Spritzguss einfügen
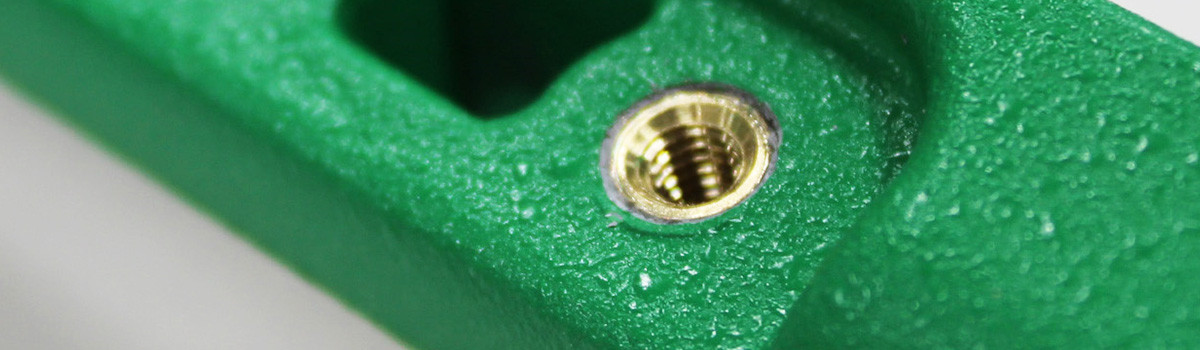
Das Einlegespritzgießen ist ein weit verbreitetes Herstellungsverfahren zur Herstellung komplexer Kunststoffteile mit eingebetteten Komponenten. Bei dieser Technik werden vor dem Spritzgussvorgang Metall- oder Kunststoffteile in den Formhohlraum eingelegt. Das geschmolzene Material umfließt dann das eingesetzte Element und sorgt für eine feste Verbindung zwischen den beiden Materialien. Das Spritzgießen von Einsätzen bietet mehrere Vorteile, darunter eine verbesserte Designflexibilität, eine kürzere Montagezeit und eine verbesserte Teilefunktionalität. In diesem umfassenden Leitfaden werden die verschiedenen Techniken, Vorteile und Anwendungen des Einlegespritzgießens erläutert.
Was ist Insert-Spritzguss?
Spritzgießen ist ein Herstellungsverfahren zur Herstellung einer Vielzahl von Teilen und Produkten. Beim Einlegespritzgießen handelt es sich um eine Form des Spritzgießens, bei der vorgeformte Elemente oder Einsätze in die Form eingelegt werden, bevor der Formvorgang beginnt. Diese Technik ermöglicht die Herstellung von Teilen, die spezifische Eigenschaften erfordern, die mit herkömmlichen Spritzgussverfahren nicht erreicht werden können.
Beim Einlegespritzgießen wird ein vorgeformter Einsatz in den Formhohlraum eingelegt, bevor der Formvorgang beginnt. Der Einsatz kann verschiedene Materialien enthalten, darunter Metall, Kunststoff und Keramik. Der Formvorgang beginnt wie gewohnt mit dem Einspritzen von geschmolzenem Kunststoff in den Formhohlraum. Wenn der Kunststoff abkühlt und sich verfestigt, verschmilzt er mit dem Einsatz und bildet ein einziges, integriertes Teil.
Der Einsatz von Einlegespritzguss bietet mehrere Vorteile. Einer der Hauptvorteile dieser Technik besteht darin, dass sie die Herstellung von Teilen mit spezifischen Eigenschaften ermöglicht, die mit herkömmlichen Spritzgussverfahren nicht erreicht werden können. Beispielsweise kann das Einlegespritzgießen eingesetzt werden, wenn eine Funktion einen Gewindeeinsatz oder ein Metallbauteil zur Verstärkung erfordert. Diese Technik ermöglicht auch die Herstellung von Teilen mit einer Materialkombination, beispielsweise einem Kunststoffteil mit einem Metalleinsatz.
Ein weiterer Vorteil des Einlegespritzgießens ist die Zeit- und Kostenersparnis. Anstatt mehrere Komponenten zusammenzubauen, entsteht beim Einlegespritzgießen ein einziges, integriertes Teil. Dadurch können Unternehmen den Zeit- und Kostenaufwand für die Montage reduzieren.
Auch bei der Herstellung komplexer Teile ist das Einlegespritzgießen hilfreich. Da der Einsatz vor Beginn des Formprozesses in den Formhohlraum eingesetzt werden kann, ist es möglich, Teile mit komplexen Geometrien und Merkmalen herzustellen, die mit herkömmlichen Spritzgussverfahren nur schwer zu erreichen wären.
Wie funktioniert das Einlegespritzgießen?
Dabei handelt es sich um eine Art Spritzgussverfahren, das das Einlegen vorgeformter Teile oder Einsätze in eine Form ermöglicht, bevor der Formprozess beginnt. Diese Technik ermöglicht die Herstellung von Teilen mit spezifischen Eigenschaften, die mit herkömmlichen Spritzgussverfahren nicht erreicht werden können, und ist besonders nützlich für die Herstellung komplexer Teile. Hier besprechen wir, wie das Einfügen von Spritzgussarbeiten funktioniert.
Der Einlegespritzgussprozess umfasst die folgenden Schritte:
- Platzierung einfügen:Der erste Schritt beim Einlegespritzgussverfahren besteht darin, das vorgeformte Einlegeteil in den Formhohlraum einzulegen. Hersteller können diesen Einsatz aus verschiedenen Materialien wie Metall, Kunststoff oder Keramik herstellen.
- Formklemmung:Sobald der Einsatz eingesetzt ist, wird die Form geschlossen und festgeklemmt. Ziel ist es, den Einsatz während des Formvorgangs an Ort und Stelle zu halten.
- Einspritzen von geschmolzenem Kunststoff:Beim Spritzgussverfahren wird geschmolzener Kunststoff in den Formhohlraum eingespritzt. Normalerweise erhitzen Hersteller den Kunststoff auf eine Temperatur zwischen 200 und 300 Grad Celsius und bestimmen diese anhand des verwendeten Kunststoffs.
- Abkühlung und Erstarrung: Wenn der Kunststoff abkühlt und sich verfestigt, verschmilzt er mit dem Einsatz und bildet ein einziges, integriertes Teil. Die Abkühl- und Erstarrungszeit hängt vom verwendeten Kunststoff und der Komplexität der Herstellung des Teils ab.
- Öffnen und Auswerfen der Form: Sobald das Teil abgekühlt und erstarrt ist, öffnet der Bediener die Form und wirft das Teil aus. Anschließend kann das Stück fertiggestellt und für den Einsatz vorbereitet werden.
Der Einsatz von Einlegespritzguss bietet mehrere Vorteile. Zu diesen Vorteilen gehören:
- Die Fähigkeit, Teile mit spezifischen Eigenschaften herzustellen, die mit herkömmlichen Spritzgussverfahren nicht erreicht werden können
- Elemente können als einzelnes, integriertes Teil hergestellt werden, was zu einer Reduzierung der Montagezeit und -kosten führt
- Fähigkeit, komplexe Teile mit komplexen Geometrien und Merkmalen zu erstellen
- Fähigkeit, eine Vielzahl von Materialien zu verwenden, darunter Metall, Kunststoff und Keramik
- Spritzgießen ist ein hocheffizienter und wiederholbarer Prozess, mit dem große Teilemengen mit hoher Präzision und Genauigkeit hergestellt werden können.
Arten von Einsätzen, die beim Spritzgießen verwendet werden
Hersteller können für die Herstellung von Einsätzen verschiedene Materialien verwenden, darunter Metall, Kunststoff und Keramik. Diese Einsätze ermöglichen die Herstellung von Teilen mit spezifischen Eigenschaften, die mit herkömmlichen Spritzgussverfahren nicht erreicht werden können. Hier besprechen wir die verschiedenen Arten von Einsätzen, die beim Spritzgießen verwendet werden.
- Metalleinsätze:Beim Spritzgießen werden häufig Metalleinsätze verwendet, um Kunststoffteilen zusätzliche Festigkeit und Stabilität zu verleihen. Sie bestehen typischerweise aus Messing, Stahl oder Aluminium und können je nach Anwendung mit oder ohne Gewinde ausgestattet sein. Hersteller können Metalleinsätze verwenden, um Teile mit komplexen Geometrien und Faktoren herzustellen, die eine hohe Festigkeit und Haltbarkeit erfordern.
- Kunststoffeinsätze: Kunststoffeinlagen werden im Spritzguss häufig zur Unterstützung und Verstärkung von Kunststoffteilen eingesetzt. Sie bestehen in der Regel aus Nylon-, ABS- oder Polycarbonatmaterialien und können Teile mit spezifischen Merkmalen wie Schnappverbindungen oder Gewindelöchern herstellen. Hersteller schätzen Kunststoffeinsätze wegen ihrer Fähigkeit, leichte, kostengünstige Lösungen anzubieten und sich leicht in verschiedene Formen und Größen formen zu lassen.
- Keramikeinsätze: Keramikeinsätze werden beim Spritzgießen verwendet, um Teile herzustellen, die eine hohe Festigkeit und Verschleißfestigkeit erfordern. Sie bestehen typischerweise aus Materialien wie Zirkonoxid oder Aluminiumoxid und können zur Herstellung von Teilen für die Automobil-, Luft- und Raumfahrtindustrie sowie die Medizinindustrie verwendet werden. Keramikeinsätze sind äußerst beständig gegen hohe Temperaturen, Korrosion und Abrieb und eignen sich daher ideal für raue Umgebungen.
