Thermoplastisches Spritzgießen
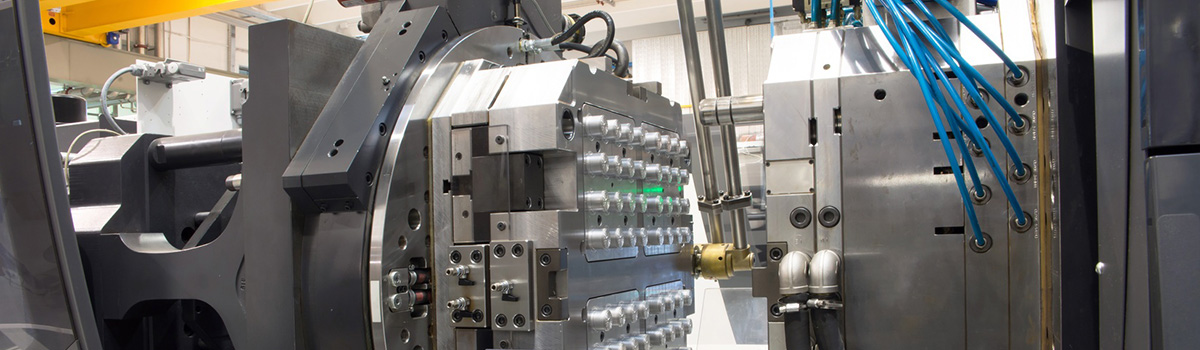
Thermoplastisches Spritzgießen ist ein beliebtes Herstellungsverfahren zur Herstellung verschiedener Kunststoffteile für verschiedene Branchen. Bei diesem Verfahren werden Kunststoffpellets geschmolzen und in eine Form eingespritzt, um eine dreidimensionale Form zu erzeugen. Thermoplastisches Spritzgießen ist äußerst effizient und kostengünstig für die Herstellung großer Mengen hochwertiger Kunststoffteile mit engen Toleranzen. In diesem umfassenden Leitfaden werden die verschiedenen Aspekte des Thermoplast-Spritzgießens untersucht, einschließlich seiner Vor- und Nachteile, der verwendeten Thermoplasttypen, des Spritzgussverfahrens, Designüberlegungen und vieles mehr.
Geschichte des thermoplastischen Spritzgusses
Die Geschichte des thermoplastischen Spritzgießens umfasst mehr als ein Jahrhundert technologischer Fortschritte, Materialentwicklungen und industrieller Anwendungen. Von seinen bescheidenen Anfängen als Zelluloidformverfahren bis hin zur heutigen hochentwickelten Technologie ist das Spritzgießen nach wie vor eine wichtige Fertigungstechnik, die Innovationen vorantreibt und verschiedene Branchen prägt.
- Frühe Entwicklungen:John Wesley Hyatt und sein Bruder Isaiah entwickelten die erste praktische Spritzgießmaschine und führten die Ursprünge des thermoplastischen Spritzgießens bis ins späte 19. Jahrhundert zurück. Im Jahr 1872 patentierten sie ein Gerät, das mithilfe eines Kolbens Zelluloid in einen Formhohlraum einspritzte und so feste Objekte herstellte. Dieser Durchbruch legte den Grundstein für das moderne Spritzgussverfahren.
- Fortschritte bei Materialien:Zu Beginn des 20. Jahrhunderts eröffnete die Einführung neuer synthetischer Polymere neue Möglichkeiten für den Spritzguss. Bakelit, ein Phenolharz, wurde aufgrund seiner hervorragenden elektrischen Isoliereigenschaften zu einem beliebten Formmaterial. In den 1930er und 1940er Jahren führten Fortschritte in der Polymerchemie zur Entwicklung anderer Thermoplaste wie Polystyrol und Polyethylen, wodurch die Palette der für den Spritzguss geeigneten Materialien weiter erweitert wurde.
- Industrielle Akzeptanz: Die weit verbreitete Einführung des thermoplastischen Spritzgießens begann in den 1950er Jahren, als die Hersteller seine Kosteneffizienz und Vielseitigkeit erkannten. Die Einführung von Hochdruckmaschinen ermöglichte schnellere Zykluszeiten und höhere Produktionsmengen. Dadurch entstand eine vielfältige Auswahl an Produkten sowohl für den persönlichen als auch für den industriellen Gebrauch. Dazu gehörten Autoteile, Haushaltsgeräte und Spielzeug.
- Technologische Innovationen:Im Laufe der Jahrzehnte entwickelte sich die Spritzgießtechnik immer weiter. In den 1960er Jahren kamen computergesteuerte Maschinen auf, die eine präzise Steuerung des Formprozesses ermöglichten. Die Einführung von Heißkanalsystemen in den 1980er Jahren reduzierte den Abfall und verbesserte die Effizienz, da keine Kanäle und Angüsse erforderlich waren. In den letzten Jahren haben Fortschritte in den Bereichen Automatisierung, Robotik und 3D-Druck die Spritzgussindustrie weiter revolutioniert, indem sie komplexe Designs ermöglicht und die Produktionszeit verkürzt haben.
- Nachhaltigkeit und Recycling:Angesichts wachsender Umweltbedenken hat die Spritzgussindustrie Nachhaltigkeitsmaßnahmen ergriffen. Hersteller haben biobasierte und recycelte Thermoplaste entwickelt und so die Abhängigkeit von Materialien auf Basis fossiler Brennstoffe verringert. Darüber hinaus haben verbesserte Recyclingtechnologien die Wiederaufbereitung von Post-Consumer- und Post-Industrial-Abfällen ermöglicht und so die Umweltauswirkungen des thermoplastischen Spritzgießens minimiert.
- Zukunftsaussichten:Die Zukunft des thermoplastischen Spritzgießens sieht vielversprechend aus. Die Branche erforscht Innovationen wie Mikrospritzguss für Miniaturbauteile, Multimaterial- und Umspritztechniken für komplexe Teile sowie die Integration intelligenter Technologien zur Prozessüberwachung und -optimierung. Darüber hinaus erwarten Forscher, dass Fortschritte bei biologisch abbaubaren Materialien und der additiven Fertigung den Bereich revolutionieren und das Spritzgießen noch nachhaltiger und vielseitiger machen werden.
Vorteile des thermoplastischen Spritzgusses
Thermoplastisches Spritzgießen bietet Herstellern zahlreiche Vorteile. Es bietet Designflexibilität und ermöglicht komplexe und komplizierte Designs mit verschiedenen Funktionen. Der Prozess ist kosteneffizient, reduziert Materialverschwendung und senkt die Stückkosten. Thermoplastisches Spritzgießen unterstützt mehrere Materialien und bietet Vielseitigkeit für verschiedene Anwendungen.
- Designflexibilität:Das thermoplastische Spritzgießen ermöglicht komplizierte und komplexe Designs mit Merkmalen wie Hinterschnitten, dünnen Wänden und unterschiedlichen Dicken und bietet Designern enorme Freiheit.
- Kosteneffizienz: Der Prozess ist hocheffizient, reduziert Materialverschwendung und senkt die Stückkosten. Das gleichzeitige Formen mehrerer Teile und schnelle Produktionszyklen tragen zu Kosteneinsparungen bei.
- Materialvielfalt: Thermoplastisches Spritzgießen unterstützt eine breite Palette von Materialien, sodass Hersteller für jede Anwendung die am besten geeignete Option auswählen können, einschließlich starrer oder flexibler, transparenter oder undurchsichtiger und chemisch beständiger Materialien.
- Stärke und Haltbarkeit:Spritzgegossene Thermoplaste können hervorragende mechanische Eigenschaften wie hohe Festigkeit, Zähigkeit und Schlagzähigkeit aufweisen. Verstärkungsmöglichkeiten wie Glas- oder Kohlefasern verbessern diese Eigenschaften zusätzlich.
- Konsistenz und Qualität:Das Spritzgießen gewährleistet eine gleichbleibende Teil-zu-Teil-Qualität und Maßgenauigkeit und liefert enge Toleranzen und zuverlässige Produkte. Das Verfahren sorgt außerdem für eine glatte und gleichmäßige Oberflächenbeschaffenheit, sodass keine zusätzlichen Nachbearbeitungsvorgänge erforderlich sind.
- Skalierbarkeit und Massenproduktion:Das Spritzgießen ist von kleinen bis großen Stückzahlen skalierbar und eignet sich daher für die Massenproduktion. Sobald Hersteller die Form erstellt haben, können sie große Mengen identischer Teile mit minimalen Abweichungen produzieren.
- Integration und Montage:Spritzgussteile können mehrere Komponenten in einem Stück integrieren, wodurch der Bedarf an zusätzlichen Montageprozessen reduziert wird. Diese Integration verbessert die Produktleistung, verkürzt die Montagezeit und senkt die Kosten.
- Nachhaltigkeit:Die Spritzgussindustrie legt einen zunehmenden Fokus auf Nachhaltigkeit. Die Verfügbarkeit biobasierter und recycelter Materialien ermöglicht die Herstellung umweltfreundlicher Produkte. Der effiziente Materialeinsatz und die Recyclingfähigkeit von Thermoplasten tragen zu einem umweltfreundlicheren Herstellungsprozess bei.
