීම සඳහා අච්චුව සකස් කිරීම හෝ වෙනස් කිරීම අවශ්ය විය හැකිය.
අච්චු නඩත්තු කිරීම: අච්චුවෙහි කල්පැවැත්ම සහ කාර්ය සාධනය සහතික කිරීම සඳහා නිතිපතා නඩත්තු කිරීම සහ අලුත්වැඩියා කිරීම ඉතා වැදගත් වේ. මෙයට පිරිසිදු කිරීම, ලිහිසි කිරීම සහ දිරාපත් වූ හෝ හානි වූ කොටස් ප්රතිස්ථාපනය කිරීම ඇතුළත් වේ.
ඉන්ජෙක්ෂන් මෝල්ඩින් මෙවලම් සඳහා උසස් තත්ත්වයේ කොටස් අඛණ්ඩව සහ කාර්යක්ෂමව නිෂ්පාදනය කිරීම සඳහා නිරවද්යතාවය සහ ප්රවීණත්වය අවශ්ය වේ. සම්පූර්ණ සැලසුම් සහ නිෂ්පාදන ක්රියාවලියක් අනුගමනය කිරීමෙන්, නිෂ්පාදකයින්ට ඔවුන්ගේ නිෂ්පාදනවල අද්විතීය අවශ්යතා සපුරාලන අච්චු සෑදිය හැකි අතර ඔවුන්ගේ එන්නත් අච්චු සැකසීමේ ක්රියාවලීන් ප්රශස්ත කළ හැකිය.
එන්නත් මෝල්ඩින් මෙවලම් වර්ග
එන්නත් අච්චු කිරීම යනු විශාල ප්රමාණවලින් කොටස් නිෂ්පාදනය කිරීම සඳහා බහුලව භාවිතා වන නිෂ්පාදන ක්රියාවලියකි. එය අච්චු කුහරයකට උණු කළ ප්ලාස්ටික් එන්නත් කිරීම සහ එය අවශ්ය හැඩයට සිසිල් කිරීමට සහ ඝන වීමට ඉඩ සලසයි. ඉන්ජෙක්ෂන් මෝල්ඩින් ටූලින් යනු ඉන්ජෙක්ෂන් මෝල්ඩින් කිරීමේදී භාවිතා කරන අච්චු නිර්මාණය කිරීමේ ක්රියාවලියයි. ඉන්ජෙක්ෂන් මෝල්ඩින් මෙවලම් වර්ග කිහිපයක් තිබේ, ඒ සෑම එකක්ම එහි වාසි සහ අවාසි ඇත.
- ද්වි-තහඩු අච්චු ද්වි-තහඩු අච්චු යනු සරලම ආකාරයේ ඉන්ජෙක්ෂන් මෝල්ඩින් මෙවලම් වේ. ඒවා අච්චු කුහරයක් සෑදීම සඳහා එකට ගැටගැසූ තහඩු දෙකකින් සමන්විත වේ. උණු කළ ප්ලාස්ටික් ගේට්ටුවක් හරහා කුහරය තුළට එන්නත් කර සිසිල් කිරීමට සහ ඝන වීමට ඉඩ සලසයි. කොටස නිර්මාණය කළ පසු, තහඩු දෙක වෙන් කර ඇති අතර, එම මුදල පිට කරනු ලැබේ. සරල ජ්යාමිතිය සහිත කුඩා හා මධ්යම ප්රමාණයේ සංරචක සඳහා ද්වි-තහඩු අච්චු සාමාන්යයෙන් භාවිතා වේ.
- ත්රි-තහඩු අච්චු ත්රි-තහඩු අච්චු තහඩු දෙකක අච්චු වලට සමාන වේ, නමුත් ඒවාට අමතර තහඩුවක් ඇත, එය ස්ට්රිපර් ප්ලේට් ලෙස හැඳින්වේ, එය වාත්තු කරන ලද කොටස ධාවන පද්ධතියෙන් වෙන් කරයි. ධාවන පද්ධතිය යනු උණු කළ ප්ලාස්ටික් අච්චු කුහරයට ලබා දෙන නාලිකා ජාලයයි. වඩාත් වැදගත් කොටස් සහ වඩාත් සංකීර්ණ ජ්යාමිතිය සඳහා ත්රී-තහඩු අච්චු භාවිතා වේ.
- Hot Runner Moulds උණුසුම් ධාවන අච්චු වලදී, උණු කළ ප්ලාස්ටික් ගේට්ටුවක් හරහා නොව රත් වූ නාලිකා මාලාවක් හරහා අච්චු කුහරයට කෙලින්ම එන්නත් කරනු ලැබේ. මෙමගින් ධාවන පද්ධතියේ අපතේ යන ද්රව්ය අඩු කරයි, ප්රතිඵලයක් ලෙස වඩාත් කාර්යක්ෂම ක්රියාවලියක් සිදුවේ. සංකීර්ණ කොටස්වල ඉහළ පරිමාවක් නිෂ්පාදනය කිරීම සඳහා උණුසුම් ධාවන අච්චු භාවිතා වේ.
- පවුල් අච්චු පවුලේ අච්චු තනි අච්චුවක කොටස් කිහිපයක් නිෂ්පාදනය කරයි. එකවර වසම් ගණනාවක් නිෂ්පාදනය කිරීමට ඉඩ සලසන ආකාරයෙන් විවිධ කුහර සකස් කර ඇත. පවුලේ අච්චු සාමාන්යයෙන් කුඩා හා මධ්යම ප්රමාණයේ වෙළුම් සහිත කොටස් සඳහා භාවිතා වේ.
- අච්චු ඇතුල් කරන්න අච්චු ඇතුල් කරන්න ලෝහ හෝ ප්ලාස්ටික් ඇතුළු කිරීම් අවශ්ය කොටස් නිෂ්පාදනය කරයි. උණු කළ ප්ලාස්ටික් එන්නත් කිරීමට පෙර ඇතුල් කිරීම් අච්චු කුහරය තුළට දමනු ලැබේ. ප්ලාස්ටික් සිසිල් වී ඝන වීමෙන් පසු, කොටස සහ ඇතුල් කිරීම ස්ථිරවම බැඳී ඇත. ශක්තිය, කල්පැවැත්ම හෝ සෞන්දර්යාත්මක ආයාචනය අවශ්ය වන ස්ථාන සඳහා ඇතුල් කිරීමේ අච්චු භාවිතා වේ.
- Overmolding Overmolding යනු කොටසක් තවත් කොටසක් මත අච්චු කරන ක්රියාවලියකි. එය බොහෝ විට මෘදු ස්පර්ශයක් හෝ වැඩිදියුණු කළ ග්රහණයක් අවශ්ය වන ස්ථාන සඳහා භාවිතා වේ. අධි මෝල්ඩින් කිරීම යනු මුලින්ම උපස්ථරයක් හෝ පාදක කොටසක් සකස් කර පසුව එය මත දෙවන ද්රව්යයක් සැකසීමයි. දෙවන ද්රව්යය වෙනස් ප්ලාස්ටික් වර්ගයක්, රබර් වැනි ද්රව්යයක් හෝ තාප ප්ලාස්ටික් ඉලාස්ටෝමරයක් විය හැකිය.
අවසාන වශයෙන්, ඉන්ජෙක්ෂන් මෝල්ඩින් මෙවලම් තෝරාගැනීම නිෂ්පාදනය කරන කොටසේ වර්ගය, අවශ්ය නිෂ්පාදන පරිමාව සහ කොටස් නිර්මාණයට සම්බන්ධ සංකීර්ණතා මට්ටම මත රඳා පවතී. ක්රියාවලිය කාර්යක්ෂම හා ලාභදායී බව සහතික කිරීම සඳහා නිසි මෙවලම් තෝරා ගැනීම අත්යවශ්ය වේ.
