הזרקה תרמופלסטית
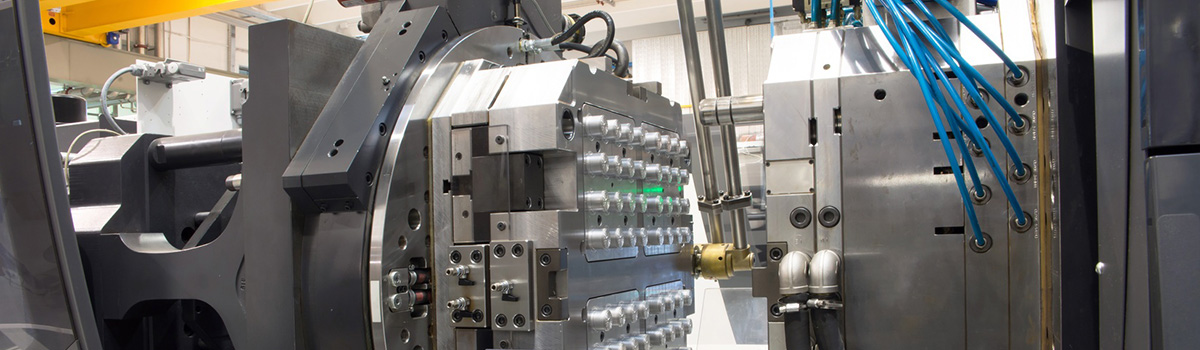
הזרקה תרמופלסטית היא תהליך ייצור פופולרי המשמש ליצירת חלקי פלסטיק שונים עבור תעשיות מרובות. תהליך זה כולל המסת כדורי פלסטיק והזרקתם לתבנית כדי לייצר צורה תלת מימדית. הזרקה תרמופלסטית היא יעילה וחסכונית ביותר לייצור כמויות גדולות של חלקי פלסטיק איכותיים עם סובלנות הדוקה. מדריך מקיף זה יבחן את ההיבטים השונים של הזרקה תרמופלסטית, לרבות יתרונותיה וחסרונותיה, סוגי התרמופלסטיים בהם נעשה שימוש, תהליך ההזרקה, שיקולי תכנון ועוד ועוד.
היסטוריה של הזרקה תרמופלסטית
ההיסטוריה של הזרקה תרמופלסטית משתרעת על פני מאה שנים של התקדמות טכנולוגית, פיתוחי חומרים ויישומים תעשייתיים. מההתחלה הצנועה שלה כתהליך יציקת צלולואיד ועד לטכנולוגיה המתוחכמת של ימינו, הזרקה ממשיכה להיות טכניקת ייצור חיונית, המניעה חדשנות ומעצבת תעשיות שונות.
- התפתחויות מוקדמות:ג'ון ווסלי הייאט ואחיו ישעיהו פיתחו את מכונת ההזרקה המעשית הראשונה, שהתחקה אחר מקורות ההזרקה התרמופלסטית לסוף המאה ה-19. בשנת 1872, הם רשמו פטנט על מכשיר שהשתמש בבוכנה כדי להחדיר צלולואיד לתוך חלל עובש, ויצר חפצים מוצקים. פריצת דרך זו הניחה את הבסיס לתהליך ההזרקה המודרני.
- התקדמות בחומרים:בתחילת המאה ה-20, הצגת פולימרים סינתטיים חדשים פתחה אפשרויות חדשות להזרקה. בקליט, שרף פנולי, הפך לחומר פופולרי ליציקה בשל תכונות הבידוד החשמלי המצוינות שלו. לאורך שנות ה-1930 וה-1940, התקדמות בכימיה של פולימרים הובילה לפיתוח של תרמופלסטיים אחרים, כגון פוליסטירן ופוליאתילן, שהרחיבו עוד יותר את מגוון החומרים המתאימים להזרקה.
- אימוץ תעשייתי: האימוץ הנרחב של הזרקה תרמופלסטית החל בשנות ה-1950, כאשר היצרנים הכירו בעלות-תועלת וברבגוניות שלו. הצגת מכונות בלחץ גבוה אפשרה זמני מחזור מהירים יותר והגדלת נפחי הייצור. כתוצאה מכך, נוצר מבחר מגוון של מוצרים לשימוש אישי ותעשייתי כאחד. אלה כללו רכיבי רכב, מכשירי חשמל לבית וכלי משחק.
- חידושים טכנולוגיים:במהלך עשרות השנים, טכנולוגיית הזרקה המשיכה להתפתח. בשנות ה-1960 של המאה ה-1980 הופיעו מכונות מבוקרות מחשב, המאפשרות שליטה מדויקת על תהליך היציקה. כניסתן של מערכות רצים חמות בשנות ה-3 הפחיתה את הפסולת ושיפרה את היעילות על ידי ביטול הצורך בראנרים ובזבים. בשנים האחרונות, התקדמות האוטומציה, הרובוטיקה וההדפסה התלת-ממדית חוללו מהפכה נוספת בתעשיית ההזרקה, ואיפשרו עיצובים מורכבים וצמצום זמן הייצור.
- קיימות ומיחזור:עם חששות סביבתיים גוברים, תעשיית ההזרקה אימצה אמצעי קיימות. היצרנים פיתחו תרמופלסטיות מבוססות ביו וממוחזרות, והפחיתו את ההסתמכות על חומרים מבוססי דלק מאובנים. בנוסף, טכנולוגיות מיחזור משופרות אפשרו עיבוד מחדש של פסולת פוסט-צרכנית ופוסט-תעשייתית, תוך מזעור ההשפעה הסביבתית של הזרקה תרמופלסטית.
- סיכויי עתיד:העתיד של הזרקה תרמופלסטית נראה מבטיח. התעשייה בוחנת חידושים כמו הזרקת מיקרו לרכיבים מיניאטוריים, טכניקות ריבוי חומרים ויציבות יתר לחלקים מורכבים, ושילוב טכנולוגיות חכמות לניטור ואופטימיזציה של תהליכים. יתר על כן, החוקרים מצפים שהתקדמות בחומרים מתכלים וייצור תוספים יחוללו מהפכה בתחום, ויהפכו את הזרקה לבר-קיימא ורב-תכליתי עוד יותר.
היתרונות של הזרקה תרמופלסטית
הזרקה תרמופלסטית מציעה יתרונות רבים ליצרנים. הוא מספק גמישות עיצובית, המאפשר עיצובים מורכבים ומורכבים עם תכונות שונות. התהליך חסכוני, מפחית בזבוז חומרים ומוזיל עלויות יחידה. הזרקה תרמופלסטית תומכת במספר חומרים, ומספקת צדדיות עבור יישומים שונים.
- גמישות עיצובית:הזרקה תרמופלסטית מאפשרת עיצובים מורכבים ומורכבים עם מאפיינים כמו חתכים, קירות דקים ועוביים משתנים, המספקים למעצבים חופש עצום.
- יעילות מחיר: התהליך יעיל ביותר, מפחית בזבוז חומרים ומוזיל עלויות יחידה. יציקה בו-זמנית של מספר חלקים ומחזורי ייצור מהירים תורמים לחיסכון בעלויות.
- צדדיות חומרים: הזרקה תרמופלסטית תומכת במגוון רחב של חומרים, מה שמאפשר ליצרנים לבחור את האפשרות המתאימה ביותר לכל יישום, לרבות חומרים קשיחים או גמישים, שקופים או אטומים וחומרים עמידים כימית.
- חוזק ועמידות:תרמופלסטיים בהזרקה יכולים להפגין תכונות מכניות מצוינות, כגון חוזק גבוה, קשיחות ועמידות בפני פגיעות. אפשרויות חיזוק, כמו סיבי זכוכית או פחמן, משפרות עוד יותר את התכונות הללו.
- עקביות ואיכות:הזרקה מבטיחה איכות עקבית של חלק לחלק ודיוק ממדים, ומספקת סובלנות הדוקה ומוצרים אמינים. התהליך מספק גם גימור משטח חלק ואחיד, ומבטל את הצורך בפעולות גימור נוספות.
- מדרגיות וייצור המוני:הזרקה ניתנת להרחבה מנפחים נמוכים לגבוהים, מה שהופך אותו מתאים לייצור המוני. ברגע שהיצרנים יוצרים את התבנית, הם יכולים לייצר כמויות גדולות של חלקים זהים עם שינויים מינימליים.
- אינטגרציה והרכבה:חלקים יצוקים בהזרקה יכולים לשלב מספר רכיבים למקשה אחת, מה שמפחית את הצורך בתהליכי הרכבה נוספים. אינטגרציה זו משפרת את ביצועי המוצר, מפחיתה את זמן ההרכבה ומפחיתה עלויות.