Diese Vorteile haben es zu einer weit verbreiteten Fertigungsmethode in verschiedenen Branchen gemacht und bieten hochwertige, kostengünstige und umweltfreundliche Lösungen für komplexe Produktanforderungen.
Nachteile des thermoplastischen Spritzgusses
Während das thermoplastische Spritzgießen zahlreiche Vorteile bietet, gibt es auch einige Nachteile. Hersteller müssen diese Faktoren sorgfältig bewerten und gegen die Vorteile abwägen, um die Eignung des thermoplastischen Spritzgusses für ihre spezifischen Anwendungen zu bestimmen.
- Hohe Anfangsinvestition: Der Aufbau eines Thermoplast-Spritzgussbetriebs erfordert eine erhebliche Anfangsinvestition in die Formenkonstruktion und -herstellung sowie den Kauf von Spezialmaschinen. Die mit der Herstellung von Formen und Werkzeugen verbundenen Kosten können erheblich sein, insbesondere bei komplexen und komplizierten Designs.
- Designbeschränkungen: Während das thermoplastische Spritzgießen Designflexibilität bietet, bestehen bestimmte Einschränkungen. Beispielsweise kann es eine Herausforderung sein, eine gleichmäßige Wandstärke im gesamten Teil zu erreichen, was zu Schwankungen in der Materialverteilung und potenziellen Strukturschwächen führt. Darüber hinaus kann das Vorhandensein von Hinterschneidungen oder komplexen Geometrien den Einsatz zusätzlicher Formmerkmale oder sekundärer Arbeitsgänge erforderlich machen, was die Kosten und die Produktionszeit erhöht.
- Lange Vorlaufzeiten:Der Prozess des Entwerfens und Herstellens von Formen für den Spritzguss kann zeitaufwändig sein und zu längeren Vorlaufzeiten für die Produktentwicklung führen. Der Design-Iterationsprozess, die Formenherstellung und das Testen können den gesamten Produktionszeitplan erheblich verlängern, was für Projekte mit engen Fristen möglicherweise nicht geeignet ist.
- Einschränkungen bei der Materialauswahl:Obwohl das thermoplastische Spritzgießen eine breite Palette von Materialien unterstützt, gibt es bestimmte Einschränkungen und Einschränkungen. Für einige Materialien gelten möglicherweise besondere Verarbeitungsanforderungen oder sie sind nur begrenzt verfügbar, was sich auf die Design- und Materialauswahl für eine bestimmte Anwendung auswirkt.
- Einschränkungen der Teilegröße:Spritzgießmaschinen unterliegen Größenbeschränkungen, sowohl hinsichtlich der physischen Größe des Geräts als auch der Größe der Formen, die sie aufnehmen können. Für die Herstellung großer Teile sind möglicherweise spezielle Geräte oder alternative Fertigungsmethoden erforderlich.
- Umweltbelastung:Während die Branche auf Nachhaltigkeit hinarbeitet, fallen beim thermoplastischen Spritzgussverfahren immer noch Abfallstoffe an, darunter Ausschuss und Angüsse. Um die Auswirkungen auf die Umwelt zu minimieren, sind eine ordnungsgemäße Entsorgung und Wiederverwertung dieser Materialien erforderlich.
- Die Komplexität der Prozessoptimierung:Das Erreichen optimaler Prozessparameter für das thermoplastische Spritzgießen kann komplex und zeitaufwändig sein. Hersteller müssen Temperatur, Druck, Abkühlraten und Zykluszeiten sorgfältig kontrollieren und optimieren, um eine gleichbleibende Teilequalität sicherzustellen und Fehler zu minimieren.
Arten von Thermoplasten, die beim Spritzgießen verwendet werden
Dies sind nur einige Beispiele für die üblicherweise im Spritzguss verwendeten Thermoplaste. Jedes Material verfügt über einzigartige Eigenschaften, die es aufgrund seiner Festigkeit, Flexibilität, chemischen Beständigkeit, Transparenz und Kosten für bestimmte Anwendungen geeignet machen. Hersteller sollten diese Eigenschaften und Anforderungen berücksichtigen, wenn sie den geeigneten Thermoplast für ihre Spritzgussprojekte auswählen.
- Polypropylen (PP):Polypropylen ist ein vielseitiger Thermoplast, der häufig beim Spritzgießen verwendet wird. Es bietet eine hervorragende chemische Beständigkeit, eine geringe Dichte und eine gute Schlagzähigkeit. PP (Polypropylen) findet vielfältige Anwendungsmöglichkeiten in Verpackungen, Automobilkomponenten, Haushaltsgeräten und medizinischen Geräten.
- Polyethylen (PE):Polyethylen ist ein weiterer weit verbreiteter Thermoplast im Spritzguss. Es ist in verschiedenen Formen erhältlich, beispielsweise als Polyethylen hoher Dichte (HDPE) und Polyethylen niedriger Dichte (LDPE). PE bietet eine gute chemische Beständigkeit, Zähigkeit und Flexibilität und eignet sich daher für Flaschen, Behälter und Rohre.
- Polystyrol (PS):Polystyrol ist ein vielseitiger Thermoplast, der für seine Klarheit, Steifigkeit und Erschwinglichkeit bekannt ist. Es findet häufig Verwendung in Verpackungen, Konsumgütern und Einwegprodukten. PS (Polystyrol) ermöglicht eine schnelle Verarbeitung und bietet eine gute Dimensionsstabilität, kann jedoch spröde und anfällig für Spannungsrisse durch Umwelteinflüsse sein.
- Acrylnitril-Butadien-Styrol (ABS): ABS ist ein beliebter Thermoplast, der für seine hervorragende Schlagfestigkeit und Haltbarkeit bekannt ist. Es vereint die Eigenschaften von Acrylnitril, Butadien und Styrol zu einem vielseitigen Material, das sich für Automobilteile, Elektronikgehäuse und Spielzeug eignet.
- Polyvinylchlorid (PVC): PVC ist ein weit verbreiteter Thermoplast, der für seine hervorragende chemische Beständigkeit, Haltbarkeit und geringen Kosten bekannt ist. Abhängig von der Formulierung und den verwendeten Zusatzstoffen kann es starr oder flexibel sein. PVC (Polyvinylchlorid) wird häufig im Bauwesen, in der elektrischen Isolierung, in Gesundheitsprodukten und in Verpackungen verwendet.
- Polycarbonat (PC): Polycarbonat ist ein transparenter Thermoplast mit außergewöhnlicher Schlagzähigkeit und hoher Hitzebeständigkeit. Es wird häufig in Anwendungen eingesetzt, die optische Klarheit erfordern, wie z. B. Automobilkomponenten, Schutzhelme und elektronische Displays.
- Nylon (Polyamid):Nylon ist ein starker und langlebiger Thermoplast, der für seine hervorragenden mechanischen Eigenschaften und chemischen Beständigkeit bekannt ist. Es wird häufig in Anwendungen eingesetzt, die eine hohe Festigkeit erfordern, wie z. B. Automobilteile, Industriekomponenten und Konsumgüter.
- Polyethylenterephthalat (PET):PET ist ein beliebter Thermoplast zur Herstellung von Flaschen, Behältern und Verpackungsmaterialien. Es bietet gute Klarheit, chemische Beständigkeit und Barriereeigenschaften und eignet sich daher für Lebensmittel- und Getränkeanwendungen.
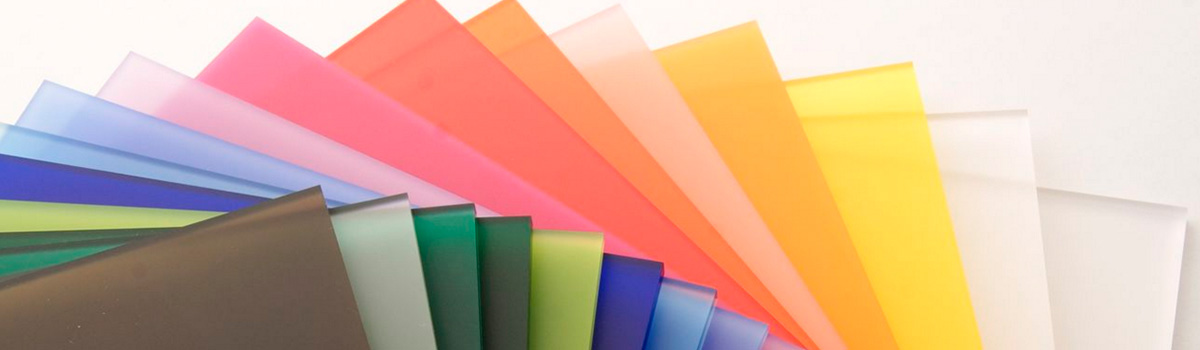
Eigenschaften von Thermoplasten für den Spritzguss
Diese Eigenschaften von Thermoplasten spielen eine entscheidende Rolle bei der Bestimmung ihrer Eignung für bestimmte Spritzgussanwendungen. Hersteller müssen diese Eigenschaften sorgfältig abwägen und den geeigneten Thermoplast basierend auf der gewünschten Leistung, den Umgebungsbedingungen und den Kostenanforderungen auswählen.
