එන්නත් අච්චු ගැසීමේ පොදු අච්චු දෝෂ සඳහා විසඳුම්
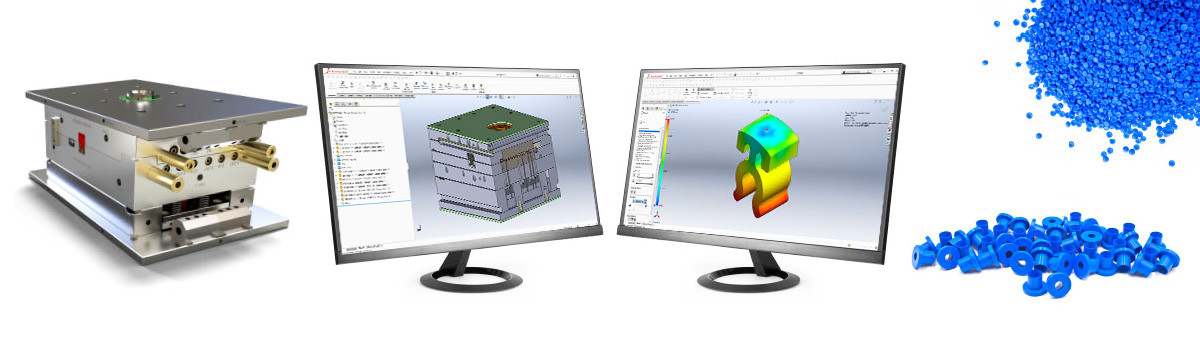
ප්ලාස්ටික් ඉන්ජෙක්ෂන් මෝල්ඩින් කොටස් සැකසීමට අච්චු භාවිතා කරන විට දෝෂ බහුලව දක්නට ලැබෙන අතර මෙය බොහෝ දුරට සැකසුම් කාර්යක්ෂමතාවයට බලපායි. ප්ලාස්ටික් එන්නත් අච්චු කොටස් සඳහා පොදු අච්චු දෝෂ සහ විසඳුම් පහත දැක්වේ.
කෙටි පහරවල්
අච්චු සම්පූර්ණයෙන් පුරවා නොතිබීම නිසා සාදන ලද නිෂ්පාදන අසම්පූර්ණ බව කෙටි වෙඩි තැබීම් සඳහන් කරයි.
මෙම දෝෂය සාමාන්යයෙන් පෙනෙන්නේ ගේට්ටුවෙන් දුරස්ථම ස්ථානයේ හෝ අච්චුවේ ඇති පටු ප්රදේශ හරහා පමණක් ළඟා විය හැකි කොටස්වල පටු ප්රදේශ දියවීමේ ප්රවාහයට බලපාන බැවිනි.
කෙටි වෙඩි තැබීම ක්ෂුද්ර ප්රවාහ සලකුණු ඇති කිරීමට හෝ නිෂ්පාදනයේ විශාල කොටසක් පැහැදිලිවම අතුරුදහන් වීමට හේතු විය හැක.
හේතුව:
කෙටි වෙඩි තැබීම් සඳහා හේතු ඇතුළත් වේ:
අච්චුව තුළට එන්නත් කරන ලද අමුද්රව්ය ප්රමාණවත් නොවේ.
දියවීමේ ප්රතිරෝධය විශාල වන අතර එහි ප්රතිඵලයක් ලෙස අච්චුව සම්පූර්ණයෙන්ම පිරවිය නොහැක.
අච්චුවේ වාතාශ්රය දුර්වල වන අතර දියවීම අවහිර කරන කුහර ජනනය වීමට හේතු වේ, උණු කිරීම අච්චුවේ සමහර ප්රදේශවලට ගලා යා නොහැක.
බර්ස්
බර්ර් ජනනය වන්නේ අච්චු කුහරයේ සිට නිෂ්පාදනයට නිස්සාරණය කරන ලද අතිරික්ත අමුද්රව්ය ඇලවීමෙනි.
මෙම දෝෂය නිෂ්පාදනයේ දාරවල හෝ අච්චුවේ එක් එක් කොටසෙහි සිදුවනු ඇත. අමුද්රව්ය අච්චුවෙන් හෝ චලනය වන සහ සවි කරන අච්චු වල බන්ධන ස්ථානවලින් පිටාර ගැලීම විය හැකිය.
හයිඩ්රොලික් පීඩනය හෝ කෝණික පින් නිසා ඇති වන අච්චු හරය මත ද බර්ස් සොයාගත හැකිය.