- Verbundeinsätze: Hersteller kombinieren zwei oder mehr Materialien wie Metall und Kunststoff und formen sie zu Verbundeinsätzen, wodurch ein einziges, integriertes Teil entsteht. Hersteller können gemischte Einsätze verwenden, um Teile mit spezifischen Eigenschaften zu entwickeln, die mit herkömmlichen Spritzgussverfahren nicht erreicht werden können. Darüber hinaus können sie diese Einsätze individuell an die individuellen Anforderungen bestimmter Anwendungen anpassen.
- Umspritzte Einsätze: Während des Spritzgussverfahrens formen Hersteller Einsätze in ein Kunststoffteil, was zu sogenannten überspritzten Einsätzen führt. Bei diesem Verfahren wird eine erste Kunststoffschicht um den Einsatz herum entwickelt und dann eine zweite Schicht über der ersten Schicht angebracht, um ein einzelnes, integriertes Teil zu schaffen. Hersteller verwenden häufig umspritzte Einsätze, um Teile herzustellen, die Materialien kombinieren, beispielsweise um einen Metalleinsatz in eine Kunststoffkomponente zu integrieren.
Metalleinsätze vs. Kunststoffeinsätze
Bei diesem Verfahren werden vorgeformte Teile oder Einsätze verwendet, die vor Beginn des Kunststoffspritzgussprozesses in eine Form eingelegt werden. Hersteller können Einsätze aus verschiedenen Materialien herstellen, darunter Metall und Kunststoff, und jeder Typ weist seine einzigartigen Vor- und Nachteile auf. Dieser Artikel vergleicht Metall- und Kunststoffeinsätze und hilft Ihnen dabei, die beste Option für Ihre Anwendung zu ermitteln.
Metalleinsätze
Aufgrund ihrer hohen Festigkeit und Haltbarkeit verwenden Hersteller beim Formen häufig Metalleinsätze. Sie bestehen typischerweise aus Messing, Stahl oder Aluminium und können je nach Anwendung mit oder ohne Gewinde ausgestattet sein. Beim Spritzgießen werden häufig Metalleinlagen verwendet, um Kunststoffteilen zusätzliche Festigkeit und Stabilität zu verleihen.
Vorteile von Metalleinsätzen
- Hohe Festigkeit und Haltbarkeit
- Beständig gegen Verschleiß
- Es kann durch Threading zusätzliche Funktionalität bieten
- Ideal für Teile mit hohen Beanspruchungen oder Belastungsanforderungen
Nachteile von Metalleinsätzen
- Höhere Kosten als Kunststoffeinsätze
- Schwieriger zu formen als Kunststoffeinsätze
- Schwer, was bei bestimmten Anwendungen ein Problem darstellen kann
Kunststoffeinsätze
Kunststoffeinsätze werden aufgrund ihrer Vielseitigkeit und Kosteneffizienz gerne zum Formen verwendet. Hersteller fertigen sie in der Regel aus Materialien wie Nylon, ABS oder Polycarbonat und können sie leicht in verschiedene Formen und Größen formen. Kunststoffeinsätze sind leicht und ermöglichen die Herstellung von Teilen mit spezifischen Merkmalen, wie z. B. Schnappverbindungen oder Gewindelöchern.
Vorteile von Kunststoffeinsätzen
- Kosteneffizient
- Leichtgewicht
- Lässt sich leicht in verschiedene Formen und Größen formen
- Ideal für Teile mit geringerer Beanspruchung oder Tragfähigkeitsanforderungen
Nachteile von Kunststoffeinsätzen
- Weniger haltbar als Metalleinsätze
- Nicht ideal für Teile mit hohen Belastungs- oder Traganforderungen
- Mit der Zeit kann es anfälliger für Abnutzung sein
Wann sollten Sie Metalleinsätze wählen?
Metalleinsätze eignen sich hervorragend für Teile, die eine hohe Festigkeit und Haltbarkeit erfordern, da sie verschleißfest sind und die zusätzliche Funktionalität eines Gewindes bieten. Metalleinlagen eignen sich auch hervorragend für Funktionen mit hohen Beanspruchungen oder Belastungsanforderungen. Sie sind jedoch teurer als Kunststoffeinsätze und möglicherweise schwieriger zu formen.
Zu den Anwendungen, die möglicherweise Metalleinsätze erfordern, gehören:
- Automobil- und Luft- und Raumfahrtkomponenten
- Medizinische Geräte
- Industrielle Ausrüstung
- Unterhaltungselektronik
Wann sollten Sie Kunststoffeinsätze wählen?
Kunststoffeinsätze sind kostengünstig und vielseitig für Teile mit geringeren Belastungs- oder Tragfähigkeitsanforderungen. Sie weisen leichte Eigenschaften auf; Hersteller können sie in verschiedenen Formen und Größen formen. Kunststoffeinsätze eignen sich auch ideal für Positionen, die besondere Merkmale wie Schnappverbindungen oder Gewindelöcher erfordern. Für Details mit hohen Belastungs- oder Tragfähigkeitsanforderungen müssen sie jedoch möglicherweise besser geeignet sein.
Anwendungen, die möglicherweise Kunststoffeinsätze erfordern, sind im Lieferumfang enthalten
- Konsumgüter
- Haushaltsgeräte
- Spielsachen und Spiele
- Elektronik
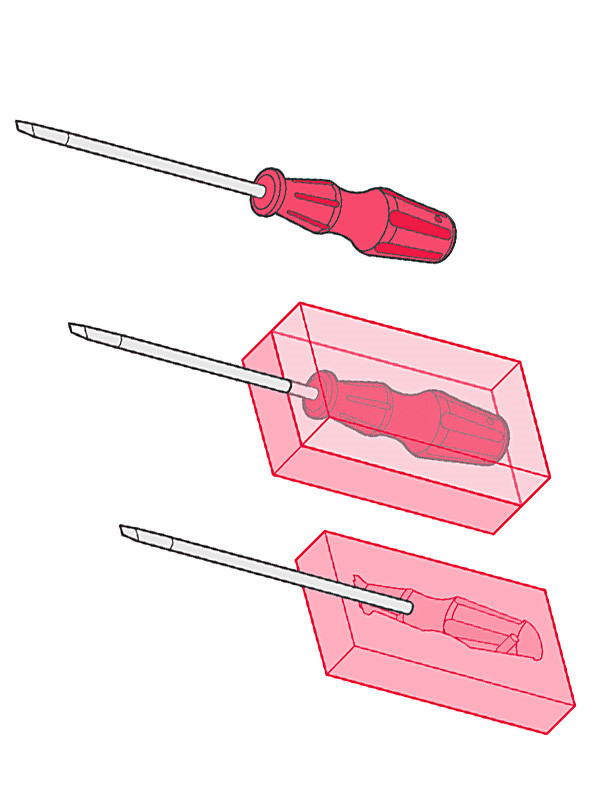
Vorteile des Insert-Spritzgießens
Das Einlegespritzgießen ist ein beliebtes Herstellungsverfahren, bei dem vorgeformte Teile oder Einsätze in eine Form eingelegt werden, bevor der Kunststoffspritzgussprozess beginnt. Diese Technik bietet zahlreiche Vorteile gegenüber herkömmlichen Formverfahren und ist daher eine beliebte Wahl für verschiedene Anwendungen. In diesem Artikel werden einige der Hauptvorteile des Einlegespritzgießens erläutert.
- Kosteneffizient: Das Spritzgießen von Einsätzen kann eine kostengünstige Fertigungslösung sein, da es die Notwendigkeit der Montage separater Teile nach dem Spritzgießen überflüssig macht. Durch die Integration der Einsätze während des Formens können Hersteller die Arbeits- und Montagekosten senken und gleichzeitig die Produktionseffizienz steigern.
- Verbesserte Teilefestigkeit: Das Einlegespritzgießen kann die Festigkeit und Haltbarkeit von Teilen verbessern, indem in verschiedenen Bereichen des Teils unterschiedliche Materialien verwendet werden. Diese Funktion kann besonders bei Anwendungen von Vorteil sein, bei denen Details hohen Belastungen oder Belastungen standhalten müssen.
- Erhöhte Designflexibilität: Das Einlegespritzgießen bietet eine größere Designflexibilität, da komplexe Teile mit zahlreichen Merkmalen und Funktionen entstehen. Dieses Verfahren eignet sich gut für komplizierte Designs und Geometrien und ist daher die ideale Wahl für solche Details.
- Konsistenz und Genauigkeit: Das Einlegespritzgießen bietet eine hervorragende Konsistenz und Genauigkeit bei der Teileproduktion. Wir positionieren die vorgeformten Einsätze präzise in der Form und stellen so sicher, dass sie genau entsprechend den Anforderungen jedes Teils platziert werden. Dadurch erreichen wir einheitliche Abmessungen und eine außergewöhnliche Qualitätskontrolle der produzierten Teile.
- Reduzierte Zykluszeit: Das Einlegespritzgießen kann die Zykluszeit verkürzen, indem mehrere Schritte in einem einzigen Prozess kombiniert werden. Diese Methode kann Zeit sparen und die Produktivität steigern, insbesondere bei der Verarbeitung großer Produktionsmengen.