- Mechanische Eigenschaften:Beim Spritzgießen verwendete Thermoplaste können verschiedene mechanische Eigenschaften aufweisen, darunter Zugfestigkeit, Schlagfestigkeit und Biegefestigkeit. Diese Eigenschaften bestimmen die Fähigkeit des Materials, den ausgeübten Kräften standzuhalten, und seine allgemeine Haltbarkeit in verschiedenen Anwendungen.
- Chemische Resistenz:Viele beim Spritzgießen verwendete Thermoplaste weisen eine bemerkenswerte Beständigkeit gegenüber Chemikalien, Lösungsmitteln und Ölen auf. Diese Eigenschaft ist von entscheidender Bedeutung für Anwendungen, die rauen Umgebungen oder korrosiven Substanzen ausgesetzt sind.
- Thermische Stabilität:Die thermische Stabilität von Thermoplasten bezieht sich auf ihre Fähigkeit, erhöhten Temperaturen ohne nennenswerte Verschlechterung standzuhalten. Einige Thermoplaste weisen eine hervorragende Hitzebeständigkeit auf, sodass sie ihre mechanischen Eigenschaften auch bei hohen Temperaturen beibehalten.
- Elektrische Eigenschaften:Beim Spritzgießen verwendete Thermoplaste können spezifische elektrische Eigenschaften aufweisen, darunter elektrische Isolierung, Leitfähigkeit oder Durchschlagsfestigkeit. Diese Eigenschaften sind für Anwendungen in der Elektro- und Elektronikindustrie von entscheidender Bedeutung, wo Materialien eine zuverlässige elektrische Leistung bieten müssen.
- Transparenz und Klarheit:Bestimmte Thermoplaste wie Polycarbonat und PET bieten eine hervorragende Transparenz und Klarheit und eignen sich daher für Anwendungen, bei denen optische Eigenschaften erforderlich sind. Hersteller verwenden diese Materialien häufig in Produkten wie transparenten Fenstern, Linsen und Displays.
- Flexibilität und Robustheit: Flexibilität und Zähigkeit sind wesentliche Eigenschaften von Thermoplasten, die in Anwendungen eingesetzt werden, die Schlagfestigkeit und Haltbarkeit erfordern. Einige Thermoplaste wie ABS und Nylon bieten eine hervorragende Zähigkeit, sodass sie wiederholten Stößen standhalten, ohne zu brechen.
- Dimensionsstabilität:Unter Dimensionsstabilität versteht man die Fähigkeit eines Thermoplasten, seine Form und Größe unter verschiedenen Bedingungen, einschließlich Temperaturänderungen, beizubehalten. Materialien mit guter Dimensionsstabilität sorgen für einheitliche Teileabmessungen und minimieren das Risiko von Verformungen oder Verformungen.
- Chemische Kompatibilität:Die chemische Kompatibilität von Thermoplasten bezieht sich auf ihre Fähigkeit, einer Zersetzung oder Wechselwirkung mit verschiedenen Chemikalien, einschließlich Säuren, Basen und Lösungsmitteln, zu widerstehen. Um eine optimale Leistung zu gewährleisten, ist die Auswahl eines Thermoplasts, der der spezifischen chemischen Umgebung standhält, der er bei der beabsichtigten Anwendung ausgesetzt ist, von entscheidender Bedeutung.
- Dichte: Thermoplaste haben unterschiedliche Dicken, die sich auf ihr Gewicht und die Gesamteigenschaften der Teile auswirken können. Materialien mit geringer Dichte wie Polyethylen bieten leichte Lösungen, während Materialien mit hoher Dichte wie Polypropylen für zusätzliche Festigkeit und Steifigkeit sorgen.
Spritzgussprozess: Schritt für Schritt
Der Spritzgussprozess folgt diesen Schritten und ermöglicht die effiziente und präzise Herstellung hochwertiger thermoplastischer Teile. Jeder Schritt erfordert eine sorgfältige Kontrolle und Überwachung, um konsistente Teileabmessungen, Materialeigenschaften und Gesamtqualität sicherzustellen.
- Formendesign und -herstellung: Der erste Schritt im Spritzgussprozess ist die Konstruktion und Herstellung der Form. Hersteller müssen einen präzisen und detaillierten Formentwurf erstellen, um die gewünschten Teilespezifikationen zu erreichen. Anschließend fertigen die Hersteller die Form mit verschiedenen Techniken, wie zum Beispiel CNC oder Funkenerosion (EDM).
- Material vorbereitung: Der nächste Schritt ist die Vorbereitung, sobald die Form fertig ist. Thermoplastische Pellets oder Granulate werden anhand der gewünschten Materialeigenschaften ausgewählt und in einem Trichter geschmolzen. Anschließend führen die Bediener das Material in den Zylinder der Spritzgießmaschine, wo es geschmolzen und homogenisiert wird.
- Injektion:Während der Einspritzphase spritzen Bediener den geschmolzenen Thermoplast unter hohem Druck in den Formhohlraum. Die Einspritzeinheit der Maschine drückt das geschmolzene Material durch eine Düse in die Form. Das Material füllt den Formhohlraum und nimmt die Form des gewünschten Teils an.
- Abkühlung und Erstarrung:Nach dem Befüllen der Form lassen die Bediener den geschmolzenen Kunststoff abkühlen und erstarren. Die Kühlung ist entscheidend für die Dimensionsstabilität und die ordnungsgemäße Formung der Teile. Bediener können den Kühlprozess steuern, indem sie Kühlmittel durch Kanäle innerhalb der Form zirkulieren lassen oder Kühlplatten verwenden.
- Öffnen und Auswerfen der Form:Bediener öffnen die Form und werfen das Teil aus dem Formhohlraum aus, sobald der Kunststoff erstarrt ist. Das Auswurfsystem innerhalb der Maschine verwendet Stifte, Auswerferplatten oder Luftstöße, um den Bereich aus der Form zu entfernen. Die Form ist dann für den nächsten Einspritzzyklus bereit.
- Nachbearbeitung: Nach dem Auswerfen kann das Teil Nachbearbeitungsvorgängen wie Beschneiden, Entgraten oder Oberflächenveredelung unterzogen werden. Diese Schritte tragen dazu bei, überschüssiges Material zu entfernen, raue Kanten zu glätten und das endgültige Erscheinungsbild des Teils zu verbessern.
- Qualitätskontrolle: Der letzte Schritt besteht darin, die gespritzten Teile auf Qualität zu prüfen und sicherzustellen, dass sie den festgelegten Anforderungen entsprechen. Zur Überprüfung der Qualität und Integrität des Teils können verschiedene Qualitätskontrolltechniken eingesetzt werden, darunter Maßmessungen, Sichtprüfungen und Funktionstests.
- Recycling und Materialwiederverwendung:Beim Spritzgießen anfallendes Überschuss- oder Ausschussmaterial kann recycelt und wiederverwendet werden. Die Reduzierung des Einsatzes neuer thermoplastischer Materialien trägt dazu bei, Abfall zu minimieren und die Nachhaltigkeit zu verbessern.
Ausrüstung für den Spritzguss
Diese Ausrüstungskomponenten erleichtern den Spritzgussprozess, vom Schmelzen und Einspritzen des thermoplastischen Materials bis hin zum Formen, Abkühlen und Auswerfen des Endteils. Der ordnungsgemäße Betrieb und die Wartung dieser Anlagenkomponenten sind entscheidend für eine effiziente und qualitativ hochwertige Spritzgussproduktion.
- Spritzgießmaschine:Die Hauptausrüstung beim Spritzgießen ist für das Schmelzen des thermoplastischen Materials, das Einspritzen in die Form und die Steuerung des Prozesses verantwortlich.
- Schimmel: Die speziell angefertigte Form, um die gewünschte Form und die gewünschten Eigenschaften des Kunststoffteils zu erzeugen, besteht aus zwei Hälften, der Kavität und dem Kern. Der Bediener montiert es an der Schließeinheit der Spritzgießmaschine.
- Trichter:Behälter, der das thermoplastische Material in Pellet- oder Granulatform aufnimmt und es dem Zylinder der Spritzgießmaschine zum Schmelzen und Einspritzen zuführt.
- Zylinder und Schraube: Der Zylinder, eine zylindrische Kammer, schmilzt und homogenisiert das thermoplastische Material, während die Schnecke darin rotiert, um das Material zu schmelzen, zu mischen und zu standardisieren.
- Heiz- und Kühlsysteme:Spritzgießmaschinen verfügen über Heizelemente, wie zum Beispiel elektrische Heizgeräte oder Heizgeräte mit heißem Öl, um die Temperatur des Zylinders zu erhöhen, und Kühlsysteme, wie zum Beispiel Wasser- oder Ölzirkulation, um die Form zu kühlen und das Kunststoffteil zu verfestigen.
- Auswerfersystem:Entfernt das geformte Teil nach dem Erstarren aus dem Formhohlraum, typischerweise mithilfe von Auswerferstiften, Platten oder Luftstößen beim Öffnen der Form.
- Kontrollsystem:Überwacht und steuert verschiedene Parameter des Spritzgussprozesses und ermöglicht es dem Bediener, Parameter wie Einspritzgeschwindigkeit, Temperatur, Druck und Abkühlzeit einzustellen und anzupassen.