- קיימות:תעשיית ההזרקה מראה התמקדות גוברת בקיימות. הזמינות של חומרים מבוססי ביו וממוחזרים מאפשרת לייצר מוצרים ידידותיים לסביבה. השימוש היעיל בחומרים וניתנות המיחזור של תרמופלסטיים תורמים לתהליך ייצור ירוק יותר.
יתרונות אלו הפכו אותה לשיטת ייצור מאומצת במגוון תעשיות, המספקות פתרונות איכותיים, חסכוניים וידידותיים לסביבה לדרישות מוצר מורכבות.
חסרונות של הזרקה תרמופלסטית
בעוד שהזרקה תרמופלסטית מציעה יתרונות רבים, ישנם גם מספר חסרונות. היצרנים צריכים להעריך בזהירות את הגורמים הללו ולשקול אותם מול היתרונות כדי לקבוע את ההתאמה של הזרקה תרמופלסטית ליישומים הספציפיים שלהם.
- השקעה ראשונית גבוהה: הקמת פעולת הזרקה תרמופלסטית דורשת השקעה ראשונית משמעותית בתכנון וייצור תבניות ורכישת מכונות מיוחדות. העלויות הכרוכות ביצירת תבניות וכלי עבודה יכולות להיות משמעותיות, במיוחד עבור עיצובים מורכבים ומורכבים.
- מגבלות עיצוב: בעוד שהזרקה תרמופלסטית מציעה גמישות עיצובית, קיימות מגבלות מסוימות. לדוגמה, השגת עובי דופן אחיד בכל החלק עלולה להיות מאתגרת, ולהוביל לשונות בחלוקת החומרים ולחולשות מבניות אפשריות. בנוסף, נוכחות של חתכים או גיאומטריות מורכבות עשויה לדרוש שימוש בתכונות עובש נוספות או פעולות משניות, מה שמגדיל את העלויות וזמן הייצור.
- זמני עופרת ארוכים:תהליך העיצוב והייצור של תבניות להזרקה יכול להיות גוזל זמן, מה שמוביל לזמני אספקה ארוכים יותר לפיתוח המוצר. תהליך איטרציית העיצוב, ייצור התבניות והבדיקה יכולים להוסיף זמן משמעותי לציר הזמן הכולל של הייצור, שאולי לא יתאים לפרויקטים עם מועדים צפופים.
- אילוצי בחירת חומרים:למרות שהזרקה תרמופלסטית תומכת במגוון רחב של חומרים, ישנן מגבלות ומגבלות מסוימות. לחומרים מסוימים עשויים להיות דרישות עיבוד ספציפיות או זמינות מוגבלת, מה שמשפיע על בחירת העיצוב ובחירת החומרים עבור יישום מסוים.
- מגבלות גודל חלק:למכונות הזרקה יש מגבלות גודל, הן מבחינת הגודל הפיזי של המכשיר והן מבחינת גודל התבניות שהן יכולות להכיל. ייצור חלקים ענקיים עשוי לדרוש ציוד מיוחד או שיטות ייצור חלופיות.
- השפעה על הסביבה:בעוד התעשייה פועלת למען קיימות, תהליך ההזרקה התרמופלסטית עדיין מייצר חומרי פסולת, כולל גרוטאות וזרמים. סילוק ומחזור נכון של חומרים אלה נחוצים כדי למזער את ההשפעה הסביבתית.
- המורכבות של אופטימיזציה של תהליך:השגת פרמטרי תהליך אופטימליים עבור הזרקה תרמופלסטית יכולה להיות מורכבת וגוזלת זמן. היצרנים חייבים לשלוט בקפידה ולבצע אופטימיזציה של טמפרטורה, לחץ, קצבי קירור וזמני מחזור כדי להבטיח איכות חלקית עקבית ולמזער פגמים.
סוגי תרמופלסטיים המשמשים בהזרקה
אלו הן רק כמה דוגמאות לתרמופלסטיות הנפוצות בשימוש בהזרקה. לכל חומר תכונות ייחודיות, מה שהופך אותו למתאים ליישומים ספציפיים המבוססים על חוזק, גמישות, עמידות כימית, שקיפות ועלות. היצרנים צריכים לשקול את המאפיינים והדרישות הללו בבחירת התרמופלסטי המתאים לפרויקטי ההזרקה שלהם.
- פוליפרופילן (PP):פוליפרופילן הוא תרמופלסטי רב תכליתי בשימוש נפוץ בהזרקה. הוא מציע עמידות כימית מעולה, צפיפות נמוכה וחוזק השפעה טוב. ל-PP (פוליפרופילן) יש יישומים רחבי טווח באריזות, רכיבי רכב, מכשירי חשמל ביתיים ומכשור רפואי.
- פוליאתילן (PE):פוליאתילן הוא תרמופלסטי נוסף בשימוש נרחב בהזרקה. הוא זמין בצורות שונות, כגון פוליאתילן בצפיפות גבוהה (HDPE) ופוליאתילן בצפיפות נמוכה (LDPE). PE מציע עמידות כימית טובה, קשיחות וגמישות, מה שהופך אותו מתאים לבקבוקים, מיכלים וצינורות.
- פוליסטירן (PS):פוליסטירן הוא תרמופלסטי רב תכליתי הידוע בבהירות, קשיחות ובמחיר סביר שלו. הוא מוצא שימוש נפוץ באריזות, מוצרי צריכה ומוצרים חד פעמיים. PS (פוליסטירן) מאפשר עיבוד מהיר ומספק יציבות מימדית טובה, אך הוא יכול להיות שביר ורגיש לפיצוח מתח סביבתי.
- אקרילוניטריל בוטאדיאן סטירן (ABS): ABS הוא תרמופלסטי פופולרי הידוע בעמידות הפגיעה והעמידות המצוינים שלו. הוא משלב את המאפיינים של אקרילוניטריל, בוטאדיאן וסטירן כדי ליצור חומר רב תכליתי המתאים לחלקי רכב, תאים אלקטרוניים וצעצועים.
- פוליוויניל כלוריד (PVC): PVC הוא תרמופלסטי בשימוש נרחב הידוע בעמידות הכימית המעולה שלו, עמידותו ועלותו הנמוכה. זה יכול להיות קשיח או גמיש בהתאם לניסוח והתוספים המשמשים. PVC (פוליויניל כלוריד) מוצא שימוש נפוץ בבנייה, בידוד חשמלי, מוצרי בריאות ואריזות.
- פוליקרבונט (PC): פוליקרבונט הוא תרמופלסטי שקוף עם השפעה יוצאת דופן ועמידות בחום גבוהה. הוא מוצא שימוש נפוץ ביישומים הדורשים בהירות אופטית, כגון רכיבי רכב, קסדות בטיחות ותצוגות אלקטרוניות.
- ניילון (פוליאמיד):ניילון הוא תרמופלסטי חזק ועמיד הידוע בתכונות המכניות המצוינות שלו ובעמידותו הכימית. הוא מוצא שימוש נפוץ ביישומים הדורשים חוזק גבוה, כגון חלקי רכב, רכיבים תעשייתיים ומוצרי צריכה.
- פוליאתילן טרפתלאט (PET):PET הוא תרמופלסטי פופולרי לייצור בקבוקים, מיכלים וחומרי אריזה. הוא מציע בהירות טובה, עמידות כימית ותכונות מחסום, מה שהופך אותו מתאים ליישומי מזון ומשקאות.
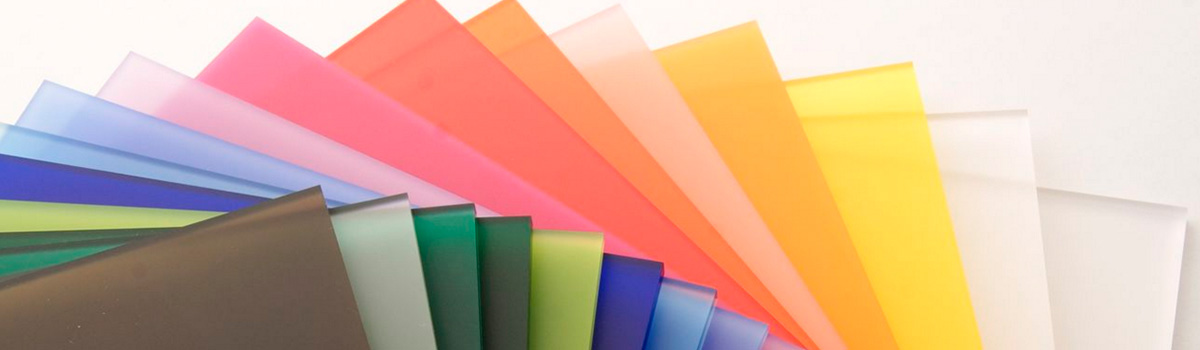
מאפיינים של תרמופלסטיים המשמשים בהזרקה
תכונות אלו של תרמופלסטיות ממלאות תפקיד מכריע בקביעת התאמתם ליישומי הזרקה ספציפיים. על היצרנים לשקול היטב את המאפיינים הללו ולבחור את התרמופלסטי המתאים בהתבסס על הביצועים הרצויים, תנאי הסביבה ודרישות העלות.