- Materialvielfalt: Das Einlegespritzgießen kann bei verschiedenen Materialien eingesetzt werden, darunter Kunststoff, Metall und Keramik. Hersteller können jetzt für jede Anwendung das am besten geeignete Material auswählen, indem sie Festigkeit, Haltbarkeit und Kosten berücksichtigen.
- Vorteile für die Umwelt: Das Spritzgießen von Einlegeteilen kann auch Vorteile für die Umwelt bieten, indem es den Abfall reduziert und den Materialeinsatz minimiert. Da wir die Einsätze präzise in die Form einlegen, entsteht weniger Materialabfall als bei herkömmlichen Formmethoden. Die Umsetzung kann zu einer Verringerung der Umweltbelastung und einer Reduzierung der Herstellungskosten führen.
Designüberlegungen für das Einsatzformen
Insert Moulding ist ein beliebtes Herstellungsverfahren, bei dem vorgeformte Einsätze in einen Kunststoffspritzgussprozess integriert werden. Diese Technik bietet zahlreiche Vorteile, darunter eine verbesserte Teilefestigkeit, geringere Montagekosten und eine größere Designflexibilität. Allerdings erfordert die Konstruktion von Teilen für das Umspritzen eine sorgfältige Berücksichtigung mehrerer Faktoren, um eine erfolgreiche und effiziente Produktion sicherzustellen. In diesem Artikel werden einige der wichtigsten Designüberlegungen für das Umspritzen besprochen.
- Platzierung einfügen: Die Platzierung des Einsatzes in der Form ist entscheidend für den Erfolg des Einsatzformprozesses. Der Einsatz muss präzise in der Form positioniert werden, um sicherzustellen, dass er während des Formvorgangs vollständig vom Kunststoffmaterial umschlossen wird. Designer müssen außerdem sicherstellen, dass der Einsatz den Fluss des Kunststoffmaterials nicht behindert oder Probleme mit der Trennfuge verursacht.
- Materialverträglichkeit: Die Auswahl der Materialien sowohl für das Einlegeteil als auch für das Kunststoffmaterial ist entscheidend für den Erfolg des Einlegeformverfahrens. Die Materialien müssen kompatibel sein, um Verbindungsprobleme oder Materialunverträglichkeiten zu vermeiden. Konstrukteure müssen die Materialeigenschaften wie Schmelzpunkt, Schrumpfung und Wärmeausdehnungskoeffizient sorgfältig berücksichtigen, um ein erfolgreiches Umspritzen zu gewährleisten.
- Teilegeometrie: Die Geometrie des Teils ist ein weiterer wichtiger Gesichtspunkt beim Umspritzen. Das Design muss eine ordnungsgemäße Füllung und Verpackung des Kunststoffmaterials um den Einsatz herum ermöglichen, um sicherzustellen, dass dieser vollständig eingekapselt ist. Die Teilegeometrie muss außerdem eine ausreichende Belüftung und Kühlung ermöglichen, um Probleme mit Verzug, Schrumpfung oder Einfallstellen zu vermeiden.
- Formschrägen und Hinterschnitte: Das Vorhandensein von Entformungsschrägen und Hinterschnitten kann die Formbarkeit eines Teils beim Umspritzen beeinträchtigen. Konstrukteure müssen die Platzierung und Geometrie von Entformungsschrägen und Hinterschnitten sorgfältig abwägen, um sicherzustellen, dass sie den Einsatz problemlos aus der Form entfernen können, ohne das Teil oder die Form zu beschädigen.
- Überlegungen zur Werkzeugausstattung: Die für das Umspritzen erforderlichen Werkzeuge können komplexer sein als bei herkömmlichen Formverfahren. Konstrukteure müssen das Formdesign sorgfältig abwägen, einschließlich der Platzierung und Geometrie des Einsatzes, des Angusses und der Entlüftung sowie aller notwendigen Nebenmaßnahmen. Darüber hinaus müssen die Werkzeuge in der Lage sein, enge Toleranzen einzuhalten, um eine ordnungsgemäße Platzierung der Einsätze sicherzustellen und Probleme mit der Teilequalität zu vermeiden.
Materialien, die beim Einlegespritzgießen verwendet werden
Das Einlegespritzgießen ist ein hochspezialisiertes Verfahren, mit dem komplexe Teile präzise und konsistent hergestellt werden. Bei diesem Verfahren werden vorgefertigte Elemente, sogenannte Einsätze, verwendet, die vor dem Spritzgießen in eine Form eingelegt werden. Diese Einsätze können aus verschiedenen Materialien hergestellt werden, jedes mit einzigartigen Eigenschaften und Vorteilen. Hier besprechen wir die am häufigsten beim Einlegespritzgießen verwendeten Materialien und ihre Vorteile.
Metallindustrie
Beim Spritzgießen werden häufig Einsätze aus Metallen wie Stahl, Aluminium und Messing verwendet. Diese Materialien bieten eine hervorragende Festigkeit und Haltbarkeit und eignen sich daher ideal für Teile, die eine hohe Verschleiß- und Reißfestigkeit erfordern. Darüber hinaus halten Metalleinsätze hohen Temperaturen stand und eignen sich daher für den Einsatz in anspruchsvollen Anwendungen wie der Luft- und Raumfahrt- und Automobilindustrie. Zu den spezifischen Vorteilen der Verwendung von Metalleinsätzen beim Spritzgießen gehören:
- Hohe Festigkeit und Haltbarkeit
- Ausgezeichnete Hitzebeständigkeit
- Korrosionsbeständigkeit
- Fähigkeit, hohem Druck und Stress standzuhalten
Kunststoffe
Kunststoffeinsätze werden auch häufig beim Spritzgießen verwendet, wobei Materialien wie PEEK, PTFE und UHMW eine beliebte Wahl sind. Diese Materialien bieten ein hohes Maß an Temperaturbeständigkeit, chemischer Beständigkeit und geringen Reibungseigenschaften. Aufgrund ihrer hohen Präzision und Sauberkeit, die bei diesen Anwendungen entscheidende Faktoren sind, eignen sich diese Komponenten gut für den Einsatz in medizinischen Geräten und der Halbleiterfertigung. Zu den besonderen Vorteilen der Verwendung von Kunststoffeinsätzen im Spritzguss gehören:
- Hohe chemische Beständigkeit
- Hervorragende Temperaturbeständigkeit
- Eigenschaften mit geringer Reibung
- Leicht zu bearbeiten und zu formen
Keramik
Beim Spritzgießen finden Keramikeinsätze aufgrund ihrer hohen Festigkeit, Härte und Verschleißfestigkeit Verwendung. Diese Materialien eignen sich ideal für Anwendungen, bei denen das Teil hohen Temperaturen oder rauen Umgebungen standhalten muss. Darüber hinaus bieten Keramikeinsätze eine hervorragende Dimensionsstabilität und eignen sich daher für feinmechanische Anwendungen. Zu den spezifischen Vorteilen der Verwendung von Keramikeinsätzen beim Spritzgießen gehören:
- Hohe Festigkeit und Härte
- Hervorragende Verschleißfestigkeit
- Hohe Temperaturbeständigkeit
- Dimensionsstabilität
Composite
Verbundwerkstoffe wie Kohlefaser oder Glasfaser werden beim Spritzgießen aufgrund ihres hohen Festigkeits-Gewichts-Verhältnisses verwendet. Die Luft- und Raumfahrtindustrie sowie die Automobilindustrie verwenden diese Materialien häufig dort, wo Gewichtsreduzierung von entscheidender Bedeutung ist. Verbundeinsätze bieten eine hohe Steifigkeit und Festigkeit und eignen sich daher ideal für Windkraftanlagen und Hochleistungssportgeräteanwendungen. Zu den spezifischen Vorteilen der Verwendung von Verbundeinsätzen beim Spritzgießen gehören:
- Hohes Verhältnis von Festigkeit zu Gewicht