Spritzgießmaschinen: Typen und Eigenschaften
Jeder Spritzgießmaschinentyp hat seine eigenen Eigenschaften und Vorteile, sodass Hersteller das am besten geeignete Gerät für ihre spezifischen Produktionsanforderungen auswählen können.
- Hydraulische Spritzgießmaschinen: Diese Maschinen nutzen hydraulische Systeme, um den notwendigen Druck zu erzeugen, um geschmolzenen Kunststoff in die Form einzuspritzen. Sie sind bekannt für ihre hohe Spannkraft, präzise Steuerung und Vielseitigkeit bei der Handhabung verschiedener Thermoplaste. Hydraulische Maschinen eignen sich für die Großserienproduktion und können komplexe Formen aufnehmen.
- Elektrische Spritzgießmaschinen:Elektrische Maschinen nutzen elektrische Servomotoren für den Betrieb der Maschine, einschließlich der Einspritz-, Klemm- und Auswerfersysteme. Sie bieten präzise Steuerung, Energieeffizienz und schnellere Reaktionszeiten als hydraulische Maschinen. Elektrische Maschinen eignen sich ideal für Präzisionsformanwendungen, die eine hohe Wiederholgenauigkeit und Genauigkeit erfordern.
- Hybrid-Spritzgießmaschinen:Hybridmaschinen vereinen die Vorteile hydraulischer und elektrischer Geräte. Sie nutzen eine Kombination aus hydraulischen und elektrischen Servosystemen, um eine hohe Präzision, Energieeffizienz und Kosteneffizienz zu erreichen. Hybridmaschinen eignen sich für ein breites Anwendungsspektrum und sorgen für ein ausgewogenes Verhältnis zwischen Leistung und Betriebskosten.
- Zweiplatten-Spritzgießmaschinen: Zweiplattenmaschinen haben ein einzigartiges Design mit zwei separaten Platten zum Spannen der Form. Dieses Design sorgt für verbesserte Stabilität, verbesserte Formsynchronisation und ermöglicht größere Formgrößen und höhere Schließkräfte. Zweiplattenmaschinen eignen sich für große und komplexe Teile, die eine präzise Formgebung erfordern.
- Mehrkomponenten-Spritzgießmaschinen:Hersteller konzipieren diese Maschinen so, dass sie Teile mit mehreren Materialien oder Farben in einem einzigen Formzyklus herstellen. Sie verfügen über verschiedene Einspritzeinheiten und Formen, die das gleichzeitige Einspritzen unterschiedlicher Materialien ermöglichen. Mehrkomponentenmaschinen bieten Flexibilität und Effizienz bei der Herstellung komplexer Teile mit unterschiedlichen Eigenschaften.
- Mikrospritzgießmaschinen:Mikrospritzgießmaschinen wurden speziell für die Herstellung kleiner und präziser Teile entwickelt und bieten eine unglaublich hohe Präzision und Genauigkeit. Sie können komplizierte Details mit engen Toleranzen und minimalem Materialabfall herstellen. In der Elektronik, Medizintechnik und Mikrooptik kommen häufig Mikrospritzgussmaschinen zum Einsatz.
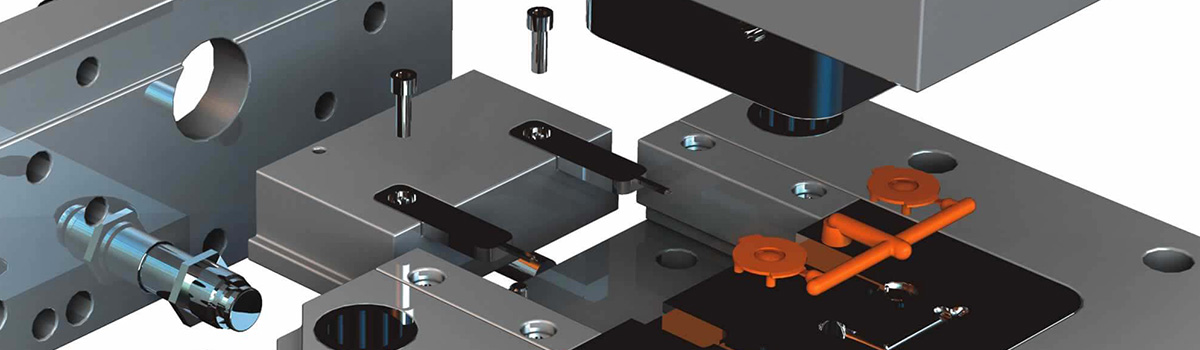
Überlegungen zum Formendesign für das Spritzgießen
Sorgfältige Überlegungen zur Formkonstruktion sind für eine erfolgreiche Spritzgussproduktion unerlässlich.
- Teiledesign:Das Formdesign sollte den spezifischen Anforderungen des Teils gerecht werden, einschließlich seiner Form, Abmessungen und Funktionsmerkmale. Hersteller sollten Formschrägen, Wandstärken, Hinterschneidungen und alle notwendigen Elemente sorgfältig berücksichtigen, um eine einfache Entformung und Teilequalität sicherzustellen.
- Form Material: Die Auswahl des Formmaterials ist entscheidend für die Erzielung von Haltbarkeit, Dimensionsstabilität und Hitzebeständigkeit. Zu den gängigen Formmaterialien gehören Stahllegierungen, Aluminiumlegierungen und Werkzeugstähle. Die Wahl des Materials hängt von Faktoren wie Produktionsvolumen, Teilekomplexität und erwarteter Werkzeuglebensdauer ab.
- Kühlsystem:Eine effiziente Kühlung ist für die ordnungsgemäße Erstarrung der Teile und die Minimierung der Zykluszeit unerlässlich. Das Formdesign sollte Kühlkanäle oder strategisch positionierte Einsätze enthalten, um eine gleichmäßige Formkühlung zu gewährleisten. Durch die richtige Kühlung wird das Risiko von Verzug, Schrumpfung und Teiledefekten verringert.
- Entlüftung:Damit während des Injektionsvorgangs Luft und Gase entweichen können, ist eine ausreichende Entlüftung erforderlich. Eine unzureichende Entlüftung kann zu Gaseinschlüssen, Brandflecken oder unvollständiger Teilefüllung führen. Hersteller können eine Entlüftung erreichen, indem sie Entlüftungsnuten, Stifte oder andere Mechanismen in das Formdesign integrieren.
- Auswurfsystem:Das Formdesign sollte ein wirksames Auswurfsystem umfassen, um das geformte Teil sicher und effizient aus dem Formhohlraum zu entfernen. Das Auswurfsystem kann aus Auswerferstiften, Hülsen oder anderen Mechanismen bestehen, die strategisch positioniert sind, um eine Beeinträchtigung der Funktion oder kritischer Merkmale zu vermeiden.
- Tordesign:Durch den Anschnitt gelangt geschmolzener Kunststoff in den Formhohlraum. Das Anschnittdesign sollte eine ordnungsgemäße Füllung der Teile gewährleisten, Fließlinien minimieren und ein vorzeitiges Einfrieren des Materials verhindern. Zu den Standardangusskonstruktionen gehören Kantenanschnitte, Tunnelanschnitte und Heißkanalsysteme, abhängig von den Teileanforderungen und Materialeigenschaften.
- Trennlinie:Das Formdesign sollte eine geeignete Trennlinie definieren, also die Linie, an der die beiden Hälften der Form zusammenkommen. Durch die richtige Platzierung der Trennfugen wird eine minimale Fehlanpassung von Graten und Trennfugen gewährleistet und eine effiziente Formmontage ermöglicht.
- Wartung und Wartungsfreundlichkeit der Form: Hersteller sollten die Einfachheit von Wartung, Reparatur und Werkzeugwartung berücksichtigen. Formkomponenten sollten zur Reinigung, Inspektion und zum Austausch leicht zugänglich sein. Durch die Integration von Funktionen wie Schnellwechseleinsätzen oder modularen Formdesigns kann die Wartungsfreundlichkeit der Form verbessert werden.
Formmaterialien für den Spritzguss
Die Zusammenarbeit mit Formmaterialspezialisten und die Berücksichtigung der spezifischen Anforderungen der Formanwendung können dabei helfen, das am besten geeignete Material für die Erzielung optimaler Formleistung und Teilequalität zu ermitteln.
- Stahllegierungen: Stahllegierungen wie Werkzeugstähle (z. B. P20, H13) und rostfreie Stähle werden aufgrund ihrer hervorragenden Haltbarkeit, Hitzebeständigkeit und Verschleißfestigkeit häufig für Spritzgussformen verwendet. Diese Materialien halten den hohen Temperaturen und Drücken im Spritzgussprozess stand und bieten eine gute Dimensionsstabilität für die Herstellung hochwertiger Teile.
- Aluminiumlegierungen:Aluminiumlegierungen wie 7075 und 6061 sind leicht und bieten eine gute Wärmeleitfähigkeit, wodurch sie für Formen geeignet sind, die eine effiziente Kühlung erfordern. Hersteller verwenden Aluminiumformen häufig für die Prototypenherstellung, die Produktion kleiner Stückzahlen oder für Anwendungen, bei denen eine Gewichtsreduzierung von entscheidender Bedeutung ist. Aluminiumformen können jedoch im Vergleich zu Stahllegierungen eine geringere Haltbarkeit aufweisen.
