Fall in Indien
DJmolidngs Einlegeform-Spritzgussservice für indische Unternehmen
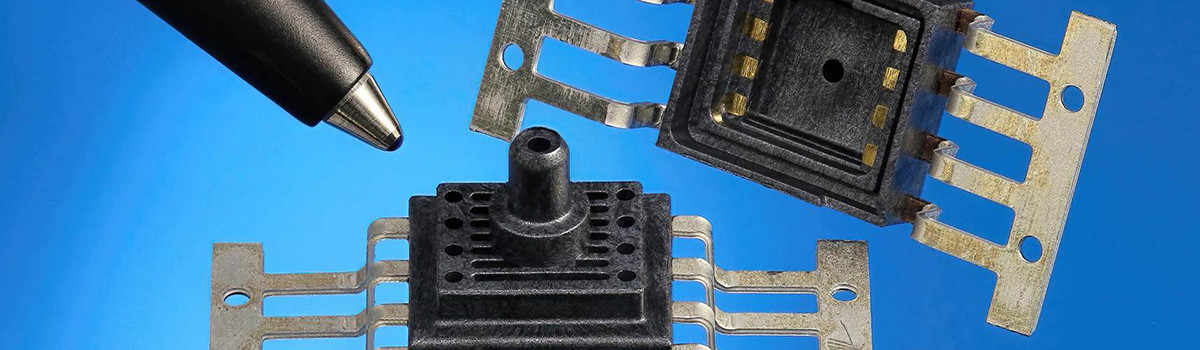
Bei der Einlegeform handelt es sich im Allgemeinen um eine Art Form, mit der Muttern, Metallteile oder Hartplastikteile in Hohlräumen für den Spritzguss fixiert werden.
DJmolding bietet den Insert-MLOD-Spritzgussservice für den indischen Markt an und wir produzieren zahlreiche Kunststoffteile für Insert-Molding für verschiedene Branchen, insbesondere für Hersteller von Haushaltsgeräten. Einige indische Hersteller von Haushaltsgeräten beziehen die Kunststoffteile des Insert Mouldings schon lange von DJmolding. Wir haben eine sehr gute Partnerschaft mit diesen indischen Unternehmen.
Spritzgießen von Einsatzmuttern: Das Material der Muttern kann Edelstahl, Kupfer, Bronze und Stahl sein, im Allgemeinen werden Kupfermuttern häufig verwendet. Kupfer lässt sich leicht rändeln, wodurch sich Muttern und Kunststoffe besser verbinden lassen. Die Toleranz der Muttern-Innenbohrungen sollte innerhalb von 0.02 mm liegen, andernfalls kann es leicht zu Graten kommen, wenn die Toleranz über 0.02 mm liegt. Bei der Formmontage müssen Muttern zum Testen in Einsteckstifte montiert werden. Wenn es fest zwischen Muttern und Stiften sitzt, wäre es schwierig, das Teil auszuwerfen, was zu Auswurfspuren oder Klebeproblemen führen würde. Wenn es locker sitzt, kann es zu Blitzen kommen.
Spritzgießen von Metallteilen:
Metallteile können aus Edelstahl, Aluminium, Kupfer, Stahl usw. sein. Die Toleranz von Metallteilen sollte innerhalb von 0.02 mm liegen, da es sonst schwierig ist, das Material abzudichten, und es leicht zu Graten kommt. Die Fläche der Metallteile kann nicht zu groß ausgelegt werden.
Wenn die Einfüllfläche für Metallteile zu groß ist, wäre es aufgrund des großen Temperaturunterschieds zwischen den Metallteilen sehr schwierig, eine vollständige Einspritzung zu erreichen. Die Positionen der Metallteile werden in der Regel im Hohlraum festgelegt, da sich der Hohlraum nicht bewegt. Dies trägt dazu bei, Grate zu vermeiden, die durch das Lösen von Metallteilen bei der Bewegung entstehen können (was in schweren Fällen zu Schäden an der Form führen kann). In besonderen Fällen können Positionen von Metallteilen nur im Kern oder an der Seitenfläche des Produkts vorgesehen werden.
