ઈન્જેક્શન મોલ્ડિંગની સામાન્ય મોલ્ડિંગ ખામીના ઉકેલો
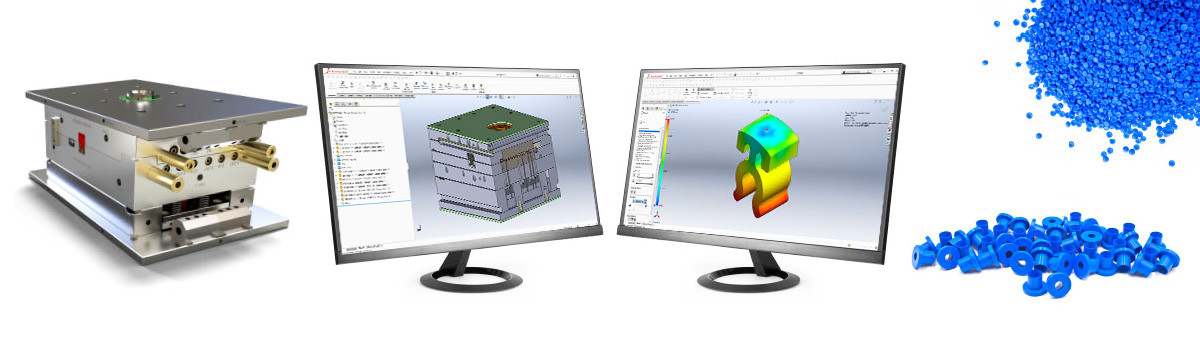
પ્લાસ્ટિક ઇન્જેક્શન મોલ્ડિંગ ભાગો પર પ્રક્રિયા કરવા માટે મોલ્ડનો ઉપયોગ કરતી વખતે ખામી સામાન્ય છે, અને આ પ્રક્રિયાની કાર્યક્ષમતાને મોટા ભાગે અસર કરે છે. નીચેના સામાન્ય મોલ્ડિંગ ખામીઓ અને પ્લાસ્ટિક ઈન્જેક્શન મોલ્ડ ભાગો માટે ઉકેલો છે.
ટૂંકા શોટ
શોર્ટ શોટ્સ એ બનાવેલ ઉત્પાદનોનો સંદર્ભ આપે છે કારણ કે મોલ્ડ સંપૂર્ણ રીતે ભરાયેલા નથી.
આ ખામી સામાન્ય રીતે ગેટથી દૂરના સ્થાને અથવા ઘાટ પરના સાંકડા વિસ્તારોમાંથી જ પહોંચી શકાય તેવા ભાગો પર દેખાય છે કારણ કે સાંકડા વિસ્તારો પીગળવાના પ્રવાહને અસર કરી શકે છે.
શોર્ટ શોટ માઇક્રો ફ્લો માર્કસનું કારણ બની શકે છે અથવા ઉત્પાદનનો મોટો ભાગ દેખીતી રીતે ગુમ થઈ શકે છે.
કારણ:
ટૂંકા શોટના કારણોમાં શામેલ છે:
મોલ્ડમાં ઇન્જેક્ટ કરાયેલ કાચો માલ પૂરતો નથી.
ગલનનો પ્રતિકાર મોટો છે, પરિણામે ઘાટ સંપૂર્ણપણે ભરી શકાતો નથી.
ઘાટનું વેન્ટિંગ નબળું હોય છે અને પોલાણની ઉત્પત્તિનું કારણ બને છે જે મેલ્ટને અવરોધે છે, જેનાથી પીગળવું ઘાટના કેટલાક વિસ્તારોમાં વહેતું નથી.
દફન
મોલ્ડ પોલાણમાંથી ઉત્પાદનમાં બહાર કાઢવામાં આવેલા વધારાના કાચા માલના સંલગ્નતામાંથી બરર્સ ઉત્પન્ન થાય છે.
આ ખામી ઉત્પાદનની કિનારીઓ અથવા ઘાટના દરેક બનેલા ભાગ પર રહેશે. કાચો માલ મોલ્ડમાંથી અથવા મૂવિંગ અને ફિક્સિંગ મોલ્ડની બોન્ડિંગ સાઇટ્સમાંથી ઓવરફ્લો થઈ શકે છે.
