Grundlagen des Kunststoffspritzgusses
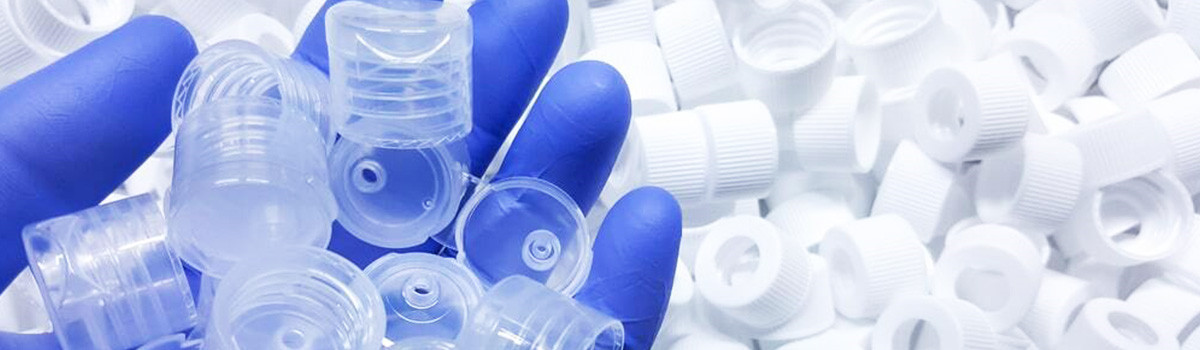
Erkunden Sie den Spritzgussprozess und wie er funktioniert.
Kunststoffspritzguss ist eine beliebte Fertigungstechnik, bei der thermoplastische Pellets in große Mengen komplexer Teile umgewandelt werden. Das Spritzgussverfahren eignet sich für eine Vielzahl von Kunststoffmaterialien und ist ein wesentlicher Aspekt des modernen Lebens – Handyhüllen, Elektronikgehäuse, Spielzeug und sogar Autoteile wären ohne es nicht möglich. In diesem Artikel werden die Grundlagen des Spritzgießens erläutert, die Funktionsweise des Spritzgießens beschrieben und die Unterschiede zum 3D-Druck veranschaulicht.
Was sind die Grundlagen des Kunststoffspritzgusses?
Zu den Grundlagen des Kunststoff-Spritzgussverfahrens gehören die Erstellung des Produktdesigns, die Herstellung einer Form, die dem Produktdesign entspricht, das Schmelzen der Kunststoffharzpellets und die Verwendung von Druck zum Einspritzen der geschmolzenen Pellets in die Form.
Nachfolgend finden Sie eine Aufschlüsselung der einzelnen Schritte:
1. Erstellen des Produktdesigns
Konstrukteure (Ingenieure, Formenbauer usw.) erstellen ein Teil (in Form einer CAD-Datei oder eines anderen übertragbaren Formats) und befolgen grundlegende Designrichtlinien, die für den Spritzgussprozess spezifisch sind. Konstrukteure sollten versuchen, die folgenden Merkmale in ihre Entwürfe aufzunehmen, um den Erfolg einer Kunststoffspritzgussform zu steigern:
*Vorsprünge für Gewindeeinsätze/Befestigungen
*Konstante oder nahezu konstante Wandstärken
*Glatte Übergänge zwischen variablen Wandstärken
*Hohlräume in Dickschnitten
*Abgerundeten Ecken
*Entformungsschrägen an senkrechten Wänden
*Rippen für Stützen
*Reibpassungen, Schnappverbindungen und andere Verbindungsmerkmale ohne Verbindungselemente
*Lebende Scharniere
Darüber hinaus sollten Designer die folgenden Merkmale minimieren, um Fehler in ihren Designs zu reduzieren:
*Ungleichmäßige Wandstärken oder besonders dünne/dicke Wände
* Vertikale Wände ohne Formschrägen
*Plötzliche geometrische Veränderungen (Ecken, Löcher etc.)