ඉන්ජෙක්ෂන් මෝල්ඩින් සැලසුම් මාර්ගෝපදේශ
ඉන්ජෙක්ෂන් මෝල්ඩින් යනු ප්ලාස්ටික් කොටස් නිෂ්පාදනය සඳහා බහුලව භාවිතා වන නිෂ්පාදන ක්රියාවලියකි. ඉන්ජෙක්ෂන් මෝල්ඩින් සඳහා කොටස් සැලසුම් කිරීම, විස්තර සාර්ථකව නිෂ්පාදනය කළ හැකි බව සහතික කිරීම සඳහා අනුගමනය කළ යුතු ක්රියාවලිය, ද්රව්ය සහ සැලසුම් මාර්ගෝපදේශ පිළිබඳ හොඳ අවබෝධයක් අවශ්ය වේ. මතක තබා ගත යුතු එන්නත් අච්චු සැලසුම් මාර්ගෝපදේශ කිහිපයක් මෙන්න:
බිත්ති ඝණත්වය, එම කොටසෙහි බිත්ති ඝණත්වය ඒකාකාරී විය යුතු අතර අවශ්ය ශක්තිය සහ ක්රියාකාරීත්වය පවත්වා ගනිමින් හැකි තරම් තුනී විය යුතුය. මෙය සිසිලනය සහ චක්රීය කාලය අඩු කිරීමට උපකාරී වන අතර විකෘති වීමේ සහ ගිලී යාමේ අවදානම අවම කරයි.
Ribs සහ Bosses කොටසෙහි ශක්තිය සහ දෘඪතාව වැඩි කිරීම සඳහා ඉළ ඇට සහ ප්රධානීන් භාවිතා කළ හැකිය. ඉළ ඇට නාමික බිත්ති ඝණකමෙන් 60% ට වඩා වැඩි නොවිය යුතු අතර, ලොක්කන් නාමික බිත්ති ඝණකම මෙන් 1.5 ගුණයක් විය යුතුය.
කෙටුම්පත් කෝණය, කොටස් ඉවත් කිරීම පහසු කිරීම සහ අච්චුවට හානි වීම වැළැක්වීම සඳහා අවම වශයෙන් අංශක 1-2 ක කෙටුම්පත් කෝණයක් සියලු සිරස් මතුපිට භාවිතා කළ යුතුය.
ආතති සාන්ද්රණය වැලැක්වීම සඳහා පිරවුම් සහ Radii තියුණු කොන් සහ දාර වළක්වා ගත යුතු අතර, එය ඉරිතැලීම් හා අසාර්ථක වීමට හේතු විය හැක. ඒ වෙනුවට, ෆිලට් සහ රේඩිය ආතතිය බෙදා හැරීම සහ කොටසෙහි ශක්තිය වැඩි දියුණු කළ යුතුය.
ගේට්ටු සහ ධාවකයන් ගේට්ටු සහ ධාවකයන්ගේ පිහිටීම සහ සැලසුම හොඳ කොටසක ගුණාත්මක භාවයක් ලබා ගැනීම සඳහා ඉතා වැදගත් වේ. ඇතුල්වීම් කොටසෙහි ඝන කොටසෙහි හැකි තරම් කුඩා විය යුතුය. පීඩනය පහත වැටීම අවම කිරීම සහ ප්රවාහය උපරිම කිරීම සඳහා ධාවකයන් නිර්මාණය කළ යුතුය.
මතුපිට නිමාව යෙදුම් අවශ්යතා මත පදනම්ව කොටසෙහි මතුපිට නිමාව සඳහන් කළ යුතුය. දෘශ්ය කොටස් සඳහා ඉහළ මතුපිට නිමාවක් අවශ්ය විය හැකි අතර සැඟවුණු කොටස් සඳහා පහළ මතුපිට නිමාවක් පිළිගත හැකිය.
ද්රව්ය තෝරාගැනීම කොටස සඳහා තෝරාගත් ද්රව්ය එන්නත් කිරීම සඳහා සුදුසු විය යුතු අතර අවශ්ය යාන්ත්රික, තාප සහ රසායනික ගුණාංග සපුරාලිය යුතුය.
ඉන්ජෙක්ෂන් මෝල්ඩින් හි ද්විතියික මෙහෙයුම්
ඉන්ජෙක්ෂන් මෝල්ඩින් යනු විවිධ ප්ලාස්ටික් කොටස් නිෂ්පාදනය කිරීම සඳහා භාවිතා කරන බහුකාර්ය නිෂ්පාදන ක්රියාවලියකි. ප්රාථමික වාත්තු ක්රියාවලියට අමතරව, බොහෝ ස්ථාන වලට අපේක්ෂිත හැඩය, නිමාව හෝ ක්රියාකාරීත්වය ලබා ගැනීම සඳහා ද්විතියික මෙහෙයුම් අවශ්ය වේ. එන්නත් අච්චු ගැසීමේ දෛනික ද්විතියික මෙහෙයුම් කිහිපයක් මෙන්න:
- කප්පාදු කිරීම යනු අච්චුවෙන් පිටකිරීමෙන් පසු අච්චු කරන ලද කොටසෙන් අතිරික්ත ද්රව්ය ඉවත් කිරීමයි. මෙය සාමාන්යයෙන් සිදු කරනු ලබන්නේ ටිම් මුද්රණ යන්ත්රයක් හෝ CNC යන්ත්රයක් භාවිතා කරමිනි. කොටසෙහි අවසාන හැඩය සහ ප්රමාණය ලබා ගැනීම සඳහා බොහෝ විට කප්පාදු කිරීම අවශ්ය වේ.
- වෙල්ඩින් තාපය, පීඩනය හෝ දෙකේම එකතුවක් භාවිතා කරමින් ප්ලාස්ටික් කොටස් දෙකක් හෝ වැඩි ගණනක් ඒකාබද්ධ කරයි. මෙය බොහෝ විට තනි අච්චුවකින් නිපදවිය නොහැකි විශාල හෝ වඩාත් සංකීර්ණ ලක්ෂණ නිර්මාණය කිරීමට භාවිතා කරයි.
- අලංකාර කිරීම යනු අච්චු කරන ලද කොටසෙහි මතුපිටට දෘශ්ය හෝ ක්රියාකාරී ලක්ෂණ එකතු කිරීමේ ක්රියාවලියයි. පින්තාරු කිරීම, මුද්රණය කිරීම, ලේබල් කිරීම හෝ වයනය හෝ රටාවක් යෙදීම මෙයට ඇතුළත් විය හැකිය.
- එකලස් කිරීම යනු සම්පූර්ණ නිෂ්පාදනයක් නිර්මාණය කිරීම සඳහා කොටස් කිහිපයක් සම්බන්ධ කිරීමේ ක්රියාවලියයි. ගාංචු, ඇලවුම් හෝ වෙනත් සම්බන්ධක ශිල්පීය ක්රම භාවිතයෙන් මෙය කළ හැකිය.
- Insert Molding Insert molding යනු කලින් සාදන ලද ලෝහයක් හෝ ප්ලාස්ටික් ඇතුළු කිරීමක් වටා ප්ලාස්ටික් වාත්තු කිරීමයි. මෙය බොහෝ විට ඉහළ ශක්තියක් හෝ කල්පැවැත්මක් සහිත කොටස් නිර්මාණය කිරීමට භාවිතා කරයි.
- Overmolding Overmolding යනු කලින් සාදන ලද කොටසකට වඩා දෙවන ද්රව්යයක් අච්චු ගැසීමේ ක්රියාවලියයි. මෙය මෘදු-ස්පර්ශ මතුපිටක් එක් කිරීමට, ග්රහණය වැඩි දියුණු කිරීමට හෝ ද්වි-ස්වර හෝ බහු-ද්රව්ය කැබැල්ලක් නිර්මාණය කළ හැකිය.
- ආලේපනය එහි පෙනුම, කල්පැවැත්ම හෝ වෙනත් ගුණාංග වැඩි දියුණු කිරීම සඳහා කොටසෙහි මතුපිටට තුනී ද්රව්ය ස්ථරයක් යොදයි. මෙය ක්රෝම්, නිකල් හෝ කුඩු ආලේපන වැනි ආලේපන ඇතුළත් විය හැක.