- Hohe Steifigkeit und Festigkeit
- Gute Schlagfestigkeit
- Niedriger thermischer Ausdehnungskoeffizient
Gummi
Gummimaterialien wie Silikon oder Neopren werden beim Spritzgießen aufgrund ihrer Flexibilität und Dichtungseigenschaften verwendet. Diese Materialien werden häufig in der Medizin- und Automobilindustrie verwendet, wo Abdichtung und Polsterung unerlässlich sind. Gummieinsätze bieten eine hervorragende Beständigkeit gegenüber Chemikalien und hohen Temperaturen und eignen sich daher ideal für den Einsatz in rauen Umgebungen. Zu den spezifischen Vorteilen der Verwendung von Gummieinlagen beim Spritzgießen gehören:
- Hervorragende Dichteigenschaften
- Hohe Flexibilität
- Chemikalien- und Temperaturbeständigkeit
- Gute Vibrationsdämpfung
Foam
Schaumstoffe wie Polyurethan oder Polystyrol werden beim Spritzgießen aufgrund ihrer leichten und stoßdämpfenden Eigenschaften verwendet. Diese Materialien werden häufig in der Verpackungs- und Automobilindustrie verwendet, wo Dämpfung und Schlagfestigkeit von entscheidender Bedeutung sind. Schaumstoffeinlagen bieten eine hohe Isolierung und sind daher ideal für temperaturempfindliche Anwendungen. Zu den besonderen Vorteilen der Verwendung von Schaumstoffeinlagen im Spritzguss gehören:
- Leicht und flexibel
- Hervorragende Stoßdämpfung
- Gute Isolationseigenschaften
- Seine Fähigkeit, komplexe Formen zu formen
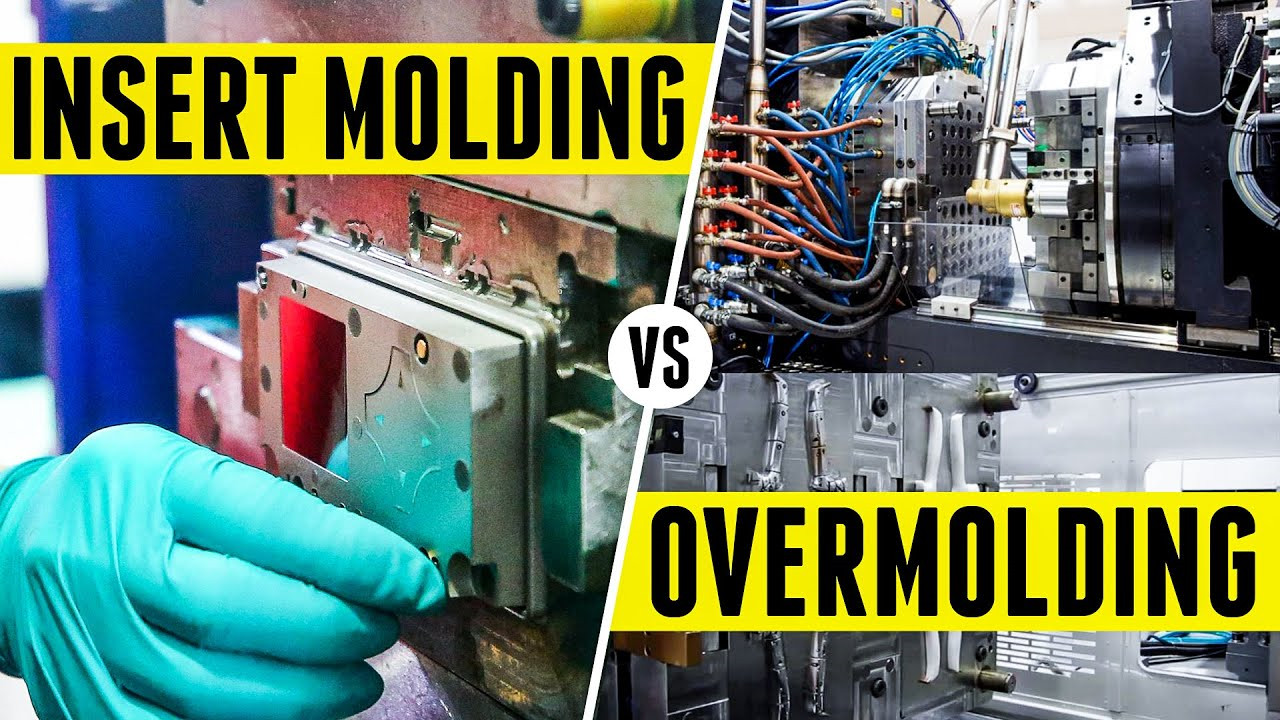
Insert Molding vs. Overmolding: Was ist der Unterschied?
Umspritzen und Umspritzen sind zwei häufig verwendete Verfahren beim Spritzgießen mehrerer Materialien. Obwohl diese Prozesse ähnlich erscheinen mögen, weisen sie einige grundlegende Unterschiede auf. Hier besprechen wir die Unterschiede zwischen Umspritzen und Umspritzen.
Formteil einlegen
Beim Insert Moulding handelt es sich um ein Verfahren, bei dem vorgefertigte Teile, sogenannte Inserts, in eine Form eingelegt werden, bevor der Spritzgussprozess stattfindet. Anschließend wird das Kunststoffmaterial um die Einsätze herumgespritzt, wodurch ein fertiges Produkt entsteht, das die Eigenschaften des Einsatzes und des Kunststoffmaterials vereint. Dieses Verfahren wird häufig in der Automobil-, Medizin- und Luft- und Raumfahrtindustrie eingesetzt, um Teile mit einem hohen Maß an Präzision herzustellen.
Vorteile des Umspritzens
- Hohe Präzision und Genauigkeit
- Verbesserte Teilefestigkeit und Haltbarkeit
- Reduzierte Montagezeit und -kosten
- Fähigkeit, Materialien mit unterschiedlichen Eigenschaften zu kombinieren
Umspritzen
Beim Umspritzen handelt es sich um einen Prozess, bei dem ein zweites Material über ein bereits vorhandenes Teil gespritzt wird. Hersteller verwenden dieses Verfahren, um Soft-Touch-Griffe, Griffe und andere Verbraucherprodukte herzustellen. Das umspritzte Material ist typischerweise weich und gummiartig und bietet verbesserten Halt und Komfort. Abhängig von der Komplexität des Teils können wir das Umspritzen im Ein- oder Zwei-Schuss-Verfahren durchführen.
Vorteile des Überformens
- Verbesserte Ergonomie und Ästhetik
- Verbesserter Halt und Komfort
- Reduzierte Montagezeit und -kosten
- Fähigkeit, Materialien mit unterschiedlichen Eigenschaften zu kombinieren
Unterschiede zwischen Umspritzen und Umspritzen
- Beim Insert-Molding werden vorgefertigte Teile eingefügt, beim Overmolding wird ein zweites Material über ein bereits vorhandenes Teil gespritzt.
- Wir nutzen das Umspritzen, um Teile mit einem hohen Maß an Präzision herzustellen, während wir das Umformen einsetzen, um die Ergonomie und Ästhetik eines Produkts zu verbessern.
- Bei der Umspritzung werden Materialien mit unterschiedlichen Eigenschaften kombiniert, während beim Umspritzen ein weiches, gummiartiges Material für den umspritzten Teil verwendet wird.
- Umspritzen wird häufig in der Automobil-, Medizin- und Luft- und Raumfahrtindustrie eingesetzt, während Umspritzen häufig bei Konsumgütern wie Werkzeugen, Elektronik und Körperpflegeartikeln zum Einsatz kommt.
Techniken zur Insert-Platzierung
Beim Insert-Molding handelt es sich um einen Prozess, bei dem vorgefertigte Teile oder Einsätze in eine Form eingelegt werden, bevor der Spritzgussprozess erfolgt. Das Kunststoffmaterial wird um die Einsätze herumgespritzt, um ein fertiges Produkt zu schaffen. Die Platzierung der Einsätze ist entscheidend für den Erfolg des Insert-Molding-Prozesses. Hier besprechen wir einige Techniken für die Platzierung von Einsätzen.
- Manuelle Platzierung: Bei dieser Technik platziert ein Bediener die Einsätze manuell in der Form. Hersteller verwenden diese Technik üblicherweise für kleine oder einfache Teile, die nur wenige Einsätze erfordern. Dies kann jedoch zeitaufwändig und arbeitsintensiv sein und es besteht ein höheres Fehlerrisiko aufgrund der manuellen Platzierung.
- Automatisierte Platzierung: Bei dieser Technik werden die Einsätze mithilfe eines computergestützten Systems, beispielsweise eines Roboters oder einer Bestückungsmaschine, in die Form eingelegt. Diese Technik ist schneller und genauer als die manuelle Platzierung und eignet sich daher ideal für große Produktionsläufe oder komplexe Teile. Es erfordert jedoch eine Anfangsinvestition in die Ausrüstung und muss für die Produktion in kleinem Maßstab möglicherweise kostengünstiger sein.
- Umspritzen mit Insert Moulding: Wir platzieren die Einsätze in einem zweiten, überspritzten Teil und positionieren es dann in der Primärform. Hersteller verwenden diese Technik häufig für Schadensfälle mit komplexen Geometrien oder schwer zugänglichen Bereichen. Es können auch Materialien mit unterschiedlichen Eigenschaften kombiniert werden, beispielsweise ein starrer Kunststoffeinsatz mit einem weichen Formmaterial.
- Selbstklebende Einlagen:Bei dieser Technik beschichten wir die Einsätze vorab mit einem Kleberücken, sodass wir sie ohne manuelle oder automatisierte Platzierung in die Form einlegen können. Der Kleberücken schmilzt beim Spritzgießen und verbindet den Einleger mit dem Kunststoffmaterial. Diese Technik wird üblicherweise für kleine, einfache Teile verwendet und kann die Produktionszeit und -kosten reduzieren.
- Gewindeeinsätze: Bei dieser Technik werden Gewindeeinsätze in die Form eingesetzt und zur Herstellung von Gewinden im fertigen Produkt verwendet. Hersteller verwenden diese Technik häufig bei der Herstellung von Produkten, die das Einsetzen einer Schraube oder eines Bolzens erfordern, wie z. B. elektronische Geräte oder Automobilteile.
Arten von Einlegespritzgießmaschinen
Eine der Schlüsselkomponenten des Spritzgießprozesses ist die Spritzgießmaschine. Diese Maschinen gibt es in verschiedenen Ausführungen, jede mit einzigartigen Merkmalen und Vorteilen. Hier sehen wir uns die verschiedenen Arten von Einlegespritzgießmaschinen an.