බර්ස් වල බරපතලකම වෙනස් වේ, සමහර විට සිහින්, සමහර විට ඝන.
හේතුව:
බර්ස් සඳහා හේතු ඇතුළත් වේ:
කලම්ප අච්චු මතුපිටට හානි වී හෝ දැඩි ලෙස පැළඳ සිටී.
චලනය වන අච්චුව සහ සවිකරන අච්චුව අගුලු දමා ඇති විට ඒවා විසන්ධි වේ.
අච්චුවේ ඇති අමුද්රව්යවල පීඩනය අච්චු කලම්ප බලයට වඩා වැඩිය.
ඉහත සඳහන් කළ තුන්වන කොන්දේසිය විවිධ හේතු නිසා ඇතිවේ. පහත සඳහන් අවස්ථා වලදී, අමුද්රව්යවල පීඩනය අච්චු කලම්ප බලයට වඩා වැඩි වේ.
ඉන්ජෙක්ෂන් අච්චුවේ පළමු අදියරේදී (පුස් පිරවීමේ අදියර), ඕනෑවට වඩා අමුද්රව්ය පුරවා ඇති අතර එමඟින් අච්චුව තුළ පීඩනය වැඩි වේ.
අච්චු පිරවීමේ ක්රියාවලියේදී, දියවන ප්රවාහයේ විශාල ප්රතිරෝධය අච්චුව තුළ පීඩනය ද ඉහළ නංවයි.
පීඩන රඳවා ගැනීමේ අදියරේදී අච්චු කුහරයේ පීඩනය ඉතා ඉහළ ය.
පුස් කලම්ප බලය ප්රමාණවත් නොවේ.
පිරිහීම
වියෝජනය බොහෝ ප්රතිඵලවලට හේතු විය හැක. ගැටලුවේ තරම සහ බරපතලකම ද වෙනස් වේ. වඩාත්ම බරපතල අවස්ථාවෙහිදී, එය නිෂ්පාදනයේ සම්පූර්ණ දුර්වර්ණ වීම සහ දුර්වල යාන්ත්රික ගුණාංග ඇති විය හැක. දේශීය පරිහානිය පමණක් අඳුරු ඉරි හෝ පැල්ලම් ඇති කරයි.
හේතුව:
ක්ෂය වීම සිදුවන්නේ අමුද්රව්ය වලට හානි වීමෙනි. ප්ලාස්ටික් සෑදෙන දිගු දාම අණු අධික තාපය හෝ අධික කැපුම් ආතතිය යටතේ දිරාපත් වේ. අණු දිරාපත් වීමේදී වාෂ්පශීලී වායුව පිරිහීමේ ක්රියාවලිය වේගවත් කරන අතර එමඟින් අමුද්රව්ය වර්ණ ගැන්වීමට හේතු වේ. අණු විශාල ප්රමාණයක වියෝජනය අවසානයේ අමුද්රව්යවල අන්තර්ගතය බිඳ දමන අතර යාන්ත්රික ගුණාංග කෙරෙහි ඍණාත්මක බලපෑමක් ඇති කරයි.
ද්රව්ය බැරලයේ අසමාන උෂ්ණත්වය හේතුවෙන් දේශීය පරිහානිය ඇති විය හැක.
පහත දැක්වෙන අවස්ථා වලදී පිරිහීම සිදුවිය හැකිය:
අමුද්රව්ය ද්රව්ය බැරලයේ හෝ උණුසුම් ධාවන පද්ධතියේ අධික ලෙස රත් වේ.
අමුද්රව්ය බැරලයේ වැඩි කාලයක් පවතී.
ඉන්ජෙක්ෂන් මෝල්ඩින් ක්රියාවලියේදී, අමුද්රව්ය මත ඇති කරන කැපුම් ආතතිය ඉතා විශාලය. තුණ්ඩ අවහිර වී ඇත්නම් හෝ ගේට්ටු සහ ධාවකය ඉතා පටු නම්, එය කැපුම් ආතතිය වැඩි කරයි.
විරූපණය
සාමාන්ය අවස්ථාවන්හිදී, නිෂ්පාදනවල හැඩය අච්චු වලට අනුකූල විය යුතුය. විරූපණය යනු නිෂ්පාදනවල විරූපණයයි.