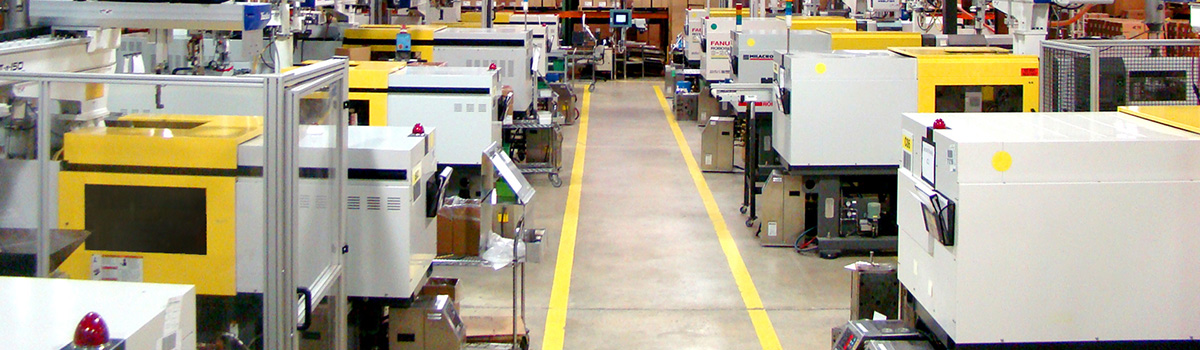
ප්ලාස්ටික් ඉන්ජෙක්ෂන් මෝල්ඩින් කිරීමේ වාසි
ප්ලාස්ටික් ඉන්ජෙක්ෂන් මෝල්ඩින් යනු ඉහළ නිරවද්යතාවයකින්, අනුකූලතාවයකින් සහ ගුණාත්මක බවකින් යුත් ප්ලාස්ටික් කොටස් නිෂ්පාදනය කිරීම සඳහා බහුලව භාවිතා වන නිෂ්පාදන ක්රියාවලියකි. එය අච්චු කුහරයකට උණු කළ ප්ලාස්ටික් එන්නත් කිරීම සහ එය සිසිල් කිරීමට සහ ඝන වීමට ඉඩ සලසයි. ප්ලාස්ටික් එන්නත් අච්චුවෙහි වාසි කිහිපයක් මෙන්න:
- ඉහළ කාර්යක්ෂමතාව සහ ඵලදායිතාව ප්ලාස්ටික් ඉන්ජෙක්ෂන් මෝල්ඩින් යනු ඉහළ අනුකූලතාවයක් සහ ගුණාත්මක භාවයක් සහිත විශාල කොටස් විශාල ප්රමාණයක් නිෂ්පාදනය කළ හැකි ඉතා කාර්යක්ෂම සහ ස්වයංක්රීය ක්රියාවලියකි. උසස් ස්වයංක්රීය තාක්ෂණය සමඟ, නිෂ්පාදන චක්ර කාලය තත්පර දක්වා අඩු කළ හැකි අතර, එමඟින් සංකීර්ණ හා සංකීර්ණ කොටස් ඉහළ පරිමාවකින් නිෂ්පාදනය කිරීමට ඉඩ සලසයි.
- අධි නිරවද්යතාවය සහ නිරවද්ය එන්නත් අච්චුව සංකීර්ණ සහ සංකීර්ණ කොටස් නිෂ්පාදනය කිරීමේදී නිරවද්යතාවය සහ නිරවද්යතාවය වැඩි කරයි. පරිගණක පාලිත යන්ත්රෝපකරණ සහ උසස් මෘදුකාංග ඉහළ පුනරාවර්තන හැකියාව සහ නිරවද්යතාවයෙන් දැඩි ඉවසීමක් සක්රීය කරයි.
- බහුකාර්යතාව එන්නත් කිරීම යනු විවිධ ප්රමාණවලින්, හැඩවලින් සහ සංකීර්ණත්වයෙන් යුත් පුළුල් පරාසයක ප්ලාස්ටික් කොටස් නිපදවිය හැකි බහුකාර්ය ක්රියාවලියකි. සංකීර්ණ විස්තර සහිත කුඩා කැබලිවල සිට සංකීර්ණ ජ්යාමිතිය සහිත විශාල ප්රමාණ දක්වා සෑම දෙයක්ම සෑදීමට ක්රියාවලිය භාවිතා කළ හැකිය.
- ද්රව්ය නම්යශීලී ඉන්ජෙක්ෂන් මෝල්ඩින් සඳහා තාප ප්ලාස්ටික්, තාප කට්ටල සහ ඉලාස්ටෝමර් ඇතුළු පුළුල් පරාසයක ප්ලාස්ටික් ද්රව්ය භාවිතා කළ හැකිය. මෙය විවිධ යාන්ත්රික, තාප සහ රසායනික ගුණ සහිත කොටස් නිෂ්පාදනය කිරීමට ඉඩ සලසයි.
- අඩු අපද්රව්ය නිෂ්පාදන එන්නත් අච්චුව නිෂ්පාදනයේදී අවම අපද්රව්ය ජනනය කරන බැවින් අඩු අපද්රව්ය නිෂ්පාදන ක්රියාවලියකි. ඕනෑම අතිරික්ත ද්රව්යයක් පහසුවෙන් ප්රතිචක්රීකරණය කර නිෂ්පාදනයේදී නැවත භාවිතා කළ හැකි අතර එය පරිසර හිතකාමී නිෂ්පාදන ක්රියාවලියක් බවට පත් කරයි.
- අඩු කරන ලද ශ්රම පිරිවැය එන්නත් අච්චු ගැසීමේ ස්වයංක්රීයකරණයේ ඉහළ මට්ටම ශ්රම-දැඩි ක්රියාවලීන්ගේ අවශ්යතාවය අවම කරයි, ශ්රම පිරිවැය සැලකිය යුතු ලෙස අඩු කරයි. මෙය අවසාන නිෂ්පාදනයේ ගුණාත්මක භාවය සහ අනුකූලතාව වැඩි දියුණු කිරීම, මානව දෝෂ ඇතිවීමේ අවදානම ද අඩු කරයි.
- අඩු කරන ලද පශ්චාත්-නිෂ්පාදන මෙහෙයුම් එන්නත් අච්චුව ඉහළ නිරවද්යතාවයකින් සහ අනුකූලතාවයකින් යුත් කොටස් නිෂ්පාදනය කරයි, කැපීම, විදීම හෝ ඇඹරීම වැනි පශ්චාත් නිෂ්පාදන මෙහෙයුම් සඳහා අවශ්යතාවය අඩු කරයි. මෙය අවසන් නිෂ්පාදනයේ නිෂ්පාදන කාලය සහ පිරිවැය අඩු කරයි.
- අනුකූලතාව සහ ගුණාත්මක එන්නත් අච්චුව ඉහළ මට්ටමේ අනුකූලතාවයක් සහ ගුණාත්මක භාවයක් සහිත කොටස් නිෂ්පාදනය කරයි. උසස් තාක්ෂණය සහ පරිගණක පාලිත යන්ත්රෝපකරණ සෑම විස්තරයක්ම හැඩයෙන්, ප්රමාණයෙන් සහ ගුණයෙන් සමාන බව සහතික කරයි.
- නිර්මාණ නම්යශීලී ඉන්ජෙක්ෂන් මෝල්ඩින් මඟින් සංකීර්ණ ජ්යාමිතීන්, යටි කැපීම් සහ සංකීර්ණ විස්තර සහිත කොටස් නිෂ්පාදනය කිරීමට ඉඩ සලසන බැවින්, ඉහළ මට්ටමේ නිර්මාණ නම්යශීලී බවක් ලබා දේ. වෙනත් නිෂ්පාදන ක්රියාවලීන් භාවිතයෙන් සෑදිය නොහැකි අද්විතීය හැඩතල සහ කාර්යයන් සහිත කොටස් නිර්මාණය කිරීමට මෙමගින් නිර්මාණකරුවන්ට හැකියාව ලැබේ.
- අධි-පරිමා නිෂ්පාදනය සඳහා පිරිවැය-ඵලදායී ඉන්ජෙක්ෂන් මෝල්ඩින් ප්ලාස්ටික් කොටස් නිෂ්පාදනය කිරීම සඳහා ලාභදායී ක්රියාවලියකි. ආරම්භක මෙවලම් පිරිවැය ඉහළ විය හැකි නමුත් නිෂ්පාදන පරිමාව වැඩි වන විට කොටසක පිරිවැය අඩු වේ. මෙය කොටස් විශාල ප්රමාණයක් නිෂ්පාදනය කිරීම සඳහා කදිම ක්රියාවලියක් බවට පත් කරයි.