Lassen Sie uns zunächst definieren, was eine Einlegespritzgießmaschine ist. Bei einer Einlegespritzgießmaschine handelt es sich um eine Spritzgießmaschine, die das Einlegen vorgeformter Bauteile wie Metall- oder Kunststoffeinsätze in die Form vor dem Einspritzen des Kunststoffmaterials ermöglicht. Mit dieser Fähigkeit ist es möglich, komplexe Teile herzustellen, die zusätzliche Merkmale wie Gewindeöffnungen oder Metallstützen erfordern.
Hier sind die verschiedenen Arten von Einlegespritzgießmaschinen:
- Vertikale Spritzgießmaschinen:Diese Maschinen haben eine vertikale Ausrichtung, bei der die Form vertikal montiert wird. Sie sind ideal für das Einlegeformen, da sie ein einfaches Einführen des Einlegeteils in die Form von oben ermöglichen. Dieser Maschinentyp benötigt außerdem weniger Stellfläche und eignet sich besser für kleinere Produktionsläufe.
- Horizontale Spritzgießmaschinen:Diese Maschinen haben ein flaches Ausrichtungsdesign, bei dem die Form horizontal montiert wird. Sie eignen sich am besten für größere Produktionsläufe und werden von Herstellern in der Regel für die Herstellung wichtigerer Teile eingesetzt. Bei horizontalen Maschinen können die Einsätze von der Seite geladen werden, wodurch es schwieriger wird, die richtige Ausrichtung sicherzustellen.
- Rundtisch-Spritzgießmaschinen:Diese Maschinen verfügen über einen Drehtisch, der es ermöglicht, mehrere Formen zu montieren und für die Produktion in die Spritzeinheit zu drehen. Dieser Maschinentyp ist ideal für das Einlegegießen, da er verschiedene Einsätze in die Form ermöglicht und so komplexere Teile erzeugt.
- Shuttle-Spritzgießmaschinen: Diese Maschinen verfügen über einen Shuttle, der die Form zwischen der Spritzeinheit und dem Formbereich hin und her bewegt. Sie eignen sich am besten für kleine Produktionsläufe und sind ideal für das Einlegespritzen, da sie ein einfaches Be- und Entladen der Einlegeteile ermöglichen.
Prozessparameter für das Umspritzen von Einsätzen
Das resultierende Produkt weist im Vergleich zum herkömmlichen Spritzguss eine höhere Festigkeit und Haltbarkeit auf. Die Prozessparameter beim Umspritzen sind entscheidend für die Erzielung qualitativ hochwertiger und konsistenter Ergebnisse. Hier betrachten wir die Prozessparameter für das Umspritzen.
- Materialauswahl: Die Materialauswahl ist ein wesentlicher Prozessparameter beim Umspritzen. Das Kunststoffmaterial muss mit dem Einsatzmaterial und der Anwendung kompatibel sein. Die Kompatibilität stellt sicher, dass der Einsatz und das Kunststoffmaterial gut haften, was zu einem starken und langlebigen Produkt führt.
- Temperatur: Die Temperatur spielt beim Umspritzen eine entscheidende Rolle. Wir müssen die Formtemperatur richtig einstellen, um sicherzustellen, dass das Kunststoffmaterial gleichmäßig fließt und die Kavität ohne Hohlräume oder Verformungen füllt. Wir müssen auch die Temperatur des Einsatzes berücksichtigen, um sicherzustellen, dass das Kunststoffmaterial gut am Einsatz haftet, ohne thermische Schäden zu verursachen.
- Einspritzdruck: Der Einspritzdruck ist ein weiterer wesentlicher Parameter beim Umspritzen. Wir müssen die Spannung richtig einstellen, um sicherzustellen, dass wir das Kunststoffmaterial gleichmäßig und schnell in den Formhohlraum einspritzen. Ein hoher Einspritzdruck kann zu einer Verformung des Einlegeteils oder der Form führen, während ein niedriger Einspritzdruck zu einer unvollständigen Füllung des Formhohlraums führen kann.
- Einspritzgeschwindigkeit: Auch beim Umspritzen ist die Einspritzgeschwindigkeit ein wesentlicher Parameter. Wir müssen die Rate richtig einstellen, um sicherzustellen, dass das Kunststoffmaterial den Formhohlraum gleichmäßig und ohne Hohlräume oder Verformungen füllt. Eine hohe Einspritzgeschwindigkeit kann zu Turbulenzen im Kunststoffmaterial führen, was zu Fehlern im Endprodukt führen kann.
- Kühlzeit: Die Abkühlzeit ist erforderlich, damit sich das Kunststoffmaterial verfestigt und die endgültige Produktform erhält. Wir müssen die Abkühlzeit richtig einstellen, um sicherzustellen, dass das fertige Produkt die gewünschte Form und Größe erhält. Eine kürzere Abkühlzeit kann zu Verformung oder Schrumpfung führen, während eine längere Abkühlzeit zu längeren Zykluszeiten und verringerter Produktivität führen kann.
- Auswurfzeit: Wir benötigen die Auswurfzeit, um das fertige Produkt aus der Form auszuwerfen. Wir müssen die Auswurfzeit richtig einstellen, um das fertige Produkt ohne Beschädigung oder Verformung zu entnehmen. Eine kürzere Auswurfzeit kann zu einem unvollständigen Auswurf oder einer Beschädigung des Produkts führen, während eine längere Auswurfzeit zu längeren Zykluszeiten und verringerter Produktivität führen kann.
Häufige Fehler bei der Einlegeformung und wie man sie vermeidet
Das Einsatzformen ist ein beliebtes Herstellungsverfahren, bei dem vorgeformte Komponenten wie Metall- oder Kunststoffeinsätze in die Form eingelegt werden, bevor das Kunststoffmaterial eingespritzt wird. Dieses Verfahren führt zu substanzielleren und langlebigeren Produkten als beim herkömmlichen Spritzgießen. Allerdings kann das Umspritzen, wie jedes andere Herstellungsverfahren, Mängel aufweisen, die sich auf die Qualität und Konsistenz des Endprodukts auswirken. Hier werfen wir einen genaueren Blick auf häufige Fehler beim Einspritzen von Einlegeteilen und wie man sie vermeidet.
Blitz: Grat ist ein Defekt, der auftritt, wenn überschüssiges Kunststoffmaterial aus der Form austritt und eine dünne Schicht auf der Oberfläche des fertigen Produkts bildet. Dieser Mangel kann das Aussehen und die Funktion des Produkts beeinträchtigen. Um Flash zu vermeiden, können Sie die folgenden Schritte unternehmen:
- Reduzieren Sie den Einspritzdruck
- Erhöhen Sie die Schließkraft der Form
- Verwenden Sie ein Formtrennmittel
- Erhöhen Sie die Abkühlzeit
Kurzer Schuss: Ein zu geringer Schuss ist ein Fehler, der auftritt, wenn das Kunststoffmaterial den Formhohlraum nicht ausfüllt, was zu einem unvollständigen oder zu kleinen Produkt führt. Um einen Kurzschuss zu vermeiden, können Sie folgende Schritte unternehmen:
- Erhöhen Sie den Einspritzdruck
- Erhöhen Sie die Einspritzgeschwindigkeit
- Erhöhen Sie die Materialtemperatur
- Erhöhen Sie die Formtemperatur
Verzug: Verzug ist ein Mangel, wenn sich das fertige Produkt aufgrund ungleichmäßiger Abkühlung oder Schrumpfung verformt oder verdreht. Um Verzug zu vermeiden, können Sie die folgenden Schritte unternehmen:
- Erhöhen Sie die Formtemperatur
- Erhöhen Sie die Abkühlzeit
- Erhöhen Sie den Packungsdruck
- Verwenden Sie ein ausgewogenes Kühlsystem
Einfallstellen: Einfallstellen sind Vertiefungen oder Vertiefungen, die auf der Oberfläche des fertigen Produkts aufgrund ungleichmäßiger Abkühlung oder Schrumpfung entstehen. Um Einfallstellen zu vermeiden, können Sie folgende Maßnahmen ergreifen:
- Erhöhen Sie die Formtemperatur
- Erhöhen Sie die Abkühlzeit
- Erhöhen Sie den Packungsdruck
- Verwenden Sie dickere Wände oder Rippen, um das Produkt zu verstärken
Delaminierung: Delaminierung ist ein Fehler, der auftritt, wenn sich das Kunststoffmaterial und das Einsatzmaterial nicht richtig verbinden, was zu einer Trennung oder einem Ablösen führt. Um eine Delamination zu vermeiden, können Sie folgende Schritte unternehmen:
- Verwenden Sie ein kompatibles Kunststoffmaterial und setzen Sie das Dosenmaterial ein
- Erhöhen Sie den Einspritzdruck und die Geschwindigkeit
- Erhöhen Sie die Einsatztemperatur
- Erhöhen Sie die Formtemperatur
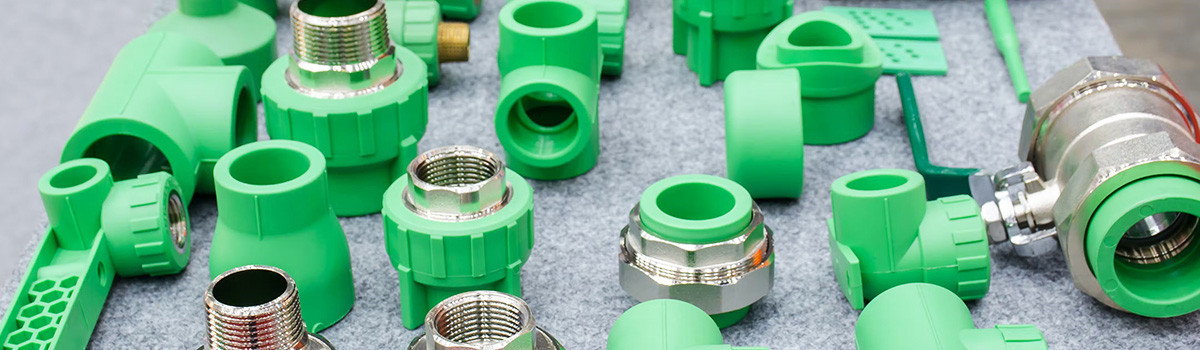
Nachbearbeitungsvorgänge für das Umspritzen von Einsätzen
Nach Abschluss des Umspritzprozesses müssen wir jedoch mehrere Nachformvorgänge durchführen, um sicherzustellen, dass das Endprodukt den gewünschten Spezifikationen entspricht. Hier werfen wir einen genaueren Blick auf die Nachbearbeitungsvorgänge für das Umspritzen von Einlegeteilen.
