ભારતમાં કેસ
ભારતીય કંપનીઓ માટે ડીજેમોલિડંગની ઇન્સર્ટ મોલ્ડ ઇન ઇન્જેક્શન મોલ્ડિંગ સર્વિસ
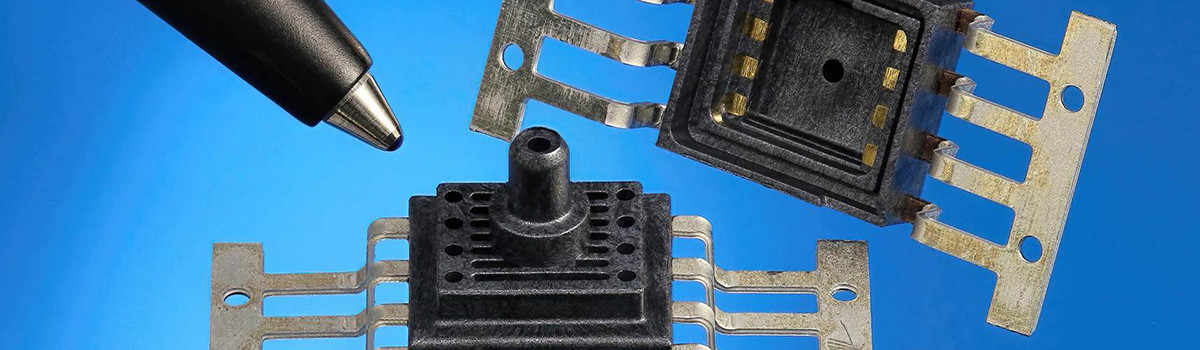
ઇન્સર્ટ મોલ્ડ એ સામાન્ય રીતે એક પ્રકારનો ઘાટ છે જે ઇન્જેક્શન મોલ્ડિંગ માટે પોલાણની અંદર નટ્સ, ધાતુના ભાગો અથવા સખત પ્લાસ્ટિકના ભાગો બનાવે છે.
ડીજેમોલ્ડિંગ ભારતના બજાર માટે ઇન્સર્ટ મલોડ ઇન્જેક્શન મોલ્ડિંગ સેવા પ્રદાન કરે છે, અને અમે વિવિધ ઉદ્યોગો માટે, ખાસ કરીને હોમ એપ્લાયન્સિસના ઉત્પાદકો માટે ઘણા બધા ઇન્સર્ટ મોલ્ડિંગના પ્લાસ્ટિક ભાગોનું ઉત્પાદન કરીએ છીએ. કેટલાક ભારતીય હોમ એપ્લાયન્સીસના ઉત્પાદકો ડીજે મોલ્ડિંગના સ્વરૂપમાં ઇન્સર્ટ મોલ્ડિંગના પ્લાસ્ટિકના ભાગોને લાંબા સમય સુધી ખરીદે છે. ભારતની આ કંપનીઓ સાથે અમારી ખૂબ સારી ભાગીદારી છે.
નટ્સ ઇન્જેક્શન મોલ્ડિંગ દાખલ કરો: બદામ સામગ્રી સ્ટેનલેસ સ્ટીલ, તાંબુ, કાંસ્ય અને સ્ટીલ હોઈ શકે છે, સામાન્ય રીતે કોપર બદામનો સામાન્ય રીતે ઉપયોગ થાય છે. કોપરને ઘૂંટવું સરળ છે, જે બદામ અને પ્લાસ્ટિકને સારી રીતે જોડવામાં મદદ કરે છે. અખરોટના આંતરિક બોરની સહિષ્ણુતા 0.02mm ની અંદર નિયંત્રિત હોવી જોઈએ, અન્યથા જો સહનશીલતા 0.02mmથી વધુ હોય તો સરળતાથી ફ્લેશ થઈ શકે છે. મોલ્ડ ફિટિંગમાં, પરીક્ષણ માટે ઇન્સર્ટ પિનમાં નટ્સ એસેમ્બલ કરવાની જરૂર છે. જો તે બદામ અને પિન વચ્ચે ચુસ્ત ફિટિંગ છે, તો તે ભાગને બહાર કાઢવો મુશ્કેલ હશે અને બહાર નીકળવાના ગુણ અથવા ચોંટવાની સમસ્યાઓનું કારણ બનશે. જો તે ઢીલું ફિટિંગ છે, તો તે ફ્લેશનું કારણ બનશે.