ප්ලාස්ටික් ඉන්ජෙක්ෂන් මෝල්ඩින් බොහෝ වාසි ලබා දෙයි, එය ප්ලාස්ටික් කොටස් නිෂ්පාදනය සඳහා ජනප්රිය තේරීමක් කරයි. එහි ඉහළ කාර්යක්ෂමතාව, නිරවද්යතාවය, බහුකාර්යතාව, ද්රව්ය නම්යශීලී බව, අඩු අපද්රව්ය නිෂ්පාදනය, අඩු කරන ලද ශ්රම පිරිවැය සහ අනුකූලතාව සහ ගුණාත්මකභාවය විවිධ යෙදුම් සඳහා කදිම ක්රියාවලියක් බවට පත් කරයි. ඉහළ පරිමා නිෂ්පාදනය සඳහා ඉහළ නිර්මාණ නම්යශීලීභාවය සහ පිරිවැය-ඵලදායීතාවය සහිත සංකීර්ණ සහ සංකීර්ණ කොටස් නිෂ්පාදනය කිරීමේ හැකියාව එය ඉහළ ඉල්ලුමක් ඇති නිෂ්පාදන ක්රියාවලියක් බවට පත් කරයි.
ප්ලාස්ටික් ඉන්ජෙක්ෂන් මෝල්ඩින්ගේ අවාසි
ප්ලාස්ටික් ඉන්ජෙක්ෂන් මෝල්ඩින් යනු බහුලව භාවිතා වන නිෂ්පාදන ක්රියාවලියක් වන අතර එය පුළුල් පරාසයක ප්ලාස්ටික් කොටස් සහ නිෂ්පාදන නිෂ්පාදනය කිරීම සඳහා උණු කළ ප්ලාස්ටික් අච්චු කුහරයකට එන්නත් කිරීම ඇතුළත් වේ. ප්ලාස්ටික් ඉන්ජෙක්ෂන් මෝල්ඩින් බොහෝ වාසි ඇතත්, අවාසි කිහිපයක් ද ඇත. ප්ලාස්ටික් එන්නත් අච්චුවෙහි ප්රධාන අවාසි කිහිපයක් මෙන්න:
- ඉහළ මෙවලම් පිරිවැය: ප්ලාස්ටික් ඉන්ජෙක්ෂන් මෝල්ඩින් සඳහා අච්චුවක් සැලසුම් කිරීම සහ නිෂ්පාදනය කිරීමේ පිරිවැය ඉතා ඉහළ විය හැකිය. මක්නිසාද යත්, අච්චුව උසස් තත්ත්වයේ ද්රව්ය වලින් සෑදිය යුතු අතර අපේක්ෂිත කොටස නිර්මාණය කිරීම සඳහා නිශ්චිතවම යන්ත්රගත කළ යුතුය. මීට අමතරව, කුඩා පරිමාණ නිෂ්පාදන ධාවනය සඳහා අච්චුව සැලසුම් කිරීමේ සහ නිෂ්පාදනය කිරීමේ පිරිවැය තහනම් විය හැකි අතර, ප්ලාස්ටික් එන්නත් අච්චුව අඩු පරිමාවකින් නිෂ්පාදනය කිරීම සඳහා අඩු ලාභදායී වේ.
- දිගු ඊයම් කාලය: ප්ලාස්ටික් ඉන්ජෙක්ෂන් මෝල්ඩින් සඳහා අච්චුවක් සැලසුම් කිරීම සහ නිෂ්පාදනය කිරීමේ ක්රියාවලිය දිගු කාලයක් ගත විය හැකි අතර, ප්ලාස්ටික් කොටස් නිෂ්පාදනය ප්රමාද කළ හැකිය. වෙළඳපල ඉල්ලුමේ වෙනස්වීම් වලට ඉක්මනින් ප්රතිචාර දැක්වීමට හෝ නව නිෂ්පාදන වේගයෙන් සංවර්ධනය කිරීමට අවශ්ය ව්යාපාර සඳහා මෙය විශේෂයෙන් ගැටලුකාරී විය හැක.
- සීමිත නම්යශීලීභාවය: අච්චුව නිර්මාණය කර නිෂ්පාදනය කළ පසු, සැලසුම වෙනස් කිරීම හෝ නිෂ්පාදන ක්රියාවලිය වෙනස් කිරීම පහසු සහ ලාභදායී වේ. මෙය ප්ලාස්ටික් ඉන්ජෙක්ෂන් මෝල්ඩින්ගේ නම්යශීලී බව සීමා කළ හැකි අතර එය අභිරුචි හෝ එක්-ආකාරයේ නිෂ්පාදන නිෂ්පාදනය සඳහා අඩු සුදුසුකමක් බවට පත් කළ හැකිය.
- පාරිසරික ගැටළු: ප්ලාස්ටික් ඉන්ජෙක්ෂන් මෝල්ඩින් ප්ලාස්ටික් විශාල ප්රමාණයක් මත රඳා පවතී, එය අහිතකර පාරිසරික බලපෑම් ඇති කළ හැකිය. ප්ලාස්ටික් අපද්රව්ය ප්රධාන පාරිසරික ගැටළුවක් වන අතර ප්ලාස්ටික් එන්නත් අච්චු ගැසීම මෙම ගැටලුවට දායක විය හැකිය. මීට අමතරව, ප්ලාස්ටික් නිෂ්පාදන නිෂ්පාදනය කිරීමේ ක්රියාවලිය පරිසරයට තවදුරටත් බලපෑම් කළ හැකි බලශක්ති සහ ස්වභාවික සම්පත් භාවිතා කිරීම අවශ්ය වේ.
- ඉහළ සීරීම් අනුපාත: ප්ලාස්ටික් එන්නත් අච්චුවකින් සැලකිය යුතු සීරීම් ද්රව්ය නිපදවිය හැකි අතර, ඒවා බැහැර කිරීමට හෝ ප්රතිචක්රීකරණය කිරීමට මිල අධික විය හැක. මීට අමතරව, ඉවතලන ද්රව්ය නිෂ්පාදනය සමස්ත නිෂ්පාදන පිරිවැය වැඩි කිරීමට සහ නිෂ්පාදන ක්රියාවලියේ කාර්යක්ෂමතාව අඩු කිරීමට හේතු වේ.
- සීමිත ද්රව්ය විකල්ප: ප්ලාස්ටික් ඉන්ජෙක්ෂන් මෝල්ඩින් මූලික වශයෙන් භාවිතා කරනුයේ ලෝහ හෝ පිඟන් මැටි වැනි අනෙකුත් ද්රව්යවලට සාපේක්ෂව සීමිත ගුණ ඇති තාප ප්ලාස්ටික් ද්රව්ය වලින් කොටස් සහ නිෂ්පාදන නිෂ්පාදනය සඳහා ය. ඉහළ ශක්තියක්, උෂ්ණත්ව ප්රතිරෝධයක් හෝ වෙනත් උසස් ගුණාංග අවශ්ය වන යෙදුම් සඳහා මෙය ප්ලාස්ටික් ඉන්ජෙක්ෂන් මෝල්ඩින් අඩු සුදුසුකමක් බවට පත් කළ හැකිය.
ප්ලාස්ටික් ඉන්ජෙක්ෂන් මෝල්ඩින් වල සීමාවන්
ප්ලාස්ටික් ඉන්ජෙක්ෂන් මෝල්ඩින් බොහෝ වාසි ලබා දෙන අතර, ඇතැම් සීමාවන් ද ක්රියාවලිය සමඟ සම්බන්ධ වේ. ප්ලාස්ටික් එන්නත් අච්චු ගැසීමේ සීමාවන් කිහිපයක් මෙන්න:
ඉහළ ආරම්භක මෙවලම් පිරිවැය: අච්චුව සැලසුම් කිරීම සහ නිෂ්පාදනය කිරීමේ මූලික පිරිවැය වැඩි කළ හැක. පුනරාවර්තන එන්නත් අච්චු ගැසීමේ ක්රියාවලියට ඔරොත්තු දීම සඳහා අච්චුව නිරවද්ය සහ කල් පවතින ඒවා විය යුතු අතර, මෙය විශේෂයෙන් සංකීර්ණ හෝ විශාල අච්චු සඳහා සැලකිය යුතු පෙර ආයෝජනයක් අවශ්ය වේ.
ඊයම් කාලය: අච්චුව නිෂ්පාදනය කිරීම සඳහා ගතවන කාලය සැලකිය යුතු විය හැකිය, අච්චුවේ සංකීර්ණත්වය සහ ප්රමාණය අනුව සති සිට මාස දක්වා. මෙය විශේෂයෙන් කාල සංවේදී ව්යාපෘති සඳහා නිෂ්පාදන කාලරාමුවෙහි ප්රමාදයන් ඇති කළ හැක.