- Entgraten:Beim Entgraten handelt es sich um einen Prozess, bei dem überschüssiges Material wie Grate oder Grate vom fertigen Produkt entfernt werden. Dieser Vorgang kann je nach Größe und Komplexität des Produkts manuell oder automatisch durchgeführt werden.
- Trimmen:Beim Trimmen handelt es sich um einen Vorgang, bei dem überschüssiges Material oder Vorsprünge vom fertigen Produkt entfernt werden. Dieser Vorgang kann je nach Form und Größe des Produkts mit verschiedenen Schneidwerkzeugen oder -methoden durchgeführt werden.
- Reinigung: Beim Reinigen handelt es sich um einen Prozess, bei dem jeglicher Schmutz, Ablagerungen oder Verunreinigungen vom fertigen Produkt entfernt werden. Dieser Prozess kann mit verschiedenen Reinigungsmitteln oder -methoden durchgeführt werden, abhängig von der Art des Materials, das beim Umspritzen verwendet wird.
- Montage:Bei der Montage handelt es sich um einen Prozess, bei dem mehrere Komponenten zu einem fertigen Produkt zusammengefügt werden. Dieser Prozess kann je nach Materialart und gewünschtem Endprodukt mit verschiedenen Methoden wie Ultraschallschweißen, Heißprägen oder Kleben durchgeführt werden.
- Testing: Beim Testen handelt es sich um einen Prozess, der sicherstellt, dass das fertige Produkt den gewünschten Spezifikationen und Qualitätsstandards entspricht. Dieser Prozess kann je nach Produkttyp und Verwendungszweck unterschiedliche Tests umfassen, beispielsweise mechanische, elektrische oder visuelle Inspektionen.
Zusätzlich zu diesen Post-Molding-Vorgängen müssen bei der Gestaltung eines Insert-Molding-Prozesses auch mehrere Faktoren berücksichtigt werden, die den Bedarf an Post-Molding-Vorgängen minimieren. Diese beinhalten:
- Auswahl der geeigneten Materialien für den Einleger und das Formteil
- Sicherstellen, dass der Einsatz während des Formvorgangs richtig positioniert und an Ort und Stelle gehalten wird
- Anpassen der Formparameter wie Temperatur und Druck, um Defekte und überschüssiges Material zu minimieren
- Verwendung hochwertiger Formen und Geräte, um Konsistenz und Genauigkeit des Endprodukts sicherzustellen
Anwendungen des Einlegespritzgießens
Das Einlegespritzgießen ist ein äußerst vielseitiges Herstellungsverfahren, das in vielen Branchen zur Herstellung hochwertiger, komplexer Teile mit größerer Festigkeit und Haltbarkeit eingesetzt wird. Hier werfen wir einen genaueren Blick auf die Anwendungen des Einlegespritzgießens und seine Vorteile für verschiedene Branchen.
- Automobilindustrie:Die Automobilindustrie ist einer der bedeutendsten Anwender des Einlegespritzgießens. Es findet Verwendung bei der Herstellung verschiedener Komponenten, darunter Airbaggehäuse, Sicherheitsgurte und Motorkomponenten. Das Verfahren ermöglicht das präzise und genaue Formen von Teilen, die den rauen Bedingungen im Automobileinsatz standhalten.
- Elektronik-Industrie:Auch die Elektronikindustrie setzt bei der Herstellung von Komponenten für Geräte wie Smartphones, Laptops und andere elektronische Geräte stark auf das Einlegespritzgießen. Der Prozess findet Anwendung bei der Herstellung von Elementen wie Steckverbindern, Schaltern und Gehäusen für elektronische Komponenten. Der Prozess ist äußerst effizient und ermöglicht die schnelle und kostengünstige Herstellung großer Stückzahlen.
- Medizinische Industrie: Auch die Medizinbranche profitiert erheblich vom Einlegespritzgießen. Das Verfahren findet bei der Herstellung verschiedener Komponenten Anwendung, darunter chirurgische Instrumente, Arzneimittelverabreichungsgeräte und medizinische Implantate. Das Verfahren ermöglicht die präzise Formung von Elementen, die den Belastungen im medizinischen Einsatz standhalten, und ermöglicht die Produktion großer Stückzahlen.
- Luft-und Raumfahrtindustrie: Die Luft- und Raumfahrtindustrie ist eine weitere Branche, in der das Einlegespritzgießen in großem Umfang zum Einsatz kommt. Anwendung findet das Verfahren bei der Herstellung von Bauteilen wie Luftkanälen, Halterungen und Gehäusen für Flugzeugkomponenten. Das Verfahren ermöglicht die Herstellung hochfester Bauteile, die den hohen Belastungen und extremen Temperaturen im Luft- und Raumfahrteinsatz standhalten.
- Konsumgüterindustrie: Die Konsumgüterindustrie nutzt das Einlegespritzgießen in großem Umfang zur Herstellung einer breiten Palette von Produkten wie Spielzeug, Haushaltsgeräten und Sportgeräten. Der Prozess ermöglicht die Herstellung hochwertiger, langlebiger, leichter und ästhetisch ansprechender Komponenten.
Neben diesen Branchen wird das Einlegespritzgießen auch in vielen anderen Anwendungen eingesetzt, darunter:
- Verpackungsindustrie: zur Herstellung von Kappen, Verschlüssen und anderen Verpackungskomponenten
- Baugewerbe: zur Herstellung von Rohren, Formstücken und anderen Bauelementen
- Militärindustrie: zur Herstellung von Teilen für Militärfahrzeuge und -ausrüstung
Anwendungen in der Automobilindustrie
Die Automobilindustrie ist einer der bedeutendsten Anwender des Kunststoffspritzgusses, da er eine kostengünstige und effiziente Möglichkeit zur Herstellung komplexer Fahrzeugkomponenten darstellt. Hier werfen wir einen genaueren Blick auf die verschiedenen Anwendungen des Kunststoffspritzgusses in der Automobilindustrie.
- Innenkomponenten: Der Innenraum eines Fahrzeugs besteht aus mehreren Kunststoffkomponenten, die für die Gesamtästhetik und Funktionalität des Fahrzeugs wesentlich sind. Zu diesen Komponenten gehören ein Armaturenbrett, Türverkleidungen, Lüftungsschlitze der Klimaanlage und Lenkradkomponenten. Das Spritzgießen ermöglicht die schnelle und kostengünstige Produktion dieser Teile in großen Stückzahlen bei gleichzeitig hoher Genauigkeit.
- Außenkomponenten: Das Äußere eines Fahrzeugs besteht aus mehreren Kunststoffkomponenten, darunter Stoßstangenabdeckungen, Scheinwerferbaugruppen und Rücklichtbaugruppen. Beim Spritzgießen werden diese Komponenten mit hoher Präzision hergestellt und stellen so sicher, dass sie den strengen Sicherheits- und Qualitätsstandards der Automobilindustrie entsprechen.
- Motorkomponenten: Spritzguss findet auch bei der Herstellung verschiedener Motorkomponenten Anwendung, darunter Luftansaugkrümmer, Motorabdeckungen und Ölfilter. Wir müssen diese Komponenten nach strengen Toleranzen und Standards herstellen, und das Spritzgießen ermöglicht die Herstellung hochwertiger Zutaten, die diese Anforderungen erfüllen.
- Elektrische Bauteile: Auch die elektrischen Komponenten eines Fahrzeugs wie Stecker, Schalter und Sensorgehäuse werden im Spritzgussverfahren hergestellt. Diese Komponenten müssen langlebig sein und rauen Betriebsbedingungen standhalten, und das Spritzgießen ermöglicht die Herstellung hochwertiger Zutaten, die diesen Bedingungen standhalten.
- HVAC-Komponenten:Beim Spritzgießen werden mehrere Komponenten hergestellt, die im HVAC-System eines Fahrzeugs verwendet werden, darunter Klimakanäle und Lüftungsschlitze. Diese Komponenten müssen mit präzisen Toleranzen hergestellt werden, um eine ordnungsgemäße Luftzirkulation und Belüftung im Auto zu gewährleisten.
