Lösungen für häufige Formfehler beim Spritzgießen
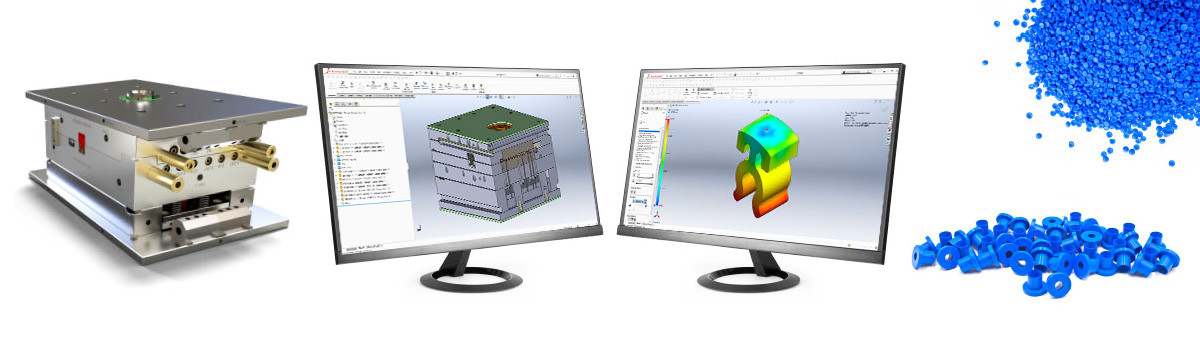
Bei der Verarbeitung von Kunststoffspritzgussteilen mit Formen treten häufig Mängel auf, die die Verarbeitungseffizienz erheblich beeinträchtigen. Im Folgenden sind häufige Formfehler und Lösungen für Kunststoffspritzgussteile aufgeführt.
Kurze Aufnahmen
Kurze Aufnahmen beziehen sich auf die hergestellten Produkte, die unvollständig sind, da die Formen nicht vollständig gefüllt sind.
Dieser Defekt tritt normalerweise an der Stelle auf, die am weitesten vom Anguss entfernt ist, oder an Teilen, die nur durch die engen Bereiche der Form erreicht werden können, da die engen Bereiche den Fluss der Schmelze beeinträchtigen können.
Ein zu kurzer Schuss kann zu Mikrofließspuren führen oder dazu führen, dass offensichtlich ein großer Teil des Produkts fehlt.
Ursache:
Zu den Ursachen für Kurzschüsse gehören:
Das in die Form eingespritzte Rohmaterial reicht nicht aus.
Der Widerstand von Schmelzen ist groß, so dass die Form nicht vollständig gefüllt werden kann.
Die Entlüftung der Form ist schlecht und es entsteht Kavitation, die die Schmelze blockiert und dazu führt, dass die Schmelze nicht in bestimmte Bereiche der Form fließen kann.
Grate
Grate entstehen durch das Anhaften von überschüssigem Rohmaterial, das aus dem Formhohlraum extrudiert wird, am Produkt.
Dieser Defekt tritt an den Kanten des Produkts oder an jedem aus Schimmel bestehenden Teil auf. Das Rohmaterial kann aus der Form oder den Verbindungsstellen der beweglichen und fixierenden Formen austreten.
Auch am Formkern sind Grate zu finden, die auf hydraulischen Druck oder schräge Stifte zurückzuführen sind.
Die Schwere der Grate ist unterschiedlich, mal dünn, mal dicker.
Ursache:
Ursachen für Grate sind:
Die Oberfläche der Spannform ist beschädigt oder stark abgenutzt.
Die bewegliche Form und die Fixierform werden verschoben, wenn sie verriegelt sind.
Der Druck des Rohmaterials in der Form ist höher als die Schließkraft der Form.
Die oben erwähnte dritte Bedingung würde sich aus verschiedenen Gründen ergeben. In den folgenden Situationen ist der Druck des Rohmaterials höher als die Schließkraft der Form.
In der ersten Phase der Spritzgussform (Formfüllphase) wird zu viel Rohmaterial eingefüllt, was den Druck im Inneren der Form erhöht.
Während des Füllvorgangs der Form erhöht ein großer Widerstand des Schmelzeflusses auch den Druck im Inneren der Form.
Der Druck im Formhohlraum ist während der Druckhaltephase zu hoch.
Die Schließkraft der Form reicht nicht aus.