બર્ર્સ મોલ્ડ કોર પર પણ મળી શકે છે, જે હાઇડ્રોલિક દબાણ અથવા કોણીય પિનને કારણે છે.
burrs ની તીવ્રતા બદલાય છે, ક્યારેક પાતળા, ક્યારેક ગાઢ.
કારણ:
બર્ર્સ માટેના કારણોમાં શામેલ છે:
ક્લેમ્પિંગ મોલ્ડ સપાટીને નુકસાન થાય છે અથવા ભારે પહેરવામાં આવે છે.
મૂવિંગ મોલ્ડ અને ફિક્સિંગ મોલ્ડ જ્યારે લૉક હોય ત્યારે તે અસ્પષ્ટ હોય છે.
મોલ્ડમાં કાચા માલનું દબાણ મોલ્ડ ક્લેમ્પિંગ ફોર્સ કરતા વધારે છે.
ઉપરોક્ત ઉલ્લેખિત ત્રીજી સ્થિતિ વિવિધ કારણોથી પરિણમશે. નીચેની પરિસ્થિતિઓમાં, કાચા માલનું દબાણ મોલ્ડ ક્લેમ્પિંગ ફોર્સ કરતા વધારે છે.
ઈન્જેક્શન મોલ્ડના પ્રથમ તબક્કે (મોલ્ડ ફિલિંગ સ્ટેજ) ખૂબ જ કાચો માલ ભરવામાં આવે છે, જે મોલ્ડની અંદર દબાણ વધારે છે.
મોલ્ડ ભરવાની પ્રક્રિયા દરમિયાન, ગલન પ્રવાહનો મોટો પ્રતિકાર પણ ઘાટની અંદર દબાણ વધારશે.
પ્રેશર હોલ્ડિંગ સ્ટેજ દરમિયાન મોલ્ડ કેવિટી પ્રેશર ખૂબ વધારે હોય છે.
મોલ્ડ ક્લેમ્પિંગ ફોર્સ પર્યાપ્ત નથી.
અધોગતિ
વિઘટન ઘણા પરિણામો તરફ દોરી શકે છે. સમસ્યાનું પ્રમાણ અને ગંભીરતા પણ અલગ અલગ હોય છે. સૌથી ગંભીર કિસ્સામાં, તે ઉત્પાદનના સંપૂર્ણ વિકૃતિકરણ અને નબળા યાંત્રિક ગુણધર્મોનું કારણ બની શકે છે. સ્થાનિક અધોગતિ માત્ર શ્યામ પટ્ટાઓ અથવા ફોલ્લીઓનું કારણ બનશે.
કારણ:
કાચા માલને નુકસાન થવાથી અધોગતિ થાય છે. લાંબી સાંકળના અણુઓ કે જે પ્લાસ્ટિક બનાવે છે તે અતિશય ગરમી અથવા અતિશય શીયર સ્ટ્રેસની ક્રિયા હેઠળ વિઘટિત થશે. પરમાણુઓના વિઘટન દરમિયાન, અસ્થિર ગેસ અધોગતિની પ્રક્રિયાને ઝડપી બનાવશે, જે કાચા માલના રંગને રંગવાનું કારણ બનશે. મોટી માત્રામાં પરમાણુઓનું વિઘટન આખરે કાચા માલની સામગ્રીને તોડી નાખશે અને યાંત્રિક ગુણધર્મોને નકારાત્મક અસર કરશે.
સામગ્રી બેરલના અસમાન તાપમાનને કારણે સ્થાનિક અધોગતિ થઈ શકે છે.
નીચેની પરિસ્થિતિઓમાં અધોગતિ થઈ શકે છે:
મટિરિયલ બેરલ અથવા હોટ રનર સિસ્ટમમાં કાચા માલને વધુ ગરમ કરવામાં આવી રહ્યો છે.
કાચો માલ બેરલમાં લાંબા સમય સુધી રહે છે.