મેટલ ભાગો ઇન્જેક્શન મોલ્ડિંગ દાખલ કરો:
મેટલ ભાગો સ્ટેનલેસ સ્ટીલ, એલ્યુમિનિયમ, કોપર, સ્ટીલ ... વગેરે હોઈ શકે છે. ધાતુના ભાગોની સહિષ્ણુતા 0.02mm ની અંદર નિયંત્રિત હોવી જોઈએ, અન્યથા સામગ્રીને સીલ કરવી મુશ્કેલ છે અને ફ્લેશ રાખવું સરળ છે. ધાતુના ભાગોના વાવેતર વિસ્તારને ખૂબ મોટી ડિઝાઇન કરી શકાતી નથી.
જો ધાતુના ભાગો માટે ભરવાનું ક્ષેત્રફળ ખૂબ મોટું હોય, તો મેટલ ભાગો વચ્ચેના તાપમાનમાં મોટો તફાવત હોવાથી સંપૂર્ણ ઇન્જેક્શન પ્રાપ્ત કરવું ખૂબ જ મુશ્કેલ હશે. ધાતુના ભાગોની સ્થિતિ સામાન્ય રીતે પોલાણમાં ડિઝાઇન કરવામાં આવે છે કારણ કે પોલાણ ખસેડતું નથી, જે ધાતુના ભાગોને હલનચલનમાં ગુમાવવાથી ફ્લેશ પરિણામ ટાળવામાં મદદ કરે છે (ગંભીર કિસ્સામાં, ઘાટને નુકસાન પહોંચાડી શકે છે). ખાસ કિસ્સાઓમાં, ધાતુના ભાગોની સ્થિતિ ફક્ત ઉત્પાદનની મુખ્ય અથવા બાજુની સપાટી પર જ ડિઝાઇન કરી શકાય છે.
સખત પ્લાસ્ટિક ઇન્જેક્શન મોલ્ડિંગ દાખલ કરો:
સામાન્ય રીતે ઉચ્ચ ગલનબિંદુ સાથે સખત પ્લાસ્ટિક પસંદ કરો, જેમ કે PEEK, PA66+30GF, PP+30GF, PA12+30GF, PPS….વગેરે. આ સખત પ્લાસ્ટિક માટે સહનશીલતા ચોક્કસ હોવી જોઈએ. સીલિંગ એરિયામાં સંકોચન, ડેન્ટ અને વિરૂપતા જેવી ખામીઓ હોઈ શકતી નથી. મોલ્ડ ફિટિંગમાં, સખત પ્લાસ્ટિકને પરીક્ષણ માટે ઘાટની અંદર મૂકવું જોઈએ, અને વધુ સારી સીલિંગ પ્રાપ્ત કરવા માટે સીલિંગ વિસ્તારની આસપાસ 0.05-0.1mm પ્રી-પ્રેસિંગ છોડી દેવું જોઈએ.
પ્લાસ્ટિકના સખત ભાગને ખૂબ મોટા વાવેતર વિસ્તારની ડિઝાઇન ન કરવી જોઈએ, જે તાપમાનમાં તફાવતનું કારણ બને છે અને ઇન્જેક્શનમાં સામગ્રી ભરવાનું મુશ્કેલ બનાવે છે. સામાન્ય રીતે પોલાણની બાજુમાં સખત પ્લાસ્ટિકના ભાગને નિશ્ચિત કરો, કારણ કે પોલાણ ખસેડતું નથી, મોલ્ડ ખસેડવામાં ફ્લેશ અથવા નુકસાનકારક મોલ્ડને ટાળવા માટે. ખાસ કિસ્સાઓમાં, ધાતુના ભાગોની સ્થિતિ ફક્ત ઉત્પાદનની મુખ્ય અથવા બાજુની સપાટી પર જ ડિઝાઇન કરી શકાય છે.
મુખ્ય મુદ્દાઓ ડિઝાઇન કરો
1. નટ્સ ઇન્સર્ટવાળા ઉત્પાદનો માટે ડિઝાઇન સંકોચન, જ્યારે મેટલ ભાગો અને સખત પ્લાસ્ટિક ઇન્સર્ટવાળા ઉત્પાદનો માટે ડિઝાઇન સંકોચનની જરૂર નથી. એવા ક્ષેત્રો માટે કે જેને સખત સહિષ્ણુતાની જરૂર હોય, ઉત્પાદનોની કદ સહિષ્ણુતાને મધ્યમાં સંશોધિત કરો.