- תכונות מכאניות:תרמופלסטיים המשמשים בהזרקה יכולים להפגין תכונות מכניות שונות, כולל חוזק מתיחה, עמידות בפני פגיעות וחוזק כיפוף. תכונות אלו קובעות את יכולת החומר לעמוד בכוחות המופעלים ואת העמידות הכוללת שלו ביישומים שונים.
- עמידות כימית:תרמופלסטיים רבים המשמשים בהזרקה הם בעלי עמידות יוצאת דופן בפני כימיקלים, ממיסים ושמנים. תכונה זו חיונית עבור יישומים הכוללים חשיפה לסביבות קשות או לחומרים מאכלים.
- יציבות תרמית:היציבות התרמית של תרמופלסטיים מתייחסת ליכולתם לעמוד בטמפרטורות גבוהות ללא השפלה משמעותית. חלק מהתרמופלסטיים מציגים עמידות בחום מעולה, המאפשרת להם לשמור על תכונותיהם המכניות גם בטמפרטורות גבוהות.
- תכונות חשמליות:תרמופלסטיים המשמשים בהזרקה יכולים להיות בעלי תכונות חשמליות ספציפיות, כולל בידוד חשמלי, מוליכות או חוזק דיאלקטרי. מאפיינים אלה חיוניים ליישומים בתעשיות חשמל ואלקטרוניקה, שבהן החומרים חייבים לספק ביצועים חשמליים אמינים.
- שקיפות ובהירות:תרמופלסטיים מסוימים, כגון פוליקרבונט ו-PET, מציעים שקיפות ובהירות מעולים, מה שהופך אותם למתאימים ליישומים הדורשים תכונות אופטיות. יצרנים משתמשים בחומרים אלו בדרך כלל במוצרים כגון חלונות שקופים, עדשות ותצוגות.
- גמישות וקשיחות: גמישות וקשיחות הן תכונות חיוניות של תרמופלסטיות המשמשות ביישומים הדורשים עמידות בפני פגיעות ועמידות. חלק מהתרמופלסטיים, כגון ABS וניילון, מציעים קשיחות מעולה, המאפשרים להם לעמוד בפני פגיעות חוזרות ונשנות מבלי להישבר.
- יציבות מימדית:יציבות ממדית מתייחסת ליכולת של תרמופלסטי לשמור על צורתו וגודלו בתנאים משתנים, כולל שינויי טמפרטורה. חומרים בעלי יציבות מימדית טובה מבטיחים ממדי חלקים עקביים, וממזערים את הסיכון לעיוות או עיוות.
- תאימות כימית:התאימות הכימית של תרמופלסטיים מתייחסת ליכולתם להתנגד לפירוק או אינטראקציה עם כימיקלים שונים, כולל חומצות, בסיסים וממיסים. כדי להבטיח ביצועים אופטימליים, בחירת תרמופלסטי שיכול לעמוד בסביבה הכימית הספציפית שהוא יפגוש ביישום המיועד היא חיונית.
- צפיפות: לתרמופלסטיים יש עוביים משתנים, מה שיכול להשפיע על משקלם ועל תכונות החלק הכוללות. חומרים בצפיפות נמוכה, כגון פוליאתילן, מציעים פתרונות קלים, בעוד חומרים בעלי צפיפות גבוהה, כגון פוליפרופילן, מספקים חוזק וקשיחות נוספים.
תהליך הזרקה: שלב אחר שלב
תהליך ההזרקה מלווה את השלבים הללו, ומאפשר ייצור יעיל ומדויק של חלקים תרמופלסטיים איכותיים. כל שלב דורש בקרה וניטור זהירים כדי להבטיח מידות חלקים עקביות, תכונות חומר ואיכות כללית.
- עיצוב וייצור תבניות: השלב הראשון בתהליך ההזרקה הוא עיצוב וייצור התבנית. על היצרנים ליצור עיצוב תבנית מדויק ומפורט כדי להשיג את מפרט החלק הרצוי. לאחר מכן, יצרנים מייצרים את התבנית באמצעות טכניקות שונות, כגון CNC או עיבוד פריקה חשמלית (EDM).
- הכנת חומר: השלב הבא הוא הכנה לאחר שהתבנית מוכנה. כדורים או גרגירים תרמופלסטיים נבחרים על סמך תכונות החומר הרצויות ומומסים בהופר. לאחר מכן, המפעילים מזינים את החומר לתוך הקנה של מכונת ההזרקה, שם הוא עובר התכה והומוגנית.
- זריקה:במהלך שלב ההזרקה, מפעילים מחדירים את התרמופלסטי המותך לחלל התבנית בלחץ גבוה. יחידת ההזרקה של המכונה דוחפת את החומר המומס דרך זרבובית ואל התבנית. החומר ממלא את חלל התבנית, מקבל את הצורה של החלק הרצוי.
- קירור והתמצקות:לאחר מילוי התבנית, המפעילים מאפשרים לפלסטיק המותך להתקרר ולהתמצק. הקירור חיוני להשגת יציבות מימדית ויצירת חלקים תקינים. מפעילים יכולים לשלוט בתהליך הקירור על ידי זרימת נוזל קירור דרך תעלות בתוך התבנית או באמצעות לוחות קירור.
- פתיחה ופליטת עובש:מפעילים פותחים את התבנית ומוציאים את החלק מחלל התבנית לאחר שהפלסטיק מתמצק. מערכת הפליטה בתוך המכונה משתמשת בפינים, לוחות מפלט או תקיעות אוויר כדי להסיר את האזור מהתבנית. לאחר מכן התבנית מוכנה למחזור ההזרקה הבא.
- לאחר עיבוד: לאחר הפליטה, החלק עשוי לעבור פעולות שלאחר עיבוד, כגון חיתוך, פירוק או גימור משטח. שלבים אלה עוזרים להסיר עודפי חומר, להחליק קצוות גסים ולשפר את המראה הסופי של החלק.
- ביקורת איכות: השלב האחרון כולל בדיקת האיכות של החלקים המוזרקים והבטחת שהם עומדים בדרישות המפורטות. ניתן להשתמש בטכניקות שונות של בקרת איכות, לרבות מדידת ממדים, בדיקה ויזואלית ובדיקות תפקודיות, כדי לאמת את איכותו ושלמותו של החלק.
- מיחזור ושימוש חוזר בחומרים:ניתן למחזר ולעשות שימוש חוזר בכל עודפי חומר או גרוטאות שנוצרו במהלך ההזרקה. צמצום השימוש בחומר תרמופלסטי חדש עוזר למזער פסולת ולשפר את הקיימות.
ציוד המשמש בהזרקה
רכיבי ציוד אלו מקלים על תהליך ההזרקה, מהתכה והזרקת החומר התרמופלסטי ועד לעיצוב, קירור והוצאת החלק הסופי. תפעול ותחזוקה נכונה של רכיבי ציוד אלו חיוניים להשגת ייצור הזרקה יעיל ואיכותי.
- מכונת הזרקה:הציוד העיקרי בהזרקה אחראי על המסת החומר התרמופלסטי, הזרקתו לתבנית ובקרה על התהליך.
- עובש: התבנית, שעוצבה בהתאמה אישית ליצירת הצורה והתכונות הרצויות של חלק הפלסטיק, מורכבת משני חצאים, החלל והליבה. מפעילים מרכיבים אותו על יחידת ההידוק של מכונת ההזרקה.
- קוֹטֵף:מיכל המחזיק את החומר התרמופלסטי בצורת גלולה או גרגירים ומזין אותו לחבית של מכונת ההזרקה לצורך התכה והזרקה.
- חבית ובורג: החבית, תא גלילי, נמסה והומוגנית את החומר התרמופלסטי כשהבורג מסתובב בתוכו כדי להמיס, לערבב ולתקן את החומר.
- מערכות חימום וקירור:למכונות הזרקה יש גופי חימום, כמו תנורי חימום חשמליים או תנורי חימום המשתמשים בשמן חם, להעלאת טמפרטורת החבית, ומערכות קירור, כמו זרימת מים או שמן, לקירור התבנית ולמצק את חלק הפלסטיק.