තත්වය වඩාත් නරක අතට හැරෙන විට, අච්චුවෙන් පිටවන විට නිෂ්පාදන සම්පූර්ණයෙන්ම විකෘති වනු ඇත. තත්ත්වය බරපතල නොවන විට, නිෂ්පාදනයේ හැඩය කුඩා අක්රමිකතා පෙනෙනු ඇත.
දිගු නමුත් ආධාරක දාර නොමැතිව හෝ විශාල ගුවන් යානා යනු විරූපණයට වඩාත්ම අවදානම් සහිත ප්රදේශ වේ.
හේතුව:
විකෘති වීමට හේතු:
අච්චුව මුදා හරින විට උෂ්ණත්වය ඉතා ඉහළ ය.
ඝන සහ තුනී ප්රදේශවල සිසිලන කාලය වෙනස් වන බැවින් හෝ අච්චුවේ චලන සහ අච්චු සවි කිරීමේදී අච්චු උෂ්ණත්ව වෙනස නිසා නිෂ්පාදන ඇතුළත හැකිලීම වෙනස් වේ.
පිරවීමේදී පුස් ප්රවාහය සුමට නොවේ (ඊනියා “ශීතකරණ දිශානතිය”) හෝ පීඩන රඳවා ගැනීමේ අදියරේදී අච්චු කුහරය තුළ පීඩනය ඉතා ඉහළ ය.
අපද්රව්ය
අපද්රව්ය බොහෝ විට විවිධ වර්ණ, පැල්ලම් හෝ ඉරි සහිත ලප ස්වරූපයෙන් දිස් වේ. වඩාත් සුලභ වන්නේ කළු ලපයයි.
අපද්රව්ය කුඩා ලප පමණක් විය හැකි නමුත්, එය බරපතල වූ විට පැහැදිලි ඉරි හෝ වර්ණ ඉවත් කිරීමේ විශාල කොටසක් ද විය හැකිය.
හේතුව:
අපිරිසිදුකම් ඇති වන්නේ අමුද්රව්ය සමඟ මිශ්ර කර ඇති ද්රව්ය නිසා ය:
අමුද්රව්ය බැරල් වලට ප්රවාහනය කරන විට සන්ඩ්රීස් සමඟ මිශ්ර වේ.
අමුද්රව්ය වියෝජනය වීම ඕනෑම කැපුම් යාන්ත්රණයකින් වැටී යන්ත්ර බෝල්ට්, වියළන බෙරයේ අභ්යන්තර බිත්තිය, සන්ධි / තුණ්ඩ වැනි අමුද්රව්යවලට මිශ්ර විය හැකිය.
ලැමිෙන්ටේෂන්
ලැමිනේෂන් මඟින් නිෂ්පාදනවල මතුපිට “සමේ ආචරණය” ජනනය කරනු ඇත, එය නිෂ්පාදනවල සහ අනෙකුත් අමුද්රව්යවල මතුපිට ගුණ සහ වයනයෙහි වෙනස නිසා ඇති වන අතර එය ඉවත් කළ හැකි පීල් කරන සමක් සාදයි.
ලැමිනේෂන් බැරෑරුම් වන විට, සම්පූර්ණ හරස්කඩ ප්රදේශය විවිධ ස්ථරවලින් සමන්විත වන අතර, එකට උණු වී නැත. අඩුපාඩු පැහැදිලිව පෙනෙන විට, නිෂ්පාදනවල පෙනුම අවශ්යතා සපුරාලිය හැකි නමුත් නිෂ්පාදනවල යාන්ත්රික ගුණාංග බිඳ දමයි.
හේතුව:
ලැමිනේෂන් සඳහා ප්රධාන හේතු දෙකක් තිබේ. පළමු එක තමයි විවිධ අමුද්රව්ය වර්ග දෙකක් වැරදි ලෙස මිශ්ර වූ විට. අමුද්රව්ය දෙක පීඩනය යටතේ එකවර බැරලයට ප්රවාහනය කරනු ලැබේ. කෙසේ වෙතත්, අච්චුව සිසිල් කළ විට එකට උණු කළ නොහැකි විට, නිෂ්පාදන සෑදීම සඳහා විවිධ ස්ථර බලහත්කාරයෙන් එකට තද කර ඇති ආකාරයටම.
දෙවනුව: සීතල දියවීම පටු ගේට්ටුව හරහා යාමට බල කෙරෙන්නේ නම්, කප්පාදු ආතතිය ජනනය වනු ඇත. අධික කැපුම් ආතතිය නිසා දියවන ස්ථරය කල්තියා දිය වී සම්පූර්ණයෙන්ම විලයනය කළ නොහැක.