- Kupferlegierungen:Kupferlegierungen wie Berylliumkupfer weisen eine hohe Wärmeleitfähigkeit und gute Bearbeitbarkeit auf. Sie finden Verwendung in Formen, die für eine effektive Kühlung eine hervorragende Wärmeübertragung erfordern. Kupferlegierungen können dazu beitragen, die Zykluszeiten zu verkürzen, indem sie die Wärme schnell vom Formteil ableiten, was zu einer schnelleren Erstarrung führt.
- Werkzeugstähle:Werkzeugstähle, einschließlich H13, S7 und D2, sind für Hochleistungswerkzeuganwendungen konzipiert. Diese Stähle bieten eine Kombination aus hoher Festigkeit, Härte und Verschleißfestigkeit. Werkzeugstähle eignen sich für Formen mit hohem Produktionsvolumen, abrasiven Materialien oder anspruchsvollen Formbedingungen.
- Nickellegierungen:Nickellegierungen wie Inconel und Hastelloy sind für ihre außergewöhnliche Korrosionsbeständigkeit, Hochtemperaturfestigkeit und thermische Stabilität bekannt. Hersteller verwenden diese Legierungen in Formen, die korrosive Materialien verarbeiten oder eine Beständigkeit gegenüber extremen Temperaturen und aggressiven Formumgebungen erfordern.
- Kompositmaterialien:Verbundwerkstoffe wie verstärkte Kunststoffe oder Verbundwerkstoffe mit Metalleinlagen werden gelegentlich für bestimmte Formanwendungen verwendet. Diese Materialien bieten ausgewogene Eigenschaften wie hohe Festigkeit, thermische Stabilität und reduziertes Gewicht. Verbundformen können für spezifische Produktionsanforderungen eine kostengünstige Alternative sein.
Arten von Spritzgussformen
Spritzgießen ist ein vielseitiges und weit verbreitetes Herstellungsverfahren für Kunststoffteile.
- Zwei-Platten-Form:Das Zweiplattenwerkzeug ist die gebräuchlichste Art von Spritzgusswerkzeugen. Es besteht aus zwei Platten, der Hohlraumplatte und der Kernplatte, die getrennt werden, um den Auswurf des Formteils zu ermöglichen. Die Hohlraumplatte enthält die Hohlraumseite der Form, während die Kernplatte die Kernseite beherbergt. Aufgrund ihres relativ einfachen Aufbaus verwenden Hersteller Zweiplattenformen zur Herstellung einer breiten Palette von Teilen.
- Drei-Platten-Form:Die Drei-Platten-Form ist eine Weiterentwicklung der Zwei-Platten-Form. Dazu gehört eine zusätzliche Platte, der Angusskanal oder die Angussplatte. Die Angussplatte schafft einen separaten Kanal für Anguss, Angusskanäle und Anschnitte und ermöglicht so eine einfachere Entnahme des Formteils. Hersteller verwenden üblicherweise Dreiplattenformen für Details mit komplexen Angusssystemen oder wenn die Vermeidung von Angussresten auf dem Werkstück gewünscht wird.
- Heißkanalform:Das Anguss- und Angusssystem wird in Heißkanalformen erhitzt, sodass das Material nicht bei jedem Zyklus erstarren und wieder aufschmelzen muss. Das Heißkanalsystem besteht aus beheizten Verteilern und Düsen, die den geschmolzenen Zustand des Kunststoffs aufrechterhalten. Heißkanalformen bieten Vorteile wie kürzere Zykluszeiten, geringeren Materialabfall und eine verbesserte Teilequalität durch Minimierung von Angussresten.
- Kaltkanalform: Kaltkanalformen verfügen über ein traditionelles Kanal- und Anschnittsystem, bei dem der geschmolzene Kunststoff durch Kaltkanäle fließt, die bei jedem Zyklus erstarren. Anschließend entfernen die Bediener die verfestigten Läufer, was zu Materialverschwendung führt. Hersteller verwenden in der Regel komplexe Angussformen für die Produktion kleinerer Stückzahlen oder wenn die Materialkosten aufgrund ihres einfacheren Designs weniger kritisch sind.
- Form einfügen:Einlegeformen integrieren beim Spritzgießen Metall- oder Kunststoffeinsätze in den Formhohlraum. Einsätze können vorab in die Form eingelegt oder durch automatisierte Prozesse eingefügt werden. Diese Form ermöglicht es, zusätzliche Komponenten oder Verstärkungselemente in das Formteil zu integrieren und so dessen Funktionalität oder Festigkeit zu erhöhen.
- Umspritzung: Beim Umspritzen wird ein Material über ein anderes geformt, wobei typischerweise ein starres Kunststoffsubstrat mit einem weicheren Elastomer oder Thermoplast verbunden wird. Dieser Prozess ermöglicht die Herstellung von Teilen mit mehreren Materialien oder Texturen in einer einzigen Form und bietet so verbesserte Griffigkeit, Polsterung oder ästhetische Merkmale.
Faktoren, die die Spritzgusskosten beeinflussen
Die Berücksichtigung dieser Faktoren kann Herstellern dabei helfen, die Kosten des Spritzgießens abzuschätzen und zu optimieren und so ein Gleichgewicht zwischen Qualität, Effizienz und Kosteneffizienz für ihre spezifischen Produktionsanforderungen sicherzustellen.
- Teilekomplexität:Die Komplexität des Teiledesigns spielt eine wichtige Rolle bei der Bestimmung der Spritzgusskosten. Komplizierte Geometrien, Hinterschneidungen, dünne Wände oder komplexe Merkmale erfordern möglicherweise zusätzliche Werkzeuge, Spezialformen oder längere Zyklen, was die Gesamtherstellungskosten erhöht.
- Materialauswahl:Die Wahl des thermoplastischen Materials beeinflusst die Spritzgusskosten. Verschiedene Materialien haben unterschiedliche Preise pro Kilogramm und Faktoren wie Materialverfügbarkeit, Eigenschaften und Verarbeitungsanforderungen können die Gesamtmaterialkosten beeinflussen.
- Werkzeug- und Formenbau: Die anfänglichen Werkzeug- und Formkonstruktionskosten sind bei den Spritzgusskosten von erheblicher Bedeutung. Faktoren wie die Komplexität der Form, die Anzahl der Kavitäten, die Formgröße und das Formmaterial tragen zu den Werkzeug- und Formenherstellungskosten bei. Komplexere Formen oder Formen, die erweiterte Funktionen erfordern, können die Vorabinvestition erhöhen.
- Produktionsvolumen: Das Produktionsvolumen wirkt sich direkt auf die Kosten pro Teil beim Spritzgießen aus. Höhere Stückzahlen führen oft zu Skaleneffekten und senken die Kosten pro Teil. Umgekehrt können bei Produktionsläufen mit geringem Volumen aufgrund von Rüst-, Werkzeug- und Materialverschwendung höhere Kosten anfallen.
- Zykluszeit: Die Zykluszeit, die die Kühl- und Auswurfphasen umfasst, beeinflusst die Produktionskapazität und die Gesamtkosten. Längere Zykluszeiten führen zu einer geringeren Produktionsleistung und möglicherweise höheren Preisen. Durch die Optimierung des Formdesigns, des Kühlsystems und der Prozessparameter können Zykluszeiten minimiert und die Effizienz verbessert werden.
- Qualitätsanforderungen:Strenge Qualitätsanforderungen oder spezifische Zertifizierungen können sich auf die Spritzgusskosten auswirken. Das Einhalten exakter Toleranzen, Anforderungen an die Oberflächenbeschaffenheit oder zusätzliche Tests erfordern möglicherweise andere Ressourcen, Prozesse oder Inspektionen, was die Gesamtkosten erhöht.
- Sekundäroperationen:Wenn die geformten Teile Nachbearbeitungsvorgänge wie Montage, Lackierung oder zusätzliche Endbearbeitungsschritte erfordern, können diese Vorgänge die Gesamtkosten des Spritzgusses erhöhen.
- Lieferant und Standort:Die Wahl des Spritzgusslieferanten und dessen Standort können sich auf die Kosten auswirken. Arbeitskosten, Gemeinkosten, Logistik- und Transportkosten variieren je nach Standort des Lieferanten und wirken sich auf die gesamten Herstellungskosten aus.