- מערכת מפלט:מסיר את החלק היצוק מחלל התבנית לאחר התמצקות, בדרך כלל תוך שימוש בסיכות מפלט, צלחות או תקיעות אוויר במהלך פתיחת התבנית.
- מערכת בקרה:מעקב ובקרה על פרמטרים שונים של תהליך ההזרקה, ומאפשר למפעילים להגדיר ולהתאים פרמטרים כגון מהירות הזרקה, טמפרטורה, לחץ וזמן קירור.
מכונות הזרקה: סוגים ומאפיינים
לכל סוג של מכונת הזרקה יש את המאפיינים והיתרונות שלו, המאפשרים ליצרנים לבחור את המכשיר המתאים ביותר לדרישות הייצור הספציפיות שלהם.
- מכונות הזרקה הידראולית: מכונות אלו משתמשות במערכות הידראוליות כדי ליצור את הלחץ הדרוש להזרקת פלסטיק מותך לתוך התבנית. הם ידועים בכוח ההידוק הגבוה שלהם, בשליטה מדויקת וברבגוניות בטיפול בתרמופלסטיים שונים. מכונות הידראוליות מתאימות לייצור בקנה מידה גדול ויכולות להכיל תבניות מורכבות.
- מכונות הזרקה חשמליות:מכונות חשמליות משתמשות במנועי סרוו חשמליים לתפעול המכונה, לרבות מערכות ההזרקה, ההידוק והפליטה. הם מציעים שליטה מדויקת, יעילות אנרגטית וזמני תגובה מהירים יותר מאשר מכונות הידראוליות. מכונות חשמליות הן אידיאליות ליישומי יציקה מדויקת הדורשים חזרה ודיוק גבוהים.
- מכונות הזרקה היברידיות:מכונות היברידיות משלבות את היתרונות של מכשירים הידראוליים וחשמליים כאחד. הם משתמשים בשילוב של מערכות סרוו הידראוליות וחשמליות כדי להשיג דיוק גבוה, יעילות אנרגטית וחסכוניות. מכונות היברידיות מתאימות למגוון רחב של יישומים, ומספקות איזון בין ביצועים ועלויות תפעול.
- מכונות הזרקת שתי צלחות: מכונות שתי פלטות בעלות עיצוב ייחודי עם שתי לוחות נפרדות להידוק התבנית. עיצוב זה מספק יציבות משופרת, סנכרון תבנית משופר ומאפשר גדלי תבנית גדולים יותר וכוחות הידוק גבוהים יותר. מכונות דו פלטות מתאימות לחלקים גדולים ומורכבים הדורשים יציקה מדויקת.
- מכונות הזרקה מרובות רכיבים:יצרנים מתכננים מכונות אלה כדי לייצר חלקים עם חומרים או צבעים מרובים במחזור דפוס אחד. יש להם יחידות הזרקה ותבניות שונות, המאפשרות הזרקה בו-זמנית של חומרים שונים. מכונות מרובות רכיבים מציעות גמישות ויעילות בייצור חלקים מורכבים בעלי מאפיינים משתנים.
- מכונות מיקרו הזרקה:תוכננו במיוחד לייצור חלקים קטנים ומדויקים, מכונות הזרקה מיקרו מציעות דיוק ודיוק גבוהים להפליא. הם יכולים לייצר פרטים מורכבים עם סובלנות הדוקה ובזבוז חומרים מינימליים. אלקטרוניקה, מכשירים רפואיים ומיקרו-אופטיקה משתמשים בדרך כלל במכונות מיקרו-הזרקה.
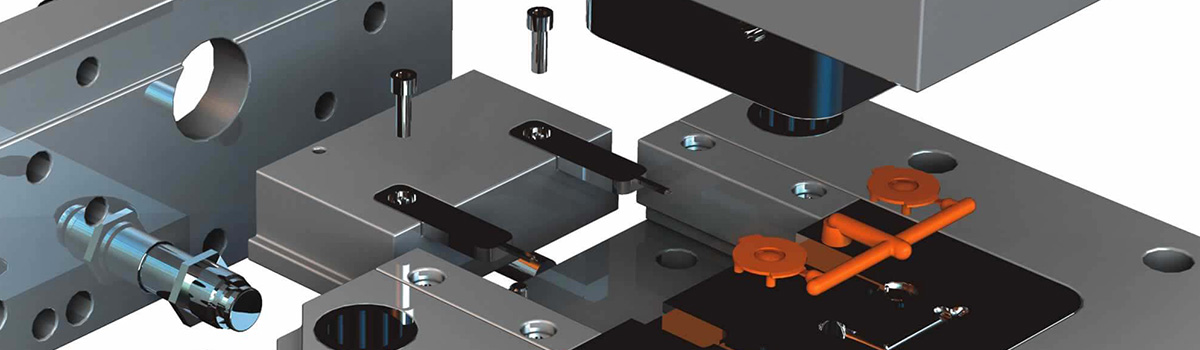
שיקולי עיצוב עובש עבור הזרקה
שיקולי עיצוב קפדניים של תבניות חיוניים לייצור מוצלח של הזרקה.
- עיצוב חלק:עיצוב התבנית צריך להתאים לדרישות הספציפיות של החלק, כולל צורתו, מידותיו ותכונותיו הפונקציונליות. היצרנים צריכים לשקול כראוי את זוויות הטיוטה, עובי הדופן, חתכים תחתונים וכל האלמנטים הדרושים כדי להבטיח קלות פליטה ואיכות חלק.
- חומר עובש: בחירת חומרי התבנית היא קריטית להשגת עמידות, יציבות ממדית ועמידות בחום. חומרי עובש נפוצים כוללים סגסוגות פלדה, סגסוגות אלומיניום ופלדות כלי עבודה. בחירת החומר תלויה בגורמים כגון נפח ייצור, מורכבות החלק וחיי הכלי הצפוי.
- מערכת קירור:קירור יעיל חיוני להתמצקות חלקים נכונה ולמזעור זמן המחזור. עיצוב התבנית צריך לשלב תעלות קירור או תוספות במיקום אסטרטגי כדי להבטיח קירור אחיד של התבנית. קירור נכון מפחית את הסיכון לעיוות, התכווצות ופגמים בחלקים.
- אוורור:יש צורך באוורור נאות כדי לאפשר בריחת אוויר וגזים במהלך תהליך ההזרקה. אוורור לא מספיק עלול להוביל למלכודות גז, לסימני צריבה או למילוי חלק לא שלם. היצרנים יכולים להשיג אוורור על ידי שילוב חריצי אוורור, פינים או מנגנונים אחרים בעיצוב התבנית.
- מערכת פליטה:עיצוב התבנית צריך לכלול מערכת פליטה יעילה כדי להסיר בצורה בטוחה ויעילה את החלק היצוק מחלל התבנית. מערכת הפליטה יכולה להיות מורכבת מסיכות מפלט, שרוולים או מנגנונים אחרים, הממוקמים באופן אסטרטגי כדי למנוע הפרעה לתפקוד או לתכונות קריטיות.
- עיצוב שער:השער הוא המקום שבו פלסטיק מותך נכנס לחלל העובש. עיצוב השער צריך להבטיח מילוי נכון של חלקים, למזער קווי זרימה ולמנוע הקפאת חומרים מוקדמת. עיצובי שערים סטנדרטיים כוללים שערי קצה, שערי מנהרה ומערכות חמות, בהתאם לדרישות החלק ותכונות החומר.
- קו פרידה:עיצוב התבנית צריך להגדיר קו פרידה מתאים, שהוא הקו שבו מתאחדים שני חצאי התבנית. מיקום נכון של קו הפרידה מבטיח חוסר התאמה מינימלית של הבזק ושל קו הפרידה ומקל על הרכבה יעילה של התבניות.
- תחזוקה ושירות של עובש: על היצרנים לשקול את קלות התחזוקה, התיקון וטיפול בתבניות. רכיבי העובש צריכים להיות נגישים בקלות לניקוי, בדיקה והחלפה. שילוב תכונות כמו תוספות לשינוי מהיר או עיצובי תבניות מודולריים יכולים לשפר את יכולת השירות של התבניות.
חומרי עובש המשמשים בהזרקה
שיתוף פעולה עם מומחי חומרי תבניות והתחשבות בצרכים הספציפיים של יישום הדפוס יכולים לעזור לקבוע את החומר המתאים ביותר להשגת ביצועי תבנית אופטימליים ואיכות חלקים.
- סגסוגות פלדה: סגסוגות פלדה, כגון פלדות כלי עבודה (למשל, P20, H13) ופלדות אל חלד, משמשות בדרך כלל לתבניות הזרקה בשל העמידות המצוינת שלהן, עמידותן בחום ועמידותן בפני שחיקה. חומרים אלו יכולים לעמוד בטמפרטורות ובלחצים הגבוהים בתהליך ההזרקה ומציעים יציבות מימדית טובה לייצור חלקים באיכות גבוהה.