මිශ්ර කිරීමේ අවදානම:
දැනගත යුතු එක් දෙයක් නම්, සමහර අමුද්රව්ය එකට මිශ්ර කිරීම ප්රබල රසායනික ප්රතික්රියාවක් ඇති කරයි, එනම් PVC සහ Avetal මිශ්ර නොකළ යුතුය.
රිදී රේඛීය
Sliver linear යනු දේශීය සංසිද්ධියක් විය හැකි නමුත්, එය බරපතල වූ විට මුළු මතුපිටටම ව්යාප්ත විය හැක.
රිදී රේඛීය නිෂ්පාදනවල පෙනුමට බලපාන අතර නිෂ්පාදනවල යාන්ත්රික ගුණාංගවලටද හානි කරයි.
හේතුව:
පහත කරුණු දෙක රිදී රේඛීය වීමට හේතු වේ:
අමුද්රව්ය තෙත් වන අතර සමහර ඒවා වාතයේ වාෂ්ප අවශෝෂණය කරයි. අමුද්රව්ය ඉතා තෙත් නම්, බැරලයේ අධික උෂ්ණත්වය සහ අධික පීඩනය යටතේ පීඩන වාෂ්ප ජනනය විය හැකිය. මෙම වාෂ්ප නිෂ්පාදනයේ මතුපිට හරහා කැඩී රිදී තීරු සාදයි.
දියවීම තාප හානියට ලක් වූ අතර දේශීය හායනය ජනනය කරයි. ජනනය වන වාෂ්පශීලී වායුව අච්චුව මත මතුපිට අවහිර කර නිෂ්පාදන මතුපිට ඉරි ජනනය කරනු ඇත.
මෙය පිරිහීම තරම් නරක නැත. දියවීමේ උෂ්ණත්වය ඉහළ මට්ටමක පවතින තාක් කල් හෝ ප්ලාස්ටික්කරණයේදී හෝ අච්චුව තුළට එන්නත් කිරීමේදී එය කැපුම් ආතතියට ලක්වන තාක් කල්, මෙය සිදුවිය හැකිය.
ග්ලොස් / සෙවන
නිෂ්පාදනවල මතුපිට නිමාව අච්චු වලට සමාන විය යුතුය. දෙකේ මතුපිට නිමාව වෙනස් වූ විට, දීප්තිය/සෙවණැලි දෝෂ ඇති විය.
දෝෂ ඇති වූ විට මතුපිට අඳුරු වනු ඇත, රළු මතුපිට සිනිඳු සහ දිලිසෙන වේ.
හේතුව:
දිලිසීම / සෙවනැල්ල සඳහා හේතු ඇතුළත් වේ:
ද්රවය සුමට ලෙස ගලා යාම හෝ අච්චු මතුපිට උෂ්ණත්වය අඩු වීම, ද්රව්ය අච්චු ගැසීමේදී අච්චු මතුපිට නිමාව අනුපිටපත් කළ නොහැක.
පීඩනය රඳවා ගැනීමේදී, කුහරයේ පීඩනය, සිසිලන ක්රියාවලියේදී ද්රව්ය අච්චුවේ මතුපිටට ඇලී සිටීමට ප්රමාණවත් නොවන අතර, හැකිලීමේ ලකුණු ඉතිරි කරයි.
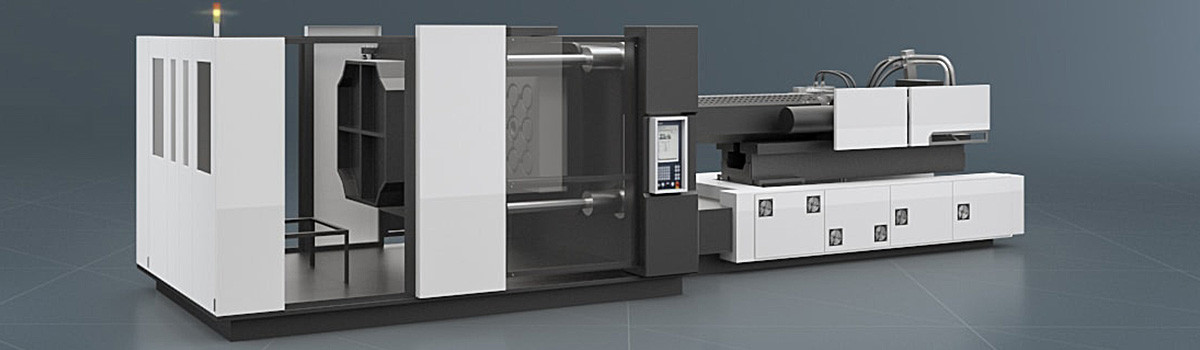
ප්රවාහ ලකුණු
නිෂ්පාදනවල මතුපිට විවිධ ආකාරවලින් ගලා යන සලකුණු සොයාගත හැකිය. සාමාන්යයෙන්, එය සෙවනැලි ප්රදේශයක් සාදනු ඇත.