ઈન્જેક્શન મોલ્ડિંગ પ્રક્રિયા દરમિયાન, કાચા માલ પર દબાણયુક્ત દબાણ ખૂબ મોટું છે. જો નોઝલ અવરોધિત છે, અથવા દરવાજા અને રનર ખૂબ સાંકડા છે, તો તે દબાણમાં વધારો કરશે.
વિકૃતિ
સામાન્ય પરિસ્થિતિઓમાં, ઉત્પાદનોના આકાર મોલ્ડના આકાર સાથે સુસંગત હોવા જોઈએ. વિરૂપતા ઉત્પાદનોની વિકૃતિનો સંદર્ભ આપે છે.
જ્યારે સ્થિતિ વધુ ખરાબ થાય છે, ત્યારે ઉત્પાદનો જ્યારે બીબામાંથી બહાર કાઢવામાં આવે છે ત્યારે તે સંપૂર્ણપણે વિકૃત થઈ જાય છે. જ્યારે સ્થિતિ ગંભીર નથી, ત્યારે ઉત્પાદનના આકારમાં નાની અનિયમિતતા દેખાશે.
લાંબા પરંતુ આધાર વગરની કિનારીઓ અથવા મોટા વિમાનો એવા વિસ્તારો છે જે વિરૂપતા માટે સૌથી વધુ સંવેદનશીલ હોય છે.
કારણ:
વિકૃતિના કારણો:
જ્યારે મોલ્ડ છોડવામાં આવે ત્યારે તાપમાન ખૂબ ઊંચું હોય છે.
જેમ કે જાડા અને પાતળા વિસ્તારોમાં ઠંડકનો સમય અલગ હોય છે, અથવા મોલ્ડને ખસેડવા અને ફિક્સિંગ મોલ્ડમાં મોલ્ડ તાપમાનનો તફાવત, ઉત્પાદનોની અંદર સંકોચન અલગ હોય છે.
ભરતી વખતે મોલ્ડનો પ્રવાહ સરળ હોતો નથી (કહેવાતા "ફ્રીઝિંગ ઓરિએન્ટેશન") અથવા પ્રેશર હોલ્ડિંગ સ્ટેજ પર મોલ્ડ કેવિટીની અંદરનું દબાણ ખૂબ વધારે હોય છે.
અશુદ્ધિઓ
અશુદ્ધિઓ ઘણીવાર વિવિધ રંગો, પેચ અથવા પટ્ટાઓમાં ફોલ્લીઓના સ્વરૂપમાં દેખાય છે. સૌથી સામાન્ય એક બ્લેક સ્પોટ છે.
અશુદ્ધિઓ માત્ર નાના ફોલ્લીઓ હોઈ શકે છે, પરંતુ જ્યારે તે ગંભીર હોય ત્યારે સ્પષ્ટ પટ્ટાઓ અથવા ડી-કલરિંગનો મોટો ભાગ પણ હોઈ શકે છે.
કારણ:
અશુદ્ધિઓ કાચા માલ સાથે મિશ્રિત વિવિધ વસ્તુઓને કારણે થાય છે, જેમ કે:
કાચો માલ જ્યારે તેને બેરલમાં લઈ જવામાં આવે છે ત્યારે તેને વિવિધ વસ્તુઓ સાથે મિશ્રિત કરવામાં આવે છે.
કાચા માલનું વિઘટન કોઈપણ કટીંગ મિકેનિઝમમાંથી પડતું હોઈ શકે છે અને કાચી સામગ્રીમાં મિશ્રિત થઈ શકે છે, જેમ કે મશીન બોલ્ટ, ડ્રાયિંગ ડ્રમની આંતરિક દિવાલ, સાંધા/નોઝલ.
લુપ્તતા
લેમિનેશન ઉત્પાદનોની સપાટી પર "ત્વચાની અસર" જનરેટ કરશે, જે ઉત્પાદનો અને અન્ય કાચી સામગ્રીની સપાટીના ગુણધર્મો અને ટેક્સચરમાં તફાવતને કારણે થાય છે, અને તે છાલવાળી ત્વચા બનાવે છે જેને દૂર કરી શકાય છે.