2.સામાન્ય રીતે મોલ્ડ ડિઝાઇનિંગમાં સ્ટાન્ડર્ડ પિન-પોઇન્ટ ગેટ સાથે મોલ્ડ બેઝ અપનાવો, અને સેકન્ડરી ઇન્જેક્શનમાં, શક્ય તેટલા પોલાણમાં દાખલ કરવાના ભાગો મૂકો. ઇન્સર્ટ્સને કેવિટીમાં ફિક્સ કરવાની શરતે, ઇન્જેક્શન મોલ્ડિંગ પછી કોરમાં ડાબી બાજુનો ભાગ કેવી રીતે બનાવવો તે ધ્યાનમાં લો, આ રીતે, ભાગને બહાર કાઢી શકાય છે. સામાન્ય રીતે પોલાણમાં સ્થિતિસ્થાપક બ્લોક્સ અને સ્થિતિસ્થાપક ગુંદર ઉમેરો જેથી ભાગ કોરમાં રહે. સ્થિતિસ્થાપક બ્લોક્સ અને ગુંદર વચ્ચેનું અંતર ખૂબ મોટું હોઈ શકતું નથી, અન્યથા સ્થિતિસ્થાપક બળ સખત પ્લાસ્ટિક અથવા મેટલ ભાગોના વિકૃતિનું કારણ બનશે. અંતર સામાન્ય રીતે 2mm ની અંદર ડિઝાઇન કરવામાં આવે છે, અને જ્યારે મેટલ અથવા સખત પ્લાસ્ટિક ઇન્સર્ટમાં પ્રમાણમાં મોટો વાવેતર વિસ્તાર હોય ત્યારે સ્થિતિસ્થાપક બ્લોક્સ અને સ્થિતિસ્થાપક ગુંદરના જથ્થામાં યોગ્ય રીતે વધારો કરે છે.
3. સામગ્રીની જાડાઈ 1.3-1.8mm ની અંદર શ્રેષ્ઠ છે (લગભગ 1.5mm શ્રેષ્ઠ છે), જો નહીં, તો ઉત્પાદન રેખાંકનો દ્વારા તપાસવાની જરૂર છે અને ગ્રાહકને તેમાં ફેરફાર કરવાનું સૂચન કરો. જો સામગ્રીની જાડાઈ 1.3mm કરતાં પાતળી હોય, તો તે સામગ્રી ભરવા માટે મુશ્કેલ છે, જ્યારે સામગ્રીની જાડાઈ 1.8mm કરતાં વધુ જાડાઈ હોય, તો ઉત્પાદનમાં સંકોચન થવું સરળ છે.
4. ઘાટમાં ગેટીંગ ખૂબ મહત્વનું છે. ગેટ પોઈન્ટ માટે સામગ્રી ભરવાનું સંતુલન સંપૂર્ણ રીતે ધ્યાનમાં લેવું જોઈએ. જ્યારે સામગ્રી જ્યાં ધાતુ અથવા સખત પ્લાસ્ટિકના ભાગો નિશ્ચિત છે તે વિસ્તારમાં દોડે છે, ત્યારે સામગ્રી ભરવાની ઝડપ અને દબાણ ઘટશે કારણ કે દાખલ પ્રતિકાર અને તાપમાનમાં તફાવત છે.
5.મોલ્ડ ઇજેક્ટર સિસ્ટમ માટે, બહાર નીકળવાનું સંતુલન ધ્યાનમાં લેવું આવશ્યક છે અથવા બહાર નીકળ્યા પછી વિરૂપતા થશે. ભાગોને સંતુલનમાં બહાર કાઢી ન શકાય તે માટે, સ્ટ્રક્ચર ડિઝાઇનમાં સંતુલનની સમસ્યાને સુધારવા માટે તૂટીને ધ્યાનમાં લેવાની જરૂર છે.