- סגסוגות אלומיניום:סגסוגות אלומיניום, כגון 7075 ו-6061, הן קלות משקל ומציעות מוליכות תרמית טובה, מה שהופך אותן למתאימות לתבניות הדורשות קירור יעיל. יצרנים משתמשים לעתים קרובות בתבניות אלומיניום ליצירת אב טיפוס, ייצור בנפח נמוך או יישומים שבהם הפחתת משקל היא קריטית. עם זאת, תבניות אלומיניום עשויות להיות בעלות עמידות נמוכה יותר בהשוואה לסגסוגות פלדה.
- סגסוגות נחושת:סגסוגות נחושת, כגון נחושת בריליום, מציגות מוליכות תרמית גבוהה ויכולת עיבוד טובה. הם מוצאים שימוש בתבניות הדורשות העברת חום מעולה לקירור יעיל. סגסוגות נחושת יכולות לעזור להפחית את זמני המחזור על ידי פיזור מהיר של חום מהחלק היצוק, וכתוצאה מכך להתמצקות מהירה יותר.
- פלדות כלי עבודה:פלדות כלי עבודה, כולל H13, S7 ו-D2, מיועדות ליישומי כלי עבודה בעלי ביצועים גבוהים. פלדות אלו מציעות שילוב של חוזק גבוה, קשיות ועמידות בפני שחיקה. פלדות כלי עבודה מתאימות לתבניות בעלות נפחי ייצור גבוהים, חומרים שוחקים או תנאי יציקה תובעניים.
- סגסוגות ניקל:סגסוגות ניקל, כגון Inconel ו- Hastelloy, ידועות בעמידותן יוצאת הדופן בפני קורוזיה, חוזק בטמפרטורה גבוהה ויציבות תרמית. היצרנים משתמשים בסגסוגות אלו בתבניות המטפלות בחומרים קורוזיביים או דורשות עמידות לטמפרטורות קיצוניות ולסביבות דפוס אגרסיביות.
- חומרים מרוכבים:חומרים מרוכבים, כגון פלסטיק מחוזק או חומרים מרוכבים עם תוספות מתכת, משמשים מדי פעם ליישומי דפוס ספציפיים. חומרים אלה מציעים איזון של תכונות, כגון חוזק גבוה, יציבות תרמית ומשקל מופחת. תבניות מרוכבות יכולות להיות חלופות חסכוניות לדרישות ייצור ספציפיות.
סוגי תבניות הזרקה
הזרקה היא תהליך ייצור רב תכליתי ונפוץ עבור חלקי פלסטיק.
- תבנית דו צלחות:תבנית הדו-צלחות היא הסוג הנפוץ ביותר של תבנית הזרקה. הוא מורכב משתי לוחות, לוחית החלל ולוח הליבה, הנפרדות כדי לאפשר פליטת החלק היצוק. צלחת החלל מכילה את צד החלל של התבנית, בעוד שצלחת הליבה מכילה את צד הליבה. היצרנים משתמשים בתבניות דו צלחות לייצור מגוון רחב של חלקים בשל העיצוב הפשוט יחסית שלהן.
- תבנית שלוש צלחות:תבנית שלושת הלוחות היא גרסה מתקדמת של תבנית הדו-צלחות. הוא כולל צלחת נוספת, הראנר או צלחת ה-Sprue. לוחית הרץ יוצרת תעלה נפרדת עבור הזרימה, הרצים והשערים, ומאפשרת הסרה קלה יותר של החלק היצוק. יצרנים משתמשים בדרך כלל בתבניות שלוש צלחות לפרטים עם מערכות שער מורכבות או כאשר רצוי להימנע משריד שער על היצירה.
- תבנית ראנר חמה:מערכת הראנר והשער מחוממת בתבניות ראנר חמות, ומבטלת את הצורך בהתמצקות והמסה מחדש של החומר בכל מחזור. מערכת הראנר החם מורכבת מסעפות ומחרירים מחוממים השומרים על המצב המותך של הפלסטיק. תבניות רץ חמות מציעות יתרונות כמו זמן מחזור מופחת, בזבוז חומר נמוך יותר ואיכות חלקים משופרת על ידי מזעור שרידי שער.
- עובש קר ראנר: לתבניות רץ קר יש מערכת ראנר ושער מסורתית שבה הפלסטיק המותך זורם דרך רצים קרים שמתמצקים עם כל מחזור. לאחר מכן המפעילים מסירים את הרצים המוצקים, וכתוצאה מכך לבזבוז חומר. יצרנים משתמשים בדרך כלל בתבניות רינר מורכבות לייצור בנפח נמוך יותר או כאשר עלויות החומרים פחות קריטיות בגלל העיצוב הפשוט יותר שלהן.
- הכנס תבנית:תבניות הכנס משלבות תוספות מתכת או פלסטיק לתוך חלל התבנית במהלך ההזרקה. ניתן להכניס תוספות מראש לתבנית או להכניס אותן בתהליכים אוטומטיים. תבנית זו מאפשרת שילוב רכיבים נוספים או אלמנטים מחזקים לתוך החלק היצוק, תוך שיפור הפונקציונליות או החוזק שלו.
- עובש יתר: יציקת יתר כוללת יציקת חומר אחד על פני חומר אחר, בדרך כלל חיבור של מצע פלסטי קשיח עם אלסטומר או תרמופלסטי רך יותר. תהליך זה מאפשר יצירה של חלקים עם מספר חומרים או טקסטורות בתבנית אחת, המספק אחיזה, ריפוד או תכונות אסתטיות משופרות.
גורמים המשפיעים על עלויות הזרקה
התחשבות בגורמים אלה יכולה לעזור ליצרנים להעריך ולמטב את עלות ההזרקה, להבטיח איזון בין איכות, יעילות וחסכוניות עבור דרישות הייצור הספציפיות שלהם.
- מורכבות חלק:המורכבות של עיצוב החלק משחקת תפקיד משמעותי בקביעת העלות של הזרקה. גיאומטריות מורכבות, חתכים תחתונים, קירות דקים או מאפיינים מורכבים עשויים לדרוש כלי עבודה נוספים, תבניות מיוחדות או מחזורים ארוכים יותר, מה שמגדיל את עלות הייצור הכוללת.
- בחירת חומר:הבחירה בחומר תרמופלסטי משפיעה על עלות ההזרקה. לחומרים שונים יש מחירים משתנים לקילוגרם, וגורמים כגון זמינות החומר, תכונות ודרישות עיבוד יכולים להשפיע על עלות החומר הכוללת.
- עיצוב כלי עבודה ותבנית: עלויות האבזור הראשוניות ועיצוב התבניות הן משמעותיות בעלויות ההזרקה. גורמים כמו מורכבות העובש, מספר החללים, גודל העובש וחומר העובש תורמים להוצאות כלי העבודה וייצור התבניות. תבניות מורכבות יותר או תבניות הדורשות תכונות מתקדמות יכולות להגדיל את ההשקעה מראש.
- נפח ייצור: נפח הייצור משפיע ישירות על העלות לחלק בהזרקה. ספרים גבוהים יותר מביאים לרוב ליתרונות לגודל, ומפחיתים את העלות לחלק. לעומת זאת, ריצות ייצור בנפח נמוך עשויות לגרור חיובים גבוהים יותר עקב התקנה, כלי עבודה ובזבוז חומרים.
- זמן מחזור: זמן המחזור, הכולל את שלבי הקירור והפליטה, משפיע על כושר הייצור והעלות הכוללת. זמני מחזור ארוכים יותר מביאים להפחתת תפוקת הייצור ולמחירים גבוהים יותר. אופטימיזציה של עיצוב התבנית, מערכת הקירור ופרמטרי התהליך יכולה למזער את זמני המחזור ולשפר את היעילות.
- דרישות איכות:דרישות איכות מחמירות או אישורים ספציפיים יכולים להשפיע על עלות ההזרקה. עמידה בסובלנות מדויקת, דרישות גימור פני השטח או בדיקות נוספות עשויות לדרוש משאבים, תהליכים או בדיקות אחרים, שיוסיפו לעלות הכוללת.
- פעולות משניות:אם החלקים המעוצבים דורשים פעולות לאחר עיבוד כגון הרכבה, צביעה או שלבי גימור נוספים, פעולות אלו יכולות להוסיף לעלות הכוללת של הזרקה.
- ספק ומיקום:בחירת ספק ההזרקה ומיקומם יכולים להשפיע על העלויות. עלויות העבודה, התקורות, הוצאות הלוגיסטיקה וההובלה משתנות בהתאם למיקומו של הספק, ומשפיעות על עלות הייצור הכוללת.