Degradierung
Die Zerlegung könnte zu vielen Ergebnissen führen. Auch das Ausmaß und die Schwere des Problems variieren. Im schlimmsten Fall kann es zu einer vollständigen Verfärbung des Produkts und zu schlechten mechanischen Eigenschaften kommen. Lokaler Abbau führt lediglich zu dunklen Streifen oder Flecken.
Ursache:
Die Verschlechterung wird dadurch verursacht, dass das Rohmaterial beschädigt wird. Langkettige Moleküle, die Kunststoffe bilden, zersetzen sich unter Einwirkung übermäßiger Hitze oder übermäßiger Scherbeanspruchung. Bei der Zersetzung von Molekülen beschleunigt das flüchtige Gas den Abbauprozess, was zu einer Entfärbung des Rohmaterials führt. Durch die Zersetzung einer großen Menge an Molekülen wird der Inhalt des Rohmaterials zerstört und die mechanischen Eigenschaften werden negativ beeinflusst.
Eine örtliche Verschlechterung kann durch eine ungleichmäßige Temperatur des Materialzylinders verursacht werden.
In den folgenden Situationen kann es zu einer Verschlechterung kommen:
Das Rohmaterial wird im Materialbehälter oder im Heißkanalsystem überhitzt.
Das Rohmaterial bleibt zu lange im Fass.
Beim Spritzgießprozess ist die auf das Rohmaterial ausgeübte Scherbeanspruchung zu groß. Wenn die Düsen verstopft sind oder Anschnitte und Angusskanäle zu schmal sind, erhöht sich die Scherbeanspruchung.
Deformation
Im Normalfall sollten die Formen der Produkte denen der Formen entsprechen. Die Verformung bezieht sich auf die Verformung von Produkten.
Wenn sich der Zustand verschlechtert, verformen sich die Produkte beim Auswerfen aus der Form vollständig. Wenn der Zustand nicht schwerwiegend ist, weist die Produktform kleine Unregelmäßigkeiten auf.
Lange, aber ohne Stützkanten oder große Flächen sind Bereiche, die am anfälligsten für Verformungen sind.
Ursache:
Ursachen für Verformungen:
Beim Lösen der Form ist die Temperatur zu hoch.
Da die Abkühlzeit in dicken und dünnen Bereichen unterschiedlich ist oder der Formtemperaturunterschied zwischen beweglicher Form und fixierter Form unterschiedlich ist, ist die Schrumpfung im Inneren der Produkte unterschiedlich.
Der Formfluss ist beim Füllen nicht gleichmäßig (die sogenannte „Gefrierausrichtung“) oder der Druck im Formhohlraum ist in der Druckhaltephase zu hoch.
Verunreinigungen
Die Verunreinigungen treten oft in Form von Flecken in verschiedenen Farben, Flecken oder Streifen auf. Am häufigsten kommt der schwarze Fleck vor.
Bei Verunreinigungen kann es sich nur um winzige Flecken handeln, bei schwerwiegenden Verunreinigungen können sie aber auch deutliche Streifen oder einen großen Teil der Verfärbung darstellen.
Ursache:
Die Verunreinigungen werden durch mit Rohstoffen vermischte Kleinigkeiten verursacht, wie zum Beispiel:
Beim Transport in die Fässer wird das Rohmaterial mit Kleinteilen vermischt.
Die Zersetzung des Rohmaterials kann von Schneidmechanismen herabfallen und in Rohmaterialien wie Maschinenbolzen, Innenwand der Trockentrommel, Verbindungen/Düsen eingemischt werden.
Laminierung
Durch die Laminierung entsteht auf der Oberfläche der Produkte ein „Hauteffekt“, der durch die unterschiedlichen Eigenschaften und Texturen der Oberfläche von Produkten und anderen Rohstoffen verursacht wird, und es bildet sich eine abziehbare Haut, die entfernt werden kann.
Bei einer ernsthaften Laminierung besteht die gesamte Querschnittsfläche aus verschiedenen Schichten und ist nicht miteinander verschmolzen. Wenn die Mängel weniger offensichtlich sind, entspricht das Erscheinungsbild der Produkte möglicherweise den Anforderungen, beeinträchtigt jedoch die mechanischen Eigenschaften der Produkte.