සැලසුම් සීමාවන්: ඉන්ජෙක්ෂන් මෝල්ඩින් සලකා බැලිය යුතු ඇතැම් සැලසුම් සීමාවන් ඇත. නිදසුනක් ලෙස, නිසි පිරවීම සහ සිසිලනය සහතික කිරීම සඳහා කොටස පුරා ඒකාකාර බිත්ති ඝණත්වය ලබා ගැනීම ඉතා වැදගත් වේ. අතිරේකව, අච්චුවෙන් පහසුවෙන් පිට කිරීම සක්රීය කිරීම සඳහා සිරස් පෘෂ්ඨ මත කෙටුම්පත් කෝණ අවශ්ය වේ.
කොටස් ප්රමාණයේ සීමාවන්: කුඩා හා මධ්යම ප්රමාණයේ කොටස් නිෂ්පාදනය කිරීම සඳහා එන්නත් අච්චුව වඩාත් සුදුසු වේ. විශාල කොටස් සඳහා විශේෂිත උපකරණ සහ විශාල අච්චු අවශ්ය විය හැකිය, පිරිවැය සහ සංකීර්ණත්වය එකතු කිරීම.
ද්රව්ය තෝරාගැනීම: ඉන්ජෙක්ෂන් මෝල්ඩින් ප්ලාස්ටික් ද්රව්ය සඳහා පුළුල් පරාසයක ඉඩ ලබා දෙන අතර, අනෙකුත් නිෂ්පාදන ක්රියාවලියට සාපේක්ෂව ද්රව්ය තෝරාගැනීම තවමත් සීමා වේ. ඉහළ ද්රවාංක හෝ දුර්වල ප්රවාහ ලක්ෂණ සහිත ද්රව්ය එන්නත් අච්චු කිරීම සඳහා සුදුසු නොවේ.
මතුපිට නිමාව: ඉන්ජෙක්ෂන් මෝල්ඩින් ක්රියාවලියේ ප්රතිඵලයක් ලෙස කොටසේ මතුපිට පෙනෙන ගෙතුම් රේඛා හෝ වෙන්වීමේ රේඛා ඇති විය හැක. උසස් තත්ත්වයේ මතුපිට නිමාවක් ලබා ගැනීම අභියෝගාත්මක විය හැකි අතර, ඔප දැමීම හෝ ආලේපනය වැනි වෙනත් ක්රම අවශ්ය විය හැකිය.
සීමිත යටි කැපීම්: යටි කැපීම යනු අච්චුවෙන් පහසුවෙන් ඉවත් කිරීම වළක්වන කොටසක ලක්ෂණ හෝ විස්තර වේ. යටි කැපීම් මගින් පිටකිරීමේ ක්රියාවලිය සංකීර්ණ කළ හැකි අතර අපේක්ෂිත කොටස ජ්යාමිතිය සාක්ෂාත් කර ගැනීම සඳහා අමතර අච්චු විශේෂාංග හෝ ද්විතියික මෙහෙයුම් අවශ්ය වේ.
සීමිත අළුත්වැඩියා විකල්ප: අච්චුවකට හානි සිදුවුවහොත් හෝ වෙනස් කිරීමක් අවශ්ය නම්, පවතින අච්චුව අලුත්වැඩියා කිරීමට හෝ වෙනස් කිරීමට එය මිල අධික හා කාලය ගත විය හැකිය. සමහර විට, සම්පූර්ණයෙන්ම නව අච්චුවක් නිෂ්පාදනය කිරීමට අවශ්ය විය හැකිය, අතිරේක වියදම් සහ ප්රමාදයන් ඇති කරයි.
මෙම සීමාවන් තිබියදීත්, ප්ලාස්ටික් ඉන්ජෙක්ෂන් මෝල්ඩින් ප්ලාස්ටික් කොටස් නිෂ්පාදනය සඳහා ඉතා බහුකාර්ය සහ බහුලව භාවිතා වන නිෂ්පාදන ක්රියාවලියක් ලෙස පවතී. සැලසුම් සහ නිෂ්පාදන සැලසුම් අදියර තුළ මෙම සීමාවන් ප්රවේශමෙන් සලකා බැලීමෙන්, ඒවායේ බලපෑම අවම කර ගැනීමටත්, ඉන්ජෙක්ෂන් මෝල්ඩින් වල වාසි ඵලදායී ලෙස භාවිතා කිරීමටත් හැකි වේ.
ප්ලාස්ටික් ඉන්ජෙක්ෂන් මෝල්ඩින්ගේ යෙදුම්
ප්ලාස්ටික් ඉන්ජෙක්ෂන් මෝල්ඩින් යනු පුළුල් පරාසයක ප්ලාස්ටික් කොටස් නිෂ්පාදනය කළ හැකි බහුකාර්ය නිෂ්පාදන ක්රියාවලියකි. ප්ලාස්ටික් එන්නත් අච්චු ගැසීමේ යෙදුම් කිහිපයක් මෙන්න:
- පාරිභෝගික නිෂ්පාදන: සෙල්ලම් බඩු, මුළුතැන්ගෙයි උපකරණ සහ ඉලෙක්ට්රොනික උපකරණ වැනි විවිධ නිෂ්පාදන නිෂ්පාදනය කිරීමට එන්නත් අච්චුව බහුලව භාවිතා වේ. මෙම ක්රියාවලියට සංකීර්ණ ජ්යාමිතිය සහ නිරවද්ය මානයන් සහිත උසස් තත්ත්වයේ කොටස් නිපදවිය හැකි අතර, දැඩි ඉවසීම් සහ සංකීර්ණ හැඩතල අවශ්ය නිෂ්පාදන සඳහා එය වඩාත් සුදුසු වේ.
- මෝටර් රථ අමතර කොටස්: උපකරණ පුවරු සංරචක, දොර හැසිරවීම් සහ ආලෝකය වැනි බොහෝ මෝටර් රථ ප්ලාස්ටික් සංරචක, එන්නත් අච්චුව භාවිතයෙන් නිෂ්පාදනය කෙරේ. මෙම ක්රියාවලිය ඉහළ නිෂ්පාදන පරිමාවන් සහ ස්ථාවර ගුණාත්මක භාවය සඳහා ඉඩ සලසයි, එය මෝටර් රථ නිෂ්පාදකයින් සඳහා ලාභදායී විකල්පයක් බවට පත් කරයි.
- වෛද්ය උපකරණ: එන්නත් අච්චු ගැසීම සාමාන්යයෙන් සිරින්ජ, ආශ්වාස කරන්නන් සහ රෝග විනිශ්චය උපකරණ වැනි වෛද්ය උපකරණ නිෂ්පාදනය කිරීමට භාවිතා කරයි. මෙම ක්රියාවලිය උපාංගවල ගුණාත්මකභාවය සහ විශ්වසනීයත්වය සහතික කිරීම, ඉහළ නිරවද්යතාවයකින් සහ අනුකූලතාවයකින් යුත් කොටස් නිෂ්පාදනය කළ හැකිය.
- ඇසුරුම්කරණය: බහාලුම්, පියන සහ තොප්පි වැනි ප්ලාස්ටික් ඇසුරුම් නිෂ්පාදනය කිරීම සඳහා එන්නත් අච්චුව බහුලව භාවිතා වේ. මෙම ක්රියාවලිය ස්ථාවර මානයන් සහ උසස් තත්ත්වයේ නිමාවකින් යුත් කොටස් තිබිය හැකි අතර, එය ආකර්ෂණීය පෙනුමක් සහ ආරක්ෂිතව ගැලපෙන ඇසුරුම් කිරීම සඳහා සුදුසු වේ.
- අභ්යවකාශය සහ ආරක්ෂාව: ඉන්ජෙක්ෂන් මෝල්ඩින් ගුවන් යානා අභ්යන්තරය, ආලෝකකරණය සහ සන්නිවේදන පද්ධති වැනි විවිධ අභ්යවකාශ සහ ආරක්ෂක සංරචක නිෂ්පාදනය කරයි. ක්රියාවලියට සැහැල්ලු, කල් පවතින ද්රව්ය සහිත කොටස් තිබිය හැකි අතර, ඒවා ඉහළ ශක්තියට බර අනුපාත අවශ්ය වන යෙදුම් සඳහා සුදුසු වේ.