જ્યારે લેમિનેશન ગંભીર હોય છે, ત્યારે સમગ્ર ક્રોસ સેક્શન વિસ્તાર વિવિધ સ્તરોથી બનેલો હોય છે, અને એકસાથે ઓગળવામાં આવ્યો નથી. જ્યારે ખામીઓ ઓછી સ્પષ્ટ હોય છે, ત્યારે ઉત્પાદનોનો દેખાવ જરૂરિયાતોને પૂર્ણ કરી શકે છે, પરંતુ ઉત્પાદનોના યાંત્રિક ગુણધર્મોને તોડી નાખશે.
કારણ:
લેમિનેશનના બે મુખ્ય કારણો છે. પ્રથમ એ છે કે જ્યારે બે અલગ-અલગ પ્રકારની કાચી સામગ્રી ખોટી રીતે ભળી જાય છે. બે કાચા માલના દબાણ હેઠળ એક જ સમયે બેરલમાં પરિવહન કરવામાં આવશે. જો કે, જ્યારે મોલ્ડને ઠંડું કરવામાં આવે ત્યારે તેને એકસાથે ઓગળી શકાતું નથી, જેમ કે ઉત્પાદનો બનાવવા માટે વિવિધ સ્તરોને બળપૂર્વક એકસાથે દબાવવામાં આવે છે.
બીજું: જો ઠંડા પીગળને સાંકડા દરવાજામાંથી પસાર થવાની ફરજ પાડવામાં આવે છે, તો દબાણમાં તણાવ પેદા થશે. ખૂબ વધારે શીયર સ્ટ્રેસને કારણે અગાઉથી ઓગળેલા મેલ્ટ લેયરને સંપૂર્ણપણે ફ્યુઝ કરી શકાતું નથી.
મિશ્રણનું જોખમ:
એક બાબત જેનું ધ્યાન રાખવું જોઈએ તે એ છે કે કેટલાક કાચા માલને એકસાથે મિશ્રિત કરવાથી મજબૂત રાસાયણિક પ્રતિક્રિયા થશે, જેમ કે PVC અને Avetal મિશ્રિત ન હોવા જોઈએ.
સિલ્વર રેખીય
સ્લિવર રેખીય માત્ર સ્થાનિક ઘટના હોઈ શકે છે, પરંતુ જ્યારે તે ગંભીર હોય ત્યારે સમગ્ર સપાટી પર વિસ્તૃત થઈ શકે છે.
સિલ્વર રેખીય ઉત્પાદનોના દેખાવને અસર કરશે અને ઉત્પાદનોના યાંત્રિક ગુણધર્મોને પણ નુકસાન પહોંચાડશે.
કારણ:
નીચેના બે બિંદુઓ સિલ્વર રેખીયનું કારણ બને છે:
કાચો માલ ભીનો છે અને તેમાંના કેટલાક હવામાં વરાળને શોષી લેશે. જો કાચો માલ ખૂબ ભીનો હોય, તો દબાણયુક્ત વરાળ ઉચ્ચ તાપમાન અને બેરલના ઉચ્ચ દબાણ હેઠળ ઉત્પન્ન થઈ શકે છે. આ વરાળ ઉત્પાદનની સપાટીને તોડીને ચાંદીના પટ્ટાઓ બનાવે છે.
ઓગળવાથી થર્મલ નુકસાન થયું છે અને સ્થાનિક અધોગતિ પેદા કરે છે. ઉત્પન્ન થયેલ અસ્થિર ગેસ મોલ્ડ પરની સપાટી પર અવરોધિત થશે અને ઉત્પાદનોની સપાટી પર પટ્ટાઓ પેદા કરશે.
આ અધોગતિ જેટલું ખરાબ નથી. જ્યાં સુધી મેલ્ટનું તાપમાન ઊંચું હોય અથવા પ્લાસ્ટિસાઇઝેશન દરમિયાન શીયર સ્ટ્રેસને આધિન હોય અથવા મોલ્ડમાં ઇન્જેક્ટ કરવામાં આવે ત્યાં સુધી આવું થઈ શકે છે.