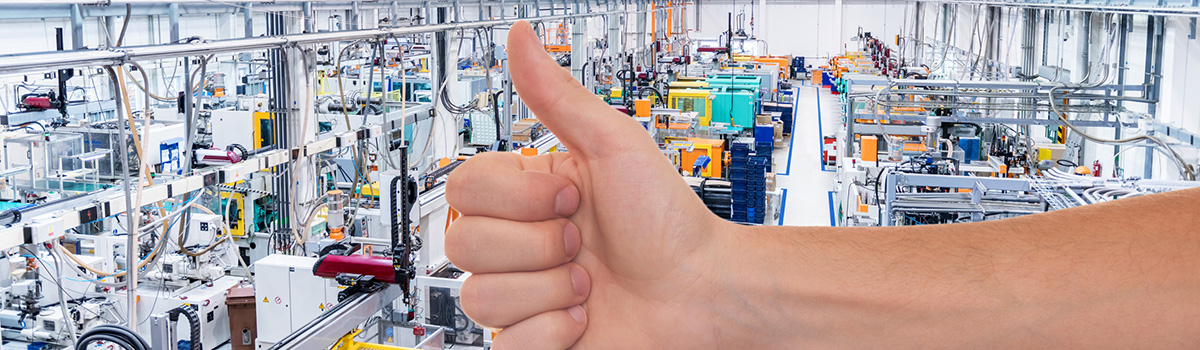
בקרת איכות בהזרקה
הטמעת אמצעי בקרת איכות חזקים לאורך תהליך ההזרקה עוזרת לזהות ולטפל בפגמים פוטנציאליים, חריגות או חוסר עקביות, ומבטיחה ייצור של חלקים באיכות גבוהה העומדים במפרט ודרישות הלקוח.
- ניטור תהליכים: ניטור רציף של פרמטרים מרכזיים של תהליך, כגון טמפרטורת התכה, לחץ הזרקה, זמן קירור וזמן מחזור, מבטיח עקביות וחזרה בייצור חלקי. ניטור בזמן אמת ומערכות אוטומטיות יכולות לזהות שינויים או סטיות מפרמטרים שנקבעו, מה שמאפשר התאמות בזמן ושמירה על יציבות התהליך.
- בדיקה ומדידה:סקירה ומדידה קבועה של חלקים יצוקים חיוניים כדי לוודא את דיוק הממדים, איכות החלקים ועמידה במפרטים. השירותים שלנו מכסים מגוון שיטות בקרת איכות, כגון מדידת מידות, ניתוח איכות פני השטח, ביצוע בדיקות חזותיות וביצוע בדיקות תפקודיות. טכניקות בדיקה שונות, כגון מכונות מדידת קואורדינטות (CMM) ומערכות בדיקה אופטיות וויזואלית, משמשות להערכה מדויקת.
- בקרת תהליכים סטטיסטיים (SPC): SPC כרוך באיסוף וניתוח נתוני תהליך לניטור ובקרה על איכות ההזרקה. שיטות סטטיסטיות, כגון תרשימי בקרה וניתוח יכולות תהליכים, עוזרות לזהות מגמות, לזהות וריאציות בתהליך ולהבטיח שהתהליך נשאר בגבולות בקרה מוגדרים. SPC מאפשר זיהוי יזום של בעיות ומקל על אופטימיזציה של תהליכים.
- בדיקת חומר: בדיקת חומרי הגלם, כגון תרמופלסטיים, תוספים וחומרי צבע, מבטיחה את איכותם והתאמתם להזרקה. בדיקות חומר עשויות לכלול ניתוח של אינדקס זרימת נמס (MFI), תכונות מכניות, מאפיינים תרמיים והרכב החומר. אימות איכות החומר מסייע במניעת פגמים וחוסר עקביות בחלקים המעוצבים.
- תחזוקה ובדיקה של כלי עבודה:תחזוקה נכונה ובדיקה שוטפת של תבניות ההזרקה הן חיוניות להבטחת האיכות בהזרקה. ניקוי, שימון והערכה קבועים של רכיבי העובש עוזרים למנוע בלאי, נזק או השפלה שעלולים להשפיע על איכות החלקים. תיקון או החלפה בזמן של רכיבי עובש בלויים או פגומים חיוניים לשמירה על ביצועי דפוס עקביים.
- תיעוד ומעקב:שמירה על תיעוד מקיף ורישומי עקיבות חיונית לבקרת איכות בהזרקה. חיוני לרשום פרמטרים של תהליך, תוצאות בדיקה, מידע חומרי וכל שינוי או התאמה שנעשו במהלך הייצור. תיעוד מתאים מאפשר מעקב אחר חלקים, מקל על ניתוח סיבת השורש ומבטיח עקביות באיכות.
- הדרכה ופיתוח מיומנויות: מתן הכשרה נאותה ותוכניות פיתוח מיומנויות למפעילים, טכנאים ואנשי בקרת איכות משפרת את הבנתם בתהליכי הזרקה, דרישות איכות וטכניקות בדיקה. צוות מיומן היטב יכול לזהות פגמים, לפתור בעיות וליישם אמצעי תיקון ביעילות, תוך הבטחת ייצור באיכות גבוהה.
פגמים נפוצים בהזרקה וכיצד להימנע מהם
בדיקה, ניטור וניתוח שוטפים של תהליכי הזרקה ותחזוקה והתאמה נכונה של ציוד ותבניות יכולים לסייע בזיהוי וטיפול בליקויים הנפוצים הללו.
- סימני כיור:סימני כיור הם שקעים או חריצים על פני החלק היצוק הנגרמים מקירור לא אחיד או התכווצות. יש לשקול מיקום ועיצוב נכון של השער, תכנון אופטימלי של מערכת הקירור וחלוקת עובי דופן אחידה כדי למנוע סימני כיור. הגדלת לחץ ההזרקה או התאמת זמן הקירור יכולים גם לעזור למזער סימני כיור.
- עיוות:עיוות מתייחס לעיוות או כיפוף של חלק יצוק לאחר פליטה עקב קירור לא אחיד או מתחים שיוריים. שמירה על עובי דופן אחיד, שימוש בתעלות קירור מתאימות והקפדה על מילוי ואריזה מאוזנים של התבנית חיוניים למניעת עיוות. אופטימיזציה של טמפרטורת התבנית, שימוש בזוויות טיוטה מתאימות ושליטה בטמפרטורת החומר ומהירות ההזרקה יכולים לעזור למזער את העיוות.
- פלאש:הבזק מתרחש כאשר חומר עודף זורם לתוך קו הפרידה של התבנית, וכתוצאה מכך הקרנות דקות ולא רצויות או חומר נוסף על החלק הסופי. ניתן למנוע הבזק ביעילות על ידי הבטחת עיצוב נכון של התבנית, כולל הפעלת כוח הידוק מתאים, יישור מדויק ושימוש בטכניקות אוורור מתאימות. אופטימיזציה של פרמטרי תהליך כגון לחץ הזרקה, טמפרטורה וזמן מחזור מפחית את ההבזק.
- צילום קצר:זריקה מהירה מתרחשת כאשר החומר המוזרק אינו ממלא את חלל העובש, וכתוצאה מכך חלק לא שלם. בחירת חומר נכונה, הבטחת טמפרטורת התכה וצמיגות נאותים ושמירה על לחץ וזמן הזרקה מתאימים חיוניים כדי להימנע מתמונות קצרות. בנוסף, אימות עיצוב התבנית עבור גודל רץ ושער מספיק ואוורור נכון יכול לעזור למנוע יריות מהירות.
- קווי ריתוך:קווי ריתוך מתרחשים כאשר שתיים או יותר חזיתות זרימת חומר מותך נפגשות ומתמצקות, וכתוצאה מכך קו או סימן גלוי על פני החלק. עיצוב טוב של שער ורץ, טמפרטורת התכה אופטימלית, מהירות הזרקה והתאמת זרימת החומר וגיאומטריית החלק יכולים למזער קווי ריתוך. ניתוח זרימת עובש ואופטימיזציה של מיקום שערים יכולים גם לעזור למנוע או להפחית קווי ריתוך.
- סימני צריבה:סימני צריבה הם שינויי צבע או כתמים שחורים על פני החלק היצוק הנגרמים מחום יתר או התחממות יתר של החומר. הימנעות מטמפרטורת התכה קיצונית, שימוש בתעלות קירור מתאימות ואופטימיזציה של זמן המחזור יכולים לסייע במניעת סימני צריבה. אוורור נאות, עיצוב נכון של שער ושליטה בטמפרטורת העובש תורמים גם הם למזעור סימני צריבה.