6. ઈન્જેક્શન મોલ્ડિંગમાં બહાર કાઢવામાં આવ્યા પછી ભાગોના દેખાવની લાયકાતની ખાતરી કરવા માટે, ઇજેક્ટર ઉપકરણ એબીએસ અથવા પીએમએમએ સાથે દાખલ કરાયેલ સખત પ્લાસ્ટિકનું ગઠ્ઠું હોવું જોઈએ. જો ઓવર મોલ્ડમાં સ્લાઇડ સીલિંગ હોય, તો શક્ય તેટલી પોલાણમાં સ્લાઇડ્સ ડિઝાઇન કરો, કારણ કે કેવિટીમાંની સ્લાઇડ્સ મોલ્ડ ફિટિંગને સરળ બનાવે છે.
7. SA (સીમ ભથ્થું) સીલ કરવાની મજબૂતાઈની ખાતરી કરવા માટે, બે વાર ઈન્જેક્શન મોલ્ડિંગમાંથી બનાવેલ ઉત્પાદન માટે, સીલિંગ SA ની પહોળાઈ ઓછામાં ઓછી 0.8mm હોવી જોઈએ. સેકન્ડરી ઈન્જેક્શન સામગ્રી માટે સખત પ્લાસ્ટિક છે, સીલિંગ SA ની પહોળાઈ ઓછામાં ઓછી 1.0mm હોવી જોઈએ, અન્યથા, ગ્રાહકને ઉત્પાદનમાં ફેરફાર કરવાનું સૂચન કરવાની જરૂર છે.
8.મોલ્ડ ડિઝાઇનમાં, આપણે ઇન્જેક્શન મોલ્ડિંગ મશીનોને ઉત્પાદન માટે ધ્યાનમાં લેવું જોઈએ કે તે કયા પ્રકારનું મશીન અપનાવે છે, ઊભી અથવા આડી. તે સૂચવવામાં આવે છે કે ઘણી બધી પોલાણની રચના ન કરો, ખાસ કરીને ઠંડા દોડવીરો સાથેના ઘાટ માટે કારણ કે ઘણી બધી પોલાણ દોડનારને લાંબો બનાવે છે, સામગ્રીનો બગાડ કરે છે અને ઉચ્ચ કાર્યક્ષમતા ઇન્જેક્શન પ્રાપ્ત કરવા માટે હાનિકારક પણ છે. ઈન્જેક્શન મોલ્ડિંગ મશીનને મેચ કરવા માટે, અમારે ઉત્પાદનની ગોઠવણી માટે તે કોમ્પેક્ટ અને વાજબી છે કે કેમ તે ધ્યાનમાં લેવું જોઈએ. દરેક વખતે જ્યારે ઉત્પાદનો મોલ્ડમાં મૂકવામાં આવે ત્યારે તે જ સ્થિતિમાં હોય તેની ખાતરી કરવા માટે ઉત્પાદનોને નિશ્ચિત કરી શકાય છે. બીજી રીત એ છે કે જો મોલ્ડ બંધ થતાં પહેલાં ભાગ યોગ્ય જગ્યાએ ન હોય તો ચેતવણી આપવા માટે ડિઝાઇન પ્રતિક્રિયા સિસ્ટમ છે, જે ઘાટ બંધ થવામાં મદદ કરે છે. આ રીતે, ભાગો મોલ્ડમાં સમાન સ્થિતિમાં છે, જે ઈન્જેક્શન મોલ્ડિંગમાં યોગ્ય દર અને ઉત્પાદન કાર્યક્ષમતા વધારે છે.
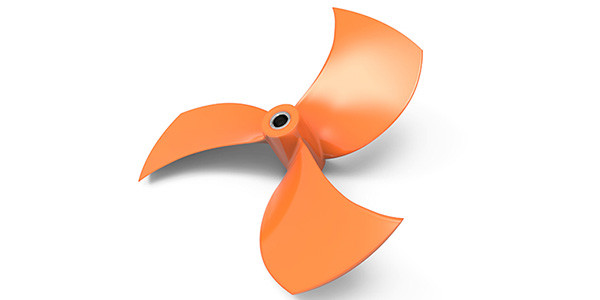
9.એક સ્ટીલ સપોર્ટ ડિઝાઇન કરવો આવશ્યક છે કારણ કે મોલ્ડ ઇન્જેક્શન એરિયા ઇન્જેક્શનમાં ખૂબ દબાણ ધરાવે છે (આકાર અને કદમાં ભાગ કરતાં 5-10 મીમી મોટો હોવો જોઈએ). ઓવર-મોલ્ડિંગ વિસ્તારની આસપાસના ભાગો વચ્ચે ગેપ છોડવો જોઈએ નહીં, અન્યથા સેકન્ડરી ઈન્જેક્શન પછી ભાગનો આકાર બહાર આવશે. SA (સીમ ભથ્થું) વિનાના ભાગો માટે આ પાસાને વધુ ધ્યાન આપવાની જરૂર પડશે.