*Schlecht gestaltete Verrippung
*Hinterschneidungen/Überhänge
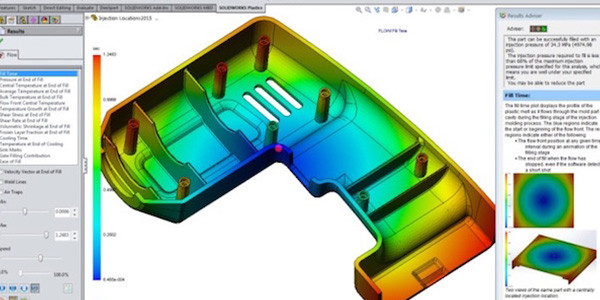
2. Herstellung einer Werkzeugform, die zum Produktdesign passt
Hochqualifizierte Maschinisten und Werkzeugmacher fertigen anhand des Produktdesigns eine Werkzeugform für die Spritzgussmaschine. Eine Werkzeugform (auch einfach als Werkzeug bezeichnet) ist das Herz und die Seele der Spritzgießmaschine. Sie sind sorgfältig entworfen, um den Negativhohlraum für das Produktdesign und zusätzliche Merkmale wie Angüsse, Angusskanäle, Tore, Entlüftungen, Auswerfersysteme, Kühlkanäle und bewegliche Komponenten aufzunehmen. Werkzeugformen werden aus bestimmten Stahl- und Aluminiumsorten hergestellt, die Zehntausenden (und manchmal Hunderttausenden) von Heiz- und Kühlzyklen standhalten können, wie z. B. 6063-Aluminium, P20-Stahl, H13-Stahl und 420-Edelstahl. Der Formherstellungsprozess dauert mehr als 20 Wochen, einschließlich Herstellung und Genehmigung, was diesen Schritt zum umfangreichsten Aspekt des Spritzgießens macht. Es ist auch der teuerste Teil des Spritzgießens, und sobald eine Werkzeugform hergestellt ist, kann sie nicht drastisch geändert werden, ohne dass zusätzliche Kosten entstehen.
3. Schmelzen der Kunststoffharzpellets
Nachdem die Bediener die fertige Form erhalten haben, wird sie in die Spritzgießmaschine eingesetzt und die Form schließt sich, wodurch der Spritzgießzyklus gestartet wird.
Kunststoffgranulat wird in den Trichter und in das Fass eingefüllt. Die hin- und hergehende Schnecke wird zurückgezogen, wodurch Materialien in den Raum zwischen Schnecke und Zylinder rutschen können. Die Schnecke taucht dann nach vorne und drückt das Material in den Zylinder und näher an die Heizbänder, wo es zu geschmolzenem Kunststoff schmilzt. Die Schmelztemperatur wird gemäß den Materialspezifikationen konstant gehalten, so dass keine Degradation im Zylinder oder in der Form selbst auftritt.
4. Verwenden von Druck zum Einspritzen der geschmolzenen Pellets in die Form
Die hin- und hergehende Schnecke drückt diesen geschmolzenen Kunststoff durch die Düse, die in einer Vertiefung in der Form sitzt, die als Formeingussbuchse bekannt ist. Der Druck der beweglichen Platte passt die Form und die Düse eng aneinander und stellt sicher, dass kein Kunststoff entweichen kann. Der geschmolzene Kunststoff wird durch diesen Prozess unter Druck gesetzt, wodurch er in alle Teile des Formhohlraums eintritt und die Hohlraumluft durch die Formentlüftungen verdrängt.
Komponenten für Spritzgießmaschinen
Die Komponenten einer Spritzgießmaschine umfassen einen Trichter, einen Zylinder, eine sich hin- und herbewegende Schnecke, Heizer, eine bewegliche Platte, eine Düse, eine Form und einen Formhohlraum.