Hartplastik-Spritzguss einlegen:
Wählen Sie normalerweise Hartkunststoffe mit hohem Schmelzpunkt, wie PEEK, PA66+30GF, PP+30GF, PA12+30GF, PPS usw. Die Toleranzen für diese Hartkunststoffe sollten genau sein. Im Dichtungsbereich können keine Mängel wie Schrumpfung, Delle und Verformung auftreten. Bei der Formanpassung sollte der Hartplastik zum Testen in die Form gegeben werden und 0.05 bis 0.1 mm um den Dichtungsbereich herum vorgedrückt bleiben, um eine bessere Abdichtung zu erreichen.
Das Hartplastikteil sollte nicht für eine zu große Fläche ausgelegt werden, da dies zu Temperaturunterschieden führt und das Einfüllen des Materials beim Einspritzen erschwert. Normalerweise wird das Hartplastikteil an der Seite der Kavität befestigt, da sich die Kavität nicht bewegt, um Grate oder sogar eine Beschädigung der Form bei der Formbewegung zu vermeiden. In besonderen Fällen können Positionen von Metallteilen nur im Kern oder in der Seitenfläche des Produkts geplant werden.
Design-Schlüsselpunkte
1. Design-Schrumpfung für Produkte mit Muttereinsätzen, während für Produkte mit Metallteilen und Hartplastik-Einsätzen keine Design-Schrumpfung erforderlich ist. Für Bereiche, die eine strenge Toleranz erfordern, ändern Sie die Größentoleranz der Produkte auf den Mittelwert.
2. Verwenden Sie bei der Formkonstruktion normalerweise eine Formbasis mit standardmäßigem Pin-Point-Anguss und platzieren Sie bei der Sekundäreinspritzung die Einlegeteile so weit wie möglich im Hohlraum. Unter der Bedingung, dass die Einsätze in der Kavität befestigt werden, überlegen Sie, wie ein Teil nach dem Spritzgießen im Kern verbleibt, damit der Teil ausgeworfen werden kann. Fügen Sie normalerweise elastische Blöcke in den Hohlraum und elastischen Kleber ein, damit das Teil im Kern bleibt. Der Abstand zwischen elastischen Blöcken und Kleber darf nicht zu groß sein, da sonst die elastische Kraft zu einer Verformung harter Kunststoff- oder Metallteile führt. Der Abstand ist normalerweise auf 2 mm ausgelegt und die Menge der elastischen Blöcke und des elastischen Klebers kann entsprechend erhöht werden, wenn die Metall- oder Hartplastikeinsätze eine relativ große Fläche haben.
3. Die beste Materialstärke liegt zwischen 1.3 und 1.8 mm (ungefähr 1.5 mm ist am besten). Wenn nicht, müssen Sie die Produktzeichnungen überprüfen und dem Kunden vorschlagen, es zu ändern. Bei einer Materialstärke von weniger als 1.3 mm ist die Materialfüllung schwierig, bei einer Materialstärke von mehr als 1.8 mm kann es bei der Produktion leicht zu Schrumpfungen kommen.
4.Anguss ist in der Form sehr wichtig. Das Gleichgewicht der Materialfüllung für den Angusspunkt sollte vollständig berücksichtigt werden. Wenn Material in den Bereich gelangt, in dem Metall- oder Hartplastikteile befestigt sind, verringern sich die Geschwindigkeit der Materialfüllung und der Druck aufgrund des Widerstands und der Temperaturdifferenz der Einsätze.
5. Bei einem Formauswerfersystem muss das Gleichgewicht des Auswurfs berücksichtigt werden, sonst kommt es nach dem Auswurf zu einer Verformung. Da Teile nicht im Gleichgewicht ausgeworfen werden können, muss ein Zusammenklappen in Betracht gezogen werden, um das Gleichgewichtsproblem bei der Strukturkonstruktion zu verbessern.