Zusätzlich zu diesen Anwendungen verwenden Hersteller das Spritzgießen, um mehrere andere Automobilkomponenten herzustellen, darunter Kraftstoff-, Brems- und Aufhängungssysteme.
Der Einsatz von Spritzguss in der Automobilindustrie bietet zahlreiche Vorteile, darunter:
- Hohe Effizienz:Das Spritzgießen ermöglicht die schnelle Herstellung hochwertiger Komponenten in großen Mengen und reduziert so Produktionszeiten und -kosten.
- Präzision:Das Spritzgießen ermöglicht die Herstellung von Bauteilen mit hoher Genauigkeit und Konsistenz und stellt sicher, dass sie strengen Qualitätsstandards entsprechen.
- Anpassung: Spritzguss ermöglicht die Herstellung komplexer Formen und Designs und ermöglicht es Herstellern, Komponenten individuell anzupassen, um spezifische Designanforderungen zu erfüllen.
Anwendungen in der medizinischen Industrie
In der Medizinindustrie kommt es auf Präzision und Zuverlässigkeit an und macht das Kunststoffspritzgießen zu einem idealen Herstellungsverfahren für die Herstellung medizinischer Komponenten. Hier werfen wir einen genaueren Blick auf die verschiedenen Anwendungen des Kunststoffspritzgusses in der Medizinbranche.
- Chirurgische Instrumente: Durch Spritzgießen werden viele chirurgische Instrumente hergestellt, darunter Pinzetten, Klemmen und Skalpelle. Hersteller müssen diese Komponenten mit strengen Toleranzen und Standards herstellen, um höchste Genauigkeit und Präzision zu gewährleisten.
- Medizinische Geräte:Hersteller nutzen Spritzguss auch zur Herstellung medizinischer Geräte wie Katheter und Beatmungskomponenten. Um die Sicherheit und Zuverlässigkeit der Patienten zu gewährleisten, müssen Hersteller diese Komponenten nach strengen Standards herstellen.
- Diagnosekomponenten: Hersteller verwenden Spritzguss, um verschiedene Komponenten herzustellen, die in Diagnosegeräten verwendet werden, beispielsweise Pipetten, Spritzen und Reagenzgläser. Diese Komponenten müssen mit präzisen Toleranzen hergestellt werden, um genaue Testergebnisse zu gewährleisten.
- Verpackung: Im Spritzgussverfahren werden Verpackungen für medizinische Produkte wie Sterilschalen, Behälter und Verpackungskomponenten hergestellt. Diese Komponenten müssen nach strengen Standards hergestellt werden, um die Sterilität und Sicherheit medizinischer Produkte zu gewährleisten.
- Dentalkomponenten: Beim Spritzgießen werden verschiedene Dentalkomponenten hergestellt, darunter Mundschutz, Schienen und kieferorthopädische Teile. Diese Komponenten müssen mit präzisen Toleranzen hergestellt werden, um die richtige Passform und den Komfort für den Patienten zu gewährleisten.
Zusätzlich zu diesen Anwendungen verwenden Hersteller das Spritzgießen zur Herstellung mehrerer anderer medizinischer Komponenten, darunter Prothesen, Hörgeräte und Laborgeräte.
Der Einsatz von Spritzguss in der Medizinbranche bietet zahlreiche Vorteile, darunter:
- Hohe Präzision:Das Spritzgießen ermöglicht die Herstellung von Bauteilen mit hoher Genauigkeit und Konsistenz und stellt sicher, dass sie strengen Qualitätsstandards entsprechen.
- Anpassung:Spritzguss ermöglicht die Herstellung komplexer Formen und Designs und ermöglicht es Herstellern, Komponenten individuell anzupassen, um spezifische Designanforderungen zu erfüllen.
- Kosteneffizient: Spritzgießen ist ein kostengünstiges Herstellungsverfahren, das hochwertige Komponenten in großen Mengen produziert und so Produktionszeiten und -kosten reduziert.
Anwendungen in der Elektronikindustrie
Die Elektronikindustrie ist ein Bereich, der stark auf präzise und effiziente Fertigungsprozesse angewiesen ist. Aufgrund seiner Genauigkeit, Vielseitigkeit und Geschwindigkeit ist das Kunststoffspritzgießen ein ideales Verfahren zur Herstellung elektronischer Komponenten. Hier werfen wir einen genaueren Blick auf die verschiedenen Anwendungen des Kunststoffspritzgusses in der Elektronikindustrie.
- Anschlüsse: Durch Spritzgießen wird eine breite Palette von Steckverbindern hergestellt, die in der Elektronikindustrie verwendet werden, darunter USB-Anschlüsse, HDMI-Anschlüsse und Audio-Buchsen. Diese Komponenten müssen mit präzisen Toleranzen hergestellt werden, um eine ordnungsgemäße Funktion und Kompatibilität sicherzustellen.
- Gehäuse und Gehäuse: Im Spritzgussverfahren werden Gehäuse und Gehäuse für elektronische Geräte hergestellt, darunter Mobiltelefone, Laptops und andere Unterhaltungselektronik. Hersteller müssen diese Komponenten nach präzisen Spezifikationen herstellen, um eine ordnungsgemäße Passform und Funktion sicherzustellen.
- Schalter: Beim Spritzgießen werden verschiedene Arten von Bedienelementen hergestellt, die in elektronischen Geräten verwendet werden, darunter Wippschalter, Druckschalter und Schiebeschalter. Um eine zuverlässige Funktion zu gewährleisten, müssen diese Komponenten mit genauen Toleranzen gefertigt werden.
- LED-Komponenten:Beim Spritzgießen werden verschiedene Komponenten hergestellt, die in der LED-Beleuchtung verwendet werden, darunter Linsen, Reflektoren und Diffusoren. Hersteller müssen diese Komponenten nach präzisen Spezifikationen herstellen, um eine ordnungsgemäße Lichtverteilung und Effizienz sicherzustellen.
- Netzteilkomponenten: Beim Spritzgießen werden verschiedene Komponenten für Netzteile hergestellt, darunter Steckdosen, Stecker und Kabelanschlüsse. Diese Komponenten müssen mit präzisen Toleranzen hergestellt werden, um einen sicheren und zuverlässigen Betrieb zu gewährleisten.
Zusätzlich zu diesen Anwendungen verwenden Hersteller das Spritzgießen, um mehrere andere elektronische Komponenten herzustellen, darunter Tastaturen, Computermäuse und Fernbedienungen.
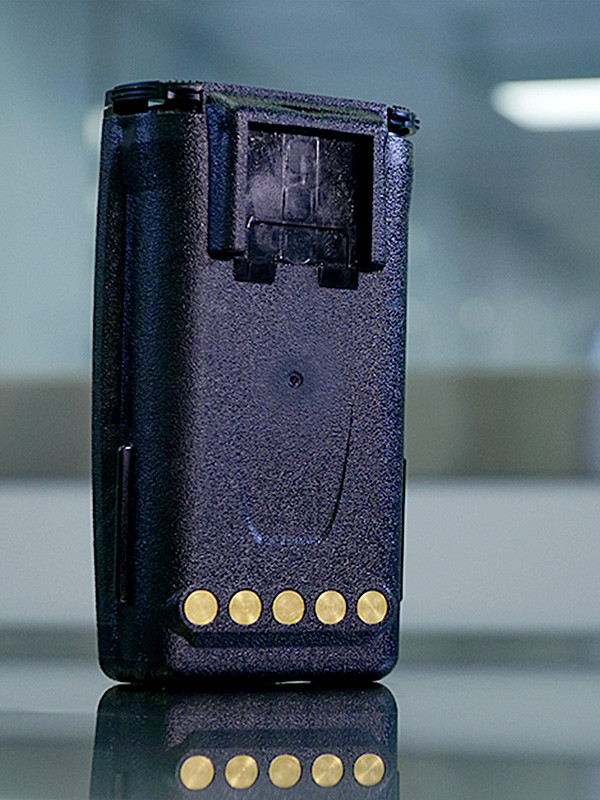
Der Einsatz von Spritzguss in der Elektronikindustrie bietet zahlreiche Vorteile, darunter:
- Hohe Präzision: Das Spritzgießen ermöglicht die Herstellung von Bauteilen mit hoher Genauigkeit und Konsistenz und stellt sicher, dass sie strengen Qualitätsstandards entsprechen.
- Anpassung: Spritzguss ermöglicht die Herstellung komplexer Formen und Designs und ermöglicht es Herstellern, Komponenten individuell anzupassen, um spezifische Designanforderungen zu erfüllen.
- Geschwindigkeit: Spritzgießen ist ein schnelles und effizientes Herstellungsverfahren, das die Herstellung hochwertiger Komponenten in großen Mengen ermöglicht und so Produktionszeiten und -kosten reduziert.
Anwendungen in der Luft- und Raumfahrtindustrie
Die Luft- und Raumfahrtindustrie ist ein Sektor, der ein Höchstmaß an Präzision, Genauigkeit und Haltbarkeit aller seiner Komponenten erfordert. Kunststoffspritzguss wird in der Luft- und Raumfahrtindustrie immer häufiger eingesetzt, da es die Möglichkeit bietet, komplexe Geometrien herzustellen, das Gewicht zu reduzieren und die strukturelle Integrität zu verbessern. Hier werfen wir einen genaueren Blick auf die verschiedenen Anwendungen des Kunststoffspritzgusses in der Luft- und Raumfahrtindustrie.