- ඉදිකිරීම්: ඉන්ජෙක්ෂන් මෝල්ඩින් ප්ලාස්ටික් උළු, සෙවිලි, සහ පැති වැනි විවිධ ඉදිකිරීම් ද්රව්ය නිෂ්පාදනය කළ හැක. මෙම ක්රියාවලිය ස්ථාවර මානයන් සහ උසස් තත්ත්වයේ නිමාවකින් යුත් කොටස් තිබිය හැකි අතර, එය ඉදිකිරීම් සමාගම් සඳහා ආකර්ෂණීය විකල්පයකි.
- ක්රීඩා සහ විනෝදාස්වාදය: ගොල්ෆ් ක්ලබ්, ටෙනිස් ජාවාරම් සහ බයිසිකල් උපාංග වැනි ක්රීඩා උපකරණ නිෂ්පාදනය කිරීමේදී එන්නත් අච්චුව බහුලව භාවිතා වේ. මෙම ක්රියාවලිය මඟින් උපකරණවල ක්රියාකාරීත්වය සහ කල්පැවැත්ම සහතික කරමින් සැහැල්ලු ද්රව්ය සහ නිරවද්ය ජ්යාමිතිය සහිත කොටස් නිපදවිය හැක.
සමස්තයක් වශයෙන්, ප්ලාස්ටික් ඉන්ජෙක්ෂන් මෝල්ඩින් යනු විවිධ යෙදුම් සඳහා උසස් තත්ත්වයේ ප්ලාස්ටික් කොටස් නිෂ්පාදනය කළ හැකි බහුකාර්ය සහ බහුලව භාවිතා වන නිෂ්පාදන ක්රියාවලියකි. නිශ්චිත සැලසුම් සහ නිෂ්පාදන අවශ්යතා සපුරාලීම සඳහා ක්රියාවලිය සකස් කළ හැකි අතර, එය විවිධ කර්මාන්තවල නිෂ්පාදකයින් සඳහා ආකර්ශනීය විකල්පයක් බවට පත් කරයි.
මෝටර් රථ කර්මාන්තය සහ ප්ලාස්ටික් ඉන්ජෙක්ෂන් මෝල්ඩින්
මෝටර් රථ කර්මාන්තය ප්ලාස්ටික් ඉන්ජෙක්ෂන් මෝල්ඩින් තාක්ෂණයේ සැලකිය යුතු පරිශීලකයෙකි. ප්ලාස්ටික් ඉන්ජෙක්ෂන් මෝල්ඩින් කිරීමේ ක්රියාවලිය මෝටර් රථ අමතර කොටස් සහ සංරචක නිෂ්පාදනයේ විප්ලවීය වෙනසක් ඇති කර ඇති අතර එමඟින් ඉහළ නිරවද්යතාවයකින් සහ නිරවද්යතාවයකින් සංකීර්ණ හැඩයන් නිෂ්පාදනය කිරීමට හැකි වේ. මෝටර් රථ කර්මාන්තයේ ප්ලාස්ටික් ඉන්ජෙක්ෂන් මෝල්ඩින් භාවිතා කරන ක්රම කිහිපයක් මෙන්න:
- අභ්යන්තර කොටස්: ප්ලාස්ටික් ඉන්ජෙක්ෂන් මෝල්ඩින් උපකරණ පුවරු සංරචක, දොර පැනල්, ටිම් කෑලි සහ තවත් බොහෝ අභ්යන්තර සාධක නිෂ්පාදනය කරයි. මෙම කොටස් සංකීර්ණ හැඩතල සහ වයනය සමඟ නිර්මාණය කළ හැකි අතර එක් එක් වාහන මාදිලියේ ශෛලිය හා ක්රියාකාරී අවශ්යතාවලට ගැලපෙන පරිදි සකස් කළ හැක.
- බාහිර කොටස්: ප්ලාස්ටික් ඉන්ජෙක්ෂන් මෝල්ඩින් බම්පර්, ග්රිල්, පැති දර්පණ සහ තවත් බොහෝ බාහිර අංග නිෂ්පාදනය කිරීමට ද භාවිතා කරයි. මෙම කොටස් ආන්තික කාලගුණික තත්ත්වයන්ට ඔරොත්තු දෙන පරිදි නිර්මාණය කළ හැකි අතර විවිධ වර්ණවලින් සහ නිමාවකින් සාදා ඇත.
- යට-හූඩ් සංරචක: ප්ලාස්ටික් ඉන්ජෙක්ෂන් මෝල්ඩින් එන්ජින් ආවරණ, වාතය ලබා ගැනීමේ පද්ධති සහ සිසිලන පද්ධති කොටස් ඇතුළුව බොහෝ යට-හූඩ් විශේෂාංග නිෂ්පාදනය කරයි. මෙම සංරචක තාප ප්ලාස්ටික් ද්රව්ය සමඟ ලබා ගත හැකි ඉහළ උෂ්ණත්වය සහ රසායනික ප්රතිරෝධය අවශ්ය වේ.
- විද්යුත් සහ ඉලෙක්ට්රොනික සංරචක: ප්ලාස්ටික් ඉන්ජෙක්ෂන් මෝල්ඩින් සම්බන්ධක, නිවාස සහ සංවේදක ඇතුළු විවිධ විද්යුත් සහ ඉලෙක්ට්රොනික උපාංග නිෂ්පාදනය කරයි. මෙම සංරචක සඳහා ඉහළ නිරවද්යතාවයක් සහ විශ්වසනීයත්වයක් අවශ්ය වන අතර, ප්ලාස්ටික් ඉන්ජෙක්ෂන් මෝල්ඩින්ගේ නිරවද්යතාව සහ අනුකූලතාවයෙන් ලබා ගත හැකිය.
- සැහැල්ලු කිරීම: ප්ලාස්ටික් ඉන්ජෙක්ෂන් මෝල්ඩින් බොහෝ විට වාහනයක සමස්ත බර අඩු කිරීමට, ඉන්ධන කාර්යක්ෂමතාව වැඩි කිරීමට සහ විමෝචනය අඩු කිරීමට උපකාරී වන සැහැල්ලු කොටස් නිෂ්පාදනය කිරීමට භාවිතා කරයි. සැහැල්ලු බරින් වාහනයක හැසිරවීම සහ කාර්ය සාධනය වැඩිදියුණු කළ හැකිය.
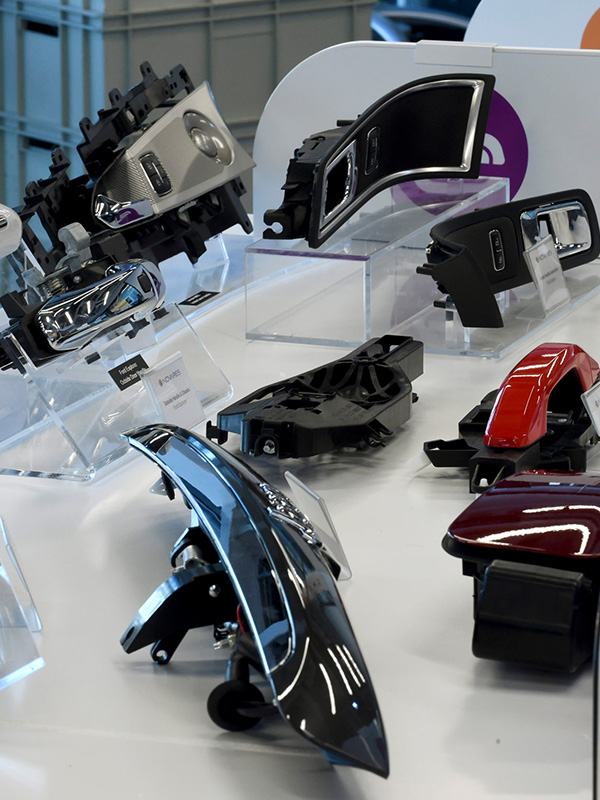
වෛද්ය කර්මාන්තය සහ ප්ලාස්ටික් එන්නත් අච්චු ගැසීම
විවිධ වෛද්ය උපකරණ සහ සංරචක නිෂ්පාදනය කිරීම සඳහා වෛද්ය කර්මාන්තයේ ප්ලාස්ටික් එන්නත් අච්චුව බහුලව භාවිතා වේ. ප්ලාස්ටික් එන්නත් අච්චු ගැසීමේ ක්රියාවලිය ඉහළ නිරවද්යතාවයකින් සහ නිරවද්යතාවයකින් සංකීර්ණ හැඩතල නිෂ්පාදනය කිරීමට ඉඩ සලසයි, එය බොහෝ වෛද්ය යෙදුම් සඳහා කදිම නිෂ්පාදන ක්රමයක් බවට පත් කරයි. වෛද්ය කර්මාන්තයේ ප්ලාස්ටික් එන්නත් අච්චුව භාවිතා කරන ක්රම කිහිපයක් මෙන්න:
- වෛද්ය උපකරණ: ප්ලාස්ටික් එන්නත් අච්චුව ශල්ය උපකරණ, රෝග විනිශ්චය මෙවලම්, ඖෂධ බෙදා හැරීමේ පද්ධති ඇතුළු විවිධ වෛද්ය උපකරණ නිෂ්පාදනය කරයි. මෙම උපාංගවලට බොහෝ විට ඉහළ නිරවද්යතාවයක් සහ නිරවද්යතාවයක් අවශ්ය වන අතර ප්ලාස්ටික් එන්නත් අච්චුව මෙම අවශ්යතා සපුරාලිය හැකිය.