6. Um die Eignung des Aussehens der Teile nach dem Auswerfen beim Spritzgießen zu gewährleisten, muss die Auswerfvorrichtung aus einem mit ABS oder PMMA eingelegten Hartplastikklumpen bestehen. Wenn die Überform über eine Gleitdichtung verfügt, sollten Sie so viele Gleiter wie möglich im Hohlraum entwerfen, da Gleiter im Hohlraum das Einpassen der Form erleichtern.
7. Um die Stärke der Siegel-SA (Nahtzugabe) sicherzustellen, sollte die Breite der Siegel-SA bei Produkten, die durch zweimaliges Spritzgießen hergestellt werden, mindestens 0.8 mm betragen. Da es sich bei dem sekundären Einspritzmaterial um Hartplastik handelt, sollte die Breite der Dichtungs-SA mindestens 1.0 mm betragen. Andernfalls muss der Kunde eine Änderung des Produkts vorschlagen.
8. Bei der Formenkonstruktion sollten wir die Spritzgießmaschinen für die Produktion berücksichtigen, um zu sehen, welcher Maschinentyp verwendet wird, vertikal oder horizontal. Es wird empfohlen, nicht zu viele Hohlräume zu konstruieren, insbesondere bei Formen mit Kaltkanälen, da zu viele Hohlräume den Kanal verlängern, Material verschwenden und außerdem schädlich für die Erzielung einer hocheffizienten Einspritzung sind. Um die Spritzgießmaschine anzupassen, müssen wir überlegen, ob sie kompakt und für die Produktanordnung geeignet ist. Die Produkte müssen fixiert werden können, um sicherzustellen, dass sich die Produkte jedes Mal in der gleichen Situation befinden, wenn sie in die Form gebracht werden. Eine andere Möglichkeit besteht darin, dass das Design-Reaktionssystem vor dem Schließen der Form warnt, wenn das Teil nicht an der richtigen Stelle ist, wodurch das Schließen der Form verhindert wird. Auf diese Weise befinden sich die Teile in der Form in der gleichen Situation, was die Qualifikationsraten und die Produktionseffizienz beim Spritzgießen erhöht.
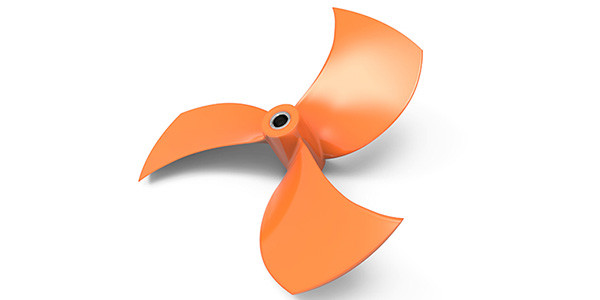
9. Es muss eine Stahlstütze vorgesehen werden, da der Einspritzbereich der Form beim Einspritzen einem großen Druck ausgesetzt ist (sollte in Form und Größe 5–10 mm größer sein als das Teil). Es darf kein Spalt zwischen den Teilen im Bereich des Überspritzens gelassen werden, da das Teil sonst nach dem zweiten Einspritzen seine Form verliert. Bei Teilen ohne SA (Nahtzugabe) muss diesem Aspekt viel mehr Aufmerksamkeit geschenkt werden.
10. Beim Spritzgießen kommt es leicht zu Luftaustritten. Daher kommt es beim Spritzgießen leicht zu Luftaustritten, daher muss die Entlüftung bei der Formkonstruktion vollständig berücksichtigt werden. In allen toten Winkeln und Positionen für Wasserleitungen über große Entfernungen müssen Entlüftungslöcher in Hartplastikteilen vorgesehen werden, da es viel schwieriger ist, Material in tote Winkel zu füllen.