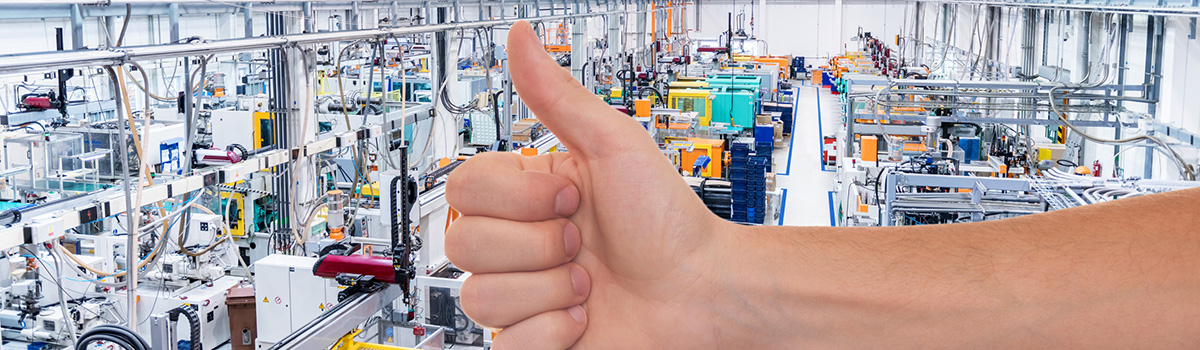
Qualitätskontrolle im Spritzguss
Durch die Implementierung robuster Qualitätskontrollmaßnahmen während des gesamten Spritzgussprozesses können potenzielle Mängel, Abweichungen oder Inkonsistenzen erkannt und behoben werden, sodass die Produktion hochwertiger Teile sichergestellt wird, die den Kundenspezifikationen und -anforderungen entsprechen.
- Prozessüberwachung: Die kontinuierliche Überwachung wichtiger Prozessparameter wie Schmelzetemperatur, Einspritzdruck, Abkühlzeit und Zykluszeit gewährleistet Konsistenz und Wiederholbarkeit bei der Teileproduktion. Echtzeitüberwachung und automatisierte Systeme können Variationen oder Abweichungen von eingestellten Parametern erkennen, was zeitnahe Anpassungen ermöglicht und die Prozessstabilität aufrechterhält.
- Inspektion und Messung:Regelmäßige Überprüfungen und Messungen von Formteilen sind unerlässlich, um Maßgenauigkeit, Teilequalität und Einhaltung der Spezifikationen zu überprüfen. Unsere Dienstleistungen umfassen eine Reihe von Methoden zur Qualitätskontrolle, wie z. B. das Messen von Maßen, die Analyse der Oberflächenqualität, die Durchführung von Sichtprüfungen und die Durchführung von Funktionstests. Zur genauen Auswertung kommen verschiedene Prüftechniken wie Koordinatenmessgeräte (KMG) sowie optische und visuelle Prüfsysteme zum Einsatz.
- Statistische Prozesskontrolle (SPC): Bei SPC handelt es sich um das Sammeln und Analysieren von Prozessdaten zur Überwachung und Steuerung der Spritzgussqualität. Statistische Methoden wie Regelkarten und Prozessfähigkeitsanalysen helfen dabei, Trends zu erkennen, Prozessschwankungen zu erkennen und sicherzustellen, dass der Prozess innerhalb definierter Kontrollgrenzen bleibt. SPC ermöglicht die proaktive Identifizierung von Problemen und erleichtert die Prozessoptimierung.
- Materialprüfung: Durch die Prüfung der Rohstoffe wie Thermoplaste, Additive und Farbstoffe wird deren Qualität und Eignung für den Spritzguss sichergestellt. Zu den Materialtests können die Analyse des Schmelzflussindex (MFI), der mechanischen Eigenschaften, der thermischen Eigenschaften und der Materialzusammensetzung gehören. Die Überprüfung der Materialqualität trägt dazu bei, Fehler und Inkonsistenzen in den Formteilen zu vermeiden.
- Werkzeugwartung und -inspektion:Die ordnungsgemäße Wartung und regelmäßige Inspektion der Spritzgussformen sind entscheidend für die Qualitätssicherung beim Spritzgießen. Regelmäßige Reinigung, Schmierung und Beurteilung der Formkomponenten tragen dazu bei, Verschleiß, Beschädigung oder Verschlechterung zu verhindern, die sich auf die Teilequalität auswirken könnten. Die rechtzeitige Reparatur oder der Austausch abgenutzter oder beschädigter Formkomponenten ist für die Aufrechterhaltung einer gleichbleibenden Formleistung unerlässlich.
- Dokumentation und Rückverfolgbarkeit:Die Führung umfassender Dokumentations- und Rückverfolgbarkeitsaufzeichnungen ist für die Qualitätskontrolle im Spritzguss unerlässlich. Es ist wichtig, Prozessparameter, Prüfergebnisse, Materialinformationen und alle während der Produktion vorgenommenen Änderungen oder Anpassungen aufzuzeichnen. Eine ordnungsgemäße Dokumentation ermöglicht die Rückverfolgbarkeit von Teilen, erleichtert die Ursachenanalyse und gewährleistet eine gleichbleibende Qualität.
- Schulung und Kompetenzentwicklung: Durch die Bereitstellung angemessener Schulungs- und Kompetenzentwicklungsprogramme für Bediener, Techniker und Qualitätskontrollpersonal wird deren Verständnis für Spritzgussprozesse, Qualitätsanforderungen und Inspektionstechniken verbessert. Gut geschultes Personal kann Mängel erkennen, Probleme beheben und Korrekturmaßnahmen effektiv umsetzen und so eine qualitativ hochwertige Produktion sicherstellen.
Häufige Spritzgussfehler und wie man sie vermeidet
Regelmäßige Inspektion, Überwachung und Analyse von Spritzgussprozessen sowie die ordnungsgemäße Wartung und Einstellung von Geräten und Formen können dabei helfen, diese häufigen Fehler zu erkennen und zu beheben.
- Einfallstellen:Einfallstellen sind Vertiefungen oder Vertiefungen auf der Oberfläche des Formteils, die durch ungleichmäßiges Abkühlen oder Schrumpfen entstehen. Um Einfallstellen zu vermeiden, sollten die richtige Position und Gestaltung des Angusses, ein optimales Design des Kühlsystems und eine gleichmäßige Wandstärkenverteilung berücksichtigt werden. Auch eine Erhöhung des Einspritzdrucks oder eine Anpassung der Abkühlzeit können helfen, Einfallstellen zu minimieren.
- Verzug:Unter Verzug versteht man die Verformung oder Biegung eines Formteils nach dem Auswerfen aufgrund ungleichmäßiger Abkühlung oder Eigenspannungen. Die Aufrechterhaltung einer gleichmäßigen Wandstärke, die Verwendung geeigneter Kühlkanäle und die Sicherstellung einer ausgewogenen Füllung und Packung der Form sind entscheidend, um Verformungen zu vermeiden. Die Optimierung der Formtemperatur, die Verwendung geeigneter Entformungswinkel sowie die Steuerung der Materialtemperatur und der Einspritzgeschwindigkeit können dazu beitragen, den Verzug zu minimieren.
- Blitz:Grate entstehen, wenn überschüssiges Material in die Trennfuge der Form fließt, was zu dünnen, unerwünschten Vorsprüngen oder zusätzlichem Material am endgültigen Teil führt. Grate lassen sich wirksam verhindern, indem man auf eine ordnungsgemäße Formkonstruktion achtet, einschließlich der Anwendung einer angemessenen Schließkraft, einer präzisen Ausrichtung und der Verwendung geeigneter Entlüftungstechniken. Durch die Optimierung von Prozessparametern wie Einspritzdruck, Temperatur und Zykluszeit wird der Grat reduziert.
- Kurzer Schuss:Ein schneller Schuss entsteht, wenn das eingespritzte Material den Formhohlraum nicht ausfüllt, was zu einem unvollständigen Teil führt. Um kurze Fotos zu vermeiden, sind die richtige Materialauswahl, die Sicherstellung einer angemessenen Schmelzetemperatur und -viskosität sowie die Aufrechterhaltung eines angemessenen Einspritzdrucks und einer angemessenen Einspritzzeit unerlässlich. Darüber hinaus kann die Überprüfung des Formdesigns auf ausreichende Anguss- und Anschnittgröße sowie eine ordnungsgemäße Entlüftung dazu beitragen, schnelle Schüsse zu verhindern.
- Schweißlinien:Schweißnähte entstehen, wenn zwei oder mehr Fließfronten geschmolzenen Materials aufeinandertreffen und sich verfestigen, was zu einer sichtbaren Linie oder Markierung auf der Teileoberfläche führt. Durch eine gute Anschnitt- und Angusskonstruktion, optimale Schmelzetemperatur und Einspritzgeschwindigkeit sowie die Anpassung des Materialflusses und der Teilegeometrie können Bindenähte minimiert werden. Die Analyse des Formflusses und die Optimierung der Anschnittplatzierung können ebenfalls dabei helfen, Schweißnähte zu verhindern oder zu mildern.
- Brandflecken:Brandflecken sind Verfärbungen oder schwarze Flecken auf der Oberfläche des Formteils, die durch übermäßige Hitze oder Überhitzung des Materials entstehen. Durch die Vermeidung extremer Schmelzetemperaturen, die Verwendung geeigneter Kühlkanäle und die Optimierung der Zykluszeit können Brandflecken vermieden werden. Eine ausreichende Entlüftung, die richtige Anschnittkonstruktion und die Kontrolle der Formtemperatur tragen ebenfalls zur Minimierung von Brandflecken bei.