ગ્લોસ/શેડો
ઉત્પાદનોની સપાટીની પૂર્ણાહુતિ મોલ્ડની જેમ જ હોવી જોઈએ. જ્યારે બેની સપાટીની પૂર્ણાહુતિ અલગ હોય છે, ત્યારે ચળકાટ/છાયાની ખામીઓ જોવા મળે છે.
જ્યારે ખામીઓ આવી હોય ત્યારે સપાટી અંધકારમય હશે, અને ખરબચડી સપાટી સરળ અને ચળકતી હશે.
કારણ:
ગ્લોસ/શેડોના કારણોમાં નીચેનાનો સમાવેશ થાય છે:
ઓગળવું અન-સરળ વહે છે અથવા ઘાટની સપાટીનું તાપમાન ઓછું છે, પરિણામે જ્યારે મટિરિયલ મોલ્ડિંગ કરવામાં આવે ત્યારે ઘાટની સપાટીની પૂર્ણાહુતિ ડુપ્લિકેટ થઈ શકતી નથી.
પ્રેશર હોલ્ડિંગ દરમિયાન, પોલાણમાં દબાણ એટલું ઊંચું હોતું નથી કે સામગ્રી ઠંડકની પ્રક્રિયામાં ઘાટની સપાટી પર ચોંટી જાય છે, જેનાથી સંકોચનના ગુણ રહે છે.
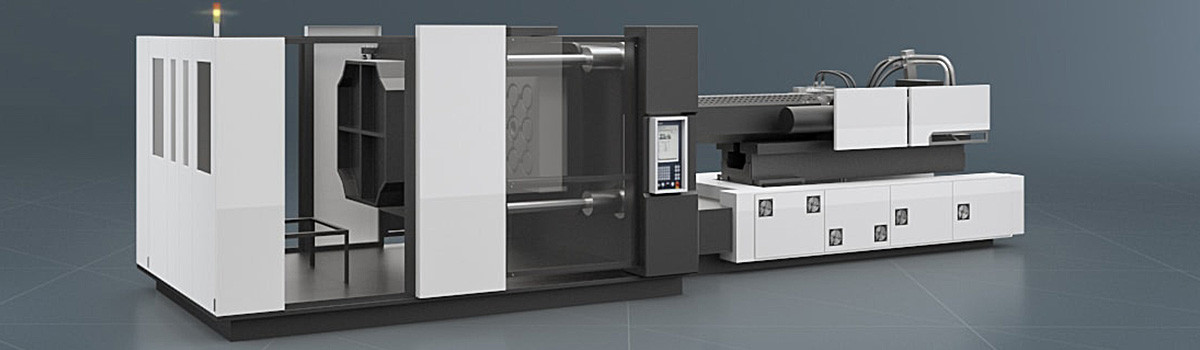
પ્રવાહના ગુણ
પ્રવાહના ગુણ ઉત્પાદનોની સપાટી પર બહુવિધ સ્વરૂપોમાં મળી શકે છે. સામાન્ય રીતે, તે છાયા વિસ્તાર બનાવશે.
પ્રવાહના ગુણ ઉત્પાદનોની સપાટી પર કોઈ એમ્બોસિંગ અથવા ડિપ્રેશન પેદા કરતા નથી, જે આંગળીઓથી અનુભવી શકાતા નથી. આ ખામીને ડ્રેગ માર્ક્સ, ગોસ્ટિંગ અને શેડોઝ પણ કહેવામાં આવે છે.
જ્યારે પ્રવાહના ગુણ સ્પષ્ટ હોય, ત્યારે તે ગ્રુવ્સ પેદા કરશે અને ઉત્પાદનોની સપાટી પર નિશાનો જેવી ખામીઓ છોડી દેશે.