ප්රවාහ සලකුණු නිෂ්පාදනවල මතුපිට කිසිදු එම්බෝස් කිරීමක් හෝ අවපාතයක් ඇති නොකරයි, එය ඇඟිලිවලට දැනිය නොහැක. මෙම දෝෂය ඇදගෙන යාමේ සලකුණු, අවතාර සහ සෙවනැලි ලෙසද හැඳින්වේ.
ප්රවාහ ලකුණු පැහැදිලිව පෙනෙන විට, එය කට්ට ඇති කරයි, සහ නිෂ්පාදන මතුපිට ලකුණු වැනි දෝෂ ඇති කරයි.
හේතුව:
ප්රවාහ ලකුණු සොයා ගත හැක්කේ:
උණුවීමේ ප්රවාහය දුර්වල හෝ අච්චුවේ මතුපිට උෂ්ණත්වය අඩු වන අතර, අච්චු පිරවීමේ ක්රියාවලියේදී ප්ලාස්ටික් විශාල ප්රවාහ ප්රතිරෝධයක් ඇති කරයි.
අච්චු පිරවීමේදී, ප්රතිරෝධය සහිත දියවන ප්රවාහය, ඩයි එකේ අසමාන මතුපිට, ඩයි මතුපිට මුද්රණය කර ඇති ලකුණු හෝ රටා හෝ පිරවුම් ක්රියාවලියේදී දියවන ප්රවාහ දිශාව වෙනස් වීම නිසා ඇති විය හැක.
සන්ධි රේඛාව
පුස් පිරවීමේදී දියවන පෙරමුනු දෙකක් හමු වූ විට සම්බන්ධ වන රේඛාව ජනනය වන අතර, රේඛාවක් මෙන් නිෂ්පාදනයේ මතුපිට දිස්වනු ඇත.
සන්ධි රේඛාව නිෂ්පාදනවල මතුපිට ඇති ඉරිතැලීම් රේඛාව වැනිය, එය හඳුනා ගැනීමට පැහැදිලි නැත.
අච්චු නිර්මාණය කරන විට, සමහර දෘශ්ය සන්ධි රේඛා නොවැළැක්විය හැකිය. මෙම අවස්ථාවේ දී, නිෂ්පාදනවල ශක්තිය හා පෙනුම හානි වීම වැළැක්වීම සඳහා හැකි තරම් සන්ධි රේඛාව කෙටි කරයි.
හේතුව:
දියවන පෙරමුනේ පරම්පරාව සඳහා බොහෝ හේතු තිබේ. වඩාත්ම විය හැකි හේතුව පුස් හරයේ දාර දිගේ දියවී යාම විය හැකිය. දියවී යන විට එය සන්ධි රේඛා නිපදවයි. දියවන ඉදිරිපස දෙකක උෂ්ණත්වය ඒවා සාර්ථකව එකට ෆියුස් කිරීමට ඉඩ ප්රමාණවත් විය යුතු අතර නිෂ්පාදනවල ශක්තියට හා පෙනුමට බලපාන්නේ නැත.
දියවී යන දෙකම සම්පූර්ණයෙන්ම එකට ඒකාබද්ධ කළ නොහැකි වූ විට, දෝෂ ඇතිවේ.
දෝෂ සඳහා හේතු:
අච්චුවෙහි ඝන සහ තුනී කොටස් ඇති අතර, දියවන ගලායාමේ වේගය වෙනස් වේ, උණු කිරීම අච්චුවේ තුනී කොටස හරහා ගලා යන විට, උෂ්ණත්වය අඩු වේ.
එක් එක් ධාවකයාගේ දිග වෙනස් වේ. හුදකලා ධාවකයන් සිසිල් කිරීමට පහසු වනු ඇත.