Nachbearbeitungsvorgänge: Endbearbeitung und Montage
Nach dem Spritzgießen erfordern viele Formteile möglicherweise zusätzliche Nachbearbeitungs- und Montagevorgänge, um das gewünschte Endprodukt zu erhalten. Zu diesen Nachbearbeitungsvorgängen können gehören:
- Trimmen:Entfernen Sie überschüssiges Material oder Grate rund um das Formteil mit Besäum- oder Schneidwerkzeugen.
- Oberflächenbehandlung:Verbessern des Aussehens oder der Funktionalität der Teileoberfläche durch verschiedene Techniken wie Lackieren, Beschichten oder Strukturieren.
- Montage:Zusammenfügen mehrerer Formteile oder Hinzufügen von Komponenten wie Befestigungselementen, Einsätzen oder Etiketten, um das Endprodukt fertigzustellen.
- Testing:Überprüfung der Teilequalität und -funktionalität durch verschiedene Testmethoden wie Dimensionsanalyse, Materialeigenschaftenprüfung oder Leistungsprüfung.
- Verpackung und Versand:Ordnungsgemäße Verpackung und Etikettierung des fertigen Produkts für den Versand an Kunden oder Endverbraucher.
Die Auswahl der Nachformungsvorgänge hängt von der spezifischen Anwendung und den gewünschten Endprodukteigenschaften ab. Um die gewünschte absolute Produktqualität und Funktionalität zu erreichen, ist eine enge Zusammenarbeit zwischen Spritzgussexperten, Finishing- und Montagespezialisten und dem Kunden entscheidend. Eine ordnungsgemäße Planung und Integration von Nachbearbeitungsvorgängen in den Herstellungsprozess kann dazu beitragen, eine effiziente Produktion und eine pünktliche Lieferung hochwertiger Produkte sicherzustellen.
Spritzguss im Vergleich zu anderen Kunststoffherstellungsverfahren
Jeder Kunststoffherstellungsprozess hat Vorteile und Einschränkungen, wodurch er für unterschiedliche Anwendungen geeignet ist.
- Spritzguss: Spritzgießen ist ein äußerst vielseitiges und weit verbreitetes Herstellungsverfahren zur Herstellung von Kunststoffteilen. Es bietet Vorteile wie eine hohe Produktionseffizienz, eine präzise Teilereplikation und die Möglichkeit, komplexe Geometrien zu erstellen. Das Spritzgießen eignet sich für Großserienproduktionen und ermöglicht die Verwendung einer breiten Palette thermoplastischer Materialien. Es bietet eine hervorragende Maßhaltigkeit und Oberflächengüte und eignet sich daher ideal für verschiedene Branchen wie die Automobilindustrie, Konsumgüter und medizinische Geräte.
- Blasformen: Blasformen ist ein Verfahren, das hauptsächlich zur Herstellung hohler Kunststoffteile wie Flaschen, Behälter und Automobilkomponenten verwendet wird. Dabei wird Kunststoff geschmolzen und in einen Formhohlraum aufgeblasen, wodurch die gewünschte Form entsteht. Das Blasformen eignet sich für die Massenproduktion und kann große, leichte Teile mit gleichmäßiger Wandstärke herstellen. Im Vergleich zum Spritzgießen sind jedoch die Teilekomplexität und die Materialauswahl eingeschränkt.
- Thermoformen:Thermoformen ist ein Verfahren zur Herstellung von Kunststoffteilen durch Erhitzen einer thermoplastischen Folie und deren Formgebung mithilfe von Formen oder Vakuumformen. Es findet häufig Verwendung in Verpackungen, Einwegprodukten und großformatigen Produkten wie Tabletts und Abdeckungen. Thermoformen bietet eine kostengünstige Produktion großer Teile und ermöglicht ein schnelles Prototyping. Im Vergleich zum Spritzguss bestehen jedoch Einschränkungen hinsichtlich der Teilekomplexität, der Materialauswahl und der Maßhaltigkeit.
- Extrusion:Extrusion ist ein kontinuierlicher Prozess zur Herstellung von Kunststoffprofilen, -platten, -schläuchen und -folien. Dabei wird Kunststoffharz geschmolzen und durch eine Matrize gepresst, um die gewünschte Form zu erzeugen. Die Extrusion eignet sich zur Herstellung langer, kontinuierlicher Längen von Kunststoffprodukten mit einheitlichem Querschnitt. Während die Extrusion hohe Produktionsraten und Kosteneffizienz bietet, sind sie im Vergleich zum Spritzguss hinsichtlich komplexer Teilegeometrien und präziser Maßkontrolle begrenzt.
- Formpressen:Beim Formpressen wird eine vorher abgemessene Menge duroplastischen Materials in einen beheizten Formhohlraum gegeben und unter hohem Druck komprimiert, bis es aushärtet. Es wird häufig bei der Herstellung von Teilen mit hoher Festigkeit und Dimensionsstabilität verwendet, beispielsweise für Automobilkomponenten und elektrische Isolierungen. Formpressen bietet eine gute Teilekonsistenz, eine hohe Produktionseffizienz und die Möglichkeit, eine breite Palette von Materialien zu verwenden. Im Vergleich zum Spritzgießen sind jedoch die Teilekomplexität und die Zykluszeit begrenzt.
Anwendungen des thermoplastischen Spritzgusses
Thermoplastisches Spritzgießen wird aufgrund seiner Vielseitigkeit, Effizienz und Kosteneffizienz in verschiedenen Branchen häufig eingesetzt. Zu den Anwendungen des thermoplastischen Spritzgießens gehören:
- Automobilindustrie: Die Automobilindustrie verwendet in großem Umfang thermoplastisches Spritzgießen zur Herstellung verschiedener Komponenten, darunter Innen- und Außenverkleidungen, Armaturenbretter, Türverkleidungen, Stoßstangen und elektrische Anschlüsse. Der Prozess ermöglicht eine präzise Teilereplikation, komplexe Geometrien und leichte Materialien und verbessert so die Kraftstoffeffizienz und Designflexibilität.
- Konsumgüter:Spritzguss findet vielfältige Anwendung bei der Herstellung von Konsumgütern wie Haushaltsgeräten, elektronischen Geräten, Verpackungsbehältern und Spielzeug. Das Verfahren ermöglicht die Massenproduktion langlebiger, qualitativ hochwertiger Produkte mit einheitlichen Abmessungen und Oberflächenbeschaffenheit. Es ermöglicht auch Anpassungsoptionen und schnelle Produktiterationen.
- Medizinische Geräte:Das Spritzgießen spielt in der medizinischen Industrie eine entscheidende Rolle bei der Herstellung einer breiten Palette von Geräten, darunter Spritzen, chirurgische Instrumente, implantierbare Komponenten und Arzneimittelverabreichungssysteme. Das Verfahren gewährleistet die Herstellung steriler, präziser und biokompatibler Teile, die den strengen regulatorischen Anforderungen des Gesundheitssektors entsprechen.
- Elektronik- und Elektroindustrie:Die Elektronikindustrie nutzt Spritzguss zur Herstellung elektrischer Steckverbinder, Gehäuse, Schalter und anderer Komponenten. Das Verfahren bietet eine hohe Maßgenauigkeit, eine hervorragende Oberflächengüte und die Möglichkeit, Funktionen wie Umspritzen und Umspritzen zu integrieren, was eine effiziente Produktion komplexer elektronischer Baugruppen ermöglicht.
- Verpackungsindustrie:Verschiedene Branchen, darunter Lebensmittel und Getränke, Pharmazeutika und Körperpflege, verwenden häufig Spritzguss zur Herstellung von Verpackungsbehältern, Kappen, Verschlüssen und Flaschen aus Kunststoff. Der Prozess ermöglicht die Schaffung leichter, langlebiger und ästhetisch ansprechender Verpackungslösungen mit effizienten Herstellungszyklen.
- Luft-und Raumfahrtindustrie:In der Luft- und Raumfahrtbranche wird Spritzguss zur Herstellung leichter und leistungsstarker Komponenten wie Luftkanäle, Halterungen, Innenverkleidungen und Strukturteile eingesetzt. Der Prozess ermöglicht die Verwendung fortschrittlicher Materialien und komplizierter Teilegeometrien und trägt so zur Gewichtsreduzierung und verbesserten Kraftstoffeffizienz bei.
Umweltauswirkungen des thermoplastischen Spritzgusses
Thermoplastisches Spritzgießen ist aufgrund seiner vielen Vorteile ein beliebtes Herstellungsverfahren, es ist jedoch auch wichtig, seine Auswirkungen auf die Umwelt zu berücksichtigen. Hier sind einige Punkte, die Sie beachten sollten:
- Materialeffizienz:Thermoplastisches Spritzgießen fördert die Materialeffizienz durch Minimierung des Abfalls. Der Prozess nutzt eine präzise Kontrolle über die in die Form eingespritzte Materialmenge, wodurch der Bedarf an überschüssigem Material reduziert wird. Hersteller können auch Nachschleif- und Recyclingtechniken einsetzen, um Schrott oder Ausschussteile wiederzuverwenden und so den Materialabfall weiter zu reduzieren.
- Energieverbrauch:Hersteller konzipieren Spritzgießmaschinen energieeffizient, wobei moderne Modelle über fortschrittliche Technologien wie Servomotoren und Antriebe mit variabler Drehzahl verfügen. Diese Funktionen optimieren den Energieverbrauch, indem sie den Stromverbrauch während des Formens reduzieren, was zu einem geringeren Energiebedarf und einer geringeren Umweltbelastung führt.