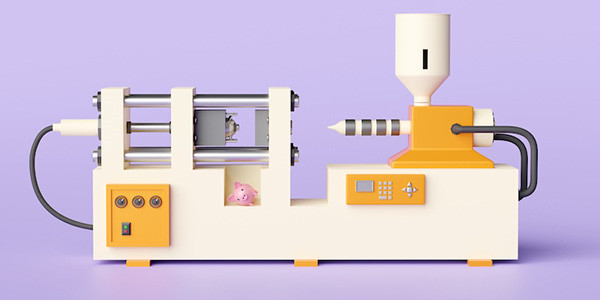
Weitere Informationen zu den einzelnen Spritzgusskomponenten finden Sie in der folgenden Liste:
*Trichter: die Öffnung, durch die das Kunststoffgranulat in die Maschine eingeführt wird.
*Fass: das äußere Gehäuse der Spritzgießmaschine, das die Kolbenschnecke und das Kunststoffgranulat enthält. Das Fass ist mit mehreren Heizbändern umwickelt und mit einer beheizten Düse versehen.
*Kolbenschraube: die Korkenzieherkomponente, die das Kunststoffmaterial fördert und unter Druck setzt, wenn es durch das Fass schmilzt.
*Heizungen: Diese auch als Heizbänder bezeichneten Komponenten versorgen das Kunststoffgranulat mit thermischer Energie und verwandeln es von einer festen Form in eine Flüssigkeit. form.
*Bewegliche Platte: Das mit dem Formkern verbundene bewegliche Bauteil, das beide Formhälften durch Druck luftdicht hält und beim Freilegen des fertigen Teils auch den Formkern freigibt.
*Düse: die beheizte Komponente, die einen Standardauslass für geschmolzenen Kunststoff in den Formhohlraum bietet und sowohl Temperatur als auch Druck so stabil wie möglich hält.
*Schimmel: die Komponente oder Komponenten, die den Formhohlraum und zusätzliche unterstützende Merkmale wie Auswerferstifte, Angusskanäle, Kühlkanäle, Entlüftungen usw. enthalten. Formen sind mindestens in zwei Hälften geteilt: die stationäre Seite (näher am Zylinder) und die Form Kern (auf der beweglichen Platte).
*Formhohlraum: der negative Raum, der, wenn er mit geschmolzenem Kunststoff gefüllt ist, ihn in das gewünschte Endteil formt, plus Stützen, Anschnitte, Angusskanäle, Angüsse usw.
Wie funktioniert Spritzguss?
Sobald der Kunststoff die Form einschließlich ihrer Angüsse, Angusskanäle, Anschnitte usw. gefüllt hat, wird die Form auf einer festgelegten Temperatur gehalten, um eine gleichmäßige Erstarrung des Materials in die Form des Teils zu ermöglichen. Während des Abkühlens wird ein Haltedruck aufrechterhalten, um sowohl den Rückfluss in den Zylinder zu stoppen als auch Schrumpfungseffekte zu reduzieren. An diesem Punkt wird in Erwartung des nächsten Zyklus (oder Schusses) mehr Kunststoffgranulat in den Trichter gegeben. Beim Abkühlen öffnet sich die Platte und ermöglicht das Auswerfen des fertigen Teils, und die Schnecke wird wieder zurückgezogen, sodass Material in den Zylinder eindringen und den Prozess von vorne beginnen kann.
Der Spritzgusszyklus funktioniert nach diesem kontinuierlichen Prozess – Schließen der Form, Zuführen/Erhitzen des Kunststoffgranulats, Pressen in die Form, Abkühlen zu einem festen Teil, Auswerfen des Teils und erneutes Schließen der Form. Dieses System ermöglicht die schnelle Produktion von Kunststoffteilen, und je nach Design, Größe und Material können an einem Arbeitstag bis zu 10,000 Kunststoffteile hergestellt werden.
Djmolding ist ein Spritzgussunternehmen mit geringem Volumen in China. Unser Kunststoffspritzgussverfahren produziert kundenspezifische Prototypen und Endverbraucher-Produktionsteile mit Vorlaufzeiten von nur 1 Tag, Lieferant von Kunststoffspritzgussteilen mit geringem Volumen für bis zu 10000 Teile pro Jahr