10.એર ટ્રિપ સરળતાથી છે ઈન્જેક્શન મોલ્ડિંગમાં એર ટ્રિપ સરળતાથી થાય છે, તેથી મોલ્ડ ડિઝાઇનિંગમાં વેન્ટિંગને સંપૂર્ણપણે ધ્યાનમાં લેવું જોઈએ. લાંબા-અંતરની પાણીની લાઇન માટે તમામ અંધ ખૂણાઓ અને સ્થાનોમાં, સખત પ્લાસ્ટિકના ભાગ પર વેન્ટિંગ છિદ્રો ડિઝાઇન કરવી આવશ્યક છે કારણ કે અંધ ખૂણામાં સામગ્રી ભરવાનું વધુ મુશ્કેલ છે.
11. ઇન્જેક્ટેડ મટિરિયલ અને ક્વોલિફાઇડ થ્રસ્ટ સંપૂર્ણ રીતે ભરેલા છે તેની ખાતરી કરવા માટે, એક રીત એ છે કે ભાગના ખૂણા પર અંડરકટ્સ ડિઝાઇન કરો જેથી એડહેસિવ પરિણામ વધે અને પછી ભાગો વધુ ચુસ્તપણે વળગી રહે.
12. સીલિંગ એરિયા અને પાર્ટિંગ લાઇન એરિયામાં, આપણે કેવિટી અને કોરમાંથી ડિમોલ્ડ ન કરવું જોઈએ, કારણ કે મોલ્ડમાં ક્લેમ્પિંગ લાઇન્સ અને ડ્રાફ્ટ ડિમોલ્ડિંગથી મોલ્ડ ફિટિંગમાં ફ્લેશ થશે. LISS-OFF દ્વારા ડિમોલ્ડ કરવાનો પ્રયાસ કરો.
દાખલ મોલ્ડના ગેટ પોઈન્ટ પ્રકારો
ઇન્સર્ટ મોલ્ડ માટેના ગેટ પોઇન્ટને હોટ સ્પ્રુ વાલ્વ ગેટ, હોટ સ્પ્રુ પિન ગેટ, પિન-પોઇન્ટ ગેટ, સબ ગેટ, એજ ગેટ... વગેરેને ડાયરેક્ટ કરવા માટે ડિઝાઇન કરી શકાય છે.
હોટ સ્પ્રુ વાલ્વ ગેટ: સારી તરલતા, સ્થિતિ પસંદ કરતી લવચીક, નાનો ગેટ પોઇન્ટ. મોટા ઉત્પાદન માટે અને જાડા દિવાલની જાડાઈવાળા ઉત્પાદનો માટે સુટ્સ. સામગ્રીને બચાવવામાં મદદ કરી શકે છે, ગેટ માટે કોઈ સામગ્રીનો કચરો નહીં, ટૂંકા લીડ સમય અને ઉચ્ચ ગુણવત્તા. એકમાત્ર ખામી એ સહેજ ગેટીંગ ટ્રેસ છે.
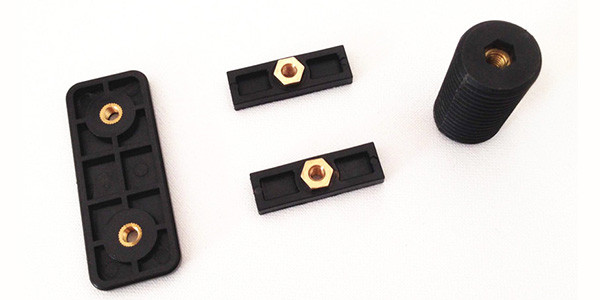
હોટ સ્પ્રુ પિન ગેટ: સારી તરલતા, સ્થિતિ પસંદ કરતી લવચીક, નાનો ગેટ પોઇન્ટ. મોટા ઉત્પાદન માટે અને જાડા દિવાલની જાડાઈવાળા ઉત્પાદનો માટે સુટ્સ. સામગ્રીને બચાવવામાં મદદ કરી શકે છે, ગેટ માટે કોઈ સામગ્રીનો કચરો નહીં, ટૂંકા લીડ સમય અને ઉચ્ચ ગુણવત્તા. પરંતુ ત્યાં ખામીઓ છે, જેમ કે ગેટ પોઈન્ટની આસપાસ 0.1mm સામગ્રી બાકી છે, અને ગડબડ કરવી સરળ છે. ગેટ પોઈન્ટની આસપાસ ડાબી સામગ્રીને આવરી લેવા માટે ગ્રુવ્સ બનાવવાની જરૂર છે.