- Innenkomponenten: Durch Spritzgießen werden eine Reihe von Innenraumkomponenten für Flugzeuge hergestellt, darunter Sitzlehnen, Ablagetische und Gepäckfächer. Diese Komponenten müssen leicht und langlebig sein und hohen Belastungen und Abnutzungserscheinungen standhalten.
- Strukurelle Komponenten: Beim Spritzgießen werden Strukturbauteile für Flugzeuge hergestellt, darunter Flügelspitzen, Verkleidungen und Rumpfabschnitte. Diese Komponenten müssen leicht, stark und langlebig sein, um die Sicherheit und Effizienz des Flugzeugs zu gewährleisten.
- Motorkomponenten:Beim Spritzgießen werden verschiedene Komponenten für Flugzeugtriebwerke hergestellt, darunter Turbinenschaufeln, Treibstoffdüsen und Gehäuse. Diese Komponenten müssen nach präzisen Spezifikationen hergestellt werden, um hohen Temperaturen, Drücken und Belastungen standzuhalten.
- Elektrische Bauteile: Beim Spritzgießen werden elektrische Komponenten für Flugzeuge hergestellt, darunter Steckverbinder, Schalter und Kabelbäume. Diese Komponenten müssen mit präzisen Toleranzen hergestellt werden, um eine ordnungsgemäße Funktion und Zuverlässigkeit zu gewährleisten.
- Instrumentierungskomponenten:Im Spritzgussverfahren werden Instrumentierungskomponenten für Flugzeuge hergestellt, darunter Bedienfelder und Instrumentengehäuse. Diese Komponenten müssen langlebig sein und hohen Temperaturen, Drücken und Vibrationen standhalten.
Zusätzlich zu diesen Anwendungen verwenden Hersteller das Spritzgießen, um mehrere andere Komponenten für die Luft- und Raumfahrtindustrie herzustellen, darunter Halterungen, Befestigungselemente und Dichtungen.
Der Einsatz von Spritzguss in der Luft- und Raumfahrtindustrie bietet zahlreiche Vorteile, darunter:
- Gewichtsreduzierung: Das Spritzgießen ermöglicht die Herstellung von Leichtbauteilen, die das Gewicht des Flugzeugs reduzieren, was zu einem geringeren Treibstoffverbrauch und einer höheren Effizienz führt.
- Präzision:Das Spritzgießen ermöglicht die Herstellung von Teilen mit hoher Genauigkeit und Konsistenz und stellt sicher, dass sie strengen Qualitätsstandards entsprechen.
- Anpassung:Spritzguss ermöglicht die Herstellung komplexer Formen und Designs und ermöglicht es Herstellern, Komponenten individuell anzupassen, um spezifische Designanforderungen zu erfüllen.
- Haltbarkeit: IBeim Spritzgießen entstehen Teile, die langlebig sind und hohen Belastungen, Temperaturen und Drücken standhalten und so die Sicherheit und Zuverlässigkeit des Flugzeugs gewährleisten.
Anwendungen in der Konsumgüterindustrie
Die Konsumgüterindustrie ist einer der kritischsten Sektoren der Weltwirtschaft. Konsumgüter sind Produkte, die Menschen täglich nutzen, darunter Haushaltsgegenstände, Elektronik, Spielzeug und Körperpflegeprodukte. Kunststoffspritzguss erfreut sich in der Konsumgüterindustrie aufgrund seiner Fähigkeit, hochwertige Komponenten mit Präzision und Genauigkeit herzustellen, immer größerer Beliebtheit. Hier werfen wir einen genaueren Blick auf die verschiedenen Anwendungen des Kunststoffspritzgusses in der Konsumgüterindustrie.
- Verpackung: Spritzguss wird in großem Umfang bei der Herstellung von Verpackungsmaterialien für Konsumgüter eingesetzt, darunter Lebensmittelverpackungen, Getränkeflaschen und Kosmetikbehälter. Das Spritzgießen ermöglicht die Herstellung komplexer Formen und Designs und stellt sicher, dass die Verpackungsmaterialien funktional und optisch ansprechend sind.
- Haushaltsgegenstände: Im Spritzgussverfahren werden eine Reihe von Haushaltsgegenständen hergestellt, darunter Küchenutensilien, Vorratsbehälter und Reinigungsmittel. Diese Artikel müssen langlebig und leicht sein und dem täglichen Gebrauch standhalten.
- Spielzeuge: Im Spritzgussverfahren werden verschiedene Spielzeuge hergestellt, darunter Actionfiguren, Puppen und Brettspiele. Diese Spielzeuge müssen nach genauen Spezifikationen hergestellt werden, um sicherzustellen, dass sie sicher und langlebig sind.
- Körperpflegeprodukte: Im Spritzgussverfahren entstehen einzigartige Pflegeprodukte, darunter Zahnbürsten, Rasierer und Shampooflaschen. Diese Produkte müssen ästhetisch ansprechend und funktional sein und einer häufigen Nutzung standhalten.
- Elektronik: Beim Spritzgießen werden verschiedene Komponenten für elektronische Geräte hergestellt, darunter Gehäuse, Tasten und Anschlüsse. Diese Komponenten müssen langlebig und leicht sein und hohen Temperaturen und Drücken standhalten.
Zusätzlich zu diesen Anwendungen verwenden Hersteller das Spritzgießen, um mehrere andere Komponenten für die Konsumgüterindustrie herzustellen, darunter Automobilteile, medizinische Geräte und Industrieausrüstung.
Der Einsatz von Spritzguss in der Konsumgüterindustrie bietet zahlreiche Vorteile, darunter:
- Kosteneffizient:Spritzgießen ermöglicht die Herstellung hochwertiger Komponenten zu geringeren Kosten als andere Herstellungsverfahren.
- Anpassung: IDas Spritzgießen ermöglicht die Herstellung von Elementen mit komplexen Formen und Designs, sodass Hersteller Funktionen anpassen können, um spezifische Designanforderungen zu erfüllen.
- Präzision: Das Spritzgießen zeichnet sich durch hochpräzise und konsistente Details aus, die strengen Qualitätsstandards entsprechen.
- Haltbarkeit: Das Spritzgießen macht Teile langlebig und hält hohen Belastungen, Temperaturen und Drücken stand, wodurch die Sicherheit und Zuverlässigkeit der Produkte gewährleistet wird.
Zukünftige Trends beim Einlegespritzgießen
Da die Technologie voranschreitet und sich die Anforderungen der Verbraucher ändern, entwickelt sich die Einlegespritzgussindustrie ständig weiter. Hersteller suchen immer nach Möglichkeiten, die Effizienz zu verbessern, Kosten zu senken und qualitativ hochwertigere Produkte herzustellen. Hier werfen wir einen Blick auf einige zukünftige Trends beim Einlegespritzgießen.
- Automation: Die Automatisierung erfreut sich in der Fertigungsindustrie immer größerer Beliebtheit, und das Einlegespritzgießen bildet da keine Ausnahme. Automatisierte Systeme können die Arbeitskosten senken, die Produktionsgeschwindigkeit erhöhen und die Qualitätskontrolle verbessern.
- Nachhaltigkeit: Angesichts der wachsenden Umweltbedenken suchen Hersteller nach Möglichkeiten, Abfall zu reduzieren und die Nachhaltigkeit zu verbessern. Die Verwendung recycelter Materialien und die Entwicklung von Produkten, die leicht recycelt oder wiederverwendet werden können, sind nur einige Möglichkeiten, wie Hersteller dieses Problem angehen.
- 3D-Druck: Bei einigen Aspekten des Einlegespritzgießens kommt bereits der 3D-Druck zum Einsatz, es besteht jedoch das Potenzial, dass er in Zukunft noch stärker zum Einsatz kommt. Die Möglichkeit, schnell Prototypen zu erstellen und maßgeschneiderte Bauteile herzustellen, ist nur ein Vorteil des 3D-Drucks.
- Fortgeschrittene Werkstoffe: Forscher und Hersteller entwickeln neue Materialien, die verschiedenen Temperaturen, Drücken und Belastungen standhalten.
- Intelligente Fertigung:Bei der intelligenten Fertigung kommt es darauf an, mithilfe von Technologie Daten in Echtzeit zu sammeln und zu analysieren, was eine schnellere Entscheidungsfindung und eine effizientere Produktion ermöglicht. Diese Technologie kann die Qualitätskontrolle verbessern, Ausfallzeiten reduzieren und die Produktivität steigern.
Zusammenfassung
Das Einlegespritzgießen ist ein vielseitiges und kostengünstiges Herstellungsverfahren, das die Herstellung komplexer Teile mit eingebetteten Komponenten ermöglicht. Seine Vorteile gegenüber herkömmlichen Montagemethoden machen es in verschiedenen Branchen beliebt, darunter Automobil, Medizin, Elektronik, Luft- und Raumfahrt sowie Konsumgüter. Durch das Verständnis der verschiedenen Techniken, Materialien und Designüberlegungen beim Einlegespritzgießen können Hersteller ihre Produktionsprozesse optimieren und ihren Kunden qualitativ hochwertige Produkte liefern. Mit fortschreitender Technologie können wir mit noch innovativeren Anwendungen des Einlegespritzgießens rechnen.