કારણ:
પ્રવાહના ગુણ શોધી શકાય છે જ્યારે:
મેલ્ટની પ્રવાહક્ષમતા નબળી હોય છે અથવા ઘાટની સપાટીનું તાપમાન ઓછું હોય છે, જેના પરિણામે મોલ્ડ ભરવાની પ્રક્રિયામાં પ્લાસ્ટિકનો મોટો પ્રવાહ પ્રતિકાર થાય છે.
મોલ્ડ ફિલિંગમાં, પ્રતિકાર સાથે મેલ્ટ ફ્લો, જે ડાઇની અસમાન સપાટી, ડાઇ સપાટી પર છાપવામાં આવેલા માર્ક અથવા પેટર્ન અથવા ફિલિંગ પ્રક્રિયા દરમિયાન ઓગળેલા પ્રવાહની દિશામાં ફેરફારને કારણે થઈ શકે છે.
સંયુક્ત રેખા
જોડાવાની લાઇન ત્યારે જનરેટ થાય છે જ્યારે મોલ્ડ ભરવા દરમિયાન બે પીગળેલા મોરચા મળે છે, અને ઉત્પાદનની સપાટી પર લાઇનની જેમ દેખાશે.
જોઈન્ટિંગ લાઇન એ ઉત્પાદનોની સપાટી પરની ક્રેકીંગ લાઇન જેવી છે, જે શોધવા માટે સ્પષ્ટ નથી.
મોલ્ડ ડિઝાઇન કરતી વખતે, કેટલીક દૃશ્યમાન સાંધાવાળી રેખાઓ અનિવાર્ય છે. આ કિસ્સામાં, ઉત્પાદનોની મજબૂતાઈ અને દેખાવને નુકસાન ન થાય તે માટે શક્ય તેટલી સાંધાની લાઇન ટૂંકી કરો.
કારણ:
મેલ્ટ ફ્રન્ટની પેઢી માટે ઘણા કારણો છે. સૌથી સંભવિત કારણ મોલ્ડ કોરની કિનારીઓ સાથે ઓગળતો પ્રવાહ હોઈ શકે છે. જ્યારે બે પીગળે છે, ત્યારે તે સાંધાવાળી રેખાઓ ઉત્પન્ન કરે છે. બે મેલ્ટ ફ્રન્ટનું તાપમાન એટલું ઊંચું હોવું જોઈએ કે જેથી તેઓ સફળતાપૂર્વક એકસાથે ફ્યુઝ થઈ શકે અને ઉત્પાદનોની મજબૂતાઈ અને દેખાવને અસર ન કરે.
જ્યારે બે પીગળીને સંપૂર્ણપણે એકસાથે જોડાઈ શકતા નથી, ત્યારે ખામીઓ ઉત્પન્ન થશે.
ખામીના કારણો:
ઘાટમાં જાડા અને પાતળા ભાગો હોય છે, અને ઓગળવાની ગતિ અલગ હોય છે, જ્યારે પીગળવું ઘાટના પાતળા ભાગમાંથી વહે છે, ત્યારે તાપમાન ઓછું હોય છે.
દરેક દોડવીરની લંબાઈ અલગ-અલગ હોય છે. એકલા દોડવીરો ઠંડક મેળવવા માટે સરળ હશે.
પ્રેશર હોલ્ડિંગ સ્ટેજ દરમિયાન સંપૂર્ણપણે ઓગળવા દેવા માટે મોલ્ડ કેવિટી પ્રેશર પૂરતું નથી.
બાકીના પરપોટા મેલ્ટ ફ્રન્ટને ફ્યુઝ કરવામાં અસમર્થ બનાવે છે, જે બર્નિંગ તરફ દોરી જશે.
બર્નિંગ
બર્નિંગ ટૂંકા શોટ જેવું જ છે, પરંતુ અનિયમિત વિલીન થતી ધાર અને સહેજ સળગતી ગંધ સાથે. જ્યારે સ્થિતિ ગંભીર હોય ત્યારે ઉત્પાદન પર કાર્બન બ્લેક વિસ્તારો દેખાશે, તેની સાથે પ્લાસ્ટિક બળવાની ગંધ પણ આવશે.