પિન-પોઇન્ટ ગેટ: લવચીક, નબળી તરલતા, લાંબી દોડવીરનું અંતર, નાનો ગેટ પોઇન્ટ પસંદ કરતી સ્થિતિ. નાના બેચ ઉત્પાદન માટે પોશાકો. ગેટ પોઈન્ટની આસપાસ વધુ કચરો. ઉત્પાદનમાં ગેટ પોઈન્ટને ક્લેમ્પ કરવા માટે યાંત્રિક હથિયારોની જરૂર છે. લાંબા લીડ સમય. ખામી 0.1-0.2 મીમી સામગ્રી છે જે ગેટ પોઇન્ટની આસપાસ બાકી છે, ગેટ પોઇન્ટની આસપાસ ડાબી સામગ્રીને આવરી લેવા માટે ખાંચો બનાવવાની જરૂર છે.
સબ ગેટ: પોલાણ, કોર, બાજુની દિવાલો અને ઇજેક્ટર પિનમાં પાંસળી પર ડિઝાઇન કરી શકાય છે. ગેટ પોઈન્ટ લવચીક રીતે પસંદ કરી શકે છે, રેડતા ગેટ આપોઆપ ભાગથી અલગ થાય છે, સહેજ ગેટીંગ ટ્રેસ. ખામીઓ: ગેટ પોઈન્ટની આસપાસની સામગ્રીને બહાર કાઢવામાં સરળ, ગેટીંગની સ્થિતિમાં સૂકાઈ જવાના ચિહ્નો સર્જવામાં સરળ, હાથ વડે સામગ્રીને લૂછી નાખવાની જરૂર છે, પોલાણમાંથી ગેટ પોઈન્ટથી દબાવવામાં ઘણું નુકશાન.
એજ ગેટ: પીગળેલું પ્લાસ્ટિક દરવાજામાંથી વહે છે, બાજુની સમાનરૂપે સોંપવામાં આવે છે, તાણ ઘટાડે છે; પોલાણમાં હવા પ્રવેશવાની સંભાવનાને ઘટાડે છે, છટાઓ અને પરપોટા થવાનું ટાળો. ખામીઓ: રેડવાની ગેટ આપમેળે ભાગથી અલગ થઈ શકતો નથી, ભાગની કિનારીઓ પર ડાબા સ્પ્રુ ચિહ્નો, ગેટ ફ્લેટ રેડવાની પ્રક્રિયા કરવા માટે સાધનોની જરૂર છે. એજ ગેટ પ્રમાણસર ઇન્જેક્શન અને પ્રેશર હોલ્ડિંગમાં મદદ કરી શકે છે, અને પ્રેશર હોલ્ડિંગ અને ફીડિંગ માટે પણ સારું છે, આ રીતે, તે એરલાઇન્સ, ફ્લો માર્કસ...વગેરે સુધારવા માટે વધુ સારું છે.
ઇન્સર્ટ મોલ્ડ માટે પ્રોસેસિંગ અને ફિટિંગ
1.પ્રક્રિયા કરતા પહેલા, મોલ્ડની પ્રોસેસીંગ ટેકનોલોજી પર કામ કરો. ઉચ્ચ-ચોકસાઇવાળા પ્રોસેસિંગ મશીનો, હાઇ-સ્પીડ મશીન, સ્લો-ફીડિંગ એનસી વાયર કટ મશીન, મિરર EDM (ઇલેક્ટ્રિક ડિસ્ચાર્જ મશીનિંગ) મશીન વગેરે પસંદ કરો.
2. ડિઝાઈન 0.05-0.1mm પ્રી-પ્રેસિંગના સ્થાનમાં બાકી છે.
3. મોલ્ડ બેઝ પ્રોસેસિંગમાં ચોકસાઇની આવશ્યકતાઓની નોંધ કરો, મોલ્ડ બેઝ મેળવ્યા પછી સહિષ્ણુતાનું નિરીક્ષણ કરો અને જો સહનશીલતા અયોગ્ય હોય તો તેનો ઉપયોગ કરશો નહીં.