Ursache:
Es gibt zwei Hauptursachen für die Laminierung. Der erste Grund liegt darin, dass zwei verschiedene Arten von Rohstoffen falsch miteinander vermischt werden. Unter Druck werden die beiden Rohstoffe gleichzeitig in das Fass transportiert. Allerdings kann die Form beim Abkühlen nicht zusammengeschmolzen werden, ebenso wie verschiedene Schichten gewaltsam zusammengepresst werden, um Produkte zu formen.
Zweitens: Wenn die kalte Schmelze gezwungen wird, durch den schmalen Anguss zu gelangen, wird eine Scherspannung erzeugt. Eine zu hohe Scherbeanspruchung führt dazu, dass die zuvor geschmolzene Schmelzschicht nicht vollständig verschmolzen werden kann.
Vermischungsgefahr:
Man sollte sich darüber im Klaren sein, dass das Mischen einiger Rohstoffe zu starken chemischen Reaktionen führt. PVC und Avetal dürfen beispielsweise nicht gemischt werden.
Silber linear
Der lineare Splitter kann nur ein lokales Phänomen sein, kann sich aber bei schwerwiegenden Folgen auf die gesamte Oberfläche ausdehnen.
Silber linear beeinträchtigt das Aussehen der Produkte und beeinträchtigt auch die mechanischen Eigenschaften der Produkte.
Ursache:
Die folgenden zwei Punkte verursachen die Silberlinearität:
Das Rohmaterial ist nass und einige von ihnen absorbieren den Dampf in der Luft. Wenn das Rohmaterial zu feucht ist, kann bei der hohen Temperatur und dem hohen Druck des Fasses unter Druck stehender Dampf entstehen. Diese Dämpfe durchbrechen die Oberfläche des Produkts und bilden silberne Streifen.
Die Schmelze wird thermisch geschädigt und führt zu lokaler Degradation. Das erzeugte flüchtige Gas wird an der Oberfläche des Schimmels blockiert und erzeugt Streifen auf der Oberfläche der Produkte.
Dies ist nicht so schlimm wie die Verschlechterung. Solange die Temperatur der Schmelze hoch ist oder sie beim Plastifizieren oder Einspritzen in die Form einer Scherbeanspruchung ausgesetzt ist, kann dies passieren.
Glanz/Schatten
Die Oberflächenbeschaffenheit der Produkte sollte mit der der Formen übereinstimmen. Wenn die Oberflächenbeschaffenheit von zwei unterschiedlich ist, treten Glanz-/Schattenfehler auf.
Wenn Mängel auftreten, ist die Oberfläche düster, während die raue Oberfläche glatt und glänzend ist.
Ursache:
Zu den Ursachen für Glanz/Schatten gehören:
Die Schmelze fließt ungleichmäßig oder die Temperatur der Formoberfläche ist niedrig, was dazu führt, dass die Oberflächenbeschaffenheit der Form beim Formen des Materials nicht reproduziert werden kann.
Während des Druckhaltens ist der Druck in der Kavität nicht hoch genug, damit das Material beim Abkühlen an der Oberfläche der Form haften bleibt und Schrumpfspuren hinterlässt.
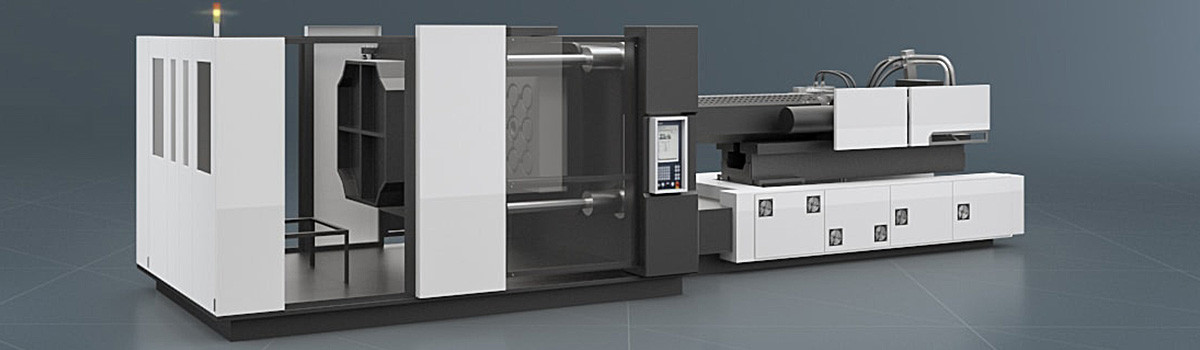
Fließmarken
Fließspuren können auf der Oberfläche von Produkten in vielfältiger Form auftreten. Im Allgemeinen entsteht ein Schattenbereich.