- බද්ධ කිරීම්: සන්ධි ප්රතිස්ථාපන, දන්ත බද්ධ කිරීම් සහ තවත් බොහෝ දේ ඇතුළුව විවිධ බද්ධ කිරීම් නිෂ්පාදනය කිරීමට ප්ලාස්ටික් එන්නත් අච්චුව භාවිතා කරයි. මෙම බද්ධ කිරීම් රෝගියාගේ ව්යුහ විද්යාවට ගැලපෙන පරිදි නිර්මාණය කර ජෛව අනුකූල ද්රව්ය සමඟ නිෂ්පාදනය කළ හැකිය.
- රසායනාගාර උපකරණ: ප්ලාස්ටික් එන්නත් අච්චුව පයිප්ප, ක්ෂුද්ර තහඩු සහ පරීක්ෂණ නල නිෂ්පාදනය කරයි. විශ්වසනීය ප්රතිඵල සහතික කිරීම සඳහා මෙම සංරචක සඳහා ඉහළ නිරවද්යතාවයක් සහ නිරවද්යතාවක් අවශ්ය වේ.
- ඇසුරුම්කරණය: වඳ බාධක පද්ධති සහ තනි නිෂ්පාදන සඳහා අභිරුචි ඇසුරුම් ඇතුළුව වෛද්ය උපාංග සඳහා ඇසුරුම් නිෂ්පාදනය කිරීමට ප්ලාස්ටික් එන්නත් අච්චුව භාවිතා කරයි. මෙම ඇසුරුම් විසඳුම් මගින් වෛද්ය උපාංගයේ වඳභාවය සහ අඛණ්ඩතාව පවත්වා ගැනීමට උපකාරී වේ.
- තනි භාවිත උපාංග: ප්ලාස්ටික් එන්නත් අච්චුව බොහෝ විට සිරින්ජ, ඉඳිකටු සහ කැතීටර් වැනි තනි භාවිත උපාංග නිෂ්පාදනය කරයි. මෙම උපකරණ අඩු වියදමකින් ඉහළ පරිමාවකින් සෑදිය හැකි අතර සෞඛ්ය ආරක්ෂණ සැකසුම් තුළ ආසාදන පැතිරීම වැළැක්වීමට උපකාරී වේ.
පාරිභෝගික නිෂ්පාදන සහ ප්ලාස්ටික් එන්නත් මෝල්ඩින්
ප්ලාස්ටික් ඉන්ජෙක්ෂන් මෝල්ඩින් එහි බහුකාර්යතාව, කාර්යක්ෂමතාව සහ පිරිවැය-ඵලදායීතාවය හේතුවෙන් පාරිභෝගික නිෂ්පාදන නිෂ්පාදනය සඳහා බහුලව භාවිතා වේ. ප්ලාස්ටික් එන්නත් අච්චු ගැසීමේ ක්රියාවලිය ඉහළ නිරවද්යතාවයකින් සහ නිරවද්යතාවයකින් සංකීර්ණ හැඩතල නිෂ්පාදනය කිරීමට ඉඩ සලසයි, එය බොහෝ පාරිභෝගික යෙදුම් සඳහා කදිම නිෂ්පාදන ක්රමයක් බවට පත් කරයි. පාරිභෝගික නිෂ්පාදන නිෂ්පාදනයේදී ප්ලාස්ටික් එන්නත් අච්චු භාවිතා කරන ක්රම කිහිපයක් මෙන්න:
- සෙල්ලම් බඩු: ප්ලාස්ටික් එන්නත් අච්චුව කුඩා රූපවල සිට විශාල සෙල්ලම් කට්ටල දක්වා පුළුල් පරාසයක සෙල්ලම් බඩු නිෂ්පාදනය කරයි. මෙම ක්රියාවලිය සංකීර්ණ මෝස්තර සහ විස්තර නිර්මාණය කිරීමට සහ විවිධ වර්ණ හා ද්රව්ය වලින් සෙල්ලම් බඩු සෑදීමට ඉඩ සලසයි.
- ගෘහ භාණ්ඩ: ප්ලාස්ටික් එන්නත් අච්චුව කුස්සියට උපකරණ, ගබඩා බහාලුම් සහ පිරිසිදු කිරීමේ සැපයුම් ඇතුළු විවිධ ගෘහ භාණ්ඩ නිෂ්පාදනය කරයි. මෙම නිෂ්පාදන කල් පවතින, සැහැල්ලු සහ භාවිතයට පහසු වන පරිදි නිර්මාණය කළ හැකිය.
- ඉලෙක්ට්රොනික: ප්ලාස්ටික් ඉන්ජෙක්ෂන් මෝල්ඩින් පරිගණක නිවාස, දුරකථන ආවරණ සහ චාජර් ඇතුළු බොහෝ ඉලෙක්ට්රොනික උපාංග නිෂ්පාදනය කරයි. ක්රියාවලියේ නිරවද්යතාවය සහ නිරවද්යතාවය මෙම සංරචක ඉහළ මට්ටමේ අනුකූලතාවයකින් සහ විශ්වසනීයත්වයකින් සාදා ඇති බව සහතික කරයි.
- පුද්ගලික සත්කාර නිෂ්පාදන: ප්ලාස්ටික් ඉන්ජෙක්ෂන් මෝල්ඩින් දත් බුරුසු, රේසර් සහ හිසකෙස් බුරුසු ඇතුළු අද්විතීය සත්කාර නිෂ්පාදන නිෂ්පාදනය කරයි. මෙම නිෂ්පාදන භාවිතයේ පහසුව සහ ආරක්ෂාව සහතික කිරීම සඳහා ඉහළ නිරවද්යතාවයක් සහ නිරවද්යතාවයක් අවශ්ය වේ.
- වාහන උපාංග: ප්ලාස්ටික් ඉන්ජෙක්ෂන් මෝල්ඩින් මඟින් උපකරණ පුවරු සංරචක, කෝප්ප රඳවනයන් සහ තවත් දේ ඇතුළුව මෝටර් රථ උපාංග මාලාවක් නිෂ්පාදනය කරයි. මෙම සංරචක සැහැල්ලු, කල් පවතින, සහ දෛනික භාවිතයේ දිරාපත්වීමට ඔරොත්තු දෙන ලෙස නිර්මාණය කළ හැකිය.
ප්ලාස්ටික් එන්නත් අච්චු ගැසීමේදී පාරිසරික සලකා බැලීම්
ප්ලාස්ටික් ඉන්ජෙක්ෂන් මෝල්ඩින් යනු බහුලව භාවිතා වන නිෂ්පාදන ක්රියාවලියක් වන නමුත් සැලකිය යුතු පාරිසරික ඇඟවුම් ඇත. ප්ලාස්ටික් එන්නත් අච්චු ගැසීමේදී පාරිසරික කරුණු කිහිපයක් මෙන්න:
- ද්රව්ය තෝරාගැනීම: ඉන්ජෙක්ෂන් මෝල්ඩින් සඳහා භාවිතා කරන ප්ලාස්ටික් ද්රව්ය තෝරාගැනීම පරිසරයට සැලකිය යුතු ලෙස බලපෑ හැකිය. සමහර ද්රව්ය ජෛව හායනයට ලක්විය හැකි හෝ ප්රතිචක්රීකරණය කළ හැකි වන අතර අනෙක් ඒවා එසේ නොවේ. ජෛව හායනයට ලක්විය හැකි හෝ ප්රතිචක්රීකරණය කළ හැකි ද්රව්ය භාවිතා කිරීමෙන් ප්ලාස්ටික් එන්නත් අච්චු ගැසීමේ පාරිසරික බලපෑම අවම කර ගත හැක.