જો ખામીઓ દૂર કરવામાં ન આવે તો, ઘાટ પર ઘણી વખત કાળો દેખાવ જોવા મળે છે. જો બળીને ઉત્પાદિત ગેસ અથવા તેલના પદાર્થોને તાત્કાલિક તપાસવામાં ન આવે, તો તે હવાના છિદ્રોને અવરોધિત કરી શકે છે. બર્નિંગ સામાન્ય રીતે માર્ગોના છેડે જોવા મળે છે.
કારણ:
બર્નિંગ આંતરિક કમ્બશન અસરને કારણે થાય છે. જ્યારે હવામાં દબાણ ખૂબ જ ટૂંકા સમયમાં તીવ્રપણે વધશે, ત્યારે તાપમાન વધશે અને બર્નિંગનું કારણ બનશે. એકત્રિત માહિતી અનુસાર, ઈન્જેક્શન મોલ્ડિંગ પ્રક્રિયામાં આંતરિક કમ્બશન અસર 600 ડિગ્રી સુધી ઉચ્ચ તાપમાન પેદા કરી શકે છે.
બર્નિંગ ઉત્પન્ન થઈ શકે છે જ્યારે:
મોલ્ડ ભરવાની ઝડપ ઝડપી છે જેથી મોલ્ડ કેવિટીમાંથી હવાને રદ કરી શકાતી નથી, અને આવનારા પ્લાસ્ટિકના બ્લોકને કારણે હવાના પરપોટા ઉત્પન્ન કરે છે અને સંકુચિત થયા પછી આંતરિક કમ્બશન અસર તરફ દોરી જાય છે.
હવાના છિદ્રો અવરોધિત છે અથવા વેન્ટિલેશન સરળ નથી.
મોલ્ડમાંની હવા હવાના છિદ્રોમાંથી રદ થવી જોઈએ. જો વેન્ટિલેશન સ્થિતિ, સંખ્યા, કદ અથવા કાર્યોથી પ્રભાવિત થાય છે, તો હવા ઘાટમાં રહેશે અને બર્નિંગ તરફ દોરી જશે. મોટા મોલ્ડ ક્લેમ્પિંગ ફોર્સ પણ નબળા વેન્ટિલેશન તરફ દોરી જશે.
સંકોચન
સંકોચન એ ઉત્પાદનોની સપાટી પરના સહેજ હોલોનો ઉલ્લેખ કરે છે.
જ્યારે ખામીઓ થોડી હોય છે, ત્યારે ઉત્પાદનોની સપાટી અસમાન હોય છે. જ્યારે તે ગંભીર છે, ત્યારે ઉત્પાદનોનો મોટો વિસ્તાર તૂટી જશે. કમાનો, હેન્ડલ્સ અને પ્રોટ્રુઝનવાળા ઉત્પાદનો ઘણીવાર સંકોચન ખામીથી પીડાય છે.
કારણ:
ઠંડક દરમિયાન કાચા માલના મોટા વિસ્તારના સંકોચનને કારણે સંકોચન થાય છે.
ઉત્પાદનોના જાડા વિસ્તારમાં (જેમ કે કમાન), સામગ્રીનું મુખ્ય સમશીતોષ્ણ નીચું હોય છે, તેથી સંકોચન સપાટી કરતાં પાછળથી થાય છે, જે કાચા માલની અંદર સંકોચન બળ ઉત્પન્ન કરશે અને બાહ્ય બાજુને અંદરની તરફ ખેંચે છે. સંકોચન ઉત્પન્ન કરવા માટે.
સંકોચન નીચેની પરિસ્થિતિઓમાં થાય છે:
ઘાટની પોલાણમાં દબાણ ઠંડકની પ્રક્રિયામાં કાચા માલના સંકોચનથી ઉત્પન્ન થતા બળ કરતાં ઓછું હોય છે.
ઠંડકની પ્રક્રિયા દરમિયાન ઘાટની પોલાણનો અપૂરતો દબાણ સમય, પરિણામે કાચો માલ ગેટમાંથી પોલાણમાંથી બહાર નીકળી જાય છે.