Fließmarken erzeugen keine Prägungen oder Vertiefungen auf der Oberfläche der Produkte, die mit den Fingern nicht ertastet werden können. Dieser Defekt wird auch als Schleifspuren, Geisterbilder und Schatten bezeichnet.
Wenn Fließspuren offensichtlich sind, entstehen Rillen und es entstehen Fehler wie Markierungen auf der Oberfläche der Produkte.
Ursache:
Fließmarken können gefunden werden, wenn:
Die Fließfähigkeit der Schmelze ist schlecht oder die Oberflächentemperatur der Form ist niedrig, was zu einem großen Fließwiderstand des Kunststoffs beim Füllprozess der Form führt.
Beim Befüllen der Form entsteht dem Schmelzefluss ein Widerstand, der durch die unebene Oberfläche der Matrize, die auf der Matrizenoberfläche aufgedruckten Markierungen oder Muster oder die Änderung der Fließrichtung der Schmelze während des Füllvorgangs verursacht werden kann.
Verbindungslinie
Die Verbindungslinie entsteht, wenn beim Füllen der Form zwei Schmelzfronten aufeinandertreffen, und erscheint auf der Oberfläche des Produkts wie eine Linie.
Die Verbindungslinie ist wie die Risslinie auf der Oberfläche von Produkten, die nicht offensichtlich zu erkennen ist.
Bei der Gestaltung von Formen sind einige sichtbare Verbindungslinien unvermeidbar. In diesem Fall wird die Verbindungslinie so weit wie möglich verkürzt, um eine Beschädigung der Festigkeit und des Aussehens der Produkte zu verhindern.
Ursache:
Es gibt viele Gründe für die Entstehung einer Schmelzfront. Der wahrscheinlichste Grund könnte der Schmelzefluss entlang der Kanten des Formkerns sein. Beim Zusammentreffen der beiden Schmelzen entstehen die Verbindungslinien. Die Temperatur der beiden Schmelzfronten sollte hoch genug sein, um eine erfolgreiche Verschmelzung zu ermöglichen und die Festigkeit und das Aussehen der Produkte nicht zu beeinträchtigen.
Wenn die beiden Schmelzen nicht vollständig miteinander verschmelzen können, entstehen Defekte.
Ursachen für Mängel:
Die Form hat dickere und dünnere Teile und die Fließgeschwindigkeit der Schmelzen ist unterschiedlich. Wenn die Schmelze durch den dünnen Teil der Form fließt, ist die Temperatur niedrig.
Die Länge jedes Läufers ist unterschiedlich. Einzelläufer werden sich leicht abkühlen können.
Der Druck im Formhohlraum reicht nicht aus, um ein vollständiges Schmelzen der Schmelze während der Druckhaltephase zu ermöglichen.
Die verbleibenden Blasen verhindern, dass die Schmelzfront schmelzen kann, was ebenfalls zum Verbrennen führt.
Verbrennung
Der Abbrand ähnelt dem von Kurzschrot, allerdings mit unregelmäßigen Auslaufkanten und leichtem Brandgeruch. Wenn der Zustand schwerwiegend ist, treten auf dem Produkt Rußflecken auf, begleitet von einem Geruch verbrannten Plastiks.
Werden die Mängel nicht beseitigt, kommt es häufig zu schwarzen Ablagerungen auf der Gussform. Wenn die bei der Verbrennung entstehenden Gas- oder Ölstoffe nicht sofort kontrolliert werden, können sie die Luftlöcher verstopfen. Am Ende der Wege kommt es meist zu Verbrennungen.
Ursache:
Die Verbrennung entsteht durch den inneren Verbrennungseffekt. Wenn der Luftdruck in sehr kurzer Zeit stark ansteigt, steigt die Temperatur und es kommt zu Verbrennungen. Den gesammelten Daten zufolge kann der Verbrennungseffekt im Spritzgussverfahren hohe Temperaturen von bis zu 600 Grad erzeugen.
Brennen kann auftreten, wenn:
Die Füllgeschwindigkeit der Form ist schnell, so dass die Luft nicht aus dem Formhohlraum entweichen kann und durch die Blockierung des einströmenden Kunststoffs Luftblasen entstehen, die nach dem Komprimieren zu einer inneren Verbrennung führen.