- බලශක්ති පරිභෝජනය: ප්ලාස්ටික් ඉන්ජෙක්ෂන් මෝල්ඩින් ප්ලාස්ටික් උණු කිරීම සහ අච්චුව තුළට එන්නත් කිරීම සඳහා සැලකිය යුතු ශක්තියක් අවශ්ය වේ. විදුලි යන්ත්ර සහ සංවෘත ලූප පද්ධති වැනි බලශක්ති කාර්යක්ෂම උපකරණ සහ ක්රියාවලීන් බලශක්ති පරිභෝජනය සහ පාරිසරික බලපෑම අඩු කළ හැකිය.
- අපද්රව්ය කළමනාකරණය: ප්ලාස්ටික් එන්නත් අච්චු ගැසීම අතිරික්ත ද්රව්ය, දෝෂ සහිත කොටස් සහ ඇසුරුම් වලින් අපද්රව්ය ජනනය කරයි. අපද්රව්ය ප්රතිචක්රීකරණය කිරීම සහ නැවත භාවිතා කිරීම වැනි නිසි අපද්රව්ය කළමනාකරණ පිළිවෙත් ප්ලාස්ටික් එන්නත් අච්චු ගැසීමේ පාරිසරික බලපෑම අවම කිරීමට උපකාරී වේ.
- රසායනික භාවිතය: පුස් මුදා හැරීමේ කාරක සහ පිරිසිදු කිරීමේ ද්රාවක වැනි ප්ලාස්ටික් එන්නත් අච්චු වල ඇති සමහර රසායනික ද්රව්ය පරිසරයට හානි කළ හැකිය. පරිසර හිතකාමී විකල්ප භාවිතා කිරීම හෝ මෙම රසායනික ද්රව්ය භාවිතය අවම කිරීම පාරිසරික බලපෑම අවම කර ගැනීමට උපකාරී වේ.
- ජීවිතයේ අවසානය සලකා බැලීම්: ඉන්ජෙක්ෂන් මෝල්ඩින් මගින් නිපදවන ප්ලාස්ටික් නිෂ්පාදන බොහෝ විට අවසන් වන්නේ කුණු ගොඩවල්වල වන අතර එය දිරාපත් වීමට වසර සිය ගණනක් ගත විය හැකිය. ප්රතිචක්රීකරණය හෝ ජෛව හායනය සඳහා නිෂ්පාදන සැලසුම් කිරීම ප්ලාස්ටික් එන්නත් අච්චුවේ පාරිසරික බලපෑම අඩු කළ හැකිය.
ප්ලාස්ටික් ඉන්ජෙක්ෂන් මෝල්ඩින් අනාගතය
තාක්ෂණයේ සහ ද්රව්යවල දියුණුව ක්රියාවලිය වඩාත් කාර්යක්ෂම, පිරිවැය-ඵලදායී සහ තිරසාර බවට පත් කිරීමට අපේක්ෂා කරන බැවින්, ප්ලාස්ටික් ඉන්ජෙක්ෂන් මෝල්ඩින්ගේ අනාගතය යහපත් බව පෙනේ. ප්ලාස්ටික් එන්නත් අච්චු ගැසීමේ අනාගතය හැඩගස්වා ගැනීමට ඉඩ ඇති ප්රවණතා සහ වර්ධනයන් කිහිපයක් මෙන්න:
- ආකලන නිෂ්පාදනය: ත්රිමාණ මුද්රණය ලෙසද හැඳින්වෙන ආකලන නිෂ්පාදනය, ප්ලාස්ටික් එන්නත් අච්චුව පරිවර්තනය කළ හැකි නැගී එන තාක්ෂණයකි. අච්චු නිර්මාණය කිරීම සඳහා ත්රිමාණ මුද්රණය භාවිතා කිරීමෙන්, නිෂ්පාදකයින්ට සම්ප්රදායික අච්චු සෑදීමේ ක්රම හා සම්බන්ධ කාලය සහ පිරිවැය සැලකිය යුතු ලෙස අඩු කළ හැකිය.
- ස්මාර්ට් නිෂ්පාදනය: ස්වයංක්රීයකරණය, දත්ත විශ්ලේෂණ සහ යන්ත්ර ඉගෙනීම ඇතුළත් වන ස්මාර්ට් නිෂ්පාදනය, ප්ලාස්ටික් එන්නත් අච්චු ගැසීමේ විප්ලවීය වෙනසක් සිදු කරනු ඇතැයි අපේක්ෂා කෙරේ. ක්රියාවලි ප්රශස්ත කිරීම සඳහා සංවේදක සහ දත්ත විශ්ලේෂණ භාවිතා කිරීමෙන් නිෂ්පාදකයින්ට කාර්යක්ෂමතාව වැඩි දියුණු කිරීමට, නාස්තිය අඩු කිරීමට සහ ඵලදායිතාව වැඩි කිරීමට හැකිය.
- තිරසාර ද්රව්ය: ජෛව ප්ලාස්ටික් සහ ප්රතිචක්රීකරණය කරන ලද ප්ලාස්ටික් වැනි තිරසාර ද්රව්ය ප්ලාස්ටික් එන්නත් අච්චු කර්මාන්තයේ වැඩි වැඩියෙන් ජනප්රිය වෙමින් පවතී. මෙම ද්රව්ය පාරිසරික ප්රතිලාභ ලබා දෙන අතර තිරසාර ඉලක්ක සපුරා ගැනීමට නිෂ්පාදකයින්ට උපකාර කළ හැකිය.
- මයික්රෝ මෝල්ඩින්: ඉහළ නිරවද්යතාවයකින් කුඩා කොටස් නිෂ්පාදනය කිරීම ඇතුළත් වන ක්ෂුද්ර අච්චුව සෞඛ්ය ආරක්ෂණ සහ ඉලෙක්ට්රොනික උපකරණ වැනි කර්මාන්තවල වඩාත් තීරණාත්මක වෙමින් පවතී. තාක්ෂණයේ සහ ද්රව්යවල දියුණුව ක්ෂුද්ර මෝල්ඩින් වඩාත් ප්රවේශ විය හැකි සහ ලාභදායී කිරීමට බලාපොරොත්තු වේ.
- අභිරුචිකරණය: පාරිභෝගිකයින් වඩාත් පුද්ගලාරෝපිත නිෂ්පාදන ඉල්ලා සිටින බැවින්, ප්ලාස්ටික් එන්නත් අච්චුව වඩාත් නම්යශීලී සහ අභිරුචිකරණය කිරීමට අපේක්ෂා කෙරේ. තත්ය කාලීන ප්රතිපෝෂණ සහ යන්ත්ර ඉගෙනීම වැනි තාක්ෂණයේ දියුණුව, ඉක්මනින් සහ කාර්යක්ෂමව අභිරුචි නිෂ්පාදන නිෂ්පාදනය කිරීමට නිෂ්පාදකයින්ට හැකි වේ.
නිගමනය:
ප්ලාස්ටික් ඉන්ජෙක්ෂන් මෝල්ඩින් යනු පුළුල් පරාසයක නිෂ්පාදන නිෂ්පාදනයේ විප්ලවීය වෙනසක් ඇති කළ ඉතා බහුකාර්ය සහ කාර්යක්ෂම නිෂ්පාදන ක්රියාවලියකි. වෛද්ය උපකරණවල සිට මෝටර් රථ උපාංග දක්වා, ප්ලාස්ටික් එන්නත් අච්චුව ඉහළ නිෂ්පාදන අනුපාත, සැලසුම් නම්යශීලීභාවය සහ පිරිවැය-ඵලදායීතාවය ඇතුළු අනෙකුත් නිෂ්පාදන ක්රියාවලීන්ට වඩා බොහෝ වාසි ලබා දෙයි. තාක්ෂණයේ සහ ද්රව්යවල අඛණ්ඩ දියුණුවත් සමඟ, ප්ලාස්ටික් එන්නත් අච්චු ගැසීමේ අනාගතය දීප්තිමත් වන අතර, මෙම ක්රියාවලිය ඉදිරි වසරවලදී නිෂ්පාදන කර්මාන්තයේ ඊටත් වඩා වැදගත් කාර්යභාරයක් ඉටු කරනු ඇත.