פעולות לאחר יציקה: גימור והרכבה
לאחר ההזרקה, חלקים יצוקים רבים עשויים לדרוש פעולות גימור והרכבה נוספות כדי להשיג את התוצר הסופי הרצוי. פעולות אלה לאחר הדפוס עשויות לכלול:
- זְמִירָה:הסר כל עודפי חומר או הבזק סביב החלק היצוק באמצעות כלי חיתוך או חיתוך.
- טיפול שטח:שיפור המראה או הפונקציונליות של משטח החלק באמצעות טכניקות שונות כגון צביעה, ציפוי או טקסטורה.
- הַרכָּבָה:חיבור מספר חלקים יצוקים או הוספת רכיבים כגון מחברים, תוספות או תוויות להשלמת המוצר הסופי.
- בדיקה:אימות של איכות ופונקציונליות של חלקים באמצעות שיטות בדיקה שונות כגון ניתוח ממדים, בדיקת מאפייני החומר או בדיקת ביצועים.
- אריזה ומשלוח:אריזה ותווית נכונה של המוצר המוגמר למשלוח ללקוחות או למשתמשי קצה.
הבחירה של פעולות לאחר יציקה תלויה ביישום הספציפי ובמאפייני המוצר הסופי הרצויים. שיתוף פעולה הדוק בין מומחי הזרקה, מומחי גימור והרכבה, והלקוח הוא מכריע להשגת איכות ופונקציונליות המוצר האבסולוטית הרצויה. תכנון נכון ושילוב פעולות לאחר יציקה בתהליך הייצור יכולים לעזור להבטיח ייצור יעיל ואספקה בזמן של מוצרים באיכות גבוהה.
הזרקה לעומת תהליכי ייצור פלסטיק אחרים
לכל תהליך ייצור פלסטיק יש יתרונות ומגבלות, מה שהופך אותם למתאימים ליישומים שונים.
- הזרקה: הזרקה היא תהליך ייצור רב תכליתי ונפוץ לייצור חלקי פלסטיק. הוא מציע יתרונות כמו יעילות ייצור גבוהה, שכפול חלקים מדויק ויכולת ליצור גיאומטריות מורכבות. הזרקה מתאימה להפעלות ייצור בנפח גבוה ומאפשרת שימוש במגוון רחב של חומרים תרמופלסטיים. הוא מציע דיוק מימד וגימור משטח מעולה, מה שהופך אותו לאידיאלי עבור תעשיות שונות כגון רכב, מוצרי צריכה ומכשור רפואי.
- דפוס מכה: דפוס נשיפה הוא תהליך המשמש בעיקר לייצור חלקי פלסטיק חלולים, כגון בקבוקים, מיכלים ורכיבי רכב. זה כולל המסת פלסטיק וניפוחו לחלל תבנית, יצירת הצורה הרצויה. דפוס נשיפה מתאים לייצור בנפח גבוה ויכול לייצר חלקים גדולים וקלים בעלי עובי דופן אחיד. עם זאת, הוא מוגבל מבחינת מורכבות החלקים ובחירת החומרים בהשוואה להזרקה.
- תרמופורמינג:תרמופורמינג הוא תהליך המשמש לייצור חלקי פלסטיק על ידי חימום יריעה תרמופלסטית ועיצובה באמצעות תבניות או יצירת ואקום. הוא מוצא שימוש נפוץ באריזות, במוצרים חד פעמיים ובמוצרים בקנה מידה גדול כמו מגשים וכיסויים. Thermoforming מציע ייצור חסכוני עבור חלקים גדולים ומאפשר יצירת אב טיפוס מהיר. עם זאת, יש לו מגבלות לגבי מורכבות החלקים, בחירת החומרים ודיוק הממדים בהשוואה להזרקה.
- שִׁחוּל:שחול הוא תהליך מתמשך לייצור פרופילי פלסטיק, יריעות, צינורות וסרטים. זה כרוך בהמסת שרף פלסטי ובכוחו דרך תבנית כדי ליצור את הצורה הרצויה. אקסטרוזיה מתאימה לייצור אורכים ארוכים ומתמשכים של מוצרי פלסטיק עם חתך רוחב עקבי. בעוד שהשחול מציעה שיעורי ייצור גבוהים וחסכוניות, היא מוגבלת מבחינת גיאומטריות חלקים מורכבות ושליטה ממדית מדויקת בהשוואה להזרקה.
- דפוס דחיסה:יציקת דחיסה כוללת הנחת כמות שנמדדה מראש של חומר תרמוסטי בחלל תבנית מחומם ודחיסתו בלחץ גבוה עד להחלמה. הוא מוצא שימוש נפוץ בייצור חלקים בעלי חוזק ויציבות מימדית גבוהה, כגון רכיבי רכב ובידוד חשמלי. דפוס דחיסה מציע עקביות חלק טובה, יעילות ייצור גבוהה ויכולת להשתמש במגוון רחב של חומרים. עם זאת, הוא מוגבל מבחינת מורכבות החלק וזמן המחזור בהשוואה להזרקה.
יישומים של הזרקה תרמופלסטית
תעשיות שונות משתמשות רבות בהזרקה תרמופלסטית בשל הרבגוניות, היעילות והעלות-תועלת שלה. חלק מהיישומים של הזרקה תרמופלסטית כוללים:
- תעשיית הרכב: תעשיית הרכב עושה שימוש נרחב בהזרקה תרמופלסטית לייצור רכיבים שונים, כולל חיפוי פנים וחוץ, לוחות מחוונים, לוחות דלתות, פגושים ומחברים חשמליים. התהליך מאפשר שכפול מדויק של חלקים, גיאומטריות מורכבות וחומרים קלים, משפר את יעילות הדלק וגמישות העיצוב.
- מוצרי צריכה:הזרקה מוצאת יישומים נרחבים בייצור מוצרי צריכה כגון מכשירי חשמל ביתיים, מכשירים אלקטרוניים, מיכלי אריזה וצעצועים. התהליך מאפשר ייצור המוני של מוצרים עמידים ואיכותיים בעלי מידות עקביות וגימור פני השטח. זה גם מאפשר אפשרויות התאמה אישית ואיטרציות מהירות של מוצרים.
- מכשירים רפואיים:הזרקה ממלאת תפקיד מכריע בתעשייה הרפואית לייצור מגוון רחב של מכשירים, כולל מזרקים, מכשירים כירורגיים, רכיבים מושתלים ומערכות אספקת תרופות. התהליך מבטיח ייצור של חלקים סטריליים, מדויקים וביו תואמים העומדים בדרישות הרגולטוריות המחמירות של מגזר הבריאות.
- תעשיית האלקטרוניקה והחשמל:תעשיית האלקטרוניקה משתמשת בהזרקה לייצור מחברים חשמליים, מארזים, מתגים ורכיבים אחרים. התהליך מציע דיוק מימדים גבוה, גימור משטח מעולה, ויכולת לשלב תכונות כגון יציקת הוספה ועיצוב יתר, המאפשרים ייצור יעיל של מכלולים אלקטרוניים מורכבים.
- תעשיית האריזה:תעשיות שונות, כולל מזון ומשקאות, תרופות וטיפוח אישי, משתמשות בדרך כלל בהזרקה לייצור מיכלי אריזות פלסטיק, פקקים, סגרים ובקבוקים. התהליך מאפשר יצירת פתרונות אריזה קלים, עמידים ומושכים מבחינה אסתטית עם מחזורי ייצור יעילים.
- תעשיית התעופה והחלל:תחום התעופה והחלל משתמש בהזרקה לייצור רכיבים קלים ובעלי ביצועים גבוהים כגון תעלות אוויר, סוגרים, לוחות פנים וחלקי מבנה. התהליך מאפשר שימוש בחומרים מתקדמים וגיאומטריות חלקים מורכבות, התורמים להפחתת משקל ולשיפור יעילות הדלק.
ההשפעה הסביבתית של הזרקה תרמופלסטית
הזרקה תרמופלסטית היא תהליך ייצור פופולרי בשל יתרונותיו הרבים, אך חיוני לקחת בחשבון גם את ההשפעה הסביבתית שלו. הנה כמה נקודות שכדאי לקחת בחשבון:
- יעילות חומר:הזרקה תרמופלסטית מקדמת את יעילות החומר על ידי מזעור הפסולת. התהליך מנצל שליטה מדויקת על כמות החומר המוזרקת לתבנית, ומפחית את הצורך בחומר עודף. יצרנים יכולים גם להשתמש בטכניקות טחינה ומחזור כדי לעשות שימוש חוזר בגרוטאות או בחלקים שנדחו, ולהפחית עוד יותר את פסולת החומר.