Die Luftlöcher sind blockiert oder die Belüftung ist nicht reibungslos.
Die Luft in der Form sollte aus den Luftlöchern entweichen. Wenn die Belüftung durch Position, Anzahl, Größe oder Funktionen beeinträchtigt wird, bleibt die Luft in der Form und führt zu Verbrennungen. Eine große Schließkraft der Form führt außerdem zu einer schlechten Belüftung.
Schrumpfung
Unter Schrumpfung versteht man die leichten Vertiefungen auf der Oberfläche von Produkten.
Bei geringfügigen Mängeln ist die Oberfläche der Produkte uneben. Wenn es ernst wird, wird der große Produktbereich zusammenbrechen. Produkte mit Wölbungen, Griffen und Vorsprüngen weisen häufig Schrumpfungsfehler auf.
Ursache:
Die Schrumpfung entsteht durch großflächige Schrumpfung der Rohstoffe beim Abkühlen.
Im dicken Bereich von Produkten (z. B. Bogen) ist die Kerntemperatur des Materials niedrig, so dass die Schrumpfung später erfolgt als die der Oberfläche, was eine Kontraktionskraft im Inneren des Rohmaterials erzeugt und die Außenseite in die nach innen gerichtete Vertiefung zieht um die Schrumpfung zu erzeugen.
Schrumpfungen treten in folgenden Situationen auf:
Der Druck im Formhohlraum ist geringer als die Kraft, die durch die Schrumpfung des Rohmaterials beim Abkühlprozess entsteht.
Unzureichende Druckbeaufschlagungszeit des Formhohlraums während des Abkühlvorgangs, was dazu führt, dass das Rohmaterial vom Anschnitt aus dem Hohlraum fließt.
Das Rohmaterial verfügt während der Form- und Druckhaltephase nicht über ausreichende Pufferkapazität, da die Schnecke vollständig zurückgezogen wird, bevor das überschüssige Rohmaterial eingespritzt wird.
Die Querschnittsflächen von Anschnitten und Angusskanälen sind weitaus kleiner als die Dicke der Produkte, was bedeutet, dass die Anschnitte bereits vor dem Extrusionsprozess der Produkte gefroren sind.
Bubbles
Die Vakuumblasen werden in Form von Luftblasen dargestellt, die leicht auf den transparenten Produkten zu finden sind. Dies ist auch im Querschnitt undurchsichtiger Produkte zu erkennen.
Ursache:
Luftblasen sind der Vakuumanteil von Produkten, der entsteht, wenn das Rohmaterial während des Abkühlprozesses schrumpft.
Ähnlich wie beim Schrumpfen erzeugt das Innere des Rohmaterials die Kontraktionskraft. Der Unterschied besteht darin, dass sich das äußere Erscheinungsbild der Produkte bei der Blasenbildung verfestigt und es zu keinem Kollaps kommt, sodass Hohlblasen entstehen.
Die Ursachen für Blasen sind dieselben wie für die Reduktion, darunter:
Ineffizienter Formhohlraumdruck
Unzureichende Druckbeaufschlagungszeit im Hohlraum
Die Größe von Läufer und Tor ist zu klein
Spritzspuren
Spritzmarkierungen beziehen sich auf den Gewindebereich gegenüber dem Anschnitt. Die Spritzspuren beeinträchtigen nicht nur das Aussehen der Produkte, sondern auch die Festigkeit der Produkte.
Ursache:
Spritzflecken entstehen dadurch, dass die Schmelze während des Formfüllvorgangs unkontrolliert fließt.
Unter dem enormen Druck gelangt der geschmolzene Kunststoff in die Form. Wenn die Formfüllgeschwindigkeit zu hoch ist, wird der Kunststoff aus dem offenen Spalt des Formhohlraums austreten, schnell zurückfedern und abkühlen. Zu diesem Zeitpunkt bilden sich Fäden, die den geschmolzenen Kunststoff daran hindern, in die Anschnitte einzudringen.
Die Hauptursache für Spritzflecken ist die falsche Position der Tore oder die Torkonstruktion. Die folgenden beiden Situationen verschlimmern die Mängelsituation:
Hohe Formfüllgeschwindigkeit
Schlechter Schmelzfluss beim Füllen der Form