- Abfallwirtschaft:Während die Materialverschwendung minimiert wird, sollten Hersteller angemessene Abfallmanagementpraktiken für den Umgang mit übrig gebliebenen Materialien, Angüssen oder Angusskanälen einführen. Hersteller können Recyclingprogramme einrichten, um beim Spritzgießen anfallende Kunststoffabfälle zu sammeln und wiederzuverwenden und so den Abfall auf Mülldeponien zu reduzieren.
- Emissionsreduzierung: Beim thermoplastischen Spritzgießen entstehen im Allgemeinen weniger Emissionen als bei anderen Herstellungsverfahren. Hersteller können Emissionen reduzieren, indem sie umweltfreundliche Materialien verwenden, energieeffiziente Geräte einsetzen und fortschrittliche Abgas- und Filtersysteme einsetzen, um freigesetzte Emissionen aufzufangen.
- Nachhaltige Materialauswahl:Die Auswahl thermoplastischer Materialien kann die Umweltverträglichkeit des Spritzgießens erheblich beeinflussen. Die Entscheidung für biologisch abbaubare oder biobasierte Kunststoffe sowie recycelte oder recycelbare Materialien kann dazu beitragen, den gesamten ökologischen Fußabdruck des Prozesses zu reduzieren.
Überlegungen zum Lebenszyklus: Die Berücksichtigung des gesamten Lebenszyklus des geformten Produkts ist für die Bewertung seiner Umweltauswirkungen von entscheidender Bedeutung. Während der Entwurfs- und Materialauswahlphasen sollten Hersteller Faktoren wie die Haltbarkeit des Teils, seine Recyclingfähigkeit und die Möglichkeit einer Entsorgung oder Wiederverwendung am Ende der Lebensdauer berücksichtigen.
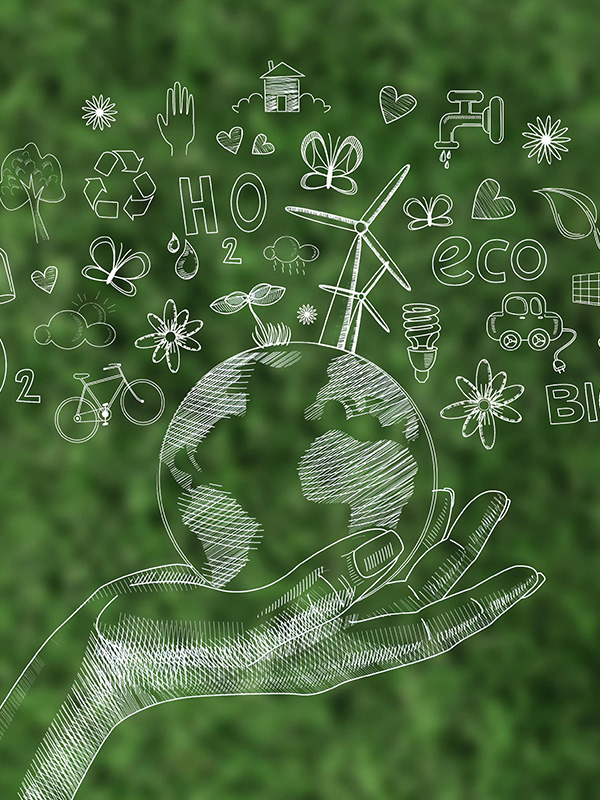
Zukunft des thermoplastischen Spritzgusses
Die Zukunft des thermoplastischen Spritzgießens sieht vielversprechend aus, mit kontinuierlichen technologischen Fortschritten und einer steigenden Nachfrage nach hochwertigen Präzisionsteilen in verschiedenen Branchen. Zu den wichtigsten Entwicklungen, die in den kommenden Jahren erwartet werden, gehören:
- Verstärkter Einsatz von Automatisierung und Robotik zur Verbesserung der Effizienz und Kostensenkung.
- Die Bemühungen konzentrieren sich auf die Entwicklung neuer Materialien und Prozesse, um die Teileleistung zu verbessern und neue Anwendungen zu ermöglichen.
- Es handelt sich um eine zunehmende Einführung nachhaltiger Praktiken, wie z. B. die Verwendung recycelter Materialien und die Optimierung des Energieverbrauchs, um die Umweltauswirkungen des Spritzgießens zu reduzieren.
- Stärkere Integration digitaler Technologien wie 3D-Druck und Simulationssoftware zur Verbesserung von Design- und Produktionsprozessen.
Der weltweite Spritzgussmarkt wächst, insbesondere in Schwellenländern, angetrieben durch die steigende Nachfrage nach Kunststoffprodukten in verschiedenen Branchen.
Auswahl des richtigen Spritzgusspartners
Die Wahl des richtigen Spritzgusspartners ist entscheidend für den Erfolg Ihres Projekts. Nehmen Sie sich die Zeit, mehrere Optionen zu bewerten, Besuche vor Ort durchzuführen und ausführliche Gespräche zu führen, um eine kompatible und langfristige Partnerschaft sicherzustellen.
- Fachwissen und Erfahrung:Suchen Sie nach einem Spritzgusspartner mit umfassendem Wissen und Erfahrung in der Branche. Sie sollten über eine nachgewiesene Erfolgsbilanz bei der Bereitstellung hochwertiger Produkte und Lösungen für Kunden in verschiedenen Branchen verfügen. Berücksichtigen Sie ihr Verständnis für verschiedene Materialien, Formenkonstruktionen und Herstellungsprozesse.
- Fertigungsmöglichkeiten: Bewerten Sie die Fertigungskapazitäten des Spritzgusspartners. Stellen Sie sicher, dass sie über eine gut ausgestattete Anlage mit modernen Maschinen und Technologien verfügen, um Ihre Projektanforderungen zu erfüllen. Berücksichtigen Sie ihre Produktionskapazität, ihre Fähigkeit, unterschiedliche Teilegrößen und -komplexitäten zu handhaben, und ihre Fähigkeit, Ihre gewünschten Produktionsmengen und Zeitpläne einzuhalten.
- Qualitätssicherung:Qualität steht beim Spritzgießen an erster Stelle. Bewerten Sie die Qualitätskontrollsysteme und Zertifizierungen des potenziellen Partners. Suchen Sie nach Partnern, die strenge Qualitätsstandards einhalten, über robuste Inspektionsprozesse verfügen und umfassende Tests durchführen, um die Qualität und Konsistenz der Teile sicherzustellen.
- Design- und Engineering-Unterstützung:Ein zuverlässiger Spritzgusspartner sollte Design- und Engineering-Unterstützung bieten, um das Design Ihres Teils für die Herstellbarkeit zu optimieren. Sie sollten über qualifizierte Ingenieure verfügen, die wertvolle Beiträge zur Materialauswahl, zum Formendesign und zur Prozessoptimierung leisten können, um die Qualität und Effizienz der Teile zu verbessern.
- Kostenwettbewerbsfähigkeit:Obwohl die Kosten nicht der einzige entscheidende Faktor sein sollten, ist es wichtig, die Preisgestaltung und Kostenwettbewerbsfähigkeit des Spritzgusspartners zu bewerten. Fordern Sie detaillierte Angebote an und berücksichtigen Sie Werkzeugkosten, Materialkosten, Arbeitskosten und alle zusätzlichen Dienstleistungen, die sie anbieten.
- Kommunikation und Zusammenarbeit:Effektive Kommunikation und Zusammenarbeit sind für eine erfolgreiche Partnerschaft unerlässlich. Stellen Sie sicher, dass der Spritzgusspartner über gute Kommunikationskanäle verfügt, auf Ihre Anfragen reagiert und regelmäßige Projektaktualisierungen bereitstellen kann. Durch einen kooperativen Ansatz können wir sicherstellen, dass wir Ihre Anforderungen erfüllen und etwaige Herausforderungen umgehend angehen.
- Kundenreferenzen und Bewertungen:Suchen Sie nach Kundenreferenzen oder lesen Sie Rezensionen/Erfahrungsberichte, um Einblicke in die Erfahrungen anderer Kunden mit dem Spritzgusspartner zu erhalten. Die Beschaffung dieser Informationen kann dabei helfen, die Zuverlässigkeit, Schnelligkeit und den allgemeinen Grad der Kundenzufriedenheit zu bestimmen.
Zusammenfassung
Thermoplastisches Spritzgießen ist eine vielseitige und kostengünstige Methode zur Herstellung von Kunststoffteilen in großen Mengen. Seine Fähigkeit, komplexe Formen mit hoher Präzision und Konsistenz herzustellen, ist zu einer beliebten Wahl für verschiedene Branchen geworden, darunter Automobil, Medizin, Elektronik und Konsumgüter. Wenn Sie die verschiedenen Aspekte des thermoplastischen Spritzgießens verstehen, einschließlich seiner Vor- und Nachteile sowie Designüberlegungen, können Sie fundierte Entscheidungen über die Auswahl des richtigen Spritzgießpartners für Ihre Geschäftsanforderungen treffen.