11.Um sicherzustellen, dass das eingespritzte Material und der qualifizierte Druck vollständig gefüllt sind, besteht eine Möglichkeit darin, an den Ecken des Teils Hinterschnitte zu entwerfen, um das Klebeergebnis zu verbessern und dann dafür zu sorgen, dass die Teile fester haften.
12. Im Dichtungsbereich und im Trennlinienbereich sollten wir die Form nicht aus Hohlraum und Kern entnehmen, da die Klemmlinien in der Form und die Formschräge beim Entformen Grate in der Formpassung verursachen. Versuchen Sie es mit LISS-OFF zu entformen.
Angusspunkttypen der Einsatzform
Der Angusspunkt für die Einsatzform kann so gestaltet werden, dass er den Ventilanguss des heißen Angusses, den Anguss des heißen Angussstifts, den punktförmigen Anguss, den Unteranguss, den Kantenanguss usw. steuert.
Heißanguss-Nadelverschluss: gute Liquidität, flexible Positionsauswahl, kleiner Angusspunkt. Geeignet für Massenproduktion und für Produkte mit dicker Wandstärke. Kann dazu beitragen, Material zu sparen, keine Materialverschwendung für den Anguss zu verursachen, kurze Vorlaufzeiten zu gewährleisten und eine hohe Qualität zu erzielen. Der einzige Mangel ist die leichte Angussspur.
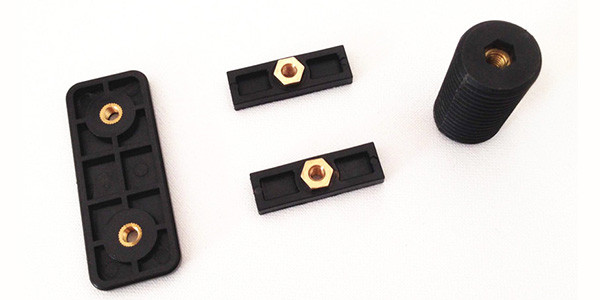
Heißanguss-Pin-Anguss: gute Liquidität, flexible Positionsauswahl, kleiner Gate-Point. Geeignet für Massenproduktion und für Produkte mit dicker Wandstärke. Kann dazu beitragen, Material zu sparen, keine Materialverschwendung für den Anguss zu verursachen, kurze Vorlaufzeiten zu gewährleisten und eine hohe Qualität zu erzielen. Aber es gibt Mängel, wie etwa 0.1 mm Materialreste rund um den Angusspunkt, die leicht entgraten können. Es müssen Rillen angebracht werden, um das linke Material rund um den Angusspunkt abzudecken.
Punktgenaues Tor: Positionsauswahl flexibel, schwache Liquidität, lange Läuferdistanz, kleiner Gate-Punkt. Anzüge für die Kleinserienfertigung. Mehr Abfallmaterial rund um den Torpunkt. Benötigen Sie mechanische Arme, um den Angusspunkt in der Produktion festzuklemmen. Lange Vorlaufzeit. Der Defekt besteht darin, dass rund um den Angusspunkt noch 0.1–0.2 mm Material verbleibt. Es müssen Rillen angebracht werden, um das verbleibende Material rund um den Angusspunkt abzudecken.
Nebentor: kann an Rippen im Hohlraum, im Kern, an den Seitenwänden und an den Auswerferstiften gestaltet werden. Angusspunkt kann flexibel gewählt werden, Gießanguss trennt sich automatisch vom Teil, leichte Angussspur. Mängel: Material lässt sich leicht um den Angusspunkt herum herausziehen, es entstehen leicht Trocknungsspuren in der Angussposition, Material muss von Hand ausgewischt werden, großer Druckverlust am Angusspunkt durch Hohlräume.