පීඩන රැඳවුම් අවධියේදී සම්පූර්ණයෙන්ම උණුවීමට ඉඩ දීමට අච්චු කුහරයේ පීඩනය ප්රමාණවත් නොවේ.
ඉතිරි බුබුලු දියවන ඉදිරිපස විලයනය කිරීමට නොහැකි වන අතර එය පිළිස්සීමට ද හේතු වේ.
ගිනි ගනිමින්
පිළිස්සීම කෙටි වෙඩි තැබීමකට සමාන වේ, නමුත් අක්රමවත් වියැකී යන දාර සහ සුළු දැවෙන සුවඳක් ඇත. තත්වය බරපතල වන විට, ප්ලාස්ටික් දැවෙන සුවඳ සමඟ නිෂ්පාදනයේ කාබන් කළු ප්රදේශ දිස්වනු ඇත.
දෝෂ ඉවත් නොකළ හොත්, අච්චුව මත බොහෝ විට කළු තැන්පත් වේ. පිළිස්සීමෙන් නිපදවන ගෑස් හෝ තෙල් ද්රව්ය වහාම පරීක්ෂා නොකළ හොත්, ඒවා වායු කුහර අවහිර කළ හැකිය. පිළිස්සීම සාමාන්යයෙන් මාර්ගවල කෙළවරේ දක්නට ලැබේ.
හේතුව:
අභ්යන්තර දහන බලපෑම හේතුවෙන් පිළිස්සීම සිදු වේ. ඉතා කෙටි කාලයක් තුළ වාතයේ පීඩනය තියුනු ලෙස වැඩි වන විට, උෂ්ණත්වය ඉහළ ගොස් පිළිස්සුම් ඇති කරයි. එකතු කරන ලද දත්ත වලට අනුව, ඉන්ජෙක්ෂන් මෝල්ඩින් ක්රියාවලියේ අභ්යන්තර දහන බලපෑම අංශක 600 දක්වා ඉහළ උෂ්ණත්වයක් ඇති කළ හැකිය.
පහත සඳහන් අවස්ථා වලදී පිළිස්සීම සිදු කළ හැකිය:
අච්චුව පිරවීමේ වේගය වේගවත් වන අතර එමඟින් වාතය පුස් කුහරයෙන් ඉවත් කළ නොහැකි අතර එන ප්ලාස්ටික් අවහිර වීම නිසා වායු බුබුලු ජනනය කරයි, සම්පීඩනය කිරීමෙන් පසු අභ්යන්තර දහන බලපෑමට මග පාදයි.
වායු කුහර අවහිර වී හෝ වාතාශ්රය සුමට නොවේ.
අච්චුවෙහි වාතය වායු කුහර වලින් අවලංගු කළ යුතුය. පිහිටීම, අංකය, ප්රමාණය හෝ ක්රියාකාරිත්වය මගින් වාතාශ්රය බලපාන්නේ නම්, වාතය අච්චුවේ රැඳී ඇති අතර පිළිස්සීමට තුඩු දෙනු ඇත. විශාල පුස් කලම්ප බලය ද දුර්වල වාතාශ්රය ඇති කරයි.
හැකිලීම
හැකිලීම යනු නිෂ්පාදනවල මතුපිට ඇති කුඩා සිදුරු වේ.
අඩුපාඩු සුළු වන විට, නිෂ්පාදනවල මතුපිට අසමාන වේ. එය බරපතල වන විට, නිෂ්පාදනවල විශාල ප්රදේශය කඩා වැටෙනු ඇත. ආරුක්කු, හැන්ඩ්ල් සහ නෙරා ඇති නිෂ්පාදන බොහෝ විට හැකිලීමේ දෝෂ වලින් පීඩා විඳිති.
හේතුව:
සිසිලනය අතරතුර අමුද්රව්ය විශාල ප්රදේශයක හැකිලීම නිසා හැකිලීම සිදුවේ.
නිෂ්පාදනවල ඝන ප්රදේශයේ (ආරුක්කු වැනි) ද්රව්යයේ මධ්ය උෂ්ණත්වය අඩු බැවින්, මතුපිටට වඩා පසු හැකිලීම සිදුවනු ඇත, එය අමුද්රව්ය තුළ හැකිලීමේ බලයක් නිපදවන අතර පිටත පැත්ත අභ්යන්තර අවපාතයට ඇද දමයි. හැකිලීම නිෂ්පාදනය කිරීමට.