- צריכת אנרגיה:היצרנים מתכננים מכונות הזרקה כדי להיות חסכוניות באנרגיה, עם דגמים מודרניים המשלבים טכנולוגיות מתקדמות כגון מנועי סרוו והנעים במהירות משתנה. תכונות אלו מייעלות את צריכת האנרגיה על ידי הפחתת צריכת החשמל במהלך הדפוס, וכתוצאה מכך דרישות אנרגיה נמוכות יותר והפחתת ההשפעה הסביבתית.
- ניהול פסולת:תוך מזעור בזבוז חומר, על היצרנים ליישם נוהלי ניהול פסולת נאותים לטיפול בשאריות חומרים, זרמים או רצים. יצרנים יכולים להקים תוכניות מיחזור לאיסוף ושימוש חוזר בפסולת פלסטיק שנוצרת במהלך הזרקה, ובכך להפחית את הפסולת הנשלחת למזבלות.
- הפחתת פליטות: הזרקה תרמופלסטית מייצרת בדרך כלל פליטות נמוכות יותר מתהליכי ייצור אחרים. היצרנים יכולים להפחית את הפליטות על ידי שימוש בחומרים ידידותיים לסביבה, יישום ציוד חסכוני באנרגיה, ושימוש במערכות פליטה וסינון מתקדמות כדי ללכוד את כל הפליטות המשתחררות.
- בחירות חומרים בר קיימא:הבחירה של חומרים תרמופלסטיים יכולה להשפיע באופן משמעותי על הקיימות הסביבתית של הזרקה. בחירה בפלסטיק מתכלה או מבוסס ביו, כמו גם חומרים ממוחזרים או ניתנים למחזור, יכולה לסייע בהפחתת טביעת הרגל האקולוגית הכוללת של התהליך.
שיקולי מחזור חיים: התחשבות בכל מחזור החיים של המוצר היצוק חיונית להערכת ההשפעה הסביבתית שלו. במהלך שלבי התכנון ובחירת החומרים, היצרנים צריכים לשקול גורמים כגון עמידות החלק, יכולת המיחזור שלו והפוטנציאל לסילוק או שימוש חוזר בסוף החיים.
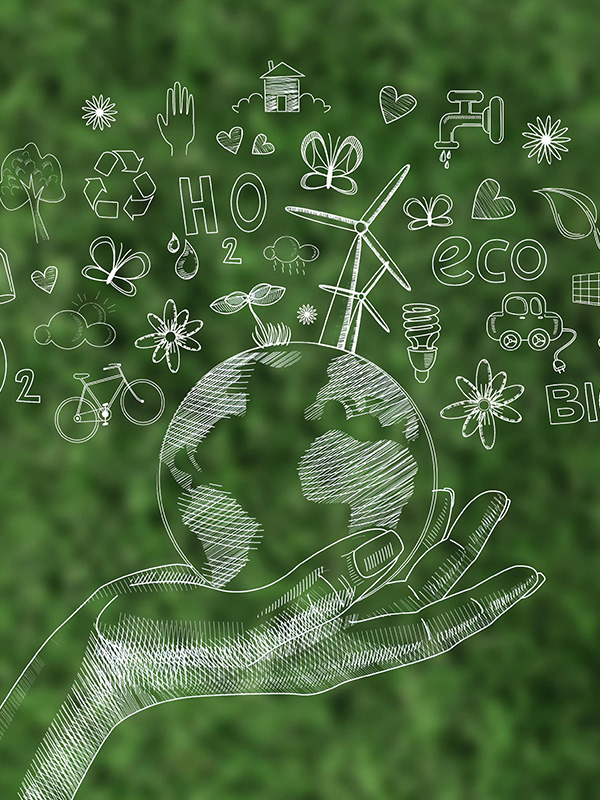
עתיד הזרקה תרמופלסטית
העתיד של הזרקה תרמופלסטית נראה מבטיח, עם התקדמות מתמשכת בטכנולוגיה וביקוש מוגבר לחלקים איכותיים ומדויקים בתעשיות שונות. חלק מההתפתחויות המרכזיות הצפויות בשנים הקרובות כוללות:
- שימוש מוגבר באוטומציה ורובוטיקה לשיפור היעילות והפחתת עלויות.
- המאמצים מתמקדים בפיתוח חומרים ותהליכים חדשים כדי לשפר את ביצועי החלקים ולאפשר יישומים חדשים.
- זהו אימוץ הולך וגובר של שיטות קיימא, כגון שימוש בחומרים ממוחזרים וייעול צריכת האנרגיה, כדי להפחית את ההשפעה הסביבתית של הזרקה.
- אינטגרציה רבה יותר של טכנולוגיות דיגיטליות, כגון תוכנות הדפסה ותלת מימד, לשיפור תהליכי התכנון והייצור.
שוק ההזרקה העולמי מתרחב, במיוחד בכלכלות מתעוררות, מונע מהביקוש הגובר למוצרי פלסטיק בתעשיות שונות.
בחירת השותף המתאים להזרקה
בחירת השותף הנכון להזרקה היא קריטית להצלחת הפרויקט שלך. קח את הזמן כדי להעריך אפשרויות מרובות, לנהל ביקורים באתר ולהשתתף בדיונים יסודיים כדי להבטיח שותפות תואמת וארוכת טווח.
- מומחיות וניסיון:חפשו שותף להזרקה עם ידע וניסיון רב בענף. הם צריכים להיות בעלי רקורד מוכח של אספקת מוצרים ופתרונות באיכות גבוהה ללקוחות במגזרים שונים. שקול את ההבנה שלהם לגבי חומרים שונים, עיצובי תבניות ותהליכי ייצור.
- יכולות ייצור: העריכו את יכולות הייצור של השותף להזרקה. ודא שיש להם מתקן מאובזר היטב עם מכונות וטכנולוגיות מודרניות כדי להתמודד עם דרישות הפרויקט שלך. שקול את יכולת הייצור שלהם, את היכולת להתמודד עם גדלים ומורכבות של חלקים שונים, ויכולת לעמוד בהיקפי הייצור הרצויים ובלוחות הזמנים הרצויים שלך.
- בקרת איכות:האיכות היא ערך עליון בהזרקה. הערכת מערכות בקרת האיכות וההסמכות של השותף הפוטנציאלי. חפש שותפים העוקבים אחר תקני איכות מחמירים, בעלי תהליכי בדיקה חזקים ומבצעים בדיקות מקיפות כדי להבטיח איכות ועקביות של חלקים.
- תמיכה בתכנון והנדסה:שותף אמין בהזרקה צריך להציע תמיכה בתכנון והנדסה כדי לייעל את עיצוב החלק שלך לאפשרות ייצור. הם צריכים להיות מהנדסים מיומנים שיכולים לספק מידע רב ערך על בחירת חומרים, עיצוב תבניות ואופטימיזציה של תהליכים כדי לשפר את איכות ויעילות החלקים.
- תחרותיות בעלויות:למרות שהעלות לא צריכה להיות הגורם הקובע הבלעדי, חיוני להעריך את התמחור והתחרותיות בעלויות של שותף ההזרקה. בקש הצעות מחיר מפורטות ושקול עלויות כלי עבודה, עלויות חומרים, עלויות עבודה וכל שירות נוסף שהם מספקים.
- תקשורת ושיתוף פעולה:תקשורת ושיתוף פעולה יעילים חיוניים לשותפות מוצלחת. ודא שלשותף ההזרקה יש ערוצי תקשורת טובים, מגיב לפניותיך ויכול לספק עדכוני פרויקט שוטפים. גישה שיתופית תעזור להבטיח שאנו עומדים בדרישות שלך ונותנים מענה מיידית לכל אתגרים.
- הפניות וסקירות של לקוחות:חפש הפניות מלקוחות או קרא ביקורות/עדויות כדי לקבל תובנות לגבי חוויותיהם של לקוחות אחרים עם השותף להזרקה. השגת מידע זה יכולה לעזור לקבוע את מהימנותם, המהירות ורמת שביעות הרצון הכוללת של הלקוחות שלהם.
סיכום
הזרקה תרמופלסטית היא שיטה רב-תכליתית וחסכונית לייצור חלקי פלסטיק בכמויות גדולות. היכולת שלה לייצר צורות מורכבות בדיוק ועקביות גבוהות הפכה לבחירה פופולרית עבור תעשיות שונות, כולל רכב, רפואה, אלקטרוניקה ומוצרי צריכה. על ידי הבנת ההיבטים השונים של הזרקה תרמופלסטית, לרבות היתרונות, החסרונות ושיקולי העיצוב שלה, אתה יכול לקבל החלטות מושכלות לגבי בחירת השותף המתאים להזרקה לצרכי העסק שלך.