Randtor: geschmolzener Kunststoff fließt durch den Anschnitt, wird seitlich gleichmäßig verteilt, verringert die Spannung; Verringern Sie die Möglichkeit, dass Luft in den Hohlraum eindringt, und vermeiden Sie die Bildung von Streifen und Blasen. Mängel: Gießanguss lässt sich nicht automatisch vom Teil trennen, hinterlässt Angussspuren an den Kanten des Teils, es werden Werkzeuge benötigt, um den Gießanguss flach zu verarbeiten. Der Randanschnitt kann dabei helfen, die Einspritzung und das Halten des Drucks zu dosieren, und eignet sich auch gut zum Halten und Zuführen des Drucks. Auf diese Weise eignet er sich besser zur Verbesserung von Luftleitungen, Fließmarken usw.
Bearbeitung und Montage für Einlegeform
1. Erarbeiten Sie vor der Verarbeitung die Verarbeitungstechnologie des Schimmels. Wählen Sie hochpräzise Bearbeitungsmaschinen, Hochgeschwindigkeitsmaschinen, NC-Drahtschneidemaschinen mit langsamem Vorschub, Spiegelerodiermaschinen usw.
2.Design 0.05–0.1 mm an der Stelle des Vorpressens belassen.
3. Beachten Sie die Präzisionsanforderungen bei der Verarbeitung der Formbasis, überprüfen Sie die Toleranz nach Erhalt der Formbasis und verwenden Sie sie nicht, wenn die Toleranz nicht erfüllt ist.
4. Legen Sie Muttern, Metallteile und Hartplastikteile in die Form, um sie in die Form einzupassen. Wenn Sie Probleme bei der Formanpassung feststellen, überprüfen Sie die Muttern, Metallteile, Hartplastikteile und Formen, um festzustellen, welche davon falsch ist. Bearbeiten Sie das Teil so weit wie möglich gemäß der Zeichnung, was die Nachverfolgbarkeit der Daten in der Zukunft erleichtert.
5. Die Schleifmaschine kann nicht zum Formeneinbau verwendet werden. Wenden Sie sich an Maschinen, um Korrekturen vorzunehmen, wenn die Form nicht gut passt.
6. Führen Sie vor dem Test einen Aktionstest durch, um Fehlmontagen und fehlerhafte Montagen zu vermeiden. Ein falscher Zusammenbau führt zu Schäden an der Formbasis.
Formprüfung für Einlegeform
1. Bei der Prüfung einer Form muss man die Reihenfolge des Öffnens, Schließens und Auswerfens einer Form genau kennen. Verstehen Sie die strukturellen Merkmale und Eigenschaften von Metallteilen und Hartplastikteilen.
2. Informieren Sie sich genau über die Probenmenge, die der Kunde benötigt, und bereiten Sie genügend Muttern, Metallteile und Hartplastik vor, da für die Formenprüfung viele Proben erforderlich sind.
3. Beachten Sie, ob die Form ohne Einsätze aus Muttern, Metallteilen oder Hartplastik getestet werden kann. Wenn Einsatzmuttern, Metallteile und Hartplastik nicht in der Form zusammengebaut werden, kann es zu Mängeln kommen, z. B. zum Anhaften an der Form oder zu Fehlschüssen.
4.In vielen Fällen muss die Wasserlinienplatte an der Form angepasst werden, aber manchmal kann die Wasserlinienplatte in einigen Einsatzformen aufgrund ihrer Struktur nicht angepasst werden, oder noch schlimmer, die Form sitzt stark fest und muss geändert werden, oder die Form wird beschädigt Öffnung.
5. Bei der Formprüfung können Probleme auftreten, wie z. B. kurze Schüsse, Flugreisen, Blitze oder Anhaften an der Form. Wenn an einer Spritzgießmaschine Probleme festgestellt werden können, ist es besser, sie zu lösen.
DJmolding verfügt über mehr als 10 Jahre Erfahrung im Umspritzen. Wenn Sie Fragen haben, kontaktieren Sie uns bitte.