4.મોલ્ડ ફિટિંગ માટે મોલ્ડની અંદર બદામ, ધાતુના ભાગો અને સખત પ્લાસ્ટિકના ભાગો મૂકો. જો મોલ્ડ ફિટિંગમાં સમસ્યા જણાય, તો બદામ, ધાતુના ભાગો, સખત પ્લાસ્ટિકના ભાગો અને મોલ્ડ દ્વારા તપાસો કે કયો ખોટો છે. શક્ય હોય ત્યાં સુધી ડ્રોઇંગ અનુસાર ભાગની પ્રક્રિયા કરો, જે ભવિષ્યમાં ડેટાને ટ્રેસ કરવામાં મદદ કરે છે.
5.મોલ્ડ ફિટિંગ માટે ગ્રાઇન્ડરનો ઉપયોગ કરી શકાતો નથી. જ્યાં મોલ્ડ ફિટિંગ સારું ન હોય ત્યાં સુધારવા માટે મશીનો તરફ વળો.
6.અજમાયશ પહેલાં એક્શન ટેસ્ટિંગ કરો, મિસ એસેમ્બલિંગ અને ભૂલથી એસેમ્બલિંગ ટાળો. ભૂલથી એસેમ્બલ કરવાથી મોલ્ડ બેઝને નુકસાન થશે.
દાખલ મોલ્ડ માટે મોલ્ડ પરીક્ષણ
1.મોલ્ડ પરીક્ષણમાં, વ્યક્તિએ ઘાટને ખોલવા, બંધ કરવા અને બહાર કાઢવાના ક્રમ વિશે સ્પષ્ટપણે જાણવાની જરૂર છે. ધાતુના ભાગો અને સખત પ્લાસ્ટિકના ભાગોના માળખાકીય લક્ષણો અને ગુણધર્મોને સમજો.
2. ગ્રાહકને જરૂરી નમૂનાના જથ્થા વિશે સ્પષ્ટપણે જાણો, પૂરતા પ્રમાણમાં બદામ, ધાતુના ભાગો અને સખત પ્લાસ્ટિક તૈયાર કરો, કારણ કે તેને મોલ્ડ પરીક્ષણમાં ઘણા નમૂનાઓની જરૂર છે.
3. નોંધ કરો કે શું બદામ, ધાતુના ભાગો અથવા સખત પ્લાસ્ટિકના દાખલ વિના મોલ્ડનું પરીક્ષણ કરી શકાય છે. જો નટ્સ દાખલ કરો, ધાતુના ભાગો અને સખત પ્લાસ્ટિકને ઘાટમાં એસેમ્બલ કરવામાં ન આવે, તો ભાગમાં ખામીઓ હોઈ શકે છે જેમ કે ઘાટમાં ચોંટી જવું અથવા શોર્ટ શોટ.
4.ઘણા કિસ્સાઓમાં, મોલ્ડ પર વોટરલાઇન પ્લેટને સમાયોજિત કરવાની જરૂર છે, પરંતુ કેટલીકવાર તે તેમના બંધારણના આધારે કેટલાક ઇન્સર્ટ મોલ્ડમાં પાણીની લાઇન પ્લેટને સમાયોજિત કરી શકતી નથી, અથવા તેનાથી પણ ખરાબ, ઘાટ ભારે અટવાઇ જાય છે અને તેને સુધારવાની જરૂર છે, અથવા મોલ્ડને નુકસાન થાય છે. ઉદઘાટન
5.મોલ્ડ ટેસ્ટિંગમાં સમસ્યાઓ આવી શકે છે, જેમ કે શોર્ટ શોટ, એર ટ્રિપ્સ, ફ્લૅશ અથવા મોલ્ડને વળગી રહેવું. જો ઈન્જેક્શન મોલ્ડિંગ મશીન પર સમસ્યાઓ ચકાસી શકાય છે, તો તેને હલ કરવી વધુ સારું છે.
ડીજેમોલ્ડિંગ પાસે 10+ વર્ષથી વધુનો ઇન્સર્ટ મોલ્ડિંગ અનુભવ છે, જો તમને કોઈ પ્રશ્ન હોય, તો કૃપા કરીને અમારો સંપર્ક કરો.