કાચા માલમાં મોલ્ડિંગ અને પ્રેશર હોલ્ડિંગ સ્ટેજ દરમિયાન પર્યાપ્ત બફરિંગ ક્ષમતા હોતી નથી કારણ કે વધુ પડતા કાચા માલને ઇન્જેક્ટ કરવામાં આવે તે પહેલાં સ્ક્રુ સંપૂર્ણપણે પાછી ખેંચી લેવામાં આવે છે.
ગેટ અને રનર્સના ક્રોસ સેક્શન વિસ્તારો ઉત્પાદનોની જાડાઈ કરતા ઘણા નાના છે, જેનો અર્થ છે કે ઉત્પાદનોની બહાર કાઢવાની પ્રક્રિયા પહેલા દરવાજાઓ પહેલેથી જ સ્થિર થઈ ગયા છે.
બબલ્સ
શૂન્યાવકાશ પરપોટા હવાના પરપોટાના સ્વરૂપમાં રજૂ કરવામાં આવે છે, જે પારદર્શક ઉત્પાદનો પર સરળતાથી મળી શકે છે. તે અપારદર્શક ઉત્પાદનોના ક્રોસ સેક્શન પર પણ જોઈ શકાય છે.
કારણ:
હવાના પરપોટા એ ઉત્પાદનોનો શૂન્યાવકાશ ભાગ છે, જે ઠંડકની પ્રક્રિયા દરમિયાન કાચો માલ સંકોચાય ત્યારે ઉત્પન્ન થાય છે.
સંકોચનની જેમ, કાચા માલની અંદરથી સંકોચન બળ ઉત્પન્ન થાય છે. તફાવત એ છે કે જ્યારે પરપોટા બને છે ત્યારે ઉત્પાદનોનો બાહ્ય દેખાવ મજબૂત બને છે, અને ત્યાં કોઈ પતન થતું નથી, તેથી હોલો પરપોટા ઉત્પન્ન થાય છે.
પરપોટાના કારણો ઘટાડાના કારણો જેવા જ છે, જેમાં નીચેનાનો સમાવેશ થાય છે:
બિનકાર્યક્ષમ મોલ્ડ પોલાણ દબાણ
અપર્યાપ્ત પોલાણ દબાણ સમય
રનર અને ગેટનું કદ ખૂબ નાનું છે
છંટકાવ ગુણ
સ્પ્રેઇંગ માર્કસ ગેટની સામેના થ્રેડેડ વિસ્તારનો સંદર્ભ આપે છે. છંટકાવના ગુણ માત્ર ઉત્પાદનોના દેખાવને જ અસર કરતા નથી, પરંતુ ઉત્પાદનોની મજબૂતાઈને પણ અસર કરે છે.
કારણ:
મોલ્ડ ભરવાની પ્રક્રિયા દરમિયાન મેલ્ટ ફ્લો નિયંત્રણ બહાર જવાને કારણે છંટકાવના ગુણ થાય છે.
મોટા દબાણ હેઠળ પીગળેલું પ્લાસ્ટિક મોલ્ડમાં પ્રવેશ કરે છે. જો મોલ્ડ ભરવાની ઝડપ ઘણી વધારે હોય, તો પ્લાસ્ટિક મોલ્ડ કેવિટીના ખુલ્લા અંતરમાંથી બહાર નીકળી જશે અને ઝડપથી પાછું ફરીને ઠંડુ થઈ જશે. તે સમયે, થ્રેડો રચાય છે, જે દરવાજામાં પ્રવેશતા પીગળેલા પ્લાસ્ટિકને અવરોધે છે.
છાંટવાના ગુણનું મુખ્ય કારણ દરવાજાઓની ખોટી સ્થિતિ અથવા દરવાજાની ડિઝાઇન છે. નીચેની બે પરિસ્થિતિઓ ખામીઓની સ્થિતિને વધુ ખરાબ કરશે:
ઉચ્ચ મોલ્ડ ભરવાની ઝડપ
ઘાટ ભરવા દરમિયાન નબળો ઓગળવાનો પ્રવાહ