පහත සඳහන් අවස්ථා වලදී හැකිලීම සිදු වේ:
සිසිලන ක්රියාවලියේදී අමුද්රව්ය හැකිලීමෙන් ජනනය වන බලයට වඩා අච්චු කුහරයේ පීඩනය අඩුය.
සිසිලන ක්රියාවලියේදී අච්චු කුහරයේ පීඩන කාලය ප්රමාණවත් නොවීම නිසා අමුද්රව්ය ද්වාරයෙන් කුහරයෙන් පිටතට ගලා යයි.
අධික අමුද්රව්ය එන්නත් කිරීමට පෙර ඉස්කුරුප්පු ඇණ සම්පූර්ණයෙන්ම ඉවත් කර ඇති බැවින් අච්චු සහ පීඩන රඳවා ගැනීමේ අදියරේදී අමුද්රව්යයට ප්රමාණවත් බෆරින් ධාරිතාවක් නොමැත.
ගේට්ටු සහ ධාවකයන්ගේ හරස්කඩ ප්රදේශ නිෂ්පාදනවල thickness ණකමට වඩා බෙහෙවින් කුඩා වන අතර එයින් අදහස් කරන්නේ නිෂ්පාදන නිස්සාරණය කිරීමේ ක්රියාවලියට පෙර දොරටු දැනටමත් ශීත කර ඇති බවයි.
බුබුලු
රික්ත බුබුලු වායු බුබුලු ආකාරයෙන් ඉදිරිපත් කර ඇති අතර එය විනිවිද පෙනෙන නිෂ්පාදන මත පහසුවෙන් සොයාගත හැකිය. එය විනිවිද නොපෙනෙන නිෂ්පාදනවල හරස්කඩ මත ද දැකිය හැකිය.
හේතුව:
වායු බුබුලු යනු නිෂ්පාදනවල රික්ත කොටස වන අතර, සිසිලන ක්රියාවලියේදී අමුද්රව්ය හැකිලීමේදී නිපදවනු ලැබේ.
හැකිලීමට සමානව, අමුද්රව්ය ඇතුළත සංකෝචන බලය නිපදවයි. වෙනස කුමක්ද, බුබුලු සෑදූ විට නිෂ්පාදනවල බාහිර පෙනුම ඝන වී ඇති අතර, කඩා වැටීමක් නොමැත, එබැවින් හිස් බුබුලු ජනනය වේ.
බුබුලු ඇතිවීමට හේතු අඩුවීමට සමාන වේ, ඇතුළුව:
අකාර්යක්ෂම අච්චු කුහරයේ පීඩනය
ප්රමාණවත් නොවන කුහරය පීඩන කාලය
ධාවකයේ සහ ගේට්ටුවේ ප්රමාණය ඉතා කුඩාය
ඉසින ලකුණු
ඉසින ලකුණු ගේට්ටුව ඉදිරිපිට නූල් පෙදෙසට යොමු කරයි. ඉසින ලකුණු නිෂ්පාදනවල පෙනුමට පමණක් නොව, නිෂ්පාදනවල ශක්තියටද බලපායි.
හේතුව:
පුස් පිරවීමේ ක්රියාවලියේදී පාලනයකින් තොරව දියවී යාම නිසා ඉසින ලකුණු ඇතිවේ.
උණු කළ ප්ලාස්ටික් විශාල පීඩනයක් යටතේ අච්චුවට ඇතුල් වේ. අච්චුව පිරවීමේ වේගය වැඩි නම්, ප්ලාස්ටික් අච්චු කුහරයේ විවෘත පරතරයෙන් පිටවන අතර ඉක්මනින් ආපසු පැමිණ සිසිල් වේ. එම අවස්ථාවේ දී, නූල් සාදනු ලබන අතර, ද්වාර ප්ලාස්ටික් ගේට්ටුවලට ඇතුල් වීම අවහිර කරයි.
ලකුණු ඉසීමට ප්රධාන හේතුව ගේට්ටු වල වැරදි පිහිටීම හෝ ගේට්ටුවේ සැලසුමයි. පහත සඳහන් අවස්ථා දෙක දෝෂ වල තත්වය වඩාත් නරක අතට හැරෙනු ඇත:
ඉහළ අච්චු පිරවීමේ වේගය
පුස් පිරවීමේදී දුර්වල දියවන ප්රවාහය